焦炉煤气脱硫脱氰方法研究
NNF法脱硫脱氰技术的应用与实践

燃料与化工Fuel&Chemical Processes Nov.2018Vol.49No.6法脱硫脱氰技术的应用与实践张加民朱灿朋北京首钢国际工程公司北京摘要:介绍了焦炉煤气脱硫脱氰的方法及NNF法脱硫脱氰工艺的原理和流程。
总结了NNF法脱硫脱氰工艺的特点和优势,并为后续NNF法脱硫脱氰装置优化设计提出新思路。
关键词:焦炉煤气;脱硫脱氰;NNF工艺;FRC法中图分类号:TQ546文献标识码:A文章编号:1001-3709(2018)06-0044-03Application of NNF process desulphurization and decyanation technologyZhang Jiamin Zhu Canpeng(B eijing Shougang International Engineering Co.,Ltd.,B eijing100043,China)Abstractwords收稿日期:2018-02-06作者简介:张加民(1979-),男,工程师基金项目:2018年11月第49卷第6期燃料与化工Fuel &Chemical Processes1.2 工艺流程与常规湿式脱硫流程基本相同煤气经过预冷塔冷却后进入脱硫塔在碱或催化剂的作用下吸收煤气中的2和净化后的煤气进入管网吸收后的富液自流至再生槽进行再生反应在脱硫液中3和2等杂质成为42x +14等盐类再生后的脱硫液经过冷却器送入脱硫塔循环使用为提高脱硫效率减少脱硫循环液中硫磺和铵盐的富集需要抽出一部分废液进行脱盐处理对于法法法等湿式氧化脱硫脱氰工艺而言亟需处理产生副盐的脱硫废液法的工艺产品为硫磺配套提盐系统工艺流程见图再生后抽出一定量富含硫磺和铵盐的脱硫液送入离心分离机分离后的硫磺在熔硫釜加热脱水熔融后取出硫磺产品分离后的滤液与熔硫釜出来的滤液一同被送至提盐工序提盐后的液体再返回再生塔循环使用图1 NNF 法脱硫工艺流程图2 NNF 法工艺应用与实践首钢国际首次在山西长治工业园区焦化项目中采用法脱硫工段总投资为万元其中设备投资为万元2.1 主要设计参数法脱硫脱氰为孔捣固焦炉配套脱硫工段主要设计参数见表和表表1 气体设计参数参数预冷塔前脱硫塔后煤气量(干)/(Nm 3·h -1)76623(最大)71610(正常)-温度/℃5038压力/kPa 25-NH 3/(g ·Nm -3)5~8-H 2S /(g ·Nm -3)7以下≦0.02HCN /(g ·Nm -3)1.5≦0.10表2 主要设备设计参数工艺参数设备参数/mm材质备注预冷塔 操作压力:25kPa,操作温度:50℃DN4000,H =16400碳钢聚丙烯花环填料脱硫塔 操作压力:25kPa,操作温度:35~40℃DN6600,H =46590碳钢聚丙烯花环填料再生塔操作压力:25kPa,操作温度:35~40℃DN11200,H =12500碳钢圆筒形空塔2.2 运行效果本工程于年月投产经调试后该套装置运行效果良好各项指标基本达到设计要求脱硫塔后出口煤气2含量变化见图图2 NNF 法脱硫后煤气中H 2S 含量2.3 工艺改进补充碱源法的碱源是焦炉煤气中固有的氨为达到设计要求煤气中氨含量应大于3当氨含量不足时脱硫脱氰的反应不完全同时铵盐的生成量较低脱除氰化氢所需的多硫化铵的量不足严重影响脱硫脱氰效率因此焦炉煤气中氨含量是法脱硫脱氰效果的关键因素在工程中出现过煤气中氨含量较低的情况实际检测到煤气中氨含量低于3时脱硫塔后的2含量超过3工程解决办法是向系统内补燃料与化工Fuel&Chemical Processes Nov.2018Vol.49No.6氨设计上是从后续工段蒸氨系统引出路氨源作为备用补氨系统提盐法脱硫脱氰系统中脱硫液在系统内循环一段时间后脱硫液中的铵盐和硫磺颗粒富集必须将一部分脱硫液抽出处理脱除富集的铵盐和硫磺颗粒在长治工程中把脱硫废液送至提盐系统实践发现提盐系统运行受设计操作及含盐浓度等因素影响提盐系统稳定与否是制约脱硫系统的另一因素如果采取脱硫废液焚烧制酸工艺则法脱硫受其他工序影响较小产品优化在法的硫磺工艺中硫磺产品品质不高纯度约为且为生硫磺产品附加值低故建议硫磺工艺改为脱硫废液焚烧制酸工艺2.4工艺特点与同类技术相比法具有脱硫效率高投资和运行费用低无排放无污染等优点几种脱硫脱氰工艺参数对比见表由表可知法脱硫效率可达以上脱氰效率可达以上脱硫脱氰后的煤气可达到城市煤气标准表3几种脱硫脱氰工艺特点参数NNF法真空碳酸钾法HPF法脱硫效率[11]99%98.5%96.4%脱氰效率[11]93%86%75%废液处理需要需要需要设备数量多多较少作业难易度比较容易很难比较难是否需用药品否2种否是否需用催化剂是否是产品质量低高低环境保护很好一般不符合法脱硫脱氰的主要设备是玻璃钢或不锈钢法主要脱硫设备可由普通碳钢制造大大降低了投资成本另外以煤气中的氨为碱源节省了脱硫原料所需苦味酸催化剂价廉易得且消耗少表为运行成本比较[12]表4运行成本比较(煤气处理量60000m3/h)元/km3脱硫脱氰工艺NNF法真空碳酸钾法HPF法运行成本6.5710.9578.02注:运行成本涵盖了产品销售价格。
PDS法焦炉煤气脱硫工艺分析

返回
工艺原理:
总反应方程式 2H2S + O2 → 2S + 2H2O 这方程式是整个脱硫的目的和整体过程,也是经常被大多数人忽略的一个反应方程 式,总方程式决定了总体思维模式。 3.2脱硫原理 对于无机硫: H2S+Na2CO3 → NaHS + NaHCO3 这是典型的复分解反应,也是酸碱中和反应,无须任何催化剂,即使加入催化剂, 也不能影响到反应平衡。 对于有机硫: RSH + Na2CO3 → RSNa + NaHCO3 虽然有机硫的平衡常数比无机硫小,但酸碱中和的推动力,能够使反应进行的深度 也很高。 3.3再生原理 对于无机硫: NaHS + 1/2 O2 → S + NaOH 对于有机硫: 2RSNa + 1/2 O2+ H2O → RSSR + 2NaOH
返回
工艺流程图:
返回
工艺分析:
PDS脱硫工艺是以酞菁钴磺酸盐系化合物的混合物为催化 剂的湿式氧化法脱硫工艺,其工艺过程与HPF工艺类同。 最初使用的PDS是双核酞菁钴六磺酸铵,后改进到二双核 酞菁钴砜+磺酸铵,其活性比原PDS提高一倍。PDS法硫 容量可大于0.5g/L,不发生堵塞,副产品盐类增长速度缓 慢,脱硫率大于97%,脱氰率大于95%,有机硫的脱除率 大于40%,PDS结合栲胶法可以达到更好的脱硫效果,该 工艺的缺点是产生大量废液不好处理,目前独立焦化厂使 用此工艺的较多。
PDS法焦炉煤气脱硫工艺分析
应化3141 张斌
关键词:焦炉煤气;PDS脱硫
人机化 含含 体硫氢 有有 也。及 焦多 未 有不多 油种 经 较但种 气 净 大污结 萘体 化 毒染构 氰组 的 害空复 化分 焦 性气杂 氢, 炉 。,的 ,尤 煤 对有 硫其 气 中
煤化工(焦化厂)焦炉煤气6大脱硫技术详解与脱硫工艺选择
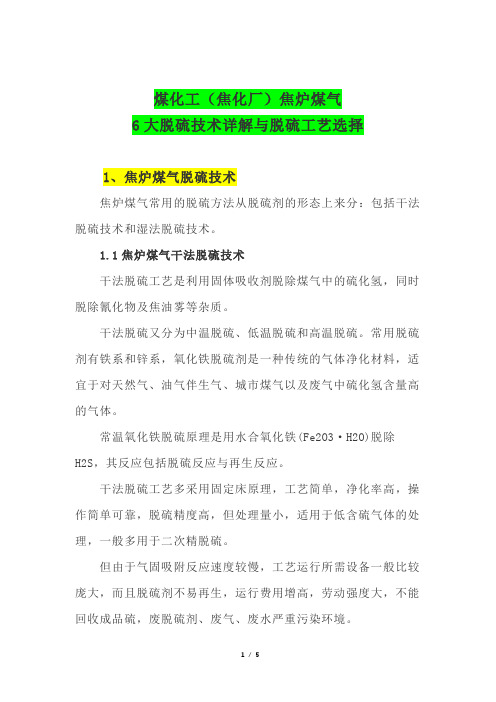
煤化工(焦化厂)焦炉煤气6大脱硫技术详解与脱硫工艺选择1、焦炉煤气脱硫技术焦炉煤气常用的脱硫方法从脱硫剂的形态上来分:包括干法脱硫技术和湿法脱硫技术。
1.1焦炉煤气干法脱硫技术干法脱硫工艺是利用固体吸收剂脱除煤气中的硫化氢,同时脱除氰化物及焦油雾等杂质。
干法脱硫又分为中温脱硫、低温脱硫和高温脱硫。
常用脱硫剂有铁系和锌系,氧化铁脱硫剂是一种传统的气体净化材料,适宜于对天然气、油气伴生气、城市煤气以及废气中硫化氢含量高的气体。
常温氧化铁脱硫原理是用水合氧化铁(Fe2O3·H2O)脱除H2S,其反应包括脱硫反应与再生反应。
干法脱硫工艺多采用固定床原理,工艺简单,净化率高,操作简单可靠,脱硫精度高,但处理量小,适用于低含硫气体的处理,一般多用于二次精脱硫。
但由于气固吸附反应速度较慢,工艺运行所需设备一般比较庞大,而且脱硫剂不易再生,运行费用增高,劳动强度大,不能回收成品硫,废脱硫剂、废气、废水严重污染环境。
1.2焦炉煤气湿法脱硫技术湿法工艺是利用液体脱硫剂脱除煤气中的硫化氢和氰化氢。
常用的方法有氨水法、单乙醇胺法、砷碱法、VASC脱硫法、改良 ADA法、TH 法、苦味酸法、对苯二酚法、HPF 法以及一些新兴的工艺方法等。
1.2.1 氨水法(AS法):氨水法脱硫是利用焦炉煤气中的氨,在脱硫塔顶喷洒氨水溶液(利用洗氨溶液)吸收煤气中 H2S,富含 H2S 和 NH3的液体经脱酸蒸氨后再循环洗氨脱硫。
在脱硫塔内发生的氨水与硫化氢的反应是:H2S+2NH3·H2O →(NH4)2S+2H2O。
AS 循环脱硫工艺为粗脱硫,操作费用低,脱硫效率在 90 %以上,脱硫后煤气中的 H2S 在200~500 mg·m-3。
1.2.2 VASC法:VASC法脱硫过程是洗苯塔后的煤气进入脱硫塔,塔内填充聚丙烯填料,煤气自下而上流经各填料段与碳酸钾溶液逆流接触,再经塔顶捕雾器出塔。
煤气中的大部分 H2S 和 HCN 和部分 CO2被碱液吸收,碱液一般主要是 Na2CO3或 K2CO3溶液。
真空碳酸钾法焦炉煤气脱硫脱氰工艺的特点

真空碳酸钾法焦炉煤气脱硫脱氰工艺的特点李玉秀白玮张爽(中冶焦耐工程技术有限公司,鞍山114002)1 概述真空碳酸钾法焦炉煤气脱硫脱氰工艺是使用碳酸钾溶液直接吸收煤气中的硫化氢和氰化氢,属于湿式吸收法脱硫工艺。
真空碳酸钾法脱硫脱氰后产生的酸性气体,既可以采用克劳斯法生产元素硫,也可以采用接触法生产硫酸。
马鞍山钢铁公司焦化厂和武汉钢铁公司焦化厂采用真空碳酸钾法脱硫、克劳斯法生产硫磺装置;鞍钢新区(鱿鱼圈)焦化厂和首钢京唐公司焦化厂采用真空碳酸钾法脱硫、接触法生产硫酸装置。
中冶焦耐公司在吸收国内外真空碳酸盐法脱硫工艺技术和生产实践的基础上,与高等院校合作,开发出了具有自主知识产权的脱硫脱氰新工艺,已在宝钢股份化工公司梅山分公司、韶钢焦化厂、邯钢新区焦化厂、天津天铁集团焦化厂、山西焦化、武钢防城港焦化厂等得到应用,脱硫后产生的酸性气体则采用丹麦托普索公司的WSA(湿接触法)制酸工艺。
2 真空碳酸钾法焦炉煤气脱硫工艺简述真空碳酸钾法脱硫装置设置在粗苯回收装置后,位于焦炉煤气净化流程的末端,工艺流程见图1。
图1 真空碳酸钾法脱硫装置的工艺流程来自洗苯塔后的煤气进入脱硫塔,煤气自下而上与贫液(碳酸钾溶液)逆流接触,煤气中的硫化氢和氰化氢等酸性气体被吸收。
其主要反应为:K2CO3+H2S → KHCO3+KHSK2CO3+HCN → KCN+KHCO3K2CO3+CO2+H2O → 2KHCO3同时,在脱硫塔上段加入一定碱液(NaOH),进一步脱除煤气中的硫化氢,使煤气中的硫化氢含量最终≤200mg/m3。
使用后的碱液(NaOH)用于蒸氨装置分解固定铵盐。
吸收了酸性气体的富液与再生塔底出来的热贫液换热后,由顶部进入再生塔再生,再生塔在真空和低温下运行,富液与再生塔底上升的水蒸汽接触,使酸性气体从富液中解吸出来,其反应如下:KHS+KHCO3→ K2CO3+H2SKCN+ KHCO3→ K2CO3+HCN2KHCO3→ K2CO3+CO2+H2O从再生塔顶出来的酸性气体经冷凝冷却和脱水后,用真空泵送至后续克劳斯装置生产元素硫或制酸装置生产硫酸。
焦炉煤气HPF脱硫废液的产生及处置

焦炉煤气HPF脱硫废液的产生及处置摘要:介绍了焦炉煤气的脱硫生产中脱硫废液的产生过程及危害,对目前存在的处理处置方法进行了分析和比较。
关键词:脱硫废液副盐一、焦炉煤气脱硫脱氰焦炉煤气是炼焦企业的主要副产品之一,含有大量化学产品。
随着煤化工产品线的延长,对焦炉煤气中化产品的回收利用也越来越广泛。
焦炉煤气中的硫化氢和氰化氢对于回收化学产品可能造成很大的危害,必须予以脱除。
二、脱硫脱氰工艺介绍目前,国内外焦炉煤气脱硫、脱氰的技术已达几十种之多,其中HPF脱硫脱氰工艺得到了广泛的应用。
目前国内约有50家规模不等的焦化厂脱硫系统采用了HPF工艺。
1.HPF脱硫工艺原理HPF脱硫工艺利用蒸氨工段的氨水作吸收剂,加入PDS、对苯二酚等催化剂将煤气中的H2S、HCN等酸性气体转化为硫氢酸铵等盐类,从而使焦炉煤气得到净化。
脱硫过程中的主要反应为[1]:通过上述反应可以看出,煤气中的硫化氢和氰化氢经过吸收转化进入到脱硫液中,并在催化剂的作用下形成了硫氢化铵、硫化铵、硫氰酸铵等物质,煤气得到净化。
2.脱硫液再生伴随上述脱硫反应的进行,脱硫液中产生了大量的硫氢化铵、硫化铵、硫氰酸铵等,抑制了脱硫、脱氰反应的进行,造成脱硫效率降低。
为了保持较高的脱硫效率,同时实现对脱硫液循环使用,必须对脱硫液进行再生处理。
再生过程如下[1]:脱硫富液中的硫氢化铵、硫化铵、硫氰酸铵大部分在催化剂的作用下与氧气反应生产单质硫、二氧化碳和氨水。
其中单质硫以固体硫膏的形式得到去除,CO2经吹脱后逸出,氨水继续使用,脱硫反应的主要产物得到了去除。
三、脱硫废液的产生及危害1.脱硫废液的产生在脱硫液再生过程中,除了2.2所示的反应外,还存在如下副反应[1]:上述副反应产生的NH4SCN、(NH4)2S2O3和(NH4)2SO4(通常被称为副盐)在脱硫液中不断积累,达到一定浓度后,严重影响再生反应的进行,进而影响硫化氢和氰化氢的吸收。
生产实际表明,当脱硫液中副盐浓度增长到250g/L后,塔后硫化氢含量就会超过50mg/L。
焦炉煤气中硫化氢和氰化氢的脱除

三、AutoCAD绘制楼梯详图(步骤)
楼梯剖面详图的绘制: 1.设置绘图环境; 2.绘制定位轴线、室外地坪线、楼面位
置线、梯段位置线等; 3.绘制墙体、楼板、梯段等构件; 4.绘制门、窗并补充细节; 5.标注; 6.打印出图.
小结
1.了解制图标准; 2.掌握建筑施工图的阅读方法; 3.掌握计算机绘制建筑施工图
14 详图所在图图号
25 页号
(不同图上)
ห้องสมุดไป่ตู้
(用标准图集)
剖面详图索引符号:
被剖切部位粗实线, 引出线表示剖切后投影方向
详图符号:直径为14毫米的粗实线园,细实线水平直径及编号。
12 详图编号
5
14 基本图所在页号
(详图与基本图在一张上) (详图与基本图不在一张上)
外墙身详图的阅读
1. 图名、比例; 2. 墙体轴线、墙厚、墙体与轴线的关系; 3. 各构件的断面形状、尺寸、材料及相
焦炉煤气中硫化氢和氰化氢的脱除
第五章
焦炉煤气中硫化氢和氰化氢的脱除
第一节 概述 第二节 焦炉煤气的干法脱硫 第三节 改良蒽醌二磺酸钠(改良ADA)法脱硫和栲胶法 第四节 HPF法脱硫 第五节 苦味酸法脱硫 第六节 氨水法脱硫
第一节 概述
一、脱除煤气中的硫化氢和氰化氢的重要性
二、脱除煤气中硫化氢和氰化氢的方法
目前我国焦化厂焦炉煤气脱硫的方法主要采用以下几 种:
1. 煤气干法脱硫 2. AS法脱硫 3. 改良ADA法和栲胶法脱硫 4. HPF法脱硫
第二节 焦炉煤气的干法脱硫
一、干法脱硫原理
国内许多焦化厂采用氢氧化铁法进行焦炉煤气的干法 脱硫。其脱硫原理为:将焦炉煤气通过含有氢氧化铁的脱 硫 剂 , 使 硫 化 氢 与 脱 硫 剂 中 的 有 效 成 分 Fe(OH)3 反 应 生 成 Fe2S3或FeS。当含硫量达到一定程度后,使脱硫剂与空气 接触,在有水存在下,空气中的氧将铁的硫化物氧化使之 又转变成氢氧化铁,脱硫剂得到再生,再重复使用。当煤 气中含氧时,则使脱硫剂的脱硫和再生同时进行。
焦炉煤气湿法脱硫脱氰工艺进展

焦炉煤气湿法脱硫脱氰工艺进展发布时间:2021-09-01T07:20:26.117Z 来源:《科学与技术》2021年第29卷第4月第12期作者:王万厂[导读] 焦炉煤气是指炼焦用煤在炼焦炉中经过一系列反应生成焦炭、焦油产品时伴随生成的可燃王万厂内蒙古恒坤化工有限公司内蒙古鄂尔多斯 016215摘要:焦炉煤气是指炼焦用煤在炼焦炉中经过一系列反应生成焦炭、焦油产品时伴随生成的可燃性气体。
焦炉煤气中包含硫化氢、氰化氢等有害物质,不仅会腐蚀设备,导致催化剂中毒,还会对环境造成破坏,威胁人们的生命健康。
因此,在使用焦炉煤气前需要去掉其中的有害物质,即脱硫脱氰。
关键词:焦炉煤气;脱硫脱氰;湿式氧化法引言:在炼焦时,煤中的部分硫转化为硫化物,因此焦炉煤气中一般含有 4~10 g/m3的硫化氢(H2S)、1.0~2.5 g/m3的氰化氢(HCN),这两种物质的腐蚀性很强,且有毒,如果不及时去除,会在煤气接下来的生产中腐蚀生产设备,导致催化剂中毒而失去催化作用,影响生产质量。
而且燃烧时产生的废气对环境会造成严重污染,并威胁人们的健康。
因此,必须采取有效的措施对焦炉煤气进行脱硫脱氰处理,以提升焦炉煤气的质量,防止生产设备被腐蚀,在减少环境污染的同时回收硫磺资源。
1 焦炉煤气脱硫脱氰工艺进展现阶段,我国的焦炉煤气脱硫脱氰工艺以煤气净化工艺为基础。
20世纪80年代,以宝钢为代表的钢铁企业先后引进了更加先进的脱硫工艺,如单乙醇胺(MEA)法、塔卡哈斯(TH)等。
然而我国很多焦化企业依然采用落后的蒽醌二磺酸钠ADA法、氢氧化铁干法,少部分焦化企业至今没有设置脱硫装置,而此时我国脱硫催化剂ZL脱硫脱氰工艺尚在摸索中。
20世纪90年代,我国焦化企业陆续引进氨-硫化氢循环洗涤法、苦味酸FRC法、真空碳酸盐法等脱硫工艺,随后以湿式氧化脱硫技术为基础研制出多种符合我国实际需求的煤气脱硫脱氰方法,如醌钻铁类催化剂HPF法、双核酞菁钴磺酸盐催化剂PDS法、酞菁钴络合物RTS法等。
工艺方法——焦炉煤气脱硫技术

工艺方法——焦炉煤气脱硫技术工艺简介焦炉煤气是炼焦过程的副产品,是H2、CH4、CO2、CO等气体组成的混合物,焦炉煤气的产率和构成取决于炼焦用煤的质量及炼焦过程操作条件。
焦炉煤气是一种高热值煤气,可作燃料使用,也可用作化工产品的重要原料,如合成氨、甲醇等。
焦炉煤气无论是作燃料,还是作生产原料,使用前需进行净化处理,以脱除煤气中H2S及HCN 等,满足环保和生产要求。
焦炉煤气脱硫工艺可分为干法脱硫工艺和湿法脱硫工艺2大类。
一、干法脱硫工艺干法脱硫工艺是指使用固体脱硫剂,在固定床层中进行H2S的物理或化学吸附、吸收与化学反应。
干法脱硫技术主要包括活性炭系、铁系、锌系、铜系、锰系及钙系等脱硫剂。
干法脱硫效率高,生产成本低,但脱硫剂需要定期更换,劳动强度大,同时失效的脱硫剂需进行处理。
因此,干法脱硫工艺主要用于湿法脱硫后的精脱硫。
二、湿法脱硫工艺湿法脱硫工艺是指利用液体形式的脱硫剂脱除煤气中的H2S和HCN。
按溶液的吸收和再生性质又分为湿式吸收法,包括物理吸收法、化学吸收法和物理-化学吸收法以及湿式氧化法。
湿法脱硫具有焦炉煤气处理量大、脱硫效率高等特点,在国内焦炉煤气脱硫中较为常用。
1、湿式吸收法湿式吸收法是以单乙醇胺、碳酸盐及氨溶液等不同的碱源作吸收液,吸收焦炉煤气中的H2S和HCN,吸收液在一定操作条件下经解吸释放出H2S等酸性气体,借助制酸工艺或克劳斯工艺,将酸性气体转化生成硫酸或硫磺产品。
湿式吸收法包括真空碳酸盐法、氨硫联合洗涤法及单乙醇胺法。
(1)真空碳酸盐法真空碳酸盐法脱硫工艺是—种物理—化学吸收方法,溶液中起吸收作用的是碳酸钠(或碳酸钾)。
焦炉煤气与吸收液逆流进行传质并发生反应,HCN、H2S及CO2被吸收液吸。
吸收了H2S的等酸性气体的溶液循环到再生塔,在一定操作条件下,H2S等酸性气体析出,实现吸收液的再生。
酸性气体经克劳斯法生成硫磺或经Topsoe法生成浓硫酸。
该工艺特点如下:脱硫剂单一,脱硫效率可达99%;产品质量好,硫磺纯度可达99.7%;采用真空解吸,操作温度低,为50-60℃,可有效利用循环氨水余热。
第五节焦炉煤气脱硫脱氰

第五节 焦炉煤气脱硫脱氰焦炉煤气中含硫化氢4~8g /m 3,氰化氢0.5~2g /m 3。
两者都是有害杂质,既腐蚀设备,又污染环境,危害人体健康。
因此,焦炉煤气必须脱硫脱氰。
目前,世界各国对焦炉煤气中硫化氢和氰化氢的含量作了限制,规定焦炉煤气用于冶炼优质钢时,硫化氢允许含量为1~2g /m 3;用作城市煤气时,硫化氢允许含量低于20mg /m 3,氰化氢含量低于5.0mg /m 3;供化工合成工业时,硫化氢允许含量为1~2mg /m 3。
焦炉煤气脱硫脱氰有干法和湿法两种工艺。
一、干法脱硫干法脱硫是一种比较古老的脱硫方法。
这种方法的工艺和设备都比较简单,操作和维修也比较容易,至今一些小焦化厂仍在使用。
但该法为间歇操作,占地面积大,脱硫剂的更换和再生工作的劳动强度大,现代化的大型焦化厂已不再采用。
干法脱硫通常以氢氧化铁为脱硫剂。
当焦炉煤气通过脱硫剂时,煤气中的硫化氢与氢氧化铁接触,生成硫化铁,这是吸收反应。
硫化铁与煤气中氧接触,在有水分的条件下,硫化铁转化为氢氧化铁并析出元素硫,这是再生反应。
干法脱硫的过程就是吸收反应和再生反应的多次循环。
其反应式为:Fe 2O 3·H 2O+3H 2S→Fe 2S·H 2O+3H 2OFe 2S 3·H 2O+23O 2→Fe 2O 3·H 2O+3S 干法脱硫的主要设备有箱式和塔式两种。
箱式脱硫器如图4-18所示。
它是用钢板焊制或用钢筋混凝土制成的长方形箱体,内壁涂沥青或沥青漆。
为了防止漏气,箱盖做成水封式,或用由螺栓压紧的橡皮垫圈密封。
箱高1. 5~2m ,箱内水平木格上装有四层脱硫剂,每层厚0. 3~0. 4m ,上下各留有空间,使气流分布均匀图4-18 箱式脱硫器塔式脱硫器如图4-18所示。
它是由钢板制成的直立圆筒,直径为6~9m ,高为12~18m 。
塔内叠置10~14个吊筐,筐中央留有圆孔,上下连接形成一条圆形直立通道。
焦炉煤气脱硫脱氰技术及优化建议
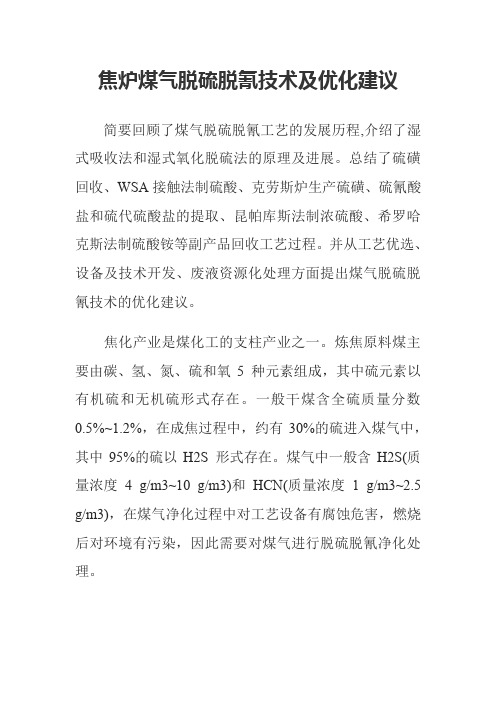
焦炉煤气脱硫脱氰技术及优化建议简要回顾了煤气脱硫脱氰工艺的发展历程,介绍了湿式吸收法和湿式氧化脱硫法的原理及进展。
总结了硫磺回收、WSA接触法制硫酸、克劳斯炉生产硫磺、硫氰酸盐和硫代硫酸盐的提取、昆帕库斯法制浓硫酸、希罗哈克斯法制硫酸铵等副产品回收工艺过程。
并从工艺优选、设备及技术开发、废液资源化处理方面提出煤气脱硫脱氰技术的优化建议。
焦化产业是煤化工的支柱产业之一。
炼焦原料煤主要由碳、氢、氮、硫和氧5 种元素组成,其中硫元素以有机硫和无机硫形式存在。
一般干煤含全硫质量分数0.5%~1.2%,在成焦过程中,约有30%的硫进入煤气中,其中95%的硫以H2S 形式存在。
煤气中一般含H2S(质量浓度 4 g/m3~10 g/m3)和HCN(质量浓度 1 g/m3~2.5 g/m3),在煤气净化过程中对工艺设备有腐蚀危害,燃烧后对环境有污染,因此需要对煤气进行脱硫脱氰净化处理。
笔者在煤气脱硫脱氰工艺原理分析的基础上,总结了副产品回收技术,并对煤气脱硫脱氰技术的优化提出建议,旨在促进新技术的开发。
1 焦炉煤气脱硫脱氰工艺发展简述目前,国内的煤气脱硫脱氰技术是在煤气净化工艺基础上建立的。
20 世纪70 年代以前,我国绝大部分焦化企业的焦炉煤气净化工艺沿用与原苏联20 世纪40 年代焦炉炉型相配套的初冷-洗氨-终冷-洗苯的煤气净化工艺流程,一般不设置脱硫装置,仅对氨进行回收。
20 世纪80 年代末开始,随着煤气净化技术的引进,宝钢等一些大型钢铁企业,陆续引进了MEA 法、TH 法等脱硫工艺。
但国内大部分焦化企业仍停留在采用氢氧化铁干法或ADA 法脱硫的阶段,甚至有些焦化企业没有脱硫装置。
此时,我国的ZL 脱硫脱氰工艺正处于研究探索阶段。
20 世纪90 年代初,国内焦化生产企业先后引进了FRC 法、氨-硫化氢循环洗涤法(AS 法)、真空碳酸盐法等脱硫技术。
之后在湿式氧化脱硫技术基础上,开发出了诸多适合我国国情的煤气脱硫脱氰新技术,如栲胶法、HPF法、PDS 法、888 法、APS 法、OMC 法、OPT 法、YST 法和RTS 法等,极大地推动了我国焦化行业湿式脱硫脱氰技术的发展[3]。
- 1、下载文档前请自行甄别文档内容的完整性,平台不提供额外的编辑、内容补充、找答案等附加服务。
- 2、"仅部分预览"的文档,不可在线预览部分如存在完整性等问题,可反馈申请退款(可完整预览的文档不适用该条件!)。
- 3、如文档侵犯您的权益,请联系客服反馈,我们会尽快为您处理(人工客服工作时间:9:00-18:30)。
焦炉煤气脱硫脱氰方法研究蔡 颖,赫文秀α(内蒙古科技大学生物与化学工程学院,内蒙古包头 014010) 摘 要 焦炉煤气中的硫化氢和氰化氢是非常有害的物质,在后续生产过程中对生产设备产生腐蚀、引起催化剂中毒、污染大气环境及影响人类健康,因此使用前必须首先脱硫脱氰。
本文详细论述了焦炉煤气脱硫脱氰国内外的研究现状,常见工艺,重点说明湿式氧化工艺的使用情况和研究状况,简略作一工艺比较。
关键词 焦炉煤气;脱硫脱氰;湿法 煤在炼焦过程中,约有30~35%的硫转化成硫化氢等硫化物,和氰化氢等一起进入煤气中,形成气体杂质。
焦炉煤气中一般含有硫化氢5~8g(m-3,氰化氢1~2.5g(m-3[1],硫化氢和氰化氢具有很强的腐蚀性、毒性,在煤气的后续生产过程中,对生产设备、管道产生极强的腐蚀,引起合成气化学反应催化剂中毒失活,严重影响最终产品的收率和质量;作为工业和民用燃料时,燃烧产生的排放废气中的硫化物,严重污染环境,危害人民健康,是必须严格控制的环境污染源之一。
因而不论是用于工业合成原料气,或用于燃料气,都必须按照不同用途的技术要求,采用相适应的工艺方法,将焦炉煤气进行脱硫脱氰净化处理,提高煤气质量,减少对环境的污染和设备的腐蚀,同时回收重要的硫磺资源。
1 焦炉煤气脱硫脱氰方法概述随着煤焦化行业的快速发展,国内外焦炉煤气脱硫脱氢技术及其为防止二次污染的废液(废气)处理技术已达50余种[1],有代表性的约10余种[1],如何合理选择符合生产实际的脱硫脱氢工艺技术,充分了解各种工艺方法及特点是十分必要的。
煤气的脱硫脱氰方法按吸收剂的形态可分为干法和湿法两大类。
1.1 干法脱硫[2][3]干法工艺是利用固体吸附剂脱除煤气中的硫化氢和有机硫,脱硫的净化度较高,适用于低含硫气体处理,多用于精脱硫,操作简单可靠,目前常用的脱硫剂为价廉的氧化铁,而其他如活性炭、分子筛、氧化锰、氧化锌等脱硫剂都较昂贵,较少使用;干法脱硫的设备庞大,脱硫剂更换频繁,消耗量大,不易再生,致使操作费用增高,劳动强度大,同时不能回收成品硫,废脱硫剂、废气、废水严重污染环境,因此一般不考虑干法脱硫工艺。
1.2 湿法工艺[2][3][4]湿法工艺是利用液体脱硫剂脱除煤气中的硫化氢和氰化氢,按溶液的吸收和再生性质又分为湿式氧化法、化学吸收法、物理吸收法和物理—化学吸收法。
湿式氧化法是利用碱液吸收硫化氢和氰化氢,在载氧体的催化作用下,将吸收的硫化氢氧化成单质硫,同时吸收液得到再生,是焦炉煤气脱硫脱氰比较普遍使用的方法,因其使用的催化剂的不同,湿式氧化法有改良ADA法、萘醌法、胶法、FRC法、TH法、H PF法、PD S法、O PT法、络合铁法、氨水催化法等;湿式吸收的三种方法主要用于天然气和炼油厂的煤气脱硫,不能直接回收硫磺,较少在焦炉煤气脱硫脱氰中使用。
2 国内外湿法脱硫工艺现状[5]~[14]从上世纪八十代初迄今二十多年来,国内焦炉煤气脱硫脱氰工艺不断进步和发展,新的工艺技术不断地用于工业生产,尤其是湿式氧化法脱硫工艺发展更快[4],在焦化行业应用极为广泛。
2.1 FRC法FRC法利用焦炉煤气中的氨在触媒苦味酸的作用下脱除硫化氢,利用多硫化铵脱除氰化氢。
FRC 法脱硫脱氰效率高,煤气经脱硫塔后,硫化氢含量可降到0.02g m3,氰化氢可降到0.1g m3;催化剂苦味酸耗量少且便宜易得,操作费用低;再生率高,新用空气量少,废气含氧量低,无二次污染。
但因苦味酸是爆炸危险品,运输贮存困难,且工艺流程长,占地多,投资高等因素使用受到限制。
2.2 TH法该技术由T akahax法脱硫脱氰和H irohax法废液处理两部分组成。
脱硫采用煤气中的氨为碱源,以1,4-萘醌2-磺酸钠为催化剂的氧化法脱硫脱氰工艺。
工艺特点:脱硫脱氰效率高,自带氨,运行成本低;煤气中的HCN先经脱硫转化为N H4SCN再经湿式氧化将其转化为(N H4)2SO4随母液送往硫铵装置,比其他流程的硫铵产量高;流程比较简单,操作费用低,蒸汽耗量少。
TH法脱硫工艺的不足:处理装置在高温高压和强腐蚀条件下操作,对主要设备的材质要求高,制造难度大;吸收所需液气比、再生所需要空气量较大,废液处理操作压力高,故整个装置电耗大,投资和运行费高;所需催化剂目前尚需进口。
由于上述种种原因,除宝钢有这套装置外,其他1 2006年第10期 内蒙古石油化工α焦化厂尚未采用此工艺。
2.3 改良A.D.A法该工艺是以钠为碱源,以钒作为脱硫的基本催化剂,蒽醌二磺酸钠(A.D.A)作为还原态钒的再生载氧体,适量添加酒石酸钾钠(或少量三氯化铁及乙二胺四乙酸)组成脱硫液,脱硫效率高,国内比较普遍应用在城市民用煤气净化工艺中。
该工艺存在的主要问题有:悬浮液的硫磺颗粒小,回收困难,易造成过滤器堵塞;有副反应发生,使脱硫液消耗量增大;脱有机硫和氢化氰的效率差;脱硫废液处理困难,国内工业化装置多采用提盐工艺,但流程长、操作复杂、能耗高、操作环境恶劣、劳动强度大、所得盐类产品如硫氰酸钠、硫代硫酸钠品位不高,经济效益差,易造成二次污染;有细菌积累;腐蚀严重。
2.4 栲胶法(TV法)栲胶法是我国特有的脱硫技术,是目前国内使用较多的脱硫方法之一。
该法主要有碱性栲胶脱硫(以橡碗栲胶和偏钒酸钠作为催化剂)和氨法栲胶(以氨代替碱)2种。
栲胶是由植物的果皮、叶和干的水淬液熬制而成,主要成分是丹宁。
由于来源不同,丹宁组分也不同,但都是由化学结构十分复杂的多羟基芳香烃化合物组成,具有酚式或醌式结构。
栲胶法有如下特点:栲胶资源丰富,价廉易得,运行费用比改良ADA低;基本上无硫堵塔问题;栲胶既是氧化剂又是钒的配合剂,溶液的组成比改良ADA的简单;栲胶脱硫腐蚀性小;栲胶需要熟化预处理,栲胶质量及其配制方法得当与否是决定栲胶法使用效果的主要因素。
2.5 PD S法PD S法是以双核酞菁钴磺酸盐为脱硫催化剂的脱硫方法,由国内自主开发,目前在国外尚未有成功的使用双核酞菁钴磺盐进行工业化气体脱硫的报道。
PD S催化剂活性好,用量小,无毒。
其工艺特点:脱硫脱氰能力优于ADA溶液;抗中毒能力强,对设备的腐蚀性小;易再生,再生时浮出的硫泡沫颗粒大,易分离,硫磺回收率高,还能脱除部分有机硫;催化剂可单独使用,不加钒,无废液排出;脱硫成本只有ADA法的30%左右,有显著的经济效益。
该方法经过不断改进和完善,PD S可以和ADA、栲胶联合使用,效果很好;催化剂也已由最初的原型,开发到目前的P-400、888型等,形成诸如H PF法等新方法。
2.6 H PF法H PF法是国内自行开发的以氨为碱源,H PF为复合催化剂的湿式液相催化氧化脱硫脱氰工艺。
H PF催化剂活性高、流动性好,不仅对脱硫脱氰过程起催化作用,而且对再生过程也有催化作用,脱硫脱氰效率高。
该方法在脱硫脱氰过程中,循环脱硫液中盐类积累速度缓慢,废液量较其他湿式氧化法少,直接回兑炼焦配煤中,处理简单和经济。
研究表明,在焦炉的炼焦条件下,搀入配煤中的脱硫废液的盐类,在炭化室内高温裂解生成硫化氢后,大部分进入荒煤气,仅有极少部分与焦碳反应。
而废液中的N H4SCN高温裂解时转化为氮、氨和二氧化碳,并不转化为氰化氢。
因此,煤气脱硫脱氰装置中不会产生N H4SCN 的积累问题,流程短,一次性投资少。
但是硫磺质量差,收率低,熔硫操作环境有待改善。
3 结语焦炉煤气中的硫化氢、氰化氢是有毒物质,无论从环保需要,还是从资源回收利用考虑,都应对煤气进行脱硫脱氰。
目前采用的各种焦炉煤气脱硫工艺各有优缺点。
目前采用较多的氨法H PF脱硫工艺,脱硫脱氰效率高,脱硫后煤气含硫化氢量可降至0.05g m3以下;由于脱硫脱氰装置设置在氨回收装置前,大大减轻了终冷和粗苯等后续装置设备及管道的腐蚀;流程简单,革除黄血盐装置,且投资省,原材料和动力消耗低,可大幅度降低煤气净化过程中的蒸汽消耗量;若增设废气处理装置和脱硫废液回兑配煤的装置,可使H PF工艺成为真正的无污染工艺。
PD S法也是非常具有竞争力的方法,其脱硫成本只有ADA 法的30%左右,脱硫脱氰能力优于ADA法,对原有采用改良ADA法的脱硫装置,增加PD S溶液滴加设备,即可将改良ADA法脱硫改为PD S法,具有显著的经济效益和社会效益。
参考文献[1] 肖瑞华,白金锋主编.煤化学产品工艺学[M].北京:冶金工业出版社,20031[2] 王睿,石冈等.工业气体中H2S的脱除方法.天然气工业[J].1999(5):84~901[3] 王泽民.煤气脱硫工艺探讨.江西化工[J].1999(4):28~291[4] 朱文利,刘运良.焦炉煤气脱硫方法评述[J].洁净煤技术.1997,3(3):34~371[5] 梁锋,徐丙根等.湿式氧化法脱硫的技术进展.现代化工[J].2003,23(5):21~241[6] 顾德华.酒钢90000Nm3 h焦炉煤气脱硫脱氰工艺参数选择.甘肃冶金[J].2005,27(3):29~331[7] 徐翰初,韩永霞,宫玉秀.焦炉煤气净化新技术.山东冶金[J].2004,26(2):1~61[8] 徐翰初,韩永霞,宫玉秀.焦炉煤气净化新技术.山东冶金[J].2004,26(3):1~51[9] 江建方,削波等.焦炉煤气净化工艺研究进展.化工环保[J].2003,23(1):17~211[10] 刘玲.PD S脱硫技术的应用.化学工业与工程技术[J].2003,24(4):42~441[11] 杨宪文,王燕飞等.PD S法高硫煤气净化工艺的研究.化肥工业[J].1997,24(4):20~251[12] 解宝灵.栲胶法脱硫在焦炉煤气中的应用.山西能源与节能[J].2002,27(4):38~391[13] 张兴柱.H PF湿式氧化法焦炉煤气脱硫脱氰技术.燃料与化工[J].2003,34(4):205~2061[14] 钟锦明,董天和,杜占文.氨法H PF焦炉煤气脱硫工艺的开发.燃料与化工[J].1997,28(5):152~15612内蒙古石油化工 2006年第10期 。