陶瓷成型方法
陶瓷材料的成型方法(一)

陶瓷材料的成型方法(一)陶瓷材料已经成为我们生活中一个智能更要的工具了,在现代陶瓷材料的生产中,常用的成型方法有挤制成型、干压成型、热压铸成型、注浆成型、轧膜成型、等静压成型、热压成型和流延成型等。
1.挤制成型挤制成型主要用于制造片形、棒形和管形制品,如电阻的基体蜂窝陶瓷载体的陶瓷棒、陶瓷管等陶瓷制品。
该成型方法生产效率高,产量大、操作简便,使用的挤压机分卧式和立式两种。
配料中新土含量较大时,成型的坯料一般不加黏合剂,配料经过真空练泥、闲料后即可用于挤制成型。
坯料中一般含水量为16%一25%。
配料中含茹土少或不含教土时,将均匀混合了熟合剂的粉料经真空练泥和闲料后,再用于挤制成型。
挤制成型的氧化铝瓷球常用的教合剂有糊精、桐油、甲基纤维素(MC)、羧印基纤维素、泽丙基甲基纤维素(HPMC)和亚硫酸纸浆废液等。
挤制资管时应注意防止坯体变形,管的外径越大,壁越薄,机械强度越差,越容易变形。
2.干压成型干压成型是最常用的成型方法之一,适用于成型简单的瓷件,如圆片形等,对模具质量的要求较高。
该方法少产效率高,易于自动化,制品烧成收缩率小,不易变形。
干压成型方法所用坯料的含水量一般控制在4%一8%左右。
干压常用熟合剂主要有聚乙烯醇(PVA)水溶液、石蜡、亚硫酸纸浆废液等。
通常配料中黏合剂的加入量为:聚乙烯醇水溶液3%一8%、石蜡8%左右、亚硫酸纸浆废液10%左右。
干压成型是利用模具在泊压机上进行的。
干压成型的加压方式有单面加压和双面加压两种。
直接受压一端的压力大,坯体密度大;远离加压一端的压力小,密度小。
金属填料的双面加压时坯体两端直接受压,两端密度大,中间密度小。
造粒料并加润滑剂时,双面加压的尔意图,坯体密度非常均匀。
成型压力的大小直接影响资体的密度和收缩率。
如某BaTiO3系资料,外加5%聚乙烯醇水溶液造粒,在相同烧成条件下,成型压力为0.5MPa时,收缩系数为1.15—1.16;成型乐力为0.6MPa时,收缩系数为1.13—1.14;成型压力为0.7MPa时,收缩系数为1.11-1.12;成型压力为0.8MPa时,收缩系数为1.03。
传统陶瓷板的成型方法

传统陶瓷板的成型方法
传统陶瓷板的成型方法主要有以下几种:
1. 干压成型:干压成型是最常用的成型方法之一,也是手机陶瓷背板主流的成型工艺之一。
它需要将经过造粒、流动性好、颗粒级配合适的粉料装入金属模腔内,然后通过压头施加压力,使模腔内粉体颗粒重排变形而被压实,形成具有一定强度和形状的陶瓷素坯。
2. 等静压成型:等静压成型是在传统干压成型基础上发展起来的特种成型方法。
它利用流体传递压力,从各个方向均匀地向弹性模具内的粉体施加压力,使粉体在各个方向承受的压力都一样,因此能避免坯体内密度的差别。
等静压成型的陶瓷结构件具有均匀致密的坯体、烧成收缩较小且各个方向均匀收缩等优点,但设备较为复杂、昂贵,生产效率也不高,只适合生产特殊要求的材料。
3. 湿法成型:注浆成型是湿法成型的一种。
请注意,传统陶瓷板的成型方法可能因材料、工艺和设备等因素而有所不同。
在实际应用中,应根据具体情况选择合适的成型方法。
陶瓷成型方法

陶瓷成型方法
1. 手工成型:传统的陶瓷制作方法,艺术性强,表现力丰富,但制作速度慢,效率低。
2. 模具成型:通过将陶瓷原料压入模具中,辅以压力使其成型,效率高,但制作过程中难以控制细节。
3. 电子成型:利用专门的CAD系统将设计图转换为数字信号,再通过特殊设备将陶瓷原料成型,制作速度快,精度高,但设备价格昂贵。
4. 注射成型:利用氧化铝陶瓷高压注射机将陶瓷原料注入特定模具中成型,制造精度高,成型时间短,但需要较高的生产能力。
5. 吸塑成型:将陶瓷粉末与塑料混合后进行吸塑,成型速度快,成本较低,适合大批量生产,但制作出的产品密度、耐蚀性等性能差距较大。
古代瓷器的6种成型方法

1、手工捏塑法人们用手随心所欲地对泥土进行创作,捏出一些较小的器物,这是最原始最简单的成型方法。
2、泥条盘筑法将泥土搓成泥条,从器底起从下往上将泥条盘筑成器壁直至器口,再用泥浆胶合成全器,最后抹平器壁盘筑时留下的泥缝。
此法出现在新石器时代中期。
3、泥片围接法将原料泥块先加工成泥片,然后将泥片围接组合成需要的形状,如宜兴紫砂茶壶多用此法做成。
4、轮制成型法将泥料放置于轮盘,利用轮盘转动产生的离心力而成型的方法。
它主要用于圆体器型的制作,轮制有慢轮、快轮之分。
5、印模法将泥料嵌入特制的模子中成型的方法。
主要用于制作陶瓷俑、动物和器物部件、纹饰等。
6、注浆法把泥料灌入石膏等模子中,利用石膏模型的毛细管作用力将悬浮的浆料吸附于模具内壁而成型的方法。
注浆法大大提高了胎体的产量和质量,有利于陶瓷生产的发展。
怎样挑选瓷器方法一:一、购买陶瓷餐具一定要选择正规的市场和店面,切不可贪便宜购买没有正式生产厂家的劣质产品。
国家规定,将陶瓷餐具置于4%的醋酸中浸泡,铅的溶出量不得大于7毫克/升,镉的溶出量不得大于0.5毫克/升。
二、购买时要注意看餐具的成色,用手触摸餐具表面,看内壁是否光洁;三、闻闻是否有异味;四、不要购买颜色过于鲜艳的陶瓷餐具。
通常颜色越鲜艳的餐具,重金属就越容易超标;五、应购买原料、工艺控制比较严格的釉中彩、釉下彩餐具;六、餐具使用前用沸水煮5分钟或用食醋浸泡2—3分钟,以溶解方法二:1、看色泽这里说的看色泽主要是看骨瓷的不覆盖花面的胎体部分的色泽,真正骨炭含量高的优质骨瓷,其色泽应该是乳白色或者称为奶白色。
骨瓷不是越白越好,自然的乳白色才是好的骨瓷。
2、听声音听声音有两种方法,第一种就是把瓷器碗托在一只手的手心中(注意:一定不要抓在手心中),另一只手弹下骨瓷的碗口边缘处,好的骨瓷声音清越如钟声一样有清脆的回音,响声越长久说明胎体更圆滑,瓷的品质更好。
第二种就是注入碗中三分之一左右的水,一只手沾些水沿着碗边转会发出“唧唧”的共鸣声,碗越大效果越明显。
陶瓷成型技法

陶瓷成型技法
陶瓷成型技法是指在陶瓷制作过程中所采用的一系列成型方法和工艺。
下面是一些常见的陶瓷成型技法:
1. 捏塑法:利用手揉、捏、压、拉等手法将陶土进行成型,是最原始也是最简单的陶瓷成型技法。
2. 制模法:先制作一个模具,然后将陶土填充在模具中进行成型。
常见的模具有木模、石膏模等。
3. 轮盘法:将陶土放在旋转的陶轮上,通过双手或工具的操作,使陶土成型。
4. 出胚法:用陶土制作出胚,然后在胚上进行雕刻、切割等工艺,最后再烧制成为陶瓷作品。
5. 造型法:利用刀、铲等工具对陶土进行削减、切割、雕刻等方式进行成型。
6. 手捻法:将陶土在手中捻成不同形状的器物,常用于制作简单的杯子、碗等。
7. 装饰法:在成型的陶瓷作品上进行装饰,常见的装饰技法有刻画、绘画、粘贴等。
8. 粘砖法:将陶土切割成不同形状的砖块,再用粘结剂将砖块黏结在一起。
以上是一些常见的陶瓷成型技法,根据制作的需要和设计的要求,可以灵活运用这些技法进行陶瓷制作。
陶瓷原位凝固胶态成形基本原理及工艺过程
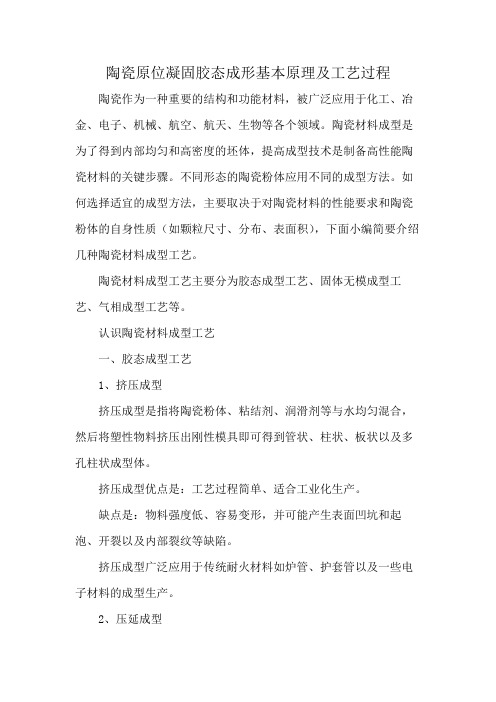
陶瓷原位凝固胶态成形基本原理及工艺过程陶瓷作为一种重要的结构和功能材料,被广泛应用于化工、冶金、电子、机械、航空、航天、生物等各个领域。
陶瓷材料成型是为了得到内部均匀和高密度的坯体,提高成型技术是制备高性能陶瓷材料的关键步骤。
不同形态的陶瓷粉体应用不同的成型方法。
如何选择适宜的成型方法,主要取决于对陶瓷材料的性能要求和陶瓷粉体的自身性质(如颗粒尺寸、分布、表面积),下面小编简要介绍几种陶瓷材料成型工艺。
陶瓷材料成型工艺主要分为胶态成型工艺、固体无模成型工艺、气相成型工艺等。
认识陶瓷材料成型工艺一、胶态成型工艺1、挤压成型挤压成型是指将陶瓷粉体、粘结剂、润滑剂等与水均匀混合,然后将塑性物料挤压出刚性模具即可得到管状、柱状、板状以及多孔柱状成型体。
挤压成型优点是:工艺过程简单、适合工业化生产。
缺点是:物料强度低、容易变形,并可能产生表面凹坑和起泡、开裂以及内部裂纹等缺陷。
挤压成型广泛应用于传统耐火材料如炉管、护套管以及一些电子材料的成型生产。
2、压延成型压延成型是指将陶瓷粉体、添加剂和水混合均匀,然后将塑性物料经两个相向转到滚柱压延,而成为板状素坯的成型方法。
压延法成型优点是:密度高,适于片状、板状物件的成型。
3、注射成型陶瓷注射成型是借助高分子聚合物在高温下熔融、低温下凝固的特性来进行成型的,成型之后再把高聚物脱除。
注射成型优点是:可成型形状复杂的部件,并且具有高的尺寸精度和均匀的显微结构。
缺点是:模具设计加工成本和有机物排除过程中的成本比较高。
目前,注射成型新技术主要有水溶液注射成型和气相辅助注射成型。
(1)水溶液注射成型水溶液注射成型采用水溶性的聚合物作为有机载体,很好的解决了脱脂问题。
水溶液注射成型技术优点是:自动化控制水平高,而且成本低。
(2)气体辅助注射成型气体辅助注射成型是把气体引入聚合物熔体中而使成型过程更容易进行。
适合于腐蚀性流体和高温高压下流体的陶瓷管道成型。
4、注浆成型注浆成型工艺是利用石膏模具的吸水性,将制得的陶瓷粉体浆料注入多孔质模具,由模具的气孔把浆料中的液体吸出,而在模具中留下坯体。
陶瓷的三大成型方法

陶瓷的三大成型方法
陶瓷是一种古老的工艺品,制作陶瓷的方法也有很多种。
在这里,我们将介绍陶瓷的三大成型方法:手工制作、轮盘制作和压制制作。
手工制作是最传统的制作陶瓷的方法之一。
这种方法需要使用手工工具,如刀子、刮刀和模具等,将陶泥塑成所需要的形状。
手工制作需要一定的技巧和经验,但可以制作出非常独特和精美的陶瓷作品。
轮盘制作是一种使用陶瓷轮盘的制作方法。
这种方法需要将陶泥放在轮盘上,然后利用手的力量使轮盘旋转。
在旋转的同时,使用手工工具将陶泥塑成所需要的形状。
这种方法可以制作出形状规整、大小一致的陶瓷作品。
压制制作是一种使用陶瓷模具的制作方法。
这种方法需要将陶泥放在模具内部,然后使用手的力量将陶泥压实。
在陶泥变硬之后,将陶瓷从模具中取出。
这种方法可以制作出形状相同、大小一致的陶瓷作品。
除了这三种成型方法外,还有其他的制作方法,如注模制作、挤出成型等。
每种方法都有其独特的优点和缺点,可以根据需要选择适合自己的制作方法。
无论使用哪种制作方法,制作陶瓷都需要注意以下几点:
1. 选择好的陶泥。
陶泥质地、水分含量等因素都会影响成型效果。
2. 考虑好陶瓷的用途。
不同用途的陶瓷需要不同的形状、大小和材质等。
3. 注意细节。
陶瓷的细节处理非常重要,如刻线、打磨等。
4. 控制好温度和湿度。
陶瓷制作需要一定的温度和湿度,需要注意控制好这些因素。
总的来说,陶瓷制作需要一定的技巧和经验,但是也需要耐心和细心。
只有这样,才能制作出精美的陶瓷作品。
陶艺的制作的七种方法

陶艺的制作的七种方法包括:⑴捏塑成型法——用挤、压、抹的方法,归纳起来,用手直接对泥料进行揉、搓、捏、挤、压、抹等最原始、最纯朴的操作,并加以简单的辅助工具,使泥料成型的方法就叫作捏塑成型法。
捏塑成型法在陶艺制作中广泛运用,不同比例大小的陶艺作品都可以通过捏塑成型的方法来制作。
⑵泥条成型法——是一项需要精确、技能和时间的艺术形式,也是一门非常古老原始及世界广为运用的陶艺技法。
从我国现已出土的原始陶器中,仔细观察能够发现有泥条成型的痕迹。
泥条成型的壶、罐和雕塑能在博物馆内见到。
②泥条成型法较为常见的是盘筑..,就是将泥条一圈一圈能过围绕、粘接而构筑成形体,后再进行整修、刮划、打磨等艺术加工,使泥条痕迹不易表露。
除了盘筑外,还可以有些较为现代和个人化的表现,如泥条竖立成型、泥条编织成型等。
③搓泥条的方法:双手将泥块捏成粗条,然后反粗泥条压在桌上前后滚动,并向两边用力拉伸,最后搓成一根粗细均匀的泥条。
⑶泥板成型法——将泥块通过人工或压泥机滚压成泥板,然后用这些泥板来塑造作品的方式,传统也称为镶器成型。
制作时利用湿泥的柔软特点,可以随意扭曲、挤压塑造造型;利用干泥的坚硬特点,也可以进行泥板拼贴、粘接来造型。
在黏结中要求使用的的泥板保持干湿度的一致。
⑷拉坯成型法——拉坯成型是陶艺造型的又一种方法,它是借助于陶车转盘的快速转动来进行手工拉制坯体造型,同时它也是最广泛应用的一种成型方法,但是拉坯需手、脑及全身配合默契,高度协调的手工造型方法,要求具有一定技艺,需在多次练习中慢慢掌握拉坯造型的一些方法和技巧,通过反复练习,熟而生巧才能完成造型创作。
⑸模具成型法——①压坯成型法——指将干粉或湿泥放入模具中,用机器压出造型的方法,可以分为干粉压坯成型和湿泥压坯成型。
有些志砖就是干粉压制成型的,而有些杯子或盘子是由湿泥压制成型的。
②印坯成型法——把模具分成若干片,把擀好的泥片分别粘在石膏模具上,然后进行黏结组合。
印坯成型和注浆成型原理一样,通过石膏模具吸收水分成型。
陶瓷成型方法
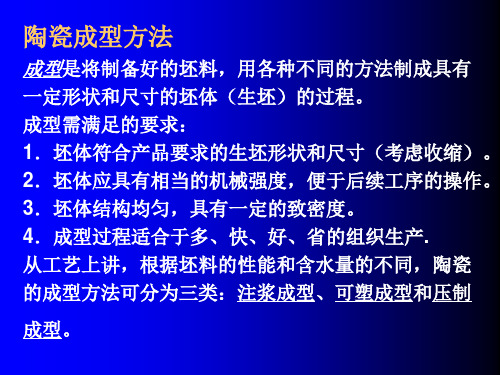
2、热压铸成型工艺
3、热压铸成型工艺 主要工艺参数:
(1) 腊浆温度:60~75℃,温度升 高,则腊浆的粘度下降,坯体致 密,但冷却收缩相应大。温度过 低,则易出现欠注、皱纹等缺陷。 (2) 钢模温度。决定坯体冷却凝固 的速度。一般为20~30℃。 (3) 成型压力:与浆桶深度、料浆 性能有关。压力升高,坯体的致 密度增加,坯体的收缩程度下降。 一般可以采用0.3~0.5 MPa。
3、强化注浆成型方法
(注浆方法的改进)
在注浆过程中人为地施加外力,加速注浆过程的进行,使吸浆 速度和坯体强度得到明显改善的方法。 1) 真空注浆 模具外抽真空,或模具在负压下成型,造成模具内外压力差, 提高成型能力,减小坯体的气孔和针眼。
2)
离心注浆
使模型在旋转情况下进浆,料浆在离心力的作用下紧靠 模壁形成致密的坯体。气泡较轻,易集中在中间最后破 裂排出,故可提高吸浆速度与制品质量。要求:泥浆中 的颗粒分布范围窄,否则大颗粒集中在靠近模型的坯体 表面,而小颗粒集中在坯体内面,造成坯体组织不均匀, 收缩不一致。
2. 滚压成型的主要控制因素 (1) 对泥料的要求:水分低、可塑性好。成型时模具 既有滚动,又有滑动,泥料主要受压延力的作用。要求有 一定的可塑性和较大的延伸量。可塑性低,易开裂;可塑 性高,水分多易粘滚头。阳模滚压和阴模滚压对泥料的要 求有差别。阴模滚压受模型的承托和限制,可塑性可以稍 低,水分可稍多。 (2) 滚压过程控制:分压下(轻)、压延(稳)、抬起 (慢)阶段。 (3) 主轴转速(n1)和滚头转速(n2) :控制生产效率; 对坯料的施力形式,控制坯体的密度均匀和表面光洁。 滚压头的温度热滚压:100~130℃,在泥料表面产生一 层气膜,防止粘滚头,坯体表面光滑。冷滚压:可用塑料 滚压头,如聚四氟乙烯。
陶瓷基本知识——陶器成型的六种方法

陶器成型的六种方法商·白陶刻饕餮纹双系壶陶器的成型方法有多种,它有一个不断进步的发展过程。
根据考古研究,已知的制陶方法有:1.捏制;2.泥片贴筑法手制;3.泥条盘筑法手制;4.轮制;5.模制;6.雕塑法手制等。
也许还有别的某种古代制陶方法,只是尚未考证出来,那就有待今后的发现。
1.捏制是最初的制陶方法,也是最简便容易的方法,也就是用手捏成形状,属于手制的一种。
捏制方法在小型陶塑中经常使用,捏制的器皿比较少见,往往是粗糙的、不规整的,也比较小型。
在其他进步方法大量使用的情况下,捏制也偶尔采用,只是用于不需要太讲究的陶器上,尤其是陶塑。
晚期陶塑如果仅仅只是捏制,没有采用雕塑方法,可以反映出制作的草率、随便,甚至可能缺乏工艺价值。
2.泥片贴筑法是一种较早使用的手制方法,它是用捏制的粘湿的泥片,在一个类似内模的物体外面,一块一块敷贴成陶器整体,一般是从下往上敷贴,至少以两层薄片贴合起来,有的多达数层。
有学者干脆认为它是一种模制法,但实际上同模制方法还是有明显区别的,所谓的内模,其实并不是模子,而应该是一种陶垫。
在外表加工上,也已使用了陶拍和抹子。
因而这已是初具成熟的方法,看来并不是最原始的。
从考古出土的陶器上观察,可以见到陶器上时有片块状剥落现象,在陶片上可看出成层挤压现象。
这种方法成型的陶器,常显厚重,形状不太规则,口沿也不很整齐。
考古发现和研究表明,在我国距今七八干年以前的新石器时代早期文化中,普遍都是采用这种泥片贴筑的制陶术。
这种制陶方法的发现和确认,也只是在七八十年代以来,大批早期新石器时代文化遗存被认识和发掘出土之后,才被考古学家考证的。
泥片贴筑法大约在距今六七千年左右的时候,逐渐为新起的泥条盘筑法制陶术所取代。
3.泥条盘筑法是继泥片贴筑方法之后,较为进步的一种陶器手制方法,它是较广泛持久使用的制陶术之一。
此法是将泥料做成泥条,然后从下至上盘绕成型,再用陶垫、陶拍、陶抹等工具抵压、抹拭、仔细加工。
陶瓷的五种成型方法

陶瓷的五种成型方法陶瓷是一种广泛应用于日常生活和工业领域的材料,成型是陶瓷制作的重要环节。
本文将介绍陶瓷的五种成型方法,包括手工成型、模具成型、轮盘成型、注浆成型和挤出成型。
一、手工成型手工成型是最古老、最传统的陶瓷成型方法之一。
通过手工将陶泥塑造成所需形状,然后进行干燥和烧制。
手工成型的优点是灵活性强,可以根据需求进行自由创作,但是生产效率较低。
二、模具成型模具成型是一种常用的陶瓷成型方法。
首先制作出所需形状的模具,然后将陶泥放入模具中,经过压实、挤压等工艺,使陶泥成型。
模具成型的优点是生产效率高,形状一致,但是对于复杂形状的陶瓷制品较难实现。
三、轮盘成型轮盘成型是一种利用陶瓷轮盘进行成型的方法。
陶泥放在旋转的轮盘上,通过手工操作使陶泥成型。
轮盘成型的优点是成型速度快,形状规整,但是对于大型陶瓷制品不适用。
四、注浆成型注浆成型是一种利用注浆机进行成型的方法。
将陶泥制成浆状,通过注浆机注入到模具中,经过一段时间的固化后,取出成型的陶瓷制品。
注浆成型的优点是生产效率高,制品表面光滑,但是对于细节丰富的陶瓷制品较难控制。
五、挤出成型挤出成型是一种利用挤出机进行成型的方法。
将陶泥制成柱状,通过挤出机的压力将陶泥挤出成所需形状。
挤出成型的优点是生产效率高,制品成型快速,但是对于复杂形状的陶瓷制品较难实现。
总结起来,陶瓷的成型方法包括手工成型、模具成型、轮盘成型、注浆成型和挤出成型。
不同的成型方法适用于不同的陶瓷制品,根据需求选择合适的成型方法可以提高生产效率和产品质量。
陶瓷制品的成型过程需要经过多道工序,包括制模、成型、干燥和烧制等,每一道工序都需要严格控制,以确保最终的陶瓷制品质量。
希望通过本文的介绍,能够让读者对陶瓷的成型方法有更深入的了解。
陶瓷的成型方法

陶瓷的成型方法陶瓷是一种广泛应用的材料,它在生活、建筑、工业等方面都有着重要的作用。
而陶瓷的成型方法是制作陶瓷制品的关键步骤之一。
本文将介绍几种常见的陶瓷成型方法。
1. 手工塑型手工塑型是最古老、最基础的陶瓷成型方法之一。
它通过手工将陶土塑造成所需的形状。
首先,将陶土揉搓成一定的软硬度,然后使用手指、工具等将其塑造成所需的形状。
这种方法制作的陶瓷制品具有独特的手工感,常见的有陶瓷花盆、陶瓷雕塑等。
2. 旋转成型旋转成型是一种利用旋转机械进行成型的方法。
在旋转成型机上,将陶土放置在转盘上,通过转动盘面和手工塑造的方式,将陶土成型。
这种方法可以制作出各种形状的陶瓷制品,如碗、盘、杯等。
旋转成型制作的陶瓷制品形状规整,表面光滑。
3. 注塑成型注塑成型是一种利用模具进行成型的方法。
首先,将陶土制作成一定的浆状,然后将其注入模具中,经过一定的压力和时间,陶土在模具中成型。
注塑成型可以制作出复杂形状的陶瓷制品,如花瓶、餐具等。
这种方法制作的陶瓷制品精度高,形状规整。
4. 压制成型压制成型是一种利用压力进行成型的方法。
将陶土放置在模具中,然后使用压力机对其进行压制,使其成型。
压制成型适用于制作厚度较大的陶瓷制品,如砖块、瓷砖等。
这种方法制作的陶瓷制品坚固耐用,可以应用于建筑和装饰领域。
5. 混料成型混料成型是一种将陶土与其他材料混合后进行成型的方法。
在陶土中加入一定比例的其他材料,如石英砂、长石等,然后进行搅拌、研磨等操作,最后进行成型。
混料成型可以改善陶瓷制品的性能,如增加强度、改善耐磨性等。
这种方法制作的陶瓷制品具有多样化的特点,可以适应不同的需求。
以上是几种常见的陶瓷成型方法,每种方法都有其适用的范围和特点。
不同的成型方法可以制作出各种形状、功能和用途的陶瓷制品。
在实际应用中,根据需要选择合适的成型方法,可以有效提高陶瓷制品的质量和生产效率。
随着科技的发展,陶瓷的成型方法也在不断创新和完善,为人们带来更多的可能性。
陶瓷成型工艺

陶瓷成型工艺一、干压成型干压成型又称模压成型,是最常用的成型方法之一,也是手机陶瓷背板主流的成型工艺之一,小米MIX系列的陶瓷后盖都是干压成型的。
干压成型是将经过造粒、流动性好,颗粒级配合适的粉料,装入金属模腔内,通过压头施加压力,压头在模腔内位移,传递压力,使模腔内粉体颗粒重排变形而被压实,形成具有一定强度和形状的陶瓷素坯。
图单向和双向加压时压坯密度沿高度的分布,(a)单向加压,(b)双向加压二、流延成型流延成型(tepe-casting)又称为刮刀成型。
它的基本原理是将具有合适黏度和良好分散性的陶瓷浆料从流延机浆料槽刀口处流至基带上,通过基带与刮刀的相对运动使浆料铺展,在表面张力的作用下形成具有光滑上表面的坯膜,坯膜的厚度主要由刮刀与基带之间间隙来调控。
坯膜随基带进入烘干室,溶剂蒸发有机黏结剂在陶瓷颗粒间形成网络结构,形成具有一定强度和柔韧性的坯片,干燥的坯片与基带剥离后卷轴待用。
然后可安所需形状切割,冲片或打孔,最后经过烧结得到成品。
流延成型工艺可以分为非水基流延成型、水基流延成型、凝胶流延成型等。
流延成型制备陶瓷基片工艺包括浆料制备、流延成型、干燥、脱脂、烧结等工序,其中最关键的是浆料的制备和流延工艺的控制。
图流延成型法制备陶瓷基片的工艺流程图三、注射成型陶瓷注射成型(ceramic injection molding,CIM),是将聚合物注射成型方法与陶瓷制备工艺相结合而发展起来的一种制备陶瓷零部件的新工艺。
陶瓷注射成型的制造过程主要包括四个环节:(1)注射喂料的制备:将合适的有机载体与陶瓷粉末在一定温度下混炼、干燥、造粒,得到注射用喂料;(2)注射成型:混炼后的注射混合料于注射成型机内被加热转变为粘稠性熔体,在一定的温度和压力下高速注入金属模具内,冷却固化为所需形状的坯体,然后脱模;(3)脱脂:通过加热或其它物理化学方法,将注射成型坯体内的有机物排除;(4)烧结:将脱脂后的陶瓷素坯在高温下致密化烧结,获得所需外观形状、尺寸精度和显微结构的致密陶瓷部件。
陶瓷成型技术

粘接泥工艺性能及配制方法 粘接泥工艺性能: 1)黏着性好 2)干燥收缩小,干燥强度大,干燥时不开裂 3)与坯釉结合良好烧结性能、烧成温度与坯釉相适 应 4)烧成时应与坯件粘为一体。 5)热稳定性好
配制粘接泥的方法: 1)坯泥加部分釉料 2)坯泥加少量熔剂 3)坯泥加可塑性粘土 4)坯泥加少量瘠性料
八、 热压注成型 热压注成形:利用蜡类材料热熔冷固的特点,将 配料混合后的陶瓷细粉与熔化的蜡料粘合剂加热 搅拌成具有流动性与热塑性的蜡浆,在热压注机 中用压缩空气将热熔蜡浆注满金属模空腔,蜡浆 在模腔内冷凝形成坯体,再行脱模取件。
蜡浆制备过程示意图
热压注成形工艺流程图
2、蜡浆 粉料可使用废瓷和矿物料(需预烧)配制。 粉料细度:在工艺上一般控制万孔筛的筛余不 大于5%,并要全部通过0.2mm孔径的筛。试验证 明,若能进一步减少大颗粒尺寸,使其不超过 60um,并尽量减少1~2um细颗粒,则能制成性能 良好的蜡浆和产品。 此外,粉料的含水量应控制在0、2%以下。含 水过多配成的蜡浆粘度大,甚至无法调成均匀的 浆料。粉料在与石蜡混合前需在烘箱中烘至 60~80度。
3)注浆成型对石膏模型的要求 (1)设计合理,易于脱模,各部位及吸水均匀,能保 证坯体收缩一致。 (2)孔隙率和吸水率适度,比可塑成型模型略大。 (3)模型的湿度要严格控制,一般应保持5%左右的 吸水率,过干会引起坯体开裂;过湿会延长注浆时 间,甚至难于成型。
4)陶瓷生产对石膏模型的主要性能要求 (1)要求模型有合适的气孔率和足够的机械强度。 (2)保证有良好的吸水性,又要有良好的耐用性能。 相同材质的石膏模型,气孔率高则强度下降。生产 中注浆成形的石膏模气孔率要求达到40~50%,可 塑成形的石膏模气孔率则要求30~40%,且这些气 孔又要求呈毛细孔状态。不同的产品对模型的机械 强度要求也不完全相同,一般好的石膏模型其抗压 强度达90kg/cm2(882Pa)以上,抗折强度在 80kg/cm2(784Pa)以上。此外,模型的工作面要 光滑,尺寸要正确,规格要统一。
陶瓷制作中常见的成型方法
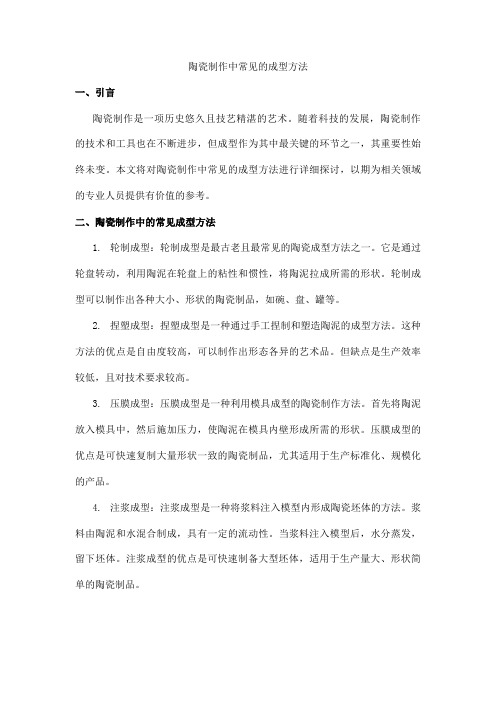
陶瓷制作中常见的成型方法一、引言陶瓷制作是一项历史悠久且技艺精湛的艺术。
随着科技的发展,陶瓷制作的技术和工具也在不断进步,但成型作为其中最关键的环节之一,其重要性始终未变。
本文将对陶瓷制作中常见的成型方法进行详细探讨,以期为相关领域的专业人员提供有价值的参考。
二、陶瓷制作中的常见成型方法1.轮制成型:轮制成型是最古老且最常见的陶瓷成型方法之一。
它是通过轮盘转动,利用陶泥在轮盘上的粘性和惯性,将陶泥拉成所需的形状。
轮制成型可以制作出各种大小、形状的陶瓷制品,如碗、盘、罐等。
2.捏塑成型:捏塑成型是一种通过手工捏制和塑造陶泥的成型方法。
这种方法的优点是自由度较高,可以制作出形态各异的艺术品。
但缺点是生产效率较低,且对技术要求较高。
3.压膜成型:压膜成型是一种利用模具成型的陶瓷制作方法。
首先将陶泥放入模具中,然后施加压力,使陶泥在模具内壁形成所需的形状。
压膜成型的优点是可快速复制大量形状一致的陶瓷制品,尤其适用于生产标准化、规模化的产品。
4.注浆成型:注浆成型是一种将浆料注入模型内形成陶瓷坯体的方法。
浆料由陶泥和水混合制成,具有一定的流动性。
当浆料注入模型后,水分蒸发,留下坯体。
注浆成型的优点是可快速制备大型坯体,适用于生产量大、形状简单的陶瓷制品。
5.热压成型:热压成型是一种利用热压工艺将陶泥压制成型的工艺方法。
该方法能够在较低的压力下制备出密度高、机械强度大的陶瓷制品。
同时,热压成型能够有效地减少坯体中的气泡和裂纹,提高产品质量。
三、成型方法的比较与选择在选择陶瓷成型方法时,需综合考虑以下因素:1.产品形状和尺寸:不同成型方法适用于不同形状和尺寸的陶瓷制品。
例如,轮制成型适用于制作圆形或扁形的陶瓷制品;捏塑成型适用于制作形态各异的艺术品;压膜成型适用于复制大规模、标准化生产的陶瓷制品;注浆成型适用于制备大型、形状简单的陶瓷坯体;热压成型适用于生产高密度、高质量的陶瓷制品。
2.生产效率和成本:不同成型方法的生产效率和成本各不相同。
陶瓷成型的方法

陶瓷成型的方法
陶瓷可是一门古老而神奇的艺术啊!那陶瓷成型的方法到底有哪些呢?
常见的陶瓷成型方法有拉坯成型、注浆成型和压制成型等。
就拿拉坯成型来说吧,步骤就是先把揉好的陶泥放在拉坯机的转盘中心,然后通过双手的配合,让陶泥逐渐变成我们想要的形状。
这过程中可不能马虎啊,要注意力集中,手的力度和位置都得恰到好处,不然一不小心就前功尽弃啦!而且啊,陶泥的湿度也得把握好,太干或太湿都会影响成型效果。
在陶瓷成型过程中,安全性和稳定性那是相当重要的呀!就像走钢丝一样,稍有不慎就可能出问题。
比如说使用机器的时候,要是不注意操作规范,很容易受伤呢!还有陶泥如果放置不稳,也可能会倒塌。
所以在这个过程中,一定要谨慎再谨慎,确保一切都在安全稳定的状态下进行。
陶瓷成型方法的应用场景那可多了去了!无论是制作精美的艺术品,还是实用的餐具等,都离不开这些方法呀。
它们的优势也很明显呢,能让我们创造出各种形状和风格的陶瓷作品,满足不同人的需求和喜好。
这就好比是魔法,能把普通的陶泥变成让人惊叹的宝贝!
看看那些著名的陶瓷产地,不就是靠着这些成型方法制作出了无数令人赞叹的作品吗?比如说景德镇的陶瓷,那精美的造型和细腻的质感,不就是这些方法的完美体现嘛!这些实际案例充分展示了陶瓷成型方法的强大威力和实际应用效果。
陶瓷成型方法就是创造陶瓷艺术的神奇钥匙啊!通过这些方法,我们能把想象变成现实,让陶瓷绽放出独特的魅力!。
- 1、下载文档前请自行甄别文档内容的完整性,平台不提供额外的编辑、内容补充、找答案等附加服务。
- 2、"仅部分预览"的文档,不可在线预览部分如存在完整性等问题,可反馈申请退款(可完整预览的文档不适用该条件!)。
- 3、如文档侵犯您的权益,请联系客服反馈,我们会尽快为您处理(人工客服工作时间:9:00-18:30)。
陶瓷工艺学
§
陶瓷工艺学
注意:调制石膏浆时只能将石膏粉到人调和水中。
制作流程:石膏浆注入模具,然后经干燥、脱模、干燥、修模
陶瓷工艺学
第5章 陶瓷成型方法
成型是将制备好的坯料,用各种不同的方法制成具有
一定形状和尺寸的坯体(生坯)的过程。 成型需满足的要求: 1.坯体符合产品要求的生坯形状和尺寸(考虑收缩)。 2.坯体应具有相当的机械强度,便于后续工序的操作。 3.坯体结构均匀,具有一定的致密度。 4.成型过程适合于多、快、好、省的组织生产. 从工艺上讲,根据坯料的性能和含水量的不同,陶瓷 的成型方法可分为三类:注浆成型、可塑成型和压制 成型。
三、旋压成形 四、其他塑性成形方法 雕塑、印坯、拉坯
陶瓷工艺学
§ 3 压制成型
一、定义
将含有一定水分(或其它粘结剂)的粒状粉料填充于模 具之中,对其施加压力,使之成为具有一定形状和强度 的陶瓷坯体的成型方法叫做压制成型。又称模压成型 (stamping process)、干压成型(dry pressing)。
3
排腊
陶瓷工艺学
§4
修坯与粘结
可塑法和注浆法成型的生坯件,表面不太光滑,边口 都呈毛边现象,多合模型的注浆坯件会有接缝痕迹, 某些产品的进一步加工如挖底、打孔等,都需要进一 步加工修平。工厂称此为修坯,这是成型工艺中的一 项必要的工序,决定产品的表面质量、外观质量等。 湿修:坯体的水分16~19%。 干修:坯体的水分 < 2%。 粘结:是制造壶、坯及一些小口花瓶、坛子等不能一 体成型的坯体所必须的工序。
陶瓷工艺学
陶瓷工艺学
4、压制成型常见缺陷 1)规格尺寸不合格:尺寸超标或变形扭曲。原因是 填料分布不均,如粉料流动性差,或操作不当,使坯 体收缩不一致及失控。 2)裂纹:布料不均匀;坯体设计壁厚差大;压制保 压不足,排气不足; 3)麻面(粘模):坯料干湿不均;模具表面光洁度 不高;原料颗粒表面残留可溶性盐类或电解质。 4)掉边、掉角。
一 概述: 工艺过程:将制备好的坯料泥浆注入多孔性模型内,由于 多孔性模型的毛细管力吸水性,泥浆在贴近模壁的一侧被 模子吸水而形成一均匀的泥层,并随时间的延长而加厚, 当达到所需厚度时,将多余的泥浆倾出,最后该泥层继续 脱水收缩而与模型脱离,从模型取出后即为毛坯.
工艺特点: (1)适于成型各种产品,形状复杂、不规则、 薄、体积较大而且尺寸要求不严的器物,如花瓶、汤碗、 椭圆形盘、茶壶等。 (2)坯体结构均匀,但含水量大且不均匀,干燥与烧成 收缩大。
陶瓷工艺学
§ 2 可塑成型
利用外力对坯料进行成型。基本原理是基于坯料的可塑性。 一、滚压成型 1.工艺原理和特点:成型时盛放着泥料的石膏模型和滚压头分 别绕自己的轴线以一定的速 度同方向旋转。滚压头在旋 转的同时逐渐靠近石膏模型, 对泥料进行滚压成型。 优点:坯体致密、组织结构 均匀、表面质量高。 阳模滚压(外滚压):滚压 头决定坯体形状和大小,模 型决定内表面的花纹。 阴模滚压(内滚压):滚压 头形成坯体的内表面。
粉料含水量8%~15%时为半干压成型;
粉料含水量为3%~7%时为干压成型;
特殊的压制工艺(如等静压法),坯料水分可在3%以 下。
陶瓷工艺学
一、压制成型的模具和设备 模具可用工具钢制成。 产品外形不合理,决定了模具设 计不合理,致使影响成型质量,因 此,有时宁可对产品的外形作一些 修改,使模具设计合理。 模具设计应遵循的原则:便于粉 料填充和移动,脱模方便,结构简 单,设有透气孔,装卸方便,壁厚 均匀,材料节约等。 模具加工应注意尺寸精确,配合 精密,工作面要光滑等。施压设备 :机械压机、油压机或水压机等。
陶瓷工艺学
(3) 成型的生坯强度高,内部结构均匀,不会象挤压 成型那样使颗粒产生有规则的定向排列。 (4) 可以采用较干的坯料成型,也不必或很少使用粘 合剂或润滑剂,有利于减少干燥和烧成收缩。 (5) 对制品的尺寸和尺寸之间的比例没有很大的限制。 (二) 等静压成型的分类 根据成型温度常温等静压(或冷等静压,CIP)、高 温等静压(或热等静压,HIP)。
陶瓷工艺学
二、等静压成型 (一) 等静压成型原理 1、定义:是装在封闭模具中的粉体在各个方向同时均匀 受压成型的方法。等静压成型是干压成型技术的一种 新发展,但模型的各个面上都受力,故优于干压成型。 2、等静压成型过程该工艺主要是利用了液体或气体能够 均匀地向各个方向传递压力的特性来实现坯体均匀受 压成型的。
陶瓷工艺学
二、塑压成型 将可塑泥料放在模型中在常 温下压制成型的方法。 模型:蒸压型的α-半水石膏, 内部盘绕多孔性纤维管,用 以通压缩空气或抽真空。成 型压力与坯泥的含水量有关。 坯体的致密度较旋坯法、滚 压法都高。因此,需要提高 模型强度:采用多孔性树脂 模、多孔金属模。
陶瓷工艺学
陶瓷工艺学
陶瓷工艺学
成型方法分类
热法(热压注法):钢模
注 浆 常压冷法注浆 成 型 法 冷法 加压冷法注浆
成型 方法 可塑成型法 无模
抽真空冷法注浆
石 膏 模
坯料含水量 30~40%
有模
坯料含水量18~26%
干压成型法:钢模 ,坯料含水量6~8% 等静压成型法:橡皮膜,坯料含水1.5~3%
陶瓷工艺学
§ 1 注浆成型
陶瓷工艺学
3、强化注浆成型方法
(注浆方法的改进)
在注浆过程中人为地施加外力,加速注浆过程的进行,使吸浆 速度和坯体强度得到明显改善的方法。 1) 真空注浆 模具外抽真空,或模具在负压下成型,造成模具内外压力差, 提高成型能力,减小坯体的气孔和针眼。
陶瓷工艺学
2) 离心注浆
使模型在旋转情况下进浆,料浆在离心力的作用下紧靠 模壁形成致密的坯体。气泡较轻,易集中在中间最后破 裂排出,故可提高吸浆速度与制品质量。要求:泥浆中 的颗粒分布范围窄,否则大颗粒集中在靠近模型的坯体 表面,而小颗粒集中在坯体内面,造成坯体组织不均匀, 收缩不一致。
陶瓷工艺学
3)压力注浆
通过提高泥浆压力来增大注浆过程推动力,加速水分的 扩散,不仅可缩短注浆时间,还可减少坯体的干燥收缩 和脱模后坯体的水分。注浆压力越高,成型速度越大, 生坯强度越高。但是受模型强度的限制。 模型的材料:石膏模型、多孔树脂模型、无机填料模型。 根据压力的大小可将压力注浆分为: 微压注浆:压力<0.03 MPa 采用石膏模型 中压注浆:压力0.15~0.4 MPa 强度较高的石膏模 型,树脂模型 高压注浆:压力> 2 MPa 高强度树脂模型
陶瓷工艺学
四、注浆成型常见缺陷分析
1、开裂:由于收缩不均匀产生的应力引起。如石膏模各部干 湿不均;制品厚薄差;注浆不连续而形成含气夹层;解凝剂用 量不当,有凝聚倾向;泥浆未经陈腐,水分不均,流动性差; 可塑粘土用量不当;脱模过早或过迟;干燥温度过高。 2、坯体生成不良或缓慢:电解质用量不当,浆料中有促进凝 聚的杂质(如石膏、硫酸钠等);泥浆或模具水分过高;泥浆 温度过低(低于10℃);模具气孔率低、吸水率低。 3、脱模困难:新模表面有油膜;泥浆或模具水分过多;泥浆 粘土用量过多;泥浆原料颗粒过细。 4、气泡针孔:模具过干过湿过热或过旧;泥浆排气不良;注 浆过快,不利排气;模具设计不利排气;浆料存放过久或温度 过高;模具内浮尘未清。 5、变形:原因同开裂
陶瓷工艺学
2、热压铸成型工艺
陶瓷工艺学
3、热压铸成型工艺 主要工艺参数:
(1) 腊浆温度:60~75℃,温度升 高,则腊浆的粘度下降,坯体致 密,但冷却收缩相应大。温度过 低,则易出现欠注、皱纹等缺陷。 (2) 钢模温度。决定坯体冷却凝固 的速度。一般为20~30℃。 (3) 成型压力:与浆桶深度、料浆 性能有关。压力升高,坯体的致 密度增加,坯体的收缩程度下降。 一般可以采用0.3~0.5 MPa。
陶瓷工艺学
高压注浆成 型原理图
微压注浆成 型原理图
陶瓷工艺学
4)热浆注浆
在模型两端设置电极,料浆注满后,马上接交流电,利用 料浆中少量电解质的导电性加热,升温至50℃左右,可 加快吸浆速度。当泥浆温度为15~55℃,粘度会降低 50~60%,坯体成型速度提高32~42%。 5 )电泳成型 根据料浆中粘土粒子(带有负 电荷)在电流作用下能向阳极 移动,把坯料带往阳极而沉积 在金属模的表面而成型的。模 型用铝、镍、镀钴的铁等。 影响因素:主要为电压、电流、 成型时间、泥浆浓度及电解质 含量等。
陶瓷工艺学
2. 滚压成型的主要控制因素 (1) 对泥料的要求:水分低、可塑性好。成型时模具 既有滚动,又有滑动,泥料主要受压延力的作用。要求有 一定的可塑性和较大的延伸量。可塑性低,易开裂;可塑 性高,水分多易粘滚头。阳模滚压和阴模滚压对泥料的要 求有差别。阴模滚压受模型的承托和限制,可塑性可以稍 低,水分可稍多。 (2) 滚压过程控制:分压下(轻)、压延(稳)、抬起 (慢)阶段。 (3) 主轴转速(n1)和滚头转速(n2) :控制生产效率; 对坯料的施力形式,控制坯体的密度均匀和表面光洁。 滚压头的温度热滚压:100~130℃,在泥料表面产生一 层气膜,防止粘滚头,坯体表面光滑。冷滚压:可用塑料 滚压头,如聚四氟乙烯。
陶瓷工艺学
陶瓷工艺学
3. 等静压成型与干压成型的主要差别 (1) 粉料各个方向受压,粉料颗粒的直线位移减少,利于 把粉料压到相当的密度,同时消耗在粉料颗粒运动时 的摩擦功相应减少,提高了压制效率。 (2) 粉料内部和外部介质中的压强相等,因此空气排出 困难,限制通过增大压力来压实粉料的可能,故生产 中有必要排除装模后粉料中的少量空气。 4. 等静压成型的优点 (1) 与施压强度大致相同的其它压制成型相比,等静压成 型可以得到较高的生坯密度,且密度在各个方向上都 比较均匀。 (2) 生坯内部的应力小(压强的方向性差别小于其它成 型方法,颗粒间、颗粒与模型间的摩擦力减小)。
陶瓷工艺学
3、滚压成型常见缺陷 1)粘滚头:泥料可塑性太强或水分过多;滚头转速太快; 滚头过于光滑及下降速度慢;滚头倾角过大。 2)开裂:坯料可塑性差;水分太少,水分不均匀;滚头 温度太高,坯体表面水分蒸发过快,引起坯体内应力增大。 3)鱼尾:坯体表面呈现鱼尾状微凸起。原因是滚头摆动; 滚头抬离坯体太快。 4)底部上凸:滚头设计不当或滚头顶部磨损; 滚头安装 角度不当;泥料水分过低。 5)花底:坯体中心呈菊花状开裂。原因是模具过干过热; 泥料水分少;转速太快;滚头中心温度高;滚头下压过猛; 新模具表面有油污。