动力电芯配组标准
笔记本电池换芯(18650)详解
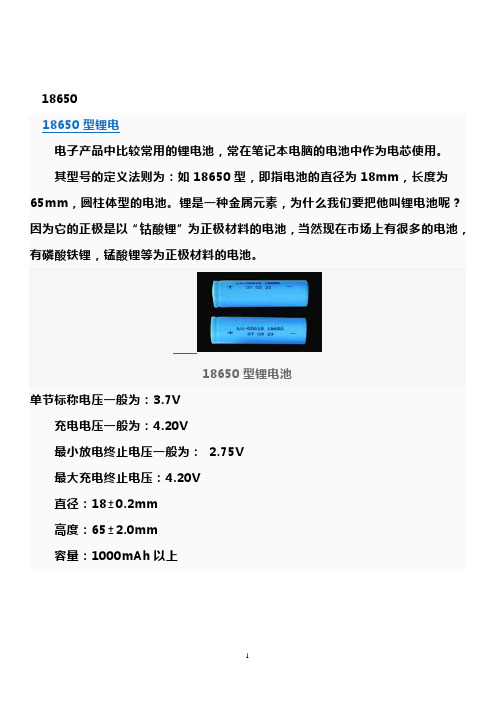
1865018650型锂电电子产品中比较常用的锂电池,常在笔记本电脑的电池中作为电芯使用。
其型号的定义法则为:如18650型,即指电池的直径为18mm,长度为65mm,圆柱体型的电池。
锂是一种金属元素,为什么我们要把他叫锂电池呢?因为它的正极是以“钴酸锂”为正极材料的电池,当然现在市场上有很多的电池,有磷酸铁锂,锰酸锂等为正极材料的电池。
18650型锂电池单节标称电压一般为:3.7V充电电压一般为:4.20V最小放电终止电压一般为:2.75V最大充电终止电压:4.20V直径:18±0.2mm高度:65±2.0mm容量:1000mAh以上目前全球生产此型号锂电池最大的厂商有日本的三洋(已被松下收购)、松下、三星、索尼等,索尼公司就曾为臭名昭著的笔记本电池爆炸事件而大伤脑筋过。
笔记本电脑用的锂电池首先介绍一下笔记本电脑用的18650电芯通常容量为2200mAh(毫安时),可解释为:以3.7V电压、2200mA(毫安)电流供电,可以使用1小时(hour)。
更高规格的容量为2400mAh、2600mAh(三洋电芯居多,索尼的笔记本多数采用2600mAh的规格)。
以下以常见的3.7V/2200mAh电芯为例。
一、通常说的三芯电池即三节18650电芯串联而形成的电池组。
该电池组最终标示参数为11.1V/2200mAh。
11.1V=3.7V×3,串联时输出电流不变仍为2200mAh。
也有标10.8V的,即单个电芯有电压降产生导致总电压降低。
现在市面流行的上网本多为此规格电池组。
二、四芯电池有2种情况:四个串联和两串两并。
四个串联电池组最终标示参数为:14.8V/2200mAh。
14.8V=3.7V×4,串联时输出电流不变仍为2200mAh。
两串两并即四个电芯分两组,两两串联后再并联,电池组最终标示参数为:7.4V/4400mAh。
7.4V=3.7V×2,输出电流为4400mAh=2200mAh×2。
32140圆柱电芯分选配组标准

《32140圆柱电芯分选配组标准》一、引言在当今社会,随着新能源产业的快速发展,电池作为能源存储和传输的重要组成部分,其品质和性能要求也越来越高。
而作为电池的核心部件之一,圆柱电芯的标准化和分选配组显得尤为重要。
本文将深入探讨《32140圆柱电芯分选配组标准》,希望能帮助读者更全面、深入地理解圆柱电芯的标准和应用。
二、32140圆柱电芯分选配组标准的定义和内容在介绍《32140圆柱电芯分选配组标准》之前,首先我们需要了解圆柱电芯的基本概念和结构。
圆柱电芯是一种常见的锂离子电池类型,其外形呈圆柱形,有着较高的能量密度和循环寿命。
而《32140圆柱电芯分选配组标准》则是针对这类电池的一项国家标准,旨在规范圆柱电芯的参数范围、品质要求以及组装配对方法。
具体而言,《32140圆柱电芯分选配组标准》包括了以下几个方面的内容:1. 参数范围:对圆柱电芯的几何尺寸、电性能、充放电特性等关键参数进行了规定,以确保电池的稳定性和可靠性。
2. 品质要求:对正极、负极材料、隔膜、电解液等原材料的品质进行了详细描述,要求其符合国家标准和行业规范。
3. 组装配对方法:针对圆柱电芯的分选配组工艺进行了规范,包括分容量、内阻、循环寿命等方面的要求。
三、探讨圆柱电芯分选配组标准的意义和作用《32140圆柱电芯分选配组标准》的制定和实施,不仅有利于保障圆柱电芯产品的质量和性能,还能推动整个新能源产业的健康发展。
具体来说,其意义和作用主要体现在以下几个方面:1. 保障产品质量:标准化的生产和检测流程能够有效杜绝劣质产品的流入市场,提高电池产品的整体质量水平。
2. 促进技术创新:规范的标准为行业内的企业和科研机构提供了统一的技术参考,有利于促进电池技术的进步和创新。
3. 降低生产成本:统一的标准和要求能够简化生产流程和管理手段,有助于降低生产成本和提高生产效率。
四、个人观点和理解作为电池行业的从业者,我深刻理解《32140圆柱电芯分选配组标准》对于产品质量和行业发展的重要意义。
32140圆柱电芯分选配组标准

32140圆柱电芯分选配组标准1. 尺寸一致性在分选配组圆柱电芯时,尺寸一致性是首要考虑的因素。
电芯的长度和直径应符合规格要求,尺寸偏差应在允许范围内。
使用精确的测量工具对电芯进行检测,以确保其尺寸符合规格。
2. 重量一致性重量一致性对于圆柱电芯的性能和安全性至关重要。
在分选配组时,应使用高精度的称重设备对电芯进行称重,确保其重量在允许的范围内。
如果重量偏差超出允许范围,应进行筛选或调整。
3. 电阻值一致性电阻值是衡量电芯性能的重要指标之一。
在分选配组时,应对电芯的电阻值进行测量,确保其符合规格要求。
如果电阻值偏差超出允许范围,应进行筛选或调整。
4. 电压一致性电压一致性是保证电池组性能和安全性的关键因素。
在分选配组时,应使用电压表对电芯进行电压测试,确保其电压值在允许的范围内。
如果电压偏差超出允许范围,应进行筛选或调整。
5. 电池容量一致性电池容量一致性对于保证电池组的续航时间和性能至关重要。
在分选配组时,应对电芯的容量进行测试,确保其符合规格要求。
如果容量偏差超出允许范围,应进行筛选或调整。
6. 电池内阻一致性电池内阻一致性对于保证电池组的性能和安全性至关重要。
在分选配组时,应对电芯的内阻进行测量,确保其符合规格要求。
如果内阻偏差超出允许范围,应进行筛选或调整。
7. 电池外观质量电池外观质量对于保证电池组的美观度和安全性至关重要。
在分选配组时,应对电芯的外观进行检查,包括是否有划痕、破损、漏液等情况。
如果外观质量不符合要求,应进行筛选或调整。
8. 耐压性能圆柱电芯必须能够承受一定的耐压要求。
在分选配组时,应对电芯进行耐压测试,以确保其符合规格要求。
如果耐压性能不符合要求,应进行筛选或调整。
9. 循环寿命循环寿命是衡量圆柱电芯使用寿命的重要指标之一。
在分选配组时,应对电芯的循环寿命进行测试,以确保其符合规格要求。
如果循环寿命不符合要求,应进行筛选或调整。
PACK组合电池组配参数及压差工艺标准

文件名称:Packing电池压降及组配参数和产品压差标准 1 OF 6页 码1.0、目的明确Packing所有锂电电池压降及锂电电池的组配参数和产品压差参数标准。
2.0、适用范围:适用于东莞市迈科新能源有限公司锂电Packing所有锂电电池的生产和组配操作及产品压差测试。
3.0、定义3.1 压降的定义:二次测电压的值对比第一次测电压的值的差值。
3.2 压差的定义:组配好的两个 电芯之间的电压差值。
3.3 自耗电率的定义:搁置后所下降的电压值除以搁置的天数,等同于压降率。
3.4 压降差的定义:两个电芯之间的压降率的差值。
3.5 组配的定义:将两个同型号的电芯进行串联或并联,以满足客户所要求的电压或容量。
4.0、职责PROD: 根据工程的MI及SOP文件执行产品的生产操作及定期的设备保养QA: 根据工程的相关文件执行对产品生产的各个环节进行品质监督。
PE: 负责产线所有设备维护及产线异常问题处理。
PMC: 负责产线生产计划的计划和调度。
5.0、电池组配作业流程操作5.1 锂电电池配组标准,见下表:文件名称:Packing电池压降及组配参数和产品压差标准 2 OF 6页 码5.2 电池配组作业流程图文件名称:Packing电池压降及组配参数和产品压差标准 3 OF 6页 码文件名称:Packing电池压降及组配参数和产品压差标准 4 OF 6页 码5.3 电池配组流程说明:5.3.1 电芯上线前,必须确认该批电芯的搁置状态,检查胶盒上的标示卡。
标示卡上体现了该盒电芯的状态,包含入库日期(必须是实际生产日期)。
用当天的日期减去标示卡上的日期,得出电芯的搁置天数。
不同的搁置状态按相应的作业流程进行操作。
5.3.2 电芯外观检查,将电芯外观不良品挑选出来。
外观不良:断极耳、腐蚀、气胀、角位破损、 Cpp不良、漏液、表面电解液、划痕、划伤、凹/凸点、起皱,等。
5.3.3 测试一次电压:依据搁置状态不同,使用内阻仪测试电压值时,将电压值末两位写到电芯上;使用安杰伦测试电压值时,将电压值末三位数写到电芯上。
磷酸铁锂动力电池设计知识详解

***结构设计 PACK独特技术— —“八个一致”配组原则
自放电一致 电压一致 内阻一致 容量一致
八个一致
循环寿命一致 平台一致 恒流比一致 带电量一致
结内论阻:一八致个一致的配组原则,可确保动力电池组正常使用8年后容量保持率依然在80% 以上。
19
PACK独特技术— —“八个一致”配组原则
PACK独特技术— —“八个一致”配组原则
PACK独特技术— —“八个一致”配组原则
电池的成组原则为:使用同一个档次的电芯组装,当某一批次该档次的电 芯数量不够时,使用相邻批次同档电压同档容量的电芯补足缺额。严禁不同电 压、不同内阻档次电芯用于同一电池组的组装。如图:
Y14C10同档次电芯 (数量较Y14C14同 档电芯多)
Y14C11同档次电芯 (数量较Y14C13同 档电芯多)
目录
1 认识磷酸铁锂电池 2 ***高品质电芯 3 ***独特的结构设计 4 ***强大的电池管理系统 5 ***动力锂电池的安全测试
认识磷酸铁锂电池
1 什么是磷酸铁锂电池
铁锂知识
2 磷酸铁锂电池的应用领域
3 磷酸铁锂电池的比较优势
认识磷酸铁锂电池
什么是磷酸铁锂电池 是指以磷酸铁锂作为正极材料的锂离子电池。相对其它传统正极材料的 锂电池,磷酸铁锂电池具有安全可靠性高,循环寿命长和经济环保等优 点。
单体电池正负极焊接螺纹铜柱,用螺母紧固连接,牢固性强
按GB/T 2423.10中规定测试电池组的抗机械振动,试验后电池组没有 机械损坏、没有变形和紧固部位的松动现象。电池组完好,无损伤。
导 电 性: 螺母紧固连接部位进行阻抗测试,阻值较小,可以进行大电流导电。 电池进行串并联,内阻影响小。
散 热 性: 同大电池(如几十安时,上百安时)相比,小电池组合结构间隙分布 均匀,散热效果好。
电动汽车动力电池参数匹配研究

电动汽车动力电池参数匹配研究作者:严永利周运强董晓文于志科赵慧玲吉海军来源:《中国科技博览》2018年第09期[摘要]随着纯电动汽车的大量应用,对电动车设计研发过程中的动力电池匹配设计要求也越来越高。
为保障电动汽车的整车续航里程等要求,就要求对电动汽车的动力电池进行合理的计算和匹配选型。
另外,动力电池是电动汽车整车的能量来源,整车所有的能量消耗都来自动力电池。
因此所选择的动力电池的类型、质量和各种技术参数都会影响电动汽车的整车性能,动力电池参数匹配主要包括电池容量、电池数目、电池电压等参数的匹配。
本文从实际出发,对电动汽车动力电池的匹配计算方法进行了深入的分析,为行业同仁在进行电动汽车动力电池参数匹配时提供可行的思路。
[关键词]电动汽车,动力电池,参数匹配中图分类号:U469.72 文献标识码:A 文章编号:1009-914X(2018)09-0110-011 动力电池的匹配原则动力电池类型的选择要符合电动汽车的运行要求。
电动汽车要求动力电池具有较高的比能量和比功率,以满足电动汽车续驶里程和动力性的要求,同时也希望动力电池具有与汽车使用寿命相当的充放电循环寿命,拥有高效率、良好的性价比以及免维护特性。
目前可用于纯电动汽车的动力电池主要有铅酸蓄电池、金属氢化物镍蓄电池和锂离子蓄电池。
其中锂离子蓄电池的高能量和充放电速度快等优越性能得到越来越多的关注,是目前市场前景最好的一种产品。
动力电池的电压等级要与驱动电机的电压等级相一致,且满足电机电压变化的要求。
同时,由于电动空调、DC-DC、空调系统(PTC和压缩机)、电动真空泵和电动转向助力泵等附件也消耗一定的电能,所以电池组的总电压要大于驱动电机的额定电压。
动力电池一般有能量型和功率型两种,为满足电动汽车的行驶要求,采用能量型电池,匹配时主要考查电池的能量,即电池应具有足够大的容量,以增加车辆的续驶里程。
电池容量与其功率成正比,容量越大,其输出的功率也越大,所以其输出功率均能满足整车电力系统的要求,因此主要是根据其续驶里程来确定电池容量,并且确定的电池容量还须符合市场现有产品的标准,并通过对现有产品反复验证进行设计。
锂离子动力电池组电芯不一致的原因分析及相关建议控制策略

锂离子动力电池组电芯不一致的原因分析及相关建议控制策略收益于下游新能源电动车及小电动工具的发展,锂电池的制造技术及组装方式也不断改进来适用下游的用电设备的发展。
锂电池作为电动汽车的动力电源时,因为高功率、大容量的要求,单体锂离子电芯并不能满足要求,所以就要对锂离子电芯进行串、并联组合使用。
由于锂电芯在做成电池组时,会出现的短板效应,即单体电芯的不一致性会造成电池组在使用过程中出现容量衰减过快、寿命较短,内阻增加等问题。
因此动力电池组在成组前会根据设备的使用条件,对单电池需要进行筛选,配对进行组合。
单电芯在制造出来后,因为设计,工艺生产过程的影响导致电芯的电压、容量、内阻、寿命、自放电率等参数存在不一致。
有些可以根据生产工艺和设计通过一定的手段和方法进行筛选来降低单体电池的不一致性,但是有些无法定义,这也导致了同批电池组,同样的条件下使用,电芯的寿命长短不一致。
锂离子电池不一致性主要表现在两个方面:1)单体电芯性能参数(电池容量、内阻和自放电率等)的差异2)电芯荷电状态(SOC)的差异。
戴海峰等研究发现,电池单体之间容量的差异分布接近威尔分布,而内阻的离散程度较容量更为显著,且同批次电池的内阻一般满足正态分布的规律,自放电率也呈现近似正态分布。
SOC表征着电池的荷电状态,是电池剩余容量与额定容量的比值,解竞等认为由于电池的不一致性,电池的容量衰减速率不同,导致电池间的最大可用容量存在差异。
容量小的电池的SOC变化速率比容量大的电池快,充放电时更快达到截止电压。
锂离子电池出现不一致性问题的原因很多,主要有2个方面:1)制造过程这设计到原材料的性能差异,生产设备,设备的工艺参数,生产工艺流程等方面。
比如制造过程的每个环节例如配料时浆料的均匀度、涂布时面密度及表面张力的控制等都会造成单体电池性能的差异。
罗雨等研究了锂离子电池生产制造工艺对电池一致性的影响,重点研究了水性粘结剂体系的锂离子电池生产制片工艺对电池一致性的影响。
单体组合液态锂电池分容配阻技术指标

5、此标准执行后,之前所有的组合分容技术标准均统一执行此技术标准.
备注:此标准不包括动力电池,动力电池请参照工程另行下发的各种型号电池组不同的配组分容技术标准.
制作
■生产部■
产品编号
产品型号
版本号
A1
日期
液态锂、聚合物电芯组合及分容技术标准
项目
电芯间参数差别
内阻
电压
容量
一、液态锂电芯
1
串联时
<5mΩ
<20mV
<20mAh
2
并联时
<5mΩ
〈20mV
<20mAh
二、聚合物电芯
1
串联时
<3mΩ
<20mV
<20mAh
2
并联时
<3mΩ
<20mV
<20mAh
液态锂、聚合物电芯组技术标准
液态锂、聚合物组合时分容标准
1、当电池的容量<1800mAh时,可按1C5A的电流进行分容测试,串联时充电限制电压按4.2V*N(N为串联的电芯节数)计算,放电截止电压2.75V*N;
2、当电池的容量>1800mAh时,可按1.5A的电流进行分容测试;
3、具体的容量要求,请参照工程另行下发的各种型号电池组不同的容量要求,执行时要相互参照;
电芯配对 操作流程
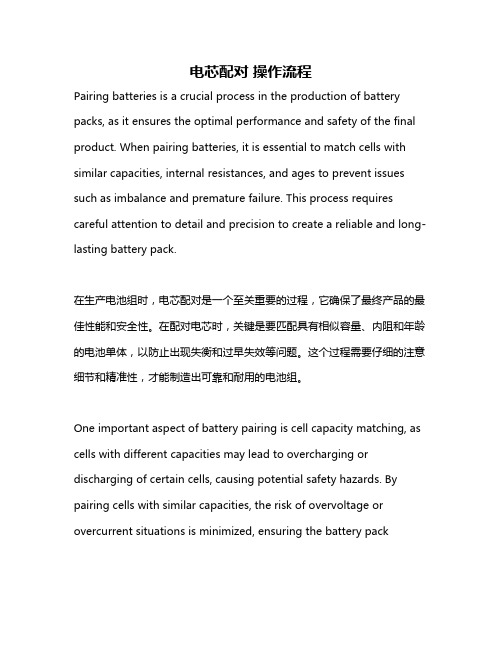
电芯配对操作流程Pairing batteries is a crucial process in the production of battery packs, as it ensures the optimal performance and safety of the final product. When pairing batteries, it is essential to match cells with similar capacities, internal resistances, and ages to prevent issues such as imbalance and premature failure. This process requires careful attention to detail and precision to create a reliable and long-lasting battery pack.在生产电池组时,电芯配对是一个至关重要的过程,它确保了最终产品的最佳性能和安全性。
在配对电芯时,关键是要匹配具有相似容量、内阻和年龄的电池单体,以防止出现失衡和过早失效等问题。
这个过程需要仔细的注意细节和精准性,才能制造出可靠和耐用的电池组。
One important aspect of battery pairing is cell capacity matching, as cells with different capacities may lead to overcharging or discharging of certain cells, causing potential safety hazards. By pairing cells with similar capacities, the risk of overvoltage or overcurrent situations is minimized, ensuring the battery packoperates within safe limits. Capacity matching also helps to improve the overall performance and longevity of the battery pack.电池配对的一个重要方面是单体容量匹配,因为容量不同的电池单体可能导致某些电池过充或过放,从而造成潜在的安全隐患。
新能源汽车电池包装配方案的研究
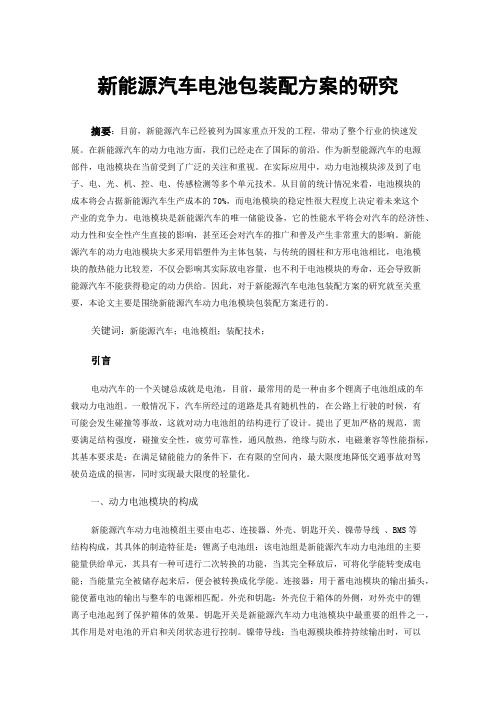
新能源汽车电池包装配方案的研究摘要:目前,新能源汽车已经被列为国家重点开发的工程,带动了整个行业的快速发展。
在新能源汽车的动力电池方面,我们已经走在了国际的前沿。
作为新型能源汽车的电源部件,电池模块在当前受到了广泛的关注和重视。
在实际应用中,动力电池模块涉及到了电子、电、光、机、控、电、传感检测等多个单元技术。
从目前的统计情况来看,电池模块的成本将会占据新能源汽车生产成本的70%,而电池模块的稳定性很大程度上决定着未来这个产业的竞争力。
电池模块是新能源汽车的唯一储能设备,它的性能水平将会对汽车的经济性、动力性和安全性产生直接的影响,甚至还会对汽车的推广和普及产生非常重大的影响。
新能源汽车的动力电池模块大多采用铝塑件为主体包装,与传统的圆柱和方形电池相比,电池模块的散热能力比较差,不仅会影响其实际放电容量,也不利于电池模块的寿命,还会导致新能源汽车不能获得稳定的动力供给。
因此,对于新能源汽车电池包装配方案的研究就至关重要,本论文主要是围绕新能源汽车动力电池模块包装配方案进行的。
关键词:新能源汽车;电池模组;装配技术;引言电动汽车的一个关键总成就是电池,目前,最常用的是一种由多个锂离子电池组成的车载动力电池组。
一般情况下,汽车所经过的道路是具有随机性的,在公路上行驶的时候,有可能会发生碰撞等事故,这就对动力电池组的结构进行了设计。
提出了更加严格的规范,需要满足结构强度,碰撞安全性,疲劳可靠性,通风散热,绝缘与防水,电磁兼容等性能指标,其基本要求是:在满足储能能力的条件下,在有限的空间内,最大限度地降低交通事故对驾驶员造成的损害,同时实现最大限度的轻量化。
一、动力电池模块的构成新能源汽车动力电池模组主要由电芯、连接器、外壳、钥匙开关、镍带导线、BMS等结构构成,其具体的制造特征是:锂离子电池组:该电池组是新能源汽车动力电池组的主要能量供给单元,其具有一种可进行二次转换的功能,当其完全释放后,可将化学能转变成电能;当能量完全被储存起来后,便会被转换成化学能。
锂离子电芯配对方法

锂离子电芯配对方法
1. 容量配对:对于电芯的容量,可以通过测量电芯的放电容量来判断,将容量相似的电芯组合在一起。
通常情况下,容量配对的容差范围在3%以内。
2. 电阻配对:通过测量电芯的内阻来判断,将内阻相似的电芯组合在一起。
电阻配对的目的是为了保证电池组中各个电芯的放电平衡,减少因内阻不均衡而引起的电池过热问题。
3. 电压配对:通过测量电芯的电压来判断,将电压相近的电芯组合在一起。
电压配对的目的是为了使电芯在充电和放电过程中的电压变化趋势一致,保证电池组的电压稳定性。
4. 外观配对:通过对电芯的外观进行观察和比较,如尺寸、外壳、标志等,将外观相似的电芯组合在一起。
5. 内部结构配对:通过对电芯的内部结构进行观察和比较,如正负极材料、电解液、隔膜等,将内部结构相似的电芯组合在一起。
需要注意的是,无论采用何种配对方法,都需要在配对过程中进行严格的测试和验证,以确保电芯的质量和性能符合要求。
此外,电池组内的电芯配对应尽量避免串接不相似的电芯,以免因电芯参数不匹配而导致电池组的不稳定性和安全性问题。
动力电池PACK简介

10
各工序设备配置说明
模组PACK测试 →充放电,DCIR测试工序方案
测试设备架构图
测试设备效果图(部分展示)
测试设备配置:HYNN-IGBT-750V300A-2Ch 测试设备15台,单台双通道,共计30通道, HYNN-EPT120V300A-2CH测试设备10台,单台双通道,共计20通道; 优势分析:1、采用国际先进的IGBT/MOSFET高频开关技术,能够实现电池测试过程中电能的高品质双向流动,基本不产生谐波电流和无功 THDI<3%,PF>0.99; 2、功能齐全,可实现对成组动力电池系统通过设定工况模拟进行充放电试验、对电池组的容量、效率、荷电状态、热性能等综合性 能进行评价、验证电池管理系统的电池检测精度和能量状态估计的准确性,为电池组装车后的有效管理提供试验依据; 3、可对接MES系统,系统中的节能调度模块采用人工智能算法,根据用户使用习惯,及产能情况,预算整个产线的功率使用状况, 智能调配充放电机柜的起始时间,使电池释放的电能充分利用,同时减轻厂区配电压力;也可在用电低谷时保存电能,用电高峰
⑤每台设备具有功能,把电芯的来料参数、测试数据,产品信息、物料来料信息,锁紧螺丝扭力等数据上传并存储至工控机机,以便调
取与追溯,以及连接工厂整个MES系统进行智能管理。
3
各工序设备配置说明
方案亮点
电芯组装段,设备采用数据信息统一共享,将整个 模组内的20-24个电芯,根据容量/K值/电压/内阻系 统自动配组/分选/缓存/AB单元组合,再自动堆叠成 模组,保证了模组的性能达到最佳。 本方案电芯段设备自动化程度高,省时省力,不仅 提高了生率产效,同时也保证了良品率;模组 PACK段,采用人机结合的方式,保证生产效率的 同时,降低了设备成本与制造成本。 A/B单元将2-3个电芯并联组合成一体,支架上设有 鸳鸯扣,可任意正反扣合成所需模组,结构稳定, 操作简单,极耳焊接牢固可靠,并且焊接效率高。 PACK组装段,操作工位与物料小车合并,利用 AGV小车运输的方式,不仅节省员工搬运强度与工 时,还保证了车间的再利用空间。 电芯缓存/配组,采用两套各9组独立顶升机构,利 用吸塑盘盛装保护,两套机构交替工作,保证足够 缓存数量可任意配对20-24个电芯组合模组。
电芯配组筛选标准_解释说明
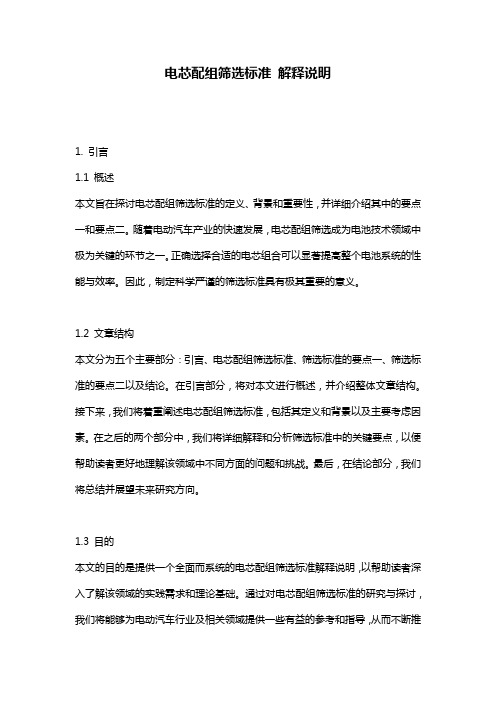
电芯配组筛选标准解释说明1. 引言1.1 概述本文旨在探讨电芯配组筛选标准的定义、背景和重要性,并详细介绍其中的要点一和要点二。
随着电动汽车产业的快速发展,电芯配组筛选成为电池技术领域中极为关键的环节之一。
正确选择合适的电芯组合可以显著提高整个电池系统的性能与效率。
因此,制定科学严谨的筛选标准具有极其重要的意义。
1.2 文章结构本文分为五个主要部分:引言、电芯配组筛选标准、筛选标准的要点一、筛选标准的要点二以及结论。
在引言部分,将对本文进行概述,并介绍整体文章结构。
接下来,我们将着重阐述电芯配组筛选标准,包括其定义和背景以及主要考虑因素。
在之后的两个部分中,我们将详细解释和分析筛选标准中的关键要点,以便帮助读者更好地理解该领域中不同方面的问题和挑战。
最后,在结论部分,我们将总结并展望未来研究方向。
1.3 目的本文的目的是提供一个全面而系统的电芯配组筛选标准解释说明,以帮助读者深入了解该领域的实践需求和理论基础。
通过对电芯配组筛选标准的研究与探讨,我们将能够为电动汽车行业及相关领域提供一些有益的参考和指导,从而不断推动电动汽车技术的进步和创新。
2. 电芯配组筛选标准2.1 定义和背景:电芯配组筛选标准是指在电池组装过程中,基于特定需求和性能要求,对不同的电芯进行评估和选择的一套准则。
随着电动汽车、可再生能源等领域的快速发展,对于电芯的品质和性能要求也越来越高。
因此,制定适合的筛选标准成为保证整个电池系统性能稳定和可靠性的关键。
2.2 主要考虑因素:确定适当的电芯配组筛选标准需要综合考虑多个因素,包括但不限于以下几点:a) 容量匹配:为了确保整个电池组具有一致的容量水平,需要通过严格筛选选择具有相似容量值的电芯。
这有助于降低不同子模块之间的差异性,并提高整体功率输出效率。
b) 内阻匹配:内阻是影响电池寿命与充放电性能的重要参数。
通过精确测量内阻并筛选出内阻值较接近的电芯,可以使整个系统更加平衡,并提升功率传输效率和循环寿命。
纯电动汽车动力电池匹配设计

纯电动汽车动力电池匹配设计摘要:发展新能源汽车产业已上升为国家战略,纯电动汽车是新能源汽车发展的核心力量,其具备噪音低、效率高、零排放等优点,适合城市道路运输。
而车辆购置成本中动力电池成本占了一半以上,动力电池电量直接影响整车续航里程,一味追求续航里程,使得整车成本进一步增加。
本文从整车布局要求、续航里程、车辆安全性等方面综合考量,提出了动力电池匹配设计方法,作为整车电池选型的理论依据。
关键词:动力电池;匹配设计;续航里程1动力电池系统简介动力电池系统最基本的功能存储由外部电网,或者驱动系统回馈产生的电能。
电芯采用串、并联方式组成电池组,电池组放置在一个或多个密封并且屏蔽的箱体里面,一个或多个箱体使用可靠的接插件进行连接。
使用电池管理系统对电池组进行综合管理,实时采集各电芯的电压值、各温度传感器的温度值、电池组的总电压值和总电流值,电池组与箱体的绝缘电阻值等数据,并根据系统中设定的阀值判定电池组工作是否正常。
为满足便利维修,动力电池系统设有维修开关,通过维修开关能够方便断开动力电池组的高压回路,更换动力电池系统中的熔断器等易损件;动力电池系统为汽车零部件,因此要求动力电池系统采用的各个部件为汽车级。
2 动力电池系统部件要求动力电池系统设计以满足车辆动力要求为前提,同时从电池系统自身内部结构和安全设计、电池管理等方面进行设计,主要包括以下几个部分:(1)电池箱外观尺寸:电池箱体尺寸主要根据车辆提供的电池安装空间进行设计,并且要考虑到接插件、高低压线束布置与机械连接部位的尺寸影响。
电池箱内部尺寸,主要从整体设计考虑,从电池的排布、线束的排布以及电池管理系统尺寸位置、热管理系统尺寸及位置等方面进行设计。
电池箱的外观设计主要从空间布局、材料特性、防护等级、绝缘安全、标识等方面进行设计。
(2)电池性能参数:电池系统参数,比如电压平台、额定容量、额定能量、最大可持续放电电流、瞬间峰值放电电流、瞬间峰值充电电流等,在设计时要根据车辆的动力参数、高低压附件电气耗电量进行匹配。
280电芯 储能电芯配组标准

280电芯储能电芯配组标准280Ah储能电芯是一种大容量锂离子电池,广泛应用于储能系统、电动汽车等领域。
在实际应用中,为了确保电池组的安全性能和稳定性能,需要对280电芯进行合理的配组。
以下是一些建议的配组标准:1. 电池容量匹配:确保电池组中每个电芯的容量相互匹配,避免因容量差异导致的电池组性能不一致和寿命缩短。
一般来说,电芯容量差异不应超过5%。
2. 电池电压匹配:电池组中每个电芯的电压应相互匹配,以确保电池组在充放电过程中的稳定性。
通常,电芯电压差异不应超过0.05V。
3. 内阻匹配:电芯的内阻会影响电池组的充放电性能和安全性。
在配组时,应尽量选择内阻相近的电芯,以减小电池组内部的电阻损耗和热量产生。
4. 外观检查:检查电芯外观是否有破损、变形、脏污等问题,确保电芯表面干净整洁,连接处无松动。
5. 性能测试:对电芯进行性能测试,包括充放电曲线、循环寿命、容量保持率等指标,确保电芯性能良好。
6. 一致性:为了保证电池组的一致性,可以采用分组配对的方式进行配组。
将性能相近的电芯分为一组,每组内的电芯数量可以根据实际需求进行调整。
7. 温度管理系统:在电池组中加入温度管理系统,确保电芯在充放电过程中温度稳定,降低热失控风险。
8. 电池管理系统(BMS):配组时应考虑电池管理系统的设计,确保电池组在充放电过程中的安全管理和性能监控。
9. 电路设计:合理设计电池组的电路布局,确保充放电电路、保护电路、温度监测电路等部分工作稳定。
10. 可靠测试:在电池组配组完成后,进行可靠测试,包括循环寿命测试、充放电性能测试、温度稳定测试等,确保电池组在实际应用中的稳定性能。
综上所述,280Ah储能电芯配组标准主要包括电池容量、电压、内阻匹配,外观检查,性能测试,一致性,温度管理系统,电池管理系统,电路设计以及可靠测试等方面。
在实际应用中,可以根据具体情况调整配组标准,以满足实际需求。
一种锂离子电池的电芯的分选配组方法与流程
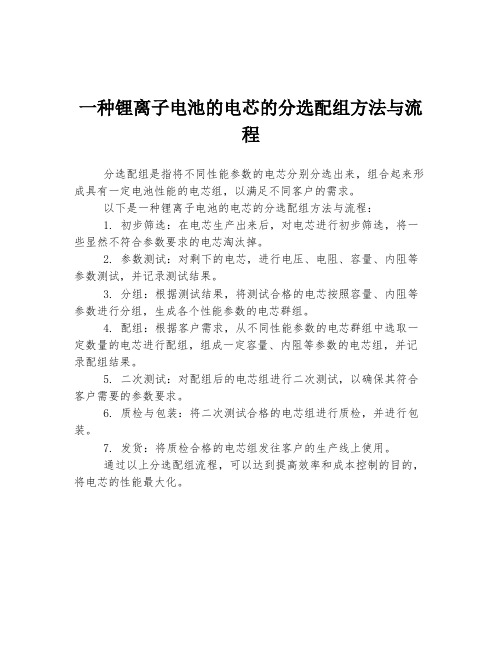
一种锂离子电池的电芯的分选配组方法与流
程
分选配组是指将不同性能参数的电芯分别分选出来,组合起来形成具有一定电池性能的电芯组,以满足不同客户的需求。
以下是一种锂离子电池的电芯的分选配组方法与流程:
1. 初步筛选:在电芯生产出来后,对电芯进行初步筛选,将一些显然不符合参数要求的电芯淘汰掉。
2. 参数测试:对剩下的电芯,进行电压、电阻、容量、内阻等参数测试,并记录测试结果。
3. 分组:根据测试结果,将测试合格的电芯按照容量、内阻等参数进行分组,生成各个性能参数的电芯群组。
4. 配组:根据客户需求,从不同性能参数的电芯群组中选取一定数量的电芯进行配组,组成一定容量、内阻等参数的电芯组,并记录配组结果。
5. 二次测试:对配组后的电芯组进行二次测试,以确保其符合客户需要的参数要求。
6. 质检与包装:将二次测试合格的电芯组进行质检,并进行包装。
7. 发货:将质检合格的电芯组发往客户的生产线上使用。
通过以上分选配组流程,可以达到提高效率和成本控制的目的,将电芯的性能最大化。
读透此文后,你就是K值专家

知行锂电●技艺┃读透此文后,你就是K值专家!引言:K值是用于描述电芯自放电速率的物理量,其计算方法为两次测试的开路电压差除以两次电压测试的时间间隔,公式为OCV2-OCV1/△T。
电芯在出货之前,一定要进行K值测试,并将K值大(等价于自放电)的电芯挑出来。
对于一个每家必测且如此重要的物理量,我们显然有必要对其进行深入的研究,本文的内容,便是如此。
如何测试K值在电芯分容后,并不可以马上测试电压,而是要将刚完成分容的电芯存储几天后(本文称呼其为第一次存储)再进行OCV1的测试,然后再存储几天(本文称呼其为第二次存储)进行OCV2测试。
电芯的K值,由OCV2减去OCV1后的差值,再除以两次存储之间的时间差值算得。
一般而言,第一次存储我们会使用45度或更高一些的高温条件,其目的有两个:通过高温存储将有腐蚀气账的电芯预先挑出来;通过高温存储让电芯的电压降速率逐步平稳,待存储过后再进行电压及K值测试,可以得到一致性比较好的结果(关于此点原理,下文还会继续介绍)。
综合以上内容,目前我们常见的K值测试及计算方法如下:K值有何意义K值作为一个电芯厂出货前必须测试的项目,自然有着其不可替代的价值,对电芯全检并筛选K值有如下意义:1)筛选内部微短路电芯:极片上的颗粒或微量金属残渣、隔膜上的微小缺陷、电芯在组装过程中引入的粉尘等,都会造成电芯内部微短路。
对于微短路电芯,仅通过容量及一次电压是无法完成筛选的,因此必须引入K值测试:通过精确计算其电压降速率来判断电芯是否存在微短路情况。
2)避免电芯长期存储之后电压降低太多:K值是电芯电压降速率的定量描述,K值过大,说明电芯电压降速度太快。
这样的电芯出货给客户,如果客户无法及时出货给到终端,那么电芯的电压一致性会随着时间的推移变的越来越差,长期存储后甚至无法满足设备开机等最基本功能,这显然是终端客户无法接受的(买个新开封的手机想试试,开机前还要先充电半小时......)3)辅助筛选其它性能不良电芯:根据小编的经验,当电芯K值较大时,其便存在腐蚀气账或循环不良的可能。
储能机组生产工艺流程
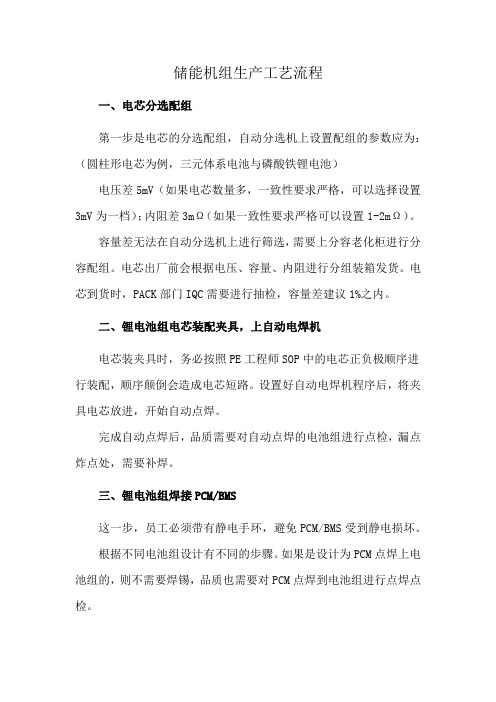
储能机组生产工艺流程一、电芯分选配组第一步是电芯的分选配组,自动分选机上设置配组的参数应为:(圆柱形电芯为例,三元体系电池与磷酸铁锂电池)电压差5mV(如果电芯数量多,一致性要求严格,可以选择设置3mV为一档);内阻差3mΩ(如果一致性要求严格可以设置1-2mΩ)。
容量差无法在自动分选机上进行筛选,需要上分容老化柜进行分容配组。
电芯出厂前会根据电压、容量、内阻进行分组装箱发货。
电芯到货时,PACK部门IQC需要进行抽检,容量差建议1%之内。
二、锂电池组电芯装配夹具,上自动电焊机电芯装夹具时,务必按照PE工程师SOP中的电芯正负极顺序进行装配,顺序颠倒会造成电芯短路。
设置好自动电焊机程序后,将夹具电芯放进,开始自动点焊。
完成自动点焊后,品质需要对自动点焊的电池组进行点检,漏点炸点处,需要补焊。
三、锂电池组焊接PCM/BMS这一步,员工必须带有静电手环,避免PCM/BMS受到静电损坏。
根据不同电池组设计有不同的步骤。
如果是设计为PCM点焊上电池组的,则不需要焊锡,品质也需要对PCM点焊到电池组进行点焊点检。
如果PCM/BMS需要焊锡,连接螺丝的PACK,对焊点,螺丝连接点也需要进行点检。
保证品质。
电压采集线,需要按照顺序B-,B1……依次到B+;或拔下电压采集线排插后焊接,焊接完成,对采集排插进行检测,确认无误后再连接BMS。
四、半成品绝缘对电压采集线,导线,正负极输出线,进行必要固定与绝缘。
辅料常规为高温胶布,青稞纸,环氧板,扎带等。
需要有安全意识,切勿对电池组电压采集线或输出导线进行叠加压迫,容易导致挤压破损造成短路。
五、半成品测试电池组加上BMS后,可以进行一次半成品测试,常规测试包括:简单充放电测试、整组内阻测试、整组容量测试、整组过充测试、整组过放测试、短路测试、过流测试。
如有特殊要求需进行高温低温测试、针刺测试、跌落测试、盐雾测试等,特殊锂电池组测试,有破坏性,建议抽检。
需要注意电池组的承受能力,如整组过充测试时,BMS是否可以耐高压;短路测试时BMS是否可以承受瞬间高压高电流;过流测试时BMS是否可以承受脉冲电流等。
- 1、下载文档前请自行甄别文档内容的完整性,平台不提供额外的编辑、内容补充、找答案等附加服务。
- 2、"仅部分预览"的文档,不可在线预览部分如存在完整性等问题,可反馈申请退款(可完整预览的文档不适用该条件!)。
- 3、如文档侵犯您的权益,请联系客服反馈,我们会尽快为您处理(人工客服工作时间:9:00-18:30)。
动力电芯配组标准标准化管理处编码[BBX968T-XBB8968-NNJ668-MM9N]
文件编号:NW-SOP-PE-188
工作规范
页码:1 of 2 版次:A0 文件名称:作业指导书-动力电池配组标准
修订状态
版本修订记录编制审核批准生效日期A0首次发行
目的
规范和指导进行动力电池配组。
范围
适用于本公司生产的动力电池和外购的动力电池。
定义
配组:指电池需要2个或以上数量电池的并联或者串联;
自耗电:指单个电池在老化储存前后的电压相差的数值;
自耗电差:指两个电池或多个电池在同一条件下测试的自耗电之间的数值差;
电压差:指两个电池或多个电池在同一条件下测试的电压之间的数值差;
容量差:指两个电池或多个电池在同一条件下测试的容量之间的数值差;
内阻差:指两个电池或多个电池在同一条件下测试的内阻之间的数值差;
平台容量:指电芯充满电后放电到规定电压所释放出的容量。
锰电芯、三元电芯放电到,铁电芯放电到。
(例:锰/三元电芯充满电后进行放电,记录时放电容量和时放电容
量,时的容量即平台容量,时的容量是电芯的整体容量。
);
平台容量比:平台容量/整体容量*100%;
平台容量比差:指两个电池或多个电池在同一条件下测试的平台容量比之间的数值差。
配组方法和要求
充/放电流要求:容量≤10AH,充/放电流1C;容量>10AH,充/放电流10A。
配组前容量测试:以恒流恒压方式对电池进行充电,直到电流降至0.02C时结束充电,然后放电至电池所要求终止电压,记录每个电池的平台容量和整体容量。
配组前充电要求:配组前对电池进行充电,标称电压为体系的电池充电到,标称电压为体系的电池充电到,然后恒压充电直到电流降至0.02C时结束充电。
老化储存测电压降和内阻变化:将充电后的电池静置超过1小时,然后用内阻仪测量内阻(精确到Ω),用4位半万用表20V直流档测量电压,精确到。
记录测试时间,将电池在常温下储存7天(具体老化时间可根据客户要求的出货交期决定),准时取出依序进行电压、内阻的测量,获得自耗电、内阻和电压数据。
配组要求:。