化学腐蚀法显示InP单晶和外延层中的缺陷
单晶硅中可能出现的各种缺陷

单晶硅中可能出现的各种缺陷【1】缺陷,是对于晶体的周期性对称的破坏,使得实际的晶体偏离了理想晶体的晶体结构。
在各种缺陷之中,有着多种分类方式,如果按照缺陷的维度,可以分为以下几种缺陷:点缺陷:在晶体学中,点缺陷是指在三维尺度上都很小的,不超过几个原子直径的缺陷。
其在三维尺寸均很小,只在某些位置发生,只影响邻近几个原子,有被称为零维缺陷。
线缺陷:线缺陷指二维尺度很小而第三维尺度很大的缺陷,也就是位错。
我们可以通过电镜等来对其进行观测。
面缺陷:面缺陷经常发生在两个不同相的界面上,或者同一晶体内部不同晶畴之间。
界面两边都是周期排列点阵结构,而在界面处则出现了格点的错位。
我们可以用光学显微镜观察面缺陷。
体缺陷:所谓体缺陷,是指在晶体中较大的尺寸范围内的晶格排列的不规则,比如包裹体、气泡、空洞等。
一、点缺陷点缺陷包括空位、间隙原子和微缺陷等。
1、空位、间隙原子点缺陷包括热点缺陷(本征点缺陷)和杂质点缺陷(非本征点缺陷)。
1.1热点缺陷其中热点缺陷有两种基本形式:弗仑克尔缺陷和肖特基缺陷。
单晶中空位和间隙原子在热平衡时的浓度与温度有关。
温度愈高,平衡浓度愈大。
高温生长的硅单晶,在冷却过程中过饱和的间隙原子和空位要消失,其消失的途径是:空位和间隙原子相遇使复合消失;扩散到晶体表面消失;或扩散到位错区消失并引起位错攀移。
间隙原子和空位目前尚无法观察。
1.2杂质点缺陷A、替位杂质点缺陷,如硅晶体中的磷、硼、碳等杂质原子B、间隙杂质点缺陷,如硅晶体中的氧等 1.3点缺陷之间相互作用一个空位和一个间隙原子结合使空位和间隙原子同时湮灭(复合),两个空位形成双空位或空位团,间隙原子聚成团,热点缺陷和杂质点缺陷相互作用形成复杂的点缺陷复合体等。
2、微缺陷 2.1产生原因如果晶体生长过程中冷却速度较快,饱和热点缺陷聚集或者他们与杂质的络合物凝聚而成间隙型位错环、位错环团及层错等。
Cz硅单晶中的微缺陷,多数是各种形态的氧化物沉淀,它们是氧和碳等杂质,在晶体冷却过程中,通过均质成核和异质成核机理形成。
半导体碳化硅外延层中的缺陷及检测技术详解
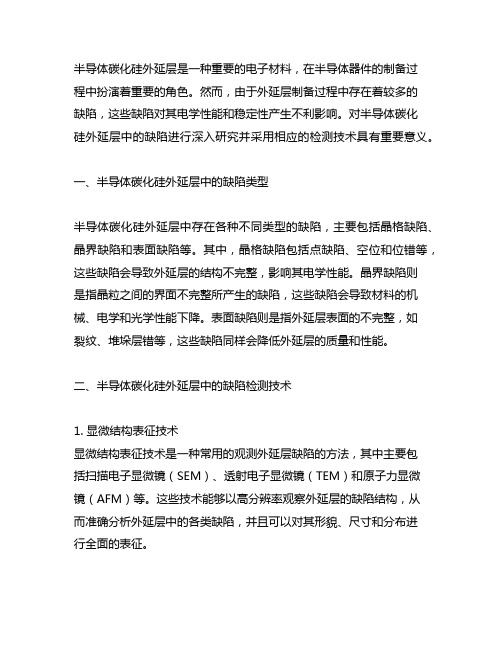
半导体碳化硅外延层是一种重要的电子材料,在半导体器件的制备过程中扮演着重要的角色。
然而,由于外延层制备过程中存在着较多的缺陷,这些缺陷对其电学性能和稳定性产生不利影响。
对半导体碳化硅外延层中的缺陷进行深入研究并采用相应的检测技术具有重要意义。
一、半导体碳化硅外延层中的缺陷类型半导体碳化硅外延层中存在各种不同类型的缺陷,主要包括晶格缺陷、晶界缺陷和表面缺陷等。
其中,晶格缺陷包括点缺陷、空位和位错等,这些缺陷会导致外延层的结构不完整,影响其电学性能。
晶界缺陷则是指晶粒之间的界面不完整所产生的缺陷,这些缺陷会导致材料的机械、电学和光学性能下降。
表面缺陷则是指外延层表面的不完整,如裂纹、堆垛层错等,这些缺陷同样会降低外延层的质量和性能。
二、半导体碳化硅外延层中的缺陷检测技术1. 显微结构表征技术显微结构表征技术是一种常用的观测外延层缺陷的方法,其中主要包括扫描电子显微镜(SEM)、透射电子显微镜(TEM)和原子力显微镜(AFM)等。
这些技术能够以高分辨率观察外延层的缺陷结构,从而准确分析外延层中的各类缺陷,并且可以对其形貌、尺寸和分布进行全面的表征。
2. 光学特性表征技术半导体碳化硅外延层的缺陷对其光学性能有着重要的影响,因此利用光学特性表征技术对外延层中的缺陷进行检测具有重要意义。
这些技术主要包括拉曼光谱、荧光光谱和激光散射等。
利用这些技术可以非常精确地分析外延层材料的光学响应,进而发现其中的缺陷和不完整结构。
3. 电学性能表征技术半导体碳化硅外延层的缺陷会影响其电学性能,因此通过电学性能表征技术可以检测外延层中的缺陷。
这些技术主要包括电子束诱导电流(EBIC)、深能量电子捕捉谱(DLTS)和微观电磁声谱等。
这些技术能够量化外延层中的缺陷浓度和类型,并且可以准确地分析缺陷对外延层电学性能的影响。
4. X射线和能谱技术X射线和能谱技术是一种常用的物质表征技术,通过测量外延层材料的X射线衍射图谱和能谱图谱,可以准确地鉴定外延层中的各类缺陷。
外延层缺陷及其减少方法--

减少外延层缺陷的方法
一、仔细地抛光、清洗硅衬底,做到表面光洁度好、清洁、无划痕和损 伤、无沾污。
二、采用超纯石墨基座,最好采用CVD涂覆碳化硅的石墨基座,以减少 来源于基座的金属杂质影响。
六、对外延用衬底C和O含量进行控制。 氧、碳、氢、氮是硅中研究最多的四种非金属元素。对于氧、碳 杂质,通常的做法是控制硅中氧含量,降低碳含量。一般的IC 工艺仍 然使用间隙氧含量在8~28ppm的硅衬底。此外,氧沉淀一直是令人 瞩目的研究课题。使用磁场控制直拉单晶中氧含量的实验还在继续, 实验证明,采用cusp 磁场可有效地控制硅单晶中的氧,对改善 200mm 以上的大直径单晶的均匀性具有实际意义。在IC工艺中,氧 沉淀对金属杂质的内吸除(IG)是有益的,IG 可延长少子寿命并提高 器件成品率。由于电路的设计线宽不断减小,氧浓度及其轴向和径向 均匀性的精确控制,在硅单晶的生长工艺中显得更为重要。 七、可用内吸除法或激光吸除法形成衬底表面洁净区(近乎无缺陷、无 有害杂质),然后再生长外延。
九、要减少金属杂质对外延片的沾污,首先要对各种沾污源进行控制和防 护。例如选用低金属含量的衬底;加强衬底硅片的清洗,经常对外延基 座和反应室进行HCl高温处理等。 另外可以使用杂质吸除技术。目前在硅外延生产中常用的吸除技 术是:(1)增强吸杂技术;在衬底背面淀积多晶硅,再在外面淀积SiO2 。以这样的衬底生产的外延片称为增强吸杂外延片。对于这种外延片, 多晶硅和SiO2起背封作用降低了气相自掺杂。多晶硅层因其晶粒 间界对金属杂质起吸除作用,多晶硅也促进了硅片体内的氧沉淀生长, 起内吸除作用即形成增强吸除功能 。 (2)背面软损伤吸杂:它是通过喷浆在衬底背面形成软机械损伤,在外 延过程中,利用这种机械损伤来吸杂。研究显示,在外延过程中,背面软 损伤诱生出来半环形位错起吸杂作用。这种半环形位错一端起自软损 伤,另一端绕过半环又回到背面,因此它不是延伸缺陷,不会影响硅外延 层上的器件。
第二章 化学腐蚀法检测晶体缺陷

而许多空位聚集成团,当它蹋蹦时形成位错圈时,可以 用化学腐蚀法或透射电子显微镜观察。
2、填隙原子(自间隙原子):晶体中的原子由于热运动或 辐射离开平衡位置跑到晶格的空隙中,这样的原子称为填隙 原子。如图所示:
图 2-3-2 弗仑克尔缺陷
填隙原子存在的方式: (1)与空位结合而消失。 (2)聚集成团形成间隙性位错圈。 (3)在生长界面附近凝聚形成微缺陷。
图 2-3-12 位错的攀移
6、位错的显示:通过化学腐蚀法显示晶体的位错,不同的 晶面上缺陷的腐蚀坑不同。如图所示:
(111)晶面
(110)晶面 图 2-3-12 刃位错的腐蚀坑图 像
3、半导体晶体的电化学腐蚀机理:
利用半导体晶体在各种酸或碱性电解质溶液中,表面构成了 微电池,由于微电池的电化学作用使晶体表面受到腐蚀,其 实质是一种氧化还原反应。
(1)在HNO3和HF溶液电解质溶液中的腐蚀 负极:
Si 2 H 2O 2 p SiO2 4 H 2e SiO2 6 HF H 2 SiF6 2 H 2O
正极:
HNO3 3H NO 2H2O 3 p
总反应:
3Si 4HNO3 18HF 3H2 SiF6 4NO 8H2O
无氧化剂时,发生析氢反应,反应速度较慢 正极:
2H 2e H 2
注:用CrO3或铬酸加在HF中也可以提高腐蚀速度
(2)在NaOH和KOH溶液电解质溶液中的腐蚀 负极:
第2章 化学腐蚀法检测晶体缺陷
2.1 半导体晶体的电化学腐蚀机理及常用 腐蚀剂 2.2 半导体单晶体的缺陷 2.3 硅单晶位错的检测 2.4 单晶硅中漩涡缺陷的检测 2.5 化学工艺中的安全知识 2.6 金相显微镜简介
Ar +刻蚀对InGaAs,n—InP和p-InP表面损伤及消除

中 图分 类 号 :T 2 N1
文 献 标 识 码 :A
文 章 编 号 :0 5 -17 2 0 )10 2 .5 2 34 7 (0 70 -1 20 Fra bibliotek1 引言
Ⅲ. V族 化 合 物 半 导 体 I Ga n As和 I P是 制 备 n 红外探 测器 、 光器 等 器件 的重 要 材料 . 基 于 I . 激 如 n Ga / n As I P结 构 的 红 外 探 测 器 , 探 测 器 具 有 室 温 该 工作 、 探测 率高 等优 点 , 光 通信 和航 天遥感 领 域有 在 重要 的 应 用[ 。. 1 ] 目前 , I n /n As I P台面  ̄ P N I P I Ga / n 制作 多采 用选 择性 湿 法 化学 腐蚀 法 , 蚀 I P层 一 腐 n 般采用 HC1H2 / 0系 和 HC / P 系腐蚀 液 , lH。 O 腐蚀 I Ga n As 层 一 般 采 用 H2 O / O / O 系 、 S 4 H2 2 H2 H3 O / o / o 系 和 酒 石 酸/ O2H2 系 腐 P H2 2 H2 H2 / O 蚀液 . 由于湿 法腐 蚀一般 为 各 向同性 , 其缺 点是 掩蔽 层下 面有 横 向钻 蚀 现象 , 点 是 对 腐 蚀 后 的 表 面不 优 产 生损 伤[ . 4 干法 刻 蚀 有 图 形 转 移 精 度 高 、 相 异 ] 各 性、 可控 性好 等 优 点 , 是 干 法 刻 蚀 会 造 成 晶格 损 但 伤, 使器 件 性 能 降 低[ . 法 刻 蚀 对 Ga 5 干 ] As和 A1 . Ga 的损 伤研究 较 多 , 对 I P和 I Ga 研究 较 As 而 n n As 少. 本文 通过 Ar 法 刻蚀 对 IGa , .n 干 n Asn I P和 P . IP表 面损 伤进行 了研 究 , n 计算 出 了损 伤 层 厚度 , 并 用 湿法 腐蚀 损伤 层 . 实验表 明 , 干法 和湿 法相 结合 对 制 作基 于 IGa / n n AsI P结 构 的 台 面 器 件 非 常 有 意 义, 这样 既 可 以增 强 光敏 面 的图形保 真度 , 可 以减 又 小 台面 的侧 面损 伤 .
外延层缺陷及其减少方法--

当在一个晶面上同时形成许多晶核时,它们大多数不可能错配,错 配只发生在很少的晶核上。而且随着外延层的生长逐渐扩大,最终沿 着三个(111)面发育成一倒立四面体。
由于此四面体是错配的晶核发育成,因此在它与正常生长的晶体的 界面两侧,原子是失配的。也就是说,晶格的完整性在这些界面附近 受到破坏。
但在层错内部,晶格仍然是完整的。由错配的晶核为起源的层错, 并不一定沿着三个(111)面发展到表面,即在表面并不都成三角形 ,在某些情况下,层错周围的正常生长可以抢先占据上面的自由空间 ,因而使得层错不能充分发育。于是表现在层错的腐蚀图型不是完整 的三角形,而可能是一条直线,或者是一鱼。
(2)背面软损伤吸杂:它是通过喷浆在衬底背面形成软机械损伤,在外 延过程中,利用这种机械损伤来吸杂。研究显示,在外延过程中,背面软 损伤诱生出来半环形位错起吸杂作用。这种半环形位错一端起自软损 伤,另一端绕过半环又回到背面,因此它不是延伸缺陷,不会影响硅外延 层上的器件。
外延层缺陷与衬底有关的几项
一、存在于衬底中并连续延伸到外延层中的线位错。(图中1)
二、在衬底表面杂质产生外延层堆垛层错的成核。此外衬底表面残存的 氧化物、吸取的碳氢化合物也导致堆垛层错。 (图中2)
三、外延工艺引起的外关或或与表面加工(抛光面划痕、损伤)、碳沾污等有关 ,形成的表面锥体缺陷(如角锥体、三棱锥体、圆锥体、小丘)或其 他生长体。 (图中4)
九、要减少金属杂质对外延片的沾污,首先要对各种沾污源进行控制和防 护。例如选用低金属含量的衬底;加强衬底硅片的清洗,经常对外延基 座和反应室进行HCl高温处理等。
另外可以使用杂质吸除技术。目前在硅外延生产中常用的吸除技 术是:(1)增强吸杂技术;在衬底背面淀积多晶硅,再在外面淀积SiO2 。以这样的衬底生产的外延片称为增强吸杂外延片。对于这种外延片, 多晶硅和SiO2起背封作用降低了气相自掺杂。多晶硅层因其晶粒 间界对金属杂质起吸除作用,多晶硅也促进了硅片体内的氧沉淀生长, 起内吸除作用即形成增强吸除功能 。
外延薄膜中的缺陷
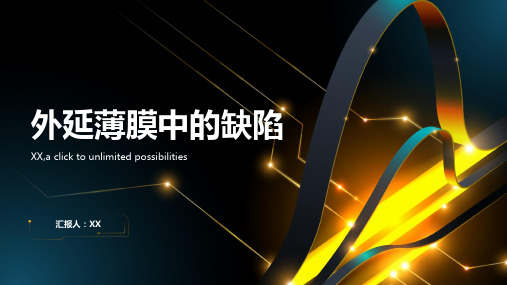
衬底与外延薄膜的匹配:确保衬底与外 延薄膜在晶格结构、热膨胀系数等方面 相匹配,以减少因失配引起的缺陷。
杂质控制
杂质来源:原材料、设备、环境等 杂质扩散:控制扩散速度和范围 杂质类型:金属、非金属等 杂质检测:采用各种检测手段
表面重构优化
表面重构的概念: 通过改变薄膜表面 的原子排列,提高 薄膜的稳定性和性 能。
衬底表面的粗糙度、不均匀性以及附着力的强弱等因素也会影响外延薄 膜中缺陷的形成。
衬底中的杂质和缺陷可以传递到外延薄膜中,从而影响其结构和性能。
衬底温度对外延薄膜中缺陷的形成也有影响,温度过高或过低都可能导 致缺陷的产生。
杂质的影响
杂质的存在会导 致外延薄膜中缺 陷的形成。
杂质的类型和浓 度对缺陷的形成 有重要影响。
动力学演化
缺陷的生成与扩散
缺陷间的相互作用
缺陷与外延薄膜的相互作用
缺陷演化的动力学模型
缺陷的相互作用与竞争
不同缺陷之间的相互作用 方式
缺陷之间的竞争关系及其 演化过程
缺陷相互作用的物理机制 和影响因素
缺陷竞争对薄膜性能的影 响和作用机理
缺陷的扩散与迁移
缺陷在外延薄膜中的扩散方式 缺陷扩散的驱动力与影响因素 缺陷的迁移机制与动力学过程 缺陷扩散与迁移对薄膜性能的影响
外延薄膜中的缺陷
XX,a click to unlimited possibilities
汇报人:XX
目录
01 外 延 薄 膜 的 缺 陷 类 型
03 外 延 薄 膜 中 缺 陷 的
演化机制
05 外 延 薄 膜 中 缺 陷 的 控制方法
02 外 延 薄 膜 中 缺 陷 的 形成原因
04 外 延 薄 膜 中 缺 陷 的 表征技术
实验一 半导体材料的缺陷显示及观察

这个四面体相当于前述的许多小正四面体堆积起来的。由于此四面体是由错配的晶核发育而成的,因此,在它与正常生长的晶体的界面两侧,原子是失配的。也就是说,晶格的完整性在这些界面附近受到破坏,但在层错的内部,晶格仍是完整的。
由错配的晶核为起源的层错,并不一定都能沿三个<111>面发展到表面,即在表面并不都呈三角形。在外延生长过程中,形成层错的机理较复杂。在某些情况下,层错周围的正常生长可能很快,抢先占据了上面的自由空间,因而使得层错不能充分发育。这表现在层错的腐蚀图形不是完整的三角形,而可能是一条直线,或者为一角,如图6所示。
配制好抛光液倒入氟塑料杯中,将清洗干净的硅片用镊子轻轻夹入抛光液中,密切注意表面变化,操作时注意样品应始终淹没在抛光液中,同时应当不停地搅拌以改进抛光均匀性,待硅片表面光亮如镜,则抛光毕,迅速将硅片夹入预先准备好的去离子水杯中,再用流动的去离子水冲洗,在抛光过程中,蚀速对温度异常敏感。一般说来在温度18℃~25℃的范围,抛光时间约为1.5~4分钟。
在外延生长过程中,层错的形成和传播如图4所示。假定衬底表面层的原子是按A型排列的,即按正常生长层序,外延生长的第一层应为B型排列。但由于某种原因,使得表面的某一区域出现反常情况而成C型排列。即按ABCACABC……(抽出B层)排列。它向上发展,并逐层扩大,最终沿三个〈111〉面发育成为一倒立的四面体(见图5)。
目镜物镜视场直径
外延薄膜中的缺陷ppt课件

外延薄膜中的应变与失配位错
<0 膜内压应力
f =0 无应力
>0 膜内张应力
fit
strain
relax
pseudomorphic, 晶体. 结构一样
产生位错的临界厚度
产生失配位错的驱动力来自 薄膜应变能的降低.
无位错薄膜单位面积内的应变能
E
2ehf
2 1v 1v
e 切变模量;v 泊松比
h 薄膜厚度;f 失配度
.
金属中的点缺陷:空位间隙原子,替代杂质 平衡缺陷浓度:
n e x ( E T p ) /k S ] [ T eS x /k ) e p x E / ( k ) p T (
面心密堆积中的间隙:
四面体间隙位坐标: (1/4,1/4, 1/4)
+
各原子坐标
其余四面体间隙坐标。
.
面心密堆积中的间隙
用薄膜应变场对穿过位错的作用应力(=2F/hb)和位错自身 的线张应力d (=2Fd/b)相等为判据
(e=0), 也可以得到薄膜临界厚度的表达式. 但是, 要求上述两个应力相 等的判据实际上是过低了, 因为此时位错受到的净作用力为零, 即使依靠热激活, 位错运动速度也太小, 因此更合理的判据是: 对穿过位错的作用应力应超过位错线张力, 即:
的荷电状态,
.
间隙位置坐标: (1/2,1/2, 1/2)
+
各原子坐标 其余间隙位置坐标。
金刚石结构中的间隙
.
金刚石结构的晶胞中原子在底面的投影, 数字是垂直 方向上的坐标, 其单位是晶格常数的1/8(b), 四面体间
隙(方形)和六角间隙(三角形)在底面的投影,
.
晶胞中有8个原子,8个四面 体间隙,16个六面体间隙 原子半径:0.2165, T间隙到最近邻原子中心的 距离0.433,到次近邻的距离 0.500; H间隙到最近邻原子中心距 离为0.415
单晶硅中可能出现的各种缺陷
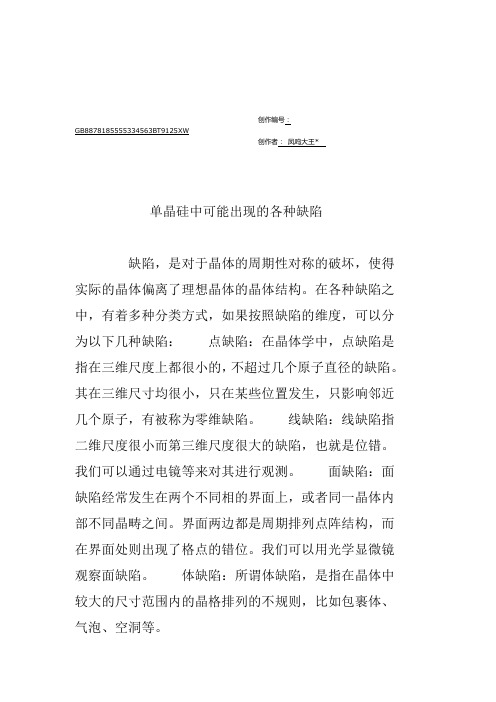
创作编号:GB8878185555334563BT9125XW创作者:凤呜大王*单晶硅中可能出现的各种缺陷缺陷,是对于晶体的周期性对称的破坏,使得实际的晶体偏离了理想晶体的晶体结构。
在各种缺陷之中,有着多种分类方式,如果按照缺陷的维度,可以分为以下几种缺陷:点缺陷:在晶体学中,点缺陷是指在三维尺度上都很小的,不超过几个原子直径的缺陷。
其在三维尺寸均很小,只在某些位置发生,只影响邻近几个原子,有被称为零维缺陷。
线缺陷:线缺陷指二维尺度很小而第三维尺度很大的缺陷,也就是位错。
我们可以通过电镜等来对其进行观测。
面缺陷:面缺陷经常发生在两个不同相的界面上,或者同一晶体内部不同晶畴之间。
界面两边都是周期排列点阵结构,而在界面处则出现了格点的错位。
我们可以用光学显微镜观察面缺陷。
体缺陷:所谓体缺陷,是指在晶体中较大的尺寸范围内的晶格排列的不规则,比如包裹体、气泡、空洞等。
一、点缺陷点缺陷包括空位、间隙原子和微缺陷等。
1、空位、间隙原子点缺陷包括热点缺陷(本征点缺陷)和杂质点缺陷(非本征点缺陷)。
1.1热点缺陷其中热点缺陷有两种基本形式:弗仑克尔缺陷和肖特基缺陷。
单晶中空位和间隙原子在热平衡时的浓度与温度有关。
温度愈高,平衡浓度愈大。
高温生长的硅单晶,在冷却过程中过饱和的间隙原子和空位要消失,其消失的途径是:空位和间隙原子相遇使复合消失;扩散到晶体表面消失;或扩散到位错区消失并引起位错攀移。
间隙原子和空位目前尚无法观察。
1.2杂质点缺陷A、替位杂质点缺陷,如硅晶体中的磷、硼、碳等杂质原子B、间隙杂质点缺陷,如硅晶体中的氧等 1.3点缺陷之间相互作用一个空位和一个间隙原子结合使空位和间隙原子同时湮灭(复合),两个空位形成双空位或空位团,间隙原子聚成团,热点缺陷和杂质点缺陷相互作用形成复杂的点缺陷复合体等。
2、微缺陷2.1产生原因如果晶体生长过程中冷却速度较快,饱和热点缺陷聚集或者他们与杂质的络合物凝聚而成间隙型位错环、位错环团及层错等。
InP中的深能级杂质与缺陷(续)

孙 聂 枫 等 :IP 中 的深 能 级 杂 质 与 缺 陷 ( ) n 续
样存 在 上述 缺 陷 ,F 浓 度 的 变 化在 IP中造 成 的 e n 杂质 条纹 以及 由此 造成 的 电阻率 的起伏 在实验 中很 容易 被观察 到 。实验 发现 S—n 中 的亮 点 缺 陷与 I P I
制备 S—n I P材料 需要 在 晶体 中掺 入 F I e的浓度 达 1 c 3 上_ O mI 以 3 引。实 验 研 究 表 明 ,S — P衬 II n 底 中的 F e在外 延生 长 过程 中会 向外 延 层 扩散 ,从 而降 低器 件 的性 能 。S—n 中高浓 度 F I P I e还 造 成离
还进 一步 分裂 为一 系列 能级 。低 温下 的红外 吸 收谱
可测 到 电子在 这些 能级 间跃迁 所对 应 的吸 收 ,由此
收 稿 日期 :2 0 — 6 1 O80— 5 E mal n s n h if . e _ i fu @ e o n t : n
微 纳 电子 技 术 第4 卷 第1期 6 1 5 1 2
中 图分 类号 :TN 0 . 3 3 4 2 ;O 7 文 献标识 码 :A 文章 编号 :1 7 4 7 ( o 8 1 O 2 6 44 6 卜 7 6 2 0 )1 一 6 卜0
De p I u iisa d Del t n I P C0 tn e ) e mp rte n fcsi n ( n i u d e
2 ,£ “ 0 . 2 ,S m ∞ c r ,T P P 口 s £ s 锄 s Ac 0 C
EEACCLeabharlann :71 5 ; 81 0; 7 2 5F 6 10
0 c ,B 厂S f P
硅单晶中晶体缺陷的腐蚀显示

硅单晶中晶体缺陷的腐蚀显示实验安排:4人/组时间:两小时地点:北方工业大学第三教学楼2403房间实验所用主要设备:金相显微镜一、实验目的硅单晶中的各种缺陷对器件的性能有很大的影响,它会造成扩散结面不平整,使晶体管中出现管道,引起p-n 结的反向漏电增大等。
各种缺陷的产生和数量的多少与晶体制备工艺和器件工艺有关。
晶体缺陷的实验观察方法有许多种,如透射电子显微镜、X光貌相技术、红外显微镜及金相腐蚀显示等方法。
对表面缺陷也可以用扫描电子显微镜来观察。
由于金相腐蚀显示技术设备简单,操作易掌握,又较直观,是观察研究晶体缺陷的最常用的方法之一。
金相腐蚀显示可以揭示缺陷的数量和分布情况,找出缺陷形成、增殖和晶体制备工艺及器件工艺的关系,为改进工艺,减少缺陷、提高器件合格率和改善器件性能提供线索。
二、原理硅单晶属金刚石结构,在实际的硅单晶中不可能整块晶体中原子完全按金刚石结构整齐排列,总又某些局部区域点阵排列的规律性被破坏,则该区域就称为晶体缺陷。
硅单晶中的缺陷主要有点缺陷、线缺陷和面缺陷等三类。
晶体缺陷可以在晶体生长过程中产生,也可以在热处理、晶体加工和受放射性辐射时产生。
在硅单晶中缺陷区不仅是高应力区,而且极易富集一些杂质,这样缺陷区就比晶格完整区化学活拨性强,对化学腐蚀剂的作用灵敏,因此容易被腐蚀而形成蚀坑,在有高度对称性的低指数面上蚀坑形状通常呈现相应的对称性,如位错在(111)、(100)、(110)面上分别呈三角形、方形和菱形蚀坑。
用作腐蚀显示的腐蚀剂按不同作用大体可分为两类,一类蚀非择优腐蚀剂,它主要用于晶体表面的化学抛光,目的在于达到清洁处理,去除机械损伤层和获得一个光亮的表面;另一类是择优腐蚀剂,用来揭示缺陷。
一般腐蚀速度越快择择优性越差,而对择优腐蚀剂则要求缺陷蚀坑的出现率高、特征性强、再现性好和腐蚀时间短。
通常用的非择优腐蚀剂的配方为:HF(40-42%):HNO3(65%)=1:2.5它们的化学反应过程为:Si+4HNO3+6HF=H2SiF6+4NO2+4H2O通常用的择优腐蚀剂主要有以下二种:(1)希尔腐蚀液(铬酸腐蚀液)先用CrO3与去离子水配成标准液:标准液=50g CrO3+100g H2O然后配成下列几种腐蚀液:A. 标准液:HF(40-42%)=2:1(慢速液)B. 标准液:HF(40-42%)=3:2(中速液)C. 标准液:HF(40-42%)=1:1(快速液)D. 标准液:HF(40-42%)=1:2(快速液)一般常用的为配方C液,它们的化学反应过程为:Si+CrO3+8HF=H2SiF6+CrF2+3H2O(2)达希腐蚀液达希(Dash)腐蚀液的配方为:HF(40-42%):HNO3(65%):CH3COOH(99%以上)=1:2.5:10硅单晶中不同种类的缺陷需选用上述不同的配方,采用不同的腐蚀工艺。
晶体缺陷显示实验

晶体缺陷显示实验指导实验名称:晶体缺陷显示实验实验目的:1、了解掌握硅单晶片研磨、热处理、化学抛光和化学腐蚀的操作方法。
2、学会在金相显微镜下观测硅单晶中的位错或点缺陷。
实验内容:在硅单晶(选〈111〉晶向)片上通过研磨和热处理、化学抛光和化学腐蚀的方法显示晶体缺陷。
用“非择优腐蚀剂”进行表面化学抛光;然后用“择优腐蚀剂”进行化学腐蚀来揭示晶体缺陷。
在金相显微镜下观测硅晶体位错或漩涡缺陷(点缺陷)的腐蚀坑,根据显示的腐蚀坑数目来计算缺陷密度。
实验原理:1、常用的“非择优腐蚀剂”为:HF (40—42 %):HNO3 (65%) = 1:2.5。
主要用于硅片表面化学抛光,以达到表面清洁处理,去除机械损伤层,获得光亮表面的目的。
(其反应原理为:Si + 4HNO3 + 6HF = H2SiF6 + 4NO2↑+4 H2O )2、常用的“择优腐蚀剂”为:标准液:HF (40—42 %) = 3:1慢速液标准液:HF (40—42 %) = 2:1中速液标准液:HF (40—42 %) = 1:1中速液标准液:HF (40—42 %) = 1:2快速液(其中标准液为:CrO3:H2O = 1:2 重量比)。
用来揭示缺陷,一般来说腐蚀速度越快,择优性越差。
根据现在气温我们选1:1的中速液。
(其反应原理为:Si + CrO3 + 8HF = H2SiF6 + CrF2 + 3H2O )硅晶体中位错线或点缺陷附近晶格发生畸变,不稳定。
位错或漩涡缺陷在硅片表面露头处周围,腐蚀速度比较快,从而形成缺陷腐蚀坑(如图)。
腐蚀坑的数目可在金相显微镜中数出,单位面积内腐蚀坑的数目称为缺陷密度。
三角坑是因为硅(111)面容易显露出来的结果。
实验方法和步骤:1、用14μ刚玉细砂在玻璃板上研磨硅片30—40分钟。
2、在ZKL—1F型石英管扩散炉中对硅片进行退火处理1小时。
3、带上乳胶手套,在通风橱中用量筒、烧杯配适当量的“非择优腐蚀剂”,将硅片放入其中进行抛光,时间大约3—4分钟,以试剂变成棕黄色并冒烟为准。
半导体缺陷解析及中英文术语一览

一、半导体缺陷1.位错:位错又可称为差排(英语:dislocation),在材料科学中,指晶体材料的一种内部微观缺陷,即原子的局部不规则排列(晶体学缺陷)。
从几何角度看,位错属于一种线缺陷,可视为晶体中已滑移部分与未滑移部分的分界线,其存在对材料的物理性能,尤其是力学性能,具有极大的影响。
产生原因:晶体生长过程中,籽晶中的位错、固-液界面附近落入不溶性固态颗粒,界面附近温度梯度或温度波动以及机械振动都会在晶体中产生位错。
在晶体生长后,快速降温也容易增殖位错。
(111)呈三角形;(100)呈方形;(110)呈菱形。
2.杂质条纹:晶体纵剖面经化学腐蚀后可见明、暗相间的层状分布条纹,又称为电阻率条纹。
杂质条纹有分布规律,在垂直生长轴方向的横断面上,一般成环状分布;在平行生长轴方向的纵剖面上,呈层状分布。
反映了固-液界面结晶前沿的形状。
产生原因:晶体生长时,由于重力产生的自然对流和搅拌产生的强制对流,引起固-液界近附近的温度发生微小的周期性变化,导致晶体微观生长速率的变化,或引起杂质边界厚度起伏,一截小平面效应和热场不对称等,均使晶体结晶时杂质有效分凝系数产生波动,引起杂质中杂质浓度分布发生相应的变化,从而在晶体中形成杂质条纹。
解决方案::调整热场,使之具有良好的轴对称性,并使晶体的旋转轴尽量与热场中心轴同轴,抑制或减弱熔热对流,可以使晶体中杂质趋于均匀分布。
采用磁场拉晶工艺或无重力条件下拉晶可以消除杂质条纹。
3.凹坑:晶体经过化学腐蚀后,由于晶体的局部区域具有较快的腐蚀速度,使晶体横断面上出现的坑。
腐蚀温度越高,腐蚀时间越长,则凹坑就越深,甚至贯穿。
4.空洞:单晶切断面上无规则、大小不等的小孔。
产生原因:在气氛下拉制单晶,由于气体在熔体中溶解度大,当晶体生长时,气体溶解度则减小呈过饱和状态。
如果晶体生长过快,则气体无法及时从熔体中排出,则会在晶体中形成空洞。
5.孪晶:使晶体断面上呈现金属光泽不同的两部分,分界线通常为直线。
InP、InAs和GaSb单晶材料缺陷和晶体完整性研究的开题报告

InP、InAs和GaSb单晶材料缺陷和晶体完整性研究的开题报告一、研究背景InP、InAs和GaSb是典型的III-V族半导体材料,在光电子、微电子和红外探测等领域具有广泛的应用。
然而,在材料的生长和制备过程中,晶体缺陷和非理想晶体结构的产生对其性能和应用带来了一定的影响,因此进行缺陷和晶体完整性研究具有重要的科学和工程价值。
二、研究内容本课题旨在探究InP、InAs和GaSb单晶材料的缺陷和晶体完整性问题,具体研究内容如下:1.研究材料的生长和制备过程中可能产生的缺陷及其类型,分析不同缺陷对晶体结构和性能的影响。
2.利用X射线衍射、扫描电镜、透射电镜等分析方法,对InP、InAs 和GaSb单晶材料的晶体结构进行研究,探究其晶格常数、晶体结构和缺陷密度等相关特性。
3.通过光学测试、电学测试等方法,研究晶体中缺陷对光电特性和电学性能的影响,探究其应用前景。
三、研究意义通过对InP、InAs和GaSb单晶材料的缺陷和晶体完整性研究,可以深入了解其材料性质和应用特性,为优化材料生长和制备工艺提供理论和实验依据。
同时,探究晶体缺陷对光电特性和电学性能的影响,对该类材料广泛应用于光电子、微电子和红外探测等领域具有重要的科学和工程价值。
四、研究计划1.第一阶段:熟悉InP、InAs和GaSb单晶材料的性质和应用特性,了解不同缺陷类型及其对晶体结构和性能的影响。
2.第二阶段:对InP、InAs和GaSb单晶材料的生长和制备过程进行探究,研究不同生长条件对晶体缺陷的影响。
3.第三阶段:利用X射线衍射、扫描电镜、透射电镜等分析方法对材料的晶体结构和缺陷进行研究,并分析其晶格常数、晶体结构和缺陷密度等相关特性。
4.第四阶段:通过光学测试、电学测试等方法,研究晶体中缺陷对光电特性和电学性能的影响,探究其应用前景。
五、预期结果与创新性1.阐明InP、InAs和GaSb单晶材料的缺陷类型及其对晶体结构和性能的影响,为相应领域的研究提供重要依据。
容器微观缺陷种类及消除方法

容器微观缺陷种类及消除方法随着工业生产智能化的不断发展,各种新型容器应用越来越广泛,作为容器制造产业链中不可或缺的一个环节——容器表面缺陷检测技术得以蓬勃发展,一些人们过往难以发现或难以避免的容器微观缺陷现在逐渐被人们所关注。
本文将介绍容器微观缺陷种类及其消除方法。
容器微观缺陷种类容器微观缺陷种类有很多种,常见的可分为以下几类:1. 毛刺毛刺是一种比较常见的微观缺陷,它是容器内部凝固后的表面不平整,形成的锋利角或突出部分,机械加工的摩擦、磨损会使得其表面变得更加粗糙,进而对容器使用造成负面影响。
2. 金属飞溅金属飞溅是指容器表面金属被熔化后飞散在物体表面的相变物质,这种微观缺陷不仅会降低容器的质量,还会对环境带来危险,极易引发火灾等事故。
3. 气孔气孔是一种空洞或中空表面,在容器表层形成圆形或溢出状的细小气泡,这种气泡形成的原因与所使用的材料、制造工艺等一系列因素有关。
裂纹是在容器内外形成的裂缝现象,通常出现在表面受到撞击或加工过程中的损伤较大时,如果不及时处理处理容器的使用寿命将缩短。
容器微观缺陷消除方法针对不同的容器微缺陷种类,有不同的处理方法,基本的方法有以下几种:1. 研磨法研磨法是一种通过切削或磨削,使缺陷表面变平滑的方法,针对毛刺、气孔等缺陷类型效果较好,但需注意切削或磨削技术是否符合标准。
2. 超声波法超声波法是一种利用超声波在容器表面形成的频率振动以消除毛刺、金属飞溅等缺陷的方法,其处理效果相对较好,但费用较高。
3. 焊接补救法焊接补救法通常在容器裂纹严重时采取,通过专业技术的加工对裂纹进行补救焊接,可以使容器在一定程度上继续使用,消除不利影响。
4. 化学蚀刻法化学蚀刻法是通过在容器内外表面局部涂层蚀刻液进行反应消除毛刺、气孔、金属飞溅等缺陷的方法,但注意蚀刻量需要控制,不可过多。
容器微观缺陷通常会对容器的强度、寿命、美观度等方面产生负面影响,为了保证制品质量和生产效率,解决这些微观缺陷的问题就显得极为重要。
化孔镀层缺陷成因分析及对策
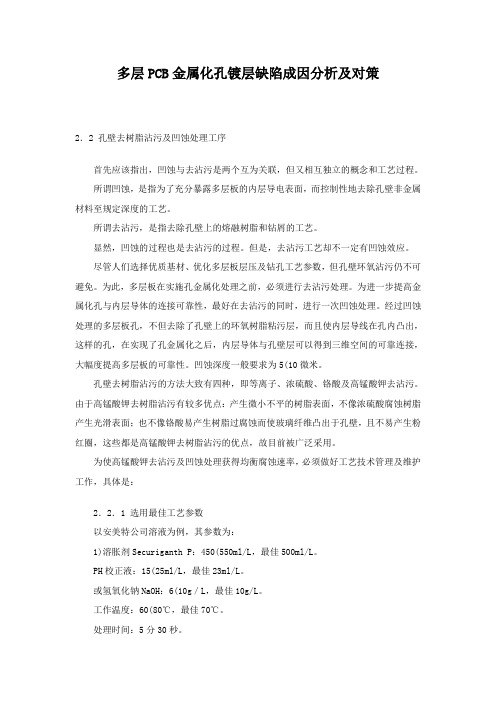
多层PCB金属化孔镀层缺陷成因分析及对策2.2 孔壁去树脂沾污及凹蚀处理工序首先应该指出,凹蚀与去沾污是两个互为关联,但又相互独立的概念和工艺过程。
所谓凹蚀,是指为了充分暴露多层板的内层导电表面,而控制性地去除孔壁非金属材料至规定深度的工艺。
所谓去沾污,是指去除孔壁上的熔融树脂和钻屑的工艺。
显然,凹蚀的过程也是去沾污的过程。
但是,去沾污工艺却不一定有凹蚀效应。
尽管人们选择优质基材、优化多层板层压及钻孔工艺参数,但孔壁环氧沾污仍不可避免。
为此,多层板在实施孔金属化处理之前,必须进行去沾污处理。
为进一步提高金属化孔与内层导体的连接可靠性,最好在去沾污的同时,进行一次凹蚀处理。
经过凹蚀处理的多层板孔,不但去除了孔壁上的环氧树脂粘污层,而且使内层导线在孔内凸出,这样的孔,在实现了孔金属化之后,内层导体与孔壁层可以得到三维空间的可靠连接,大幅度提高多层板的可靠性。
凹蚀深度一般要求为5(10微米。
孔壁去树脂沾污的方法大致有四种,即等离子、浓硫酸、铬酸及高锰酸钾去沾污。
由于高锰酸钾去树脂沾污有较多优点:产生微小不平的树脂表面,不像浓硫酸腐蚀树脂产生光滑表面;也不像铬酸易产生树脂过腐蚀而使玻璃纤维凸出于孔壁,且不易产生粉红圈,这些都是高锰酸钾去树脂沾污的优点,故目前被广泛采用。
为使高锰酸钾去沾污及凹蚀处理获得均衡腐蚀速率,必须做好工艺技术管理及维护工作,具体是:2.2.1 选用最佳工艺参数以安美特公司溶液为例,其参数为:1)溶胀剂Securiganth P:450(550ml/L,最佳500ml/L。
PH校正液:15(25ml/L,最佳23ml/L。
或氢氧化钠NaOH:6(10g/L,最佳10g/L。
工作温度:60(80℃,最佳70℃。
处理时间:5分30秒。
2)高锰酸钾KMnO4:50(60g/L,最佳60g/L。
氢氧化钠NaOH: 30(50g/L,最佳40g/L。
工作温度:60(80℃,最佳70℃。
处理时间:12分。
钛合金半成品腐蚀检查常见材料缺陷分析
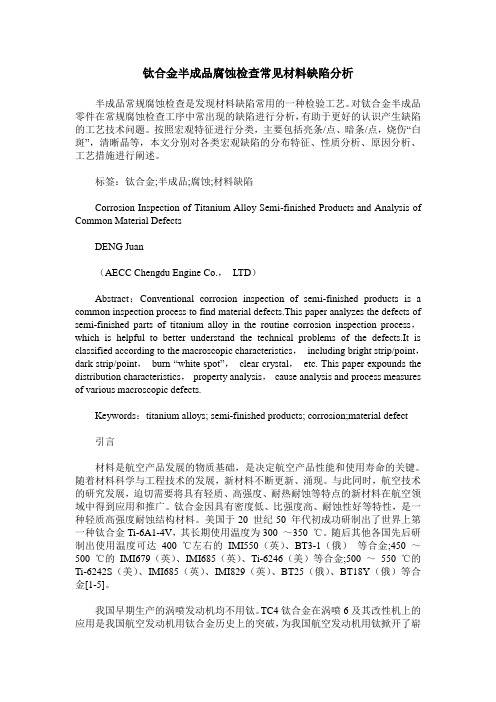
钛合金半成品腐蚀检查常见材料缺陷分析半成品常规腐蚀检查是发现材料缺陷常用的一种检验工艺。
对钛合金半成品零件在常规腐蚀检查工序中常出现的缺陷进行分析,有助于更好的认识产生缺陷的工艺技术问题。
按照宏观特征进行分类,主要包括亮条/点、暗条/点,烧伤“白斑”,清晰晶等,本文分别对各类宏观缺陷的分布特征、性质分析、原因分析、工艺措施进行阐述。
标签:钛合金;半成品;腐蚀;材料缺陷Corrosion Inspection of Titanium Alloy Semi-finished Products and Analysis of Common Material DefectsDENG Juan(AECC Chengdu Engine Co.,LTD)Abstract:Conventional corrosion inspection of semi-finished products is a common inspection process to find material defects.This paper analyzes the defects of semi-finished parts of titanium alloy in the routine corrosion inspection process,which is helpful to better understand the technical problems of the defects.It is classified according to the macroscopic characteristics,including bright strip/point,dark strip/point,bu rn “white spot”,clear crystal,etc. This paper expounds the distribution characteristics,property analysis,cause analysis and process measures of various macroscopic defects.Keywords:titanium alloys; semi-finished products; corrosion;material defect引言材料是航空产品发展的物质基础,是决定航空产品性能和使用寿命的关键。
InP 中的深能级杂质与缺陷

InP中的深能级杂质与缺陷微纳电子技术孙聂枫,赵有文,孙同年(1.中国电子科技集团公司 第十三研究所 专用集成电路国家重点实验室,石家庄 050051;2.中国科学院 半导体研究所,北京 100083)0 引言InP材料具有许多优点:直接跃迁型能带结构和高的电光转换效率;电子迁移率高,易于制成半绝缘材料,适合制作高频微波器件和电路;工作温度高 (400~450 ℃);具有强的抗辐射能力;作为太阳能电池材料时转换效率较高等。
这些特性决定了InP材料在微波、毫米波通信、光纤通信、制导/导航、卫星等民用和军事 等领域的广泛应用。
InP材料因其自身不可替代的优越性做为一种非常重要的战略性半导体材料得到了各发达国家的重视。
有关InP材料、器件的制备以及特性 的研究工作已持续开展。
1989年开始IEEE等国际组织召开了国际InP 及相关材料会议(IPRM),2008年召开了第20届IPRM会议。
1968年J.B.Mullin等人口利用液封直拉技术生长了InP单晶,使得人们利用较大直径的InP材料开展特性研究及器件制备成为可能。
20世纪 70年代以来,人们对InP材料中的杂质和缺陷的认识越来越丰富而深刻,并在70年代中后期首次实现了以InP单晶为衬底制作的长波长激光器室温下的激 射,使InP单晶的制备和特性研究开始逐步引起人们的重视。
80年代初期,InP基高电子迁移率晶体管的出现,说明InP在微电子领域也具有优异的特性, 使人们认为有可能在InP上方便地实现光电集成。
作为微电子器件应用材料,半绝缘InP有很多优于GaAs的性质:①InP器件的电流峰谷比高于GaAs,比GaAs器件有更高的转换效率;②惯性能量时间常数小,只及GaAs的一半,故其工作频率的极限比GaAs器件高出一倍;③InP峰谷比的温度系数比GaAs小,且热导率比GaAs高,更有利于制作连续波器件,且所制器件有更大的功率输出;④InP材料的D/μ(D为电子扩散系数,μ为负微分迁移率)低,使InP器件有更好的噪声特性;⑤在较高频率下,InP基的Gun器件有源层的长度是GaAs器件的2倍,可简化器件的制作工艺等;⑥电子峰值漂移速度比GaAs高,可以制作出工作速度和频率更高的器件;⑦InP器件比同类GaAs器件有更小的功耗和更低的噪声。