最新国产三釜聚酯装置介绍
聚酯装置简介和重点部位及设备(图文)
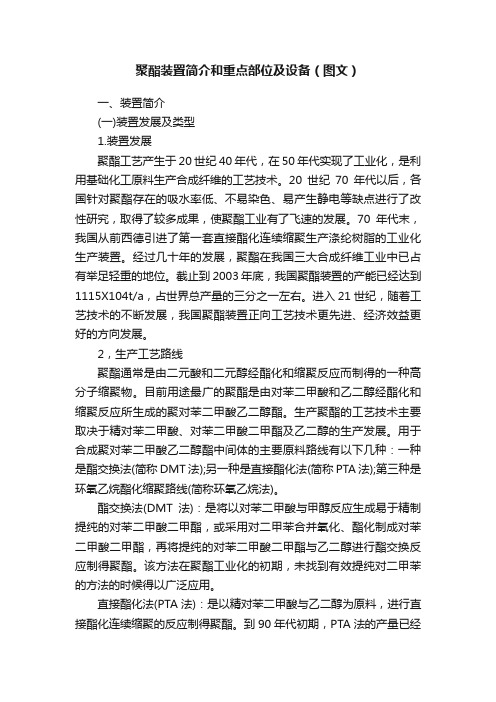
聚酯装置简介和重点部位及设备(图文)一、装置简介(一)装置发展及类型1.装置发展聚酯工艺产生于20世纪40年代,在50年代实现了工业化,是利用基础化工原料生产合成纤维的工艺技术。
20世纪70年代以后,各国针对聚酯存在的吸水率低、不易染色、易产生静电等缺点进行了改性研究,取得了较多成果,使聚酯工业有了飞速的发展。
70年代末,我国从前西德引进了第一套直接酯化连续缩聚生产涤纶树脂的工业化生产装置。
经过几十年的发展,聚酯在我国三大合成纤维工业中已占有举足轻重的地位。
截止到2003年底,我国聚酯装置的产能已经达到1115X104t/a,占世界总产量的三分之一左右。
进入21世纪,随着工艺技术的不断发展,我国聚酯装置正向工艺技术更先进、经济效益更好的方向发展。
2,生产工艺路线聚酯通常是由二元酸和二元醇经酯化和缩聚反应而制得的一种高分子缩聚物。
目前用途最广的聚酯是由对苯二甲酸和乙二醇经酯化和缩聚反应所生成的聚对苯二甲酸乙二醇酯。
生产聚酯的工艺技术主要取决于精对苯二甲酸、对苯二甲酸二甲酯及乙二醇的生产发展。
用于合成聚对苯二甲酸乙二醇酯中间体的主要原料路线有以下几种:一种是酯交换法(简称DMT法);另一种是直接酯化法(简称PTA法);第三种是环氧乙烷酯化缩聚路线(简称环氧乙烷法)。
酯交换法(DMT法):是将以对苯二甲酸与甲醇反应生成易于精制提纯的对苯二甲酸二甲酯,或采用对二甲苯合并氧化、酯化制成对苯二甲酸二甲酯,再将提纯的对苯二甲酸二甲酯与乙二醇进行酯交换反应制得聚酯。
该方法在聚酯工业化的初期,未找到有效提纯对二甲苯的方法的时候得以广泛应用。
直接酯化法(PTA法):是以精对苯二甲酸与乙二醇为原料,进行直接酯化连续缩聚的反应制得聚酯。
到90年代初期,PTA法的产量已经超过了DMT法,成为聚酯工业的主流生产工艺。
环氧乙烷法因为使用环氧乙烷代替乙二醇(EG),可省去环氧乙烷水解工序,合成反应生成物为单一的对苯二甲酸双卢—羟乙酯(BHET),不需要回收设备,工艺流程短,成本低,所以是较有前途的生产方法。
聚酯装置生产过程危险性分析
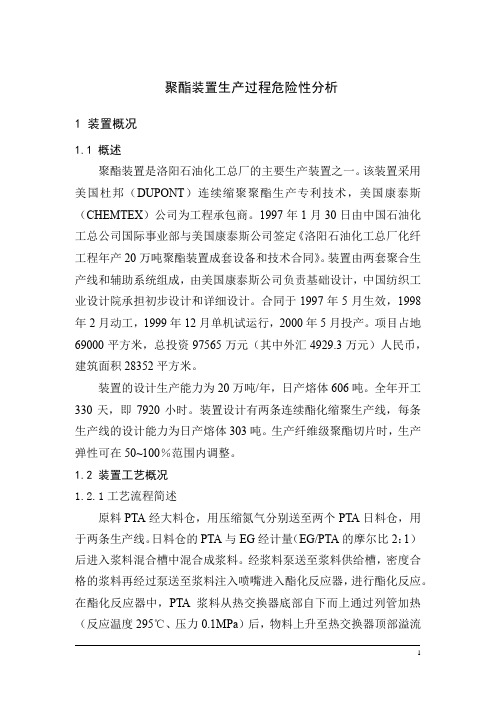
聚酯装置生产过程危险性分析1 装置概况1.1 概述聚酯装置是洛阳石油化工总厂的主要生产装置之一。
该装置采用美国杜邦(DUPONT)连续缩聚聚酯生产专利技术,美国康泰斯(CHEMTEX)公司为工程承包商。
1997年1月30日由中国石油化工总公司国际事业部与美国康泰斯公司签定《洛阳石油化工总厂化纤工程年产20万吨聚酯装置成套设备和技术合同》。
装置由两套聚合生产线和辅助系统组成,由美国康泰斯公司负责基础设计,中国纺织工业设计院承担初步设计和详细设计。
合同于1997年5月生效,1998年2月动工,1999年12月单机试运行,2000年5月投产。
项目占地69000平方米,总投资97565万元(其中外汇4929.3万元)人民币,建筑面积28352平方米。
装置的设计生产能力为20万吨/年,日产熔体606吨。
全年开工330天,即7920小时。
装置设计有两条连续酯化缩聚生产线,每条生产线的设计能力为日产熔体303吨。
生产纤维级聚酯切片时,生产弹性可在50~100%范围内调整。
1.2 装置工艺概况1.2.1工艺流程简述原料PTA经大料仓,用压缩氮气分别送至两个PTA日料仓,用于两条生产线。
日料仓的PTA与EG经计量(EG/PTA的摩尔比2:1)后进入浆料混合槽中混合成浆料。
经浆料泵送至浆料供给槽,密度合格的浆料再经过泵送至浆料注入喷嘴进入酯化反应器,进行酯化反应。
在酯化反应器中,PTA浆料从热交换器底部自下而上通过列管加热(反应温度295℃、压力0.1MPa)后,物料上升至热交换器顶部溢流至蒸汽分离器,完成酯化反应。
总反应时间90分钟,酯化率92%。
蒸汽分离器中的液态酯化料在热虹吸作用下进行循环,一部分齐聚物经齿轮泵、冷却器,温度降至275℃左右送至预缩聚釜反应。
循环抽出比为100:1。
在送往预缩聚釜的齐聚物管线上,催化剂、稳定剂等通过装在管线上的喷嘴进入齐聚物中。
酯化料在进入预缩聚釜前,需加入一定量的EG作为动力气。
聚酯三釜流程模型开发及应用

聚酯三釜流程模型开发及应用下载温馨提示:该文档是我店铺精心编制而成,希望大家下载以后,能够帮助大家解决实际的问题。
文档下载后可定制随意修改,请根据实际需要进行相应的调整和使用,谢谢!并且,本店铺为大家提供各种各样类型的实用资料,如教育随笔、日记赏析、句子摘抄、古诗大全、经典美文、话题作文、工作总结、词语解析、文案摘录、其他资料等等,如想了解不同资料格式和写法,敬请关注!Download tips: This document is carefully compiled by theeditor. I hope that after you download them,they can help yousolve practical problems. The document can be customized andmodified after downloading,please adjust and use it according toactual needs, thank you!In addition, our shop provides you with various types ofpractical materials,such as educational essays, diaryappreciation,sentence excerpts,ancient poems,classic articles,topic composition,work summary,word parsing,copy excerpts,other materials and so on,want to know different data formats andwriting methods,please pay attention!聚酯三釜流程是一种常见的聚酯生产工艺流程,包括酯化釜、预缩聚釜和终缩聚釜三个主要反应釜。
新型70m 3PVC聚合釜釜顶冷凝器的研制与应用

e r nd r ii g pr uc i iy,t a i n ta ut twa :6 ne gy a a sn od tv t her to ofi pu nd o pu s1 0,a h ai n uta d nd t e r to ofi p n
传 热配置 合理 , 树脂 产量 、 质量 稳定 。随着 化工 生产
公司、 山西 榆社 化工 股份有 限公 司 、 内蒙古 亿利 化学
高 达 1: 。 5
[ 中图 分 类 号 ]TQ 2 . ; Q0 16 3 5 3 T 5.
[ 献 标 志 码 ]B 文
[ 章 编 号 ]10 —7 3 (0 00 0 3 —0 文 0 9 9 72 1 )6— 0 9 4
De e o m e n p i a i n o e t p f o e h a o d n e o 0 m s PVC o y e i e s v lp nta d a plc to f a n w y e o v r e d c n e s r f r 7 p l m rz r
一
上提 高其 整体 技术水 平 、 产能 力和产 品质 量 , 为 生 成
P C行 业 迫 切 需 要 突 破 的 问 题 。 目前 , 国 P V 我 VC 生产 装置仍 然 以 7 0m。P C 聚合 釜为 主 流设 备 , V 其
产 能 占所 有 聚 合 釜 生 产 总 量 的 6 % 以上 。 0
次试 车成 功 。该 技术 经 消化 吸收在 国 内得 到 了大
范 围 的推广 , 极大 地推 动 了国 内 P C 产业 的快速 发 V
展, 随后 四川 省金路 树脂 有 限公 司 、 四川 永祥股 份有
限公 司、 顶 山神 马氯碱 化工 有 限责任公 司 、 平 江苏梅 兰 化工集 团有 限公 司 、 江 巨化 股 份有 限公 司 电化 浙 厂 、 疆 中泰 化学股 份有 限公 司 、 新 新疆 天业 集 团有 限
最新国产三釜聚酯装置介绍

最新国产三釜聚酯装置介绍咨询电话:(0086)571 82718253 转 773【作者:未知】【发布时间:2006/10/24 14:36:32】【字体:大中小】【关闭】该技术为中国聚酯技术的一个重大进步,作为聚酯技术的管理人员有必要向各位同行介绍一下,加强一下各位朋友对聚酯发展的新动向的了解。
新三釜聚酯装置是中国纺织机械(集团)有限公司(CTMC)北京英诺威逊聚合技术有限公司自主开发的拥有完整知识产权的新技术。
该装置包含新型双区酯化釜、新型多层预缩聚釜和原创性栅缝降膜终缩聚塔各一台,三者均不设机械搅拌。
双区酯化釜和多层预缩聚釜已成功用于宜兴市明阳化纤厂470吨/日聚酯工程。
栅缝降膜终缩聚塔中试结果令人耳目一新,不仅聚合速度显著高于传统的卧式圆盘或鼠笼搅拌釜,还能直接生产圆盘或鼠笼釜无法得到的高粘聚酯产品,取消SSP。
目前已有数家世界著名聚酯生产企业希望北京英诺威逊聚合技术有限公司向其授权或与其合作完成栅缝降膜塔直接生产高粘聚酯技术商品化。
新型双区酯化釜理想型酯化反应器优化设计原则:◇酯化前期物料全混型流动,用酯化物溶解PTA粉末,避免非均相反应麻烦;酯化后期保持平推流动,提高酯化反应速度;◇强化传热,以合理的方式满足酯化巨大的热量需求;◇简化结构,降低建设投资和运行成本。
酯化反应器现状:目前,国内外酯化反应器主要有两类:Zimmer和Inventa配置两台搅拌釜串联,第二酯化釜采用内外室或多层结构向平推流靠近。
这种配置酯化率可达97%,能满足工艺要求,但占用空间大,制造维修运行成本较高。
DuPont采用单台自然循环酯化釜,无机械搅拌,结构简单,维修及运行成本较低。
该釜为外置循环,占用空间较大。
浆料注入外循环管后和回流的酯化物混合升温,浆料中水份和部分EG迅速蒸发,两相混合流体从下封头进入列管换热器。
与浮力相比,气泡水平运动的推动力十分微弱,较多气泡垂直上升进入进料管口上方区域列管,其余列管气泡含量较低,部分含气泡较少的列管内物料密度较高,可能向下倒流,影响传热和酯化速率。
48m~3聚合釜生产SG-3型PVC树脂的研究

( uzo n o g h mi l o Ld, no g 5 4 1 hn ) G i uJ h n e c . t. ln 2 0 , ia h i C aC , A 5 C
Ab ta t o i ee t ip ra t e es de ,n eie l ip ra t sslce .h e t omuao sr c :S medf r n s es n r t ida dt a s e sn ee tdT eb s fr l f f d w u h d d wa
第 3期
21 0 2年 3 月
中 国 氯碱
Chi l r na Ch o —Al a i kl
No3 . Ma . 01 r, 2 2 1 9
4 聚合釜生产 S 3型 P C树脂的研 究 8m3 G一 V
徐 祖 华
( 州金 宏化 工有 限责任公 司 , 州 安龙 5 2 0 ) 贵 贵 5 4 1
表 1 分 散 剂 最佳 用量 的 试 验 结 果
PA V 3的试 验结 果见 表 4 。
表 4 P 3 试 验 结 果 VA 的
批 号 粘 数/mL・- ( g ) 杂 质粒 子数 / 个
挥 发 物 含 量/ %
标 准 ( 级 )9 批 9 批 9 批 10 优 7 8 9 0 批 15 1 7 3 ~ 2 ≤1 6
散 剂 的最佳用 量 。P A1的试验 结果见 表 2 V 。
表 2 P A1 V 的试 验结 果
3 简单工艺流程
将 定 量 的水 、 散 剂 、 H 调节 剂 、 分 p 引发 剂 加 入 聚 合 釜 , 压 、 真 空 合 格 后 启 动 单 体 泵 , 入 定 试 抽 加 量 的单体 。 冷搅 2 ~ 0m n 恒温 (20 05 o , 应 0 3 i, 5 . .) 【 反 - + =
新型多功能三元共聚PETG.PCTG聚酯制备方法

功能性.半连续合成聚合PETG/PCTG聚酯整套制备方法PETG/PCTG聚酯制备:生态多功能三元共聚PETG聚酯半连续酯化、连续聚合成PETG/PCTG聚酯整套设备:我公司主要从事聚酯技术转让和工程服务、是国内第一家生态多功能三元共聚PETG聚酯,半连续酯化、连续聚合成PETG/PCTG聚酯整套设备工程公司!生态多功能三元共聚PETG/PCTG聚酯整套设备从系统设计和制造及安装,积累了丰富的经验。
现可为用户提供设计、制造、安装、仪表自动化、调试、操作人员的技术培训等一条龙服务。
PETG/PCTG产品简介:是一种非结晶型共聚聚酯材料、是由二元醇(乙二醇,EG)与二元酸(对苯二甲酸,TPA)缩聚而成线型的一种高透明度的共聚聚酯塑料原料。
具有接近玻璃的密度、良好的韧性和耐冲击强度、优异的低温韧性、高抗撕性及良好的加工性能、优异的耐化学腐蚀性能。
可采取传统的挤出、注塑、吹塑及吸塑等成型方法进行加工、具有优异的透明度、光泽度、良好的韧性、加工性和优异的着色性。
广泛应用于:高性能收缩膜、化妆品包装容器、药品包装及医疗透明配件、牙刷及个人护理品、笔及文具、家电及小家电的透明件、玩具、日用品、灯饰、吹瓶、透明管材及异型材、薄膜、包装、片材、板材等领域!”PETG/PCTG聚酯全套制备组成:PETG/PCTG聚酯整套设备由打桨釜、酯化釜、聚合釜、竖式分馏柱、竖式冷凝器、卧式冷凝器、贮收器、真空泵、加热器、制带机、切粒机、卧式冷凝水糟、仪表、温度、电器控制拒等组成、全套设备与物料接触部分采用316L不锈钢制作!一、双酸一醇共聚改性PET-A及其单向热收缩膜制备工艺:一种双酸一醇共聚改性PET-A的制备方法是以精对苯二甲酸(PTA)、间苯二甲酸(IPA)和乙二醇(MEG)为主要原料进行三元共聚改性制得PET-A聚酯,其单向热收缩膜制备工艺包括纵向和横向两种制备工艺,所得热收缩膜的各项性能相同。
原材料易得、制备工艺简单环保、产品透明度高,应用广泛,单向热收缩膜的制备工艺专用于食品包装热收缩薄膜材料,产品经纵向或横向拉伸后的成品透明度良好,热收缩率在95~130℃、2~3s内达45~80%,可替代有毒PVC热收缩食品包装袋及其他系列的热收缩包装材料。
聚酯装置流程与聚酯生产概述
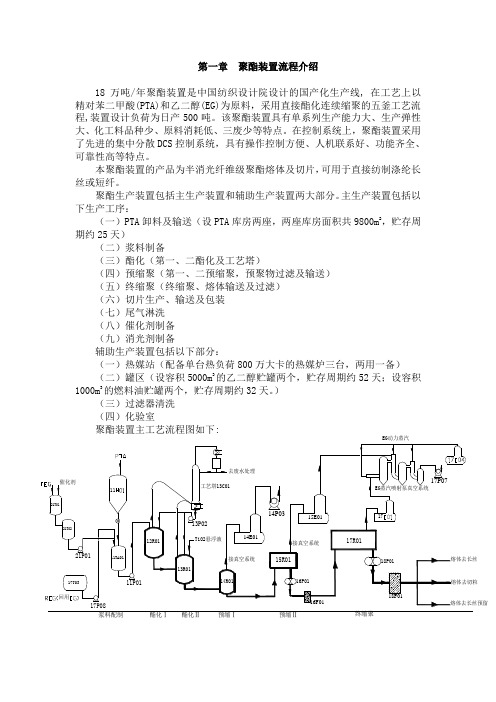
第一章 聚酯装置流程介绍 18万吨/年聚酯装置是中国纺织设计院设计的国产化生产线, 在工艺上以精对苯二甲酸(PTA)和乙二醇(EG)为原料,采用直接酯化连续缩聚的五釜工艺流程,装置设计负荷为日产500吨。
该聚酯装置具有单系列生产能力大、生产弹性大、化工料品种少、原料消耗低、三废少等特点。
在控制系统上,聚酯装置采用了先进的集中分散DCS 控制系统,具有操作控制方便、人机联系好、功能齐全、可靠性高等特点。
本聚酯装置的产品为半消光纤维级聚酯熔体及切片,可用于直接纺制涤纶长丝或短纤。
聚酯生产装置包括主生产装置和辅助生产装置两大部分。
主生产装置包括以下生产工序: (一)PTA 卸料及输送(设PTA 库房两座,两座库房面积共9800m 2,贮存周期约25天) (二)浆料制备 (三)酯化(第一、二酯化及工艺塔) (四)预缩聚(第一、二预缩聚,预聚物过滤及输送) (五)终缩聚(终缩聚、熔体输送及过滤) (六)切片生产、输送及包装 (七)尾气淋洗 (八)催化剂制备 (九)消光剂制备 辅助生产装置包括以下部分: (一)热媒站(配备单台热负荷800万大卡的热媒炉三台,两用一备) (二)罐区(设容积5000m 3的乙二醇贮罐两个,贮存周期约52天;设容积1000m 3的燃料油贮罐两个,贮存周期约32天。
) (三)过滤器清洗 (四)化验室 聚酯装置主工艺流程图如下:终缩聚预缩Ⅱ预缩Ⅰ酯化Ⅱ酯化Ⅰ浆料配制EG动力蒸汽外购原料PTA通过叉车将PTA贮存于PTA仓库,人工将PTA投入链板输送前的小料仓后,用链板输送方式将PTA送到聚酯大楼的日料仓。
另一主要原料乙二醇贮存在罐区,用泵通过管线送入车间。
催化剂三醋酸锑(或乙二醇锑)用桶装、消光剂二氧化钛用袋装运入聚酯大楼四楼。
聚酯装置主要由催化剂配制、二氧化钛配制、浆料配制、酯化、缩聚、切片生产及包装等几个工序组成。
酯化缩聚设置了五个反应器,其中两个是酯化反应器,两个是预缩聚反应器,一个后缩聚反应器。
国产70m 3聚合釜PVC树脂质量的优化控制
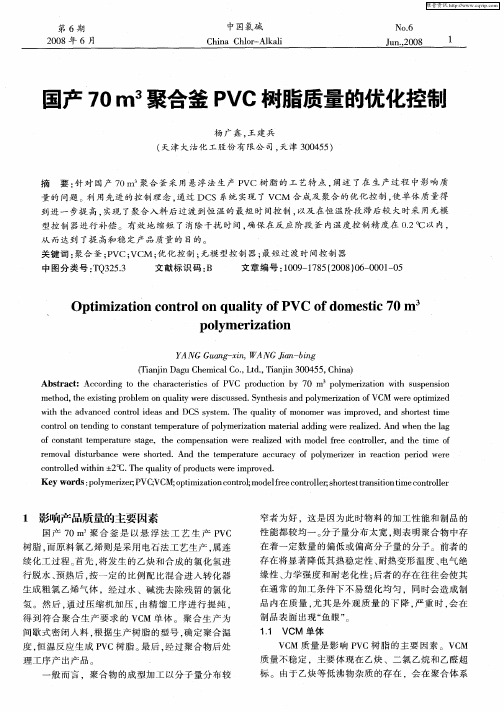
(i j auC e iaC .Ld, ini 04 5C ia Ta i D g hmcl o,t. aj 30 5, hn) nn T n
Ab t a t sr c :Ac o d n o t e c a a t r t s o VC p o u t n b 0 m。p l me z t n wi u p n in c r i g t h h r ce si f P r d ci y 7 i c o o y r a i t s s e so i o h
1 影响产 品质量 的主要 因素
国 产 7 聚合 釜 是 以悬 浮 法 工 艺 生 产 P C 0m V 树脂 , 而原 料氯 乙烯 则是 采用 电石 法工 艺生 产 , 连 属 续 化工 过程 。 先 , 发生 的乙炔 和合成 的氯 化氢 进 首 将 行 脱水 、 预热 后 , 按一 定 的 比例 配 比混合 进入 转化 器
me h d t e e itn r b e o ai we e d s us e S n h ssa d p l me z to fVCM r p i z d t o , h x si gp o lm n qu l ̄ r ic s d. y t e i n o y r a in o i we e o tmie wih t e a v nc d c n r li e sa d DCS s se t h d a e o to d a n y t m.Th uaiy o n me s i r v d n h re ttme e q lt fmo o rwa mp o e ,a d s o t s i c n r lo e di gt o sa tt mp r t r fp l o to nt n n o c n t n e e a u eo oyme z to t ra d n r e l e An i r a in mae la di g we e r ai d. d whe hel g i z n t a o o t n e fc nsa tt mpe a u e sa e t e c mpe ai n we e r aie t de r e c n r le ,a d t e tme o r t r tg , h o ns to r e lz d wih mo lfe o tol r n h i f r mo a it ba c r h re e v l d sur n e we e s o d.An h e t d t e t mpe aur a c r c f p lme ie n r a to ro r r t e c u a y o o y rz r i e ci n pe d we e i
聚酯多元醇反应釜-概述说明以及解释

聚酯多元醇反应釜-概述说明以及解释1.引言1.1 概述:聚酯多元醇反应釜是在聚酯多元醇生产中起着关键作用的设备。
通过化学反应将原料中的多元醇和酸酐等物质在反应釜内进行反应,从而合成聚酯多元醇。
反应釜的设计和运行对于产品质量和生产效率有着重要影响。
在本文中,我们将详细探讨聚酯多元醇反应釜的基本原理、结构和工作原理,以及其在生产中的应用。
通过深入了解反应釜的功能和特点,我们可以更好地理解其在聚酯多元醇生产中的重要性,同时也可以展望未来反应釜的发展趋势,为生产提供更好的技术支持和指导。
1.2 文章结构:本文主要分为三个部分:引言、正文和结论。
引言部分将介绍聚酯多元醇反应釜的背景和意义,以及本文的研究目的。
通过对该主题的概述,读者可以更好地了解聚酯多元醇反应釜在化工生产中的重要性。
正文部分将详细介绍聚酯多元醇反应釜的基本原理、结构和工作原理,以及在聚酯多元醇生产中的应用。
读者将通过这一部分了解到反应釜在生产过程中的具体作用和重要性。
结论部分将对本文进行总结,强调聚酯多元醇反应釜的重要性,并展望未来反应釜的发展方向。
最后,给出结论,为读者提供更全面的认识和思考。
1.3 目的:本文的目的是探讨聚酯多元醇反应釜在化工生产中的重要性和应用。
通过了解聚酯多元醇反应釜的基本原理、结构和工作原理,以及在生产过程中的应用,可以更好地理解和掌握这一关键设备在生产过程中的作用。
同时,通过总结反应釜的重要性和展望未来发展方向,可以为行业提供一定的参考和思路,促进反应釜技术的进步和发展。
通过本文的研究,旨在为聚酯多元醇反应釜的使用和优化提供理论支持和实践指导,促进化工生产的高效、安全和可持续发展。
2.正文2.1 聚酯多元醇反应釜的基本原理聚酯多元醇反应釜是一种用于生产聚酯多元醇的设备,其基本原理是通过一系列的化学反应将原料混合在一起并在特定的温度和压力下进行反应,最终得到所需的聚酯多元醇产品。
在反应釜中,一般会添加聚酯原料、催化剂和其他助剂,然后加热反应釜使其达到适当的温度,促使反应发生。
国产70m 3聚合釜生产装置的安全保证

No 3 .
Ma.2 0 r ,0 6
P lvnl hoie o聚iy 烯 y 氯 乙l d C r
.
第 3期
2O O 6年 3月
【 装置与设备 】
国产 7 0m3聚合 釜 生产 装 置 的安全 保 证
顾正明 , 惠正纲 ( 无锡格林艾普化工股份有限公司, 江苏 无锡 2 44 ) 10 1
i r vn n e lci r r f n rd c d. mp o i a dp re tn a eb e y ito u e g g il
近几年 , 随着 国 民经济 的高速增长 , V P C树 脂 的需求也迅猛增加。20 年 4 , 01 月 无锡格林艾普化 工股份有限公司( 简称格林艾普公司) 国内首家采 在
内将形成 2 0 8 万~30万 a V 5 c的生产能力…。 P
随着 P VC树脂生产规模的逐步扩大 , 关键设备 聚合釜的 日 趋大型化 , P C树脂的安全生产和环 对 V 用 国产 7 聚合釜装置生产悬浮法 P C树脂 , O m3 V 并 境保护提 出了更高的要求。结合格林艾普公司生产 获得成功。江苏江东化工股份有 限公 司、 四川金路 实际情况 , 就格林艾普公司 P C聚合装置安全设施 V
国产 7 3 0m 聚合釜生产装置具有工艺较成熟 、
这不仅因为单釜容积大 、 投料单体多 , 发生意外事故
时损失大 , 而且 在事故发生时处理更为 困难 ( 3 与 O
可靠性高 、 稳定性好 、 投资费用少 、 经济效益好等优
势, 结合先进 的 D二 ( s控制 , 极大地 降低 了操作Байду номын сангаас员 的劳动强度 , 是近几年 国内 P C行业发展的主流装 V
浅析国产70m 3聚合釜PVC生产的自动控制

图 2 聚合釜循环冷却 工艺
循 环 E水
以笔者应用为例 , 国产 7 0m 聚合釜 P C生产 V
过程 控制采 用美 国 H ny e 公 司的 P S 1 oe l w l K 2 0系统 , 其结 构如图 3所示 。 C0 20控制器 实现所 要求 的程 序控 制和 连续 调 节, 通过 系统所提供 的 C n o Mou 组 态实现 IO ot l d l r e / 回路 的显示 和控 制 ;eu neC n o M dl 组态 实 Sqe c ot l oue r
此种工艺水 和单体 、 助剂等共 同密 闭加入 釜 内, 入釜水温 随着 釜 内温 度 、 单体 等 加入 量不 断 变化 。
冷热混合纯水一般控制在 8 0~10℃。等温入料过 0
程 中聚合釜入料的几个单元操作 同时进行 。因此对 设备 、 表 、 制等 的配合 要 求高 。其 工 艺 流程 如 仪 控
第4 期
杨广鑫等 . 浅析 国产 7 0m 聚合釜 P C生产 的 自动控制 V
・ 7・ 7
作 的画面显示整 个生产 过程状 况 ; 时具 有 报警记 同 录、 报表 、 历史趋势数据和打 印功能等 。
论是常规仪表 还是 计算 机控 制 , 本 采用 串级 调节 基
思想 , 其效果 在 当时较 人工 操作 理想 。随着 科 技发
级调节 , 内冷管利用单参数控制 。
等温入料工艺人釜水分别用热纯水和冷纯水进
循
行勾兑 , 勾兑 比例根据 聚合釜反应温度 、 单体加入 量 和单体温度 、 助剂量和助剂温度 、 夹套水温等计算得
出。在入料过程 中先加 一定 量的冷热 混合纯 水 , 同 时启动加入单体 , 然后加入各种助剂 , 最后按时 间进 行水 冲洗 管路 。此时聚合 釜 内温度达到或接近反应 温度 。如果 釜 内温度 未达 到反应 温度 , 则采 用蒸 汽 夹套 升温使 釜 内温度 达 到反 应 温度 , 内压力 达到 釜
三釜凝聚改造让合成胶全面降耗

在合成橡胶生产过程 中,凝聚环节所消耗的
能量 占总能耗的6 % o 。近年来 ,国外开始采用先 进装备技术来回收这一环节所消耗的大量能源, 但对该技术封锁严密。国内合成橡胶生产 中的凝 聚环节 亟待破解 节能 降耗难 题 。 巴陵石化是 目前国内最大的热塑性橡胶生产 企业,同时还有一套年产3 万吨的顺丁橡胶生产 装置,企业共有9 条凝聚 ( 工序 )生产线。近年
种 。其 中耐酸防腐 、耐碱 防腐 、耐油防腐 类涂 膜,高强真空粘接剂、硅橡胶粘接剂 、无机高温 粘接剂等产品填补了很多建筑 、机械 、化工、石
油 、造船行业领域防水与粘合材料的空白。
( 胶9 网> 橡 1
硅橡 胶防水材料受 市场青 睐
从事军转 民技术产品研究的天津航天环宇科 技发展有限公司,今年以来通过技术推广服务 、 强化产品宣传、加大高科技含量产 品研发力度等
新型橡胶除臭剂破解环保难题
在前不久召开的全国第六届橡胶环保型助剂 生产和应用技术研讨会上,河北任县泰斗合成材 料厂带来的橡胶污染治理新技术赢得 了来 自全国
来,巴陵石化集中力量在凝聚工艺优化方面进行 攻关,将其列为节能重点技改项 目。科研人员通
过借鉴合成橡胶其他产品的凝聚生产技术, 自 行 开 发设计 出顺丁橡 胶三 釜凝 聚新 技术 。 2 0年初,合成橡胶事业部启动顺丁装置凝 08 聚 工艺 改造 项 目, 5 初 一 次开 车 成 功 ,这 是该 月 技术在全球 同类装置上的首次应用。应用实践表 明,在 同等条件下,每吨顺丁橡胶生产 的蒸汽单
均属于无毒、无味材料,不会对人和环境产生污
染。
为使这一 优越性 能的材料发挥社会效益,
环宇公司积极组织召开了设计人员 、 施工企业 、 开发建设单位参加的技术推广 、性能论证会,为
聚酯装置说明、危险因素以及防范措施(最新版)
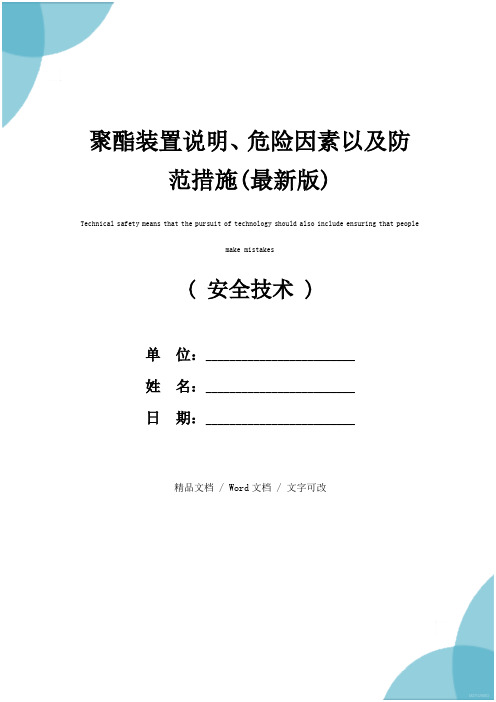
( 安全技术 )单位:_________________________姓名:_________________________日期:_________________________精品文档 / Word文档 / 文字可改聚酯装置说明、危险因素以及防范措施(最新版)Technical safety means that the pursuit of technology should also include ensuring that peoplemake mistakes聚酯装置说明、危险因素以及防范措施(最新版)一、装置简介(一)装置发展及类型1.装置发展聚酯工艺产生于20世纪40年代,在50年代实现了工业化,是利用基础化工原料生产合成纤维的工艺技术。
20世纪70年代以后,各国针对聚酯存在的吸水率低、不易染色、易产生静电等缺点进行了改性研究,取得了较多成果,使聚酯工业有了飞速的发展。
70年代末,我国从前西德引进了第一套直接酯化连续缩聚生产涤纶树脂的工业化生产装置。
经过几十年的发展,聚酯在我国三大合成纤维工业中已占有举足轻重的地位。
截止到2003年底,我国聚酯装置的产能已经达到1115×104t/a,占世界总产量的三分之一左右。
进入21世纪,随着工艺技术的不断发展,我国聚酯装置正向工艺技术更先进、经济效益更好的方向发展。
2.生产工艺路线聚酯通常是由二元酸和二元醇经酯化和缩聚反应而制得的一种高分子缩聚物。
目前用途最广的聚酯是由对苯二甲酸和乙二醇经酯化和缩聚反应所生成的聚对苯二甲酸乙二醇酯。
生产聚酯的工艺技术主要取决于精对苯二甲酸、对苯二甲酸二甲酯及乙二醇的生产发展。
用于合成聚对苯二甲酸乙二醇酯中间体的主要原料路线有以下几种:一种是酯交换法(简称DMT法);另一种是直接酯化法(简称PTA 法);第三种是环氧乙烷酯化缩聚路线(简称环氧乙烷法)。
酯交换法(DMT法):是将以对苯二甲酸与甲醇反应生成易于精制提纯的对苯二甲酸二甲酯,或采用对二甲苯合并氧化、酯化制成对苯二甲酸二甲酯,再将提纯的对苯二甲酸二甲酯与乙二醇进行酯交换反应制得聚酯。
国产70.4m 3聚合釜的研制

厂 一 道 ,对 7 . m 聚 合 釜 釜 体 结 构 对 传 热 性 能 的 04 3
影 响 、釜用 三 叶后 掠 式搅 拌 器 的设 计 开发 与利 用 等 方 面进 行 了研 究 ,力 争 为我 国在 国产 聚合 釜 研 制 带
2 聚合 釜 的结构 特 点
2 1 聚合 釜 的技 术参 数 .
见 表 l 。
表 1 聚 合 釜 技 术 特 性 釜 体
全容积/ 3 m
70. 4
夹 套
我 国聚 氯 乙烯 生产 工艺 主要 以悬 浮 法 为 主 , 占 整个 聚氯 乙 烯 产 量 的 3 %。 目前 ,国 内 以 悬 浮 法 5
我公 司 4万 taP C装 置 是 在 “ 五 ” 期 间 引 / V 七 进美 国 B. . odi F G o r h公 司先 进 的聚 合 生产 技 术 ,同 c 时购 买 与 之 相 匹 配 的 进 口 设 备 ,采 用 悬 浮 法 生 产 P C的具 有 8 代末 期 世 界先 进 水 平 的进 口装 置 , V 0年 其核 心 设 备 是 两 台规 格 为 7 .m 聚 合 釜 ,釜 上 装 04 3
及 生 产能 力 都较 小 ,主要 原 因是 在 此 之 前 , 国内化
主 体 材 料 焊 缝 系 数
1M R+S S0 1M R 1/ 25 6n U3 4 6 n / 0 Q 3 一A
10 . l 60 0. 5 8
电 机 功 率 / W k
传 动 方 式
工 设 备制 造行 业 还没 有 能力 生产 大 型 聚合 釜 及 相关 配 套 设备 ,在 进 口装 置 中则 主要 以 7 .m 、15
聚酯化合成反应釜

聚酯化合成反应釜简介
聚酯化合成反应釜是一种用于聚酯化合成反应的设备,通常由不锈钢制成,具有耐高压、耐腐蚀、耐高温等特性。
聚酯化合成反应釜广泛应用于化工、制药、食品等行业中,用于生产聚酯树脂、聚酯纤维、聚酯薄膜等产品。
聚酯化合成反应釜通常包括反应釜体、搅拌装置、加热装置、冷却装置、压力表、安全阀等部件。
在反应过程中,反应釜内的原料经过加热、搅拌和冷却等处理,最终生成聚酯产品。
聚酯化合成反应釜的操作需要严格遵守安全规定,避免发生意外事故。
在操作前需要对设备进行检查,确保设备完好无损,并对反应釜内的原料和催化剂进行检查,以确保其符合生产要求。
同时,需要对反应釜进行加热和冷却控制,以保证反应过程的稳定性和反应产物的质量。
- 1、下载文档前请自行甄别文档内容的完整性,平台不提供额外的编辑、内容补充、找答案等附加服务。
- 2、"仅部分预览"的文档,不可在线预览部分如存在完整性等问题,可反馈申请退款(可完整预览的文档不适用该条件!)。
- 3、如文档侵犯您的权益,请联系客服反馈,我们会尽快为您处理(人工客服工作时间:9:00-18:30)。
最新国产三釜聚酯装置介绍咨询电话:(0086)571 82718253 转 773【作者:未知】【发布时间:2006/10/24 14:36:32】【字体:大中小】【关闭】该技术为中国聚酯技术的一个重大进步,作为聚酯技术的管理人员有必要向各位同行介绍一下,加强一下各位朋友对聚酯发展的新动向的了解。
新三釜聚酯装置是中国纺织机械(集团)有限公司(CTMC)北京英诺威逊聚合技术有限公司自主开发的拥有完整知识产权的新技术。
该装置包含新型双区酯化釜、新型多层预缩聚釜和原创性栅缝降膜终缩聚塔各一台,三者均不设机械搅拌。
双区酯化釜和多层预缩聚釜已成功用于宜兴市明阳化纤厂470吨/日聚酯工程。
栅缝降膜终缩聚塔中试结果令人耳目一新,不仅聚合速度显著高于传统的卧式圆盘或鼠笼搅拌釜,还能直接生产圆盘或鼠笼釜无法得到的高粘聚酯产品,取消SSP。
目前已有数家世界著名聚酯生产企业希望北京英诺威逊聚合技术有限公司向其授权或与其合作完成栅缝降膜塔直接生产高粘聚酯技术商品化。
新型双区酯化釜理想型酯化反应器优化设计原则:◇酯化前期物料全混型流动,用酯化物溶解PTA粉末,避免非均相反应麻烦;酯化后期保持平推流动,提高酯化反应速度;◇强化传热,以合理的方式满足酯化巨大的热量需求;◇简化结构,降低建设投资和运行成本。
酯化反应器现状:目前,国内外酯化反应器主要有两类:Zimmer和Inventa配置两台搅拌釜串联,第二酯化釜采用内外室或多层结构向平推流靠近。
这种配置酯化率可达97%,能满足工艺要求,但占用空间大,制造维修运行成本较高。
DuPont采用单台自然循环酯化釜,无机械搅拌,结构简单,维修及运行成本较低。
该釜为外置循环,占用空间较大。
浆料注入外循环管后和回流的酯化物混合升温,浆料中水份和部分EG迅速蒸发,两相混合流体从下封头进入列管换热器。
与浮力相比,气泡水平运动的推动力十分微弱,较多气泡垂直上升进入进料管口上方区域列管,其余列管气泡含量较低,部分含气泡较少的列管内物料密度较高,可能向下倒流,影响传热和酯化速率。
DuPont单釜酯化率不足94%,必须与其特有的上流式预缩聚反应器(UFPP)配套,在UFPP中加入大量EG继续提高酯化率。
新型双区酯化釜简介:遵循理想型酯化反应器优化设计原则并针对现行酯化反应器缺陷,北京英诺威逊聚合技术有限公司发明了新型双区酯化釜。
该釜由釜体、列管换热器、釜内区域分隔板及各区域内构件组成,其结构及釜内物料和蒸汽流动途径示意见图1。
图中“←”为液相流;“<——”为气相流;“<====”为气、液混合流;釜体含上封头1、外筒2、下封头3和夹套4。
列管换热器含壳体5,环形上管板6,环形下管板7,多根换热列管8,内筒9,带直立段的底部小封头10和小封头中的内管11及置于小封头和内管间的环状静态混合器12以及未标代号的连接法兰、壳程挡板、拉杆等通用构件;为提供静态混合器12的安装位置,底部小封头10通常带直立段。
区域分隔板包括圆筒隔板13和圆台隔板14;上封头1、外筒2上段、圆台隔板14、圆筒隔板13、换热器壳体5及底部小封头10围成第一酯化区;外筒2下段、下封头3、圆筒隔板13和圆台隔板14围成第二酯化区。
第一酯化区内构件包括导流内管15、导流圆台16、导流环状栅板17以及气相导流圈18和旋风分离器19。
第二酯化区内构件包含2圈导流环板20以及加热盘管21。
第一酯化区设以下工艺管口:小封头10下侧壁均布4个浆料进口a,半数运行,半数备用,运行口和备用口相间。
小封头10底部设第一酯化区酯化物出口b。
列管换热器壳体5设若干对热媒进口c和出口d。
上封头设蒸汽出口e。
第二酯化区设以下工艺介质管口:外筒2开酯化物进口f,下封头3和圆筒隔板13交接处设酯化产物出口g。
外筒2和圆台隔板14交接处设蒸汽出口h,下封头3和外筒2开与加热盘管21相连的若干对热媒进口j、出口k。
列管换热器设热媒进出口c、d,釜体夹套设热媒进出口l、m。
此外,新型双区酯化釜还须开设温度、压力、液位等仪表接口及人孔或其它必要的附加接口。
新型双区酯化釜工作过程:乙二醇(EG)和对苯二甲酸(TPA)摩尔比为1.6~1.8的浆料通过喷嘴从浆料进口a 进入第一酯化区小封头10和内管11间环状空间下部,和从小封头内管11循环回流的酯化物汇合升温,浆料中水份和部分EG迅速蒸发,两相混合流经静态混合器12使气泡均布,由换热器环形下管板7进入诸换热列管8,在列管中被壳程热媒加热升温进行酯化,反应生成的水及浆料中过量的EG蒸发,气液混合物穿过环形上管板6,沿以圆筒隔板13、圆台隔板14和外筒2为外缘,以导流内管15、导流圆台16、导流环状栅板17为内缘的通道继续上升至第一酯化区上部,液体穿过导流环状栅板栅缝从周边向中央汇聚,气体冲出液面后被气相导流圈18改变流动方向朝下冲,靠惯性除去雾沫夹带,再经旋风分离器19进一步除去雾沫后从e 口离釜。
导流环状栅板17内侧脱除气体后的酯化物熔体密度高于外侧气液混合物密度,受密度差驱使沿导流环状栅板17、导流圆台16、导流内管15、换热器内筒9、小封头内管11组成的内侧通道向下循环回流。
绝大多数循环回流酯化物经小封头内管11和小封头10底部间环隙流向小封头内管11外侧,和通过a口送进的浆料混合,继续下一个循环。
少部分酯化物从b口流出第一酯化区,通过连接管道进入第二酯化区f口。
从f口进入的酯化物在第二酯化区从外向内顺序流过各圈导流环板20呈平推流动,从加热盘管21补充热量维持工艺设定温度,酯化产物从g口离釜。
物料在第二酯化区流动途径见图2。
第二酯化区产生的蒸汽从h口离釜。
第一酯化区温度260~270oC,压力0.15~0.20MPa,停留时间120~180分钟,酯化率91~92%;第二酯化区温度265~275 oC,压力0.11~0.12MPa,停留时间45~75分钟,酯化率96.5~97%。
新型双区酯化釜优点:显然,双区酯化釜完全满足理想型酯化反应器条件,与Zimmer或Inventa酯化技术比较,反应釜数少,无机械搅拌,制造维修及运行成本低,酯化后期更贴近平推流。
与DuPont酯化技术比较,浆料EG对PTA摩尔比降低,能耗低,酯化率达97%,不必在预缩聚过程补加EG,不仅节能,还可降低蒸汽中雾沫夹带。
双区酯化釜采用内置循环,比DuPont 的外置循环反应釜占据空间更小。
因小封头内静态混合器12改善了诸换热列管内气相分布均匀性,强化传热,加速酯化反应。
新型多层预缩聚釜理想型预缩聚反应器设计原则:◇物料呈平推流动◇温度渐升,压力渐降◇后期拥有较大气液界面◇减小气相中雾沫夹带◇结构简单,制造维修运行费用低预缩聚反应器现状:Zimmer及Inventa过去都采用两台反应器串联,近来倾向改用单台多层反应器。
据Zimmer介绍,采用单台预缩聚釜的四釜流程比原采用两台预缩聚釜串连的五釜流程设备投资省6.4%,工程设计省2.4%,安装省10.7%,建筑成本省40.0%,劳动力成本及维修保养费用省1.7%,公用工程消耗省2.3%,生产成本总体下降5.2%(1)。
无论Zimmer或Inventa,其多层预缩聚釜底部均设机械搅拌。
机械搅拌不仅使设备结构复杂,制造维修运行费用增加,而且与平推流原则相悖。
但如不设搅拌,底层物料会出现严重沟流及死区,设置搅拌乃不得已而为之。
DuPont采用单台上流式预缩聚反应釜(UFFP),釜数少,无机械搅拌,结构简单,投资省。
但釜内塔盘存在较多死区,必须依靠剧烈鼓泡来自洁,否则会严重结焦。
UFPP原本为酯交换路线设计。
EG和DMT进行酯交换反应后,物系中存留大量游离EG,酯交换生成物进入UFPP,所含游离EG恰好可用作鼓泡自洁,应属合理设计。
随着技术发展进步,直接酯化法取代酯交换法。
酯化齐聚物中游离EG极少,无法完成鼓泡自洁。
为避免结焦,只有向齐聚物中补加大量EG。
预缩聚工序本应及时移出反应生成的EG以促使平衡向右移动,釜内补加大量EG和反应原理冲突,而且会额外增加能耗,加剧蒸汽中雾沫夹带。
实际上,DuPont工艺中UFPP兼具第二酯化反应器功能,DuPont的酯化反应器和其预缩聚反应器配套属合理配置,但如将其分拆,用DuPont的酯化和其他形式的预缩聚或其他形式的酯化和DuPont的预缩聚配套,恐怕都不是很好的选择。
新型多层预缩聚釜简介:遵循理想型预缩聚反应器优化设计原则并针对Zimmer和Inventa底层设机械搅拌的多层反应器缺陷,北京英诺威逊聚合技术有限公司发明了无机械搅拌的新型多层预缩聚釜。
该釜包含釜体、釜内区域分隔板和各区域内构件,其结构及物料流向示意见图3。
釜体包含上封头1,外筒体2,下封头3和夹套4;下封头3通常做成锥形以利于物料流动。
区域分隔板包含2块环状隔板5.1、5.2和一根中央管6,它们将釜内空间分割成上、中、下3层反应区及一个中央蒸汽通道区。
上层反应区以上封头1为顶,上层环状隔板5.1为底;中层反应区以上层环状隔板5.1为顶,第二层环状隔板5.2为底,上层和中层反应区均以其顶和底之间的外筒体2和中央管6为本区域外壁和内壁。
底层反应区以下层环状隔板5.2为顶,以下封头3为底,以其顶和底之间的外筒体2下段为外壁。
各区域内构件包括:上层和中层反应区各自底部环状隔板5上设置的导流螺旋板7,其结构及物流方向见图4;导流螺旋板7之间设加热盘管9。
底层反应区上方设锥形伞板10,为将锥形伞板10固定在下封头3上,设3或4根立柱11;伞板锥顶设小挡圈12,小挡圈底部和伞板间有环状间隙;伞板边缘设若干导流针13;锥形伞板面上开设多个菱形或橄榄型孔并在其上方设折流通道14。
中央蒸汽通道区域的中央管6内设内管15,6和15组成一台旋风分离器。
新型多层预缩聚釜含以下工艺管口:第一第二层反应区设物料进口a,物料出口b。
进料管通常伸进釜内,物料从导流螺旋板的内端上方流入,从导流螺旋板外端最低处流出。
釜底层进料管伸进釜内从上方进入伞板锥顶档圈内,出料口b设在下封头底部。
第一第二层反应区均在中央管6管壁处开蒸汽入口c,c口设一导向管引导蒸汽从切线方向进入6和15的环隙,首层蒸汽入口c1设有阻尼阀K,上封头顶部设蒸汽出口d。
各层反应区开设若干对加热盘管热媒进口e,出口f。
釜体夹套设若干对热媒进口g,出口h。
此外,多层预缩聚釜还开设有温度、压力、液位等仪表接口以及人孔和其它必要的附加管口。
新型多层预缩聚釜工作过程如下:来自酯化釜的齐聚物用泵或靠位差喂入新预缩聚釜上层反应区物料进口a1,顺导流螺旋板流动,从物料出口b1流出,通过外部接管进入中层反应区物料进口a2,顺导流螺旋板流动,从物料出口b2流出,通过外部接管进入釜底反应区物料进口a3,流进伞板锥顶挡圈,穿过挡圈底部和伞板间环隙或越过挡圈顶溢流,均匀地沿伞板降膜,至伞板边缘处被导流针引向釜壁均匀降膜,在底层反应区由上向下、由四周向中央呈平推流流动,最后从下封头物料出口b3出釜。