PCB电镀线除油剂
PCB电镀工艺介绍

可编写可更正PCB电镀工艺介绍线路板的电镀工艺, 大体可以分类 : 酸性光明铜电镀、电镀镍/金、电镀锡,文章介绍的是关于在线路板加工过程是, 电镀工艺的技术以及工艺流程, 以及详尽操作方法.二.工艺流程:浸酸→全板电镀铜→图形转移→酸性除油→二级逆流漂洗→微蚀→二级逆流漂洗→浸酸→镀锡→二级逆流漂洗→逆流漂洗→浸酸→图形电镀铜→二级逆流漂洗→镀镍→二级水洗→浸柠檬酸→镀金→回收→2-3 级纯水洗→烘干三.流程说明:(一)浸酸①作用与目的:除去板面氧化物, 活化板面 , 一般浓度在5%,有的保持在10%左右 , 主若是防范水分带入造成槽液硫酸含量不牢固;②酸浸时间不宜太长, 防范板面氧化; 在使用一段时间后, 酸液出现浑浊或铜含量太高时应及时更换 , 防范污染电镀铜缸和板件表面;③此处应使用级硫酸;( 二 ) 全板电镀铜:又叫一次铜, 板电 ,Panel-plating①作用与目的:保护方才积聚的薄薄的化学铜, 防范化学铜氧化后被酸浸蚀掉, 经过电镀将其加后到必然程度② 全板电镀铜相关工艺参数:槽液主要成分有硫酸铜和硫酸, 采用高酸低铜配方 , 保证电镀时板面厚度分布的均匀性和对深孔小孔的深镀能力; 硫酸含量多在180 克/ 升 , 多者到达240 克 / 升 ; 硫酸铜含量一般在75 克 / 升左右 , 另槽液中增加有微量的氯离子, 作为辅助光彩剂和铜光剂共同发挥光彩收效; 铜光剂的增加量或开缸量一般在3-5ml/L,铜光剂的增加一般依照千安小时的方法来补充也许依照实质生产板收效; 全板电镀的电流计算一般按 2 安/平方分米乘以板上可电镀面积, 对全板电来说 , 以即板长 dm×板宽 dm×2×2A/DM2;铜缸温度保持在室温状态 , 一般温度不高出 32 度 , 多控制在22 度 , 因此在夏季因温度太高, 铜缸建议加装冷却温控系统 ;1③工艺保护:每日依照千安小时来及时补充铜光剂, 按 100-150ml/KAH 补充增加 ; 检查过滤泵可否工作正常 , 有无漏气现象 ; 每隔 2-3 小时应用干净的湿抹布将阴极导电杆擦洗干净; 每周要如期解析铜缸硫酸铜〔 1 次/周〕, 硫酸〔 1次/ 周〕 , 氯离子〔 2次 / 周〕含量 , 并经过霍尔槽试验来调整光剂含量 , 并及时补充相关原料; 每周要冲刷阳极导电杆 , 槽体两端电接头 , 及时补充钛篮中的阳极铜球, 用低电流 0。
电镀除油剂配方

电镀除油剂配方概述电镀除油剂是一种用于去除金属表面油污和杂质的化学溶液。
它在电镀工业中起着至关重要的作用,能够净化金属表面,提高电镀效果和质量。
本文将介绍电镀除油剂的配方、原理和应用。
配方以下是一种常见的电镀除油剂配方:•氢氧化钠:10-20g/L•碳酸氢钠:5-15g/L•磷酸二氢钾:1-5g/L•表面活性剂:0.5-2g/L这种配方可根据具体应用需求进行微调,以达到最佳效果。
原理电镀除油剂通过其成分中的碱性物质和表面活性剂发挥作用。
其主要原理如下:1.碱性物质(如氢氧化钠、碳酸氢钠)能与酸性物质(如油脂、脱脂剂)反应生成皂化物,将其溶解或乳化。
2.表面活性剂能够破坏液体表面的张力,使其更容易与油污接触并分散。
通过以上原理,电镀除油剂能够有效地去除金属表面的油污和杂质,为后续电镀工艺提供干净的基材。
应用电镀除油剂广泛应用于各种金属电镀工艺中,包括但不限于以下几个方面:1.预处理:在金属电镀之前,需要对基材进行预处理以确保表面干净。
电镀除油剂可以去除表面的油脂、氧化物和其他污染物,为后续电镀工艺做好准备。
2.脱脂:在某些情况下,金属表面可能存在大量的脱脂剂残留。
使用电镀除油剂可以将这些脱脂剂彻底去除,以保证电镀质量。
3.清洗:在一些特殊情况下,金属表面可能需要进行清洗以去除附着物。
电镀除油剂可以有效地清洗金属表面,并确保无残留。
使用注意事项在使用电镀除油剂时需要注意以下事项:1.安全操作:电镀除油剂可能对皮肤和眼睛有刺激性,使用时应佩戴适当的防护装备,避免接触皮肤和眼睛。
2.通风环境:电镀除油剂的使用应在通风良好的环境中进行,以避免吸入有害气体。
3.浓度控制:根据具体情况,调整电镀除油剂的浓度以达到最佳效果。
过高或过低的浓度都可能影响去污效果。
4.温度控制:电镀除油剂在一定温度范围内工作效果更好。
根据具体产品说明,保持适当的工作温度。
结论电镀除油剂是金属电镀工业中不可或缺的化学品。
通过配方中的碱性物质和表面活性剂,它能够有效去除金属表面的油污和杂质。
镀前除油工艺
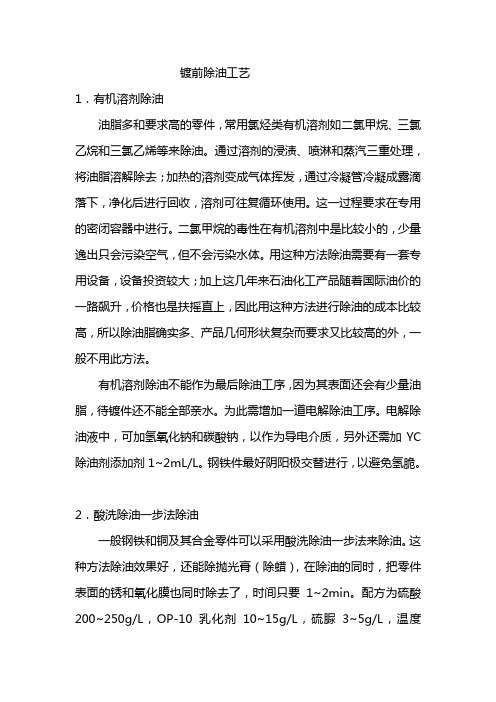
镀前除油工艺1.有机溶剂除油油脂多和要求高的零件,常用氯烃类有机溶剂如二氯甲烷、三氯乙烷和三氯乙烯等来除油。
通过溶剂的浸渍、喷淋和蒸汽三重处理,将油脂溶解除去;加热的溶剂变成气体挥发,通过冷凝管冷凝成露滴落下,净化后进行回收,溶剂可往复循环使用。
这一过程要求在专用的密闭容器中进行。
二氯甲烷的毒性在有机溶剂中是比较小的,少量逸出只会污染空气,但不会污染水体。
用这种方法除油需要有一套专用设备,设备投资较大;加上这几年来石油化工产品随着国际油价的一路飙升,价格也是扶摇直上,因此用这种方法进行除油的成本比较高,所以除油脂确实多、产品几何形状复杂而要求又比较高的外,一般不用此方法。
有机溶剂除油不能作为最后除油工序,因为其表面还会有少量油脂,待镀件还不能全部亲水。
为此需增加一道电解除油工序。
电解除油液中,可加氢氧化钠和碳酸钠,以作为导电介质,另外还需加YC 除油剂添加剂1~2mL/L。
钢铁件最好阴阳极交替进行,以避免氢脆。
2.酸洗除油一步法除油一般钢铁和铜及其合金零件可以采用酸洗除油一步法来除油。
这种方法除油效果好,还能除抛光膏(除蜡),在除油的同时,把零件表面的锈和氧化膜也同时除去了,时间只要1~2min。
配方为硫酸200~250g/L,OP-10乳化剂10~15g/L,硫脲3~5g/L,温度65~75℃。
铜件除油可用硫酸150~200g/L,PC-3铜件除油除膜剂30~35g/L,温度65~75℃。
这一配方也可用于铜铁组合零件,铜离子不会置换到铁零件上。
在酸洗除油一步法过程中,溶液表面会浮着一层油脂,要及时用勺子把它沓到油水分离器中去。
通过油水分离和过滤,这种油脂可回收。
要方便的话,可把除油槽设计有溢油口,将上浮的油让其从溢油口流出,然后用塑料泵泵到油水分离器中去。
所以要将表面浮油除去,一是不让其流入水体,造成污染,二是避免浮油粘污零件。
这种溶液到铁离子积累过多时,需要更换。
更换下来的溶液经过滤和冷冻,还可回收硫酸亚铁,冷冻过滤后的溶液仍可继续使用,这样就可将污染减少到最低的程度。
9种pcb的标准溶液

9种pcb的标准溶液PCB(Printed Circuit Board,印刷电路板)是电子设备中不可或缺的一部分,它通过在表面覆盖一层特定的电子导电材料,用来连接和支持电子元器件,从而实现电路功能。
在PCB的制造过程中,标准溶液是必不可少的材料。
下面将介绍9种常用的PCB标准溶液。
1.铜腐蚀液:用来清除PCB表面的氧化铜,以便于后续步骤的操作。
铜腐蚀液通常含有含有硫酸、过氧化氢、氯化铁等成分,能有效地腐蚀掉铜表面的氧化物。
2.碱性清洗剂:主要用于清洗PCB表面的油污和杂质,以保证PCB 的表面干净。
碱性清洗剂通常含有氢氧化钠、氢氧化钾等成分,能够中和酸性物质并溶解污渍。
3.氧化剂:用于PCB表面的氧化处理,以使金属表面形成一层氧化膜,以增强PCB的耐腐蚀性和附着力。
常见的氧化剂有硝酸铜、硝酸铁等。
4.配铜液:根据PCB设计要求,在PCB表面电镀一层铜。
铜能提高电导性能,并保护PCB线路不受氧化、腐蚀的侵害。
5.酸性洗涤剂:用于去除PCB表面的污渍、油污和杂质。
酸性洗涤剂通常含有氯化铁、氢氟酸等成分,能够有效去除PCB表面的有机污渍。
6.退镀溶液:用于去除电镀层上的铜,以便于PCB下一步的操作。
退镀溶液通常含有硫酸、硝酸等成分,能够迅速溶解电镀层上的铜。
7.全蚀剂:用于蚀刻PCB上的铜层,以便于形成所需的导线线路。
全蚀剂通常含有盐酸、过氧化氢等成分,能够快速剥离掉铜层。
8.防焊膏:用于PCB焊接过程中保护PCB未焊接部分不受焊锡侵蚀。
防焊膏通常在PCB表面涂覆一层保护膜,焊接后可以把保护膜去除,保护PCB的表面线路免受氧化、腐蚀。
9.阻焊油墨:用于PCB的阻焊工艺,通过在PCB表面涂覆一层阻焊油墨,以便于焊接过程中阻止焊锡漆涂敷到不需要焊接的位置。
阻焊油墨能够提高PCB的可靠性和焊接质量。
以上是9种常用的PCB标准溶液,它们在PCB的制造和加工过程中发挥着重要的作用。
每种溶液都有其特定的化学成分和作用,以满足不同制程要求。
镀锌板除油的方法
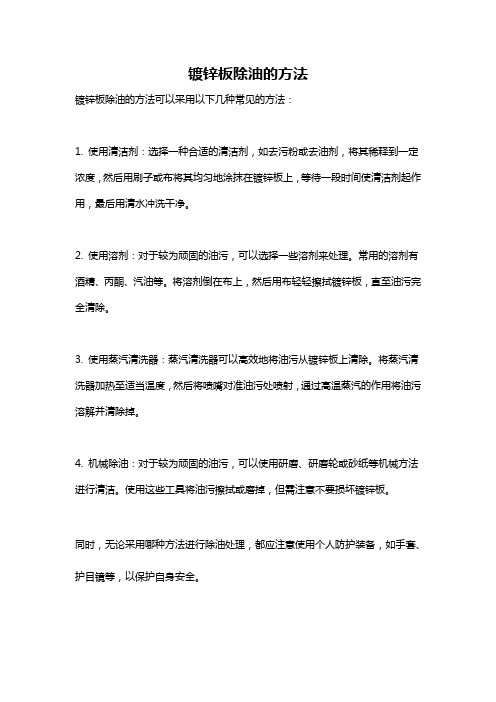
镀锌板除油的方法
镀锌板除油的方法可以采用以下几种常见的方法:
1. 使用清洁剂:选择一种合适的清洁剂,如去污粉或去油剂,将其稀释到一定浓度,然后用刷子或布将其均匀地涂抹在镀锌板上,等待一段时间使清洁剂起作用,最后用清水冲洗干净。
2. 使用溶剂:对于较为顽固的油污,可以选择一些溶剂来处理。
常用的溶剂有酒精、丙酮、汽油等。
将溶剂倒在布上,然后用布轻轻擦拭镀锌板,直至油污完全清除。
3. 使用蒸汽清洗器:蒸汽清洗器可以高效地将油污从镀锌板上清除。
将蒸汽清洗器加热至适当温度,然后将喷嘴对准油污处喷射,通过高温蒸汽的作用将油污溶解并清除掉。
4. 机械除油:对于较为顽固的油污,可以使用研磨、研磨轮或砂纸等机械方法进行清洁。
使用这些工具将油污擦拭或磨掉,但需注意不要损坏镀锌板。
同时,无论采用哪种方法进行除油处理,都应注意使用个人防护装备,如手套、护目镜等,以保护自身安全。
PCB线路板的电镀铜工艺
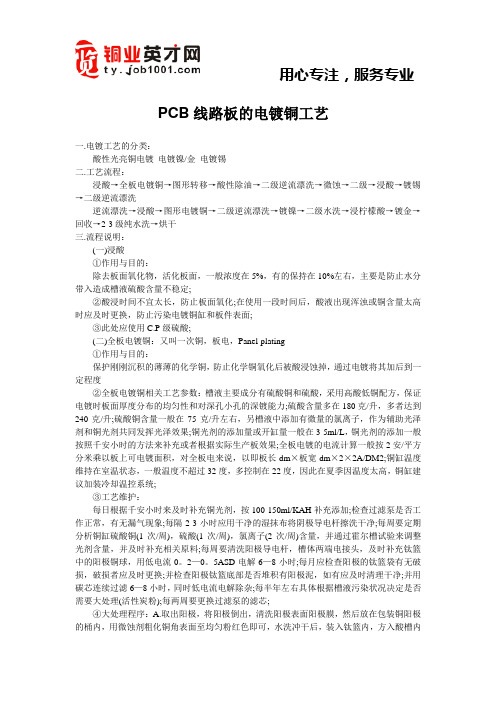
PCB线路板的电镀铜工艺一.电镀工艺的分类:酸性光亮铜电镀电镀镍/金电镀锡二.工艺流程:浸酸→全板电镀铜→图形转移→酸性除油→二级逆流漂洗→微蚀→二级→浸酸→镀锡→二级逆流漂洗逆流漂洗→浸酸→图形电镀铜→二级逆流漂洗→镀镍→二级水洗→浸柠檬酸→镀金→回收→2-3级纯水洗→烘干三.流程说明:(一)浸酸①作用与目的:除去板面氧化物,活化板面,一般浓度在5%,有的保持在10%左右,主要是防止水分带入造成槽液硫酸含量不稳定;②酸浸时间不宜太长,防止板面氧化;在使用一段时间后,酸液出现浑浊或铜含量太高时应及时更换,防止污染电镀铜缸和板件表面;③此处应使用C.P级硫酸;(二)全板电镀铜:又叫一次铜,板电,Panel-plating①作用与目的:保护刚刚沉积的薄薄的化学铜,防止化学铜氧化后被酸浸蚀掉,通过电镀将其加后到一定程度②全板电镀铜相关工艺参数:槽液主要成分有硫酸铜和硫酸,采用高酸低铜配方,保证电镀时板面厚度分布的均匀性和对深孔小孔的深镀能力;硫酸含量多在180克/升,多者达到240克/升;硫酸铜含量一般在75克/升左右,另槽液中添加有微量的氯离子,作为辅助光泽剂和铜光剂共同发挥光泽效果;铜光剂的添加量或开缸量一般在3-5ml/L,铜光剂的添加一般按照千安小时的方法来补充或者根据实际生产板效果;全板电镀的电流计算一般按2安/平方分米乘以板上可电镀面积,对全板电来说,以即板长dm×板宽dm×2×2A/DM2;铜缸温度维持在室温状态,一般温度不超过32度,多控制在22度,因此在夏季因温度太高,铜缸建议加装冷却温控系统;③工艺维护:每日根据千安小时来及时补充铜光剂,按100-150ml/KAH补充添加;检查过滤泵是否工作正常,有无漏气现象;每隔2-3小时应用干净的湿抹布将阴极导电杆擦洗干净;每周要定期分析铜缸硫酸铜(1次/周),硫酸(1次/周),氯离子(2次/周)含量,并通过霍尔槽试验来调整光剂含量,并及时补充相关原料;每周要清洗阳极导电杆,槽体两端电接头,及时补充钛篮中的阳极铜球,用低电流0。
除挂灰配方之电解除油剂
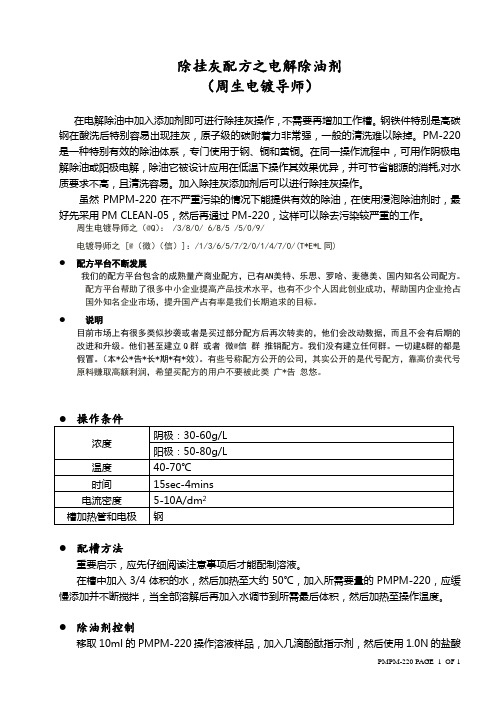
除挂灰配方之电解除油剂(周生电镀导师)在电解除油中加入添加剂即可进行除挂灰操作,不需要再增加工作槽。
钢铁件特别是高碳钢在酸洗后特别容易出现挂灰,原子级的碳附着力非常强,一般的清洗难以除掉。
PM-220是一种特别有效的除油体系,专门使用于钢、铜和黄铜。
在同一操作流程中,可用作阴极电解除油或阳极电解,除油它被设计应用在低温下操作其效果优异,并可节省能源的消耗,对水质要求不高,且清洗容易。
加入除挂灰添加剂后可以进行除挂灰操作。
虽然PMPM-220在不严重污染的情况下能提供有效的除油,在使用浸泡除油剂时,最好先采用PM CLEAN-05,然后再通过PM-220,这样可以除去污染较严重的工作。
周生电镀导师之(@Q): /3/8/0/ 6/8/5 /5/0/9/电镀导师之 [@(微)(信)]:/1/3/6/5/7/2/0/1/4/7/0/(T*E*L同)●配方平台不断发展我们的配方平台包含的成熟量产商业配方,已有AN美特、乐思、罗哈、麦德美、国内知名公司配方。
配方平台帮助了很多中小企业提高产品技术水平,也有不少个人因此创业成功,帮助国内企业抢占国外知名企业市场,提升国产占有率是我们长期追求的目标。
●说明目前市场上有很多类似抄袭或者是买过部分配方后再次转卖的,他们会改动数据,而且不会有后期的改进和升级。
他们甚至建立Q群或者微@信群推销配方。
我们没有建立任何群。
一切建&群的都是假冒。
(本*公*告*长*期*有*效)。
有些号称配方公开的公司,其实公开的是代号配方,靠高价卖代号原料赚取高额利润,希望买配方的用户不要被此类广*告忽悠。
●配槽方法重要启示,应先仔细阅读注意事项后才能配制溶液。
在槽中加入3/4体积的水,然后加热至大约50℃,加入所需要量的PMPM-220,应缓慢添加并不断搅拌,当全部溶解后再加入水调节到所需最后体积,然后加热至操作温度。
●除油剂控制移取10ml的PMPM-220操作溶液样品,加入几滴酚酞指示剂,然后使用1.0N的盐酸来滴定溶液变色,记录下盐酸的毫升数。
PCB电镀工艺介绍[

PCB 电镀工艺介绍线路板地电镀工艺 ,大约可以分类 :酸性光亮铜电镀、电镀镍 /金、电镀锡 ,文章介绍地是 关 于 在 线 路 板 加 工 过 程 是 ,电 镀 工 艺 地 技 术 以 及 工 艺 流程 ,以 及 具 体 操 作 方 法 . 二 .工艺流程:浸酸T 全板电镀铜T 图形转移T 酸性除油T 二级逆流漂洗 T 微蚀T 二级逆流漂洗 T 浸酸T镀锡T 二级逆流漂洗 T 逆流漂洗T 浸酸T 图形电镀铜 T 二级逆流漂洗 T 镀镍T 二级水洗T 浸柠檬 酸 t 镀 金 t回 收 t2-3 级 纯水 洗 T 烘 干三.流程说明 :(一>浸酸① 作用与目地:除去板面氧化物 , 活化板面 , 一般浓度在 5%,有地保持在 10%左右 ,主要是 防止水分带入造成槽液 硫酸 含 量 不 稳 定。
② 酸浸时间不宜太长 ,防止板面氧化。
在使用一段时间后 ,酸液出现浑浊或铜含量太高时应及时更 换, 防止污 染电 镀铜缸和 板件 表面。
③此处应使用C.P 级 硫 酸。
( 二 > 全板 电 镀 铜 : 又 叫一次铜, 板电,Panel-plating ① 作用与目地: 保护刚刚沉积地薄薄地化学铜 ,防止化学铜氧化后被酸浸蚀掉 ,通过电镀将其加后 到 一定程度② 全板电镀铜相关工艺参数:槽液主要成分有硫酸铜和硫酸 ,采用高酸低铜配方 ,保证电镀时板面厚度分布地均匀性和对深孔小孔地深镀能力。
硫酸含量多在 180 克/升,多者达到 240克/升。
硫酸铜含量一般在 75克/升左右 ,另槽液中添加有微量地氯离子 ,作为辅助光泽剂和铜 光剂共同发挥光泽效果。
铜光剂地添加量或开缸量一般在3-5ml/L, 铜光剂地添加一般按照千安小时地方法来补充或者根据实际生产板效果。
全板电镀地电流计算一般按2 安/平方分M 乘以板上可电镀面积,对全板电来说,以即板长 dmx 板宽dmX2疋A/ DM2。
铜缸温度维持在室温状, 一般温度不超过 32 度,多控制22 度,因此在夏季因温度太高 ,铜缸建议加装却 温 控系 统。
PCB电镀沉铜药水控制工艺
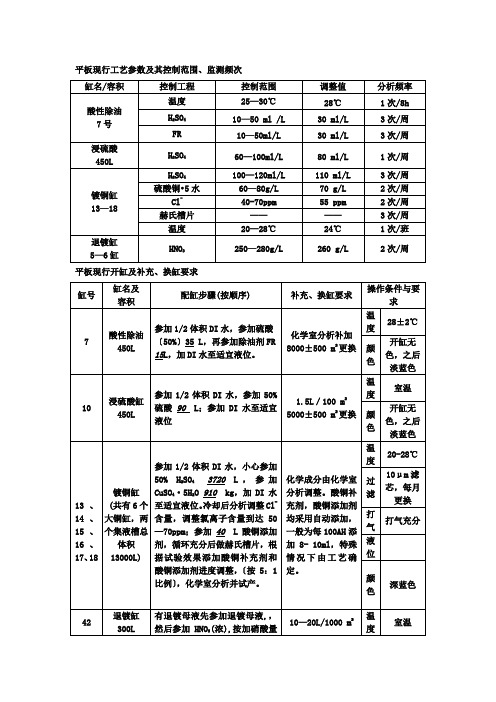
平板现行工艺参数及其控制范围、监测频次平板现行开缸及补充、换缸要求平板药缸工艺操作标准图电工艺参数及其控制范围、监测频次图电开缸及补充、换缸要求图电药缸工艺操作标准开缸标准.2 开缸方法说明:1)除微蚀、预浸、浸酸外,其他各缸开缸后化学分析并根据分析结果进行调整,但凹蚀缸KMnO4减 K2MNO4浓度≥40g/l时不作额外补充。
药水颜色及循环过滤要求沉铜自动添加药水准备及自动添加频次设置1)自动添加药水备料〔满量生产〕沉铜液880A每天需备料1—2桶沉铜液880E每天需备料10L甲醛每天需备料15L氢氧化钠每天需配制含300g/L的溶液100L,每桶〔50L〕配制时先加半桶DI水,参加NaOH 15㎏搅拌均匀,补充DI水,再搅拌均匀,待冷却后使用。
自动添加桶液位低于1/4时必须及时补充药剂生产线开缸方法自动加药系统控制〔说明蚀刻自动添加原理及添加量〕蚀刻段:比重到达设定值(例如:1.193)时,开始自动添加蚀刻子液PH值低于设定值时,开始自动添加氨水PH值高于设定值时,开始自动添加氯化铵自动添加药水流量、添加频次每周由工艺确认、调整,每周比照重值、PH值设定、校准,由工艺负责。
备注:A.电镀后经补黑油的板件,干膜较难退下,可根据实际情况,适当降低退膜速度。
B. 孤立线路易夹膜的板件应适当降低退膜速度。
/min。
工艺参数控制露铜点:指冲板时刚好能把干膜全部洗掉所走过的距离,•此距离占整显影段的百分率, 例如走在中间时停止,然后观察板面露铜的局部,假设只有一半即为50%。
重氮片工艺参数控制:干膜存放。
电镀前处理除油除锈工艺流程
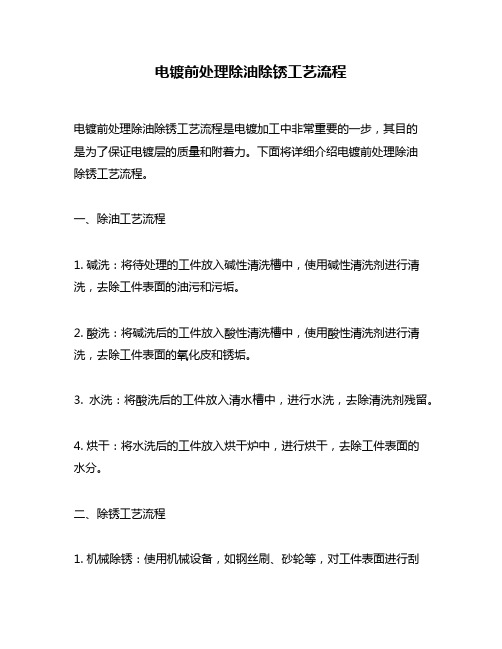
电镀前处理除油除锈工艺流程
电镀前处理除油除锈工艺流程是电镀加工中非常重要的一步,其目的
是为了保证电镀层的质量和附着力。
下面将详细介绍电镀前处理除油
除锈工艺流程。
一、除油工艺流程
1. 碱洗:将待处理的工件放入碱性清洗槽中,使用碱性清洗剂进行清洗,去除工件表面的油污和污垢。
2. 酸洗:将碱洗后的工件放入酸性清洗槽中,使用酸性清洗剂进行清洗,去除工件表面的氧化皮和锈垢。
3. 水洗:将酸洗后的工件放入清水槽中,进行水洗,去除清洗剂残留。
4. 烘干:将水洗后的工件放入烘干炉中,进行烘干,去除工件表面的
水分。
二、除锈工艺流程
1. 机械除锈:使用机械设备,如钢丝刷、砂轮等,对工件表面进行刮
磨,去除表面的锈垢和氧化皮。
2. 化学除锈:将待处理的工件放入除锈槽中,使用除锈剂进行清洗,
去除工件表面的锈垢和氧化皮。
3. 水洗:将除锈后的工件放入清水槽中,进行水洗,去除清洗剂残留。
4. 烘干:将水洗后的工件放入烘干炉中,进行烘干,去除工件表面的
水分。
以上就是电镀前处理除油除锈工艺流程的详细介绍。
在实际操作中,
需要根据不同的工件材质和表面情况,选择不同的清洗剂和除锈剂,
以达到最佳的清洗效果。
同时,为了保证电镀层的质量和附着力,还
需要严格控制每个环节的操作时间和温度,确保工艺流程的稳定性和
可靠性。
PCB电镀过程铜面粗糙原因分析
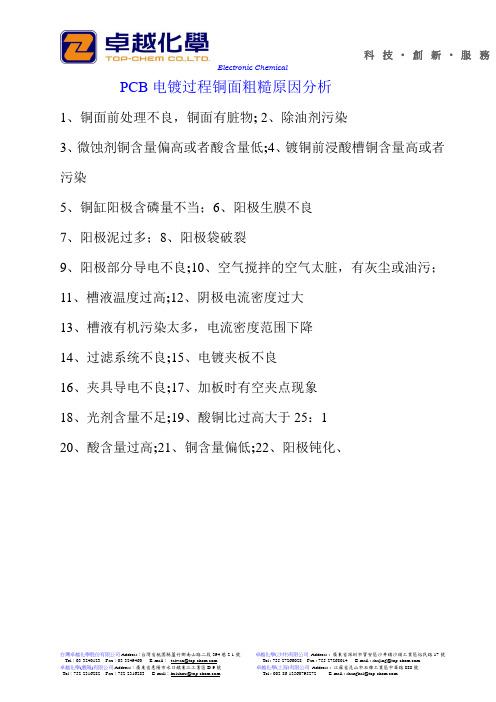
Electronic Chemical 台灣卓越化學股份有限公司Address :台灣省桃園縣蘆竹鄉南山路二段394巷2-1號 卓越化學(沙井)有限公司 Address : 廣東省深圳市寶安區沙井鎮沙頭工業區裕民路17號 Tel :03-3240123 Fax :03-3249460 E-mail : taiwan@ Tel : 755-27266028 Fax : 755-27268014 E-mail : shajing@ 卓越化學(惠陽)有限公司Address :廣東省惠陽市水口鎮東江工業區D-9號 卓越化學(上海)有限公司 Address : 江蘇省昆山市石牌工業區中華路888號 Tel :752-2316282 Fax :752-2316283 E-mail :huizhou@ Tel : 002-86-135******** E-mail : shanghai@
PCB 电镀过程铜面粗糙原因分析
1、铜面前处理不良,铜面有脏物;
2、除油剂污染
3、微蚀剂铜含量偏高或者酸含量低;
4、镀铜前浸酸槽铜含量高或者污染
5、铜缸阳极含磷量不当;
6、阳极生膜不良
7、阳极泥过多;8、阳极袋破裂
9、阳极部分导电不良;10、空气搅拌的空气太脏,有灰尘或油污;
11、槽液温度过高;12、阴极电流密度过大
13、槽液有机污染太多,电流密度范围下降
14、过滤系统不良;15、电镀夹板不良
16、夹具导电不良;17、加板时有空夹点现象
18、光剂含量不足;19、酸铜比过高大于25:1
20、酸含量过高;21、铜含量偏低;22、阳极钝化、。
PCB电镀工艺流程

PCB电镀工艺流程浸酸→全板电镀铜→图形转移→酸性除油→二级逆流漂洗→微蚀→二级浸酸→镀锡→二级逆流漂洗→浸酸→图形电镀铜→二级逆流漂洗→镀镍→二级水洗→浸柠檬酸→镀金→回收→2-3级纯水洗→烘干。
PCB电镀工艺流程说明一、浸酸1、作用与目的除去板面氧化物,活化板面,一般浓度在5%,有的保持在10%左右,主要是防止水分带入造成槽液硫酸含量不稳定;酸浸时间不宜太长,防止板面氧化;在使用一段时间后,酸液出现浑浊或铜含量太高时应及时更换,防止污染电镀铜缸和板件表面;此处应使用C.P级硫酸。
二、全板电镀铜1、作用与目的:保护刚刚沉积的薄薄的化学铜,防止化学铜氧化后被酸浸蚀掉,通过电镀将其加后到一定程度;全板电镀铜相关工艺参数:槽液主要成分有硫酸铜和硫酸,采用高酸低铜配方,保证电镀时板面厚度分布的均匀性和对深孔小孔的深镀能力;硫酸含量多在180克/升,多者达到240克/升;硫酸铜含量一般在75克/升左右,另槽液中添加有微量的氯离子,作为辅助光泽剂和铜光剂共同发挥光泽效果;铜光剂的添加量或开缸量一般在3-5ml/L,铜光剂的添加一般按照千安小时的方法来补充或者根据实际生产板效果;2、全板电镀的电流计算一般按2A/平方分米乘以板上可电镀面积,对全板电来说,以即板长×板宽×2×2A/DM2;铜缸温度维持在室温状态,一般温度不超过32度,多控制在22度,因此在夏季因温度太高,铜缸建议加装冷却温控系统。
3、工艺维护每日根据千安小时来及时补充铜光剂,按100-150ml/KAH补充添加;检查过滤泵是否工作正常,有无漏气现象;每隔2-3小时应用干净的湿抹布将阴极导电杆擦洗干净;每周要定期分析铜缸硫酸铜(1次/周),硫酸(1次/周),氯离子(2次/周)含量,并通过霍尔槽试验来调整光剂含量,并及时补充相关原料;每周要清洗阳极导电杆,槽体两端电接头,及时补充钛篮中的阳极铜球,用低电流0.2-0.5ASD电解6-8小时;每月应检查阳极的钛篮袋有无破损,破损者应及时更换;并检查阳极钛篮底部是否堆积有阳极泥,如有应及时清理干净;并用碳芯连续过滤6-8小时,同时低电流电解除杂;每半年左右具体根据槽液污染状况决定是否需要大处理(活性炭粉);每两周要更换过滤泵的滤芯。
电镀除油工艺原理(上)
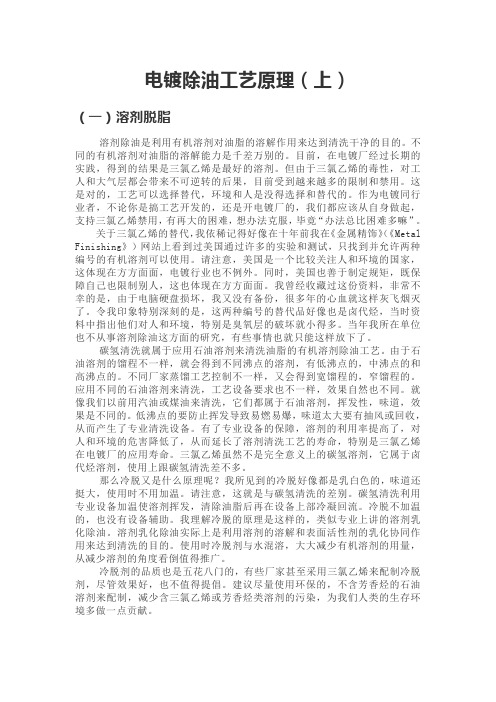
电镀除油工艺原理(上)(一)溶剂脱脂溶剂除油是利用有机溶剂对油脂的溶解作用来达到清洗干净的目的。
不同的有机溶剂对油脂的溶解能力是千差万别的。
目前,在电镀厂经过长期的实践,得到的结果是三氯乙烯是最好的溶剂。
但由于三氯乙烯的毒性,对工人和大气层都会带来不可逆转的后果,目前受到越来越多的限制和禁用。
这是对的,工艺可以选择替代,环境和人是没得选择和替代的。
作为电镀同行业者,不论你是搞工艺开发的,还是开电镀厂的,我们都应该从自身做起,支持三氯乙烯禁用,有再大的困难,想办法克服,毕竟“办法总比困难多嘛”。
关于三氯乙烯的替代,我依稀记得好像在十年前我在《金属精饰》(《Metal Finishing》)网站上看到过美国通过许多的实验和测试,只找到并允许两种编号的有机溶剂可以使用。
请注意,美国是一个比较关注人和环境的国家,这体现在方方面面,电镀行业也不例外。
同时,美国也善于制定规矩,既保障自己也限制别人,这也体现在方方面面。
我曾经收藏过这份资料,非常不幸的是,由于电脑硬盘损坏,我又没有备份,很多年的心血就这样灰飞烟灭了。
令我印象特别深刻的是,这两种编号的替代品好像也是卤代烃,当时资料中指出他们对人和环境,特别是臭氧层的破坏就小得多。
当年我所在单位也不从事溶剂除油这方面的研究,有些事情也就只能这样放下了。
碳氢清洗就属于应用石油溶剂来清洗油脂的有机溶剂除油工艺。
由于石油溶剂的馏程不一样,就会得到不同沸点的溶剂,有低沸点的,中沸点的和高沸点的。
不同厂家蒸馏工艺控制不一样,又会得到宽馏程的,窄馏程的。
应用不同的石油溶剂来清洗,工艺设备要求也不一样,效果自然也不同。
就像我们以前用汽油或煤油来清洗,它们都属于石油溶剂,挥发性,味道,效果是不同的。
低沸点的要防止挥发导致易燃易爆,味道太大要有抽风或回收,从而产生了专业清洗设备。
有了专业设备的保障,溶剂的利用率提高了,对人和环境的危害降低了,从而延长了溶剂清洗工艺的寿命,特别是三氯乙烯在电镀厂的应用寿命。
PCB电镀沉铜药水控制工艺
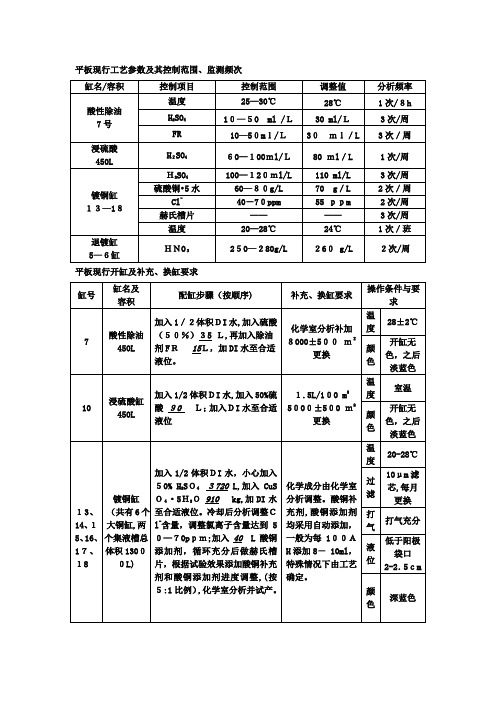
平板现行工艺参数及其控制范围、监测频次平板现行开缸及补充、换缸要求平板药缸工艺操作规范图电工艺参数及其控制范围、监测频次图电开缸及补充、换缸要求图电药缸工艺操作规范4.2.3沉铜线各药水缸工艺控制要求:(罗门哈斯药水体系)4.2.6开缸规范4.2.6.2 开缸方法说明:1)除微蚀、预浸、浸酸外,其他各缸开缸后化学分析并根据分析结果进行调整,但凹蚀缸KMnO4减K2MNO4浓度≥40g/l时不作额外补充。
4. 2.7药水颜色及循环过滤要求4.2.8沉铜自动添加药水准备及自动添加频次设置1)自动添加药水备料(满量生产)沉铜液880A每天需备料1—2桶沉铜液880E每天需备料10L甲醛每天需备料15L氢氧化钠每天需配制含300g/L的溶液100L,每桶(50L)配制时先加半桶DI水,加入N aOH 15㎏搅拌均匀,补充DI水,再搅拌均匀,待冷却后使用。
自动添加桶液位低于1/4时必须及时补充药剂4.2.1 各个药水控制范围4.2.3 自动加药系统控制(说明蚀刻自动添加原理及添加量)蚀刻段:比重达到设定值(例如:1.193)时,开始自动添加蚀刻子液PH值低于设定值时,开始自动添加氨水PH值高于设定值时,开始自动添加氯化铵自动添加药水流量、添加频次每周由工艺确认、调整,每周对比重值、PH值设定、校准,由工艺负责。
备注:A.电镀后经补黑油的板件,干膜较难退下,可根据实际情况,适当降低退膜速度。
B. 孤立线路易夹膜的板件应适当降低退膜速度。
C. 对于有平板加厚要求的板件,可根据实际情况适当降低蚀刻速度,一般比相应控制范围降低0.2-0.4m/min。
5.0蚀刻液配制4. 1.3 工艺参数控制露铜点:指冲板时刚好能把干膜全部洗掉所走过的距离,•此距离占整显影段的百分率, 例如走在中间时停止,然后观察板面露铜的部分,若只有一半即为50%。
4.1.5 干膜存放4.1.6 生产参数测量频次。
PCB电镀工艺流程介绍

PCB电镀工艺介绍线路板的电镀工艺,大约可以分类:酸性光亮铜电镀、电镀镍/金、电镀锡,文章介绍的是关于在线路板加工过程是,电镀工艺的技术以及工艺流程,以及具体操作方法.二.工艺流程:浸酸→全板电镀铜→图形转移→酸性除油→二级逆流漂洗→微蚀→二级逆流漂洗→浸酸→镀锡→二级逆流漂洗→逆流漂洗→浸酸→图形电镀铜→二级逆流漂洗→镀镍→二级水洗→浸柠檬酸→镀金→回收→2-3级纯水洗→烘干三.流程说明:(一)浸酸①作用与目的:除去板面氧化物,活化板面,一般浓度在5%,有的保持在10%左右,主要是防止水分带入造成槽液硫酸含量不稳定;②酸浸时间不宜太长,防止板面氧化;在使用一段时间后,酸液出现浑浊或铜含量太高时应及时更换,防止污染电镀铜缸和板件表面;③此处应使用C.P级硫酸;(二)全板电镀铜:又叫一次铜,板电,Panel-plating①作用与目的:保护刚刚沉积的薄薄的化学铜,防止化学铜氧化后被酸浸蚀掉,通过电镀将其加后到一定程度②全板电镀铜相关工艺参数:槽液主要成分有硫酸铜和硫酸,采用高酸低铜配方,保证电镀时板面厚度分布的均匀性和对深孔小孔的深镀能力;硫酸含量多在180克/升,多者达到240克/升;硫酸铜含量一般在75克/升左右,另槽液中添加有微量的氯离子,作为辅助光泽剂和铜光剂共同发挥光泽效果;铜光剂的添加量或开缸量一般在3-5ml/L,铜光剂的添加一般按照千安小时的方法来补充或者根据实际生产板效果;全板电镀的电流计算一般按2安/平方分米乘以板上可电镀面积,对全板电来说,以即板长dm×板宽dm×2×2A/DM2;铜缸温度维持在室温状态,一般温度不超过32度,多控制在22度,因此在夏季因温度太高,铜缸建议加装冷却温控系统;③工艺维护:每日根据千安小时来及时补充铜光剂,按100-150ml/KAH补充添加;检查过滤泵是否工作正常,有无漏气现象;每隔2-3小时应用干净的湿抹布将阴极导电杆擦洗干净;每周要定期分析铜缸硫酸铜(1次/周),硫酸(1次/周),氯离子(2次/周)含量,并通过霍尔槽试验来调整光剂含量,并及时补充相关原料;每周要清洗阳极导电杆,槽体两端电接头,及时补充钛篮中的阳极铜球,用低电流0。
电镀去油剂的配方介绍

电镀去油剂的配方介绍电镀去油剂在电镀工艺中起着非常重要的作用。
它能够有效地去除金属表面的油污、氧化物和其他污染物,为后续的电镀步骤打下良好的基础。
本文将介绍一种常见的电镀去油剂配方,并探讨其原理和应用情况。
一、电镀去油剂配方介绍电镀去油剂的配方可以根据具体的电镀工艺和金属材料的要求而有所不同。
下面是一种常用的电镀去油剂配方,供参考:1. 去油助剂:10%~30%2. 乳化剂:5%~15%3. 稀释剂:55%~80%该配方中的去油助剂主要是去除金属表面的油污,常见的去油助剂有烷基苯磺酸盐、硫酸、甘油等。
乳化剂的作用是将去油助剂和稀释剂进行乳化,以便更好地均匀分散在溶液中。
稀释剂则是通过稀释去油助剂和乳化剂的浓度,使得去油剂达到最佳使用浓度。
二、电镀去油剂的原理电镀去油剂主要依靠其与金属表面的物理和化学作用来去除油污和污染物。
去油助剂的表面张力较低,能够渗入到金属表面的油污中,从而分离出来。
去油助剂中的活性成分能够与金属表面上的氧化物和其他污染物发生化学反应,将其转化为易于移除的物质。
乳化剂的作用是将去油助剂和稀释剂进行乳化形成稳定的乳液。
通过乳化剂的作用,去油助剂得以更均匀地分散在溶液中,并且将其固定在金属表面上,以增加去油的效果。
三、电镀去油剂的应用情况电镀去油剂广泛应用于各类电镀工艺中。
无论是金属的预处理,还是电子元器件和汽车零部件的表面处理,都离不开去油剂的使用。
通过去除金属表面的油污和污染物,电镀去油剂能够提供一个干净的表面,以确保电镀涂层的附着力和耐久性。
值得注意的是,不同的金属材料和电镀工艺对去油剂的要求也有所不同。
铝合金表面容易生成氧化膜,对应的去油剂需要具备良好的去氧化膜和去油效果。
而对于一些特殊金属材料如钛合金或镍基合金,可能需要使用特殊的去油剂来满足其特殊的处理要求。
四、我对电镀去油剂的观点和理解作为一种重要的电镀前处理剂,电镀去油剂在电镀工艺中起着至关重要的作用。
它能够有效去除金属表面的油污和污染物,为后续的电镀步骤提供一个清洁的基础。
PCB电镀工艺流程
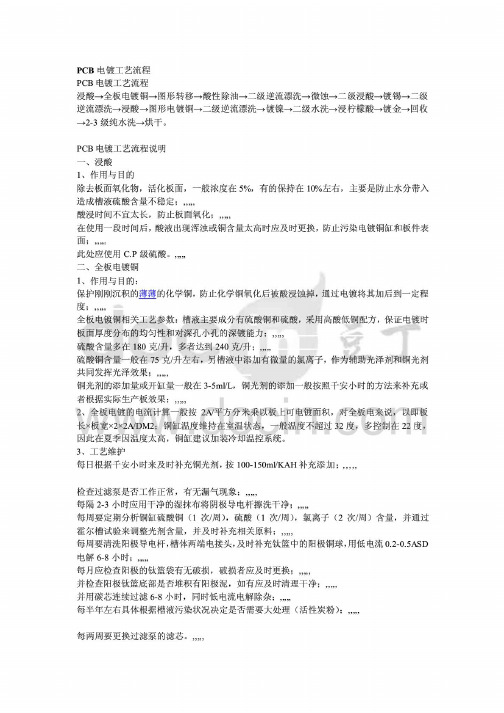
干后备用, "'"
将拙液转移到备用植内,加入 1-3mVL 的 30% 的双氧水,开始加、温,待温度加到 65 度左右
打开空气搅拌,保温空气搅拌 2-4 小时, "'"
关掉空气搅拌,按 3-5 克/升将活性碳粉缓慢溶解到槽液中,待溶解彻底后,打开空气搅拌,
因此在夏季因温度太 高 ,铜缸建议加装冷却温控系统。
3 、 工 艺维护
每日根据千安小时来及时补充铜光剂, 按 100-150mVKAH 补充添加; "'"
检查过滤泵是否 工作正常 , 有无漏气现象;川,
每隔 2-3 小时应用干净的温抹布将阴极导电杆擦洗干净;川"
每周要定期分析铜缸硫酸铜(1次/周) , 硫酸(1次/周) , 氯离子 (2 次/周〉含量,并通过
如此保温 2-4 小时; "'"
关掉空气搅拌 , 加、温,让活性碳粉慢慢沉淀至槽底 ; '"''
待温度降至 40 度左右,用 10um 的 pp 滤芯加助滤粉过滤槽液至清洗干净的 工 作槽'内,打开
空气搅拌,放入阳极,挂入电解板,按 0.2-0.5ASD 电流密度低电流电解 6-8 小时; '"''
每周要清洗阳极导电杆,槽'体两端电接头,及时补充钦篮中的阳极保角,用低电流 0.2-0.5ASD
电解 6-8 小时; "'"
每月应检查阳极的铁篮袋有无破损,破损者应及时更换;并检查阳极钦篮底部是否堆积有阳
电路板清洗剂说明书
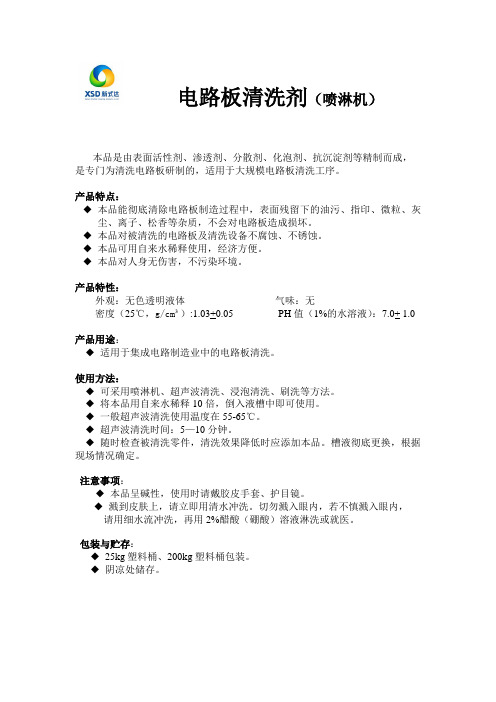
电路板清洗剂(喷淋机)本品是由表面活性剂、渗透剂、分散剂、化泡剂、抗沉淀剂等精制而成,是专门为清洗电路板研制的,适用于大规模电路板清洗工序。
产品特点:
◆本品能彻底清除电路板制造过程中,表面残留下的油污、指印、微粒、灰
尘、离子、松香等杂质,不会对电路板造成损坏。
◆本品对被清洗的电路板及清洗设备不腐蚀、不锈蚀。
◆本品可用自来水稀释使用,经济方便。
◆本品对人身无伤害,不污染环境。
产品特性:
外观:无色透明液体气味:无
密度(25℃,g/cm³):1.03+0.05 PH值(1%的水溶液):7.0+ 1.0 产品用途:
◆适用于集成电路制造业中的电路板清洗。
使用方法:
◆可采用喷淋机、超声波清洗、浸泡清洗、刷洗等方法。
◆将本品用自来水稀释10倍,倒入液槽中即可使用。
◆一般超声波清洗使用温度在55-65℃。
◆超声波清洗时间:5—10分钟。
◆随时检查被清洗零件,清洗效果降低时应添加本品。
槽液彻底更换,根据现场情况确定。
注意事项:
◆本品呈碱性,使用时请戴胶皮手套、护目镜。
◆溅到皮肤上,请立即用清水冲洗。
切勿溅入眼内,若不慎溅入眼内,
请用细水流冲洗,再用2%醋酸(硼酸)溶液淋洗或就医。
包装与贮存:
◆25kg塑料桶、200kg塑料桶包装。
◆阴凉处储存。
pcb电镀除油作用
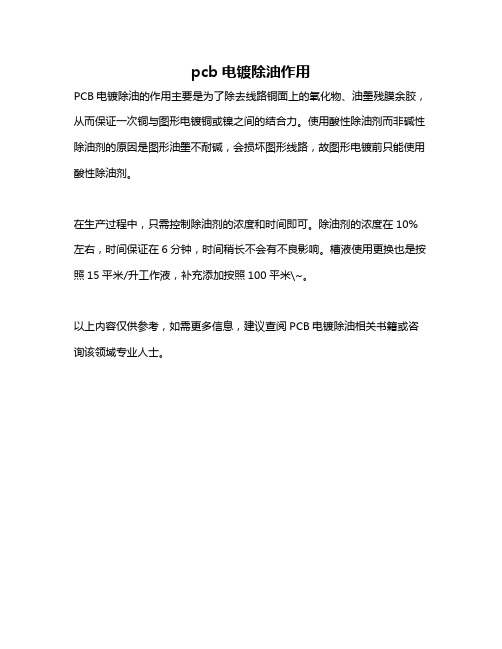
pcb电镀除油作用
PCB电镀除油的作用主要是为了除去线路铜面上的氧化物、油墨残膜余胶,从而保证一次铜与图形电镀铜或镍之间的结合力。
使用酸性除油剂而非碱性除油剂的原因是图形油墨不耐碱,会损坏图形线路,故图形电镀前只能使用酸性除油剂。
在生产过程中,只需控制除油剂的浓度和时间即可。
除油剂的浓度在10%左右,时间保证在6分钟,时间稍长不会有不良影响。
槽液使用更换也是按照15平米/升工作液,补充添加按照100平米\~。
以上内容仅供参考,如需更多信息,建议查阅PCB电镀除油相关书籍或咨询该领域专业人士。
- 1、下载文档前请自行甄别文档内容的完整性,平台不提供额外的编辑、内容补充、找答案等附加服务。
- 2、"仅部分预览"的文档,不可在线预览部分如存在完整性等问题,可反馈申请退款(可完整预览的文档不适用该条件!)。
- 3、如文档侵犯您的权益,请联系客服反馈,我们会尽快为您处理(人工客服工作时间:9:00-18:30)。
PCB电镀线除油剂
2 生产方法:
(1)向清洗干净的专用容器中,加入DI水;
(2)搅拌下缓慢加入需要的浓硫酸;
(3)依次加入各材料搅拌至完全溶解;
(4)加DI水至总重量为1000KG,搅拌半小时;
(5)过滤、装桶。
(如果生产过程控制严格,溶解后无明显悬浮物或沉淀物,可直接用纱布过滤灌装)
3.配方原理及说明
采用酸和表面活性剂相结合的方式,增强产品的除油效果,而且保证产品残留物对电镀铜槽不会产生不良影响。
该产品低泡,适合浸泡和喷淋方式清洗。
使用效果接近甚至超过进口产品水平。
此产品配方关键在于选材。
4. 除油剂的作用
利用低泡表面活性剂有效清除铜表面手印、油渍及氧化物,为后续工序提供洁净的待镀表面。
5.操作条件
6. 镀液配制
(1)在洁净槽内加入3/4体积的纯水;
(2)缓慢加入所需量的浓硫酸, 开启循环;
(3)冷却至40℃以下加入所需量酸铜除油剂SF-92103,补充液位至标准刻度。
7.槽液维护
(1)每生产500平方英尺补加除油剂和98%硫酸各0.3 L;
(2)当生产面积达50 ft2/L槽液需更槽处理。
8. 分析方法
(1)量取1ml槽液,放置于250ml锥形瓶中;
(2)加入50ml纯水和5~6滴甲基橙指示剂;
(3)用1M氢氧化钠标准溶液滴定至由红色变为黄色,记录消耗的NaOH的体积。
计算:硫酸含量(毫升/升)=26.7×滴定毫升数
除油剂与硫酸同等量补加。
9. 电镀除油剂检验方法(略)。