浅析铸钢工艺的常见问题
浅析球墨铸铁件缺陷产生原因及防止措施

浅析球墨铸铁件缺陷产生原因及防止措施
1、坯料的缺陷:由于坯料的杂质含量过高,砂砾过大,沿铸缸边缘空隙较大等,都有可能导致炉内坯料缺陷大,从而产生球墨铸铁件缺陷。
2、成型工艺有问题:如砂芯型腔孔形不规则,型腔深度低,入型质量差,表面光洁度及粘结质量差等,都有可能产生球墨铸铁件缺陷。
3、浇注不合理:球墨铸铁件的浇注工艺过程中需要满足一定的条件,当不合理时,会导致溶质的不均匀分布,产生球墨铸铁件缺陷。
4、冷却不合理:冷却工艺是球墨铸铁件质量重要影响因素,冷却不合理,有可能使坯体结晶不良,从而产生球墨铸铁件缺陷。
二、防止球墨铸铁件缺陷的措施
1、提高坯料质量:在生产过程中,应加强原料检查,确保原料质量良好,并严格控制杂质含量,以减少成型过程中缺陷的发生。
2、改进成型工艺:应采用有利于消除和避免缺陷的成型工艺,如采用自动模具成型等技术,减少缺陷产生的可能性。
3、改善浇注工艺:采用有利于消除缺陷的浇注工艺,如采用连续浇铸或提高浇注压力,改善浇注品质,以减少球墨铸铁件缺陷。
4、优化冷却工艺:采用合理的冷却系统可以有效地控制坯体扩大速度,减少坯体内部残余应力,提高结晶度,以减少球墨铸铁件缺陷的产生。
三、结论
球墨铸铁件的缺陷的产生主要由坯料质量、成型工艺、浇注工艺以及冷却工艺不合理等原因引起。
因此,为防止球墨铸铁件缺陷的产生,应采取提高坯料质量、改进成型工艺、改善浇注工艺以及优化冷却工艺等措施。
只有这样,才能在生产过程中控制住缺陷,获得优良质量的球墨铸铁件。
浅析铸钢件消失模铸造常见缺陷与防治

浅析铸钢件消失模铸造常见缺陷与防治摘要:在铸造过程中,常常会遇到一些常见的问题。
在相同的铸造部位中,局部增碳、表皮增碳、容积增碳,而且相同部位的增碳效果也不尽相同。
因此,文章从理论上分析了铸钢零件的碳化机理及成因,并提出了相应的改进措施,以便在实际应用中得到应用。
关键词:铸钢件;消失模铸造;缺陷分析及预防引言铸件的品质取决于钢中的化学组成、纯化和最佳浇注技术。
要保证铸件的生产工艺,要对整个生产工艺进行严密的监控,从原料、工艺路线、型芯制造、合箱、浇注、落砂、铸件清理直至最后的热处理都要格外重视。
因为很多铸造表面不能进行处理,因此对表面质量、形状和尺寸有着很高的要求。
铸造零件的主要问题有缩松、缩松、空气孔、冷热裂纹、白点、偏析及裂纹破裂等。
因此,对采用消失模工艺的铸造零件所存在的特殊的碳化问题进行了归纳和归纳,并对解决这些问题进行了一些有益的探讨。
一、碳缺陷的过程分析白色模具的主要原材料为 EPS (EPS)。
EPS的主要成分是碳氢化合物,而白色的模具在高温下会很快地被还原成H2和 C。
白色模具分解产生的H2,在空穴中与O2相溶,形成H2O,并以气态逃逸。
如果在短期的O2供给不足的情况下,C元素就会在模子里以黑色烟雾的方式存在,从而使铸造中的碳含量升高。
结果表明:在消失模铸造中,基本没有氢量的升高,而碳化物的升高则很难消除。
而且在铸造温度较低或在凝固终止区经常出现非均一的碳化现象,而在铸造的表层上最容易出现渗碳。
二、渗碳缺陷及处理措施在铸造过程中,由于碳化物的存在,会直接影响到铸造的组织和工艺,而碳化物的大量增多会使铸造产品失效。
当前,针对提高碳源的机制,提出了如下的控制方法。
1.选择高质量的泡沫塑料气泡的品质对煤粉的汽化速度和产品的结构有很大的关系。
优质的泡沫塑料既保证了强度,又保持了较小的致密性。
在钢铸造白模具材料中,第一个选用的是生球,也就是不加再生破碎或废弃的旧料,这是最好的解决办法。
2.选择合理的铸造工艺为避免白色模具的汽化和快速的燃烧,模具包装采用“能站立而不是平卧”的原理,以保证白色模具的快速燃烧。
铸钢件不良发生原因与对策改善
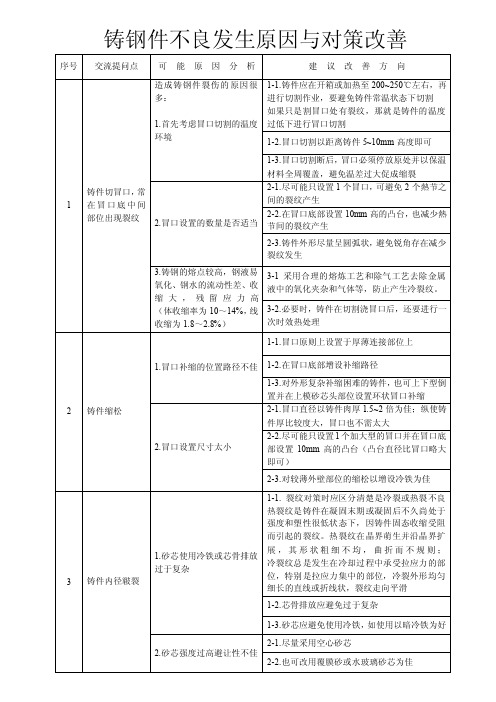
过于部位, 冷裂外形 均匀 细长的直线或折线状,裂纹走向平滑
1-2.芯骨排放应避免过于复杂
1-3.砂芯应避免使用冷铁,如使用以暗冷铁为好
2-1.尽量采用空心砂芯 2.砂芯强度过高避让性不佳
2-2.也可改用覆膜砂或水玻璃砂芯为佳
铸钢件不良发生原因与对策改善
2-3.铸件外形尽量呈圆弧状,避免锐角存在减少 裂纹发生
3.铸钢的熔点较高,钢液易 氧化、钢水的流动性差、收 缩 大 , 残留 应 力 高 (体收缩率为 10~14%,线 收缩为 1.8~2.8%)
3-1 采用合理的熔炼工艺和除气工艺去除金属 液中的氧化夹杂和气体等,防止产生冷裂纹。
3-2.必要时,铸件在切割浇冒口后,还要进行一 次时效热处理
1.工艺方案与充型速度慢产 生的表面气孔
1-1.铸钢工艺方案采用 1 : 1.1 : 1.2 减压模式设 计 效 果 会 比 较 好( 灰 铸使 用 铁 增 压式 对 效 果 较 好) 1-2.浇注速度加快后,浇注首温 1550~1560℃, 就可下降 20℃左右 1-3.浇口杯高度应高于冒口 10cm 以上,提高压 力促进气体排出
2.铸钢件生产技术比较难, 厂家焊补现象十分普遍
1-2. 对气孔缺陷应着眼于预防,即在清理前的 造型、浇注过程中防止出现气孔,这是积极的、 有效的解决办法 1-3.清理造型砂箱上的生锈渣片,可以避免锈渣 掉入模型表面,在造模过程中粘黏在砂模壁上, 浇注时形成大量气体 1-1.铸 疵 发生 位 置固 定 及数 量 多的 应予 对 策 改 善 1-2.铸 疵 发生 位 置不 固 定或 不 良数 量少 的 铸 件 建议不做对策 1-3.铸钢件不良品建议尽量焊补挽救,不轻易报 废 2-1.铸 钢 件生 产 厂家 必 需建 立 焊补 工艺 流 程 管 控 2-2.必需建制专业的焊补人员进行焊补作业 2-3.毛胚件与加工件应分开焊补,并对加工件及 行必要的保护加工件 2-4.大型铸件焊补,需进行预热措施 2-5.单一条裂纹铸件可焊补;缩孔及多条或多处 裂纹的铸件不可焊补 2-6.铸 件 较大 巢 孔必 需 以一 层 一层 堆焊 的 方 式 进行焊补 2-7.堆 焊 作业 必 须每 焊 一层 降 温保 温后 再 焊 下 一层,防止过热产生新的裂纹 2-8.焊补作业之前应对焊条进行预热
浅析铸钢件消失模铸造常见缺陷与防治措施
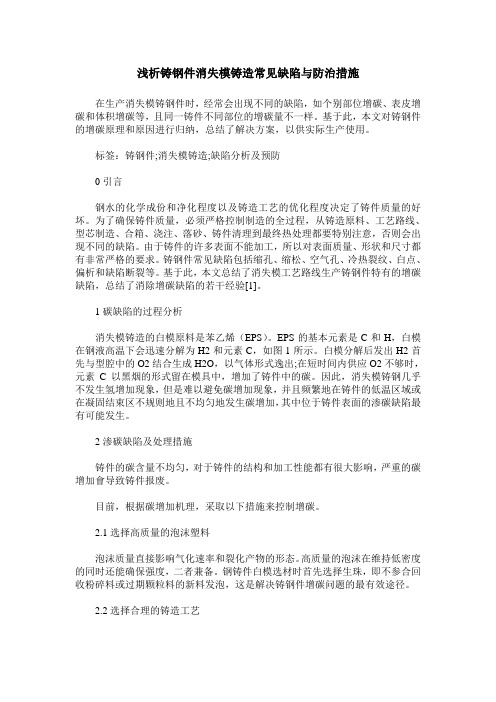
浅析铸钢件消失模铸造常见缺陷与防治措施在生产消失模铸钢件时,经常会出现不同的缺陷,如个别部位增碳、表皮增碳和体积增碳等,且同一铸件不同部位的增碳量不一样。
基于此,本文对铸钢件的增碳原理和原因进行归纳,总结了解决方案,以供实际生产使用。
标签:铸钢件;消失模铸造;缺陷分析及预防0引言钢水的化学成份和净化程度以及铸造工艺的优化程度决定了铸件质量的好坏。
为了确保铸件质量,必须严格控制制造的全过程,从铸造原料、工艺路线、型芯制造、合箱、浇注、落砂、铸件清理到最终热处理都要特别注意,否则会出现不同的缺陷。
由于铸件的许多表面不能加工,所以对表面质量、形状和尺寸都有非常严格的要求。
铸钢件常见缺陷包括缩孔、缩松、空气孔、冷热裂纹、白点、偏析和缺陷断裂等。
基于此,本文总结了消失模工艺路线生产铸钢件特有的增碳缺陷,总结了消除增碳缺陷的若干经验[1]。
1碳缺陷的过程分析消失模铸造的白模原料是苯乙烯(EPS)。
EPS的基本元素是C和H,白模在钢液高温下会迅速分解为H2和元素C,如图1所示。
白模分解后发出H2首先与型腔中的O2结合生成H2O,以气体形式逸出;在短时间内供应O2不够时,元素C以黑烟的形式留在模具中,增加了铸件中的碳。
因此,消失模铸钢几乎不发生氢增加现象,但是难以避免碳增加现象,并且频繁地在铸件的低温区域或在凝固结束区不规则地且不均匀地发生碳增加,其中位于铸件表面的渗碳缺陷最有可能发生。
2渗碳缺陷及处理措施铸件的碳含量不均匀,对于铸件的结构和加工性能都有很大影响,严重的碳增加會导致铸件报废。
目前,根据碳增加机理,采取以下措施来控制增碳。
2.1选择高质量的泡沫塑料泡沫质量直接影响气化速率和裂化产物的形态。
高质量的泡沫在维持低密度的同时还能确保强度,二者兼备。
钢铸件白模选材时首先选择生珠,即不参合回收粉碎料或过期颗粒料的新料发泡,这是解决铸钢件增碳问题的最有效途径。
2.2选择合理的铸造工艺为了防止白模气化和燃烧速度过快,模型装箱采取“能站不要躺”的原则,确保白模不会太快燃烧发气。
铸造工艺缺陷及解决措施
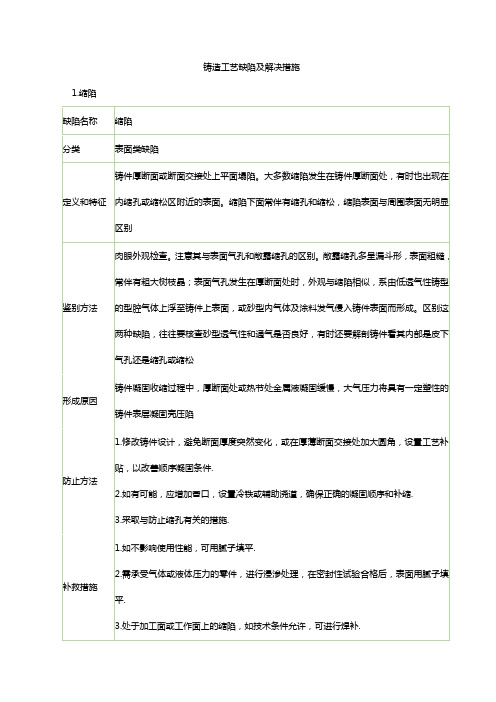
1.使用耐火度高的细粒原砂.
2.采用再生砂时,去除过细的砂粒、死烧粘土、灰分、金属氧化物、废金属、铁包砂及其他有害杂质,提高再生砂质量。定期补充适量新砂.
3.水是强烈氧化剂,应严格控制湿型砂水分,加入适量煤粉、沥青、碳氢化合物等含碳材料,在砂型中形成还原性气氛。但高压造型时应减少含碳材料加入量,以减少发气量.
防止方法
浇注前浇包中应备有足以充满铸型的金属液;浇注速度适当,浇注操作遵守工艺规程.
补救措施
概率因子
0.7
缺陷名称
未浇满
分类
残缺类缺陷
定义和特征
鉴别方法
形成原因
上箱过矮,金属的静压力小,易发生未浇满.
防止方法
保证有足够的液态金属压头充满型腔.
补救措施
浇注前浇包中应备有足以充满铸型的金属液;浇注速度适当,浇注操作遵守工艺规程
保证压铁的重量,箱夹的强度,数量足够,并选择合适的位置.
补救措施
概率因子
0.5
缺陷名称
跑火
分类
残缺类缺陷
定义和特征
鉴别方法
形成原因
金属液充型剧烈,易使型芯破裂造成跑火缺陷
防止方法
控制浇温,充型要平稳.
补救措施
概率因子
0.3
4.脉纹
缺陷名称
脉纹
分类
多肉类缺陷
定义和特征
鉴别方法
形成原因
硅砂在573℃发生相变膨胀,浇注时铸型表面易产生裂纹.
概率因子
3.跑火
缺陷名称
跑火
分类
残缺类缺陷
定义和特征
鉴别方法
形成原因
砂箱的接合面未清理干净封箱不妥等因素使跑火缺陷容易发生
防止方法
铸钢件缺陷产生的原因分析
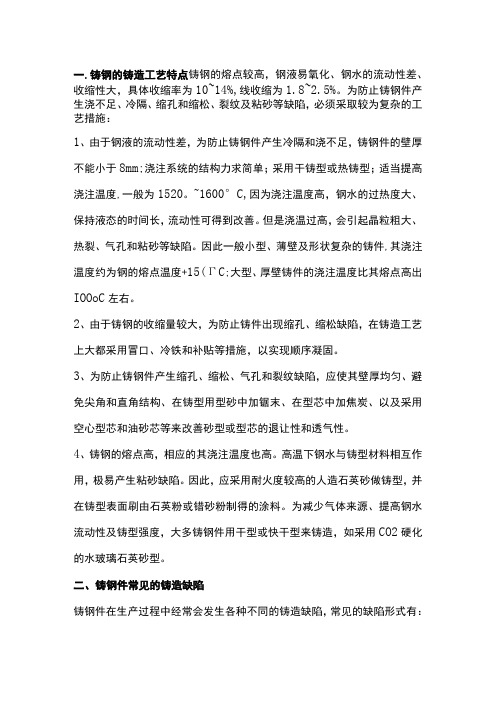
一.铸钢的铸造工艺特点铸钢的熔点较高,钢液易氧化、钢水的流动性差、收缩性大,具体收缩率为10~14%,线收缩为1.8~2.5%。
为防止铸钢件产生浇不足、冷隔、缩孔和缩松、裂纹及粘砂等缺陷,必须采取较为复杂的工艺措施:1、由于钢液的流动性差,为防止铸钢件产生冷隔和浇不足,铸钢件的壁厚不能小于8mm;浇注系统的结构力求简单;采用干铸型或热铸型;适当提高浇注温度,一般为1520。
~1600°C,因为浇注温度高,钢水的过热度大、保持液态的时间长,流动性可得到改善。
但是浇温过高,会引起晶粒粗大、热裂、气孔和粘砂等缺陷。
因此一般小型、薄壁及形状复杂的铸件,其浇注温度约为钢的熔点温度+15(ΓC;大型、厚壁铸件的浇注温度比其熔点高出IOOoC左右。
2、由于铸钢的收缩量较大,为防止铸件出现缩孔、缩松缺陷,在铸造工艺上大都采用冒口、冷铁和补贴等措施,以实现顺序凝固。
3、为防止铸钢件产生缩孔、缩松、气孔和裂纹缺陷,应使其壁厚均匀、避免尖角和直角结构、在铸型用型砂中加锯末、在型芯中加焦炭、以及采用空心型芯和油砂芯等来改善砂型或型芯的退让性和透气性。
4、铸钢的熔点高,相应的其浇注温度也高。
高温下钢水与铸型材料相互作用,极易产生粘砂缺陷。
因此,应采用耐火度较高的人造石英砂做铸型,并在铸型表面刷由石英粉或错砂粉制得的涂料。
为减少气体来源、提高钢水流动性及铸型强度,大多铸钢件用干型或快干型来铸造,如采用CO2硬化的水玻璃石英砂型。
二、铸钢件常见的铸造缺陷铸钢件在生产过程中经常会发生各种不同的铸造缺陷,常见的缺陷形式有:砂眼、粘砂、气孔、缩孔、缩松、夹砂、结疤、裂纹等。
A)砂眼缺陷砂眼是由于金属液从砂型型腔表面冲下来的砂粒(块),或者在造型、合箱操作中落入型腔中的砂粒(块)来不及浮入浇冒系统,留在铸件内部或表面而造成的。
砂眼缺陷处内部或表面有充塞着型(芯)砂的小孔,是一种常见的铸造缺陷。
B)粘砂缺陷在铸件表面上,全部或部分覆盖着一层金属(或金属氧化物)与砂(或涂料)的混(化)合物或一层烧结构的型砂,致使铸件表面粗糙,难于清理。
连铸工作中的问题与总结
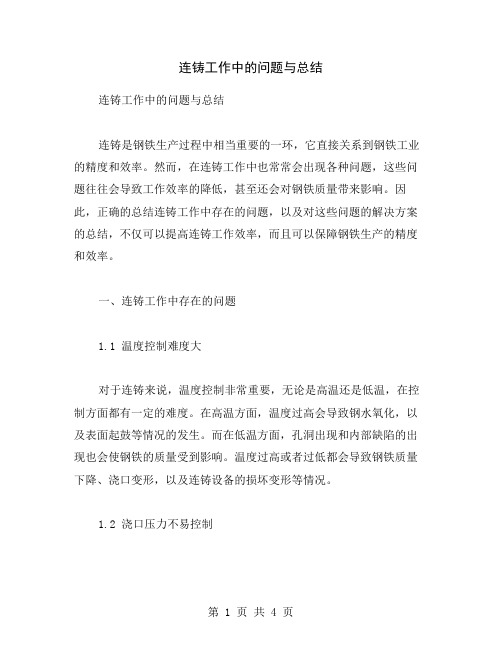
连铸工作中的问题与总结连铸工作中的问题与总结连铸是钢铁生产过程中相当重要的一环,它直接关系到钢铁工业的精度和效率。
然而,在连铸工作中也常常会出现各种问题,这些问题往往会导致工作效率的降低,甚至还会对钢铁质量带来影响。
因此,正确的总结连铸工作中存在的问题,以及对这些问题的解决方案的总结,不仅可以提高连铸工作效率,而且可以保障钢铁生产的精度和效率。
一、连铸工作中存在的问题1.1 温度控制难度大对于连铸来说,温度控制非常重要,无论是高温还是低温,在控制方面都有一定的难度。
在高温方面,温度过高会导致钢水氧化,以及表面起鼓等情况的发生。
而在低温方面,孔洞出现和内部缺陷的出现也会使钢铁的质量受到影响。
温度过高或者过低都会导致钢铁质量下降、浇口变形,以及连铸设备的损坏变形等情况。
1.2 浇口压力不易控制在连铸过程中,浇口的压力也是一个很重要的因素。
因为,当浇口的压力不稳定的时候,就会导致钢水流速的不稳定,出现一些问题,如不稳定的流速就会导致钢铁坯面整平不良、表面有凸起等问题;如果压力太大,就会导致过削钢铁表面,影响钢铁的外观质量。
1.3 浇注速度控制困难在连铸中,加工铸坯的速度对钢水流体的控制也会有影响。
高速浇注增加了钢水氧化和钢水粘滞度的风险,同时也并不利于钢水的混匀,会对钢铁产品的质量产生负面影响。
低速浇注的阻力较大,只能增加钢水流体的切应力,不能达到良好的混合效果。
因此,快并不一定好,慢也不一定准确,调节浇注速度是一项十分困难的任务。
1.4 非均匀铸坯厚度虽然连铸设备可以控制铸坯的厚度,但越往两端,铸坯的厚度也越难控制。
对于非均匀厚度的铸件,在铸造过程中,可能会出现鱼鳞状的铸态,严重影响铸件表面质量。
同时,厚度的不均匀也会导致温度不均匀,进一步影响铸坯质量。
二、针对问题的解决方案2.1 温度控制温度控制是一项非常重要的工作,如果能保持均衡的温度,并且能够避免过高或者过低的温度,就可以使得铸坯的质量得到保证。
铸造的困惑和难点

铸造的困惑和难点
1、工艺纪律好象与产品质量不是对应关系
不执行工艺纪律产品质量常常没问题、严格执行工艺纪律反而有时还出现质量问题,这是铸造工艺纪律常常很难执行的一个最大思想障碍和理解误区。
常见的困惑:
1)面对员工反问“我以前经常这样做没有问题啊”?专业技术人员常常哑然。
2)上次不按工艺生产跟踪后产品无异常,这次也出现了,抓还是不抓?管还是不管?应该不会有问题的吧?下不了决心。
2、影响因素不是单一、而都是错综复杂的
1)找到关键和主要影响因素是困难和复杂的
2)根据实践数据得出的结论经常是不统一甚至是相反
3)常常得出错误的结论,总是不能解决问题
4)需要大量的统计和分析工具
5)改变任何一个参数,对产品质量都是正面和副面作用并存的,解决了这个问题,又出现了那个问题,反反复复,焦头烂额,最后容易泄气,试验统计结果变来变去,越搞越糊涂,无法确定工艺方案。
3、要达到的最终目的不是直接而是间接测量的
1)产品需要的是可靠性,可靠性是由组织决定的,而我们测量的物理和化学等特性与组织并不能划等号。
2)金相和成分完全一样的产品,其机械性能的表现是不一样的。
3)机械性能一样的产品其可靠性有时是千差万别的。
六种铸件常见缺陷的产生原因及防止方法
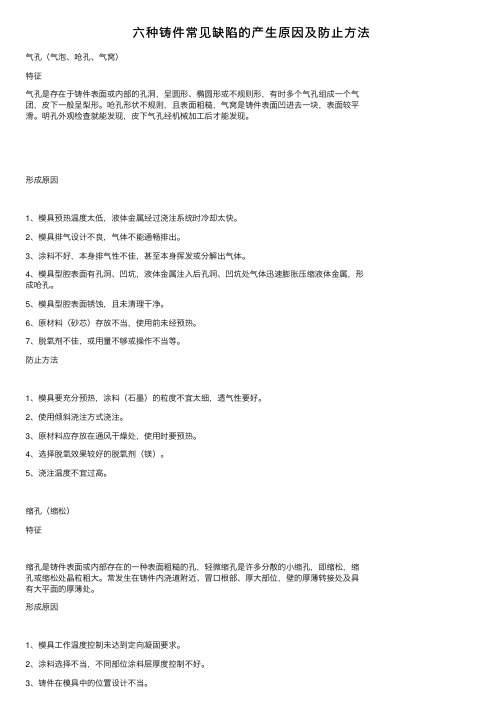
六种铸件常见缺陷的产⽣原因及防⽌⽅法⽓孔(⽓泡、呛孔、⽓窝)特征⽓孔是存在于铸件表⾯或内部的孔洞,呈圆形、椭圆形或不规则形,有时多个⽓孔组成⼀个⽓团,⽪下⼀般呈梨形。
呛孔形状不规则,且表⾯粗糙,⽓窝是铸件表⾯凹进去⼀块,表⾯较平滑。
明孔外观检查就能发现,⽪下⽓孔经机械加⼯后才能发现。
形成原因1、模具预热温度太低,液体⾦属经过浇注系统时冷却太快。
2、模具排⽓设计不良,⽓体不能通畅排出。
3、涂料不好,本⾝排⽓性不佳,甚⾄本⾝挥发或分解出⽓体。
4、模具型腔表⾯有孔洞、凹坑,液体⾦属注⼊后孔洞、凹坑处⽓体迅速膨胀压缩液体⾦属,形成呛孔。
5、模具型腔表⾯锈蚀,且未清理⼲净。
6、原材料(砂芯)存放不当,使⽤前未经预热。
7、脱氧剂不佳,或⽤量不够或操作不当等。
防⽌⽅法1、模具要充分预热,涂料(⽯墨)的粒度不宜太细,透⽓性要好。
2、使⽤倾斜浇注⽅式浇注。
3、原材料应存放在通风⼲燥处,使⽤时要预热。
4、选择脱氧效果较好的脱氧剂(镁)。
5、浇注温度不宜过⾼。
缩孔(缩松)特征缩孔是铸件表⾯或内部存在的⼀种表⾯粗糙的孔,轻微缩孔是许多分散的⼩缩孔,即缩松,缩孔或缩松处晶粒粗⼤。
常发⽣在铸件内浇道附近、冒⼝根部、厚⼤部位,壁的厚薄转接处及具有⼤平⾯的厚薄处。
形成原因1、模具⼯作温度控制未达到定向凝固要求。
2、涂料选择不当,不同部位涂料层厚度控制不好。
3、铸件在模具中的位置设计不当。
4、浇冒⼝设计未能达到起充分补缩的作⽤。
5、浇注温度过低或过⾼。
防⽌⽅法1、提⾼磨具温度。
2、调整涂料层厚度,涂料喷洒要均匀,涂料脱落⽽补涂时不可形成局部涂料堆积现象。
3、对模具进⾏局部加热或⽤绝热材料局部保温。
4、热节处镶铜块,对局部进⾏激冷。
5、模具上设计散热⽚,或通过⽔等加速局部地区冷却速度,或在模具外喷⽔,喷雾。
6、⽤可拆缷激冷块,轮流安放在型腔内,避免连续⽣产时激冷块本⾝冷却不充分。
7、模具冒⼝上设计加压装置。
8、浇注系统设计要准确,选择适宜的浇注温度。
球墨铸铁件生产中若干问题的探讨
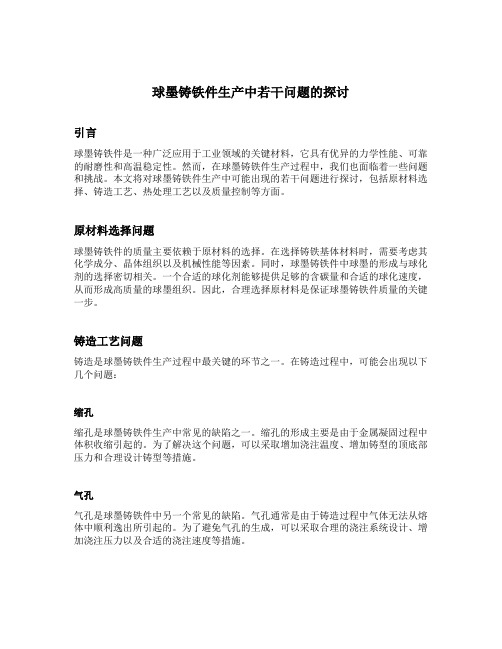
球墨铸铁件生产中若干问题的探讨引言球墨铸铁件是一种广泛应用于工业领域的关键材料,它具有优异的力学性能、可靠的耐磨性和高温稳定性。
然而,在球墨铸铁件生产过程中,我们也面临着一些问题和挑战。
本文将对球墨铸铁件生产中可能出现的若干问题进行探讨,包括原材料选择、铸造工艺、热处理工艺以及质量控制等方面。
原材料选择问题球墨铸铁件的质量主要依赖于原材料的选择。
在选择铸铁基体材料时,需要考虑其化学成分、晶体组织以及机械性能等因素。
同时,球墨铸铁件中球墨的形成与球化剂的选择密切相关。
一个合适的球化剂能够提供足够的含碳量和合适的球化速度,从而形成高质量的球墨组织。
因此,合理选择原材料是保证球墨铸铁件质量的关键一步。
铸造工艺问题铸造是球墨铸铁件生产过程中最关键的环节之一。
在铸造过程中,可能会出现以下几个问题:缩孔缩孔是球墨铸铁件生产中常见的缺陷之一。
缩孔的形成主要是由于金属凝固过程中体积收缩引起的。
为了解决这个问题,可以采取增加浇注温度、增加铸型的顶底部压力和合理设计铸型等措施。
气孔气孔是球墨铸铁件中另一个常见的缺陷。
气孔通常是由于铸造过程中气体无法从熔体中顺利逸出所引起的。
为了避免气孔的生成,可以采取合理的浇注系统设计、增加浇注压力以及合适的浇注速度等措施。
夹杂物是球墨铸铁件中可能出现的另一个问题。
它主要指的是非金属夹杂物,如氧化物、硫化物等。
夹杂物的生成往往与熔体中的气体和杂质有关。
为了减少夹杂物的产生,需要采取适当的熔炼和净化措施,以提高熔体的纯净度。
热处理工艺问题热处理是球墨铸铁件生产过程中不可或缺的一部分,它能够改善球墨铸铁件的力学性能和组织结构。
然而,在热处理过程中也可能出现以下一些问题:马氏体组织不均匀球墨铸铁在热处理过程中需要通过控制冷却速度形成良好的马氏体组织。
然而,由于铸铁件的不均匀性,很容易引起马氏体组织的不均匀分布。
为了解决这个问题,可以通过合理的工艺控制和提高冷却速度的方法来改善马氏体组织的均匀性。
铸造可能遇到的问题和解决方案

铸造可能遇到的问题和解决方案标题,铸造中常见问题及解决方案。
在铸造过程中,常常会遇到一些问题,这些问题可能会影响产品的质量和生产效率。
以下是一些铸造中常见的问题以及可能的解决方案。
1. 气孔和气泡。
气孔和气泡是铸造中常见的质量问题,可能会导致产品强度不足或者外观质量不佳。
这可能是由于熔融金属中的气体未能完全排除所致。
解决方案,采取适当的浇注系统设计,确保熔融金属能够充分充填模具,同时使用合适的除气剂和浇口设计来减少气孔和气泡的产生。
2. 热裂纹。
热裂纹是由于金属在冷却过程中产生的应力超过了其承受能力
而引起的。
这可能会导致产品在使用过程中出现裂纹。
解决方案,通过合理的冷却控制和合适的金属合金选择,可以减少热裂纹的发生。
此外,预热模具和采用合适的退火工艺也可以有效减少热裂纹的产生。
3. 金属收缩。
金属在冷却过程中会收缩,如果不加以控制,可能会导致产品尺寸不准确甚至变形。
解决方案,通过合理的浇注系统设计和冷却控制,可以减少金属收缩对产品质量的影响。
此外,采用合适的模具设计和金属合金选择也可以减少金属收缩带来的问题。
总之,铸造过程中可能会遇到各种质量问题,但通过合理的工艺控制和技术手段,这些问题是可以得到解决的。
只有不断改进工艺和技术,才能确保铸造产品的质量和稳定性。
铸钢件气孔缺陷的分析及预防

铸钢件气孔缺陷的分析及预防
铸钢件是一种重要的金属零件,广泛应用于各种机械设备和工程结构中。
然而,由于制造和铸造过程中可能发生气孔缺陷,影响其性能和寿命。
因此,对铸钢件气孔缺陷的分析和预防是非常重要的。
首先,分析铸钢件气孔缺陷的原因。
气孔缺陷是在铸造过程中由于气体存在所产生的孔洞。
常见的原因有以下几点:
1.铸造工艺不合理。
例如,铸造温度过低或过高,浇注速度过快或过慢,模具设计不合理等,都会导致气孔的产生。
2.原料质量问题。
铸造原料杂质含量高或含水量过多也会导致气孔的产生。
3.浇注系统不完善。
例如,浇口设计不合理、浇注系统中存在堵塞或过多的曲折通道等都会导致气孔的产生。
其次,预防铸钢件气孔缺陷可以从以下几个方面入手。
2.选择优质的原材料。
减少杂质含量、控制含水量等,有助于减少气孔的产生。
3.完善浇注系统。
设计合理的浇口和通道,以及设置无死角的通道,可以避免气孔的产生。
最后,对于已经产生的铸钢件气孔缺陷,可以采用以下方法处理。
1.打孔。
对于小型的气孔,可以通过钻孔或冲孔等方式将气孔的部分打通,减少对零件性能的影响。
2.热处理。
通过热处理的方式,可以将气孔的位置和体积减小,并达到改善铸钢件性能的目的。
综上所述,铸钢件气孔缺陷的分析和预防是非常重要的。
在铸造工艺、原材料选择和浇注系统设计等方面采取合理的措施,可以有效地降低气孔的产生,从而提高铸钢件的性能和寿命。
同时,对于已经产生的气孔缺陷,也可以通过打孔和热处理等方式来得到有效地处理。
铸钢件常见质量问题及主要影响因素汇总

-3-
(2)机械性能 A.热处理 化学成分决定后,热处理是影响机械性能的关键因素,要 有正确的热处理工艺和正确的操作方法。化学成分影响热 处理工艺,因此同种牌号的钢种化学成分波动不能大。 B.取样位置的方法 抗拉试棒和冲击试块的取样位置如下:
3.造型方法 自硬砂在操作过程中变形小,有效地保证铸件的形状尺寸精度; 自硬砂起模太早,强度不够,砂型和砂芯会变形; 砂芯的哈夫面不平,影响铸件尺寸。 放置不当,会引起砂型(芯)的变形。 涂料堆集会影响铸件的尺寸。 4.合箱操作 合箱是将砂型,砂芯装配起来,对铸件的形状尺寸影响很大,最大的影响
是砂芯位置和错箱。
-5-。
二.如何保证铸件的形状尺寸
1.合理的工艺措施 (1)合适的工艺参数:缩水,工艺补正量,反变形量等。 (2)合理的工艺方案。 2.模型 模型是决定铸件形状尺寸准确性的主要因素。曲面形状, 空间形状,非规则部位的尺寸,壁厚几乎完全由模具形成, 生产中一是测量困难,二是难以控制,这就要求模具一定 要尺寸、形状准确。 模具的基本要求:分模型的技术要求和管理要求。 (1)材料:种类,级别,干燥程度; (2)结构; (3)尺寸,平直度; (4)表面状况,光洁度,油漆的质量和种类; (5)使用方面的要求。 -6-
-15-
(4)采取措施消除铸件中的孤立热节;
(5)用冷铁延长冒口的补缩距离和急冷无法补贴的局部孤立 热节; (6)减少钢水中的低熔点夹杂物,如FeO,FeS,MnO2, SiO2, 等,炼钢时使这些夹杂物进入渣中,用底注包浇注,钢水在 包中适当的镇静时间等。
-16-
七.粘砂
铸钢件常见缺陷之一 1.形式:分机械粘砂和化学粘砂两种。
铸造产生的缺陷及防止措施
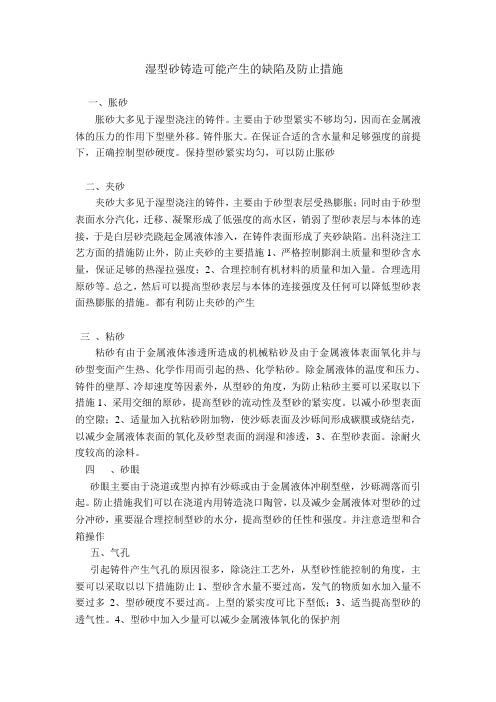
湿型砂铸造可能产生的缺陷及防止措施一、胀砂胀砂大多见于湿型浇注的铸件。
主要由于砂型紧实不够均匀,因而在金属液体的压力的作用下型壁外移。
铸件胀大。
在保证合适的含水量和足够强度的前提下,正确控制型砂硬度。
保持型砂紧实均匀,可以防止胀砂二、夹砂夹砂大多见于湿型浇注的铸件,主要由于砂型表层受热膨胀;同时由于砂型表面水分汽化,迁移、凝聚形成了低强度的高水区,销弱了型砂表层与本体的连接,于是白层砂壳跷起金属液体渗入,在铸件表面形成了夹砂缺陷。
出科浇注工艺方面的措施防止外,防止夹砂的主要措施1、严格控制膨润土质量和型砂含水量,保证足够的热湿拉强度;2、合理控制有机材料的质量和加入量。
合理选用原砂等。
总之,然后可以提高型砂表层与本体的连接强度及任何可以降低型砂表面热膨胀的措施。
都有利防止夹砂的产生三、粘砂粘砂有由于金属液体渗透所造成的机械粘砂及由于金属液体表面氧化并与砂型变面产生热、化学作用而引起的热、化学粘砂。
除金属液体的温度和压力、铸件的壁厚、冷却速度等因素外,从型砂的角度,为防止粘砂主要可以采取以下措施1、采用交细的原砂,提高型砂的流动性及型砂的紧实度。
以减小砂型表面的空隙;2、适量加入抗粘砂附加物,使沙砾表面及沙砾间形成碳膜或烧结壳,以减少金属液体表面的氧化及砂型表面的润湿和渗透,3、在型砂表面。
涂耐火度较高的涂料。
四、砂眼砂眼主要由于浇道或型内掉有沙砾或由于金属液体冲刷型壁,沙砾凋落而引起。
防止措施我们可以在浇道内用铸造浇口陶管,以及减少金属液体对型砂的过分冲砂,重要湿合理控制型砂的水分,提高型砂的任性和强度。
并注意造型和合箱操作五、气孔引起铸件产生气孔的原因很多,除浇注工艺外,从型砂性能控制的角度,主要可以采取以以下措施防止1、型砂含水量不要过高,发气的物质如水加入量不要过多2、型砂硬度不要过高。
上型的紧实度可比下型低;3、适当提高型砂的透气性。
4、型砂中加入少量可以减少金属液体氧化的保护剂六、裂纹铸件裂纹有很多形式,除了合金性质、浇注工艺和铸件表面结构的原因外,各种能够减少砂型膨胀。
铸造工艺常见的缺陷及质量控制措施
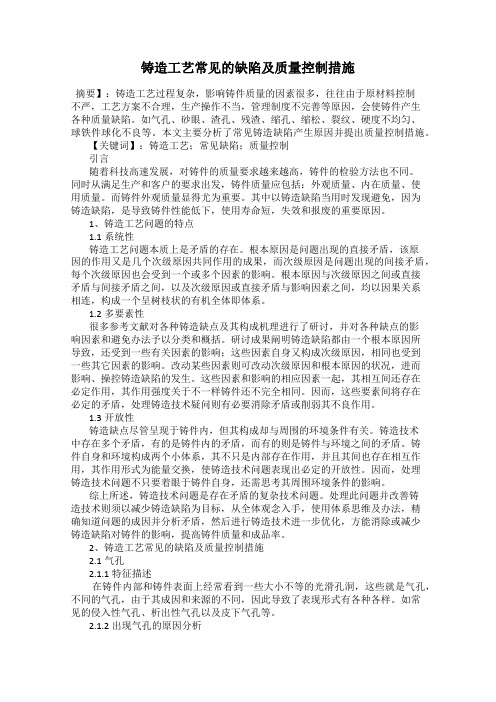
铸造工艺常见的缺陷及质量控制措施摘要】:铸造工艺过程复杂,影响铸件质量的因素很多,往往由于原材料控制不严,工艺方案不合理,生产操作不当,管理制度不完善等原因,会使铸件产生各种质量缺陷。
如气孔、砂眼、渣孔、残渣、缩孔、缩松、裂纹、硬度不均匀、球铁件球化不良等。
本文主要分析了常见铸造缺陷产生原因并提出质量控制措施。
【关键词】:铸造工艺;常见缺陷;质量控制引言随着科技高速发展,对铸件的质量要求越来越高,铸件的检验方法也不同。
同时从满足生产和客户的要求出发,铸件质量应包括:外观质量、内在质量、使用质量。
而铸件外观质量显得尤为重要。
其中以铸造缺陷当用时发现避免,因为铸造缺陷,是导致铸件性能低下,使用寿命短,失效和报废的重要原因。
1、铸造工艺问题的特点1.1系统性铸造工艺问题本质上是矛盾的存在。
根本原因是问题出现的直接矛盾,该原因的作用又是几个次级原因共同作用的成果,而次级原因是问题出现的间接矛盾,每个次级原因也会受到一个或多个因素的影响。
根本原因与次级原因之间或直接矛盾与间接矛盾之间,以及次级原因或直接矛盾与影响因素之间,均以因果关系相连,构成一个呈树枝状的有机全体即体系。
1.2多要素性很多参考文献对各种铸造缺点及其构成机理进行了研讨,并对各种缺点的影响因素和避免办法予以分类和概括。
研讨成果阐明铸造缺陷都由一个根本原因所导致,还受到一些有关因素的影响;这些因素自身又构成次级原因,相同也受到一些其它因素的影响。
改动某些因素则可改动次级原因和根本原因的状况,进而影响、操控铸造缺陷的发生。
这些因素和影响的相应因素一起,其相互间还存在必定作用,其作用强度关于不一样铸件还不完全相同。
因而,这些要素间将存在必定的矛盾,处理铸造技术疑问则有必要消除矛盾或削弱其不良作用。
1.3开放性铸造缺点尽管呈现于铸件内,但其构成却与周围的环境条件有关。
铸造技术中存在多个矛盾,有的是铸件内的矛盾,而有的则是铸件与环境之间的矛盾。
铸件自身和环境构成两个小体系,其不只是内部存在作用,并且其间也存在相互作用,其作用形式为能量交换,使铸造技术问题表现出必定的开放性。
铸造工艺缺陷及解决措施
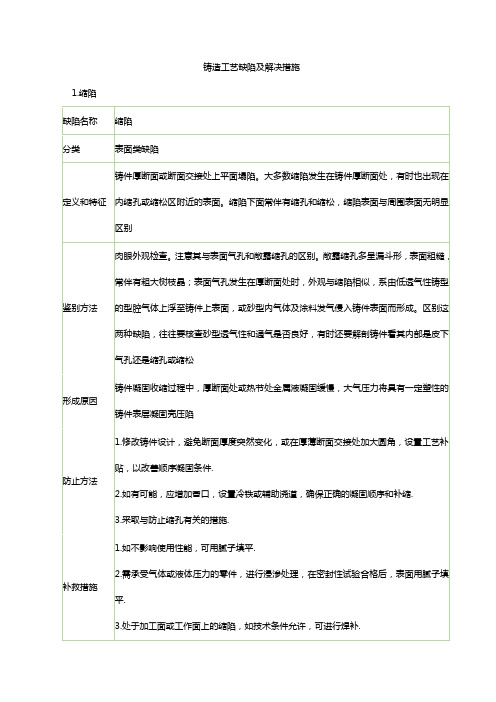
概率因子
0.3
缺陷名称
脉纹
分类
多肉类缺陷
定义和特征
鉴别方法
形成原因
浇温高,浇注时间长,树脂砂膨胀厉害,型芯易产生裂纹.
防止方法
控制浇注温度,浇注速度适中.
补救措施
概率因子
0.3
缺陷名称
脉纹
分类
多肉类缺陷
定义和特征
鉴别方法
形成原因
型芯中的局部过热处,易膨胀开裂
防止方法
在局部过热的地方采用特种砂或增厚涂层的厚度
形成原因
铸件凝固收缩过程中,厚断面处或热节处金属液凝固缓慢,大气压力将具有一定塑性的铸件表层凝固壳压陷
防止方法
1.修改铸件设计,避免断面厚度突然变化,或在厚薄断面交接处加大圆角,设置工艺补贴,以改善顺序凝固条件.
2.如有可能,应增加冒口,设置冷铁或辅助浇道,确保正确的凝固顺序和补缩.
3.采取与防止缩孔有关的措施.
3.易氧化合金钢在还原性或中性气氛中浇注.
4.调整合金成分以提高其流动性,适当提高浇注温度和浇注速度,防止金属液在浇注过程中氧化,改进型砂和涂料成分以防止型壁与金属液发生化学反应,包内静置足够时间并加强挡渣,金属型铸造时适当提高型温 5.在浇注系统中设置过滤网和集渣包
补救措施
有皱皮缺陷的铸件通常不会报废,不加工表面的皱皮可用砂轮打磨掉,加工表面的皱皮一般可机械加工掉
鉴别方法
肉眼外观检查。易于同其他表面缺陷相区别。象皮状皱皮有较深的网状沟槽,是球墨铸铁件和镁合金铸件特有的缺陷,根据合金种类易与一般皱皮相区别
形成原因
1.镁球墨铸铁在加镁处理时形成的化合物(氧化物、硫化物、硅酸盐等),通常以薄膜形式分散在金属液中,在浇包中上浮缓慢,浇注时随金属液进入铸型,并上浮至铸件上表面,离心铸造时则聚集在铸件内壁,
谈铸钢熔炼方面的几个问题

谈铸钢熔炼方面的几个问题摘要:铸造行业是国民经济发展的支柱行业之一,为人们生产和生活提供了必须的物质。
但是在其长期性发展中,还存在着一系列技术难题,本文对铸铁熔炼中的问题进行了简要分析,为当前工作提供有效参考。
关键词:铸钢;熔炼;问题;对策我国铸造行业最大问题是铸件质量差,这个“软肋”在铸件内在质量上可以看出,在这方面我国落后于其他工业国家。
我国在国际市场上的竞争力就是依靠价格,这使我国铸造企业的利润低,导致企业处于有心无力的状态,特别是研发、技术、条件和治理等方面,这些为我国铸造行业的发展带来了阻力。
为了改善这种局面,针对性对以下三个问题进行探讨:1 炼清洁钢, 提高铸钢件冶金质量铸钢件冶金质量涉及到方方面面,我开始从基础谈起。
首先从钢液精炼方面,其要与铸件的质量要求相匹配。
在工业生产中是以价值为导向,提高铸钢件的冶金质量要重视规格。
1.1 充分脱氧的重要性在炼钢过程中, 钢液氧化必不可少。
炼钢时先从脱氢、氮开始,接着清除金属内的夹杂物,这些都依赖氧化脱碳完成。
当炼好后,还要脱除其中的氧,这样才能保证钢的质量。
在熔炼时使用了不氧化法,但大气中的氧也会对钢造成影响,并且很多材料将氧带进钢液中。
因此脱氧是关键。
脱氧时要防止二次氧化,这样才能保证钢液处于脱氧的状态。
1.2 脱氧不充分时,铸件会出现气孔熔炼结束后,出现钢液脱氧不彻底的问题,主要是液流发生了二次氧化,特别是在出钢、浇注时, 当钢液进入铸型时出现凝固和温度下降, 这时处在铸型界面内的钢液中的Fe O增加,Fe O会与碳反应生成CO, 这样就形成了皮下气孔。
钢是经过凝固后形成的合金,以硬皮形式存在,这种硬皮是由细小柱状晶构成,硬皮在钢液浇注到铸型过程中形成, 一般出现在钢液/铸型的界面上,细小柱状晶垂直于界面并尖端向内,当硬皮体积收缩后会出现微小的孔隙, 这为气泡的形成创造了外部条件。
析出的初生晶体会使其表面钢液内碳的含量发生变化后形成富碳层,温度的改变和晶粒的增加,钢液中Fe O含量也在变化。
- 1、下载文档前请自行甄别文档内容的完整性,平台不提供额外的编辑、内容补充、找答案等附加服务。
- 2、"仅部分预览"的文档,不可在线预览部分如存在完整性等问题,可反馈申请退款(可完整预览的文档不适用该条件!)。
- 3、如文档侵犯您的权益,请联系客服反馈,我们会尽快为您处理(人工客服工作时间:9:00-18:30)。
浅析铸钢工艺的常见问题
摘要:在当今发展社会,铸钢冷却壁越来越被人们关注,技术也在不断的改进和创新。
铸钢冷却壁作为换代高炉冷却壁,它与铸铁冷却壁相比有着本质上的性能提升。
本文主要介绍了铸钢冷却壁铸造过程中各工序的要点,并从模样制作及造型方面进行了分析探讨。
关键词:模样制作;铸钢冷却壁;铸造工艺;高炉冷却设备
1 模样制作
1.1 模样材质及缩尺的选择
在高炉中使用的冷却壁,一般一层的数量大约是40块,适合小批量手工生产。
本厂在铸钢冷却壁的生产中使用CO2水玻璃砂造型,要求木模强度高,尺寸精确且不易变形,确保能满足一个批量的生产。
一般来说,在凝固过程中,冷却壁本体和冷却壁内水管的收缩是不一致的。
根据本厂的生产经验,冷却壁本体的收缩要稍大于冷却水管。
冷却壁本体的收缩和冷却壁的结构、内部冷却水管的分布状况等因素有关;而冷却水管的收缩和水管的壁厚、水管在浇注过程中的防熔穿措施等因素有关。
本厂在试制的时候冷却壁本体选用20‰的缩尺,冷却水管选用18‰的缩尺,然后根据试制结果及时修正各种参数。
1.2 砖槽部位的模样设计
冷却壁热面镶耐火砖用的砖槽部位是铸造难点之一,砖槽部位的砂型造型方法一般有两种。
第一种是将砖槽部位的齿状砂型设计成砂芯,通过下芯的方式来形成砖槽型腔,如图1。
但是该方法有以下缺点:大多数冷却壁的热面都是锥面,每条砖槽芯的曲面半径和长度都不一样,工人在下芯的时候不易区分,影响造型效率;且在浇注过程中,砖槽芯容易被钢液推倒造成铸件报废。
第二种方法是,做木模整体实样,将砖槽处阻碍起模的部分做成活块,如图2。
但缺点是活块较薄,容易吸湿变形,对木模的制作要求较高。
生产中可以根据冷却壁的结构采用最合适的方法。
2 造型
2.1 砖槽部位砂型
热面砖槽是铸钢冷却壁的铸造难点之一,如果处理不当,会使砖槽处出现热粘砂、气孔等缺陷。
缺陷难以清理,使砖槽尺寸难以保证,甚至导致铸件报废。
所以本厂在造型的工序中,在砖槽部位使用10 mm左右的铬铁矿砂作面砂,这样可以有效地防止热粘砂,并且易于清理,使砖槽部分表面光洁,尺寸精确。
2.2 浇注系统
浇注系统的设置非常重要,铸钢冷却壁的浇注系统是由耐火砖管组成,采用开放式的浇注系统,保证钢液平稳充型、不会从浇注系统中喷射出来。
一般从冷却壁侧面或底面引进内浇道,如图3。
内浇道在埋设的时候要注意,不要使内浇道口直接对着冷却水管,避免钢液冲刷冷却水管导致其熔穿。
2.3 冷却水管的防熔穿措施
在铸钢冷却壁的铸造过程中,防止冷却水管熔穿,并使其“熔而不化”,是铸造工艺中的最大难点。
防熔穿措施主要有两种。
(1)从外部防止冷却水管熔穿。
从外部防止冷却水管熔穿,可以在水管外焊制一层随型内冷铁笼,或在水管外表涂刷隔热涂层。
此类方法虽然可以从一定程度上防止水管熔穿,但是如果设计不当,将会严重影响冷却水管和冷却壁本体之间的熔合率,使水管的散热能力极大地降低,这也削弱了铸钢冷却壁导热性能好的优势。
2)从内部防止冷却水管熔穿。
从内防止水管熔穿,可以在冷却水管内部通入气体/固体冷却介质。
通气可以使用氮气或者其他稀有气体,通气能够防止水管内壁在浇注过程中被氧化,并且保护冷却水管使其“熔而不穿”。
几乎所有形状的冷却水管都可以用通气的方式来冷却,但是通气需要额外的通气设备,并且通气时的气压、流速等诸多参数需要根据具体情况,反复摸索才能得出。
通入(灌入)固体冷却介质到冷却水管中是一种比较简易并且可靠的方法,对灌入的固体介质的要求是:蓄热能力大,有较强的激冷作用;热膨胀系数小,热稳定性好;不发生化学反应,不生成气体;不熔化、不粘连管壁、易清理。
通常使用多种材料混合而成。
但是,这种方法只适用于形状简单的冷却水管,如“U”形管。
对于形状复杂的“W”形管、“S”形管,灌入、导出固体冷却介质都十分麻烦,增加了清整的难度。
另外,固体冷却介质成本较高,应该及时回收利用。
在生产过程中,可以根据不同情况,将两种思路结合运用,达到防止冷却水管熔穿的目的。
3 熔炼与浇注
熔炼与浇注是铸钢冷却壁铸造过程中的决定性环节,其中主要有以下几方面的因素需要重视。
3.1 成分控制
本厂生产的铸钢冷却壁的材质大部分属于ZG230-450,冷却水管的材质为20 G。
冷却壁的材质与冷却水管的材质相近,并且可以满足一般高炉内的工况要求,在熔炼时须保证钢液成分符合牌号要求。
3.2 浇注温度
要使冷却水管在浇注过程中“熔而不穿”,关键是控制浇注温度。
要做好浇注时温度的控制,从出钢时就要开始着手。
出钢时测定温度,如果温度过高,可以通过延长出钢时间、出钢后钢包静置一段时间等方法来降低钢液温度,确保浇注时温度合适。
本厂在浇注时使用红外线测温仪Raytek Marathon MR来监控钢液温度,确保浇注温度在工艺规定的范围内。
本厂生产的某型号单层“4进4出”U型冷却水管的冷却壁,材质为ZG230-450,本体壁厚135 mm,冷却壁本体连同浇注系统和冒口共重1.8 t左右。
工艺规定浇注温度在1 580~1 540 ℃,浇注时一个钢包连续浇注6块冷却壁,钢包至少装载11 t钢液。
开始浇注第一块冷却壁的同时测温,及时反馈钢液温度并做出调整直到浇注结束,保证整个浇注过程中钢液的温度在规定范围内。
从生产结果看来,在温度范围内浇注出来的冷却壁内部冷却水管“熔而不穿”,如图4。
外表面光洁无热粘砂。
3.3 浇注速度控制
在浇注开始时,要避免钢液流速过快,从内浇道喷射出冲刷冷却水管、以致熔穿水管的情况。
在整个浇注过程中要遵守“先慢后快”的原则:浇注开始时,要求钢液平稳充型;等砂型型腔内的钢液液面达到一定高度时可以逐渐加大浇注速度,迅速充型,直到浇注结束。
如果浇注速度过慢会导致上型坍塌等铸造缺陷。
4 清整
由于在铸件难以清理的部位使用了铬铁矿砂,清砂时易剥离,所以清整工序
相对简单。
冷却壁本体上要合理设置工艺吊把,方便冷却壁的吊运以及倒出冷却水管内的固体冷却介质,避免冷却水管在吊运时被刮伤、撞弯。
铸件在粗清整后,进行退火热处理。
在退火时,要做好冷却水管的防氧化措施。
亦有文献指出,可以通过利用高炉烘炉来消除冷却壁铸造内应力,如果可以通过该工艺消除铸造应力,那么可以无须设计繁杂的热处理工序,大大节约冷却壁制作成本并提高质量延长其使用寿命,进而使高炉的寿命进一步提高。
5 结束语
通过合理的模样设计以及在难清整的部位放置铬铁矿砂,可以使铸钢冷却壁尺寸准确、外表光滑;在冷却水管内部通入冷却介质、在冷却水管外设置冷铁或刷隔热涂层可以有效的保护水管不熔穿、不变形。
并且能够顺利的通过水压、通球试验;严格控制浇注温度和浇注速度可以保证冷却壁内冷却水管不被熔穿,达到“熔而不化”的临界状态,使冷却水管和冷却壁本体熔合紧密,保证铸钢冷却壁导热性能好的优势。
注:文章内所有公式及图表请用PDF形式查看。