采用电渣重熔工艺冶炼高质量轴承钢
电弧炉冶炼滚动轴承钢的冶炼操作讲解

电弧炉冶炼滚动轴承钢的冶炼操作讲解电弧炉是一种用电能产生高温熔炼金属的设备,广泛应用于钢铁行业。
下面,我将给你讲解电弧炉冶炼滚动轴承钢的操作步骤。
冶炼滚动轴承钢的第一步是准备工作。
操作人员需要检查电弧炉设备是否正常运行,确认废钢以及其他冶炼辅料(如铁合金、渣化剂等)是否齐全。
此外,还需要准备足够的电能供应和冷却水。
接下来是装料过程。
操作人员先将电弧炉保温层的上部覆盖层开启,然后将锭块或废钢块放入炉膛中,尽量使之均匀分布。
冶炼滚动轴承钢一般采用多次装料的方式,每次装料数量不宜过多,以免超出炉膛容量。
装料完成后,开始进行熔化过程。
首先,操作人员需要将保温层的上部覆盖层关闭,以便提高炉内温度。
随后,将电极下降至距离料面适当的位置,点火并慢慢增加电流。
炉膛内的料块开始熔化,并且由于电弧的作用,金属液体开始受到搅拌和搅碎。
在熔化过程中,还需要添加适量的渣化剂。
这些渣化剂可以吸附炉膛中的杂质和不良气体,提高冶炼的纯度。
渣化剂的添加通常在熔化过程中根据操作人员的经验来决定,以保证最佳的冶炼效果。
当炉内金属液体达到目标温度后,进入合金化阶段。
此时,操作人员需要添加适量的合金元素或铁合金。
这些合金元素的添加将改变钢的成分和性能,使其满足滚动轴承钢的需求。
合金化阶段需要根据冶炼配方和合金元素含量来调整,以保证合金元素的均匀分布。
合金化完成后,进行净化操作。
净化是为了进一步提高钢的纯度,通常采用气体还原或真空净化的方式。
操作人员将适量的还原剂或净化气体引入炉膛,通过化学反应或物理吸附去除金属液体中的杂质和不良气体。
最后,是铸型过程。
冶炼好的钢液通常需要通过连铸工艺进行连铸,并形成所需的规格和形状。
操作人员将钢液倒入连铸机的浇注箱中,通过连铸结晶器冷凝为连续的铸坯。
铸坯进一步加工后,就成为了滚动轴承的原材料。
以上就是电弧炉冶炼滚动轴承钢的操作步骤。
每个步骤都需要操作人员根据钢种和工艺要求来进行操作,并且要严格控制每一步骤的温度、时间和添加量,以确保最终产品的质量。
精炼渣系对钢中夹杂物的影响
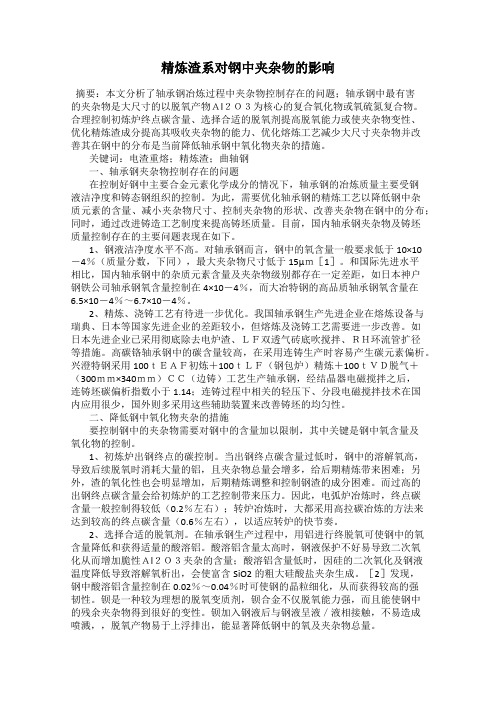
精炼渣系对钢中夹杂物的影响摘要:本文分析了轴承钢冶炼过程中夹杂物控制存在的问题;轴承钢中最有害的夹杂物是大尺寸的以脱氧产物Al2O3为核心的复合氧化物或氧硫氮复合物。
合理控制初炼炉终点碳含量、选择合适的脱氧剂提高脱氧能力或使夹杂物变性、优化精炼渣成分提高其吸收夹杂物的能力、优化熔炼工艺减少大尺寸夹杂物并改善其在钢中的分布是当前降低轴承钢中氧化物夹杂的措施。
关键词:电渣重熔;精炼渣;曲轴钢一、轴承钢夹杂物控制存在的问题在控制好钢中主要合金元素化学成分的情况下,轴承钢的冶炼质量主要受钢液洁净度和铸态钢组织的控制。
为此,需要优化轴承钢的精炼工艺以降低钢中杂质元素的含量、减小夹杂物尺寸、控制夹杂物的形状、改善夹杂物在钢中的分布;同时,通过改进铸造工艺制度来提高铸坯质量。
目前,国内轴承钢夹杂物及铸坯质量控制存在的主要问题表现在如下。
1、钢液洁净度水平不高。
对轴承钢而言,钢中的氧含量一般要求低于10×10-4%(质量分数,下同),最大夹杂物尺寸低于15μm[1]。
和国际先进水平相比,国内轴承钢中的杂质元素含量及夹杂物级别都存在一定差距,如日本神户钢铁公司轴承钢氧含量控制在4×10-4%,而大冶特钢的高品质轴承钢氧含量在6.5×10-4%~6.7×10-4%。
2、精炼、浇铸工艺有待进一步优化。
我国轴承钢生产先进企业在熔炼设备与瑞典、日本等国家先进企业的差距较小,但熔炼及浇铸工艺需要进一步改善。
如日本先进企业已采用彻底除去电炉渣、LF双透气砖底吹搅拌、RH环流管扩径等措施。
高碳铬轴承钢中的碳含量较高,在采用连铸生产时容易产生碳元素偏析。
兴澄特钢采用100tEAF初炼+100tLF(钢包炉)精炼+100tVD脱气+(300mm×340mm)CC(边铸)工艺生产轴承钢,经结晶器电磁搅拌之后,连铸坯碳偏析指数小于1.14;连铸过程中相关的轻压下、分段电磁搅拌技术在国内应用很少,国外则多采用这些辅助装置来改善铸坯的均匀性。
GCr15性能要求
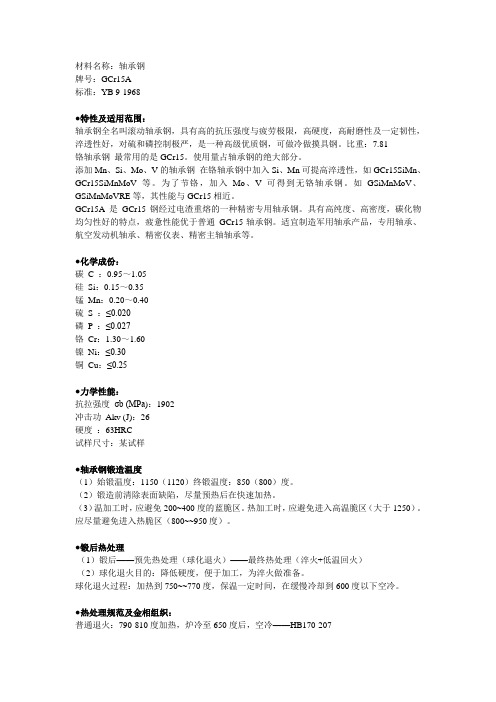
材料名称:轴承钢牌号:GCr15A标准:YB 9-1968●特性及适用范围:轴承钢全名叫滚动轴承钢,具有高的抗压强度与疲劳极限,高硬度,高耐磨性及一定韧性,淬透性好,对硫和磷控制极严,是一种高级优质钢,可做冷做摸具钢。
比重:7.81铬轴承钢最常用的是GCr15。
使用量占轴承钢的绝大部分。
添加Mn、Si、Mo、V的轴承钢在铬轴承钢中加入Si、Mn可提高淬透性,如GCr15SiMn、GCr15SiMnMoV等。
为了节铬,加入Mo、V可得到无铬轴承钢。
如GSiMnMoV、GSiMnMoVRE等,其性能与GCr15相近。
GCr15A是GCr15钢经过电渣重熔的一种精密专用轴承钢。
具有高纯度、高密度,碳化物均匀性好的特点,疲惫性能优于普通GCr15轴承钢。
适宜制造军用轴承产品,专用轴承、航空发动机轴承、精密仪表、精密主轴轴承等。
●化学成份:碳C :0.95~1.05硅Si:0.15~0.35锰Mn:0.20~0.40硫S :≤0.020磷P :≤0.027铬Cr:1.30~1.60镍Ni:≤0.30铜Cu:≤0.25●力学性能:抗拉强度σb (MPa):1902冲击功Akv (J):26硬度:63HRC试样尺寸:某试样●轴承钢锻造温度(1)始锻温度:1150(1120)终锻温度:850(800)度。
(2)锻造前清除表面缺陷,尽量预热后在快速加热。
(3)温加工时,应避免200~400度的蓝脆区。
热加工时,应避免进入高温脆区(大于1250)。
应尽量避免进入热脆区(800~~950度)。
●锻后热处理(1)锻后——预先热处理(球化退火)——最终热处理(淬火+低温回火)(2)球化退火目的:降低硬度,便于加工,为淬火做准备。
球化退火过程:加热到750~~770度,保温一定时间,在缓慢冷却到600度以下空冷。
●热处理规范及金相组织:普通退火:790-810度加热,炉冷至650度后,空冷——HB170-207等温退火:790-810度加热,710-720度等温,空冷——HB207-229球化退火:轴承钢预先热处理是球化退火。
电渣重熔技术在中国的应用和发展
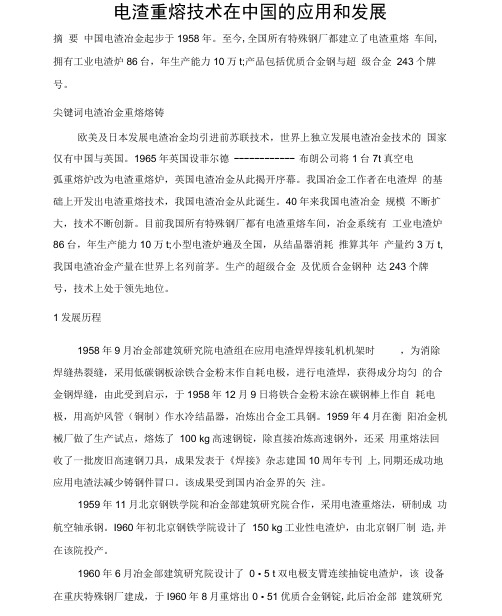
电渣重熔技术在中国的应用和发展摘要中国电渣冶金起步于1958年。
至今,全国所有特殊钢厂都建立了电渣重熔车间,拥有工业电渣炉86台,年生产能力10万t;产品包括优质合金钢与超级合金243个牌号。
尖键词电渣冶金重熔熔铸欧美及日本发展电渣冶金均引进前苏联技术,世界上独立发展电渣冶金技术的国家仅有中国与英国。
1965年英国设菲尔德 ------------ 布朗公司将1台7t真空电弧重熔炉改为电渣重熔炉,英国电渣冶金从此揭开序幕。
我国冶金工作者在电渣焊的基础上开发出电渣重熔技术,我国电渣冶金从此诞生。
40年来我国电渣冶金规模不断扩大,技术不断创新。
目前我国所有特殊钢厂都有电渣重熔车间,冶金系统有工业电渣炉86台,年生产能力10万t;小型电渣炉遍及全国,从结晶器消耗推算其年产量约3万t,我国电渣冶金产量在世界上名列前茅。
生产的超级合金及优质合金钢种达243个牌号,技术上处于领先地位。
1发展历程1958年9月冶金部建筑研究院电渣组在应用电渣焊焊接轧机机架时,为消除焊缝热裂缝,采用低碳钢板涂铁合金粉末作自耗电极,进行电渣焊,获得成分均匀的合金钢焊缝,由此受到启示,于1958年12月9日将铁合金粉末涂在碳钢棒上作自耗电极,用高炉风管(铜制)作水冷结晶器,冶炼出合金工具钢。
1959年4月在衡阳冶金机械厂做了生产试点,熔炼了100 kg高速钢锭,除直接冶炼高速钢外,还采用重熔法回收了一批废旧高速钢刀具,成果发表于《焊接》杂志建国10周年专刊上,同期还成功地应用电渣法减少铸钢件冒口。
该成果受到国内冶金界的矢注。
1959年11月北京钢铁学院和冶金部建筑研究院合作,采用电渣重熔法,研制成功航空轴承钢。
I960年初北京钢铁学院设计了150 kg工业性电渣炉,由北京钢厂制造,并在该院投产。
1960年6月冶金部建筑研究院设计了0 • 5 t双电极支臂连续抽锭电渣炉,该设备在重庆特殊钢厂建成,于I960年8月重熔出0 • 51优质合金钢锭,此后冶金部建筑研究院帮助重庆特殊钢厂、大冶钢厂建立电渣车间,开发产品。
轴承钢的生产与工艺技术
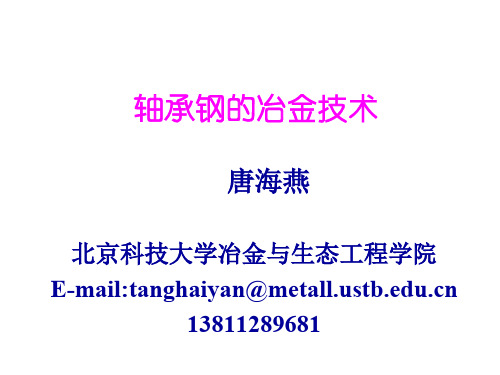
日本小仓钢厂连铸轴承钢的残余元素的控制
元素
含量
P
S
Cu
Ni
Ti
炉 数 143
143
143
平均值 /% 0.0084 0.0049 0.013
标准偏差 0.0015 0.0009 0.005
143 0.013 0.002
143 0.011 0.0003
13
A12O3夹杂、点状不变形夹杂及含钛的碳氮化物夹杂对轴 承的疲劳失效影响最为严重。
为减少氧化渣的带入,采用无渣出钢技术或真空 除渣技术。
采用以RH 为主的真空脱气炉外精炼装置,进一步 降低钢中氧、氢和氮含量。
29
国外的生产特点
1)规模大:提高生产率,降低成本 2)除渣:采用EBT、真空吸渣和换钢包除 渣等技术,将氧
化渣彻底排除 3)铝脱氧:精炼前用铝沉淀脱氧 4)长时间搅拌:促使夹杂物上浮 5)高碱度渣精炼:碱度控制4~6 6)连铸:由于轴承钢的碳含量高,生产的铸坯容易产生偏
高15倍,T[O]≤5ppm时寿命则可提高30倍。 国外平均已控制在8ppm左右,山阳特殊钢公司已降到
5.4ppm,最低降到3-4ppm,瑞典SKF一般为5-8ppm。 国内10ppm左右,兴澄特钢5~7ppm.
10
氮的存在易使钢中形成氮化钛,一般控制 在50ppm以下。
氢为间隙元素,对轴承钢有害无益,在压 力加工应力条件下,会产生白点缺陷,且 分布极不均匀。OVAKO公司实物中[H]均控 制在≤1ppm。
世界各国的冶金工作者长期以来,从纯净度出发,主要从 事两方面的工作,一是减少钢中夹杂物的含量,二是控制 夹杂物的成分、尺寸、分布,即改善夹杂物的性质和形态。
减少夹杂物的数量,主要是降低钢中的氧含量,其手段是 炉外精炼;改善夹杂物的性质和形态则主要依赖于精炼渣 的化学成分。
高品质轴承钢的冶炼工艺和理论研究.
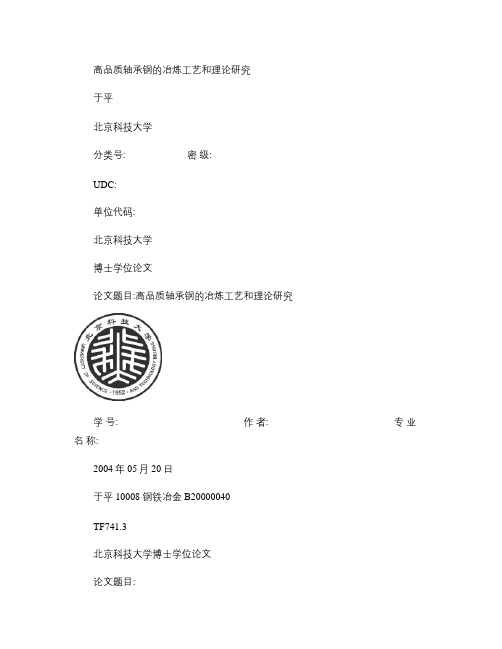
1.7课题研究的目的及内容(39
1.7.1课题来源及研究的目的和意义(39
独创性说明
本人郑重声明:所呈交的论文是我个人在导师指导下进行的研究工作及取得研究成果。尽我所知,除了文中特别加以标注和致谢的地方外,论文中不包含其他人已经发表或撰写的研究成果,也不包含为获得北京科技大学或其他教育机构的学位或证书所使用过的材料。与我一同工作的同志对本研究所做的任何贡献均已在论文中做了明确的说明并表示了谢意。
技术探讨我国轴承钢管的发展现状及生产工艺

技术探讨我国轴承钢管的发展现状及⽣产⼯艺冯志坚8⽉初,海关总署发布数据显⽰,6⽉份,我国出⼝轴承44708万套,出⼝⾦额达到195064万元,同⽐分别增长5.0%和4.2%;上半年累计出⼝255963万套,出⼝⾦额达到110.6亿元,同⽐分别增长0.9%和2.0%。
其中,轴承钢管作为轴承套圈的原材料,在我国轴承⼯业发展过程中起到了重要作⽤。
⽬前,中国已是装备制造⼤国,但实现“强”还有⼀定距离,其原因之⼀,是装备的轴承性能影响了整机的关键性能。
轴承钢是⽤于设备轴承制造的⼀种重要基础钢种,在众多品种的钢铁产品中被称为“钢中之王”,⼴泛应⽤于运输机械(汽车、⾼速列车等)、⼯程机械、冶⾦、⽯油化⼯、发电、航空航天、军⼯、风电和海洋⼯程等领域。
轴承钢的质量优劣,直接决定了重⼤装备和精密装备轴承的好坏。
轴承钢应具有长寿命、⾼精度、⾼刚度和⾼耐磨性等性能。
同时,轴承钢也是检验项⽬多、质量要求严、⽣产难度⼤的钢种之⼀。
作为“钢中之王”家族成员,轴承钢管是轴承钢⼆⽕成材产品。
作为轴承套圈⽤钢,其⽣产有其特殊性和严格要求。
由于我国整体冶炼⽔平限制和⽣产企业⾃⾝存在的问题,以及轴承套圈加⼯技术的发展现状,我国轴承钢管在质量、⽣产成本、材料利⽤率等⽅⾯的优势并不明显,其发展空间受到挤压。
⽬前,我国轴承钢管⽣产存在哪些问题?我国轴承钢管的⽣产⼯艺现状如何?轴承钢管今后的发展思路是什么?这些都是需要探讨的问题。
轴承钢管整体现状有待改变⽬前,我国国内轴承钢管产量仅占轴承钢总产量的8%,与发达国家占⽐20%~30%相⽐,仍有很⼤差距。
在轴承钢管品质⽅⾯,国内产品也存在品质稳定性差、疲劳寿命短、洁净度低等问题。
我国轴承钢管的应⽤,⼀般局限于普通轴承的轴承套圈⽤料,⾼端轴承套圈仍依赖进⼝。
1品种结构不合理,坯料供给⽭盾突出我国很多钢铁企业均存在钢材品种“全⽽不专”的⽣产现状。
⼀些企业的产品品种覆盖板、管、型、材和特殊钢材,普通钢材同质化问题严重,低端竞争呈现⽩热化。
轴承钢的分类
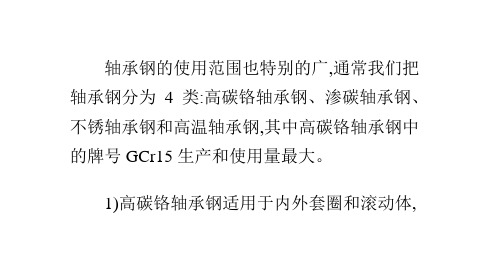
她只能这么想,因为她连他的模样都没来得及小瞥一下,他就过去了
严格的要求,并对部分钢材规定逐支进行超声波 检验,进行末端淬透性检验。多制成棒材,用于农 业及其他机械等部门。
3)不锈轴承钢适用于有不锈和抗大气腐蚀 的轴承以及精密微型轴承。牌号 G95Cr18、
G102Cr18Mo 等,为高碳高铬马氏体型钢,对化学 成分、硬度、低倍组织和高倍组织都作出严格规 定,要求采用电弧炉并经电渣重熔(可采用非真 空感应炉或真空感应炉冶炼并经电渣重熔)工艺 生产。多用于腐蚀条件下的轴承。
她只能这么想,因为她连他的模样都没来得及小瞥一下,他就过去了
夹杂物、显微孔隙、显微组织、碳化物不均匀度、 脱碳深度检验;供冷镦和冲压用钢还要进行顶锻 检验。这类钢要用电炉冶炼,还要求进行真空脱 气处理或其他精炼方法冶炼。这类钢适用于制造 通用的轴承套圈和滚动体。
2)渗碳轴承钢适用于有冲击和抗震要求的 轴承。牌号 G20CrMo、G20CrNiMoG20CrN12Mo 等, 属于低碳合金结构钢。对冶炼方法、化学成分、 力学性能、低倍组织(酸浸低倍和塔形发纹)、高 倍组织(非金属夹杂物、晶粒度、显微组织)规定
5)特殊轴承材料适用于有防磁和抗特殊介 质腐蚀的轴承,如 G52f2c9a 易博
她只能这么想,因为她连他的模样都没来得及小瞥一下,他就过去了
轴承钢的使用范围也特别的广,通常我们把 轴承钢分为 4 类:高碳铬轴承钢、渗碳轴承钢、 不锈轴承钢和高温轴承钢,其中高碳铬轴承钢中 的牌号 GCr15 生产和使用量最大。
1)高碳铬轴承钢适用于内外套圈和滚动体,
回火硬度为 HRC61-64。牌号 GCr15、GCr15SiMn 等,要求钢中 P、 S 含量不大于 0.025%,并限制 Ni、 Cu 等 残 余 元 素 含 量 , 钢 中 氧 含 量 控 制 在 (12X10-6)%之内。规定进行酸浸低倍组织检验; 根据要求,进行淬火断口检验;规定进行非金属
高铁轴承钢的技术质量特性识别及重点研制方向
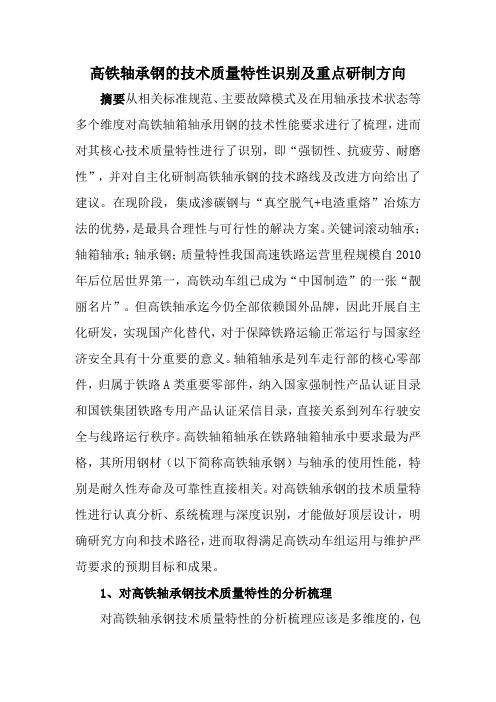
高铁轴承钢的技术质量特性识别及重点研制方向摘要从相关标准规范、主要故障模式及在用轴承技术状态等多个维度对高铁轴箱轴承用钢的技术性能要求进行了梳理,进而对其核心技术质量特性进行了识别,即“强韧性、抗疲劳、耐磨性”,并对自主化研制高铁轴承钢的技术路线及改进方向给出了建议。
在现阶段,集成渗碳钢与“真空脱气+电渣重熔”冶炼方法的优势,是最具合理性与可行性的解决方案。
关键词滚动轴承;轴箱轴承;轴承钢;质量特性我国高速铁路运营里程规模自2010年后位居世界第一,高铁动车组已成为“中国制造”的一张“靓丽名片”。
但高铁轴承迄今仍全部依赖国外品牌,因此开展自主化研发,实现国产化替代,对于保障铁路运输正常运行与国家经济安全具有十分重要的意义。
轴箱轴承是列车走行部的核心零部件,归属于铁路A类重要零部件,纳入国家强制性产品认证目录和国铁集团铁路专用产品认证采信目录,直接关系到列车行驶安全与线路运行秩序。
高铁轴箱轴承在铁路轴箱轴承中要求最为严格,其所用钢材(以下简称高铁轴承钢)与轴承的使用性能,特别是耐久性寿命及可靠性直接相关。
对高铁轴承钢的技术质量特性进行认真分析、系统梳理与深度识别,才能做好顶层设计,明确研究方向和技术路径,进而取得满足高铁动车组运用与维护严苛要求的预期目标和成果。
1、对高铁轴承钢技术质量特性的分析梳理对高铁轴承钢技术质量特性的分析梳理应该是多维度的,包括相关标准规范、主要故障模式和在用轴承技术状态等,这样才有可能得出比较全面系统准确的识别与认知。
1.1相关标准规范1.1.1欧洲标准EN 12080国际上公认的铁路轴箱轴承权威技术标准是欧洲标准EN 12080:“Railway applications-Axleboxes-Rolling bearings”,最早发布于1998年3月,迄今为止又进行了2次修订。
对1998,2007和2017版进行比较,尤其关注最新2017版所修订的内容,可以厘清轴箱轴承的基本技术要求以及技术进步脉络。
发展中的轨道交通车辆用轴承
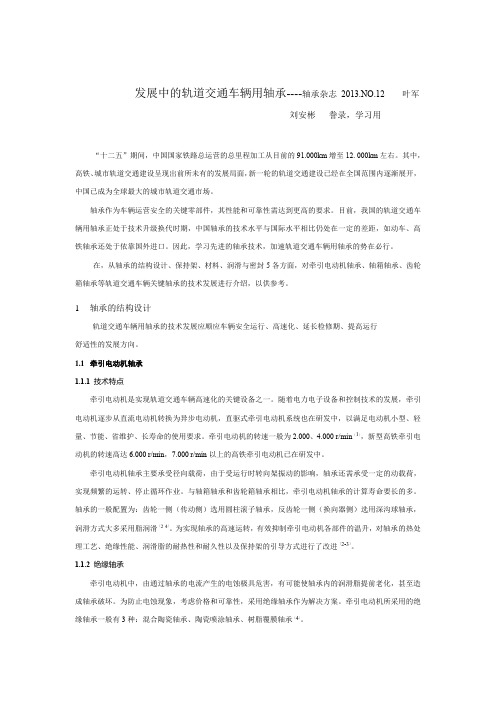
发展中的轨道交通车辆用轴承----轴承杂志2013.NO.12 叶军刘安彬誊录,学习用“十二五”期间,中国国家铁路总运营的总里程加工从目前的91.000km增至12. 000km左右。
其中,高铁、城市轨道交通建设呈现出前所未有的发展局面,新一轮的轨道交通建设已经在全国范围内逐渐展开,中国已成为全球最大的城市轨道交通市场。
轴承作为车辆运营安全的关键零部件,其性能和可靠性需达到更高的要求。
目前,我国的轨道交通车辆用轴承正处于技术升级换代时期,中国轴承的技术水平与国际水平相比仍处在一定的差距,如动车、高铁轴承还处于依靠国外进口。
因此,学习先进的轴承技术,加速轨道交通车辆用轴承的势在必行。
在,从轴承的结构设计、保持架、材料、润滑与密封5各方面,对牵引电动机轴承、轴箱轴承、齿轮箱轴承等轨道交通车辆关键轴承的技术发展进行介绍,以供参考。
1轴承的结构设计轨道交通车辆用轴承的技术发展应顺应车辆安全运行、高速化、延长检修期、提高运行舒适性的发展方向。
1.1牵引电动机轴承1.1.1 技术特点牵引电动机是实现轨道交通车辆高速化的关键设备之一。
随着电力电子设备和控制技术的发展,牵引电动机逐步从直流电动机转换为异步电动机,直驱式牵引电动机系统也在研发中,以满足电动机小型、轻量、节能、省维护、长寿命的使用要求。
牵引电动机的转速一般为2.000、4.000 r/min〔1〕,新型高铁牵引电动机的转速高达6.000 r/min,7.000 r/min以上的高铁牵引电动机已在研发中。
牵引电动机轴承主要承受径向载荷,由于受运行时转向架振动的影响,轴承还需承受一定的动载荷,实现频繁的运转、停止循环作业。
与轴箱轴承和齿轮箱轴承相比,牵引电动机轴承的计算寿命要长的多。
轴承的一般配置为:齿轮一侧(传动侧)选用圆柱滚子轴承,反齿轮一侧(换向器侧)选用深沟球轴承,润滑方式大多采用脂润滑〔2-4〕。
为实现轴承的高速运转,有效抑制牵引电动机各部件的温升,对轴承的热处理工艺、绝缘性能、润滑脂的耐热性和耐久性以及保持架的引导方式进行了改进〔2-3〕。
轴承钢的质量要求及其缺陷
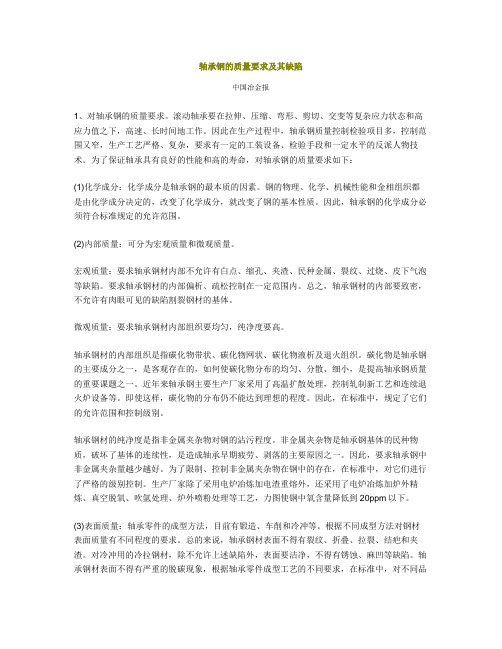
轴承钢的质量要求及其缺陷中国冶金报1、对轴承钢的质量要求。
滚动轴承要在拉伸、压缩、弯形、剪切、交变等复杂应力状态和高应力值之下,高速、长时间地工作。
因此在生产过程中,轴承钢质量控制检验项目多,控制范围又窄,生产工艺严格、复杂,要求有一定的工装设备、检验手段和一定水平的反派人物技术。
为了保证轴承具有良好的性能和高的寿命,对轴承钢的质量要求如下:(1)化学成分:化学成分是轴承钢的最本质的因素。
钢的物理、化学、机械性能和金相组织都是由化学成分决定的,改变了化学成分,就改变了钢的基本性质。
因此,轴承钢的化学成分必须符合标准规定的允许范围。
(2)内部质量:可分为宏观质量和微观质量。
宏观质量:要求轴承钢材内部不允许有白点、缩孔、夹渣、民种金属、裂纹、过烧、皮下气泡等缺陷。
要求轴承钢材的内部偏析、疏松控制在一定范围内。
总之,轴承钢材的内部要致密,不允许有肉眼可见的缺陷割裂钢材的基体。
微观质量:要求轴承钢材内部组织要均匀,纯净度要高。
轴承钢材的内部组织是指碳化物带状、碳化物网状、碳化物液析及退火组织。
碳化物是轴承钢的主要成分之一,是客观存在的,如何使碳化物分布的均匀、分散、细小,是提高轴承钢质量的重要课题之一。
近年来轴承钢主要生产厂家采用了高温扩散处理,控制轧制新工艺和连续退火炉设备等。
即使这样,碳化物的分布仍不能达到理想的程度。
因此,在标准中,规定了它们的允许范围和控制级别。
轴承钢材的纯净度是指非金属夹杂物对钢的沾污程度。
非金属夹杂物是轴承钢基体的民种物质,破坏了基体的连续性,是造成轴承早期疲劳、剥落的主要原因之一。
因此,要求轴承钢中非金属夹杂量越少越好。
为了限制、控制非金属夹杂物在钢中的存在,在标准中,对它们进行了严格的级别控制。
生产厂家除了采用电炉冶炼加电渣重熔外,还采用了电炉冶炼加炉外精炼、真空脱氧、吹氩处理、炉外喷粉处理等工艺,力图使钢中氧含量降低到20ppm以下。
(3)表面质量:轴承零件的成型方法,目前有锻造、车削和冷冲等。
电渣重熔冶炼技术

电渣重熔冶炼技术电渣重熔冶炼技术是一种先进的冶金技术,其主要应用于金属材料的回收和再利用。
该技术利用电弧加热,将废旧金属材料熔化,通过电渣的作用,将杂质分离出来,得到高纯度的金属材料,从而实现资源的有效利用和环境的保护。
一、电渣重熔冶炼技术的原理电渣重熔冶炼技术是利用电弧加热将废旧金属材料熔化,通过电渣的作用,将杂质分离出来,得到高纯度的金属材料。
在电渣重熔冶炼过程中,电极和金属材料之间形成的电弧产生高温,将金属材料熔化。
同时,电极和金属材料之间的电流产生电渣,电渣起到了隔离空气和杂质的作用,使金属材料被分离出来,从而得到高纯度的金属材料。
二、电渣重熔冶炼技术的应用1. 废旧金属材料的回收和再利用废旧金属材料中含有很多有价值的金属元素,如铁、铜、铝等。
这些金属元素可以通过电渣重熔冶炼技术进行回收和再利用,从而实现资源的有效利用和环境的保护。
2. 金属材料的精炼和纯化电渣重熔冶炼技术可以将金属材料中的杂质分离出来,得到高纯度的金属材料。
这一过程可以对金属材料进行精炼和纯化,提高其质量和性能。
3. 金属材料的合金化电渣重熔冶炼技术可以将不同种类的金属材料进行熔合,形成合金材料。
这些合金材料具有更好的性能和应用价值,可以广泛应用于冶金、机械制造、航空航天等领域。
三、电渣重熔冶炼技术的优点1. 能够回收和再利用废旧金属材料,实现资源的有效利用。
2. 能够精炼和纯化金属材料,提高其质量和性能。
3. 能够将不同种类的金属材料进行熔合,形成合金材料,具有更好的性能和应用价值。
4. 能够实现无污染生产,保护环境。
四、电渣重熔冶炼技术的发展趋势随着社会经济的快速发展,金属材料的需求量越来越大。
电渣重熔冶炼技术的应用将会越来越广泛,发展前景十分广阔。
未来,电渣重熔冶炼技术将会更加智能化、自动化,实现无人化生产。
同时,电渣重熔冶炼技术将会与其他领域的技术相结合,形成更加高效、环保、节能的新型冶金技术,为人类的发展和进步做出更大的贡献。
H13钢的应用现状
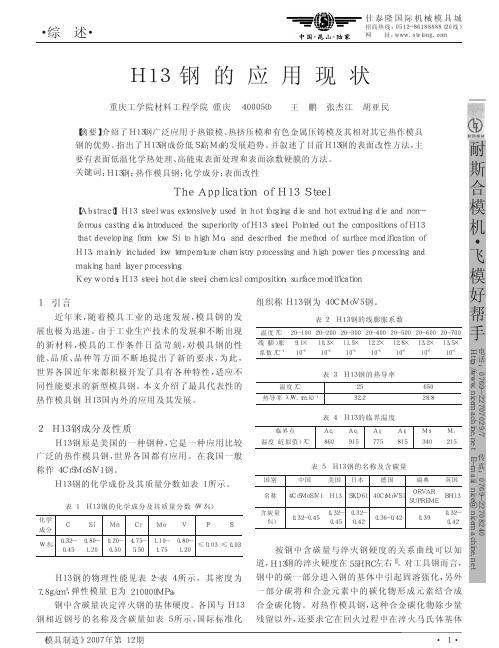
( 1) 预热处理明显地改 善了 H13 钢的 组织, 有 效 500℃~550℃分级淬火和油淬[18]。以100mm棒料的H13
消除了带状碳化物, 大大减少了粗大碳化物的数量, 钢为例, 油淬时, 棒料中心的冷却速度曲线不与TTT曲
可获得分布均匀、尺寸细小的碳化物组织。
线中的碳化物析出线相遇, 因此钢的冲击韧性不受影
含量的提高有利于增加材料的热强度, 但对韧度不利。 钼: 钼也是碳化物形成元素, 和铬一样, 可提高钢
的高温硬度和淬透性。此外, 钼还可细化晶粒, 减小回 火脆性。
钒: 钒比铬和钼更容易形成碳化物, 极少溶入铁 的固溶体中。钒的碳化物使钢具有良好的热硬性, 并
可细化晶粒, 提高钢的耐磨性。 硅: 硅是对铁素体进行置换固溶强化非常有效的
表 1 H13 钢的化学成分及其质量分数( W/%)
化学
C
Si Mn Cr Mo V
P
S
成分
传
表 5 H13 钢的名称及含碳量
真
国别
中国
美国 日本
德国
瑞典 英国
ORVAR
名称 4Cr5MoSiV1 H13 SKD61 40CrMoVSi
BH13
SUPREME
含炭量
0.32~ 0.32~
0.32~
0.32~0.45
钢的优势。指出了H13钢成份低Si高Mo的发展趋势。并叙述了目前H13钢的表面改性方法, 主
耐
要有表面低温化学热处理、高能束表面处理和表面涂敷硬膜的方法。
关键词: H13钢; 热作模具钢; 化学成分; 表面改性
斯
The Application of H13 Steel
合
【Abstr act】H13 steel was extensively used in hot forging die and hot extruding die and non-
重大装备用轴承钢关键技术开发

重大装备用轴承钢关键技术开发
重大装备用轴承钢关键技术开发涉及以下主要方面:
1. 钢种选择:选择适合重大装备用轴承钢的合金组成和特性,以满足高强度、高耐磨性、高抗腐蚀性等要求。
2. 熔炼技术:采用先进的熔炼工艺,如真空冶炼、电炉冶炼等,确保钢的纯净度和均匀性,减少夹杂物和非金属夹杂物的含量。
3. 热处理技术:确定适当的热处理工艺,包括淬火、回火等工艺,以实现钢的理想组织和性能。
4. 精密加工技术:开发适用于重大装备用轴承钢的精密加工工艺,包括切削、磨削、热处理等,以确保轴承的精度和表面质量。
5. 润滑技术:研究合适的润滑材料和润滑方式,以减少轴承的摩擦、磨损和能量损失,延长轴承寿命。
6. 检测技术:发展高效、准确的检测方法,如无损检测、金相检测、硬度检测等,以评估轴承钢的质量和性能。
7. 储存和保护技术:制定合理的储存和保护措施,以防止轴承钢受到氧化、腐蚀等损害,确保其性能稳定。
通过以上关键技术的开发和应用,可以提高重大装备用轴承钢的质量和性能,从而增加装备的可靠性和使用寿命。
国内外轴承的对比

期间提高轴承的使用性能和可靠性影响轴承产品使用性能和可靠性的因素很多,但轴承钢材料质量的优劣则对其有着直接影响。
换句话说,如果轴承钢材料自身的质量存在有一定的不足,想大幅度提高轴承产品的使用寿命和可靠性将成为一句空话。
轴承钢中氧含量的多少对钢中非金属夹杂物的数量起着决定性的作用,其含量的降低对提高轴承产品的使用寿命起着很大的作用,但对提高轴承产品可靠性方面的作用有一定的影响,并不是主要影响因素对于我国长期使用制造军用轴承产品的轴承钢是采用电渣重熔的冶炼方法生产的(检验标准为军甲—61),其中的含氧量高于采用真空脱气方法冶炼的轴承钢,但其使用寿命、尤其是可靠性方面大大地优于一般真空脱气轴承钢,原因是电渣重熔钢的结晶组织、非金属夹杂物和碳化物的颗粒大小及分布状态优于真空脱气钢。
由此说明,钢材的结晶组织、非金属夹杂物和碳化物的颗粒大小及分布状态是目前影响我国轴承产品使用寿命和可靠性的主要因素。
另外,在《高碳铬轴承钢》(GB/T18254)中关于非金属夹杂物检验评级是采用ASTME45中的图iii,即改型的JK图片,在钢坯上检验。
但从国外有关非金属夹杂物检验及对轴承使用寿命影响等有关资料报道来看,这种评级方法对于低氧量、高纯洁度轴承钢具有一定的局限性,已不能准确地评价轴承钢中的非金属夹杂物,国外已采用其它的检验方法进行评级,例如SAM方法等。
所以只有在以上方面有所突破,我国轴承钢的质量和轴承产品的质量才能真正迈上一个新的台阶,希望轴承钢生产企业在这方面给予高度的重视。
但从总体而言,我国生产的轴承钢表面质量与国外相比仍存在着明显的差距。
江苏兴澄钢铁有限公司生产的轴承钢表面质量较好,平均表面裂纹出现率都在0.7%以下。
1 润滑润滑脂的选用主要指深沟2 保持架材料,主要指专项应用,即时别的国产化,保持架材料和加工工艺也不行3 一些油孔的加工方式,油孔设计,包括位置和大小4 内外圈的壁厚差外圈也原来越薄,国内成都重型研究所在轧机轴承进行理论和实际试验,已经取得成果其余,包括哈瓦洛都是测绘后上线直接使用,效果很难判定。
- 1、下载文档前请自行甄别文档内容的完整性,平台不提供额外的编辑、内容补充、找答案等附加服务。
- 2、"仅部分预览"的文档,不可在线预览部分如存在完整性等问题,可反馈申请退款(可完整预览的文档不适用该条件!)。
- 3、如文档侵犯您的权益,请联系客服反馈,我们会尽快为您处理(人工客服工作时间:9:00-18:30)。
降低。因此, 我们认为金属熔池的浮升不是夹杂 物被去除的主要过程, 但元素在金属熔池中氧化 生成的夹杂物, 特别是其中的硅酸盐类大颗粒夹 杂物主要是靠金属熔池的浮升来去除。
表 2 结晶速度对夹杂物的评级的影响 T ab le 2 Crystallization rate inf luence on
evaluatin g the inc lu sion grade
!大型铸锻件 ∀ HEAVY CA ST ING AND FORG ING
N o. 3 M ay 2009
表 3 不同渣系下原始电极和 重熔金属的夹杂物评级分析
Tab le 3 O r iginal e lec trode at d ifferen t slag quotiety and the eva luation ana lysis of re m elting m e tal
为此我们进行了试验。首先对熔化电极末端
31
N o. 3 M ay 2009
!大型铸锻件 ∀ HEAVY CAST ING AND FORG ING
进行了研究。按试验条件 ( 1) 进行冶炼, 通入氩 气保护, 然后突然停电, 将电极迅速提出渣面。用 阳极切割机自中心沿纵向切开电极熔化末端, 用 oberhoffer试剂腐蚀显 示出熔化部分的铸 态结晶 区, 划出熔化和未熔化区分界线, 对全部视场中的 非金属夹杂物进行分析。用比 20 mm 的自耗电 极放大 20倍的相纸将全部非金属夹杂物记录下 来, 计算出熔化区、未熔化区单位面积的夹杂物面 积, 及单位面积夹杂数, 其结果见表 1、图 1。
K ey word s: e lectro slag re m e lting; bea ring stee;l inclusion; m e lting
现代工业的发展对轴承钢的要求日益严格, 为了保证轴承钢在高负荷、高速度条件下正常工 作, 对轴承钢的提纯和均匀化都有相当高的要求。 即轴承钢中的非金属夹杂物: 氧化物、硅酸盐 D i ergarten评级法不超过 0. 5级。显然, 这个要求是 非一般冶炼方法所能满足的。为此, 我们决定采 用电渣重熔工艺冶炼高质量轴承钢 [ 3~ 5] 。为了 更有效地控制轴承钢的质量, 我们就电渣重熔对 钢中夹杂物的去除过程进行了研究, 查明电渣重 熔提纯钢的主要发生阶段, 并以此为依据制定了 渣系、电制度、电极冶炼终脱氧制度。
2 试验结果及讨论
2. 1 电渣重熔提纯的过程 关于电渣重熔提纯的机理, 目前观点不统一。
有些学者 [ 5, 9] 认为: 电渣 重熔去除夹杂物 主要是 利用金属熔池的浮升。另一些学者 [ 10, 11 ] 则认为: 夹杂物的去除则是熔滴自耗电极末端向金属熔池 过渡时的渣洗结果。苏联学者的试验还证明电渣 重熔去硫过程主要发生在电极熔化末端。
炉渣 编号
炉渣的化学成分 ( 质量分数, % )
试验 炉数
C aO A l2 O3 CaF2 C aC2 /次
非金属夹杂物
试验 含量 (% )
片数
/个
氧化物和 硅酸盐
硫化物
原始电极 - - - ∋ 1 1 5 35 60 ∋ 2 1 20 30 50 ∋ 3 1 - - 100 ∋ 4 1 5 33 60 2
关键词: 电渣重熔; 轴 承钢; 夹杂物; 冶炼 中图分类号 : TF 14 文献标识码: B
M e lting the H igh Q uality B earing Steel by ESR T echno logy
Guo L ibo
Abstract: L itera tures 1& 2 show ed that: the converg ence o f non m eta llic inclusion in stee l is the roo t o f fatigue and breakage, espec ia lly those brittleness inc lusion like a lum ina and titan ium n itr ide, therefore, the con tro lling to the in clusion in bearing stee l is the key to guaran tee its qua lity. W e tested and researched the purification procedure of e lec tro slag re m e lting technology, m eanw hile, w e se t down the technology param e ters of ESR based on tested results. P ractical produc tion showed the effic iency o f new techno logy.
编号 铸锭结晶速度 试片数
非金属夹杂物的评级
/(m /h)
/个 氧化物 硫化物 . 48
17
1. 03 0. 5 0. 029 4
17
0. 65 0. 5 0. 115 7
# 面积小于 0. 05 ∃ 10- 3mm2 的夹杂物 % 面积等于 ( 0. 05~ 0. 10) ∃ 10- 3mm2 的夹杂物 & 面积等于 ( 0. 10~ 0. 20) ∃ 10- 3mm2 的夹杂物 ∃ 面积大于 0. 20 ∃ 10- 3mm2 的夹杂物 图 1 电极末端夹杂物分布图 (显微镜观察倍数 100倍 )
收稿日期: 2009 02 10
冷却水温: 60~ 70 电流: 800 A ~ 900 A 电压: 40 V ~ 42 V ( 2) 500kg工业电渣炉。双电极送进机构交 替工作, 采用连续抽锭式。变压器容量 240 kVA。 工艺制度为: 自耗电极: 85 mm 结晶器: 240 mm 渣系: M gO: 3% ; CaO: 5% ; A l2 O3: 32% ; CaF2: 6 0% 渣重: 19 kg 冷却水温: 60~ 70 电流: 3 000 A ~ 4 500 A 电压: 45 V ~ 55 V
F igure 1 Inc lusion d istr ibution picture at the end
of electrode ( m ultip le o fm icro scope: 100 tim es. )
表 1 熔化区、未熔化区单位面积内
夹杂物的面积及单位面积夹杂数
Tab le 1 In clusion propor tion and its quan tity
( 3) 在电极熔化末端温度最高, 我们用钨 钼 热电 偶 测 得 电 极 端 头 附 近 温 度 在 1 810 ~ 1 840 。
( 4) 电极熔化端头部分首先和炉渣作用, 原 始夹杂含量最高。 2. 2 炉渣成分对去除夹杂物的影响
在夹杂物被炉渣吸收的过程中, 起决定性因 素的是炉渣对夹杂物的吸附能力。一般来说, 钢 液和夹杂物间的界面张力 钢 夹杂 愈大, 炉渣和夹 杂物之间的界面张力 渣 夹杂 愈小, 夹杂物愈易被 炉渣吸附。
( 1) 在电极熔化末端熔滴形成的过程中钢渣 作用最充分。在电极末端锥体逐渐消失过程中几 乎任何一部分都有机会和渣相接触, 任何一部分 都有可能暴露在表面, 便于熔渣吸收。
( 2) 在电极熔化末端熔滴形成时间虽不及熔 池存在时间长, 但仍然比熔滴过渡时间长, 我们用 示波器测得在电极熔化末端熔滴形成过程一般为 ( 0. 23~ 0. 37) s, 而熔滴通过渣池时间按粘滞液体 中自由落体公式计算为 ( 0. 08~ 0. 11) s。
熔炼电规范 编号
电流 /A 电压 /V
∋ 1 1 5 35 60 10 59 0. 946 0. 67
∋ 1 4 5 40 55 4 31 0. 84 0. 62
表 5 不同熔炼电规范对去除夹杂物的影响 Table 5 D ifferen t re m e lting spec ifica tion
influence to the e lim ination of inc lu sion
1 试验设备和条件
试验是在两种炉子上进行的。炉子的特点及 试验条 件如下: ( 1) 20 kg 小型 电渣 炉。由 HG 1000小型电渣焊机改装, 变压器容量为 160 kVA。 工艺制度为:
自耗电极: 20 mm 结晶器: 100 mm 渣系: M gO: 3% ; CaO: 5% ; A l2 O3: 32% ; CaF2: 60% 渣重: 1. 5 kg
为了验证金属熔池中夹杂物的浮升对提纯的 影响, 我们通过改变结晶器尺寸来获得不同结晶 速度, 并进行分 析对比, 结果见 表 2。由表 2 可 知, 随着铸锭结晶速度的减慢, 钢锭中的氧化物、 硫化物没有改变, 仅点状硅酸盐夹杂物评级有所
32
电极熔化末端去除夹杂物的物理化学条件最 好, 我们认为有以下几个因素:
7 122 2. 26 2. 11 10 94 0. 946 0. 41 5 38 1. 09 0. 52 3 23 1. 129 0. 60 3 21 1. 31 0. 26
表 4 调整渣系后原始电极和 重熔金属的夹杂物评级分析 Tab le 4 O r ig inal e lectrode after the ad ju stm en t of slag quotiety and the eva luation ana lysis of re m elting m e tal
在我们的研究条件下, 钢液是固定的轴承钢, 所以我们只能从改变冶炼渣成分、改变电极原始 夹杂物性质种类、改善钢渣接触条件入手促进夹 杂物进入炉渣。
在试验过程中, 我们曾试验 4种渣系, 对原始 电极及重熔金属取样, 进行夹杂物评级对比, 结果 见表 3。从表 3 可知, 采用 4种 渣系进行电渣重 熔, 非金属夹杂物评级普遍下降。但以 ∋ 1 1号 渣 CaO A l2O 3 C aF2 为最佳。据此我们再进行调 整, 实验结果见表 4。从表 4可见, 随渣中 A l2 O3 的增加, 氧化物、硫化物评级都依次下降。