换热器汇总
板式换热器分类汇总

板式换热器分类汇总
一、按板式换热器分类
1)板翅式换热器
由封闭在带有冷、热流体进出口的集流箱中的换热板束构成。
板束由平板和波纹翅片交互叠合,钎焊固定而成。
冷、热流体流经平板两侧换热,翅片增加了传热面积,又促进了流体的湍动,并对设备有增强作用。
2)螺旋板换热器
由两张保持一定间距的平行金属板卷制而成,冷、热流体分别在金属板两侧的螺旋形通道内流动。
这种换热器的传热系数高(约比管壳式换热器高1~4倍),平均温度差大(因冷、热流体可作完全的逆流流动),流动阻力小,不易结垢;但维修困难。
使用压力不超过2MPa。
3)平板式换热器
由一定形状的波纹薄板和密封垫片交互叠合,并用框架夹紧组装而成。
冷、热流体分别在波纹板两侧的流道中流过,经板片进行换热。
波纹板通常由厚度为0.5~3mm的不锈钢、铝、钛、钼等薄板冲制而成。
平板式换热器的优点是传热系数高(约比管壳式换热器高2~4倍),容易拆洗,并可增减板片数以调整传热面积。
操作压力通常不超过2MPa,操作温度不超过250℃。
二、按焊接形式分类
1)板壳式换热器、
2)半焊接板式换热器、
3)钎焊板式换热器。
4)全焊接板式换热器、
三、按根据结构来区分
1)螺旋板式换热器
2)可拆卸板式换热器(又叫带密封垫片的板式换热器)
3)板卷式换热器(又叫蜂窝式换热器)
4)焊接板式换热器。
换热器技术要求汇总
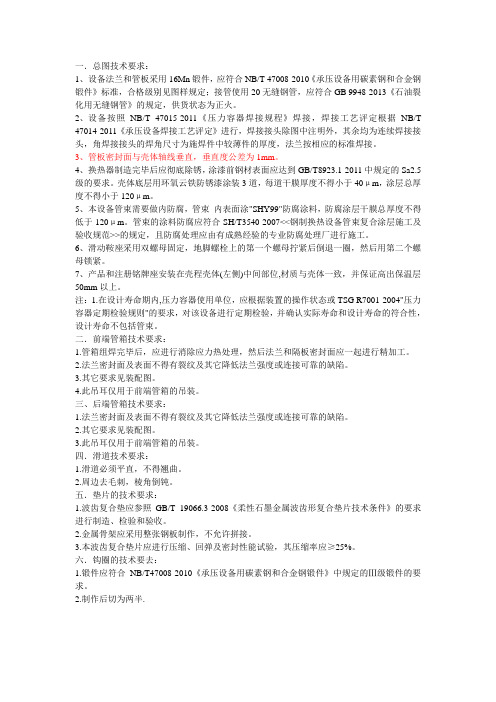
一.总图技术要求:1、设备法兰和管板采用16Mn锻件,应符合NB/T 47008-2010《承压设备用碳素钢和合金钢锻件》标准,合格级别见图样规定;接管使用20无缝钢管,应符合GB 9948-2013《石油裂化用无缝钢管》的规定,供货状态为正火。
2、设备按照NB/T 47015-2011《压力容器焊接规程》焊接,焊接工艺评定根据NB/T 47014-2011《承压设备焊接工艺评定》进行,焊接接头除图中注明外,其余均为连续焊接接头,角焊接接头的焊角尺寸为施焊件中较薄件的厚度,法兰按相应的标准焊接。
3、管板密封面与壳体轴线垂直,垂直度公差为1mm。
4、换热器制造完毕后应彻底除锈,涂漆前钢材表面应达到GB/T8923.1-2011中规定的Sa2.5级的要求。
壳体底层用环氧云铁防锈漆涂装3道,每道干膜厚度不得小于40μm,涂层总厚度不得小于120μm。
5、本设备管束需要做内防腐,管束内表面涂"SHY99"防腐涂料,防腐涂层干膜总厚度不得低于120μm。
管束的涂料防腐应符合SH/T3540-2007<<钢制换热设备管束复合涂层施工及验收规范>>的规定,且防腐处理应由有成熟经验的专业防腐处理厂进行施工。
6、滑动鞍座采用双螺母固定,地脚螺栓上的第一个螺母拧紧后倒退一圈,然后用第二个螺母锁紧。
7、产品和注册铭牌座安装在壳程壳体(左侧)中间部位,材质与壳体一致,并保证高出保温层50mm以上。
注:1.在设计寿命期内,压力容器使用单位,应根据装置的操作状态或TSG R7001-2004"压力容器定期检验规则"的要求,对该设备进行定期检验,并确认实际寿命和设计寿命的符合性,设计寿命不包括管束。
二.前端管箱技术要求:1.管箱组焊完毕后,应进行消除应力热处理,然后法兰和隔板密封面应一起进行精加工。
2.法兰密封面及表面不得有裂纹及其它降低法兰强度或连接可靠的缺陷。
化工原理课程设计——换热器的设计
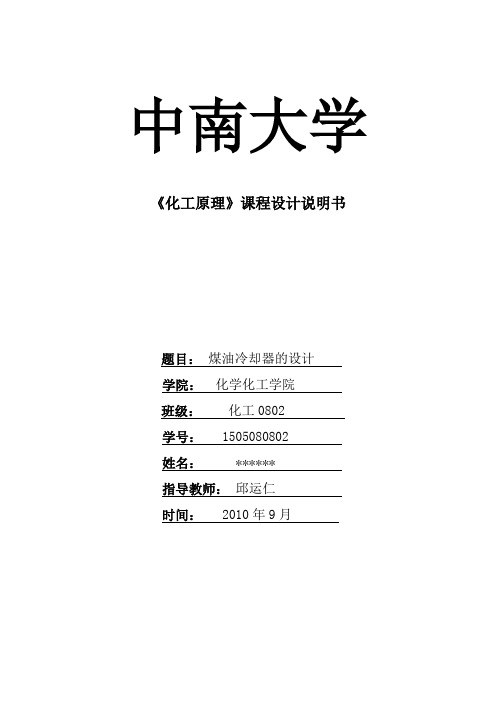
中南大学《化工原理》课程设计说明书题目:煤油冷却器的设计学院:化学化工学院班级:化工0802学号: **********姓名: ******指导教师:***时间:2010年9月目录§一.任务书 (2)1.1.题目1.2.任务及操作条件1.3.列管式换热器的选择与核算§二.概述 (3)2.1.换热器概述2.2.固定管板式换热器2.3.设计背景及设计要求§三.热量设计 (5)3.1.初选换热器的类型3.2.管程安排(流动空间的选择)及流速确定3.3.确定物性数据3.4.计算总传热系数3.5.计算传热面积§四. 机械结构设计 (9)4.1.管径和管内流速4.2.管程数和传热管数4.3.平均传热温差校正及壳程数4.4.壳程内径及换热管选型汇总4.4.折流板4.6.接管4.7.壁厚的确定、封头4.8.管板4.9.换热管4.10.分程隔板4.11拉杆4.12.换热管与管板的连接4.13.防冲板或导流筒的选择、鞍式支座的示意图(BI型)4.14.膨胀节的设定讨论§五.换热器核算 (21)5.1.热量核算5.2.压力降核算§六.管束振动 (25)6.1.换热器的振动6.2.流体诱发换热器管束振动机理6.3.换热器管束振动的计算6.4.振动的防止与有效利用§七. 设计结果表汇 (28)§八.参考文献 (29)§附:化工原理课程设计之心得体会 (30)§一.化工原理课程设计任务书1.1.题目煤油冷却器的设计1.2.任务及操作条件1.2.1处理能力:40t/h 煤油1.2.2.设备形式:列管式换热器1.2.3.操作条件(1).煤油:入口温度160℃,出口温度60℃(2).冷却介质:循环水,入口温度17℃,出口温度30℃(3).允许压强降:管程不大于0.1MPa,壳程不大于40KPa(4).煤油定性温度下的物性数据ρ=825kg/m3,黏度7.15×10-4Pa.s,比热容2.2kJ/(kg.℃),导热系数0.14W/(m.℃)1.3.列管式换热器的选择与核算1.3.1.传热计算1.3.2.管、壳程流体阻力计算1.3.3.管板厚度计算1.3.4.膨胀节计算1.3.5.管束振动1.3.6.管壳式换热器零部件结构§二.概述2.1.换热器概述换热器是化工、炼油工业中普遍应用的典型的工艺设备。
换热器的传热系数K汇总
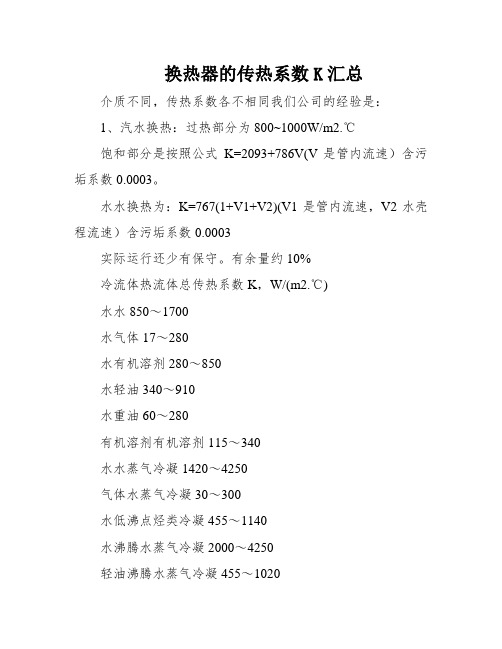
换热器的传热系数K汇总介质不同,传热系数各不相同我们公司的经验是:1、汽水换热:过热部分为800~1000W/m2.℃饱和部分是按照公式K=2093+786V(V是管内流速)含污垢系数0.0003。
水水换热为:K=767(1+V1+V2)(V1是管内流速,V2水壳程流速)含污垢系数0.0003实际运行还少有保守。
有余量约10%冷流体热流体总传热系数K,W/(m2.℃)水水850~1700水气体17~280水有机溶剂280~850水轻油340~910水重油60~280有机溶剂有机溶剂115~340水水蒸气冷凝1420~4250气体水蒸气冷凝30~300水低沸点烃类冷凝455~1140水沸腾水蒸气冷凝2000~4250轻油沸腾水蒸气冷凝455~1020不同的流速、粘度和成垢物质会有不同的传热系数。
K值通常在1800~2200W/m2·℃范围内。
列管换热器的传热系数不宜选太高,一般在800-1000 W/m2·℃。
螺旋板式换热器的总传热系数(水—水)通常在1000~2000W/m2·℃范围内。
板式换热器的总传热系数(水(汽)—水)通常在3000~5000W/m2·℃范围内。
1.流体流径的选择哪种流体流经换热器的管程,哪种流体流经壳程,以下各点可供选择时参考(以牢固管板式换热器为例)(1)不洁净和易结垢的流体宜走管内,以便于洗濯管子。
(2)腐蚀性的流体宜走管内,以免壳体和管子同时受腐蚀,而且管子也便于清洗和检修。
(3)压强高的流体宜走管内,以免壳体受压。
(4)饱和蒸气宜走管间,以便于及时排除冷凝液,且蒸气较洁净,冷凝传热系数与流速关系不大。
(5)被冷却的流体宜走管间,可利用外壳向外的散热作用,以增强冷却效果。
(6)需要提高流速以增大其对流传热系数的流体宜走管内,因管程流通面积常小于壳程,且可采用多管程以增大流速。
(7)粘度大的液体或流量较小的流体,宜走管间,因流体在有折流挡板的壳程流动时,由于流速和流向的不断改变,在低Re(Re>100)2下即可达到湍流,以提高对流传热系数。
板式换热器清洗方法汇总及注意事项

板式换热器清洗方法汇总及注意事项【摘要】板式换热器由于流通截面较小,结垢后容易产生堵塞,导致换热效率下降,直接影响设备的安全使用及企业的正常生产。
本文介绍了使用福世泰克高效环保清洗剂针对板式换热器的两种清洗方式,即闭路在线循环清洗和拆卸浸泡清洗工艺,以及清洗过程中的注意事项,为板式换热器的安全除垢提供保证。
【关键词】板式换热器;清洗;板换清洗;福世泰克清洗剂;1.板式换热器简介板式换热器是用薄金属板(一般为不锈钢)压制成具有一定形状波纹的换热板片,然后加密封胶垫,叠装而成的一种换热器(见图1)。
主要由板片、密封胶垫、夹紧螺栓、压紧板、整机框架等零部件组成。
冷热介质通过相邻换热板片流经各自通道,中间通过一层薄换热板片进行换热,因此具有高效节能,换热系数高,使用安全可靠,结构紧凑,休积小,占地少,组合灵活,调整维修方便等特点。
图1-板式换热器结构2.板式换热器的清洗准备工作2.1板式换热器结垢分析板式换热器一般可分为:水-水交换和汽-水交换两种方式。
水-水交换方式冷热介质均为水,且冷热水温差不大大概在70-90℃之间、两边结垢情况基木相同;汽一水交换方式热介质为水蒸气,一般不易结垢。
冷介质为水,温度约90℃,易结垢。
其垢样大致可分为水垢和污垢,尤以水垢为主。
水垢主要是水中溶解的各种盐类受热分解溶解度降低而结晶沉积在传热片上,通常为碳酸盐、磷酸盐、硫酸盐、和硅酸盐这类垢结晶政密比较坚硬且难以清除。
污垢一般是由颗粒细小的泥沙、尘土、不溶性盐类的泥装物、胶状氢氧化物、杂物碎屑、腐蚀产物、油污、藻类等组成,这种垢体积较大,疏松容易清除。
2.2清洗工艺选择板式换热器的清洗方式分为闭路循环清洗和拆卸浸泡清洗两种工艺,在清洗前可根据循环水质进行垢样分析,对照下表选取相应的清洗工艺:清洗工艺结垢形式优点缺点说明闭路循环清洗水垢劳动量小、工序简单,且不容易造成换热器滲漏、零配件损坏等不良形响除垢不够彻底当板式换热器结垢情况严重、换热效率低下,甚至堵塞时必须采取拆卸清洗;当板式换热器结垢较轻或老化严重时,可采取不拆卸清洗。
化工原理-17换热器的传热计算汇总

积分上式得
(NTU)c
t2
t1
dt Tt
S
0
KdS qm,ccpc
基于冷流体的传热单元数
对于热流体,同样可写出
(NTU)h
T1 T2
dT T t
基于热流体的传热单元数
24
二、传热单元数法
传热单元数是温度的量纲为一函数,它反 映传热推动力和传热所要求的温度变化,传热 推动力愈大,所要求的温度变化愈小,则所需 要的传热单元数愈少。
并流:
若对流体的温度有所限制,如冷流体被加热 时不得超过某一温度,或热流体被冷却时不得低 于某一温度,则宜采用并流操作。
12
一、平均温度差法
(2)错流和折流时的平均温度差 单管程,多管程 单壳程,多壳程
13
一、平均温度差法
图5-10 错流和折流示意图 14
一、平均温度差法
先按逆流计算对数平均温度差,然后再乘以
存在逆流和并流的缘故。
t(并 流 ) t(错 、 折 流 ) t(逆 流 )
通常在换热器的设计中规定, t 值不应小
于0.8,否则值太小,经济上不合理。若低于此 值,则应考虑增加壳方程数,将多台换热器串 联使用,使传热过程接近于逆流。
18
二、传热单元数法
1. 传热效率ε 换热器的传热效率ε定义为
KS qm,ccpc
27
二、传热单元数法
若热流体为最小值流体,则
1exp[(NTU)m in(1CR)]
1CR
式中
(NTU)min
KS Cmin
KS qm,hcph
CR
Cmin Cmax
qm,hcph qm,ccpc
28
二、传热单元数法
化工原理课程设计——换热器的设计
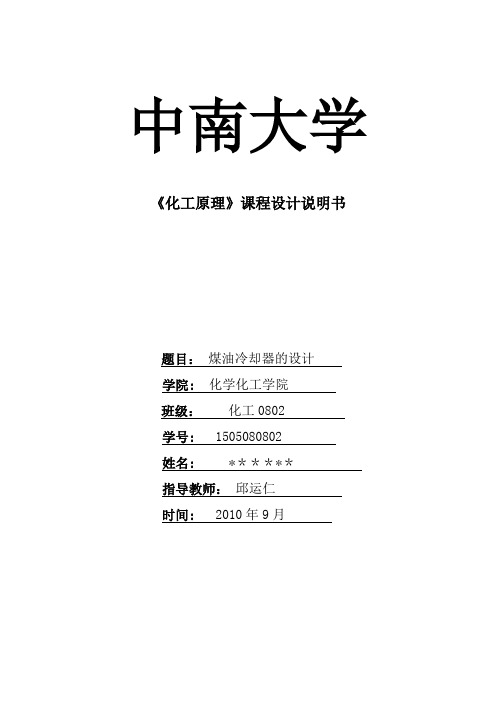
中南大学《化工原理》课程设计说明书题目:煤油冷却器的设计学院: 化学化工学院班级:化工0802学号: 1505080802姓名: ******指导教师:邱运仁时间: 2010年9月目录§一。
任务书 (2)1。
1.题目1.2.任务及操作条件1。
3.列管式换热器的选择与核算§二.概述………………………………………………………………………………………………….。
-3-2。
1.换热器概述2.2。
固定管板式换热器2.3。
设计背景及设计要求§三。
热量设计 (5)3.1.初选换热器的类型3。
2。
管程安排(流动空间的选择)及流速确定3。
3.确定物性数据3。
4。
计算总传热系数3。
5.计算传热面积§四。
机械结构设计 (9)4。
1。
管径和管内流速4。
2.管程数和传热管数4。
3.平均传热温差校正及壳程数4。
4.壳程内径及换热管选型汇总4。
4。
折流板4。
6.接管4。
7.壁厚的确定、封头4.8。
管板4。
9.换热管4。
10。
分程隔板4。
11拉杆4。
12.换热管与管板的连接4.13.防冲板或导流筒的选择、鞍式支座的示意图(BI型)4。
14。
膨胀节的设定讨论§五.换热器核算 (21)5.1。
热量核算5.2.压力降核算§六。
管束振动.................................................................................................。
(25)6.1。
换热器的振动6。
2。
流体诱发换热器管束振动机理6.3.换热器管束振动的计算6。
4.振动的防止与有效利用§七。
设计结果表汇................................................................................................。
(28)§八.参考文献.........................................................................................................。
聚四氟乙烯热交换器汇总

聚四氟乙烯热交换器聚四氟乙烯换热器是化工设备新品种,由于聚四氟乙烯材质耐蚀性冠于多种合金、非金属甚至贵金属,故此类设备对于解决制药工业、石油化工等强腐蚀性流涕无聊的换热问题具有重要意义。
聚四氟乙烯黄热设备是在我国工业需要大量不含杂质的物料冷凝,而缺乏及耐腐蚀又具有高洁净率换热材质的局面下问世的。
此种设备极大地提高了换热设备的耐蚀性和换热介质的洁净率,在石油化工、硫酸、医药、电镀、轻工等领域得到广泛的应用。
在工业生产中,为了工业流程的需要,往往需要进行各种不同方式的热量变换,如:加热、冷却、蒸发赫冷凝等,换热器就是用来实现上述热量交换与传递的设备。
通过各种设备,一边使热量从温度较高的流体传递给温度较低的流体,以满足生产工艺的需要。
换热器应用极为广泛,使实现化工生产必不可少的设备,它通常占化工厂总投资的10%--20%,在是由工业,换热器设备约占全部工艺设备投资的35%--40%。
在化工生产的热交换过程中,除了遇到高温高压、深冷等一些条件外,还常常伴随一些腐蚀性很强的介质,这就不仅要求实现工艺流程需要的热交换,同时要求这些设备必须具有抗腐蚀性能。
因而化工生产对制造换热器以及用不锈钢和钛、钽、锆等稀有金属制成的换热器就是噶怒防腐需要而生产的。
用石墨、玻璃、陶瓷及钛、钽、锆等材料制成的换热器具有防腐性能,但仍存在很大的局限性。
例如:用石墨、陶瓷、玻璃等材料制成的换热器尽管其防腐性较好,但有易碎、体积大、导热性能差、效率低等缺点。
用钛、钽、锆等稀有金属制成的换热器,虽导热性好,但价格昂贵,一般用户难以承受,如:锆、钛换热器价格是不锈钢换热器价格的5倍。
在我国目前国立情况下难以大面积推广。
聚四氟乙烯又称泰佛隆,简称F—4,是工程塑料的一种,它具有优异的化学稳定性。
已它为主要原料制成的换热器具有极耐腐蚀、极好的表面不沾性、较快的温度范围赫耐老化寿命长等优点。
是解决强腐蚀、强氧化介质传热过程中的理想设备。
F—4换热器除了在高温下,元素氟、熔融状态金属及其铵溶液、三氟化氯、六氟化铀及全氟煤油能与其反应外,对于其它物质在其使用范围内均几乎不作用。
换热器的传热系数K汇总
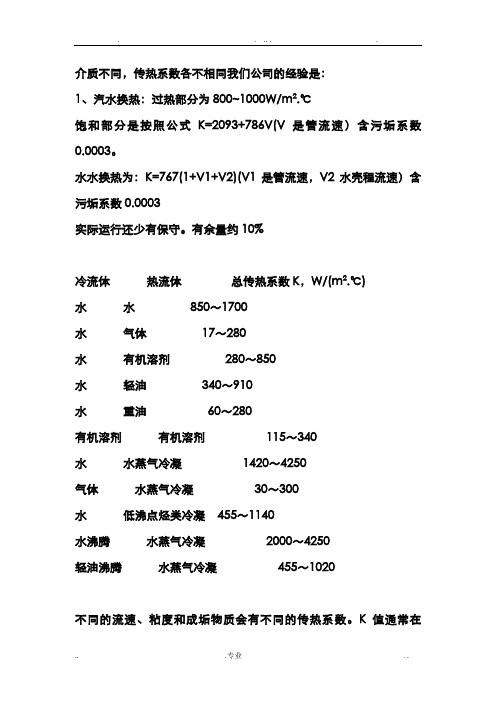
介质不同,传热系数各不相同我们公司的经验是:1、汽水换热:过热部分为800~1000W/m2.℃饱和部分是按照公式K=2093+786V(V是管流速)含污垢系数0.0003。
水水换热为:K=767(1+V1+V2)(V1是管流速,V2水壳程流速)含污垢系数0.0003实际运行还少有保守。
有余量约10%冷流体热流体总传热系数K,W/(m2.℃)水水 850~1700水气体 17~280水有机溶剂 280~850水轻油 340~910水重油60~280有机溶剂有机溶剂115~340水水蒸气冷凝1420~4250气体水蒸气冷凝30~300水低沸点烃类冷凝 455~1140水沸腾水蒸气冷凝2000~4250轻油沸腾水蒸气冷凝455~1020不同的流速、粘度和成垢物质会有不同的传热系数。
K值通常在800~2200W/m2·℃围。
列管换热器的传热系数不宜选太高,一般在800-1000 W/m2·℃。
螺旋板式换热器的总传热系数(水—水)通常在1000~2000W/m2·℃围。
板式换热器的总传热系数(水(汽)—水)通常在3000~5000W/m2·℃围。
1.流体流径的选择哪一种流体流经换热器的管程,哪一种流体流经壳程,下列各点可供选择时参考(以固定管板式换热器为例)(1) 不洁净和易结垢的流体宜走管,以便于清洗管子。
(2) 腐蚀性的流体宜走管,以免壳体和管子同时受腐蚀,而且管子也便于清洗和检修。
(3) 压强高的流体宜走管,以免壳体受压。
(4) 饱和蒸气宜走管间,以便于及时排除冷凝液,且蒸气较洁净,冷凝传热系数与流速关系不大。
(5) 被冷却的流体宜走管间,可利用外壳向外的散热作用,以增强冷却效果。
(6) 需要提高流速以增大其对流传热系数的流体宜走管,因管程流通面积常小于壳程,且可采用多管程以增大流速。
(7) 粘度大的液体或流量较小的流体,宜走管间,因流体在有折流挡板的壳程流动时,由于流速和流向的不断改变,在低Re(Re>100)下即可达到湍流,以提高对流传热系数。
(整理)板式换热器的计算方法[1]
![(整理)板式换热器的计算方法[1]](https://img.taocdn.com/s3/m/07ecc754ddccda38366baf01.png)
板式换热器的计算方法板式换热器的计算是一个比较复杂的过程,目前比较流行的方法是对数平均温差法和NTU法。
在计算机没有普及的时候,各个厂家大多采用计算参数近似估算和流速-总传热系数曲线估算方法。
目前,越来越多的厂家采用计算机计算,这样,板式换热器的工艺计算变得快捷、方便、准确。
以下简要说明无相变时板式换热器的一般计算方法,该方法是以传热和压降准则关联式为基础的设计计算方法。
以下五个参数在板式换热器的选型计算中是必须的:∙总传热量(单位:kW).∙一次侧、二次侧的进出口温度∙一次侧、二次侧的允许压力降∙最高工作温度∙最大工作压力如果已知传热介质的流量,比热容以及进出口的温度差,总传热量即可计算得出。
温度T1 = 热侧进口温度T2 = 热侧出口温度t1 = 冷侧进口温度t2= 冷侧出口温度热负荷热流量衡算式反映两流体在换热过程中温度变化的相互关系,在换热器保温良好,无热损失的情况下,对于稳态传热过程,其热流量衡算关系为:(热流体放出的热流量)=(冷流体吸收的热流量)在进行热衡算时,对有、无相变化的传热过程其表达式又有所区别。
(1)无相变化传热过程式中Q----冷流体吸收或热流体放出的热流量,W;m h,m c-----热、冷流体的质量流量,kg/s;C ph,C pc------热、冷流体的比定压热容,kJ/(kg·K);T1,t1------热、冷流体的进口温度,K;T2,t2------热、冷流体的出口温度,K。
(2)有相变化传热过程两物流在换热过程中,其中一侧物流发生相变化,如蒸汽冷凝或液体沸腾,其热流量衡算式为:一侧有相变化两侧物流均发生相变化,如一侧冷凝另一侧沸腾的传热过程式中r,r1,r2--------物流相变热,J/kg;D,D1,D2--------相变物流量,kg/s。
对于过冷或过热物流发生相变时的热流量衡算,则应按以上方法分段进行加和计算。
对数平均温差(LMTD)对数平均温差是换热器传热的动力,对数平均温差的大小直接关系到换热器传热难易程度.在某些特殊情况下无法计算对数平均温差,此时用算术平均温差代替对数平均温差,介质在逆流情况和在并流情况下的对数平均温差的计算方式是不同的。
换热器的设计

第一章设计方案概述和简介1.1 概述在不同温度的流体间传递热能的装置称为热交换器,简称为换热器。
化工生产中换热器的使用十分普遍,由于无理的性质、歘热要求各不相同,换热器的种类很多。
了解各种换热器的特点,根据工艺要求正确选用适当类型的换热器是非常重要的。
按照热量交换的方法不同,分为间壁式换热器、直接接触式换热器、蓄热式换热器三种。
化工生产中绝大多数情况下不允许冷、热两流体在传热过程中发生混合,所以,间壁式换热器的应用最广泛。
在换热器中至少要有两种温度不同的流体,一种流体温度较高,放出热量:另一种流体温度较低,吸收热量。
换热器在化工、石油、动力、制冷、食品等行业中都有广泛应用,且它们是上述这些行业的通用设备,并占有十分重要的地位。
1.2 方案简介根据列管式换热器的结构特点,主要分为以下四种。
以下根据本次的设计要求,介绍几种常见的列管式换热器。
1.2.1 列管式换热器的分类1.2.1.1 固定管板式换热器固定管办事换热器的两端和壳体连为一体,管子则固定于管板上,它的结余构简单;在相同的壳体直径内,排管最多,比较紧凑;由于这种结构式壳测清洗困难,所以壳程宜用于不易结垢和清洁的流体。
当管束和壳体之间的温差太大而产生不同的热膨胀时,用使用管子于管板的接口脱开,从而发生介质的泄漏。
1.2.1.2 U型管换热器U型管换热器结构特点是只有一块管板,换热管为U型,管子的两端固定在同一块管板上,其管程至少为两程。
管束可以自由伸缩,当壳体与U型环热管由温差时,不会产生温差应力。
U型管式换热器的优点是结构简单,只有一块管板,密封面少,运行可靠;管束可以抽出,管间清洗方便。
其缺点是管内清洗困难;哟由于管子需要一定的弯曲半径,故管板的利用率较低;管束最内程管间距大,壳程易短路;内程管子坏了不能更换,因而报废率较高。
此外,其造价比管定管板式高10%左右。
1.2.1.3 浮头式换热器其结构特点是两端管板之一不与外科固定连接,可在壳体内沿轴向自由伸缩,该端称为浮头。
(整理)换热器的传热系数K

介质不同,传热系数各不相同我们公司的经验是:1、汽水换热:过热部分为800~1000W/m2.℃饱和部分是按照公式K=2093+786V(V是管内流速)含污垢系数0.0003。
水水换热为:K=767(1+V1+V2)(V1是管内流速,V2水壳程流速)含污垢系数0.0003实际运行还少有保守。
有余量约10%冷流体热流体总传热系数K,W/(m2.℃)水水 850~1700水气体 17~280水有机溶剂 280~850水轻油 340~910水重油60~280有机溶剂有机溶剂115~340水水蒸气冷凝1420~4250气体水蒸气冷凝30~300水低沸点烃类冷凝 455~1140水沸腾水蒸气冷凝2000~4250轻油沸腾水蒸气冷凝455~1020不同的流速、粘度和成垢物质会有不同的传热系数。
K值通常在800~2200W/m2·℃范围内。
列管换热器的传热系数不宜选太高,一般在800-1000 W/m2·℃。
螺旋板式换热器的总传热系数(水—水)通常在1000~2000W/m2·℃范围内。
板式换热器的总传热系数(水(汽)—水)通常在3000~5000W/m2·℃范围内。
1.流体流径的选择哪一种流体流经换热器的管程,哪一种流体流经壳程,下列各点可供选择时参考(以固定管板式换热器为例)(1) 不洁净和易结垢的流体宜走管内,以便于清洗管子。
(2) 腐蚀性的流体宜走管内,以免壳体和管子同时受腐蚀,而且管子也便于清洗和检修。
(3) 压强高的流体宜走管内,以免壳体受压。
(4) 饱和蒸气宜走管间,以便于及时排除冷凝液,且蒸气较洁净,冷凝传热系数与流速关系不大。
(5) 被冷却的流体宜走管间,可利用外壳向外的散热作用,以增强冷却效果。
(6) 需要提高流速以增大其对流传热系数的流体宜走管内,因管程流通面积常小于壳程,且可采用多管程以增大流速。
(7) 粘度大的液体或流量较小的流体,宜走管间,因流体在有折流挡板的壳程流动时,由于流速和流向的不断改变,在低Re(Re>100)下即可达到湍流,以提高对流传热系数。
换热器设计常用数据汇总

换热器设计常用数据汇总1、压降选择下表列出常用换热器得压降值以供参考。
表2-1管壳式换热器得合理压降操作情况操作压力合理得压力降减压操作P=0~100Kpa(绝) P/10低压操作P=0~70Kpa(表) P/2P=70~1000Kpa(表) 35Kpa 中压操作(包括用泵) P=1000 ~3000Kpa(表) 35~180Kpa较高压操作P=3000~8000Kpa(表) 70~250Kpa 2、管径选择固定管板式换热器:表2-2 常用国内换热管得规格材料钢管标准外径mmx厚度mm碳钢GB8163-87 19 x 2碳钢GB8163-8725x 2碳钢GB8163-87 25 x2、5不锈钢GB2270-80 19x 2不 锈钢GB 2270-80 25 x 23、 折流板选择(Baff le)单弓形圆缺型折流板得建议开口高度为直径得10~45%,双弓形折流板得建议开口高度为直径得15~25%。
4、 流速选择(vel oc ity )表2-3管壳式换热器中常用得流速范围流体得种类 一般流体 易结垢流体 气体 流速m /s管程 0、5~3、0 >1、0 5、0~30 壳程0、2~1、5>0、53、0~15表2-4水得流速表(管内)类别管材最低流速(m/s) 最高流速(m/s)适宜流速(m/s)凝结水 钢管 0、6~0、9 0、6~0、9 0、6~0、9 0、75~0、9 0、75~0、93、0 3、7 3、7 3、0 2、41、8~2、4 1、8~2、4 1、8~2、4 1、8~2、4 1、8~2、4 河水(干净得) 钢管 循环水(处理得) 钢管 海水 含铜镍得管 海水铝铜管5、流型(flow fraction)在HTRI设计结果report中,报告右下角给出了5种流体所占分率。
为保证换热器又较好得传热效率,建议B>0、6,E<0、15,A最好小于0、1,但不得大于0、2。
换热器的传热系数K汇总
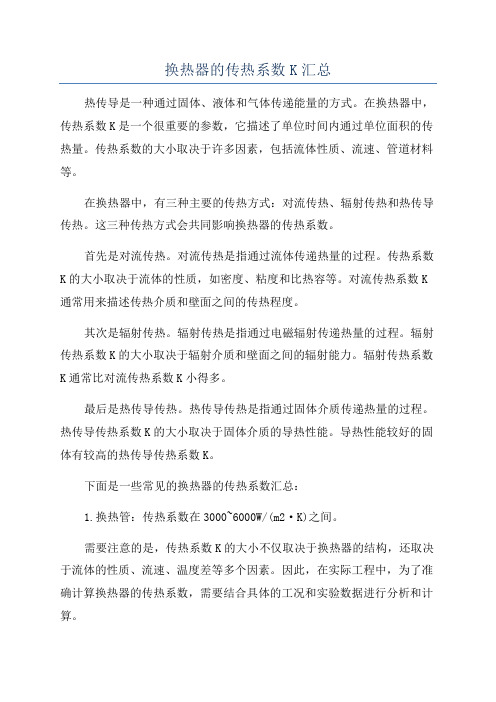
换热器的传热系数K汇总
热传导是一种通过固体、液体和气体传递能量的方式。
在换热器中,传热系数K是一个很重要的参数,它描述了单位时间内通过单位面积的传热量。
传热系数的大小取决于许多因素,包括流体性质、流速、管道材料等。
在换热器中,有三种主要的传热方式:对流传热、辐射传热和热传导传热。
这三种传热方式会共同影响换热器的传热系数。
首先是对流传热。
对流传热是指通过流体传递热量的过程。
传热系数K的大小取决于流体的性质,如密度、粘度和比热容等。
对流传热系数K 通常用来描述传热介质和壁面之间的传热程度。
其次是辐射传热。
辐射传热是指通过电磁辐射传递热量的过程。
辐射传热系数K的大小取决于辐射介质和壁面之间的辐射能力。
辐射传热系数K通常比对流传热系数K小得多。
最后是热传导传热。
热传导传热是指通过固体介质传递热量的过程。
热传导传热系数K的大小取决于固体介质的导热性能。
导热性能较好的固体有较高的热传导传热系数K。
下面是一些常见的换热器的传热系数汇总:
1.换热管:传热系数在3000~6000W/(m2·K)之间。
需要注意的是,传热系数K的大小不仅取决于换热器的结构,还取决于流体的性质、流速、温度差等多个因素。
因此,在实际工程中,为了准确计算换热器的传热系数,需要结合具体的工况和实验数据进行分析和计算。
换热器传热系数测定汇总

换热器传热系数测定汇总姓名: _________ 学号: ______________ 报告成绩:一、实验目的 套管换热器的操作方法: 加深对其概念流传热系数的理解。
式4 ,量下的彳5 热器的三、实验原理1、对流传热系数'的测定:Q i常数A 、m 的值。
F 普通套管换热器的了器传操作汽法流热的基本理论,掌握i 测定方法,3、 「应用线性回归分析方法,确定关联式Nu ARe m Pr 0.44、了解强化换热的基本方式,确定传热强 化比 Nu/Nu 0。
二、实验内容与要求对流传测系数a i 。
传热系数同空气流速下强化套管换热器的对流 传热 3糸数别求普通管、强化管换热器准数关联 Nu ARe m Pr 0.4中常数A 、m 的值。
、传据准数鈣式Nu N 。
U 计算同一流、分别求取普通套管换热器、强化套管换 的总传热系数K 。
(5-1)(n 式中C);'—管内流体传热传率系数W ; W/m P mn V m C p m tQ i3600(5-2) 式中:V—空气流过测量段上平均体积,m3/h ;P m —测量段上空气的平均密度,n ;S—管内传热面积,m;(kg.g );均温度差, (5-3) 当2> t 1 />0.5时,可简化为 t m TWt1 t 2(5-4) 式中:(5-平均流速:Nu c0.4 Re(5-8)Pr测量段上空气的平均比热,J£管内流体空气与管内壁面的平T wt 1 T w t 2t m ----------------------------------------------.T S t 1 ln -------T S t 2式中温度1,卜—冷流体(空气)的入口、出 口温度,一,壁面平均温度,°C 。
2、对流传热系数准数关联式的实验确定: 流体在管内作强制对流时,处于被加热状 态,准数关联式的形式为:Nu ARe^Pr i(5-5)其中,传热准数:Nu 「 d6)-7)其中:u-测量段上空气的V uF 3600d i u i i雷诺准数:Re' ―T(5普朗特准数: Pr iC Pi i换热器求换热器所得的准关数值 联式中,可以得到Nu 及Nu o ,强化比= 5、、换热器总传热系数K o 0 '、 试验中右忽略换热器的热 传热过程中热空气升传获量的相等,对 表面为基准的总传热系数:K ot m S 。
化工原理课程设计__换热器.
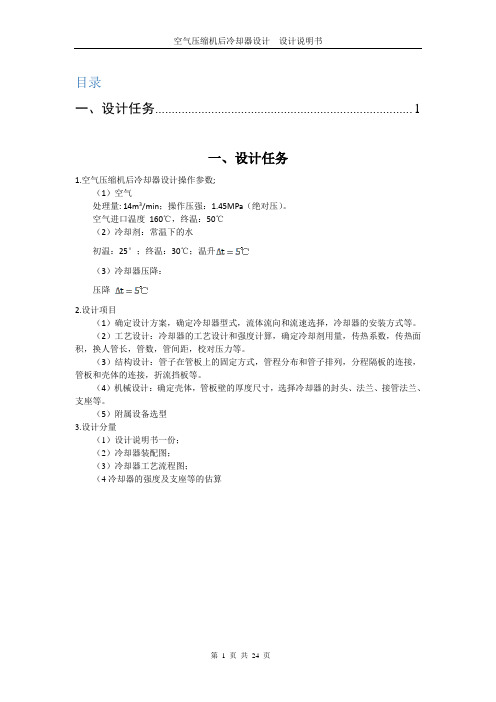
目录一、设计任务 (1)一、设计任务1.空气压缩机后冷却器设计操作参数;(1)空气处理量: 14m3/min;操作压强:1.45MPa(绝对压)。
空气进口温度160℃,终温:50℃(2)冷却剂:常温下的水初温:25°;终温:30℃;温升(3)冷却器压降:压降2.设计项目(1)确定设计方案,确定冷却器型式,流体流向和流速选择,冷却器的安装方式等。
(2)工艺设计:冷却器的工艺设计和强度计算,确定冷却剂用量,传热系数,传热面积,换人管长,管数,管间距,校对压力等。
(3)结构设计:管子在管板上的固定方式,管程分布和管子排列,分程隔板的连接,管板和壳体的连接,折流挡板等。
(4)机械设计:确定壳体,管板壁的厚度尺寸,选择冷却器的封头、法兰、接管法兰、支座等。
(5)附属设备选型3.设计分量(1)设计说明书一份;(2)冷却器装配图;(3)冷却器工艺流程图;(4冷却器的强度及支座等的估算一、设计任务书二、确定设计方案2.1 选择换热器的类型本设计中空气压缩机的后冷却器选用带有折流挡板的固定管板式换热器,这种换热器适用于下列情况:①温差不大;②温差较大但是壳程压力较小;③壳程不易结构或能化学清洗。
本次设计条件满足第②种情况。
另外,固定管板式换热器具有单位体积传热面积大,结构紧凑、坚固,传热效果好,而且能用多种材料制造,适用性较强,操作弹性大,结构简单,造价低廉,且适用于高温、高压的大型装置中。
采用折流挡板,可使作为冷却剂的水容易形成湍流,可以提高对流表面传热系数,提高传热效率。
本设计中的固定管板式换热器采用的材料为钢管(20R钢)。
2.2 流动方向及流速的确定本冷却器的管程走压缩后的热空气,壳程走冷却水。
热空气和冷却水逆向流动换热。
根据的原则有:(1)因为热空气的操作压力达到1.1Mpa,而冷却水的操作压力取0.3Mpa,如果热空气走管内可以避免壳体受压,可节省壳程金属消耗量;(2)对于刚性结构的换热器,若两流体的的温度差较大,对流传热系数较大者宜走管间,因壁面温度与对流表面传热系数大的流体温度相近,可以减少热应力,防止把管子压弯或把管子从管板处拉脱。
化工原理课程设计管壳式换热器汇总

设计一台换热器目录化工原理课程设计任务书设计概述试算并初选换热器规格1.流体流动途径的确定2.物性参数及其选型3.计算热负荷及冷却水流量4.计算两流体的平均温度差5.初选换热器的规格工艺计算1.核算总传热系数2.核算压强降经验公式设备及工艺流程图设计结果一览表设计评述参考文献化工原理课程设计任务书一、设计题目:设计一台换热器二、操作条件:1、苯:入口温度80℃,出口温度40℃。
2、冷却介质:循环水,入口温度35℃。
3、允许压强降:不大于50kPa。
4、每年按300天计,每天24小时连续运行。
三、设备型式:管壳式换热器四、处理能力:99000吨/年苯五、设计要求:1、选定管壳式换热器的种类和工艺流程。
2、管壳式换热器的工艺计算和主要的工艺尺寸的设计。
3、设计结果概要或设计结果一览表。
4、设备简图。
(要求按比例画出主要结构及尺寸)5、对本设计的评述及有关问题的讨论。
1.设计概述1.1热量传递的概念与意义1.热量传递的概念热量传递是指由于温度差引起的能量转移,简称传热。
由热力学第二定律可知,在自然界中凡是有温差存在时,热就必然从高温处传递到低温处,因此传热是自然界和工程技术领域中极普遍的一种传递现象。
2.化学工业与热传递的关系化学工业与传热的关系密切。
这是因为化工生产中的很多过程和单元操作,多需要进行加热和冷却,例如:化学反应通常要在一定的温度进行,为了达到并保持一定温度,就需要向反应器输入或输出热量;又如在蒸发、蒸馏、干燥等单元操作中,都要向这些设备输入或输出热量。
此外,化工设备的保温,生产过程中热能的合理利用以及废热的回收利用等都涉及到传热的问题,由此可见;传热过程普遍的存在于化工生产中,且具有极其重要的作用。
总之,无论是在能源,宇航,化工,动力,冶金,机械,建筑等工业部门,还是在农业,环境等部门中都涉及到许多有关传热的问题。
应予指出,热力学和传热学既有区别又有联系。
热力学不研究引起传热的机理和传热的快慢,它仅研究物质的平衡状态,确定系统由一个平衡状态变成另一个平衡状态所需的总能量;而传热学研究能量的传递速率,因此可以认为传热学士热力学的扩展。
- 1、下载文档前请自行甄别文档内容的完整性,平台不提供额外的编辑、内容补充、找答案等附加服务。
- 2、"仅部分预览"的文档,不可在线预览部分如存在完整性等问题,可反馈申请退款(可完整预览的文档不适用该条件!)。
- 3、如文档侵犯您的权益,请联系客服反馈,我们会尽快为您处理(人工客服工作时间:9:00-18:30)。
风冷翅片管式换热器管内热阻与铜管翅片的接触热阻及管外空气侧的热阻比为2:1:7
翅片间距对传热系数有显著影响
翅片间距的影响受控于管排数,翅片间距越小,阻力系数f越大,管排数对阻力系数的影响很小。
翅片厚度越小,传热越好。
管排数越少,传热系数越大,管排数最好不要大于3。
1、风机功率不变的情况下,传热系数和传热温差随管排数的增加均减小,总换热量则先增加后减小,而平均每
排管的换热量随着管排数的增加而减小。
通过计算,每增加1排管,平均每排管的换热量将减少18%左右,这说明增加管排数尽管增大了传热面积,但不能使总换热量显著持续的增加,因此不是一种经济的强化换热方式。
2、风速增大的情况下,换热量随风速的增加而增加,增加量随管排数的增加而减小,但是平均每排管的换热量
逐渐减小,最大可减少122%。
3、不同的风机功率水平下,换热量达到最大值的管排数不同,风机功率越大,换热量达到最大值的管排数也增
大。
同时通过计算得出,在相同条件下,不同制冷剂的换热量会有不同,但管排数对使用不同制冷剂的换热性能影响趋势一致。
管排数对换热的影响
1、保持风机功率不变,当迎风面积不变时,增加管排数
a.空气侧压降增大,因风机功率不变,使得风机全压增大,因此风机风量随管排数增加而减少。
b.风机风量的变化量随管排数增加而越来越小,则空气侧压降的变化量也越来越小,说明管排数对压降的影
响随管排数的增加而减少。
c.迎风面积不变,只改变管排数,管排数增加风量减少,导致迎面风速也减小,则空气侧换热系数也随之降
低。
但风速随管排数增加而减少的量比较小,所以空气侧平均换热系数变化并不显著。
又因管排数增加使得换热面积增大,所以总换热量增加。
d.随管排数增加,换热量的增加量越来越小,说明随管排数增加,空气侧压降越来越大,风量减少使得空气
侧换热系数减小,同时,湿空气比焓差亦随之增加,但增加量逐渐减少,因此总换热量的增加越来越小。
e.增加管排数增大了换热面积,但却也增大了空气侧阻力,使进风量减少,同时推动湿空气与水膜之间热湿
交换的动力比焓差随管排数增加而增大,但随管排数增加其增加量逐渐减小,因此,当管排数增加到一定值时,总换热量反倒会开始减小。
f.对于风冷翅片管式换热器,空气的对流换热系数比制冷剂侧的换热系数小1至2个数量级,因此换热器的
热阻70%左右是在空气侧,管内侧换热系数的变化对传热系数的影响较小。
g.换热器管排数增加时,总换热量先增加后减小,其平均每排管的换热量是逐渐递减的。
这说明管排数的增
加,使得总换热量有所增加,但是平均到每排管时其换热量反倒会减少,所以增加管排数尽管增大了换热面积,但不能使总换热量一直增加。
h.管排数持续增加至一定值时,使压降亦持续增大,从而使得换热系数和换热温差不断减小,所以尽管随管
排数增加换热面积增加,但总的换热量反倒几乎不变。
综上所述:
迎面风速一定时,只增加管排数,总换热面积随之增大,所以总换热量随管排数增加而增加,但随管排数增加空气侧压降是增大的,进风量在减小,所以总换热量虽然增加了,但平均到每排管的换热量反倒减小了,因此管排数增加到一定值后,总换热量就会开始减小。
迎面风速变化的情况下,即风机功率改变。
在每一个风速状态下,随管排数增加其换热量的变化趋势是一致的,但不同的迎面风速下,使换热量达到最大值的管排数是不同的,其变化规律是:随着迎面风速的增大,使换热量达到最大值的管排数也增加。
当改变管内制冷剂种类时,随管排数增加其换热量的变化趋势是一致的,但因不同的制冷剂其本身固有的物性不同,所以使用不同的制冷剂,使换热量达到最大值的管排数亦不同。
迎风面积不变,风机功率一定时,管排数增加,导致风阻增大,风量减小,空气侧换热系数减小,但总换热面积增大,初始增加管排数时,管排数增加的不多,所以风阻增大的不多,但总换热面积随管排数增加成指数增大,所以此时总换热量是增大的,但平均每排管的换热量反而是减小的。
当管排数增大到一定数量,风阻过大,导致风量减少过多,使空气侧换热系数大大降低,由此引起的换热量减少量大于增加管排数从而增加换热面积所增加的换热量,此时,总换热量开始减少。
由上述可得:风机功率一定,迎风面积一定时,当管排数增大到某一定值,总换热量达到最大值,此后,继续增加管排数对总换热量不再起到增大作用,反而会使总换热量随之减小。