数控机床螺纹切削循环指令编程
数控车床螺纹加工编程指令的应用

数控车床螺纹加工编程指令的应用济宁职业技术学院(山东)张玉香在目前的FANUC 和广州数控系统的车床上,加工螺纹一般可采用3 种方法:G32 直进式切削方法、G92直进式固定循环切削方法和G76 斜进式复合固定循环切削方法。
由于它们的切削方式和编程方法不同,造成的加工误差也不同,在操作使用时需仔细分析,以便加工出高精度的零件。
1.编程方法(1)G32 直进式螺纹切削方法指令格式:图1G32直进式螺纹切削方法指令格式:G32 X(U )_ Z(W )_ F_ ;该指令用于车削圆柱螺纹、圆锥螺纹、端面螺纹。
其编程方法与G01 相似,如图1所示。
使用说明:①式中(X ,Z )和(U ,W )为螺纹的终点坐标,即图1 中B 点的坐标值;F 后的数值为导程(单线时为螺距)。
②当α=0°时,作直螺纹加工,编程格式为G32 Z_F_或G32 W_F_ ;当α<45°时加工锥螺纹,螺距以Z轴方向的值指定;当α>45°时螺距以X 轴方向的值指定;当α=90°时,加工端面螺纹,编程格式为G32 X_ F_或G32 U_ F_ 。
③螺纹切削中进给速度倍率开关无效,进给速度被限制在100% ;螺纹切削中不能停止进给,一旦停止进给切深便急剧增加,非常危险。
因此,进给暂停在螺纹加工中无效。
④在螺纹切削程序段后的第一个非螺纹切削程序段期间,按进给暂停键时刀具在非螺纹切削程序段停止。
⑤主轴功能的确定。
在编写螺纹加工程序时,只能使用主轴恒转速控制功能(程序中编入G97 ),由于进给速度的最大值和最小值系统参数已设定,在加工螺纹时为了避免进给速度超出系统设定范围,所以主轴转速不宜太高,一般用如下公式计算:(取)且从粗加工到精加工,主轴转速必须保持恒定。
否则,螺距将发生变化,会出现乱牙。
⑥螺纹起点和终点轴向尺寸的确定。
螺纹加工时应注意在有效螺纹长度的两端留出足够的升速段和降速段,以剔除两端因进给伺服电动机变速而产生的不符合要求的螺纹段,通常:δ=(2~3 )螺距δ=(1~2 )螺距⑦螺纹起点和终点径向尺寸的确定。
数控车床循环指令详解
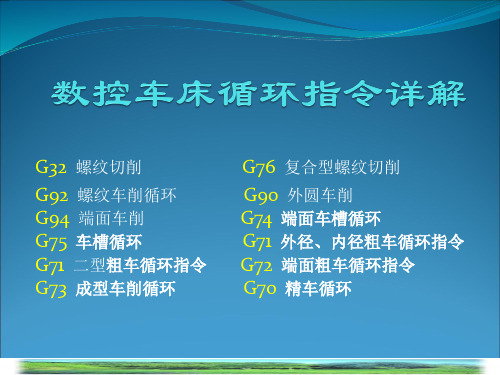
(4)Q nf是指定精加工路线的最后一个程序段的段号; (5)U u是X方向上的精加工余量,直径值; (6)W w是Z方向上的精加工余量。 (7)粗车过程中从程序段号Pns~Qnf之间的任何F 只有G71指令中指定的F、S、T功能有效。
图16.6
G71有两种情况,也就是一型和二型。
一型:也就是沿X轴同一方向递增或递减。一型
工序3 精车加工 精车
G00 X150; Z150; N4; S300 M03 T0303; G00 X48 Z-64; G01 X2 F0.05; G00 X150; Z150; M05; M30;
工序4 切断 程序结束
地址 内容
说明
1851
X向间隙数值。数值为半径值。
1852
Z向间隙数值
3204 0/1 PAR设置0是为中括号[ ]。 设置1是为小括号( )
G32 螺纹切削
G92 螺纹车削循环 G94 端面车削 G75 车槽循环 G71 二型粗车循环指令 G73 成型车削循环
G76 复合型螺纹切削
G90 外圆车削 G74 端面车槽循环 G71 外径、内径粗车循环指令 G72 端面粗车循环指令 G70 精车循环
该指令用于车削等螺距直螺纹、锥螺纹。
格式:G32 X(U)__ Z(W)__ F__
格式:G92 X(U) Z(W) R F
XZ螺纹终点坐标,R表示螺纹起始点与终点在X 向的坐标增量值(半径值),圆柱螺纹切削R为0可 省略。一般外锥螺纹R为负值,内锥螺纹R为正值。
T0202 (螺纹刀) M3 S400 G0 X22 Z5 G92 X20 Z-15 R-0.625 I14 F2 X19.6 I14 X19.2 I14 X18.9 14 X18.75 14 X18.631 I14 X18.631 I14 (精车) G0 X100 Z100 M5 M30
数控车床螺纹切削循环G92

数控车床螺纹切削循环G92(FANUC-6T)1、G92指令格式:螺纹切削循环G92为简单螺纹循环,该指令可切削锥螺纹和圆柱螺纹,其循环路线与前述的单一形状固定循环基本相同,只是F后边的进给量改为螺距值即可,其指令格式为:G92 X(U)—Z(W)—I—F—图4—40a所示为圆锥螺纹循环,图b所示为圆柱螺纹循环。
刀具从循环点开始,按A、B、C、D进行自动循环,最后又回到循环起点A。
图中虚线表示按R快速移动,实线表示按F指定的工作进给速度移动。
X、Z为螺纹终点(C点)的坐标值;U、W为螺纹终点坐标相对于螺纹起点的增量坐标,I为锥螺纹起点和终点的半径差。
加工圆柱螺纹时I为零,可省略。
图4-40 螺纹循环G922.(1)螺纹牙型高度(螺纹总切深)螺纹牙型高度是指在螺纹牙型上,牙顶到牙底之间垂直于轴线的距离。
图4—41所示,它是车削时;车刀总切入深度。
图4—41 螺纹牙型高度根据GBl92~197—81普通螺纹国家标准规定,普通螺纹的牙型理论高度H=0.866P,实际加工时,由于螺纹车刀刀尖半径的影响,螺纹的实际切深有变化。
根据GBl97—81规定螺纹车刀可,在牙底最小削平高度H/8处削平或倒圆。
则螺纹实际牙型高度可按下式计算:h=H一2(H/8)=0.6495P式中: H--螺纹原始三角形高度,H=0.866P(mm);p--螺距(mm)。
(2)螺纹起点与螺纹终点径向尺寸的确定螺纹加工中,径向起点(编程大径)的确定决定于螺纹大径。
例如要加工M30x2—6g外螺纹,自GBl97—81知:螺纹大径基本偏差为ES=-0.038mm;公差为Td=0.28mm;则螺纹大径尺寸为φ30-0.318-0.038mm.所以螺纹大径应在此范围内选取,并在加工螺纹前,由外圆车削来保证。
径向终点(编程小径)的确定决定于螺纹小径。
因为编程大径确定后,螺纹总切深在加工中是由编程小径(螺纹小径)来控制的。
螺纹小径的确定应考虑满足螺纹中径公差要求。
螺纹切削指令
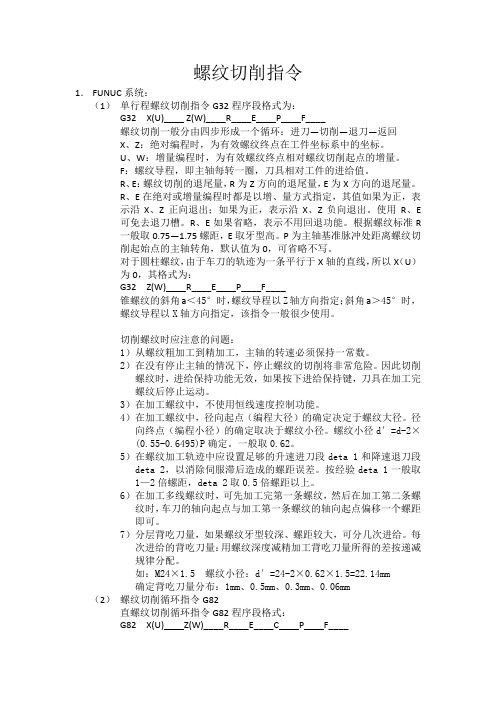
螺纹切削指令1.FUNUC系统:(1)单行程螺纹切削指令G32程序段格式为:G32 X(U)____ Z(W)____R____E____P____F____螺纹切削一般分由四步形成一个循环:进刀—切削—退刀—返回X、Z:绝对编程时,为有效螺纹终点在工件坐标系中的坐标。
U、W:增量编程时,为有效螺纹终点相对螺纹切削起点的增量。
F:螺纹导程,即主轴每转一圈,刀具相对工件的进给值。
R、E:螺纹切削的退尾量,R为Z方向的退尾量,E为X方向的退尾量。
R、E在绝对或增量编程时都是以增、量方式指定,其值如果为正,表示沿X、Z正向退出;如果为正,表示沿X、Z负向退出。
使用R、E可免去退刀槽。
R、E如果省略,表示不用回退功能。
根据螺纹标准R一般取0.75—1.75螺距,E取牙型高。
P为主轴基准脉冲处距离螺纹切削起始点的主轴转角,默认值为0,可省略不写。
对于圆柱螺纹,由于车刀的轨迹为一条平行于X轴的直线,所以X(U)为0,其格式为:G32 Z(W)____R____E____P____F____锥螺纹的斜角a<45°时,螺纹导程以Z轴方向指定;斜角a>45°时,螺纹导程以X轴方向指定,该指令一般很少使用。
切削螺纹时应注意的问题:1)从螺纹粗加工到精加工,主轴的转速必须保持一常数。
2)在没有停止主轴的情况下,停止螺纹的切削将非常危险。
因此切削螺纹时,进给保持功能无效,如果按下进给保持键,刀具在加工完螺纹后停止运动。
3)在加工螺纹中,不使用恒线速度控制功能。
4)在加工螺纹中,径向起点(编程大径)的确定决定于螺纹大径。
径向终点(编程小径)的确定取决于螺纹小径。
螺纹小径d′=d-2×(0.55-0.6495)P确定。
一般取0.62。
5)在螺纹加工轨迹中应设置足够的升速进刀段deta 1和降速退刀段deta 2,以消除伺服滞后造成的螺距误差。
按经验deta 1一般取1—2倍螺距,deta 2取0.5倍螺距以上。
螺纹切削复合循环指令G76

项目六
螺纹车削
任务要求:本任务要完成下图所示工件左端外圆、 螺纹底孔及内螺纹加工,毛坯已预制φ20mm,深 26mm的底孔。
复合循环车削内螺纹实例
项目六
螺纹车削
任务分析:在工艺方面,本任务重点放在内螺纹加工工艺上。 在编程方面,在学习了螺纹切削指令G32编程,螺纹切削单一固定 循环G92指令编程后,引入FANUC 0i系统的螺纹切削复合循环G76 指令编程。
螺纹总切深:内螺纹加工中,螺纹总切深的取值与外螺纹加工相 同,即h'≈1.3P(直径量)。
螺纹牙高k ≈0.65P=0.65×2=1.3(mm)。
实际加工中,螺纹牙高能否达到0.65P?对k值赋 0.65P对加工有何影响? 分层切削第一刀切削深度△d取值0.3mm(半径量),最小切深△dmin 取值0.1mm(半径量),精加工余量d取值-0.1mm(半径量)。
…
内螺纹加工
项目六
螺纹车削
三、使用螺纹复合循环G76时的注意事项
1.G76可以在MDI方式下使用。 2.在执行G76循环时,如按下循环暂停键,则刀具在螺纹切 削后的程序段暂停。 3.G76指令为非模态指令,所以必须每次指定。 4.在执行G76时,如要进行手动操作,刀具应返回到循 环操作停止的位置。
项目六
螺纹车削
内螺纹车削
硬质合金三角内螺纹车刀几何角度 Nhomakorabea项目六
螺纹车削
二、螺纹切削复合循环指令G76
1.指令格式 G76 Pmrα Q△dmin Rd; G76 X(U) Z(W) Ri Pk Q△d F ; m :精加工重复次数01~99; r:倒角量,即螺纹切削退尾处(45°)的Z向退刀距离。 α:刀尖角度(螺纹牙型角)。 △dmin:最小切深,该值用不带小数点的半径值指定; d:精加工余量,该值用带小数点的半径量表示; X(U) Z(W) :螺纹切削终点处的坐标; i:螺纹半径差。如果i=0,则进行圆柱螺纹切削; k:牙型编程高度。该值用不带小数点的半径量表示; △d:第一刀切削深度,该值用不带小数点的半径量表示; L:导程。如果是单线螺纹,则该值为螺距。
螺纹切削单一固定循环指令g92

06 G92指令的未来发展与展 望
技术发展趋势
智能化
随着人工智能和机器学习技术的不断发展,G92指令将进一步实现 智能化,能够自动识别和优化切削参数,提高加工效率和精度。
集成化
未来,G92指令将更加集成化,能够与其他数控加工指令和软件进 行无缝对接,实现更高效、便捷的加工过程控制。
定制化
针对不同材料、不同加工需求,G92指令将提供更加定制化的解决方 案,满足个性化加工需求。
螺纹切削单一固定循环指令G92
contents
目录
• G92指令概述 • G92指令的格式与参数 • G92指令的应用场景 • G92指令的注意事项与优化建议 • G92与其他螺纹切削指令的比较 • G92指令的未来发展与展望
01 G92指令概述
G92指令的定义
G92指令是数控车床中用于切削螺纹 的单一固定循环指令。
THANKS FOR WATCHING
感谢您的观看
它通过一个程序段来定义切削螺纹的 整个过程,简化了编程步骤。
G92指令的用途
G92指令主要用于车削圆柱螺纹和圆锥螺纹。 它能够实现直进法或斜进法切削螺纹,满足不同加工需求。
G92指令的特点
G92指令具有简单、方便、高效的特点。
它只需要一个程序段就可以完成整个切削过程, 减少了编程工作量。
G92指令可以通过调整参数实现多种切削效果, 如切削深度、螺纹长度等,提高了加工灵活性。
05 G92与其他螺纹切削指令 的比较
与G76指令的比较
加工方式
G92是单一固定循环指令,而G76是多段固 定循环指令。
编程方式
G92的编程方式相对简单,只需要指定螺纹的起点 和终点即可。而G76需要指定更多的参数,如刀具 半径、主轴转速等。
数控技术《螺纹铣削编程方法》

80
螺纹的铣削编程方法
例如
M30
20 80
根据上图所示,所要铣削的螺纹为M27。查表得螺距为3mm。根据我Байду номын сангаас以前学习的计算公式,螺纹 小径为D1=D-13×P=27-13×3=231,一般由于螺纹加工时牙顶会因为挤压胀大,所以小径实际为D1 实=D1=23101×3=234。那么我们在加工之前要首先加工一个Φ234的孔,孔的加工方法上个任务学 习过,就不介绍了。
第四页,共七页。
螺纹的铣削编程方法
程序 O0001; G54 G90 G40; G0 X0 Y50. Z50.; M03 S3000; G0 Z5.; G42 G01 Y0 D01 F2000; G02 X13.5 R6.75 F1500; G02 I-13.5 Z2.; G02 I-13.5 Z-1.; G02 I-13.5 Z-4.; ...... G02 I-13.5 Z-22.; G02 X0 R6.75 F2000; G00 Z50.; M05; M30;
图10-47参考程序
说明 程序名 建立坐标系,绝对值编程方法,取消刀具补偿 定外到建立补偿起始点 主轴正转,转速3000r/min 下刀到Z5mm处 建立刀具右补偿 圆弧进刀 切削第一圈螺纹 切削第二圈螺纹
最后一圈螺纹 圆弧退刀 抬刀 主轴停 程序结束
以上为铣削螺纹最后一刀的程序,没有分层铣削,实际加工中要采用前面讲述的分层铣削的形式。
第七页,共七页。
第五页,共七页。
谢谢观看
第六页,共七页。
内容总结
螺纹的铣削编程方法。采用螺纹铣削加工的先决条件是机床具备螺旋插补功能,当然目前的全功能型机床 都可加工。编程指令:G02/G03 _ Y_ I_ J_ _ F_。I、J为圆弧圆心相对于圆弧起点的增量〔参照圆弧插补一 章〕。G54 G90 G40。建立坐标系,绝对值编程方法,取消刀具补偿。G0 X0 Y50. Z50.。G42 G01 Y0 D01 F2000。G02 I-13.5 Z2.。谢谢观看
螺纹循环指令
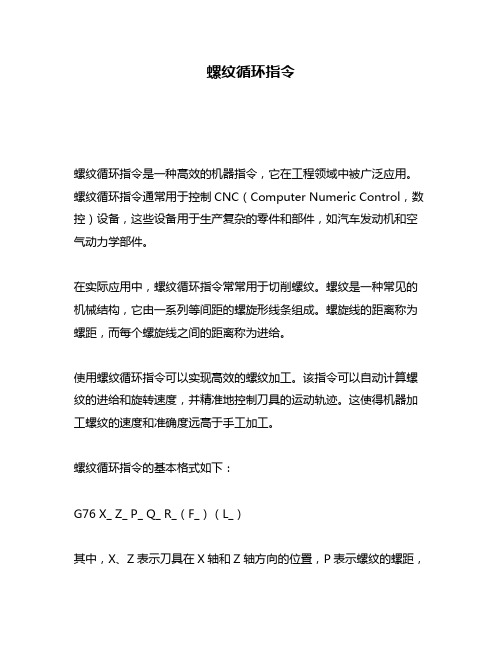
螺纹循环指令
螺纹循环指令是一种高效的机器指令,它在工程领域中被广泛应用。
螺纹循环指令通常用于控制CNC(Computer Numeric Control,数控)设备,这些设备用于生产复杂的零件和部件,如汽车发动机和空气动力学部件。
在实际应用中,螺纹循环指令常常用于切削螺纹。
螺纹是一种常见的机械结构,它由一系列等间距的螺旋形线条组成。
螺旋线的距离称为螺距,而每个螺旋线之间的距离称为进给。
使用螺纹循环指令可以实现高效的螺纹加工。
该指令可以自动计算螺纹的进给和旋转速度,并精准地控制刀具的运动轨迹。
这使得机器加工螺纹的速度和准确度远高于手工加工。
螺纹循环指令的基本格式如下:
G76 X_ Z_ P_ Q_ R_(F_)(L_)
其中,X、Z表示刀具在X轴和Z轴方向的位置,P表示螺纹的螺距,
Q表示螺纹的深度,R表示每圈螺旋线的升高量,F表示切削进给速度,L表示切削刀具的类型。
螺纹循环指令的使用需要一定的机器加工和编程知识。
在编写程序时,需要了解机床的性能参数和螺纹的几何特征,以保证程序的正确性和
高效性。
同时,还需要对切削参数进行合理的选择和优化,以提高机
器加工的效率和质量。
总体来说,螺纹循环指令是一种非常有用的机器指令,在机械加工领
域具有广泛的应用。
对于机床操作者和程序员来说,了解螺纹循环指
令的基本原理和应用方法,可以帮助他们更好地处理各种螺纹加工任务,提高机械加工过程的效率和精度。
螺纹切削循环G92指令数控加工基础说课课件

重点难点
9
数控加工基础
说课课件 教法分析
1 2 3 4
讲授法 情境教学法 案例分析法 分组讨论法
10
数控加工基础
说课课件 教法分析
1 2 3 4
讲授法 讲授法: 情境教学法 案例分析法 分组讨论法 通过与前面学习的G32单行程 切削指令对比讲解G92指令特点及 使用方法,强调指令的应用,弱化 理论分析。
11
数控加工基础
说课课件 教法分析
1 2 3 4
讲授法 情境教学法 案例分析法 分组讨论法
情境教学法: 利用我院新建成的数控工作站, 理论联系实际,让学生树立产品质量 意识、效率意识、安全意识。
12
数控加工基础
说课课件 教法分析
1 2 3 4
讲授法 情境教学法 案例分析法 分组讨论法
案例分析法: 结合零件加工实例,利用斯沃数 控仿真软件对零件进行动态仿真加工, 让学生参与软件操作和编制程序过程, 通过观察每条指令执行过程和结果, 加深对编程指令的理解。
5
数控加工基础
说课课件 一
理论学习目标
教材分析
技能训练目标 情感目标
数控编程
1
2 3 4
教材选用 教材特色 课题目标
1.了解数控程序基本结构。 2.掌握螺纹车削的参数编程方法。 3.理解编制机械加工工艺规程的方法。 4.理解带螺纹轴类零件的加工工艺。 5.掌握零件公差在编程时的处理方法。
机械制造 公差与配合
说课课件
数字 计算 编程 仿真 纠错 讨论
1 2 3 4 5
新课导入 理论讲解 编程实例 归纳总结 课外作业
理论
实践
提高
1.外圆倒角 2.退刀槽尺寸 3.螺纹走刀路线 (起刀升速阶段 和收刀降速阶段)
数控机床螺纹切削循环指令编程

原点
X1=59.1、X2=58.5 X3= 57.9、X4= 57.5 X5= 57.4
2、δ1、δ2计算 δ 1=n× p/400= 600× 2/400=3 δ 1=n× p/1800= 600× 2/1800=2/3
取δ 1=5、 δ 2=3
查得:分5次切削
得:
ap1=0.9、ap2=0.6
ap3= 0.6、ap4= 0.4
2.螺纹加工切削用量的选用(1 )
(1)主轴转速 n 由于螺距一定,随着转速的增大,进
给速度(Vf=nf)会随之增大,相应的惯性 也会增大,若数控系统加减速性能较差,就 会产生较大的误差,因此对经济型数控车床 ,加工螺纹时,转速一般取值为:
n*p≤ 3500∽ 4000 对于经济型数控车床,若螺距为3,转速 为1500r/min,合适吗?
分析: 1、切削用量选择
n=600r/min F=2 切削深度ap按表查
查得:分5次切削 ap1=0.9、ap2=0.6 ap3= 0.6、ap4= 0.4
ap5= 0.1 得:每次切削终点X坐标 值:
切削起点Z坐标值: Z1=5.
终点Z坐标值: Z2= -53.
3.螺纹加工注意事项(1)
1 、系统若无“退尾” 功能,螺纹加工前,应先加工出退刀 槽 “退尾” 功能的作用是,在加工到终点前,刀具沿45度 方向退出。加工退刀槽的目的是保证切屑能够及时落下, 防止堆积,产生过大的抗力造成崩刀。
2.螺纹加工切削用量的选用(2 )
(2)进给速度 螺纹加工时数控车床主轴转 速和工作台纵向进给量存在严格数量关系, 即主轴旋转1转,工作台移动一个待加工工 件螺纹导程距离。因此在加工程序中只要给 出主轴转速和螺纹导程,数控系统会自动运 算并控制工作台纵向移动速度。
螺纹切削单一固定循环指令G92
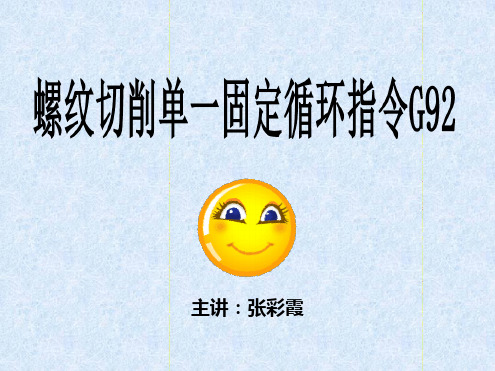
新课巩固
1. G92 指令的格式 2. G92 指令的动作演示(视频) 3. G92 指令的编程(实例)
4. 在数控车床上加工螺纹时的注意事项
布置作业
1.课堂作业:
(1 )复习课上内容。 (2 )教材P141 :第11 题 (做在作业本上)
2. 实习任务:
用G92 指令编写如下图所示工件的程序,并进行加工。
W25.0; U-3.8; G32 W-25.0 F1.5; G00 U3.8; W25.0; G00 X100.0 Z100.0; M05; M30;
新课导入
? G32指令主要用于一些单一、特殊高精度螺纹 (圆柱
螺纹、等螺距的锥螺纹和端面螺纹 )的切削加工,为了适 应一些多加工元素 (有圆柱面、圆锥面、圆弧面、螺纹面 等等)零件的切削加工,则引入了另一类加工指令——称为 螺纹切削单一固定循环指令 G92。另一方面, G32指令 加工时,车刀的切入、切出、返回均需编入程序,程序 量较长且易出错。所以从减少程序段的长度,提高程序 编制正确率的角度出发,亦引入 G92指令。那么,本次 课我们就共同来学习该指令的一些知识。
螺纹的总切深量为18mm背吃刀量分别为11mm05mm01mm和01mmgg3232指令主要用于一些单一指令主要用于一些单一特殊高精度螺纹特殊高精度螺纹圆柱圆柱螺纹螺纹等螺距的锥螺纹和端面螺纹等螺距的锥螺纹和端面螺纹的切削加工的切削加工为了适为了适应一些多加工元素应一些多加工元素有圆柱面有圆柱面圆锥面圆锥面圆弧面圆弧面螺纹面螺纹面等等等等零件的切削加工零件的切削加工则引入了另一类加工指令则引入了另一类加工指令称为称为螺纹切削单一固定循环指令螺纹切削单一固定循环指令gg9292
1.1mm 、0.5mm 、0.1mm 和0.1mm)
常见的数控车床螺纹加工代码

在数控车床上,G32、G76和G92是用于螺纹加工的G代码。
以下是每种代码的用法示例:G32 的用法示例:G32 是用于恒定螺距的单向螺纹切削。
以下是使用G32的一个简单示例:G00 X40 Z2 ; 快速定位到螺纹加工的起始点,X40是直径,Z2是距离工件端面的距离G32 Z-20 F2.0 ; 从Z2切削到Z-20,F2.0是螺距(每转进给量)```在这个示例中,刀具从Z2的位置开始,沿着Z轴向下移动到Z-20的位置,进行螺纹加工,螺距设置为2.0mm。
G76 的用法示例:G76 是一个复合螺纹切削循环,适用于加工更复杂的螺纹,如多线螺纹或变螺距螺纹。
以下是使用G76的一个示例:G00 X45 Z5 ; 快速定位到螺纹加工的起始点T0101 M08 ; 换刀至1号刀具,开启切削液G76 P(m)(r)(a) Q(△dmin) R(d)G76 X(u) Z(w) R(i) P(k) Q(△d) F(f)m:最后精加工次数,是模态值;r:螺纹倒角量,是模态值;a:表示刀尖角度;Δdmin:表示最小切入量;d:精加工余量,用半径编程指定;Δd :表示第一次粗切深(半径值);X 、Z:表示螺纹终点的坐标值;u:表示增量坐标值;w:表示增量坐标值;i:表示螺纹的半径余量i=0,,为切直螺纹;k:表示螺纹牙高;△d:第一次切入量;f:螺纹导程。
G92 的用法示例:G92 主要用于设置螺纹的固定循环,可以用于重复螺纹加工操作。
以下是使用G92的一个示例:G00 X40 Z5 ; 快速定位到螺纹加工的起始点G92 X36 Z-20 F2 ; 设置螺纹加工的循环,X36是螺纹的终点直径,Z-20是螺纹的终点Z 坐标,螺距为2M05 ; 停止主轴转动G00 X100 Z100 ; 快速退回到安全位置M30 ; 程序结束在这个示例中,G92用于设置螺纹的加工循环,每次循环都会重复执行到下一个Z深度,直到达到最终的螺纹深度。
螺纹加工数控编程
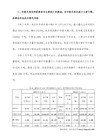
1、 G32用于公制螺纹加工、G33用于英制螺纹加工
2、 X(U)、 Z(W)为切削终点坐标、F 为螺纹导程
螺 纹 加 工 一 般 指 令
G32/G33与G01的区别是:通过脉冲编码器,能保证刀具在直线 移动时与主轴保持同步,即主轴旋转一周,刀具移动一个导程。
(二)应用类型 1、切削圆柱螺纹 G32/G33 Z(W)---F----
2、切削圆锥螺纹 G32/G33 X(U)---- Z(W)---3、切削端面螺纹 G32/G33 X(U)---- F----
F----
螺 纹 加 工 一 般 指 令
螺纹加工涉及6个方面的问题,编程时应多加注意:
1、主轴应指令恒转速(G97),螺纹加工中直径“X”是变化的
加 工 螺 纹 时 应 注 意 的 事 项
O0001 G50 X100. Z100. X59.1 G32 Z-53. F2 G97 M03 S600 G00 X62. T0101 Z5. G00 X62. Z5.
螺纹加工数控编程
螺纹加工指令
数控车床主要用于加工轴类、盘类等 回转体零件。机器中最常用的零件就是轴, 其作用是支撑零件、传递运动,如齿轮等, 齿轮一般通过螺纹实现轴向定位,所以螺 纹是轴类零件主要的组成面,掌握螺纹加 工的编程方法,对提高数控车削编程能力 意义重大。
本讲主要内容
一.螺纹概述 二.螺纹加工指令的格式 三.螺纹加工应注意的事项 四.螺纹加工举例 五.螺纹加工单一循环指令
加 工 螺 纹 时 应 注 意 的 事 项
径会变大Δ d ,加工内螺纹时直径会变小Δ d 。所以加工内螺纹时,孔径
应车到 d+Δ d ,加工外螺纹时,直径应车到 D-Δ d ,
• 常用螺纹切削的进给次数与背吃刀量 • (米制、双边) ( mm )
数控车床加工工艺编程-三角螺纹的编程

西门子系统螺纹循环指令LCYC97参数及含义
R100:螺纹起始点直径 R101:纵向轴螺纹起始点 R102:螺纹终点直径 R103:纵向轴螺纹终点 R104:螺纹导程值 R105:加工类型(数值:1,2) R106:精加工余量,无符号 R109:空刀导入量,无符号 R110:空刀退出量,无符号 R111:螺纹深度,无符号 R112:起始点偏移,无符号 R113:粗切次数,无符号 R114:螺纹头数,无符号
三角螺纹的编程
在西门子数控车床上加工螺纹,需要用到螺 纹加工的编程指令,那么我们来看一下螺纹 加工的编程指令是什么?先给大家介绍恒螺 距螺纹切削指令G33
பைடு நூலகம்
•恒螺距螺纹G33的指令格式 及含义
G33 X Z K SF_
x、z:螺纹加工的终点坐标 k:螺纹的螺距 sf:起点偏移量
•G33加工范围
圆柱螺纹 圆锥螺纹 外螺纹 内螺纹 单螺纹 多重螺纹
编程实例
参考程序
THANKS
螺纹切削循环指令编程
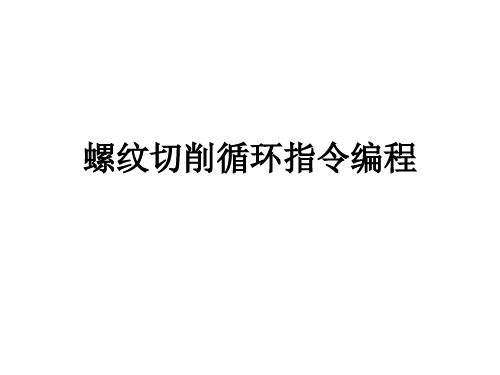
3、车削螺纹前圆柱体(孔)预加工尺寸控制 、车削螺纹前圆柱体(
4、螺纹车刀的安装与找正 、
4、螺纹车刀的安装与找正 、
4、螺纹车刀的安装与找正 、
4、螺纹车刀的安装与找正 、
4、螺纹车刀的安装与找正 、
5、螺纹车削刀具切入与切出行程的确定 、
5、螺纹车削刀具切入与切出行程的确定 、
三、螺纹切削单一固定循环指令编 程(G92) )
4、编程举例 、
4、编程举例 、
四、螺纹切削复合循环指令编程 (G76) )
1、指令格式 、
1、指令格式 、
1、指令格式 、
2、刀具走刀路线分析 、
2、刀具走刀路线分析 、
2、刀具走刀路线分析 、
3、指令应用说明 、
4、编程举例 、
4、编程举例 、
零件加工工艺分析: 零件加工工艺分析: ●对零件进行外圆表面粗、精加工并倒角至图纸尺 寸; ●螺纹退刀槽加工; ●M20×2.5螺纹粗、精加工; ●工件切断并保证全长。 零件加工所使用的刀具: 零件加工所使用的刀具: ⑴外圆车刀T0101; ⑵切槽刀T0202(刀宽为3mm); ⑶60°螺纹车刀T0303。
1、指令格式 、
1、指令格式 、
2、刀具走刀路线分析 、
3、指令应用说明 、
3、指令应用说明 、
4、编程举例 、
编写如图所示工件加工程序, 编写如图所示工件加工程序,工件 毛坯为¢32mm. 毛坯为¢32mm.
4、编程举例 、
零件加工工艺路线分析: 零件加工工艺路线分析: ⑴工件外圆表面的粗加工与精加工并倒角; ⑵螺纹退刀槽加工; ⑶螺纹的粗加工与精加工。 零件加工所使用的刀具: 零件加工所使用的刀具: ⑴外圆车刀T0101; ⑵切槽刀T0202(刀宽为3mm); ⑶60°螺纹车刀T0303。
螺纹加工指令G32

螺纹加工指令G32、G92、G76数控车床可以加工直螺纹、锥螺纹、端面螺纹,见图所示。
加工方法上分为单行程螺纹切削、简单螺纹切削循环和螺纹切削复合循环。
(1)单行程螺纹切削G32指令格式:G32 X(U)____ Z(W)____ F____指令中的X(U)、Z(W)为螺纹终点坐标,F为螺纹导程。
使用G32指令前需确定的参数如图a所示,各参数意义如下:L:螺纹导程,当加工锥螺纹时,取X方向和Z方向中螺纹导程较大者;α:锥螺纹锥角,如果α为零,则为直螺纹;δ1、δ2:为切入量与切除量。
一般δ1=2~5mm、δ2=(1/4~1/2)δ1。
图a图b螺纹加工实例:如图b所示,螺距L=3.5mm,螺纹高度=2mm,主轴转速N=514r/min,δ1=2mm、δ2=lmm,分两次车削,每次车削深度为lmm。
加工程序为:N0 G50 X50.0 Z70.0 设置工件原点在左端面N2 S514 T0202 M08 M03 指定主轴转速514r/min、调螺纹车刀N4 G00 Xl2.0 Z72.0;快速走到螺纹车削始点(12.0,72.0)N6 G32 X41.0 Z29.0 F3.5;螺纹车削N8 G00 X50.0;沿X轴方向快速退回N10 Z72.0;沿Z轴方向快速退回N12 X10.0;快速走到第二次螺纹车削起始点N14 G32 X39.0 Z29.0;第二次螺纹车削N16 G00 X50.0;沿X轴方向快速退回N18 G30 U0 W0 M09;回参考点N20 M30;程序结束(2)螺纹切削循环指令G92螺纹切削循坏G92为简单螺纹循环,该指令可以切削锥螺纹和圆柱螺纹,其循环路线与前述的单一形状固定循环基本相同,只是F后续进给量改为螺距值。
其指令格式为:G92 X(U)____Z(W)____R____F____;如图为螺纹切削循环图。
刀具从循环起点A开始,按A→B→C→D→A路径进行自动循环。
图中虚线表示刀具快速移动,实线表示按F指定的工作速度移动。
- 1、下载文档前请自行甄别文档内容的完整性,平台不提供额外的编辑、内容补充、找答案等附加服务。
- 2、"仅部分预览"的文档,不可在线预览部分如存在完整性等问题,可反馈申请退款(可完整预览的文档不适用该条件!)。
- 3、如文档侵犯您的权益,请联系客服反馈,我们会尽快为您处理(人工客服工作时间:9:00-18:30)。
2.螺纹加工切削用量的选用(1)
(1)主轴转速 n 由于螺距一定,随着转速的增大,进
给速度(Vf=nf)会随之增大,相应的惯性 也会增大,若数控系统加减速性能较差,就 会产生较大的误差,因此对经济型数控车床, 加工螺纹时,转速一般取值为:
n*p≤ 3500∽ 4000 对于经济型数控车床,若螺距为3,转速 为1500r/min,合适吗?
,加工外螺纹时,直径应车
到 D-Δ d ,
4.螺纹车刀的安装与找正(1)
车螺纹时,为了保证牙型正确,对装刀提 出了较严格的要求。装刀时刀尖高低应对 准工件轴线,并且车刀刀尖角的中心线必 须与工件轴线严格保持垂直,这样车出的 螺纹,其两牙型半角才会相等;如果把车 刀装歪,就会产生牙型歪斜,如图所示。
分析: 1、切削用量选择
n=600r/min F=2 切削深度ap按表查
查得:分5次切削 ap1=0.9、ap2=0.6 ap3= 0.6、ap4= 0.4
ap5= 0.1 得:每次切削终点X坐标 值:
切削起点Z坐标值: Z1=5.
终点Z坐标值: Z2= -53.
3.螺纹加工注意事项(1)
1、系统若无“退尾” 功能,螺纹加工前,应先加工出退 刀槽 “退尾” 功能的作用是,在加工到终点前,刀具沿 45度方向退出。加工退刀槽的目的是保证切屑能够及时落 下,防止堆积,产生过大的抗力造成崩刀。
切削起点Z坐标值: Z1=5.
终点Z坐标值: Z2= -53.
ap5= 0.1
得:X坐标值:
3.螺纹加工注意事项(3)
3、螺纹加工结束后,直径会发生变化。
切削加工过程是一个挤压、塑性变形、断裂的过程,加工外螺
纹时直径会变大Δ d ,加工内螺纹时直径会变小Δ d 。所以加工内
螺纹时,孔径应车到 d+Δ d
旋合长度代号 顶径公差带代号
中径公差带代号
公称直径
普通螺纹代号
3.螺纹标记含义(2)
(2)内螺纹标记 内螺纹标记如图所示。
M20×1.5—6H—S— LH
螺纹旋向 螺纹短旋合长度 中径和顶径公差带代号 螺距(指细牙) 公称直径 普通螺纹代号
3.螺纹标记含义(3)
(3)关于螺纹标记的几点说明: 3)对于左旋螺纹,应在旋合长度之后标注 “LH”代号,右旋螺纹不需要标注; 4)对于螺纹旋合长度,分为三组,即短旋合长 度(S)、中等旋合长度(N)和长旋合长度 (L),一般采用中等旋合长度。
(2)斜进式螺纹加工
刀具沿着螺纹一侧顺次进刀。 这种加工方法适合于大螺距 螺纹加工,在螺纹精度要求 不是很高的情况下加工更为 方便,可以做到一次成型。 在加工较高精度螺纹时,可 以先采用斜进法粗加工,然 后用直进法进行精加工。但 要注意刀具起始点定位要准 确,否则会产生“乱牙”现 象,造成零件报废。
原点
X1=59.1、X2=58.5 X3= 57.9、X4= 57.5 X5= 57.4
2、δ1、δ2计算 δ 1=n× p/400= 600× 2/400=3 δ 1=n× p/1800= 600× 2/1800=2/3
取δ 1=5、 δ 2=3
查得:分5次切削
得:
ap1=0.9、ap2=0.6
ap3= 0.6、ap4= 0.4
0.6
0.7
0.7
0.7
0.8
0.2
0.4
0.6
0.6
0.6
0.6
0.6
0.16Βιβλιοθήκη 0.40.40.4
0.6
0.6
0.1
0.4
0.4
0.4
0.4
0.15
0.4
0.4
0.4
0.2
0.2
0.4
8次
0.15
0.3
9次
0.2
原点
X1=59.1、X2=58.5 X3= 57.9、X4= 57.5 X5= 57.4
二、螺纹加工工艺设计
1.螺纹加工走刀路线设计(1)
直进法螺纹加工 车削过程是在每次往复行 程后车刀沿横向进刀,通 过多次行程把螺纹车削好。 这种加工方法由于刀具两 侧刃同时工作,切削力较 大,但排屑困难,容易产 生扎刀现象,但牙型正确, 一般用于车削螺距小于3 ㎜的螺纹。
1.螺纹加工走刀路线设计(2)
数控车床螺纹切削循环 指令编程
一、螺纹基础知识
1.常见螺纹类型(1)
(1)按照用途分类 螺纹按用途不同可 分为联接螺纹和传动螺纹。
1.常见螺纹类型(2)
(2)按照牙型分类 按牙型不同分为三角形、 圆形、矩形、梯形、锯齿形螺纹。 (3)按照螺旋线旋向分类 按螺旋线方向不 同分为右旋螺纹和左旋螺纹。 (4)按照螺旋线数分类 按螺旋线数多少分 为单线螺纹和多线螺纹。 (5)按照母体形状分类 按母体形状不同分 为圆柱螺纹和圆锥螺纹。
2.螺纹加工切削用量的选用(2)
(2)进给速度 螺纹加工时数控车床主轴转 速和工作台纵向进给量存在严格数量关系, 即主轴旋转1转,工作台移动一个待加工工 件螺纹导程距离。因此在加工程序中只要给 出主轴转速和螺纹导程,数控系统会自动运 算并控制工作台纵向移动速度。
2.螺纹加工切削用量的选用(3)
(3)背吃刀量 如果螺纹牙型较深、螺距较 大,则可采用分次进给方式进行加工。每次 进给的背吃刀量用螺纹深度减去精加工背吃 刀量所得的差按递减规律分配。常用螺纹加 工切削次数与背吃刀量数值如表所示。
螺距 牙深
1次 2次 3次
4次
切削
次数
5次
及对
应背 吃刀
6次
量
(㎜) 7次
公制螺纹
21.0.螺纹1.5加工2.切0 削2用.5 量3的.0 选用3.5(84).0
0.649 0.974 1.299 1.624 1.949 2.273 2.598
0.7
0.8
0.9
1.0
1.2
1.5
1.5
0.4
0.6
2.螺纹概述
1、相邻两牙型间的距离为螺距p 2、螺距与螺纹线数的乘积为“导程”
S= p× L L(线数) 3、螺纹大径为公称直径,小径为:
d=D—0.6495p× 2 0.6495p为牙高
4、国标中规定了螺纹的简化画法 及标注
3.螺纹标记含义(1)
(1)外螺纹标记 外螺纹标记如图所示。
M 20—5g 6g— S
3.螺纹加工注意事项(2)
2、切削螺纹时,刀具应该有足够的引入、引出长度δ1、 δ2 数控伺服系统本身有“滞后性”,在螺纹加工的“起始段”
和“结束段”会出现螺距不规则现象,故应有引入、引出长度。 计算公式如下:δ1=n× p/400、 δ2=n× p/1800
分析: 1、切削用量选择
n=600r/min F=2 切削深度ap按表查