内燃机械加工制造时曲轴强度的控制方法分析(正式)
曲轴的受力情况分析及主要强化方式
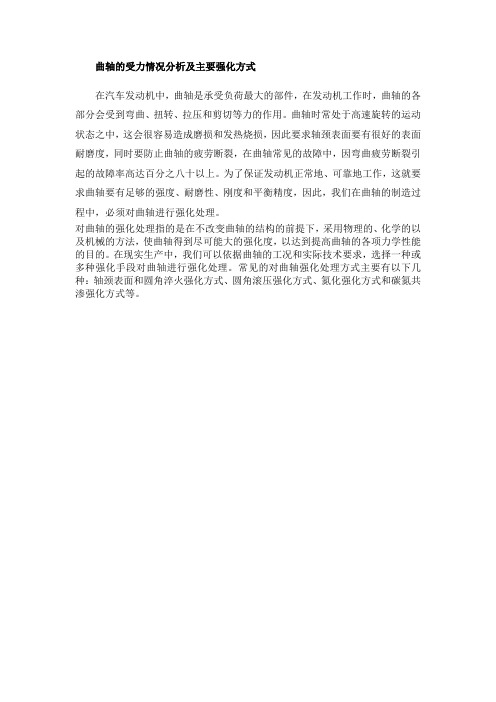
曲轴的受力情况分析及主要强化方式
在汽车发动机中,曲轴是承受负荷最大的部件,在发动机工作时,曲轴的各部分会受到弯曲、扭转、拉压和剪切等力的作用。
曲轴时常处于高速旋转的运动状态之中,这会很容易造成磨损和发热烧损,因此要求轴颈表面要有很好的表面耐磨度,同时要防止曲轴的疲劳断裂,在曲轴常见的故障中,因弯曲疲劳断裂引起的故障率高达百分之八十以上。
为了保证发动机正常地、可靠地工作,这就要求曲轴要有足够的强度、耐磨性、刚度和平衡精度,因此,我们在曲轴的制造过程中,必须对曲轴进行强化处理。
对曲轴的强化处理指的是在不改变曲轴的结构的前提下,采用物理的、化学的以及机械的方法,使曲轴得到尽可能大的强化度,以达到提高曲轴的各项力学性能的目的。
在现实生产中,我们可以依据曲轴的工况和实际技术要求,选择一种或多种强化手段对曲轴进行强化处理。
常见的对曲轴强化处理方式主要有以下几种:轴颈表面和圆角淬火强化方式、圆角滚压强化方式、氮化强化方式和碳氮共渗强化方式等。
内燃机车柴油机锻钢曲轴氮化变形超差校直工艺方法
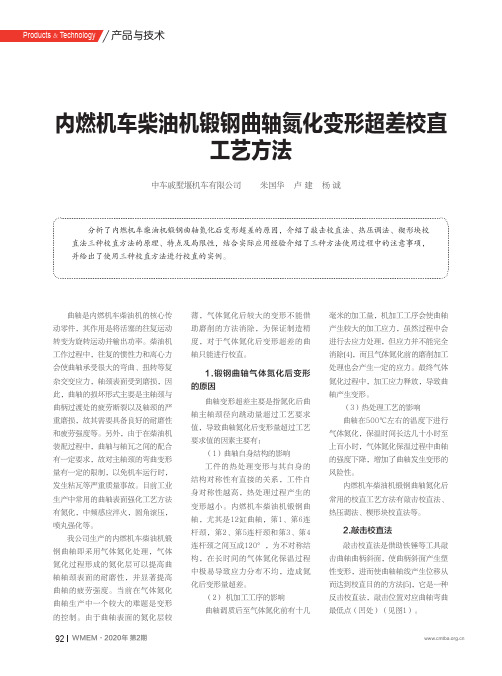
产品与技术内燃机车柴油机锻钢曲轴氮化变形超差校直工艺方法中车戚墅堰机车有限公司 朱国华 卢 建 杨 诚分析了内燃机车柴油机锻钢曲轴氮化后变形超差的原因,介绍了敲击校直法、热压调法、楔形块校直法三种校直方法的原理、特点及局限性,结合实际应用经验介绍了三种方法使用过程中的注意事项,并给出了使用三种校直方法进行校直的实例。
曲轴是内燃机车柴油机的核心传动零件,其作用是将活塞的往复运动转变为旋转运动并输出功率。
柴油机工作过程中,往复的惯性力和离心力会使曲轴承受很大的弯曲、扭转等复杂交变应力,轴颈表面受到磨损,因此,曲轴的损坏形式主要是主轴颈与曲柄过渡处的疲劳断裂以及轴颈的严重磨损,故其需要具备良好的耐磨性和疲劳强度等。
另外,由于在柴油机装配过程中,曲轴与轴瓦之间的配合有一定要求,故对主轴颈的弯曲变形量有一定的限制,以免机车运行时,发生粘瓦等严重质量事故。
目前工业生产中常用的曲轴表面强化工艺方法有氮化,中频感应淬火,圆角滚压,喷丸强化等。
我公司生产的内燃机车柴油机锻钢曲轴即采用气体氮化处理,气体氮化过程形成的氮化层可以提高曲轴轴颈表面的耐磨性,并显著提高曲轴的疲劳强度。
当前在气体氮化曲轴生产中一个较大的难题是变形的控制。
由于曲轴表面的氮化层较薄,气体氮化后较大的变形不能借助磨削的方法消除,为保证制造精度,对于气体氮化后变形超差的曲轴只能进行校直。
1.锻钢曲轴气体氮化后变形的原因曲轴变形超差主要是指氮化后曲轴主轴颈径向跳动量超过工艺要求值,导致曲轴氮化后变形量超过工艺要求值的因素主要有:(1)曲轴自身结构的影响工件的热处理变形与其自身的结构对称性有直接的关系,工件自身对称性越高,热处理过程产生的变形越小。
内燃机车柴油机锻钢曲轴,尤其是12缸曲轴,第1、第6连杆颈,第2、第5连杆颈和第3、第4连杆颈之间互成120°,为不对称结构,在长时间的气体氮化保温过程中极易导致应力分布不均,造成氮化后变形量超差。
保证曲轴加工刚性的措施

保证曲轴加工刚性的措施曲轴是内燃机的核心部件之一,承受着高强度、高频率的复杂载荷。
曲轴加工刚性直接关系到整个发动机的性能和使用寿命。
因此,在曲轴加工过程中采取必要的措施保证其加工刚性非常重要。
本文将从选材设计、加工工艺和工控系统三个方面介绍保证曲轴加工刚性的措施。
选材设计材料选择曲轴所使用的钢材应是具有高强度、高韧性和良好韧性与硬度的合金钢,在吸收冲击和承载载荷时必须具有高硬度和高耐久性。
目前常用的曲轴材料有40Cr、42CrMo、35CrMo等。
40Cr是一种常见的中碳合金钢,具有良好的可加工性和热处理性,常用于制作低扭矩、低功率发动机。
42CrMo是一种高强度、高韧性的钢材,能够支撑高效率和高功率引擎的工作。
35CrMo钢材具有高温强度和较高的冲击韧性,适用于高负荷生产过程中的曲轴需求。
钢材的选用应根据具体的车型、需要承受的力量等因素进行定制。
设计结构优化为了保证加工性能和强度,曲轴的结构应有序列优化,同时考虑满足动力需求,安装规则和进气系统比例等因素。
曲轴需要用于支承和传输动力,如何平衡传输和支承双重要素也需要进行设计和优化。
结构设计改进包括但不限于增加轴头半径、增加主轴直径、调整强度分布和加工槽数量等措施。
可以通过晶界控制、表面处理等工艺手段来实现材质强度提升和结构性优化,以提高加工刚性。
加工工艺曲轴是数控加工的一个重要应用对象,其加工过程中生产出的表面质量、直径规格等指标是影响加工刚性的重要因素。
以下是几个常见的曲轴加工工艺措施:粗加工钢坯经粗加工之后应先经调控退火,然后继续进行精加工。
粗加工时,曲轴的长度应该比终加工长度长30-50mm,以便可以进行锯除头尾、抛光、焊接等操作。
同时应注意曲轴的端面要垂直于曲轴轴线,这可以通过专业设备和工具实现。
精加工精加工是保证曲轴加工刚性的关键。
曲轴轴颈磨削过程中应采用磨削后加工磨削工艺,在一定的磨削精度下,保证通轴加工轮廓和相邻磨削之间的常量间距。
发动机曲轴强度分析
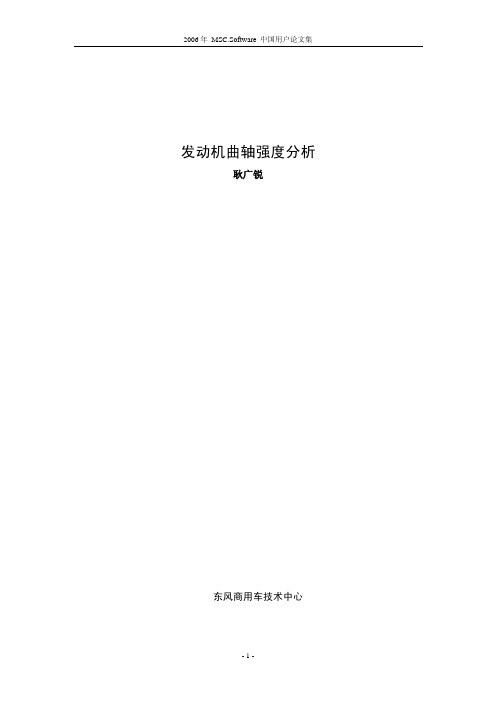
新方案一 2.21 2.35
新方案二 2.22 2.41
新方案三 1.95 2.18
4 分析结论
4.1 强度
从表 3 可以看出,压工况下新方案一曲轴的应力比现生产应力要稍高一些,最大增幅 (内圆角)为 18%(45Mpa),新方案二较新方案一曲柄销增大了 3mm(增大 3.6%),但外圆角应 力几乎没有改变,内圆角应力略有降低(8Mpa,降 2.8%),说明增加曲轴的曲柄销直径对降 低圆角的应力水平效果较小;新方案三与新方案一相比圆角半径减小 0.5mm(减小 9%),外 圆角应力增大 14.5%(42Mpa),内圆角应力增大 7.9%(23Mpa),说明曲轴内、外圆角半径对 圆角的应力水平影响显著,圆角的应力水平与圆角半径成反比。
nσ
=
σ
aka
(
σ −1 βεσ )
+ ϕσ σ
m
kσ =1.0。
β=1.3。
-5-
(1)
2006 年 MSC.Software 中国用户论文集
εσ=0.64
ϕσ
=
2σ −1 − 1.5σ −1 1.5σ −1
= 0.33
考虑到多缸发动机曲轴一般扭转振动以及动载荷对曲轴的冲击作用将增大曲轴应力。
因此,再引用动力强化系数 λd 和动荷系数 C 修正原有的安全系数 nσ :
4.2 安全系数
一般钢曲轴的安全系数大于 1.5 即可,从表 5 可以看出,新设计曲轴各方案的安全系 数均已达到曲轴设计所规定的许用范围之内,但略小于现生产。
5 参考文献
[1] MSC Nastran Quick Reference Guide[k]. [2] 陆际清,沈祖.汽车发动机设计[M]. 北京:清华大学出版社,1993.
曲轴强度的传统方法与多体动力学方法
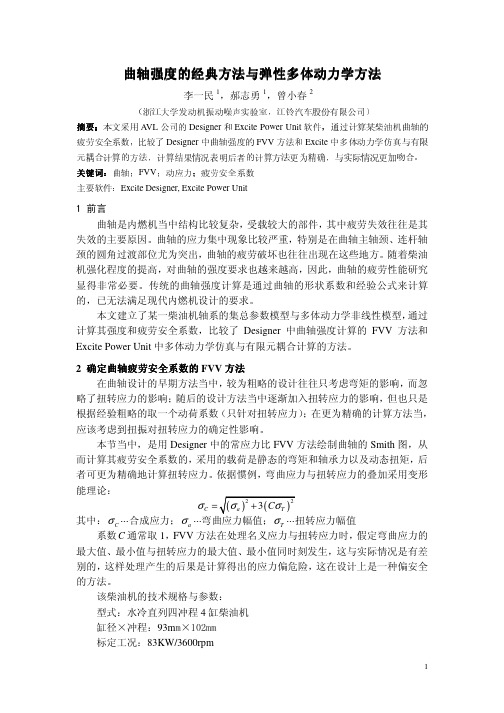
曲轴强度的曲轴强度的经典经典经典方法与方法与方法与弹性多体动力学方法弹性多体动力学方法弹性多体动力学方法李一民1,郝志勇1,曾小春2(浙江大学发动机振动噪声实验室,江铃汽车股份有限公司)摘要摘要::本文采用AVL 公司的Designer 和Excite Power Unit 软件,通过计算某柴油机曲轴的疲劳安全系数,比较了Designer 中曲轴强度的FVV 方法和Excite 中多体动力学仿真与有限元耦合计算的方法,计算结果情况表明后者的计算方法更为精确,与实际情况更加吻合。
关键词关键词::曲轴;FVV ;动应力;疲劳安全系数主要软件:Excite Designer, Excite Power Unit1 前言曲轴是内燃机当中结构比较复杂,受载较大的部件,其中疲劳失效往往是其失效的主要原因。
曲轴的应力集中现象比较严重,特别是在曲轴主轴颈、连杆轴颈的圆角过渡部位尤为突出,曲轴的疲劳破坏也往往出现在这些地方。
随着柴油机强化程度的提高,对曲轴的强度要求也越来越高,因此,曲轴的疲劳性能研究显得非常必要。
传统的曲轴强度计算是通过曲轴的形状系数和经验公式来计算的,已无法满足现代内燃机设计的要求。
本文建立了某一柴油机轴系的集总参数模型与多体动力学非线性模型,通过计算其强度和疲劳安全系数,比较了Designer 中曲轴强度计算的FVV 方法和Excite Power Unit 中多体动力学仿真与有限元耦合计算的方法。
2 确定曲轴疲劳安全系数的FVV 方法在曲轴设计的早期方法当中,较为粗略的设计往往只考虑弯矩的影响,而忽略了扭转应力的影响;随后的设计方法当中逐渐加入扭转应力的影响,但也只是根据经验粗略的取一个动荷系数(只针对扭转应力);在更为精确的计算方法当,应该考虑到扭振对扭转应力的确定性影响。
本节当中,是用Designer 中的常应力比FVV 方法绘制曲轴的Smith 图,从而计算其疲劳安全系数的,采用的载荷是静态的弯矩和轴承力以及动态扭矩,后者可更为精确地计算扭转应力。
内燃机曲轴强度计算
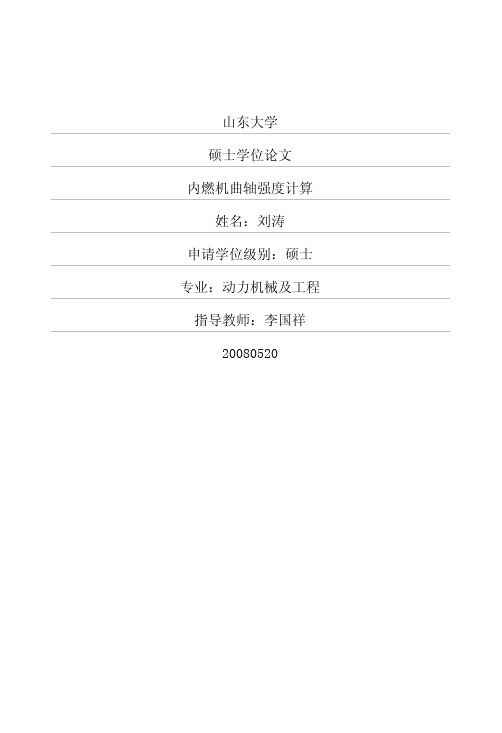
山东人学硕十学侮论文
faclQf of纛l lel accurately。ThrOugh the test of crankshaft s{atic s£_fess lo proVe the 丘nite element method’s computation model,the dependency of the quality of l疑esh was disellssed。l透eanwhile,{珏e fesul£showed{he graVi£a£ion and centri蚕lgal force could be ne91ected in the analysis of crankshaft static stress.Through the
山东大学 硕士学位论文 内燃机曲轴强度计算 姓名:刘涛 申请学位级别:硕士 专业:动力机械及工程 指导教师:李国祥
20080520
摘甍
本页已使用福昕阅读器进行编辑。 福昕软件(C)2005-2009,版权所有, 仅供试用。
摘要
曲轴是发动机中最重要的零件之一。曲轴的疲劳失效及断裂将弓I起其它 零件随之损坏,甚至造成安全事故,特别是随着发动机的动力性和可靠性要 求的提高,其强度问题变得更加重要。然而,对曲轴的疲劳强度进行准确预 测是一件困难的事。寻找一种实用性强、精度可靠的曲轴强度考核方法,对 企业来说具有较强的实际意义。本文以WD615型柴油机曲轴为主要研究对 象,引入现代动力学仿真及有限元法对曲轴常规强度设计方法进行改良,结 合有限元法与非线性多体动力学仿真求取曲轴的动态应力,进而进行疲劳计 算,并通过弯曲疲劳试验考察曲轴的实际强度。
本文所傲的主要工作内容可概括为以下几点: 1.利用动力学软件ADAMS对曲轴系统进行多刚体运动学及动力学仿 真,为曲轴强度设计提供较为准确静载荷边界。比较分析认为,在计算活塞 加速度、活塞侧击力、曲柄销载荷时,应用传统簸法具有快速、简易可信的 优点;但当需要计算主轴承载荷时,现代的仿真计算方法在操作上就更简单, 且精度高,并且可以为整个轴系动力学分析提供丰富、全面的仿真数据。 2.在分析比较多种常规莹轴强度设计方法的基础上,提出改进方法, 运用实体建模软件计算截面模量,有限元法计算威力分布状况,可较为准确 求取圆焦的应力集中系数。通过曲轴静态应力试验验证有限元计算模型,研 究应力计算精度对网格的依耐性;同时阐明了重力和离心力在曲轴静应力分 析中是可以忽略不计的。对wD615型柴油机曲轴进行疲劳计算,证明了改 进方法的J下确性。 3.结合有限元法和非线性多体动力学软件EXCITE对轴系总成进行动 态响应研究,考虑弯曲、扭转的耦合作用,求取曲轴在整个工作循环的动态 应力,并运用疲劳分析软件分析其疲劳强度。比较分析说明在进行曲轴详细 设计或对轴承润滑及强度考核时不能忽略曲轴的柔性作用。阐述了基于动态 应力的疲劳强度分析比常规疲劳强度分析更具说服力。 4.在谐振式弯益疲劳试验台上,利用疲劳极限统计分析法对本文研究 的曲轴进行疲劳试验,从试验研究的角度考核曲轴的疲劳强度。
浅析内燃机机械维修中的常见问题及控制措施
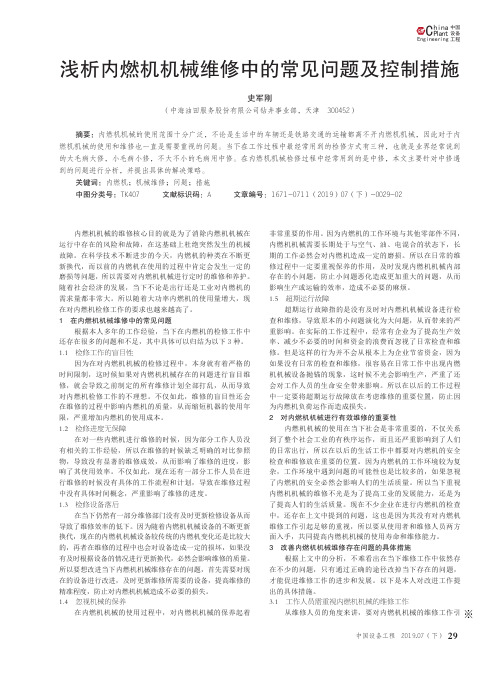
29中国设备工程Engineer ing hina C P l ant中国设备工程 2019.07 (下)浅析内燃机机械维修中的常见问题及控制措施史军刚(中海油田服务股份有限公司钻井事业部,天津 300452)摘要:内燃机机械的使用范围十分广泛,不论是生活中的车辆还是铁路交通的运输都离不开内燃机机械,因此对于内燃机机械的使用和维修也一直是需要重视的问题。
当下在工作过程中最经常用到的检修方式有三种,也就是业界经常说到的大毛病大修,小毛病小修,不大不小的毛病用中修。
在内燃机机械检修过程中经常用到的是中修,本文主要针对中修遇到的问题进行分析,并提出具体的解决策略。
关键词:内燃机;机械维修;问题;措施中图分类号:TK407 文献标识码:A 文章编号:1671-0711(2019)07(下)-0029-02内燃机机械的维修核心目的就是为了消除内燃机机械在运行中存在的风险和故障,在这基础上杜绝突然发生的机械故障。
在科学技术不断进步的今天,内燃机的种类在不断更新换代,而以前的内燃机在使用的过程中肯定会发生一定的磨损等问题,所以需要对内燃机机械进行定时的维修和养护。
随着社会经济的发展,当下不论是出行还是工业对内燃机的需求量都非常大。
所以随着大功率内燃机的使用量增大,现在对内燃机检修工作的要求也越来越高了。
1 在内燃机机械维修中的常见问题根据本人多年的工作经验,当下在内燃机的检修工作中还存在很多的问题和不足,其中具体可以归结为以下3种。
1.1 检修工作的盲目性因为在对内燃机机械的检修过程中,本身就有着严格的时间限制,这时候如果对内燃机机械存在的问题进行盲目维修,就会导致之前制定的所有维修计划全部打乱,从而导致对内燃机检修工作的不理想。
不仅如此,维修的盲目性还会在维修的过程中影响内燃机的质量,从而缩短机器的使用年限,严重增加内燃机的使用成本。
1.2 检修进度无保障在对一些内燃机进行维修的时候,因为部分工作人员没有相关的工作经验,所以在维修的时候缺乏明确的对比参照物,导致没有显著的维修成效,从而影响了维修的进度,影响了其使用效率。
轴的强度校核方法
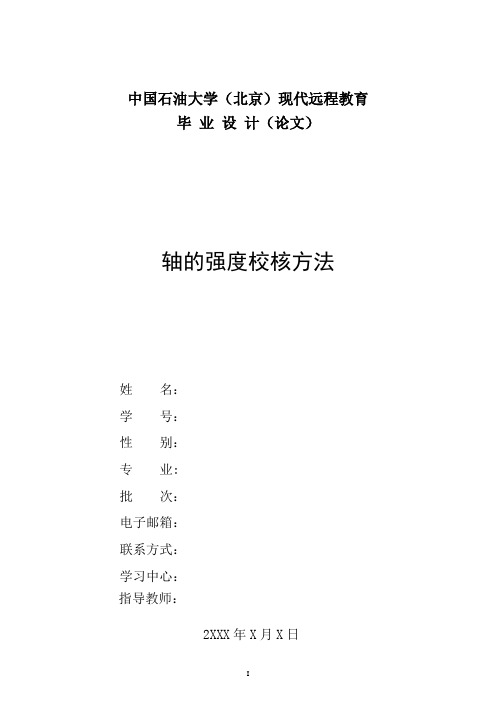
中国石油大学(北京)现代远程教育毕业设计(论文)轴的强度校核方法姓名:学号:性别:专业:批次:电子邮箱:联系方式:学习中心:指导教师:2XXX年X月X日中国石油大学(北京)现代远程教育毕业设计(论文)轴的强度校核方法摘要轴是用来支承回转运动零件,如带轮、齿轮、蜗轮等,同时实现同一轴上不同零件间的回转运动和动力的传递的重要的零件。
为实现机械产品的完整和可靠设计,轴的设计应考虑选材、结构、强度和刚度等要求。
并应对轴的材料或设备的力学性能进行检测并调节,轴的强度校核应根据轴的具体受载及应力情况,采取相应的计算方法,并恰当地选取其许用应力。
最后确定轴的设计能否达到使用要求,对轴的设计十分重要。
本文根据轴的受载及应力情况,介绍了几种典型的常用的对轴的强度校核计算的方法,并对如何精确计算轴的安全系数做了具体的介绍。
当校核结果如不满足承载要求时,则必须修改原结构设计结果,再重新校核。
最后,本文对提高轴的疲劳强度和刚度提出相应改进方法,并对新材料,新技术的应用进行了展望。
关键词:轴;强度;弯矩;扭矩;目录第一章引言 (5)1.1轴类零件的特点 (5)1.2轴类零件的分类 (6)1.3轴类零件的设计要求 (6)1.3.1、轴的设计概要 (6)1.3.2、轴的材料 (6)1.3.3、轴的结构设计 (7)1.4课题研究意义 (9)第二章轴的强度校核方法 (11)2.1强度校核的定义 (11)2.2常用的轴的强度校核计算方法 (11)2.2.1按扭转强度条件计算: (11)2.2.2按弯曲强度条件计算: (13)2.2.3按弯扭合成强度条件计算 (13)2.2.4精确计算(安全系数校核计算) (20)第三章提高轴的疲劳强度和刚度的措施 (25)3.1合理的选择轴的材料 (25)3.2合理安排轴的结构和工艺 (25)3.3国内外同行业新材料、新技术的应用现状 (26)总结 (31)参考文献 (32)第一章引言1.1轴类零件的特点轴是组成各类机械的主要和典型的零件之一,主要起支承传动零部件,传递扭矩和承受载荷的作用。
内燃机曲轴粗加工定心工序演变及选用分析
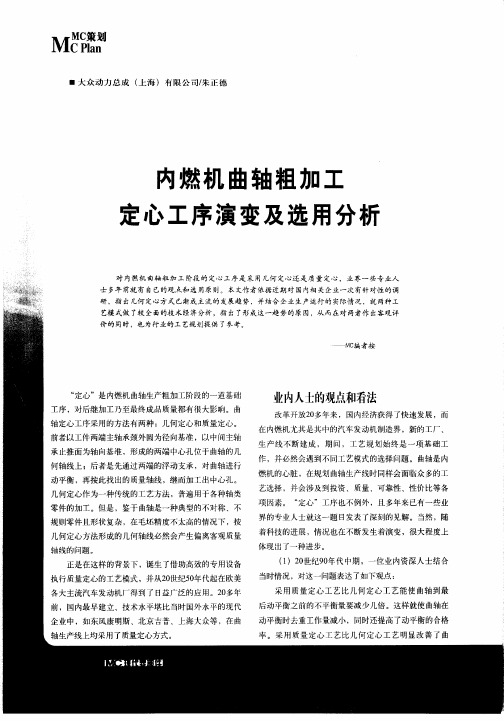
_ 大 众 动 力 总 成 ( 海 )有 限 公 司/ 上 朱正 德
内燃机 曲轴粗加工
定心工序演变及选用分析
对 内燃 机 曲轴粗 加 工 阶段 的 定心 工序 是 采 用几何 定心还 是 质 量 定 心 ,业 界 一些 专 业人
士 多年前就有 自已的观点和选 用原 则。本文作者依据近期对国内相关企业一次有针对性的调
进行动平衡时 ,初始不平衡量可能超 出平衡机要求而 无 法平衡。在这种 情况下应 优先选 用质量 定心机 。 ( )近 期 ,在 一些 主流汽车 发动机 厂工艺 规划 人 3 员的交流中 ,则进一 步形成 了如 下共识 :
传统 的几何定心方法又重新取得主流地位呢?
两种工艺模式的技术经济性分析
各大主流汽车 发动机厂得到 了 日益广 泛的应用。2 多年 0
前 ,国内最早 建立 、技术水平堪 比当时国外水平的现代
( )2 世纪9 年代 中期 ,一位业 内资深人 士结合 1 0 0
当时情 况 ,对这一 问题表达 了如下观点 : 采 用质 量定 心工 艺 比几何 定心 工艺 能使 曲轴 到最 后动平衡之前的 不平衡量 要减 少几倍 。这样就使 曲轴在
轴线的问题。
艺选择 ,并会涉及到投资 、质量、可靠性 、性价比等各
项 因素 。 “ 定心 ”工序也 不例 外 ,且多年来 已有一些业 界的专业人士就这一题 目发表 了深 刻的见解。当然 ,随 着科技的进展 ,情况也在 不断发生着演变 ,很大程度上 体现出了一种进步 。
正是 在这样的背景下 ,诞生 了借助高效的专用设备 执行 质量定心 的工艺模式 ,并从2 世纪5 年代起在欧美 0 0
10 0 %
柴油机曲轴强度的三维有限元分析

柴油机曲轴强度的三维有限元分析
曲轴是汽车发动机的核心部件,强度的耐受力是汽车发动机的重要性能指标之一。
随着汽车发动机的发展,柴油机曲轴的强度是汽车发动机比较重要的研究课题。
柴油机曲轴强度的研究主要通过有限元分析来进行,有限元分析是一种计算机模拟技术,可以很好地表示柴油机曲轴的强度。
通过将复杂的多维几何模型转换为有限元数据,可以快速地模拟出柴油机曲轴的强度。
在进行有限元分析之前,必须首先建立柴油机曲轴的三维模型,用于准确表示曲轴的详细几何信息和物理参数,其中最重要的是曲轴的弹性参数。
模型的建立可以通过CAD软件或CATIA软件完成,而且可以很容易地调整和改进曲轴的几何尺寸和物理参数。
接下来,就需要将柴油机曲轴的三维模型转换为有限元模型,有限元模型可以表示曲轴的几何尺寸和物理参数,这也是有限元分析的关键步骤。
在有限元模型的建立中,还要考虑柴油机曲轴的热应力和振动响应的影响,以便更准确地模拟曲轴的强度。
有了有限元模型,就可以灵活地进行有限元分析,开始对曲轴的强度进行模拟。
有限元分析需要指定曲轴的应力状态和荷载情况,根据不同的应力状态和荷载情况,可以分析出曲轴的极限强度和疲劳寿命。
此外,还可以通过有限元分析,更精确地研究柴油机曲轴的热应力和振动响应,以及曲轴的不同部件在受力和受荷的分布情况,这些
将有助于更好地设计柴油机曲轴,提高曲轴的强度和可靠性。
总之,利用有限元分析,可以有效地研究柴油机曲轴的强度,而有限元分析的过程至少包括三维模型的建立,有限元模型的建立和有限元分析,这是实现柴油机曲轴强度可靠性评估的关键环节。
试论内燃机曲轴结构强度问题对结构设计的影响
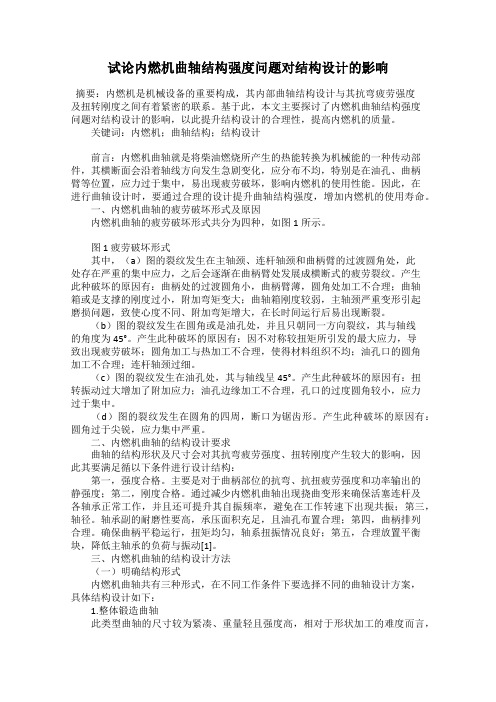
试论内燃机曲轴结构强度问题对结构设计的影响摘要:内燃机是机械设备的重要构成,其内部曲轴结构设计与其抗弯疲劳强度及扭转刚度之间有着紧密的联系。
基于此,本文主要探讨了内燃机曲轴结构强度问题对结构设计的影响,以此提升结构设计的合理性,提高内燃机的质量。
关键词:内燃机;曲轴结构;结构设计前言:内燃机曲轴就是将柴油燃烧所产生的热能转换为机械能的一种传动部件,其横断面会沿着轴线方向发生急剧变化,应分布不均,特别是在油孔、曲柄臂等位置,应力过于集中,易出现疲劳破坏,影响内燃机的使用性能。
因此,在进行曲轴设计时,要通过合理的设计提升曲轴结构强度,增加内燃机的使用寿命。
一、内燃机曲轴的疲劳破坏形式及原因内燃机曲轴的疲劳破坏形式共分为四种,如图1所示。
图 1 疲劳破坏形式其中,(a)图的裂纹发生在主轴颈、连杆轴颈和曲柄臂的过渡圆角处,此处存在严重的集中应力,之后会逐渐在曲柄臂处发展成横断式的疲劳裂纹。
产生此种破坏的原因有:曲柄处的过渡圆角小,曲柄臂薄,圆角处加工不合理;曲轴箱或是支撑的刚度过小,附加弯矩变大;曲轴箱刚度较弱,主轴颈严重变形引起磨损问题,致使心度不同、附加弯矩增大,在长时间运行后易出现断裂。
(b)图的裂纹发生在圆角或是油孔处,并且只朝同一方向裂纹,其与轴线的角度为45°。
产生此种破坏的原因有:因不对称较扭矩所引发的最大应力,导致出现疲劳破坏;圆角加工与热加工不合理,使得材料组织不均;油孔口的圆角加工不合理;连杆轴颈过细。
(c)图的裂纹发生在油孔处,其与轴线呈45°。
产生此种破坏的原因有:扭转振动过大增加了附加应力;油孔边缘加工不合理,孔口的过度圆角较小,应力过于集中。
(d)图的裂纹发生在圆角的四周,断口为锯齿形。
产生此种破坏的原因有:圆角过于尖锐,应力集中严重。
二、内燃机曲轴的结构设计要求曲轴的结构形状及尺寸会对其抗弯疲劳强度、扭转刚度产生较大的影响,因此其要满足循以下条件进行设计结构:第一,强度合格。
柴油机曲轴强度的三维有限元分析

柴油机曲轴强度的三维有限元分析
柴油机设备具有重要的意义,它是用于产生动力的关键组件。
为了确保柴油机的高效、安全和可靠性运行,对柴油机曲轴的强度进行分析是非常重要的。
有限元分析是用来研究复杂结构的计算方法,可以在短的时间内获得较准确的结果。
本文将重点探讨柴油机曲轴强度的三维有限元分析方法。
首先,本文探讨了有限元分析在柴油机强度计算中的应用。
有限元分析是一种数值分析方法,可以准确地考虑复杂工程结构中所有细节,因此可以准确计算柴油机曲轴的强度。
本文还介绍了在有限元分析中建模的步骤,包括几何建模、单元划分、材料参数和边界条件的设置,以及有限元程序的使用。
其次,本文分析了使用有限元分析计算柴油机曲轴强度的结果。
首先,该研究对柴油机曲轴的三维模型进行了建模和仿真,并分析了曲轴计算结果。
研究结果表明,柴油机曲轴的有限元分析能够很好地刻画实际情况,计算结果与实验结果一致。
该研究还分析了柴油机曲轴的强度敏感度,总结了有限元分析考虑的可能参数。
最后,本文对柴油机曲轴的三维有限元分析方法进行了总结,分析了其可行性和有效性,以及其影响柴油机结构可靠度的优劣点。
最后,建议在设计制造柴油机曲轴时,应结合实际情况,考虑复杂运动情况以及负载分布,特别是在高强度轴上应尽可能增加对结构强度的分析,从而提高柴油机曲轴的可靠性和安全性。
综上所述,柴油机曲轴强度的三维有限元分析可以有效地考虑复
杂的结构特性,准确地分析柴油机曲轴的强度,以提高柴油机的可靠性和安全性。
内燃机曲轴强度研究的现状_讨论与展望

图 2 连续梁计 算模型 Fig. 2 Calculating model of cont inuous beam
1. 1. 1. 3 应力集中系数的计算 在曲轴中 ,轴颈与曲柄的过渡圆角处和轴颈油孔 附近存在严重的应力集中现象 ,传统方法通常用应力 集中系数修正由简支梁法或连续梁法计算所得的名义 应力 ,以计算曲轴的最大工作应力。 以往 一般 通 过试 验方 法研 究确 定应 力 集中 系 数 [3, 5 ] ,提出的应力集中系数计算公式都是经 验计算 式 ,使用时必须注意其适用的参数范围、试验条件以及 应用场合 ,否则可能产生很大的误差。 另外 ,它们没有 考虑过渡圆角处三维形状的影响 ,因此不能用于精确 计算。 有限元和边界元方法的应用 ,为准确地计算应力 集中系数提供了可能。由于曲轴几何形状复杂 ,三维有 限元分析比较费时 ,因此 Guag lia no 等人进行了试验 测试和数值分析 [6 ]。结果表明 ,具有相同载荷和边界条 件的二维和三维分析所得的应力集中系数数值相近。 从节省计算时间考虑 ,可以使用曲轴的平面模型确定 应力集中系数。 为了在较短时间内方便精确地预测应 力集中系数 , Shiomi 等人应用人工神经网络技术研制 了一个预测应力集中系数的系统 [ 7]。 该系统建立在由 曲轴几何形状和有限元计算得到的应力集中系数组成 的数据库的基础上 ,提出了一个适应传递函数运算法 则作为神经网络的学习方法 ,可以利用有限的数据计 算不同曲轴的应力集中系数。 1. 1. 2 有限元方法 传统方法根据名义应力和应力集中系数计算曲轴 危险部位的应力。由于曲轴形状复杂 ,名义应力的准确
浅谈曲轴设计加工及强度仿真校核方法
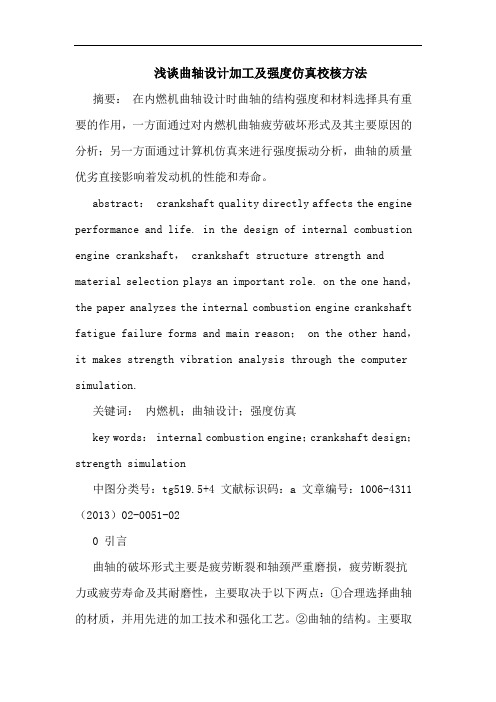
浅谈曲轴设计加工及强度仿真校核方法摘要:在内燃机曲轴设计时曲轴的结构强度和材料选择具有重要的作用,一方面通过对内燃机曲轴疲劳破坏形式及其主要原因的分析;另一方面通过计算机仿真来进行强度振动分析,曲轴的质量优劣直接影响着发动机的性能和寿命。
abstract: crankshaft quality directly affects the engine performance and life. in the design of internal combustion engine crankshaft, crankshaft structure strength and material selection plays an important role. on the one hand,the paper analyzes the internal combustion engine crankshaft fatigue failure forms and main reason; on the other hand,it makes strength vibration analysis through the computer simulation.关键词:内燃机;曲轴设计;强度仿真key words: internal combustion engine;crankshaft design;strength simulation中图分类号:tg519.5+4 文献标识码:a 文章编号:1006-4311(2013)02-0051-020 引言曲轴的破坏形式主要是疲劳断裂和轴颈严重磨损,疲劳断裂抗力或疲劳寿命及其耐磨性,主要取决于以下两点:①合理选择曲轴的材质,并用先进的加工技术和强化工艺。
②曲轴的结构。
主要取决于产品的设计问题曲轴有组合式和整体式之分。
前者用于重型和低速发动机中,后者主要用于中大功率发动机中。
柴油机曲轴静强度有限元分析与优化
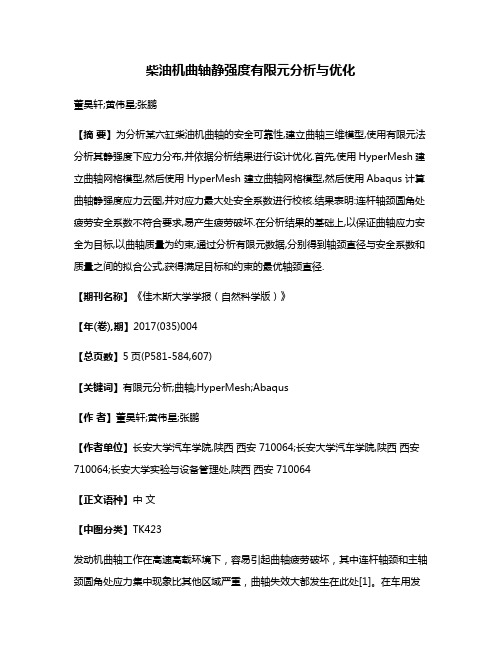
柴油机曲轴静强度有限元分析与优化董昊轩;黄伟星;张鹏【摘要】为分析某六缸柴油机曲轴的安全可靠性,建立曲轴三维模型,使用有限元法分析其静强度下应力分布,并依据分析结果进行设计优化.首先,使用HyperMesh建立曲轴网格模型,然后使用HyperMesh 建立曲轴网格模型,然后使用Abaqus 计算曲轴静强度应力云图,并对应力最大处安全系数进行校核.结果表明:连杆轴颈圆角处疲劳安全系数不符合要求,易产生疲劳破坏.在分析结果的基础上,以保证曲轴应力安全为目标,以曲轴质量为约束,通过分析有限元数据,分别得到轴颈直径与安全系数和质量之间的拟合公式,获得满足目标和约束的最优轴颈直径.【期刊名称】《佳木斯大学学报(自然科学版)》【年(卷),期】2017(035)004【总页数】5页(P581-584,607)【关键词】有限元分析;曲轴;HyperMesh;Abaqus【作者】董昊轩;黄伟星;张鹏【作者单位】长安大学汽车学院,陕西西安 710064;长安大学汽车学院,陕西西安710064;长安大学实验与设备管理处,陕西西安 710064【正文语种】中文【中图分类】TK423发动机曲轴工作在高速高载环境下,容易引起曲轴疲劳破坏,其中连杆轴颈和主轴颈圆角处应力集中现象比其他区域严重,曲轴失效大都发生在此处[1]。
在车用发动机曲轴设计和优化过程中,有限元法可精确分析出其应力分布情况,有效缩短研发优化周期,提高效率,节约费用[2~3]。
目前对曲轴分析优化多集中在单纯通过增大轴径以达到可靠性要求[1,4],少有分析轴径增大带来的质量变化和安全性变化关系以获得准确的优化结果。
以有限元法为基础,以应力分布结果为导向,得到轴颈直径增加值与曲轴质量增加和疲劳安全系数之间的关系,获得满足要求优化值并进行验证。
1.1 曲轴建模柴油机曲轴,材料为45号钢,弹性模量为206800,泊松比为0.29。
在Catia中建立曲轴三维模型,如图1所示。
- 1、下载文档前请自行甄别文档内容的完整性,平台不提供额外的编辑、内容补充、找答案等附加服务。
- 2、"仅部分预览"的文档,不可在线预览部分如存在完整性等问题,可反馈申请退款(可完整预览的文档不适用该条件!)。
- 3、如文档侵犯您的权益,请联系客服反馈,我们会尽快为您处理(人工客服工作时间:9:00-18:30)。
编订:__________________
单位:__________________
时间:__________________
内燃机械加工制造时曲轴强度的控制方法分析(正
式)
Deploy The Objectives, Requirements And Methods To Make The Personnel In The Organization Operate According To The Established Standards And Reach The Expected Level.
Word格式 / 完整 / 可编辑
文件编号:KG-AO-2656-23 内燃机械加工制造时曲轴强度的控
制方法分析(正式)
使用备注:本文档可用在日常工作场景,通过对目的、要求、方式、方法、进度等进行具体、周密的部署,从而使得组织内人员按照既定标准、规范的要求进行操作,使日常工作或活动达到预期的水平。
下载后就可自由编辑。
作为内燃机械重要的零配件,曲轴强度体现在抗疲劳和抗断裂两个方面,如果曲轴强度水平不足,可能会引起内燃机其他零配件的损坏。
本文将通过对当前内燃机械曲轴强度现状的分析,深入研讨内燃机械加工制造时的曲轴强度控制方法。
1.内燃机械曲轴强度现状分析
1.1.结构复杂
内燃机械的曲轴结构复杂,在加工时,一方面要求具有较为可观的承受荷载能力,而且要兼顾机械的功率需求,因此在加工制造时,要求保证曲轴强度达到既定的水平。
曲轴在内燃机械中的作用是承受气缸内砌体作用力,并以旋转、往复等运动方式,为内燃机械运行提供惯性力。
但由于内燃机械运行时产生的
荷载在周期内不断变化,以致曲轴持续承受弯曲应力和扭转应力,尤其是过渡圆角位置,应力过于集中,最终导致曲轴的疲劳失效。
1.2.永久性性能变化
在内燃机械实际应用时,随着使用时间的加长,曲轴局部某点可能会出现永久性的性能变化,反复循环载荷作用下,逐渐形成裂纹,甚至扩展至断裂破裂,即我们常说的疲劳断裂。
疲劳断裂具有低应力性、突然性、时间性、敏感性等特征,国内内燃机械的加工制造,大约有80%以上内燃机械结构强度破坏,就是因为曲轴的疲劳破坏引起,大约占其他强度破坏故障率的95%左右。
2.内燃机械加工制造时曲轴强度控制方法
2.1.建立曲轴系统动力学模型
鉴于内燃机械的结构复杂,在加工制造曲轴时,应该建立曲轴系统的动力学模型,并借助各类动力学仿真软件和专业模块,以形成包括模板、子系统、装配等在内的模型结构。
模型的建立,一方面更改了模
板的子系统,使得模型参数化,另一方面是按照一定的几何体约束比例,设定模板的参数,然后集合多个子系统,为子系统的信息传递和求解提供渠道。
在建立曲轴系统动力学模型的基础上,建立初始拓扑结构,其中所涉及的数据涵盖了内燃机械的汽缸数、冲程数、缸心距、连杆尺寸和轴承布置等,而子系统的建立,要求对曲轴部件的尺寸、密度和转动惯量等进行调整。
2.2.分析曲轴系统动力学仿真结果
曲轴系统动力学仿真结果的分析,是通过对曲轴系统动力学模型的应用,全方位调整曲轴强度设计的差异性。
首先是减振器的参数调试,系统测量布置是在曲轴上方设置发动机,其左右侧分别为位移传感器、信号齿轮和飞轮,其中位移传感器由采集卡和PC机组成,在进行减振器参数调整之后,通过扭振响应曲线,可以看出振幅轴向基本一致,其数据误差对曲轴强度设计精度影响不大。
其次是活塞加速度比较分析,通过对曲轴转角、连杆摆角、曲柄半径、曲柄连杆比、连杆中心距等参数的确定,借助倍角余弦函数,表示
活塞的位移,这样所计算出来的内燃机械曲轴加速度,在实际曲轴强度设计中就能够避免相对误差的影响。
再次是活塞侧击力比较分析,即曲轴在爆发压力作用下的精度误差,鉴于所有曲柄销载荷曲线的一致性,可利用现代算法取值曲柄销径向和切向的峰值,以此检验连杆的质量等效。
2.3.曲轴应力计算
曲轴强度的控制,需要准确分析曲轴的应力分布,因此需要通过曲轴应力计算,以改善有效应力集中系数的精度。
在此笔者建议应用有限元分析法,对曲轴应力展开计算,并得出曲轴的疲劳安全系数。
在计算之前,还需要评估曲轴高应力位置的疲劳安全,期间假定曲柄销圆角和主轴颈圆角为高应力区域,然后将曲拐相互独立的主轴颈,简化成截断简支梁模型,这样就能够判断出弯曲应力对曲轴的破坏程度。
至于曲轴改进后常规强度,一方面是根据计算的结果,判断曲轴强度是否合格,进而确定安全系数,并进行扭振修正、屈服极限分析、表面处理、尺寸影响消除等,
另一方面是利用截断简支梁模型,分析工作弯矩和计算截面模量,进而确定曲轴应力幅值和平均应力。
2.4.曲轴弯曲疲劳试验
曲轴弯曲疲劳试验,常见的试验方法有成组试验法、配对升降法、疲劳极限统计分析法三种,其中成组试验法适用于曲轴过载时的疲劳强度,可相对合理估算出曲轴安全寿命;配对升降法是按照国家标准试验规范,选取随机出现的成对数据,但只适用于分散性较小的试件;疲劳极限统计分析法,主要通过应力—寿命双对数坐标,找出循环断裂点,根据数值选取真实的断裂强度。
在此笔者推荐使用疲劳极限统计分析法,这种分析方法要求控制好试验台应变片的电阻值,以及栅长、栅宽、灵敏系数、精度等级等,并标定载荷,即在“静标动测”原理范围内,分析试件某个部位的静态应变和动态应变,然后得出静标曲线的应变值和确定在该应变值下的激振转速大小。
至于系统误差的分析,则要归结为人为或者系统的误差,前者只需要提高试验人员的技术水平,并规范技术操作
规范即可,后者则需要考量应变片在系统中的动载荷测量情况,调节各点应变量的真实值,使得更加接近测量目标点。
文章通过研究,基本明确了内燃机械曲轴强度现状及发展情况,其中所涉及到的曲轴强度控制方法,是基于实际曲轴强度控制工作的经验总结,但鉴于内燃机械加工制造时曲轴控制在技术要求方面具有差异性,这些方法的应用,有必要结合实际条件,对其进行适当调整、补充和完善。
请在这里输入公司或组织的名字
Enter The Name Of The Company Or Organization Here。