非高炉炼铁--重点设备介绍
非高炉炼铁

非高炉炼铁一、非高炉炼铁的发展高炉炼铁是炼铁生产的主题,经过长期的发展,它的技术已经非常成熟。
但它也存在固有的不足,即对冶金焦的强烈依赖。
但随着焦煤资源的日渐贫乏,冶金焦价格越来越高。
因此,使炼铁生产摆脱对冶金焦的依赖是开发非高炉炼铁的原动力。
经过数百年的发展,至今已形成了以直接还原和熔融还原为主的现代化非高炉炼铁工业体系。
现代化钢铁工艺流程主体由四部分构成,焦炉、造块设备(例如烧结机)、高炉和转炉。
高炉使用冶金焦为主题能源,他是由焦煤经炼焦得到。
高炉的产品是液态生铁,它经转炉冶炼成转炉钢。
熔融还原的产品相当于高炉铁水。
高炉使用冶金焦,熔融反应则使用非焦煤。
这样就使炼铁摆脱了对冶金焦的依赖。
直接还原的产品是在熔点以下还原得到固态金属铁,称为直接还原铁(DRI),又称海绵铁。
直接还原的流程可分为煤基直接还原、气基直接还原和电热直接还原三大类。
煤基直接还原以煤为主要能源,主要是使用回转炉为主体设备的流程。
气基直接还原以天然气为主题能源。
包括竖炉、反应罐和流化床流程。
电热直接还原以电力为主要能源,是使用电热竖炉直接还原流程。
熔融还原的主体能源主要分为三种:非焦煤,焦炭和电力。
熔炼设备是熔融还原流程的精华。
还原设备决定了适用原料的性质。
例如流化床可直接处理粉料,竖炉则适用于处理块状炉料。
二、重点设备分析直接还原的核心装置是一个还原单元。
占有重要地位的还原设备有竖炉,反应罐,回转炉和流化床。
熔融还原的核心装置时一个还。
原单元和一个熔炼造气单元。
最受重视的还原设备是竖炉和流化床,最重要的熔炼造气设备是煤炭流化床和铁浴炉。
竖炉是一种成熟的还原设备。
除了产量在海绵铁工业中高居榜首外,熔融还原也将它作为还原单元最实际的选择。
目前唯一的工业化二步法熔融还原流程COREX即使用竖炉还原单元。
作为还原设备,流化床的地位非常微妙。
海绵铁工业中流化床的生产能力并不大。
但他具有一个竖炉无法比拟的优点:可直接使用粉矿。
这个特点使流化床成为熔融还原中最受青睐的还原设备。
非高炉炼铁
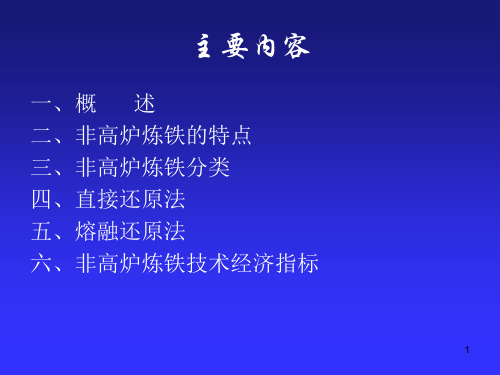
3.二步法-KR法(COREX法)工艺介绍
二步法: 将熔融还原
过程分为固相预还 原及熔态终还原并 分别在两个反应器 中完成; 优点:
改善了能量 利用,降低了渣中 FeO浓度。
12
六、非高炉炼铁技术经济指标
1.单位容积利用系数:
每立方米反应器有效容积每天的产品量,即 η=Q/Vu, t/(m3.d)
8
3.使用气体还原剂举例(Midrex法)
工艺过程: 天 然 气 + 净 化 炉 顶 气 (300-
400℃)→混合室→重整炉 (Ni 催 化 剂 ) →900-950 ℃反应:
CH4+H2O=CO+3H2 CH4+CO2=2CO+2H2 还原气→竖炉(炉料炉顶加入) →停留6h →冷却带N2冷却 至100℃ →炉料排出
主要内容
一、概 述 二、非高炉炼铁的特点 三、非高炉炼铁分类 四、直接还原法 五、熔融还原法 六、非高炉炼铁技术经济指标
1
一、概 述
1.概 念 非高炉炼铁法是高炉法之外,不用焦炭
炼铁的各种工艺方法的统称。
2.发展史 1770 年 第 一 个 直 接 还 原 法 专 利 诞 生
→1857 年 提 出 完 整 的 近 代 直 接 还 原 (Chenot)构思→1873建成第一座非高炉 装置→上世纪20年代电炉(矿热炉)炼铁 →70年代具备一定规模→近期又重新成为 研究热点
高炉流程: 矿石A在高炉内升温、
还原、熔化为铁水B→[C] 已达到饱和→在炼钢过程 脱C→再去除多余氧成为成 品钢液; 非高炉流程:
矿石被升温、还原为 海绵铁→在电炉中熔化还 原未还原部分→得到成品 钢液
4
钢铁生产过程产品中氧量、碳量的变化
非高炉炼铁知识大全

提纲
第一部分 钢铁生产及短流程炼钢概论 第二部分 直接还原理论与工艺 第三部分 熔融还原理论与工艺
第一部分 钢铁生产及短流程炼钢概 论
一、什么是短流程
1.世界钢铁工业发展概况 起步阶段 时 间:1865年前后 工 艺:空气侧吹转炉炼钢法(1865年 英国贝赛麦) 代表国家:英国 中 国:公元前2世纪采用类似侧吹转炉 炼钢法—李约瑟
废钢资源优势
(1)、废钢铁是再生资源,可无限循环利用。 从钢材→制品→使用→报废→回炉炼钢,每830年一个轮回,无限循环使用 (2)、废钢铁是一种载能资源,用废钢铁炼钢 可以大量节约能源。废钢直接炼钢比矿石炼铁 后再炼钢可节能60%,节水40% (3)废钢铁是一种环保资源,废钢直接炼钢比 铁矿石炼铁炼钢可减少排放废气86%,废水76% 和废渣97%,有利于清洁生产和排废减量
钢水1t 图6. 废钢—电炉流程示意图
什么是短流程(续)
2. 钢铁生产方法及流程(续) 五种流程(续) 粉矿
1.237t 石灰石0.096t 543kg煤 (493kW•h熔化用电) (109kW•h脱硫和辅助 设备用电) 137kW•h制氧用电 404m3氧气 铁 燃料0.010t 废钢0.263t
粉矿
区域3
图11 按还原剂和铁矿石种类分直接还原工艺
直接还原生产及技术现状(续)
1.国外现状(续) 技术现状(续) 按炉型分: •竖炉 •回转窑 •转底炉 •流化床等
直接还原生产及技术现状(续)
1.国外现状(续) 技术现状(续) 按含铁料粒度分: •块矿/球团 •粉矿
表1 不同直接还原工艺的主要特点比较
型式 竖炉 竖炉(间歇) 竖炉 多层流化床 回转窑 还 800 800~900 700~800 1100~1200 原 温度/℃ 800~900 炉 还原率/% 92~96 85 92~94 93 90 熔炼炉 废气处理 电炉 电炉 循环使用 TFe:88 C:2.2 脉石:4.3 电炉 电炉 电炉
精炼-连铸主要设备介绍

精炼-连铸主要设备介绍精炼-连铸主要设备介绍铁水预处理设备铁水预处理就是在铁水兑入转炉之前对其进行脱除杂质元素或从铁水中回收有价值元素的一种铁水处理工艺。
普通铁水预处理包括铁水脱硅、脱硫和脱磷(即“三脱”)。
特殊铁水预处理是针对铁水中的特殊元素进行提纯精炼或资源综合利用而进行的处理过程,如铁水提钒、提铌、提钨等。
根据我厂铁水及设备的实际情况,主要介绍现普遍采用的类似生产二区的喷吹Mg-CaO的铁水喷粉脱硫设备。
可以达到的冶金效果(S≤0.005%)精炼-连铸主要设备介绍精炼及连铸设备北营炼钢厂精炼-连铸主要设备介绍铁水包脱硫工艺设备图精炼-连铸主要设备介绍铁水喷粉脱硫的主要设备:1、铁水罐2、储存仓:内部装有高地位料位指示器、液态化床3、喷粉罐:由于喷粉的高压容器,能稳定而无脉冲的将脱硫粉剂经喷枪喷至铁水罐内。
4、喷枪及喷枪支架5、测温取样装置6、扒渣机:扒渣小车以液压缸为动力,带动扒渣臂和扒渣耙子摆动,将铁水渣扒除。
7、铁水罐倾翻车:主要是两个液压缸8、渣罐及渣盘车、电子称、电控系统、液压渣、氮气管路精炼-连铸主要设备介绍精炼设备简介一、二次冶金工艺流程:高炉――铁水预处理――转炉――钢水二次精炼――连铸二、主要的精炼方式:二次精炼就是对转炉钢水根据目的进行炉外(相对于转炉)处理。
为了创造最佳的冶金反应条件,所采用的基本手段不外乎搅拌、真空、加热、渣洗、喷吹及喂丝等几种或几种的组合。
根据主要功能,常见的精炼设备有:吹氩设备、喂丝设备、LF炉、DH、RH、LVD、ASEA-SKF、V0D等精炼-连铸主要设备介绍三、各种精炼设备介绍:(一)吹氩:分为底吹、顶吹两种方式。
精炼-连铸主要设备介绍(二)喷粉及喂丝合金的喂入与喷粉工艺示意图精炼-连铸主要设备介绍(三)LF炉钢包处理型处理钢水过程中,因钢水的温降而使渣及合金成分的调整以及处理时间等都受到限制。
如果用提高初炼炉出钢温度的办法保证渣熔化及足够的精炼时间,势必加重初炼炉的负担,降低炉衬寿命,命中率也比较低,不具备工业性连续生产的条件。
非高炉炼铁技术概述

非高炉炼铁技术概述摘要:随着焦煤资源日益减少,高炉炼铁技术发展受到限制,非高炉炼铁成为了日益关注的冶炼技术。
文章阐述了非高炉炼铁技术的发展现状、分类,工艺流程及特点,同时展望了其未来的发展前景。
关键词:非高炉炼铁直接还原熔融还原非焦煤一、引言目前,生铁主要来源于高炉冶炼产品,高炉炼铁技术成熟,具有工艺简单,产量高,生产效率大等优点。
但其必须依赖焦煤,而且其流程长,污染大,设备复杂。
因此,世界各国学者逐渐着手研究和改进非高炉炼铁技术。
二、非高炉炼铁工艺非高炉炼铁是指以铁矿石为原料并使用高炉以外的冶炼技术生产铁产品的方法。
在当今焦煤资源缺乏,非焦煤资源丰富的情况下,非高炉炼铁以非焦煤为能源,不但环保,而且省去了烧结、球团等工序,缩短了流程。
因此非高炉炼铁一直被认为是一种环保节能、投资小、生产成本低的生产工艺。
非高炉炼铁可分为直接还原炼铁工艺和熔融还原炼铁工艺两种。
1.直接还原炼铁工艺直接还原炼铁工艺是一种以天然气、煤气、非焦煤粉为能源和还原剂,在铁矿石软化温度下,将铁矿石中铁氧化物还原成铁的生产工艺。
据统计直接还原冶炼工艺多达40余种,大部分已经实现了大规模工业化生产[1]。
目前,直接还原炼铁工艺主要有气基直接还原、煤基直接还原两大类。
1.1气基直接还原气基直接还原是指用CO或H2等还原气体作还原剂还原铁矿石的炼铁方法。
具有生产效率高、容积利用率高、热效率高、能耗低、操作容易等优点,是DRI(directly reduced iron)生产最主要的方法,约占DRI总产量的90%以上[2]。
气基直接还原代表工艺有HYL反应罐法、Midrex-竖炉法、流化床法等[3]。
HYL反应罐法是由墨西哥希尔萨(HojalataYLamina,HYLSA)公司于20世纪50年代初开发的,其工业化标志着现代化直接还原的开始。
HYL反应罐法具有作业稳定,设备可靠等优点,但其作业不连续,还原气利用差,能耗高及产品质量不均匀。
四种新型非高炉炼铁技术

四种新型非高炉炼铁技术非高炉炼铁技术作为一种能消除块矿、焦煤和废钢三大资源不足的危机,减四种新型非高炉炼铁技术轻钢铁业的资源、能源和环境压力的炼铁技术,长期以来都受到人们的关注和研究,以下四种比较新颖的有:1 .Hi-QIP工艺Hi-QIP工艺由日本JFE公司开发的,主要特点是转底炉炼铁。
相比于旧有的转底炉工艺,Hi-QIP转底炉首次使用含碳料层,同时另一特点是经还原熔化的铁在炉内生成。
Hi-QIP工艺中,铁矿石(或块矿)是铁源,煤是还原剂,石灰石是熔剂。
这些原料经混匀后并装入碳质原料床,然后用烧嘴加热。
铁矿石被还原和熔化,而在料层中煤的混合料被气化,并如同还原剂一起进入到炉料中起反应。
石灰石熔化并同混合料中的灰分和脉石成分生成渣。
熔化的铁和渣流入坑中,冷却凝固,生成粒铁。
粒铁和渣粒用螺旋装置从炉中排出,此工艺可以连续生产粒铁。
2 . Fastmet工艺Fastmet工艺由日本神户制钢开发的,主要特点是使用煤基转底炉还原钢铁厂产生的烟尘或矿粉。
原料:80%的铁矿石、20%煤和来自球团的有机粘含剂1.5%,经加工干燥到170℃装入煤基转底炉,生产出DRI产品,后续DRI产品在氮氧保护下送压块机造块。
Fastmet工艺的DRI热压块,含0.08%S高硫,被作为高炉原料,而不直接用于炼钢。
3 . Finex工艺Finex工艺由韩国浦项和西门子的MT共同开发的,由炉底的熔化器-气化器构成。
Finex工艺是将磨制煤粉和氧气喷吹到炉子,炉子上部有四个流化床反应器,铁矿粉或工厂的烟尘由反应器下降与气化器上升的煤气相遇,产生反应,还原出铁。
Finex工艺环境友好特性十分显著,SO2排放是传统高炉3%,氮氧化物是1%,粉尘是28%。
4.Tecnored工艺Tecnored工艺炼铁工艺是在巴西经过20多年发展而成,由模块结构的反应器组成。
铁矿粉或铁性粉尘和氧化铁皮同碳基的还原剂(如石油焦)和有机粘合剂精心紧密混匀生成球团,在炉身1.5m的长方形反应器中反应,燃料煤是沿反应器的两个边长装入,保持燃料资源总是来自还原区,抑制球团自身还原,同时抑制了CO2到CO的还原反应,较节能。
非高炉炼铁--重点设备介绍
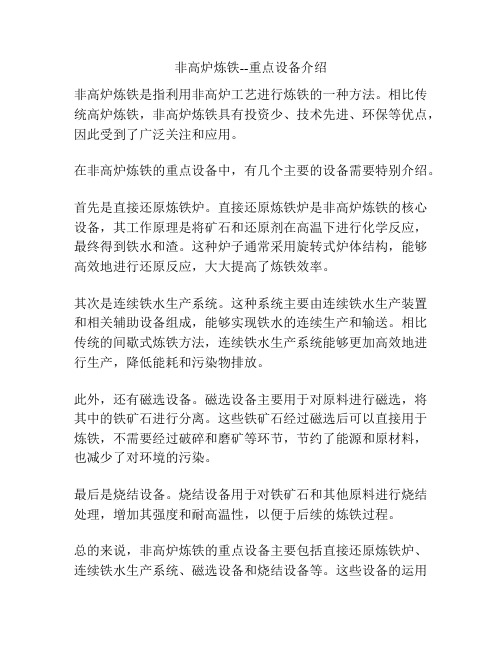
非高炉炼铁--重点设备介绍
非高炉炼铁是指利用非高炉工艺进行炼铁的一种方法。
相比传统高炉炼铁,非高炉炼铁具有投资少、技术先进、环保等优点,因此受到了广泛关注和应用。
在非高炉炼铁的重点设备中,有几个主要的设备需要特别介绍。
首先是直接还原炼铁炉。
直接还原炼铁炉是非高炉炼铁的核心设备,其工作原理是将矿石和还原剂在高温下进行化学反应,最终得到铁水和渣。
这种炉子通常采用旋转式炉体结构,能够高效地进行还原反应,大大提高了炼铁效率。
其次是连续铁水生产系统。
这种系统主要由连续铁水生产装置和相关辅助设备组成,能够实现铁水的连续生产和输送。
相比传统的间歇式炼铁方法,连续铁水生产系统能够更加高效地进行生产,降低能耗和污染物排放。
此外,还有磁选设备。
磁选设备主要用于对原料进行磁选,将其中的铁矿石进行分离。
这些铁矿石经过磁选后可以直接用于炼铁,不需要经过破碎和磨矿等环节,节约了能源和原材料,也减少了对环境的污染。
最后是烧结设备。
烧结设备用于对铁矿石和其他原料进行烧结处理,增加其强度和耐高温性,以便于后续的炼铁过程。
总的来说,非高炉炼铁的重点设备主要包括直接还原炼铁炉、连续铁水生产系统、磁选设备和烧结设备等。
这些设备的运用
使得非高炉炼铁在提高炼铁效率、降低成本、减少环境污染等方面具有显著优势。
随着科技的不断发展,相信非高炉炼铁的设备和工艺会更加完善,为炼铁行业的可持续发展做出更大的贡献。
现代钢铁企业冶金设备概述

现代钢铁企业冶金设备概述现代钢铁企业是一个庞大的工业体系,其中冶金设备是其重要的组成部分。
冶金设备主要涉及炼铁、炼钢、连铸以及热处理等过程,在钢铁生产中扮演着至关重要的角色。
随着科技的不断进步和工业技术的不断完善,现代钢铁企业的冶金设备也在不断更新换代,各种高效、节能的新型设备层出不穷。
本文将对现代钢铁企业的冶金设备进行概述,从炼铁设备、炼钢设备、连铸设备以及热处理设备等方面进行介绍。
一、炼铁设备:炼铁设备是指用于炼制铁水(生铁)的各种冶炼设备,主要包括高炉、炼铁炉、煤气净化设备等。
高炉是炼铁的主要设备,通常是由筑炉、炉壳、炉缸和炉喉等部分组成,通过煤焦煤气化产生的热能,将生铁矿石还原成铁水。
现代高炉设备多为大型化、自动化和智能化的高炉炉墙冷却、螺旋鼓风等技术的应用,提高了炉内燃烧效率,减少了能源消耗。
随着技术的不断更新,高炉炉缸、炉身和炉顶等部件也采用了新型材料和新工艺,提高了设备的耐磨性和耐高温性,延长了设备的使用寿命。
而炼铁炉和煤气净化设备也在不断更新换代,采用了先进的脱硫、脱硝技术,减少了排放的有害气体,保护了环境。
现代炼铁设备不仅提高了生产效率,降低了生产成本,而且也大大减少了对环境的污染。
炼钢是将生铁中的杂质去除,并使其成分、结构、性能得到适当调整,从而生产合格的钢材的过程。
炼钢设备主要包括转炉、电弧炉、炼钢连铸机等。
转炉是炼钢的主要设备之一,其主要包括本体、氧气和燃料喷吹系统、底吹吹氧系统等部分,通过氧气吹炼,将生铁炼成优质的钢材。
现代转炉设备采用了高效节能的先进技术,如氧气底吹技术、氧气侧吹技术、自动化控制技术等,在提高炉效率、降低炼钢成本的也减少了对环境的污染。
电弧炉是另一种常用的炼钢设备,通过电弧将废钢、废铁等原料熔炼成钢水,广泛应用于不锈钢、合金钢、特种钢的炼钢生产中。
炼钢连铸机是将炼好的钢水连续铸造成铸坯或铸锭的设备,主要包括结晶器、铸型、冷却平台、切割机等部分。
现代炼钢连铸机采用了先进的浇铸技术,如双流浇铸、多喷嘴浇铸、水冷铸坯,提高了铸坯的质量和生产效率。
第三章_非高炉炼铁重点设备介绍(下)
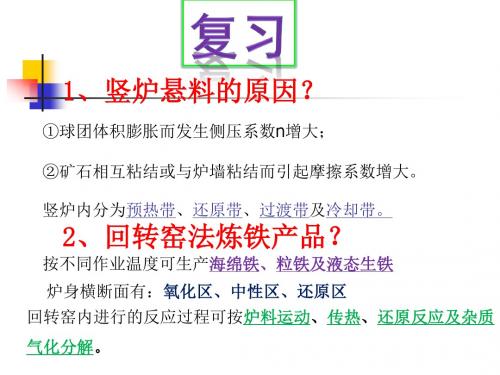
3.2.2 流化参数
临界流化条件:气流对料层向上的摩擦力等于料层的 质量。由此可得: 整理得:
式中: S——流化床截面积;Lmf——临界流化床高度; εmf——临界流化床孔隙率;ρs——固体颗粒密度。 固定床压将为:
umf的二次方程:
如Rep很低,压降以粘度损失为主,忽略动能损失, 有: 很高,压降以动能损失为主可忽略粘度损失,有:
3.4 熔炼造气煤炭流化床
3.4.1 熔炼煤的有效热值
热收入——煤的燃烧; CH4和H2O比例很低,可忽略H2的热效应; 干基热量为Qd;
煤在熔炼过程中放出的全部热量(Q)为碳素燃烧热和煤灰成渣热之和,
Q包括造气热(Qg,干基造气热Qgd)和熔炼煤的有效热值(Qe,干基有
效热值Qed);
Du和Pu是粒度的函数。
粒度较小(0.1mm)时, pu较大,ut和umf相对差别很
大,u0的控制和床层的提高
较容易。利于提高产率和还 原气体利用率。但粒度太低, 易粘结失流。
粒度较大时,Du较大,流速控
制容易。但umf提高幅度较ut显著, 会造成床层极限高度Lmax降低和 还原气利用率降低的问题。
1、竖炉悬料的原因?
①球团体积膨胀而发生侧压系数n增大;
②矿石相互粘结或与炉墙粘结而引起摩擦系数增大。
竖炉内分为预热带、还原带、过渡带及冷却带。
2、回转窑法炼铁产品?
按不同作业温度可生产海绵铁、粒铁及液态生铁 炉身横断面有:氧化区、中性区、还原区 回转窑内进行的反应过程可按炉料运动、传热、还原反应及杂质 气化分解。
3.3.4 还原速度与气体利用率
流化床的反应条件:
匀,尾气还原需最低与FeO和Fe平衡,还原气利用率
炼铁生产的原理及使用设备介绍

炼铁生产的原理及使用设备介绍
炼铁是指将铁矿石还原、冶炼成铁的过程。
它是现代工业中最重要的基础产业之一。
炼铁的原理是将矿石在高温条件下还原,将铁元素从氧化物中还原出来。
具体的过程包括矿石的破碎、磨细、烧结、还原等环节。
在炼铁生产中,常用的设备包括高炉、烧结机、球团机、焦炉等。
其中,高炉是最主要的设备。
它是一种大型的冶炼设备,采用热力学原理,将矿石还原成铁。
高炉通常由钢筋混凝土或钢制而成,高度可达50米以上。
高炉内部包括上部的炉喉、炉身和下部的炉腰、炉缸等部分。
矿石、焦炭和烧结块通过炉喉加入炉腰,经过还原反应,产生高炉煤气和液态铁,最终在炉底收集液态铁。
烧结机和球团机是将矿石进行预处理的设备。
烧结机将矿石进行高温烧结,使矿石颗粒间产生结合作用,从而使矿石颗粒更加坚固。
球团机则将矿石粉末添加一定比例的粘结剂,制成直径3-6mm的球团矿,以便在高炉中使用。
焦炉则是为高炉提供焦炭的主要设备,它是一种大型的垂直炉子。
焦炉内将煤炭进行加热、干燥和热解,产生焦炭和一定量的煤气。
焦炭不仅是高温燃料,还能提供一定的结合作用。
总之,炼铁生产的原理是将铁矿石还原、冶炼成铁,需要使用高炉、烧结机、球团机、焦炉等设备。
这些设备相互配合,共同完成炼铁的整个过程。
非高炉炼铁设备形式的选择

世界金属导报/2010年/3月/2日/第015版工程装备非高炉炼铁设备形式的选择李振洪张海涛直接还原和熔融还原是现代非高炉炼铁的主体,均是以摆脱高炉流程对炼焦煤依赖为目的钢铁行业前沿技术。
至今,世界上开发出的非高炉炼铁工艺成百上千种,但产业化的工艺并不多,即使已经产业化或初步产业化的COREX、FINEX、HIsmelt等方法除工艺及生产流程设计存在的问题外,主体设备形式的选择也值得研讨。
现有非高炉炼铁技术的能耗均高于高炉,有的甚至还比高炉流程高出许多,不能说与设备形式的选择不无关系。
由于诸多原因的存在,目前开发的非高炉炼铁技术在工业化上不可能完全取代高炉。
生产设备为工艺服务,非高炉炼铁要超过高炉的经济技术指标要求,取代高炉生产,除先进的炼铁工艺外,还要有先进的设备。
因此,对设备形式的选择、组合、衔接与匹配则显得特别重要。
1.还原设备还原设备既可作为熔融还原的预还原单元,也可作为直接还原铁的生产设备,在设备形式上大同小异,原理相同。
金属化率高的还原铁是电炉、高炉的优质原料,可直接作为商品出售。
依照原料条件的不同,侧重点不同,还原设备的类别划分也不尽相同。
通常使用的还原设备有流化床形式,回转床形式和移动床形式等,非连续性操作的罐装法还原形式不符合技术进步的方向,本文不讨论。
1.1回转床形式采用回转床的煤基直接还原设备是成熟的,在还原铁的生产中占有重要地位。
我国天津钢管公司引进英国戴维公司年产30万t DRC煤基回转窑生产线已安全运行多年。
该套设备由两条年产15万t生产线组成,每条生产线安装的主体设备包括1台5×80m回转窑和1条 3.5×50m 冷却筒。
原料铁矿石、煤炭、返焦、熔剂等定量装入回转窑和供料端,窑体慢慢滚动,在铁矿石和焦炭被加热及铁矿被还原的同时炉料向出料端移动。
回转窑内砌筑耐火材料,并在进料端、中部和出料端设有耐火材料挡料圈,以延长炉料在炉窑内的停留时间。
从窑的出料端喷入的碎煤为直接还原的吸热提供热源。
非高炉炼铁

1.6.3 炉内主要过程
炉内一般过程
炉料下降过程中,与上升的煤气流相互作用,被加热,发 生干燥、还原、熔化、造渣等一系列物理化学反应,最后 生成液态渣、铁,聚集于炉缸,周期地从高炉排出,上升 的煤气流将能量传给炉料,温度不断降低,成分不断变化, 最后变成高炉煤气从炉顶排出 实质:在尽量低能量消耗的条件下,通过受控的炉料及煤 气流的逆向运动,高效率地完成还原、造渣、传热及渣铁 反应等过程,得到化学成分与温度较为理想的液态铁
1.6.4 高炉炼铁原料及其他辅助材料
①灰分低,固体碳高 ②含硫低 ③可磨性好:易磨 ④粒度细:-200目占80% ⑤爆炸性弱:安全 ⑥燃烧性要弱、反应性要好
固体燃料: 煤 喷 吹 燃 料
天然气,石油气,焦炉和高炉煤气, 气体燃料:
转炉煤气,发生炉煤气
重油,柴油,焦油 液体燃料:
1.6.4 高炉炼铁原料及其他辅助材料
性能 ①物理性能 a.致密度,气孔率,吸水率 b.透气性 c.耐压强度 d.热膨胀性 ②使用性能 a.耐火度:抗高温熔化性能的指标,用耐火锥变 形的温度表示。它表征耐火材料的热性质,主要 取决于化学组成,杂质数量和分散程度。实际使 用温度要比耐火度低。
1.6.4 高炉炼铁原料及其他辅助材料
b.荷重软化点:在施加一定压力并以一定升温速度 加热时,当耐火材料塌毁时的温度。它表征耐火材料 的机械特性。耐火材料的实际使用温度不得超过荷重 软化点。 c.耐急冷急热性(抗热震性):是指在温度急剧变 化条件下,不开裂。不破碎的性能。 d.抗蠕变性能:荷重工作温度下,形变率 e,导热性及导电性 f.抗渣性:在使用过程中抵御渣化的能力。 耐火材料选择原则:使用的温度,使用的环境
高炉法 现 代 炼 铁 法 非高炉法
非高炉炼铁法

非高炉炼铁法简介非高炉炼铁法以不用焦煤为主要特征,按其工艺特征、产品类型及用途分为直接还原法和熔融还原法两大类。
直接还原法以气体、液体燃料及非焦煤为能源,在铁矿石或含铁团块呈固态的软化温度下进行还原获得直接还原铁(DRI)或海绵铁,其产品低密度多孔呈海绵状结构,含碳低,未排除脉石杂质。
熔融还原法则以非焦煤为能源,产品类似高炉的铁水。
目前,非高炉炼铁法以直接还原工艺为主,该方法对铁原料要求高,TFe>66%,酸性脉石含量(SiO2+Al23)<5.5%(但不宜过低),一般S含量<0.03%,P<0.02%,其它有害元素尽可能低,各种工艺对原料粒度要求不一。
铁原料和煤灰分的软化温度决定了直接还原工艺的作业温度。
在燃料方面,当前各种工艺中,以使用天然气为主,能量利用率高、生产率高,但我国天然气资源缺乏。
国内直接还原厂以使用非焦煤(褐煤、烟煤、无烟煤)为主,现在世界各国也以发展煤基直接还原为主。
直接还原工艺的主要方法有:1. 回转窑直接还原法:回转窑结构是一个可转动的筒形高温反应器。
含铁原料与还原煤从窑尾连续加入,排料端设置主燃烧喷嘴和还原煤喷入装置,沿窑身长度方向装有若干供风管或燃料喷嘴,随窑体转动,固体物料在翻滚移动过程中,被高温气流加热,进行物料的干燥、预热、碳酸盐的分解、铁氧化物还原及渗碳反应从而得到DRI。
比较有代表的是SL-RN 法、DRC法、Krupp-Codir法等。
2. 竖炉直接还原法:竖炉法目前占直接还原铁产量的90%左右,其中以Midrex和MYL为主,工艺成熟,占直接还原工艺的主导地位。
竖炉的反应条件与高炉上部间接还原区相似,不出现熔化现象的还原冶炼过程,使用单一矿石料,没有造渣过程。
以前竖炉的燃料和还原剂是天然气,近年出现了煤制气以及使用焦炉煤气竖炉直接还原工艺,这扩大了竖炉工艺的使用范围,但目前煤基竖炉工艺还不成熟,生产成本偏高,工艺还需进一步完善。
3. 罐式直接还原法:以HYL为代表,用H2、CO或其混合气将装于移动或固定容器内的铁团还原成DRI的方法。
金属冶炼中的设备及工具介绍

汇报人:可编辑 2024-01-06
CONTENTS
目录
• 金属冶炼设备 • 金属冶炼工具 • 金属冶炼中的安全设备与工具 • 新技术与未来发展
CHAPTER
ห้องสมุดไป่ตู้01
金属冶炼设备
炼铁设备
01
02
03
高炉
用于将铁矿石还原成液态 铁,是炼铁过程中最主要 的设备。
直接还原炉
采用非高炉炼铁工艺,通 过直接还原方式将铁矿石 转化为海绵铁。
用于金属板材和管材的轧制,根据用途可分为热轧机 和冷轧机。
矫直机
用于对轧制后的金属板材进行矫直,提高板材的平直 度和表面质量。
剪切机
用于金属板材和管材的定尺剪切,以满足不同规格和 长度要求。
CHAPTER
02
金属冶炼工具
耐火材料
耐火材料
性能
在金属冶炼过程中,耐火材料是必不 可少的工具之一。它能够承受高温环 境,为金属熔炼提供良好的保护。
新材料的应用
高性能耐火材料
研发和采用高性能的耐火材料,提高冶炼设备的耐高温、耐磨损 性能,延长设备使用寿命。
新型过滤材料
采用新型的过滤材料,对金属溶液进行高效过滤,提高产品质量和 减少废品率。
高强度结构材料
采用高强度结构材料,减轻设备重量,提高设备刚度和稳定性,降 低能耗和生产成本。
自动化与智能化发展
耐火材料的性能主要取决于其化学成 分、矿物组成和显微结构。优质的耐 火材料应具备较高的耐火度、热稳定 性和抗侵蚀性。
种类
耐火材料有多种类型,如粘土、高岭 土、莫来石等,它们具有不同的物理 和化学性质,适用于不同的冶炼工艺 。
冶炼炉辅助工具
非高炉炼铁技术重点是以煤代焦 DRI最佳装备是煤基竖炉

非高炉炼铁技术重点是以煤代焦 DRI最佳装备是煤基竖炉陈守明我国粗钢产量连续高速增长,2011年达6.995亿吨,占全球粗钢产量45%;但产业结构不合理,工艺以高炉炼铁-转炉炼钢长流程为主,铁钢比高、电炉钢比例小,能源资源消耗大、生产成本高,经济效益一路下滑,优化结构、节能增效势在必行。
直接还原铁(DRI)不仅是一种重要的冶金原料,由于不以焦炭为主要能源,称非高炉炼铁,是一种节能增效的冶金新工艺。
发展DRI产业不仅可以为电炉炼钢、转炉炼钢、高炉炼铁、铸造等产业提供大量优质冶金炉料,有助于这些企业节能增效,而且节省大量焦炭,对于缓减高炉炼铁焦炭供应紧张局面、降低成本有利。
同时,国内中小铁矿和非炼焦煤的综合利用、提高附加值,可促进中西部地区经济发展。
国家工信部2011年底颁发的《钢铁工业“十二五”发展规划》中,“重点领域和任务”的技术创新重点第一项即非高炉炼铁技术。
中国DRI多年来产量始终在几十万吨徘徊,主要因为工艺、装备未根据国情自主创新,未显示节能减排优势,工程投资大、生产成本高,经济效益不理想。
DRI工艺按还原剂分为气基法和煤基法,按主体设备分有竖炉法、隧道窑法、回转窑法、转底炉法等。
根据冶金原理和中国能源资源结构、经济技术条件,煤基法比较适宜;按机械和热工原理,这几类工业炉窑虽然都能生产DRI,但竖炉是其优选优化成果,性能更好。
炼铁理论和生产实践均可证明,煤基竖炉DRI能耗低、工程投资少,可取的更好效益。
1 煤基竖炉DRI工艺节能的理论根据1.1 DRI流程短炼铁是钢铁冶金上游工序。
考察钢铁生产流程,如图1所示,流程最短、能耗最低路线是从铁矿石直接炼钢的虚线ideal Route。
但这一路线很难实现,因为还原与升温同时进行,高温下金属铁融化后,还原剂中的碳即渗入铁中,铁水含碳量大于钢的标准。
为了得到含碳量较低的钢,不得不增加炼钢工序,将铁水中的碳再氧化脱去。
现代钢铁生产的高炉-转炉炼钢流程就是这样,称作二步法炼钢。
非高炉炼铁重点设备介绍(上)56页共58页文档

36、如果我们国家的法律中只有某种 神灵, 而不是 殚精竭 虑将神 灵揉进 宪法, 总体上 来说, 法律就 会更好 。—— 马克·吐 温 37、纲纪废弃之日,便是暴政兴起之 时。— —威·皮 物特
38、若是没有公众舆论的支持,法律 是丝毫 没有力 量的。 ——菲 力普斯 39、一个判例造出另一个判例,它们 迅速累 聚,进 而变成 法律。 ——朱 尼厄斯
40、人类法律,事物有规律,这是不 容忽视 的。— —爱献 生
谢谢!
36、自己的鞋子,自己知道紧在哪里。——西班牙
37、我们唯一不会改正的缺点是软弱。——拉罗什福科
xiexie! 38、我这个人走得很慢,但是我从不后退。——亚伯拉罕·林肯
39、勿问成功的秘诀为何,且尽全力做你应该做的事吧。——美华纳
40、学而不思则罔,思而不学则殆。——孔子
- 1、下载文档前请自行甄别文档内容的完整性,平台不提供额外的编辑、内容补充、找答案等附加服务。
- 2、"仅部分预览"的文档,不可在线预览部分如存在完整性等问题,可反馈申请退款(可完整预览的文档不适用该条件!)。
- 3、如文档侵犯您的权益,请联系客服反馈,我们会尽快为您处理(人工客服工作时间:9:00-18:30)。
应;最佳煤气H2/(H2+CO);反应空区;影响 竖炉生产率的操作因素
3.2 回转窑
3.2.1 回转窑法炼铁过程
最重要的固体还原剂直接还原工艺。 按不同作业温度可生产海绵铁、粒铁及液态生铁,
其中低温作业的回转窑海绵铁法最有意义。 原料:细粒煤(0~3mm),脱硫剂(0~3mm石灰
4)反应空区:还原反应停滞的反应空间。 特点:Fe2O3→Fe3O4的还原过程已全部结束,而
Fe3O4→FexO的还原仍没有发生,此时矿石还原度 为0.111。
床层温度较低,气相浓度较小就易发生。
5)影响竖炉生产率的操作因素 操作因素→还原速度→生产率
温度:提高入炉煤气温度,有利于提高生产率。
一般可用经验公式确定炉料在回转窑中的停留 时间 。
对于粉料:
式中:θ——炉料堆角;P——窑体斜度,rad; D——窑径。
对于颗粒炉料和球团矿:
式中: θ‘——堆角增量;
R——窑半径,m; g——重力加速度。
回转窑的利用系数
式中:ψ——填充率,%; ——总的停留时间,s;
(3)传热过程
炉料必须加热到800℃才能开始金属铁的还原。 预热段占回转窑长度40%。
3.2.5 硫及有害杂质的去除
脱硫:燃料及矿石中硫→气流。 回转窑气流中H2少,气态硫以COS为主。 COS可被CaO和Fe吸收,CaO更易吸收,故CaO多,
气化脱硫率也愈低。
回转窑中CaS脱硫机理。
脱硫剂:白云石
不利影响:减少硫的挥发率;增加燃料消耗,同时 增加入炉流量;降低炉料含铁量,降低生产率。
①球团体积膨胀而发生侧压系数n增大; ②矿石相互粘结或与炉墙粘结而引起摩擦系数增大。
竖炉利用系数:
式中:τ∑——包括预热、还原、过渡及冷却 各段总的停留时间,h;
Fev——炉料容积含铁量; Fep——产品含铁量,%
3.1.2 传热过程
竖炉内炉料-气流间的传热过程决定了预热炉料 及冷却炉料需要的时间。
正常情况下回转窑处于塌落、滚落和瀑布型落下三 种状态中。
(2)炉料停留时间
由于回转窑不断转动,有摩擦力,炉料不断被推进。 炉料轴心方向的推进速度为ωs。
式中:K——窑体转动一周带炉料下落的次数; N——窑体转速,r/min; S——炉料被带起一次所推进的距离,m。
则炉料停留时间为:
式中:L——窑体长度,m。
冷却带的传热过程与预热带类似。 冷却带中易发生析碳反应(2CO→C+CO2)。
后果:析碳过多,阻碍气流,降低冷却作用。
原因:冷却带处于CO分解反应易发生温度区,新还 原的金属铁具有析碳反应的触媒效应。
措施:保证一定的冷却煤气氧化度。
3.1.3 还原过程
(1)竖炉还原数学模型
简化的一步未反应核模型的导出式:
1)浓度场派生效应:床层中煤气有效成分的浓度与 (CA-CB/Ke)↓→阻碍矿石还原度↑,反之亦然。 结果:减弱操作参数(矿石粒度、矿石还原性、 还原气体入炉成分等)对矿石还原程度的影响。
2)温度场派生效应:任何影响反应床温度分布 的因素都会对还原过程产生显著的影响;反之,矿 石还原度的变化对床层温度场也有一定的影响,即 温度场变化对矿石还原有“反馈”作用。
炉料顺行的条件:有效重力F≥0。根据Janssen公式:
式中:D——竖炉直径,m; M——炉料堆比重,kg/m3; f——炉料与炉墙摩擦系数; n——侧压系数。
高炉中,△P/Z→M,即F→0,下料不顺; 竖炉中,△P/Z 较小(2Pa/m3),M较大
(2000Pa/m3),竖炉不会因为煤气浮力引起悬料。 竖炉悬料的原因:
减小预热段长度的分析:
增大加热面积。
减小炉料填充率。一般填充率<20%,如过小,则 还原条件变坏,所以扩大加热面积作用有限。
增加传热系数。
传热方式为对流(70%)和辐射(25%),操作 温度受限制,气流速度不能过大,所以提高传热 系数可能性不大。
提高尾气温度。有效
尾气温度不能小于500℃,一般多控制在600~ 800℃。 热效率降低(废气热能利用)。
第三章 重点设备介绍
直接还原 气基:竖炉、流化床、反应罐 煤基:回转窑、 反应罐、竖炉
熔融还原 还原单元:竖炉、流化床 熔炼造气单元:煤炭流化床、铁浴炉
3.1 还原竖炉
竖炉法目前占直接还原法的83%; 炉内反应过程与高炉间接还原带相似; 竖炉内分为预热带、还原带、过渡带及
冷却带。
3.1.1 炉料运动
重于泰山,轻于鸿毛。08:12:2608:12: 2608:12Thurs day, December 10, 2020
不可麻痹大意,要防微杜渐。20.12.1020.12.1008:12:2608: 12:26December 10, 2020
加强自身建设,增强个人的休养。2020年12月10日 上午8时 12分20.12.1020.12.10
杂质去除方式;
踏实,奋斗,坚持,专业,努力成就 未来。20.12.1020.12.10Thurs day, December 10, 2020
弄虚作假要不得,踏实肯干第一名。08:12:2608:12: 2608:1212/10/2020 8:12:26 AM
安全象只弓,不拉它就松,要想保安 全,常 把弓弦 绷。20.12.1008:12:2608:12Dec-2010-Dec-20
追求卓越,让自己更好,向上而生。2020年12月10日星期 四上午8时12分 26秒08:12:2620.12.10
严格把控质量关,让生产更加有保障 。2020年12月 上午8时 12分20.12.1008:12December 10, 2020
重规矩,严要求,少危险。2020年12月10日 星期四8时12分 26秒08:12:2610 December 2020
如:煤气H2/H2+CO对还原过程的影响。 H2多,矿石还原度的↑使床层温度↓,阻碍还原 CO多,矿石还原度的↑使床层温度↑,促进还原
即温度场的变化可对铁矿石的还原过程产生一种 反馈作用,作用的效果由煤气中H2和CO相对含量所 决定。
3)最佳煤气H2/H2+CO
动力学:H2↑→反应速率常数和扩散系数↑→还原 速度显著↑
➢ 碳的反应性(Rb)。影响重大。 ➢ 配碳量。Mc↑,还原速度↑。常配加过剩碳量,
为理论值的100~200%。 ➢ 温度。T↑,促进还原,对气化尤为明显。受
限于灰分熔点及矿石的软化点。使窑内温度 有控制地达到最高极限是重要的操作原则。 ➢ 填充率。↑填充率,↓矿石氧化程度,有利于 矿石还原。受限于传热。 ➢ 触媒效应。Li、Na、K改善接触条件。
传热方式
窑尾部分 窑头部分
炉气热辐射
<50% >80%
气流与炉料对流 ≈30% ≈10%
炉墙对炉料导热 ≈30% <5%
实际回转窑内,气流-炉料呈逆流运动,可有五种 传热途径。
令回转窑内预热段炉料吸收热量为Q。 解出:
当入窑炉料温度tso=0时,有: 预热段炉料温度按升高至800℃,预热段长度为
3.2.4 回转窑还原过程
(1)数学模型 还原段的数学模型应结合固体碳还原速率方程。
回转窑还原段中可认为CO→100%,Kb→∞。 或
回转窑操作温度(900~1000℃)下, 矿石的还原速度很快,上式中前项的值大 大高于后项之值,因此碳的气化反应是回 转窑中还原过程的限制环节。
(2)影响还原的因素
煤气流量:流量↑,气固比↑,炉内平均温度↑,推 动力(CA-CB/Ke)↑,促进还原,但利用率↓
矿石入炉粒度:缩小矿石粒度能提高矿石还原速度, 但实际效果不明显。
矿石粒度减小同时有利于传热和冷却,从而提高生 产率。
但需满足炉料透气性的限制。
3.1 还原竖炉学习重点
炉料运动:顺行条件;悬料原因; 传热过程:还原剂、炉料温度分布;预热带
石、白云石),块铁矿(5~20mm)。 炉体稍有倾斜(4%),转速4r/m。窑头外侧有烧
嘴燃烧燃料(煤粉、煤气或然油),废气炉尾排出, 炉气与炉料逆向运动。
炉料在预热段加热,蒸发水分及分解石灰石;在 800℃以后,再进行固体碳还原。
放出CO再氧化区被氧化,提供热量。
炉身横断面有:氧化区、中性区、还原区。 回转窑内进行的反应过程可按炉料运动、传热、还
温度场效应:H2↑→温度↓→还原速度↓ 最佳煤气成分:矿石还原度在某一煤气成分 ( H2/H2+CO)下达到最大值。它与移动床温度条件, 即操作条件和矿石的特性参数有关。
数模计算结果: H2/H2+CO≈0.3 实际生产: H2/H2+CO>0.5, H2+CO>0.75
应舍弃追求使用高H2煤气的观点
而: 由物料平衡:
由热平衡得:
联立以上方程式即为移动床还原过程完整的数学 模型的微分方程组,可用于描述稳态条件下的竖炉 还原过程。
边界条件:气体出口处:Z=0,R=0; 气体入口处:Z=Zi;tg=tgi; CA=CAi;P=Pi。
(2)竖炉中矿石还原过程的特点
主要特点在于移动床反应器内存在两种影响矿石 还原过程的因素,即床层中还原气体的浓度场和 炉料与煤气的温度场。
预热带主要进行气-固相的热交换过程。
对于料柱中一微元段dZ,由热平衡有:
炉料:
⑴
煤气:
⑵
式中:Gs,Gg——炉料及煤气流通量,kg/m2;
β——气-固相间传热系数;
A——单位体积炉料表面积,m2。
由(1)得:
由(2)得:
两式相等得:
即:
积分得:
(3)
由边界条件:ts=tso时,tg=tg‘代入上式得:
其它气化温度低的杂质气化去除。
Pb:PbO、PbS、Pb蒸汽压低,不能大量气化,但 Pb粒易析离海绵铁而被气流带走; Na、K:虽气化温度低,但形成硅酸盐,难还原; P:挥发率低,形成磷酸盐。