皮带秤控制系统PLC软件设计方案
基于PLC的电子皮带秤自控系统的设计与实现
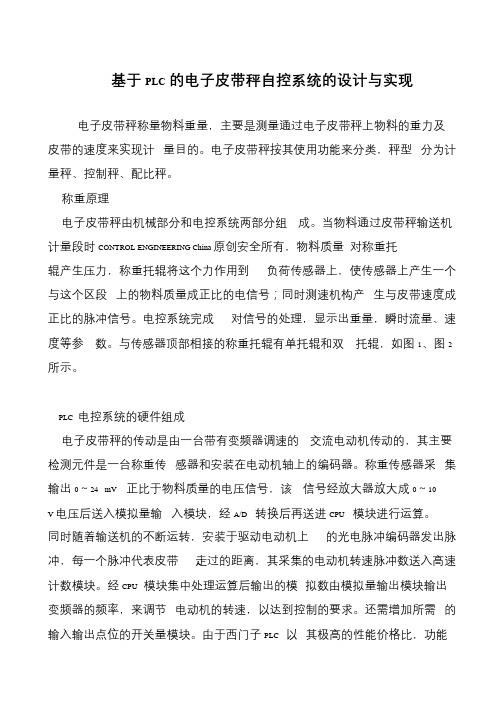
基于PLC的电子皮带秤自控系统的设计与实现
电子皮带秤称量物料重量,主要是测量通过电子皮带秤上物料的重力及
皮带的速度来实现计量目的。
电子皮带秤按其使用功能来分类,秤型分为计量秤、控制秤、配比秤。
称重原理
电子皮带秤由机械部分和电控系统两部分组成。
当物料通过皮带秤输送机计量段时CONTROL ENGINEERING China 原创安全所有,物料质量对称重托辊产生压力,称重托辊将这个力作用到负荷传感器上,使传感器上产生一个与这个区段上的物料质量成正比的电信号;同时测速机构产生与皮带速度成正比的脉冲信号。
电控系统完成对信号的处理,显示出重量,瞬时流量、速度等参数。
与传感器顶部相接的称重托辊有单托辊和双托辊,如图1、图2 所示。
PLC 电控系统的硬件组成
电子皮带秤的传动是由一台带有变频器调速的交流电动机传动的,其主要检测元件是一台称重传感器和安装在电动机轴上的编码器。
称重传感器采集输出0~24 mV 正比于物料质量的电压信号,该信号经放大器放大成0~10 V 电压后送入模拟量输入模块,经A/D 转换后再送进CPU 模块进行运算。
同时随着输送机的不断运转,安装于驱动电动机上的光电脉冲编码器发出脉冲,每一个脉冲代表皮带走过的距离,其采集的电动机转速脉冲数送入高速计数模块。
经CPU 模块集中处理运算后输出的模拟数由模拟量输出模块输出变频器的频率,来调节电动机的转速,以达到控制的要求。
还需增加所需的输入输出点位的开关量模块。
由于西门子PLC 以其极高的性能价格比,功能。
基于PLC的皮带集中控制系统设计

l 系统设计 的意义
采用 P L C对 皮 带 集 中控 制 系 统 具 有 强 大 优 势 , 这 些 优 势 体
现在 :
3 皮带集 中控 制 系统工艺控制要求
本系统有集中、 就地 、 检修三种工作模式。一般系统运行在 集控工作模 式下 , 当组成 生产流水线 时 , 本机根据前 后闭锁 关 系 自动启停 , 同时检测各检测 保护 一般 系统运行在集控工作模 式下设备 的状况 ; 运行 就地工作模式 时 , 操 作员手动 操作按钮 启动/ 停 止皮带机 , 所有保护设备均投 入使用; 运 行检修工 作模 式时 , 操作员手动单 台启动/ 停止 皮带, 保护 设备可有选择性 的 投入使用。 在检修模式下 , 可将使皮带低速运行 。 工作方式的改 变, 只有在皮带输送机不转时进行 ; 皮带输送机运 作时 , 不能改 变其工作方式。 ( 1 ) 程序设计 中, 报警停车等故障信号 自动保 持, 即一旦发 出故 障信号 , 即使经 维修后信号 消失 , 计算机 内仍保 留信 号故 障状态 , 这 时复 位 指 令 可 以清 除 故 障保 持 信 号 。 ( 2 ) 皮带输送机按照逆流 启动 , 顺流延 时停 车, 并具有闭锁 功能 。 ( 3 ) 对 设备 故障和工艺参数 的异 常实时报 警 , 并进行 声光 提示 , 系统状态对位显示 , 更便于维护 。 ( 4 ) 可与 电视 系统配合 , 实 时监视皮 带机重 点部位运 行情 况, 以确保 人员及 设备的安全 ; 具 有喊话 、 打点通讯 功能 , 基本 实现无人值守。 ( 5 ) 皮 带运输机 就地控制箱上 设启停 、 起 动预警按钮 , 设备 启 动前发 出预警 信号 , 提示有 关人员应立 即远离 设备 ; 现场可 随 时停车 , 若设备 由集控启动 , 控制 系统接 到现场 停车信号 后, 可作急停处理, 实施故障停车操作。 ( 6 ) 具有联 网功能 , 能与全矿 井 自动化 监控 系统可靠 的联 接、 实现全局监控 。
基于plc控制皮带秤的毕业设计

唐山工业职业技术学院毕业设计题目:基于plc控制皮带秤的毕业设计姓名:高健专业:电气自动化班级:08电气11班学号:指导教师:任伟2011年4月14日前言皮带传输机又称带式输送机,是一种连续输送机械,也是一种通用机械。
皮带输送机被广泛的应用在港口、电厂、钢铁企业,水泥、食品以及轻工业的生产线。
它可以运送散状物料,也可以运送成件物品。
工作过程中噪声较小,结构简单,皮带输送机可用于水平或倾斜运输。
电子皮带秤是用于测量通过皮带传输机的物料的重量,其基本原理是,连续测量通过皮带单位距离的物料重量,同时测量皮带移动了多少个单位距离,在一段时间内将每个单位距离的重量累计起来就是这段时间皮带所运输的货物的总量。
目录前言 (1)1电子皮带秤 (2)1.1电子皮带秤简介 (2)1.2电子皮带秤工作原理 (3)2设计方案分析 (4)2.1设计思想 (4)2.2设计方案组成 (5)3 系统硬件 (6)3.1系统主控制器 (6)3.1.1适用范围 (6)3.1.2 cpu单元设计 (6)3.2称重传感器 (6)3.2.1称重传感器的原理 (7)3.2.2称重传感器的选择 (8)3.2.3称重传感器的安装 (9)3.2.4称重传感器选择注意问题 (10)3.3测速传感器 (11)3.4变频调速原理 (11)3.5电动机功率的选择 (13)3.6变频器 (13)4控制要求 (15)4.1系统的工艺流程 (16)4.2系统的控制流程 (16)4.3PLC控制系统硬件设置 (17)4.4plc外部接线图 (17)5主程序 (18)7总结 (21)参考文献 (21)1 电子皮带秤1.1 电子皮带秤简介皮带秤经历了纯机械式皮带秤、传感器电子仪表皮带秤发展到今天的传感器微机式皮带秤和微机智能化皮带秤,日新月异的电子计算机技术在皮带秤中的应用,极大地提高了皮带秤的计量精度,改善了它的稳定性,简化了操作程序,易于维护,使其广泛应用于各行各业。
plc皮带课程设计
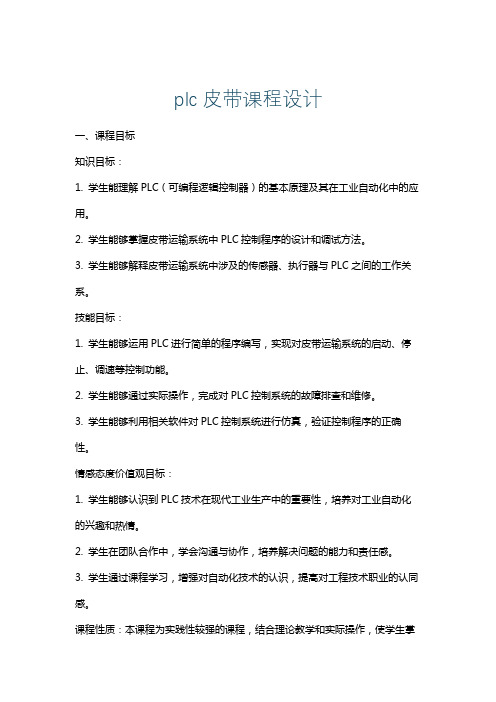
plc皮带课程设计一、课程目标知识目标:1. 学生能理解PLC(可编程逻辑控制器)的基本原理及其在工业自动化中的应用。
2. 学生能够掌握皮带运输系统中PLC控制程序的设计和调试方法。
3. 学生能够解释皮带运输系统中涉及的传感器、执行器与PLC之间的工作关系。
技能目标:1. 学生能够运用PLC进行简单的程序编写,实现对皮带运输系统的启动、停止、调速等控制功能。
2. 学生能够通过实际操作,完成对PLC控制系统的故障排查和维修。
3. 学生能够利用相关软件对PLC控制系统进行仿真,验证控制程序的正确性。
情感态度价值观目标:1. 学生能够认识到PLC技术在现代工业生产中的重要性,培养对工业自动化的兴趣和热情。
2. 学生在团队合作中,学会沟通与协作,培养解决问题的能力和责任感。
3. 学生通过课程学习,增强对自动化技术的认识,提高对工程技术职业的认同感。
课程性质:本课程为实践性较强的课程,结合理论教学和实际操作,使学生掌握PLC在皮带运输系统中的应用。
学生特点:学生具备一定的电气基础和编程知识,对实际操作有较高的兴趣。
教学要求:教师需结合理论讲解与实际操作,注重培养学生的动手能力和实际问题解决能力。
在教学过程中,关注学生的个体差异,鼓励学生积极参与,充分调动学生的主观能动性。
通过课程学习,使学生达到预期的学习成果,为后续相关课程打下坚实基础。
二、教学内容本课程教学内容主要包括以下三个方面:1. PLC基本原理与结构- 介绍PLC的发展历程、基本组成和分类。
- 详细讲解PLC的工作原理,包括扫描周期、输入/输出处理等。
- 分析PLC在工业自动化中的应用案例。
2. 皮带运输系统中PLC控制程序设计- 指导学生了解皮带运输系统的基本构成和工作原理。
- 教授PLC控制程序设计的基本流程,包括需求分析、硬件选型、程序编写等。
- 结合教材章节,讲解PLC编程语言(如梯形图、指令表等)的应用。
3. PLC控制系统操作与维护- 讲解传感器、执行器与PLC的连接方法,掌握外部设备调试技巧。
基于plc控制皮带秤的毕业设计
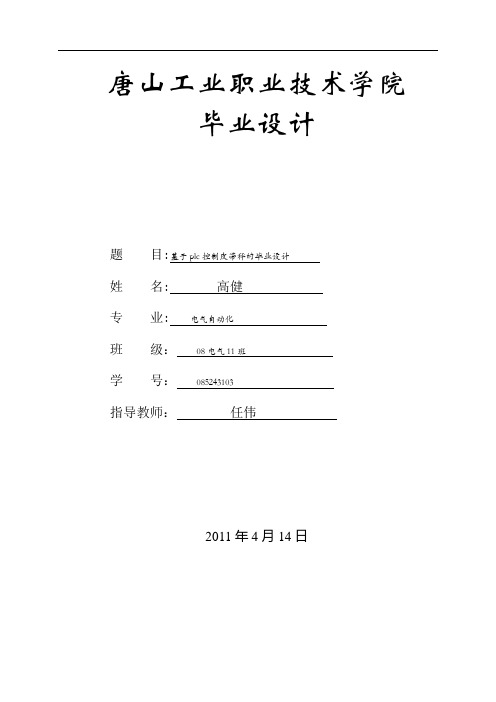
唐山工业职业技术学院毕业设计题目:基于plc控制皮带秤的毕业设计姓名: 高健专业: 电气自动化班级:08电气11班学号:085243103指导教师:任伟2011年4月14日前言皮带传输机又称带式输送机,是一种连续输送机械,也是一种通用机械。
皮带输送机被广泛的应用在港口、电厂、钢铁企业,水泥、食品以及轻工业的生产线。
它可以运送散状物料,也可以运送成件物品。
工作过程中噪声较小,结构简单,皮带输送机可用于水平或倾斜运输。
电子皮带秤是用于测量通过皮带传输机的物料的重量,其基本原理是,连续测量通过皮带单位距离的物料重量,同时测量皮带移动了多少个单位距离,在一段时间内将每个单位距离的重量累计起来就是这段时间皮带所运输的货物的总量。
目录前言 (1)1电子皮带秤 (2)1.1电子皮带秤简介 (2)1.2电子皮带秤工作原理 (3)2设计方案分析 (4)2。
1设计思想 (4)2.2设计方案组成 (5)3 系统硬件 (6)3.1系统主控制器 (6)3。
1.1适用范围 (6)3.1.2 cpu单元设计 (6)3.2称重传感器 (6)3.2。
1称重传感器的原理 (7)3。
2。
2称重传感器的选择 (8)3。
2。
3称重传感器的安装 (9)3。
2。
4称重传感器选择注意问题 (10)3.3测速传感器 (11)3。
4变频调速原理 (11)3.5电动机功率的选择 (13)3。
6变频器 (13)4控制要求 (15)4。
1系统的工艺流程 (16)4.2系统的控制流程 (16)4。
3PLC控制系统硬件设置 (17)4.4plc外部接线图 (17)5主程序 (18)7总结 (21)参考文献 (21)1 电子皮带秤1.1 电子皮带秤简介皮带秤经历了纯机械式皮带秤、传感器电子仪表皮带秤发展到今天的传感器微机式皮带秤和微机智能化皮带秤,日新月异的电子计算机技术在皮带秤中的应用,极大地提高了皮带秤的计量精度,改善了它的稳定性,简化了操作程序,易于维护,使其广泛应用于各行各业.皮带秤具有动态测量和自动在线测量等优点,被广泛应用于产品的定量包装和工业配料等工业现场,不仅起到减员增效、节支创收和减少误差的作用,而且加强了企业的管理,缩短作业时间,改善了操作条件,提高劳动生产率,降低劳动强度,从而大大提高了生产的自动化程度,被广泛应用于煤炭、石油、化工、电力、轻工、冶金、矿山、交通运输、港口、建筑、机械制造和国防等各个领域.皮带秤正以其独特的优势,作为一种新兴的高技术产业受到全世界的普遍关注,具有十分广阔的发展前景。
基于PLC的智能组合秤控制系统设计

基于PLC的智能组合秤控制系统设计1控制系统的总体结构方案1.1 智能组合秤的机械结构常规一般的组合秤的结构主要组成部分是一个由多个部件组成的复杂的机械系统,它们分别是:输入斗、主振动器、线振盘、缓存斗、称量斗、传感器、记忆斗和集料斗。
1.2 工作原理组合秤在整个生产流程中扮演着至关重要的角色,而产品包装机则是其中的关键组成部分。
在机器启动后,物料被送至组合式料斗[3]。
主振动机的振动使物料均匀地进入各管线。
经过管道的振动,物料被轻松地送入底部的缓冲器中。
当缓冲器门打开时,物料就可以被卸下来,然后进入底部的称重器中进行称重。
完成称重之后,称重器门又会打开,物料就会再次进入底部的记录器中。
当检测到料斗门关闭时,缓冲斗再次将物料送至料斗。
在称重过程中,在称重过程中,将称重过程与存储过程相结合,使称重过程达到最优。
这时,所选物料斗门开启,物料落入料斗中,最终成袋,完成包装[4]。
PLC被视为整体集成控制系统的关键部分,它能够从称量传感器获取的模拟信息,经由编写的程序和对应的数据进行分析,最终产生一种可靠的控制信息,从而驱动步进电机,实现对指定的料斗门的自动启动。
2智能组合秤的硬件设计2.1 系统整体电气结构设计结合现代称重控制系统的优缺点,本方案以PLC作为核心控制部件,采用主从式分布式控制和测量的基本理论知识,将分布式I/O、传感器、驱动器和执行器等设备连接成链式控制系统,实现组合称重[8]。
系统的电气结构工作图包括重量检测模块、A/D转换模块、料位检测、振机控制和步进电机控制系统。
系统由多个关键组件组成,包括PLC系统核心控制器、称重传感器、步进电机控制系统、光电传感器、主振动器和直线振动器,以及料位检测装置和料位加料装置。
PLC系统核心控制器是下位机的核心,它负责传递生产信息,并接收控制命令。
同时,它还接收来自外部控制器的输入信号,并输出控制信号以实现步进电机的旋转动作[9]。
称重传感器用于采集物料的重量,并将其转换为标准电压信号。
基于PLC自动配料皮带运输机控制系统的设计_毕业设计论文

基于PLC自动配料皮带运输机控制系统的设计摘要在现代化的工业生产中常常需要对物料进行加工、搬运,如果这些繁杂的工作由人工完成的话不但效率低,而且劳动强度大,不适合现代化的生产需要。
本文主要对基于PLC自动配料皮带运输机控制系统进行了详细的研究,该系统有两大部分构成:自动配料装置及皮带运输机控制系统。
该控制系统具有精度高、成本低、抗干扰能力强、故障率低、操作维护简单等特点,具有良好的应用价值,在建材、化工、食品机械、钢铁、冶金、煤矿等工业生产中广泛使用。
本次设计主要的内容:采用三菱FX2N系列PLC实现控制系统的设计,着重从带式运输机,液体混合装置系统两个方面深入研究,确定其控制要求,明确PLC 的机型的选择,确定I/O地址的分配,设计I/O接线图、控制流程图及梯形图,深入理解PLC的编程方法,按照控制要求对自动配料皮带运输机系统进行编程。
关键字:PLC,自动配料皮带运输机,程序,设计!!所有下载了本文的注意:本论文附有CAD图纸和完整版最终设计,凡下载了本文的读者请留下你的联系方式(QQ邮箱),或加我百度用户名QQ,我把图纸发给你。
最后,希望此文能够帮到你!PLC-BASED AUTOMATIC CONTROL SYSTEM FORBELT CONVEYOR DESIGNABSTRACTIn modern industrial production is often a need for materials for processing, handling, if the complexity of the work completed by the manual, then not only inefficient, but also labor-intensive, not suitable for modern production. In this paper, PLC-based automatic control system for belt conveyor carried out a detailed study, which consisted of two major systems: Automatic batching plant and control system for belt conveyor. The control system has high accuracy, low cost, anti-interference ability, low failure rate, simple operation and maintenance, has a good application value, In building materials, chemical industry, food machinery, iron and steel, metallurgy, coal and other widely used in industrial production.The main design elements: the use of Mitsubishi FX2N Series PLC control system design, focusing on transport belt, liquid mixing device-depth study of two aspects of the system to determine control requirements, the model explicitly the choice of PLC, determine the I / O address allocation, the design of I / O wiring diagram, control flow chart and the ladder, in-depth understanding of PLC programming method, in accordance with the control requirements of the transport belt automatic programming system.KEY WORDS: PLC, automatic transport belt ingredients, program, design目录前言 (1)第1章可编程序控制器概述 (2)1.1可编程序控制器的产生和发展 (2)1.2可编程控制器的基本组成和工作原理 (6)1.2.1 PLC的基本组成 (6)1.2.2 PLC的工作原理 (9)1.3可编程序控制器的特点 (11)第2章三菱FX2N系列可编程控制器简介 (13)2.1 FX2N系列PLC的结构特点 (13)2.2 FX2N系列PLC的基本组成 (14)2.3 FX2N系列可编程控制器内部元件及功能 (14)第3章应用PLC实现控制系统的设计 (19)3.1选题依据 (19)3.2方案研究与选择 (19)3.3结构设计及控制要求 (21)第4章系统的总体设计 (24)4.1 PLC机型的选择及外部接线图 (24)4.2 I/O设备及I/O编号的分配 (24)4.3顺序功能图的设计 (25)4.4梯形图的设计及程序分析 (26)结论 (30)谢辞 (31)参考文献 (32)附录 (33)外文资料翻译 (35)前言PLC目前已广泛应用于工业生产的自动化控制领域,无论是从国外引进的自动化生产线,还是自行设计的自动控制系统,都普遍采用了PLC控制。
基于plc的电子皮带秤设计
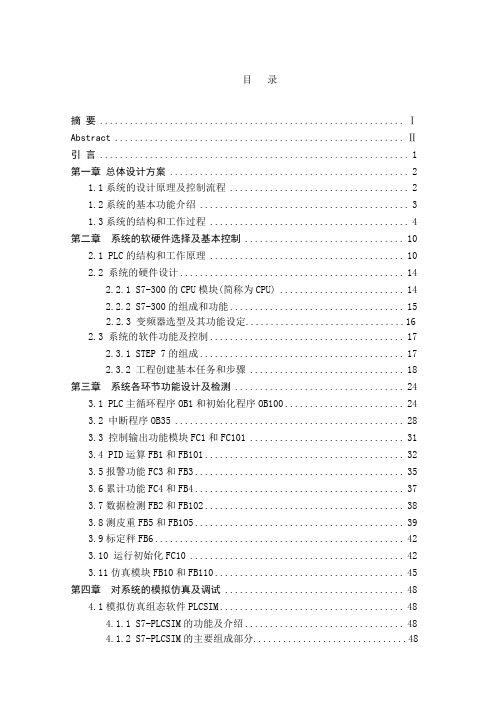
目录摘要 (Ⅰ)Abstract (Ⅱ)引言 (1)第一章总体设计方案 (2)1.1系统的设计原理及控制流程 (2)1.2系统的基本功能介绍 (3)1.3系统的结构和工作过程 (4)第二章系统的软硬件选择及基本控制 (10)2.1 PLC的结构和工作原理 (10)2.2 系统的硬件设计 (14)2.2.1 S7-300的CPU模块(简称为CPU) (14)2.2.2 S7-300的组成和功能 (15)2.2.3 变频器选型及其功能设定 (16)2.3 系统的软件功能及控制 (17)2.3.1 STEP 7的组成 (17)2.3.2 工程创建基本任务和步骤 (18)第三章系统各环节功能设计及检测 (24)3.1 PLC主循环程序OB1和初始化程序OB100 (24)3.2 中断程序OB35 (28)3.3 控制输出功能模块FC1和FC101 (31)3.4 PID运算FB1和FB101 (32)3.5报警功能FC3和FB3 (35)3.6累计功能FC4和FB4 (37)3.7数据检测FB2和FB102 (38)3.8测皮重FB5和FB1O5 (39)3.9标定秤FB6 (42)3.10 运行初始化FC10 (42)3.11仿真模块FB10和FB110 (45)第四章对系统的模拟仿真及调试 (48)4.1模拟仿真组态软件PLCSIM (48)4.1.1 S7-PLCSIM的功能及介绍 (48)4.1.2 S7-PLCSIM的主要组成部分 (48)4.1.3 配置过程 (48)4.2 模拟组态步骤 (50)结论 (51)谢辞 (52)参考文献 (53)河南城建学院毕业设计论文摘要摘要随着计算机、网络、数据库等相关技术的不断发展和完善,自动化系统得到极大的完善。
本说明书根据配料生产的特点和要求,介绍了皮带秤S7-300 PLC自动配料控制系统的设计方案及仿真、使用方法。
系统完成了配料系统的设计要求,并对控制系统的主要控制功能以及结构作了详细的介绍。
皮带运输机PLC自动控制项目设计方案

⽪带运输机PLC⾃动控制项⽬设计⽅案⽪带运输机PLC⾃动控制项⽬设计⽅案1 前⾔1.1设计的⽬的和意义冶⾦、煤矿、化⼯、机械、钢铁、建材、⾷品等⼯业⽣产中,需要⼴泛使⽤⽪带运输机,它为企业的⽣产承担了绝⼤多数散料运输任务。
可编程控制器(PLC)是以微处理器技术为基础,综合计算机技术和⾃动化技术发展起来的⼀种新型⼯业控制器,⼴泛应⽤于⼯业⽣产的各个领域。
由于PLC采⽤的控制系统或设备具有可靠性⾼,控制易于实现,系统设计灵括,能在实验室进⾏现场模拟调试,编程简单,安装⽅便,较好的抗⼲扰能⼒,被誉为当代⼯业⽣产⾃动化的⽀柱之⼀,正在得到越来越⼴泛的应⽤。
利⽤PLC可以使⽪带运输机的传动系统逐渐实现了全⾃动控制状态,并且使⽪带运输机具有完善的控制特性及简易的操作、基本免维护的⼯作量,达到⼀种经济、安全、可靠且运⾏效率⾼的状况, 其独特的易于使⽤性、可靠性和灵活性越来越受到⼴⼤⼯程技术⼈员的青睐。
对于港⼝、⼚区⼴泛使⽤的⽪带运输机,应⽤PLC控制,可以使⽪带机⽣产线的控制更加灵活、可靠。
通过PLC进⾏控制提⾼了企业⽣产的效率,为⼯业⽣产的进⾏节省了⼤量的⼈⼒、物⼒、财⼒。
1.2 ⽪带运输机的现状电⽓传动技术以运动机械的驱动装置---电动机为控制对象,以微电⼦装置为核⼼,以电⼒电⼦功率变换装置为执⾏机构,在⾃动控制理论的指导下完成电⽓传动⾃动控制系统,控制电动机的转矩和转速,将电能转换成机械能,实现⼯作机械的旋转运动或反复运动。
因电机的种类的不同,我们可以将分为直流电动机传动和交流电动机传动。
⾃19世纪80年代起⾄19世纪末,⼯业上传动⽤的电动机⼀直被直流电机垄断,到了19世纪末,出现了三相电源和结构简单且坚固耐⽤的交流⿏笼型电机以后,交流电机才在不调速的领域代替了直流电动机传动装置。
对⽣产过程的监视和控制,在初级阶段是由⼈⼯进⾏的。
⼯作⼈员凭⾃⼰的感官或借助于仪表等来监视⽣产过程,⽤头脑做出判断决策,并视情况进⾏必要的控制。
皮带运输机的plc控制系统设计

摘要在物流企业机电输送中,需要把一件物品从某一位置搬到另一位置,并且能自动完成工序,因此输送带控制系统被广泛运用于物流行业,然而,传统的接触继电器控制系统有着接线复杂、抗干扰能力差和容易接触不良从而造成故障的缺陷,而且功能扩展性差。
PLC系统因其可靠性高、编程简单、功能完善而越来越受到青睐,传统的接触继电器控制系统已逐步被PLC系统所取代.目前传统的继电接触器控制系统己逐步为PLC所取代这是一种发展的趋势。
接触继电器控制系统是根据一定的生产机械,一定的生产工艺,采用硬接线方式,以完成一定的逻辑控制(包括空间控制、时间控制等)功能的。
而一旦生产机械不同或生产工艺变更,则系统必须重新设计改造。
而PLC技术,由于采用了微电了技术和计算机技术,其逻辑控制功能可以通过软件编程来实现。
因此当生产机械或生产工艺变更,只需改变程序或变更一下接线端子就可以了。
本文介绍了基于的输送带控制系统,该系统通过控制输送带的运行与停止、翻身电机和推杆电机的正反转,实现了工作的顺利进行.关键词:PLC;输送带;使用目录摘要 (I)1前言 (1)1。
1研究背景 (1)1.2文献综述 (2)1。
3设计工作方案 (3)2PLC系统的工作分析及特点 (4)2。
1 工作流程分析 (5)2.2 系统的工作步进时序图 (6)2.3 PLC的特点 (6)3输送带控制系统描述及其系统运行要求 (7)4确定系统的输入输出点数及PLC类型 (8)5 PLC皮带运输机概述 (9)5.1 PLC控制技术在煤矿井下的应用 (9)5。
2 控制系统组成 (10)6 皮带运输机的设计 (10)6.1系统总体设计 (10)6。
2 系统的硬件设计 (11)6。
2.1 PLC 选型 (11)6.2.2 I/O 分配表 (12)6.2。
3 I/O 接线图 (12)6.3 系统的软件设计 (13)6。
3.1 模块编程思想 (13)6.3。
2 主程序的设计 (14)7 结语 (16)1前言目前,输送带控制系统在工业领域有着广泛的应用,此外,输送带控制系统也广泛运用于物流行业,采用传统的接触继电器控制系统,不仅接线复杂、抗干扰能力差,易因接触不良而造成故障,而且功能扩展性差。
皮带运输机PLC控制系统设计
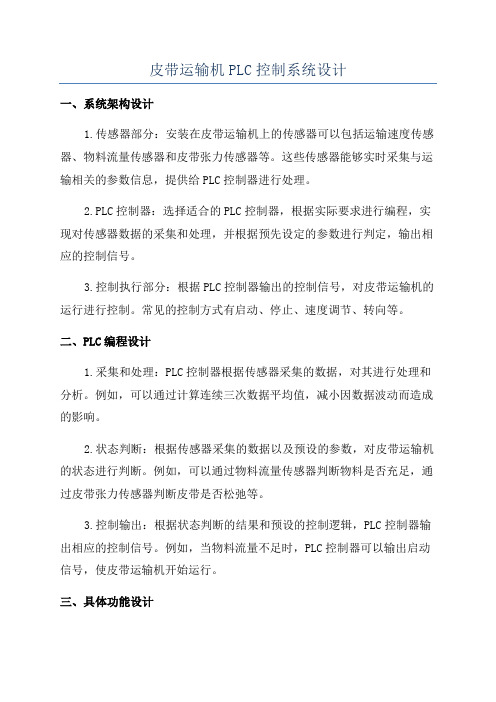
皮带运输机PLC控制系统设计一、系统架构设计1.传感器部分:安装在皮带运输机上的传感器可以包括运输速度传感器、物料流量传感器和皮带张力传感器等。
这些传感器能够实时采集与运输相关的参数信息,提供给PLC控制器进行处理。
2.PLC控制器:选择适合的PLC控制器,根据实际要求进行编程,实现对传感器数据的采集和处理,并根据预先设定的参数进行判定,输出相应的控制信号。
3.控制执行部分:根据PLC控制器输出的控制信号,对皮带运输机的运行进行控制。
常见的控制方式有启动、停止、速度调节、转向等。
二、PLC编程设计1.采集和处理:PLC控制器根据传感器采集的数据,对其进行处理和分析。
例如,可以通过计算连续三次数据平均值,减小因数据波动而造成的影响。
2.状态判断:根据传感器采集的数据以及预设的参数,对皮带运输机的状态进行判断。
例如,可以通过物料流量传感器判断物料是否充足,通过皮带张力传感器判断皮带是否松弛等。
3.控制输出:根据状态判断的结果和预设的控制逻辑,PLC控制器输出相应的控制信号。
例如,当物料流量不足时,PLC控制器可以输出启动信号,使皮带运输机开始运行。
三、具体功能设计1.启动和停止控制:根据传感器采集的物料流量和皮带张力等信息,PLC控制器可以自动判断何时启动或停止皮带运输机。
当物料流量低于设定值时,PLC控制器输出启动信号,使皮带运输机开始运行;当物料流量达到设定值或超过设定值时,PLC控制器输出停止信号,使皮带运输机停止运行。
2.运行速度控制:在运输过程中,根据物料的性质和工艺要求,需要调节皮带运输机的运行速度。
PLC控制器可以根据传感器采集的参数信息,自动调节皮带运输机的运行速度,以实现最佳的运输效果。
3.报警和故障诊断:根据传感器采集的数据和PLC编程设计,PLC控制器可以实时监测皮带运输机的运行状态,当出现异常情况或故障时,及时进行报警,并进行相应的故障诊断和处理。
四、安全设计与人机界面1.安全设计:在PLC控制系统设计中,安全是一个重要的考虑因素。
配料皮带秤PLC自动控制系统设计开题报告

配料皮带秤PLC自动控制系统设计开题报告电信学院毕业设计开题报告电气工程及其班级电气四班姓名白丽霞专业自动化王晓兰肖骏题目类型工程设计学号 10230419 指导教师配料皮带秤PLC自动控制系统设计题目一、选题背景及依据(简述题目的技术背景和设计依据,如实说明选题目的、意义,列出主要参考文献)1、选题背景及依据配料皮带秤在诸多行业的工业生产过程中占有及其重要的地位,配料皮带秤工序的合理性、稳定性、准确性以及快速性直接影响到以后各生产环节的顺利进行。
配料生产系统是一种将多种原料按一定比例混合在一起,进行加工生产出某种产品的过程。
其中配料是生产中必不可缺少的关键环节,落后的配料设备不仅效率低,而且配料不准,手工操作又将人的因素引入配料环节,使工艺配方难以在生产中实现,严重影响产品质量的稳定及进一步提高。
因此实现高精度的快速的配料皮带秤对工业企业生产有极为重要的意义。
目前国内皮带秤自动配料系统主要是采用单片机进行简单的称量计算和PID调节,功能简单,控制精度低,管理功能弱,可靠性不高。
而金川集团镍冶炼厂的皮带秤自动配料系统也采用了单片机控制,其配料车间就有20多台皮带配料秤,只能对分散在厂房每个地方的配料秤主机依次进行设置,对于连续配料的质量有很大的影响,一是会浪费原材料,二是影响生产的顺利进行,重则影响生产效率,在某些重要生产岗位上,配料失误甚至会酿成事故,可见配料精度与配料速度影响着整个生产的质量和产量。
PLC具有高可靠性,丰富的I/O接口模块,模块化结构适合各种工业控制的需要,编程简单易学,安装简单维修方便等特点。
而可靠性高,稳定性好是PLC相比于单片机的最大的优点。
本课题是基于镍冶炼厂皮带配料秤的应用现状,提出皮带配料秤与整个镍冶炼生产过程控制系统集中架构在一起,实现生产过程控制系统与配料系统的集中控制,通过上位机对现场配料情况进行实时监控,并可直接在上位机上进行相关参数的设定,使得整个系统自动化程度和生产效率得到了进一步的提高。
基于PLC的直压恒张力电子皮带秤设计
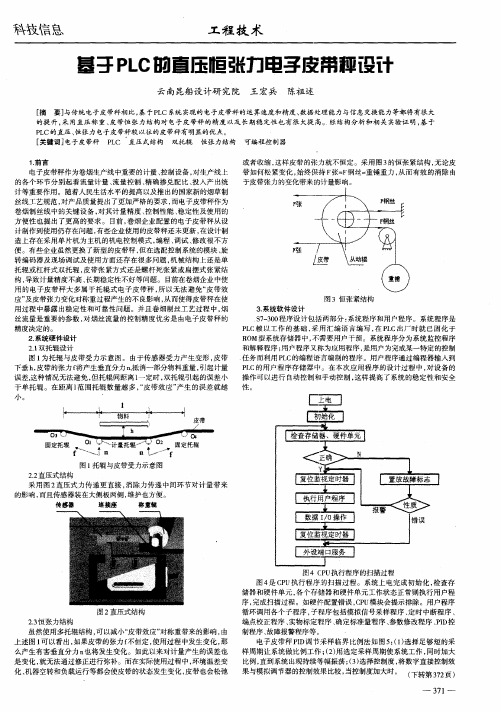
或者收缩 , 这样皮带的张力就不恒定 。采用 图 3 的恒张紧结构 , 无论皮 带如何 松紧变化 , 始终保 持 F F 张= 钢丝 : 重锤重力 , 而有效的消 除由 从 于皮带张力的变化带来的计 量影响。
图 3恒张紧结构 3系统软件设计 . s — 0 程序设 计包括两部分 : 程序和用户程序 。系统程序是 730 系统 P C 以工作 的基础 , L 赖 采用 汇编语 言编写 , P C出厂时 就已 固化于 在 L R M型系统存储器 中, 需要用户干预 。系统程序 分为系统监控程序 O 不 和解释程序 ; 用户程序又称为应用程序 , 是用户为完成某一特定的控制 任务而利用 P C L 的编程语言编制的程序。用户程序通过编程器输入到 PC L 的用户程序 存储器 中。在本次应用 程序的设计 过程 中, 设备的 对 操作可 以进行 自动控制和手 动控 制 , 这样提 高了系统的稳定性 和安全
பைடு நூலகம்
科技信 息
工 程 技 术
双层热缩管硇 应用
天 津市 油管厂 郑克 宁
[ 摘 要] 汽车用热 收缩双壁 管( 以下简称 : 双层 热缩管) 是伴 随着汽车制动油管防腐要 求的提 高而产生的新材料 , 在九十年代初就进 入 了我 国, 近几年才被普遍应用。特别在 当前小型车加 装大功率发动机 以 A s 及 B 和助力转 向的增 多, 使得制动 油管的布置越来越复 杂, 常常 出现油 管之 间以及油 管与相 关零件之 间的干涉 问题 , 双层热缩管为油管提供 了可靠的保护。本文就双层热缩管在汽车制动 系统和燃油 系统的保护作 用进行探讨 。并且对热缩管的质量要 求做 出分析 。 [ 关键词] 双层热缩管 防腐 干涉 布置
基于PLC的皮带集中控制系统方案
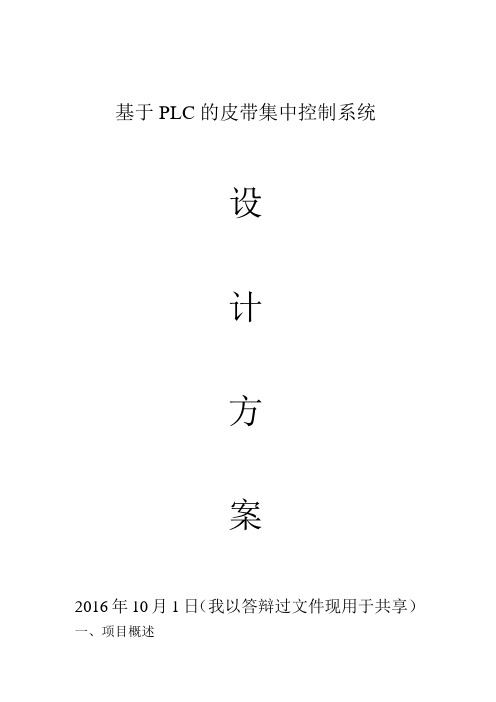
(1)控制系统由喷煤中控室集中控制。
(2)解决集中控制存在的事故隐患,减少各设备之间相互脱节、无法充分发挥效率的缺点。实现现场无人操作,仅设巡检人员。
(3)本系统采用分布式控制(PLC控制系统),实现提高指挥效率和生产率,达到减人提效的目的。
(4)实现集中控制:智能化操作和手动操作方式。
开关量输入模块(16点,120/230VUC)
DI16xUC 120/230V
6ES7 421-1FH20-OAAO
开关量输入模块(16点,120/230VUC)
DI16xUC 120/230V
6ES7 421-1FH20-OAAO
开关量输入模块(16点,120/230VUC)
D016Xac120/230V/2A
(4)保护
①一偏保护
②二偏保护
③紧停保护
④打滑 保护
五、控制系统主要功能与特点
(一)集中控制
1.系统容量
系统输入/输出点位,数据采集记录,存储空间40G
2. 扩展功能
选择的计算机和系统软件留有备用容量和接口,可以很方便地进行扩展(如增加胶带机的保护装置);分布式系统结构具有良好的扩展性,如胶带机随生产的发展增多,可方便的增加胶带机控制。
(2)实现皮带运输远程集中控制、可视化操作。
(3)保证系统安全可靠运行,最终实现提出的各项技术指标和要求。
(4)免费培训现场工程技术人员,最终达到基本掌握系统硬件的组成和基本原理,熟练掌握PLC语言的编程,掌握组态软件的基本使用。
三、系统概述
目前,现有的各条胶带机已经实现集中控制。根据现场实际使用要求,达到安全可靠运行以及减人提效目的。
3. 控制功能
具有远程启动、停止、复位和测试功能,并可进行集中远程编程、 故障(保护)屏蔽及控制方式转换点动操作等功能控制。
基于三菱PLC的皮带秤设计
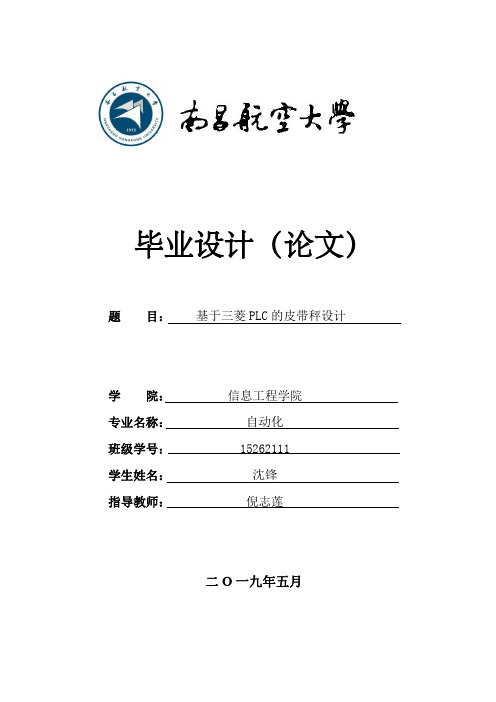
毕业设计(论文)题目:基于三菱PLC的皮带秤设计学院:信息工程学院专业名称:自动化班级学号:********学生姓名:**指导教师:***二O一九年五月基于三菱FX3u系列PLC的皮带秤设计摘要:在工程实践中,特别是基础能源建设运行过程,散状物料的动态称重过程尤为关键,它的运行效率、称重精度、运行可维护性和稳定性直接影响到工厂运行的效率、收益和成本,一套出色的皮带秤能够完美的解决物料动态称重问题,能够解决因误差而带来的利益矛盾和纠纷。
本设计以三菱FX3u系列PLC为控制基础,依托三菱高运行速度、大容量数据、便捷输入输出口辅以高精度称重、测速传感器,对电机速度进行控制和称重;由于本过程为动态过程,而动态称重需要较高精度的称重传感器,进行定时采样,实践证明,科学的称架设计和严格的控制算法能够极大提高称重精度,本课设的电机为普通三相交流异步电机,较之能够用旋转编码器的步进电机,优点为荷载大,缺点为速度控制不精准,因此三菱PLC的PID指令算法和光束测速传感器就产生巨大作用,另外,三菱的外置特殊模块A/D,D/A转换模块的使用,变频器的使用,触摸屏的远程控制极大的丰富了此款皮带秤的可操作性、稳定性和精度,相应的附加功能也更加丰富和适用。
关键词:三菱PLC皮带秤动态称重PID算法指导老师签名:Design of belt scale based on mitsubishi FX3u series PLC Abstract:In engineering practice,especially in energy infrastructure operation process, it is important to the dynamic weighing process of loose materials,its operation efficiency, weighing accuracy,the maintainability and stability directly affects the efficiency of the factory,the benefits and costs,a good belt scale can perfectly solve the problem of dynamic weighing material,can be solved by the benefits of error and contradictions and disputes.This design takes mitsubishi FX3u series PLC as the control basis.Relying on mitsubishi's high running speed,large capacity data,convenient input and output,assisted by high-precision weighing and velocity sensor,it controls and weighs the motor speed.Because this process is A dynamic process,and need A high precision weighing sensor,weighting for time sampling,the practice proved that science said frame design and strict control algorithm can greatly increase the weighing accuracy,this class of motor for ordinary three-phase ac asynchronous motor than have the stepper motor,rotary encoder to advantage for large load,shortcomings of speed control is not accurate,so the algorithm of PID instruction and mitsubishi PLC beam speed sensors will have A huge role,in addition, mitsubishi's external special A/D module,D/A conversion module,the use of the use of frequency converter and touch screen remote control greatly enriched,This belt scale's operability,stability and accuracy,the corresponding additional functions are more rich and applicable.Keyword:Mitsubishi PLC belt scale dynamic weighing PID algorithmSignature of Supervisor:目录1皮带秤的历史及国内外发展状况简介 (1)1.1世界第一台皮带秤 (1)1.2皮带秤在国外的发展 (1)1.3皮带秤在国内的发展 (2)2称重皮带的称重原理分析 (3)2.1称重皮带的两种算法 (3)2.2累积法 (3)2.3积分法 (4)2.4本次采用方法 (5)3PLC的简介 (6)3.1可编程序控制器 (6)3.2三菱FX系列PLC的简介 (6)3.3FX3u型PLC使用说明 (6)3.4FX3u产品的特点 (7)3.5PLC的编程语言 (7)4速度传感器和称重传感器的选择 (8)4.1传感器选择依据 (8)4.2速度传感器的选择 (8)4.3皮带秤称架的选择及分析 (10)4.4称重传感器的选择 (11)5三菱PLC中PID指令解析 (13)5.1PID算法的意义 (13)5.2PID指令的参数明晰 (13)5.3PID参数调整 (14)5.4设计程序结果 (15)6AD、DA模块的运用 (17)6.1选择型号说明 (17)6.2FX2n-2AD技术性能与输出特性 (17)6.3FX2n-2DA的技术性能和输出特性 (24)6.4BFM的使用规则 (25)7变频器的使用 (28)7.1E700系列变频器简述 (28)7.2E700变频器的接线端子 (28)7.3三菱FR-700变频器控制电路 (29)7.4操作面板的介绍 (32)7.5变频器的参数设置 (33)8电容屏的设计 (34)8.1软件介绍 (34)8.2画面简介 (34)总结 (39)参考文献 (40)致谢 (41)1皮带秤的历史及国内外发展状况简介1.1世界第一台皮带秤皮带秤者,应时之物,为衡器大宗。
基于PLC的电子皮带秤设计
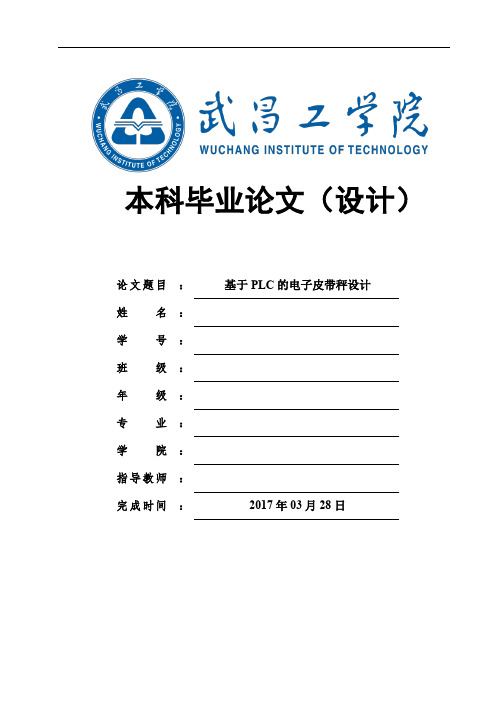
本科毕业论文(设计)论文题目:基于PLC的电子皮带秤设计姓名:学号:班级:年级:专业:学院:指导教师:完成时间:2017年03月28日作者声明本毕业论文(设计)是在导师的指导下由本人独立撰写完成的,没有剽窃、抄袭、造假等违反道德、学术规范和其他侵权行为。
对本论文(设计)的研究做出重要贡献的个人和集体,均已在文中以明确方式标明。
因本毕业论文(设计)引起的法律结果完全由本人承担。
毕业论文(设计)成果归武昌工学院所有。
特此声明。
作者专业:作者学号:作者签名:2017年3月28日基于PLC的电子皮带秤设计XThe Design of Electronic Belt ScaleBased on PLCX, X2017年03月28日摘要很多技术如PLC技术的发展,极大地提高了社会生产效率,提高了产品生产的质量,在生产环节中,配料行业的地位尤为重要,合理稳定而又准确快速的配料生产工序直接关乎生产中的各个步骤,因此配料生产行业拥有着广阔的发展前景。
外部接线简单,内部程序的简单性都是PLC的优点。
PLC在外部接线没有发生变化时,不仅可以很快的重新设计程序,而且其内部的软继电器寄存器可以实现多种极为复杂的控制功能,且不易发生故障,不易受到干扰,使用寿命长,执行命令时间短,可以使用多重指令,等优点,这些优点都正好弥补了传统继电器的缺点。
因此,本研究选择的研究对象是基于PLC的电子皮带秤。
本文在研究时,遵循配料生产的特点和生产要求。
研究了S7-300 PLC电子皮带秤自动配料控制系统的设计、仿真和使用方式。
本设计中的系统依据配料生产的要求,详细的介绍了控制系统的主要控制功能和结构。
重点介绍了STEP7软件的各项情况,包括对其的选择、安装、程序的设计和整体系统的调试。
关键词:电子皮带秤;S7-300;PLCAbstractWith the computer, network, database and other related technologies continue to develop and improve the automation system has been greatly improved. PLC application greatly improved the quality of products and production efficiency, in the entire ingredients industry has a broad application prospects. The batching system occupies an extremely important position in the industrial production process of many industries. The rationality, stability, accuracy and rapidity of the batching process directly affect the subsequent production process. PLC has the advantage of simple external wiring, internal program variable, without changing the wiring in the case, you can re-design process, the construction period is short, the internal soft relay is a register, no contacts, low failure rate, long life, anti-jamming capability Strong, the implementation of a short time, the application of instructions, can achieve complex control functions, etc. The traditional relay is the lack of contact system, high failure rate, the average repair time is long, short life, power consumption, change the system function , Will be re-wiring, heavy workload, easy mistakes, the implementation of a long time and so on. Therefore, this study selected PLC-based electronic belt scale for research.According to the characteristics and requirements of batch production, this paper introduces the design scheme and simulation and use method of automatic batching control system of belt scale S7-300 PLC. The system has completed the design requirements of the batching system, and the control system of the main control functions and the structure of a detailed introduction. But also highlights the STEP7 software selection, installation, ladder program design and the overall system debugging and so on.Keywords:electronic belt scale; s7-300; plc目录1 引论 (1)2 总体设计方案 (2)2.1系统的工作原理和流程图 (2)1.2系统的基本功能 (3)2.3系统的结构和工作过程 (4)2.4 PLC控制系统软件设计 (6)3 系统各环节功能设计及检测 (8)3.1 PLC主循环程序OB1和初始化程序OB100 (8)3.2 中断程序OB35 (13)3.3 控制输出功能模块FC1和FC101 (15)3.4 PID运算FB1和FB101 (17)3.5报警功能FC3和FB3 (20)3.6累计功能FC4和FB4 (22)3.7数据检测FB2和FB102 (23)3.8测皮重FB5和FB1O5 (24)3.9标定秤FB6 (27)3.10 运行初始化FC10 (27)3.11仿真模块FB10和FB110 (30)4 对系统的模拟仿真及调试 (33)4.1模拟仿真组态用软件PLCSIM (33)4.1.2 S7-PLCSIM的主要组成部分 (33)4.1.3 配置过程 (33)4.2 模拟组态步骤 (35)结语 (36)致谢 (37)主要参考文献 (38)附录 (39)1 引论如今像医疗、建材、修路以及包装等各行各业都在广泛地使用PLC自动配料控制系统和应用计算机技术。
- 1、下载文档前请自行甄别文档内容的完整性,平台不提供额外的编辑、内容补充、找答案等附加服务。
- 2、"仅部分预览"的文档,不可在线预览部分如存在完整性等问题,可反馈申请退款(可完整预览的文档不适用该条件!)。
- 3、如文档侵犯您的权益,请联系客服反馈,我们会尽快为您处理(人工客服工作时间:9:00-18:30)。
第一章 总体设计方案
1.1
通过产臂上皮带装置及料的重量测定流量,由电磁振动给料机控制给料量,连续计 量秤。优点连续计量,缺点动态计量影响精度。称重给料机将经过皮带上的物料,通过 称重秤架下的称重传感器进行检测重量,以确定皮带上的物料重量;重量信号送入皮带 给料机控制器,产生并显示累计量/瞬时量。给料控制器将该量与设定量进行比较,由控 制器输出信号控制变频器,实现定量给料的要求。可由上位P(机设定各种相关参数,并 与PLC实现系统的自动控制。它可以采用两种运行方式:自动方式和半自动/手动方式。
I/O模块是CPU与现场I/O装置或其它外部设备之间的连接部件。将外部输入信号
变换成CPU能接受的信号,或将CPU勺输出信号变换成需要的控制信号去驱动控制对象,
以确保整个系统正常工作
5.编程器
编程器适用于用户程序的编制、编辑、调试检查和监视,还可以通过其键盘去调用 和显示PLC的一些内部状态和系统参数。它通过通讯端口与CPU联系,完成人机对话连
接。
6.外部设备
一般PLC都配有盒式录音机、打印机、EPA写入器、高分辨率屏幕彩色图形监控系 统等外部设备。
2.1.2
PLC采用了一种不同于一般计算机的运行方式,即扫描方式。
1.工作过程
当PLC投入运行后,其工作过程一般分为三个阶段,即输入采样、用户程序执行 和输出刷新三个阶段,如下图所示。完成上述三个阶段称作一个扫描周期。在整个运行 期间,PLC的CPU以一定的扫描速度重复执行上述三个阶段。
采集模块,选用合适的变频器。
(2)控制室
由一台控制计算机(PC)以及打印机、组态软件等组成。上位PC接受PLC采集的信 息,对监控对象进行故障报警以及参数显示,向下属PLC发送控制信息。在本系统中,
它具有生产工艺流程图显示、电机启动停止控制、变频器工作状态显示、事故报警显示、 变频器运行参数设置和显示等功能。
整个配料混合系统由料仓、混合机、称重模块、电磁振动给料机、放料闸门等装置 及控制系统构成。控制系统采用PLC控制、上位机管理的方式设计。
(1)工业现场 工业现场包括驱动皮带的电动机,皮带秤秤体,称重传感器、控制电振给料机的变 频器,料斗料位传感器,各种电磁阀,西门子可编程控制器及其扩展模块等。
PLC采集电机、电磁阀、变频器等有关的控制对象的信息,经过对输入信息的处理, 反馈控制监控对象,将信息送入上一级监控机(上位机)。另一方面接受监控机(上位机)的控制指令,通过对输入和操作指令的分析、判断,进行综合处理,输出控制信号,控 制变频系统的工作,完成监控机对监控对象的实际控制。
1)输入采样阶段
在输入采样阶段,PLC以扫描方式依次读入所有输入状态和数据, 并将它们存入I/O映象区中的相应单元内。输入采样结束后,转入用户程序执行和输出刷新阶段。在这两 个阶段中,即使输入状态和数据发生变化,I/O映象区中相应单元的状态和数据也不会 改变。因此,如果输入是脉冲信号,则该脉冲信号的宽度必须大于一个扫描周期,才能 保证在任何情况下,该输入均能被读入。
图1-1系统控制流程图
1.2系统的基本功能监控功能:对皮带称配料过程的瞬时流量、日累计、月累计、年累计等参数进行检 测和监视;
画面显示:通过计算机显示器可显示配料过程中有关控制参数的运行状况,以及显 示实时配料曲线和表格;
通讯功能:工控机与PLC和仪表之间进行可进行双向数据及信息交换; 数据处理:配料系统可自动对采集的信号进行运算处理,并输出到相应的控制量; 控制功能:根据操作前相应的设定值,自动控制设备的正常运行,包括PID调节;
本系统中,实行一台变频器对一台电振给料机控制。用PLC输出的数字量信号作为 变频器的控制端输入信号,通过接受PLC的信号控制电机转速大小,并且向PLC反馈自 身工作状态信号;当发生故障时,向PLC及上位机发出报警信号。变频器对电振给料机
的控制具有完善的自我保护和电机保护功能
为了保证系统的可靠性,应采用较高性能的PLC选择合适的工业现场应用的数据
报警功能: 上位机以画面方式和声光信号方式对各种参数超限或设备状态异常进行 报警。
1.3
自动配料系统中, 设置上位机进行配料、 料流计量控制,建立配料模型, 统计打印, 下位机采用PLC进行皮带顺序控制、电磁振动给料机变频控制。皮带输送机用变频器驱 动控制,确保系统配料误差<0.5 %。配料系统由8条皮带秤配料线组成,8台皮带秤分 别编号为1#, 2#, 3#、4#、5#、6#、7#、8#,每台秤上分别输送不同的料。系统中每台 秤均由可编程控制器(PLC)和上位机(主机)实现两级控制。
图1-2系统结构示意图
第二章相关内容简介
2.1
2.1.1
PLC的实质是一种专用于工业控制的计算机,其硬件结构基本上是与微型计算机相 同的,如下图所示。
编程器
图2-1 PLC的结构
1.中央处理单元((CPU)
中央处理单元(CPU)是PLC的控制中枢。它按照PLC系统程序赋予的功能接收并存 储从编程器键入的用户程序和数据;检查电源、存储器、I/O以及警戒定时器的状态,
并能诊断用户程序中的语法错误。
2.存储器
存放系统软件的存储器称为系统程序存储器。存放应用软件的存储器称为用户程序 存储器。
3.电源
PLC的电源在整个系统中起着十分重要的作用。 一般交流电压波动在10%--15%范围 内,可以不采取其它措施而将PLC直接连接到交流电网上去。
4.输入输出元件(I/O模块)
2)用户程序执行阶段
在用户程序执行阶段,PLC总是按由上而下的顺序依次地扫描用户程序(梯形图)。 构成的控制线路,并按先 左后右、先上后下的顺序对由触点构成的控制线路进行逻辑运算,然后根据逻辑运算的
结果,刷新该逻辑线圈在系统RAM存储区中对应位的状态;或者刷新该输出线圈在I/O映象区中对应位的状态;或者确定是否要执行该梯形图所规定的特殊功能指令。即,在 用户程序执行过程中,只有输入点在I/O映象区内的状态和数据不会发生变化,而其他 输出点和软设备在I/O映象区或系统RAM存储区内的状态和数据都有可能发生变化,而