金安金沙江大桥正交异性桥面板U肋全熔透焊缝焊接工艺方案
金安金沙江大桥正交异性桥面板U肋全熔透焊缝焊接工艺方案

金安金沙江大桥正交异性桥面板U肋全熔透焊缝焊接工艺方案发表时间:2019-06-25T15:19:24.400Z 来源:《建筑学研究前沿》2019年4期作者:赵杰章黄[导读] 高频脉冲焊接+内焊技术的全熔透焊接工艺成熟稳定,可作为金沙江大桥U肋桥面板单元实际生产的工艺。
上海振华重工(集团)股份有限公司上海市 200125摘要:金安金沙江大桥是目前为止世界上最大跨径山区悬索桥,施工环境恶劣,结构施工工艺复杂,技术难度大,为确保工程质量及施工安全,项目团队克服重重困难,高效完成钢桥结构的制作与发运。
一、项目简介金安金沙江大桥是主桥主跨为1386米的双塔双索面单跨简支板桁结合加劲梁悬索桥,华坪岸边跨为跨径320米的无悬吊结构,丽江岸为跨径205米的无悬吊结构。
跨度为330+1386+205米,横向缆距27米,吊索顺桥向间距为10.8米。
二、编制目的1.为了充分验证金沙江大桥板单元U肋与顶板全熔透焊接工艺的可行性、方案的合理性、设备加工能力以及工装的适用性。
2.保证板单元U肋焊接批量化生产的稳定性。
3.根据试验结果确定金沙江项目板单元U肋板单元全熔透焊缝检测标准、探伤工艺、以及无损检测评判标准。
4.后续对检验结果进行分析、比对、总结,不断对板单元U肋焊接工艺方案进行完善。
三、U肋板试验板单元为验证板单元U肋与顶板全熔透焊接工艺的可行性,选取金安金沙江大桥项目中典型U肋桥面板单元作为U肋熔透焊试验,尺寸为2320*9500毫米的U肋板单元,包含4根9.5米长U肋进行3件试验。
四、焊接方案选择为选择合适的板单元U肋全熔透焊接方法,对各焊接方案进行比选,采用多种焊接材料、焊接气体、焊接角度、焊缝坡口,进行多种焊接方式组合的焊接工艺试验,择优选取焊接方案。
表4.1 U肋全熔透方案比选六、板单元U肋试制件制造工艺流程6.1 板单元U型肋制作板单元U肋采用常规数控切割机数控下料。
坡口采用机加工,两端螺栓孔需按中心线划线后机加工出孔。
钢桥U肋角焊缝全熔透焊接工艺
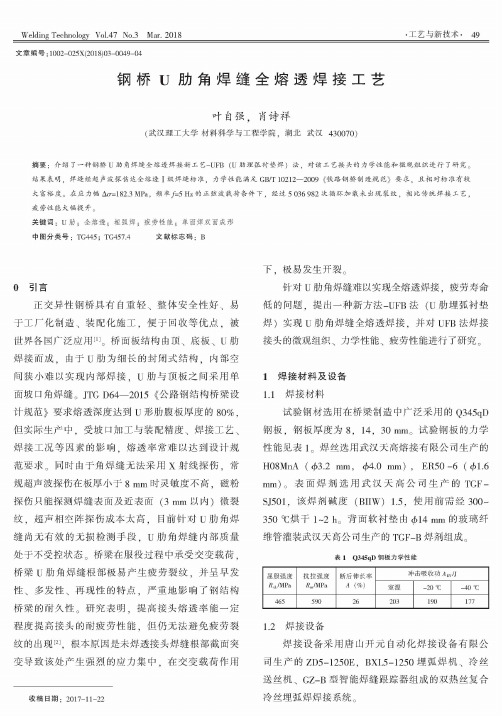
中 图 分 类 号 :TG445; TG457.4
文献标志码: B
0 引言
正交异性钢桥具有自重轻、整 体 安 全 性 好 、易
于 工 厂 化 制 造 、装 配 化 施 工 ,便 于 回 收 等 优 点 ,被
世 界 各 国 广 泛 应 用 [1]。桥 面 板 结 构 由 顶 、底 板 、 u 肋
焊 接 而 成 ,由 于 U 肋 为 细 长 的 封 闭 式 结 构 ,内部空
大 富 裕 度 。 在 应 力 幅 A! = 182.3MPa,频 率 / = 5 H z 的 正 弦 波 载 荷 条 件 下 , 经 过 5 0 3 6 9 8 2 次 循 环 加 载 未 出 现 裂 纹 ,相 比 传 统 焊 接 工 艺 ,
疲劳性能大幅提升。
ห้องสมุดไป่ตู้
关 键 词 :U 肋 ; 全 熔 透 ; 埋 弧 焊 ; 疲 劳 性 能 ; 单 面 焊 双 面 成 形
摘 要 :介 绍 了 一 种 钢 桥 U 肋 角 焊 缝 全 熔 透 焊 接 新 工 艺 -UFB ( U 肋 埋 弧 衬 垫 焊 # 法 , 对 该 工 艺 接 头 的 力 学 性 能 和 微 观 组 织 进 行 了 研 究 。
结 果 表 明 , 焊 缝 经 超 声 波 探 伤 达 全 熔 透 I 级 焊 缝 标 准 , 力 学 性 能 满 足 GB/T 10212— 2 0 0 9 《铁 路 钢 桥 制 造 规 范 》 要 求 , 且 相 对 标 准 有 较
1 焊接材料及设备 1 . 1 焊接材料
试 验 钢 材 选 用 在 桥 梁 制 造 中 广 泛 采 用 的 〇345qD 钢 板 ,钢 板 厚 度 为 8 ,14,30 mm。试 验 钢 板 的 力 学 性 能 见 表 1。焊丝选用武汉天高熔接有限公司生产的 H08MnA - "3.2 mm, "4.0 mm) , E R 50 -6 - "1.6 mm# 。 表 面 焊 剂 选 用 武 汉 天 高 公 司 生 产 的 T:F SJ5 0 1 ,该 焊 剂 碱 度 (BIIW) 1.5,使 用 前 需 经 3 0 0 ~ 350 Y 烘 干 1 ~ 2 h。背 面 软 衬 垫 由 "14 m m 的玻璃纤 维管灌装武汉天高公司生产的T G F -B 焊剂组成。
桥面板U肋焊接工艺探讨
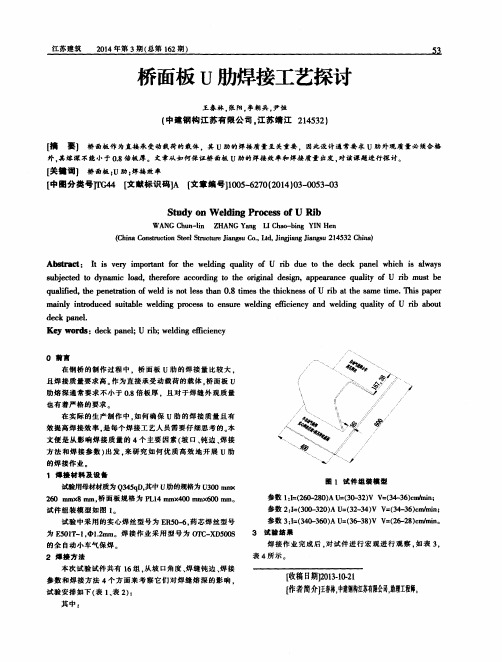
- - -
、 稳 \ ’ 。 、 、
ห้องสมุดไป่ตู้
}
, . ’ . 乇 ・
・
在实 际的生产制作 中 . 如何 确保 U肋 的焊接质量且 有
效提高焊接效 率。 是 每 个 焊 接工 艺人 员需 要 仔 细 思 考 的 。 本
文便是 从影响 焊接质量 的 4个 主要 因素 ( 坡口、 钝边 、 焊 接 方 法和焊接 参数 ) 出发 。 来研究 如何 优质 高效地 开展 U肋 的焊接作业 。
S t u d y o n We l d i n g Pr o c e s s o f U Ri b
W ANG C h u n - l i n Z HANG Ya n g L I C h a o - b i n g YI N He n
钢桥面板U肋焊缝抗疲劳设计及焊接新工艺

钢桥面板U 肋焊缝抗疲劳设计及焊接新工艺张华阮家顺沈俊杰黄超李立明乐凯宏(武船重型工程股份有限公司,武汉430415)摘要:针对U 肋与桥面板焊缝易产生疲劳开裂问题,结合相关研究成果,分析了焊缝尺寸对T 型接头角焊缝疲劳特性的影响,指出双面焊接条件下U 肋焊缝的尺寸要求,建议设计焊缝熔深不低于U 肋板厚的75%,焊脚尺寸不小于4mm 。
此外,提出了基于聚弧深熔气保焊的U 肋双面焊接新工艺,可大幅提高焊接工效,降低焊接成本。
关键词:U 肋焊缝;双面焊接;抗疲劳设计;聚弧深熔气保焊;焊接工艺DOI :10.13206/j.gjg201901016ANTI-FATIGUE DESIGN AND WELDING PROCESS OF U-RIB WELD OF STEEL BRIDGE DECKZHANG HuaRUAN JiashunSHEN JunjieHUANG ChaoLI LimingLE Kaihong(Wuchuan Heavy Engineering Co.Ltd ,Wuhan 430415,China )ABSTRACT :In view of the fatigue cracking problem of the weld of U-rib and steel bridge ,combined with the related research results ,the effect of weld size on the fatigue characteristics of T-joint fillet was analyzed.Therefore ,the size requirements of U-ribbed weld under the condition of double-sided welding were put forward.It was suggested that the design required that the weld penetration was no less than 75%of U-ribbed plate thickness and the size of welding foot was no less than 4mm.In addition ,a new U-rib double-sided welding process based on poly-arc deep-melt gas-shielded welding was proposed ,which could avoid welding groove ,greatly improve welding efficiency and reduce welding cost.KEY WORDS :U-rib weld ;double-sided welding ;anti-fatigue design ;poly-arc deep-melt gas-shielded welding ;welding process第一作者:张华,男,1981年出生,硕士,高级工程师。
《2024年正交异性钢桥面板焊接工艺参数研究》范文
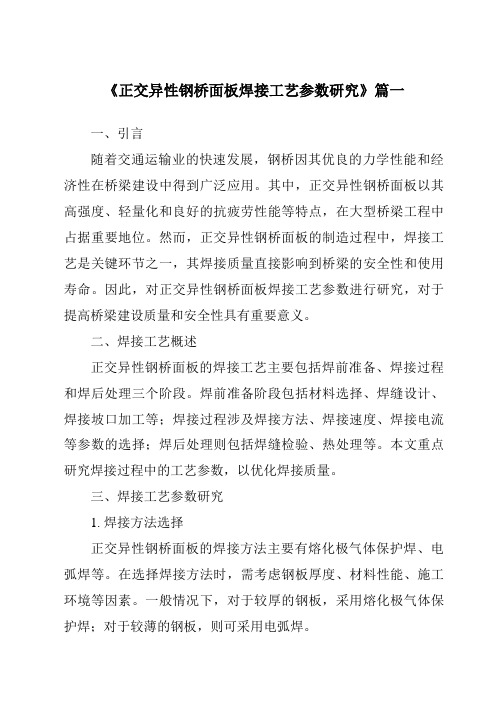
《正交异性钢桥面板焊接工艺参数研究》篇一一、引言随着交通运输业的快速发展,钢桥因其优良的力学性能和经济性在桥梁建设中得到广泛应用。
其中,正交异性钢桥面板以其高强度、轻量化和良好的抗疲劳性能等特点,在大型桥梁工程中占据重要地位。
然而,正交异性钢桥面板的制造过程中,焊接工艺是关键环节之一,其焊接质量直接影响到桥梁的安全性和使用寿命。
因此,对正交异性钢桥面板焊接工艺参数进行研究,对于提高桥梁建设质量和安全性具有重要意义。
二、焊接工艺概述正交异性钢桥面板的焊接工艺主要包括焊前准备、焊接过程和焊后处理三个阶段。
焊前准备阶段包括材料选择、焊缝设计、焊接坡口加工等;焊接过程涉及焊接方法、焊接速度、焊接电流等参数的选择;焊后处理则包括焊缝检验、热处理等。
本文重点研究焊接过程中的工艺参数,以优化焊接质量。
三、焊接工艺参数研究1. 焊接方法选择正交异性钢桥面板的焊接方法主要有熔化极气体保护焊、电弧焊等。
在选择焊接方法时,需考虑钢板厚度、材料性能、施工环境等因素。
一般情况下,对于较厚的钢板,采用熔化极气体保护焊;对于较薄的钢板,则可采用电弧焊。
2. 焊接电流与电压焊接电流和电压是影响焊接质量的关键参数。
电流过大或过小都会导致焊缝成形不良,电压过高或过低则会影响电弧的稳定性。
因此,在焊接过程中,需根据钢板厚度、材料性能等因素,合理选择焊接电流和电压。
3. 焊接速度焊接速度直接影响焊缝的冷却速度和热输入量。
焊接速度过快,会导致焊缝未完全熔合,降低焊缝强度;焊接速度过慢,则会导致焊缝过热,产生热裂纹等问题。
因此,在保证焊缝质量的前提下,应选择合适的焊接速度。
4. 坡口角度与间隙坡口角度和间隙的大小直接影响焊缝的成形和质量。
坡口角度过大或过小都会导致焊缝成形不良,间隙过大则会导致焊缝填充不饱满,间隙过小则会增加焊接难度。
因此,在焊前准备阶段,需根据钢板厚度和材料性能等因素,合理设计坡口角度和间隙。
四、实验研究为研究正交异性钢桥面板的焊接工艺参数,我们进行了系列实验。
新型抗疲劳正交异性钢桥面板U肋双面组焊修施工工法(2)

新型抗疲劳正交异性钢桥面板U肋双面组焊修施工工法新型抗疲劳正交异性钢桥面板U肋双面组焊修施工工法一、前言随着交通运输的快速发展,桥梁的使用频率也在不断增加。
为了确保桥梁的可靠性和安全性,在桥梁建设中需要使用高质量的桥面板。
新型抗疲劳正交异性钢桥面板U肋双面组焊修施工工法应运而生,其具有高强度、抗疲劳性好等优点,能够提高桥梁的使用寿命和承载能力。
二、工法特点该工法采用新型抗疲劳正交异性钢桥面板,通过U肋双面组焊修施工工法进行安装。
以下是该工法的特点:1. 高强度:新型抗疲劳正交异性钢桥面板具有较高的强度和刚度,能够提高桥梁的承载能力。
2. 抗疲劳性好:钢桥面板采用了特殊工艺和材料,具有良好的抗疲劳性能,降低了桥梁的维修频率。
3. 施工简便:U肋双面组焊修施工工法采用了现代化的焊接技术,施工简单方便,高效率。
4. 长寿命:因为采用了高质量的材料和专业的施工工法,所以新型抗疲劳正交异性钢桥面板具有较长的使用寿命。
三、适应范围该工法适用于各类桥梁的建设和维修,可以满足各种不同类型和规模的桥梁项目的需求。
四、工艺原理该工法通过对施工工法与实际工程之间的联系、采取的技术措施进行分析和解释,让读者了解该工法的理论依据和实际应用。
五、施工工艺该工法的施工过程分为以下几个阶段:1.准备工作:包括现场测量,材料准备,机具设备的布置等。
2. 钢桥面板安装:将钢桥面板安装在桥梁上,通过U肋双面组焊修施工工法进行焊接连接。
3. 焊接工艺控制:对焊接参数进行控制,确保焊接质量。
4. 检验与验收:对焊接质量进行检验与验收,包括焊缝的无损检测、外观检查等。
六、劳动组织该工法涉及到焊接工人、吊装工、检验员等多个工种,需要合理安排劳动组织,提高施工效率。
七、机具设备该工法所需的机具设备包括焊接机、起重机、角磨机等。
这些机具设备具有良好的性能和使用方法,能够满足施工的需要。
八、质量控制为了确保施工过程中的质量达到设计要求,该工法采取了多项质量控制措施,包括焊接过程的参数控制,焊缝的无损检测等。
公路桥梁正交异性钢桥面板U肋双面焊接技术指南T∕CHTS 10029-2020

T/CHTS 1 0029一 2020
2 术语和符号
2.1 术 语
2.1 .I U肋双面焊接 U一rib double-sided welding 在 U肋与桥面板连接处均实施 内、外侧焊接的双 面 焊缝连接。
2. .2 无定位焊装配 fixing position and assembly system onu 一r ib and bridge deck welding connec-
T/CHTS 1 0029一 2020
公路桥梁正交异性钢桥面板 U肋来自面焊接技术指 南总则 0.1 为规 范公 路桥 梁正 交异性 钢桥 面板 U 肋 双 面焊接技 术 ,制定 本指南 。 0.2 本指 南适 用于公 路桥 梁正 交异 性钢桥 面板 U 肋 的双面焊 接 。 0.3 除应符 合本 指南 外 ,尚应符 合有 关法 律 、法 规及 国家 、行业 现行 有关 标准 的规 定 。
T/CHTS 1 0029一 2020
目次
总则 2 术语和符号
术语 2.2 符 号 3 基本规定 ······························,·······································,··································…… 3 3.1 一般规定 ···································································································…… 3 3.2 焊接材料 ·······················································································....···.....…… 3 3.3 焊缝形式 ···································································································…… 3 4 焊接工艺评定 ·································································································..…… 5 4.1 一般要求 ················································,··················································…… 5 4.2 试件要求 ···································································································…… 5 4.3 试件检验 ···································································································…… 5 5 组装及焊接 ·····························,······································································..…… 6 5.1 组装 ······································································································...…… 6 5.2 焊接环境 ·····················……,·····················································,·················…… 6 5.3 焊接工艺 ···································································································…… 6 5.4 返修 ·········································································································…… 7 6 焊接质量检验 ···································································································…… 8 6.1 一般规定.,’·································································································…… 8 6.2 焊缝外观检验 ························,····································································…… 8 6.3 质量要求 ·····································……t’·····················································…… 8 附录 A U肋部分熔透焊缝超声波相控阵检测 ····························································…… 01 用词说明 ············································································································…… n
正交异性桥面板单元焊接工艺及变形控制
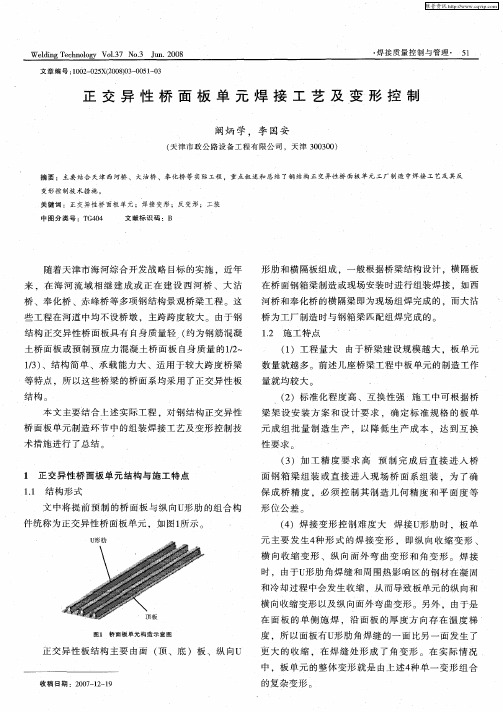
量就 均较 大 。 ( )标准 化 程度 高 、互 换 性强 施 工 中可 根 据桥 2
梁架 设 安装 方 案 和设 计 要 求 ,确 定 标 准 规 格 的板 单
元 成 组批 量 制 造 生 产 ,以降 低 生 产 成 本 ,达 到 互 换
性 要 求
( )加 工 精 度 要 求 高 预 制 完 成 后 直 接 进 入 桥 3
( )工程 量 大 由于桥 梁建 设 规模 越 大 ,板 单元 1
数量 就越 多 。前述 几座 桥梁 工程 中板 单元 的制造 工作
等 特点 ,所 以这 些桥梁 的桥面 系均 采用 了正 交异 性板
结构 。 本 文主要 结 合上 述实 际工程 ,对钢 结构 正交 异性 桥面 板单 元制 造环 节 中的组 装焊 接 工艺及 变形 控制 技 术措 施进 行 了总结 。
形 肋 和横 隔板 组成 ,一 般根据 桥梁 结构 设计 ,横 隔板
在桥 面钢 箱梁 制造 或现 场安装 时进 行组 装焊 接 ,如西 河 桥 和奉化 桥 的横 隔梁 即为现 场组 焊完 成 的 ,而 大沽
桥 为 工厂 制造 时与钢 箱 梁匹配 组 焊完成 的 。 12 施 工 特点 . ’
量 。反 变 形 量 借 鉴 以往 各 类 型单 元 件 的变 形 统 计 数 据 ,通过 理论 计算 并根 据工 程 的试验 结果 进行 归纳 确
板单 元 的制作工 艺 流程 如 图2 所示 。
定 。该装 置 可实现 机械 液压 动力 ,解 决 了人力 施压 预
变形 不均 匀 的难题 ,为单 元件 制造 中焊 接变形 的控制
维普资讯
w ln no o 7N. u.08 ei T hog V1 o J 20 d g e ly . 3 3 n
板单元u形肋角焊缝全熔透焊接技术研究
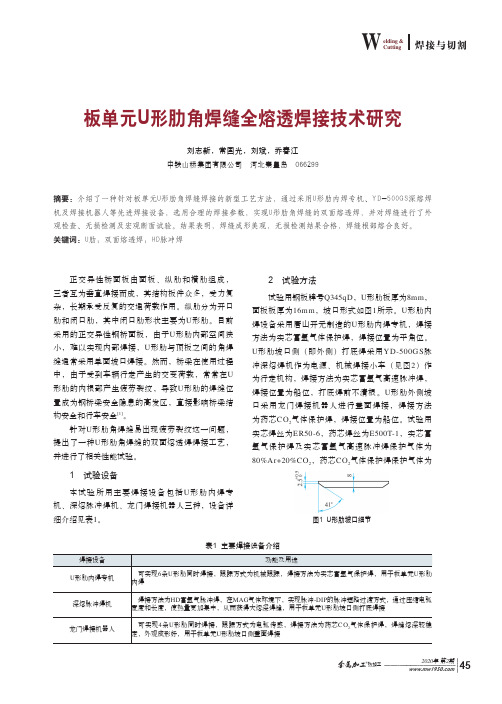
图1 U形肋坡口细节功能及用途形肋同时焊接,跟踪方式为机械跟踪,焊接方法为实芯富氩气保护焊,用于板单元图2 HCD500-6机械焊接小车试验过程3.1 组装组装前将U形肋坡口两侧30mm范围内的铁锈、油污等清除干净,并打磨至露出金属光泽,采用形肋组装机器人在U形肋坡口侧进行定位焊,定位焊长度为50~100mm,间距400~600mm,组装间隙0~0.5mm内。
3.2 焊接1)U形肋内角焊缝的焊接采用U形肋内焊专U形肋角焊缝的内部焊接(见图3),焊接参2。
为防止焊漏,调整焊丝边缘与角焊缝根部形肋坡口侧盖面焊焊接参数熔敷简图焊接电流/A电弧电压/V焊接速度/cm·min-1摆幅/mm摆动频率/次·min-1气体流量/L·min-1注:盖面焊接时,焊枪前倾角注:为了保证熔透,焊丝扎丝位置偏表2 U形肋内角焊缝焊接参数熔敷简图焊接电流/A电弧电压/V焊接速度/cm·min-1焊枪与水平面倾角/(°)260284840a)U形肋角焊缝内部焊接 b)内角焊坡口侧焊接效果图3 U形肋内角焊(3)U肋坡口侧盖面焊U形肋坡口侧盖面焊,焊接参数见表4 试验结果a)U形肋内角焊缝外观 b)U形肋外侧角焊缝外观图4 U形肋角焊缝焊缝外观4.2 焊缝无损检测试验焊后24h进行相控阵超声波检测,检测结果为合格。
4.3 U形肋角焊缝宏观断面U形肋角焊缝宏观断面如图5所示,从图5中可以看出,U形肋角焊缝已实现熔透焊接,焊缝根部熔合良好。
a)内角焊缝 b)外侧角焊缝图5 U形肋熔透角焊缝宏观断面5 结束语通过采用板单元U形肋内焊+外焊的方式,实现。
钢桥面板U肋角焊缝全熔透焊接工艺研究

Welding & Cutting
钢桥面板U肋角焊缝全熔透焊接工艺研究
裴雪峰,车平,冯辉 中铁宝桥集团有限公司 陕西宝鸡 721006
摘要:随着U肋内焊设备的研发和对钢桥面板抗疲劳性能要求的不断提高,U肋角焊缝要求从单面部分熔透焊 接逐渐发展到双面全熔透焊接。通过U肋角焊缝双面全熔透焊接工艺试验研究,结合深中通道项目的实桥应用 情况,对板单元U肋角焊缝全熔透焊接工艺进行了研究,并就一些相关问题提出了建议。 关键词:钢桥面板;U肋角焊缝;全熔透焊接;工艺研究
U肋实体模型
每块试件 试件数量
焊缝长度 /m
/块
焊接 方法
熔透合格率 (%)
90
5
双面埋 弧焊
76.4~88.8
双面埋
90
5
弧焊 90.6~96.4
双面埋
90
3
弧焊 97.3~99.1
表4 U肋角焊缝全熔透试验焊接参数
焊接 部位
焊接材料
焊接电流 电弧电压 焊接速度 焊接
与规格
/mm
/A
/V /mm·min-1 位置 备注
SU35、 U肋全熔 φ1.6 透角焊缝 SU35、
φ 3.2
380±30 640±30
32±2 32±2
400±40
横位
内侧 焊缝
480±40
船位
外侧 焊缝
4 U肋全熔透焊接工艺的应用
深中通道是集“桥、岛、隧、水下互通”于一 体的世界级跨海通道工程,制造标准高。项目主体 工程全长约24.03km,跨海长度22.39km,陆域段 长度1.64km,其中桥梁工程全长约17km,钢箱梁 总量约28万t,公司参与制造的伶仃洋大桥钢箱梁 (1/2)及西泄洪区非通航孔桥钢箱梁,工程量约 9.11万t,设计明确要求钢桥面板U肋角焊缝采用全 熔透焊接。
桥面板复合钢板对接焊缝与u肋t接焊缝无损检测技术规程

桥面板复合钢板对接焊缝与u肋t接焊缝无损检测技术规程全文共四篇示例,供读者参考第一篇示例:一、技术背景随着桥梁建设规模的不断扩大和桥梁结构的复杂化,桥梁结构的安全性和可靠性越来越受到人们的重视。
桥面板复合钢板对接焊缝和U肋T接焊缝的质量直接影响到桥梁结构的承载能力和使用寿命。
对这些焊缝的无损检测技术要求越来越高。
二、技术要求1.焊缝类型桥面板复合钢板对接焊缝和U肋T接焊缝是桥梁结构中常见的焊缝类型。
这些焊缝一般由工字焊、焊接槽以及焊缝堆焊等焊接工艺组成。
在焊接过程中,要保证焊缝的质量达到要求。
2.检测原则无损检测技术是指在不破坏焊缝本身的情况下,通过检测仪器对焊缝进行检测,以发现焊缝中的缺陷或安全隐患。
检测原则应该是全面、细致、准确、可靠。
3.检测方法目前,常见的无损检测方法主要包括超声波检测、X射线检测、涡流检测、磁粉检测等。
根据不同的焊缝类型和检测要求,选择合适的检测方法进行检测。
4.检测仪器为了保证无损检测的准确性和可靠性,选择合适的检测仪器也是非常重要的。
要根据具体的检测需求和焊缝的特点选用合适的仪器,并严格按照相应规程操作。
5.检测结果评定根据检测结果,评定焊缝的质量等级,并及时采取相应的措施进行修复或更换。
三、技术规程1.检测前准备在进行无损检测之前,需要做好以下准备工作:(1)准备好相应的检测仪器和设备;(2)对检测人员进行培训,确保其熟悉检测仪器和操作流程;(3)进行现场勘查,了解焊缝的具体情况和要求。
(1)选择合适的检测方法和仪器,根据具体情况确定检测的范围和方式;(2)按照操作规程进行检测,确保检测的全面性和准确性;(3)记录检测结果,并评定焊缝的质量等级。
四、总结无损检测技术在桥面板复合钢板对接焊缝和U肋T接焊缝中的应用,能够有效地发现焊缝中的缺陷和安全隐患,保证桥梁结构的安全性和可靠性。
在桥梁建设中,对这些焊缝的无损检测技术应该得到充分的重视和应用。
第二篇示例:一、前言桥面板复合钢板是桥梁结构中常见的构件,其对接焊缝与u肋t接焊缝质量直接关系到桥梁的安全和使用寿命。
- 1、下载文档前请自行甄别文档内容的完整性,平台不提供额外的编辑、内容补充、找答案等附加服务。
- 2、"仅部分预览"的文档,不可在线预览部分如存在完整性等问题,可反馈申请退款(可完整预览的文档不适用该条件!)。
- 3、如文档侵犯您的权益,请联系客服反馈,我们会尽快为您处理(人工客服工作时间:9:00-18:30)。
金安金沙江大桥正交异性桥面板U肋全熔透焊缝焊接工艺方
案
摘要:金安金沙江大桥是目前为止世界上最大跨径山区悬索桥,施工环境恶劣,结构施工工艺复杂,技术难度大,为确保工程质量及施工安全,项目团队克服重
重困难,高效完成钢桥结构的制作与发运。
一、项目简介
金安金沙江大桥是主桥主跨为1386米的双塔双索面单跨简支板桁结合加劲
梁悬索桥,华坪岸边跨为跨径320米的无悬吊结构,丽江岸为跨径205米的无悬
吊结构。
跨度为330+1386+205米,横向缆距27米,吊索顺桥向间距为10.8米。
二、编制目的
1.为了充分验证金沙江大桥板单元U肋与顶板全熔透焊接工艺的可行性、方
案的合理性、设备加工能力以及工装的适用性。
2.保证板单元U肋焊接批量化生产的稳定性。
3.根据试验结果确定金沙江项目板单元U肋板单元全熔透焊缝检测标准、探
伤工艺、以及无损检测评判标准。
4.后续对检验结果进行分析、比对、总结,不断对板单元U肋焊接工艺方案
进行完善。
三、U肋板试验板单元
为验证板单元U肋与顶板全熔透焊接工艺的可行性,选取金安金沙江大桥项
目中典型U肋桥面板单元作为U肋熔透焊试验,尺寸为2320*9500毫米的U肋
板单元,包含4根9.5米长U肋进行3件试验。
四、焊接方案选择
为选择合适的板单元U肋全熔透焊接方法,对各焊接方案进行比选,采用多
种焊接材料、焊接气体、焊接角度、焊缝坡口,进行多种焊接方式组合的焊接工
艺试验,择优选取焊接方案。
表4.1 U肋全熔透方案比选
六、板单元U肋试制件制造工艺流程
6.1 板单元U型肋制作
板单元U肋采用常规数控切割机数控下料。
坡口采用机加工,两端螺栓孔需
按中心线划线后机加工出孔。
长度允许偏差:±2.0毫米,宽度允许偏差:±2.0毫米。
6.2 桥面板划线
(1)在试验件顶板上划出纵、横向基准线,基线两端各打三个样冲眼。
根
据基线及纵向U形肋图纸定位尺寸,顶、底板拼接组装间隙和焊接收缩量,划出
纵向U肋装配线。
6.3 U肋装配
(1)将顶板置于无码组装胎架上,根据纵基线控制纵基线与横向限位挡的
距离,用夹紧装置固定顶板,复测纵基线与横向限位挡的距离,合格后方可进行
后续工作。
(2)组装U肋板:以U肋板装配线为基准用无码组装胎架组装U肋板,组
装时需要注意的事项如下:
① 每块板单元组装完成后必须严格检查U肋板的各个定位尺寸。
合格后方
可进行后续工作。
② 组装后,在醒目位置按照要求标注相关标识,确保唯一性,方便后续跟踪。
③ 距端部30毫米以内不进行定位焊,焊缝长70毫米,每道定位焊间隔为500毫米,U肋定位焊焊缝厚度3~4毫米,装配间隙≤0.5毫米。
6.4 U肋内焊
板单元U肋内侧焊缝采用U肋内焊专机进行焊接,焊前调节焊丝角度,保证
内侧焊丝与底板夹角30~45°调节。
6.5 板单元U肋外侧焊接打底
板单元U肋外侧焊缝打底时使用聚弧深熔焊焊接设备,采用金属粉芯焊丝进
行焊接。
焊前需检查聚弧深熔焊设备,确保稳定焊接。
焊接时需注意焊丝与顶板
角度以及胎架角度,胎架角度30°,焊枪与底板夹角30~45°调节。
6.6 板单元U肋外侧焊接盖面
板单元U肋外侧焊缝盖面时使用U肋焊接机器人进行焊接,采用金属粉芯焊
丝进行焊接,焊接胎架角度30°。
6.7 板单元校正
板单元U肋试验板单元矫正前,需测量试验板单元焊接横向收缩及纵向收缩,并准确记录数据。
(1)构件应根据变形情况采用冷矫或热矫对其进行修整矫正。
(2)修整不得使构件表面产生凹痕或其它损伤。
(3)火攻矫正时应监控加热温度,一般应控制在600℃以下,严禁过烧,不
宜在同一区域内多次反复加热。
对于矫正温度需超过600℃时应根据试验结果控
制矫正温度上限不得超过800℃。
(4)加热后应缓慢冷却,不得用水急冷;在室温下局部修整采用锤击时,
需加垫板。
(5)矫正后的构件应放在平台上检查。
七、检验检测方法、比例、范围及验收要求
7.1焊缝质量验收等级
U肋全熔透焊缝的质量等级定为Ⅱ级。
7.2板单元检验批次的划分及验收
单个工程应将板单元分为:首制件检验批和批量制造检验批。
首制件检验批,按5块板单元为一个批次。
批量制造检验批,按10块板单元为一个批次。
7.3焊缝外观检验要求
7.3.1检验数量:全部板单元。
7.3.2检验范围:内侧焊缝检测两端各1000毫米范围,对断丝、熄弧等可疑
部位应采用内窥镜等摄像设备辅助检查;外侧焊缝全长。
7.3.3检验时机:待焊缝温度降至室温后,进行VT检验。
7.3.4检验方法:目视检测、内窥镜等摄像设备。
7.3.5验收要求:按《公路桥涵施工技术规范》JTG/T F50-2011中第19.6.1
项第1条款执行。
7.4焊缝表面及近表面检测要求
7.4.1检测比例:
① 首制件制造(前5个板单元):全部板单元100%检测,每条外侧焊缝两端各1000毫米;
② 批量制造:板单元数量的10%。
7.4.2检测范围:每条外侧焊缝两端各1000毫米。
7.4.3检测时机:焊缝经100%VT合格后。
7.4.4检测方法:磁粉检测,应符合《焊缝无损检测磁粉检测》GB/T 26951-2011的规定。
7.4.5焊缝验收:应达到《焊缝无损检测焊缝磁粉检测验收等级》GB/T 26952-2011中2X级的规定。
7.5焊缝内部缺陷检测要求
7.5.1检测比例:
① 首制件制造(前5个板单元):每块板单元每条焊缝全长100%;
② 批量制造:每批次板单元数量的10%。
抽检板单元U型肋两侧的焊缝至少各一条,且抽检焊缝条数占全部焊缝条数的比例不<30%,不足一条按一条计。
抽检板单元平均一条焊缝不合格缺陷达到3处时,增加一块板单元检测。
7.5.2检测范围:
①整条焊缝(螺栓孔范围除外);
②外观检查时发现未焊满、断弧、电弧跑偏等需100%检测,且两端各延长100毫米,不受检验批次限制;
③螺栓孔范围仅做顶板侧检测。
7.5.3检测时机:焊缝经100%VT合格后
7.5.4检测方法:超声检测
①按相关规范进行检验。
②按《公路桥涵施工技术规范》JTG/T F50-2011中表F2.0.1 全熔透焊缝设置波幅曲线灵敏度。
7.5.5焊缝缺陷评定
①焊缝熔透为合格。
②单个缺陷长度≤100毫米时判定为合格。
③缺陷累计指示长度在任意的焊缝长度lw(lw=1000毫米)范围内不超过20%时,可判定本评定区域焊缝合格。
缺陷累计指示长度是指所有单独的可验收显示在每条焊缝长度范围内单个缺陷指示长度之和。
④裂纹危害性缺陷,判断为不合格。
7.6返修后的检测
所有修复后的焊缝按照原检测方法进行复验,并在返修部位两端各增加100毫米检测。
7.7批量生产条件
① 首制件每块焊缝全熔透长度占焊缝全长的96%时,方可进入批量制造阶段。
② 首制件首个检验批不合格,但在分析原因并采取有效措施,在第二个首制件检验批检验合格,也可进入批量生产。
③ 如首制件第二检验批不合格,应停产整顿,重新制定施工方案。
④ 当设备或工艺发生重大调整时,或者一个批次的超过3个板单元不合格应重启首制件检验批的检验要求。
八、U肋全熔透焊缝工艺指导文件
对实际工况进行了焊评试验,根据焊接工艺焊评结果,编制相应的焊接工艺文件,用于指导批量生产。
九、返修工艺
板单元U肋焊缝缺陷超出验收要求规定的上限值,需要采用专项返修方案进行返修,板单元U肋坡口缺陷及焊接缺陷的清除范围除应包括缺陷全长外,还应由此缺陷两端各外延。
1010.2 宏观腐蚀试样
为进一步查看焊缝质量情况,针对装配定位焊及易产生缺陷部位进行取样,通过宏观金相腐蚀,确认该部位是否存在缺陷及类型。
从宏观腐蚀结果得出,U肋熔深均能满足标准要求,且不存在缺陷。
10.3 综合总结:
1.采用该U肋全熔透焊接工艺,全尺寸板单元试验探伤合格率不低于96%,极大的提升了U肋桥面板单元的疲劳性能,解决了焊接熔深控制的行业难题;
2.高频脉冲焊接+内焊技术的全熔透焊接工艺成熟稳定,可作为金沙江大桥U 肋桥面板单元实际生产的工艺。
参考文献
1.刘斌马健汪磊陈军刚陈孔令《云南金安金沙江大桥总体设计》云南省交通规划设计研究院,云南昆明,650041,页码:P82—P87
2.马立芬杨春松《钢箱梁U肋角焊缝全熔透焊接技术探究》上海振华重工(集团)股份有限公司上海 200125,页码:P89—P92。