供应商评估表(图表记录)
IATF16949供应商评估表
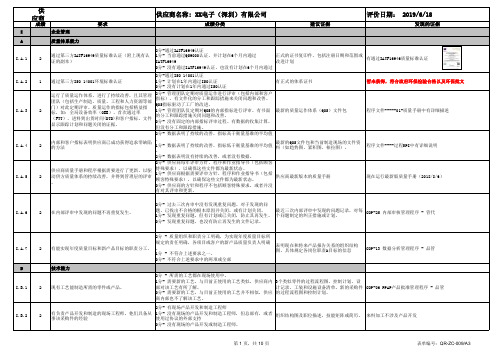
有正式的体系证书
暂未获得,符合政府环保检验合格以及环保批文
2
运行了质量运作体系,进行了持续改善,且其管理 团队(包括生产制造、质量、工程和人力资源等部 门)对此定期评审。质量运作的指标包括精益指 标,如:全局设备效率(OEE)、首次通过率 (FTT)、进料到出货时间(DTD)和客户指标。文件 显示跟踪计划和问题关闭的证据。
过程评审,样件进度和交付信息,评估新方 法或有竞争力方法的证据资料。类似产品或 过程的能力指数百分比/检测点满意公差百 分比数据。样件控制计划与生产控制计划对 比。
COP-40 新产品制作管理程序
管理能力
2分- 组织机构图职责明确,核心人员的平均工作时间至少
2年。
2
供应商有组织结构图,结构图上标识了关键人员、 1分- 组织机构图职责明确,核心人员的平均工作时间大于 组织机构图、书面的职责分工、各岗位的平
I.F.1
2 物料计划&物流部门全天侯可联系。
2分 - 明确地规定了全天侯的沟通要求,以协调生产和发 运计划 1分 - 有联系人协调生产和发运计划 0分- 没有联系人协调生产和发运计划
明确规定了各班次的联系人姓名、职务和电 话号码。周末发生紧急情况时,也有联系人 和电话。
G I.G.1 I.G.2
分供应方的管理
外部测试资源清单和先前测试的示例,供应
商设施鉴定报告。当前的测试范围与采购计 划所需的对照,试验进度、按计划执行情况
COP-04 MSA量测系统管制程序
和设施的评审。
2
样件为现有生产工艺生产和具代表性零件的产量。 使用最新的方法和模具去生产样件
2分 - 样件生产过程与生产件的一样,正在自行开发或与 合作伙伴一起开发最有效的样件制造方法。 1分 - 样件代表量产,但是工艺不同。正在使用有效的样 件制造方法,但不积极追求效率。 0分- 样件不能代表量产,方式陈旧、无效,或者存在质量 或时间方面的问题
供应商现场评估表
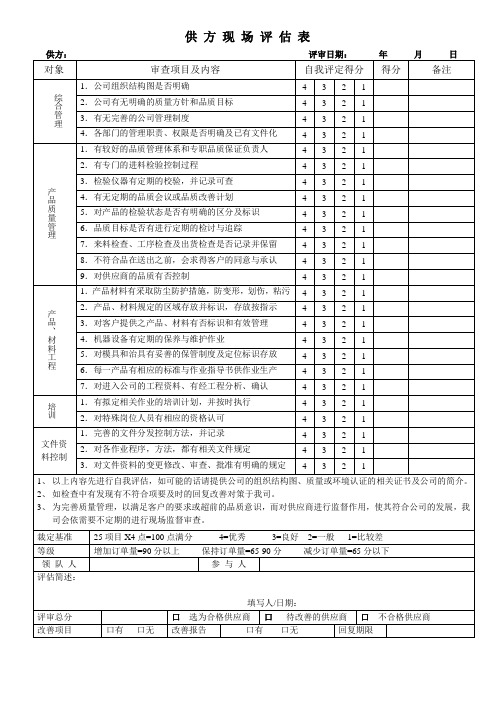
供方:评审日期:年月日
对象
审查项目及内容
自我评定得分
得分
备注
综合管理
1.公司组织结构图是否明确
4
3
2
1
2.公司有无明确的质量方针和品质目标
4
3
2
1
3.有无完善的公司管理制度
4
3
2
1
4.各部门的管理职责、权限是否明确及已有文件化
4
3
2
1
产品质量管理
1.有较好的品质管理体系和专职品质保证负责人
裁定基准
25项目X4点=100点满分4=优秀3=良好2=一般1=比较差
等级
增加订单量=90分以上保持订单量=65-90分减少订单量=65分以下
领队人
参与人
评估简述:
填写人/日期:
评审总分
口选为合格供应商
口待改善的供应商
口不合格供应商
改善项目
口有口无
改善报告
口有口无
回复期限
4
3
2
1
3.对文件资料的变更修改、审查、批准有明确的规定
4
3
2
1
1、以上内容先进行自我评估,如可能的话请提供公司的组织结构图、质量或环境认证的相关证书及公司的简介。
2、如检查中有发现有不符合项要及时的回复改善对策于我司。
3、为完善质量管理,以满足客户的要求或超前的品质意识,而对供应商进行监督作用,使其符合公司的发展,我司会依需要不定期的进行现场监督审查。
4
3
2
1
2.有专门的进料检验控制过程
4
3
2
1
3.检验仪器有定期的校验,并记录可查
4
供应商质量评估

成绩 Level for Element 3 SCORE 1: ☐ 没有计划,管理者不支持任何计划 SCORE 2: ☐ 如果预算和时间允许有部分培训. ☐ 没有培训计划文件 ☐ 一些经理开始承认业务/质量方面的培训的必要. ☐ 公司内部存在一个正是的培训体系 ☐ 培训仅限于基础的技术方面 ☐ 新员工的培训和转换存在于某些业务领域 ☐ 管理者对于质量和流程管理提高的培训有一个全面地了解. SCORE 3: ☐ 公司的主要业务领域-统计分析和解决方案有一个合理的的培训计划 ☐ 管理者要求整个公司有年度培训计划 ☐ 多数员工接受与其工作相关的能力提高的培训 ☐ 培训计划与业务和 质量目标紧密相联. ☐ 培训计划应以文件形式存在包括新进员工和工程流动人员和经理级人员等 SCORE 4: ☐ 有余公司整体目标紧密相关的完善的质量培训标识/项目 ☐ 全课程的完整培训记录包含在培训计划之内,设计公司的各个领域 ☐ 所有雇员都接受了广泛的培训包括个人的需要和发展 ☐ 各个层次的管理者都应定期的对培训计划进行回顾合总结 ☐ 为支持战略性的计划已经建立了绩效考核训练 ☐ 所有使党员共接受过相关提能力提高训练 SCORE 5: ☐ 战略目标和个人发展需要推动所有层次的培训,而且与客户满意目标相吻合 ☐ 在完成业务和客户满意基础者上的培训效果衡量标准已经很明显的起了积极作用。 4.新产品/加工/技术/服务发展方针和程序是否存在,它们是否被明确的定义在项目计划 中,并附有合适的说明和批准确认?
5 of 25
注意事项: a. 有方针和程序存在,这些方针和政策定义好工作的最低要求,适当的资源和发展的期 望,且包括介绍和生产新产品、新设计/改进的设计的过程、技术和服务等。这些政策 方针和过程还要定义好执行过程中的责权。 b. 合格的人员配备,人员要求有充分的智慧足以被指派到任何一个项目中 c. 现存的政策方针和程序要保证新产品、新技术和新服务等能够适应所建立的业绩目 标,包括周期目标和测量和先期导入。 d. 这些政策和程序要求有适合的管理可视性,要求确认批准要优先考虑新产品/新设计/新 更改的重要的工序/新技术和新产品服务。 e. 组织要适应新产品/新设计/新更改的重要的工序/新技术和新产品服务。 Performance Level for Element 4 元素 4 的执行水平评分 SCORE 1: 1 分: 企业根本没有新产品/工序/技术/服务发展的政策方针和程序存在。 SCORE 2: 2 分: ☐ 有一些非正式的程序存在,但是文档不完全,配合不协调。 ☐ 有些业务领域开始意识到有建立更高纪律性改变的必要。 ☐ 一些政策方针和程序存在,而且有一些主要的领域正在执行,但是,其中的一些政 策方针缺乏合适的可测量的要求。 ☐ 管理可视性和确认批准存在不一致性。 ☐ 有一些成功的项目案例,包括计划新产品、新工序、新技术或服务发展项目中定义 好合格的人员执行的职责分别是什么。 SCORE 3:3 分 ☐ 有健全的政策和流程已经由组织的关键部门安排好并建档。 ☐ 这些现存的政策要求有清晰完整的项目计划并用合适的措施归档管理,各负其责。 ☐ 这些政策和流程要求所有人员都足能胜任这些项目。 ☐ 管理确认在适当的位置是个必要条件。最关键的业务领域要符合现存的政策和程 序。 SCORE 4: 4 分: ☐ 所有适当的业务领域都有设计得很好的政策和程序存在, ☐ 这些文档要求,整个项目的计划和转折点都被证明适合所有新产品/工序/技术/服务 发展项目。 ☐ 这些文档还要求“失败模式影响分析”(FMEA’S)的发展要适合所有新产品/新改 变的重要工序,同时清楚说明执行要求的最低限度。 ☐ 适合的管理确认要融入这个过程 ☐ 要求有证据能够证明所有的新产品/工序/技术/服务项目都能够适应这个组织的政策 和流程。 ☐ 管理要确保对于这些成文的要求全力支持和先行做到。 SCORE 5: 5 分: ☐ 政策方针和程序都被很完整的说明并成文,并且都根据不同客户的特殊要求专门制 定。 ☐ 如何使这些流程更好的适用于各个项目被很完整的设计好。
采购年终总结图表分析

采购年终总结图表分析引言采购是企业供应链管理中至关重要的环节,对企业的运营和利润有着重要的影响。
年终总结是评估采购绩效、发现问题和制定改进措施的重要工具。
本文将根据采购年终总结的图表分析,对过去一年的采购工作进行评估和分析。
1. 采购金额分析首先,我们来分析过去一年的采购金额情况。
通过查看图表,我们可以看到每个季度的采购金额的变化趋势。
根据图表,我们可以分析不同季度的采购金额是否有显著的差异,以及可能导致这些差异的原因。
例如,如果第一季度的采购金额明显低于其他季度,可能是因为季节性需求减少或者供应商变更等原因。
2. 供应商分析其次,我们来分析过去一年的供应商情况。
通过查看图表,我们可以看到每个供应商的采购金额占比情况。
根据图表,我们可以确定哪些供应商是我们的主要合作伙伴,以及他们在整体采购中的重要性。
我们还可以分析不同供应商之间的采购金额差异,以及可能导致这些差异的原因。
例如,如果某个供应商的采购金额比其他供应商高得多,可能是因为他们的产品质量更好或者价格更具竞争力。
3. 采购周期分析另外,我们来分析过去一年的采购周期情况。
通过查看图表,我们可以看到每个采购订单的处理时间。
根据图表,我们可以确定平均采购周期和最长的采购周期,以评估我们的采购效率。
我们还可以分析不同供应商之间的采购周期差异,以及可能导致这些差异的原因。
例如,如果某个供应商的采购周期明显长于其他供应商,可能是因为他们的交付速度较慢或者在物流方面存在问题。
4. 采购成本分析最后,我们来分析过去一年的采购成本情况。
通过查看图表,我们可以看到不同类别的采购成本占比情况。
根据图表,我们可以确定哪些采购成本项是我们的主要支出,以及它们在整体采购成本中的重要性。
我们还可以分析不同采购成本项之间的差异,以及可能导致这些差异的原因。
例如,如果某个采购成本项占比较高,可能是因为某个产品的成本增加或者物流成本上升等原因。
结论通过以上的图表分析,我们可以对过去一年的采购工作进行综合评估。
供应商现场考察评估表

出厂检验能力
检测设备的计量和管理
不合格品的控制及预防
客户投诉系统
质管人员 生产设备有几台? 工艺人员 主要是哪些?
生产设备的自动化程度
设备状态
模具、刀具储存 生产设备的更新和保养 情况 核心技术及工艺是否符 设备 合要求 、工 艺及 技术 是否生产同类产品
5.开关公司需使用的工具储存室落锁,有防止损坏的措施;4:开关公司使用的工 具被特别存放;3:开关公司需使用的工具被单独存放;2:开关公司需使用的工具 被清晰标示;1:开关公司需使用的工具未单独存放。 5:设备很新,有维修保养规范,每天保养并有记录;4:设备较新,定期保养并有 记录;3:设备有明显磨损,定期保养有记录;2:设备有明显磨损并有污渍,无保 养记录;1:设备陈旧,无保养。 5:完全符合;4:大部分符合;3:基本符合;2:类似;1:无关 20 5:是,经验在5年以上;4:是,经验在3年以上;3:是,经验在1年以上;2:类 似产品经验;1:无关 5:关键/一般工序工艺规范、作业指导书清晰,并有效指导生产;4:有关键工序 控制,有效执行,一般工序控制待改进;3:关键工序控制,有效执行,一般工序 控制不足;2:一般工序控制有效执行,无关键工序工艺规范;1:无相关工艺措施 5:充裕,具备自主开发能力;4:充裕,具备共同开发能力;3:技术力量能保证 批量生产质量;2:技术力量稍欠缺;1:技术力量严重不足。 5:独立样件部门+快速样件制作能力;4:独立样件部门;3:正常产品线产品; 2:外部制作; 5:开发周期短于约定要求质量可靠;4:开发周期短于约定要求,质量一般;3: 符合约定要求,符合质量要求;2:开发周期长于约定要求,质量一般;1:周期或 质量不符合要求。 5:超出期望;4:符合要求;3:基本符合要求;2:部分符合要求;1:大部分不 符合要求。 5:同行业市场占有率超过50%,为行业巨头;4:占有率在30%~50%,同行业排名前 三;3:占有率在20%~30%,具有一定影响力;2:占有率在10%左右,对市场影响不 大;1:份额极低,无影响力 5:完善严谨的成本控制和定价体系,各项成本控制到位;4:较好,各项成本比率 合理;3:有成本控制流程,效果不明显;2:成本控制不严谨,无跟踪;1:控制 无效。
北京奔驰供应商评审

潜在供应商评估指南评估范围A – Management管理B - Technology and Development技术与开发C – Quality质量D – Production生产E - Engineering (Product and Process)工程(产品和过程)F - Logistics / Supply物流与供应G - Sub-supplier Management分供商管理H - Cost Management成本管理Scoring Guide打分指南团队评价必须用Excel文件记录,在注释页上输入注释。
在DC流程颜色表示的定义:0分红色供应商示范既无文件化流程/程序,又无应用的实例过程肯定会发生产品缺陷和招致顾客抱怨。
1分红色有文件化流程/程序,但不完善或没有完全的贯彻。
过程大概会发生产品缺陷和招致顾客抱怨。
2分绿色流程/程序是完整的并备有证明文件,贯彻情况可以接受。
过程大概不会发生产品缺陷和招致顾客抱怨。
3分绿色具有完整的备有证明文件流程/程序,并得到完全地贯彻。
依照评估团队专家的意见,过程不会发生产品缺陷和顾客抱怨。
N/A项绿色评估团队同意不记分的这些问题,记分箱内输进NA,并在注释页解释原因。
对于特殊的商品/过程,问题不适用。
注意:每一项问题的打分,团队必须达成一致意见。
A – Management/管理注解:提交并详细说明所有范围、级别的公司经营(例如:管理部门、工厂管理、项目管理)发展的质量方针。
允许已经同意的特殊目标和质量体系。
质量必须当作一项全面的经营任务。
经营必须涉及它自身具有的如下题目:商业计划国内外性能资料对照商业成果员工满意客户满意管理层描述在公司内负责利润和消耗的组织实体。
注,商业计划意味着:当地的工厂执行目标Checklist Overview:1是否制定目标,并且始终遵循?1a供应商是否有更新商业计划的流程?1b所有目标是否都源于商业计划?2否有管理评审流程?2a是否界定和控制所有等级的目标?2b 供应商是否实施定期的内部质量评审?2c 是否有针对评审(结果)的纠正和预防措施?3是否有流程来评估已经建立的资源能力(如人员、设备、方法和材料)?3a为提高顾客满意度,组织是否识别和分配适当的资源?4是否有合适的方法来管理员工满意度的流程?4a供应商是否有关于(提高)质量意识的流程?4b应商是否推行员工极力活动(例:小组活动)以保证和改善质量?5是否有支持完成商业经营范围和履行顾客需求的培训计划?5a供应商是否有针对员工的书面化的培训和开发计划?5b个人培训,培训计划是否合适于岗位说明?5c在顾客需求和目标绩效方面,员工得到了哪些信息?A1是否制定目标,并且始终遵循?Comments: 注解:目标是.对于产品、过程、操作和所有级别服务界定的规范。
利用excel表格制作各种品质图表QC7+MSA+SPC

5 492.7
469.3
489.0
480.4
509.4 484.9 495.6
6 492.3
492.7
520.1
534.5
501.4 507.6 507.5
7 502.3
499.6
521.0
504.5
500.0 515.2 493.9
8 505.2
501.3
481.7
479.8
480.5 482.3 493.3
所涉及的函数:
1. 统计函数: ‘CORREL’
返回单元格区域 array1 和 array2 之间的相关系数。使用 相关系数可以确定两种属性之间的关系。例如,可以检测 某地的平均温度和空调使用情况之间的关系。 语法 CORREL(array1,array2) Array1 第一组数值单元格区域。 Array2 第二组数值单元格区域。
可以使用函数 IF 对数值和公式进行条件检测。
VLOOKUP 在表格或数值数组的首列查找指定的数值,并由此返回表格或数组
当前行中指定列处的数值。
所涉及的公式:
重复性: EV R * K1
再现性:
AV [(X DIFF * K2 )2 (EV 2 / nr)]
GR&R: 样板间变差: 样板总变差:
9 519.8
484.9
488.4
487.4
495.0 490.6 511.3
10 485.6
507.5
502.5
497.8
501.0 518.5 527.2
如何对该些数据进行处理呢?我们就可以运用直方图就行分析!
从下图我们可以轻松的分析出数据的分布情况。
电阻500+/-20直方图分析
供应商过程审核报告VDA6.3
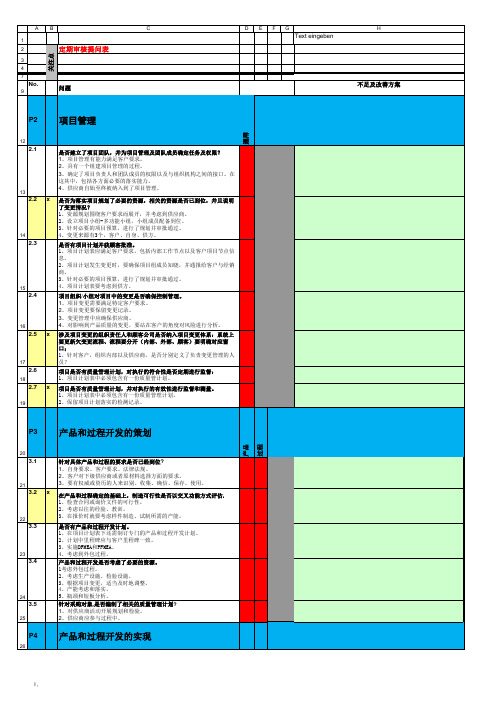
开关必须确保不被无权限的人操作):
1、设备必须有能力满足具体特性的公差方面的要求-设备精度。
2、特殊特性的能力证明,如PPK、CPK。
54
3、不能证明能力的特殊特性,必须实施100%检验。
6.2.4 x 在生产中产品的特殊特性是否得到控制。
1、生产控制计划中必须标记产品的特殊特性以及过程参数,并实施SPC。
2、一旦出现偏差,必须具有反应计划。
3、特殊特性存档义务要考虑客户要求。 55
6.2.5
废弃件,重新加工件和嵌件是否分隔存放并有标识。
1、没有被批准的零部件必须被隔离和标识。
2、存放报废/返工零部件的容器必须具有适当标识。
56
3、必要时设置隔离仓库,并实施样管理。
6.2.6
材料和零件在流程中是否能防止混料和错用。(符合顾客规定的标识、
20
3.1
针对具体产品和过程的要求是否已经到位?
1、自身要求、客户要求、法律法规。
2、客户对下级供应商或者原材料选择方面的要求。
21
3、要有权威或资历的人来识别、收集、确信、保存、使用。
3.2 x 在产品和过程确定的基础上,制造可行性是否以交叉功能方式评估.
1、检查合同或询价文件的可行性。
2、考虑以往的经验、教训。
批量生产
过程输入
是否在开发和批量生产之间进行了项目交接? 1、向客户提交PPAP。
按生产批量和必要数量的购入材料是否能按时供到合适地点(如:仓 库,工作位置)? 1、正确的产品(原材料、零部件),必须以约定的质量和数量,在正确 的包装形式下,并附有正确的文件,在约定的时间交付给约定的工位。 2、JIT、看板管理、FIFO。
I,
H
不足及改善方案ABCຫໍສະໝຸດ D E FGNo.
供应商考察评估表(中英文版本)
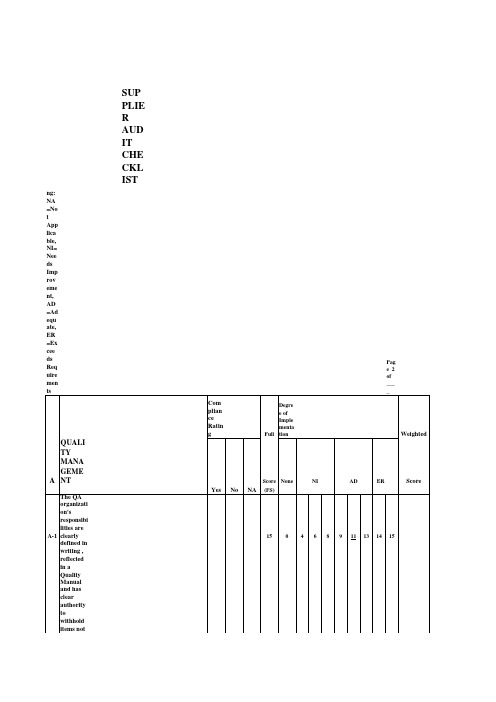
10 0 3 4 5 6 7 8 9 10 20 0 6 8 10 12 14 16 18 20
instructio ns defining characteri stics, equipmen and methods used during inspection . 检验员有 受控的作 业指导书 指导,指 导书内容 包 括了检验 的项目、 设备和方 法。
TOTAL RATIN
10 0 3 4 5 6 7 8 9 10 105 20 0 6 8 10 12 14 16 18 20
verified, analyzed and improvem ent actions are generated on a continuou s basis. 在生产中 发现的不 合格物料 经过确认 、分析并 在 持续的基 础上推进 改善活动 。 Nonconformin g materials are properly D-3 identified and segregate d from good material. 不合格物 料能明确 区分并与 合格物料 隔离。
Com plian ce Ratin g
Degre e of Imple menta Full tion
Pag e2 of ___ _
Weighted
Score None
NI
Yes No NA (FS)
AD
ER
Score
15 0 4 6 8 9 11 13 14 15
meeting acceptabl e quality standards 品质保证 组织的职 责以书面 形式明确 定义,并 反 映在品质 手册中; 品质保证 组织有权 停止不符 合 质量标准 的项目。 There is QA Manual and revision history A-2 reveals continuou s update and review within the 品质保证 手册和历 史版本能 体现出一 年内的持 续 更新和评 审。 The QA organizati on operates a defect A-3 preventio program that includes defect analysis and the generatio n of improvem ent actions 品质保证 组织推行 包括了缺 陷分析和 改善行动 的 缺陷预防 计划 The QA organizati on prepares and issues A-4 periodic reports and maintains records relative to process
供应商综合能力评估表

无正规管理办法,凭组长、领班口头盲目指挥生产,质量难以得到控制。
2
生产工艺
主要工序均有简洁而实效的作业指导书,现场文件均受到控制。
1()
特殊工序才有指导书,且指导书不太科学实效,工人有时不按文件进行操作,有时文件不是最新有效版本。
6
无工艺性的文件,全凭组长、领班口头指示操作,或凭工人自己经验操作。
Fo
2
质量管理体系
有文件化的质量管理体系,结构比较完善;体系能够有效运行,质量手册和程序文件的规定能够认真执行。
10
有文件化的质量管理体系,但不太完善;体系基本上能够运行,质量手册和程序文件的规定不太严格
6
无文件化的质量管理体系,只有一些习惯性做法或口头程序在实施。
2
技术能力
有自行设计、开发主要产品的能力,有一套完善的产品设计开发控制制度。
2
检验过程控制
主要检验过程得到严格控制,如每批测试前检查仪器设备,检验员严格按文件操作,检验结果有专人校核等。
1()
关键检验过程受控,但有时未能严格按文件操作,检验结果由检验员一
2
产品交付
能按合同要求的期限、交付条件交货。
10
基本上能按合同要求的期限和交付条件交货。
6
经常拖延交期,交付条件也常变化。
2
售后服务
对客户有良好的服务,主动调查客户的服务需求,并主动尽力实施;客户有抱怨能及时纠正改善和预防,并能将信息及时反馈给客户,客户投诉非常少。
1()
对客户服务较好,但不太主动,客户偶有投诉,会解决,但不太及时。
6
对客户的投诉经常推卸责任,或拖很长时间才予以解决,且类似问题时有发生。
2
成本与价格
重视改善流程、提高效率、开源节流、降低成本,因此产品售价能稳中有降。
供应商现场质量体系审核项目一览表

有标准
31
修理工序及再投入工序等明确并且恰当。
规定每件产品的修理次数。
检验/ 试验的
1.
检验项目/抽 样标准是否
有工序内检查,出厂检查的标准。项目,内容,判定,抽取数量等明确。
管理
明确?
工序内检查出的次品立刻分析,并且反馈到前工序。
32
外观检查有极限条件下的产品样本吗。
检查标准是否考虑了最终客户的使用环境。
每天对计划完成情况进行跟踪管理。
6.
是否把握工 序能力?
各流程收集的数据是否系统管理?是否反映到生产管理?
是否流程能力通过成品率来管理,并有效的用于改进活动?是否有有成效? 28
是否管理Cp值?是否>1.3?
是否引入了SPC、质量成本条款?
7. 成品半成品 实行彻底的标识管理。储存的产品中是否有没有标识? 的使用,保
7
跟踪管理质量改进的进度。
总结并汇报质量改进完成情况。
设计控 1. 有没有设计 有制度,正在实施,评审成员也合适。
制
评审制度?
评审充分结合考虑其他产品出现过的故障及实效。 8
明确了顾客的要求。
样品的确认~批量生产的过渡~可靠性确认~出厂确认等各阶段评审是否进行。
2.
是否实施新 元件引入和 可靠性试验
有设备地线,Earth bound,保险丝,地板,桌子等的标准,检查频率无问题。 42
异常时的处理明确。
设备设置/移动时,确实确认了是否拔掉地线。
3.
清洁区的管 理规定
有洁净区的管理标准。
清洁度的测定值无问题,测定频率也妥当。 43
异常时的处理明确。
外部气体引入处设有化学过滤器,除去杂质。
1. 包装/辅助材 包装有规范。(考虑到防止材料出现缺陷吗?) 料的管理
SQE(供应商品质工程)

SQE(供应商品质工程)有两方面的工作:一是供应商的品质控制方面,二是企业内IQC工作的品质控制;SQE的工作还包括:1.建立合格供应商管理系统;2.供应商评审系统,包括供应商体系审核表和评分标准;3.IQC品质保证系统的建立,包括IQC运作流程、技术标准以及检测方法;4.制订不合格批处理程序,其中包括各种特殊情况的处理方法;SQE最重要的能力就是建立各种品质保证体系的能力,通过各种品质保证系统的有效运作,使得企业所有的物料的品质得到保证;系统的建立和完善是SQE首先要完成的,不然的话,很容易成为繁忙的消防队员。
SPC统计的手法是品质管理的基本技能和方法,实际的品质管控工作,其实不管你有没有导入这些统计手法,其实你都在运用,只是没有系统化而已。
比方说,你的检验员在对产品进行抽检时的尺寸测量,2小时一模的抽检频率,这个频率就是一种统计方法。
当出现了不良品,我们得分析一下不良的原因,一个班生产了1万只产品,有500只不良,不良率5%。
再细分,缺料200只,划伤250只,黑点50只。
这时可以导入鱼骨图来找原因了,从人、机、料、法、环的各个因素去找原因,再改善。
QC七大手法其实在检验过程中就体现了,导不导入都在做。
做的好不好,有没有效而已。
SPC则是一个系统工程了,需要投入软硬件才能见效。
硬件是人员、设备的配备,测量是SPC数据的来源,所需数据测量工作非常繁重。
软件的投入是整个管理体系得建立问题改善团队,这个说得容易,做起来很难,很多推行不了的原因就在此。
SPC是控制制程稳定性的,当我们根据数据判断出制程可能出现不稳定因素时,怎么去改善它,才是SPC的真正目的。
没有一个完善的管理体系和规程,往往弄到最后就变成了一种装饰,应付某种需要存在的工具。
品管七大手法:检查表——收集、整理资料;排列图——确定主导因素;散布图——展示变数之间的线性关系;因果图——寻找引发结果的原因;分层法——从不同角度层面发现问题;直方图——展示过程的分布情况;控制图——识别波动的来源;PDCA _计划实施检查改进SPC- (Statistical Process Control):为了贯彻预防原则,应用统计技术对过程中的各个阶段进行评估和监察,从而保证产品与服务满足要求的均匀性。
供应商管理评估表
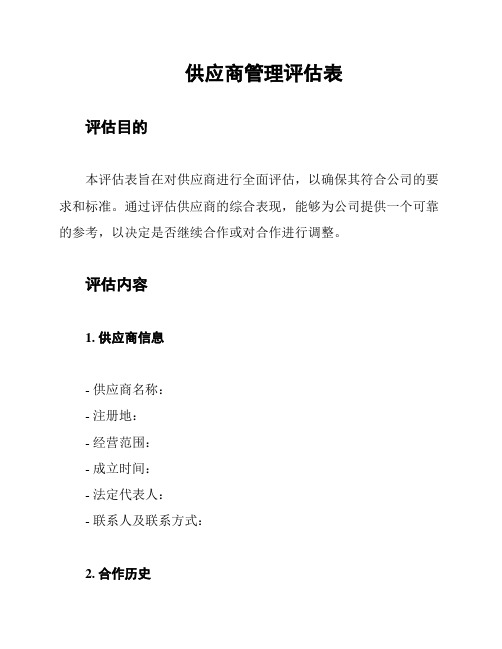
供应商管理评估表评估目的本评估表旨在对供应商进行全面评估,以确保其符合公司的要求和标准。
通过评估供应商的综合表现,能够为公司提供一个可靠的参考,以决定是否继续合作或对合作进行调整。
评估内容1. 供应商信息- 供应商名称:- 注册地:- 经营范围:- 成立时间:- 法定代表人:- 联系人及联系方式:2. 合作历史- 与供应商合作的起始时间:- 合作期间是否存在纠纷或投诉记录:- 是否曾解除与供应商的合同:3. 质量管理- 供应商是否具备相关质量管理认证(如ISO9001):- 是否有质量管理体系及其有效性:- 是否定期进行质量检查和评估:- 是否有应对质量问题的有效措施和改进计划:4. 交付能力- 是否能够按时交付产品或提供服务:- 是否存在延迟交付或未能履约的记录:- 是否有紧急情况下的备用计划:- 是否配备适当的物流和运输设施:5. 价格合理性- 产品或服务的价格是否与市场相符:- 是否存在异常高或异常低的价格情况:- 是否有价格调整的合理机制:6. 服务水平- 是否能够及时响应客户的需求:- 是否提供专业的技术支持和售后服务:- 是否积极解决客户投诉和问题:评估结果根据以上评估内容,对供应商进行综合评估,确定评估结果,并采取相应的措施。
评估结果可分为以下几类:- 合格:供应商在各个评估项上表现良好,符合公司的要求和标准。
- 待完善:供应商在某些评估项上存在一些不足或待改进的地方,需要与供应商进行沟通和协商,制定改进计划。
- 不合格:供应商在多个评估项上表现不符合公司要求,需要采取相应的措施,如暂停合作或寻找替代供应商。
评估结果应以客观、可验证的数据为依据,并及时将结果反馈给相关部门和供应商,以便进行后续管理和决策。
备注评估表可根据具体情况进行调整和补充。
建议定期对供应商进行评估,以确保合作关系的质量和稳定性。
以上为供应商管理评估表的基本内容,具体实施时可根据实际需求和要求进行修改和补充。
供应商评估表
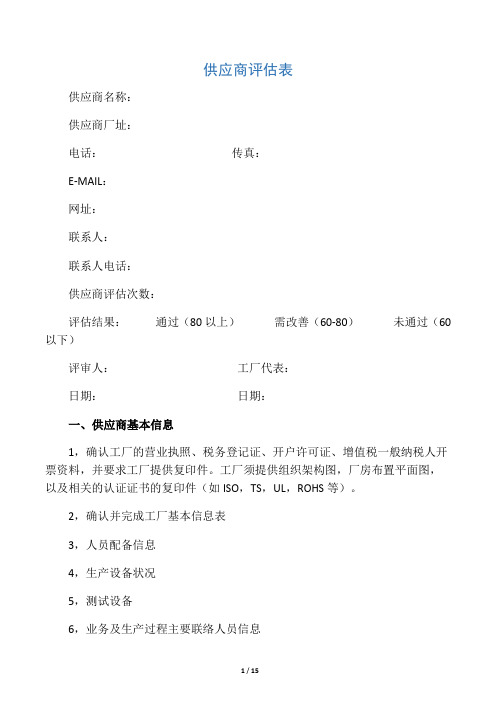
供应商评估表供应商名称:供应商厂址:电话:传真:E-MAIL:网址:联系人:联系人电话:供应商评估次数:评估结果:通过(80以上)需改善(60-80)未通过(60以下)评审人:工厂代表:日期:日期:一、供应商基本信息1,确认工厂的营业执照、税务登记证、开户许可证、增值税一般纳税人开票资料,并要求工厂提供复印件。
工厂须提供组织架构图,厂房布置平面图,以及相关的认证证书的复印件(如ISO,TS,UL,ROHS等)。
2,确认并完成工厂基本信息表3,人员配备信息4,生产设备状况5,测试设备6,业务及生产过程主要联络人员信息二、厂房布置合理性、安全性(每项1分共占9%)1、确认工厂的车间布局的方式是否合理,是否利于工序之间产品的传送?()2、厂房各位置的标识是否清楚,包括安全标识等?()3、消防/生产防护设备是否齐全有效,安全操作说明指示是否公告,点检记录是否完善?()4、逃生通路是否有明确指示,逃生通路是否顺畅无杂物堆积堵塞?灭火器、消防栓是否被阻挡?()5、是否未发现违规行为导致事故或火灾隐患?()6、生产区域是否足够的光照及良好的通风条件?()7、工厂的机器、设备、装置是否适合目前即将要开始的定单产品的生产需要?()8、车间一般的内务管理是否规范流畅?()9、工厂整体的环境是否符合环保和生产要求?()总结:三、订单、工程及生产计划(每项0.5分共占7.5%)1、是否已建立订单合同的评审程序并进行评审?()2、订单合同的审核是否能保证客户的需求被理解并得到有效贯彻执行?()3、当订单合约、规格的内容(产品的要求、数量、交期。
)变更时是否有相应的沟通并确保能满足变更的要求?()4、订单信息要求或变更是否传达到相关的部门(工程、生产、品保。
)?()5、确认工厂工程应用的硬件及处理软件是否能满足工程制作之需要?()6、工程MI的制作是否依据客户文件要求严谨制作(如UL、DATE CODE要求等)?()7、是否有定义工程变更/制程变更流程?相关的变更执行之前是否有经过审核,核准?()8、工程的变更是否有经过相关的EQ问客处理,并按客户答复之要求制作?()9、客供资料及M I制作资料是否为受控文件?()0、对客户文件的保密处理措施是否到位,是否允许员工私自用移动存储设备拷贝客户或工程制作资料?()1、工厂是否有ERP管理系统?()2、计划部是否对订单产品有效的分类(如按客户的重要性,订单的交期轻重缓急,产品的复杂性及难度,是样板还是大货等,依据什么方式排序生产)?()3、生产计划部的订单排程、管控、调度是否合理有序?()4、是否有专人每天现场跟进订单产品的生产进度?()5、对特殊情况、特殊订单产品生产计划部门的处理执行是否有效可行?()总结:四、生产现场(共占26%)(一)入料仓(每项1分)1、仓储环境是否达到物料储存环境之要求(包括温、湿、清洁度等)?()2、对产品搬运、储存、出入库等是否有相应的作业程序?()3、所有物料有无经过IQC的抽样检验,检验合格或不合格的物料是否分区放置以便区分?()4、不同物料是否有效分类区别摆放,是否有效标识?()5、合格、不合格及退货或者待报废物料是否区分处理,有无有效标识?对质量异常之物料是否及时反馈供应商?()6、有效期的物料是否对其有效期进行监控,及时通知生产使用,以免造成浪费或污染?()7、对于超出储存期限的材料再次使用有无相应的验证流程?是否执行?()8、化学类、危险类物料的安全保护措施是否建立,并能有效的执行?()9、物料入仓、领料是否有相关记录?()(二)生产车间(每项1分)1、生产现场是否有建立作业指导文件,包括生产流程卡,本岗位的生产作业指导书,设备维护保养记录,品质异常处理程序等?()2、确认设备制造能力,设备是否处于正常运转状态,设备是否有维修保养记录,闲置或异常状况的设备是否有标示?()3、人员技能,员工是否有经过上岗培训,是否经过考核合格后上岗,是否有相关的培训考核记录?员工是否依据作业指导书进行作业,对本职位产品质量控制标准是否清楚明确?异常状况的发生是否具有应变处理措施等(如重大品质、设备异常处理方法;重大安全隐患的意识和处理等)?()4、环境,生产环境是否能满足生产之需要,设备的布置是否合理规范便于产品在车间之间进行流转,通道是否畅通,是否满足5S之审核要求,其他如噪音、异味、粉尘等影响身体健康安全的环境条件是否达标?()5、生产计划单的生产安排,各车间的生产安排是否按照生产计划部统一的调度生产,或依据ERP系统中订单的分类安排生产?()6、生产流程控制,各车间的生产流程是否有序,作业是否规范?首件检查记录是否完整?()7、产品工序之间的转移控制是否能够有效控制(合格品的下转,不合格品的回转是否有流程卡跟踪,以及其他相关的记录)?()8、各生产车间是否有本车间加工的控制标准?()9、各车间对本车间的产品是否订立了直通要求,确认其控制效果的是否有相关的记录?()0、各车间对本车间的异常情况的处理是否有制定相关的程序文件,异常情况的预防、处理的力度是否执行到位?()1、是否有返工流程?返工区域是否进行标识?返工的不良产品是否被标识和重新转到品质部门重新检验?()2、各车间的生产状况是否达到安全生产之要求?()(三)包装及成品仓库(每项1分)1、对产品的搬运、储存、包装与交货是否有相应的作业程序?()2、是否按客户的包装程序要求进行包装?包装是否符合运输安全之要求?包装信息是否符合客户要求?()3、仓储环境是否能满足产品储存之要求?()4、摆放、卫生环境是否规范、干净等?()5、出货是否有相应的出货记录?()总结:五、品质保证(共占40.5%)(一)质量管理体系(每项1分)1、是否有得到相关的体系认证(如IS000、TS16949等)以及其他需要的准入认证(UL、ROHS)等,或基于该类体系要求持续改善品质而建立的品质体系类管理系统?()2、品质管理系统文件中是否涵盖分级:质量方针和目标、质量手册、程序类文件、作业类文件以及相关的表单记录?()3、体系类文件是否为受控,是否能确保外来文件得到识别?()4、是否有制定并有效保存所有的生产品质记录,记录是否清晰标识,以便查阅?()5、文件的修改或变更是否能够与现行的修改状态有效识别?()6、质量目标是否体现质量方针的要求,并已量化?()7、公司的质量目标是否分解到各部门?()8、是否根据制定的目标定期对实际达成情况及时作统计分析?对于超出目标的项目是否采取相应的纠正预防措施,并跟踪其效果?是否有持续改善的计划?()9、各部门的相互关系及职责是否明确定义(部门组织图、工作职责等)?()0、是否制定合理的内审计划,是否依据计划进行内审?()1、内审的内容是否全面,是否涵盖质量、环保等体系的审核?()2、内审中发现的不符合或已经失效,是否采取有效的纠正预防措施并落实?()3、是否有指定一名管理者代表负责质量体系,内部审核人员的资格要求是否有明确的规定?()4、管理评审会议是否包含如下项目:品质环境目标的达成状况、内审结果、客户反馈投诉、预防纠正措施的执行状况、前一次管理评审会议问题点的纠正改善实施状况、影响管理系统的变更?()5、是否有保证所有与品质有关人员可以达到品质保证要求的培训体系?()(二)品质的划分(每项1分)1、工厂是如何对品质部门划分,其组织结构图中的品质部门是否为独立于生产部门的?()2、品质负责人员是否有权因产线存在重大品质问题,要求停线以纠正品质问题?()3、IQC是否清晰本岗位的主要职能,是否对所有来料都能有效的检验、控制及相关的记录统计等?()4、IPQC是否清晰本岗位的主要职能,生产车间的生产状况、品质巡检、记录核查、相关异常协调管控、以及状态记录统计分析汇总等工作是否能执行到位?()5、半成品检验QC是否清晰本岗位的主要职能,常规的外观检验、不良的修理、品质报表等是否明确标准、记录准确?()6、功能测试QC是否清楚本岗位的主要职能,是否有相关的测试记录?()7、成检QC是否清楚本岗位的主要职能,常规的成品外观检验,特性检验,品质报表等是否明确标准、记录准确?()8、QA岗位职能是否明确,各类安规测试、特性测试、可靠性测试、品质报告、品质数据汇总分析是否全面、对品质改善是否有起到明显的效应?()(三)工厂品质控制方法(每项0.5分)1、工厂是否有合适的品质管理手法,如TQM,六西格玛、QC七大手法是否有效应用于品质的管理与分析?()2、现场的品质报表是否对品质管理起到有效的效用(查看现场的相关品质记录,并抽取一个时段的品质记录表单)?()3、结合现场抽取时段的品质记录表单,查看工厂品质部电脑中的案例分析及相关品质分析图表,确认工厂品质手法是否强有力的执行,分析方法是否有效?()4、有没有免检产品的相关规定?有无建立免检和常规检验的转换规则?()(四)品质检验员的技能(每项1分)1、检验员是否在经过上岗培训,是否有相关的培训记录?()2、检验人员是否在培训后进行过相关的品质检验流程,品质检验标准的考核?()3、检验人员是否为考核合格后才允许上岗作业(是否有上岗证)?()4、现场的检验人员的作业是否规范?是否依据文件要求全检或按抽样计划进行抽检?()5、现场检验人员对品质标准的判定是否准确(现场从员工身上了解其品质知识及个人的相关技能如何)?()(五)检验设备及工具(每项0.5分)1、检验设备、仪器等工具工具的配置是否能满足常规检验之需要?()2、工厂现有的检验设备、仪器等工具是否稳定、是否有进行校验,是否在校验期内?()3、检验设备、仪器等工具的检验精度是否能满足常规产品之检验需要?()4、检验设备、仪器等工具是否有相关的维护保养记录?()5、对特殊类检验设备是否为专职人员上岗操作?()6、检验设备异常情况时工厂的处理方式是否可行?()(六)不良品的处理及追溯(每项0.5分)1、不良品是否有效标识?()2、不良品是否有进行分类分区放置?()3、不良品是否有进行相关的品质记录以便提供相关数据给品质管理人员进行分析、处理及协调生产部门改善品质?()4、是否有定义不良品修补的标准?()5、不良品的报废处理方式是否有文件指导并执行?()6、各类不良是否都能有效追溯?()(七)客户反馈(投诉)处理及服务(每项0.5分)1、是否建立了客户投诉处理与服务流程?()2、是否建立与客户的定期沟通制度?是否有客户满意度调查制度与满意度持续提升计划?()3、产品信息是否与客户有效沟通,其沟通方式是否为有据可循的?()4、对客户的询价、合同或订单的处理是否及时、报价合理准确、订单信息确认清晰无误等?()5、对客户订单的产品投诉的反应时效是否快捷,对品质异常的客诉处理是否能及时调动、组织相关人员进行品质分析及改善(8D),必要时是否有足够追溯性鉴别及追回问题产品?()6、出现的重大品质问题时,是否有一定的程序可以保障其他客户类似情况的发生,或通知已产生品质异常问题而可能受到影响的其他客户?()(八)物理、化学实验室(每项0.5分)1、各类检测设备是否齐全,测量工具是否有得到相关部门的有效校验,是否处于校验的有效期?()2、化学药水是否有空管控,特别是高酸高碱剧毒化学物的使用是否有严格的控制指导文件监控使用?()3、物理检测和化学药水的使用是否有相关的记录报表跟踪?()总结:六、工厂的供应商管理(每项1分共占9%)1、工厂的供应商是否有进行严格的审核制度评估,是否对其供应商制定相关的供应商评估程序?()2、工厂是否对现有的供应资源有效的评级,是否有合格供应商清单、并经核准和严格执行?()3、是否根据计划按期审核供应商的品质及环境控制系统,以确保其系统的正常维持与持续改善?()4、对于审核评估未达标准者,是否采取必要的措施与处分(Eg:改善措施跟踪、降低采购比例等)?()5、是否与供应商签署必要的质量协议?()6、工厂对合格供应商的品质、货期异常的处理是否有建立相关的文件说明和跟踪验证供应商的品质分析改善之结果?()7、是否有外包业务,对于外包情况,是否制定外包商选择及管理程序?()8、是否有完善的系统对外包商的品质状况作实时监测、或趋势分析,及要求外包商提供纠正改善预防措施?()9、工厂和其供应商之间是否有相关的保密类协议以保障彼此的权益?()总结:七、环保体系和社会责任(每项1分共占8%)1、工厂是否有相关的环保体系认证( ISO14001 )?()2、三废排放是否符合相关的法律法规的要求?()3、工厂是否存在环保不达标的相关记录?()4、对危险化学物品是否制定了相应的应急措施?()5、工厂的用工条件是否符合国家相关法律之要求,是否存在未成年人的用工现象,是否存在用工歧视现象?()6、员工的薪资、社保、福利是否依据相关法律准时发放?()7、是否存在强迫劳动、强迫加班现象?()8、员工的健康是否能得到有效的保障?()总结:评审结果及总结报告:。
全球采购供应商调查表(中文翻译)

全球采购供应商调查表
比例
95 - 100% 杰出---------- 总实际分值2405 90 - 94% 优秀----------
80 - 89% 满意---------- 最大可能的分值3000 70 - 79% 可接受-------
以下- 70% 不满意------- 百分比80%
全球采购供应商调查
全球采购供应商调查
全球采购供应商调查
调查的目的是评估或检查**公司的现在或潜在的供应商的体系。
这个调查分为10个种类。
此调查将根据以下方针对供应商执行:
A.现在供应商
1.如果分数值大于905,供应商将不被审查,但以下除外:
2.如果分数值在80%-90%之间,供应商将在每两年被审查一次。
3.如果分数值小于80%,供应商将会每年审查一次。
4.如果供应商每增加一个新产品或者新程序,全球供应商采购小组将会根据判
断来决定是否重新审查供应商。
5.如果供应商已经证实了很大的质量体系的变动,将会被审查。
6.根据全球采购小组的判断,可以随时审查供应商。
B.潜在供应商
1.在与新的供应商交易之前要进行供应商的调查
审查问题等级在3级以下,则要求书面的矫正措施计划被**公司全球采购小组生
成文件纳入到审查报告中。
- 1、下载文档前请自行甄别文档内容的完整性,平台不提供额外的编辑、内容补充、找答案等附加服务。
- 2、"仅部分预览"的文档,不可在线预览部分如存在完整性等问题,可反馈申请退款(可完整预览的文档不适用该条件!)。
- 3、如文档侵犯您的权益,请联系客服反馈,我们会尽快为您处理(人工客服工作时间:9:00-18:30)。
供应商评估表
供应商名称:
供应商厂址:
电话:传真:
E-MAIL:
网址:
联系人:
联系人电话:
供应商评估次数:
评估结果:通过(80以上)需改善(60-80)未通过(60以下)
评审人:工厂代表:
日期:日期:
一、供应商基本信息
1,确认工厂的营业执照、税务登记证、开户许可证、增值税一般纳税人开票资料,并要求工厂提供复印件。
工厂须提供组织架构图,厂房布置平面图,以及相关的认证证书的复印件(如ISO,TS,UL,ROHS等)。
2,确认并完成工厂基本信息表
成立时间厂房面积
主营产品主要客户
员工人数每月产能
营业证号税务证号
生
产
制
程
能
力
其他
备注
3,人员配备信息
管理人员工程技术人员
生产操作人员品控人员
后勤支持人员
4,生产设备状况
设备名称数量备注(设备状况,特殊制造能力)
5,测试设备
设备名称数量备注设备名称数量备注
6,业务及生产过程主要联络人员信息
职位姓名电话职位姓名电话
二、厂房布置合理性、安全性(每项1分共占9%)
1、确认工厂的车间布局的方式是否合理,是否利于工序之间产品的传送?()
2、厂房各位置的标识是否清楚,包括安全标识等?()
3、消防/生产防护设备是否齐全有效,安全操作说明指示是否公告,点检记录是否完善?
()4、逃生通路是否有明确指示,逃生通路是否顺畅无杂物堆积堵塞?灭火器、消防栓是否被阻挡?()
5、是否未发现违规行为导致事故或火灾隐患?()
6、生产区域是否足够的光照及良好的通风条件?()
7、工厂的机器、设备、装置是否适合目前即将要开始的定单产品的生产需要?
()
8、车间一般的内务管理是否规范流畅?()
9、工厂整体的环境是否符合环保和生产要求?()总结:
三、订单、工程及生产计划(每项0.5分共占7.5%)
1、是否已建立订单合同的评审程序并进行评审?()
2、订单合同的审核是否能保证客户的需求被理解并得到有效贯彻执行?()
3、当订单合约、规格的内容(产品的要求、数量、交期。
)变更时是否有相应的沟通并确保能满足变更的要求?()
4、订单信息要求或变更是否传达到相关的部门(工程、生产、品保。
)?()
5、确认工厂工程应用的硬件及处理软件是否能满足工程制作之需要?()
6、工程MI的制作是否依据客户文件要求严谨制作(如UL、DATE CODE要求等)?
()7、是否有定义工程变更/制程变更流程?相关的变更执行之前是否有经过审核,核准?
()
8、工程的变更是否有经过相关的EQ问客处理,并按客户答复之要求制作?()
9、客供资料及M I制作资料是否为受控文件? ()
10、对客户文件的保密处理措施是否到位,是否允许员工私自用移动存储设备拷贝客户或工程制作资料?()
11、工厂是否有ERP管理系统?()
12、计划部是否对订单产品有效的分类(如按客户的重要性,订单的交期轻重缓急,产品的复杂性及难度,是样板还是大货等,依据什么方式排序生产)?()
13、生产计划部的订单排程、管控、调度是否合理有序?()
14、是否有专人每天现场跟进订单产品的生产进度?()
15、对特殊情况、特殊订单产品生产计划部门的处理执行是否有效可行?()总结:
四、生产现场(共占26%)
(一)入料仓(每项1分)
1、仓储环境是否达到物料储存环境之要求(包括温、湿、清洁度等)?()
2、对产品搬运、储存、出入库等是否有相应的作业程序?()
3、所有物料有无经过IQC的抽样检验,检验合格或不合格的物料是否分区放置以便区分?
()
4、不同物料是否有效分类区别摆放,是否有效标识?()
5、合格、不合格及退货或者待报废物料是否区分处理,有无有效标识?对质量异常之物料是否及时反馈供应商?()
6、有效期的物料是否对其有效期进行监控,及时通知生产使用,以免造成浪费或污染?
()
7、对于超出储存期限的材料再次使用有无相应的验证流程?是否执行?()
8、化学类、危险类物料的安全保护措施是否建立,并能有效的执行?()
9、物料入仓、领料是否有相关记录?()
(二)生产车间(每项1分)
1、生产现场是否有建立作业指导文件,包括生产流程卡,本岗位的生产作业指导书,设备维护保养记录,品质异常处理程序等?()
2、确认设备制造能力,设备是否处于正常运转状态,设备是否有维修保养记录,闲置或异常状况的设备是否有标示?()
3、人员技能,员工是否有经过上岗培训,是否经过考核合格后上岗,是否有相关的培训考核记录?员工是否依据作业指导书进行作业,对本职位产品质量控制标准是否清楚明确?异常状况的发生是否具有应变处理措施等(如重大品质、设备异常处理方法;重大安全隐患的意识和处理等)?()
4、环境,生产环境是否能满足生产之需要,设备的布置是否合理规范便于产品在车间之间进行流转,通道是否畅通,是否满足5S之审核要求,其他如噪音、异味、粉尘等影响身体
健康安全的环境条件是否达标?()5、生产计划单的生产安排,各车间的生产安排是否按照生产计划部统一的调度生产,或依据ERP系统中订单的分类安排生产?()6、生产流程控制,各车间的生产流程是否有序,作业是否规范?首件检查记录是否完整?
()7、产品工序之间的转移控制是否能够有效控制(合格品的下转,不合格品的回转是否有流程卡跟踪,以及其他相关的记录)?()
8、各生产车间是否有本车间加工的控制标准?()
9、各车间对本车间的产品是否订立了直通要求,确认其控制效果的是否有相关的记录?
()10、各车间对本车间的异常情况的处理是否有制定相关的程序文件,异常情况的预防、处理的力度是否执行到位?()11、是否有返工流程?返工区域是否进行标识?返工的不良产品是否被标识和重新转到品质部门重新检验?()12、各车间的生产状况是否达到安全生产之要求?()(三)包装及成品仓库(每项1分)
1、对产品的搬运、储存、包装与交货是否有相应的作业程序?()
2、是否按客户的包装程序要求进行包装?包装是否符合运输安全之要求?包装信息是否符合客户要求?()
3、仓储环境是否能满足产品储存之要求?()
4、摆放、卫生环境是否规范、干净等?()
5、出货是否有相应的出货记录?()
总结:
五、品质保证(共占40.5%)
(一)质量管理体系(每项1分)
1、是否有得到相关的体系认证(如ISO9000、TS16949等)以及其他需要的准入认证(UL、ROHS)等,或基于该类体系要求持续改善品质而建立的品质体系类管理系统?
()2、品质管理系统文件中是否涵盖分级:质量方针和目标、质量手册、程序类文件、作业类文件以及相关的表单记录?()
3、体系类文件是否为受控,是否能确保外来文件得到识别?()
4、是否有制定并有效保存所有的生产品质记录,记录是否清晰标识,以便查阅?
()
5、文件的修改或变更是否能够与现行的修改状态有效识别?()
6、质量目标是否体现质量方针的要求,并已量化?()
7、公司的质量目标是否分解到各部门?()
8、是否根据制定的目标定期对实际达成情况及时作统计分析?对于超出目标的项目是否采。