太阳能硅片切割中薄厚片问题分析
光伏组件的加工工艺及不良分析
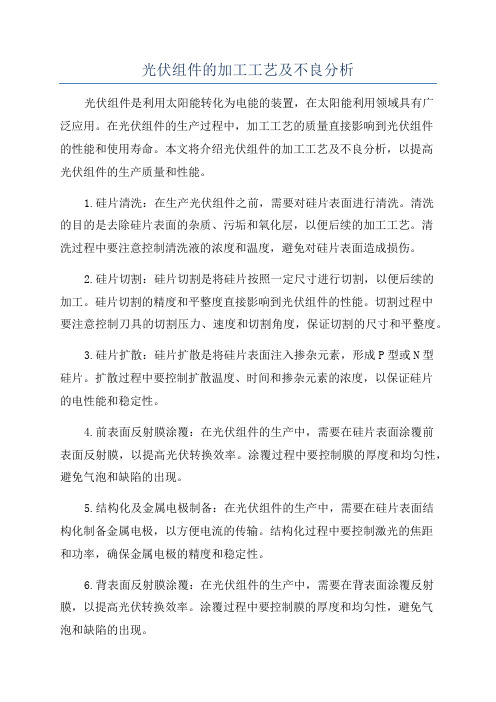
光伏组件的加工工艺及不良分析光伏组件是利用太阳能转化为电能的装置,在太阳能利用领域具有广泛应用。
在光伏组件的生产过程中,加工工艺的质量直接影响到光伏组件的性能和使用寿命。
本文将介绍光伏组件的加工工艺及不良分析,以提高光伏组件的生产质量和性能。
1.硅片清洗:在生产光伏组件之前,需要对硅片表面进行清洗。
清洗的目的是去除硅片表面的杂质、污垢和氧化层,以便后续的加工工艺。
清洗过程中要注意控制清洗液的浓度和温度,避免对硅片表面造成损伤。
2.硅片切割:硅片切割是将硅片按照一定尺寸进行切割,以便后续的加工。
硅片切割的精度和平整度直接影响到光伏组件的性能。
切割过程中要注意控制刀具的切割压力、速度和切割角度,保证切割的尺寸和平整度。
3.硅片扩散:硅片扩散是将硅片表面注入掺杂元素,形成P型或N型硅片。
扩散过程中要控制扩散温度、时间和掺杂元素的浓度,以保证硅片的电性能和稳定性。
4.前表面反射膜涂覆:在光伏组件的生产中,需要在硅片表面涂覆前表面反射膜,以提高光伏转换效率。
涂覆过程中要控制膜的厚度和均匀性,避免气泡和缺陷的出现。
5.结构化及金属电极制备:在光伏组件的生产中,需要在硅片表面结构化制备金属电极,以方便电流的传输。
结构化过程中要控制激光的焦距和功率,确保金属电极的精度和稳定性。
6.背表面反射膜涂覆:在光伏组件的生产中,需要在背表面涂覆反射膜,以提高光伏转换效率。
涂覆过程中要控制膜的厚度和均匀性,避免气泡和缺陷的出现。
7.封装及测试:最后,光伏组件需要进行封装和测试,以确保其性能和稳定性。
封装过程中要注意控制密封材料的温度和压力,确保封装的质量。
测试过程中要对光伏组件的电性能和光电性能进行全面测试,检测不良组件并进行修理处理。
在光伏组件的生产过程中,可能会出现以下不良情况:1.硅片表面损伤:硅片表面在清洗和切割过程中可能会受到损伤,导致硅片的性能降低。
解决方法是加强清洗和切割过程的控制,避免硅片表面的损伤。
2.反射膜气泡:在涂覆反射膜的过程中,可能会出现气泡和缺陷,导致光伏组件的转换效率降低。
影响太阳能硅片切割的因素
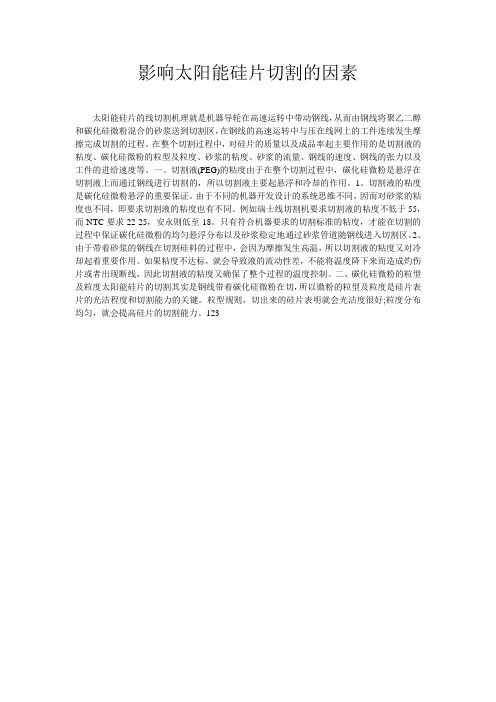
影响太阳能硅片切割的因素
太阳能硅片的线切割机理就是机器导轮在高速运转中带动钢线,从而由钢线将聚乙二醇和碳化硅微粉混合的砂浆送到切割区,在钢线的高速运转中与压在线网上的工件连续发生摩擦完成切割的过程。
在整个切割过程中,对硅片的质量以及成品率起主要作用的是切割液的粘度、碳化硅微粉的粒型及粒度、砂浆的粘度、砂浆的流量、钢线的速度、钢线的张力以及工件的进给速度等。
一、切割液(PEG)的粘度由于在整个切割过程中,碳化硅微粉是悬浮在切割液上而通过钢线进行切割的,所以切割液主要起悬浮和冷却的作用。
1、切割液的粘度是碳化硅微粉悬浮的重要保证。
由于不同的机器开发设计的系统思维不同,因而对砂浆的粘度也不同,即要求切割液的粘度也有不同。
例如瑞士线切割机要求切割液的粘度不低于55,而NTC要求22-25,安永则低至18。
只有符合机器要求的切割标准的粘度,才能在切割的过程中保证碳化硅微粉的均匀悬浮分布以及砂浆稳定地通过砂浆管道随钢线进入切割区。
2、由于带着砂浆的钢线在切割硅料的过程中,会因为摩擦发生高温,所以切割液的粘度又对冷却起着重要作用。
如果粘度不达标,就会导致液的流动性差,不能将温度降下来而造成灼伤片或者出现断线,因此切割液的粘度又确保了整个过程的温度控制。
二、碳化硅微粉的粒型及粒度太阳能硅片的切割其实是钢线带着碳化硅微粉在切,所以微粉的粒型及粒度是硅片表片的光洁程度和切割能力的关键。
粒型规则,切出来的硅片表明就会光洁度很好;粒度分布均匀,就会提高硅片的切割能力。
123。
硅片异常原因
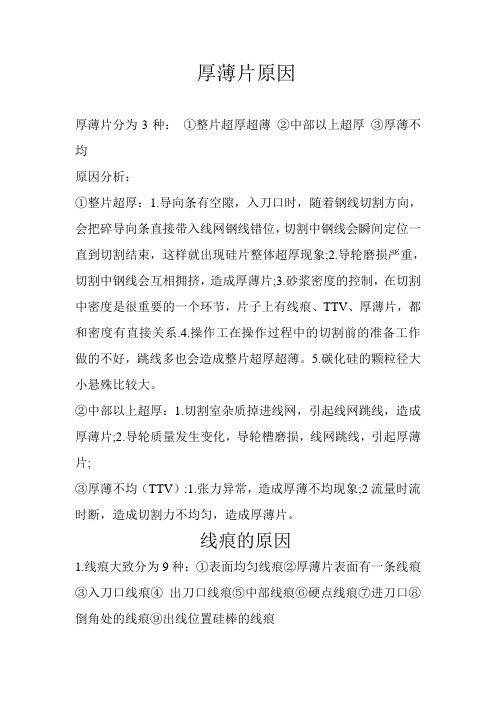
厚薄片原因厚薄片分为3种:①整片超厚超薄②中部以上超厚③厚薄不均原因分析:①整片超厚:1.导向条有空隙,入刀口时,随着钢线切割方向,会把碎导向条直接带入线网钢线错位,切割中钢线会瞬间定位一直到切割结束,这样就出现硅片整体超厚现象;2.导轮磨损严重,切割中钢线会互相拥挤,造成厚薄片;3.砂浆密度的控制,在切割中密度是很重要的一个环节,片子上有线痕、TTV、厚薄片,都和密度有直接关系.4.操作工在操作过程中的切割前的准备工作做的不好,跳线多也会造成整片超厚超薄。
5.碳化硅的颗粒径大小悬殊比较大。
②中部以上超厚:1.切割室杂质掉进线网,引起线网跳线,造成厚薄片;2.导轮质量发生变化,导轮槽磨损,线网跳线,引起厚薄片;③厚薄不均(TTV):1.张力异常,造成厚薄不均现象;2流量时流时断,造成切割力不均匀,造成厚薄片。
线痕的原因1.线痕大致分为9种:①表面均匀线痕②厚薄片表面有一条线痕③入刀口线痕④出刀口线痕⑤中部线痕⑥硬点线痕⑦进刀口⑧倒角处的线痕⑨出线位置硅棒的线痕原因分析:①表面均匀线痕:砂浆更换量不足,钢线带砂量太少,造成没有足够的切割能力,严重摩擦导致均匀线痕,冷却水温度过高,导致均匀线痕;②厚薄片表面有一条线痕:切割中有杂质进入线网,线网瞬间跳线,钢线脱离线槽,造成切割定位,导致厚薄片,在线网瞬间跳线时,钢线在交叉时,与晶棒摩擦造成一道线痕;导轮表面磨损,钢线会挤在一起,砂浆分布不均匀,造成线痕;③入刀口线痕:切割入刀口时,导向条有空隙,硬物进入线网,钢线跳线瞬间会引起线痕;④出刀口均匀线痕:砂浆少更换10~20L,切割快结束后,砂浆的颗粒基本上已经很疲惫了,棱角几乎已经变圆,切割力已经到了疲惫状态,随着钢线不断的磨损,切割力达不到,就会造成出刀口线痕;另外倒角处有残胶,钢线带砂浆经过时残胶阻止砂浆进入也会产生线痕。
⑤中部线痕:切割中,砂浆嘴断流,造成硅片中部线痕;⑥硬点线痕:硅片来料硬点,切割中小硬点可能不会造成线网断线,但钢线切到硬点时,不会与其他位置切割力一样,难免会在硬点处停留数秒,这期间会造成一道线痕;⑦进刀口:由于刚开始切割,钢线处在不稳定状态,钢线的波动产生的线痕;⑧倒角处的线痕:由于在粘结硅棒时底部残留有胶,到倒角处钢线带胶切割引起的线痕;⑨出线位置硅棒的线痕:钢线磨损量大,造成钢线光洁度、圆度不够,携带砂浆数量低,切削能力下降,线膨胀系数增大引起的。
光伏焊带厚度和层压破片关系

光伏焊带厚度和层压破片关系光伏焊带是光伏组件生产中的重要材料,其厚度与层压破片之间存在一定的关系。
本文将从光伏焊带的作用、厚度对焊接质量的影响,以及焊带厚度与层压破片的关系等方面进行探讨。
一、光伏焊带的作用光伏焊带主要用于连接太阳能电池片,起到导电和固定的作用。
焊带的材料和厚度直接影响到焊接质量和光伏组件的性能。
一般来说,焊带材料应具有导电性好、耐腐蚀、强度高等特点,以保证光伏组件的稳定运行。
二、厚度对焊接质量的影响1.厚度过大:当焊带厚度过大时,焊接过程中容易导致电池片受热不均匀,出现虚焊、脱焊等问题。
这不仅影响焊接质量,还可能降低光伏组件的发电效率。
2.厚度过小:当焊带厚度过小时,焊接过程中容易出现焊带熔断、焊接不牢固等问题。
这将导致电池片之间的连接不可靠,容易出现电池片脱落、断路等故障。
三、焊带厚度与层压破片的关系层压破片是指在光伏组件层压过程中,由于各种原因导致组件内部出现裂纹或破损的现象。
焊带厚度与层压破片的关系主要表现在以下几个方面:1.焊带厚度过大时,焊接过程中产生的热量较多,可能导致电池片与背板之间的EVA胶膜熔化过多,使组件内部应力分布不均,从而增加层压破片的风险。
2.焊带厚度过小时,焊接强度不足,可能导致电池片在层压过程中发生移位或脱落,进而引发层压破片。
3.合适的焊带厚度可以保证焊接质量和组件性能的稳定。
在选择焊带时,应根据电池片的厚度、焊接工艺和组件设计要求等因素进行综合考虑,以确保焊带厚度适中,降低层压破片的风险。
四、结论与建议通过对光伏焊带厚度与层压破片关系的探讨,我们可以得出以下结论与建议:1.选择合适的焊带厚度对保证焊接质量和降低层压破片风险至关重要。
在选择焊带时,应综合考虑电池片的厚度、焊接工艺和组件设计要求等因素。
2.加强焊接过程的监控与控制,确保焊接质量稳定可靠。
通过优化焊接工艺参数、提高操作人员技能水平等措施,降低虚焊、脱焊等问题的发生率。
3.在光伏组件生产过程中,应严格控制各个环节的工艺质量,以减少层压破片的风险。
硅片存在的问题及解决方法

硅片厚薄不均原因分析
环境
地面共振
车间温湿度变化大 导向条质量
辅料
槽距不均匀 小滑轮槽 距不均匀 无 切片机张力 不稳定
人员
树脂导向条错位,未放过滤袋/过滤网
工件和托板/工件夹紧螺丝未拧紧
线径不均匀
使用搅拌时间不到的砂浆
厚薄不 均
砂浆配置比例 主辊/导轮质量问题
工艺设计不科学
二次切割程序
工艺入门
切片工艺是设备(包括设备状态和设备准备),切割材料和基于耗材的切 割条件的综合。为确保好的切割和保持尽可能高的收率,就必须认真对待 下面每一步。
设备准备 砂浆 操作人
收率
硅块
钢线
Page 1
不同工艺参数的影响
回收砂浆
悬浮液 硅片厚度 温度 砂子粒径 TTV
线痕
砂浆流量
进给速率 设备稳定性
钢线磨损度
Page 3
花污片原因分析
环境
超纯水
辅料
柠檬酸 草 酸 乳酸 责任心差
人员
不遵守时间
违规脱胶 违规清洗
回收液质量
清洗剂质量
酸的更换量
花污片
超声波衰减
清洗剂更换量 温控不准确 预冲洗喷淋管 堵塞
自来水压力泵 时间控制器
清洗剂PLC控制系统
工艺
仪器
机器
Page 4
花污片预防和返工措施
1. 切割液掺有次氯酸,特别是回收液,对硅片腐蚀特别严重。(请品管 部门分析切割 液的成分) 2. 预冲洗的水压(2.5MPa),水质(中水),流量(5000l/h),角度(10),冲洗时 间(30-40min)等,总之预冲洗要硅片表面无明显脏污,才能进入脱胶 3. 脱胶时尽量全泡,水温50-60℃,加3%的草酸或柠檬酸或乳酸,自然倒伏。 4. 脱胶插片完毕,25-30℃纯水中超声10分钟,超声功率在2000w左右,水要循环。 (插片槽改成具有超声功能) 5. 清洗剂(不同厂家)大部分都是重量比为5%的比例,温度设为60℃,超声3-5分钟。 6. 关键是员工有没有执行和我们提供的设备工具能否满足需要. 7. 如果是个老厂,突然出现花污片了一般要在辅料上找问题(切割液 清洗液 回收液等). 8. 更换时一定要用标准容器,更换量视故硅片规格和数量而定.一般6和6.5寸8000pcs全换 一次,4000pcs时更换一半. 9. 污片返工关键技术:直接经过两槽清洗剂槽,时间3分钟,两槽纯水槽5分钟;花片返工关键 技术:0.2%的氢氟酸100l纯水,浸泡1分钟,先过纯水,再过清洗剂槽。合格率极低。 另外也可采用快速极冷法物理剥离赃物和硅片。
硅片薄厚片问题

一、概况切片工序是制备太阳能硅片的一道重要工序,太阳能硅片的切割原理是转动的钢线上携带着大量碳化硅颗粒,同时工作台位置缓慢下降,由于碳化硅的硬度大于多晶硅(晶体硅的莫氏硬度为6.5,碳化硅的莫氏硬度为9.5),依靠碳化硅的棱角不断地对硅块进行磨削,起到切割作用。
薄厚片是衡量硅片品质的一个很重要的指标。
薄厚片的存在会影响硅片合格率及电池片的生产工艺,因此这对硅片品质提出了更加严格的要求。
二、硅片厚度产生偏差的原理硅片的切割过程是在导轮上完成的,钢线在导轮上缠绕形成相互平行的均匀线网,并以10-15m/s的速度运动,砂浆经浆料嘴均匀地流到线网,砂浆中的碳化硅由于悬浮液的悬浮作用裹覆在钢线上,对硅块进行切割。
但是随着切割的进行,钢线和碳化硅都会出现不同程度地磨损,钢线的椭圆度增大,携砂能力下降,同时碳化硅的圆度变大,平均粒径减小,切割能力也有所降低,因此,通常在平行工作台运动的方向,硅片入刀点厚度小于出刀点厚度;而和硅块运动方向垂直的方向上,硅片入线侧厚度小于出线侧厚度。
硅片厚度有一定的偏差范围,对于180μm厚度的硅片,其偏差范围为±20μm,超过此范围则成为不良品--薄厚片。
从根本上讲,薄厚片的产生都是由于各种问题导致线网抖动而造成的。
三、薄厚片原因分析薄厚片可分为两大类:(1)TV(ThicknessVariation厚度偏差),主要指硅片与硅片之间相同位置之间的厚度偏差,通常存在于同一锯硅片中。
(2)TTV(TotalThicknessVariation整体厚度偏差),指同一片硅片上最厚位置与最薄位置之间的偏差。
薄厚片根据其在硅片内的分布位置可以分为四类:整片薄厚(TV);入刀点薄厚(TTV);硅片中部至出刀点薄厚(TTV);单片薄厚不均(TTV)。
其产生原因分析如下:(1)整片薄厚:a.导轮槽距不均匀。
硅片厚度=槽距-钢线直径-4倍的(碳化硅)D50,根据所需的硅片厚度要求,可以计算出最佳槽距。
硅片解决方案

硅片解决方案硅片解决方案是指针对硅片生产和应用过程中的问题,提出的一系列解决方案。
硅片是半导体材料的基础,广泛应用于电子、光电、太阳能等领域。
为了提高硅片的质量和生产效率,我们需要制定一套完善的硅片解决方案。
一、硅片生产过程中的问题及解决方案1.问题:硅片表面质量不佳解决方案:优化硅片表面处理工艺,采用先进的抛光和清洗技术,确保硅片表面的平整度和洁净度。
同时,引入自动化设备,减少人为操作对硅片表面的影响。
2.问题:硅片晶格缺陷严重解决方案:改进硅片生长技术,控制晶格缺陷的生成。
采用先进的晶体生长设备和工艺,提高硅片的结晶质量。
同时,加强对硅片生长过程中的温度、压力等参数的控制,减少晶格缺陷的产生。
3.问题:硅片厚度不均匀解决方案:优化硅片切割工艺,确保硅片厚度的均匀性。
采用先进的切割设备和工艺,控制切割参数,减少硅片厚度的偏差。
同时,加强对硅片切割过程中的加工温度和刀具磨损情况的监控,及时调整工艺参数。
二、硅片应用过程中的问题及解决方案1.问题:硅片在高温环境下易发生热应力破裂解决方案:改进硅片材料的制备工艺,提高硅片的热稳定性。
采用掺杂和合金化等方法,增强硅片的抗热应力破裂能力。
同时,加强对硅片在高温环境下的应力分析和模拟,优化硅片的结构设计。
2.问题:硅片在光电器件中易发生光衰减解决方案:改进硅片的光学特性,提高硅片的光传输效率。
采用表面纳米结构化和光学涂层等技术,增强硅片的光吸收和光耦合能力。
同时,加强对硅片光学性能的测试和评估,确保硅片在光电器件中的稳定性和可靠性。
3.问题:硅片在太阳能电池中的转化效率低解决方案:改进硅片的太阳能转化效率,提高太阳能电池的发电能力。
采用多晶硅和单晶硅等高效硅片材料,优化硅片的能带结构和电子传输性能。
同时,加强对硅片太阳能电池的工艺流程和参数的优化,提高硅片的光电转换效率。
以上是关于硅片解决方案的一些内容,通过优化硅片生产工艺和改进硅片材料性能,可以提高硅片的质量和应用效果。
太阳能光伏组件常见质量问题现象及分析

虚焊、过焊
虚焊、过焊原因
1.焊接温度过多或助焊剂涂抹过少或速度 过快会导致虚焊
2.焊接温度过高或焊接时间过长会导致过 焊现象. 组件影响:
1.虚焊在短时间出现焊带与电池片脱层, 影响组件功率衰减或失效, 2.过焊导致电池片内部电极被损坏,直接
影响组件功率衰减降低组件寿命或造成
报废 预防措施:
1.确保焊接机温度、助焊剂喷射量和焊接 时间的参数设定. 并要定期检查, 2.返修区域要确保烙铁的温度、焊接时间 和使用正确的助焊笔涂抹助焊剂. 3.加强EL检验力度,避免不良漏失下一 工序.
• 4、All that you do, do with your might; things done by halves are never done right. ----R.H. Stoddard, American poet做一切事都应尽力而为,半途而废永远不行6.17.20216.17.202110:5110:5110:51:1910:51:19
焊带偏移或焊接后翘曲破片
焊带偏移或焊接后翘曲破片原因 1.焊接机定位出现异常会造成焊带偏 移现象 2.电池片原材主栅线偏移会造成焊接 后焊带与主栅线偏移 3.温度过高焊带弯曲硬度过大导致焊 接完后电池片弯曲 组件影响: 1.偏移会导致焊带与电池面积接触减 少,出现脱层或影响功率衰减 2.过焊导致电池片内部电极被损坏, 直接影响组件功率衰减降低组件寿命 或造成报废 3.焊接后弯曲造成电池片碎片 预防措施: 1.定期检查焊接机的定位系统. 2.加强电池片和焊带原材料的来料检 验,
电池裂片
电池裂片原因
1.焊接过程中操作不当造成裂片 2.人员抬放时手法不正确造成组件裂片 3.层压机故障出现组件类片 组件影响:
太阳能切割技术详解
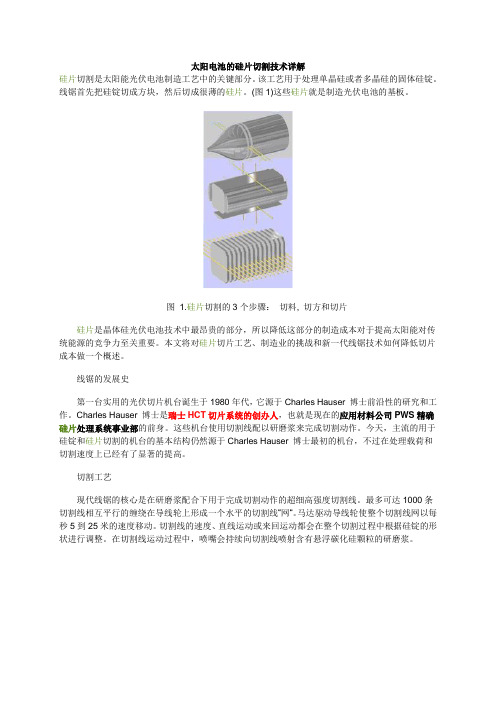
太阳电池的硅片切割技术详解硅片切割是太阳能光伏电池制造工艺中的关键部分。
该工艺用于处理单晶硅或者多晶硅的固体硅锭。
线锯首先把硅锭切成方块,然后切成很薄的硅片。
(图1)这些硅片就是制造光伏电池的基板。
图1.硅片切割的3个步骤:切料, 切方和切片硅片是晶体硅光伏电池技术中最昂贵的部分,所以降低这部分的制造成本对于提高太阳能对传统能源的竞争力至关重要。
本文将对硅片切片工艺、制造业的挑战和新一代线锯技术如何降低切片成本做一个概述。
线锯的发展史第一台实用的光伏切片机台诞生于1980年代,它源于Charles Hauser 博士前沿性的研究和工作。
Charles Hauser 博士是瑞士HCT切片系统的创办人,也就是现在的应用材料公司PWS精确硅片处理系统事业部的前身。
这些机台使用切割线配以研磨浆来完成切割动作。
今天,主流的用于硅锭和硅片切割的机台的基本结构仍然源于Charles Hauser 博士最初的机台,不过在处理载荷和切割速度上已经有了显著的提高。
切割工艺现代线锯的核心是在研磨浆配合下用于完成切割动作的超细高强度切割线。
最多可达1000条切割线相互平行的缠绕在导线轮上形成一个水平的切割线“网“。
马达驱动导线轮使整个切割线网以每秒5到25米的速度移动。
切割线的速度、直线运动或来回运动都会在整个切割过程中根据硅锭的形状进行调整。
在切割线运动过程中,喷嘴会持续向切割线喷射含有悬浮碳化硅颗粒的研磨浆。
图2. 硅块通过切割线组成的切割网.硅块被固定于切割台上,通常一次4块。
切割台垂通过运动的切割线切割网,使硅块被切割成硅片(图2)。
切割原理看似非常简单,但是实际操作过程中有很多挑战。
线锯必须精确平衡和控制切割线直径、切割速度和总的切割面积,从而在硅片不破碎的情况下,取得一致的硅片厚度,并缩短切割时间。
减少硅料消耗对于以硅片为基底的光伏电池来说,晶体硅(c-Si)原料和切割成本在电池总成本中占据了最大的部分。
光伏电池生产商可以通过在切片过程中节约硅原料来降低成本。
隐裂分析

杨宏 西安交通大学 2011-5-29
一、薄片化是晶体硅太阳电池的发 展方向
薄片化导致的问题及结果 330um→240 → 200 → 180 → 150 → 120 碎裂原因:(1)O、C and N,causing wire breaking (2)caused by wire sawing(14um30um) (3) caused by handling 高应力工艺如:烧结、焊接及层压未必损坏硅片, 但产生的应力能传播裂纹。 结果:电池线及组件线碎片率过高
28
57.拿硅片承载盒时,不小心将硅片撞碎 58.吸笔垫损坏,粘住硅片 59.弯曲片,容易掉片
60.返工片点片时容易数碎片子
61.注意力不集中,碎片
62.工作中受到外界的干扰,导致碎片
63.由于吸笔与人不协调,导致碎片
29
5 丝网印刷
1.上料时吸碎 2.行走臂走歪,员工没看见,卡碎。 3.员工在擦片时,用力不当,擦碎。 4.台面有小碎片,员工没及时发现,压碎。 5.烧结后吸片,员工不小心碰碎。 6.粘版时,员工技能不过关,取片时,取碎。 7.在更换网版后,机器参数调整不当,印刷碎。 8.员工在取片称重时,没放好撞碎。 9.碎片没清理干净,导致卡碎其他片子。 10.翻转速度快,翻碎。 11.铝背场有异物,没发现,印刷碎。 12.清理烘箱时,不小心碰碎。 13.卡口松动,卡碎。 14.烘箱抓手不平,抓碎。 15.行走臂上胶带翘起,带碎片子 16.下料时带片子,叠片碎。
四、各工艺环节如何避免对硅片造 成损伤
1 硅片检验 (1)轻拿轻放; (2)不许整理时在桌面上磕碰; (3)不许堆叠过高。
2 装片清洗
1.装片员工在打开包装盒时刀片划得过深,划到硅片产生碎片; 2.装片过程在承载盒下方未放海绵,产生裂纹或碎片; 3.吸力过大; 4 装片员工装片速度过快产生裂纹或碎片; 5.制绒,清洗员工在投片时,承载盒撞到花篮产生碎片; 6.制绒人员在观察绒面,取片时拿碎; 7.制绒人员在测减薄量时拿碎; 8.单晶制绒时员工在给已制绒硅片洒水前未确认喷头的喷雾状态,冲碎硅片; 9.承载盒放入甩干机时未放到位,甩碎硅片; 10.员工从甩干机内拿已甩干的硅片时手会碰碎硅片; 11.员工在往甩干机内放硅片时会撞到甩干机固定螺钉或内壁,撞碎硅片; 12.员工在往甩干机内放硅片时,没有对称受力不均,甩碎硅片; 13.员工带着情绪工作,产生人为碎片; 14.制绒后漂洗第一个槽子水的温度要稍高。
金刚线切割太阳能薄片实验总结
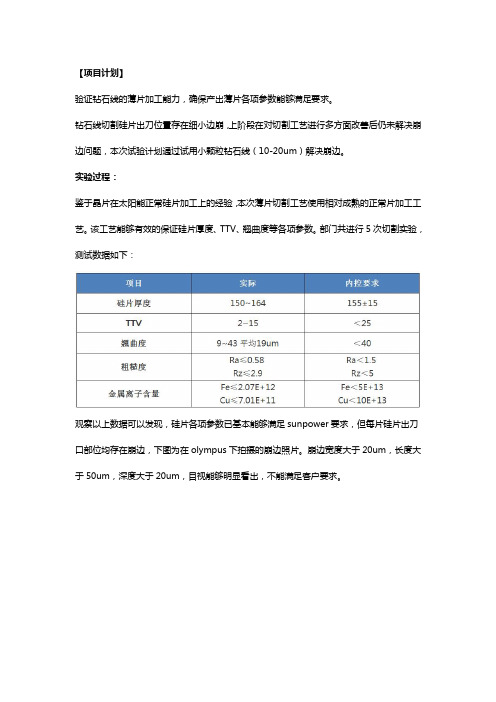
【项目计划】验证钻石线的薄片加工能力,确保产出薄片各项参数能够满足要求。
钻石线切割硅片出刀位置存在细小边崩,上阶段在对切割工艺进行多方面改善后仍未解决崩边问题,本次试验计划通过试用小颗粒钻石线(10-20um)解决崩边。
实验过程:鉴于晶片在太阳能正常硅片加工上的经验,本次薄片切割工艺使用相对成熟的正常片加工工艺。
该工艺能够有效的保证硅片厚度、TTV、翘曲度等各项参数。
部门共进行5次切割实验,测试数据如下:观察以上数据可以发现,硅片各项参数已基本能够满足sunpower要求,但每片硅片出刀口部位均存在崩边,下图为在olympus下拍摄的崩边照片。
崩边宽度大于20um,长度大于50um,深度大于20um,目视能够明显看出,不能满足客户要求。
崩边产生原因分析:由于硅片较薄,单晶切割至出刀口位置时,硅片抖动幅度较大,造成出刀口损伤。
钻石线切割时存在线弓,线运行时发生横向摆动,损伤硅棒。
切割至末尾时,单晶受线弓应力。
钻石线切割能力强,应力瞬间释放造成硅片损伤。
由于粘接胶的硬度小于单晶,从微观上看,钻石线在切割至粘接胶时,线弓瞬间降低,导致硅片该点被金刚石颗粒挂伤,造成崩边。
方案实施情况:效果分析:降低流量:钻石线工艺要求流量较大,但过大的流量冲击在硅片上导致硅片震动幅度加大。
降低流量可有效的减少震动,改善效果比较明显,但未能解决崩边。
降低线速度:降低出刀位置线运行速度,线切割能力下降,导致线弓增大。
另外,线运行速度与线的横向摆幅之间并非简单的正比关系,降低线速不一定能够减少摆动。
降低工作台下降速度:降低下降速度后,线弯曲度降低了约0.5mm左右,降幅15%。
线弓改善比较明显,但对崩边的改善效果并不明显。
斜向切割:观察前几刀切割情况发现,硅片入线、出线端很少出线崩边,斜切方式能够使进线面积最大化。
但本次实验完成后发现约有20%的硅片出刀圆弧面存在严重角崩,可能为线弓瞬间降低将硅片圆弧角挂伤。
并且粘接面仍然存在少量崩边,崩边问题未能解决。
硅片厚度对电池性能影响

硅片厚度对多晶硅太阳电池性能的影响摘要:为了进一步降低多晶硅太阳电池的成本,研究了硅片厚度对多晶硅太阳电池的短路电流密度、开路电压和效率的影响。
可以看出,在保证多晶硅太阳电池性能不变或者提高的前提下,硅片厚度可以减小到200μm,如果继续减小厚度,电池的性能将会下降。
1.引言提高太阳电池的光电转换效率和降低成本是太阳电池研究的主要方向,薄膜太阳电池能够大幅度降低材料的用量,是降低太阳电池成本最有效的手段。
多晶硅(mc-Si)太阳电池在2005年的世界太阳能电池市场中占的份额是58%。
所以,在保证太阳电池性能不变甚至提高的前提下,减少mc-Si太阳电池硅片厚度对降低光伏能源的成本具有重要意义。
2.硅片厚度对短路电流密度Jsc的影响当使用更薄的多晶硅片时,要面临的一个问题是表面的复合与基区的材料质量。
已经有实验证实,在使用SiNx作为前表面钝化层和Al作为背面场(BSF)时,当多晶硅片厚度大于200μm,Jsc与硅片厚度是相互独立的关系,只有硅片厚度小于200μm,Jsc才随着厚度的减少而减少。
BSF能阻碍光生少子向背表面运动,降低背表面复合,有利于p/n结对载流子的收集。
厚度低时,基体对入射光的吸收减少,此时BSF对太阳电池的短路电流密度的影响就更明显。
SiNx作为前表面钝化层可以降低表面复合并且提高基区材料的质量。
但是,当硅片厚度很低时,很多低能量光子将穿过硅片而不能被吸收,Jsc会出现降低的趋势。
3.硅片厚度对开路电压Voc的影响在mc-Si太阳电池的背面使用A1-BSF时,如果硅片厚度大于200μm,开路电压Voc与硅片厚度就是独立的关系。
Voc是温度T、光生电流JL(理想隋况下它等于Jsc)还有饱和电流Jo的函数:一个硅太阳电池的饱和电流Jo取决于有效的复合速度。
基区对于饱和电流的作用可以表示为:4.硅片厚度效率的影响在硅片厚度大于200μm时,使用Al-BSF的mc-Si太阳电池的效率是与硅片厚度相互独立的。
多晶硅太阳能电池组件层压过程常见不良现象原因及分析

下面是实际生产中经常遇到的一些问题。
提出问题:1、组件中有碎片。
2、组件中有气泡。
3、组件中有毛发及垃圾。
4、汇流条向内弯曲。
5、组件背膜凹凸不平。
问题分析:1、组件中有碎片,可能造成的原因:1、由于在焊接过程中没有焊接平整,有堆锡或锡渣,在抽真空时将电池片压碎。
2、本来电池片都已经有暗伤,再加上层压过早,EVA 还具有很良好的流动性。
3、在抬组件的时候,手势不合理,双手已压到电池片。
2、组件中有气泡,可能造成的原因:1、EVA 已裁剪,放置时间过长,它已吸潮。
2、EVA 材料本身不纯。
3、抽真空过短,加压已不能把气泡赶出。
4、层压的压力不够。
5、加热板温度不均,使局部提前固化。
6、层压时间过长或温度过高,使有机过氧化物分解,产出氧气。
7、有异物存在,而湿润角又大于90°,使异物旁边有气体存在。
3、组件中有毛发及垃圾,可能造成的原因:1、由于EVA、DNP、小车子有静电的存在,把飘着空的头发,灰尘及一些小垃圾吸到表面。
2、叠成时,身体在组件上方作业,而又不能保证身体没有毛发及垃圾的存在。
3、一些小飞虫子死命的往组件中钻。
4、汇流条向内弯曲,可能造成的原因:1、在层压中,汇流条位置会聚集比较多的气体。
胶板往下压,把气体从组件中压出,而那一部分空隙就要由流动性比较好EVA 来填补。
EVA 的这种流动,就把原本直的汇流条压弯。
2、EVA 的收缩。
5、组件背膜凹凸不平,可能造成的原因:1、多余的EVA 会粘到高温布和胶板上。
问题解决:1、组件中有碎片:①、首先要在焊接区对焊接质量进行把关,并对员工进行一些针对性的培训,使焊接一次成型。
②、调整层压工艺,增加抽真空时间,并减小层压压力(通过层压时间来调整)。
③、控制好各个环节,优化层压人员的抬板的手势。
2、组件中有气泡:①、控制好每天所用的EVA 的数量,要让每个员工了解每天的生产任务。
②、材料是由厂家所决定的,所以尽量选择较好的材料。
③、调整层压工艺参数,使抽真空时间适量。
单多晶太阳能硅片切割线痕问题研究

单多晶太阳能硅片切割线痕问题研究江国中在半导体行业和太阳能光伏行业中,硅棒的切割都是非常重要的一道工序,硅片质量的好坏直接关系到后续工序的制造和加工。
在众多影响硅片表面质量的问题中,线痕是最让硅片切割企业头疼的问题之一。
半导体行业对硅片表面质量要求比较高,但是线痕并不是其大问题,因为相对而言,半导体行业的硅片较厚,切割过后的抛光研磨过程可以去除线痕;而太阳能光伏行业的硅片非常薄,并且整个行业原料相对紧缺,不可能把硅料浪费在研磨损失上,再者增加研磨工艺就要增加成本,因此研磨工艺在太阳能行业是不适用的。
所以,了解线切割过程硅片线痕产生的原因,来减少线痕片的产生,是非常有必要的。
1线痕分类线痕按照形状分为单一线痕、硬质点线痕和均匀线痕。
单一线痕,有深有浅,若线痕较小还是可以接受为合格片。
由于多晶硅铸锭的原料和工艺原因,多晶锭内部多少都会有SiC和Si3N4杂质,切割完成后,就会形成形状类似单一线痕。
均匀线痕体现为整个或者部分硅片表面出现多条由深至浅状似划伤的线痕。
对于多晶硅来说,三种情况都存在;对于单晶来说,线痕只有均匀线痕和单一线痕[1]。
2单一线痕造成单一线痕的原因有很多种因素,主要有:(1)停机。
切割机有时在某些警报下会自动停机,比如:砂浆流量过低,冷却液异常,电气柜温度过高;有时也需要人为停机,比如:雷电天气致供电电压不稳,排线机构异常,突发紧急状况。
机器停止再重新启动后,由于导论心震,钢线不能完全按照原位置切割,就产生了线痕。
(2)断线。
断线后的晶棒即使能够挽救回来,但是由于停机,硅片上也会产生线痕。
产生断线的原因主要有:①张力问题。
a.收放线端排线不均匀,造成“一侧坑一侧包”的状况,钢线运动到两侧时张力急剧跳动,造成断线;张力臂由于长时间未清理,粘附砂浆过多,造成张力臂过重,调节灵敏度降低;b.张力臂转轴部分被砂浆堵塞,造成摆动不畅,都可以导致断线;c.钢线生产时产生线头穿错,也称为压线,极易造成断线;d.张力检测设备故障或由于长时间使用,张力检测值形成偏差,从而形成断线;e.钢线走线导轮磨损严重,造成钢线剧烈波动,张力不稳,导致断线。
太阳能硅片切割中薄厚片问题分析

太阳能硅片切割中薄厚片问题分析摘要:在太阳能硅片生产过程中,薄厚片的存在会影响产品的合格率,同时会影响电池片的生产工艺。
本文主要对太阳能硅片产生薄厚片的原因进行了分析,以更好地降低和避免薄厚片的产生。
1.引言切片工序是制备太阳能硅片的一道重要工序,太阳能硅片的切割原理是转动的钢线上携带着大量碳化硅颗粒,同时工作台位置缓慢下降,由于碳化硅的硬度大于多晶硅(晶体硅的莫氏硬度为6.5,碳化硅的莫氏硬度为9.5),依靠碳化硅的棱角不断地对硅块进行磨削,起到切割作用。
薄厚片是衡量硅片品质的一个很重要的指标。
薄厚片的存在会影响硅片合格率及电池片的生产工艺,因此这对硅片品质提出了更加严格的要求。
2.硅片厚度产生偏差的原理硅片的切割过程是在导轮上完成的,钢线在导轮上缠绕形成相互平行的均匀线网,并以10-15m/s的速度运动,砂浆经浆料嘴均匀地流到线网,砂浆中的碳化硅由于悬浮液的悬浮作用裹覆在钢线上,对硅块进行切割。
但是随着切割的进行,钢线和碳化硅都会出现不同程度地磨损,钢线的椭圆度增大,携砂能力下降,同时碳化硅的圆度变大,平均粒径减小,切割能力也有所降低,因此,通常在平行工作台运动的方向,硅片入刀点厚度小于出刀点厚度;而和硅块运动方向垂直的方向上,硅片入线侧厚度小于出线侧厚度。
硅片厚度有一定的偏差范围,对于180μm厚度的硅片,其偏差范围为±20μm,超过此范围则成为不良品--薄厚片。
从根本上讲,薄厚片的产生都是由于各种问题导致线网抖动而造成的。
3.薄厚片原因分析薄厚片可分为两大类:(1)TV(ThicknessVariation厚度偏差),主要指硅片与硅片之间相同位置之间的厚度偏差,通常存在于同一锯硅片中。
(2)TTV (TotalThicknessVariation整体厚度偏差),指同一片硅片上最厚位置与最薄位置之间的偏差。
薄厚片根据其在硅片内的分布位置可以分为四类:整片薄厚(TV);入刀点薄厚(TTV);硅片中部至出刀点薄厚(TTV);单片薄厚不均(TTV)。
太阳能晶棒切斜问题分析
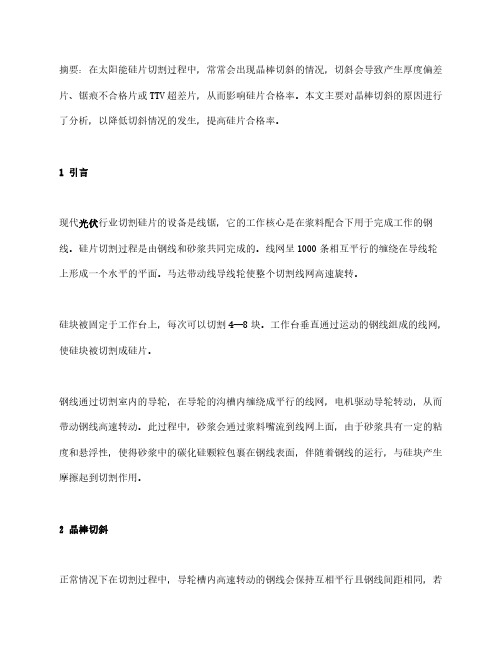
摘要:在太阳能硅片切割过程中,常常会出现晶棒切斜的情况,切斜会导致产生厚度偏差片、锯痕不合格片或TTV超差片,从而影响硅片合格率。
本文主要对晶棒切斜的原因进行了分析,以降低切斜情况的发生,提高硅片合格率。
1引言
现代光伏行业切割硅片的设备是线锯,它的工作核心是在浆料配合下用于完成工作的钢线。
硅片切割过程是由钢线和砂浆共同完成的。
线网呈1000条相互平行的缠绕在导线轮上形成一个水平的平面。
马达带动线导线轮使整个切割线网高速旋转。
硅块被固定于工作台上,每次可以切割4—8块。
工作台垂直通过运动的钢线组成的线网,使硅块被切割成硅片。
钢线通过切割室内的导轮,在导轮的沟槽内缠绕成平行的线网,电机驱动导轮转动,从而带动钢线高速转动。
此过程中,砂浆会通过浆料嘴流到线网上面,由于砂浆具有一定的粘度和悬浮性,使得砂浆中的碳化硅颗粒包裹在钢线表面,伴随着钢线的运行,与硅块产生摩擦起到切割作用。
2晶棒切斜
正常情况下在切割过程中,导轮槽内高速转动的钢线会保持互相平行且钢线间距相同,若
钢线受力的作用发生位错,摆动异常,钢线间距不均匀,则该位置的晶棒会出现切斜。
切斜导致产生大量厚度偏差片、锯痕不合格片或TTV超差片,硅片本身厚度有一定的标准浮动范围,一般来说对于厚度为180μm的硅片,其偏差范围为±20μm,超过此范围则成为薄厚片,薄厚片的产生会影响硅片的合格率及电池片的生产工艺。
- 1、下载文档前请自行甄别文档内容的完整性,平台不提供额外的编辑、内容补充、找答案等附加服务。
- 2、"仅部分预览"的文档,不可在线预览部分如存在完整性等问题,可反馈申请退款(可完整预览的文档不适用该条件!)。
- 3、如文档侵犯您的权益,请联系客服反馈,我们会尽快为您处理(人工客服工作时间:9:00-18:30)。
太阳能硅片切割中薄厚片问题分析
在太阳能硅片生产过程中,薄厚片的存在会影响产品的合格率,同时会影响电池片的生产工艺。
本文主要对太阳能硅片产生薄厚片的原因进行了分析,以更好地降低和避免薄厚片的产生。
1.引言
切片工序是制备太阳能硅片的一道重要工序,太阳能硅片的切割原理是转动的钢线上携带着大量碳化硅颗粒,同时工作台位置缓慢下降,由于碳化硅的硬度大于多晶硅(晶体硅的莫氏硬度为6.5,碳化硅的莫氏硬度为9.5),依靠碳化硅的棱角不断地对硅块进行磨削,起到切割作用。
薄厚片是衡量硅片品质的一个很重要的指标。
薄厚片的存在会影响硅片合格率及电池片的生产工艺,因此这对硅片品质提出了更加严格的要求。
2.硅片厚度产生偏差的原理
硅片的切割过程是在导轮上完成的,钢线在导轮上缠绕形成相互平行的均匀线网,并以
10-15m/s的速度运动,砂浆经浆料嘴均匀地流到线网,砂浆中的碳化硅由于悬浮液的悬浮作用裹覆在钢线上,对硅块进行切割。
但是随着切割的进行,钢线和碳化硅都会出现不同程度地磨损,钢线的椭圆度增大,携砂能力下降,同时碳化硅的圆度变大,平均粒径减小,切割能力也有所降低,因此,通常在平行工作台运动的方向,硅片入刀点厚度小于出刀点厚度;而和硅块运动方向垂直的方向上,硅片入线侧厚度小于出线侧厚度。
硅片厚度有一定的偏差范围,对于180μm厚度的硅片,其偏差范围为±20μm,超过此范围则成为不良品--薄厚片。
从根本上讲,薄厚片的产生都是由于各种问题导致线网抖动而造成的。
3.薄厚片原因分析
薄厚片可分为两大类:(1)TV(ThicknessVariation厚度偏差),主要指硅片与硅片之间相同位置之间的厚度偏差,通常存在于同一锯硅片中。
(2)TTV(TotalThicknessVariation 整体厚度偏差),指同一片硅片上最厚位置与最薄位置之间的偏差。
薄厚片根据其在硅片内的分布位置可以分为四类:整片薄厚(TV);入刀点薄厚(TTV);硅片中部至出刀点薄厚(TTV);单片薄厚不均(TTV)。
其产生原因分析如下:
(1)整片薄厚:
a.导轮槽距不均匀。
硅片厚度=槽距-钢线直径-4倍的(碳化硅)D50,根据所需的硅片厚度要求,可以计算出最佳槽距。
此外由于在切割过程中,钢线会磨损,钢线直径变小,且端口由圆形变为椭圆形,因此导轮槽距需要根据线损情况进行补偿,以保证硅片厚度均匀。
b.切割前未设好零点。
正确设置零点的方法是(以HCT机床为例):将晶棒装载入机床后,手动降工作台使四条晶棒的导向条刚刚接触线网并点击触摸屏主界面设零点按钮,然后慢速将工作台升至-1.5mm位置真正设零点并命名切割编号。
如果零点位置设置不当,导向条接触到线网,则在切割开始后钢线由于受摩擦力作用张力不稳,导致从入刀开始即产生整片薄厚。
c.导向条与硅块之间留有缝隙,切割开始后,随着钢线的运行,部分碎导向条被带入线网,钢线错位,由于钢线在切割过程中会瞬间定位,这样就造成硅片整片薄厚的现象。
d.导轮槽磨损严重。
导轮涂层为聚氨酯材料,切割一定刀数后导轮槽根部磨损严重,导轮槽切偏,切割过程中钢线在导轮槽内由于左右晃动导致产生整片薄厚。
解决措施:a.导轮开槽后检查槽距是否均匀,且要根据线损情况对导轮槽距进行补偿。
a.设置零点时,控制好导向条距离线网的位置。
b.规范粘胶操作。
硅块表面粘接导向条时,注意检查导向条是否弯曲,胶水是否涂抹均匀,保证粘接导向条后导向条与硅块之间不能有缝隙。
c.导轮使用过程中,定期使用光学投影轮廓仪对导轮槽进行检测,观察导轮槽深、角度,发现导轮槽磨损严重时则及时更换导轮。
(2)入刀点薄厚:(在硅片上出现薄厚的位置通常为入刀点至向上延伸6mm的区域)a.工作台垫板更换错误。
更换新导轮时,要根据导轮的直径更换工作台垫板(垫板厚度为305mm
减去导轮直径长度),垫板厚度错误会导致在设零点时,上工作台的两条晶棒与下工作台的两条晶棒距离线网高度不一致,导致入刀时线网不平稳。
b.入刀阶段砂浆流量大。
由于入刀时钢线处于不稳定状态,砂浆流量大会对线网造成冲击,钢线抖动,产生入刀薄厚片。
解决措施:a.根据导轮直径,更换厚度值相当的垫板。
b.调整入刀阶段砂浆流量工艺,控制好砂浆温度和砂浆流量,减少对线网的冲击力。
(3)硅片中部至出刀点薄厚:
a.切割过程中,有碎片、碎导向条等杂质混入砂浆中,随着砂浆的流动和钢线的转动卷入导轮上的线网中,引起跳线和切斜,造成该区域的硅片中部至出刀点薄厚。
b.砂浆流量不合适。
砂浆流量是否均匀、流量能否达到切割要求,对硅片切割起着关键性作用。
若果切割过程中,砂浆流量时流时断,则会造成切割力不均匀,导致产生薄厚片。
解决措施:a.开始切割前,将机床切割室内的碎片清理干净,更换切割室过滤网以及浆料缸内的过滤桶、过滤袋等,保证机床洁净度。
b.将切割室内的浆料嘴清理干净,打开砂浆,看浆料嘴喷出的砂帘是否完整无断流。
(4)单片薄厚不均:
a.钢线张力异常,波动较大。
钢线张力是硅片切割工艺的核心要素,切割过程中,收放线轴的钢线都要保持一定的张力(通常0.12mm钢线放线轴张力设定范围为22N-24N,0.13mm钢线放线轴张力设定范围为21N-23N),张力过大或过小都不利于悬浮在钢线上的碳化硅颗粒进入锯缝进行切割。
钢线张力正常波动范围为±1N。
导致钢线张力异常的因素有:气缸漏气,张力臂滑轮或切割室入线口滑轮晃动或滑轮外套切偏。
b.导轮跳动较大。
一般地,导轮径向跳动<30μm,轴向跳动<20μm,导轮跳动过大则会引起线网抖动,导致硅片薄厚不均。
c.机床水平问题。
机床不水平,则会在切割过程中产生较大的震动,从而导致线网抖动。
d.导轮问题。
主要出现在新导轮或导轮槽严重磨损的情况下,钢线直径和导轮槽根部直径不能完全吻合。
解决措施:
a.使用张力计对钢线张力进行校验,检查气缸漏气情况、滑轮晃动情况及滑轮外套磨损情况,出现异常及时更换。
b.每次更换导轮后,都要检测导轮跳动是否在正常范围内,如果不符合要求则要重新安装导轮。
c.定期检测机床水平,及时调整。
d.更换新导轮,切割第一锯硅片之前,首先进行空切操作,将钢线张力设高以达到勒导轮的目的,使得钢线可以和导轮槽根部完全吻合。
对于磨损严重的导轮则及时进行更换。
4.结语
通过对薄厚片的类型及产生原因进行分析,可以更好地减少薄厚片的产生,提高产品的成品合格率。