SMT贴片标准及工艺标准
SMT贴片

B:来料检测 => PCB的A面插件(引脚打弯)=>翻板 => PCB的B面点贴片胶 =>贴片 =>固化 =>翻板 =>波 峰焊 =>清洗 =>检测 =>返修
先插后贴,适用于分离元件多于SMD元件的情况
C:来料检测 => PCB的A面丝印焊膏 =>贴片 =>烘干 =>回流焊接 =>插件,引脚打弯 =>翻板 => PCB的B面 点贴片胶 =>贴片 =>固化 =>翻板 =>波峰焊 =>清洗 =>检测 =>返修A面混装,B面贴装。
薄膜印刷线路
薄膜印刷线路
薄膜印刷线路SMT贴片(2张)此类薄膜线路一般是用银浆在PET上印刷线路。在此类薄膜线路上粘贴黏贴电子 元器件有两种工艺工法,一种谓之传统工艺工法即3胶法(红胶、银胶、包封胶)或2胶法(银胶、包封胶),另一 种谓之新工艺即1胶法---顾名思义,就是用一种胶即可完成粘贴黏贴电子元器件,而不再用3种胶或2种胶。此新 工艺关键是使用一种新型导电胶,完全具有锡膏的导电性能和工艺性能;使用时完全兼容现行的SMT刷锡膏作业 法,毋需添加任何设备。
单面混装工艺
来料检测 => PCB的A面丝印焊膏(点贴片胶)=>贴片 =>烘干(固化)=>回流焊接 =>清洗 =>插件 =>波峰 焊 =>清洗 =>检测 =>返修
双面混装工艺
A:来料检测 =>PCB的B面点贴片胶 =>贴片 =>固化 =>翻板 => PCB的A面插件=>波峰焊 =>清洗 =>检测 =>返修
SMT工艺要求控制规范
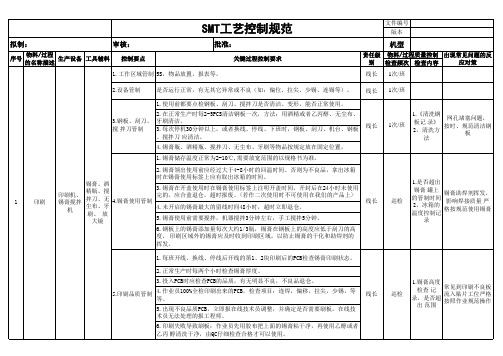
线长
1次/班
1.《清洗钢 板记 录》 2,清洗方
网孔堵塞问题, 按时、规范清洁钢
板
法
1.锡膏储存温度正常为2-10℃,需要放宽范围的以规格书为准。
2.锡膏领出使用前应经过大于4-8小时的回温时间、否则为不良品,拿出冰箱
时在锡膏使用标签上应有取出冰箱的时间。
1
印刷
印刷机、 锡膏搅拌
机
锡膏、酒 精瓶、搅 拌刀、无 尘布、牙 刷、 放
线长
后继续生产, 原因无法分析,立即通知SMT主管或相关人员。
技术员
巡检
首件不能很好完 成,就不能验证程 序,物料及上料的
正确性
4.过炉夹具的使 为防止元件的掉落,PCB变形而必须使用夹具的必须在制程工程师的指导下使 线长
用
用,特别是第一块板,必须制程工程师放入炉子。
技 术员
巡检
过炉夹具轨道不合 理,易导致卡板、 报废板,所以要严
格控制
1.工作区域管制 5S,物品放置,报表等(元件位置图,放大镜等)
线长 1次/班
2.ESD
1.凡是触及PCBA及ESD元件时需要佩戴防静电环,带静电手套; 2.防ESD设备每周必须检查,发现不良立即更换。
2
贴片
贴片机, 物料,料 盘料机 盘架
1.上料、接料、换料三对照: A.新料盘各旧料盘对照。
B.新料盘和Feederlist对照(料号和料站号)。
6.上料、换料的 C.换料记录表与Feederlist对照。
记 录,确认及
核对
2.tray盘料和不防呆元件,技术人员必须在明显位置标示极性方向。上料、换
料时核对。
线长
巡检
1.锡膏高度 检查 记
SMT贴片元器件操作
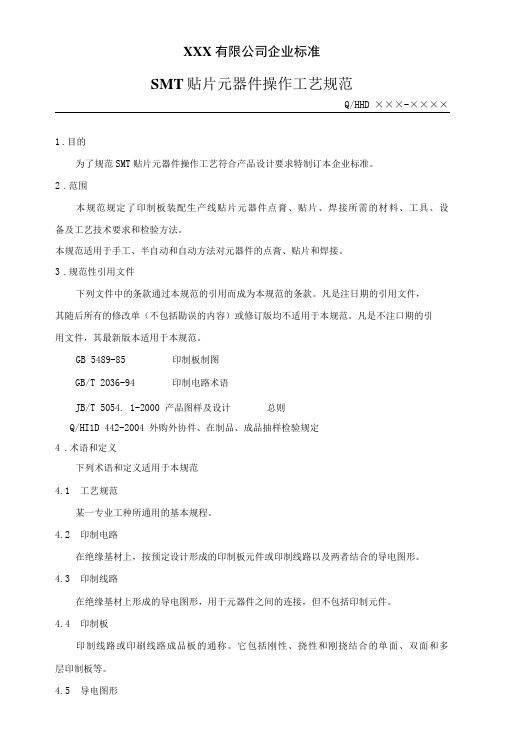
XXX有限公司企业标准SMT贴片元器件操作工艺规范Q/HHD ×××-××××1.目的为了规范SMT贴片元器件操作工艺符合产品设计要求特制订本企业标准。
2.范围本规范规定了印制板装配生产线贴片元器件点膏、贴片、焊接所需的材料、工具、设备及工艺技术要求和检验方法。
本规范适用于手工、半自动和自动方法对元器件的点膏、贴片和焊接。
3.规范性引用文件下列文件中的条款通过本规范的引用而成为本规范的条款。
凡是注日期的引用文件,其随后所有的修改单(不包括勘误的内容)或修订版均不适用于本规范。
凡是不注口期的引用文件,其最新版本适用于本规范。
GB 5489-85 印制板制图GB/T 2036-94 印制电路术语JB/T 5054. 1-2000 产品图样及设计总则Q/HI1D 442-2004 外购外协件、在制品、成品抽样检验规定4.术语和定义下列术语和定义适用于本规范4.1工艺规范某一专业工种所通用的基本规程。
4.2印制电路在绝缘基材上,按预定设计形成的印制板元件或印制线路以及两者结合的导电图形。
4.3印制线路在绝缘基材上形成的导电图形,用于元器件之间的连接,但不包括印制元件。
4.4印制板印制线路或印刷线路成品板的通称。
它包括刚性、挠性和刚挠结合的单面、双面和多层印制板等。
4.5导电图形×××× - ×× - xx实施×× - χχ发布印制板的导电材料形成的图形。
4.6字符印制板上主要用来识别元件位置和方向的字母、数字、符号和图,以便装联和更换元件。
4.7印制板组装件装配图印制板装配图是表示各种元器件和结构件等与印制板联接关系的图样。
4.8装配按印制板装配图表达的产品(部件)中的部件与部件、零件或零件间的联接图样,采用自动、半自动、手工方法,把元器件、结构件、接插件等安装在印制板基体上。
SMT贴片标准及工艺标准

印刷工艺
印刷机选择
锡膏选择
印刷精度
根据产品要求选择合适 的印刷机,确保印刷质
量。
根据产品特性选择合适 的锡膏,保证焊接质量。
印刷精度要求高,误差 需控制在一定范围内。
印刷质量检测
印刷完成后需进行质量 检测,确保无缺陷。
贴片工艺
贴片设备选择
根据产品要求选择合适的贴片 设备,确保贴片精度。
元件选择与准备
焊点完整性
焊点外观
焊点应连续、平滑,无气泡、空洞或 裂缝。
焊点应呈光亮的金属色,无氧化、变 色等现象。
焊点强度
焊点应牢固,能承受一定程度的压力 和振动,不易脱落。
元件位置标准
元件位置准确性
元件应放置在正确的位置,偏差 不超过允许范围。
元件方向正确性
元件的方向应符合电路设计要求, 极性元件方向正确。
焊点外观检测
焊点外观需光滑、连续、无气泡、无杂质。
检测工艺
01
功能检测
对产品进行功能检测,确保满足设 计要求。
尺寸检测
对产品尺寸进行检测,确保符合规 格要求。
03
02
外观检测
对外观进行检测,确保无明显缺陷。
可靠性检测
对产品进行可靠性检测,确保满足 使用要求。
04
SMT贴片质量标准
03
焊点质量标准
贴片材料的表面质量
贴片材料的表面应光滑、无缺陷,以确保良好的贴装效果。
辅助材料标准
1 2
粘合剂材料
用于固定电子元件的粘合剂应具有适当的粘性和 耐温性能。
清洁剂材料
用于清洁贴片表面的清洁剂应无腐蚀性、无残留 物。
3
包装材料
用于包装贴片产品的包装材料应具有保护性、防 潮性和抗震性。
SMT工艺设计规范
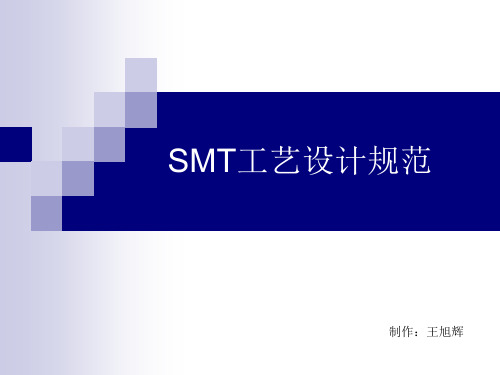
2.4 PCB焊盘设计 焊盘设计总的规则是元件的焊盘投影必须落在PCB焊盘之内,且周围留有一定的剩余 面积以利形成带弧度的焊接表面,焊盘设计应对称,双端元件两个焊盘尺寸一致。
各类型元件的焊盘具体尺寸见图表1及图示。
W L D
1)焊盘长度L=元件焊盘长度+元件焊盘高度+0.25 (mm) 2)焊盘宽度W=元件宽度+0.25 (mm) 3)焊盘间距D=元件焊盘间距-0.25(mm) 4)具体尺寸见表1 表1 普通片状元件的焊盘设计尺寸备查表
5mm 宽的工艺边 贴片完成后去除
2.3 PCB拼板设计 2.3.1对于尺寸小于50×50mm的PCB,可以设计成拼板,如图所示。但拼板后的总尺寸又 不能超出L510×W460mm的范围(包括附加的工艺边),各小拼板的方向尽量保持一致,并维 持长边在PCB的流向方向,丝印文字正对人眼。各拼板之间采用V-CUT半切口连接,如图7所 示。即两面各切入1/3的深度,中间保留1/3的板厚,可用手工很方便的分离。 在电路设计中 可直接将PCB实体拷贝拼接在一起,板间留0.3mm的余量用于切口,但注意应将完全靠边的 铜箔线路从板边往内收缩至少0.75mm,避免PCB切口加工时刀具伤及铜箔线路。采用V-CUT 拼板的PCB厚度一般不超过3.5mm。 2.3.2从设备的综合利用率和生产效率出发,我们公司自动贴片机基本按1+1配置,为最大限 度的提高设备单位产能,这样对我们前期拼板及拼板后元件有一个基本的规定,当拼板后元 件点数不少于420点,这样就达到SMT设备生产效率最大化。
焊盘从引脚弯折处开始,到元件脚边缘结束,四周再向外延伸0.3mm。 晶体管焊盘设计
焊盘从元件脚弯折处开始,到元件脚边沿结束,四周再向外延伸0.3mm。
普通集成电路芯片焊盘设计
SMT设备性能参数对生产基本的工艺要求

SMT设备性能参数对生产基本的工艺要求针对在实际的生产中设备与工艺的可制造性出现的冲突异常,现将一些在实际操作中常使用及注意事项的要求参数整理汇总,同时将经常出现的一些工艺上要求汇总与大家分享一下以便我们共同努力提高制程能力,详细如下:AI设备参数要求:SMT设备参数要求:二:550mm*650mm网框,铝框厚度25.4mm,铝框宽度38.1mm。
三:29*29英寸,网框尺寸736mm*736mm,铝框厚度40.00mm,铝框宽度40.00mm。
制程中不良案例分析及改善措施一、自动插件时,发现供料的MZ31-04M 400-500Ω热敏电阻出现引脚断裂的不良现象(见附图)。
引脚插件时断裂对自动插件设备造成损坏隐患;且从引脚断裂面分析,部分物料可能存在电性能不良可能原因:从提供的图片来分析为表面受力,工序周转时个别产品受到撞击,本体所承受的拉力较小,易断;测阻值时没有能对已受到的外力的产品测出。
措施:焊接工序增加外观全检,工序周转时由专人操作避免粗暴作业;控制锡炉的温度每小时做到点检,由QC及生产小组长监督与抽查;阻值测试现调整为全检;对员工培训。
二、发现FR105编带脱胶严重,影响机插:产生不良的原因有以下两种可能:1、在后道编带过程中,由于操作人员调试不当,没有将机器的压轮调节到位,从而使该批编带由于没有压紧,在运输过程中的受到各种力作用使得编带松动、脱胶。
2、该批次的编带粘性不良。
改善控制措施:1、对于原因一,我们对作业记录及同一机器当天其它批次的产品进行检查,并没有发现任何异常。
2、对于原因二,由于我司IQC对编带粘性没有检验手段,我们已经与供应联系,让其分析产生不良的原因,并进行整改。
3、针对我司目前对编带粘性没有检验手段这一情况,我司已经组织相关人员进行制定,目前工作正在进行中。
三、使用过程中发现有一盘二极管存在本体不齐的现象;原因:主要是胶带粘合不紧密造成。
四、引脚从根部脱焊断裂在自动插件生产时,发现供料的RY 2W301 J 编带小型电阻在引脚打弯时有引脚从根部断裂的现象,查看引脚断口可以看出引脚端部未形成良好焊点(见附图)。
SMT通用贴片检验标准

5.2.2 焊接异常---针孔/吹孔5.2.2缺陷-1,2,3级针孔/吹孔/空洞等使焊接特性降低至最低要求以下.文件编号 Doc.No审核 Audit.文件名称 Title 版本 Revision批准 Approve页码 Page标准化 Standard5.2.35.2.3 焊接异常--锡膏回流5.2.45.2.4 焊接异常-不润湿 5.2.55.2.5 焊接异常-反润湿融化的焊接料与基底金属不能形成金属性结合。
融化的焊接料先覆盖表面后退缩成一些形状不规则的的焊了堆,空当处有薄薄的焊料膜覆盖,为暴露基底金属和表面涂敷层。
5.2.75.2.7 焊接异常-焊锡过量/锡网,溅锡5.2.8 焊接异常-焊料受扰5.2.8带有冷却纹的焊点表面外观,大多发生在无铅合金中,不是受焊料受扰。
5.2.9 焊接异常-焊料破裂5.2.9缺陷-1,2,3级违反组件最大高度或引脚突出要求。
5.2.9 焊接异常-边缘夹簧/错位5.2.9文件编号 Doc.No审核 Audit.文件名称 Title 版本 Revision批准 Approve页码 Page标准化 Standard7.1.1.1元器件的安放-方向-水平7.1.5元器件的安放-DIP/SIP器件与插件引脚伸出长度满足要求文件编号 Doc.No审核 Audit.文件名称 Title 版本 Revision批准 Approve页码 Page标准化 Standard7.1.6元器件的安放-径向引脚-垂直7.1.8元器件的安放-连接器文件编号 Doc.No审核 Audit.文件名称 Title 版本 Revision批准 Approve页码 Page标准化 Standard7.3.2元器件固定--粘接剂粘接7.3.3元器件固定--粘接剂粘接文件编号 Doc.No审核 Audit.文件名称 Title 版本 Revision批准 Approve页码 Page标准化 Standard7.4.5非支撑孔--焊接7.4.5非支撑孔--焊接文件编号 Doc.No 审核 Audit.文件名称 Title版本 Revision 批准 Approve 页码 Page标准化 Standard7.4.5非支撑孔--导线弯折7.4.5支撑孔--焊接文件编号 Doc.No审核 Audit.文件名称 Title 版本 Revision批准 Approve页码 Page标准化 Standard7.4.5支撑孔--焊接--主面--引脚到孔壁7.4.5支撑孔--焊接--主面--引脚到孔壁文件编号 Doc.No审核 Audit. 年 月 日文件名称 Title 版本 Revision批准 Approve 年 月 日页码 Page标准化 Standard 年 月 日7.4.5支撑孔--焊接--辅面-焊盘区覆盖8.18.1 胶水粘固7.4.5支撑孔--焊点--引脚弯曲处的焊料文件编号 Doc.No审核 Audit. 年 月 日文件名称 Title 版本 Revision批准 Approve 年 月 日页码 Page标准化 Standard 年 月 日8.2.1.1片式元件-仅底部端子侧面偏移(A)8.2.1.2片式元件-仅底部端子侧面偏移(B)文件编号 Doc.No审核 Audit.文件名称 Title 版本 Revision批准 Approve页码 Page标准化 Standard8.2.1.3片式元件-仅底部端子末端连接宽度(C)8.2.2.1片式元件-矩形或方形端元件-侧面偏移(A)8.2.1.4片式元件-仅底部端子,最小填充高度(F)F 填充高度没有要求文件编号 Doc.No审核 Audit.文件名称 Title版本 Revision批准 Approve页码 Page标准化 Standard偏移大于50%,为不良8.2.2.3片式元件-矩形或方形端元件-末端连接宽度(C)偏移超出焊盘位置,为不良8.2.2.2片式元件-矩形或方形端元件-末端偏移(B)文件编号 Doc.No审核 Audit.文件名称 Title 版本 Revision批准 Approve页码 Page标准化 Standard8.2.2.5片式元件-矩形或方形端元件-最大填充高度(E)8.2.2.4片式元件-矩形或方形端元件-侧面连接长度(D)8.2.2.6片式元件-矩形或方形端元件-最小填充高度(F)文件编号 Doc.No审核 Audit.文件名称 Title 版本 Revision批准 Approve页码 Page标准化 Standard8.2.2.9片式元件-矩形或方形端元件-端子异常(J)8.2.2.8片式元件-矩形或方形端元件-末端重叠(J)文件编号 Doc.No审核 Audit.文件名称 Title版本 Revision批准 Approve页码 Page标准化 Standard 侧立/贴 立碑倒贴文件编号 Doc.No审核 Audit.文件名称 Title 版本 Revision批准 Approve页码 Page标准化 Standard文件编号 Doc.No审核 Audit.文件名称 Title 版本 Revision批准 Approve页码 Page标准化 Standard8.2.3.4元件端子-侧面连接长度(D)8.2.3.6元件端子-最小填充高度(F)可接收良品图片8.2.3.5元件端子-最大连接厚度(E)不可接收图片-不润湿不良现象图片文件编号 Doc.No审核 Audit.文件名称 Title 版本 Revision批准 Approve页码 Page标准化 Standard8.2.3.8元件端子-末端重叠(J)8.2.4.1城堡端子/引脚-侧面偏移(A)不可接收图片-重叠小于50%8.2.4.2城堡端子/引脚-最小侧面焊接长度(D)文件编号 Doc.No WI17-88-007审核 Audit.文件名称 Title 版本 Revision A批准 Approve页码 Page3/3标准化 Standard8.2.4.68.2.4.6 无引脚芯片端子-最小填充高度(F)8.2.5.18.2.5.1 扁平,L形,翼形引脚-侧面偏移(A)偏移大约50%,二级标准可以接收89910785 HE。
SMT贴片工艺

SMT贴片工艺SMT加工及检验作业指导书一、贴片工艺要求1.1 工艺目的本工艺要求确保SMT贴片工艺的质量,提高生产效率,降低生产成本。
1.2 工艺要求在SMT贴片工艺中,必须遵循以下工艺要求:确保设备的正常运行和维护;选择合适的贴片材料;确保贴片过程的正确性和稳定性;保证产品的质量和稳定性。
二、贴片工艺流程2.1 全自动工艺流程全自动工艺流程包括:印刷锡膏、贴片、回流焊、清洗、检验等环节。
2.2 手动贴片工艺流程手动贴片工艺流程包括:印刷锡膏、手动贴片、回流焊、清洗、检验等环节。
三、首板试贴检验3.1 首件试贴合检验在生产过程中,必须进行首件试贴合检验,以确保贴片工艺的正确性和稳定性。
3.2 生产中质检故障处理在生产过程中,如果发现质量问题,必须及时进行故障处理,以确保产品质量和生产效率。
四、手动贴装工艺4.1 手装工艺的要求手动贴装工艺要求操作人员必须熟练掌握贴装工艺,保证产品质量和生产效率。
4.2 手装贴装的应用范围手动贴装工艺适用于小批量、多品种、高质量的生产。
4.3 手装贴装工艺手动贴装工艺流程包括:印刷锡膏、手动贴片、回流焊、清洗、检验等环节。
五、SMT外观检验标准SMT外观检验标准包括以下规范:A、锡浆印制规范;B、红胶印制规范;C、Chip料放置焊接规范;D、翅膀型IC料放置焊接规范;E、J型脚放置焊接规范;F、城堡型IC放置焊接规范;G、BGA放置焊接规范;H、扁平元件脚放置焊接规范;I、其他补充。
本文介绍了贴片工艺的要求和保证贴装质量的三要素。
贴片工艺的目的是使用贴片机将片式元器件精确地贴放到印好焊膏或贴片胶的PCB表面相对应的位置上。
在贴装元器件时,需要符合产品的装配图和明细表要求,保证元器件完好无损,并且焊端或引脚不小于1/2厚度要浸入焊膏,对于焊膏挤出量也有严格的要求。
同时,元器件的端头或引脚均和焊盘图形对齐、居中,允许有一定的偏差,但要满足一定的要求范围。
保证贴装质量的三要素分别是元件正确、位置准确和工艺要求的满足。
SMT生产工艺流程及要求
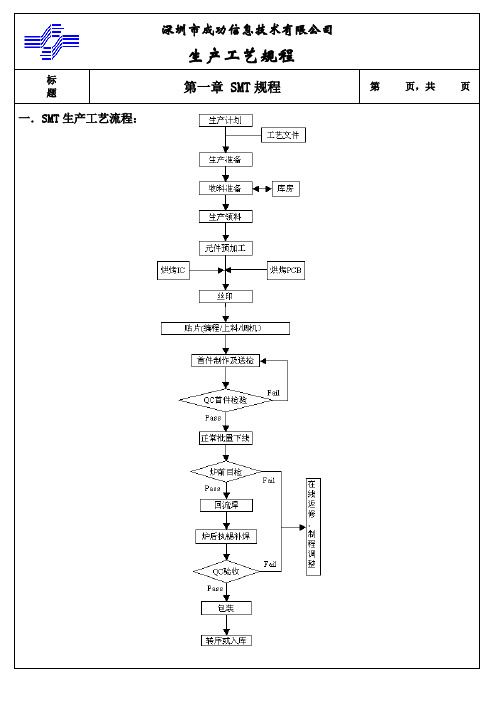
标第一章 SMT规程第页,共页题一.SMT生产工艺流程:标第一章 SMT规程第页,共页题一.SMT生产工艺要求:1.领料要求:1>作业依据:生产计划通知单、配料清单2>作业注意事项:严格按配料清单所示之相关产品信息核对所领物料相关参数的符合性、包括产品型号规格、厂商、数量、包装。
对于需QC检验的物料需看是否有IQC检验合格单,不符要求者拒收。
3>作业质量要求:不接收不符合要求之物料,即领对料。
2.物料烘烤:1>作业依据:《物料烘烤作业规范》、生产计划通知单2>作业注意事项:对于生产计划通知单上要求烘烤之物料严格按照《物料烘烤作业规范》要求执行物料烘烤,并做好相关记录,烘烤完成后需经拉长确认。
3>作业质量要求:要求烘烤之物料必须烘烤、烘烤参数设置及烘烤时间要符合文件要求各种烘烤记录必须填写清晰完整,生产拉长必须对烘烤执行情况进行确认后物料方可上线生产。
3.锡膏储存:1>作业依据:《锡膏印刷作业指导书》2>作业注意事项:先进先出,做好“锡膏、红胶管理记录”,按时执行锡膏储存温度点检(要求温度为2-10摄氏度),并做好点检记录,发现温度异常时要即时知会拉长处理,用过的锡膏或红胶瓶要拧紧瓶盖。
3>作业质量要求:按时点检,保证储存温度在2-10摄氏度范围内,做好相应记录。
4.锡膏/红胶印刷: 1>作业依据:《锡膏印刷作业指导书》\《SMT红胶印刷操作规范》2>作业注意事项:a.锡膏印刷必须在下线前做好锡膏解冻(4小时以上)及搅拌工作(搅拌时间必须在10分钟以上,搅拌时力度应适中、均匀),红胶解冻时间至少为4-8小时,并要检查钢网是否为所对应的机型、以及是否符合钢网标准(如是否完整无损坏、严重变形、堵孔等)。
b.印刷工位处不能有风扇或空调对着吹风,因为风会破坏锡膏的粘着特性。
c.丝印台及钢网在印刷前需清洁干净,不得有脏物。
d.在试印和钢过程中发现钢网或其它问题导致不能正常印刷时即时知会拉长处理。
SMT整个工艺流程细则
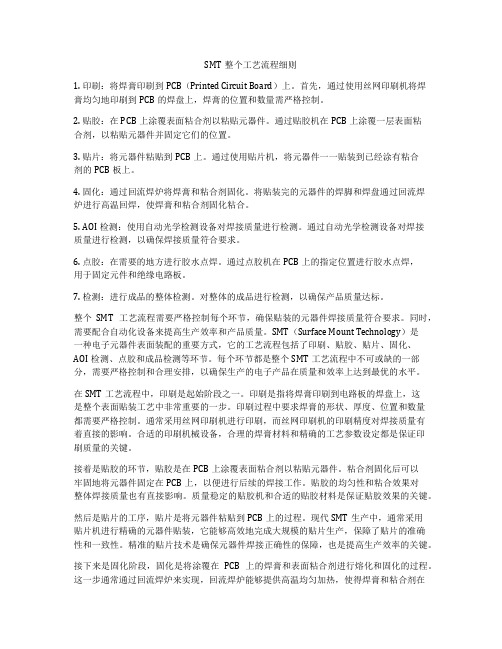
SMT整个工艺流程细则1. 印刷:将焊膏印刷到PCB(Printed Circuit Board)上。
首先,通过使用丝网印刷机将焊膏均匀地印刷到PCB的焊盘上,焊膏的位置和数量需严格控制。
2. 贴胶:在PCB上涂覆表面粘合剂以粘贴元器件。
通过贴胶机在PCB上涂覆一层表面粘合剂,以粘贴元器件并固定它们的位置。
3. 贴片:将元器件粘贴到PCB上。
通过使用贴片机,将元器件一一贴装到已经涂有粘合剂的PCB板上。
4. 固化:通过回流焊炉将焊膏和粘合剂固化。
将贴装完的元器件的焊脚和焊盘通过回流焊炉进行高温回焊,使焊膏和粘合剂固化粘合。
5. AOI检测:使用自动光学检测设备对焊接质量进行检测。
通过自动光学检测设备对焊接质量进行检测,以确保焊接质量符合要求。
6. 点胶:在需要的地方进行胶水点焊。
通过点胶机在PCB上的指定位置进行胶水点焊,用于固定元件和绝缘电路板。
7. 检测:进行成品的整体检测。
对整体的成品进行检测,以确保产品质量达标。
整个SMT工艺流程需要严格控制每个环节,确保贴装的元器件焊接质量符合要求。
同时,需要配合自动化设备来提高生产效率和产品质量。
SMT(Surface Mount Technology)是一种电子元器件表面装配的重要方式,它的工艺流程包括了印刷、贴胶、贴片、固化、AOI检测、点胶和成品检测等环节。
每个环节都是整个SMT工艺流程中不可或缺的一部分,需要严格控制和合理安排,以确保生产的电子产品在质量和效率上达到最优的水平。
在SMT工艺流程中,印刷是起始阶段之一。
印刷是指将焊膏印刷到电路板的焊盘上,这是整个表面贴装工艺中非常重要的一步。
印刷过程中要求焊膏的形状、厚度、位置和数量都需要严格控制。
通常采用丝网印刷机进行印刷,而丝网印刷机的印刷精度对焊接质量有着直接的影响。
合适的印刷机械设备,合理的焊膏材料和精确的工艺参数设定都是保证印刷质量的关键。
接着是贴胶的环节,贴胶是在PCB上涂覆表面粘合剂以粘贴元器件。
SMT贴片标准及工艺标准

二:印刷得一些不良現象
印刷得主要不良現象有少錫、錫量過多、過厚、 漏銅、短路、錫尖、偏移。
1、少錫,錫量過多,過厚。
此不良現象就是指印刷之錫量低於或高於標準錫 量,錫膏印刷過厚。
一般錫厚就是通過鋼板來決定得。錫厚不能低於 鋼板厚度或高於鋼板厚度得0、03mm。標準鋼板一般 分為:0、13mm,0、15mm,0、18mm。
錫焊應呈弧形。(如圖)
2、具有良好得導電性:即焊錫相互擴散形成合金屬、 3、具有一定得強度:即焊點必須具有一定抗拉強度 和抗衝擊韌性、 4、回焊時盡量使用N2,回焊效果更佳。
三:不良焊點、
生產中由於PCB線路設計,生產中工藝控制以及錫膏 得選擇等因素影響,均會出現不良焊點,所出現得不良時點 主要有以下几種:
SMT贴片标准及工艺标准
目錄
一:錫膏印刷工藝 二:作業貼片工藝 三:錫量回焊工藝
第一章:錫膏印刷工藝
一:簡述錫膏及印刷 錫膏可分為免洗型錫膏,現主流使用。FLUX在10
%以下,成份主要就是錫(Sn),鉛(Pb)組成,另無鉛錫 膏因單價較高還未廣泛使用。
印刷即就是通過鋼板將PCB焊墊(PAD)上印刷錫膏。 因好壞直接關系到生產品質,故有一定之標準。
件加熱至錫膏溶點溫度
恆溫區:使PCB及各種不同之零件有足夠時間吸收熱 量,以達到均溫,同時Flux完全揮發
回焊區:已活化得Flux及完全熔化得錫膏,開始進行焊 接功能
冷卻區:焊接功能完成,已熔化得錫膏快速冷卻完成焊 接
升溫區
恆溫區
預溫區
回焊區
冷卻區
圖七
二:回焊效果 1、回焊後之焊點應光滑,有光澤,吃錫性好,焊點與零
1、短路
現象:兩個直立得接點,因焊錫連通而導致電流跨越, 即不同線路上得焊點連在一起、(如圖)
SMT工艺标准

表面贴装技术(SMT)工艺标准Q/WP1101-20021范围本标准规定了本公司表面贴装生产的设备、器件、生产工艺方法、特点、参数以及产品和半成品的一般工艺要求以及关于表面贴装生产过程防静电方面的特殊要求。
本规范适用于我公司所有采用表面贴装的生产工艺。
2规范性引用文件SJ/T 10670-1995 表面组装工艺通用技术要求SJ/T 10666-1995 表面组装组件的焊点质量评定SJ/T 10668-1995 表面组装技术术语3术语3.1 一般术语a)表面组装技术---- SMT(Surface Mount Technology)。
b)表面组装元器件---SMD/SMC(Surface Mount Devices/ Surface Mount Components)。
c)表面组装组件--- SMA (Surface Mount Assemblys)。
d)表面组装印制板--- SMB (Surface Mount Board)。
e)回流焊(Reflow soldering)--- 通过重新熔化预先印制到印刷板焊盘上的锡膏焊料,实现SMD焊端或引脚与印制板焊盘之间的机械与电气连接的软钎焊。
f)峰焊(Wave soldering)--- 将熔化的软钎焊料,经电动泵或电磁泵喷流成设计要求的焊料波峰,使预先装有电子元器件的印制板通过焊料波峰,实现元器件焊端或引脚与印制板焊盘之间的机械与电气连接的软钎焊。
3.2 元器件术语a)焊端(Terminations)--- 无引线表面组装元器件的金属化外电极。
b)形片状元件(Rectangular chip component)两端无引线,有焊端,外形为薄片矩形的SMD。
c)外形封装 SOP(Small Outline Package)小外形模压塑料封装,两侧有翼形或J形短引脚的一种SMD。
d)小外形晶体管SOT(Small Outline Transistor)采用小外形封装结构的表面组装晶体管。
SMT工艺设备详解及标准工时计算方法
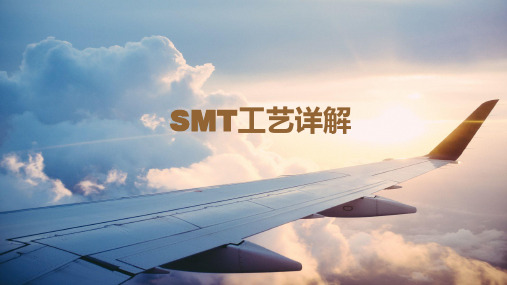
从历史上讲,贴装元器件SMC/SMD,由欧美先进技术国家发明于1960年代中期。后来的一些年较多采用这种新型 元器件是厚膜电路与混合集成电路。在先前已制作好线路、厚膜电阻与焊盘的陶瓷基板上,印刷锡膏,以手工 方式贴上无引线独石陶瓷电容MLC、被称为‘芝麻管’的短小引脚晶体管与贴装式IC,然后进行再流焊接,完成 组装,这就是雏形的SMT方式。 虽然SMC/SMD的发明及雏形的SMT技术最早在欧美形成,但进展的步履缓慢,倒是缺乏资源但善于学习西方并进 行技术再创新的日本,在1970年代中期加快了开发应用步伐。在1970年代后期日本大型电子企业集团率先研制 成功了自动贴片机,由内部的专用设备逐步改进为商品化的通用设备,大批量地应用在家用电子产品生产中。 1980年代初期SMT作为新型一大门类的先进电子板级组装工艺技术,由于自动贴片关键工艺设备的突破而正式启 动。SMT技术在发达国家的大型电子集团公司间重点开发与竞争而得到了蓬勃的发展。由于SMC/SMD无引线或短 小引线,便于改善电子产品高频性能,因此最早最多地应用量大面广的彩色电视机电子调谐器上。
二、PCBA工艺流程
SMT基本工艺构成要素包括:
1.丝网印刷:其功能是将锡膏或贴片胶漏到PCB焊盘上,为元件焊接做准备。所用设备为丝网印刷机(丝 网印刷机),位于SMT生产线前端。 2.点胶:将胶水滴在PCB板的固定位置,主要功能是将元器件固定在PCB板上。使用的设备是一台点胶机, 位于SMT生产线的前端或测试设备的后面。 3.安装:其功能是将表面组装好的元件准确安装到PCB的固定位置。所使用的设备是贴片机,它位于SMT生 产线中丝网印刷机的后面。 4.固化:其作用是熔化贴片胶,使表面组装的元件与PCB板牢固粘合。所用设备为固化炉,位于SMT生产线 贴片机后面。 5.回流焊接:其功能是熔化焊膏,并将表面组装的元件与PCB板牢固粘合。使用的设备是回流焊炉,它位 于SMT生产线贴片机的后面。 6.清洁:其功能是清除组装好的PCB上的焊剂等对人体有害的焊渣。使用的设备是清洁机,位置可以固定、 在线或离线。 7.检查:其功能是检查组装好的PCB的焊接质量和组装质量。使用的设备包括放大镜、显微镜、在线测试 仪(ICT)、飞针测试仪、自动光学检测仪(AOI)、X射线检测系统、功能测试仪等。可根据检测需要在 生产线的适当位置配置位置。 8.返修:功能是对检测出故障的PCB板进行返修。使用的工具包括烙铁、维修工作站等。可在生产线的任 何位置配置。
贴片焊盘设计标准
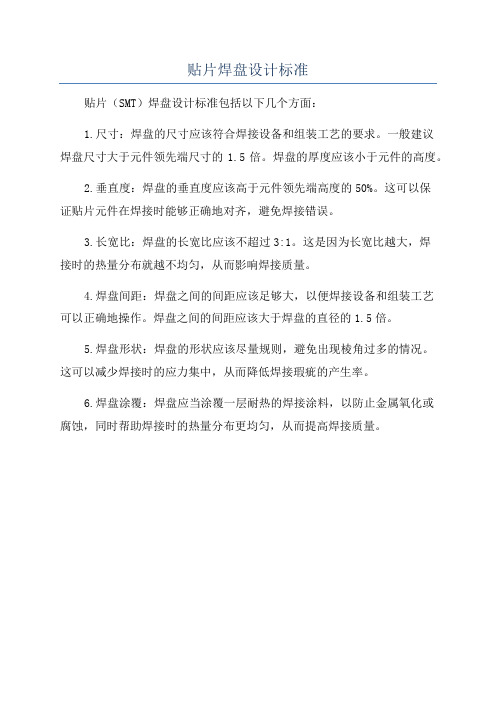
贴片焊盘设计标准
贴片(SMT)焊盘设计标准包括以下几个方面:
1.尺寸:焊盘的尺寸应该符合焊接设备和组装工艺的要求。
一般建议
焊盘尺寸大于元件领先端尺寸的1.5倍。
焊盘的厚度应该小于元件的高度。
2.垂直度:焊盘的垂直度应该高于元件领先端高度的50%。
这可以保
证贴片元件在焊接时能够正确地对齐,避免焊接错误。
3.长宽比:焊盘的长宽比应该不超过3:1。
这是因为长宽比越大,焊
接时的热量分布就越不均匀,从而影响焊接质量。
4.焊盘间距:焊盘之间的间距应该足够大,以便焊接设备和组装工艺
可以正确地操作。
焊盘之间的间距应该大于焊盘的直径的1.5倍。
5.焊盘形状:焊盘的形状应该尽量规则,避免出现棱角过多的情况。
这可以减少焊接时的应力集中,从而降低焊接瑕疵的产生率。
6.焊盘涂覆:焊盘应当涂覆一层耐热的焊接涂料,以防止金属氧化或
腐蚀,同时帮助焊接时的热量分布更均匀,从而提高焊接质量。
smt贴片检验标准

smt贴片检验标准SMT贴片检验标准。
SMT贴片技术是一种表面贴装技术,广泛应用于电子产品的制造过程中。
在SMT贴片过程中,质量检验是非常重要的环节,它直接关系到产品的质量和稳定性。
因此,建立和执行严格的SMT贴片检验标准是至关重要的。
首先,SMT贴片检验标准应包括对于各种SMT贴片设备的检验要求。
例如,对于贴片机的检验应包括设备的精度、速度、稳定性等方面的要求。
对于回流炉的检验应包括设备的加热均匀性、温度控制精度等方面的要求。
通过对设备的检验,可以确保SMT贴片过程中设备的正常运行,从而保证产品的质量。
其次,SMT贴片检验标准还应包括对于贴片材料的检验要求。
贴片材料包括贴片元件、焊膏等。
对于贴片元件的检验应包括元件的尺寸、外观、焊盘的涂覆情况等方面的要求。
对于焊膏的检验应包括焊膏的粘度、温度特性、氧化情况等方面的要求。
通过对贴片材料的检验,可以确保贴片过程中所使用的材料符合质量要求,从而保证产品的可靠性。
另外,SMT贴片检验标准还应包括对于贴片过程的检验要求。
贴片过程包括元件的贴装、回流焊接等环节。
对于贴片过程的检验应包括贴片位置的精度、焊接温度曲线的合格性、焊接后的焊点外观等方面的要求。
通过对贴片过程的检验,可以确保贴片过程的稳定性和可控性,从而保证产品的一致性和稳定性。
最后,SMT贴片检验标准还应包括对于贴片产品的检验要求。
对于贴片产品的检验应包括外观检验、功能检验等方面的要求。
外观检验应包括产品的焊点外观、组装外观等方面的要求。
功能检验应包括产品的电气性能、可靠性等方面的要求。
通过对贴片产品的检验,可以确保产品的质量符合客户的要求,从而提升产品的市场竞争力。
总之,建立和执行严格的SMT贴片检验标准对于保证产品的质量和稳定性具有重要意义。
只有通过严格的检验,才能确保SMT贴片产品的质量符合要求,从而赢得客户的信任和认可。
smt工艺技术要求

smt工艺技术要求SMT(Surface Mount Technology)是一种表面贴装技术,逐渐取代了传统的插件式组装技术,成为电子制造业中常用的工艺之一。
在SMT工艺中,要求严格的技术规范和要求常常需要被遵守,以确保产品的质量和可靠性。
以下是一些常见的SMT工艺技术要求。
首先,SMT工艺中最重要的一点是对贴片元件的准确放置。
贴片元件必须准确无误地被放置在PCB(Printed Circuit Board,印刷电路板)上。
为了实现这一点,需要使用高精度的贴片机和贴片机的相关设置。
贴片机应能够准确地检测零件的位置和方向,并将其放置在正确的位置上。
此外,需要确保PCB表面的平整度,以保证元件的贴附和焊接的质量。
其次,焊接是SMT工艺中另一个关键的环节。
焊接能够连接贴片元件和PCB,确保它们之间的良好电气连接。
对于SMT工艺中的焊接,有两种主要的方法:回流焊接和波峰焊接。
在回流焊接中,通过将整个PCB放入预热的炉子中,使焊膏熔化并连接元件和PCB。
而波峰焊接是通过将带有熔融焊料的波峰引导到PCB上,使焊膏熔化并完成连接。
无论采用哪种焊接方法,都需要确保焊接温度、时间和焊接质量的控制。
此外,SMT工艺还需要考虑到其他因素,以确保产品的质量。
例如,对于SMT工艺中的元件尺寸,要求有一定的容差范围。
如果尺寸超出了容差范围,则可能会导致元件的装配和焊接问题。
此外,在设计和制造PCB时,需要考虑到元件在PCB上的布局和排列,以便提高SMT工艺的效率和可靠性。
最后,还需要对SMT工艺中使用的设备和材料进行严格的控制。
例如,贴片机和焊接设备需要定期进行维护和校准,以确保其工作的准确性和稳定性。
此外,使用的焊膏、PCB材料和贴片元件也需要符合一定的质量标准,以确保产品的可靠性和长期使用的稳定性。
总结起来,SMT工艺技术要求多方面的考虑,包括对贴片元件的准确放置、焊接的质量控制、PCB尺寸和布局的要求,以及对设备和材料的严格控制。
smt贴片工艺流程介绍

smt贴片工艺流程介绍
SMT贴片工艺流程是指表面贴装技术(Surface Mount Technology)的工艺流程,用于电子元器件的贴片装配过程。
以下是一般的SMT贴片工艺流程介绍:
1. 钻孔:在电路板上打孔,用于通过孔技术的元件安装。
2. 原板处理:对电路板进行清洁和涂覆表面粗糙度,以提
高焊接和贴附性。
3. 贴附:将胶料或用于贴附元器件的胶水涂在电路板表面。
4. 精确定位:使用自动定位设备将元器件准确地放置在电
路板上的预定位置,通常采用精确自动点胶机或贴片机完成。
5. 固定焊接:将已定位的元器件通过回焊炉中的热熔焊料进行焊接,使元件与基板永久连接。
6. 清洗:清洗电路板以去除生产过程中的残留物,通常使用溶剂或超声波清洗机。
7. 检测:进行必要的自动或手动检测,以确保贴片工艺的质量和精度。
8. 二次焊接:在需要的情况下,对电路板的焊点进行二次焊接或再流焊,以确保全部焊点质量和可靠性。
9. 高度检测:使用高度检测设备,如光学或激光测高仪,检查元器件的高度是否符合要求。
10. 成品检验:对完成的电路板进行全面的检查,以确保符合设计要求和品质标准。
以上是一般的SMT贴片工艺流程介绍,具体的工艺流程可能会根据不同的产品要求和制造商的特定流程进行适当调整。
- 1、下载文档前请自行甄别文档内容的完整性,平台不提供额外的编辑、内容补充、找答案等附加服务。
- 2、"仅部分预览"的文档,不可在线预览部分如存在完整性等问题,可反馈申请退款(可完整预览的文档不适用该条件!)。
- 3、如文档侵犯您的权益,请联系客服反馈,我们会尽快为您处理(人工客服工作时间:9:00-18:30)。
所印刷之錫膏偏移PAD的四分之一(如圖四)
錫尖 偏移
第二章:作業貼片工藝
一:簡述SMT及貼片技術 1.SMT簡介 Surface Mount Technology 表面黏著技術 SMT已經漸漸取代大部分的傳統“手插零件”製程.符合現代潮流須求.更輕.薄.短.小.讓目前電子產品能小型化.高密度化.高
2.冷焊 現象:焊點看似碎裂、不平、焊錫溶化.未與焊點溶合或完全溶合之前凝固,焊錫表面光澤不佳表面粗糙. 3.空焊(假焊) 現象:零件腳與PAD間沾有錫,但實際上沒有被錫完全焊接上.(如圖)
4.焊點過大 焊點又圓又胖(事實上焊點過大不能對導電性及抗拉強度有所幫助,反而容易造成短路. a.焊點與相鄰可導電零件距離須大於0.5mm.(如下圖)
二:貼片的主要不良現象 1.偏移 即貼裝之零件偏離所應貼裝的位置(如圖五)
2.反向
圖五
有極性之零件角度貼裝錯誤(如圖六)
圖六
偏移 反向
3.缺件 缺件是指機台跳過應貼裝之零件而沒有貼裝
4.錯件 零件貼裝錯誤
第三章:錫量回焊工藝
一:簡述回焊過程 基板通過回焊爐先預溫再升溫將錫熔化使零件與基板結合形成電子通路 回焊過程主要通過升溫區、預熱區、恆溫區、回焊區、冷卻區。(如圖七) 升溫區:PCB零件逐漸加溫揮發多於的溶劑 預熱區:Flax的流動與錫粉表面氧化,逐漸將PCB零件加熱至錫膏溶點溫度
SMT貼片標準及工藝標準
編訂: 劉超 日期: 審核: 復核:
目錄
一:錫膏印刷工藝 二:作業貼片工藝 三:錫量回焊工藝
第一章:錫膏印刷工藝
一:簡述錫膏及印刷
錫膏可分為免洗型錫膏,現主流使用。FLUX在 10%以下,成份主要是錫(Sn),鉛(Pb)組成,另無 鉛錫膏因單價較高還未廣泛使用。
0.5mm
圖八 b. SOJC.PQFP零件兩PIJN腳焊量之最小間距不能小於兩PAD間距的1/2.(如圖)
A
B
5.零件偏移 零件之端點偏離PCB銅箔超過零件端點寬度1/4,但未空焊.
W
6.浮高 零件高翹超過1.6mm,但未空焊.
<1件經過回焊像墓碑一樣直立起來
恆溫區:使PCB及各種不同之零件有足夠時間吸收熱量,以達到均溫,同時Flux完全揮發 回焊區:已活化的Flux及完全熔化的錫膏,開始進行焊接功能 冷卻區:焊接功能完成,已熔化的錫膏快速冷卻完成焊接
升溫區
恆溫區
預溫區
回焊區
冷卻區
圖七
二:回焊效果 1.回焊後之焊點應光滑,有光澤,吃錫性好,焊點與零錫焊應呈弧形。(如圖)
回溫後之錫膏攪拌,使Flux及其他溶劑能均勻分佈。手動攪拌:15-30下。機器攪拌:1-5分鐘。攪拌的時間不可過長,如過 長因錫粉末中粒子間磨擦,錫膏的溫度上昇,引起化學變化,使錫膏的特性劣質化。
2.注意事項: (1)印刷作業環境:攝氏21-28°C。相對溼度30-65%。 (2)不同規格或廠牌的錫膏,不可混合使用。 (3)錫膏印刷在PCB並搭載零件完成後,須於6-8小時內迴焊完成。 (4)印刷錯誤之PCB,須把錫膏刮除乾淨,並使用專用溶劑擦拭乾淨,再用空氣槍清潔基板孔,不可有殘錫。
3. 印刷之PCB不可有訂狀物、錫孔、塌邊、偏移、短路等現象
二:印刷的一些不良現象 印刷的主要不良現象有少錫、錫量過多、過厚、漏銅、短路、錫尖、偏移。
1.少錫,錫量過多,過厚。 此不良現象是指印刷之錫量低於或高於標準錫量,錫膏印刷過厚。 一般錫厚是通過鋼板來決定的。錫厚不能低於鋼板厚度或高於鋼板厚度的0.03mm。標準鋼板一般分為:
2.具有良好的導電性:即焊錫相互擴散形成合金屬. 3.具有一定的強度:即焊點必須具有一定抗拉強度和抗衝擊韌性. 4.回焊時盡量使用N2,回焊效果更佳。
三:不良焊點. 生產中由於PCB線路設計,生產中工藝控制以及錫膏的選擇等因素影響,均會出現不良焊點,所出現的不良時點主要有以下几種:
1.短路 現象:兩個直立的接點,因焊錫連通而導致電流跨越,即不同線路上的焊點連在一起.(如圖)
電訊效率.舉如:翻譯機.電子記事本.手機.B.B.C. 手提電腦.儀器.上至航太科技.下至家電用品.
2.貼片機分類 一般貼片機分高速機和泛用機。 高速機是以極快的速度將細小零件吸取並裝著於基板上。 泛用機是識別大零件的外形或腳位能精準著裝於基板上 貼片機貼裝精密度非常高,貼裝之零件坐標一定要準確,不能有反向,缺件現象。
印刷即是通過鋼板將PCB焊墊(PAD)上印刷錫 膏。
因好壞直接關系到生產品質,故有一定之標準。
二:印刷品質 1.錫膏保存及使用
將錫膏置於冷藏庫(攝氏0°--10°C,相對濕度35-55%)保存。 有效期從製造日起4-5個月內使用完畢為宜。
錫膏自冷藏庫取出後,在室溫25°C 的環境下至少回溫8小時以上,方可使用。
0.13mm,0.15mm,0.18mm。 例:0.13mm,錫厚在0.15左右較好,決不能低於0.13或高於0.16。
2.露銅 露銅是指在該覆蓋錫膏的焊盤上而沒有錫膏,造成漏銅現象。(如圖一)
3.短路
圖一
短路是指相鄰PAD上之錫膏連接在一起。
(如圖二)
漏銅
圖二
4.錫尖 錫尖是指焊盤上之錫膏呈凸狀,訂狀。(如圖三)
8.反向 反向的指有極性之零件,極性錯誤