吸塑盘工艺流程
吸塑工艺是什么意思
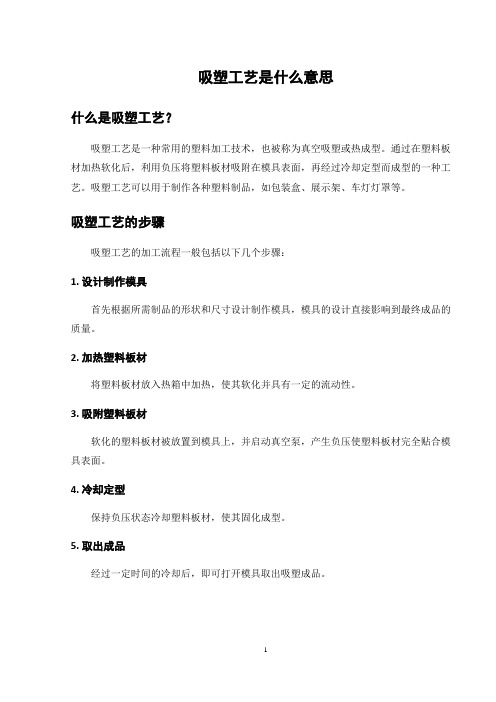
吸塑工艺是什么意思什么是吸塑工艺?吸塑工艺是一种常用的塑料加工技术,也被称为真空吸塑或热成型。
通过在塑料板材加热软化后,利用负压将塑料板材吸附在模具表面,再经过冷却定型而成型的一种工艺。
吸塑工艺可以用于制作各种塑料制品,如包装盒、展示架、车灯灯罩等。
吸塑工艺的步骤吸塑工艺的加工流程一般包括以下几个步骤:1. 设计制作模具首先根据所需制品的形状和尺寸设计制作模具,模具的设计直接影响到最终成品的质量。
2. 加热塑料板材将塑料板材放入热箱中加热,使其软化并具有一定的流动性。
3. 吸附塑料板材软化的塑料板材被放置到模具上,并启动真空泵,产生负压使塑料板材完全贴合模具表面。
4. 冷却定型保持负压状态冷却塑料板材,使其固化成型。
5. 取出成品经过一定时间的冷却后,即可打开模具取出吸塑成品。
吸塑工艺的应用吸塑工艺广泛应用于许多行业,如包装、广告、汽车等领域。
在包装行业,吸塑工艺可以制作各种形状的包装盒和托盘,为产品提供良好的保护和展示效果。
在广告行业,吸塑产品可以制作各种形状的广告展示架、标识牌等,赢得更多关注。
在汽车行业,吸塑工艺可以制作车灯灯罩、内饰零件等,提升车辆外观设计和功能性。
吸塑工艺的优势相比于传统的塑料加工工艺,吸塑工艺具有以下优势:•成型速度快:吸塑工艺一次成型,节约时间成本。
•制品质量好:吸塑成品表面光滑、尺寸精确,质量稳定。
•可塑性强:吸塑可以制作复杂形状的产品,满足不同需求。
•生产效率高:自动化生产线可实现大规模生产,提高效率。
总结吸塑工艺作为一种先进的塑料加工技术,已经在多个行业得到广泛应用,并不断发展和完善。
随着技术的进步和市场需求的不断变化,吸塑工艺将会在未来发挥更重要的作用,并为各行业带来更多创新和发展。
吸塑工艺流程纲要

吸塑工艺流程一、客户发出询价请求:途径一打询价,途径二发询价,途径三发Email询价,途径四通过网络聊天工具询价。
客户必须提供吸塑制品的长、宽、高和所用材料的厚度(或克重)、颜色和型号〔PVC、PET、PS、PP〕,产品数量和生产周期。
二、业务部门报价:吸塑制品单价的上下跟以下因素有关:吸塑制品的长、宽、高和吸塑成型的复杂程度;所用材料的类型、厚度和颜色;吸塑产品的后道加工工艺〔折边、打孔、封边等〕、订单数量和订单周期。
报价员会以客户的样品和描述有一个最初报价,最终报价会在打样之后报出。
三、电脑设计:客户对于报价根本认可后,会将要求、实物或是吸塑样品交到业务部,生产调度会要求电脑设计部将客户的实物扫描并结合印刷品的设计,制作出吸塑制品的平面设计图四、吸塑打样:客户认可电脑设计稿后,生产调度会根据吸塑产品的复杂程度决定采用哪种方式开发模具〔石膏模、铜模、铝模〕,开发周期3-5天。
吸塑打样以石膏模打样居多,其操作步骤是:1.先将实物用手工泥糊出成型轮廓;2.放到吸塑打版机上成型泡壳毛胚;3.用配好的吸塑专用石膏倒入泡壳毛胚中,风干后形成石膏毛胚;4.采用电动铣床对石膏毛胚和规那么形状进行深加工;5.手工打磨和手工添加部件;6.将各个抛光好的石膏部件粘合成完整的石膏模;7.再放入吸塑打版机吸塑成型完整的样品;8.按成品尺寸,手工切边、封边,完成全部打样过程。
如果有需求,印刷打样部门同时会将吸塑样品所用的纸卡、不干胶或彩盒一起制作,他们会借助全开的印刷数码打样机能将实际印刷结果反映出来。
五、制作生产模具:样品被客户认可后,通常会下一定数量的生产订单。
生产调度会根据产量、吸塑成型的复杂程度决定采用哪种模具量产:采用石膏模生产,模具制作过程类似于吸塑打样,优点在于生产周期短,本钱最低,制作一整版60X110cm)模具只需一到两天时间,缺乏之处在于吸塑成品外表粗糙,生产中模具容易碎裂,耐用性差无法成型深度大、复杂度高、片材厚的产品。
托盘厚片吸塑加工工艺
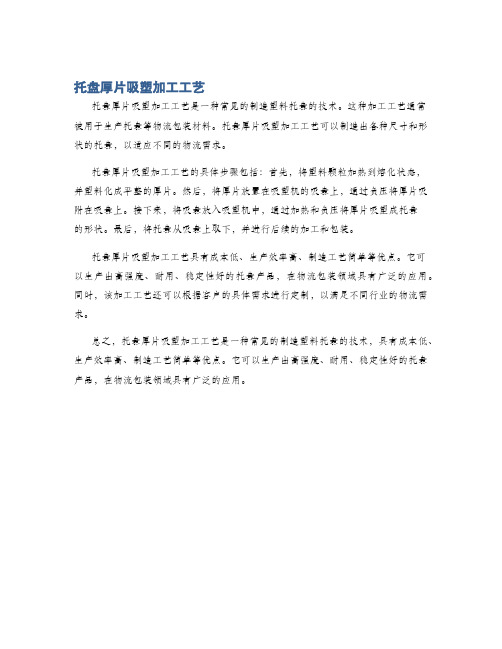
托盘厚片吸塑加工工艺
托盘厚片吸塑加工工艺是一种常见的制造塑料托盘的技术。
这种加工工艺通常被用于生产托盘等物流包装材料。
托盘厚片吸塑加工工艺可以制造出各种尺寸和形状的托盘,以适应不同的物流需求。
托盘厚片吸塑加工工艺的具体步骤包括:首先,将塑料颗粒加热到熔化状态,并塑料化成平整的厚片。
然后,将厚片放置在吸塑机的吸盘上,通过负压将厚片吸附在吸盘上。
接下来,将吸盘放入吸塑机中,通过加热和负压将厚片吸塑成托盘
的形状。
最后,将托盘从吸盘上取下,并进行后续的加工和包装。
托盘厚片吸塑加工工艺具有成本低、生产效率高、制造工艺简单等优点。
它可以生产出高强度、耐用、稳定性好的托盘产品,在物流包装领域具有广泛的应用。
同时,该加工工艺还可以根据客户的具体需求进行定制,以满足不同行业的物流需求。
总之,托盘厚片吸塑加工工艺是一种常见的制造塑料托盘的技术,具有成本低、生产效率高、制造工艺简单等优点。
它可以生产出高强度、耐用、稳定性好的托盘产品,在物流包装领域具有广泛的应用。
吸塑成型工艺流程

吸塑成型工艺流程
在现代工业生产中,吸塑成型是一种常见的加工工艺,主要用于制作各种塑料制品,如包装盒、模型、汽车零件等。
吸塑成型是利用热塑性塑料在加热软化状态下吸附在吸塑模具表面,经冷却后形成所需形状的一种加工技术。
下面将介绍吸塑成型的工艺流程。
1. 模具设计与制作
吸塑成型的第一步是设计并制作吸塑成型模具。
模具的设计应满足所需产品的形状和尺寸要求,同时考虑到塑料软化后的流动性和收缩率。
一般采用CNC加工制作模具,确保模具表面光滑、尺寸精确。
2. 材料准备
在进行吸塑成型前,需要选择适合的热塑性塑料作为原料。
常用的塑料材料有聚丙烯(PP)、聚乙烯(PE)、聚苯乙烯(PS)等。
材料的选择要根据产品的用途、外观要求等进行综合考虑。
3. 加热和成型
首先将选定的塑料片或板放置在吸塑机的加热区域,通过加热使塑料软化。
随后,将软化的塑料片移到吸塑模具上,启动吸气泵或加压系统,使塑料紧密吸附在模具表面。
塑料在模具内冷却定型后,可打开模具取出成型好的零件。
4. 后处理
成型后的产品可能需要进行一些后处理工艺,如去除边角毛刺、打磨表面、喷漆等,以提高产品的外观质量和功能性。
5. 检验和包装
最后,对成型产品进行质量检验,检查产品的尺寸精度、外观缺陷等,确保产品符合要求。
合格的产品将进行包装,以便运输和销售。
通过以上工艺流程,塑料制品经过吸塑成型加工后可以获得各种形状复杂、尺寸精确的产品。
吸塑成型作为一种高效、经济的生产工艺,被广泛应用于塑料制品的制造领域,为各行各业提供了方便和实用的解决方案。
吸塑工艺简介

吸塑
6.产品与型腔间隙尺寸 一般情况下,单边0.2mm的间隔。但是如果型腔较深就要考虑拔模对产品间隔的影响。 7.吸塑方式选择 一般是正方向吸塑成型,但是由于受产品结构等问题的影响,比如型腔深度较深而且强度要求较高,可以使用倒吸的方式。 8.切边设计 吸塑最终都需要刀模切割多余边料的,如果设计无切边的,需要注意刀模切边以后会有至少0.5mm的残留。如果该尺寸有配合的需要注意。
吸塑
9.绘图问题 抽壳: 一般情况下,大家在设计产品时打算使用1mm的材料时,会抽壳1mm。实际上吸塑成型过程中,型腔的底部以及侧边厚度会变薄,所以建议大家在设计时适当考虑产品抽壳时的厚度。一般符合前面所述的设计要求的话,以1mm材料为例,抽壳厚度可以选择0.8mm或者0.5mm。 10.模具加工成本问题 尽量减少模具的加工。 比如台阶加工能减少加工的尽量减少,平面圆角如果没有要求可以考虑吸塑成型自然角,从而降低模具加工过成本。
吸塑
4.PP PP片材是PP树脂经啤出、压光、切边等工艺过程而制成,具有质轻、表面光亮平静、耐热性好、机械性强度高、优良的化学稳定性和电绝源性、无毒等特点,经过热成型可制成饮料杯、食品盒等日用品。 PP主要特点 可在100℃长期使用并能经受121℃的高温菌处理,防潮性能突出,卫生性能可靠,广泛用于食品包装。具有优良的折合性能,可制成文具夹、盒等。
吸塑
吸塑
5、热合模具 热合模具采用优质铜或合金铝,主要针对PET高周波热封难的问题;表面处理采用特氟龙,针对PET粘模;压边花纹采用电脑刻花,纹路清晰、大小均匀一致,可根据用户要求定制各类花纹。 6、高频模具 高频模具材料为优质压线,切刀为激光刀,切边光滑无任何毛刺边撕料;压边花纹采用电脑刻花,纹路清晰、大小均匀一致,可根据用户要求定制各类花纹;飞机孔可根据客供实样或图纸而制作;主要用于双泡壳(PVC或PETG)的熔接。
吸塑工艺流程详细概述

吸塑工艺流程详细概述1. 设计产品模具:首先需要根据产品的设计要求,制作相应的塑料吸塑模具。
模具通常由铝合金或者硅胶等材料制成,能够准确地复制产品的形状。
2. 热塑性塑料清洁和预加热:将需要加工的热塑性塑料板料或者颗粒进行清洁和预加热处理,以确保塑料表面干净并使其变得柔软易塑性。
3. 将塑料片放入吸塑机中:将预加热的塑料片或颗粒放入吸塑机的固定台面上,根据产品模具形状的大小,经过形状迁移,吸附形状固化。
4. 加热和成型:吸塑机将塑料片或颗粒进行加热烘烤,使其变得柔软并开始融化。
随后,模具会通过真空吸力或者压力将软化的塑料片吸附在模具上,进行成型。
5. 冷却和固化:成型完成后,通过冷却系统或者自然冷却的方式对塑料产品进行冷却,并且固化后,塑料产品就可以取出。
6. 修整和去除余料:取出成型的产品后,需要进行修整,修剪掉多余的边角或者余料,使其更加美观和符合设计要求。
7. 检验和包装:最后,对成品进行检验,确保产品质量符合要求,然后进行包装,准备发货或者上市销售。
通过上述工艺流程,可以制作出各种各样的塑料制品,如塑料包装盒、包装袋、汽车内饰件等。
吸塑工艺因其制作过程简单、成本低廉、生产效率高等优点,被广泛应用于日常生活和工业生产中。
吸塑工艺流程详细概述8. 制品加工与后续处理:在产品完成吸塑成型后,可能需要进行一些后续加工处理,例如涂漆、丝印或者装配等。
这些加工工序有助于提升产品的外观和功能性,使其更符合市场需求。
9. 原料回收与再利用:吸塑工艺生产过程中可能会产生一定量的废料,这些废料可以被回收再利用,减少对环境的污染和资源的浪费。
通过一些再生塑料的处理,可以将其重新加工成为塑料颗粒,再次用于吸塑工艺的生产中。
吸塑工艺是一种非常灵活和高效的塑料加工技术,它可以用于加工各种种类和尺寸的塑料制品,从小型的日用品到大型的汽车零部件都可以被制作出来。
例如,塑料盒、包装盒、托盘、盒式零部件、汽车内饰、电子产品外壳等等。
吸塑生产工艺流程

吸塑生产工艺流程吸塑生产工艺流程是将塑料通过加热软化后,通过气压吸附在模具上形成所需的产品形状的一种加工工艺。
以下是一篇关于吸塑生产工艺流程的700字的文章。
吸塑生产工艺流程是一种常用的塑料加工工艺,可以制造各种形状各异的塑料产品。
吸塑生产工艺流程包括模具制作、塑料材料准备、加热吸附、冷却成型等多个环节。
首先,吸塑生产工艺的第一步是模具制作。
模具是吸塑生产的关键工具,它的制作过程包括设计、加工、组装等环节。
模具的设计要符合产品的形状和尺寸要求,同时考虑到产品的结构和功能。
制作模具所使用的材料通常是铝合金或不锈钢,具有耐高温和耐磨损的特性。
接下来是塑料材料的准备,吸塑生产通常使用的塑料材料有PVC、PS、PET等。
根据产品的要求选择适当的塑料材料,将其切割成一定长度的块状或片状,以便于后续的加热处理。
第三步是加热吸附,将切割好的塑料材料放入吸塑机中进行加热处理。
吸塑机内部有一组供热装置,可以将塑料材料加热到软化温度,使其变得柔软易形。
加热过程中需要控制好温度和加热时间,避免过热或不足。
在加热过程中,吸塑机开始工作,通过负压把软化的塑料材料吸附在模具上。
吸气机通过通风装置将模具内的空气排出,形成一个真空环境,使塑料材料能够完整地贴合在模具表面。
吸附过程需要良好的密封性和稳定的压力,以确保产品的形状和质量。
完成吸附后,需要进行冷却成型。
在吸塑机的模具下方有一个冷却装置,通过冷却水循环可以迅速将吸附在模具上的塑料材料冷却固化。
冷却的时间和温度也需要精确控制,以确保产品的尺寸和形状稳定。
最后,将冷却固化的塑料产品从模具中取出,进行后续加工和组装。
通常会进行修边、打磨、装饰、包装等工艺,使产品更加美观和实用。
吸塑生产工艺流程简单明了,通过多个环节的精确控制,可以制造各种形状和尺寸的塑料产品。
吸塑生产工艺流程不仅适用于大批量生产,也适用于小批量和个别定制的生产。
吸塑产品广泛应用于家电、玩具、宣传品、汽车零部件等领域,给人们的生活带来了便利和美好。
吸塑生产工艺介绍

从材料,模具,吸塑,冲压各环节认识吸塑产品的全过程2021年6月目录CONTENTS01吸塑流程图02常用材料的认识03模具的介绍04吸塑成型介绍05裁切包装吸塑流程图打样流程图量产流程图吸塑工艺流程图与实物试装产品图纸/实物制作/修改石膏模石膏模材料吸塑打样冲压裁切不合格合格铜模/铝模量产1成品检验包装冲切半成品检验吸塑工艺流程图吸塑成型入库吸塑原材料2材料的认识材料种类材料的判认材料特性12345聚对苯二甲酸乙二醇酯Polyethylene terephthalate PET聚苯乙烯PolystyrenePS聚丙烯polypropylenePP聚对苯二甲酸乙二醇酯PETG聚氯乙烯Polyvinyl chloridePVC吸塑常用材料透明度高,不易破边,属环保材料,可周转使用。
优点高度结晶的聚合物,表面平滑有光泽。
耐疲劳性,耐摩擦性,尺寸稳定性好。
性质成型温度:70-80℃ 冷却时间:14-20s 熔化温度:120℃开始溶化温度要求吸塑常用材料易破碎,根据温度不同会有发白现象存在,有同厂家颜色有差异。
缺点用于包装电子、五金、玩具、食品、化妆品、学习用品等。
用途吸塑常用材料2.PS的认识透明度高,不易破边,属环保材料,可周转使用。
优点拉伸强度可达60Mpa 以上,冲击强度小,耐磨性差,力学性随温度升高而变大,收缩率为0.4-0.7%。
性质成型温度:75-85℃ 冷却时间:14-20s 熔化温度:95-150℃开始溶化温度要求易破边,周使用率底,不同厂家生产的颜色有差异。
缺点用于包装电子、五金、玩具、食品、化妆品、学习用品等。
用途吸塑常用材料刚硬有韧性、抗弯强度高、抗疲劳、抗应力开裂;质轻;在100-150℃仍能保持力学性。
优点半结晶性材料,比PE要更坚硬且有更高的熔点。
由于结晶度较高,表面的刚度和抗划痕特性很好。
收缩率为1.8-2.5%。
性质成型温度:140℃以上冷却时间:24-30s溶化温度:150-220℃开始熔化温度要求0℃以下变脆;耐侯性高。
夹板吸塑工艺流程

夹板吸塑工艺流程
是一种先进的塑料加工技术,主要用于生产各种塑料制品,如托盘、盒子、盖子等。
该工艺流程包括以下几个主要步骤:
第一步:设计模具
首先,根据所需制品的形状和尺寸,设计出相应的模具。
模具设计需要考虑到产品的结构、外形和功能等因素。
设计好模具后,需要制作成实体模具。
第二步:准备原料
在夹板吸塑工艺中,常用的原料通常是塑料颗粒或片材。
根据产品的要求,选择合适的塑料材料,并将其加热至适当温度,以便后续吸塑成型。
第三步:吸塑成型
将准备好的原料放置在模具上方,然后通过加热的方式使原料软化。
一般情况下,利用吸力设备将软化的塑料材料吸附到模具的表面,迅速使其冷却凝固。
这样就可以形成产品的外形和结构。
第四步:去除余料
待产品冷却凝固后,需要将模具打开,取出成型的产品。
通常情况下,成型产品的边缘会有一些余料,需要使用切割设备将其去除,以获得整齐的产品外观。
第五步:加工处理
成型的产品表面可能会有一些不规则的部分或划痕,需要使用加工设备进行处理,使产品表面光滑柔软。
第六步:成品包装
处理完产品表面后,将成品进行包装,保护产品不受环境影响和损坏。
包装方式可以根
据产品的特性和用途来确定。
以上就是夹板吸塑工艺流程的基本步骤。
通过这些步骤,可以生产高质量的塑料制品,满足不同客户的需求。
夹板吸塑工艺具有成本低、效率高、生产周期短等优点,被广泛应用于电子、医疗、玩具、食品等多个领域。
吸塑模具制作流程
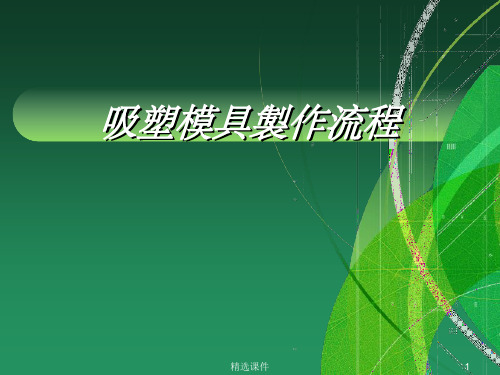
鋁模
鋁模 表面光滑度要求高的,零件小的,間距小的,形狀不 規則的必須以鋁模來制模具 ﹐鋁模使用壽命最长
u不论是铝模还是铜模,一旦模具完成,生产过程中不用担心尺寸会有变动,
因为吸塑模是单模,稳定性比较好!
精选课件
10
吸塑模具製作主要過程
設計
加工
打孔拋光
精选课件
11
吸塑模具设计步骤
序号 1
2 3 4
广泛应用于工业包装,醫療器材包裝等
二:植绒吸塑盘
是一种采用特殊材料的吸塑托盘,将普通的塑料硬片表面粘上一层绒 质材料,从而使托盘表面有种绒质的手感,用来提高包装品档次。
三:抗静电吸塑盘
是一采用特殊材料的吸塑托盘,该材料表面的电阻值小于10的11次方
欧姆。主要用于电子、IT产品的吸塑托盘。
精选课件
4
吸塑盘的展示
风干后形成石膏毛胚
手工打磨和手工添加部件
将各个抛光好的石膏部件 粘合成完整的石膏模
送樣
按成品尺寸,手工切边、 封边,完成全部打样过程
精选课件
再放入吸塑打版机吸塑 成型完整的样品
6
吸塑生產的流程
裁邊,包裝
精选课件
7
吸塑盘的设计原理
吸塑模具設計的原理:
• 设计理念:
在保证客户零件品质的前提下,设计一种包装 能够保护产品,美化产品,并且拿取方便,排版合理, 不浪费(在模具强度和空间允许的情况下,尽可能 多的摆放产品).
因为在单穴设计时需要用到原料的收缩率及成型后的平均 料厚
2. 确定TRAY的长宽规格
避免TRAY的外形尺寸与客户端纸箱尺寸不相匹配.
精选课件
14
吸塑模具设计步骤
3.TRAY的高度设计 TRAY高H=内含高A+成品上间
吸塑生产流程
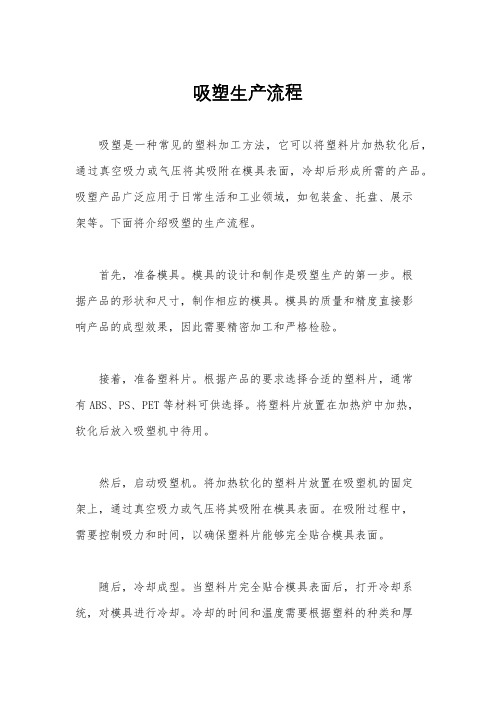
吸塑生产流程吸塑是一种常见的塑料加工方法,它可以将塑料片加热软化后,通过真空吸力或气压将其吸附在模具表面,冷却后形成所需的产品。
吸塑产品广泛应用于日常生活和工业领域,如包装盒、托盘、展示架等。
下面将介绍吸塑的生产流程。
首先,准备模具。
模具的设计和制作是吸塑生产的第一步。
根据产品的形状和尺寸,制作相应的模具。
模具的质量和精度直接影响产品的成型效果,因此需要精密加工和严格检验。
接着,准备塑料片。
根据产品的要求选择合适的塑料片,通常有ABS、PS、PET等材料可供选择。
将塑料片放置在加热炉中加热,软化后放入吸塑机中待用。
然后,启动吸塑机。
将加热软化的塑料片放置在吸塑机的固定架上,通过真空吸力或气压将其吸附在模具表面。
在吸附过程中,需要控制吸力和时间,以确保塑料片能够完全贴合模具表面。
随后,冷却成型。
当塑料片完全贴合模具表面后,打开冷却系统,对模具进行冷却。
冷却的时间和温度需要根据塑料的种类和厚度来确定,以确保产品能够完全成型。
最后,脱模和修整。
当产品冷却后,打开吸塑机,取出成型的产品。
然后进行修整,去除多余的边料和毛刺,使产品的表面光滑整洁。
通过以上几个步骤,一个吸塑产品就完成了整个生产流程。
当然,在实际生产中还需要考虑原材料的储存和管理、模具的维护和更换、产品的质量检验等环节。
吸塑生产流程需要严格控制各个环节,以确保产品质量和生产效率。
同时,随着技术的不断进步,吸塑生产流程也在不断优化和改进,以满足市场对于个性化、高品质产品的需求。
总的来说,吸塑生产流程是一个复杂而精密的过程,需要各个环节的配合和协调。
只有严格按照标准操作,才能生产出高质量的吸塑产品,满足市场和客户的需求。
希望本文能够为吸塑生产流程的了解和实践提供一些帮助。
吸塑工艺流程简介

一、吸塑制品的主要分类1、若按照材料的厚度来分类,则可以分为A、普通薄吸塑厚度为0.14~5.0mm―――主要是采用PVC、PP、PS(HIPS)、PET(包括APET和PETG)、PE、BOPS和可回收纸托等各种材质与效果的折边、对折、三折、圆筒、折盒、天地盒、高周波等非热成型吸塑制品,广泛应用于食品、医药、电子、玩具、电脑、日用品、化妆品和机械五金等行业。
B、特殊厚吸塑厚度为0.14~8.0mm―――主要是采用PVC、PP、PS(HIPS)、PET(包括APET和PETG)、ABS、PC、PE和PMMA等各种材质与效果的注塑类型吸塑制品,主要产品有冰箱内胆、广告灯箱、商品展示架、宠物笼底盘、背投电视后壳和各种机械面板等,可以替代注塑产品,具有模具费用低(只有注塑模具的1/20),生产周期短,模具开发时间短(一般只要3~5天)等特点。
之所以不就材料的种类来进行分类,主要是考虑到普通薄吸塑与特种厚吸塑所采用的材料有一些区别,但是PVC、PP、PS和PET却在这两类吸塑制品中都占有一席之地,堪称吸塑制品用材家族的“四大天王”!PVC硬片韧性适中,不易燃烧,燃烧时会产生氯气,对环境造成一定影响,PVC易热合,可采用封口机和高频机封边,是生产透明吸塑制品的主要原料PS硬片密度低,韧性差,易燃烧,燃烧时会产生苯乙烯气体(属有害气体),所以一般用来生产各种工业用的吸塑托盘。
PET硬片韧性好,透明度高,易燃烧,燃烧时不产生有害气体,属于环保材料,但价格高,适宜做高档的吸塑制品,欧美国家的吸塑泡壳一般要求采用PET硬片,但其不易热合,给封装带来很大困难,为了解决这一问题,人们在PET表面复合上一层PVC膜,取名为PETG 硬片,但价格更高一些。
PVC片材是一种用途广泛而深受欢迎的材料,PVC胶片可以分为食品级及工业级两种,且可以制成透明、彩色、防静电、镀金、植绒等各种各样片材用于真空成型,其特点主要透明度高、表面光泽好、晶点少、水纹小、用途广、耐冲击性强、并且易于成型,制成产品符合美国FDA、日本PL食品卫生标准,制成产品广泛用于玩具、食品、电子产品、医药、电器、礼品、化妆品、文具等产品外包装。
吸塑的工艺流程

吸塑的工艺流程吸塑,又称真空吸塑或热成型,是一种常见的塑料加工工艺,通过加热和真空吸力,将塑料片材成型成各种产品。
吸塑工艺广泛应用于包装、日用品、玩具、电子产品等领域,其工艺流程包括模具设计、材料选择、加热成型、冷却固化等多个环节。
下面我们将详细介绍吸塑的工艺流程。
首先是模具设计。
模具是吸塑成型的关键,其设计需要充分考虑产品的形状、尺寸、壁厚等因素。
一般来说,模具分为上模和下模,上模用于加热和成型,下模用于支撑和冷却。
模具设计需要根据产品的要求确定材料、尺寸和结构,确保成型后的产品符合设计要求。
接下来是材料选择。
吸塑常用的材料包括ABS、PS、PETG、PVC 等,不同的材料具有不同的特性,如耐高温、耐冲击、透明度等。
在选择材料时,需要考虑产品的用途、外观要求、成本等因素,以确保选择合适的材料进行成型。
然后是加热成型。
在吸塑加工中,首先将塑料片材放置在模具上模部分,然后加热至一定温度,使其软化变形。
加热的方式可以采用热风加热、红外线加热等,根据不同的材料和产品要求选择合适的加热方式。
一般来说,加热温度和时间需要根据材料的特性和厚度进行调整,以确保塑料片材能够完全软化。
接着是真空吸力。
当塑料片材软化后,上模部分下压,同时启动真空泵,将模具内部的空气抽出,形成真空状态。
在真空吸力的作用下,塑料片材紧贴模具表面,成型成产品的形状。
真空吸力的大小需要根据产品的形状和尺寸进行调整,以确保成型后的产品无气泡、无瑕疵。
最后是冷却固化。
在产品成型后,需要继续保持真空状态,同时进行冷却,使塑料片材迅速固化。
冷却的方式可以采用自然冷却或者水冷却,根据产品的要求选择合适的方式。
冷却时间需要根据材料的特性和厚度进行调整,以确保产品完全固化。
以上就是吸塑的工艺流程,通过模具设计、材料选择、加热成型、真空吸力和冷却固化等环节,将塑料片材成型成各种产品。
吸塑工艺具有成本低、生产效率高、产品质量稳定等优点,因此在各个领域得到广泛应用。
吸塑工艺流程

吸塑工艺流程吸塑工艺流程是一种将热变形塑料加热软化后,通过负压吸附到模具表面形成所需形状的塑料成型技术。
下面将详细介绍吸塑工艺的流程。
首先,准备工作是设计好所需的产品模型和制作好模具。
这一步是整个吸塑工艺流程的基础,需要根据产品的尺寸、形状和结构要求来进行设计和制作。
模具通常由铝合金或塑料制成,具有良好的导热性和耐高温的特性。
第二步是将所选的热变形塑料材料加热至一定温度,使其软化。
常用的热变形塑料材料有聚氯乙烯(PVC)、聚丙烯(PP)和聚苯乙烯(PS)等。
加热材料的方法可以是使用加热炉、热风枪或热板等。
接下来,将软化后的塑料片放置在模具的上方,然后通过负压吸附将塑料片吸附到模具的表面。
负压是通过真空泵或真空系统产生的,可以将空气抽出,形成负压环境,使塑料片与模具紧密贴合,以获得所需形状。
紧接着,将模具放入冷却器中进行冷却。
冷却可以采用自然冷却或水冷却的方式。
冷却的目的是使塑料在固化过程中保持所需形状,并且提高其硬度和稳定性。
冷却完成后,打开模具,取出成型的塑料制品。
在取出塑料制品之前,需要先将模具中的气压恢复到正常的大气压力,以避免产生形变或损坏。
最后,对成型的塑料制品进行后续的处理、修整和喷漆等,以满足最终产品的外观和质量要求。
此外,对于特殊要求的产品,还可以进行热成型和冷嵌入等工艺,来增加产品的功能和美观。
吸塑工艺流程具有简单、快速、灵活等优点,可以用于制作各种形状和尺寸的塑料制品。
它广泛应用于家电、医疗器械、玩具、广告标牌等行业,为人们的生活和工作带来了便利和美好。
当然,不同的产品具有不同的要求和流程,以上仅为一般性的吸塑工艺流程介绍。
吸塑成型知识点总结
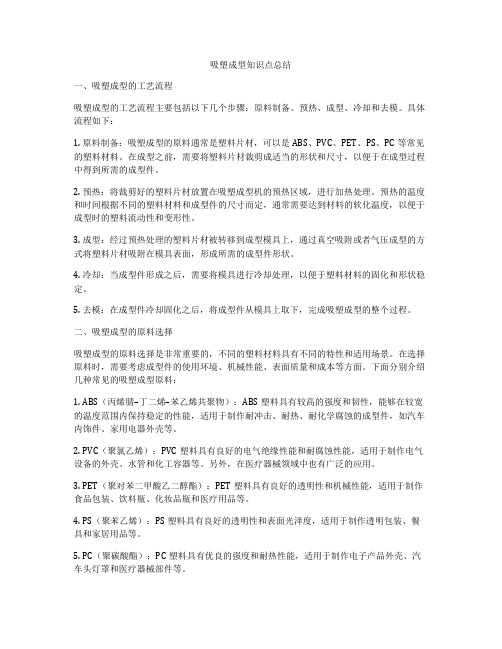
吸塑成型知识点总结一、吸塑成型的工艺流程吸塑成型的工艺流程主要包括以下几个步骤:原料制备、预热、成型、冷却和去模。
具体流程如下:1. 原料制备:吸塑成型的原料通常是塑料片材,可以是ABS、PVC、PET、PS、PC等常见的塑料材料。
在成型之前,需要将塑料片材裁剪成适当的形状和尺寸,以便于在成型过程中得到所需的成型件。
2. 预热:将裁剪好的塑料片材放置在吸塑成型机的预热区域,进行加热处理。
预热的温度和时间根据不同的塑料材料和成型件的尺寸而定,通常需要达到材料的软化温度,以便于成型时的塑料流动性和变形性。
3. 成型:经过预热处理的塑料片材被转移到成型模具上,通过真空吸附或者气压成型的方式将塑料片材吸附在模具表面,形成所需的成型件形状。
4. 冷却:当成型件形成之后,需要将模具进行冷却处理,以便于塑料材料的固化和形状稳定。
5. 去模:在成型件冷却固化之后,将成型件从模具上取下,完成吸塑成型的整个过程。
二、吸塑成型的原料选择吸塑成型的原料选择是非常重要的,不同的塑料材料具有不同的特性和适用场景。
在选择原料时,需要考虑成型件的使用环境、机械性能、表面质量和成本等方面。
下面分别介绍几种常见的吸塑成型原料:1. ABS(丙烯腈–丁二烯–苯乙烯共聚物):ABS塑料具有较高的强度和韧性,能够在较宽的温度范围内保持稳定的性能,适用于制作耐冲击、耐热、耐化学腐蚀的成型件,如汽车内饰件、家用电器外壳等。
2. PVC(聚氯乙烯):PVC塑料具有良好的电气绝缘性能和耐腐蚀性能,适用于制作电气设备的外壳、水管和化工容器等。
另外,在医疗器械领域中也有广泛的应用。
3. PET(聚对苯二甲酸乙二醇酯):PET塑料具有良好的透明性和机械性能,适用于制作食品包装、饮料瓶、化妆品瓶和医疗用品等。
4. PS(聚苯乙烯):PS塑料具有良好的透明性和表面光泽度,适用于制作透明包装、餐具和家居用品等。
5. PC(聚碳酸酯):PC塑料具有优良的强度和耐热性能,适用于制作电子产品外壳、汽车头灯罩和医疗器械部件等。
吸塑加工工艺流程
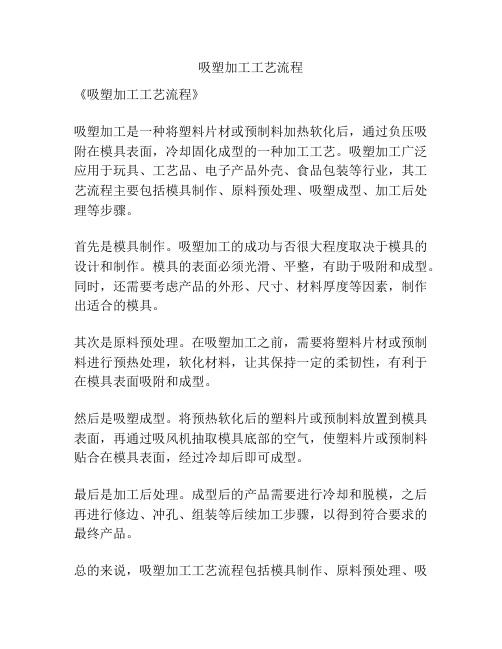
吸塑加工工艺流程
《吸塑加工工艺流程》
吸塑加工是一种将塑料片材或预制料加热软化后,通过负压吸附在模具表面,冷却固化成型的一种加工工艺。
吸塑加工广泛应用于玩具、工艺品、电子产品外壳、食品包装等行业,其工艺流程主要包括模具制作、原料预处理、吸塑成型、加工后处理等步骤。
首先是模具制作。
吸塑加工的成功与否很大程度取决于模具的设计和制作。
模具的表面必须光滑、平整,有助于吸附和成型。
同时,还需要考虑产品的外形、尺寸、材料厚度等因素,制作出适合的模具。
其次是原料预处理。
在吸塑加工之前,需要将塑料片材或预制料进行预热处理,软化材料,让其保持一定的柔韧性,有利于在模具表面吸附和成型。
然后是吸塑成型。
将预热软化后的塑料片或预制料放置到模具表面,再通过吸风机抽取模具底部的空气,使塑料片或预制料贴合在模具表面,经过冷却后即可成型。
最后是加工后处理。
成型后的产品需要进行冷却和脱模,之后再进行修边、冲孔、组装等后续加工步骤,以得到符合要求的最终产品。
总的来说,吸塑加工工艺流程包括模具制作、原料预处理、吸
塑成型、加工后处理等多个环节,各个环节的工艺控制都直接关系到产品的质量和性能。
随着科技的不断进步,吸塑加工工艺也在不断完善和提高,成为塑料加工领域中一种重要的加工工艺。
吸塑工艺流程图

吸塑工艺流程图吸塑生产过程可包括途径一打电话询价,途径二发传真询价,途径三发Email询价,途径四通过网络聊天工具询价。
客户须提供吸塑制品的长、宽、高和所用材料的厚度、颜色和型号(PVC、PET、PS),产品数量和生产周期吸塑制品单价的高低跟以下因素有关:吸塑制品的长、宽、高和吸塑成型的复杂程度;所用材料的类型厚度和颜色;吸塑产品的后道加工工艺(折边、打孔、封边等)、订单数量和订单周期。
报价员会以户的样品和描述有一个最初报价,最终报价会在打样之后报出。
客户对于报价基本认可后,会将要求、实物或是吸塑样品交到业务部,生产调度会要求电脑设计部将户的实物扫描并结合印刷品的设计,制作出吸塑制品的平面设计图客户认可电脑设计稿后,生产调度会根据吸塑产品的复杂程度决定采用哪种方式开发模具(石膏模、模、铝模),开发周期3-5天。
吸塑打样以石膏模打样居多,其操作步骤是:1.先将实物用手工泥糊成型轮廓;2.放到吸塑打版机上成型泡壳毛胚;3.用配好的吸塑专用石膏倒入泡壳毛胚中,风干后形石膏毛胚;4.采用电动铣床对石膏毛胚和规则形状进行深加工;5.手工打磨和手工添加部件;6.将各抛光好的石膏部件粘合成完整的石膏模;7.再放入吸塑打版机吸塑成型完整的样品;8.按成品尺寸,工切边、封边,完成全部打样过程。
如果有需求,印刷打样部门同时会将吸塑样品所用的纸卡、不干或彩盒一起制作,他们会借助全开的印刷数码打样机能将实际印刷结果反映出来。
样品被客户认可后,通常会下一定数量的生产订单。
生产调度会根据产量、吸塑成型的复杂程度决定用哪种模具量产:采用石膏模生产,模具制作过程类似于吸塑打样,优点在于生产周期短,成本最低制作一整版(60X110cm)模具只需一到两天时间,不足之处在于吸塑成品表面粗糙,生产中模具容易碎裂,耐用性差无法成型深度大、复杂度高、片材厚的产品。
采用电镀铜模,其工艺是将打好样的泡壳面喷上一层导电剂,再放入电解槽内镀上厚厚的铜层,电镀过程需要72小时,接着要对铜模进行灌石膏(增加硬度)、抛光、打气眼处理,采用电镀铜模生产的优点是吸塑制品表面光滑,成本适中,耐性强,缺点是模具制作周期长,无法完成精密吸塑制品的生产。
- 1、下载文档前请自行甄别文档内容的完整性,平台不提供额外的编辑、内容补充、找答案等附加服务。
- 2、"仅部分预览"的文档,不可在线预览部分如存在完整性等问题,可反馈申请退款(可完整预览的文档不适用该条件!)。
- 3、如文档侵犯您的权益,请联系客服反馈,我们会尽快为您处理(人工客服工作时间:9:00-18:30)。
吸塑盘工艺流程
一、吸塑打样
客户认可电脑设计稿后,生产调度会根据吸塑产品的复杂程度决定采用哪种方式开发模具(石膏模、铜模、铝模),开发周期3-5天。
吸塑打样以石膏模打样居多。
其操作步骤是:
1.先将实物用手工泥糊出成型轮廓;
2.放到吸塑打版机上成型泡壳毛胚;
3.用配好的吸塑专用石膏倒入泡壳毛胚中,风干后形成石膏毛胚;
4.采用电动铣床对石膏毛胚和规则形状进行深加工;
5.手工打磨和手工添加部件;
6.将各个抛光好的石膏部件粘合成完整的石膏模;
7.再放入吸塑打版机吸塑成型完整的样品;
8.按成品尺寸,手工切边、封边,完成全部打样过程。
如果有需求,印刷打样部门同时会将吸塑样品所用的纸卡、不干胶或彩盒一起制作,他们会借助全开的印刷数码打样机能将实际印刷结果反映出来。
二、制作生产模具
样品被客户认可后,通常会下一定数量的生产订单。
生产调度会根据产量、吸塑成型的复杂程度决定采用哪种模具量产: 1、
采用石膏模生产
模具制作过程类似于吸塑打样,优点在于生产周期短,成本最低,制作一整版(60X110cm)模具只需一到两天时间,不足之处在于吸塑成品表面粗糙,生产中模具容易碎裂,耐用性差无法成型深度大、复杂度高、片材厚的产品。
2、采用电镀铜模
其工艺是将打好样的泡壳表面喷上一层导电剂,再放入电解槽内镀上厚厚的
铜层,电镀过程需要72小时,接着要对铜模进行灌石膏(增加硬度)、抛光、打气眼处理,采用电镀铜模生产的优点是吸塑制品表面光滑,成本适中,耐用性适中,缺点是模具制作周期长,无法完成精密吸塑制品的生产。
3、采用吸塑铝模生产,
模具制作需要先采用电脑设计图纸,再采用CNC数控铣床加工,优点是制作周期适中,后期模具处理时间短(钻气眼工作在CNC加工时完成),吸塑产品尺寸精度高,模具耐用性强,缺点是成本高。
由于全自动高速吸塑成型机的成型范围是66X110cm左右,所以不管是石膏模、铜模还是铝模,都需要将单个的模具拼在一起,达到成型尺寸,我们都称这个过程为拼版,需要拼在打好气孔的铝板或木板上,拼好后的整版模具我们称之为底模。
对于吸塑成型深度大的产品,还需要制作上模,在底模将片材真空吸成型的同时,从片材上方施加压力,将片材均匀地拉伸到每一个部位,否则会引起局部厚度过薄。
生产模具的整个制作周期应为5至7天。
三、吸塑成型生产
采用全自动高速吸塑成型机生产,其基本原理是:
将成卷的片材拉进电炉烘箱内加热至软化状态,乘热再拉到吸塑模具上方,模具上移并抽真空,将软化的片材吸附到模具表面,同时将冷却水以雾状喷于成型片材表面,使其硬化,成型的片材再自动被拉至贮料箱,气动裁刀将成型与未成型片材分离,从而完成全部过程。
吸塑产品出现的主要质量问题大多在此过程发生:
1.吸塑不到位,是指形状变形,没有吸塑成与模具相同形状的产品;
2.吸塑
过度,是指产品过薄;
3.拉线,是指成型产品上出现不应有的线痕;
4.厚薄不均。
这些问题都需要在上好模具后,调试到位,包括:片材前进的时间、加热的温度和时间、抽真空的强度和时间、上模下落的位置、时间和深度、拼版中模具的摆放位置、模具间是否加附件等等。
四、冲床加工
吸塑成型的大版面产品必须经过冲床,用一块刀版分割成为单一的产品。
其原理是在冲床的底台上有一大张塑料砧板,将大版面成型产品放在砧板上,并把事先做好的刀模卡在单一产品上,通过冲床的上下运动,裁断出单一的成品,但这种裁断方式的不足之处在于砧板和刀模比较容易损坏,从而造成切边不光滑,有毛边,对于质量要求高的泡壳,需要用冷冲模(一个公模,一个母模)和冷冲床加工。