实用CNC加工参数设置标准
数控机床CNC参数设置

数控机床CNC参数设置1 CNC参数的调试修改方法⑴、在设置页面打开参数开关。
⑵、工作模式选择在录入方式。
⑶、在参数页面修改相应的参数。
⑷、修改完参数后关掉参数开关再按复位键,部分参数修改后还需关掉系统电源。
2了解每个CNC参数所对应的作用以及修改参数后机床性能的变化K1000M CNC参数一览表OTFP 1:输出最高频率为512Kpps。
0:输出最高频率为32Kpps。
RDRN 1:空运行时,快速运动指令运行有效。
0:空运行时,快速运动指令运行无效。
DECI 1:在返回参考点时减速信号为"1"表示减速(回零方式B 时有效)。
0:在返回参考点时减速信号为"0"表示减速。
IOF 1:用MDI键入时,偏置值为增量值。
0:用MDI键入时,偏置值为绝对值。
RS43 1:G43,G44的偏移矢量在复位时被清零。
0:G43,G44的偏移矢量在复位时保持不变。
DCS 1:MDI方式时,按【输出】键执行。
0:MDI方式时,按【循环启动】键执行。
SCW 1:最小指令增量按英制系统(机床是英制系统)。
0:最小指令增量按公制系统(机床是公制系统)。
NFDO 1:恒设为1TJHD 1:在手动示教方式中,手轮有效。
0:在手动示教方式中,手轮无效。
PM2,PM1:设定固定循环G76,G87中的退刀方向。
RSJG 0:按复位键时,系统自动关闭M03、M04、润滑、冷却输出。
1:按复位键时,对输出M03、M04、润滑、冷却输出没有影响。
MPOF 1:屏蔽电压低报警PPD 1:用绝对零点编程(G92)也设置相对坐标值。
0:用绝对零点编程(G92)不设置相对坐标值。
PCMD 1:输出波形是脉冲。
0:输出波形是方波。
PRGB :无意义。
TLCP 1:在与指定平面(G17,G18,G19)垂直的轴上进行刀具长度补偿。
(刀具长度补偿B)。
0:与指定平面无关,在Z轴上进行刀具长度补偿(刀具长度补偿A)。
CNC机床加工中的切削参数调优与控制
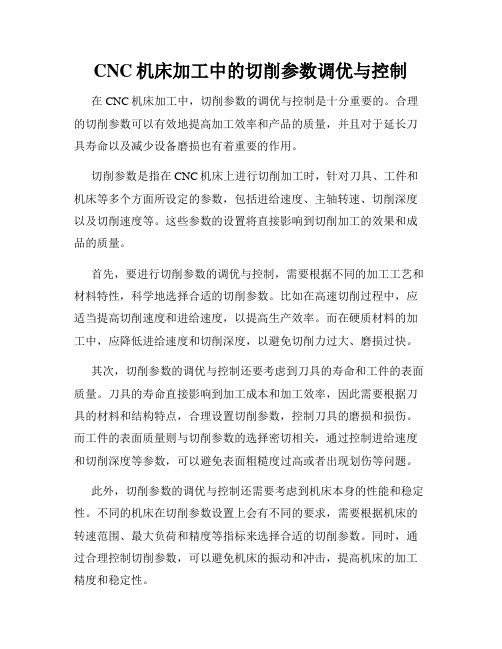
CNC机床加工中的切削参数调优与控制在CNC机床加工中,切削参数的调优与控制是十分重要的。
合理的切削参数可以有效地提高加工效率和产品的质量,并且对于延长刀具寿命以及减少设备磨损也有着重要的作用。
切削参数是指在CNC机床上进行切削加工时,针对刀具、工件和机床等多个方面所设定的参数,包括进给速度、主轴转速、切削深度以及切削速度等。
这些参数的设置将直接影响到切削加工的效果和成品的质量。
首先,要进行切削参数的调优与控制,需要根据不同的加工工艺和材料特性,科学地选择合适的切削参数。
比如在高速切削过程中,应适当提高切削速度和进给速度,以提高生产效率。
而在硬质材料的加工中,应降低进给速度和切削深度,以避免切削力过大、磨损过快。
其次,切削参数的调优与控制还要考虑到刀具的寿命和工件的表面质量。
刀具的寿命直接影响到加工成本和加工效率,因此需要根据刀具的材料和结构特点,合理设置切削参数,控制刀具的磨损和损伤。
而工件的表面质量则与切削参数的选择密切相关,通过控制进给速度和切削深度等参数,可以避免表面粗糙度过高或者出现划伤等问题。
此外,切削参数的调优与控制还需要考虑到机床本身的性能和稳定性。
不同的机床在切削参数设置上会有不同的要求,需要根据机床的转速范围、最大负荷和精度等指标来选择合适的切削参数。
同时,通过合理控制切削参数,可以避免机床的振动和冲击,提高机床的加工精度和稳定性。
在实际的CNC机床加工过程中,切削参数的调优与控制是一个不断优化和改进的过程。
随着刀具和材料的不断研发和改良,切削参数的选择也需要与时俱进。
因此,需要进行充分的实验研究和数据分析,结合工程实践经验,不断调整和改进切削参数,以求达到最佳的加工效果和成品质量。
总之,CNC机床加工中的切削参数调优与控制对于提高加工效率、保证产品质量以及延长设备和刀具的使用寿命都具有重要的意义。
通过合理选择和控制切削参数,可以实现更高效、更稳定的加工过程,为工业生产的发展做出积极的贡献。
CNC机床加工中的切削参数选择与优化

CNC机床加工中的切削参数选择与优化在CNC机床加工中,切削参数选择与优化是至关重要的一步。
正确的切削参数可以保证工件的质量,提高加工效率,同时还可以延长刀具的使用寿命。
本文将探讨CNC机床加工中的切削参数选择与优化的要点。
一、切削参数的选择在选择切削参数时,需要考虑以下几个方面:1.工件材料不同的工件材料对切削参数有着不同的要求。
一般来说,硬度较高的材料需要选择较大的进给量和切削速度,以保证切削效果。
而对于较软的材料,则需要选择较小的进给量和切削速度。
2.刀具材料和形状刀具的材料和形状也会影响切削参数的选择。
硬质合金刀具通常适用于高速切削,而高速钢刀具则适用于低速切削。
此外,刀具的形状也会对切削参数产生影响。
例如,球头刀具适合进行曲面加工,而平头刀具适合进行平面加工。
3.加工精度要求不同的加工精度要求也会对切削参数产生影响。
如果要求加工精度较高,就需要选择较小的进给量和切削速度,以提高加工的精度。
而如果加工精度要求较低,可以适当增大切削参数,以提高加工的效率。
二、切削参数的优化切削参数的优化可以通过试切试验和仿真模拟两种方法来进行。
1.试切试验试切试验是一种直接测量和比较不同切削参数效果的方法。
通过试切试验,可以找出切削参数与加工表面粗糙度、切削力等因素的关系。
根据试切试验的结果,可以调整切削参数,从而达到优化加工效果的目的。
2.仿真模拟仿真模拟是通过计算机软件对切削过程进行模拟和分析的方法。
通过仿真模拟,可以在不进行实际加工的情况下对不同的切削参数进行比较和优化。
仿真模拟可以节省时间和成本,并且可以预测加工结果,为切削参数的选择和优化提供依据。
三、切削参数的优化策略在进行切削参数的选择和优化时,可以采用以下几种常用的策略:1.保证切削稳定性切削过程中的稳定性对于保证加工质量和提高加工效率至关重要。
因此,在选择和优化切削参数时,要避免过大或过小的切削速度和进给量,以保证切削过程的稳定性。
2.控制切削温度切削过程中会产生大量的切削热量,如果温度过高,可能会导致刀具磨损加剧和工件变形。
CNC加工编程参数
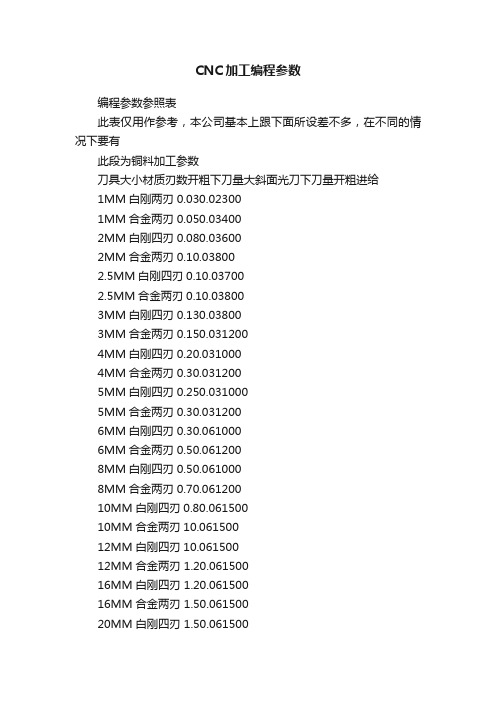
CNC加工编程参数编程参数参照表此表仅用作参考,本公司基本上跟下面所设差不多,在不同的情况下要有此段为铜料加工参数刀具大小材质刃数开粗下刀量大斜面光刀下刀量开粗进给1MM白刚两刃0.030.023001MM合金两刃0.050.034002MM白刚四刃0.080.036002MM合金两刃0.10.038002.5MM白刚四刃0.10.037002.5MM合金两刃0.10.038003MM白刚四刃0.130.038003MM合金两刃0.150.0312004MM白刚四刃0.20.0310004MM合金两刃0.30.0312005MM白刚四刃0.250.0310005MM合金两刃0.30.0312006MM白刚四刃0.30.0610006MM合金两刃0.50.0612008MM白刚四刃0.50.0610008MM合金两刃0.70.06120010MM白刚四刃0.80.06150010MM合金两刃10.06150012MM白刚四刃10.06150012MM合金两刃 1.20.06150016MM白刚四刃 1.20.06150016MM合金两刃 1.50.06150020MM白刚四刃 1.50.06150020MM合金两刃 1.50.06150025MM白刚四刃 1.50.06150025MM合金两刃 1.50.061500飞刀刀具刀具大小材质刃数开粗下刀量大斜面光刀下刀量开粗进给R6合金刀粒两刃0.450.151500R8合金刀粒两刃0.50.21500R10合金刀粒两刃0.60.2150012R0.4合金刀粒一刃0.70.1120016R0.4合金刀粒两刃0.70.1150020R0.4合金刀粒两刃0.70.1150025R0.8合金刀粒两刃10.1150030R5合金刀粒两刃0.60.31600球刀刀具刀具大小直径材质刃数开粗下刀量斜面光刀下刀量R0.51MM合金两刃0.020.02R11MM合金两刃0.040.05R1.53MM合金两刃0.060.07R24MM合金两刃0.150.1R2.55MM合金两刃0.20.1R36MM合金两刃0.30.12R48MM合金两刃0.30.12R510MM合金两刃0.50.15R612MM合金两刃0.50.15R816MM合金两刃0.60.2R1020MM合金两刃0.60.2编程参数参照表此表仅用作参考,本公司基本上跟下面所设差不多,在不同的情况下要有此段为钢料加工参数刀具大小材质刃数开粗下刀量大斜面光刀下刀量开粗进给2MM白刚四刃0.020.034002MM合金两刃0.040.035002.5MM白刚四刃0.020.034002.5MM合金两刃0.040.035003MM白刚四刃0.030.034003MM合金两刃0.050.036004MM白刚四刃0.050.036004MM合金两刃0.050.036005MM白刚四刃0.050.036005MM合金两刃0.050.038006MM白刚四刃0.060.066006MM合金两刃0.060.068008MM白刚四刃0.080.068008MM合金两刃0.10.06110010MM白刚四刃0.10.0680010MM合金两刃0.150.06110012MM白刚四刃0.130.07120012MM合金两刃0.150.07130016MM白刚四刃0.150.11300 16MM合金两刃0.20.11300 20MM白刚四刃0.20.11200 20MM合金两刃0.250.11200 25MM白刚四刃0.20.11200 25MM合金两刃0.250.131200飞刀刀具刀具大小材质刃数开粗下刀量大斜面光刀下刀量开粗进给R6合金刀粒两刃0.40.151500 R8合金刀粒两刃0.40.21500 R10合金刀粒两刃0.50.21500 12R0.4合金刀粒一刃0.20.11200 16R0.4合金刀粒两刃0.250.11500 20R0.4合金刀粒两刃0.30.11500 25R0.8合金刀粒两刃0.30.21500 30R5合金刀粒两刃0.50.31600 40R6合金刀粒两刃0.50.31500 63R5合金刀粒六刃0.60.31300球刀刀具刀具大小直径材质刃数开粗下刀量斜面光刀下刀量R11MM合金两刃0.030.03 R1.53MM合金两刃0.060.07R24MM合金两刃0.150.1 R2.55MM合金两刃0.20.1 R36MM合金两刃0.30.12 R48MM合金两刃0.30.12 R510MM合金两刃0.50.15 R612MM合金两刃0.50.15 R816MM合金两刃0.60.2 R1020MM合金两刃0.60.2下要有不同的改变光平面进给光斜面进给开粗转数光刀转数15030050006000150400550060002005004000450020050042005000200600350040002006004000450020060035004000200650400045002506003000350025065035004000250600300035003006503500400025060028003200300700300040002506002200250030080022003000300600220025004008002200300030060022002500400800220030004008001200120045010001200150040080010001000450100012001200400800800-100800450100010001000光平面进给光斜面进给开粗转数光刀转数150025003000150021002500150020002500500110022003000600120018003000600120018003000600130018002800700120016002000开粗进给光斜面进给开粗转数光刀转数300350550060006005004500450070060042004500110090040004500120080040004200150012003000380015001300300035001700150026003000180015002500300018001500250030001800150025002800下要有不同的改变光平面进给光斜面进给开粗转数光刀转数光侧面进给斜面转速2004503000320025050032003500200450300032002505003200350020045025002800250500260030002004502200250025050025003000250500180025003006502200280025050015002200300600200025002506001300230030080030080018002300300800300600120020002508004008001800200025080030080012001600250800400800150018002508004008007001200230400450100080012002504004008006001000200300450100060010002003004008005008002002504501000500800200250光平面进给光斜面进给开粗转数光刀转数15002500300015002100250015002000250050011002200300060012001800300060012001800300060013001800280070012001600200080012001600200010001200700-10001500开粗进给光斜面进给开粗转数光刀转数40040035004500 70060035004000 110090035004000 120080035004000 1500120025003000 1500130025003000 1700130022002800 1800150022002800 1800150020002600 1800150018002300。
CNC加工参数

MCS(Machine Coordinate System 机械坐标系它是所有刀具路径输出点的基本位置。
一旦移动机械坐标系,系统就得重新建立刀具路径输出点。
开始时没有对MCS作任何操作的情况下,MCS是和绝对坐标系一致的,并且MCS是被保存在零件文件里的。
RCS(Reference Coordinate System参考坐标系Link Mcs/Rcs 用于把RCS 和MCS关连起来,令两者重合,(原点位置和坐标轴方向都重合)1: 水平用于设置刀具进入或退出工件侧面的最大水平安全距离。
2: 直立用于设置刀具进入或退出上一切削高度(或素材平面上方)的最大垂直高度安全距离。
3: 最小用于在设置安全平面高度之前,设置刀具与铣削平面之间的距离。
当系统没有定义安全平面,且其水平和垂直安全距离都没有超过此设置值时,系统将把该最小距离作为进刀和退刀的安全距离。
4: 安全平面作为在进行至下一切削区域前,须把刀提到的安全平面,使用时如选择该选项,安全平面高度会与整体安全平面高度相同。
5: 先前平面选择该选项后,系统以上一单节的安全平面,作为在行进至下一切削区域前,须把刀提到的安全平面高度,使用时选择该选项,安全平面高度与上一单节安全平面设置相同。
6: 素材平面选择该选项后,系统以素材的最高平面,作为在行进至下一切削区域前,须把刀提到的安全平面高度。
使用时选择该选项,则安全平面高度会与素材平面设置相同。
7: 直接如无指定进刀起始点,系统将直接移动至开始铣削点。
自动类型1: 当其设置为线性时,系统将产生线性进刀路径。
当其设置为圆弧,则产生的进刀路径将沿着圆弧行进,其圆弧半径可由圆弧半径的输入值决定。
2: 激活区间用于设置边界与自动的线性或圆弧的最大距离。
在设置它的距离后,系统将计算其相当于刀具横向进给的数目,作为其边界开始铣削点与实际进刀点的距离。
3: 重叠距离用于设置进刀起始点和退刀结束点的相重叠距离。
该设置主要用于消除铣削时可能残留于进刀点的残料。
CNC加工编程参数
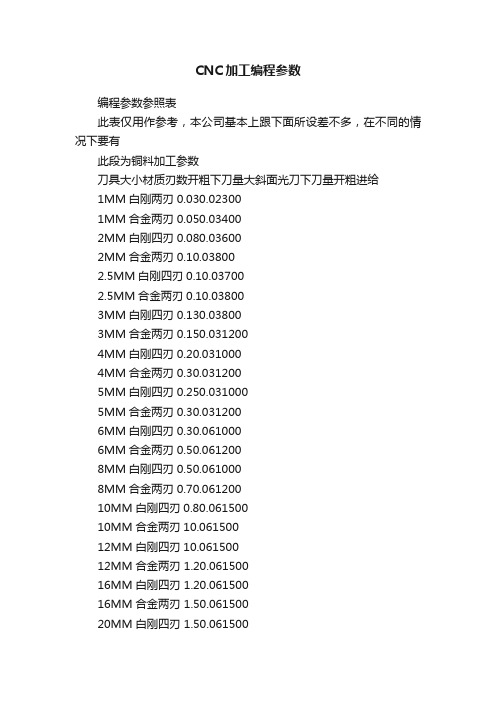
CNC加工编程参数编程参数参照表此表仅用作参考,本公司基本上跟下面所设差不多,在不同的情况下要有此段为铜料加工参数刀具大小材质刃数开粗下刀量大斜面光刀下刀量开粗进给1MM白刚两刃0.030.023001MM合金两刃0.050.034002MM白刚四刃0.080.036002MM合金两刃0.10.038002.5MM白刚四刃0.10.037002.5MM合金两刃0.10.038003MM白刚四刃0.130.038003MM合金两刃0.150.0312004MM白刚四刃0.20.0310004MM合金两刃0.30.0312005MM白刚四刃0.250.0310005MM合金两刃0.30.0312006MM白刚四刃0.30.0610006MM合金两刃0.50.0612008MM白刚四刃0.50.0610008MM合金两刃0.70.06120010MM白刚四刃0.80.06150010MM合金两刃10.06150012MM白刚四刃10.06150012MM合金两刃 1.20.06150016MM白刚四刃 1.20.06150016MM合金两刃 1.50.06150020MM白刚四刃 1.50.06150020MM合金两刃 1.50.06150025MM白刚四刃 1.50.06150025MM合金两刃 1.50.061500飞刀刀具刀具大小材质刃数开粗下刀量大斜面光刀下刀量开粗进给R6合金刀粒两刃0.450.151500R8合金刀粒两刃0.50.21500R10合金刀粒两刃0.60.2150012R0.4合金刀粒一刃0.70.1120016R0.4合金刀粒两刃0.70.1150020R0.4合金刀粒两刃0.70.1150025R0.8合金刀粒两刃10.1150030R5合金刀粒两刃0.60.31600球刀刀具刀具大小直径材质刃数开粗下刀量斜面光刀下刀量R0.51MM合金两刃0.020.02R11MM合金两刃0.040.05R1.53MM合金两刃0.060.07R24MM合金两刃0.150.1R2.55MM合金两刃0.20.1R36MM合金两刃0.30.12R48MM合金两刃0.30.12R510MM合金两刃0.50.15R612MM合金两刃0.50.15R816MM合金两刃0.60.2R1020MM合金两刃0.60.2编程参数参照表此表仅用作参考,本公司基本上跟下面所设差不多,在不同的情况下要有此段为钢料加工参数刀具大小材质刃数开粗下刀量大斜面光刀下刀量开粗进给2MM白刚四刃0.020.034002MM合金两刃0.040.035002.5MM白刚四刃0.020.034002.5MM合金两刃0.040.035003MM白刚四刃0.030.034003MM合金两刃0.050.036004MM白刚四刃0.050.036004MM合金两刃0.050.036005MM白刚四刃0.050.036005MM合金两刃0.050.038006MM白刚四刃0.060.066006MM合金两刃0.060.068008MM白刚四刃0.080.068008MM合金两刃0.10.06110010MM白刚四刃0.10.0680010MM合金两刃0.150.06110012MM白刚四刃0.130.07120012MM合金两刃0.150.07130016MM白刚四刃0.150.11300 16MM合金两刃0.20.11300 20MM白刚四刃0.20.11200 20MM合金两刃0.250.11200 25MM白刚四刃0.20.11200 25MM合金两刃0.250.131200飞刀刀具刀具大小材质刃数开粗下刀量大斜面光刀下刀量开粗进给R6合金刀粒两刃0.40.151500 R8合金刀粒两刃0.40.21500 R10合金刀粒两刃0.50.21500 12R0.4合金刀粒一刃0.20.11200 16R0.4合金刀粒两刃0.250.11500 20R0.4合金刀粒两刃0.30.11500 25R0.8合金刀粒两刃0.30.21500 30R5合金刀粒两刃0.50.31600 40R6合金刀粒两刃0.50.31500 63R5合金刀粒六刃0.60.31300球刀刀具刀具大小直径材质刃数开粗下刀量斜面光刀下刀量R11MM合金两刃0.030.03 R1.53MM合金两刃0.060.07R24MM合金两刃0.150.1 R2.55MM合金两刃0.20.1 R36MM合金两刃0.30.12 R48MM合金两刃0.30.12 R510MM合金两刃0.50.15 R612MM合金两刃0.50.15 R816MM合金两刃0.60.2 R1020MM合金两刃0.60.2下要有不同的改变光平面进给光斜面进给开粗转数光刀转数15030050006000150400550060002005004000450020050042005000200600350040002006004000450020060035004000200650400045002506003000350025065035004000250600300035003006503500400025060028003200300700300040002506002200250030080022003000300600220025004008002200300030060022002500400800220030004008001200120045010001200150040080010001000450100012001200400800800-100800450100010001000光平面进给光斜面进给开粗转数光刀转数150025003000150021002500150020002500500110022003000600120018003000600120018003000600130018002800700120016002000开粗进给光斜面进给开粗转数光刀转数300350550060006005004500450070060042004500110090040004500120080040004200150012003000380015001300300035001700150026003000180015002500300018001500250030001800150025002800下要有不同的改变光平面进给光斜面进给开粗转数光刀转数光侧面进给斜面转速2004503000320025050032003500200450300032002505003200350020045025002800250500260030002004502200250025050025003000250500180025003006502200280025050015002200300600200025002506001300230030080030080018002300300800300600120020002508004008001800200025080030080012001600250800400800150018002508004008007001200230400450100080012002504004008006001000200300450100060010002003004008005008002002504501000500800200250光平面进给光斜面进给开粗转数光刀转数15002500300015002100250015002000250050011002200300060012001800300060012001800300060013001800280070012001600200080012001600200010001200700-10001500开粗进给光斜面进给开粗转数光刀转数40040035004500 70060035004000 110090035004000 120080035004000 1500120025003000 1500130025003000 1700130022002800 1800150022002800 1800150020002600 1800150018002300。
cnc调机规范
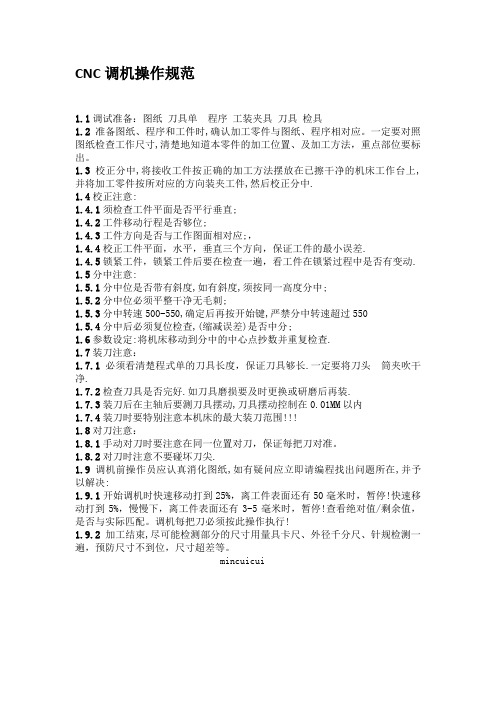
CNC调机操作规范1.1调试准备:图纸刀具单程序工装夹具刀具检具1.2准备图纸、程序和工件时,确认加工零件与图纸、程序相对应。
一定要对照图纸检查工作尺寸,清楚地知道本零件的加工位置、及加工方法,重点部位要标出。
1.3校正分中,将接收工件按正确的加工方法摆放在已擦干净的机床工作台上,并将加工零件按所对应的方向装夹工件,然后校正分中.1.4校正注意:1.4.1须检查工件平面是否平行垂直;1.4.2工件移动行程是否够位;1.4.3工件方向是否与工作图面相对应;,1.4.4校正工件平面,水平,垂直三个方向,保证工件的最小误差.1.4.5锁紧工件,锁紧工件后要在检查一遍,看工件在锁紧过程中是否有变动.1.5分中注意:1.5.1分中位是否带有斜度,如有斜度,须按同一高度分中;1.5.2分中位必须平整干净无毛刺;1.5.3分中转速500-550,确定后再按开始键,严禁分中转速超过5501.5.4分中后必须复位检查,(缩减误差)是否中分;1.6参数设定:将机床移动到分中的中心点抄数并重复检查.1.7装刀注意:1.7.1必须看清楚程式单的刀具长度,保证刀具够长.一定要将刀头筒夹吹干净.1.7.2检查刀具是否完好.如刀具磨损要及时更换或研磨后再装.1.7.3装刀后在主轴后要测刀具摆动,刀具摆动控制在0.01MM以内1.7.4装刀时要特别注意本机床的最大装刀范围1.8对刀注意:1.8.1手动对刀时要注意在同一位置对刀,保证每把刀对准。
1.8.2对刀时注意不要碰坏刀尖.1.9调机前操作员应认真消化图纸,如有疑问应立即请编程找出问题所在,并予以解决:1.9.1开始调机时快速移动打到25%,离工件表面还有50毫米时,暂停!快速移动打到5%,慢慢下,离工件表面还有3-5毫米时,暂停!查看绝对值/剩余值,是否与实际匹配。
调机每把刀必须按此操作执行!1.9.2加工结束,尽可能检测部分的尺寸用量具卡尺、外径千分尺、针规检测一遍,预防尺寸不到位,尺寸超差等。
CNC数控加工参数计算

CNC数控加工参数计算1.加工速度:加工速度是指加工过程中工件与工具之间的相对移动速度。
加工速度的选择应根据所加工材料的硬度、切削工具的性能和切削效果要求来确定。
一般而言,硬度较高的材料需要较低的加工速度,而材料硬度较低则可以选择较高的加工速度。
2.进给速度:进给速度是指工件与工具之间的相对移动速度。
进给速度的选择应根据所加工材料的硬度、切削工具的性能和切削效果要求来确定。
与加工速度不同的是,进给速度直接影响加工精度和表面质量。
一般而言,在加工精度要求较高的情况下,应选择较低的进给速度。
3.切削速度:切削速度是指切削工具相对于工件表面的线速度。
切削速度的选择应根据所加工材料的硬度、切削工具的材料和刀具半径来确定。
一般而言,材料硬度越高、刀具材料越硬、刀具半径越大,切削速度就应越低。
4.切削深度:切削深度是指切削刀具在每次进给过程中所切削掉的工件表面厚度。
切削深度的选择应考虑材料的硬度、机床的刚性和加工要求。
一般而言,硬度较高的材料和刚性较低的机床应选择较小的切削深度,以避免过大的切削力和切屑堵塞。
5.切削角度:切削角度是切削刀具与工件表面之间的夹角。
切削角度的选择应根据材料的硬度、刀具的结构和加工要求来确定。
一般而言,硬度较高的材料应选择较小的切削角度,以减小切削力和切削温度。
6.刀具半径:刀具半径是指刀具切削部分的半径。
刀具半径的选择应根据材料硬度、刀具结构和切削要求来确定。
一般而言,硬度较高的材料和需要较大的切削深度的情况下,应选择较大的刀具半径,以增加切削稳定性和提高加工效率。
7.切削液:切削液是指在CNC数控加工过程中用于冷却和润滑的液体。
切削液对于提高切削质量、延长刀具寿命和保护机床都具有重要作用。
切削液的选择应考虑材料的切削性、切削工况和环境要求。
CNC数控加工参数的选择应综合考虑工件材料、切削工具性能和加工要求。
通过合理选择和调整这些参数,可以有效提高加工质量和生产效率。
同时,为了确保加工过程的稳定性和安全性,还需要根据机床的性能和加工过程中的安全要求来选择。
自己从事CNC加工问题总结和编程参数设置

CNC问题总结一般加工过程是:先粗后半精再精加工、先面后等高、等高和曲面有时要延伸、前后余量要一致一:对加工铜电极而言1.在条件允许下一般先用大刀开出φ10或φ12进行开粗,一般为了防止工件被铣飞一般先采用上面部分下刀0.15mm,下面部分下刀在0.12,mm左右。
开粗要注意毛坯的大小,看是否铣掉完周边的毛坯,避免撞刀的发生。
2.一定要进行二次开粗,保证前后余量一致这样在光刀的情况下才能保证同样的光洁度。
3.光刀:基准台的尺寸大小一定要一致不能纳入放电间隙,光基准台有三种方式:第一是2D加工,第二是用轮廓等高加工,第三是采用开粗方式进行对边加工。
有时在光侧壁时看是否有锥度有时可以采用把铣刀的刀尖倒个R角,这样光出来的效果会更好,但是还要注意放电间隙,有的电极有粗工和精工一般在单边0.075(精)和15丝(粗),有时在铣顶部的曲面时可以看情况如果面积小可以适当用立铣刀拔面但是立铣刀必须要到R0.1或r0.2的角这样才不会有条纹出现,如果是大面积的话就应该用球刀拔面,有时用球刀进行环绕等高铣,一定要注意下面部分还有你用的R刀的高度没有铣到位,这个一定要记着。
二:对铁加工而言1.开粗很重要,第一撞刀是大忌特别注意因为φ50的刀特别大如果撞刀很伤主轴所以这点应该特别注意,开粗时应该尽量减少抬刀次数,当在拐角时应该设置过度圆弧,这样能够避免卡到现象,避免很大的噪音问题出现和提高刀片的使用寿命。
有时在一个很小的空间范围内也下了刀,这一点也特别注意因为这也是卡刀现象,我们应该做一些辅助面来把它避免掉,让后面的小刀去加工。
开粗时有时要特别注意你加工的余量因为有时候要去淬火,淬火一般留余量为0.8mm,如果不淬火一般留余量为0.45mm。
或0.35。
2.二次开粗应该可以先用环绕等高来把多余的余量去出,这样可以避免小刀子的开粗断刀或半精加工,这点要切记。
有时可以用等高开粗,但是特别要注意刀子的宽度,如果没有注意的话,也会容易断刀,所以在加工时应该注意,或者多用二次开粗形式。
CNC钻孔与攻牙参数

CNC钻孔与攻牙参数1.速度:钻孔速度是决定加工效率的重要参数,一般来说,速度越快,加工效率越高。
但是速度过快可能会导致刀具损耗加剧,因此需要根据具体情况选择合适的速度。
2.进给:进给是指刀具在工件表面上移动的速度,进给过大可能会导致刀具损坏,进给过小则会影响加工效率。
因此需要根据具体工件材料和钻孔直径选择合适的进给速度。
3.钻孔深度:钻孔深度是指刀具钻入工件的深度,一般来说,钻孔深度越大,加工难度越大。
因此在设定钻孔深度时需要考虑刀具的强度和材质,以避免刀具损坏。
4.冷却液:在CNC钻孔过程中,冷却液是必不可少的。
冷却液可以有效降低加工温度,减少摩擦力,延长刀具寿命。
因此需要根据具体材料和加工条件选择合适的冷却液种类和用量。
CNC攻牙参数:1.速度:攻牙速度是决定攻牙效率的重要参数,一般来说,速度越快,攻牙效率越高。
但是速度过快可能会导致刀具损耗加剧,因此需要根据具体情况选择合适的速度。
2.进给:进给是指刀具在工件表面上移动的速度,进给过大可能会导致刀具损坏,进给过小则会影响攻牙效率。
因此需要根据具体工件材料和攻牙直径选择合适的进给速度。
3.攻牙深度:攻牙深度是指刀具在工件上切割的深度,一般来说,攻牙深度越大,加工难度越大。
因此在设定攻牙深度时需要考虑刀具的强度和材质,以避免刀具损坏。
4.冷却液:在CNC攻牙过程中,冷却液同样是必不可少的。
冷却液可以有效降低加工温度,减少摩擦力,延长刀具寿命。
因此需要根据具体材料和加工条件选择合适的冷却液种类和用量。
总结:CNC钻孔和攻牙是在CNC加工过程中非常重要的工艺,通过合理设置钻孔和攻牙参数,可以提高加工效率,减少刀具损耗,保证加工质量。
因此在实际加工过程中,需要根据具体工件材料和尺寸,合理设置钻孔和攻牙参数,以实现高效精确的加工。
实用CNC加工参数设置标准
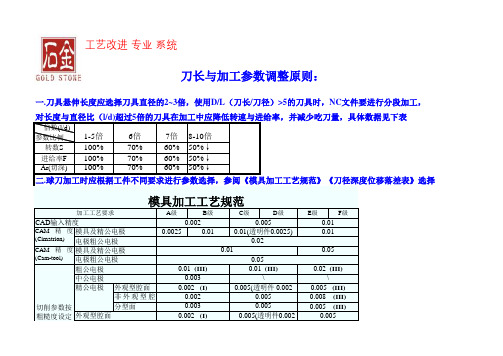
倍数(l/d)
参数比例
转数S 100%70%60%50%↓
进给率F 100%70%60%50%↓
Ar(切深)100%70%60%50%↓
A 级
B 级
C 级
D 级
E 级
F 级
0.00250.01外观型腔面非外观型腔
面分型面1-5倍6倍7倍8-10倍一.刀具悬伸长度应选择刀具直径的2~3倍,使用D/L (刀长/刀径)>5的刀具时,NC 文件要进行分段加工,对长度与直径比(l/d)超过5倍的刀具在加工中应降低转速与进给率,并减少吃刀量,具体数据见下表二.球刀加工时应根据工件不同要求进行参数选择,参阅《模具加工工艺规范》《刀径深度位移落差表》选择
模具加工工艺规范
加工工艺要求CAD 输入精度
0.0020.0050.01CAM 精度(Cimatrion)模具及精公电极0.01(透明件0.0025)
0.01电极粗公电极
0.02CAM 精度(Cam-tool)模具及精公电极0.01
0.05电极粗公电极
0.05切削参数按
粗糙度设定平优化)粗公电极
0.01 (III)0.01 (III)精公电极0.002 (I)0.005(透明件 0.002
0.0030.0050.005 (III)0.0020.0050.008 (III)0.02 (III)中公电极
0.003\\0.005 (III)外观型腔面
0.002 (I) 0.005(透明件0.0020.005
刀长与加工参数调整原则:
工 工艺改进 专业 系统
四.切削参数计算常用公式。
CNC数控雕刻机参数设置
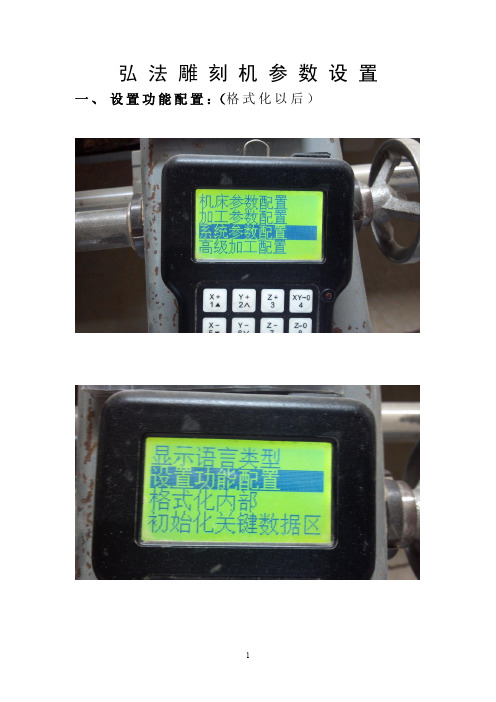
弘法雕刻机参数设置一、设置功能配置:(格式化以后)
○1掉电保护
○2选择语言
○3Z轴深度调整值
○4急停开关信号
○5硬限位开关信号
○6传统手动方式
○7换刀设备配置
○8脚踏开关
○9开盖保护开关
○10空运行时是否受速度倍率控制
○11过滤精雕转换文件中的指定
○12旋转轴采用什么标记
○13切换轴是否是旋转轴
二、脉冲当量X200
Y200
Z200
C100
三、机床尺寸
X1200
Y800
Z200
四、速度限制
X轴负方向******** X轴正方向********
Y轴负方向6000
Y轴正方向6000
Z轴负方向3000
Z轴正方向1800
五、速度设置
高速低速
X6000 X2000
Y5000 Y1500
Z4000 Z1000
加工速度20000
抬刀毫米正常200 R6脚是165(低于系统提供的Z轴高度)
七、加工时要用的参数
对刀仪厚度45.455
Y轴中心距离(-307.275)
大荣 CNC参数设置
当量公式:手柄显示数值 / 实际运动距离 * 当前当量设置值
脉冲当量 X轴: 218.30
Y轴: 153.11
Z轴: 318.72
机床尺寸: X轴: 1300.00
Y轴: 2500.00
Z轴: 350.00
电机方向 X轴: 负方向
Y轴: 正方向
Z轴: 负方向。
CNC机床加工中的切削参数调优与控制方法

CNC机床加工中的切削参数调优与控制方法CNC(Computer Numerical Control)机床是基于计算机控制和数字化的技术,广泛应用于各种切削加工行业中。
在CNC机床加工过程中,切削参数的调优与控制方法起着至关重要的作用,能够提高加工效率和产品质量。
本文将讨论CNC机床加工中的切削参数调优与控制方法。
一、切削参数的概念与重要性切削参数是指在CNC机床加工过程中,用于控制切削行为和影响加工效果的各项参数。
切削参数包括切削速度、进给速度、切削深度和切削宽度等。
这些参数的设定对零件表面质量、加工精度和加工效率等方面都有直接影响。
调优切削参数是为了使切削过程达到最佳加工效果。
切削参数的调优可以使加工精度提高,零件表面质量提升,同时还能够减少加工时间和工具磨损,降低成本。
因此,合理设定和控制切削参数对CNC机床加工至关重要。
二、切削参数调优的方法1. 实验法调优实验法调优是常用的切削参数调优方法之一。
通过实验,根据切削参数与加工效果之间的关系,找出最佳切削参数组合。
这种方法需要准备一系列实验样品,改变切削参数并记录加工的结果。
然后通过对结果分析,找出最佳的切削参数组合。
2. 经验法调优经验法调优是一种基于经验的方法。
在实际切削加工中,经验丰富的操作者可以根据自己的经验和感觉来调整切削参数。
虽然这种方法具有一定的主观性,但是经验操作者可以根据加工情况迅速找到最佳切削参数。
3. 数值模拟法调优数值模拟法调优是一种基于计算机仿真的方法。
通过建立切削过程的仿真模型,可以预测不同切削参数组合对加工结果的影响。
依据仿真结果,可以选择最佳的切削参数,提前进行切削参数调优,减少实际试切的次数。
三、切削参数的控制方法1. 实时监测与调整CNC机床在加工过程中可以通过传感器实时监测切削力、温度和振动等参数。
根据监测结果,可以通过自动控制系统调整切削参数,以保持切削过程的稳定。
通过实时监测和调整切削参数,可以减少切削过程的变化,保持加工的稳定性和精度。
非常全FANUC常用CNC参数大汇总资料

非常全!FANUC常用CNC参数大汇总
CNC参数是数控机床的灵魂,数控机床软硬件功能的正常发挥是通过参数来“沟通”的,机床的制造精度和维修后的精度恢复也需要通过参数来调整,所以,如果没有参数,数控机床就等于是一堆废铁,如果CNC参数全部丢失,将导致数控机床瘫痪。
数控系统中有关伺服控制的参数较多,不同CNC生产厂家的数控系统在参数名称、种类及功能上不尽相同。
参数设置的正确与否将直接影响进给运动的精度和稳定性,对于没有经验或权限的用户,禁止随意调整这些参数,否则容易造成数控机床不能正常工作。
下面列出FANUC系统应用中最常用的CNC参数,希望能帮助您快速查找所需要的参数。
FANUC常用CNC参数表
用检测单位求出快速进给时的跟随误差量,为了使在一定的超量范围内系统不报警,应留有50%左右的余量。
①设定标准设定值 1000。
②指定成为主轴速度模拟输出最大电压(10V)的主轴速度。
③测量输出电压
④在参数(No.3730)中设定下式的值。
⑤在设定完参数后,再次指定主轴速度模拟输出成为最大电压的主轴速度,确认输出电压已被设定为
①设定标准设定值 0。
②指定主轴速度模拟输出被设定为 0 的主轴速度。
③测量输出电压。
④在参数(No.3731)中设定下式的值。
⑤在设定完参数后,再次指定主轴速度模拟输出被
设定为 0 的主轴速度,确认
输出电压已被设定为 0V。
若是串行主轴的情形则不需要设定此参数
主轴电机的最低钳制速度
主轴电机的最高钳制速度。
数控机床CNC参数设置

数控机床CNC参数设置1 CNC参数的调试修改方法⑴、在设置页面打开参数开关。
⑵、工作模式选择在录入方式。
⑶、在参数页面修改相应的参数。
⑷、修改完参数后关掉参数开关再按复位键,部分参数修改后还需关掉系统电源。
2了解每个CNC参数所对应的作用以及修改参数后机床性能的变化K1000M CNC参数一览表OTFP 1:输出最高频率为512Kpps。
0:输出最高频率为32Kpps。
RDRN 1:空运行时,快速运动指令运行有效。
0:空运行时,快速运动指令运行无效。
DECI 1:在返回参考点时减速信号为"1"表示减速(回零方式B 时有效)。
0:在返回参考点时减速信号为"0"表示减速。
IOF 1:用MDI键入时,偏置值为增量值。
0:用MDI键入时,偏置值为绝对值。
RS43 1:G43,G44的偏移矢量在复位时被清零。
0:G43,G44的偏移矢量在复位时保持不变。
DCS 1:MDI方式时,按【输出】键执行。
0:MDI方式时,按【循环启动】键执行。
SCW 1:最小指令增量按英制系统(机床是英制系统)。
0:最小指令增量按公制系统(机床是公制系统)。
NFDO 1:恒设为1TJHD 1:在手动示教方式中,手轮有效。
0:在手动示教方式中,手轮无效。
PM2,PM1:设定固定循环G76,G87中的退刀方向。
RSJG 0:按复位键时,系统自动关闭M03、M04、润滑、冷却输出。
1:按复位键时,对输出M03、M04、润滑、冷却输出没有影响。
MPOF 1:屏蔽电压低报警PPD 1:用绝对零点编程(G92)也设置相对坐标值。
0:用绝对零点编程(G92)不设置相对坐标值。
PCMD 1:输出波形是脉冲。
0:输出波形是方波。
PRGB :无意义。
TLCP 1:在与指定平面(G17,G18,G19)垂直的轴上进行刀具长度补偿。
(刀具长度补偿B)。
0:与指定平面无关,在Z轴上进行刀具长度补偿(刀具长度补偿A)。
CNC刀路参数设定
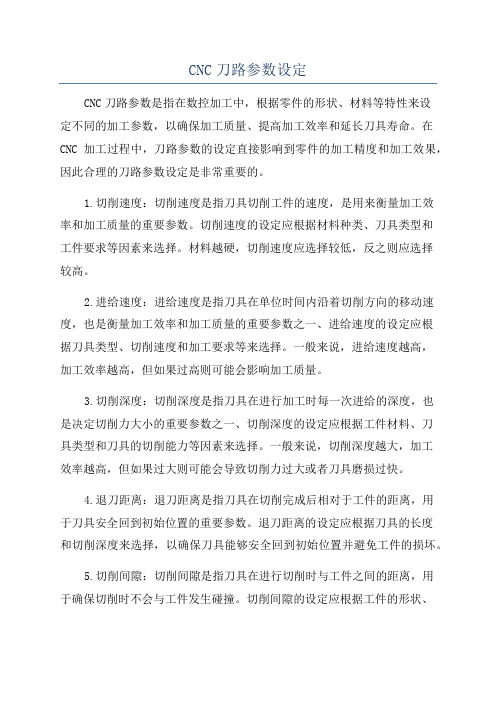
CNC刀路参数设定CNC刀路参数是指在数控加工中,根据零件的形状、材料等特性来设定不同的加工参数,以确保加工质量、提高加工效率和延长刀具寿命。
在CNC加工过程中,刀路参数的设定直接影响到零件的加工精度和加工效果,因此合理的刀路参数设定是非常重要的。
1.切削速度:切削速度是指刀具切削工件的速度,是用来衡量加工效率和加工质量的重要参数。
切削速度的设定应根据材料种类、刀具类型和工件要求等因素来选择。
材料越硬,切削速度应选择较低,反之则应选择较高。
2.进给速度:进给速度是指刀具在单位时间内沿着切削方向的移动速度,也是衡量加工效率和加工质量的重要参数之一、进给速度的设定应根据刀具类型、切削速度和加工要求等来选择。
一般来说,进给速度越高,加工效率越高,但如果过高则可能会影响加工质量。
3.切削深度:切削深度是指刀具在进行加工时每一次进给的深度,也是决定切削力大小的重要参数之一、切削深度的设定应根据工件材料、刀具类型和刀具的切削能力等因素来选择。
一般来说,切削深度越大,加工效率越高,但如果过大则可能会导致切削力过大或者刀具磨损过快。
4.退刀距离:退刀距离是指刀具在切削完成后相对于工件的距离,用于刀具安全回到初始位置的重要参数。
退刀距离的设定应根据刀具的长度和切削深度来选择,以确保刀具能够安全回到初始位置并避免工件的损坏。
5.切削间隙:切削间隙是指刀具在进行切削时与工件之间的距离,用于确保切削时不会与工件发生碰撞。
切削间隙的设定应根据工件的形状、刀具的半径和切削要求等因素来选择。
一般来说,切削间隙越小,切削精度越高,但如果过小可能会导致刀具与工件的碰撞。
6.切削方向:切削方向是指刀具在进行切削时相对于工件的移动方向,常见的切削方向有径向切削和轴向切削。
切削方向的选择应根据工件的形状和加工要求等因素来确定。
一般来说,径向切削适用于表面精度要求较高的加工,而轴向切削适用于快速去除大量金属的加工。
7.切削冷却液:切削冷却液是指在加工过程中用来冷却切削区域和清除切屑的液体。
CNC加工中心精加工切削参数计算标准标准表格格
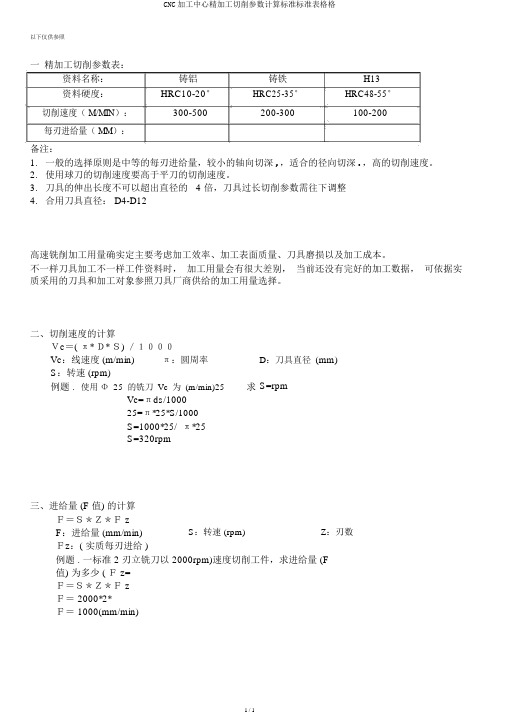
CNC 加工中心精加工切削参数计算标准标准表格格 1 / 1 以下仅供参照一 精加工切削参数表:资料名称:铸铝 铸铁 H13 资料硬度:HRC10-20° HRC25-35° HRC48-55° 切削速度( M/MIN ):300-500 200-300 100-200每刃进给量( MM ):备注:1. 一般的选择原则是中等的每刃进给量,较小的轴向切深p ,适合的径向切深 e ,高的切削速度。
2. 使用球刀的切削速度要高于平刀的切削速度。
3. 刀具的伸出长度不可以超出直径的 4 倍,刀具过长切削参数需往下调整4. 合用刀具直径: D4-D12高速铣削加工用量确实定主要考虑加工效率、加工表面质量、刀具磨损以及加工成本。
不一样刀具加工不一样工件资料时, 加工用量会有很大差别, 当前还没有完好的加工数据, 可依据实质采用的刀具和加工对象参照刀具厂商供给的加工用量选择。
二、切削速度的计算 Vc =( π* D* S) /1000 Vc :线速度 (m/min) π:圆周率D :刀具直径(mm)S :转速 (rpm) 例题 . 使用Φ 25 的铣刀 Vc 为 (m/min)25 Vc=πds/1000 求S=rpm25=π*25*S/1000S=1000*25/ π*25S=320rpm 三、进给量 (F 值) 的计算 F=S*Z*F z F :进给量 (mm/min) Fz :( 实质每刃进给 ) S :转速 (rpm)Z :刃数例题 . 一标准 2 刃立铣刀以 2000rpm)速度切削工件,求进给量 (F值) 为多少 ( F z=F=S*Z*F zF= 2000*2*F= 1000(mm/min)。
CNC加工标准
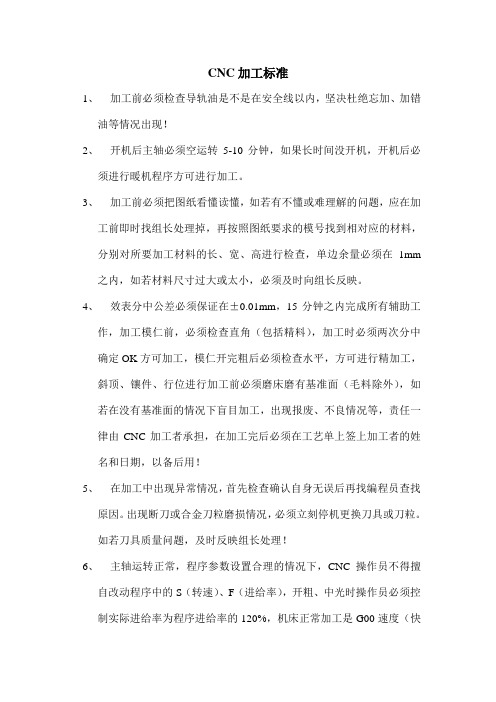
CNC加工标准1、加工前必须检查导轨油是不是在安全线以内,坚决杜绝忘加、加错油等情况出现!2、开机后主轴必须空运转5-10分钟,如果长时间没开机,开机后必须进行暖机程序方可进行加工。
3、加工前必须把图纸看懂读懂,如若有不懂或难理解的问题,应在加工前即时找组长处理掉,再按照图纸要求的模号找到相对应的材料,分别对所要加工材料的长、宽、高进行检查,单边余量必须在1mm 之内,如若材料尺寸过大或太小,必须及时向组长反映。
4、效表分中公差必须保证在±0.01mm,15分钟之内完成所有辅助工作,加工模仁前,必须检查直角(包括精料),加工时必须两次分中确定OK方可加工,模仁开完粗后必须检查水平,方可进行精加工,斜顶、镶件、行位进行加工前必须磨床磨有基准面(毛料除外),如若在没有基准面的情况下盲目加工,出现报废、不良情况等,责任一律由CNC加工者承担,在加工完后必须在工艺单上签上加工者的姓名和日期,以备后用!5、在加工中出现异常情况,首先检查确认自身无误后再找编程员查找原因。
出现断刀或合金刀粒磨损情况,必须立刻停机更换刀具或刀粒。
如若刀具质量问题,及时反映组长处理!6、主轴运转正常,程序参数设置合理的情况下,CNC操作员不得擅自改动程序中的S(转速)、F(进给率),开粗、中光时操作员必须控制实际进给率为程序进给率的120%,机床正常加工是G00速度(快速移动)必须为100%,精加工时,操作员必须控制实际进给率为程序的50%,以保证其光洁度。
7、在生产加工中,改模的铜公、改模模仁优先加工,其次为新模,新模模仁、滑块优先加工,其中钢料需外发淬火先开粗,相对应的加工此模铜公,铜公中铜打铜、线割、整公优先加工。
铜公精(F)粗(R)字码必须分清楚,线割铜公的字码必须打在铜公的底部,以免铜公需线割避空,把字码锣掉,给火花机加工带来不方便。
8、CNC操作员必须按照《模具加工工艺流程》加工,模具主管所安排的生产加工顺序,不得私自改变或调整,改模模仁,铜公及异常加工、未经批准私自加工严惩不贷。
- 1、下载文档前请自行甄别文档内容的完整性,平台不提供额外的编辑、内容补充、找答案等附加服务。
- 2、"仅部分预览"的文档,不可在线预览部分如存在完整性等问题,可反馈申请退款(可完整预览的文档不适用该条件!)。
- 3、如文档侵犯您的权益,请联系客服反馈,我们会尽快为您处理(人工客服工作时间:9:00-18:30)。
倍数(l/d)
参数比例
转数S 100%70%60%50%↓
进给率F 100%70%60%50%↓
Ar(切深)100%70%60%50%↓
A 级
B 级
C 级
D 级
E 级
F 级
0.00250.01外观型腔面非外观型腔
面分型面1-5倍6倍7倍8-10倍一.刀具悬伸长度应选择刀具直径的2~3倍,使用D/L (刀长/刀径)>5的刀具时,NC 文件要进行分段加工,二.球刀加工时应根据工件不同要求进行参数选择,参阅《模具加工工艺规范》《刀径深度位移落差表》选择
模具加工工艺规范
加工工艺要求CAD 输入精度
0.0020.0050.01CAM 精度(Cimatrion)模具及精公电极0.01(透明件0.0025)
0.01电极粗公电极
0.02CAM 精度(Cam-tool)模具及精公电极0.01
0.05电极粗公电极
0.05切削参数按
粗糙度设定平优化)粗公电极
0.01 (III)0.01 (III)精公电极0.002 (I)0.005(透明件 0.002
0.0030.0050.005 (III)0.0020.0050.008 (III)0.02 (III)中公电极
0.003\\0.005 (III)外观型腔面
0.002 (I) 0.005(透明件0.0020.005
刀长与加工参数调整原则:
工工艺改进专业系统
四.切削参数计算常用公式。