机床切削液浓度
切削液的使用、管理与机床腐蚀的防护范本

切削液的使用、管理与机床腐蚀的防护范本切削液是在机床加工过程中使用的一种液体,能够降低摩擦、冷却刀具和工件、清洗切削面等作用。
切削液的使用和管理对于提高机床加工效率、延长刀具寿命、保护机床腐蚀等方面起着重要作用。
本文将介绍切削液的使用、管理以及机床腐蚀防护的范本。
切削液的使用主要包括选择合适的切削液、正确的使用方法以及切削液的有效补给等方面。
首先,选择合适的切削液至关重要。
不同的加工材料和工艺需要选择不同的切削液。
一般而言,切削液可以分为水溶性切削液和油基切削液两类。
对于大多数金属加工,常用的是水溶性切削液,因为它能够提供良好的冷却和润滑效果。
而对于一些特殊的材料加工,如高温合金和不锈钢等,油基切削液可以提供更好的润滑和防锈效果。
其次,正确的使用方法是确保切削液效果的关键。
在使用切削液前,应将切削液与水充分混合,通常比例为1:20到1:30。
然后,将切削液均匀地喷洒在切削区域上,确保切削液能够充分润湿刀具和工件表面。
在加工过程中,应及时添加切削液,并保持足够的切削液流动量,以保证切削液能够持续地冷却和润滑刀具和工件。
另外,切削液的有效补给也是切削液使用的关键。
切削液在加工过程中会逐渐蒸发和消耗,因此需要及时地补给新的切削液。
为了保持切削液的质量,应注意定期更换切削液,通常为每个月或每三个月更换一次,具体时间根据加工情况而定。
在更换切削液时,应清洗并彻底排空切削液箱和切削液管路,然后添加新的切削液。
切削液的管理也是确保切削液有效使用和延长刀具寿命的重要环节。
首先,要定期检查切削液的质量,并进行必要的调整。
切削液质量的检查包括测量切削液的浓度、酸度和硬度等指标。
浓度的不稳定会造成切削液的性能下降,酸度的增加会引起刀具的腐蚀,硬度的变化会影响切削液的冷却效果。
因此,在使用过程中应定期进行这些指标的检测,并根据检测结果进行相应的补充或调整。
其次,要保持切削液的清洁。
切削液中容易产生切削渣和进入切屑,如果不及时清理,会严重影响切削液的冷却和润滑效果,并且增加切削液的酸度。
切削液管理办法
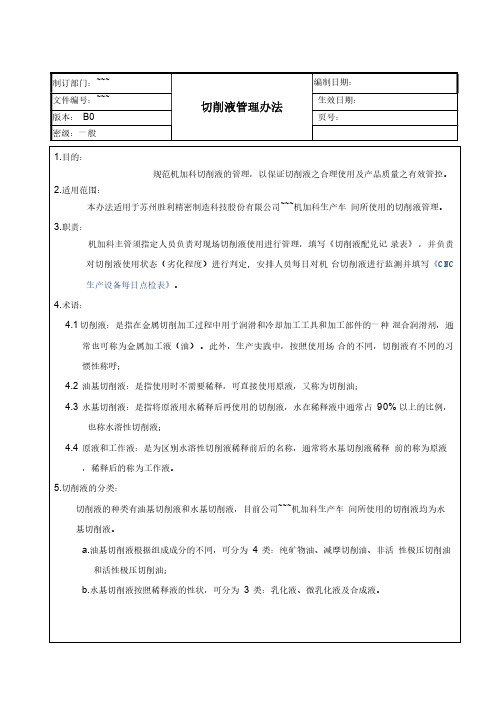
液 的 流 程 对 切 削 液 进 行 更 换 ,同时在《 切 削 液 浓 度 与 P H 值 管 制 表 》上 更 换 日
期 一 栏 填 “ N” 。
6.4.7 废 切削 液 及 切 屑 的 处 理
6.4.7.1 废 切削 液 的 处 理 :
将更换下来的废切削液,置于废切削液收集桶内,等达到一定的量,通知
测 得 PH 值 。 6.3.3 浓 度和 PH 值 检 测 时 取样 位 置 :
6.3.3.1 切 削 液 配 兑 时 , 在 搅 拌 均 匀 的 容 器 中 , 取 任 意 位 置 的 切 削 液 一 滴 放 于 折 光仪的玻璃片上进行测试;
6.3.3.2 每 日 对 机 台 切 削 液 维 护 时 , 在 机 台 切 削 液 水 槽 中 , 取 任 意 位 置 循 环 流 动 均匀的切削液一滴放于折光仪的玻璃片上进行测试。
制订部门:~~~ 文件编号:~~~ 版本: B0 密级:一般
切削液管理办法
编制日期: 生效日期: 页号:
范 围 比 较 , 调 整 油 水 比 例 并 通 过 浓 度 测 试 , 使 其 达 到 规 定 的 使 用 浓 度 及 PH 值在范围内后,填写《切削液配兑记录表》 ; d.将 切 削 液 注 入 水 桶 拉 中 ,用 小 推 车 拉 至 机 台 旁 ,注 入 水 槽 中 开 始 加 工 使 用 ; 6.3 切 削 液 浓 度 和 PH 值 检 测 方 法 : 6.3.1 浓 度检 测 ( 如 图 示 ) 6.3.1.1 使 用 工 具 : 折 光 仪 或 浓 度 计 。 6.3.1.2 检 测 步 骤 : a.用 清 水 将 折 光 仪 归 零 ; b.打 开 折 光 仪 盖 板 ; c.取 一 滴 循 环流 动 之切 削 液滴 在折 光 仪 玻 璃 片 上; d.合 上 折 光 仪 盖 板 ; e.将 折 光 仪 平 拿 于 目 视 之 高 度 ,对 着 光 亮 处 ,眼 睛 贴 近 玻 璃 镜 片 ,读 取 折 光 仪 中之液位在刻度线上的数值。
适用于数控机床的切削液选择

适用于数控机床的切削液选择数控机床作为现代制造业中不可或缺的设备之一,其切削液的选择和应用对于工件的加工质量、刀具寿命和设备性能都有着至关重要的影响。
本文将就适用于数控机床的切削液选择进行详细的探讨和分析,以帮助读者更好地了解如何选用合适的切削液,提升机床加工效率和性能。
1. 切削液的基本概念和作用切削液是指在数控机床加工过程中,用于冷却、润滑和清洗切削区域的一种液体。
它能有效地降低切削温度,减少工件和刀具的磨损,并促进切屑的排出,从而提高切削效率和加工质量。
切削液的主要作用包括:1.1 冷却切削区域:切削过程中会产生大量的热量,如果不及时冷却,会导致工件变形、刀具破裂等问题。
切削液通过吸收热量并迅速散热,保持切削区域的温度在适宜范围内。
1.2 润滑切削面:切削液能有效地润滑切削面,降低切削过程中的摩擦和热量产生,减少刀具的磨损和工件的表面粗糙度。
1.3 清洗切屑:切削液可以冲洗切屑,防止切屑在切削区域堆积,影响加工质量和刀具的寿命。
2. 切削液的选择原则2.1 适应材料和切削工艺:不同的切削液适用于不同的材料和切削工艺。
在选择切削液时,要充分考虑加工材料的种类和特性,以及切削工艺的要求,确保切削液能够与工件和刀具良好相容,并且满足特定的切削要求。
2.2 具备良好的散热性能:切削液在切削过程中要能够快速吸收和散热热量,降低切削区域的温度。
因此,切削液的导热系数和热传导性能是选择切削液时需要考虑的重要指标。
2.3 具有优异的润滑性能:切削液的润滑性能直接影响切削面的摩擦系数和磨损程度。
选择具有良好润滑性能的切削液可以有效地降低切削过程中的摩擦热量和刀具磨损,提高加工质量和刀具寿命。
2.4 对环境友好:在现代制造业追求绿色环保的潮流下,选择环境友好型的切削液也是一个重要的考虑因素。
环保性能包括切削液的挥发性、毒性和可降解性等方面。
3. 常见的切削液类型及其适应性3.1 油性切削液:油性切削液是最常用的一种切削液,其主要成分是矿物油或合成油。
第5讲切削液的配制方法

技术讲座切削液应用技术第5讲:切削液的配制方法刘镇昌济南库伦特科技有限公司济南 250101摘要:介绍水质对水基切削液性能的影响,讲述配制各种水基切削液的方法及注意事项。
关键词:切削液,水质,配制方法一般说来,绝大多数油基切削液商品是已经配制好的,买回来就可以使用,直接使用原液,不存在配制问题。
只有个别浓缩型切削油在使用前需用基础油进行稀释、调配。
这时需要考虑的问题主要是基础油的粘度、闪点和倾点。
需要根据浓缩切削油供应商的数据资料进行配制。
因此,这里主要讲述配制水基切削液的相关问题。
水基切削液的工作液浓度较低,一般在3~10%范围内(个别情况下可能使用更高浓度)。
工作液中90~97%是水。
为节省运输费用,水基切削液的商品一般是浓缩物,大多数为液态,也有膏状和粉状的。
在使用前由用户自行稀释成具有一定浓度的工作液。
这时,稀释水的水质和稀释工艺对所配制的工作液的质量有较大影响。
1 配制切削液的水质1.1 水的物理性质水是一种可以从自然界大量得到的廉价的溶剂。
水的流动性极好,有较大的比热容(是醇类、烃类有机溶剂的两倍左右)和汽化热值,故其冷却性很好,利用水的三态变化容易实现热能的转换与传输;水对无机盐、有机盐等电解质以及某些有机物,如碳水化合物、蛋白质、低碳脂肪酸和醇类等,有很强的溶解和分散能力;水无色、无臭、无味、无毒、不可燃,使用安全;水有一定的挥发性,清洗物体后较易干燥;水具有较大的表面张力,就配制切削液而言,是其缺点,但可在水中加人少量表面活性剂予以改善;由于水的溶解能力强,容易混入杂质,包括无机物、有机物和气体,这些杂质溶解或者悬浮在水中,大多对切削液有害无益。
1.2 水的硬度及分类水的硬度是反映水中钙、镁盐含量的指标。
将水煮沸并保温一段时间,水中含有的碳酸氢钙、碳酸氢镁可分解成碳酸盐沉淀析出,故由碳酸氢钙、碳酸氢镁引起的硬度称之为暂时硬度。
水中含有的钙和镁的硫酸盐及氯化物因为用煮沸方法不能除掉,故称之为永久硬度。
数控机床加工中的高效切削液的选择与使用策略

数控机床加工中的高效切削液的选择与使用策略高效切削液在数控机床加工中的选择与使用策略引言:数控机床是一种高精度、高效率的自动化加工设备,广泛应用于各个制造行业。
在数控机床加工过程中,高效切削液是关键因素之一,它能够降低摩擦、冷却工件和刀具、排除切屑、增加切削表面质量等一系列功能。
本文将从高效切削液的选择和使用策略两个方面,探讨在数控机床加工中如何有效选择和使用高效切削液。
一、高效切削液的选择策略1. 考虑切削液的基础性能高效切削液的选择需考虑其基础性能,包括切削液的润滑性、冷却性和清洗性。
润滑性能的好坏直接影响到刀具和工件的磨损情况,冷却性能则关系到加工过程中材料的热变形情况,清洗性能则影响到加工后产品的表面质量。
综合考虑这些基础性能,选择具有优秀的润滑、冷却和清洗效果的高效切削液。
2. 考虑加工材料和加工要求不同的材料和加工要求对高效切削液的选择也有一定影响。
例如,对于硬度较高的材料,需要选择具有较高极压抗磨性的切削液;对于铝合金等特殊材料,需选择具有良好防锈性能的切削液;对于微细加工等高精度要求,需选择具有低表面张力和高润湿性的切削液。
因此,在选择高效切削液前,了解加工材料及加工要求,有针对性地选择切削液。
3. 考虑环境友好性在选择高效切削液时,也要考虑其环境友好性。
选择无味、无毒、无污染的切削液,对环境和操作人员的健康都有利。
因此,尽可能选择符合环保标准的高效切削液。
二、高效切削液的使用策略1. 控制切削液的用量在加工过程中,控制切削液的用量是十分重要的。
过多的切削液不仅会浪费资源,并且可能会造成环境污染;而过少的切削液则无法发挥切削液的功能,导致切削热不及时散发,加工过程产生的切屑无法得到有效清除等问题。
因此,需要根据具体加工情况合理控制切削液的用量。
2. 定期维护和更换切削液切削液在长时间使用后会逐渐变质,降低性能,甚至产生异味。
因此,需要定期对切削液进行维护和更换。
维护切削液可以采取过滤、去污等措施,延长切削液的使用寿命;而当切削液性能明显下降时,应及时更换新的切削液,以保证加工质量和效率。
切削油的主要质量控制指标
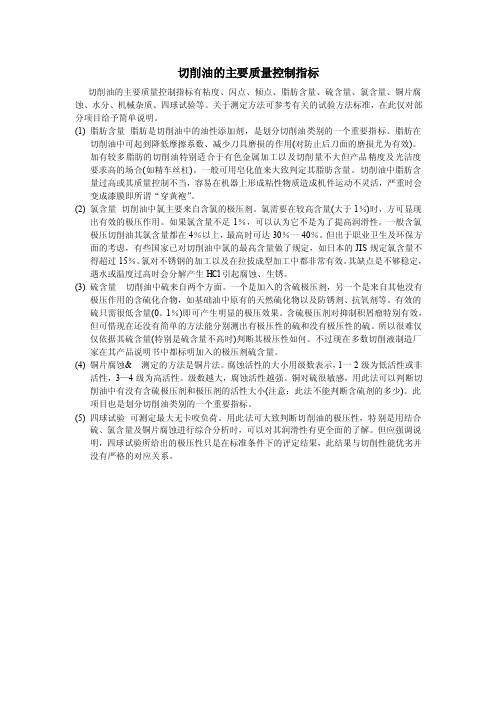
切削油的主要质量控制指标切削油的主要质量控制指标有粘度、闪点、倾点、脂肪含量、硫含量、氯含量、铜片腐蚀、水分、机械杂质、四球试验等。
关于测定方法可参考有关的试验方法标准,在此仅对部分项目给予简单说明。
(1)脂肪含量脂肪是切削油中的油性添加剂,是划分切削油类别的一个重要指标。
脂肪在切削油中可起到降低摩擦系数、减少刀具磨损的作用(对防止后刀面的磨损尤为有效)。
加有较多脂肪的切削油特别适合于有色金属加工以及切削量不大但产品精度及光洁度要求高的场合(如精车丝杠)。
一般可用皂化值来大致判定其脂肪含量。
切削油中脂肪含量过高或其质量控制不当,容易在机器上形成粘性物质造成机件运动不灵活,严重时会变成漆膜即所谓“穿黄袍”。
(2)氯含量切削油中氯主要来自含氯的极压剂。
氯需要在较高含量(大于1%)时,方可显现出有效的极压作用。
如果氯含量不足1%,可以认为它不是为了提高润滑性。
一般含氯极压切削油其氯含量都在4%以上,最高时可达30%一40%。
但出于职业卫生及环保方面的考虑,有些国家已对切削油中氯的最高含量做了规定,如日本的JIS规定氯含量不得超过15%。
氯对不锈钢的加工以及在拉拔成型加工中都非常有效。
其缺点是不够稳定,遇水或温度过高时会分解产生HCl引起腐蚀、生锈。
(3)硫含量切削油中硫来自两个方面。
一个是加入的含硫极压剂,另一个是来自其他没有极压作用的含硫化合物,如基础油中原有的天然硫化物以及防锈剂、抗氧剂等。
有效的硫只需很低含量(0。
1%)即可产生明显的极压效果。
含硫极压剂对抑制积屑瘤特别有效,但可惜现在还没有简单的方法能分别测出有极压性的硫和没有极压性的硫。
所以很难仅仅依据其硫含量(特别是硫含量不高时)判断其极压性如何。
不过现在多数切削液制造厂家在其产品说明书中都标明加入的极压剂硫含量。
(4)铜片腐蚀& 测定的方法是铜片法。
腐蚀活性的大小用级数表示,l一2级为低活性或非活性,3—4级为高活性。
级数越大,腐蚀活性越强。
cnc车床切削液

cnc车床切削液
cnc车床切削液,具有极佳的润滑性能,乳液稳定,使用寿命长,防锈性能好,清洗性能佳。
适用于铝合金、铜合金、不锈钢、铸铁等金属的车削、切削、磨削、研磨、铣削、钻孔适用。
一、cnc车床切削液参数:
二、cnc车床切削液相关推荐:
三、cnc车床切削液知识分享:
不同的切削方式选用何种切削液
金属加工选择切削液需要考虑的因素有很多,比如金属材料,经济成本,加工刀具及加工方式等,我们需要综合所有的因素来进行考虑,选择一款最实惠适用的切削液,本文主要
介绍不同切削方式应该选用何种切削液。
1 .车削、镗削
粗车:粗车时加工余量较大,因而切削深度和进给量都较大,切削阻力大,产生大量切削热,刀具磨损也较严重,主要应选择用以冷却作用为主并具有一定清洗、润滑和防锈作用的水基切削液,将切削热及时带走,降低切削温度,从而提高刀具耐用度,一般选用极压乳化液效果更好。
极压乳化液除冷却性能好之外,还具备良好的极压润滑性,可明显延长刀具使用寿命,提高切削效率,使用水基切削液要注意机床导轨面的保养,下班前要将工作台上的切削液擦干,涂上润滑油。
设备安全操作规程

机床工安全操作通则1、操作者必须熟知所操作机床的结构、性能、原理和故障处理办法,必须持有工种操作证。
2、工作前,应按规定正确穿戴好防护用品,袖口要扎紧,不准围围巾、戴手套工作,女工发辫必须挽在工作帽内。
3、开车前必须检查各种安全防护、保险、电气接地装置和润滑系统是否良好,确认无误方可开车。
4、开车时应先人工盘车或低速空转试车,检查机床运转和各传动部位,确认正常后方准工作。
5、上、落工件要稳妥,尤其是笨重、异形工件,要与起重工配合好。
6、加工旧工件前,必须将有害物质清除干净。
7、操作时,应戴防护眼镜,并采取防止金属屑飞溅伤人措施,加工铸铁、铸铜等材料时应戴好防护口罩。
8、不准用手缠绕砂布去打磨转动零件。
9、对高速转动的偏心工件或畸形工件要加配重,并作平衡试验,突出部分加护罩。
10、机床开动后,刀具应慢慢接近工件,操作者应站在安全操作位置,避开机床运动部位和金属屑飞出方向。
清除金属屑禁止嘴吹、手拨。
11、机床运转中,不准反向制动刹车,不准手摸工件或刀具,不准越过运动部位传送物件。
调整机床速度、行程,调整工、夹、刀具,测量工件,机床润滑及擦拭机床,均必须停车进行。
12、机床运行中,发现异常情况应立即停车,切断电源,然后进行检查,如属电气故障,应由电工处理。
13、机床开动后,不准擅离工作岗位,工作中途停止加工工件,因故离开工作岗位或中途停电,都必须停车、切断电源。
14、大型机床二人以上操作,必须明确主操作人统一指挥,互相配合。
非主操作人不得下令开车。
15、原材料、半成品和成品摆放要稳固,地面油污要及时清除,保持工作场地清洁畅通。
16、机床照明必须使用36V以下安全灯。
17、工作结束后,手柄、手轮放置空挡,切断电源。
交接班时,必须把本班机床运转及安全等情况交代清楚,交接记录双方签字为据。
车床作业安全规范1、开机前需检查油量,查看切削液的浓度(1:20)。
按要求润滑机床各运动部位。
2、操作前必须熟知机床每个按钮、控制部件的作用。
切削液使用规范标准[详]
![切削液使用规范标准[详]](https://img.taocdn.com/s3/m/32182f4804a1b0717ed5ddae.png)
1. 目的和围1.1目的为正确使用和管理切削液,提高切削液使用价值,特制定此规。
1.2 围工厂车间所用切削液的管理。
2. 职责工厂设备工程部油料管理人员负责对现场切削液使用进行管理,并填写《切削液日常检测维护记录》;并负责对切削液使用状态(劣化程度)进行判定。
3. 术语4. 切削液使用管理4.1 切削液分类4.1.1切削液种类:油基、水基(乳化液,微乳化液,合成液)4.1.1.1根据组成成分的不同,油基切削液可归纳为4类:A)纯矿物油B)减摩切削油C)非活性极压切削油D)活性极压切削油4.1.1.2按照稀释液的性状,水基切削液可归纳为3类:A)乳化液 B)微乳化液 C)合成液4.2切削液的应用4.2.1正确清槽,消毒和配制新液4.2.1.1排空原液:尽可能完全排空原工作液。
4.2.1.2清渣:彻底清除工作液系统和存有工作液的液槽、机床表面、泵和循环管道系统及过滤系统,清除对象包括切屑、污渣、杂油、污泥等杂质,不留死角。
4.2.1.3清洗杀菌:用1~2%的切削液和0.1~0.3%的杀菌剂配制清洗液,循环清洗系统至少不低于1小时,可延长至4小时。
4.2.1.4排空,检查清洗效果。
4.2.1.5配制新液:首先测量槽体体积(长×宽×高),按要求确定配比浓度;液槽注入新水,开启循环系统,按比例缓慢加入切削液(定量的)原液使其完全混匀(不可先加切削液后注入水稀释);使用折光仪进行浓度监测,并用折光系数校正读书,使其达到规定的使用浓度。
4.2.1.6切削液浓度=折光仪读数*折光系数切削液浓度:工作液中含有原液的质量分数。
例如,100kg工作液中含有原液5kg,则工作液的浓度为5% 4.2.1.7进入加工4.2.2切削液的日常维护4.2.2.1补给切削液时应该在其他容器预先配制成规定浓度,然后注入切削液箱。
为图省事只补充给水是引起浓度变化的重要原因,必须避免。
4.2.2.2切削液的稀释关系到乳化液的稳定。
数控机床切削液的质量检测与评估方法
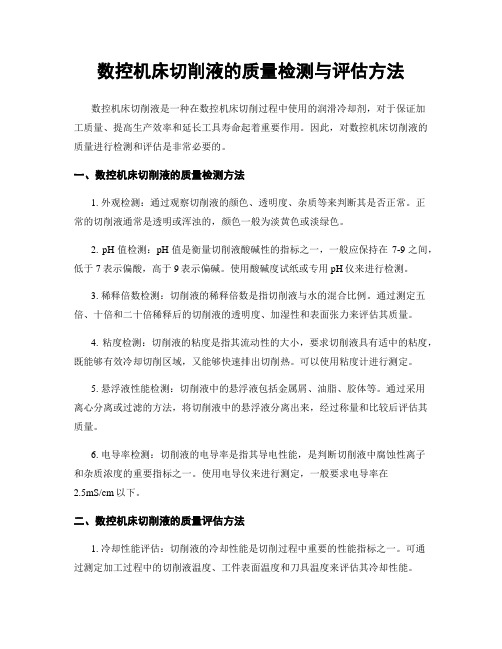
数控机床切削液的质量检测与评估方法数控机床切削液是一种在数控机床切削过程中使用的润滑冷却剂,对于保证加工质量、提高生产效率和延长工具寿命起着重要作用。
因此,对数控机床切削液的质量进行检测和评估是非常必要的。
一、数控机床切削液的质量检测方法1. 外观检测:通过观察切削液的颜色、透明度、杂质等来判断其是否正常。
正常的切削液通常是透明或浑浊的,颜色一般为淡黄色或淡绿色。
2. pH值检测:pH值是衡量切削液酸碱性的指标之一,一般应保持在7-9之间,低于7表示偏酸,高于9表示偏碱。
使用酸碱度试纸或专用pH仪来进行检测。
3. 稀释倍数检测:切削液的稀释倍数是指切削液与水的混合比例。
通过测定五倍、十倍和二十倍稀释后的切削液的透明度、加湿性和表面张力来评估其质量。
4. 粘度检测:切削液的粘度是指其流动性的大小,要求切削液具有适中的粘度,既能够有效冷却切削区域,又能够快速排出切削热。
可以使用粘度计进行测定。
5. 悬浮液性能检测:切削液中的悬浮液包括金属屑、油脂、胶体等。
通过采用离心分离或过滤的方法,将切削液中的悬浮液分离出来,经过称量和比较后评估其质量。
6. 电导率检测:切削液的电导率是指其导电性能,是判断切削液中腐蚀性离子和杂质浓度的重要指标之一。
使用电导仪来进行测定,一般要求电导率在2.5mS/cm以下。
二、数控机床切削液的质量评估方法1. 冷却性能评估:切削液的冷却性能是切削过程中重要的性能指标之一。
可通过测定加工过程中的切削液温度、工件表面温度和刀具温度来评估其冷却性能。
2. 润滑性能评估:切削液的润滑性能对机床切削过程中的摩擦和磨损起着重要作用。
可以通过测定摩擦系数和刀具磨损量来评估其润滑性能。
3. 抗菌性能评估:切削液中的细菌和真菌对切削液的质量和稳定性有一定的影响。
通过采用平皿计数法或培养法来评估切削液中的微生物数量,了解切削液的抗菌性能。
4. 稳定性评估:切削液的稳定性是指在切削过程中,切削液能够稳定地提供冷却和润滑功能。
切削液使用管理作业指导书

1.目的和范围1.1目的为正确使用和管理切削液,提高切削液使用价值,特制定此作业指导规范。
1.2 范围工厂车间所用切削液的使用和管理。
2.职责工厂设备部油料管理人员或生产现场指定人员负责对现场切削液使用进行管理,并填写《切削液日常检测维护记录》;并负责对切削液使用状态(劣化程度)进行判定。
3.切削液使用管理3.1.正确清槽,消毒和配制新液3.1.1排空原液:尽可能完全排空原工作液。
3.1.2清渣:彻底清除工作液系统和存有工作液的液槽、泵和循环管道系统及过滤系统,清除对象包括切屑、污渣、杂油、污泥等杂质,不留死角。
3.1.3清洗杀菌:用1~2%的切削液和0.1~0.3%的杀菌剂配制清洗液(或专用清洗液),循环清洗系统至少不低于1小时。
3.1.4排空,检查清洗效果。
3.1.5配制新液:首先测量槽体体积(长×宽×高),按乳化液原液说明书要求确定配比浓度;液槽注入新水,水质选用清洁的水源——自来水、地下水,必要时对配液用水进行杀菌处理和水质调整处理,配液用水硬度80~120PPM为最佳。
,开启循环系统,按比例缓慢加入切削液(定量的)原液使其完全混匀(不可先加切削液后注入水稀释);使用折光仪进行浓度监测,并用折光系数校正读数,使其达到规定的使用浓度。
3.1.6切削液浓度检测切削液浓度:工作液中含有原液的质量分数。
例如,100kg工作液中含有原液5kg,则工作液的浓度为5%。
切削液日常使用浓度不大于5%,。
根据使用的条件不同,使用浓度可在1%-5%;粗加工浓度低些,使用浓度可在1%-3%。
(特殊工艺和有特殊要求的材料除外)切削液浓度现场采用折光仪检测。
具体检测参照折光仪使用说明或操作作业指导书。
3.1.7进入加工3.2切削液的日常维护3.2.1补给切削液时应该在其他容器内预先配制成规定浓度,然后注入切削液箱。
更换新液时,对液箱、管道、机床加工区进行彻底清洗,如果不清洗或清洗不彻底,尤其是换液前的切削液已腐败,换液后有可能几天之内就会腐败,为图省事只补充给水是引起浓度变化的重要原因,必须避免。
切削液的PH值的重要性
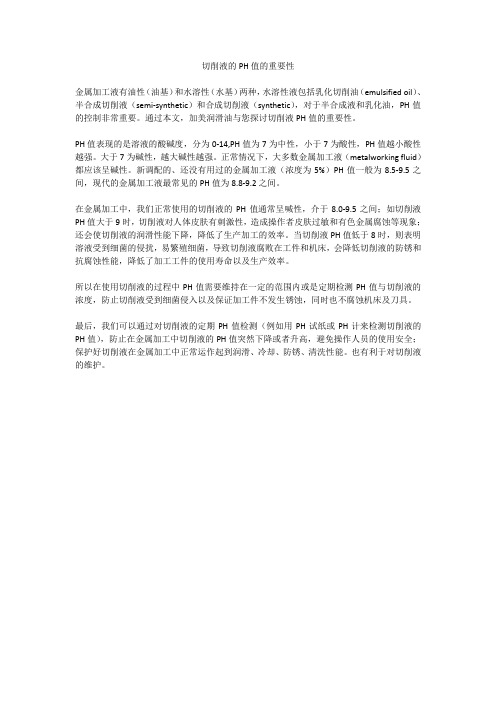
切削液的PH值的重要性
金属加工液有油性(油基)和水溶性(水基)两种,水溶性液包括乳化切削油(emulsified oil)、半合成切削液(semi-synthetic)和合成切削液(synthetic),对于半合成液和乳化油,PH值的控制非常重要。
通过本文,加美润滑油与您探讨切削液PH值的重要性。
PH值表现的是溶液的酸碱度,分为0-14,PH值为7为中性,小于7为酸性,PH值越小酸性越强。
大于7为碱性,越大碱性越强。
正常情况下,大多数金属加工液(metalworking fluid)都应该呈碱性。
新调配的、还没有用过的金属加工液(浓度为5%)PH值一般为8.5-9.5之间,现代的金属加工液最常见的PH值为8.8-9.2之间。
在金属加工中,我们正常使用的切削液的PH值通常呈喊性,介于8.0-9.5之间;如切削液PH值大于9时,切削液对人体皮肤有刺激性,造成操作者皮肤过敏和有色金属腐蚀等现象;还会使切削液的润滑性能下降,降低了生产加工的效率。
当切削液PH值低于8时,则表明溶液受到细菌的侵扰,易繁殖细菌,导致切削液腐败在工件和机床,会降低切削液的防锈和抗腐蚀性能,降低了加工工件的使用寿命以及生产效率。
所以在使用切削液的过程中PH值需要维持在一定的范围内或是定期检测PH值与切削液的浓度,防止切削液受到细菌侵入以及保证加工件不发生锈蚀,同时也不腐蚀机床及刀具。
最后,我们可以通过对切削液的定期PH值检测(例如用PH试纸或PH计来检测切削液的PH值),防止在金属加工中切削液的PH值突然下降或者升高,避免操作人员的使用安全;保护好切削液在金属加工中正常运作起到润滑、冷却、防锈、清洗性能。
也有利于对切削液的维护。
数控机床用切削液
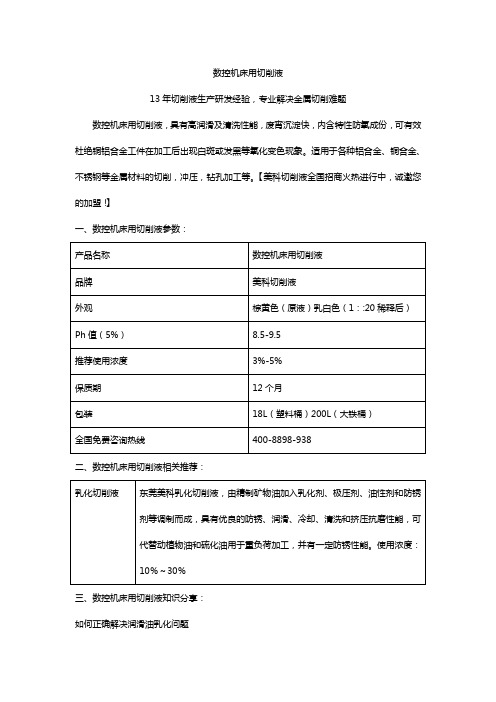
数控机床用切削液
13年切削液生产研发经验,专业解决金属切削难题
数控机床用切削液,具有高润滑及清洗性能,废宵沉淀快,内含特性防氧成份,可有效杜绝铜铝合金工件在加工后出现白斑或发黑等氧化变色现象。
适用于各种铝合金、铜合金、不锈钢等金属材料的切削,冲压,钻孔加工等。
【美科切削液全国招商火热进行中,诚邀您的加盟!】
一、数控机床用切削液参数:
二、数控机床用切削液相关推荐:
三、数控机床用切削液知识分享:
如何正确解决润滑油乳化问题
润滑油不断接触或者长期处在水分过多的环境下,很容易发生乳化问题。
油品乳化与否及乳化程度主要由油的组成成分及水的纯度、所含成分的性质决定,也与油-水体系的温度及振动情况有关。
润滑油乳化问题应该怎样解决呢?
一、要控制混入油中的水量及水质要求,在工业齿轮油使用过程中,要绝对避免轧制液混入油中,因为轧制液本身是乳化液,可以认为是油品乳化的促进剂。
大型齿轮装置集中润滑系统采用延长在用油的沉降时间、对循环用油过滤、离心分离等也是防止油品乳化的有效手段。
二、添加高质量的工业齿轮油,工业齿轮油对提高成品油抗乳化性能有很好的作用,但工业齿轮油中含有各种功能的添加剂(表面活性剂),不可避免会影响油对水的分离能力。
因而油品研制和生产人员在油中添加一定比例、具有特殊性状的破乳剂抑制这种影响,以保证油品具有良好的抗乳化性。
四、美科切削液格言分享:
许多从事人力资源工作的职场人士都表示.这两年招聘的新人多数更在意自我感受,对工作环境工作内容是否符合个人要求十分看重,而升迁与否以及薪金待遇则在他们心中位列其次。
切削油液
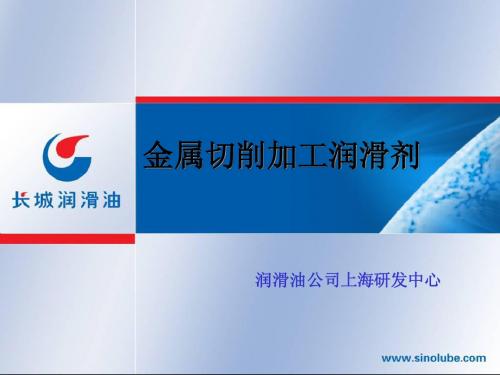
8
切削油(液)产品分类
MH类属于切削油,主要用于首先要求润滑性的 加工工艺。
MA类属于切削液。
1. MAA~MAD为乳化型水基切削液(乳白色) 2. MAE、MAF为微乳化型水基切削液(半透明) 3. MAG、MAH为合成型水基切削液(透明)
9
切削油与切削液特点比较 1) 润滑性:产品光洁度、刀具磨损 2) 冷却性 3) 防锈性 4) 使用寿命、废液处理 5) 使用中维护管理
合成液
△ ◎ △ ◎ ◎ ◎ ◎ ◎ ◎ ◎ △ △ △
17
• 乳化切削液(MAA~MAD)
乳化液在使用时需加水稀释,稀释后的工作液 呈乳白色。也称为可溶性油。
浓缩液主要成分是矿物油和乳化剂,一般含水 量10%以下,乳化剂15%~35%,还需加入一 定量的防锈剂、极压剂等。
在各种水基切削液中,乳化液的冷却性能和润 滑性能均较好,稳定性稍差。主要适用于钢、 铸铁和有色金属的切削加工。
36
• 3、砂轮堵塞、工件表面有磨削烧伤。 措施:增大供液量和压力, 换用渗透 性、净洗性好的切削液。
15
3 水基切削液
水基切削润滑剂是将浓缩液用大量水稀释后使用,因 而没有产生油烟和引起火灾的危险。水的比热容大,热导 率高,蒸发潜热大,是非常优良的冷却剂 ,且相对成本低 廉,此外还有如下优点:
① ② ③ ④ ⑤ ⑥ 在高速、高剪切操作条件下仍能与水形成稳定的混合物 能承受杂质油的影响; 乳化性能稳定,尽可能使乳液颗粒状态持续时间增长; 抗细菌、霉菌能力强,不产生有害气体; 能透过5-10μ m过滤器而不损失添加剂; 符合毒性和环保要求。
25
金属切削润滑剂的选择
从工件材料方面考虑
塑性大的材料与刀具的粘附往往比较严重,使用切削液效果显著;
加工中如何选择切削液【干货技巧】
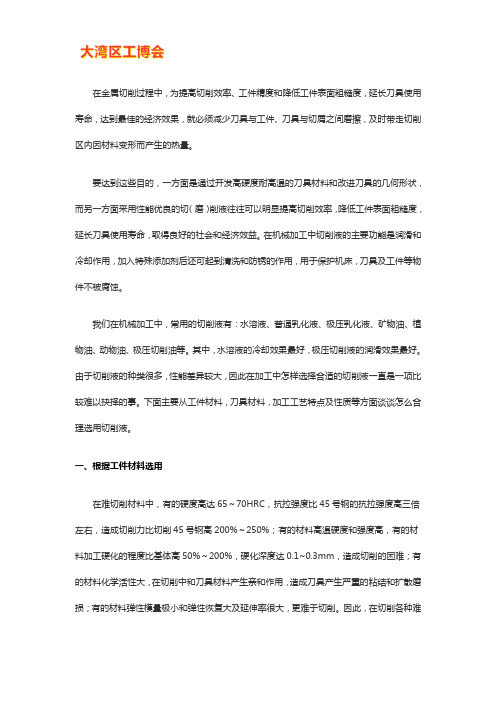
在金属切削过程中,为提高切削效率、工件精度和降低工件表面粗糙度,延长刀具使用寿命,达到最佳的经济效果,就必须减少刀具与工件、刀具与切屑之间磨擦,及时带走切削区内因材料变形而产生的热量。
要达到这些目的,一方面是通过开发高硬度耐高温的刀具材料和改进刀具的几何形状,而另一方面采用性能优良的切(磨)削液往往可以明显提高切削效率,降低工件表面粗糙度,延长刀具使用寿命,取得良好的社会和经济效益。
在机械加工中切削液的主要功能是润滑和冷却作用,加入特殊添加剂后还可起到清洗和防锈的作用,用于保护机床,刀具及工件等物件不被腐蚀。
我们在机械加工中,常用的切削液有:水溶液、普通乳化液、极压乳化液、矿物油、植物油、动物油、极压切削油等。
其中,水溶液的冷却效果最好,极压切削液的润滑效果最好。
由于切削液的种类很多,性能差异较大,因此在加工中怎样选择合适的切削液一直是一项比较难以抉择的事。
下面主要从工件材料,刀具材料,加工工艺特点及性质等方面谈谈怎么合理选用切削液。
一、根据工件材料选用在难切削材料中,有的硬度高达65~70HRC,抗拉强度比45号钢的抗拉强度高三倍左右,造成切削力比切削45号钢高200%~250%;有的材料高温硬度和强度高,有的材料加工硬化的程度比基体高50%~200%,硬化深度达0.1~0.3mm,造成切削的困难;有的材料化学活性大,在切削中和刀具材料产生亲和作用,造成刀具产生严重的粘结和扩散磨损;有的材料弹性模量极小和弹性恢复大及延伸率很大,更难于切削。
因此,在切削各种难切削材料时,要根据所切材料各自的性能与切削特点与加工阶段,选择相宜的切削液,以改善难切削材料的切削加工性,而达到加工的目的。
一般而言:加工铸铁,铸铝等脆性金属,为避免切屑堵塞冷却系统或粘附在机床上难以清除,一般不用切削液。
但精加工时为了提高表面质量,可用润滑好,黏度小的煤油或7%~10%的乳化液。
加工一般钢件,粗加工选用乳化液,精加工选用硫化乳化液。
切削液的选择和使用维护

4000üs以 下 105以下 105以下 每月一次 每月一次
每两周一次 导电度增加会有油水分离情况 每月一次 每月一次 细菌增长容易造成切削液腐败酸 化 大气中都含有微菌,一旦滋生容 易造成管路堵塞
气味
正常切削液气 味
有氧菌:无味 或污水味,厌 氧菌:臭鸡蛋 味,真菌:发 霉气味或稻草 味
4.客户加工方法(如车削、铣削、钻削、 攻螺纹等)
不同的加工方式对切削液的要求不一样。 即使是同一种加工方法,但是加工的精度 可能会是不一样,所以在反馈加工方式时 要反馈具体的加工方式。如车削就分为粗 车,半精车,精车。
下面为加工方式的一些简单分类
车削
冼削 镗削
车削分为 粗车,半精车,精车,精细车
4)加工结束后机床的防护处理 加工结束后应用切削液软管冲洗掉机床表 面的切屑和磨粒,打开机床防护门,散去 机床加工区的潮湿空气,以防止机床加工 区内金属表面生锈。 5)定期彻底清洗机床冷却系统,更换切削液。 6)节假日等长时停机处理:每天定期循环系 统,鼓入空气,防止厌氧菌生长。如有腐 败征兆,及时加入杀菌剂杀菌。
切削液的选择和 使用维护
一、切削液大体方向上的选择
1.选择依据: 切削液的品种繁多,性能差异很大,使用 中应根据切削液的性能、加工材质、加工 工艺和刀具材料等因数进行恰当的选择, 如果选者不当,冷却不充分,刀具就会很 快变钝,工件表面质量也会变差,甚至会 产生严重后果。
总体上切削液的选择依据有以下几点:
1.乳化液的配置: 乳化液的维护保养比油基切削液复杂得多。 当配制乳化液时,要先将水加满水箱,然 后边搅拌边加入乳化油。要避免将水加入 油中或用少量的水稀释乳化油,否则会得 到油包水型乳化液,这类乳化液的粘度大, 不适合一般的切削使用。
- 1、下载文档前请自行甄别文档内容的完整性,平台不提供额外的编辑、内容补充、找答案等附加服务。
- 2、"仅部分预览"的文档,不可在线预览部分如存在完整性等问题,可反馈申请退款(可完整预览的文档不适用该条件!)。
- 3、如文档侵犯您的权益,请联系客服反馈,我们会尽快为您处理(人工客服工作时间:9:00-18:30)。
41
1
2.5
2%~2.5% 拆光仪
合格
检测日期 2014.8.12 2014.8.12 2014.8.12 2014.8.12 2014.8.12 2014.8.12 2014.8.12 2014.8.12 2014.8.12 2014.8.12 2014.8.12 2014.8.12 2014.8.12 2014.8.12 2014.8.12 2014.8.12 2014.8.12 2014.8.12 2014.8.12 2014.8.12
拆光仪
合格
17
数控立式钻床
YZC-1600
3
3
7.5
≥7.5%
拆光仪
合格
18
摇臂钻床
Z3063*20/1
22
2
5
≥7.5%
拆光仪 不合格
19
摇臂钻床
Z3080*25
15
2
5
≥7.5%
拆光仪 不合格
21
数控钻床
DHKV1097/1
17
1
CXL(S)-1800.1-SP
24
EFD热处理设备 1x Sinac 100-SM- 6
序号 1
设备名称 台湾油机车床
湖州杭轴特大轴承有限公司
文件编号
机床切削液浓度检测单
规格型号
设备编 拆光仪 号 读数
检测浓度
KV-600A
13
2.5
6.25
浓度标准 ≥7.5%
版本号 检测仪器
拆光仪
判定 不合格
2
齐二高速立车 CKS5116*12/8
18
2
5
≥7.5%
拆光仪
不合格
3
台湾油机车床
KV-1600ATC
1
1
2.5
≥7.5%
拆光仪
不合格
4
台湾油机车床
KV-1600ATC
2
1
2.5
≥7.5%
拆光仪
不合格
5
台湾油机车床
VTL-2000ATC
4
0.5
1.25
≥7.5%
拆光仪
不合格
6
台湾油机车床
VTL-2000ATC
32
4.5
11.25
≥7.5%
拆光仪
合格
7
台湾油机车床
VTL-3000ATC
20
1.2
3
≥7.5%
5
DF
25
中频淬火机组
HKCC2500
10
4.8
2.5 12.5
12
≥7.5% 9%~12% 9%~12%
拆光仪
HKCC-400H
5
4.5
11.25
9%~12%
拆光仪
合格
27
数控立式磨床
MKW28160
29
2
5
2%~2.5% 拆光仪
合格
28
卧轴磨床
MG7340
拆光仪 不合格
10
双轴数控立车 DVT250×16/16
24
1
2.5
≥7.5%
拆光仪 不合格
11
双轴数控立车 DVT250×16/16
25
1
2.5
≥7.5%
拆光仪 不合格
12
双轴数控立车 DVT250×16/16
19
0.5
1.25
≥7.5%
拆光仪 不合格
15
摇臂钻床
ZN3050*16
16
5
12.5
≥7.5%