7075铝合金表面处理
7075铝合金在硼酸钠溶液体系的微弧氧化涂层性能表征
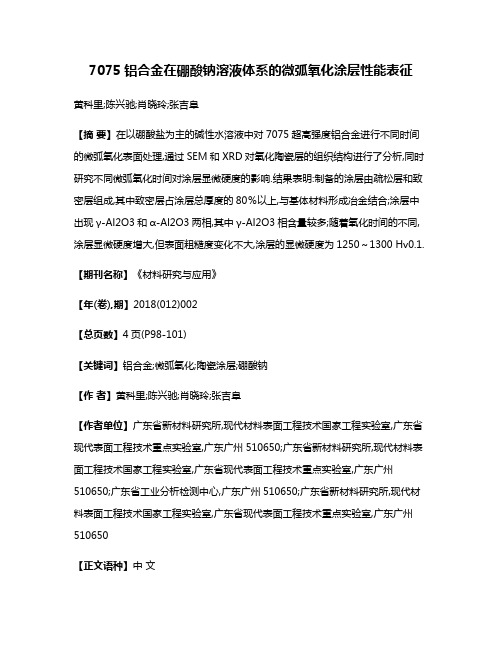
7075铝合金在硼酸钠溶液体系的微弧氧化涂层性能表征黄科里;陈兴驰;肖晓玲;张吉阜【摘要】在以硼酸盐为主的碱性水溶液中对7075超高强度铝合金进行不同时间的微弧氧化表面处理,通过SEM和XRD对氧化陶瓷层的组织结构进行了分析,同时研究不同微弧氧化时间对涂层显微硬度的影响.结果表明:制备的涂层由疏松层和致密层组成,其中致密层占涂层总厚度的80%以上,与基体材料形成冶金结合;涂层中出现γ-Al2O3和α-Al2O3两相,其中γ-Al2O3相含量较多;随着氧化时间的不同,涂层显微硬度增大,但表面粗糙度变化不大,涂层的显微硬度为1250~1300 Hv0.1.【期刊名称】《材料研究与应用》【年(卷),期】2018(012)002【总页数】4页(P98-101)【关键词】铝合金;微弧氧化;陶瓷涂层;硼酸钠【作者】黄科里;陈兴驰;肖晓玲;张吉阜【作者单位】广东省新材料研究所,现代材料表面工程技术国家工程实验室,广东省现代表面工程技术重点实验室,广东广州510650;广东省新材料研究所,现代材料表面工程技术国家工程实验室,广东省现代表面工程技术重点实验室,广东广州510650;广东省工业分析检测中心,广东广州510650;广东省新材料研究所,现代材料表面工程技术国家工程实验室,广东省现代表面工程技术重点实验室,广东广州510650【正文语种】中文【中图分类】TG174.45铝合金是现代工业中应用最广泛的有色金属材料之一,已在航空、航天、汽车、机械制造、船舶及化学工业等领域中大量应用.7075铝合金是一种冷处理锻压合金,具有强度高、机械性能良好、抗腐蚀性能及抗氧化性能好等特点,但其表面硬度较低,显微硬度通常只有170 Hv0.1,难以满足高强度、高耐磨性使用工况的要求.对其表面进行强化处理,提高表面硬度、增加耐磨性是非常必要的.一般采用表面喷涂、激光表面强化等技术,提高7075铝合金表面性能,达到抗磨损的效果.铝合金作为一种阀金属,其表面形成的氧化膜非常致密,人们也常常通过阳极氧化技术在其表面制备氧化物涂层,以提高其耐磨性.但是,通常阳极氧化制备的氧化涂层只有几个微米厚,而且比较疏松,远没有达到工业应用要求.微弧氧化(MAO)技术就是在阳极氧化[1]技术的基础上,增加电压和电流,通过电解液与相应电参数的组合,依靠弧光放电产生的瞬间高温高压,在铝、镁、钛等合金表面生长出以基体金属氧化物为主的陶瓷涂层的技术.微弧氧化获得的氧化涂层更加致密坚硬,具有广阔的应用前景.本研究以四硼酸钠为主的辅以其它添加剂的水溶液作为电解液,采用微弧氧化技术对7075铝合金表面进行处理,对不同时间微弧氧化处理后的氧化涂层的组织和性能进行了研究,为7075铝合金的表面处理工程化应用提供依据.1 试验部分1.1 基体预处理试验材料为7075超高强度铝合金,其化学成分列于表1.首先将试样加工成直径25 mm×5 mm的圆块,侧面攻M3×6 mm的螺孔,经400和800号砂纸打磨后,除油,清洗,烘干.然后通过铝导线将试样悬挂在制备好的电解液中,以备进行微弧氧化处理.表1 7075铝合金化学成分Table 1 The composition of 7075 Al alloy组成成分ZnMgCuZrCrMnAl含量w/%5.1~6.12.1~2.91.2~2.00.150.10.10余量1.2 铝合金氧化涂层的制备用WHD-60型微弧氧化设备对试样进行微弧氧化处理,外加冷却和搅拌装置,电流密度5~50 A/dm2,电压在410~480 V之间变化,氧化槽温度控制60 ℃以下.电解液是以四硼酸钠(浓度为10 g/L)为主的碱性水溶液,其中加入3 g/L的氢氧化钠、6 g/L的硅酸钠、4 g/L的乙二胺四乙酸二钠,氧化时间分别为30,45,60 min.1.3 测试方法用JSM-5910型扫描电镜(SEM,配有X-射线能谱仪(EDS))对试件进行表面形貌观察和微区元素定性分析,加速电压20 kV;用D8 Advance型X射线衍射仪分析陶瓷涂层的相成分,测试条件为Cu Kα辐射,小角度衍射,ω=1 °,扫描速度1.5秒/步,步长为0.04 °;用MH-5D显微硬度计测量涂层的截面硬度,载荷100 g,加载时间15 s.2 结果与讨论2.1 微弧氧化涂层的形貌及成分将7075铝合金在硼酸盐体系的电解液中进行不同时间的微弧氧化,其表面形貌如图1所示.从图1可见,试样表面有云状堆积物,而且没有剥落现象,堆积物中出现无规则的孔洞,孔洞大小约为3~5 μm.堆积物的形成说明在硼酸盐体系的电解液中进行微弧氧化处理形成了氧化涂层,孔洞的出现是由于微弧氧化过程所引起的,微弧氧化过程是放电-形成氧化涂层-电压击穿熔化-溶液冷却凝固的反复循环的过程.微弧氧化过程中,介电击穿总是发生在膜的最薄弱位置[2-3],放电火花在电解液中也是瞬间出现的,看起来像游动状态,经过不断的击穿-涂层熔化冷却堆积,涂层厚度不断增加,表面存在凹凸不平的疏松层.图1 不同氧化时间的涂层表面形貌(a)30 min;(b)45 min;(c)60 minFig.1 Surface image of coating,MAO试样通过不同时间的微弧氧化,其表面粗糙度列于表2.由表2可知,微弧氧化30和60 min的试样表面粗糙度约为1.84 μm,而氧化45 min的试样表面粗糙度为1.95 μm.说明在微弧氧化开始阶段(氧化时间<30 min),氧化涂层生长较慢且放电火花均匀细腻;到了45 min时放电电流较大,放电火花比较粗大,涂层增厚最快,试样表面粗糙度增大;60 min时随着涂层增厚,绝缘性增强,电流变小,放电火花又变的细腻,粗糙度降低.表2 微弧氧化涂层厚度和表面粗糙度随氧化时间的变化Table 2 Showing the change of thickness and surface roughness of ceramic layer with the increasing oxidation time氧化时间/min氧化涂层厚度/μm粗糙度/μm3050~551.844562~641.956071~741.85图2为不同氧化时间的陶瓷涂层的截面形貌.从图2可见:陶瓷涂层的厚度随氧化时间的延长而缓慢增加,氧化30 min时氧化涂层厚度为50 μm,氧化60 min 时氧化涂层厚度增加到73 μm;氧化涂层由致密层和疏松层构成,经测量氧化30~60 min的致密层厚度分别为45,62和70 μm,远大于疏松层的厚度,约占氧化涂层总厚度的80%以上,并且与基体结合良好,形成冶金结合,未见任何缺陷.图2(c)为氧化60 min时氧化涂层截面线扫描成分分析,结果显示:涂层的成分由Al,O,Mg和Zn元素组成,电解液中的B和Si元素没有出现在涂层中,初步分析这些元素没有参与氧化涂层的形成.基体材料中Zn元素含量比Mg元素的高,但是涂层中Mg元素含量却比Zn元素的高,这是在氧化涂层的形成过程中Zn元素的烧损比较严重造成的.涂层的主要组成成分为Al和O元素,这也是微弧氧化制备的目标成分.图2 陶瓷涂层的截面形貌(a)30 min;(b)45 min;(c)60 min涂层成分分布图Fig.2 Cross-sectional image of MAO coating(a) 30 min;(b)45 min;(c)composition profiles of microarc oxidaiton coating,MAO 60 min2.2 XRD物相测定图3 7075铝合金微弧氧化不同时间涂层的XRD谱线Fig.3 XRD patterns for micro-arc oxidation films with different MAO time图3为7075铝合金微弧氧化涂层的XRD谱线.从图3可见:衍射峰比较尖锐,说明涂层结晶化程度较高;涂层主要由γ-Al2O3和α-Al2O3两相组成,γ-Al2O3相比α-Al2O3相的含量高.这是由于氧化铝在结晶的过程中首先生成γ-Al2O3相,在反应微区的高温作用下,当瞬间温度高于1200℃时γ相可转变为α相,但是在液体冷却的作用下,高温时间很短,γ相转变为α相的机率变小;另外,7075铝合金中Zn元素的含量超过5%,Zn元素对α-Al2O3相的形成有强烈的阻碍作用[4],因此α-Al2O3的含量相对较少.由XRD物相分析可知,涂层主要是由Al和O元素组成,与氧化涂层截面线扫描成分分析结果相吻合.图4 7075铝合金经不同微弧氧化时间涂层显微硬度的变化Fig.4 Hardness variation as a function of microarc oxidation time on 7075 Al alloy2.3 陶瓷涂层的硬度图4为7075铝合金微弧氧化涂层的平均显微硬度随氧化时间不同而变化的情况.从图4可知,7075铝合金经微弧氧化后,涂层截面的平均显微硬度随氧化时间的延长略有增加,显微硬度(Hv0.1)值在1250~1300之间变化,当氧化时间达到60 min时,涂层截面平均显微硬度Hv0.1最大为1291.基体7075铝合金的显微硬度Hv0.1约为170,可见7075铝合金经微弧氧化后,涂层硬度远高于基体硬度.3 结论7075铝合金在硼酸盐体系的电解液中经不同时间微弧氧化后,对其涂层的表面形貌、物相构成、显微硬度进行了研究,得出如下结论:(1)微弧氧化涂层由疏松层、致密层组成,致密层占涂层总厚度的80%以上,且与基体结合较好;不同微弧氧化时间的氧化涂层的粗糙度变化不大,当氧化时间45 min时涂层的粗糙度值最高.(2)氧化涂层主要由γ-Al2O3和α-Al2O3两相组成,其中γ-Al2O3相含量较多.(3)氧化涂层截面的显微硬度值(Hv0.1)可达1250以上,随着微弧氧化时间的延长显微硬度有所增大.【相关文献】[1] 石小超,陈朝章,徐晋勇,等.铝合金微弧氧化技术研究概况[J].兵器材料科学与工程,2012,35(6):92-95.[2] 李忠盛,吴护林,潘复生.7A55铝合金微弧氧化陶瓷膜的组织和性能[J].航空材料学报,2010,30(5) 54-57.[3] 郝康达,苗景国,陈秋荣.铝酸钠浓度对7075铝合金微弧氧化膜层特性的影响[J].表面技术,2013,42(3):49-51.[4] 吴振东,姜兆华,姚忠平.纯铝及其合金的微等离子体氧化成膜特征[J].稀有金属材料与工程,2006, 35(2):148-151.。
氧化时间对7075铝合金的表面硬度和耐磨损性能的影响

氧化时间对7075铝合金的表面硬度和耐磨损性能的影响作者:李向新来源:《中国化工贸易·下旬刊》2017年第06期摘要:通过对7075铝合金进行微弧氧化处理,比较不同氧化时间对7075铝合金膜层显微硬度和薄膜形貌等产生的影响,再对氧化时间和表面微弧氧化处理工艺之间的关系进行阐述。
研究结果显示,7075铝合金表面的致密层随着时间增加而变厚,单位能耗则是随着氧化时间的增加呈现出先减小后增加的趋势。
最佳氧化时间为30min至40min之间。
关键词:氧化时间;7075铝合金;表面硬度;耐磨损性能1 实验设备及方法1.1 实验所用设备本次设备电源采用恒流双极脉冲模式,主要是因为此种模式的电源更容易控制,可以使起弧时间有效降低,减少资源的损耗现象。
所使用的材料包含KOH溶液(1.5g/l)和Na2SO3+(12.5g/l)。
铝合金的规格为45×15×2mm。
其中分别包含Si、Cu、Mn、Zn、Ti、Al等成分。
1.2 相关设备参数设置本次实验设计的参数分别为:溶液温度为28度,脉冲正负比分别为1:1,频率控制在600赫兹左右,电流密度为15A/dm2.PH溶液的浓度为10.2。
2 实验结果及相关分析2.1 氧化时间对成膜速率的影响分析随着7075铝合金氧化时间的不断增加,薄膜的厚度也跟着增加,成膜速率也呈现出明显的升高趋势。
但是当氧化时间以及电流的密度增加到某个阶段时,薄膜的成膜速率开始降低。
其原因主要是氧化时间的增加会导致脉冲电流波形发生相应变化。
波形的变化会导致溶液和金属界面上活化放电情况发生变化,波峰宽度会变窄,火花的放电程度也会变得更加激烈。
波峰高度的增加则会导致膜层击穿的能量有所增加,更容易出现微弧放电,使反应进程加速,从而使成膜速率大大增加。
如果氧化的时间太长会导致膜层击穿难度大大增加。
氧化时间如果比较长,则会导致薄膜的生长速率有所降低。
因此,氧化时间的增加会导致薄膜沉默速率有所增加,但是到达一定程度后,生长速率会呈现下降趋势。
7075铝合金的相关热处理以及表面处理

对7075铝合金深冷处理的影响K.E. Lulay, K. Khan, and D. Chaaya(发表于2002年4月8日,再经修订于2002年4月22日)众所知之,通过改变室温特性的科学,可以使得金属暴露在极端温度已经有了很广泛的研究。
虽然这项工作对高温热处理的影响已经进行了一些研究,但是在低温下(接近-196 ℃的性能研究也有许多进展。
在20世纪30年代到40年代,改变低温特性的方法首先出现,它能改善钢的切削性能。
[1]几十年来,许多工作进行了测控和解释对钢低温性能改变的效果。
[2,3]。
对一些有色金属合金也进行了研究。
通过气体金属联接管电弧焊接进行了铜合金的深冷处理,对磨损性能的影响进行了研究,[4]但并没有变化。
在本次研究中低温处理的效果,通过室温下对7075 - T651铝合金的强度、硬度进行了研究。
这是一个沉淀硬化材料,它具有高强度和耐腐蚀性而被应用。
试验样品已经处理,并再通过深冷低温处理,处理的试样放置于商业低温冷冻(-196℃)的温度进行了测试。
并且进行了两种不同长度的时间的测定,分别是2小时和48小时。
用2小时处理以确定是否有任何与时间无关的效果。
用48小时的处理以进行评价浸水效果。
深冷处理后没有再进行其它处理。
一系列的试样测试也将作为条件来建立一个标准。
所有的实验是都是在室温下进行的。
拉伸试验按照ASTM E8标准进行。
从这个实验中,对比例极限、屈服强度(0.2%残余应力)、极限拉伸强度、伸长率都进行了测定。
对硬度测试和夏比冲击试验也进行了测定。
如表1,48小时的低温处理效果对基本力学性能的影响是非常小的,一般大约只有1%的差异[5]。
最大的百分比变化是在观察夏比冲击试验中,它接近12%的差异。
2小时深冷处理后对其力学性能几乎没有什么影响。
要确定所引起的实际误差结果是取决于材料还是观察到的误差由于正常的数据变化(而不是真实误差),要通过统计t-实验来进行。
t –实验通过分析两组数据,以确定误差是测量的平均值是真实的还是一种偶然误差的结果。
7075铝合金三种表面强化工艺对比试验

基金项目:丽水高层次人才培养资助项目(2015RC28);省公益性技术应用研究计划项目(2016C31G2260014) 作者简介:肖阳(1982-),男,湖南岳阳人,讲师,硕士,研究方向为先进制造技术、材料成型与测试。 收稿日期:2018-05-08
·5 4·
·轻合金及其加工·
轻 金 属
2019年第 1期
7075铝合金三种表面强化工艺对比试验
肖 阳1,袁海洋2
(1.湖南信息职业技术学院 机电工程系,湖南 长沙 410200; 2.丽水学院 工学院,浙江 丽水 323000)
摘 要:采用机械喷丸、激光冲击强化与深滚压三种表面强化工艺处理 7075高强铝合金试样,在表面残余应力水平相 当的情况下分析表面粗糙度、表层显微硬度与表层残余应力场的分布特性及对疲劳性能的影响方式与程度。结果表 明,表面强化工艺引入的表层残余压应力场的分布合理性及其抵抗外部应力松弛的能力是改善试样疲劳寿命的最关 键因素,机械喷丸与激光冲击强化处理的应力影响层浅且表面粗糙度导致的应力集中程度较大,对低周大应力疲劳性 能的改善作用较为有限,而深滚压处理的应力场影响层深且具有高的稳定性,可同时改善试样的高周与低周疲劳性 能。 关键词:7075铝合金;表面强化;残余应力;疲劳性能 中图分类号:TB53;TG115 文献标识码:B 文章编号:1002 1752(2019)01 0054 04
研究表明,残余压应力水平及其分布状态是改 善 7075铝合金件疲劳性能的最关键因素,通过降低 平均拉应力水平,从而延缓疲劳裂纹的萌生,同时又
能引发裂纹的闭合效应有效降低疲劳裂纹扩展的驱 动力,延迟疲劳裂纹扩展[6~8]。值得注意的是,残余 压应力水平固然重要,但其抵抗外部载荷应力松弛 的能力更为重要,这与表面强化工艺对材料表层的 改性密切相关。本文即针对 7075铝合金试件分别 引入机械喷丸、激光冲击强化与深滚压三种表面强 化工艺,分析材料表面粗糙度、表层显微硬度与表层 残余应力场的分布特性,研究在表面残余压应力水 平基本相当的情况下,评估不同表面强化工艺对试 件疲劳寿命的改善效果。
铝合金表面处理的方法及应用

铝合金表面处理的方法及应用对铝及其合金进行表面处理产生的氧化膜具有装饰效果、防护性能和特殊功能,可以改善铝及其合金导电、导热、耐磨、耐腐蚀以及光学性能等。
因此,国内外研究人员运用各种方法对其进行表面处理,以提高它的综合性能,并取得了很大进展。
目前,铝及其合金材料已广泛地应用于建筑、航空和军事等领域中。
本文分类论述了铝及其合金材料表面处理的主要方法。
1·化学转化膜处理金属表面处理工业中的化学转化处理时使金属与特定的腐蚀液接触,在一定条件下,金属表面的外层原子核腐蚀液中的离子发生化学或电化学反应,在金属表面形成一层附着力良好的难溶的腐蚀生成物膜层。
换言之,化学转化处理是一种通过除去金属表面自然形成的氧化膜而在其表面代之以一层防腐性能更好、与有机涂层结合力更佳的新的氧化膜或其他化合物的技术。
1.1阳极氧化法铝的阳极氧化法是把铝作为阳极,置于硫酸等电解液中,施加阳极电压进行电解,在铝的表面形成一层致密的Al2O3膜,该膜是由致密的阻碍层和柱状结构的多孔层组成的双层结构。
阳极氧化时,氧化膜的形成过程包括膜的电化学生成和膜的化学溶解两个同时进行的过程。
当成膜速度大于溶解速度时,膜才得以形成和成长。
通过降低膜的溶解速度,可以提高膜的致密度。
氧化膜的性能是由膜孔的致密度决定的。
1.1.1硬质阳极氧化铝的硬质阳极氧化是在铝进行阳极氧化时,通过适当的方法,降低膜的溶解速度,获得更厚、更致密的氧化膜。
常规的方法是低温(一般为0℃左右)和低硫酸浓度(如<10%H2SO4)的条件下进行,生产过程存在能耗大、成本高的缺点。
改善硬质阳极氧化膜的另一种方法是改变电源的电流波形。
氧化膜的电阻很大,氧化过程中产生大量的热量,因此,传统直流氧化电流不宜过大,运用脉冲电流或脉冲电流与直流电流相叠加,可以极大地降低阳极氧化所需要的电压,并且可使用更高的电流密度,同时还可以通过调节占空比和峰值电压,来提高膜的生长速度,改善膜的生成质量,获得性能优良的氧化膜。
铝合金压铸后表面处理
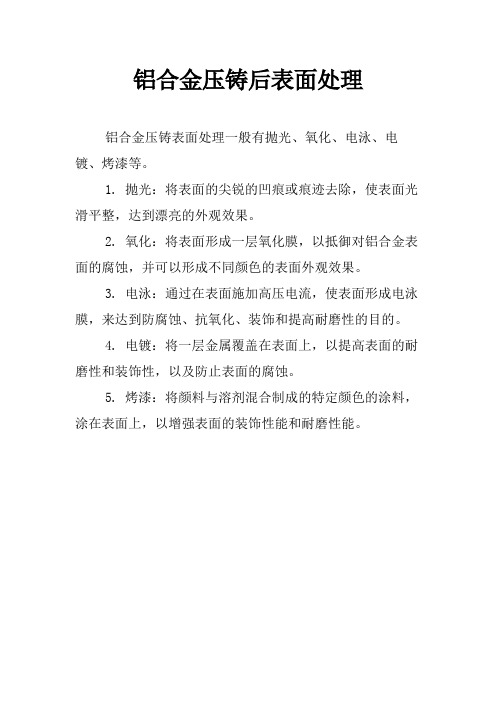
铝合金压铸后表面处理
铝合金压铸表面处理一般有抛光、氧化、电泳、电镀、烤漆等。
1. 抛光:将表面的尖锐的凹痕或痕迹去除,使表面光滑平整,达到漂亮的外观效果。
2. 氧化:将表面形成一层氧化膜,以抵御对铝合金表面的腐蚀,并可以形成不同颜色的表面外观效果。
3. 电泳:通过在表面施加高压电流,使表面形成电泳膜,来达到防腐蚀、抗氧化、装饰和提高耐磨性的目的。
4. 电镀:将一层金属覆盖在表面上,以提高表面的耐磨性和装饰性,以及防止表面的腐蚀。
5. 烤漆:将颜料与溶剂混合制成的特定颜色的涂料,涂在表面上,以增强表面的装饰性能和耐磨性能。
7075 -t6 铝合金的热处理工艺卡片

7075 -t6 铝合金是一种常用的高强度铝合金,常用于航空航天、汽车制造和机械设备等领域。
热处理是提高其性能的关键步骤之一。
下面是关于7075 -t6 铝合金热处理工艺的详细卡片。
一、7075 -t6 铝合金的特点1. 高强度:室温下抗拉强度为540MPa以上,热处理后可达到570-610MPa。
2. 耐腐蚀性好:具有良好的耐蚀性,适用于各种恶劣环境。
3. 难加工:7075 -t6 铝合金硬度较大,加工性较差,需要选用合适的工艺来进行加工。
二、热处理工艺1. 固溶处理(Solution Treatment):将7075 -t6 铝合金加热至485-490℃保温2-3小时,然后采用快速冷却方式(通常是水淬)。
2. 人工时效(Artificial Aging):将经过固溶处理的7075 -t6 铝合金放入烤箱,温度设定为120-125℃,时效24小时。
三、热处理效果1. 提高抗拉强度:经过热处理后,7075 -t6 铝合金的抗拉强度可提高10-15。
2. 提高硬度:经过热处理后,合金硬度提高,提高了其耐磨性和抗冲击性。
3. 改善加工性能:热处理后的铝合金具有更好的加工性能,适用于各种复杂加工。
四、使用注意事项1. 控制加热温度:严格控制固溶处理的加热温度和保温时间,避免过高或过低影响合金性能。
2. 快速冷却:固溶处理后应采用快速冷却方式,以保证合金组织的均匀性。
3. 时效时间控制:时效时间过长或过短都会影响合金性能,需要根据具体情况精确控制。
五、应用领域1. 航空航天:7075 -t6 铝合金的高强度和优良的耐蚀性使其成为航空航天领域中的重要结构材料。
2. 汽车制造:7075 -t6 铝合金在汽车制造领域广泛应用于车身结构、悬挂系统等部件。
3. 机械设备:由于其高强度和耐磨性,7075 -t6 铝合金在机械设备中也有着广泛的应用。
六、未来发展随着科学技术的不断进步,热处理工艺也在不断改进和完善,未来研究和应用方向主要集中在提高合金的耐高温性能和耐磨性能,以更好地满足各种复杂工况下的需求。
7075铝合金表面处理

7075铝合金表面处理1.化学镀镍、渗氮、热扩渗都是传统的铝合金表面强化技术,能够改善材料的表面性能。
研究化学镀镍加气体渗氮的复合方法处理7075铝合金表面的工艺和性能以及 7075铝合金与Mg-Zn合金相互扩散过程。
对带有镍层表面的7075铝合金进行气体渗氮,增大了铝合金的表面硬度,其硬度最高达700HV,是基体硬度的7-8倍。
2.7075铝合金表面镀硬铬工艺。
3.化学镀技术:在铝合金基体上制备 Ni-Cu-P合金镀层、Ni-P/纳米金刚石或者Ni-Co-P/Si3N4化学复合镀层。
4•铝合金复合涂层技术,研究硬质阳极氧化处理,发展具有减摩耐磨性能的自润滑铝合金复合涂层。
将铝先进行硬质阳极氧化,然后采用热浸法引入聚四氟乙烯微粒至氧化膜膜孔及表面,通过真空精密热处理后形成复合涂层。
5.复合电镀:利用复合电镀技术,在铝合金基体上电镀Ni/微米AI2O3 /纳米AI2O3复合镀层。
6.喷涂方法:在铝合金表面喷涂烧结型 WC-17CO粉末,制备 WC 涂层,以提高铝合金基体的耐磨性。
7.激光熔覆技术用激光熔覆技术对铝合金表面进行改性,在铝合金表面激光熔覆制备各种性能的硅涂层。
利用横流C02高激光器,以铝合金为基材,在其表面预置硅粉后进行激光处理,研究熔覆工艺参数优化、组织形貌、热处理研究。
8•低温常压化学气相沉积(APCVD )技术,在铝及其合金基底上制备硅氧化物陶瓷薄膜。
沉积温度为 400 C,有效提高铝及铝合金表面的耐磨性。
9.强流脉冲电子束表面改性:高能电子束在很短的脉冲时间内将能量注入材料表面极薄的一层。
利用 Nadezhda-2型强流脉冲电子束装置研究了对6063铝合金化学镀的影响和 YG8硬质合金的改性研究。
10.铝合金表面镀渗复合改性处理工艺:利用闭合场非平衡磁控溅射预先在铝合金表面制备一层 Ti膜,再进行脉冲等离子体渗氮处理,探索了铝合金表面镀渗复合改性处理工艺。
复合改性后与未处理铝合金的磨损率相比,下降了 64.7%。
7075铝合金热处理工艺
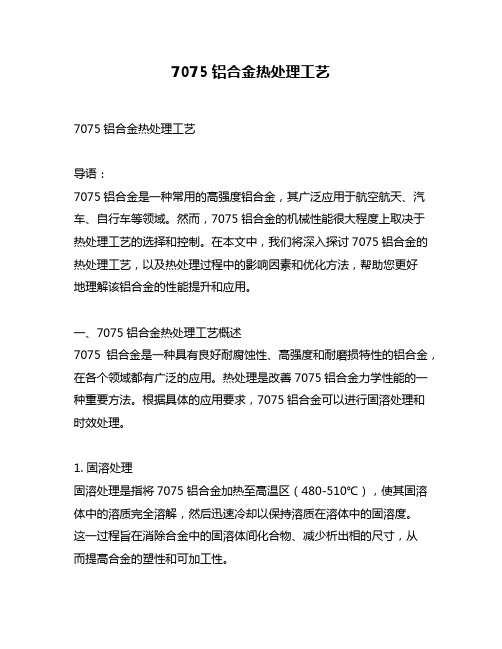
7075铝合金热处理工艺7075铝合金热处理工艺导语:7075铝合金是一种常用的高强度铝合金,其广泛应用于航空航天、汽车、自行车等领域。
然而,7075铝合金的机械性能很大程度上取决于热处理工艺的选择和控制。
在本文中,我们将深入探讨7075铝合金的热处理工艺,以及热处理过程中的影响因素和优化方法,帮助您更好地理解该铝合金的性能提升和应用。
一、7075铝合金热处理工艺概述7075铝合金是一种具有良好耐腐蚀性、高强度和耐磨损特性的铝合金,在各个领域都有广泛的应用。
热处理是改善7075铝合金力学性能的一种重要方法。
根据具体的应用要求,7075铝合金可以进行固溶处理和时效处理。
1. 固溶处理固溶处理是指将7075铝合金加热至高温区(480-510℃),使其固溶体中的溶质完全溶解,然后迅速冷却以保持溶质在溶体中的固溶度。
这一过程旨在消除合金中的固溶体间化合物、减少析出相的尺寸,从而提高合金的塑性和可加工性。
2. 时效处理时效处理是指在固溶处理后,将7075铝合金加热至相应的时效温度(120-160℃),保持一定的时间后迅速冷却。
时效处理可以促进合金中产生硬化相,如MgZn2等,提高硬度和强度,同时保持一定的可塑性。
二、7075铝合金热处理影响因素7075铝合金的热处理工艺对其性能具有重要影响。
以下是几个主要的影响因素:1. 固溶处理温度固溶处理温度会影响铝合金中溶质的溶解度和固溶体的原子排列。
高温会增加合金的塑性和可加工性,但过高的温度可能导致过度溶解和晶粒长大。
2. 固溶处理时间固溶处理时间影响溶质在固溶体中的均匀分布程度。
适当的固溶处理时间可以完全溶解溶质,并使其均匀分布在固溶体中。
3. 时效处理温度和时间时效处理温度和时间对于硬度和强度的提高至关重要。
较高的时效处理温度和较长的时效时间可以促进硬化相的析出和晶体尺寸的增长。
4. 快速冷却快速冷却是保证7075铝合金热处理效果的关键。
快速冷却可以防止固溶体溶质再次析出,从而保持合金的塑性。
7075铝合金微弧氧化陶瓷膜摩擦性能

广东化工2019年第15期·26·第46卷总第401期7075铝合金微弧氧化陶瓷膜摩擦性能夏袁昊(江苏理工学院材料学院,江苏常州213001)Friction Properties of Micro-arc Oxidation Coating on7075Aluminum AlloyXia Yuanhao(School of Materials Engineering,Jiangsu University of Technology,Changzhou213001,China)Abstract:A ceramic film was grown on the surface of7075aluminum alloy by micro-arc oxidation treatment to improve its friction properties.The effects of technological parameters such as reaction voltage and reaction time on the surface morphology,microstructure,film thickness,surface hardness and friction behavior of such prepared coatings were investigated using the scanning electron microscopy(SEM),thickness gauge,micro-hardness tester,and friction test.The relationship between reaction voltage and reaction time and film thickness,surface hardness and friction coefficient was established.Keywords:7075aluminum alloy;micro-arc oxidation;friction properties1引言7075铝合金具有较高的韧性和优良的加工性能,适用于船舶和飞机的部件材料。
铝合金型材表面处理工艺流程
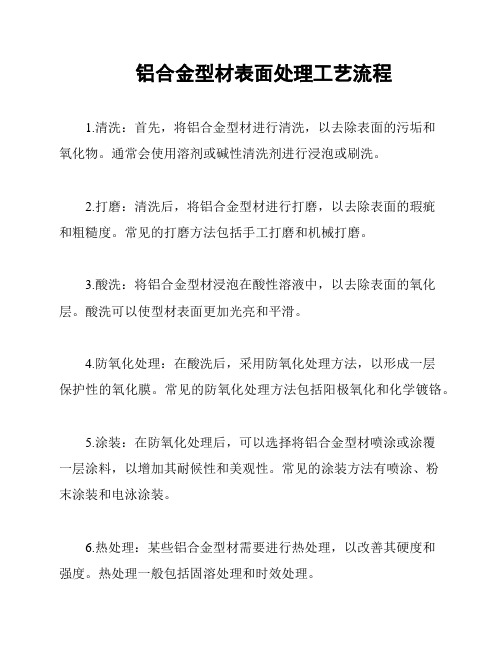
铝合金型材表面处理工艺流程
1.清洗:首先,将铝合金型材进行清洗,以去除表面的污垢和
氧化物。
通常会使用溶剂或碱性清洗剂进行浸泡或刷洗。
2.打磨:清洗后,将铝合金型材进行打磨,以去除表面的瑕疵
和粗糙度。
常见的打磨方法包括手工打磨和机械打磨。
3.酸洗:将铝合金型材浸泡在酸性溶液中,以去除表面的氧化层。
酸洗可以使型材表面更加光亮和平滑。
4.防氧化处理:在酸洗后,采用防氧化处理方法,以形成一层
保护性的氧化膜。
常见的防氧化处理方法包括阳极氧化和化学镀铬。
5.涂装:在防氧化处理后,可以选择将铝合金型材喷涂或涂覆
一层涂料,以增加其耐候性和美观性。
常见的涂装方法有喷涂、粉
末涂装和电泳涂装。
6.热处理:某些铝合金型材需要进行热处理,以改善其硬度和
强度。
热处理一般包括固溶处理和时效处理。
以上是铝合金型材表面处理工艺的基本流程,不同的型材和要求可能会有所差异。
在进行表面处理时,务必遵循相关的操作规范和安全要求,以确保处理效果和产品质量。
参考资料:
___。
铝合金材料与应用[M]。
___。
2010.
___。
现代铝加工技术[M]。
___。
2018.。
7075表面处理

7075铝合金表面处理1.化学镀镍、渗氮、热扩渗都是传统的铝合金表面强化技术,能够改善材料的表面性能。
研究化学镀镍加气体渗氮的复合方法处理7075铝合金表面的工艺和性能以及7075铝合金与Mg-Zn合金相互扩散过程。
对带有镍层表面的7075铝合金进行气体渗氮,增大了铝合金的表面硬度,其硬度最高达700HV,是基体硬度的7-8倍。
2.7075铝合金表面镀硬铬工艺。
3.化学镀技术:在铝合金基体上制备Ni-Cu-P合金镀层、Ni-P/纳米金刚石或者Ni-Co-P/Si3N4化学复合镀层。
4.铝合金复合涂层技术,研究硬质阳极氧化处理,发展具有减摩耐磨性能的自润滑铝合金复合涂层。
将铝先进行硬质阳极氧化,然后采用热浸法引入聚四氟乙烯微粒至氧化膜膜孔及表面,通过真空精密热处理后形成复合涂层。
5.复合电镀:利用复合电镀技术,在铝合金基体上电镀Ni/微米Al2O3/纳米Al2O3复合镀层。
6.喷涂方法:在铝合金表面喷涂烧结型WC-17Co粉末,制备WC涂层,以提高铝合金基体的耐磨性。
7.激光熔覆技术用激光熔覆技术对铝合金表面进行改性,在铝合金表面激光熔覆制备各种性能的硅涂层。
利用横流CO2高激光器,以铝合金为基材,在其表面预置硅粉后进行激光处理,研究熔覆工艺参数优化、组织形貌、热处理研究。
8.低温常压化学气相沉积(APCVD)技术,在铝及其合金基底上制备硅氧化物陶瓷薄膜。
沉积温度为400℃,有效提高铝及铝合金表面的耐磨性。
9.强流脉冲电子束表面改性:高能电子束在很短的脉冲时间内将能量注入材料表面极薄的一层。
利用Nadezhda-2型强流脉冲电子束装置研究了对6063铝合金化学镀的影响和YG8硬质合金的改性研究。
10.铝合金表面镀渗复合改性处理工艺:利用闭合场非平衡磁控溅射预先在铝合金表面制备一层Ti膜,再进行脉冲等离子体渗氮处理,探索了铝合金表面镀渗复合改性处理工艺。
复合改性后与未处理铝合金的磨损率相比,下降了64.7%。
航空铝合金7075表面处理工艺
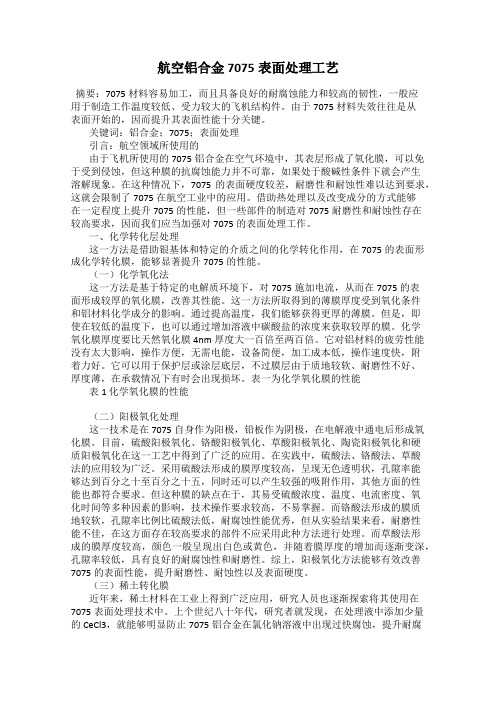
航空铝合金7075表面处理工艺摘要:7075材料容易加工,而且具备良好的耐腐蚀能力和较高的韧性,一般应用于制造工作温度较低、受力较大的飞机结构件。
由于7075材料失效往往是从表面开始的,因而提升其表面性能十分关键。
关键词:铝合金;7075;表面处理引言:航空领域所使用的由于飞机所使用的7075铝合金在空气环境中,其表层形成了氧化膜,可以免于受到侵蚀,但这种膜的抗腐蚀能力并不可靠,如果处于酸碱性条件下就会产生溶解现象。
在这种情况下,7075的表面硬度较差,耐磨性和耐蚀性难以达到要求,这就会限制了7075在航空工业中的应用。
借助热处理以及改变成分的方式能够在一定程度上提升7075的性能,但一些部件的制造对7075耐磨性和耐蚀性存在较高要求,因而我们应当加强对7075的表面处理工作。
一、化学转化层处理这一方法是借助银基体和特定的介质之间的化学转化作用,在7075的表面形成化学转化膜,能够显著提升7075的性能。
(一)化学氧化法这一方法是基于特定的电解质环境下,对7075施加电流,从而在7075的表面形成较厚的氧化膜,改善其性能。
这一方法所取得到的薄膜厚度受到氧化条件和铝材料化学成分的影响。
通过提高温度,我们能够获得更厚的薄膜。
但是,即使在较低的温度下,也可以通过增加溶液中碳酸盐的浓度来获取较厚的膜。
化学氧化膜厚度要比天然氧化膜4nm厚度大一百倍至两百倍。
它对铝材料的疲劳性能没有太大影响,操作方便,无需电能,设备简便,加工成本低,操作速度快,附着力好。
它可以用于保护层或涂层底层,不过膜层由于质地较软、耐磨性不好、厚度薄,在承载情况下有时会出现损坏。
表一为化学氧化膜的性能表1 化学氧化膜的性能(二)阳极氧化处理这一技术是在7075自身作为阳极,铅板作为阴极,在电解液中通电后形成氧化膜。
目前,硫酸阳极氧化、铬酸阳极氧化、草酸阳极氧化、陶瓷阳极氧化和硬质阳极氧化在这一工艺中得到了广泛的应用。
在实践中,硫酸法、铬酸法、草酸法的应用较为广泛。
飞机架构用7075合金的微弧氧化工艺

飞机架构用7075合金的微弧氧化工艺摘要:本文将介绍飞机架构使用7075合金的微弧氧化工艺。
该工艺适用于氧化铝和氧化硅的涂层制备,包括涂层的厚度、成分和表面形貌方面。
使用该工艺可以提高7075合金的耐磨性和耐腐蚀性,以及改善其表面质量和界面结构。
然而,该工艺还需要进一步的研究和分析,以实现更广泛的应用和优化方案。
关键词:7075合金;微弧氧化;涂层;耐磨性;耐腐蚀性;界面结构;优化方案。
正文:7075合金是一种高强度、轻质的金属材料,广泛应用于航空和汽车工业等领域。
然而,由于其易受腐蚀和磨损的特性,需要采用新的工艺来增强其性能。
微弧氧化工艺是一种新兴的表面处理技术,可以在微观尺度下形成氧化层,从而增强材料的耐磨性和耐腐蚀性。
在本文中,将研究使用7075合金的微弧氧化工艺。
首先,在该工艺中,需要准确地控制氧化涂层的成分和厚度。
在实验中,应用不同的工艺参数,如电压、电流密度和电解液成分,来调控产生的涂层的成分和厚度。
例如,可以采用钠硅酸盐或磷酸铝为电解液,以实现不同的氧化涂层。
其次,在涂层的表面形貌方面,可以通过控制微弧氧化的时间和工艺条件来实现不同形貌的涂层。
例如,可以生成具有连续、均匀和致密的氧化层,从而增强涂层的耐磨性和耐腐蚀性,并改善7075合金的表面质量。
最后,在界面结构方面,微弧氧化涂层可以形成复合层,包括铝氧化物、硅氧化物和金属氧化物。
增加涂层的复合性质,可以改善界面结构并增强涂层的附着力。
在实验中,可以采用扫描电镜和X射线衍射仪等技术来研究涂层的表面形貌和复合结构。
总之,7075合金微弧氧化涂层是一种具有潜力的技术,可以提高材料的耐磨性和耐腐蚀性,改善表面质量和界面结构。
然而,该技术仍需进一步的研究和分析,以优化工艺方案,并实现更广泛的应用。
在航空领域,7075合金是一种广泛应用的金属材料,其高强度、轻质等特性,使其受到了广泛的关注和应用。
然而,由于其易受腐蚀和磨损等特性,需要采用新的技术和材料来增强其性能。
7075铝合金表面钼酸盐钝化工艺

7075铝合金表面钼酸盐钝化工艺徐临超;陈贤杭;李勇【摘要】A environmental friendly process by molybdate for 7075 aluminum alloy surface has been investigated for replacing the high toxic one by chromate.Effects of bath composition, pH, treatment temperature and time on the properties of passivation film have been discussed. Results of Neutral Salt Spray tests show that an uniform deep black passivationfilm with corrosion resistance better than by chromate treatment is formed on the surface of 7075 aluminum alloy, non-continuous state micro structure, uniformly distributed circular bright spots.%采用环境友好型钼酸盐工艺取代铬酸盐工艺对7075铝合金表面进行钝化处理,探讨了钝化液成分、pH 值、处理温度及时间对钝化膜层耐蚀性的影响。
中性盐雾腐蚀(NSS)实验表明,采用钼酸盐钝化工艺获得膜层的耐蚀性优于铬酸盐钝化膜,膜层为无金属光泽的均匀黑色钝化膜,微观结构呈非连续性网状结构,有均匀分布的圆形亮色斑点。
【期刊名称】《浙江工贸职业技术学院学报》【年(卷),期】2015(000)002【总页数】4页(P49-52)【关键词】7075铝合金;钼酸盐钝化;耐蚀性【作者】徐临超;陈贤杭;李勇【作者单位】浙江工贸职业技术学院,浙江温州325003;浙江工贸职业技术学院,浙江温州325003;浙江工贸职业技术学院,浙江温州325003【正文语种】中文【中图分类】TG178徐临超,陈贤杭,李勇(浙江工贸职业技术学院,浙江温州325003)7075铝合金是一种冷处理锻压用合金,其强度优于软钢,机械性能好,被广泛应用于航空航天、交通运输、模具加工制造、轻工制造、机械设备零部件、工装夹具等工业领域。
- 1、下载文档前请自行甄别文档内容的完整性,平台不提供额外的编辑、内容补充、找答案等附加服务。
- 2、"仅部分预览"的文档,不可在线预览部分如存在完整性等问题,可反馈申请退款(可完整预览的文档不适用该条件!)。
- 3、如文档侵犯您的权益,请联系客服反馈,我们会尽快为您处理(人工客服工作时间:9:00-18:30)。
7075铝合金表面处理
1.化学镀镍、渗氮、热扩渗都是传统的铝合金表面强化技术,能够改善材料的表面性能。
研究化学镀镍加气体渗氮的复合方法处理7075铝合金表面的工艺和性能以及7075铝合金与Mg-Zn合金相互扩散过程。
对带有镍层表面的7075铝合金进行气体渗氮,增大了铝合金的表面硬度,其硬度最高达700HV,是基体硬度的7-8倍。
2.7075铝合金表面镀硬铬工艺。
3.化学镀技术:在铝合金基体上制备Ni-Cu-P合金镀层、Ni-P/纳米金刚石或者Ni-Co-P/Si3N4化学复合镀层。
4.铝合金复合涂层技术,研究硬质阳极氧化处理,发展具有减摩耐磨性能的自润滑铝合金复合涂层。
将铝先进行硬质阳极氧化,然后采用热浸法引入聚四氟乙烯微粒至氧化膜膜孔及表面,通过真空精密热处理后形成复合涂层。
5.复合电镀:利用复合电镀技术,在铝合金基体上电镀Ni/微米Al2O3/纳米Al2O3复合镀层。
6.喷涂方法:在铝合金表面喷涂烧结型WC-17Co粉末,制备WC涂层,以提高铝合金基体的耐磨性。
7.激光熔覆技术
用激光熔覆技术对铝合金表面进行改性,在铝合金表面激光熔覆制备各种性能的硅涂层。
利用横流CO2高激光器,以铝合金为基材,在其表面预置硅粉后进行激光处理,研究熔覆工艺参数优化、组织形貌、热处理研究。
8.低温常压化学气相沉积(APCVD)技术,在铝及其合金基底上制备硅氧化物陶瓷薄膜。
沉积温度为400℃,有效提高铝及铝合金表面的耐磨性。
9.强流脉冲电子束表面改性:高能电子束在很短的脉冲时间内将能量注入材料表面极薄的一层。
利用Nadezhda-2型强流脉冲电子束装置研究了对6063铝合金化学镀的影响和YG8硬质合金的改性研究。
10.铝合金表面镀渗复合改性处理工艺:利用闭合场非平衡磁控溅射预先在铝合金表面制备一层Ti膜,再进行脉冲等离子体渗氮处理,探索了铝合金表面镀渗复合改性处理工艺。
复合改性后与未处理铝合金的磨损率相比,下降了64.7%。
11.利用电弧离子镀在铝合金上镀制TiN膜以及Ti/TiN多层膜。
12.对铝合金进行等离子体基离子注入(Plasma Based Ion Implantation,PBII)氮、碳及磁控溅射沉积Ti结合PBII氮、碳注入,在基体表面形成改性层,从而使铝合金表面硬度、耐磨性和耐腐蚀性得到提高,延长铝合金塑料模具的使用寿命。
13.微等离子体氧化技术:将铝合金置于电解液中通电,使其表面产生微等离子体放电,从而在铝合金表面原位生长一层陶瓷膜的表面处理技术。
通过这种技术可在铝合金表面获得高硬度、高热抗、耐腐蚀性好、附着力高、色泽稳定的陶瓷膜层。
14.铝合金微弧氧化陶瓷层:通过微弧氧化可获得硬质陶瓷层;
15.铝合金硬质阳极氧化膜技术:研究常温下的硬质阳极氧化工艺,以硫酸为基础电解液,加入有机酸改性,采用恒流法直流叠加脉冲阳极氧化,在2024铝合金表面得到硬度350HV、膜厚50μm的氧化膜。
16.利用电弧氮化法直接在铝及铝合金基体上制备氮化层。
使用普通的钨极氩弧焊机,通入不同比例的氮气与氩气混合气体,在纯Al合金基体上,高温电弧使基体局部熔化,同时使氮气电离,与熔化的Al发生反应生成AlN,冷却后形成氮化层,提高抗磨料磨损和摩擦磨损性能。
17.铝合金表面快速硬质自润滑涂层的制备:以MoS2粒子为润滑改性剂,采用共生沉积方法在铝合金硬质氧化过程中将MoS2粒子沉积在铝合金的硬质氧化膜中,以达到改善膜层润滑性能的目的。
18.利用喷射沉积技术,在已有铝合金基底上制备高硅铝合金。
19.熔体搅拌铸造法:采用配料—熔化基体—加入增强颗粒—熔炼—变质处理—浇注—热处理制得陶瓷颗粒增强铝基复合材料。
20.利用无压浸渗制备工艺:先制备多孔陶瓷预制体,在氮气气氛、950℃下浸渗4h,制备具有不同陶瓷含量的Si3N4/AlN-Al复合材料。
21.熔体反应法工艺。
以Al合金为基体合金,以Al-Zr(CO3)2为反应体系,采用熔体原位反应法,制备耐热耐磨(Al2O3+Al3Zr)p/Al复合材料,研究复合材料的微观组织、内生增强体特征、力学性能、室温和高温干滑动摩擦磨损特性。