附图1(甲烷分离装置工艺流程图)
甲烷深冷分离设备布置及管道布置设计要点
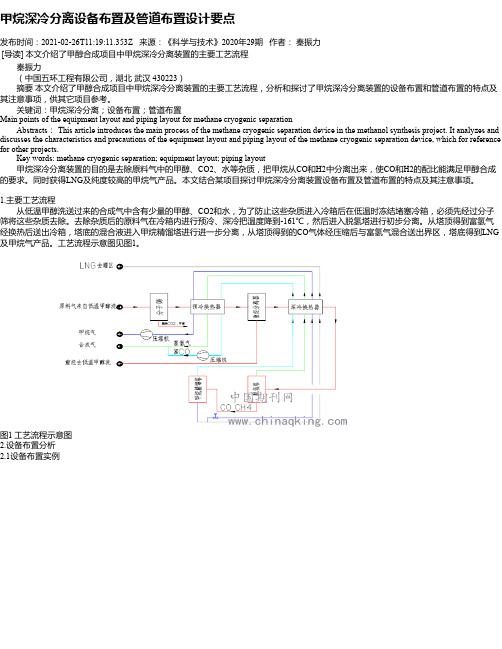
甲烷深冷分离设备布置及管道布置设计要点发布时间:2021-02-26T11:19:11.353Z 来源:《科学与技术》2020年29期作者:秦振力[导读] 本文介绍了甲醇合成项目中甲烷深冷分离装置的主要工艺流程秦振力(中国五环工程有限公司,湖北武汉 430223)摘要本文介绍了甲醇合成项目中甲烷深冷分离装置的主要工艺流程,分析和探讨了甲烷深冷分离装置的设备布置和管道布置的特点及其注意事项,供其它项目参考。
关键词:甲烷深冷分离;设备布置;管道布置Main points of the equipment layout and piping layout for methane cryogenic separation Abstracts: This article introduces the main process of the methane cryogenic separation device in the methanol synthesis project. It analyzes and discusses the characteristics and precautions of the equipment layout and piping layout of the methane cryogenic separation device, which for reference for other projects. Key words: methane cryogenic separation; equipment layout; piping layout 甲烷深冷分离装置的目的是去除原料气中的甲醇、CO2、水等杂质,把甲烷从CO和H2中分离出来,使CO和H2的配比能满足甲醇合成的要求。
同时获得LNG及纯度较高的甲烷气产品。
本文结合某项目探讨甲烷深冷分离装置设备布置及管道布置的特点及其注意事项。
甲烷分离氮气压缩操作规程
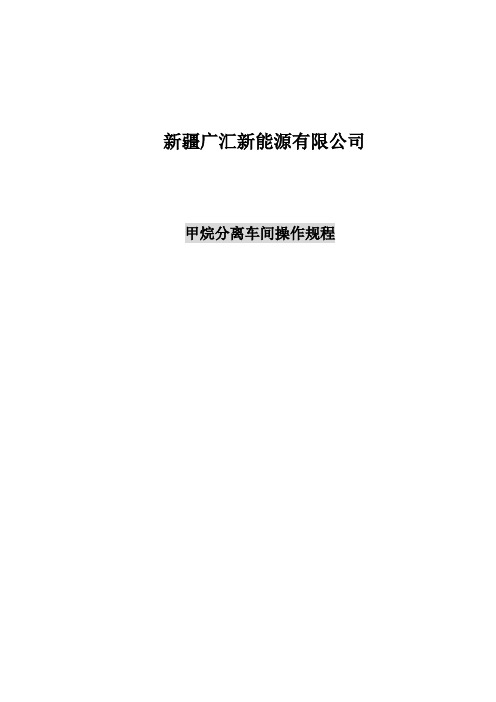
新疆广汇新能源有限公司甲烷分离车间操作规程新疆广汇新能源有限公司甲烷分离装置氮气压缩机操作规程甲烷分离装置氮气压缩操作规程编制:周桂林审核:韩玉刚审定:王斌崔志民批准:郭建民2010年12月新疆广汇新能源有限公司甲烷分离装置氮气压缩机操作规程目录一、岗位职责、任务及范围 (4)1.岗位职责 (4)2.岗位任务 (4)3.管辖范围 (4)二、岗位工艺流程简述 (4)1.机组工作原理 (4)2.工艺流程 (5)3.蒸汽系统流程 (5)4.冷却水流程 (5)5.润滑油系统流程 (5)6.干气密封系统流程 (6)7.抽真空系统流程 (6)8.轴封气系统流程 (6)三、主要工艺参数 (6)1.氮气压缩机组 (6)2.氮气汽轮机组 (7)3.设备一览表 (8)四、开车 (8)1.氮气压缩机组原始开车 (8)2.氮气压缩机正常开车 (10)3.氮气压缩机短期停车后开车 (12)五、正常操作 (12)1.机组加负荷 (12)2.机组减负荷 (13)3.机组正常操作及设备维护保养 (13)六、停车步骤 (18)1.氮气压缩机正常停车 (18)2.氮气压缩机紧急停车 (19)七、特殊操作 (19)八、安全生产及环境保护 (20)1.安全注意事项 (20)2.安全紧急预案 (20)3.环保注意事项 (23)九、附图(表) (23)1.氮气压缩机报警联锁一览表 (23)2安全阀及防爆片一览表 (24)3.联锁逻辑图(待补) (24)一、岗位职责、任务及范围1.岗位职责(1)在班长领导下,认真完成工段、车间及上级部门交给的各项工作任务。
(2)加强业务学习,提高业务技术水平,精心操作,杜绝一切操作责任事故的发生。
(3)严格执行各工艺参数指标,负责所有工艺参数的调整, 严格遵守各项规章制度。
(4)认真做好本岗位的安全生产及节能降耗工作。
(5)严格执行调度及班长指令,并有权拒绝错误指令。
(6)发现问题及时处理并向班长报告。
(7)每小时整点正负10分钟内对系统进行全面检查,并用仿宋字体填写记录报表及巡回检查内容。
甲烷分离技术工艺系统描述

工艺系统描述总述本装置的原料气来自于煤气化装置,其主要成分为CO,H2 和甲烷,本甲烷分离装置的目的是要把CO/H2从原料气中分离出来,用于下游甲醇合成装置生产甲醇,把甲烷液化生成LNG产品销售。
在甲烷液化之前,我们首先要把原料气中的水,甲醇和汞脱除掉,因为这些成分在低温条件下会结冰,堵塞设备或降低换热器的性能;然后经过两个预处理单元保护设备的性能。
脱水干燥单元利用两个分子筛系统脱除水和甲醇,另外脱汞床单元利用两个脱汞床的活性炭脱除其中的汞。
液化部分利用BV的Prico液化工艺技术把原料气中的甲烷液化从而生成LNG副产品。
PRICO工艺是由BV公司的气体,石油和化学品部门开发出来的,简单,可靠,易操作,利用合成气分馏塔把合成气产品与液体甲烷分离开。
本装置不需要单独配置CO2脱除装置,因为进界区原料气中CO2的含量为20 ppm,本装置可允许的CO2最大量为50PPM。
原料气压缩来自煤气化装置纯化单元的原料气进入甲烷分离装置入口凝聚过滤器F616A/B01,压力为2.4Mpa。
设置此过滤器的目的是去除原料气中可能存在的固体杂质和工艺液体。
过滤后的原料气进入到原料气压缩机J616A/B01,压力升高到5.1MPa。
从原料气压缩机出来的原料气在压缩机冷却器C616A/B01冷却,然后被送入到气体处理段。
干燥脱水、甲醇&脱汞原料气进入装置前已经脱除大部分水分,但仍然不能满足深冷分离的要求,为此设计了干燥脱水系统,确保深冷分离工段不受水和甲醇的影响。
分子筛过滤器/分离器F616A/B02捕获可能从原料气压缩机冷却器携带过来的工艺液体。
原料气进入到处于吸附状态的分子筛干燥器F616A/B03A/B顶部,当原料气经过床层的时候,原料气中的水和甲醇被吸附到床层上。
在任何时候,都是其中一个床层在吸附水和甲醇,另外一个床层处于再生状态,包括加热、冷却和备用,整个脱水干燥循环为24小时,其中12小时为吸附,7.3小时是加热状态,3.7小时是冷却,1.0小时为切换。
煤制气液化分离工艺技术研究
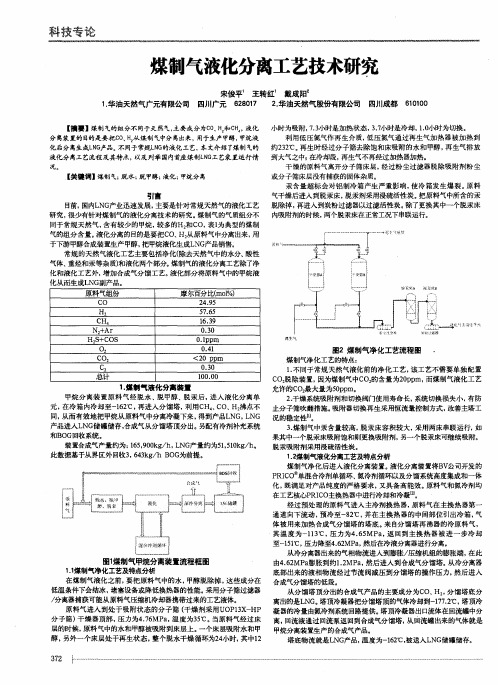
煤制气液化分离工艺技术研究
宋俊平’ 王转红’ 戴成阳 1 . 华 油天然气广元有限公司 四川广元 6 2 8 0 1 7 2 . 华油天然气股份有限公司 四川成都 6 1 0 1 0 0
【 摘要】 煤制 气的组分不 同于天然气, 主要成 分为c 0 、 H z 和c H , 液化 小时为吸 附, 7 . 3 小时是加热 状态 , 3 . 7 , J 、 时是冷却 , 1 . O 小时为切换 。
图1 煤制气甲烷分离装置流程框 图
1 . 1 煤制气 净化工艺及特点分析 在煤制气 液化之前 , 要把 原料气 中的 水 , 甲醇脱 除掉 , 这 些成分在 低温 条件下会结冰 , 堵塞设备或 降低换热 器的性能。 采用分子筛过 滤器 / 分离器捕 获可能从 原料气压缩机 冷却器携带 过来的工艺液体。 原料气 进入 到处于 吸附 状态 的分子筛 ( 干 燥剂 采用UO P 1 3 X - HP 分 子筛 ) 干 燥 器顶部 , 压 力为4 . 7 6 MP a , 温 度为3 5 " ( 2 。 当原 料气经 过床 层的时候 , 原 料气中的水和 甲醇被 吸附 到床 层上。 一 个床层吸 附水和 甲 醇, 另外 一个 床层处于 再生状 态 , 整个脱水 干燥 循环为2 4 / b 时, 其 中1 2
引育 目 前, 国内L N G 产业迅 速发展 , 主要是针对常规 天然 气的液化工艺 脱 除掉 , 再进 入到炭粉 过滤器以过滤 活性 炭 。 除了更换 其中一个脱汞床 研究, 很 少有针对 煤制气的 液化分离技术 的研究 。 煤制 气的气质组分不 内吸附剂的时候 , 两个脱 汞床在正常工况下 串联运行。 同于常规 天然 气, 含有较 少 的甲烷 , 较 多的H: 和C 0 , 表1 为典 型的煤制 气的组分含 量。 液化分离的 目 的是要 把C O 、 H 从 原料 气中分离出来, 用 于下游 甲醇合成装 置生 产甲醇 , 把甲烷 液化生成 L N G 产品销售。 常规 的天然 气液化工艺 主要包括 净化( 除去 天然 气中的水分、 酸性 气体 、 重烃和 汞等杂 质) 和液化两 个部分。 煤制气 的液化分离工艺除了净 化和液化 工艺外 , 增 加合成气分 馏工艺。 液化部分 将原料气 中的 甲烷液 化从而生成 L N G  ̄ ] I 产品。
第四章裂解气的净化与分离

2、净化与分离 A、目的 净化---除去③,主要为脱酸性气体、脱水、脱 炔; 分离---①、②、④ B、要求 据乙烯、丙稀用途而不同(表1-24.25)。 如,聚合用乙烯,丙稀要求高。在表124中,乙烯纯度要大于99.9%;在表1-25中, 丙烯纯度要大于98%。而用于次氯酸化法生产 环氧乙烷、环氧丙烷,则要求纯度较低的乙烯、 丙稀。
将富集于C2馏分中,甲基乙炔和丙二烯(简称 MAPD)将富集于C6馏分。 危害:
炔烃影响乙烯和丙烯衍生物生产过
程。
影响催化剂寿命;恶化产品质量
形成不安全因素;产生不希望的副产品
脱炔要求:炔<5×10-6,丙二烯< 5×10-5 脱炔方法:溶剂吸收法和催化加氢法 溶剂吸收法 • 吸收裂解气中的乙炔,同时回收一定量的 乙炔 • 常用的溶剂 二甲基甲酰胺(DMF) N-甲基吡咯烷酮(NMP) 丙酮
Na2CO3+H2O Na2S+2H2O
碱洗工艺流程说明
塔分三段: I段水洗塔为泡罩塔板 Ⅱ段和Ⅲ段为碱洗段填料层 碱液浓度由上而下降低: 新鲜碱液含量为18%~20%, Ⅱ段循环碱液NaOH含量约为5%~7% Ⅲ段循环碱液NaOH含量为2%~3%
碱洗工艺流程图
, 加 热 碱 器 液 ; 循 环 碱 泵 洗 ; 塔 ; 水 洗 循 环 泵 4523 1-
第四节
精馏分离
裂解气的精馏分离
精馏分离是深冷分离工艺的主体,其 目的是:把C1~C5的馏分逐一分开,对产品乙 烯、丙烯进行提纯精制。 精馏分离装置: 脱甲烷、 脱乙烷 、脱丙烷、脱 丁烷和乙烯丙烯产品塔
精馏分离方案
脱甲烷→脱乙烷→脱丙烷 脱乙烷→脱甲烷→脱丙烷
顺序分离流程 前脱乙烷流程
脱丙烷→脱甲烷→脱乙烷
甲烷化工序43100#操作规程

徐州东兴能源有限公司40000Nm3/h焦炉煤气制LNG装置焦炉煤气甲烷化工序工艺技术操作规程(43100#)文件编号:DXJC-2015-07编写:李世田审核:刘力东兴LNG技术组2015年11月目录一、任务二、原理三、工艺流程说明1、气体流程2、汽包给水流程3、气体排污和蒸汽闪蒸流程四、开车前的准备1、开车前的检查和准备2、烘炉3、煮炉4、甲烷化催化剂的装填1、开车前的确认2、氮气置换和氮气循环管线3、甲烷化催化剂的升温和蒸汽发生系统的开车4、甲烷化反应器的投料5、甲烷化系统的提量和提压注意事项6、再开车六、正常操作控制指标1、正常控制指标2、正常维护及注意事项1、计划停车2、紧急停车八、不正常情况及处理1、停电及其处理2、停仪表空气及其处理3、脱盐水中断及其处理4、冷却水中断及处理5、甲烷化反应器超温及处理6、自动调节器故障及处理7、调节阀堵塞及其处理8、报警及处理九、主要设备规格及参数十、岗位职责十一、巡回检查制度十二、交接班制度十三、安全注意事项经深度净化的焦炉气组成为:H2含量~57%、CH4含量~20.8%,CO+CO2含量12.6%,N2含量~5.6%,CnHm含量~1.87%。
焦炉气中其它的有害杂质在上游工序已经除去。
在甲烷化工序,CO、CO2与H2在催化剂的作用下反应生成CH4。
这一方面增加了CH4的产量,同时可脱去焦炉气中的CO和CO2降低后续工序的分离难度,同时回收热量副产蒸汽自用和外供。
二、工艺原理甲烷化工艺的原理是CO、CO2和H2在适当的温度、压力条件下及催化剂存在时发生甲烷化反应,其化学反应式见反应(1)和反应(2)。
CO+3H2→CH4+H2O(g) △H0=-206.2kJ/mol(1)CO2+4H→+CH4+2H2O(g) △H0298k=-165.0kJ/mol 通常情况下反应(1)比反应(2)的反应速度要快,放出的热量也更多。
反应体系中同时有变换反应存在。
煤制天然气-甲烷化_图文
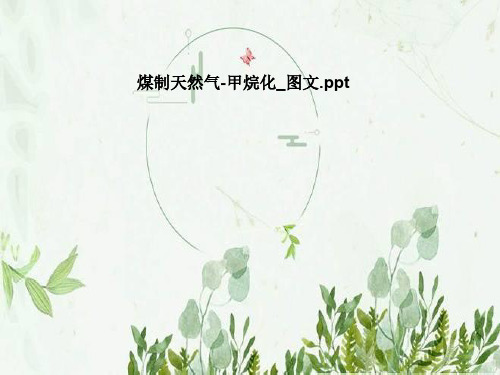
排污去闪蒸
第二甲烷化反应器 第一甲烷化反应器 第二脱硫塔 第一脱硫塔
SYNGAS
甲烷化流程
460
SUP. HEAT MP STEAM
88.27% 240 270
第五甲烷化反应器
255 136 220 26.5%
262 汽包
27.9%
41.82%
300
300
37 134
278 675 40.1%
13
甲烷化技术状况
Davy甲烷化工艺技术的特点如下:
CRG-LH催化剂已经经过工业化验证,拥有美国大平原等多项业绩。 CRG-LH催化剂具有变换功能,合成气不需要调节H/C比,转化率高。 CRG-LH催化剂使用温度范围很宽,在230~700℃温度范围内都具有很
高且稳定的活性。 可以产出高压过热蒸气(8.6~12.0MPa,535℃),用于驱动大型压缩
煤浆 型煤
炭材料
煤填充高分子 复合材料
DME 城市煤气
合成氨 尿素
二甲醚
3
煤化工——发展方向
4
煤化工——清洁能源
5
二. 甲烷化工艺
甲烷化催化剂和工艺起源于1902,初期用于脱除合成气中残留的少量碳 氧化合物(CO和CO2),用于制氢工艺——合成氨;
煤气(高CO含量)甲烷化开始于40年代,真正发展于70年代(石油危 机);
MCR-2X催化剂在高压情况下可以避免羰基形成,保持高活性 、寿命长。
可以产出高压过热蒸汽(8.6~12.0MPa,535℃),用于驱动 大型压缩机,每千Nm3天然气副产3.5吨高压过热蒸汽,能量 利用效率高。
11
甲烷化技术状况
冷却水消耗量较低(每生产1Nm3产品气,冷却水消耗低于 1.8kg);
49张化工装置流程图,超详细!

49张化工装置流程图,超详细!导读:化工厂里的装置多种多样,而很多装置作为化工人必须要熟悉,那么今天小编为大家介绍各种化工装置的流程图,不仅能帮助大家熟悉各种装置的生产流程还能了解部分生产工艺。
◆ ◆ ◆常减压电脱盐装置原则流程从油田送往炼油厂的原油往往含盐(主要是氧化物)带水(溶于油或呈乳化状态),可导致设备的腐蚀,在设备内壁结垢和影响成品油的组成,需在加工前脱除。
电脱盐基本原理:为了脱掉原油中的盐份,要注入一定数量的新鲜水,使原油中的盐充分溶解于水中,形成石油与水的乳化液。
在强弱电场与破乳剂的作用下,破坏了乳化液的保护膜,使水滴由小变大,不断聚合形成较大的水滴,借助于重力与电场的作用沉降下来与油分离,因为盐溶于水,所以脱水的过程也就是脱盐的过程。
+◆ ◆ ◆CDU装置原则流程CDU装置即常压蒸馏部分常压蒸馏原理:精馏又称分馏,它是在精馏塔内同时进行的液体多次部分汽化和汽体多次部分冷凝的过程。
原油之所以能够利用分馏的方法进行分离,其根本原因在于原油内部的各组分的沸点不同。
在原油加工过程中,把原油加热到360~370℃左右进入常压分馏塔,在汽化段进行部分汽化,其中汽油、煤油、轻柴油、重柴油这些较低沸点的馏分优先汽化成为气体,而蜡油、渣油仍为液体。
+◆ ◆ ◆VDU装置原则流程VDU装置即减压蒸馏部分减压蒸馏原理:液体沸腾必要条件是蒸汽压必须等于外界压力。
降低外界压力就等效于降低液体的沸点。
压力愈小,沸点降的愈低。
如果蒸馏过程的压力低于大气压以下进行,这种过程称为减压蒸馏。
+◆ ◆ ◆轻烃回收装置原则流程轻烃回收装置是轻烃的回收设备,采用成熟、可靠的工艺技术,将天然气中比甲烷或乙烷更重的组分以液态形式回收。
+◆ ◆ ◆RDS装置流程图RDS即渣油加氢装置,渣油加氢技术包含固定床渣油加氢处理、切换床渣油加氢处理、移动床渣油加氢处理、沸腾床渣油加氢处理、沸腾床渣油加氢裂化、悬浮床渣油加氢裂化、渣油加氢一体化技术及相应的组合工艺技术。
甲烷化设备结构(1)

绝对优势。
工艺凝液汽提塔:
• 作用:将工艺凝液中的不凝气体分离 • 原理: 气提是一个物理过程,它采用
一个气体介质破坏原气液两相平衡而建 立一种新的气液平衡状态,使溶液中的 某一组分由于分压降低而解吸出来,从 而达到分离物质的目的。
工艺凝液汽提塔:
• 例如,A为液体,B为气体,B溶于A中达到气 液平衡,气相中以B气相为主,加入气相汽提 介质C时,气相中A、B的分均降低从而破坏了 气液平衡,A、B物质均向气相扩散,但因气相 中以B为主,趋于建立一种新的平衡关系,故 大量B介质向气相中扩散,从而达到气液相分 离目的。通过控制气提介质的量可以控制气提 程度。
• 保温材料:硅酸铝。
脱硫槽的作用:
• 脱硫槽(181V102)将原料气初步分离加热后, 注入少量锅炉给水(约0.1mol%)来帮助脱硫, 该分离罐可以防止液体夹带进入净化催化剂中。 合成气加热后,被送到脱硫罐中,脱硫罐能够 在上游系统硫泄漏时起到保护作用,否则其将 成为CRG催化剂的毒物。
• 脱硫脱槽硫(1槽81的V结10构2原)从理结: 构原理上讲,与辅助 反• 应器相脱似硫。槽是进行原料气脱硫反应的容器,
在最上部装有150mm厚直径50mm的一层耐火
球。上部瓷球的作用,有气体分布器的作用,
也有吸收杂质如水份、同样有气体分布器的作
用。
主反应器的结构:
主反应器出口收集器
辅助反应器的作用:
• 辅助反应器是将主反应器反应过后经废锅
余热回收中间换热器逐步换热达到温度压力 要求(1号辅助反应器280℃、2.78MPa,2号 辅助反应器250℃、2.54MPa)的工艺气再次 串联反应以产出合格的产品气。
• 1、合成单元: • (1)、反应器类:主反应器(181R101、181R102)、
煤制天然气工艺简介(最新终极版)

一期气 化35KV 变电所 25000K VA×2
一期净 化35KV 变电所 40000K VA×2
一期空 分35KV 变电所 25000K VA×2
一期厂 用35KV 变电所 50000K VA×2
一期 35KV 备用 ×2
2号发 电机 15000 KW
全厂工艺流程简述
• 煤制天然气全套生产装置主要包括:备煤、水处理、空分、 热电、气化、煤气水分离、酚氨回收、变换和煤气冷却、低 温甲醇洗、混合制冷、硫回收、甲烷合成、天然气压缩和干 燥脱水、罐区等生产装置。其中备煤、水处理、空分、热电 为辅助生产装置,而气化、煤气水分离、酚氨回收、变换和 煤气冷却、低温甲醇洗、混合制冷、硫回收、甲烷合成、天 然气压缩和干燥脱水为化工主生产装置。 • 辅助生产装置中,备煤主要是通过破碎、筛分(弛张筛)等 生产过程为气化炉提供6~50mm的原料煤;空分采用内压 缩流程生产技术,为化工装置提供氮气和氧气;热电装置采 用循环流化床锅炉(一期)和汽轮发电机组为全厂提供蒸汽 和电能;水处理包括原水处理、脱盐水、循环水、污水处理 等生产装置,为全厂提供新鲜水、脱盐水、循环水以及对全 厂的污水进行生化处理。
• 打开灰锁泄压阀,将灰锁压力泄至常压后关闭灰 锁泄压阀,打开灰锁下锥阀将灰排出。 • 关闭灰锁下锥阀,再打开灰锁充压阀用中压蒸汽 充压,如此循环往复上述的排灰过程。
• (三)变换冷却
• 变换冷却装置为两系列,单系列变换包括1台 洗涤塔、2台预变换炉、1台主变换炉等设备。 • 其工艺原理是通过钴钼催化剂使一氧化碳与水 蒸气反应生成二氧化碳和氢气,从而降低一氧 化碳含量和提高氢气含量(即调整氢碳比), 目的是使煤气组分符合甲烷合成的要求。
•
因低温甲醇洗使用的是低温甲醇,所以必须由外部装置提供冷量。 混合制冷装置的作用就是为低温甲醇洗提供冷量;其工艺流程就是 利用蒸气透平离心式压缩机将来自低温甲醇洗的氨气压缩后进入吸 收器用贫氨水吸收后变为浓氨水,之后再进入精馏塔进行精馏,得 到的纯氨气经冷却后变为液氨,然后将液氨送到低温甲醇洗作为制 冷剂。液氨经蒸发制冷后变为氨气再重新回到压缩机进行压缩,如 此往复循环使用。
甲烷化装置工艺技术讲解
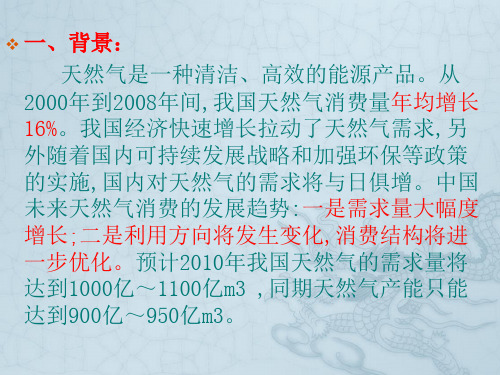
❖ (三)托普索甲烷化合成技术特点 ❖ 丹麦托普索公司也从事甲烷合成技术研究与开发。其开 ❖ 发的MCR-2X催化剂在托普索中试装置和德国的中试装 ❖ 置中,均进行了独立测试。在中试时,同一批催化剂在装 ❖ 置上的最长运行时间达到10000h,说明MCR-2X是一种 ❖ 具有长期使用且能稳定运行的催化剂。MCR-2X催化剂 ❖ 累计运行记录超过45000h。 ❖ 其MCR-2X甲烷化催化剂在200~700℃之间都具有很高 ❖ 的活性。在TREMPTM工艺中,反应是在绝热条件下进行的。 ❖ 反应产生的热量导致了很高的温升,通过循环来控制第 ❖ 一甲烷化反应器的温度。
❖ 七、甲烷化工艺技术选择及特点 ❖ (一)目前甲烷化工艺技术主要有: ❖ 1、英国戴维(DAVY)公司甲烷化技术(CRG) ❖ 2、丹麦托普索公司的甲烷化技术 ❖ 3、德国鲁奇(Lugri)的甲烷化技术。
❖ (二)英国戴维技术特点
❖ Davy甲烷化工艺中,采用CRG高镍型催化剂。 ❖ 其中镍含量约为50%。该催化剂的起活温度为 ❖ 250℃,最佳活性温度在300~600℃,失活温度大 ❖ 于700℃。在使用前须用H2进行还原,若温度低于 ❖ 200℃,催化剂会与原料气中的CO等生成羰基镍, ❖ 但是正常运行时系统温度在250℃以上.因此在开、 ❖ 停车时,一般须用蒸汽将催化剂床层温度加热或 ❖ 冷却到200℃以上,然后用氮气作为冷媒或热媒介 ❖ 质置换,避免Ni(CO)致天然气 汽车功率小, 不适合大功率汽车使用。其次, 由于天然气压缩困难, 生产、储运费用 高,天然气站的建设也需要较高的投 资。第三,目前尚无完善的天然气汽车供气网络, 天 然气汽车只适合在城市使用。第四,天然气钢瓶重达 400Kg 是汽车载荷的 10%左 右。综合以上优缺点,可 以看出在石油资源相对短缺而天然气资源相对较多的今 天,发 展天然气汽车势在必行,但需要较大的投资、 且需各地共同建设,才能建成完善的天然 气汽车供气 网络。目前一辆天然气汽车的改装费用在 7000-11000 元人民币,单是节约 燃料一项,即可在一年内收回成 本(对公交汽车而言)。综合对比其优缺点来看,在石 油资源短缺的今天,发展车用天然气势在必行。
第1章 裂解气分离

C2馏分后加氢工艺
脱乙烷塔顶 回流罐C2气
预热、注氢 一段加氢
反应气
冷却 二段加氢
反应气
冷却 C2吸收绿油
C2馏分 干燥
乙烯精馏
乙烯
后加氢工艺流程
加氢脱炔催化剂
钯系: ①温度较低 ②乙烯损失低(0· 2%~ 0· ) 5% 后 加 氢 前 加 氢
③残余乙炔低(5×10-6)
非钯系:①进料杂质含量限制不严; ②温度较高;
生产实际
一般设置两台干燥器,轮流进行干燥和再生
尝试画出流程: 提示:
两个干燥剂罐并联串联? 控制阀如何设置? 再生时如何实现温升 如何实现再生后的重新使用?
典型的两个吸附器 轮流操作的流程图
炔烃脱除
来源 裂解过程中生成 乙炔集于C2馏分 甲基乙炔和丙二 烯富集于C3馏分
危害
对产品再加工不利, 影响催化剂寿命, 恶化产品质量,形 成不安全因素,产 生副产品
前加氢与后加氢比较
前加氢
流程简化,节省投资
后加氢
工艺流程或控制复杂。 需设第二脱甲烷塔或侧 线采出塔 氢气定量供给,加氢选 择性好,温度较易控制, 不易发生飞温问题 加氢原料气中杂质少, 催化剂使用周期长,产 品纯度也高。
操作稳定性差。
氢气自给,过量,副
反应剧烈,选择性差, 造成乙烯和丙烯损失, 严重时还会导致反应温 度失控,床层飞温,威 胁生产安全。
甲烷化法:催化剂存 在的条件下,使裂解 气中的一氧化碳催化 加氢生成甲烷和水, 达到脱除CO的目的
CO脱除的方法
CO H 2 CH 4 H 2O
裂解气的深冷分离系统
脱甲烷塔 丙烯精馏
分离流程
冷箱和脱甲烷塔流程模板(打印)

脱甲烷塔的控制
必须在此强调的是,利用复杂精馏塔来提高塔 内分离过程的热力学效率,不是靠降低塔的总热负 荷,而是借助所用冷量和热量温度等级不同而实现 的。 从提高塔的热力学效率来看,带有塔侧换热器 的复杂精馏更适合于塔顶,塔底温差较大的分馏塔。 由于这时冷量或热量的温度等级差别较大,故设置 塔侧冷凝器和塔侧重沸器的效果更好。因此,凝液 分馏系统中的脱甲烷塔多采用之(塔侧重沸器1—2 台)。
脱甲烷塔的控制
通常,脱甲烷塔压力为0.7~3.2MPa。当脱甲烷塔运行 压力高于3.0MPa时,称之为高压脱甲烷塔,当脱甲烷塔运 行压力低于0.8MPa时,称之为低压脱甲烷塔,脱甲烷塔运 行压力介于高压和低压之间时,称之为中压脱甲烷塔。 对于回收乙烷的装置,脱乙烷塔及其后各塔的运行压力 应根据塔顶产品的要求,状态(气相或液相)及塔顶冷凝器 或分凝器冷却介质的温度来确定。对于脱丙烷塔,脱丁烷塔 (或脱丙,丁烷塔),塔顶温度宜比冷却介质温度高于 10~20℃,产品的冷凝温度最高不应超过50℃。
冷箱和脱甲烷塔
2作为本厂深冷核心 冷箱是一组高效、绝热保冷的低温换热设备。在 E1 的2-E1冷箱在天然 深冷分离过程中经常采用,如在天然气深加工的 气NGL回收系统中 2深冷分离过程中就采用在 -100℃左右工作的冷 E2 2起着至关重要的作 箱 。它由结构紧凑的高效板式换热器和气液分 E3 用,是天然气深冷 离器所组成。因为低温极易散冷,要求极其严密 装置的主冷箱,为 的绝热保冷,故用绝热材料把换热器和分离器均 各个物流的换热提 包装在一个箱形物内,称之为冷箱。 供了场所。
脱甲烷塔的控制
深冷操作
思考题: 1、制冷压缩机为什么要分段、分级压缩? 2、透平膨胀机的基本组成以及其工作原理是什么? 3、冷箱通常是板翅式换热器,何谓冷箱?其优缺点是什么? 4、脱甲烷塔是带有中间侧沸器的复杂精馏塔,其中间侧沸器的作 用是什么?
ProII案例-脱甲烷塔及冷箱系统流程模拟
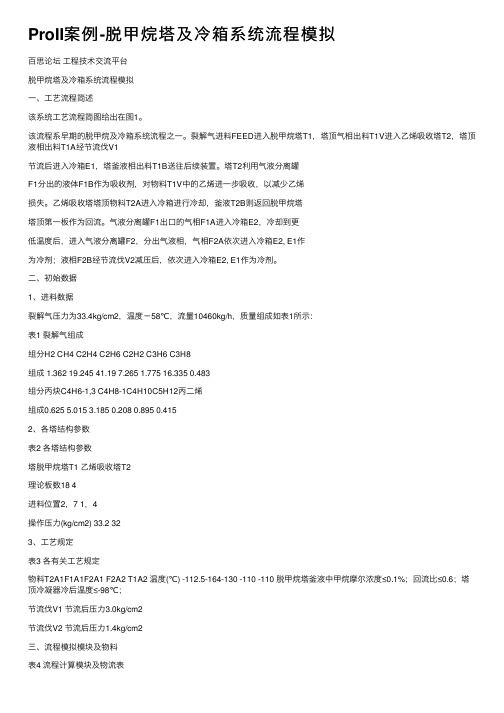
ProII案例-脱甲烷塔及冷箱系统流程模拟百思论坛⼯程技术交流平台脱甲烷塔及冷箱系统流程模拟⼀、⼯艺流程简述该系统⼯艺流程简图给出在图1。
该流程系早期的脱甲烷及冷箱系统流程之⼀。
裂解⽓进料FEED进⼊脱甲烷塔T1,塔顶⽓相出料T1V进⼊⼄烯吸收塔T2,塔顶液相出料T1A经节流伐V1节流后进⼊冷箱E1,塔釜液相出料T1B送往后续装置。
塔T2利⽤⽓液分离罐F1分出的液体F1B作为吸收剂,对物料T1V中的⼄烯进⼀步吸收,以减少⼄烯损失。
⼄烯吸收塔塔顶物料T2A进⼊冷箱进⾏冷却,釜液T2B则返回脱甲烷塔塔顶第⼀板作为回流。
⽓液分离罐F1出⼝的⽓相F1A进⼊冷箱E2,冷却到更低温度后,进⼊⽓液分离罐F2,分出⽓液相,⽓相F2A依次进⼊冷箱E2, E1作为冷剂;液相F2B经节流伐V2减压后,依次进⼊冷箱E2, E1作为冷剂。
⼆、初始数据1、进料数据裂解⽓压⼒为33.4kg/cm2,温度-58℃,流量10460kg/h,质量组成如表1所⽰:表1 裂解⽓组成组分H2 CH4 C2H4 C2H6 C2H2 C3H6 C3H8组成 1.362 19.245 41.19 7.265 1.775 16.335 0.483组分丙炔C4H6-1,3 C4H8-1C4H10C5H12丙⼆烯组成0.625 5.015 3.185 0.208 0.895 0.4152、各塔结构参数表2 各塔结构参数塔脱甲烷塔T1 ⼄烯吸收塔T2理论板数18 4进料位置2,7 1,4操作压⼒(kg/cm2) 33.2 323、⼯艺规定表3 各有关⼯艺规定物料T2A1F1A1F2A1 F2A2 T1A2 温度(℃) -112.5-164-130 -110 -110 脱甲烷塔釜液中甲烷摩尔浓度≤0.1%;回流⽐≤0.6;塔顶冷凝器冷后温度≤-98℃;节流伐V1 节流后压⼒3.0kg/cm2节流伐V2 节流后压⼒1.4kg/cm2三、流程模拟模块及物料表4 流程计算模块及物流表模块名称流程图代号⼊⼝物流号出⼝物流号脱甲烷塔 T1 FEED,T2B T1V,T1A,T1B⼄烯吸收塔 T2 T1V,F1B T2A,T2B 冷箱1 E1 T2A,F2A1,F2B2,T1V1 T2A1,F1A2,F2B3,T1V2冷箱2 E2 F1A,F2A,F2B1 F1A1,F2A1,F2B2 ⽓液分离罐 F1 T1A1 F1A,F1B⽓液分离罐 F2 F1A1 F2A,F2B 节流伐 V1 T1V T1V1节流伐 V2 F2B F2B1四、主要计算结果主要计算结果给出在表5。