油井钢管内部防腐蚀内衬系统资料
钢质管道内壁腐蚀与防腐层

管道内壁腐蚀与介质的化学性质、温度、压力、流速有关,介质中所含的酸、碱、盐和其它化学物质与管道内壁发生化学和电化学反应,直接腐蚀管道。
化工厂、炼油厂、油田污水中所含的油和溶剂会使内涂层溶胀、溶解,使其降低防腐性能。
介质的流速和固体颗粒的磨损会加速涂层的破坏,介质温度升高会增加介质的腐蚀性,而且使内涂层变软,降低机械强度,失去粘结力,降低电性能,加速涂层老化。
所以要根据介质的上述性质、状态,设计选择涂层的材料、涂层结构和涂层厚度。
为了更合理更经济的选择涂层,输水管道应分为输送常温普通水和输送油田、炼厂的含油、含化学添加剂、含酸碱盐而且带有一定温度的工业污水两类,对后者的防腐层需要提高等级并有某些特殊要求。
1.1常温普通水管道内防腐层本节钢质输水管道输送的是饮用水、江河水、海水、湖水和生活污水,温度为常温,流速处于层流速状态。
1.1.2 内腐蚀等级根据上述输送介质的化学性质和物理状态,内腐蚀等级可分为弱腐蚀、中等腐蚀和强腐蚀三个等级,见表4-1。
表 4-1 腐蚀环境和防腐层等级1.1.3 内防腐层要求管道内防腐层有两个功能,一是防腐,二是减阻。
管道内防腐层的要求与外防腐层基本相同,见本书第三章3.1.3节,包括:电性能、机械性能、稳定性、抗微生物破坏性能、施工工艺性能、经济指标和低碳、节能环保要求。
因管内有流动的液体,液体中含固体颗粒,管内衬层要抵抗固体颗粒的磨蚀,要有一定的耐磨性能,其测试方法包括国标GB/T 1768-1979《漆膜耐磨性测定法.》和国际标准ASTM D969-93《路标漆渗色程度的实验室试验方法》。
内衬层要有减阻作用,随着表面粗糙度的降低,摩擦系数也相应地减小,摩擦系数降低的比率随着雷诺数的增加及管径的减小而增加。
管径对减小摩擦系数的影响,随着雷诺数的增高而有所减少。
当雷诺数在105~107时,摩擦系数的变化最大。
内表面粗糙度为4.5μm的工业管道内涂后可提高液态介质输送能力22%,输气管道则是24%,在相同输量下液体压降低将减少33%,或者可缩小管径8%。
钢管内阴极保护防腐蚀-汇龙

河南汇龙合金材料有限公司刘珍
钢管内阴极保护防腐蚀
河南汇龙合金材料有限公司为大家讲解阴极保护是采油生
产中的一项有效而又经济的腐蚀控制方法。
对埋地管道而言,铺设前已有涂层,但涂层会留下漏涂点,施工时也会产生裸露部位,而且约占5%。
需采用阴极保护,否则将造成集中腐蚀而穿孔。
采用内涂层或衬里是管道内防腐有效途径之一,但表面处理难度大,常出现不平滑不均匀针孔、漏点。
同时涂层与金属弹性模量不一致,会导致涂层损害,产生裂纹、降低寿命。
漏点造成的集中点蚀比裸管面腐蚀更严重。
将阴极保护与内涂层保护结合起来使用,是比较完善的防腐方法。
加牺牲阳极使钢铁成为阴极,其表面呈碱性、抑制了腐蚀,同时可使钢管内表面形成致密垢层,也起到保护作用。
腐蚀挂片测试结果表明加牺牲阳极的保护度可达98%左右。
河南汇龙合金材料有限公司刘珍。
管道防腐蚀衬里安全技术

管道防腐蚀衬里安全技术背景随着社会的发展和技术的进步,现代工业中使用大量的管道进行输送、处理等工作。
而这些管道长期接触液体、气体等介质,容易出现腐蚀现象。
腐蚀一旦发生,除了影响管道的正常运行,还有可能引起安全事故。
因此,管道防腐蚀成为了工业生产中必须重视和解决的问题。
其中,管道防腐蚀衬里技术被广泛应用。
定义管道防腐蚀衬里技术是指,通过在管道内部添加一层防腐蚀材料,起到保护管道、延长使用寿命、防止腐蚀的作用的一种技术。
衬里材料的选择管道防腐蚀衬里材料的选择应根据输送介质的性质、工作温度、工作压力等多种因素综合考虑。
常用的衬里材料有:PTFE、FEP、PFA、ETFE、PVDF、PE、PP、PVC等。
其中,PTFE是一种耐腐蚀性能优异、适用于高温、高压的衬里材料;PVDF的耐腐蚀性能也很好,适用于化学品输送;PE、PP、PVC等是比较常用的工业塑料,适用于一些输送介质性质不太复杂的情况。
管道衬里主要分为手工涂装和自动喷涂两种工艺。
手工涂装是指,将衬里材料通过涂刷或滚涂等方式,手工均匀地涂敷到管道内壁上。
自动喷涂则是利用特殊的设备,将衬里材料喷洒在管道内壁上,形成匀称的衬里层。
无论选择何种工艺,都需要保证衬里层的均匀性和质量,避免出现缺陷。
衬里材料的质量控制为保证衬里层的品质,需要对衬里材料进行质量控制。
首先,应选择具有生产许可证或注册证书的衬里厂家供应衬里材料。
其次,应对衬里材料进行严格的质量检测,包括外观、试验数据等项目。
在生产过程中,还需要对每批次的衬里材料进行货物接收、质量检验、产品标识等工作,确保管道防腐蚀衬里技术的质量。
应用范围管道防腐蚀衬里技术适用于输送酸、碱、盐、油、气等多种介质的管道。
其应用范围包括:化工、石化、能源、纺织、医药等行业。
使用管道防腐蚀衬里技术可以有效预防管道的腐蚀问题,保障管道的正常使用安全。
但是,在使用管道防腐蚀衬里技术时,也需要注意一些安全问题。
例如,应注意选用适合输送介质的衬里材料,避免在输送过程中出现安全隐患;应定期检查管道的衬里层是否出现磨损、坑洼等现象,及时进行维修。
油管内衬的作用是什么意思

油管内衬的作用是什么意思
油管内衬是一种用于管道内部的保护材料,通常由特殊的聚合物材料制成,其
作用是防止管道内部受到腐蚀、磨损和化学侵蚀的影响。
在石油、天然气和化工等行业中,油管内衬起着非常重要的作用,能够延长管道的使用寿命,减少维护成本,保障管道的安全运行。
首先,油管内衬能够有效地防止管道内部的腐蚀。
在石油和化工行业中,管道
内部常常接触到腐蚀性物质,比如酸、碱、盐等,长期的腐蚀会导致管道壁厚度减少,甚至出现孔洞,从而影响管道的正常运行。
而油管内衬能够形成一层保护膜,隔绝管道壁与腐蚀性物质的直接接触,从而延长了管道的使用寿命。
其次,油管内衬还能够减少管道内部的磨损。
在输送高速流体或颗粒物料的管
道中,管道内壁会受到流体的冲击和颗粒物料的磨损,长期使用会导致管道内壁的磨损严重,甚至出现磨损孔洞。
而油管内衬的硬度和耐磨性能能够有效地减少管道内壁的磨损,保护管道的完整性,延长了管道的使用寿命。
此外,油管内衬还能够抵抗化学侵蚀。
在化工行业中,管道内部经常接触到各
种化学物质,这些化学物质可能对管道材料产生腐蚀和侵蚀,从而影响管道的使用寿命和安全性。
油管内衬能够有效地抵抗化学物质的侵蚀,保护管道的完整性和安全性。
总的来说,油管内衬在石油、天然气和化工等行业中起着非常重要的作用,能
够有效地保护管道内部,延长管道的使用寿命,减少维护成本,保障管道的安全运行。
随着技术的不断发展,油管内衬的性能和使用范围也在不断提升,相信在未来会有更多的创新和应用。
油气集输管线内防腐技术

油气集输管线内防腐技术在油气开采及集输过程中,由于含有大量H2S、CO2、凝析油和地层水等介质,对油气井套管、钻采设备、井下工具、集输管线等造成了严重的腐蚀,从而造成套管穿孔、钻采设备失灵、管线开裂等事故,甚至危及人们的生命和财产安全。
因此,硫化氢、二氧化碳和高矿化度采出水对油气田集输系统的管线及设备产生的腐蚀问题,成为当今研究的热门课题。
而各油气田的腐蚀环境不同,甚至同一油田不同井次的管线和设备也各异,腐蚀的主要因素、腐蚀机理、腐蚀形态、腐蚀程度等就变得复杂多样,不可能找到一种对所有油气田都适用的有效防腐措施。
因此,针对具体的油气田腐蚀问题,需要根据具体的腐蚀环境开展相对应的防腐研究。
一、油气集输管道内腐蚀管道内腐蚀受到管材质量、输送介质以及管道防腐水平的影响,油气集输管道内壁腐蚀主要包括以下3种:(1)H2S腐蚀:H2S离解出HS-、S2-吸附在金属表面,形成加速的吸附复合物离子Fe(HS-)。
吸附的HS-、S2-使金属的点位移向负值,促进阴极放氢的加速,而氢原子为强去极化剂,易在阴极获得电子,同时使铁原子间金属键的强度大大削弱,进一步促进阳极溶解反应而使钢铁腐蚀。
(2)CO2腐蚀:CO2与水接触形成碳酸,碳酸电离出氢离子,电离的氢离子直接还原析出氢,同时金属表面的HCO3-离子浓度极低时,H2O被还原析出氢。
(3)多相流腐蚀:按其腐蚀环境可分为清洁环境的腐蚀、冲刷环境的腐蚀、腐蚀性环境的腐蚀,以及冲蚀和腐蚀同时存在的环境腐蚀。
按腐蚀发生类型,管道内发生的腐蚀主要有以下4种:(1)均匀腐蚀:由于输送介质中含有采出水/水汽,在一定条件下与CO2、H2S等酸性气体结合对管道造成腐蚀。
(2)坑蚀:管壁涂层或保护膜不均匀、硫及硫化物的沉淀、腐蚀产物膜出现结晶剥裂等产生坑蚀。
(3)硫化物应力腐蚀开裂:硫化氢水解后吸附在钢表面的HS-会加速阴极放氢,从而导致材料韧性下降,脆性增加。
(4)冲刷腐蚀:管道表面腐蚀产物直接被输送介质带走,新的金属不断裸露,从而加速了腐蚀。
油管内衬的作用有哪些方面

油管内衬的作用有哪些方面油管内衬是一种用于保护油管内部的材料,通常由聚合物或金属制成。
它的作用十分重要,可以在很大程度上影响油管的使用寿命和安全性。
以下将从防腐蚀、减少摩擦、增加流体稳定性、防止泄漏和减少维护成本等方面来探讨油管内衬的作用。
防腐蚀。
油管内衬的主要作用之一就是防腐蚀。
在油气开采过程中,油管内部会受到酸性物质和盐水的侵蚀,导致腐蚀。
而油管内衬可以形成一层保护膜,隔离金属材料与介质的直接接触,从而减少了腐蚀的发生。
这不仅延长了油管的使用寿命,也提高了油管的安全性。
减少摩擦。
油管内衬还可以减少油管内部的摩擦。
在油气输送过程中,流体的流动会产生摩擦力,而油管内衬可以减少流体与油管内壁的直接接触,从而减少了摩擦力的产生。
这不仅有助于降低油管的能耗,也减少了油管内部的磨损,延长了油管的使用寿命。
增加流体稳定性。
油管内衬还可以增加流体的稳定性。
在油气开采过程中,流体的稳定性对于输送效率和安全性至关重要。
油管内衬可以减少流体与油管内壁的摩擦,减少了流体的湍流现象,从而提高了流体的稳定性,减少了流体的波动,保证了油气的稳定输送。
防止泄漏。
油管内衬还可以有效地防止泄漏。
在油气开采过程中,泄漏是一个非常严重的问题,不仅会造成资源的浪费,还会对环境造成严重的污染。
而油管内衬可以形成一层保护膜,防止流体直接与油管内壁的接触,从而有效地减少了泄漏的发生,保护了环境和资源。
减少维护成本。
油管内衬还可以减少油管的维护成本。
由于油管内衬的作用,油管的使用寿命得到了延长,维护周期也相应延长,从而减少了维护的频率和成本。
这对于油气开采企业来说是非常有利的,不仅降低了成本,也提高了生产效率。
总结。
油管内衬在油气开采过程中起着非常重要的作用,它不仅可以保护油管的内部,延长油管的使用寿命,还可以提高油管的安全性和稳定性。
因此,在选择油管内衬的材料和安装方式时,需要根据具体的使用环境和要求来进行选择,以确保其能够发挥最佳的作用。
油气集输管道内腐蚀及内防腐分析
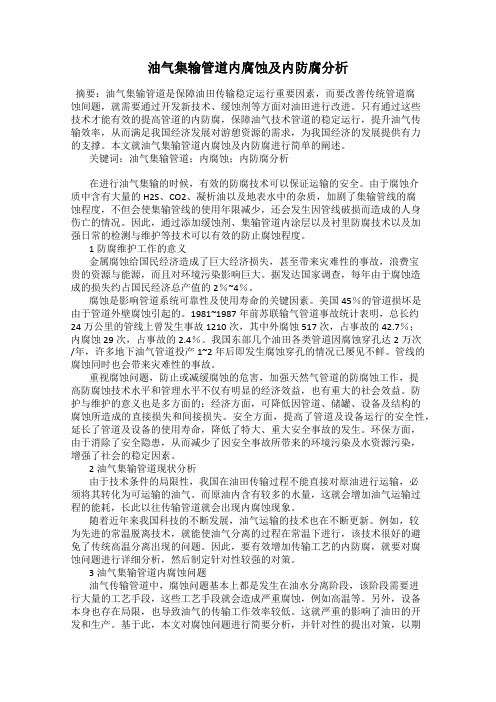
油气集输管道内腐蚀及内防腐分析摘要:油气集输管道是保障油田传输稳定运行重要因素,而要改善传统管道腐蚀间题,就需要通过开发新技术、缓蚀剂等方面对油田进行改进。
只有通过这些技术才能有效的提高管道的内防腐,保障油气技术管道的稳定运行,提升油气传输效率,从而满足我国经济发展对游憩资源的需求,为我国经济的发展提供有力的支撑。
本文就油气集输管道内腐蚀及内防腐进行简单的阐述。
关键词:油气集输管道;内腐蚀;内防腐分析在进行油气集输的时候,有效的防腐技术可以保证运输的安全。
由于腐蚀介质中含有大量的H2S、CO2、凝析油以及地表水中的杂质,加剧了集输管线的腐蚀程度,不但会使集输管线的使用年限减少,还会发生因管线破损而造成的人身伤亡的情况。
因此,通过添加缓蚀剂、集输管道内涂层以及衬里防腐技术以及加强日常的检测与维护等技术可以有效的防止腐蚀程度。
1防腐维护工作的意义金属腐蚀给国民经济造成了巨大经济损失,甚至带来灾难性的事故,浪费宝贵的资源与能源,而且对环境污染影响巨大。
据发达国家调查,每年由于腐蚀造成的损失约占国民经济总产值的2%~4%。
腐蚀是影响管道系统可靠性及使用寿命的关键因素。
美国45%的管道损坏是由于管道外壁腐蚀引起的。
1981~1987年前苏联输气管道事故统计表明,总长约24万公里的管线上曾发生事故1210次,其中外腐蚀517次,占事故的42.7%;内腐蚀29次,占事故的2.4%。
我国东部几个油田各类管道因腐蚀穿孔达2万次/年,许多地下油气管道投产1~2年后即发生腐蚀穿孔的情况已屡见不鲜。
管线的腐蚀同时也会带来灾难性的事故。
重视腐蚀问题,防止或减缓腐蚀的危害,加强天然气管道的防腐蚀工作,提高防腐蚀技术水平和管理水平不仅有明显的经济效益,也有重大的社会效益。
防护与维护的意义也是多方面的:经济方面,可降低因管道、储罐、设备及结构的腐蚀所造成的直接损失和间接损失。
安全方面,提高了管道及设备运行的安全性,延长了管道及设备的使用寿命,降低了特大、重大安全事故的发生。
油井的腐蚀及防护

2e 2+
Fe(OH)2 + 2OH2H
↓
+
↑
在酸性介质中
Fe Fe
2 H2O 2 H2O 2+ 2 OH Fe +2 OHFe + 2+
Fe
2+ 2+ Fe
阳极 反应 阴极 反应
+ e + 22e + 2OH2H+ +2OH 2H +
Fe(OH)2 Fe(OH)2
2H+ + 2e→H2
(4)细菌引起的腐蚀:在油田生产中,对生产带来麻 烦的主要细菌有:脱硫菌、铁细菌、腐生菌,他们使 金属腐蚀的原理是协同作用。
①硫酸盐还原菌在金属腐蚀中的作用原理:
硫酸盐还原菌属于厌氧菌,但在少量氧环境中也能存活。 在高含盐量水(30%)能阻止他的生长。它有极强的 硫酸盐还原作用,因而称为硫酸盐还原菌。 在金属腐蚀中的作用是——阴极去极化作用
II)CO2的分压:在中低温时,pCO2增大,腐蚀速度加 快;在高温时, pCO2增大,腐蚀速度减小。 III)流速的影响:流速增大,去极化速度加快,且阻碍 着保护膜的生成,从而腐蚀加剧,甚至导致严重的局 部腐蚀。 IV)pH值和介质成分的影响:pH值的增大,降低了原 子氢还原反应速度,从而腐蚀速率降低。 钢铁在3%NaC1的盐水溶液中腐蚀最为严重。 Ca2+ 、Mg2+的存在,通过影响钢铁表面腐蚀产 物膜的形成和性质来影响腐蚀特性,具体降低CO2的全 面腐蚀,加剧局部腐蚀;另外,溶解氧的存在也会引 发严重的局部腐蚀。 另外,金属材料本身的组成、处理工艺不同,对 CO2腐蚀的敏感性也有较大的差异(13Cr)
油气集输管道内腐蚀及内防腐技术

油气集输管道内腐蚀及内防腐技术摘要:在石油行业的发展,油气集输管道是非常重要的一部分。
如果油气技术管道内壁发生腐蚀问题,就会对油气传输产生很大影响,所以为了保证油气集输管道稳定运行,需要采取合理的措施对内壁腐蚀进行防护,提升油气集输管道传输效率,促进我国经济的发展。
关键词:油气集输管道;内腐蚀;内防腐技术引言随着社会的不断发展,对于油气资源需求越来越多。
在对油气资源进行传输中,油气集输管道的内腐蚀比较严重,出现了腐蚀穿孔问题,对油气生产企业的经济效益产生了影响,所以必须加强对油气集输管道内腐蚀及内防腐技术研究,促进石油企业的发展。
主要对油气集输管道的内腐蚀分类和油气集输管道内防腐措施进行了阐述。
1油田集输管道腐蚀机理油田集输管道主要是利用金属材料制作,而金属材料在地下深埋的过程中不可避免的会发生化学反应,从而导致金属结构发生变化,从而产生严重腐蚀现象。
在集输管道所有化学反应中电化学腐蚀是最严重的一种,土壤中存在大量的电解质,金属管道在与其接触的过程中会发生电化学反应,从而形成金属离子,导致金属材料发生改变;另外,化学腐蚀也会对金属管道材料形成严重破坏。
众所周知,在土壤环境中水分、无机盐、空气的化学成分含量非常丰富,金属管道在与其接触的过程中会发生化学反应,从而对金属材料结构产生巨大影响,甚至会导致集输管道性能遭到破坏,从而对集输管道整体功能产生严重影响。
2造成油田集输管道腐蚀的原因分析2.1管内腐蚀管内腐蚀是油气管道出现腐蚀的主要原因之一,由于油气管道内部介质为成品油以及天然气,在实际运输过程中,管道内部储存的气体会液体之间产生反应,形成具有腐蚀性的酸性物质,由于管道内部介质时刻处在不断运动过程中,从而使得管道内部酸性物质会源源不断产生,而其对管道内部产生腐蚀是相对均匀的,因此会导致管道内部产生严重的腐蚀现象。
2.2土壤腐蚀随着我国工业技术水平的不断提升,油气集输管道质量也在不断提升,管道实际的使用寿命也得到了有效提升,管道长期深埋地下,会与土壤中的水分、氧气、微生物等长期接触,由此就会形成微电池,从而形成腐蚀性,对油气管道的外壁产生严重的影响。
输油管道及管道内壁防腐保温施工方案
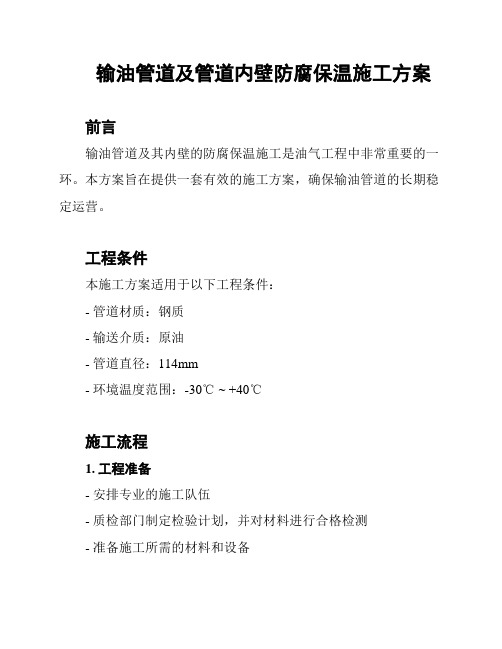
输油管道及管道内壁防腐保温施工方案
前言
输油管道及其内壁的防腐保温施工是油气工程中非常重要的一环。
本方案旨在提供一套有效的施工方案,确保输油管道的长期稳定运营。
工程条件
本施工方案适用于以下工程条件:
- 管道材质:钢质
- 输送介质:原油
- 管道直径:114mm
- 环境温度范围:-30℃ ~ +40℃
施工流程
1. 工程准备
- 安排专业的施工队伍
- 质检部门制定检验计划,并对材料进行合格检测
- 准备施工所需的材料和设备
- 安排施工现场,并确保施工区域内没有任何易燃、易爆等危险物品
2. 表面处理
- 清理管道表面的污物和氧化皮
- 采用砂轮机处理低于Sa2.5级别的区域
- 对表面进行酸洗
3. 防腐涂层施工
- 底漆施工:采用环氧底漆,干燥时间为4小时
- 中间涂层施工:采用耐磨、耐及化学腐蚀的聚氨酯涂料,可采用喷涂或刷涂方式,涂层厚度为0.5mm
- 面漆施工:采用聚尿素涂料,涂层厚度为0.5mm
4. 保温材料施工
- 在完成涂层施工后,开始进行保温材料的施工
- 采用硅酸盐复合材料(灰铸土)、玄武岩压块等薄壁保温材料,保温层厚度为50mm
质量控制
- 施工中进行质量检查,确保施工质量符合要求
- 完成施工后进行整体验收
- 实施质量跟踪和质量记录
安全事项
- 在施工过程中,严格按照操作规程进行
- 施工现场要设置警示标志,并进行安全防护措施
- 严禁在施工现场吸烟或进行其他火源
- 发生安全事故时,应立即停工并上报相关部门
以上是输油管道及管道内壁防腐保温施工方案的完整版,按照该方案进行施工,可有效保障输油管道的正常运行。
油气集输管道内腐蚀及内防腐技术分析

油气集输管道内腐蚀及内防腐技术分析在对油气进行开采以及运输的过程中,金属管道的内壁很容易出现腐蚀的情况,金属管道内壁一旦出现腐蚀,会严重影响油气运输效率,降低油田企业的经济收益。
这就需要对油气集输管道中存在的腐蚀问题进行研究和分析,同时提出针对内腐蚀问题的防腐对策,降低油气集输管道的腐蚀情况,提高油气集输管道的运输效率以及运输安全性,对促进油田企业的长远发展有重要现实意义。
标签:油气集输管道;内防腐技术;外防腐技术前言在当前对油气进行传输时,不能直接传输原油,而是将原油转化为能够运输的油气。
原油中含有比较多的水分,对原油进行转化的过程中,气体会与水分产生反应,会增加油气传输过程中的能耗,同时对油气传输管道产生不利影响。
随着我国科学技术水平的不断提高,当前的油气传输技术也在不断更新和发展,例如先进的常温脱离技术可以确保油气分离在常温环境中进行,防止高温分离出现的腐蚀问题对油气集输管道的运输效率以及安全性产生影响。
现阶段,需要对油气集输管道常见的内腐蚀问题进行研究和分析,才能够提出针对性比较强的有效的防腐措施,这对保证油气传输效率,提高油田企业的经济收益有重要意义。
一、油气集输管道内腐蚀问题在油气集输管道的应用过程中,腐蚀问题一般发生在油水分离的阶段,因为在这一阶段需要大量工艺手段,而工艺手段会导致严重腐蚀问题,例如高温以及酸性气体等。
除此之外,设备本身的问题会影响油气的传输效率,从而对油田的开发以及生产效率产生影响,会降低油田企业的经济收益。
这就需要对油气集输管道在应用过程中存在的内腐蚀问题进行分析,主要的内腐蚀问题包括以下几种:(一)反应腐蚀问题在利用油气集输管道对油气进行传输时,首先传输的是气体,在对原油进行转化的过程中,气体很容易与水进行化学反应,产生腐蚀性比较强的酸性气体。
随着酸性气体的不断增加会严重影响管道内部的稳定性,对管道内部产生大面积腐蚀情况。
这些腐蚀问题会降低油气的运输效率,影响企业的经济收益[1]。
中原油田套管内腐蚀机理及腐蚀控制技术

ቤተ መጻሕፍቲ ባይዱ
2
3
4
区未加药的油井产出液 (水 ) 介质 , 进行室内静态挂 片及动态挂片实验 ,实验结果见表 1。
文 90 块
0. 253
表 1 油井产出水介质的静态 、 动态腐蚀性实验数据 文明寨
0. 134
卫城
0. 207
马寨
0. 142
卫 79 块
0. 236
胡 19 块
0. 116
文 51 块
0. 124
SRB 含量达到了 10 个 /mL 以上 , 井下挂环腐蚀速
8
腐蚀速率 /10
pH = 4 84. 6 166. 6 pH = 5 80. 8 128. 7
-3
mm ・a
-1
pH = 6 pH = 7 28. 8 86. 9
-
27. 5 36. 4
率达到了 3. 7 mm / a。 为了更详细地了解单一 SRB 细菌对钢铁腐蚀 性的影响 ,设计了相应的实验方案 , 腐蚀介质采用 AP I推荐的培养基配方 , 材质分别为 A3 钢 , 做成标 准试片 。腐蚀试验结果见表 3。可以看出 , 温度为 25 ~37 ℃ 时 , 加入 SRB 的腐蚀速率大于未加 SRB 2+ 的腐蚀速率 。加入 SRB 的腐蚀速率随 Fe 的增加 急剧增大 ,而未加入 SRB 的腐蚀速率随 Fe 的增加 增大不 多 , 说明 SRB 的存 在促 进钢 铁腐 蚀 , 且 随 2+ 2+ Fe 的增加而加强 ; 温度为 50 ℃时 , 低 Fe 含量 时 ,随 SRB 增加腐蚀加强 ,而高 Fe 含量时 , SRB 使 2+ 腐蚀减弱 ; 60 ℃ 时 , SRB 在高低浓度 Fe 的环境中 都不能对钢铁腐蚀产生促进作用 ,相反使其变弱 。
油气集输管道内腐蚀及内防腐研究
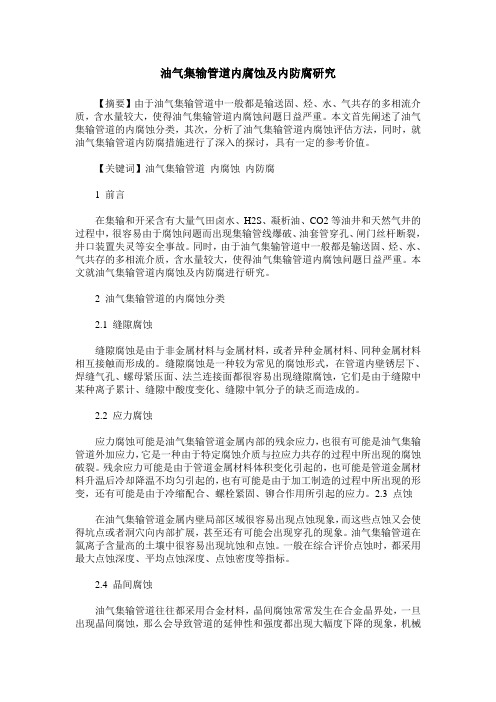
油气集输管道内腐蚀及内防腐研究【摘要】由于油气集输管道中一般都是输送固、烃、水、气共存的多相流介质,含水量较大,使得油气集输管道内腐蚀问题日益严重。
本文首先阐述了油气集输管道的内腐蚀分类,其次,分析了油气集输管道内腐蚀评估方法,同时,就油气集输管道内防腐措施进行了深入的探讨,具有一定的参考价值。
【关键词】油气集输管道内腐蚀内防腐1 前言在集输和开采含有大量气田卤水、H2S、凝析油、CO2等油井和天然气井的过程中,很容易由于腐蚀问题而出现集输管线爆破、油套管穿孔、闸门丝杆断裂,井口装置失灵等安全事故。
同时,由于油气集输管道中一般都是输送固、烃、水、气共存的多相流介质,含水量较大,使得油气集输管道内腐蚀问题日益严重。
本文就油气集输管道内腐蚀及内防腐进行研究。
2 油气集输管道的内腐蚀分类2.1 缝隙腐蚀缝隙腐蚀是由于非金属材料与金属材料,或者异种金属材料、同种金属材料相互接触而形成的。
缝隙腐蚀是一种较为常见的腐蚀形式,在管道内壁锈层下、焊缝气孔、螺母紧压面、法兰连接面都很容易出现缝隙腐蚀,它们是由于缝隙中某种离子累计、缝隙中酸度变化、缝隙中氧分子的缺乏而造成的。
2.2 应力腐蚀应力腐蚀可能是油气集输管道金属内部的残余应力,也很有可能是油气集输管道外加应力,它是一种由于特定腐蚀介质与拉应力共存的过程中所出现的腐蚀破裂。
残余应力可能是由于管道金属材料体积变化引起的,也可能是管道金属材料升温后冷却降温不均匀引起的,也有可能是由于加工制造的过程中所出现的形变,还有可能是由于冷缩配合、螺栓紧固、铆合作用所引起的应力。
2.3 点蚀在油气集输管道金属内壁局部区域很容易出现点蚀现象,而这些点蚀又会使得坑点或者洞穴向内部扩展,甚至还有可能会出现穿孔的现象。
油气集输管道在氯离子含量高的土壤中很容易出现坑蚀和点蚀。
一般在综合评价点蚀时,都采用最大点蚀深度、平均点蚀深度、点蚀密度等指标。
2.4 晶间腐蚀油气集输管道往往都采用合金材料,晶间腐蚀常常发生在合金晶界处,一旦出现晶间腐蚀,那么会导致管道的延伸性和强度都出现大幅度下降的现象,机械强度变化较快,即使管道的外型尺寸和金属质量没有发生多大的变化,但是对于油气集输管道结构的损坏却是极为严重的。
超高分子聚乙烯油管内衬管

和油管内部的防腐蚀性能 ;
• 2、抗腐蚀的内衬管降低因油管内壁腐
蚀而造成的故障 ;
• 3、特种聚乙烯管材作为一种集抗腐、
抗磨、阻力系数小、耐温等特点于一身 的新型管材将替代普通管材,作为油田 油管内衬管材可有效防止腐蚀和磨损, 提高油管和设备的使用寿命。
二、超高分子聚乙烯内衬油管 技术及性能特点
• 将留出的内衬管的两个端面缓慢
均匀加热后,通过翻边机翻边即 可。
五、凯维公司研制生产的超高分 子聚乙烯油管内衬管
1、理化指标
序
项目
单位 结果 检验方法
号
1 拉伸屈服强度 MPa
2 拉伸断裂伸长 % 率
30 GB/T8804.3-
2003
477 GB/T8804.3-
2003
3 简支梁缺口冲 kJ/m2 90 GB/T1043-
采用隔离原理,通过在油管表面内衬一层特种聚 乙烯新材料
特种聚乙
烯内衬新
材
料
挤出工艺
内衬管
内衬油管新 技术
抗磨防腐 双重特性
油管内衬新材料的研究
聚乙烯是通过乙烯(CH2=CH2)加成聚合而 成
是由重复的–CH2–单元连接而成的
化学稳定性好 自润滑性能好
广泛应用于多 种领域
低吸水率
绝缘性能好
用于有杆泵井抗磨防腐,需要对其抗磨性 能、耐温性能、机械性能等方面进行提高或改 进。
一、油田油管使用现状
• 采油井油管的偏磨、腐蚀和结垢
(杆管偏磨、杆断、管漏)导致 油井停产、减产。尤其采油井进 入特高含水期后,因杆管偏磨造 成报废占油管年总用量的1/6以上, 造成巨大的资源浪费和生产成本 增加。
井下油管和管道上使用内部防腐涂层
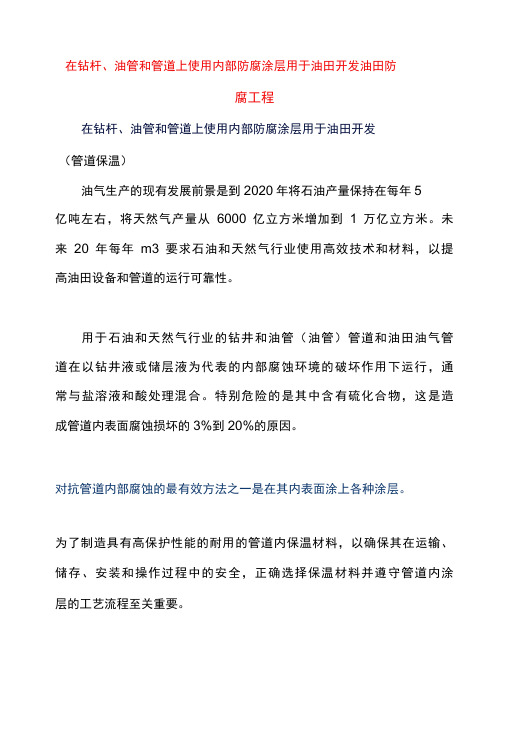
在钻杆、油管和管道上使用内部防腐涂层用于油田开发油田防腐工程在钻杆、油管和管道上使用内部防腐涂层用于油田开发(管道保温)油气生产的现有发展前景是到2020年将石油产量保持在每年5亿吨左右,将天然气产量从6000亿立方米增加到1万亿立方米。
未来20年每年m3要求石油和天然气行业使用高效技术和材料,以提高油田设备和管道的运行可靠性。
用于石油和天然气行业的钻井和油管(油管)管道和油田油气管道在以钻井液或储层液为代表的内部腐蚀环境的破坏作用下运行,通常与盐溶液和酸处理混合。
特别危险的是其中含有硫化合物,这是造成管道内表面腐蚀损坏的3%到20%的原因。
对抗管道内部腐蚀的最有效方法之一是在其内表面涂上各种涂层。
为了制造具有高保护性能的耐用的管道内保温材料,以确保其在运输、储存、安装和操作过程中的安全,正确选择保温材料并遵守管道内涂层的工艺流程至关重要。
现有管道内保温工艺流程主要规定使用环氧树脂、改性环氧树脂和酚醛树脂(用于大口径管道)和粉末聚合物(用于钻井、泵送和压缩机以及油气田)的油漆和清漆.同时,只有在固定的工厂条件下使用防腐涂料,才能使用现代技术和设备进行管道清洗、加热和保温,进行一致的分步工艺控制,确保成品的高质量产品。
钻杆内部保护虽然水基钻井液本身并没有过度腐蚀性,但其配方中的有机添加剂被高温和细菌降解会导致腐蚀性产物的形成。
严重腐蚀是由于钻井液被酸性气体(如二氧化碳、硫化氢)和地层矿化水污染,以及钻屑清除设备中活性氧不断饱和造成的。
此外,钻杆承受循环载荷,导致在高应力集中处形成微裂纹,并在重复循环中加深。
钻井液中盐类、活性氧、二氧化碳和硫化氢的存在会显着加速疲劳断裂,因为在它们存在的情况下,在管体微裂纹的底部形成阳极,在表面形成阴极,由于金属离子转变为裂纹底部的溶液,导致裂纹扩展加速。
疲劳裂纹是管道冲刷和失效的主要原因。
现有的钻杆内部涂层,就其性能而言,旨在确保保护管体内表面不受腐蚀的主要任务,尤其是着陆部位——壁厚的过渡和应力集中。
- 1、下载文档前请自行甄别文档内容的完整性,平台不提供额外的编辑、内容补充、找答案等附加服务。
- 2、"仅部分预览"的文档,不可在线预览部分如存在完整性等问题,可反馈申请退款(可完整预览的文档不适用该条件!)。
- 3、如文档侵犯您的权益,请联系客服反馈,我们会尽快为您处理(人工客服工作时间:9:00-18:30)。
油井钢管内部防腐蚀内衬系统
关键词:油管防腐套管防腐集输管防腐回注管防腐出油管防腐管线防腐
我国许多主力油田已进入中、高含水开发期,随着综合含水的不断上升,油气采集系统的腐蚀日趋严重,腐蚀成为影响管道系统可靠性及使用寿命的关键因素,是造成管道事故的最主要原因。
由于原油中有大量侵蚀性物质存在,如CO2、H2S、Cl-、少量溶解氧和细菌等,受所有这些因素及其交互作用的影响,油管必然遭受严重的腐蚀,油田安全生产受到严重的威胁。
常用的井管防腐方法有:氮化、环氧粉末喷涂、钛纳米喷涂、碳锆涂镀、PE管内衬、玻璃钢油管等。
PE管内衬价格较高,市场难以接受,其它的防腐方式,属低端防腐技术,产品质量不稳定,防腐效果不理想,缺乏竞争力。
玻璃钢内衬油管技术成熟、可靠,售价适中,具有较强的市场竞争力。
玻璃钢内衬防腐技术具有轻质、高强、耐腐蚀,几乎不被油、水、盐等介质侵蚀的特点,而且其疏水表面可减少成垢离子的附着,同时,其内表面光滑,改善了管内流休的流动状态,降低了垢晶在管壁上附挂的几率。
从60年代应用于油气设备内衬到目前为止,已成功应用于油管、套管、集输管、回注管、出油管及管线等。
美国Texas 的PaggiEstale高出水率的井中使用了玻璃钢油管,与J-55钢管相比,虽然管子本身价格高出一倍,但减少了使用钢制油管井底必须装配化学注入装置的麻烦。
大大节省了设备安装费、维修费和化学药品消耗费等开支。
注水井采用玻璃钢内衬油管比普通涂层油管防腐效果更好,使用寿命长,可以减少更换管柱的费用,并且对于因腐蚀造成油管壁厚损失小于50%的旧油管可以修复再利用。
美国North2condemn油田有500多口井应用玻璃钢内衬油管占注水井总数的80%,已用了12年,没有1口井损坏。
美国把玻璃钢内衬油管作为涂层油管的替代产品,在注水井防腐中担当起主力军的角色。
产品概述
杜奥乐产品可以为油田钢管和管线提供内部防腐内衬系统。
杜奥乐是采用独特的嵌入式内衬工艺,通过对长丝缠绕复合材
料或挤压热塑料进行制造,在钢管内形成一种耐腐材料。
这种耐腐
材料可以将油田腐蚀性的液体和气体与钢管隔离。
对于损坏的井底生产油管或海底的流线,其更换成本非常高。
杜奥乐可以在非常苛刻的环境下提供极好的耐腐保护,这是其他产
品所无法超越的。
相比较耐久性较短的喷涂涂层而言,杜奥乐不仅
具有成本效益,且满足极好的性能。
目前高性能的杜奥乐系统在全球范围内得到广泛应用,而在这
之前,在高温或酸性井底的环境下,人们使用的是高成本的耐腐蚀
合金。
杜奥乐20
杜奥乐20是杜奥乐内衬系统的主力。
杜奥乐20是在1971年由杜奥乐技术公司研发而成,主要是针对比较苛刻的腐蚀性井下环境应用。
经证实,无论是陆上或是海上的CO2注入和水注入、油井、气举油井和化学处理井,杜奥乐20都可以满足这些苛刻的应用环境。
即便在流体和气体环境中包含H2S和CO2,杜奥乐20也能表现出极好的性能。
杜奥乐20对于含BHT的油气井耐腐蚀可高达292℉(144℃),杜奥乐20一般用于水注入的环境中服务温度可达250℉(121℃)。
杜奥乐20内衬系统是由杜奥乐技术公司专门制造生产而成。
该内衬是使用GRE复合材料(玻璃钢加强的环氧树脂系统),采用纤维缠绕和高温固化工艺。
这种玻璃钢-环氧内衬系统的应用已有超过33年。
杜奥乐技术公司和杜奥乐20是世界上率先采用玻璃钢内衬的领导者。
在斜井的井下钢丝缆绳测试证实,杜奥乐20是具有最佳的耐磨性能的涂层或内衬产品。
它具有酸兼容性、耐冲击性、耐气体服务环境,其中气体服务环境是其他涂层或内衬失效的原因;此外,它还具有高级接口兼容性、耐化学性以及耐一般的拉伸和弯曲负荷。
简单地说,杜奥乐20内衬系统可以满足极好的防腐保护。
我们需要杜奥乐的原因
杜奥乐产品可以为油田钢管和管线提供内部防腐内衬系统。
杜奥乐是采用独特的嵌入式内衬工艺,通过对长丝缠绕复合材料或挤压热塑料进行制造,在钢管内形成一种耐腐材料。
这种耐腐材料可以将油田腐蚀性的液体和气体与钢管隔离。
对于损坏的井底生产油管或海底的流线,其更换成本非常高。
杜奥乐可以在非常苛刻的环境下提供极好的耐腐保护,这是其他产品所无法超越的。
相比较耐久性较短的喷涂涂层而言,杜奥乐不仅具有成本效益,且满足极好的性能。
目前高性能的杜奥乐系统在全球范围内得到广泛应用,而在这之前,在高温或酸性井底的环境下,人们使用的是高成本的耐腐蚀合金。
杜奥乐连接件选择
杜奥乐产品几乎可以通过任何连接件,安装到带有螺纹的油田管件中。
详细说明请联系我们。
杜奥乐物理性质
杜奥乐20是如何工作的?
杜奥乐技术公司生产的杜奥乐20产品是一种长纤维缠绕的玻璃钢加强环氧(GRE)内衬,主要是安装到腐蚀环境的石油管材内。
相比较内部塑料涂层,玻璃钢加强环氧内衬是一种更坚固的材料,这一点已经得到了广泛的认可。
杜奥乐20是一种有效的腐蚀阻隔层,在一系列的海上和陆上应用中都可以进行管材的保护。
杜奥乐20的优势
工作为温度为250℉;
CO2/水注入/处理;
化学处理;
采气;
与API或PREMIUM螺纹有兼容性;
35年的现场经验;
比耐腐蚀合金材料成本更低;
长期/耐久性的防腐保护;
市场上最完善的腐蚀保护系统;
最具耐磨性的内衬系统;
耐腐蚀的油田管材,可用于海水注入或盐水以及其他恶化环境的腐蚀性液体的处理。
经证实,杜奥乐20在海上和陆上的腐蚀性液体/气体注入有非常好的性能体现。
相比较海上生产作业进行海水注入和盐水处理所使用的高价合金钢管,杜奥乐20更具有成本效益。
杜奥乐挑战
由于用于海水注入和腐蚀性液体和气体处理的特殊合金管材成本较高,由此降低了经营利润,且对项目的经济价值无益。
因为拥挤的钻井平台上增加了用于去除氧气和溶解性固体的设备,该项目的成本也随之增加。
内部涂层产品不能很好的适用于强腐蚀的环境,并且油井维修作业的时间也有所缩短。
在这种情况下,会导致钻井平台运营开支远超预期水平。
州和联邦法规以及高代价的许可对项目的经济造成一定的压力,以至于井下处理得到更多关注。
杜奥乐20性能的客观证明
杜奥乐技术公司在盐水处理领域已有50多年的时间。
杜奥乐技术公司了解了足够的腐蚀问题,指导杜奥乐内衬系统的设计和生产,以及将该内衬系统安装在注入管内。
经证实杜奥乐内衬具有很好的性能,现已成为公司的核心业务。
多年来,杜奥乐内衬一直不断的改进,但是其理念从未改变过。
杜奥乐技术公司已经在全球范围内安装了7500多万英尺的杜奥乐内衬材料,其中包括在北海为很多运营商安装的用于海水注入的内衬。
杜奥乐案例1
杜奥乐案例2
杜奥乐案例3。