(高分子合成工艺学课件)第四章本体聚合工艺
聚合方法(高分子材料化学课件)

本体聚合(bulk polymerization)
锁
聚
溶液聚合(solution polymerization)
合
悬浮聚合(suspension polymerization)
实
施
乳液聚合(emulsion polymerization)
方
法
问题引导
❖ 四种聚合方法(聚合工艺、聚合实施方法)是哪些? ❖ 本体聚合体系的组成与特点 ❖ 溶液聚合体系的组成与特点 ❖ 悬浮聚合体系的组成与特点 ❖ 乳液聚合体系的组成与特点 ❖ 聚合机理对聚合方法的选择 ❖ 四种聚合方法比较
本体聚合
溶液聚合
悬浮聚合
乳液聚合
单体、引发剂
单体、引发剂、溶 单体、引发剂、分 单体、引发剂、乳
剂
散剂、水
化剂、水
单体内
溶剂内
单体内
胶束内
自由基聚合一般机 容易向溶剂转移,
理,聚合速度上升,聚合速率和聚合度 类似本体聚合
聚合度下降
都较低
Hale Waihona Puke 能同时提高聚合速 率和聚合度
设备简单,易制备 板材和型材,一般 间歇法生产,热不 容易导出
不良溶剂 高分子链卷曲
案例
聚丙烯腈纺丝液
聚乙烯醇
丙烯腈+丙烯酸酯+衣康酸 醋酸乙烯酯
硫氰化钠水溶液连续均相 甲醇
AIBN
AIBN
pH = 5
65℃
75~80℃
转化率60%
转化率70~75%
酸或碱性条件下醇解
脱单成纺丝液
聚乙烯醇PVA
PVA1799 纤维用(聚合度1700,醇解度98-100%) PVA1788 分散剂用(聚合度1700,醇解度88%左右)
第四章-本体聚合

Dow苯乙烯连续聚合流程
TEC-MTC苯乙烯本体聚合工艺流程
苯乙烯本体聚合-反应器
早期Dow塔式反应器
改进的Dow塔式反应器
卧式聚合反应器
反应器混合方式
SPS催化体系
茂金属催化剂
其他非茂金属催化剂:金属的乙酰丙酮化合物
sPS性能
高分子量聚苯乙烯
• 本体聚合制备高分子量聚苯乙烯:控制转 化率与低温聚合相结合 • 阴离子聚合挤出机制备高分子量聚苯乙烯: 采用反应挤出方法制备,聚合机理:阴离 子;分子量可以达到40万以上
总结
• 苯乙烯本体聚合基本流程:流程图及过 程描述 • 苯乙烯本体聚合控制因素 • 苯乙烯本体聚合反应器
§ 5.4 高抗冲聚苯乙烯(HIPS) 本体聚合工业过程 • HIPS定义:对聚苯乙烯用弹性体进行化学 和物理改性,得到冲击强度提高的一种不 透明热塑性塑料。 • 工业上用接枝聚合法,将弹性体(顺丁或 丁苯橡胶)溶于苯乙烯中进行本体或悬浮 聚合而制得。通常含弹性体5~12%。
影响因素
• 反应温度;低温60~70℃ • 聚合时间;20%前后聚合速率高,45%后降低, 90%后很慢 • 压力:尤其制备管、棒时采用加压工艺 • 引发剂:对染色的影响,AIBN好 • 氧气的影响:低温诱导效应;高温产生自由基 加速效应、高温分解 • 单体纯度:转移、气泡等
基本生产方法
按照加热方式分 • 水浴法:普通民用产品 • 空气浴法:工业用途及航空有机玻璃 单体是否预聚 • 单体灌膜法:模具密封要求高,产品收缩大 • 单体预聚成浆灌膜: 间歇与连续 • 间歇浇铸 • 连续浇铸
苯乙烯连续本Leabharlann 聚合工艺 • 分段聚合,逐步排除反应热,最终达到高 转化率; • 聚合到一定程度,转化率约40%,分类出 未反应单体循环使用; • 目前以分段聚合工艺为主
高分子合成工艺学课件
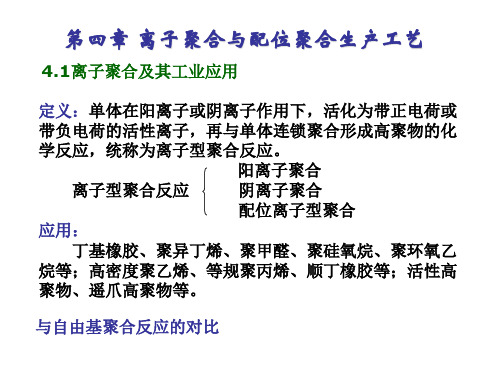
产物立构规整性好、相对分子质量高、支链少、结晶 度高。
第四章 离子聚合与配位聚合生产工艺
R HR HR HR HR HR HR H C C C C C C C C C C C C C C H HH HH HH HH HH HH H
性能:结晶、熔点、 密度、硬度、机械强 度 等规指数: R HH RR HH RR HH RR H C C C C C C C C C C C C C C H HH HH HH HH HH HH H R HH RH RR HR HR HH R C C C C C C C C C C C C C C H HH HH HH HH HH HH H
全同立构体
间同立构体体
蜡状物
无规立构体体
第四章 离子聚合与配位聚合生产工艺
单体 非极性单体:乙烯、丙烯、1-丁烯、苯乙烯、共轭双烯、 环烯烃等 极性单体:甲基丙烯酸甲酯、丙烯酸酯等 催化剂
Ziegler-Natta催化剂 典型Ziegler催化剂与典型Natta催化剂
典型催化 剂 典型 Ziegler 典型Natta 组 成 主催化剂物 态 液体 α 固体结晶 主要应用 以庚烷或甲苯为溶剂,-78℃, PE 聚丙烯、聚丁二烯等
CH3
-
CH33 CH |
CH3
~CH2- | C [BF3OH] →
CH33 CH |+ CH3
~CH2 | -C -OH
CH33 CH | CH3
+
BF3
终止之二(与水、醇、酸等终止剂作用而终止)
-
~CH2-|C [BF3OH] +
XB→
~CH2 | -C -B
+ [BF X 3OH]
+
-
第四章 离子聚合与配位聚合生产工艺
甲基丙烯酸甲酯的本体聚合及有机玻璃的制备PPT精选文档

2. 灌浆 将冷却后的浆液慢慢灌入试管中,注意检查是否有气泡。若有 气泡,将试管口朝上,用手指弹磕试管外壁使气泡逸出。 3. 后聚合 将灌浆后的模具在40℃的烘箱内进行低温聚合,当模具内聚合 物基本成为固体时升温至100℃,保温2 h,使聚合完全。 4. 脱模 将模具自然冷却至40℃以下时,脱去试管即得有机玻璃。观察 其透明性,是否有气泡。
离子聚合:
有较高的选择性,具有供电子基的单体易进行阳离子 聚合,吸电子基的单体易阴离子聚合或自由基聚合。
16
17
本体聚合的缺点:
聚合反应难控制的,这是由于本体聚合不加分散介质,聚合反 应到一定阶段后,体系粘度大,易产生自动加速现象,聚合反应热 也难以导出,因而反应温度难控制,易局部过热,导致反应不均匀, 使产物分子量分布变宽。这在一定程度上限制了本体聚合在工业上 的应用。
共价键上一对电子全部归属于某一基团,形 成阴离子,另一缺电子的基团,称做阳离子
A B A +B
6
自由基是的带单电子 的电中性集团,具有
很高的反应活性
均裂 A‥A 异裂 A‥B 异裂 A‥B
2A·
·
A+ + B-
·
A- + B+
7
电子效应(electron effect)
可分为诱导效应(induction effect)和共轭效应(resonance effect) 诱导效应—取代基的推、吸电子性 在有机化合物分子中,由于电负性不同的取代基(原子或原子团) 的影响,使整个分子中的成键电子云密度向某一方向偏移,这种 效应叫诱导效应。
H
CH2=CH
CH2 C
O
O
R
R
12
• 许多带吸电子基团的烯类单体,如丙烯腈( acrylonitrile)、丙烯酸酯类(acrylate)能同时进行阴 离子聚合和自由基聚合。
高聚物合成工艺-第四章 本体聚合工艺

4.3.2 低密度聚乙烯的生产工艺
a. 主要原料: 乙烯单体 引发剂:(过氧化物和氧)过氧化碳酸二丁酯、过氧化十二 烷酰等。 分子量调节剂:包括烷烃(乙烷、丙烷、丁烷、环己烷)、 烯烃(丙烯、异丁烯)、氢、丙酮等。丙烯、丙烷、乙烷 常用。 各种添加剂: 抗氧剂 2,6-二叔丁基-4-甲基苯酚(防老剂264) 润滑剂 油酸酰胺或硬脂酸胺等 开口剂 高分散性硅胶(SiO2),铝胶(Al2O3)等 抗静电剂 ,常用含氨基或羟基等极性基团的聚合物(如聚环 氧乙烷等)。
无须特别清洗 可能在广泛范围内共聚 反应易控,故可防止分解
窄 多 少
约达333MPa,管内产生 压力降
可达330℃,管内温差大 ﹤30%
与管尺寸有关,60S以上 取决于反应管的参数 接近柱塞流 压力脉冲法清洗管壁
可与少量的第二单体共聚 难以防止偶然的分解 宽 少 多
d. 聚合生产过程
1. 乙烯压缩:
❖ 聚合时间 聚合转化率随时间增长而增大。
❖ 压力 加压可加快反应,同时使单体沸点升高,减少因单体气 化而产生的爆聚。加压还能减少树脂表面收缩。
❖ 引发剂
引发剂用量对分子量产生较大影响,用量不同,分子 量相差很大。过氧化物是强氧化剂,会给有机玻璃染 色带来困难,一般用偶氮化合物。
❖ 氧气
低温下,氧与自由基生成稳定的基团,导致聚合诱导 期延长,转化率下降。高温时,分解产生新的活性中 心,反应速率骤增,易爆聚。因此,应保持反应体系 真空。
新鲜乙烯(3~3.3MPa) 经一次和二次压缩后,压力 最高达到250MPa(釜式)、330MPa(管式)。
2. 引发剂配制和注入:
配好的引发剂用高压泵送入乙烯进料口,或直接注入 聚合设备。
本体聚合生产工艺培训

本体聚合生产工艺培训1. 简介本文档旨在介绍本体聚合生产工艺培训的基本概念、原理和操作流程。
本体聚合生产工艺是一种重要的生产技术,在制造业和工程领域具有广泛应用。
通过本文档的学习,读者将了解本体聚合的定义、应用场景、工艺流程以及相关安全注意事项。
2. 本体聚合的定义和应用场景2.1 定义本体聚合是一种将多个独立的本体元素结合成一个整体的过程。
本体元素可以是物理产品、工艺材料或者其他组件。
通过本体聚合,可以提高产品的强度、刚度和耐久性,同时降低零部件的数量和生产成本。
2.2 应用场景本体聚合工艺广泛应用于以下领域:•汽车制造业:用于汽车车身的生产,提高车身强度和刚度。
•航空航天工程:用于航空器和航天器的结构件制造,提高飞行器的性能和耐久性。
•机械制造业:用于生产机械设备的零部件,提高设备的可靠性和耐用性。
3. 本体聚合的工艺流程本体聚合主要包括以下几个关键步骤:3.1 准备工作在进行本体聚合之前,需要进行准备工作,包括准备本体元素、准备工艺材料和设备,确保工作环境的清洁和安全。
3.2 涂层处理涂层处理是本体聚合的第一步,用于增加本体元素之间的粘附力。
常用的涂层材料包括粘接剂、胶水和融合剂。
涂层处理需要根据本体元素的材质和特性选择合适的涂层材料。
3.3 本体组装本体组装是将涂层处理后的本体元素进行组装,并使用适当的工具和设备进行压缩、固化或热处理。
本体组装需要根据本体元素的形状和尺寸选择合适的组装方法和设备。
3.4 后期处理完成本体聚合后,需要进行后期处理,包括清洁、修整和检验。
后期处理的目的是检查本体聚合的质量和性能,并确保产品达到预期要求。
4. 安全注意事项在进行本体聚合生产工艺培训时,需要注意以下安全事项:•操作人员应接受专业培训,了解本体聚合工艺的基本知识和操作规程。
•使用涂层材料和工艺设备时,应按照安全操作规程进行操作,避免意外事故的发生。
•在进行本体组装和后期处理时,应戴好个人防护设备,包括手套、护目镜和口罩,确保个人安全。
高分子化学第四章乳液聚合

体液滴体积大 比表面小。
增容胶束?
是油溶性单体和 水溶性引发剂相 遇的场所;
胶束内[M]很 高,比表面大, 提供了自由基易 扩散进入引发聚
合的条件。
增容胶束是进行聚合的主要场所。
2.成核机理
乳胶粒:含有聚合物的胶束。 成核:形成乳胶粒的过程,称为成核。
➢胶束成核(micellar nucleation)
散热易,产物呈 固态时要后处 理,也可直接使 用。
含有少量乳化 剂。
间歇, 连续
生产实例
有机玻璃 聚苯乙烯
聚乙烯
丙烯酸树脂 聚丙烯腈 聚醋酸乙烯酯
聚氯乙烯 聚苯乙烯
丁苯橡胶 丙烯酸酯类乳
液
Thank you
●—单体分子, ○—乳化剂分子, ~~聚合物
第Ⅰ阶段:存在单 体液滴,胶束及乳 胶粒子。
第Ⅱ阶段:胶束消 失,含乳胶粒及单 体液滴;乳胶粒体 积不断增大。
第Ⅲ阶段:单体 液滴消失,乳胶 粒体积不断缩小。
乳液聚合阶段示意图
二. 乳液聚合机理
乳化剂:大部分形成胶束,
(直径4~5nm,
聚
少量溶解于水中。
➢ 反相乳液聚合(inverse emulsion polymerization); 油相为连续相,单体是水溶性,即W/O(油包水)。
➢ 核壳乳液聚合(core-shell emulsion polymerization); 先后加入两种不同单体进行聚合,形成核壳结构的乳胶粒。
➢ 无皂乳液聚合(non-soap emulsion polymerization); 不加乳化剂,乳胶粒径单分散性好。
底料入烧瓶 升温至78℃;取组分2的8%-10%打底,升温至84℃, 并加入初加KPS;待兰光出现,回流不明显时开始同时滴加预乳 液及引发剂,约4h滴完;保温1h;降温为65℃,后消除,并保温 30min;降至40℃,调PH为7-8,过滤出料。
高分子合成与聚合方法课件.ppt

当1cm3的液态单体呈正方形排列时, 其表面积为6c m2;呈圆球形状时, 其表面积为4.84cm2.如果将1cm3液态 单体分散成直径为1μm的圆球时,圆 球的总数高达1.91x1012个;其总表面 积为6X104c m2,即较一个圆球的总 表面积增大12000多倍。
• 如果分散成直径为0.1μm的圆球,则其总 表面积为6X105cm2,即增大120000倍以上 。在此情况下,由于物质的表面积大大增 加,因此与表面现象有关的一些性质,如 表面活性大为增加,所以高分散性的粉状 金属,例如骨架镍、活性金属铝等暴露于 空气中都会产生自燃现象。
乳液聚合法不仅用于合成树脂的生产, 合成橡胶中产量最大的品种丁苯橡胶, 目前绝大部分也是用乳液聚合方法进 行生产。
合成树脂生产中采用乳液聚合方法的有: 聚氯乙烯及其共聚物、聚醋酸乙烯及 其共聚物、聚丙烯酸酯类共聚物等。
合成橡胶生产中采用乳液聚合方法的有 丁苯橡胶、丁腈橡胶、氯丁橡胶等。
“种子聚合”
第一节 乳液聚合特点
体系主要由单体、水、乳化剂及溶于水的引发剂4种 基本组分组成。粒径一般在1μm以下,静置时不会 沉降析出。
特点有: (1)聚合速度快,分子量高; (2)可以利用各种单体进行聚合及共聚合,有利于乳 液聚合物的改性和新产品的开发; (3)以水为反应介质,粘度小,成本低,反应热易导 出,反应平稳安全。产品可直接用作涂料和粘合剂; 这种涂料不使用有机溶剂,干燥过程中不会发生火 灾的危险,无毒,不会污染大气。 (4) 聚合反应中加有较多乳化剂,聚合物不纯,在需 要固体聚合物时后处理工序复杂,成本高。
破乳—聚合物乳液稳定性的影响因素
• 在聚合、贮存、运输和乳液直接利用时, 要求高稳定性。而在另一些情况下,例如 欲从聚合乳液生产粉状或块状高聚物时, 则要求其尽快破乳凝聚。
第四章 本体聚合工艺

间力被共价键所代替。收缩超过单体原有体积的 1/5。 根据PMMA本体聚合的特点,其聚合工艺分“预聚” 和“聚合”两段进行。
4.4.2 影响聚合反应的主要因素
反应温度 温度↑,反应速率↑ ,转化率↑, 但温度过高,会 导致链终止速率超过增长速率,同时引起长链解聚, 短链增多,分子量↓。
2. 转化率的控制 乙烯聚合时放热大,易导致急剧升温,为保证安 全生产,保证产品质量,聚合转化率不能超过30 %,大量的乙烯需循环使用。
4.3.5 低密度聚乙烯的结构、性能和应用
4.3.5.1 低密度聚乙烯的结构
▲ LDPE不完全是线型结构,而是有长、短支链,近似树枝状结构。 其结晶度64%,远低于HDPE的85%。
单体纯度 影响产品光学、力学性能。
4.4.3 有机玻璃的生产工艺
有机玻璃本体聚合的生产过程: 一般分为配料、预聚(聚合温度90~95℃,转化 率10~20%)、制模与灌浆、聚合等4个工段。
预聚:目的是缩短聚合周期,使自动加速效应提前,且预聚物有 一定黏度及体积收缩,有利于灌浆及聚合
P26 图3-1
50℃,使用受限制。 LDPE熔点为110~115℃,软化温度范围窄,低于软化温度15~
20℃,可进行延伸与造型,高于软化温度,可用挤出、注射等方 法加工。 化学稳定性好,室温几乎不溶于任何溶剂。耐弱酸碱。
4.3.5.3. 低密度聚乙烯用途
聚乙烯的生产能力长期居各品种的第一 位,消费量占世界聚烯烃的70%,占热 塑性通用塑料消费量的44%。
利用乙烯高压聚合装置,适当增加醋酸乙烯酯加料系统及回收 系统即可兼产乙烯-醋酸乙烯酯共聚物(EVA)。
高分子化学第四章
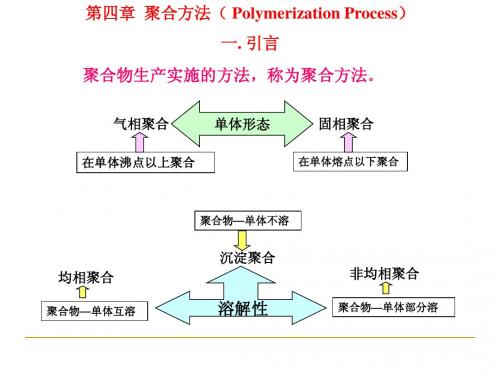
: 2. 分散剂 (dispersant )
起分散作用,使液滴稳定的物质。
分散剂类型
水溶性有机高分子
无机粉末
吸附在液滴表面
包围液滴,隔离作用
影响树脂颗粒大小和形态的因素:
机械强度(一般强度愈大,颗粒愈细); 分散剂种类和浓度; 水与单体比例(水油比); 聚合温度;
非 均 相 聚 合 ( 如 聚 合 ) , 得 不 透 明 的 粉 未 。
数,60℃以上,除了温度,还通过链转移剂来 控制分子量; 引发剂的种类和用量用以调节聚合速度。
4.5 乳液聚合(emulsion polymerization)
定义:
乳化剂,搅拌 单体(monomer) 分散介质
稳定的乳状液而进行的聚合
组分:
经典的乳液聚合
)(油溶性oilsoluble) 单体(monomer tor)(水溶性wa ter soluble) 引发剂(initia fier) 乳化剂(emulsi 分散介质(dispe rsant)(水wa ter)
第Ⅰ阶段:单体 液滴,乳胶束及 乳胶粒子;
第Ⅱ阶段:胶束 消失,含乳胶粒 及单体液滴;
乳液聚合阶段示意图
第Ⅲ阶段:单 体液滴消失, 乳胶粒体积不 断增大。
胶束成核(micellar nucleation)
水相中产生自由基,自由基由水相扩散进入胶束,在 胶束中引发增长,形成聚合物乳胶粒的过程。 大多为油溶性单体。
均相成核(homogeneous nucleation)
水相中产生的自由基引发溶于水中的单体进行增长,形 成短链自由基后,在水相中沉淀出来,沉淀粒子从水相 和单体液滴上吸附了乳化剂分子而稳定,接着又扩散入 单体,形成和胶束成核过程同样的乳胶粒子,这一过程 叫均相成核。
高分子化学聚合方法ppt课件
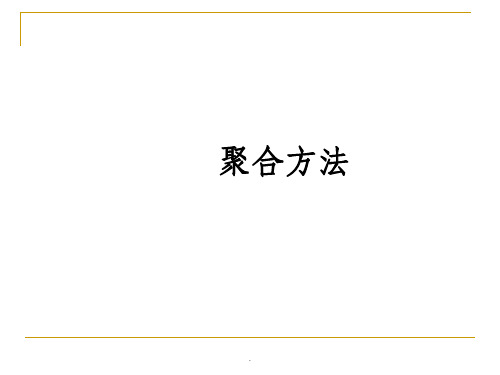
(i)阴离子型:亲水基团一般为-COONa, -SO4Na, -SO3Na等, 亲油基一般是C11~C17的直链烷基,或是C3~C6烷基与苯基或萘基结 合在一起的疏水基;常见的品种有脂肪酸钠、十二烷基硫酸钠、烷 基磺酸钠等。
乳 化 剂 分 子
聚 集
或
亲 油 基亲 水 基
珠 状 胶 束
棒 状 胶 束
.
乳化剂能形成胶束的最低浓度叫临界胶束浓度(简称CMC), CMC越小,越易形成胶束,乳化能力越强。
在搅拌和乳化剂的作用下,不溶于水的单体绝大部分(-95%) 被分散成稳定的乳化单体液滴,另有一小部分单体可渗入到胶束的 疏水(亲油)内部,形成所谓的增溶胶束,这种由于乳化剂的存在 而增大了难溶单体在水中的溶解性的现象称为胶束增溶现象。
.
(ii)阳离子型:亲水基团是阳离子, 通常是一些胺盐和季铵盐如 十六烷基三甲基溴化铵等。由于乳化效果欠佳,因此不常用。
(iii)非离子型:分子上不带有离子基团,其典型的代表聚乙烯 醇,聚环氧乙烷等。
乳液聚合最常使用的是阴离子型乳化剂,而非离子型乳化剂一 般用做辅助乳化剂与阴离子型乳化剂配合使用以提高乳液的稳定性。
均相聚合:得到透明、圆滑的小珠;非均相聚合:得到不透明、 不规整的小珠。
.
悬浮聚合中,分散剂和搅拌是两个重要的因素,二者将单体分散 成稳定的小液珠的过程可示意如下:
搅拌
单体
分散 不稳定的分散状态
凝聚
无机粉末分散作用
稳定的分散状态
水溶性高分子 的分散作用
.
高分子合成技术PPT课件
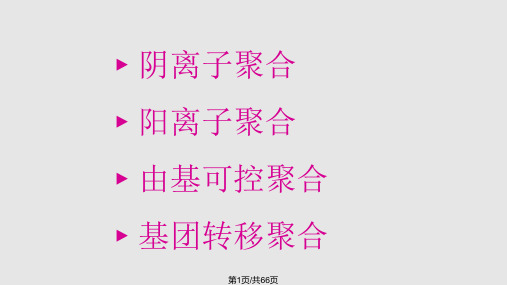
H2C CH O
CH2 CH2 F
HCl SnCl4 nBu4NCl
H H3C C
CH2 CH
CH2 CH Cl SnCl4
O
+
CH2 CH2
n
nBu4N SnCl5
F
R
R
R
MeOH
H H3C C
O
CH2 CH
CH2 CH Cl
CH2
n
CH2
F
R
R
第25页/共66页
F=
O
O
R= H or CH3
自由基活性聚合 Living Free Radical
第23页/共66页
阳离子开环聚合
Kakuchi 报道了一种阳离子开环聚合,如图。在干燥的CH2Cl2中, N2保护下,零度反应6天,最后用含氨水的甲醇溶液终止。
RO RO
*
O O
BF3 OEt2
OR
0 °C
O
RO RO
O *
OR n
阳离子开性阳离子聚合
第20页/共66页
引发剂 阳离子聚合的引发剂是亲电试剂,如质子酸 (HCl, H2SO4, HClO4等)和能够产生碳正离子 的Lewis酸(AlCl3, SnCl4, BF3, TiCl4, AgClO4 和I2等)。Lewis酸做引发剂的时候还要求有一个 共引发剂如水或有机卤化物。当有质子给体如醇、 卤化氢、有机酸或阳离子给体如特丁基氯或三苯 基氟化物存在时,反应可以顺利或加速进行。
H CH2 C
Styrene
第9页/共66页
阴离子聚合条件要求:
无
无
氧
水
无二氧 化碳
无杂质
温度: -78 ℃。
本体聚合生产工艺PPT课件

5.2.3 低密度聚乙烯的生产工艺
• 1.主要原料 • 低密度聚乙烯生产的主要原料是乙烯。 • 乙烯的纯度要求超过99.95%。 • 乙烯高压聚合中单程转化率为15%一30 • 低密度聚乙烯生产除主要原料乙烯外,还有引发剂、分子量调
节剂。此外,还有若干添加剂. • 将添加剂配制成浓度约10%的白油(脂肪族烷烃)溶液或分散液,
第31页/共82页
怎样制得分子量合适而剩余单体最少的聚合物?
工业生产上,聚合反应先在80—110℃下进行,不 仅控制活性中心数目,同时适当控制聚合放热速率, 当转化率达35%左右时,恰是自加速效应后,再逐 渐提高反应温度至230℃ ,使反应完全。
第32页/共82页
第33页/共82页
• 3.粘度和反应热
(1)预聚合
原料苯乙烯自苯乙烯车间定时送入苯乙烯贮槽,再用泵打 到高位槽中,然后由高位槽经过滤器与流量计连续流入经N2 置换的预聚釜中,在预聚釜中,通N2保护。苯乙烯被循环于 钢制夹套中的热水间接加热到80℃进行聚合。反应停留时间 视工艺条件而定。反应温度为80—100℃时,聚合物浓度最 高达到35%,
用泵计量注入低压分离器或二次造粒时加入。
第14页/共82页
• 3.聚合生产方法 • 高压聚乙烯生产工艺有釜式法和管式法两种。 • 两种工艺的个产能力相当.70年代后有偏重管式法倾向。 • (1)釜式法 • 釜式法上艺大都采用有机过氧化物为引发剂,反应压力较管
式法低,聚合物停留时间稍长,部分反应热是借连续搅拌和 夹套冷却带走。大部分反应热是靠连续通入冷乙烯和连续排 出热物料的方法加以调节,使反应温度较为恒定。此法的单 程转化率可达24.5%,生产流程简短,工艺较易控制。 • 主要缺点是反应器结构较复杂,搅拌器的设计与安装均较困 难,而且容易发生机械损坏,聚合物易粘釜。
本体聚合生产工艺课件

24.06.2020
5
3.2 本体聚合生产工艺
缺点:
(1)放热反应,传热系数小,散 热困难,温度控制较难,造成聚合 物分子量分布宽。
采取的措施:合理设计反应器的形 状、大小,增大传热面积;单体中 加入聚合物;分段聚合(预聚合)
凝胶效应是有机玻璃分子量分布宽、分子量甚至超过 100万的主要原因,也是聚合过程中必须严格控制升温速 度的理论根据。
24.06.2020
13
3.2 本体聚合生产工艺
● 聚合工艺
预聚合(制浆):釜式反应器间歇操作,引发剂用量与板 材厚薄有关(0.02-0.1%),80℃反应,需移去反应热。
加入硬脂酸便于脱模,加入少量增塑剂,如邻苯二甲 酸二丁酯或二辛酯,可增加有机玻璃的柔性。
熔融指数仅表示了相应 的熔融粘度,相对的表示了 平均分子量,但不能表示聚 乙烯的分子量分布,而分子 量分布对于聚乙烯的性能也 发生显著的影响。因此,具 有同一种密度、同一种熔融 指数的聚乙烯,由于生产条 件不同,其性能和用途可能 有所不同。
24.06.2020
24
3.2 本体聚合生产工艺
乙烯高压聚合生产流程
20
3.2 本体聚合生产工艺
b:自由基的β-位键断裂
24.06.2020
21
3.2 本体聚合生产工艺
熔融指数 数均分子量 熔融指数 数均分子量 熔融指数 数均分子量
20.9
24000
1.8
32000
0.005
53000
6.4
28000
0.25
48000
0.001
76000
在相同的条件下,熔融粘度越大,被挤压出来的树脂 重量越少。因此聚乙烯的熔融指数↓,其分子量↑。
- 1、下载文档前请自行甄别文档内容的完整性,平台不提供额外的编辑、内容补充、找答案等附加服务。
- 2、"仅部分预览"的文档,不可在线预览部分如存在完整性等问题,可反馈申请退款(可完整预览的文档不适用该条件!)。
- 3、如文档侵犯您的权益,请联系客服反馈,我们会尽快为您处理(人工客服工作时间:9:00-18:30)。
釜式法与管式法比较
项目
釜式法
管式法
压力
温度 反应器冷却带走热量
平均停留时间 生产能力
物料流动状况 反应器表面清洗方法
共聚条件 能否防止乙烯分解 产品PE分子量分布
长链分枝 微粒凝胶
大约110~250MPa,保持稳 定
可控制在130~280℃范围内 ﹤10%
10~120S之间 可在较大范围内变化 在每一反应区内充分混合
4.2 本体聚合反应器
❖ 形状一定的模具 适用于本体浇铸聚合,甲基丙烯酸甲酯经浇铸聚合生产 出有机玻璃板、管、棒材等。模具的形状因制品要求而 定,厚度需控制,防止因过热产生气泡。一般不超过 2.5cm。
❖ 釜式反应器 ❖ 管式反应器 ❖ 塔式反应器
世界最大的10家聚乙烯生产厂商:
Dow&UCC、 ExxonMobil、 Equistar、 ChevronPhillips 、 Borealis(丹麦)、 北欧化工、 沙特基础工业公司、 BP公司、 Nova公司、 Atofina(法国)
b. 引发剂的配制
在油介质(矿物油)下配制成溶液,通过计量泵 注入聚合釜的乙烯进料管或直接注入聚合釜中。
c. 聚合生产方法
釜式法:采用釜式反应器,以过氧化物为引发剂, 压力比管式法为低,反应容易控制,所得聚乙烯分 子量分布窄,有较多支链,适于做一般制品。
管式法:采用管式反应器,引发剂是过氧化物和氧, 压力大。所得聚乙烯支链少,分子量分布宽,薄膜 透明性及成型加工性比釜式法好,适宜做薄膜和电 缆等产品。缺点是聚合物粘管壁易导致堵塞。
聚合后的反应物料经适当冷却后进入高压分离 器,减压至25MPa。未反应的乙烯与聚乙烯分离, 回到二次压缩机吸入口,经加压循环使用。聚乙 烯则进入低压分离器与残存乙烯进一步分离,并 与各种添加剂混和后挤出造粒。经后处理得到成 品聚乙烯。4.3.3 影响LD源自E聚合反应的主要因素压力的影响
乙烯高压聚合是气相反应,提高压力,可加速分子间 碰撞,提高聚合反应速度,提高聚合物产率和分子量。 并降低聚乙烯分子链中的支链度及乙烯含量;考虑到 容器的耐压性和气密性,压力不可能无限制提高。
温度的影响
乙烯结构对称,无极性,反应活性低,在一定温度范围 里,聚合反应速率和聚合物产率随温度的升高而升高, 温度大于350℃,对生产安全造成危险。
引发剂的影响
引发剂的用量将影响聚合反应速度和分子量。用量通常为原料 单体量的万分之一。引发剂的选择视反应区的聚合温度而定, 近来多采用不同活性的混和引发剂。低温区以活性较高的引发 剂为主,高温区则以活性较低的为主。
第四章 本体聚合工艺
Bulk polymerization
4.1 本体聚合工艺特点
❖ 本体聚合是自由基4种实施方法中工艺过程最简单的 方法。
❖ 工艺特点:放热量大,体系传热困难,反应温度难以 控制,所得产品分子量分布宽,自动加速作用大,体 系粘度大。
❖ 在高聚物工业生产中采用本体聚合的有低密度聚乙烯, 聚苯乙烯、聚甲基丙烯酸甲酯、聚氯乙烯等。
4.3.5.2. 低密度聚乙烯的性能
❖ 聚乙烯的力学性能取决于聚合物的分子量、支化度和结晶度。 LDPE较软,在强度上低于HDPE和LLDPE。抗冲击性能优于聚 氯乙烯、聚丙烯和聚苯乙烯。
❖ LDPE脆化温度低,低温性能优良。 ❖ 非极性材料,电绝缘性能优异,适于制造高频电缆和海底电缆的
2. 转化率的控制 乙烯聚合时放热大,易导致急剧升温,为保证安全 生产,保证产品质量,聚合转化率不能超过30%, 大量的乙烯需循环使用。
4.3.5 低密度聚乙烯的结构、性能和应用
4.3.5.1 低密度聚乙烯的结构
▲ LDPE不完全是线型结构,而是有长、短支链,近似树枝状结构。 其结晶度64%,远低于HDPE的85%。
4.3.1 乙烯气相本体聚合的特点
❖ 聚合热大:高于一般的乙烯基类型的单体聚合热。 ❖ 聚合转化率低,通常为20~30%,大量的乙烯必须
循环使用。 ❖ 所得乙烯平均分子量小。 ❖ 易发生链转移反应,导致支化较多。
4.3.2 低密度聚乙烯的生产工艺
a. 主要原料: 乙烯单体 引发剂:(过氧化物和氧)过氧化碳酸二丁酯、过氧化十二 烷酰等。 分子量调节剂:包括烷烃(乙烷、丙烷、丁烷、环己烷)、 烯烃(丙烯、异丁烯)、氢、丙酮等。丙烯、丙烷、乙烷 常用。 各种添加剂: 抗氧剂 2,6-二叔丁基-4-甲基苯酚(防老剂264) 润滑剂 油酸酰胺或硬脂酸胺等 开口剂 高分散性硅胶(SiO2),铝胶(Al2O3)等 抗静电剂 ,常用含氨基或羟基等极性基团的聚合物(如聚环 氧乙烷等)。
▲ LDPE数均分子量一般在2.5×104-5×104之间,分子量分布宽 (Mw/Mn=20~50),工业上常用熔融指数相对表示相应的 分子量及流动性。
熔融指数:在标准的塑性计中,加热到一定温度,使树脂熔融后,
承受一定负荷(一般2160 g)在10 min内经过规定孔径挤压 出的树脂重量克数。在相同条件下,熔融指数越小,表明熔融 粘度越大,即分子量越高。
新鲜乙烯(3~3.3MPa) 经一次和二次压缩后,压力 最高达到250MPa(釜式)、330MPa(管式)。
2. 引发剂配制和注入:
配好的引发剂用高压泵送入乙烯进料口,或直接注入 聚合设备。
3. 聚合:
在压力110~250MPa,温度130~280℃下(釜式 法)聚合,管式法聚合温度、压力更高。
4. 聚合物与未反应的乙烯分离、挤出和后处理(包 括脱气、混和、包装、储存等):
无须特别清洗 可能在广泛范围内共聚 反应易控,故可防止分解
窄 多 少
约达333MPa,管内产生 压力降
可达330℃,管内温差大 ﹤30%
与管尺寸有关,60S以上 取决于反应管的参数 接近柱塞流 压力脉冲法清洗管壁
可与少量的第二单体共聚 难以防止偶然的分解 宽 少 多
d. 聚合生产过程
1. 乙烯压缩:
链转移剂的影响
采用不同的链转移剂,对聚合物的分子量和理化性质影响不同。 丙烷可平稳控制聚合物的分子量。丙烯能与乙烯共聚,因此除 调节分子量和密度外,还会影响聚合物的端基结构。
4.3.4 LDPE生产工艺条件分析(釜式法为例)
1. 温度和压力的控制 工业上一般采用110~250 MPa 、130℃~280℃。