聚合物合成工艺学课件.pptx
合集下载
聚合物合成工艺学
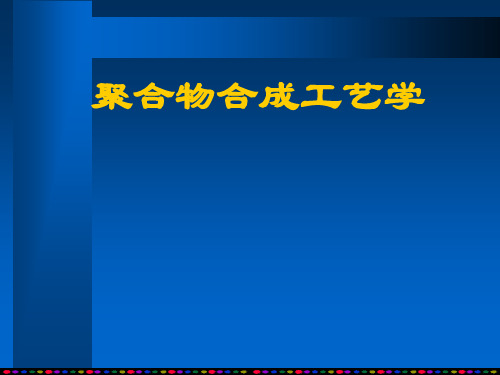
(3)聚合反应过程:涉及聚合和以聚合釜为中心旳有关热互换设备 及反应物料输送过程与设备。
(4)分离过程:涉及未反应单体旳回收、脱除溶剂、催化剂,脱除 低聚物等过程与设备。
(5)聚合物后处理过程:涉及聚合物旳输送、干燥、造粒、均匀化、 贮存、包装等过程与设备。
(6)回收过程:主要是未反应单体和溶剂旳回收与精制过程及设备。 另外三废处理和公用工程如供电、供气、供水等设备。
(7) 发展清洁生产,注重可连续发展
(8) 增强技术创新能力,培养高素质人才
5. 高分子合成工业
(1) 基本原料:石油、天然气、煤炭等为原材料。
(2) 生产过程:涉及石油开采、石油炼制、基本有机合成、高 分子合成、高分子合成材料成型等工业部门,提供主要旳原料 -单体、溶剂、塑料添加剂等辅助原料。
(3) 高分子合成工业旳任务:将基本有机合成工业生产旳单体, 经过聚合反应合成高分子化合物,从而为高分子合成材料成型 工业提供基本原料。所以基本有机合成工业、高分子合成工业 和高分子合成材料成型工业是亲密相联络旳三个工业部门。
多数引起剂受热后有分解爆炸旳危险,干燥、纯粹旳过氧化物 易分解。所以工业上过氧化物采用小包装,贮存在低温环境中, 而且防火,防撞击。
常用旳催化剂烷基金属化合物很危险,易遇空气燃烧或遇水爆炸。 金属卤化物易水解生成腐蚀气体。
(3) 聚合过程
高分子化合物旳平均分子量、分子量分布以及其构造对高分子 合成材料旳物理机械性能产生重大影响,而且生产出来旳成品 不易进行精制提纯,所以对聚合工艺条件和设备旳要求很严格:
例2. 一种年产10万t合成纤维工厂相当于200多万亩棉田旳产量, 也相当于2023万多头绵羊旳年产毛量,我国如能年产100万t合 成纤维,可节省2023多万亩土地,可养活3000-4000万人口。
(4)分离过程:涉及未反应单体旳回收、脱除溶剂、催化剂,脱除 低聚物等过程与设备。
(5)聚合物后处理过程:涉及聚合物旳输送、干燥、造粒、均匀化、 贮存、包装等过程与设备。
(6)回收过程:主要是未反应单体和溶剂旳回收与精制过程及设备。 另外三废处理和公用工程如供电、供气、供水等设备。
(7) 发展清洁生产,注重可连续发展
(8) 增强技术创新能力,培养高素质人才
5. 高分子合成工业
(1) 基本原料:石油、天然气、煤炭等为原材料。
(2) 生产过程:涉及石油开采、石油炼制、基本有机合成、高 分子合成、高分子合成材料成型等工业部门,提供主要旳原料 -单体、溶剂、塑料添加剂等辅助原料。
(3) 高分子合成工业旳任务:将基本有机合成工业生产旳单体, 经过聚合反应合成高分子化合物,从而为高分子合成材料成型 工业提供基本原料。所以基本有机合成工业、高分子合成工业 和高分子合成材料成型工业是亲密相联络旳三个工业部门。
多数引起剂受热后有分解爆炸旳危险,干燥、纯粹旳过氧化物 易分解。所以工业上过氧化物采用小包装,贮存在低温环境中, 而且防火,防撞击。
常用旳催化剂烷基金属化合物很危险,易遇空气燃烧或遇水爆炸。 金属卤化物易水解生成腐蚀气体。
(3) 聚合过程
高分子化合物旳平均分子量、分子量分布以及其构造对高分子 合成材料旳物理机械性能产生重大影响,而且生产出来旳成品 不易进行精制提纯,所以对聚合工艺条件和设备旳要求很严格:
例2. 一种年产10万t合成纤维工厂相当于200多万亩棉田旳产量, 也相当于2023万多头绵羊旳年产毛量,我国如能年产100万t合 成纤维,可节省2023多万亩土地,可养活3000-4000万人口。
高聚物合成工艺学第三版ppt课件

新中国成立后,我国的高分子材料合成工业从无到有、从小到 大,发展至今已形成一个完整的工业体系。 目前,各类材料生产配套、产品品种基本齐全,已广泛用于国 民经济和生活的各个领域。相继建成若干大型石油化工基地如 燕山、兰州、吉林、大庆、齐鲁、金山、仪征、高桥、辽阳等。
6
我国高分子材料合成工业发展趋势
(1) 扩大产能及装置大型化 (2) 产品结构调整 (3) 加强高分子材料科学与工艺学的理论基础研究 (4) 催化剂的重大作用 (5) 合成、加工与应用的一体化 (6) 计算机、信息技术迅速推广应用 (7) 发展清洁生产,注重可持续发展 (8) 增强技术创新能力,培养高素质人才
(6)回收过程:主要是未反应单体和溶剂的回收与精制过程及设备。 此外三废处理和公用工程如供电、供气、供水等设备。
21
聚合物制造工艺过程举例
22
1.3.1 原料准备与精制过程
高纯度的单体及有机溶剂。杂质对聚合反应的阻聚作用、链转移反应;催 化剂中毒及相关副反应。 一般要求单体纯度>99%。
单体贮存注意:
高聚物合成工艺学
1
第一章 绪 论
第一节 高分子合成工业概述
天然高聚物
蚕丝、羊毛、皮革、棉花、木材及天然橡胶。
合成高聚物
塑料、合成纤维、合成橡胶、涂料、粘合剂、 离子交换树脂等材料。
三大合成材料:塑料、合成纤维、合成橡胶
2
1.1.1 发展简史
早期,天然桐油,经适当处理制成油漆。 1839年,美国人发明了天然橡胶的硫化。 1855年,英国人由硝酸处理纤维素制得塑料(赛璐珞),以后又相 继制成人造纤维。(80年代末期用蛋白质-乳酪素为原料获得了 乳酪素塑料,又叫做半合成材料。)
1. 防止单体与空气接触产生爆炸、产生过氧化物。
6
我国高分子材料合成工业发展趋势
(1) 扩大产能及装置大型化 (2) 产品结构调整 (3) 加强高分子材料科学与工艺学的理论基础研究 (4) 催化剂的重大作用 (5) 合成、加工与应用的一体化 (6) 计算机、信息技术迅速推广应用 (7) 发展清洁生产,注重可持续发展 (8) 增强技术创新能力,培养高素质人才
(6)回收过程:主要是未反应单体和溶剂的回收与精制过程及设备。 此外三废处理和公用工程如供电、供气、供水等设备。
21
聚合物制造工艺过程举例
22
1.3.1 原料准备与精制过程
高纯度的单体及有机溶剂。杂质对聚合反应的阻聚作用、链转移反应;催 化剂中毒及相关副反应。 一般要求单体纯度>99%。
单体贮存注意:
高聚物合成工艺学
1
第一章 绪 论
第一节 高分子合成工业概述
天然高聚物
蚕丝、羊毛、皮革、棉花、木材及天然橡胶。
合成高聚物
塑料、合成纤维、合成橡胶、涂料、粘合剂、 离子交换树脂等材料。
三大合成材料:塑料、合成纤维、合成橡胶
2
1.1.1 发展简史
早期,天然桐油,经适当处理制成油漆。 1839年,美国人发明了天然橡胶的硫化。 1855年,英国人由硝酸处理纤维素制得塑料(赛璐珞),以后又相 继制成人造纤维。(80年代末期用蛋白质-乳酪素为原料获得了 乳酪素塑料,又叫做半合成材料。)
1. 防止单体与空气接触产生爆炸、产生过氧化物。
第三章自由基本体聚合原理及生产工艺 聚合物合成工艺学 ppt
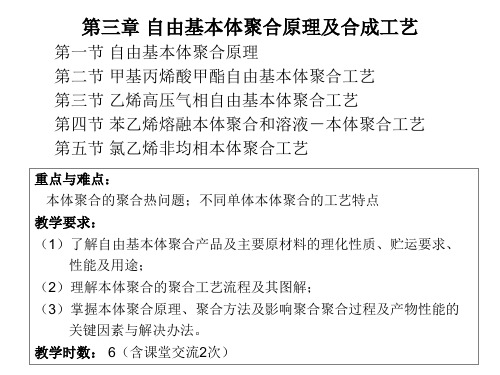
(2)对染料的要求和处理 对染料的要求: 在单体中溶解性好; 耐光、耐热、不褪色。 染料的处理工序: 染料溶于少量单体 → 水浴加热 10 min ,搅匀 → 过滤 → 备用; 若是醇溶性染料,则先溶于单体总量 2% 的丁醇 → 加 等量单体,混合均匀 → 水浴加热 10 min → 过滤 → 备用。
主要缺点是高压釜结构较复杂,尤其是搅拌器的设计与安装 均较困难,在生产中搅拌器会发生机械损坏,聚合物易于沉积 在桨上,因而造成动平衡破坏,甚至有时会出现金属碎屑堵塞 釜后的减压阀现象,使釜内温度急剧上升,导致爆炸的危险。
管式反应器: 管式反应器是细长的高压管。管式反应器的物料在管内呈活
塞式流动,反应温度沿管程有变化,因而反应温度有最高峰,因 此所合成聚乙烯分子量分布较宽。管式法早期的单程转化率较 低.大约10%左右,生产能力为3000t/a,近期单程转化率与釜 式法相近,即为24%,单线生产能力已达到 60000—80000t/a。 管式反应器的结构颇为简单和传热面积相当大。整根细长的高压 管都布置有夹套。
缩短生产周期,使自动加速现象提前到来; 预聚物有一定粘度,灌模容易,不易漏模; 体积已经部分收缩,聚合热已经部分排除,利于后期聚合。
3、制模和灌模工段工艺流程简介 制模材料:
洁净普通玻璃或钢化玻璃; 橡皮垫及玻璃纸; 铁夹; 牛皮纸及胶水。 灌浆 将预聚浆液通过漏斗灌入模具中。根据生产的板材厚度 不同一般采取不同的灌浆方法。 厚度小于 4mm 的板材,先灌浆,之后竖直置于进片架 直接进入水箱,依靠水的压力将空气排出,使浆液布满模具, 立即封合。 厚度 5~6mm 的板材,在竖直灌浆后将空气排出,使浆 液布满模板,立即封合。
3、添加剂
• 防老剂:2,6- 二叔丁基对苯酚(抗氧剂264) ; • 紫外线吸收剂:邻羟基二苯甲酮; • 润滑剂:硬脂酸铵或油酸铵或亚麻仁油酸铵或三者混合物; • 开口剂:提高薄膜开口性、滑爽性和自动包装性能,高分散
聚合物合成原理和工艺ppt课件
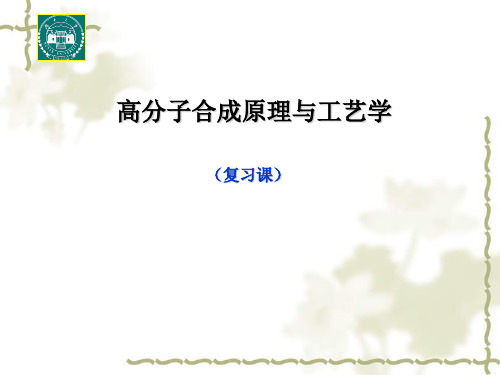
微观结构对高分子的聚集体的综合物性的变化起关键性的作用
大分子的一次结构是由合成反应的条件决定的。分子量的大 小及分布、分子链节的组成、分子链的基团及活性官能团、 大分子空间立体结构等是由合成的配方、组成、催化剂及反 应条件所控制的。大分子的一次结构又对二次、三次及高次 结构及物性起决定性的作用。
耐低温性能对某些高分子材料是重要的,从分子结构看,增 加分子的柔性,Tg值下降,二烯类弹性体、硅橡胶等的分子 链柔性好,具有较好的弹性,玻璃化温度低。
为什么高压聚乙烯比低压聚乙烯的密度低?聚合物结构有何 差异?聚合机理有何不同?低密度聚乙烯的结构是怎样产生 的?
低密度聚乙烯的生产工艺有釜式法和管式法两种。
高压聚乙烯流程分5个部分:乙烯压缩、引发剂配制和注 入、聚合、聚合物与反应的乙烯分离、挤出和后处理(包 括脱气、混合、包装、贮存等)
本体聚合按参加参加单体的相态可分为气相和液相两种。 气相本体聚合中最成熟的是LLDPE的生产。
而升高,当超过一定值后,聚合物产率、分子量及密度则降
低.
?
T
V
但V链转移增加比V链增长更快
M相应降低,即MI
此外,支化反应加快,导致产物的长支链及短支链数目增 加,产物密度降低;另外,大分子链末端的乙烯基含量也 有所增加,降低产品的抗老化能力。
Chapter 3 悬 浮 聚 合
悬 浮 聚 合:通过强烈的机械搅拌作用使不溶于水的单体 或多种单体的混合物成为液滴状分散于一种悬浮介质中进 行聚合反应的方法。
包括:PA(聚酰胺)、PC(聚碳酸酯)、POM(聚甲醛、聚氧化甲 撑)、PPO(聚苯醚)、PBT(聚对苯二甲酸丁二醇脂)、PET(聚对 苯二甲酸乙二醇脂)
特种工程塑料:长期使用温度在150℃以上的塑料。
大分子的一次结构是由合成反应的条件决定的。分子量的大 小及分布、分子链节的组成、分子链的基团及活性官能团、 大分子空间立体结构等是由合成的配方、组成、催化剂及反 应条件所控制的。大分子的一次结构又对二次、三次及高次 结构及物性起决定性的作用。
耐低温性能对某些高分子材料是重要的,从分子结构看,增 加分子的柔性,Tg值下降,二烯类弹性体、硅橡胶等的分子 链柔性好,具有较好的弹性,玻璃化温度低。
为什么高压聚乙烯比低压聚乙烯的密度低?聚合物结构有何 差异?聚合机理有何不同?低密度聚乙烯的结构是怎样产生 的?
低密度聚乙烯的生产工艺有釜式法和管式法两种。
高压聚乙烯流程分5个部分:乙烯压缩、引发剂配制和注 入、聚合、聚合物与反应的乙烯分离、挤出和后处理(包 括脱气、混合、包装、贮存等)
本体聚合按参加参加单体的相态可分为气相和液相两种。 气相本体聚合中最成熟的是LLDPE的生产。
而升高,当超过一定值后,聚合物产率、分子量及密度则降
低.
?
T
V
但V链转移增加比V链增长更快
M相应降低,即MI
此外,支化反应加快,导致产物的长支链及短支链数目增 加,产物密度降低;另外,大分子链末端的乙烯基含量也 有所增加,降低产品的抗老化能力。
Chapter 3 悬 浮 聚 合
悬 浮 聚 合:通过强烈的机械搅拌作用使不溶于水的单体 或多种单体的混合物成为液滴状分散于一种悬浮介质中进 行聚合反应的方法。
包括:PA(聚酰胺)、PC(聚碳酸酯)、POM(聚甲醛、聚氧化甲 撑)、PPO(聚苯醚)、PBT(聚对苯二甲酸丁二醇脂)、PET(聚对 苯二甲酸乙二醇脂)
特种工程塑料:长期使用温度在150℃以上的塑料。
聚合物合成工艺学考试重点ppt课件

2.比较连续生产和间歇生产工艺特点 间歇聚合的特点:a.不易实现操作过程的全部自动化,每一批产品的规格难以控制严格一致。 b.反应器单位容积单位时间内的生产能力受到影响,不适于大规模生产。c.优点:反应条件易控制,便于改变工艺 条件。所以灵活性大,适于小批量生产,容易改变品种和牌号。连续聚合特点:a.聚合反应条件是稳定的,容易实 现操作过程的全部自动化,机械化,所得产品的质量规格稳定。b.设备密闭,减少污染,适合大规模生产,劳动生 产率高,成本较低。c.缺点:不宜经常改变产品牌号,所以不便小批量生产。 3.简述高分子合成工业的三废来源、处理方法以及如何对废旧材料进行回收利用
石油裂解生产汽油、石脑油、柴油、煤油等原料,乙烯、丙稀、丁烯、丁二烯等单体以及芳烃化合物:苯、甲苯、 二甲苯。乙烯聚合产物:聚乙烯、乙丙橡胶、聚氯乙烯、聚乙酸乙烯酯、聚乙烯醇、维纶树脂、聚苯乙烯、ABS树 脂、丁苯橡胶、聚氧化乙烯、涤纶树脂。
1
1.简述四种自由基聚合生产工艺的定义以及他们的特点和优缺点?本体聚合(又称块状聚合):在不用其它反应介质情况下,单体中加 有少量或不加引发剂发生聚合的方法。乳液聚合是单体和水在乳化剂作用下形成的乳状液中进行聚合反应的一种聚合物生产方法。悬 浮聚合是将单体在强烈机械搅拌及分散剂的作用下分散、悬浮于水相当中,剂)进行聚合的方法。
2
乳液聚合优点:(1)以水作分散介质,价廉安全,比热较高,乳液粘度低,有利于搅拌传热和管道输送,便于连续操 作。同时生产灵活,操作方便,可连续可间歇。(2)聚合速率快,同时产物分子量高,可在较低的温度下聚合。(3)可 直接应用的胶乳,如水乳漆,粘结剂,纸张、皮革、织物表面处理剂更宜采用乳液聚合。乳液聚合物的粒径小。(4) 不使用有机溶剂,干燥中不会发生火灾,无毒,不会污染大气。缺点:(1)需固体聚合物时,乳液需经破乳、洗涤、 脱水、干燥等工序,生产成本较高。(2)产品中残留有乳化剂等,难以完全除尽,有损电性能、透明度、耐水性能等。 (3)聚合物分离需加破乳剂,如盐溶液、酸溶液等电解质,因此分离过程较复杂,并且产生大量的废水;如直接进行 喷雾干燥需大量热能;所得聚合物的杂质含量较高。悬浮聚合的优点:a. 以水为分散介质,价廉、不需要回收、安 全、易分离。b. 悬浮聚合体系粘度低、温度易控制、产品质量稳定。c. 由于没有向溶剂的链转移反应,其产物相对 分子质量一般比溶液聚合物高。d. 与乳液聚合相比,悬浮聚合物上吸附的分散剂量少,有些还容易脱除,产物杂质 较少。e. 颗粒形态较大,可以制成不同粒径的颗粒粒子。聚合物颗粒直径一般在0.05-0.2mm,有些可达0.4 mm.甚 至超过1mm。缺点:a. 工业上采用间歇法生产,而连续法尚未工业化。b. 反应中液滴容易凝结为大块,而使聚合热 难以导出,严重时造成重大事故。 c. 悬浮聚合法目前仅用于合成树脂的生产。溶液聚合优点:与本体聚合相比,溶剂可作为传热介质使体系传热较易, 温度容易控制;体系粘度较低,减少凝胶效应,可以避免局部过热;易于调节产品的分子量及其分布。缺点:a. 单 体浓度较低,聚合速率较慢,设备生产能力和利用率较低。b.单体浓度低和向溶剂链转移的结果,使聚合物分子量 较低。c.使用有机溶剂时增加成本、污染环境。d.溶剂分离回收费用高,除尽聚合物中残留溶剂困难。 2.举例说明自由基聚合引发剂的分类,在高聚物生产中如何选择合适的引发剂? (1)过氧化物类:大多数为有机过氧化物,通式为 R-O-O-H 或 R-O-O-R烷基(或芳基)过氧化氢:R-O-O-H,过酸,过氧 化二烷基(或芳基):R-O-O-R,过氧化二酰基,过酸酯、过氧化碳酸二酯、过氧化磺酸酯等;无机过氧类引发剂:过 硫酸盐,如过硫酸钾 K2S2O8 和过硫酸铵 (NH4)2S2O8等。(2)偶氮化合物:偶氮二异丁腈(AIBN),偶氮二(2-异丙基)丁腈 ,偶氮二(2,4-二甲基)戊腈(3)氧化还原引发体系:(a)过氧化氢-亚铁盐氧化-还原体系(b)过硫酸盐-亚硫酸盐氧化-还 原体系(c)过硫酸盐-Fe+2氧化-还原体系(d)过氧化二苯甲酰-二甲苯胺引发体系。选择:(a)根据聚合方法选择适当溶解 性能的水溶性或油溶性的引发剂。(b)根据聚合操作方式和反应温度选择适当分解速度的引发剂。(c)根据分解速度常 数选择引发剂。(d)根据分解活化能Ed选择引发剂。(e)根据引发剂的半衰期选择引发剂。 3.在聚合生产工艺中如何控制产品的分子量,举例说明常用的分子量调节剂。 控制聚合反应温度在一定范围和其他反应条件、严格控制引发剂用量,一般仅为千分之一、单体浓度及链转移剂的 种类和用量、选择适当的分子量调节剂并严格控制其用量。例如:在高压法生产低密度聚乙烯过程中用丙烷、丙烯 或量H。2作为链转移剂,以控制聚乙烯平均分子量,生产丁苯橡胶时加入硫醇作为链转移剂以控制丁苯橡胶的平均分子 4.自由基本体聚合生产中用到的聚合反应器的类型和特点(1)形状一定的模型:适用于本体浇铸聚合。这种反应装置 无搅拌器,其聚合条件应根据聚合时热传导条件而定。(2) 聚合釜:流体粘度高,多采用旋桨式或大直径的斜桨式搅 拌器。采用数个聚合釜串联,分段聚合的连续操作方式。(3)本体连续聚合反应器,包括管式反应器,物料呈层流状 态流动,使物料产生脉冲以产生湍流,单程转化率通常仅为10%~20%,多采用多管并联方式;塔式反应器:无搅 拌装置,物料呈柱塞状流动。
石油裂解生产汽油、石脑油、柴油、煤油等原料,乙烯、丙稀、丁烯、丁二烯等单体以及芳烃化合物:苯、甲苯、 二甲苯。乙烯聚合产物:聚乙烯、乙丙橡胶、聚氯乙烯、聚乙酸乙烯酯、聚乙烯醇、维纶树脂、聚苯乙烯、ABS树 脂、丁苯橡胶、聚氧化乙烯、涤纶树脂。
1
1.简述四种自由基聚合生产工艺的定义以及他们的特点和优缺点?本体聚合(又称块状聚合):在不用其它反应介质情况下,单体中加 有少量或不加引发剂发生聚合的方法。乳液聚合是单体和水在乳化剂作用下形成的乳状液中进行聚合反应的一种聚合物生产方法。悬 浮聚合是将单体在强烈机械搅拌及分散剂的作用下分散、悬浮于水相当中,剂)进行聚合的方法。
2
乳液聚合优点:(1)以水作分散介质,价廉安全,比热较高,乳液粘度低,有利于搅拌传热和管道输送,便于连续操 作。同时生产灵活,操作方便,可连续可间歇。(2)聚合速率快,同时产物分子量高,可在较低的温度下聚合。(3)可 直接应用的胶乳,如水乳漆,粘结剂,纸张、皮革、织物表面处理剂更宜采用乳液聚合。乳液聚合物的粒径小。(4) 不使用有机溶剂,干燥中不会发生火灾,无毒,不会污染大气。缺点:(1)需固体聚合物时,乳液需经破乳、洗涤、 脱水、干燥等工序,生产成本较高。(2)产品中残留有乳化剂等,难以完全除尽,有损电性能、透明度、耐水性能等。 (3)聚合物分离需加破乳剂,如盐溶液、酸溶液等电解质,因此分离过程较复杂,并且产生大量的废水;如直接进行 喷雾干燥需大量热能;所得聚合物的杂质含量较高。悬浮聚合的优点:a. 以水为分散介质,价廉、不需要回收、安 全、易分离。b. 悬浮聚合体系粘度低、温度易控制、产品质量稳定。c. 由于没有向溶剂的链转移反应,其产物相对 分子质量一般比溶液聚合物高。d. 与乳液聚合相比,悬浮聚合物上吸附的分散剂量少,有些还容易脱除,产物杂质 较少。e. 颗粒形态较大,可以制成不同粒径的颗粒粒子。聚合物颗粒直径一般在0.05-0.2mm,有些可达0.4 mm.甚 至超过1mm。缺点:a. 工业上采用间歇法生产,而连续法尚未工业化。b. 反应中液滴容易凝结为大块,而使聚合热 难以导出,严重时造成重大事故。 c. 悬浮聚合法目前仅用于合成树脂的生产。溶液聚合优点:与本体聚合相比,溶剂可作为传热介质使体系传热较易, 温度容易控制;体系粘度较低,减少凝胶效应,可以避免局部过热;易于调节产品的分子量及其分布。缺点:a. 单 体浓度较低,聚合速率较慢,设备生产能力和利用率较低。b.单体浓度低和向溶剂链转移的结果,使聚合物分子量 较低。c.使用有机溶剂时增加成本、污染环境。d.溶剂分离回收费用高,除尽聚合物中残留溶剂困难。 2.举例说明自由基聚合引发剂的分类,在高聚物生产中如何选择合适的引发剂? (1)过氧化物类:大多数为有机过氧化物,通式为 R-O-O-H 或 R-O-O-R烷基(或芳基)过氧化氢:R-O-O-H,过酸,过氧 化二烷基(或芳基):R-O-O-R,过氧化二酰基,过酸酯、过氧化碳酸二酯、过氧化磺酸酯等;无机过氧类引发剂:过 硫酸盐,如过硫酸钾 K2S2O8 和过硫酸铵 (NH4)2S2O8等。(2)偶氮化合物:偶氮二异丁腈(AIBN),偶氮二(2-异丙基)丁腈 ,偶氮二(2,4-二甲基)戊腈(3)氧化还原引发体系:(a)过氧化氢-亚铁盐氧化-还原体系(b)过硫酸盐-亚硫酸盐氧化-还 原体系(c)过硫酸盐-Fe+2氧化-还原体系(d)过氧化二苯甲酰-二甲苯胺引发体系。选择:(a)根据聚合方法选择适当溶解 性能的水溶性或油溶性的引发剂。(b)根据聚合操作方式和反应温度选择适当分解速度的引发剂。(c)根据分解速度常 数选择引发剂。(d)根据分解活化能Ed选择引发剂。(e)根据引发剂的半衰期选择引发剂。 3.在聚合生产工艺中如何控制产品的分子量,举例说明常用的分子量调节剂。 控制聚合反应温度在一定范围和其他反应条件、严格控制引发剂用量,一般仅为千分之一、单体浓度及链转移剂的 种类和用量、选择适当的分子量调节剂并严格控制其用量。例如:在高压法生产低密度聚乙烯过程中用丙烷、丙烯 或量H。2作为链转移剂,以控制聚乙烯平均分子量,生产丁苯橡胶时加入硫醇作为链转移剂以控制丁苯橡胶的平均分子 4.自由基本体聚合生产中用到的聚合反应器的类型和特点(1)形状一定的模型:适用于本体浇铸聚合。这种反应装置 无搅拌器,其聚合条件应根据聚合时热传导条件而定。(2) 聚合釜:流体粘度高,多采用旋桨式或大直径的斜桨式搅 拌器。采用数个聚合釜串联,分段聚合的连续操作方式。(3)本体连续聚合反应器,包括管式反应器,物料呈层流状 态流动,使物料产生脉冲以产生湍流,单程转化率通常仅为10%~20%,多采用多管并联方式;塔式反应器:无搅 拌装置,物料呈柱塞状流动。
聚合物的成型加工方法ppt课件

塑料发泡后的体积比发泡前增大数倍,称为发
泡倍率。发泡倍率大于5的称为高发泡;小于5 的称为低发泡;采用不同发泡工艺可获得不同
硬度的制品,即硬质、软质和半硬质泡沫塑料
精选ppt
20
成型加工过程中的化学与物理变化
精选ppt
21
1、降解与交联
聚合物在热、力ቤተ መጻሕፍቲ ባይዱ氧、光、水等作用下会发 生降解,有时也伴随有交联。
属镀饰,表面喷涂、染色等加工处理,这些方法
有时被称为高分子材料的二次加工。
精选ppt
8
塑料的成型加工 1. 挤出成型
1)、原理:将粒状聚合物或粉状物料连续加入 挤出机料筒中,借助挤出机内螺杆的挤压作 用,使受热熔融的物料在压力推动下强制、 连续地从一定形状的口模挤出,形成与口模 相似横断面的连续型材,经冷却定型得聚合 物材料或制品。
聚合物成型加工介绍
陈双俊
精选ppt
1
聚合物的成型加工:将聚合物或以聚合物 为基本成分,加入各种添加剂,在一定的 温度和压力下,将其转变为具有实用价值 的材料或制品的一种工艺过程。
精选ppt
2
精选ppt
3
精选ppt
4
精选ppt
5
聚合物的成型加工方法分类
按聚合物的成型方法原理,大致可分为:
压延机成型还可用来制造人造革、墙纸、印 花或刻花复合材料等。
精选ppt
14
精选ppt
15
精选ppt
16
4、模压成型 模压成型是热固性塑料主要的成型加工方法。
模压成型是指将计量好的成型物料加入闭合 的模具中,在热压下使树脂熔融、流 动充 满模腔,然后固化定型。
精选ppt
17
精选ppt
聚合物合成工艺PPT优质课件
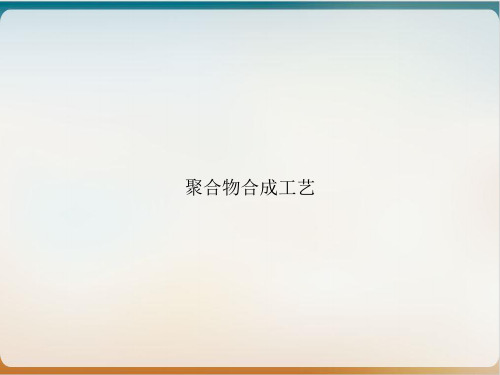
➢ St高温聚合 2.8~3.0 1
4.4悬浮聚合的工艺控制
➢ 4.4.3聚合温度
➢ 对下列参数等有重要影响
夹套温度控制曲线-曲线c
反应速率 对自下动列 加参速✓数阶等段有P重V要C树影脂响不溶于单体VC,但可吸收单体达27%(质量),形成粘性凝胶,然后聚合反应在凝胶内进行
(流程图见P48,图41)
1.93m2/m3,35m3反应釜的单位体积传热面积减少为 1.41m2/m3,减少了27%。 ✓ 因此,必需采取一些措施。
强化传热与传质的措施
✓ 内部增加带夹套的折流挡板,以尽可能增加传热
面积
✓ 改进搅拌器的结构,增加釜内的扰动,改进传热
效果
✓ 调节气体的蒸发速度 借助物料的体外循环带出
部分热量
聚合物合成工艺
(优选)聚合物合成工艺
悬浮聚合的优缺点
➢ 优点 ➢ 总体上与乳液法相近 ➢ 工艺流程较短,设备要求相对简单 ➢ 反应过程较易控制反应体系中含有大量的水作为介质,体
系的黏度较低,反应产生的热量易于除去。 ➢ 树脂的纯度比乳液法高 ➢ 三废排放量比乳液法低
悬浮聚合的优缺点
➢ 缺点
➢ 难以实现连续化生产聚合过程中分散问题在连续聚合中较难解
“鱼眼” 主要是在水相中聚合而成的聚合物 以VC悬浮聚合用14m3反应釜的单位体积传热面积为1.
通常的配比 1.0~2.5 1 “鱼眼” 主要是在水相中聚合而成的聚合物
可将两种无➢机物同时加入反应体系中,现场合成沉淀物以获得高分散性的无机粉末。
➢ VC悬浮聚合 1.5~2.5 1
➢ St低温聚合 1.4~1.6 1
➢ 4.6.1原料的合成路线
➢ 4.6.1.1电石法合成工艺—乙炔路线
4.4悬浮聚合的工艺控制
➢ 4.4.3聚合温度
➢ 对下列参数等有重要影响
夹套温度控制曲线-曲线c
反应速率 对自下动列 加参速✓数阶等段有P重V要C树影脂响不溶于单体VC,但可吸收单体达27%(质量),形成粘性凝胶,然后聚合反应在凝胶内进行
(流程图见P48,图41)
1.93m2/m3,35m3反应釜的单位体积传热面积减少为 1.41m2/m3,减少了27%。 ✓ 因此,必需采取一些措施。
强化传热与传质的措施
✓ 内部增加带夹套的折流挡板,以尽可能增加传热
面积
✓ 改进搅拌器的结构,增加釜内的扰动,改进传热
效果
✓ 调节气体的蒸发速度 借助物料的体外循环带出
部分热量
聚合物合成工艺
(优选)聚合物合成工艺
悬浮聚合的优缺点
➢ 优点 ➢ 总体上与乳液法相近 ➢ 工艺流程较短,设备要求相对简单 ➢ 反应过程较易控制反应体系中含有大量的水作为介质,体
系的黏度较低,反应产生的热量易于除去。 ➢ 树脂的纯度比乳液法高 ➢ 三废排放量比乳液法低
悬浮聚合的优缺点
➢ 缺点
➢ 难以实现连续化生产聚合过程中分散问题在连续聚合中较难解
“鱼眼” 主要是在水相中聚合而成的聚合物 以VC悬浮聚合用14m3反应釜的单位体积传热面积为1.
通常的配比 1.0~2.5 1 “鱼眼” 主要是在水相中聚合而成的聚合物
可将两种无➢机物同时加入反应体系中,现场合成沉淀物以获得高分散性的无机粉末。
➢ VC悬浮聚合 1.5~2.5 1
➢ St低温聚合 1.4~1.6 1
➢ 4.6.1原料的合成路线
➢ 4.6.1.1电石法合成工艺—乙炔路线
- 1、下载文档前请自行甄别文档内容的完整性,平台不提供额外的编辑、内容补充、找答案等附加服务。
- 2、"仅部分预览"的文档,不可在线预览部分如存在完整性等问题,可反馈申请退款(可完整预览的文档不适用该条件!)。
- 3、如文档侵犯您的权益,请联系客服反馈,我们会尽快为您处理(人工客服工作时间:9:00-18:30)。
原料:主要是液态油品和裂解副产物乙烷,C4馏分等。含有 乙烷、丙烷、丁烷等,可液化湿性天然气,也可作裂解原料。
装置:大规模装置多数是管式裂解炉。为了避免裂解管内结 焦,必须采用沸点较低的油品,例如轻柴油、石脑油以及石 油炼制过程中产生的副产品炼厂气。
过程:轻油在水蒸汽存在下,于750-820℃高温热裂解为低级 烯烃、二烯烃。为减少副反应,提高烯烃收率,液态烃在高 温裂解区的停留时间仅0.2-0.5秒。水蒸汽稀释目的在于减少 烃类分压,抑制副反应并减轻结焦速度。
石脑油裂解生产芳烃方块流程图
混合芳烃收率为石脑油总量30-33%。
4. 由C4馏分制取丁二烯
在石油炼制高温裂解过程中都会产生易液化的C4馏分(丁烷、丁 烯和丁二烯等组成的混合物)。其中1,3-丁二烯是最重要合成橡 胶原料; 1-丁烯是合成塑料原料;异丁烯是丁基橡胶原料。 石油炼制得到的炼厂气C4馏分中各种丁烯的含量超过50%,丁 烷40%,不含有丁二烯。而轻柴油裂解得到的C4馏分丁烷很少, 主要是丁烯和丁二烯。
柴油 重油 减压蒸馏
沥青 柴油 燃料油 石蜡
润滑油
第二章 生产单体的原料路线
第二章 生产单体的原料路线
石油裂解:
在一定条件下,把分子量大, 沸点高的烃断裂为分 子量小、沸点低的烃的过程。
如:C16H34
C8H18+C8H16
C8H18
C4H10 + C4H8
C4H10
CH4+C3H6
C4H10
C2H4+C2H6
用二甲基甲酰胺DMF萃取精馏丁二烯流程 1-第一萃取蒸馏塔,2-第一汽提塔,3-第二萃取蒸馏塔 4-丁二烯回收塔,5-第一精馏塔,6-第二精馏塔
轻柴油裂解生产烯烃方块流程图
25-26% 16-18%
11-12%
3. 石油裂解生产芳烃
苯、甲苯、二甲苯等芳烃是重要的化工原料,过去主要来自煤焦 油,现在则开发了由石油烃催化重整制取芳烃的路线。
原料:用全馏程石脑油(由原油经常压法直接蒸馏得到的沸点< 220oC的直馏汽油)于管式炉中,820oC下裂解生产芳烃。
原油经石油炼制工业的加工,主要是常压蒸馏(300-400oC以下) 分出石油气、石油醚、汽油、煤油、轻柴油等馏分。高沸点部 分再经减压蒸馏得到柴油、含蜡油等馏分。不能蒸出的部分称 做渣油。
各类油品的沸点范围、大致组成及用途
第二章 生产单体的原料路线
石油分馏产品: 石油气
原油 常压蒸馏
汽油 轻质油 煤油
1998年我国原油加工和主要石化产品生产能力(万t/年)
1. 石油的组成
石油主要存在于地球表面以下的一种有气味的从黄色到黑色的 粘稠液体。主要为碳、氢两种元素所组成的各种烃类混合物, 并含有少量的含氮、含硫、含氧化合物。
根据所含主要碳氢化合物类别,原油可分为石蜡基石油、环烷 基石油、芳香基石油以及混合基石油。我国所产石油大多数属 于石蜡基石油。
生产过程的裂解、分离与轻柴油裂解分离相似,同样得到聚合级 乙烯和丙烯,不同的是裂解原料组成不同。
主要特点:截取石脑油中C6-C9烃类(65-145oC馏分)进行加氢, 使其中烯烃被氢所饱和,含S、N、Cl的化合物被加氢而脱除。
在含铂催化剂作用,在重整反应器中于1. 4-1.7 MPa和520 ℃下反 应。烃类发生脱氢、环化、异构化、裂解,生成芳烃、氢气、液 化石油气和C5馏分,经分离后得芳烃浓度近50%的重整生成油。
石油有热裂化和催化裂化两种
第二章 生产单体的原料路线
热裂解
目的:提高汽油的产量
缺点:温度过高,发生结焦现象
催化裂解
目的:提高汽油的质量和产量
催化剂:硅酸铝,分子筛 (铝硅酸盐)
第二章 生产单体的原料路线
石油的催化重整
支链化:提高汽油质量 环化:生产芳烃 催化剂:Pt Re
2. 石油裂解生产烯烃
液态烃经高温裂解生成的产品成分复杂,包括氢、甲烷、乙炔、 乙烷、乙烯、丙烷、丙烯、裂解汽油等。
裂解装置可以分为以生产乙烯、丙烯、芳烃为主要产品的装置。 其生产规模通常以年产的乙烯量为标准,因此石油裂解装置工 业上称为“乙烯装置”,大型乙烯装置60万吨/年乙烯以上。
轻柴油裂解产品
石油裂解装置:裂解炉及一系列用于气体物料压缩和冷冻的压 缩机,一系列用来分离各种产品和副产品的蒸馏塔,许多热交 换器,分离油和水的装置,气体干燥,脱酸性气体等装置。还 有为利用回收能量的急冷锅炉和制冷装置冷箱。
第二章 生产单体的原料路线
第一节 国土资源与聚合物生产的原料
➢聚合物生产的主要原料为有机化合物,它主要来源于各种 资源,如石油、天然气、煤炭和各种动植物。单体原料来源 路线为:石油化工路线、煤炭路线和其它原料路线,
➢我国石油探明储量约940亿t,占世界第8位。天然气储量38 万亿m3居世界第16位。煤炭储量为7650亿t,占世界第3位。
➢对中国“地大物博”的概念重新加以认识,随着矿产开发 年代推移、深度的增加、品位下降,2000年以后我国部分矿 产将呈现下降趋势。
➢矿产资源是不可再生的。
第二节 从石油和天然气获得的石油化工原料路线
据统计,到1998年我国已建立了25个油气生产基地(其中海洋4个)。 全国年产原油1.6亿t,天然气223亿m3,分别居世界第5和第18位。 从1993年起,我国已成为石油净进口国。
由C4馏分制取丁二烯的途径: (1) 由裂解气分离得到的C4馏分中抽取丁二烯,萃取精馏方法。 (2) 用炼厂气或轻柴油裂解气C4馏分分离出来的丁烯为原料进 行氧化脱氢制取丁二烯。
萃取精馏是液体的混合物中加入较难挥发的第三组分溶剂,以增 大液体混合物中各组分的挥发度的差异,使挥发度相对地变大的 组分可由精馏塔顶馏出,挥发度相对地变小的组分则与加入的溶 剂在塔底流出分离。溶剂有:二甲基甲酰胺、乙腈、二甲亚砜等。
精制过程:用3-15%NaOH溶液洗涤裂解气脱除酸性气体(CO2、 H2S等)。炔烃(乙炔和甲基乙炔)一般用钯催化剂进行选择 性加氢转化为烯烃。大部分水蒸汽在气体压缩过程中已除去, 少量的水则用分子筛进行干燥。
分离过程:裂解气除含低级烯烃深冷分离 法)处理,将裂解气冷冻到-100℃左右,使除H2和CH4以外的低 级烃全部冷凝液化,再用精馏方法分离。
装置:大规模装置多数是管式裂解炉。为了避免裂解管内结 焦,必须采用沸点较低的油品,例如轻柴油、石脑油以及石 油炼制过程中产生的副产品炼厂气。
过程:轻油在水蒸汽存在下,于750-820℃高温热裂解为低级 烯烃、二烯烃。为减少副反应,提高烯烃收率,液态烃在高 温裂解区的停留时间仅0.2-0.5秒。水蒸汽稀释目的在于减少 烃类分压,抑制副反应并减轻结焦速度。
石脑油裂解生产芳烃方块流程图
混合芳烃收率为石脑油总量30-33%。
4. 由C4馏分制取丁二烯
在石油炼制高温裂解过程中都会产生易液化的C4馏分(丁烷、丁 烯和丁二烯等组成的混合物)。其中1,3-丁二烯是最重要合成橡 胶原料; 1-丁烯是合成塑料原料;异丁烯是丁基橡胶原料。 石油炼制得到的炼厂气C4馏分中各种丁烯的含量超过50%,丁 烷40%,不含有丁二烯。而轻柴油裂解得到的C4馏分丁烷很少, 主要是丁烯和丁二烯。
柴油 重油 减压蒸馏
沥青 柴油 燃料油 石蜡
润滑油
第二章 生产单体的原料路线
第二章 生产单体的原料路线
石油裂解:
在一定条件下,把分子量大, 沸点高的烃断裂为分 子量小、沸点低的烃的过程。
如:C16H34
C8H18+C8H16
C8H18
C4H10 + C4H8
C4H10
CH4+C3H6
C4H10
C2H4+C2H6
用二甲基甲酰胺DMF萃取精馏丁二烯流程 1-第一萃取蒸馏塔,2-第一汽提塔,3-第二萃取蒸馏塔 4-丁二烯回收塔,5-第一精馏塔,6-第二精馏塔
轻柴油裂解生产烯烃方块流程图
25-26% 16-18%
11-12%
3. 石油裂解生产芳烃
苯、甲苯、二甲苯等芳烃是重要的化工原料,过去主要来自煤焦 油,现在则开发了由石油烃催化重整制取芳烃的路线。
原料:用全馏程石脑油(由原油经常压法直接蒸馏得到的沸点< 220oC的直馏汽油)于管式炉中,820oC下裂解生产芳烃。
原油经石油炼制工业的加工,主要是常压蒸馏(300-400oC以下) 分出石油气、石油醚、汽油、煤油、轻柴油等馏分。高沸点部 分再经减压蒸馏得到柴油、含蜡油等馏分。不能蒸出的部分称 做渣油。
各类油品的沸点范围、大致组成及用途
第二章 生产单体的原料路线
石油分馏产品: 石油气
原油 常压蒸馏
汽油 轻质油 煤油
1998年我国原油加工和主要石化产品生产能力(万t/年)
1. 石油的组成
石油主要存在于地球表面以下的一种有气味的从黄色到黑色的 粘稠液体。主要为碳、氢两种元素所组成的各种烃类混合物, 并含有少量的含氮、含硫、含氧化合物。
根据所含主要碳氢化合物类别,原油可分为石蜡基石油、环烷 基石油、芳香基石油以及混合基石油。我国所产石油大多数属 于石蜡基石油。
生产过程的裂解、分离与轻柴油裂解分离相似,同样得到聚合级 乙烯和丙烯,不同的是裂解原料组成不同。
主要特点:截取石脑油中C6-C9烃类(65-145oC馏分)进行加氢, 使其中烯烃被氢所饱和,含S、N、Cl的化合物被加氢而脱除。
在含铂催化剂作用,在重整反应器中于1. 4-1.7 MPa和520 ℃下反 应。烃类发生脱氢、环化、异构化、裂解,生成芳烃、氢气、液 化石油气和C5馏分,经分离后得芳烃浓度近50%的重整生成油。
石油有热裂化和催化裂化两种
第二章 生产单体的原料路线
热裂解
目的:提高汽油的产量
缺点:温度过高,发生结焦现象
催化裂解
目的:提高汽油的质量和产量
催化剂:硅酸铝,分子筛 (铝硅酸盐)
第二章 生产单体的原料路线
石油的催化重整
支链化:提高汽油质量 环化:生产芳烃 催化剂:Pt Re
2. 石油裂解生产烯烃
液态烃经高温裂解生成的产品成分复杂,包括氢、甲烷、乙炔、 乙烷、乙烯、丙烷、丙烯、裂解汽油等。
裂解装置可以分为以生产乙烯、丙烯、芳烃为主要产品的装置。 其生产规模通常以年产的乙烯量为标准,因此石油裂解装置工 业上称为“乙烯装置”,大型乙烯装置60万吨/年乙烯以上。
轻柴油裂解产品
石油裂解装置:裂解炉及一系列用于气体物料压缩和冷冻的压 缩机,一系列用来分离各种产品和副产品的蒸馏塔,许多热交 换器,分离油和水的装置,气体干燥,脱酸性气体等装置。还 有为利用回收能量的急冷锅炉和制冷装置冷箱。
第二章 生产单体的原料路线
第一节 国土资源与聚合物生产的原料
➢聚合物生产的主要原料为有机化合物,它主要来源于各种 资源,如石油、天然气、煤炭和各种动植物。单体原料来源 路线为:石油化工路线、煤炭路线和其它原料路线,
➢我国石油探明储量约940亿t,占世界第8位。天然气储量38 万亿m3居世界第16位。煤炭储量为7650亿t,占世界第3位。
➢对中国“地大物博”的概念重新加以认识,随着矿产开发 年代推移、深度的增加、品位下降,2000年以后我国部分矿 产将呈现下降趋势。
➢矿产资源是不可再生的。
第二节 从石油和天然气获得的石油化工原料路线
据统计,到1998年我国已建立了25个油气生产基地(其中海洋4个)。 全国年产原油1.6亿t,天然气223亿m3,分别居世界第5和第18位。 从1993年起,我国已成为石油净进口国。
由C4馏分制取丁二烯的途径: (1) 由裂解气分离得到的C4馏分中抽取丁二烯,萃取精馏方法。 (2) 用炼厂气或轻柴油裂解气C4馏分分离出来的丁烯为原料进 行氧化脱氢制取丁二烯。
萃取精馏是液体的混合物中加入较难挥发的第三组分溶剂,以增 大液体混合物中各组分的挥发度的差异,使挥发度相对地变大的 组分可由精馏塔顶馏出,挥发度相对地变小的组分则与加入的溶 剂在塔底流出分离。溶剂有:二甲基甲酰胺、乙腈、二甲亚砜等。
精制过程:用3-15%NaOH溶液洗涤裂解气脱除酸性气体(CO2、 H2S等)。炔烃(乙炔和甲基乙炔)一般用钯催化剂进行选择 性加氢转化为烯烃。大部分水蒸汽在气体压缩过程中已除去, 少量的水则用分子筛进行干燥。
分离过程:裂解气除含低级烯烃深冷分离 法)处理,将裂解气冷冻到-100℃左右,使除H2和CH4以外的低 级烃全部冷凝液化,再用精馏方法分离。