【塑料橡胶制品】塑料结构件设计规范
塑胶结构设计要求规范
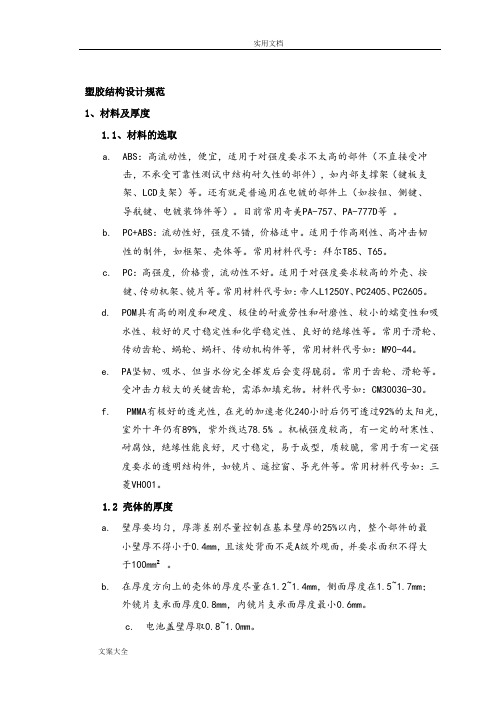
塑胶结构设计规范1、材料及厚度1.1、材料的选取a. ABS:高流动性,便宜,适用于对强度要求不太高的部件(不直接受冲击,不承受可靠性测试中结构耐久性的部件),如内部支撑架(键板支架、LCD支架)等。
还有就是普遍用在电镀的部件上(如按钮、侧键、导航键、电镀装饰件等)。
目前常用奇美PA-757、PA-777D等。
b. PC+ABS:流动性好,强度不错,价格适中。
适用于作高刚性、高冲击韧性的制件,如框架、壳体等。
常用材料代号:拜尔T85、T65。
c. PC:高强度,价格贵,流动性不好。
适用于对强度要求较高的外壳、按键、传动机架、镜片等。
常用材料代号如:帝人L1250Y、PC2405、PC2605。
d. POM具有高的刚度和硬度、极佳的耐疲劳性和耐磨性、较小的蠕变性和吸水性、较好的尺寸稳定性和化学稳定性、良好的绝缘性等。
常用于滑轮、传动齿轮、蜗轮、蜗杆、传动机构件等,常用材料代号如:M90-44。
e. PA坚韧、吸水、但当水份完全挥发后会变得脆弱。
常用于齿轮、滑轮等。
受冲击力较大的关键齿轮,需添加填充物。
材料代号如:CM3003G-30。
f. PMMA有极好的透光性,在光的加速老化240小时后仍可透过92%的太阳光,室外十年仍有89%,紫外线达78.5% 。
机械强度较高,有一定的耐寒性、耐腐蚀,绝缘性能良好,尺寸稳定,易于成型,质较脆,常用于有一定强度要求的透明结构件,如镜片、遥控窗、导光件等。
常用材料代号如:三菱VH001。
1.2 壳体的厚度a. 壁厚要均匀,厚薄差别尽量控制在基本壁厚的25%以内,整个部件的最小壁厚不得小于0.4mm,且该处背面不是A级外观面,并要求面积不得大于100mm²。
b. 在厚度方向上的壳体的厚度尽量在1.2~1.4mm,侧面厚度在1.5~1.7mm;外镜片支承面厚度0.8mm,内镜片支承面厚度最小0.6mm。
c. 电池盖壁厚取0.8~1.0mm。
d. 塑胶制品的最小壁厚及常见壁厚推荐值见下表。
塑胶产品结构设计规范

8.文件类型(4)1.品质体系类文件2.环境和职业安全体系类文件3.社会责任体系类文件文件编号版本编号 1生效日期2010-11-04 (盖受控印章处)产品二部塑胶产品结构设计规范制订申请部门会签批准产品中心运管计划处品质管理部销售中心工程部制造中心资材中心产品二部塑胶产品结构设计规范版本编号 1本页码第5 页共6页水印、热内应力、挠曲部份歪曲、颜色不同或不同透明度。
若厚胶的地方渐变成薄胶的是无可避免的话,应尽量设计成渐次的改变,并且在不超过壁厚3:1的比例下。
下图可供叁考:2、转角准则壁厚均一的要诀在转角的地方也同样需要,以免冷却时间不一致。
冷却时间长的地方就会有收缩现象,因而发生部件变形和挠曲。
此外,尖锐的圆角位通常会导致部件有缺陷及应力集中,集中应力的地方会在受负载或撞击的时候破裂。
较大的圆角提供了这种缺点的解决方法,不但减低应力集中的因素,且令流动的塑料流得更畅顺和成品脱模时更容易。
下图可供参考之用:根据产品要求,塑件材料主体壁厚不少于1.6mm。
下表为常用材料壁厚选择供参考:表6.1.2-1 常用塑胶材料的壁厚选择塑胶种类最小壁厚小型件壁厚中型件壁厚大型件壁厚ABS 0.75 1.25 1.6 3.2~5.4防火ABS 0.75 1.25 1.6 3.2~5.4PA66+玻纤0.45 0.75 1.6 2.4~3.2PMMA 0.8 1.5 2.2 4~6.5透明PC 0.95 1.8 2.3 3~4.5塑胶产品结构设计规范版本编号 1本页码第8 页共6页塑件的装配方式和实现手段,是必须在设计初期就要做出规划的环节,否则会影响到整个项目结构的实现性,甚至影响到PCB Layout和ID造型。
目前二部的塑胶外壳常用装配方式有三种:一、超声溶接:通过高频振动把能量传递到焊区,实现胶壳的融合。
适用于体型小、成型结构简单、料厚比较均匀、不需要拆卸的塑件件,但不适用于容易受超声影响的同材质塑件本体上装配有其他小件的结构,譬如开关结构、活动插脚结构等,容易在超声时造成小件和本体的熔接,活动功能无法实现。
塑胶结构设计规范
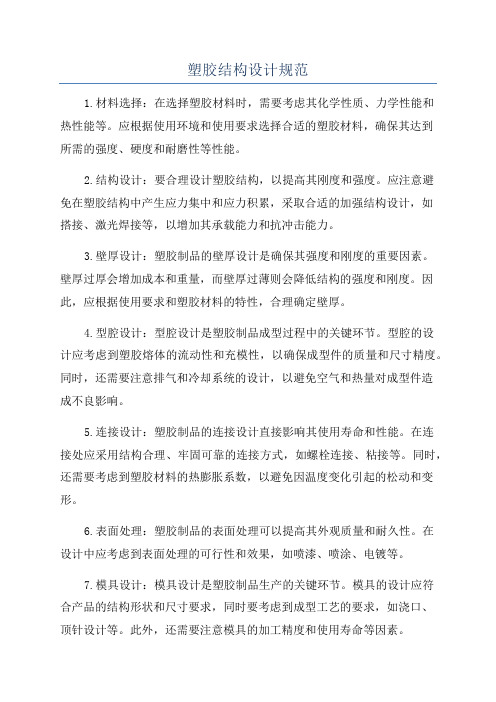
塑胶结构设计规范1.材料选择:在选择塑胶材料时,需要考虑其化学性质、力学性能和热性能等。
应根据使用环境和使用要求选择合适的塑胶材料,确保其达到所需的强度、硬度和耐磨性等性能。
2.结构设计:要合理设计塑胶结构,以提高其刚度和强度。
应注意避免在塑胶结构中产生应力集中和应力积累,采取合适的加强结构设计,如搭接、激光焊接等,以增加其承载能力和抗冲击能力。
3.壁厚设计:塑胶制品的壁厚设计是确保其强度和刚度的重要因素。
壁厚过厚会增加成本和重量,而壁厚过薄则会降低结构的强度和刚度。
因此,应根据使用要求和塑胶材料的特性,合理确定壁厚。
4.型腔设计:型腔设计是塑胶制品成型过程中的关键环节。
型腔的设计应考虑到塑胶熔体的流动性和充模性,以确保成型件的质量和尺寸精度。
同时,还需要注意排气和冷却系统的设计,以避免空气和热量对成型件造成不良影响。
5.连接设计:塑胶制品的连接设计直接影响其使用寿命和性能。
在连接处应采用结构合理、牢固可靠的连接方式,如螺栓连接、粘接等。
同时,还需要考虑到塑胶材料的热膨胀系数,以避免因温度变化引起的松动和变形。
6.表面处理:塑胶制品的表面处理可以提高其外观质量和耐久性。
在设计中应考虑到表面处理的可行性和效果,如喷漆、喷涂、电镀等。
7.模具设计:模具设计是塑胶制品生产的关键环节。
模具的设计应符合产品的结构形状和尺寸要求,同时要考虑到成型工艺的要求,如浇口、顶针设计等。
此外,还需要注意模具的加工精度和使用寿命等因素。
总之,塑胶结构设计规范是保证塑胶制品质量和性能的重要保证。
通过合理的材料选择、结构设计、壁厚设计等,可以提高塑胶结构的强度、刚度和耐久性,从而满足不同的使用需求。
塑胶产品结构设计规范
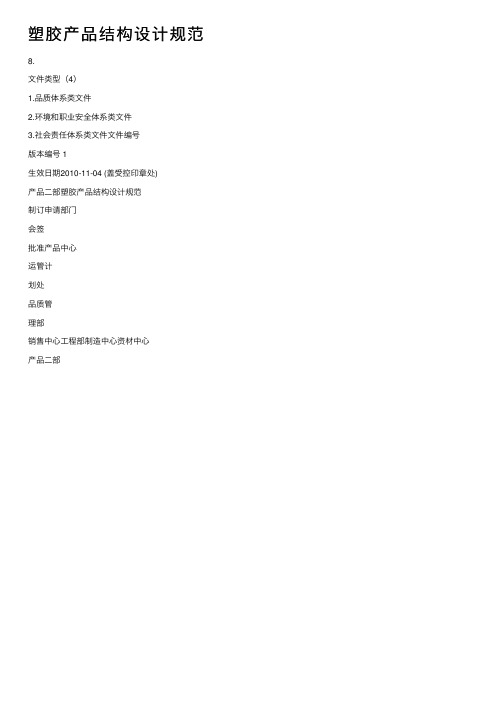
塑胶产品结构设计规范8.⽂件类型(4)1.品质体系类⽂件2.环境和职业安全体系类⽂件3.社会责任体系类⽂件⽂件编号版本编号 1⽣效⽇期2010-11-04 (盖受控印章处)产品⼆部塑胶产品结构设计规范制订申请部门会签批准产品中⼼运管计划处品质管理部销售中⼼⼯程部制造中⼼资材中⼼产品⼆部和灼热燃烧时间,t2+t3是否允许样品燃尽否否否是否允许燃烧颗粒或滴落物引燃脱脂棉否否是表6.1.1-2 球压温度评定PC 包胶PIN脚的包胶部分塑胶材料PC+ABS、PPO恒温箱测试温度95°125°125°表6.1.1-3 灼热丝燃烧评定要求3PCS,样条750±10℃(外壳厚度>0.2mm,650±10℃)判定标准30S内⽆可见⽕焰,实验样品落下的燃烧或灼热颗粒,应做到绢纸不得起⽕,松⽊板不得烧焦表6.1.1-4 胶壳跌落评定要求3PCS,2⾯/次,1M,⽔泥地⾯判定标准跌落后,外壳⽆破裂,⾼压测试能通过,电性正常6.1.2 壁厚选择塑件的壁厚要根据产品的具体要求、所选材料的性能、塑件外形的复杂程度及⼤⼩等因素确定,应尽量做到各部分壁厚均匀。
另外,需注意最⼩壁厚设计必须满⾜安规要求,具体可参考材料UL黄卡。
壁厚的选择应遵循以下原则:1、平⾯准则在⼤部份热融过程操作,包括挤压和固化成型,均⼀的壁厚是⾮常的重要的。
厚胶的地⽅⽐旁边薄胶的地⽅冷却得⽐较慢,并且在相接的地⽅表⾯在浇⼝凝固后出现收缩痕。
更甚者引致产⽣缩⽔印、热内应⼒、挠曲部份歪曲、颜⾊不同或不同透明度。
若厚胶的地⽅渐变成薄胶的是⽆可避免的话,应尽量设计成渐次的改变,并且在不超过壁厚3:1的⽐例下。
下图可供叁考:2、转⾓准则壁厚均⼀的要诀在转⾓的地⽅也同样需要,以免冷却时间不⼀致。
冷却时间长的地⽅就会有收缩现象,因⽽发⽣部件变形和挠曲。
此外,尖锐的圆⾓位通常会导致部件有缺陷及应⼒集中,集中应⼒的地⽅会在受负载或撞击的时候破裂。
塑料和橡胶制造业行业的规范制度

塑料和橡胶制造业行业的规范制度随着现代工业的发展,塑料和橡胶制造业在全球范围内得到了迅猛的增长。
然而,这一行业也面临着不少的挑战和问题,如环境污染、产品质量以及安全生产等。
为了确保行业的可持续发展,各国纷纷制定了一系列的规范制度,以引导和规范塑料和橡胶制造业的运营。
本文将重点探讨塑料和橡胶制造业行业的规范制度。
一、环境保护制度塑料和橡胶制造业的生产过程中会产生大量的废水、废气和固体废物,对环境造成严重影响。
为了减少对环境的污染,各国制定了一系列的环境保护制度。
这些制度主要包括:废水和废气排放标准、固体废物处理要求、环保设施的建设和使用等。
企业在生产过程中必须按照相关的法律法规进行排放控制和处理,以确保环境的安全和可持续发展。
二、产品质量标准制度塑料和橡胶制品广泛应用于各个领域,如建筑、汽车、电子等。
为了保证产品的质量和安全,各国制定了严格的产品质量标准制度。
这些制度包括产品的物理、化学性能、外观质量、尺寸精度等要求。
企业必须按照标准制度进行产品检测和认证,确保产品符合国家和地区的质量要求。
此外,一些国际组织还制定了全球统一的标准,以促进全球贸易的发展。
三、安全生产制度塑料和橡胶制造过程中存在一些潜在的安全风险,如化学品的使用、机械设备的操作等。
为了保障员工的安全,各国制定了一系列的安全生产制度。
这些制度包括工作场所的安全要求、危险源的识别和控制、职工安全教育培训等。
企业必须建立健全安全管理体系并进行定期的巡检和评估,以确保安全生产和员工的身体健康。
四、行业协会自律管理制度除了政府的法律法规外,塑料和橡胶制造业还建立了一些行业协会,以自律和管理行业的运营。
这些协会起着桥梁和纽带的作用,协调各个企业之间的合作和竞争关系。
行业协会制定了一系列的行业准则和行为规范,规范了企业的经营行为、产品质量、市场竞争等。
企业必须遵守协会的规定,并接受协会的监督和检查。
综上所述,塑料和橡胶制造业行业的规范制度涉及到环境保护、产品质量、安全生产和行业管理等方面。
【塑料橡胶制品】塑料扣子设计

(塑料橡胶材料)塑料扣子设计正文一、扣子的工艺分析和方案设计1、扣子的零件图2、扣子的工艺分析(1)扣子的材料制作扣子的材料是聚丙烯(PP)。
聚丙烯的机械性能因为比聚乙烯好,化学稳定性较好;聚丙烯是仅次于聚乙烯和聚氯乙烯的第三大通用塑料品种。
并且其原料易得,价格低廉,性能优良。
聚丙烯原料为无色、无味、无毒的固体。
不吸水,光泽好易着色,其流动性好。
但不耐磨,耐寒性差,光、氧作用下易降解成型时收缩大、成型性能好,易变形翘曲,柔软性好,有“铰链”的特性。
溢流间隙值为0.02mm左右。
冷却速度慢,必须充分冷却,模具设计应设有冷料穴和冷却系统不宜采用直接浇口注射否则会增加内应力,使收缩不均匀和取向明显。
应注意选择浇口位置,防止缩孔和变形。
(2)扣子的结构该电视机按钮的外形为圆盘形件,该扣子为圆盘形件,最外形尺寸为25mm,内环为21mm,并且对称分布四个小圆环直径为2mm。
(3)尺寸精度:零件图上所有未注尺寸为自由公差型腔:型腔:最外圈高度φ30-0.24、最外圈直径φ250-0.5.、内圈直径φ210-0·6、内圈高度10-0·26、型芯:对称分布孔的直径φ2+0.260、孔的高度2+0.260、(4)表面质量该塑件的表面质量要求无斑点、条纹、凹痕、起泡、变色等缺陷,及熔接痕.3、体积和密度计算塑件的质量是为了选用注射机及确定型腔数量。
经计算塑件的体积为V=811·69mm根据设计手册可查得增强聚丙烯的密度为p=1·04kg/cm,股塑件的质量W=Vp=0·844kg采用一模两件的模具结构,考虑其外形尺寸、注射时所需压力和工厂现设备等情况,初步选用注射机为XS—Z—30型。
根据以上分析,该塑件适合用注塑机构。
二、扣子的工艺设计与计算1、分型面的选择在模具设计中,分型面的选择和关键,他决定了模具的结构。
应根据分型面的选择原则和塑件的成型要求来选择分型面。
该塑件为扣子,表面质量要求较高。
橡胶塑料模具设计范例

第一节绪论随着我国橡胶制品工业的开展,橡胶制品的种类日益增多,产量日益扩大,促使着橡胶模具设计与制造由传统的经验设计到理论计算设计。
尤其是橡胶生产设备的不断提高与生产工艺的不断改良,橡胶模具越来越多,模具的制造水平与模具复杂程度也越来越高越精致。
高效率、自动化、精细、长寿命已经成为橡胶模具开展的趋势。
一、橡胶模具的分类橡胶模具根据模具结构和制品生产工艺的不同分为:压制成型模具、压铸成型模具、注射成型模具、挤出成型模具四大常用模具,以与一些生产特种橡胶制品的特种橡胶模具,如充气模具、浸胶模具等。
1.压制成型模具又称为普通压模。
它是将混炼过的、经加工成一定形状和称量过的半成品胶料直接放入模具中,而后送入平板硫化机中加压、加热。
胶料在加压、加热作用下硫化成型。
特点:模具结构简单,通用性强、使用面广、操作方便,故在橡胶模压制品中占有较大比例。
2.压铸成型模具又称传递式模具或挤胶法模具。
它是将混炼过的、形状简单的、限量一定的胶料或胶块半成品放入压铸模料腔中,通过压铸塞的压力挤压胶料,并使胶料通过浇注系统进入模具型腔中硫化定型。
特点:比普通压模复杂,适用于制作普通模压不能压制或勉强压制的薄壁、细长易弯曲的制品,以与形状复杂、难以加料的橡胶制品。
采用这种模具生产的制品致密性好、质量优越。
3.注射成型模具它是将预加热成塑性状态的胶料经注射模的浇注系统注入模具中定型硫化。
特点:结构复杂、适用于大型、厚壁、薄壁、形状复杂的制品。
生产效率高、质量稳定、能实现自动化生产。
4.挤出成型模具通过机头的成型模具制成各种截面形状的橡胶型材半成品,达到初步造型的目的,而后经过冷却定型输送到硫化罐内进展硫化或用作压模法所需要的预成型半成品胶料。
特点:生产效率高、质量稳定、能实现自动化生产。
二、成型设备模压法模具使用平板硫化机。
〔蒸汽硫化机:一般饱和蒸汽的最高压力可达0.6~0.8Mpa,硫化温度在158~168X围内。
电阻丝加热平板、油压平板硫化机〕压铸法模具使用压铸机。
塑料结构件设计规范

第一章 塑料制品的结构设计塑料制品的结构设计又称塑料制品的功能特性设计或塑料制品的工艺性。
§1.1 塑料制品设计的一般程序和原则1.1.1 塑料制品设计的一般程序1、详细了解塑料制品的功能、环境条件和载荷条件2、选定塑料品种3、制定初步设计方案,绘制制品草图(形状、尺寸、壁厚、加强筋、孔的位置等)4、样品制造、进行模拟试验或实际使用条件的试验5、制品设计、绘制正规制品图纸6、编制文件,包括塑料制品设计说明书和技术条件等。
1.1.2 塑料制品设计的一般原则1、在选料方面需考虑:(1) 塑料的物理机械性能,如强度、刚性、韧性、弹性、吸水性以及对应力的敏感性等;(2) 塑料的成型工艺性,如流动性、结晶速率,对成型温度、压力的敏感性等;(3) 塑料制品在成型后的收缩情况,及各向收缩率的差异。
2、在制品形状方面:能满足使用要求,有利于充模、排气、补缩,同时能适应高效冷却硬化(热塑性塑料制品)或快速受热固化(热固性塑料制品)等。
3、在模具方面:应考虑它的总体结构,特别是抽芯与脱出制品的复杂程度。
同时应充分考虑模具零件的形状及其制造工艺,以便使制品具有较好的经济性。
4、在成本方面:要考虑注射制品的利润率、年产量、原料价格、使用寿命和更换期限,尽可能降低成本。
§1.2 塑料制品的收缩塑料制品在成型过程中存在尺寸变小的收缩现象,收缩的大小用收缩率表示。
%10000⨯-=L L L S 式中S ——收缩率;L 0——室温时的模具尺寸;L ——室温时的塑料制品尺寸。
影响收缩率的主要因素有: (1) 成型压力。
型腔内的压力越大,成型后的收缩越小。
非结晶型塑料和结晶型塑料的收缩率随内压的增大分别呈直线和曲线形状下降。
(2) 注射温度。
温度升高,塑料的膨胀系数增大,塑料制品的收缩率增大。
但温度升高熔料的密度增大,收缩率反又减小。
两者同时作用的结果一般是,收缩率随温度的升高而减小。
(3) 模具温度。
通常情况是,模具温度越高,收缩率增大的趋势越明显。
塑胶件结构设计规范

产品设计者在选定尺寸公差时要考虑使用之塑料材料、产品形状及将来之使用条件等。 随着公差的严格要求,其制造加工精度与模具价格亦相对提高,所以产品设计者于图面上记 入公差时,要审慎的设定适用于此公差的使用条件。因此,产品设计者所设定之总公差应该 包含了使用条件和环境条件下的尺寸变化。
关键词 塑料零件、壁厚、脱模斜度、加强筋、材料选择 1、零件的形状应尽量简单、合理、便于成型
1.1 在保证使用要求前提下,力求简单、便于脱模,尽量避免或减少抽芯机构,如采用下 图例中(b)的结构,不仅可大大简化模具结构,便于成型,且能提高生产效率。
1.2 利用转换区的方法来防止突然的递变。
1.3 利用肋及浮凸物和铸空法使设计更合理。 1.4 转角处用圆弧过渡。
聚苯乙烯、有机玻璃 热固性塑料
脱模斜度 30′~1° 40′~1°30′ 50′~2° 20′~1°
在具体选择时,还应注意以下几个问题: 3.1 凡塑件精度要求高时,应采用较小的脱模斜度; 3.2 凡较高、较大的尺寸,应选用较小的脱模斜度; 3.3 塑件形状复杂的、不易脱模的应选用较大的脱模斜度; 3.4 塑件的收缩率大的应选用较大的斜度值; 3.5 塑件壁较厚时,会使成形收缩增大,脱模斜度应采用较大的数值; 3.6 如果要求脱模后塑件保持在型芯的一边,那么塑件的内表面的脱模斜度可选的比外表
塑胶零件结构设计规范
摘要 随着公司的不断发展和产品的增加,为了造型的需要产品结构件中塑料零件用 的越来越多。那么在具体设计塑料零件的结构时需要考虑哪些方面的问题?怎样合理地设计 塑料零件的结构?如何选择塑料零件的材料?壁厚选择多少合适?等等。本文对这些具体问 题进行了详细的总结。希望对大家在今后的设计中有所帮助并希望大家一起来补充完善。
塑料制品设计原则-工程
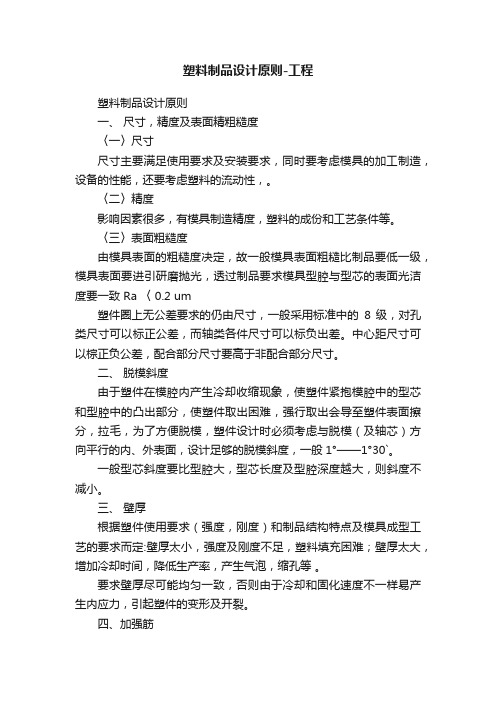
塑料制品设计原则-工程塑料制品设计原则一、尺寸,精度及表面精粗糙度〈一〉尺寸尺寸主要满足使用要求及安装要求,同时要考虑模具的加工制造,设备的性能,还要考虑塑料的流动性,。
〈二〉精度影响因素很多,有模具制造精度,塑料的成份和工艺条件等。
〈三〉表面粗糙度由模具表面的粗糙度决定,故一般模具表面粗糙比制品要低一级,模具表面要进引研磨抛光,透过制品要求模具型腔与型芯的表面光洁度要一致 Ra 〈 0.2 um塑件圈上无公差要求的仍由尺寸,一般采用标准中的8 级,对孔类尺寸可以标正公差,而轴类各件尺寸可以标负出差。
中心距尺寸可以棕正负公差,配合部分尺寸要高于非配合部分尺寸。
二、脱模斜度由于塑件在模腔内产生冷却收缩现象,使塑件紧抱模腔中的型芯和型腔中的凸出部分,使塑件取出困难,强行取出会导至塑件表面擦分,拉毛,为了方便脱模,塑件设计时必须考虑与脱模(及轴芯)方向平行的内、外表面,设计足够的脱模斜度,一般1°——1°30`。
一般型芯斜度要比型腔大,型芯长度及型腔深度越大,则斜度不减小。
三、壁厚根据塑件使用要求(强度,刚度)和制品结构特点及模具成型工艺的要求而定:壁厚太小,强度及刚度不足,塑料填充困难;壁厚太大,增加冷却时间,降低生产率,产生气泡,缩孔等。
要求壁厚尽可能均匀一致,否则由于冷却和固化速度不一样易产生内应力,引起塑件的变形及开裂。
四、加强筋设计原则:〈一〉中间加强筋要低于外壁0.5 mm 以上,使支承面易于平直。
〈二〉应避免或减小塑料的局部聚积。
〈三〉筋的排例要顺着在型腔内的流动方向。
五、支承面塑件一般不以整个平面作为支承面,而取而代之以边框,底脚作支承面。
六、圆角要求塑件防有转角处都要以圆角(圆弧)过渡,因尖角容易应力集中。
塑件有圆角,有利于塑料的流动充模及塑件的顶出,塑件的外观好,有利于模具的强度及寿命。
七、孔(槽)塑件的孔三种成型加工方法:(1)模型直接模塑出来。
(2)模塑成盲孔再钻孔通。
橡胶和塑料的规章制度
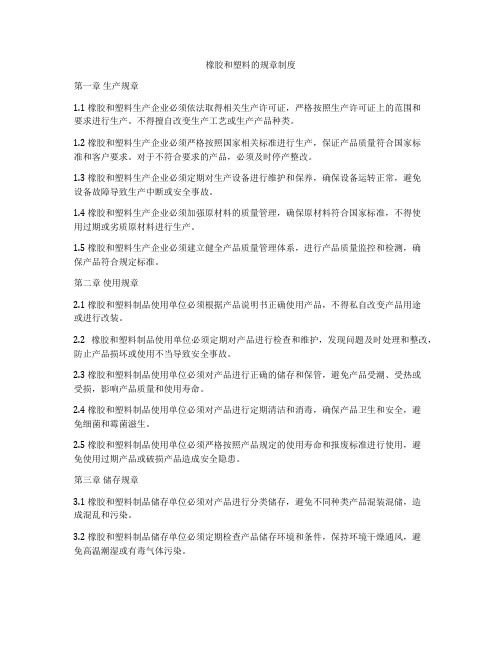
橡胶和塑料的规章制度第一章生产规章1.1 橡胶和塑料生产企业必须依法取得相关生产许可证,严格按照生产许可证上的范围和要求进行生产。
不得擅自改变生产工艺或生产产品种类。
1.2 橡胶和塑料生产企业必须严格按照国家相关标准进行生产,保证产品质量符合国家标准和客户要求。
对于不符合要求的产品,必须及时停产整改。
1.3 橡胶和塑料生产企业必须定期对生产设备进行维护和保养,确保设备运转正常,避免设备故障导致生产中断或安全事故。
1.4 橡胶和塑料生产企业必须加强原材料的质量管理,确保原材料符合国家标准,不得使用过期或劣质原材料进行生产。
1.5 橡胶和塑料生产企业必须建立健全产品质量管理体系,进行产品质量监控和检测,确保产品符合规定标准。
第二章使用规章2.1 橡胶和塑料制品使用单位必须根据产品说明书正确使用产品,不得私自改变产品用途或进行改装。
2.2 橡胶和塑料制品使用单位必须定期对产品进行检查和维护,发现问题及时处理和整改,防止产品损坏或使用不当导致安全事故。
2.3 橡胶和塑料制品使用单位必须对产品进行正确的储存和保管,避免产品受潮、受热或受损,影响产品质量和使用寿命。
2.4 橡胶和塑料制品使用单位必须对产品进行定期清洁和消毒,确保产品卫生和安全,避免细菌和霉菌滋生。
2.5 橡胶和塑料制品使用单位必须严格按照产品规定的使用寿命和报废标准进行使用,避免使用过期产品或破损产品造成安全隐患。
第三章储存规章3.1 橡胶和塑料制品储存单位必须对产品进行分类储存,避免不同种类产品混装混储,造成混乱和污染。
3.2 橡胶和塑料制品储存单位必须定期检查产品储存环境和条件,保持环境干燥通风,避免高温潮湿或有毒气体污染。
3.3 橡胶和塑料制品储存单位必须定期清点库存,及时处理过期产品或破损产品,避免影响整体产品质量和安全。
3.4 橡胶和塑料制品储存单位必须加强安全管理措施,设置防火、防爆、防盗等设施和措施,确保产品储存安全。
3.5 橡胶和塑料制品储存单位必须建立健全进出库管理制度,实行严格的出入库登记和审查,保证产品非法流失或盗窃。
9塑料制品嵌件结构的设计(精)

(3)使用嵌件的缺点 :嵌件的设置往往使模具结构复杂化,成型周期延长,制造
成本增加,难于实现自动化生产等问题。
9
塑料制品嵌件结构的设计
塑料制品嵌件结构的设计
嵌件周围覆盖的塑料层,有其最低要求,以防止冷却过程中收缩破裂。嵌件周围塑 料层厚度的推荐值如表2-9-1所示。常见金属嵌件的形式如表2-9-2所示。
Ⅺ
支 承 面 结 构 设 计
目
塑 件 的 尺 寸 及 精 度
tttl
的 设 计
孔 结 构
录
9
塑料制品嵌件结构的设计
塑料制品嵌件结构的设计
塑件内部镶嵌有金属、玻璃、木材、纤维、纸张、橡胶或已
(1)什么是嵌件?
成型的塑件等称为嵌件。
(2)使用嵌件的目的: 在于提高塑件的强度,满足塑件某些特殊要求,如导电、
2.0mm的凸环,有利于嵌件在模具中的固定,图2-9-3(b)是将嵌件突出塑件外,
用模具定位孔保证嵌件定位的结构,图2-9-3(c)所示为确保嵌件能精确地固定于 模腔中的结构,嵌件的定位部分不应低于IT8级精度,图2-9-3(d)为外形呈六角形 或其它形状的嵌件,须将其定位部分设计成圆形,以利于模具制造。对细长杆状 嵌件,须用销轴支承,以防止料流冲弯嵌件,如图2-9-3(e)所示。
9
塑料制品嵌件结构的设计
塑料制品嵌件结构的设计要点
图d板形嵌件,切开、孔眼、局部弯曲;
图f 针状嵌件,折弯、砸扁其中一段来固定。
THANKS!!!
型嵌件受力很小时,可采用菱形滚花,而不需开槽,其结构如图2-9-1(a)所示。对板
片状嵌件,可采用图2-9-1 (b)所示的嵌合方法。圆杆形嵌件,可将其中间压扁起嵌合
塑料结构件设计要求规范
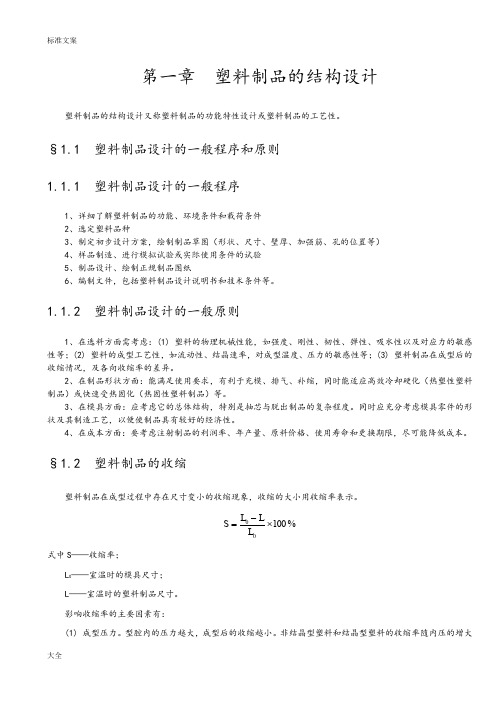
第一章 塑料制品的结构设计塑料制品的结构设计又称塑料制品的功能特性设计或塑料制品的工艺性。
§1.1 塑料制品设计的一般程序和原则 1.1.1 塑料制品设计的一般程序1、详细了解塑料制品的功能、环境条件和载荷条件2、选定塑料品种3、制定初步设计方案,绘制制品草图(形状、尺寸、壁厚、加强筋、孔的位置等)4、样品制造、进行模拟试验或实际使用条件的试验5、制品设计、绘制正规制品图纸6、编制文件,包括塑料制品设计说明书和技术条件等。
1.1.2 塑料制品设计的一般原则1、在选料方面需考虑:(1) 塑料的物理机械性能,如强度、刚性、韧性、弹性、吸水性以及对应力的敏感性等;(2) 塑料的成型工艺性,如流动性、结晶速率,对成型温度、压力的敏感性等;(3) 塑料制品在成型后的收缩情况,及各向收缩率的差异。
2、在制品形状方面:能满足使用要求,有利于充模、排气、补缩,同时能适应高效冷却硬化(热塑性塑料制品)或快速受热固化(热固性塑料制品)等。
3、在模具方面:应考虑它的总体结构,特别是抽芯与脱出制品的复杂程度。
同时应充分考虑模具零件的形状及其制造工艺,以便使制品具有较好的经济性。
4、在成本方面:要考虑注射制品的利润率、年产量、原料价格、使用寿命和更换期限,尽可能降低成本。
§1.2 塑料制品的收缩塑料制品在成型过程中存在尺寸变小的收缩现象,收缩的大小用收缩率表示。
%10000⨯-=L LL S 式中S ——收缩率;L 0——室温时的模具尺寸; L ——室温时的塑料制品尺寸。
影响收缩率的主要因素有:(1) 成型压力。
型腔内的压力越大,成型后的收缩越小。
非结晶型塑料和结晶型塑料的收缩率随内压的增大分别呈直线和曲线形状下降。
(2) 注射温度。
温度升高,塑料的膨胀系数增大,塑料制品的收缩率增大。
但温度升高熔料的密度增大,收缩率反又减小。
两者同时作用的结果一般是,收缩率随温度的升高而减小。
(3) 模具温度。
通常情况是,模具温度越高,收缩率增大的趋势越明显。
第七类塑料橡胶制品

教学内容课题名称3-1第七类塑料橡胶制品负责人签字授课班级授课时间教学方法讲授法、小组讨论法、演示法教学目标1、了解塑料橡胶商品学知识;2、掌握聚合物及其化学改性塑料归类原则;掌握橡胶制品归类细则3、学会运用本节所学归类思路对相关产品准确归类教学重点塑料聚合物(均聚、共聚)归类原则授课类型理实一体时间分配【导入】常见塑料种类制品简介【新授】知识点一初级形状塑料聚合物归类原则第39章包括塑料的初级形状(如液状、糊状、粒状、粉片及类似形状,参见本章章注六),也包括塑料的废碎料、下脚料及各种塑料的半制成品和制成品(如卫生5 25洁具、塑料糊墙物、塑料衣服及衣着附件零件、装饰品等)。
但对于某些产品即使是塑料制成的,但不归本章的,参见本章章注二本章共有26个品目,并按加工程度由低到高排列:初级形状的塑料…………………………………………3901----3914塑料的废碎料及下脚料 (3915)塑料的半制成品……………………………………… 3916---3921塑料的制成品……………………………………… 3922 ----3926(1)初级形状①液体及糊状,包括分散体(乳浊液及悬浮液)及溶液②不规则形状的块、团、粉(包括压型粉)、颗粒、粉片及类似的散装形状。
均聚—单体单元≥95%(2)聚合物分类共聚—单体单元<95%具体归类原则同品目相加;按重量最大归类;同等数量,从后归类(有列明归列明,无列名有其他归其他,无其他归本身)(1)均聚,是指其中一种单体单元的含量要≥95%,一般以“聚XX”形式出现。
例1:聚丙烯,颗粒状答案:3902.1000解释:颗粒状说明是初级形状,聚丙烯,说明丙烯含量为100%,则归3902.1000。
例2:乙烯----丙烯共聚物,其中丙烯占96%,乙烯占4%,液体状答案:3902.1000解释:液体状,说明是初级形状,只要有一种单体单元的含量≥95%,就必须要按均聚的来归。
(2)共聚,是指由两种及以上的单体单元构成,其中两种及以上的单体单元相加之和要≥95%,但是没有一种单体单元的含量≥95%。
塑料结构件设计规范教材

塑料结构件设计规范教材作为现代工业生产中的重要装备,塑料制品在许多领域都得到了广泛的应用。
而其中的塑料结构件则是塑料制品中最为重要的组成部分之一。
塑料结构件以其高效、精准、灵活等特点而广受欢迎,但为了在工业生产中获得良好的效果和使用寿命,需要对其设计进行规范。
本文将主要讨论塑料结构件设计规范教材的相关问题。
一、塑料结构件设计的标准化在塑料结构件设计中,标准化是十分必要的。
具体来说,标准化设计方案能够对生产中的产品设计、制造、检验等环节进行规范,降低产品的生产成本和交付周期,并提高产品的质量和可靠性。
二、塑料结构件设计中的基本原理塑料结构件设计中的基本原理有多个,例如传热原理、机械原理、材料科学原理等。
这些原理的掌握对于塑料结构件的设计和生产至关重要,因为只有对材料、物理力学、挤出成型等多个环节进行充分的考虑,才能够制造出质量稳定的产品。
三、塑料结构件设计的工艺规范塑料结构件的工艺规范包括了塑料成型工艺的要求、成型设备的配置和选择、成型部件等相关问题。
塑料结构件设计的成功与否取决于工艺的是否规范,因此对塑料成型工艺的了解和掌握也是塑料结构件设计中的重要部分。
四、塑料结构件设计中的重点问题塑料结构件的设计中还有一些重点问题,例如材料的选择、模具的设计、部件的接口设计、塑料件颜色的配色以及表面处理等。
这些问题的解决需要充分考虑到产品的使用环境和特殊要求,因此需要在设计时进行充分的研究和考虑。
五、塑料结构件设计的开发流程整个塑料结构件的设计开发流程包含了塑料成型工艺的规划、模具制作、样品验证、批量生产等流程,每个环节都有其重要性。
因此对于任何塑料结构件的开发设计,都需要充分考虑整个流程,保证各个环节的顺利进行,并达到设计要求。
六、塑料结构件设计中的注意事项在塑料结构件设计的过程中,还有一些需要注意的事项。
例如需要充分考虑产品的使用环境和寿命要求,设计充分考虑材料的性能和目标市场需求,预先做好样品的合格验证工作等。
塑胶结构设计规范

3-24W,USB输出: 直伸式(分模线在R角处)结构,方形R角 外形(推荐选用)
3-24W ,DC线输出: 直伸式(分模线在R角处)结构,方形R角外 形(推荐选用)
电源胶壳常规结构设计11
3.14 立式(弹片结构)胶壳PCB固定结构设计:
X(PCB 高度)
A
面壳
PCB B
01(此筋条通常2根即可,应 根据胶壳实际大小增加数量)
面壳
02
M(胶壳分型面 到底部筋条) G1(装配间隙)
PCB
B
元件面筋条
4.0-6.0 10.0MAX
引脚面筋条
A
0.15(单边间隙)
Detail 02 立式胶壳面壳&底 Scale 3:1 壳PCB卡槽尺寸
4.0-6.0
电源胶壳常规结构设计15 常规A型USB插头与胶壳(超声波封焊)配合结构尺寸设计:单位:mm
电源胶壳常规结构设计16
电源胶壳常规结构设计17 常规AC座与胶壳配合尺寸设计:
电源胶壳常规结构设计18 3.22 车充设计标准: 3.22.1 外形尺寸设计标准(除特殊要求外,常规车充外形尺寸标准参考如下图):
3.1.7 产品装配结构设计: 按功率定义两种结构
1) 24W以下功率(含):采用弹片和引线两种标准结构(主推弹片结构)
3.1.7 产品装配结构设计:
2) 30-90W功率:采用引线标准结构。因PCB LAYOUT尺寸长宽比例问题,此功 率段产品外观定义为正方型结构;
3.1.8 产品外观定义
塑胶产品结构设计准则

一、塑胶产品结构设计准则-壁厚
常用热塑性塑料的壁厚设计参考表 :
热塑性塑料 ABS PC PC+ABS POM PMMA PA PS
最薄mm 0.8 0.3 0.5 0.4 0.6 0.4 0.8
平均mm 2.3 2.4 2.4 1.6 2.4 1.6 1.6
最厚mm 3.2 9.5 6.4 3.2 6.4 3.2 6.4
➢ 成本考虑对于超过4mm的壁厚,易采用发泡成型或氮气辅助射出。 ➢ 由于UL安规要求,通常胶厚不易太薄(<1.2mm),太薄须使用特殊防火级别材料,会导致材料成
本大幅度上升。
➢ DSC设计胶厚通常取1.5mm。
二、塑胶产品结构设计准则-加强筋
基本设计守则: A. 加强筋可有效增加产品的刚性和强度而无需大幅增加产品切面面积,对一些经常受到压力、扭力、
孔洞边缘要求: 为便于尺寸管理及模具加工洞孔的边缘应预留最少0.2mm的直边,如下图参考:
1
五、塑胶产品结构设计准则-扣位 ( Snap Joints )
扣位操作原理: 当两件零件扣上时,其中一件零件的勾形伸出部份被相接零件的凸缘部份推开,直至凸缘部份 完结为止;及後,藉着塑胶的弹性,勾形伸出部份即时复位,其後面的凹槽亦即时被相接零件 的凸缘部份嵌入,此倒扣位置立时形成互相扣着的状态,扣位的操作原理图如下。
一、塑胶产品结构设计准则-壁厚
B. 转角位的设计准则亦适用於悬梁式扣位。因这种扣紧方式是需要将悬梁臂弯曲嵌入,转角位置的设 计图说明如果转角弧位R太小时会引致其应力集中系数(Stress Concentration Factor)过大,因此, 产品弯曲时容易折断,弧位R太大的话则容易出现收缩纹和空洞。因此,圆弧位和壁厚是有一定的 比例。一般介乎0.2至0.6T之间,理想数值是在0.5T左右。
【塑料橡胶制品】塑料垃圾桶通用技术条件
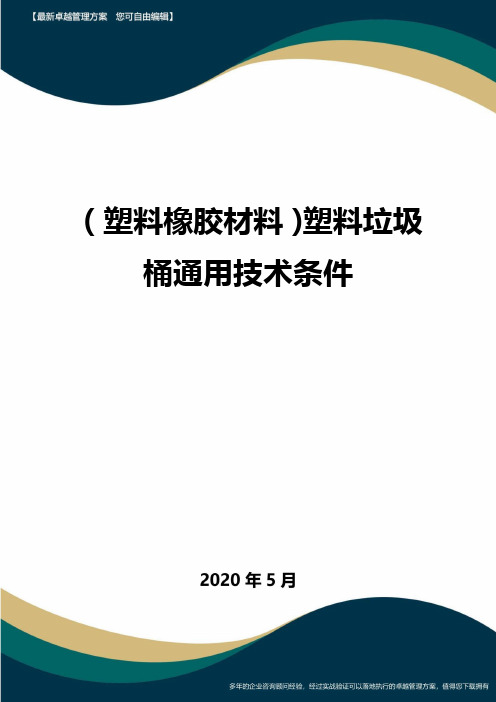
(塑料橡胶材料)塑料垃圾桶通用技术条件中华人民共和国城镇建设行业标准××××-××-××发布目次前言II1范围12规范性引用文件13术语和定义14产品分类及结构15型号与标记26技术要求27试验方法68检验规则89标志、包装、运输10附录A(资料性附录)机械性能试验记录表11 参考文献14前言本标准的附录A为资料性附录。
本标准由建设部标准定额研究所提出。
本标准由建设部城镇环境卫生标准技术归口单位归口。
本标准负责起草单位:本标准参加起草单位:本标准主要起草人:塑料垃圾桶通用技术条件1 范围本标准规定了塑料垃圾桶的分类、技术要求、试验方法、检验规则及标志、包装、运输。
本标准适用于容积为120L和240L的两轮移动式塑料垃圾桶。
2 规范性引用文件下列文件中的条款通过本标准的引用而成为本标准的条款。
凡是注日期的引用文件,其随后所有的修改单(不包括勘误的内容)或修订版均不适用于本标准,然而,鼓励根据本标准达成协议的各方研究是否可使用这些文件的最新版本。
凡是不注日期的引用文件,其最新版本适用于本标准。
GB5470塑料冲击脆化温度试验方法GB/T1033塑料密度和相对密度试验方法GB/T1043-1993硬质塑料简支梁冲击试验方法GB/T1633-2000热塑性塑料维卡软化温度(VST)的测定GB/T2411塑料邵氏硬度试验方法GB/T2828.1计数抽样检验程序第1部分:按接收质量限(AQL)检索的逐批检验抽样计划GB/T16422.2-1999塑料实验室光源暴露试验方法第2部分:氙弧灯GB/T19095城市生活垃圾分类标志3 术语和定义下列术语和定义适用于本标准。
塑料垃圾桶plasticwastecontainer能收纳和存放一定量生活垃圾的带盖(可选配脚踏翻盖机构)并可举升装车的环境卫生塑料容器。
额定容积nominalvolume塑料垃圾桶标注的容积。
塑料产品设计规范
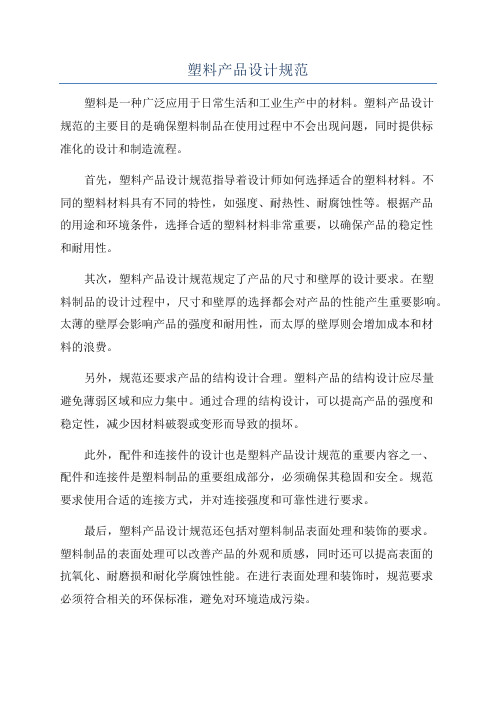
塑料产品设计规范塑料是一种广泛应用于日常生活和工业生产中的材料。
塑料产品设计规范的主要目的是确保塑料制品在使用过程中不会出现问题,同时提供标准化的设计和制造流程。
首先,塑料产品设计规范指导着设计师如何选择适合的塑料材料。
不同的塑料材料具有不同的特性,如强度、耐热性、耐腐蚀性等。
根据产品的用途和环境条件,选择合适的塑料材料非常重要,以确保产品的稳定性和耐用性。
其次,塑料产品设计规范规定了产品的尺寸和壁厚的设计要求。
在塑料制品的设计过程中,尺寸和壁厚的选择都会对产品的性能产生重要影响。
太薄的壁厚会影响产品的强度和耐用性,而太厚的壁厚则会增加成本和材料的浪费。
另外,规范还要求产品的结构设计合理。
塑料产品的结构设计应尽量避免薄弱区域和应力集中。
通过合理的结构设计,可以提高产品的强度和稳定性,减少因材料破裂或变形而导致的损坏。
此外,配件和连接件的设计也是塑料产品设计规范的重要内容之一、配件和连接件是塑料制品的重要组成部分,必须确保其稳固和安全。
规范要求使用合适的连接方式,并对连接强度和可靠性进行要求。
最后,塑料产品设计规范还包括对塑料制品表面处理和装饰的要求。
塑料制品的表面处理可以改善产品的外观和质感,同时还可以提高表面的抗氧化、耐磨损和耐化学腐蚀性能。
在进行表面处理和装饰时,规范要求必须符合相关的环保标准,避免对环境造成污染。
总之,塑料产品设计规范对确保塑料制品的质量和使用安全非常重要。
遵守规范可以帮助设计师选择适合的塑料材料、优化产品的尺寸和结构设计以及保证配件和连接件的质量。
只有遵守规范并进行有效的质量控制,才能生产出具有高质量和可靠性的塑料产品。
塑料橡胶行业标准

塑料橡胶行业标准随着工业化的快速发展,塑料橡胶行业成为现代社会中不可或缺的重要组成部分。
塑料橡胶制品广泛应用于各个领域,如建筑、电子、汽车、医疗等多个行业。
为了确保塑料橡胶产品的质量、安全和可持续发展,制定相应的行业标准十分必要。
本文将就塑料橡胶行业标准进行探讨,包括原料选择、生产工艺、质量控制等方面。
一、原料选择在塑料橡胶制品的生产中,原料的选择直接关系到产品的质量和性能。
因此,制定严格的原料选择标准是非常重要的。
首先,需要明确原料的种类和适用范围。
不同种类的塑料橡胶应使用不同的原料,并且需要考虑其与其他材料的兼容性。
其次,要求原料符合环保要求,避免使用有害物质。
此外,还需考虑原料的成本和供应稳定性等因素。
二、生产工艺塑料橡胶制品的生产工艺也需要遵守一定的规范和标准。
首先,需要确保生产设备的合理选择和使用。
不同类型的塑料橡胶制品可能需要不同的生产设备,例如挤出机、注塑机、压力机等。
其次,要求生产工艺流程的合理规划和操作规范。
包括原料的配比、加工温度、压力控制等参数的设定,以及生产过程中的质量检验和记录。
三、质量控制塑料橡胶制品的质量控制是确保产品符合规范要求的关键。
在质量控制方面,可以采用多种方法和标准进行监控和检测。
首先,可以通过抽样和批次检验来判断产品的质量状况。
抽样时应注意样品的代表性和检测方法的准确性。
其次,可以制定产品性能测试标准,如强度、硬度、耐磨性等。
同时,还需要制定外观检验标准,包括色泽、表面光洁度等。
四、环境保护塑料橡胶行业对环境的影响也是不容忽视的。
为了减少对环境的污染和资源浪费,需要建立相应的环境管理措施和标准。
首先,应加强废水、废气和固废的处理和排放标准。
合理利用再生资源,减少对原材料的依赖。
其次,要求生产企业遵守环境法律法规,进行环境影响评估和监督管理。
通过科学的环境管理,保护生态环境,促进可持续发展。
五、标准宣传和实施为了确保塑料橡胶行业标准的有效实施,需要进行广泛的宣传和培训。
- 1、下载文档前请自行甄别文档内容的完整性,平台不提供额外的编辑、内容补充、找答案等附加服务。
- 2、"仅部分预览"的文档,不可在线预览部分如存在完整性等问题,可反馈申请退款(可完整预览的文档不适用该条件!)。
- 3、如文档侵犯您的权益,请联系客服反馈,我们会尽快为您处理(人工客服工作时间:9:00-18:30)。
(塑料橡胶材料)塑料结构件设计规范塑料制品的结构设计塑料制品的结构设计又称塑料制品的功能特性设计或塑料制品的工艺性。
§1.1塑料制品设计的一般程序和原则1.1.1塑料制品设计的一般程序1、详细了解塑料制品的功能、环境条件和载荷条件2、选定塑料品种3、制定初步设计方案,绘制制品草图(形状、尺寸、壁厚、加强筋、孔的位置等)4、样品制造、进行模拟试验或实际使用条件的试验5、制品设计、绘制正规制品图纸6、编制文件,包括塑料制品设计说明书和技术条件等。
1.1.2塑料制品设计的一般原则1、在选料方面需考虑:(1)塑料的物理机械性能,如强度、刚性、韧性、弹性、吸水性以及对应力的敏感性等;(2)塑料的成型工艺性,如流动性、结晶速率,对成型温度、压力的敏感性等;(3)塑料制品在成型后的收缩情况,及各向收缩率的差异。
2、在制品形状方面:能满足使用要求,有利于充模、排气、补缩,同时能适应高效冷却硬化(热塑性塑料制品)或快速受热固化(热固性塑料制品)等。
3、在模具方面:应考虑它的总体结构,特别是抽芯与脱出制品的复杂程度。
同时应充分考虑模具零件的形状及其制造工艺,以便使制品具有较好的经济性。
4、在成本方面:要考虑注射制品的利润率、年产量、原料价格、使用寿命和更换期限,尽可能降低成本。
§1.2塑料制品的收缩塑料制品在成型过程中存在尺寸变小的收缩现象,收缩的大小用收缩率表示。
式中S——收缩率;L0——室温时的模具尺寸;L——室温时的塑料制品尺寸。
影响收缩率的主要因素有:(1)成型压力。
型腔内的压力越大,成型后的收缩越小。
非结晶型塑料和结晶型塑料的收缩率随内压的增大分别呈直线和曲线形状下降。
(2)注射温度。
温度升高,塑料的膨胀系数增大,塑料制品的收缩率增大。
但温度升高熔料的密度增大,收缩率反又减小。
两者同时作用的结果一般是,收缩率随温度的升高而减小。
(3)模具温度。
通常情况是,模具温度越高,收缩率增大的趋势越明显。
(4)成型时间。
成型时保压时间一长,补料充分,收缩率便小。
与此同时,塑料的冻结取向要加大,制品的内应力亦大,收缩率也就增大。
成型的冷却时间一长,塑料的固化便充分,收缩率亦小。
(5)制品壁厚。
结晶型塑料(聚甲醛除外)的收缩率随壁厚的增加而增加,而非结晶型塑料中,收缩率的变化又分下面几种情况:ABS和聚碳酸酯等的收缩率不受壁厚的影响;聚乙烯、丙烯腈—苯乙烯、丙烯酸类等塑料的收缩率随壁厚的增加而增加;硬质聚氯乙烯的收缩率随壁厚的增加而减小。
(6)进料口尺寸。
进料口尺寸大,塑料制品致密,收缩便小。
(7)玻璃纤维等的填充量。
收缩率随填充量的增加而减小。
表2-1、表2-2、表2-3为常用塑料的成型收缩率。
§1.3脱模斜度脱模斜度:为便于脱模,塑料制品壁在出模方向上应具有倾斜角度α,其值以度数表示(参见表2-4)。
1.3.1脱模斜度确定要点(1)制品精度要求越高,脱模斜度应越小。
(2)尺寸大的制品,应采用较小的脱模斜度。
(3)制品形状复杂不易脱模的,应选用较大的斜度。
(4)制品收缩率大,斜度也应加大。
(5)增强塑料宜选大斜度,含有自润滑剂的塑料可用小斜度。
(6)制品壁厚大,斜度也应大。
(7)斜度的方向。
内孔以小端为准,满足图样尺寸要求,斜度向扩大方向取得;外形则以大端为准,满足图样要求,斜度向偏小方向取得。
一般情况下脱模斜度。
可不受制品公差带的限制,高精度塑料制品的脱模斜度则应当在公差带内。
脱模斜度α值可按表2-4选取。
由表中可以看出,塑料硬脆、刚性大的,脱模斜度要求大。
具备以下条件的型芯,可采用较小的脱模斜度:(1)顶出时制品刚度足够。
(2)制品与模具钢材表面的摩擦系数较低。
(3)型芯表面的粗糙度值小,抛光方向又与制品的脱模方向—致。
(4)制品收缩量小,滑动摩擦力小。
1.3.2制品脱模斜度设计1、箱体与盖类制品(图2-1)当H≤50mm时,S/H=1/30~1/50当50<H≤100mm时,S/H≤1/602、格子板形制品(图2-2)当格子的间距P≤4mm时,脱模斜度α=1/10P。
格子C尺寸越大,脱模斜度越大。
当格子高度H超过8mm,脱模斜度不能取太大值时,可采用图(b)的形式,使一部分进入动模一侧,从而使脱模斜度满足要求。
3、带加强筋类制品(图2-3)A=(1.0~1.8)Tmm;B=(0.5~0.7)Tmm4、底筋类制品(图2-4)A=(1.0~1.8)Tmm;B=(0.5~0.7)Tmm5、凸台类制品(图2-5、表2-5)高凸台制品(H>30mm)的脱模斜度:型芯:型腔:型芯的脱模斜度应大于型腔。
6、最小脱模斜度(表2-6)脱模斜度影响制品的脱出情况。
如果脱模斜度很小,脱模阻力增大,顶出机构就会失去作用。
在一般情况下,不能小于最小脱模斜度,以防止制品留模。
§1.4制品壁厚确定合适的制品壁厚是制品设计的主要内容之一。
1.4.1制品壁厚的作用(1)使制品具有确定的结构和一定的强度、刚度,以满足制品的使用要求。
(2)成型时具有良好的流动状态(如壁不能过薄)以及充填和冷却效果(如壁不能太厚)(3)合理的壁厚使制品能顺利地从模具中顶出。
(4)满足嵌件固定及零件装配等强度的要求。
(5)防止制品翘曲变形。
1.4.2制品壁厚的设计基本原则——均匀壁厚。
即:充模、冷却收缩均匀、形状性好、尺寸精度高、生产率高。
(1)在满足制品结构和使用要求的条件下,尽可能采用较小的壁厚。
(2)制品壁厚的设计,要能承受顶出装置等的冲击和振动。
(3)在制品的连接固紧处、嵌件埋入处、塑料熔体在孔窗的汇合(熔接痕)处,要具有足够的厚度。
(4)保证贮存、搬运过程中强度所需的壁厚。
(5)满足成型时熔体充模所需壁厚,既要避免充料不足或易烧焦的薄壁,又要避免熔体破裂或易产生凹陷的厚壁。
制品上相邻壁厚差的关系(薄壁:厚壁)为:热固性塑料:压制1:3,挤塑1:5热塑性塑料:注塑1:1.5(2)当无法避免不均匀的壁厚时,制品壁厚设计可采用逐步过渡的形式(图2-6,图2-7),或者改制成两个制品然后再装配为一个制品(图2-8)等方法。
制品壁厚的设计可参照表2-7~表2-11。
§1.5加强筋(含凸台、角撑)1.5.1加强筋的作用(1)在不加大制品壁厚的条件下,增强制品的强度和刚性,以节约塑料用量,减轻重量,降低成本。
(2)可克服制品壁厚差带来的应力不均所造成的制品歪扭变形。
(3)便于塑料熔体的流动,在塑料制品本体某些壁部过薄处为熔体的充满提供通道。
1.5.2加强筋的形状及尺寸塑料制品上加强筋和凸台的形式和应用如图2-9,图2-10所示。
加强筋尺寸参数如图2-11,图2-12所示。
凸台的形状及尺寸参数如图2-13~图2-15所示。
角撑位于制品边缘,支撑制品壁面,以增加强度及刚度,尺寸参数如图2-16所示。
1.5.3加强筋的设计要点(1)用高度较低、数量稍多的筋代替高度较高的单一加强筋,避免厚筋底冷却收缩时产生表面凹陷(图2-17、图2-18)。
当筋的背面出现凹陷影响美观时,可采用图2-19所示的装饰结构予以遮掩。
(2)筋的布置方向最好与熔料的充填方向一致(见表2-12中示例)。
(3)筋的根部用圆弧过渡,以避免外力作用时产生应力集中而破坏。
但根部圆角半径过大则会出现凹陷。
(4)一般不在筋上安置任何零件。
(5)位于制品内壁的凸台不要太靠近内壁,以避免凸台局部熔体充填不足(图2-20)。
加强筋在防止制品变形、增加制品刚性方面的应用如图2-21~图2-22所示。
加强筋设计注意的问题参见表2-12。
§1.6支承面制品的支承面不能是整个底面,而应采用凸边或凸起支脚类结构,如三点支承、边框支承等,如图2-23~图2-26所示。
§1.7圆角制品的两相交平面之间尽可能以圆弧过渡,避免因锐角而造成应力集中等弊病(参见图2-27~图2-30)。
制品圆角的作用有:(1)分散载荷,增强及充分发挥制品的机械强度。
(2)改善塑料熔体的流动性,便于充满与脱模,消除壁部转折处的凹陷等缺陷。
(3)便于模具的机械加工和热处理,从而提高模具的使用寿命。
§1.8孔1.8.1制品孔的形式及成型方法孔的形式很多,主要可分为圆形孔(图2-31、图2-32)和非圆形孔两大类。
根据孔径与孔深度的不同,孔可用下述方法成型:(1)一般孔、浅孔,模塑成型。
(2)深孔,先模塑出孔的一部分深度,其余孔深用机械加工(如钻孔)获得。
(3)小径深孔(如孔径d<1.5mm),机械加工。
(4)小角度倾斜孔、复杂型孔,采用拼合型芯成型,避免用侧抽芯。
(5)薄壁孔、中心距精度高的孔(孔系),采用模具冲孔,以简化塑模结构。
1.8.2孔的模塑成型1、盲孔成型(型芯一端固定,参见图2-33、图2-34)图中,D——孔径、L——孔深注射、传递模塑D≤1.5mm,L=DD>1.5mm,L=(2~4)D压缩模塑L=(2~2.5)D2、通孔的成型(图2-35~图2-38)3、复杂型孔的成型(图2-39)4、孔的成型尺寸参数(表2-13~表2-15)1.8.3孔的设计要点(1)孔与孔的中心距应大于孔径(两者中的小孔)的2倍,孔中心至边缘的距离为孔径的3倍。
热塑性和热固性塑料制品的孔心距、孔边距还可参见图2-40和表2-16。
(2)孔周边的壁厚要加大,其值比与之相装配件的外径大20%~40%,以避免收缩应力所造成的不良影响。
(3)制品壁上的孔(即孔轴线与开模方向相垂直),为避免侧向抽芯,可用图2-41中的侧壁凹槽代替。
但图中的m-n面的加工难度加大。
(4)塑料熔体围绕型芯流动汇合而形成塑料制品孔时,会在孔的边缘熔体汇合处形成熔接痕(图2-42),熔接痕的存在削弱了制品的强度。
解决的措施有:1)孔与孔之间应适当加大距离,以避免熔接痕的重合连接(图2-42)。
2)型孔按盲孔设计,留有1/3壁厚的连皮,以便让熔体从型芯头上越过,使之不出现熔体汇合的熔接痕。
最后钻(冲)掉孔的连皮(图2-43)。
3)热塑性塑料和层压酚醛塑料的薄壁孔形件(如散热器窗),可用冲裁模冲压出型孔。
(5)需要钻孔的制品,模塑孔时应做出钻头的定位或导向部分的形状(图2-44和图2-45)。
(6)自攻螺纹孔、沉头螺钉孔的锥面孔,为防止孔表面破裂,锥面始端距表面应不小于0.5mm(图2-46)。
表2-17中列出了常见孔的设计注意事项。
§1.9侧面凸凹和侧孔1.9.1制品的侧凸凹制品侧壁上局部的凸出或凹缺部分称为侧凸凹,形式见图2-47。
侧凸凹制品成型中的不利点:(1)模具结构复杂,需采用对开式型腔、伸缩式型芯、侧向抽芯等结构。
(2)模具制造费用加大,制造周期加长。
(3)制品模塑周期加长,生产成本增加。
(4)模具分型面缝隙溢料机会增多,制品的飞边大。
1.9.2侧凸凹的设计与成型方法(1)制品形状成型准则:各部分都能顺利地、简单地从塑模中取出来,力求避免带有侧抽芯机构成型的侧凸凹形状。