硫化胶综合物理机械性能的测试
EPDM硫化胶的压缩永久变形试验
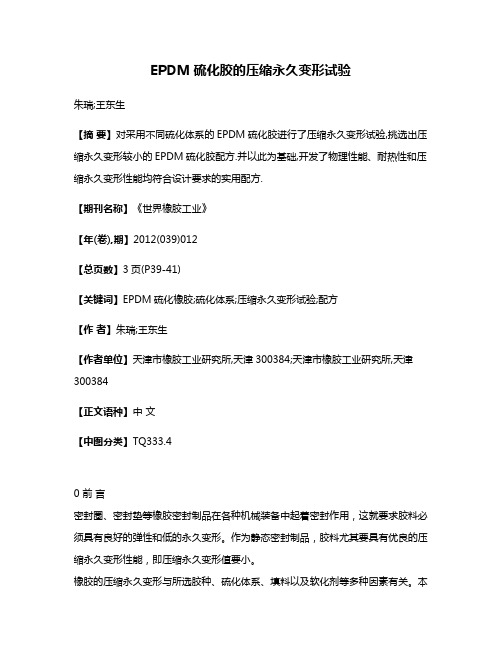
EPDM硫化胶的压缩永久变形试验朱瑞;王东生【摘要】对采用不同硫化体系的EPDM硫化胶进行了压缩永久变形试验,挑选出压缩永久变形较小的EPDM硫化胶配方.并以此为基础,开发了物理性能、耐热性和压缩永久变形性能均符合设计要求的实用配方.【期刊名称】《世界橡胶工业》【年(卷),期】2012(039)012【总页数】3页(P39-41)【关键词】EPDM硫化橡胶;硫化体系;压缩永久变形试验;配方【作者】朱瑞;王东生【作者单位】天津市橡胶工业研究所,天津300384;天津市橡胶工业研究所,天津300384【正文语种】中文【中图分类】TQ333.40 前言密封圈、密封垫等橡胶密封制品在各种机械装备中起着密封作用,这就要求胶料必须具有良好的弹性和低的永久变形。
作为静态密封制品,胶料尤其要具有优良的压缩永久变形性能,即压缩永久变形值要小。
橡胶的压缩永久变形与所选胶种、硫化体系、填料以及软化剂等多种因素有关。
本文在胶种、填料、软化剂、活性剂相同的条件下,研究了不同硫化体系对ЕРDМ硫化胶压缩永久变形性能的影响。
同时,也确定了综合性能优良的耐热密封胶料实用配方。
1 实验1.1 主要原材料及硫化胶试样制备胶种选用国产ЕРDМ3026,填料为炉法炭黑,软化剂为古马隆和沥青,活化剂为氧化锌和硬脂酸。
硫化采用硫磺+高促进剂、低硫磺+过氧化物及过氧化物三种硫化体系。
配方总量:200~217份;硫化条件:150 ℃×45 min,150 ℃×60 min。
1.2 性能测试按照GВ/Т 7759-1996测定硫化胶的压缩永久变形性,采用В型试样,试样直径13.0 mm±0.5 mm,试样高度6.3 mm±0.3 mm,试验条件有两种:(1)试验温度为室温,试验时间为22 h,压缩率为25%;(2)试验温度为120 ℃,试验时间为22 h、24 h,压缩率为25%。
按照GВ/Т 531.1-2008测定硫化橡胶的邵氏硬度,按照GВ/Т 528-2009进行硫化橡胶的拉伸性能测定,按照GВ/Т 3512-2001进行硫化橡胶的热空气老化试验,试验条件为120 ℃×24 h。
橡胶力学性能测试标准
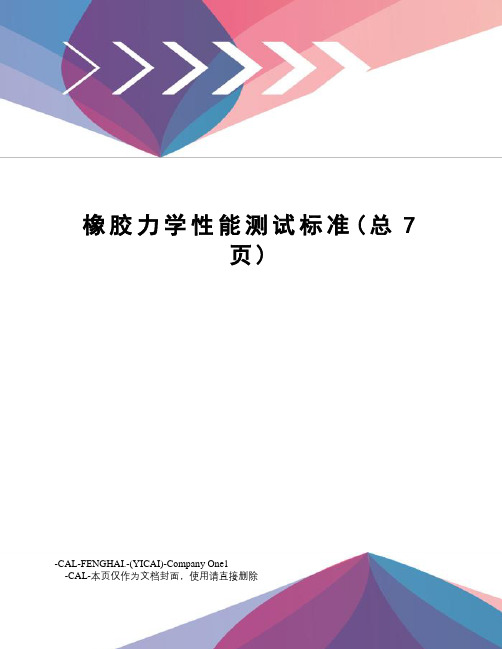
橡胶力学性能测试标准(总7页)-CAL-FENGHAI.-(YICAI)-Company One1-CAL-本页仅作为文档封面,使用请直接删除序号标准号 :发布年份标准名称(仅供参考)1 GB 1683-1981 硫化橡胶恒定形变压缩永久变形的测定方法2 GB 1686-1985 硫化橡胶伸张时的有效弹性和滞后损失试验方法3 GB 1689-1982 硫化橡胶耐磨性能的测定(用阿克隆磨耗机)4 GB 532-1989 硫化橡胶与织物粘合强度的测定5 GB 5602-1985 硫化橡胶多次压缩试验方法6 GB 6028-1985 硫化橡胶中聚合物的鉴定裂解气相色谱法7 GB 7535-1987 硫化橡胶分类分类系统的说明8 GB/T 11206-1989 硫化橡胶老化表面龟裂试验方法9 GB/T 11208-1989 硫化橡胶滑动磨耗的测定10 GB/T 11210-1989 硫化橡胶抗静电和导电制品电阻的测定11 GB/T 11211-1989 硫化橡胶与金属粘合强度测定方法拉伸法12 GB/T 1232.1-2000 未硫化橡胶用圆盘剪切粘度计进行测定第1部分:门尼粘度的测定13 GB/T 12585-2001 硫化橡胶或热塑性橡胶橡胶片材和橡胶涂覆织物挥发性液体透过速率的测定(质量法)14 GB/T 12829-2006 硫化橡胶或热塑性橡胶小试样(德尔夫特试样)撕裂强度的测定15 GB/T 12830-1991 硫化橡胶与金属粘合剪切强度测定方法四板法16 GB/T 12831-1991 硫化橡胶人工气候(氙灯)老化试验方法17 GB/T 12834-2001 硫化橡胶性能优选等级18 GB/T 13248-1991 硫化橡胶中锰含量的测定高碘酸钠光度法19 GB/T 13249-1991 硫化橡胶中橡胶含量的测定管式炉热解法20 GB/T 13250-1991 硫化橡胶中总硫量的测定过氧化钠熔融法21 GB/T 13642-1992 硫化橡胶耐臭氧老化试验动态拉伸试验法22 GB/T 13643-1992 硫化橡胶或热塑性橡胶压缩应力松弛的测定环状试样23 GB/T 13644-1992 硫化橡胶中镁含量的测定 CYDTA滴定法24 GB/T 13645-1992 硫化橡胶中钙含量的测定EGTA滴定法25 GB/T 13934-2006 硫化橡胶或热塑性橡胶屈挠龟裂和裂口增长的测定(德墨西亚型)26 GB/T 13935-1992 硫化橡胶裂口增长的测定27 GB/T 13936-1992 硫化橡胶与金属粘接拉伸剪切强度测定方法28 GB/T 13937-1992 分级用硫化橡胶动态性能的测定强迫正弦剪切应变法29 GB/T 13938-1992 硫化橡胶自然贮存老化试验方法30 GB/T 13939-1992 硫化橡胶热氧老化试验方法管式仪法31 GB/T 14834-1993 硫化橡胶与金属粘附性及对金属腐蚀作用的测定32 GB/T 14835-1993 硫化橡胶在玻璃下耐阳光曝露试验方法33 GB/T 14836-1993 硫化橡胶灰分的定性分析34 GB/T 15254-1994 硫化橡胶与金属粘接180°剥离试验35 GB/T 15255-1994 硫化橡胶人工气候老化(碳弧灯)试验方法36 GB/T 15256-1994 硫化橡胶低温脆性的测定(多试样法)37 GB/T 15584-1995 硫化橡胶在屈挠试验中温升和耐疲劳性能的测定第一部分:基本原理38 GB/T 15905-1995 硫化橡胶湿热老化试验方法39 GB/T 16585-1996 硫化橡胶人工气候老化(荧光紫外灯)试验方法40 GB/T 16586-1996 硫化橡胶与钢丝帘线粘合强度的测定41 GB/T 16589-1996 硫化橡胶分类橡胶材料42 GB/T 1681-1991 硫化橡胶回弹性的测定43 GB/T 1682-1994 硫化橡胶低温脆性的测定单试样法44 GB/T 1684-1985 硫化橡胶短时间静压缩试验方法45 GB/T 1685-1982(1989) 硫化橡胶在常温和高温下压缩应力松弛的测定46 GB/T 1687-1993 硫化橡胶在屈挠试验中温升和耐疲劳性能的测定第2部分:压缩屈挠试验47 GB/T 1688-1986 硫化橡胶伸张疲劳的测定48 GB/T 1689-1998 硫化橡胶耐磨性能的测定 (用阿克隆磨耗机)49 GB/T 1690-2006 硫化橡胶或热塑性橡胶耐液体试验方法50 GB/T 1692-1992 硫化橡胶绝缘电阻率测定51 GB/T 1693-1981(1989) 硫化橡胶工频介电常数和介质损耗角正切值的测定方法52 GB/T 1693-2007 硫化橡胶介电常数和介质损耗角正切值的测定方法53 GB/T 1694-1981(1989) 硫化橡胶高频介电常数和介质损耗角正切值的测定方法54 GB/T 1695-2005 硫化橡胶工频击穿电压强度和耐电压的测定方法55 GB/T 16996-1997 硫化橡胶暴露于自然气候或人工光后性能变化的评定56 GB/T 17782-1999 硫化橡胶压力空气热老化试验方法57 GB/T 17783-1999 硫化橡胶样品和试样的制备化学试验58 GB/T 18864-2002 硫化橡胶工业用抗静电和导电产品电阻极限范围59 GB/T 19208-2003 硫化橡胶粉60 GB/T 19242-2003 硫化橡胶在压缩或剪切状态下蠕变的测定61 GB/T 19243-2003 硫化橡胶或热塑性橡胶与有机材料接触污染的试验方法62 GB/T 20028-2005 硫化橡胶或热塑性橡胶应用阿累尼鸟斯图推算寿命和最高使用温度63 GB/T 2439-2001 硫化橡胶或热塑性橡胶导电性能和耗散性能电阻率的测定64 GB/T 2942-1991 硫化橡胶与织物帘线粘合强度的测定 H 抽出法65 GB/T 3511-2001 硫化橡胶或热塑性橡胶直接自然气候老化试验方法66 GB/T 3512-2001 硫化橡胶或热塑性橡胶热空气加速老化和耐热试验67 GB/T 3513-2001 硫化橡胶与单根钢丝粘合力的测定抽出法68 GB/T 3514-1992 硫化橡胶中游离硫含量的测定亚硫酸钠法69 GB/T 4497-1984 硫化橡胶全硫含量的测定氧瓶燃烧法70 GB/T 4499-1997 硫化橡胶中防老剂的测定薄层色谱法71 GB/T 528-1998 硫化橡胶或热塑性橡胶拉伸应力应变性能的测定72 GB/T 529-1999 硫化橡胶或热塑性橡胶撕裂强度的测定(裤形、直角形和新月形试样)73 GB/T 532-1997 硫化橡胶或热塑性橡胶与织物粘合强度的测定74 GB/T 533-1991 硫化橡胶密度的测定75 GB/T 5723-1993 硫化橡胶或热塑性橡胶试验用试样和制品尺寸的测定76 GB/T 6029-1996 硫化橡胶中促进剂的检定薄层色谱法77 GB/T 6030-1985 硫化橡胶中炭黑分散度的测定显微照相法78 GB/T 6031-1998 硫化橡胶或热塑性橡胶硬度的测定(10~100IRHD)79 GB/T 6033-1985 硫化橡胶赵氏及邵坡尔硬度试验方法80 GB/T 6034-1985 硫化橡胶压缩耐寒系数的测定81 GB/T 6035-1985 硫化橡胶拉伸耐寒系数的测定82 GB/T 6036-2001 硫化橡胶或热塑性橡胶低温刚性的测定(吉门试验)83 GB/T 6037-1985 硫化橡胶高温拉伸强度和扯断伸长率的测定84 GB/T 7755-2003 硫化橡胶或热塑性橡胶透气性的测定85 GB/T 7756-1987 硫化橡胶透气性的测定恒压法86 GB/T 7757-1993 硫化橡胶或热塑性橡胶压缩应力应变性能的测定87 GB/T 7758-2002 硫化橡胶低温性能的测定温度回缩法(TR试验)88 GB/T 7759-1996 硫化橡胶、热塑性橡胶常温、高温和低温下压缩永久变形测定89 GB/T 7760-2003 硫化橡胶或热塑性橡胶与硬质板材粘合强度的测定 90°剥离法90 GB/T 7762-2003 硫化橡胶或热塑性橡胶耐臭氧龟裂静态拉伸试验91 GB/T 7763-1987 硫化橡胶溶胀指数测定方法92 GB/T 9865.1-1996 硫化橡胶或热塑性橡胶样品和试样的制备第一部分:物理试验93 GB/T 9867-1988 硫化橡胶耐磨性能的测定(旋转辊筒式磨耗机法)94 GB/T 9870.1-2006 硫化橡胶或热塑性橡胶动态性能的测定第1部分:通则95 GB/T 9871-1988 硫化橡胶老化性能的测定(拉伸应力松弛试验)1. 吴晓辉, ASTM D638 Tensile Testing of Plastics,ISO 527. 2008.2. ASTM D 395-03 Standard Test Methods for Rubber Property-Compression Set.3. ASTM 标准号ABCDEFGP.4. ASTM 橡胶产品测定—化学分析.5. 汤龙臣, DL-T 627-2004 绝缘子用常温固化硅橡胶防污闪涂料. 2004.6. GB 1232-1982橡胶粘度的测定(用门尼粘度计). 1982.7. GB 1452~1453-87 非金属夹层结构或芯子试验方法Test method for nonmetal sandwish construction or cores. 1987.8. GB 1683-1981 硫化橡胶恒定形变压缩永久变形的测定方法.9. GB 1684-1985 硫化橡胶短时间静压缩试验方法.10. GB 1685-1982 硫化橡胶在常温和高温下压缩应力松弛的测定. 1982.11. GB 1685-1982(1989) 硫化橡胶在常温和高温下压缩应力松弛的测定.12. GB 1686-1985 硫化橡胶伸张时的有效弹性和滞后损失试验方法.13. GB 1688-1986 硫化橡胶伸张疲劳的测定.14. GB 1689-82硫化橡胶耐磨性能的测定(用阿克隆磨耗机). 1982.15. GB 1693-1981 硫化橡胶介电常数和介质损耗角正切值的测定方法.16. GB 1694-1981(1989) 硫化橡胶高频介电常数和介质损耗角正切值的测定方.17. 孙业斌, GB 2423.1-89 电工电子产品基本环境试验规程.18. 孙业斌, GB 2424.1-89 电子电工产品基本环境试验规程高温低温试验导则.19. GB 4497-1984 硫化橡胶全硫含量的测定氧瓶燃烧法.20. GB 4883-1985 数据的统计处理和解释正态样本异常值的判断和处理. 1985.21. GB 5577-1985 合成橡胶牌号规定.22. GB 5602-1985 硫化橡胶多次压缩试验方法.23. GB 6030-1985 硫化橡胶中炭黑分散度的测定显微照相法.24. GB 6033-1985 硫化橡胶赵氏及邵坡尔硬度试验方法.25. GB 6034-1985 硫化橡胶压缩耐寒系数的测定.26. GB 6035-1985 硫化橡胶拉伸耐寒系数的测定.27. GB 6037-1985 硫化橡胶高温拉伸强度和扯断伸长率的测定.28. GB 7036.1-1997 充气轮胎内胎第1部分汽车轮胎内胎.29. GB 7756-1987 硫化橡胶透气性的测定恒压法.30. GB 7763-1987 硫化橡胶溶胀指数测定方法.31. GB 7986-1997 输送带滚筒摩擦试验方法.32. GB 8827-88 防老剂甲.33. GB 9744-1997 载重汽车轮胎.34. GB 9867-88 硫化橡胶耐磨性能的测定(旋转滚筒式磨耗机法). 1988.35. GB 9867-1988 硫化橡胶耐磨性能的测定(旋转辊筒式磨耗机法).36. GB 9868-1988 橡胶获得高于或低于常温试验温度通则.37. GB 9869-88 橡胶胶料硫化特性的测定(圆盘振荡硫化仪法). 1988.38. GB 9871-1988 硫化橡胶老化性能的测定.39. GB 9896-88橡胶获得高于或低于常温实验温度通则. 1988.40. GB 11206-1989 硫化橡胶老化表面龟裂试验方法.41. GB 11208-1989 硫化橡胶滑动磨耗的测定.42. GB 11210-1989 化橡胶抗静电和导电制品电阻的测定.43. GB 11211-1989 硫化橡胶与金属粘合强度测定方法拉伸法.44. GB 11409.4-89 橡胶防老剂、硫化促进剂加热减量的测定方法.45. GB 11409.5-89 橡胶防老剂、硫化促进剂筛余物的测定方法.46. GB 11409.8-89 橡胶防老剂、硫化促进剂粘度的测定方法旋转粘度计法.47. GB 15603-1995 常用化学危险品贮存通则.48. GB-T1233-1992 橡胶初期硫化特性的测定门尼粘度法.49. GB-T1681-1991 硫化橡胶回弹性测定.50. GB-T1687-1993 硫化橡胶在屈挠实验中温升和耐疲劳性能的测定第2部分:压缩屈挠实验.51. GB-T3672.1-2002 橡胶制品的公差第1部分尺寸公差.52. GB-T3672.2-2002 橡胶制品的公差第2部分几何公差.53. GB-T5720-1993 O型橡胶密封圈试验方法.54. GB-T7759-1996 硫化橡胶、热塑性橡胶常温高温和低温下压缩永久变形的测定.55. GB-T11409.7-1989 橡胶防老剂硫化促进剂灰分的测定.56. 王磊, GB-T13022-1991 塑料薄膜拉伸试验方法. 1991.57. GB-T14832-1993 橡胶材料与液压流体的相容性试验.58. 汤龙臣, GB-T 528-1998硫化橡胶或热塑性橡胶拉伸应力应变性能的测定. 1998.59. GB-T 529-1999 硫化橡胶或热塑性橡胶撕裂强度的测定(裤形、直角形和新月形试样).60. GB-T 531-1992硫化橡胶邵氏A硬度试验方法. 1992.61. GB-T 532-1997 硫化橡胶或热塑性橡胶与织物粘合强度的测定.62. GB-T 533-1991 硫化橡胶密度的测定.63. GB-T 1190-2001 工程机械轮胎技术要求.64. GB-T 1232.1-2000 未硫化橡胶用圆盘剪切粘度计进行测定第1部分门尼粘度的测定.65. GB-T 1681-1991 硫化橡胶回弹性的测定.66. GB-T 1682-1994 硫化橡胶低温脆性的测定单试样法.67. GB-T 1687-1993?硫化橡胶在屈挠试验中温升和耐疲劳性能的测定第2部分压缩屈挠试验.68. GB-T 1689-1998 硫化橡胶耐磨性能的测定 (用阿克隆磨耗机).69. GB-T 1690-2006 硫化橡胶或热塑性橡胶耐液体试验方法.70. GB-T 1692-1992 硫化橡胶绝缘电阻率测定.71. GB-T 1695-2005 硫化橡胶工频击穿电压强度和耐电压的测定方法.72. 汤龙臣, GB-T 2406-1993 塑料燃烧性能试验方法氧指数法. 1993.73. 汤龙臣, GB-T 2408-1996 塑料燃烧性能试验方法水平法和垂直法. 1996.74. GB-T 2439-2001 硫化橡胶或热塑性橡胶导电性能和耗散性能电阻率的测定.75. 石浩, GB-T 2918-1998 塑料试样状态调节和试验的标准环境. 1998.76. 石浩, GB-T 2918 塑料试样状态调节和试样的标准环境. 1998.77. GB-T 2941-91 橡胶试样环境调节和试验的标准温度、湿度及时间. 1991.78. GB-T 2941-2006橡胶物理试验方法试样制备和调节通用程序.79. GB-T 2942-1991 硫化橡胶与织物帘线粘合强度的测定 H抽出法.80. GB-T 3358.1-1993 统计学术语第1部分一般统计术语. 1993.81. GB-T 3358.2-1993 统计学术语第2部分统计质量控制术语. 1993.82. GB-T 3358.3-1993 统计学术语第3部分试验设计术语. 1993.83. GB-T 3511-2001 硫化橡胶或热塑性橡胶直接自然气候老化试验方法.84. GB-T 3512-2001 硫化橡胶或热塑性橡胶热空气加速老化和耐热试验.85. GB-T 3513-2001 硫化橡胶与单根钢丝粘合力的测定抽出法.86. GB-T 3514-1992 硫化橡胶中游离硫含量的测定亚硫酸钠法.87. GB-T 3684-2006 运输带导电性规范和试验方法.88. GB-T 4086.1-1983 统计分布数值表正态分布.89. GB-T 4499-1997 硫化橡胶中防老剂的测定薄层色谱法.90. GB-T 5723-1993 硫化橡胶或热塑性橡胶试验用试样和制品尺寸的测定.91. GB-T 6029-1996 硫化橡胶中促进剂的检定薄层色谱法.92. GB-T 6031-1998 硫化橡胶或热塑性橡胶硬度的测定(10~100IRHD).93. GB-T 6036-2001 硫化橡胶或热塑性橡胶低温刚性的测定(吉门试验).94. GB-T 7124-86 胶粘剂拉伸剪切强度测定方法(金属对金属)The method for determination of strength properties of adhesive in shear by tension loading(Metal to metal). 1986.95. GB-T 7755-2003 硫化橡胶或热塑性橡胶透气性的测定.96. GB-T 7757-1993 硫化橡胶或热塑性橡胶压缩应力应变性能的测定.97. 王文波, GB-T 7757-1993硫化橡胶或热塑性橡胶压缩应力应变性能的测定. 1993.98. GB-T 7758-2002 硫化橡胶低温性能的测定温度回缩法(TR试验).99. GB-T 7759-1996 硫化橡胶、热塑性橡胶常温、高温和低温下压缩永久变形测定. 100. GB-T 7760-2003 硫化橡胶或热塑性橡胶与硬质板材粘合强度的测定90°剥离. 101. GB-T 7762-2003 硫化橡胶或热塑性橡胶耐臭氧龟裂静态拉伸试验.102. GB-T 8170-1987 中华人民共和国国家标准数值修约规则. 1987.103. GB-T 8826-2003 防老剂 RD.104. GB-T 8828-2003 防老剂 4010NA.105. GB-T 9865.1-1996 硫化橡胶或热塑性橡胶样品和试样的制备第一部分物理试验. 106. 李鹏, GB-T 10006-1988 塑料薄膜和薄片摩擦系数测定方法. 1988.107. 汤龙臣, GB-T 10808-2006 高聚物多孔弹性弹性材料撕裂强度的测定. 2006.108. GB-T 11407-2003 硫化促进剂M.109. GB-T 11408-2003 硫化促进剂DM.110. GB-T 11409.1-95 橡胶防老剂、硫化促进剂熔点测定方法.111. GB-T 11409.2-95 橡胶防老剂、硫化促进剂结晶点测定方法.112. GB-T 11409.3-2003 橡胶防老剂、硫化促进剂软化点的测定.113. GB-T 11409.6-2003 橡胶防老剂、硫化促进剂表观密度的测定.114. GB-T 12585-2001 硫化橡胶或热塑性橡胶橡胶片材和橡胶涂覆织物挥发性液体透过速率的测定(质量法).115. GB-T 12829-2006 硫化橡胶或热塑性橡胶小试样(德尔夫特试样)撕裂强度的测定. 116. GB-T 12830-1991 硫化橡胶与金属粘合剪切强度测定方法四板法.117. GB-T 12831-1991 硫化橡胶人工气候(氙灯)老化试验方法.118. GB-T 12833-2006 橡胶和塑料撕裂强度和粘合强度测定中的多峰曲线分析.119. GB-T 12834-2001 硫化橡胶性能优选等级.120. GB-T 13248-1991 硫化橡胶中锰含量的测定高碘酸钠光度法.121. GB-T 13249-1991 硫化橡胶中橡胶含量的测定管式炉热解法.122. GB-T 13250-1991 硫化橡胶中总硫量的测定过氧化钠熔融法.123. GB-T 13642-1992 硫化橡胶耐臭氧老化试验动态拉伸试验法.124. GB-T 13643-1992 硫化橡胶或热塑性橡胶压缩应力松弛的测定环状试样.125. GB-T 13644-1992 硫化橡胶中镁含量的测定 CYDTA滴定法.126. GB-T 13645-1992 硫化橡胶中钙含量的测定EGTA滴定法.127. GB-T 13934-1992 硫化橡胶裂口增长的测定. 化工行业标准汇编橡胶物理和化学试验方法 1997, 1992.128. GB-T 13934-2006 硫化橡胶或热塑性橡胶屈挠龟裂和裂口增长的测定(德墨西亚型). 129. GB-T 13935-1992 硫化橡胶裂口增长的测定.130. GB-T 13935-1992 硫化橡胶裂口增长的测定. 1992.131. GB-T 13936-1992 硫化橡胶与金属粘接拉伸剪切强度测定方法.132. GB-T 13937-1992 分级用硫化橡胶动态性能的测定强迫正弦剪切应变法.133. GB-T 13938-1992 硫化橡胶自然贮存老化试验方法.134. GB-T 13939-1992 硫化橡胶热氧老化试验方法管式仪法.135. GB-T 14647-1993 氯丁橡胶 CR121.136. GB-T 14834-1993 硫化橡胶与金属粘附性及对金属腐蚀作用的测定.137. GB-T 14835-1993 硫化橡胶在玻璃下耐阳光曝露试验方法.138. GB-T 14836-1993 硫化橡胶灰分的定性分析.139. GB-T 15254-1994 硫化橡胶与金属粘接180°剥离试验.140. GB-T 15255-1994 硫化橡胶人工气候老化(碳弧灯)试验方法.141. GB-T 15256-1994 硫化橡胶低温脆性的测定(多试样法).142. GB-T 15584-1995 硫化橡胶在屈挠试验中温升和耐疲劳性能的测定第1部分:基本原理. 1995.143. GB-T 15584-1995 硫化橡胶在屈挠试验中温升和耐疲劳性能的测定第一部分基本原理. 144. GB-T 15905-1995 硫化橡胶湿热老化试验方法.145. GB-T 16585-1996 硫化橡胶人工气候老化(荧光紫外灯)实验方法.146. GB-T 16585-1996 硫化橡胶人工气候老化(荧光紫外灯)试验方法.147. GB-T 16586-1996 硫化橡胶与钢丝帘线粘合强度的测定.148. GB-T 16589-1996 硫化橡胶分类橡胶材料.149. GB-T 16996-1997 硫化橡胶暴露于自然气候或人工光后性能变化的评定.150. GB-T 17782-1999 硫化橡胶压力空气热老化试验方法.151. GB-T 17783-1999 硫化橡胶样品和试样的制备化学试验.152. GB-T 18864-2002 硫化橡胶工业用抗静电和导电产品电阻极限范围.153. GB-T 19208-2003 硫化橡胶粉.154. GB-T 19242-2003 硫化橡胶在压缩或剪切状态下蠕变的测定.155. GB-T 19243-2003 硫化橡胶或热塑性橡胶与有机材料接触污染的试验方法.156. GB-T 20028-2005 硫化橡胶或热塑性橡胶应用阿累尼鸟斯图推算寿命和最高使用温度. 157. GBZ 147-2002 X射线防护材料衰减性能的测定.158. GJB 130.6-86 胶接铝蜂窝夹层结构和芯子平面剪切试验方法Test method for flatwise shear properties of adhesive-bonded aluminum honeycomb-sandwich structure and core1986.159. 孙业斌, GJB 150.1-86 军用设备环境试验方法.160. GJB 446-88 胶粘剂90°剥离强度试验方法(金属与金属)Test method for 90° peel strength of adhesiv es (metal to metal). 1988.161. GJB 标准名称.162. HB 5426-89 胶接耐久性评定用多节点剥离试验方法. 1989.163. HG 2369-1992 橡胶塑料拉力机技术条件.164. HG-T 2096-2006 硫化促进剂CBS.165. HG-T 2344-1992 硫化促进剂 TETD (二硫化四乙基秋兰姆).166. 程绍杨, HG-T 2729-1995 硫化橡胶与薄片摩擦系数的测定滑动法. 1995.167. HG-T 3644-1999 防老剂4020.168. ISO 2782-1977 硫化橡胶——透气性的测定——恒压法. ISO 2782-1977, 1977. 169. 姜广明, 版本说明. 2008.170. 标准名称.171. 标准名称(仅供参考).172. 姜广明, 拉伸.173. 拉伸撕裂测试表.174. 硫化橡胶屈挠龟裂的测定. 1992.175. 硫化橡胶——硬度的测定(硬度在30至85IRHD之间). ISO, 1979.176. 姜广明, 密度及溶胀表格.177. 食品用塑料标准.178. 塑料材料测试标准. 2006.179. 国务院, 塑料材料测试标准.180. 炭黑第一部分吸碘值的测定.181. 炭黑加热减量的测定.182. 橡胶类材料试验项目及试验规范.183. 橡胶类相关国家标准总目录大全.。
橡胶工艺----硫化篇
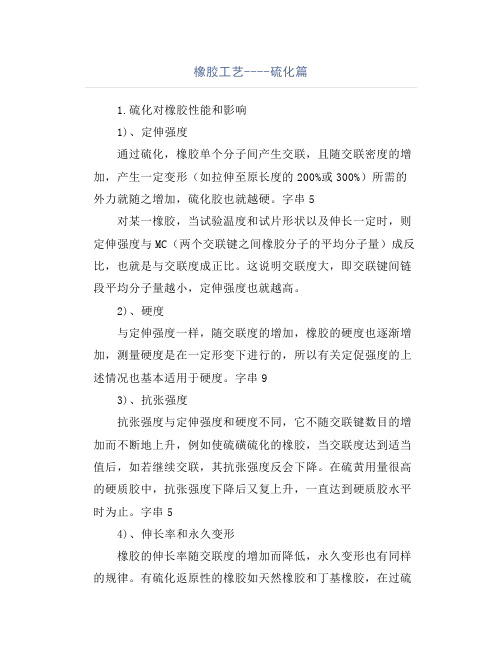
橡胶工艺----硫化篇1.硫化对橡胶性能和影响1)、定伸强度通过硫化,橡胶单个分子间产生交联,且随交联密度的增加,产生一定变形(如拉伸至原长度的200%或300%)所需的外力就随之增加,硫化胶也就越硬。
字串5对某一橡胶,当试验温度和试片形状以及伸长一定时,则定伸强度与MC(两个交联键之间橡胶分子的平均分子量)成反比,也就是与交联度成正比。
这说明交联度大,即交联键间链段平均分子量越小,定伸强度也就越高。
2)、硬度与定伸强度一样,随交联度的增加,橡胶的硬度也逐渐增加,测量硬度是在一定形变下进行的,所以有关定促强度的上述情况也基本适用于硬度。
字串93)、抗张强度抗张强度与定伸强度和硬度不同,它不随交联键数目的增加而不断地上升,例如使硫磺硫化的橡胶,当交联度达到适当值后,如若继续交联,其抗张强度反会下降。
在硫黄用量很高的硬质胶中,抗张强度下降后又复上升,一直达到硬质胶水平时为止。
字串54)、伸长率和永久变形橡胶的伸长率随交联度的增加而降低,永久变形也有同样的规律。
有硫化返原性的橡胶如天然橡胶和丁基橡胶,在过硫化以后由于交联度不断降低,其伸长率和永久变形又会逐渐增大。
5)、弹性未硫化胶受到较长时间的外力作用时,主要发生塑性流动,橡胶分子基本上没有回到原来的位置的倾向。
橡胶硫化后,交联使分子或链段固定,形变受到网络的约束,外力作用消除后,分子或链段力图回复原来构象和位置,所以硫化后橡胶表现出很大的弹性。
交联度的适当增加,这种可逆的弹性回复表现得更为显著。
2.硫化过程的四个阶段胶料在硫化时,其性能随硫化时间变化而变化的曲线,称为硫化曲线。
从硫化时间影响胶料定伸强度的过程来看,可以将整个硫化时间分为四个阶段:硫化起步阶段、欠硫阶段、正硫阶段和过硫阶段。
1)、硫化起步阶段(又称焦烧期或硫化诱导期)硫化起步的意思是指硫化时间胶料开始变硬而后不能进行热塑性流动那一点的时间。
硫起步阶段即此点以前的硫化时间。
在这一阶段内,交联尚未开始,胶料在模型内有良好的流动性。
橡胶硫化特性实验

橡胶硫化特性实验一、实验目的:(1)理解橡胶硫化特性曲线测定的意义;(2)了解ZWL-Ⅱ型橡胶硫化仪的结构原理及操作方法;(3)掌握橡胶硫化特性曲线测定和正硫化时间确定的方法。
二、实验原理:硫化是橡胶制品生产中最重要的工艺过程,在硫化过程中,橡胶经历了一系列的物理和化学变化,其物理机械性能和化学机械性能得到了改善,使橡胶材料成为有用的材料,因此硫化对橡胶及其制品是十分重要的。
硫化是在一定温度、压力和时间条件下使橡胶大分子链发生化学交联反应的过程。
橡胶在硫化过程中,其各种性能随硫化时间增加而变化。
橡胶的硫化历程可分为焦烧、预硫、正硫化和过硫四个阶段。
焦烧阶段又称硫化诱导期,是指橡胶在硫化开始前的延迟作用时间,在此阶段胶料尚未开始交联,胶料在模腔内有良好的流动性。
对于模型硫化制品,胶料的流动、充模必须在此阶段完成,否则就发生焦烧。
预硫化阶段是焦烧期以后橡胶开始交联的阶段。
随着交联反应的进行,橡胶的交联程度逐渐增加,并形成网状结构,橡胶的物理机械性能逐渐上升,但尚未达到预期的水平。
正硫化阶段,橡胶的交联反应达到一定的程度,此时的各项物理机械性能均达到或接近最佳值,其综合性能最佳。
过硫化阶段是正硫化以后继续硫化,此时往往氧化及热断链反应占主导地位,胶料会出现物理机械性能下降的现象。
从硫化反应动力学原理来说,正硫化应是胶料达到最大交联密度时的硫化状态,正硫化时间应由胶料达到最大交联密度所需的时间来确定比较合理。
在实际应用中是根据某些主要性能指标(与交联密度成正比)来选择最佳点,确定正硫化时间。
目前用转子旋转振荡式硫化仪来测定和选取正硫化点最为广泛。
这类硫化仪能够连续地测定与加工性能和硫化性能有关的参数,包括初始粘度、最低粘度、焦烧时间、硫化速度、正硫化时间和活化能等。
实际上硫化仪测定记录的是转矩值,以转矩的大小来反映胶料的硫化程度。
其测定的基本原理根据弹性统计理论:G=ρRT式中G——剪切模量,MPa;ρ——交联密度,mol/mL;R——气体常数,Pa .L / (mol .K);T——绝对温度,K。
橡胶性能测试方法、目的及设备
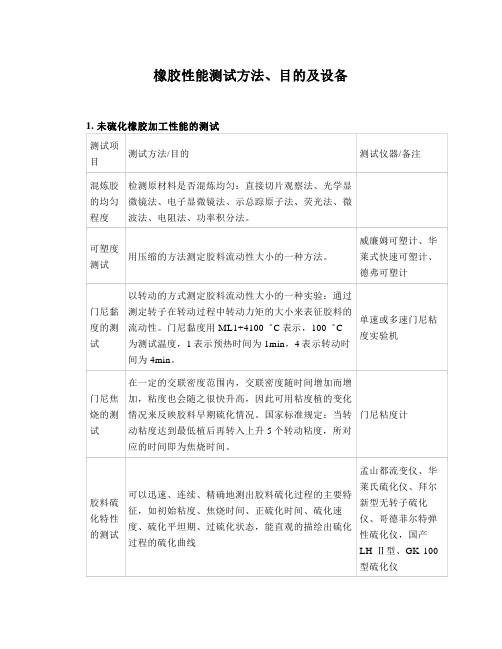
常用检测设备功能介绍:
1、拉力机:测试橡胶伸长率
2、老化试验箱:可供橡塑产品、电气绝缘及其它材料的热空气老化试验,测试塑料的加速老化结果;
3、橡塑低温脆性试验机:可以对橡胶止水带材料在低温条件下的使用性能作比较性鉴定;
4、冲片机:供橡胶厂及科研单位进行拉力试验前冲切标准橡胶试片用;
5、裁刀:配合冲片机取样用,可裁取拉伸、撕裂等试样;
6、磨耗试验机:对橡胶材料进行磨耗试验;
7、硬度计:用于测定硫化橡胶和塑料制品的硬度;
8、测厚仪:用于测量硫化橡胶和塑料制品的厚度;
9、可塑度试验:切片机用于取直径16mm的试样,然后在可塑度试验机上做可塑性试验;
10、压缩永久变形器:用于硫化橡胶,热塑性橡胶在常温,高温和低温条件下,以一定压缩率,经一定的压缩时间后测定橡胶变形量;
11、冲击弹性试验机:测定硬度为30-85IRHD之间硫化橡胶的回弹数值;
12、无转子硫化仪:用于测定未硫化橡胶的特性,找出胶料的最适合硫化时间;
13、门尼粘度计:用来测定各种未硫化的天然橡胶,合成橡胶及再生橡胶的门尼粘度,焦烧时间和流化指数。
硫化考试题

硫化专业上岗资格考试考试时间:90分钟满分100分姓名:部门:分数:一、填空题(每空1分,共计20分)1.在条件下,胶料中的与发生化学反应,由线型大分子链通过交联而成为三维立体网状结构,并使胶料的物理机械性能及其他性能随其发生根本变化,这个过程称为。
2.一个完整的硫化体系主要由、、所组成。
硫化反应是一个多元组分参与的复杂的化学反应过程。
其中与的反应占主导地位,它是形成空间网络的基本反应。
3.硫化过程共有四个阶段,最后一个阶段是。
4.硫化历程图反映的是与的变化关系曲线。
5.要实现理想的硫化历程,必须选择正确的和。
目前比较理想的是具有迟效性的硫化体系。
6.一般天然橡胶和通用合成橡胶的硫化温度为度。
7.这种以物理机械性能为考察对象,即物理机械性能处于最高值或接近最高值的硫化状态称为。
8.橡胶与硫磺的反应可能有两种形式:即进行;或以混合机理同时或相继进行反应。
9.硫化平板机俗称,是一种带有加热平板的压力机。
10.硫化的压力、温度、和时间是构成硫化工艺条件的主要因素,这些因素对产品硫化质量有决定性的影响,通常被称为。
二、判断对错题(每小题2分,计20分)11.硫化是橡胶加工的主要工艺之一,也是橡胶制品生产的最后一道工序。
( )12.生胶料在硫化过程中都需要交联剂。
( )13.在硫化过程中,胶料性能变化的转折时间,主要取决于生胶的性质。
( )14.交联密度越大,橡胶的溶胀率越大。
( )15.橡胶的各项性能指标一般都能在同时间内达到最佳值,在硫化过程中应该密切观察选择最佳时间点。
( )16.硫化温度越高越好。
( )17.DCP(过氧化二异丙苯)是硫化橡胶最常用的硫化剂。
( )18.为防止白炭黑表面吸附促进剂,可以添加二甘醇等。
( )19.氯丁橡胶的金属氧化物硫化有三种机理。
( )20.橡胶制品缺胶有时缘于胶料的黏性。
( )三、单选题(每小题2分,计20分)21.下列物质中不能使橡胶硫化的是()A 有机过氧化物B 苯醌C 合成树脂D 高锰酸钾22.下列说法错误的是()A 胶料的拉伸强度随交联密度的增加而增加B 硫化过程胶料的塑性逐步下降,弹性逐步上升C 胶料的剪切模量与交联密度成反比D 门尼黏度计法和硫化仪法都是专用仪器法23.下列化学键中不属于硫磺交联的一般化学结构的是()A 单硫键B 双硫键C 环状硫键D 伞状硫键24.以下属于促进剂的是()A 邻苯二甲酸酐B 秋兰姆类C N-环己基硫代邻苯二甲酰亚胺D 二叔丁基过氧化物25.以下能单独氧化氯丁橡胶的是()A 氧化锌B 氧化钙C 氧化铁D氧化铜26.以下关于硫化时间说法错误的是()A 硫化时间取决于胶料配方、硫化温度和压力等B 提高硫化温度可以缩短硫化时间C 加大硫化压力可以缩短硫化时间D 调整硫化配方可以缩短硫化时间27.下列不属于平板机加热方式的是()A 红外线加热B 电加热C 蒸汽加热D高温液体加热28.以下关于氯丁橡胶说法正确的是()A氯丁橡胶硫化温度稍低于天然橡胶B 耐油性能优异、耐老化、不耐燃C硫磺是氯丁橡胶主要硫化剂之一D 硫脲类促进剂是氯丁橡胶最常用的促进剂29.以下不能用作聚氨酯橡胶硫化剂的是()A 硫磺B 过氧化物C 异氰酸酯 D水杨酸30.下列有关不合格品质量缺陷说法错误的是()A 造成表面异常(平面部、胶边部)缺陷的原因是模具污染B 造成开模缩裂缺陷的原因是焦烧C 造成缺胶(明疤)缺陷的原因之一是橡胶黏着增大D造成针孔(膜状制品等)缺陷的原因之一是分散不良四、问答题(40分)31.硫化的科学意义是什么?(6分)32.若平板硫化机型号为XLB-D350X350X2型,该型号名称中的各字母和数字分别代表什么含义?(7分)33.什么是正硫化和正硫化时间?(8分)34.什么是硫化压力?它有什么作用?(9分)35.请描述硫化历程四大阶段中的第一阶段和第二阶段。
EPDM橡胶硫化曲线的测定
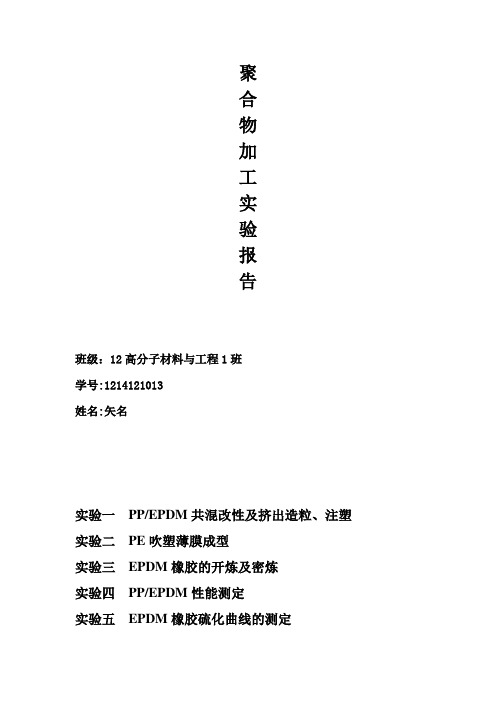
聚合物加工实验报告班级:12高分子材料与工程1班学号:1214121013姓名:矢名实验一PP/EPDM共混改性及挤出造粒、注塑实验二PE吹塑薄膜成型实验三EPDM橡胶的开炼及密炼实验四PP/EPDM性能测定实验五EPDM橡胶硫化曲线的测定实验五 EPDM橡胶硫化特性曲线的测定一、实验目的(1)理解橡胶硫化特性曲线测定的意义;(2)了解CL-2000E型无转子硫化仪的结构原理及操作方法;(3)掌握橡胶硫化特性曲线测定和正硫化时间确定的方法。
二、实验原理硫化是橡胶制坯生产中最重要的工艺过程。
在硫化过程中,橡胶经历了一系列的物理和化学变化,其物理机械性能和化学性能得到了改善,使橡胶材料成为有用的材料,因此硫化对橡胶及其制品是十分重要的。
硫化是在一定温度、压力和时间条件下使橡胶大分子链发生化学交联反应的过程。
橡胶在硫化过程中.其各种性能随硫化时间增加而变化。
橡胶的硫化历程可分为焦烧、预硫、正硫化和过硫叫个阶段。
如图28-1所示。
图 28-1 橡胶硫化历程A 起硫快速的胶料:B 有延迟特性的胶料;C 过硫后定伸强度继续上升的胶料;D 具有反原件的胶料;a1-操作焦烧时间;a2-剩余焦烧时间;b-模型硫化时间焦烧阶段又称硫化诱导期,是指橡胶在硫化开始前的延迟作用时间,在此阶段胶料尚未开始交联,胶料在模型内有良好的流动性。
对于模型硫化制品,胶料的流动、充模必须在此阶段完成,否则就发生焦烧。
预硫化阶段是焦烧期以后橡胶开始交联的阶段。
随着交联反应的进行,橡胶的交联程度逐渐增加,并形成网状结构,橡胶的物理机械性能逐渐上升.但尚未达到顶期的水平。
正硫化阶段,橡胶的交联反应达到一定的程度,此时的各项物理机械性能均达到或接近最佳值,其综合性能最佳。
过硫化阶段是正硫化以后继续硫化,此时的各项物理机械性能均达到或接近最佳值,其综合性能最佳。
过硫化阶段是正硫化以后继续硫化,此时往往氧化及热断链反应占主导地位,胶料会出现物理机械性能下降的现象。
北京化工大学橡胶实验报告
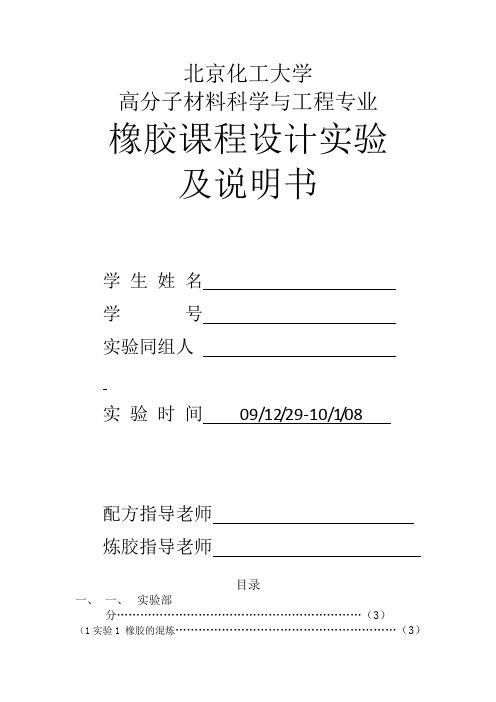
北京化工大学高分子材料科学与工程专业橡胶课程设计实验及说明书学生姓名学号实验同组人实验时间09/12/29-10/1/08配方指导老师炼胶指导老师目录一、一、实验部分 (3)(1实验1 橡胶的混炼 (3)(2实验2 橡胶的塑炼 (4)(3)实验3 硫化特性实验 (5)(4)实验4 门尼粘度实验 (6)(5)实验5硫化工艺实验 (7)(6)实验6拉伸性能测试 (8)(7)实验7撕裂强度测试 (11)(8)实验8回弹性能测试 (12)(9)实验9硬度测定 (13)(10)实验10密度测定 (14)(11)实验11热空气老化实验 (15)二、二、实验总结……………………………………………………(17)三、三、试验配方及设计说明…………………………………………(18)实验1:橡胶的塑炼一、【实验目的】塑炼实验的目的:在橡胶加工过程中,生胶的可塑性是有一定要求的,有些生胶很硬,可塑性很差,不能满足加工要求。
为了满足加工要求,必须进行塑炼,以提高可塑度,使配合剂易于混入,便于压延,压出,经过塑炼的生胶混炼时与活性填充剂,硫化促进剂等发生化学反应,对硫化速度和凝胶生成量也产生一定影响,另外,胶经过塑炼,质地均一,对硫化胶的物理机械性能也有所改善,所以塑炼是橡胶加工的基础工艺之一。
二、【实验原理】塑炼机理:低温塑炼即机械塑炼,生胶在开放式炼胶机的辊筒上,直接受到机械力的反复作用,庞大的橡胶分子在剪切力的作用下,沿着流动方向伸展,使橡胶分子链上产生局部应力集中,致使分子链断裂,断裂的分子链形成了活性游离基,活性游离基与周围的氧或其他游离基接受体结合而稳定,形成了较短的分子,所以可塑度也就增加了。
即 R-R→2R● R●+O2→R OO●机械塑炼中,生胶随温度降低而粘度增大,剪切力大,分子断裂作用增强,可塑增加较快,所以一般低辊温下塑炼。
三、【实验结果】经过塑炼,胶料的可塑度提高,改善了加工性能,为下一步的加入小药,炭黑,硫磺等配合剂打下了基础。
各种橡胶制品的检测项目和检测标准详情
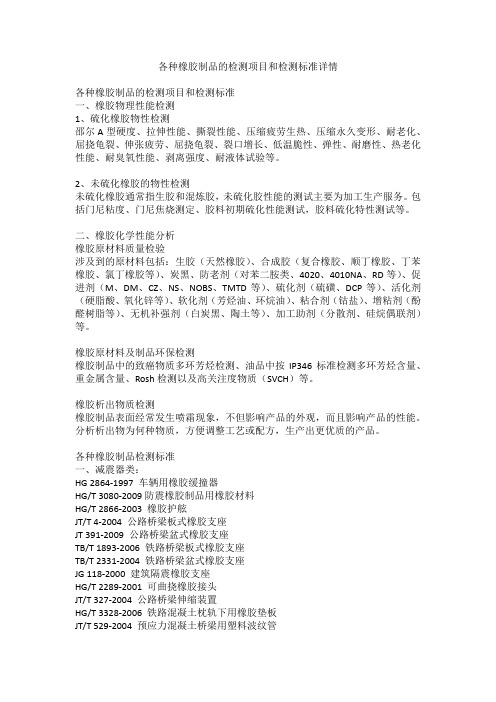
各种橡胶制品的检测项目和检测标准详情各种橡胶制品的检测项目和检测标准一、橡胶物理性能检测1、硫化橡胶物性检测邵尔A型硬度、拉伸性能、撕裂性能、压缩疲劳生热、压缩永久变形、耐老化、屈挠龟裂、伸张疲劳、屈挠龟裂、裂口增长、低温脆性、弹性、耐磨性、热老化性能、耐臭氧性能、剥离强度、耐液体试验等。
2、未硫化橡胶的物性检测未硫化橡胶通常指生胶和混炼胶,未硫化胶性能的测试主要为加工生产服务。
包括门尼粘度、门尼焦烧测定、胶料初期硫化性能测试,胶料硫化特性测试等。
二、橡胶化学性能分析橡胶原材料质量检验涉及到的原材料包括:生胶(天然橡胶)、合成胶(复合橡胶、顺丁橡胶、丁苯橡胶、氯丁橡胶等)、炭黑、防老剂(对苯二胺类、4020、4010NA、RD等)、促进剂(M、DM、CZ、NS、NOBS、TMTD等)、硫化剂(硫磺、DCP等)、活化剂(硬脂酸、氧化锌等)、软化剂(芳烃油、环烷油)、粘合剂(钴盐)、增粘剂(酚醛树脂等)、无机补强剂(白炭黑、陶土等)、加工助剂(分散剂、硅烷偶联剂)等。
橡胶原材料及制品环保检测橡胶制品中的致癌物质多环芳烃检测、油品中按IP346标准检测多环芳烃含量、重金属含量、Rosh检测以及高关注度物质(SVCH)等。
橡胶析出物质检测橡胶制品表面经常发生喷霜现象,不但影响产品的外观,而且影响产品的性能。
分析析出物为何种物质,方便调整工艺或配方,生产出更优质的产品。
各种橡胶制品检测标准一、减震器类:HG 2864-1997 车辆用橡胶缓撞器HG/T 3080-2009防震橡胶制品用橡胶材料HG/T 2866-2003 橡胶护舷JT/T 4-2004 公路桥梁板式橡胶支座JT 391-2009 公路桥梁盆式橡胶支座TB/T 1893-2006 铁路桥梁板式橡胶支座TB/T 2331-2004 铁路桥梁盆式橡胶支座JG 118-2000 建筑隔震橡胶支座HG/T 2289-2001 可曲挠橡胶接头JT/T 327-2004 公路桥梁伸缩装置HG/T 3328-2006 铁路混凝土枕轨下用橡胶垫板JT/T 529-2004 预应力混凝土桥梁用塑料波纹管GB/T 17955-2009桥梁球型支座GB 20688.4-2007橡胶支座第4部分普通橡胶支座二、胶辊类:HG/T 2287-2008 印刷胶辊HG/T 2447-2003 胶辊第4部分印染胶辊HG/T 2446-2005 胶辊第5部分造纸胶辊HG/T 2445-2005 胶辊第6部分电子打字(印)机胶辊HG/T 2697-2001 胶辊第二部分聚氨酯胶辊HG/T 2013-2001胶辊第三部分织物预缩橡胶毯三、汽车类:HG/T 2196-2004 汽车用橡胶材料分类系统GB/T 12730-2008 一般传动用窄V带HG/T 2578-1994 汽车液压制动缸用橡胶护罩HG/T 2491-2009汽车用输水橡胶软管和纯胶管HG/T 3088-1999 车辆门窗橡胶密封条集装箱门框密封条GB/T15846-2006四、橡胶手套:AQ6102-2007 耐酸(碱)手套AQ6101-2007 橡胶耐油手套GB 7543-2006 一次性使用灭菌橡胶外科手套GB 10213-2006 一次性使用医用橡胶检查手套HG/T 2888-1997 橡胶家用手套五、橡胶铺地材料类:HG/T 2015-2003 橡胶海绵地毯衬垫HG/T 3747.1-2004橡塑铺地材料第1部分橡胶地板HG/T 3747.2-2004橡塑铺地材料第2部分橡胶地砖六、橡胶鞋:HG/T 2017-2000 普通运动鞋HG/T 2016-2001 篮排球运动鞋HG/T 2870-1997 乒乓球运动鞋HG/T 3085-1999 橡塑冷粘鞋HG/T 2018-2003 轻便胶鞋HG/T 2019-2001 黑色雨靴(鞋)HG/T 2020-2001 彩色雨靴(鞋)HG/T 2401-1992 工矿靴HG/T 2182-2008 棉胶鞋HG/T 2494-2005 布面童胶鞋HG/T 2495-2007 劳动鞋七、密封制品材料:HG/T 2810-2008 往复运动橡胶密封圈材料HG/T 2811-1996 旋转轴唇形密封圈橡胶材料GB/T 9877-2008液压传动旋转轴唇形密封圈设计规范GB/T 15326-1994 旋转轴唇形密封圈外观质量GB/T 13871.1-2007 密封元件为弹性体材料的旋转轴唇形密封圈第1部分:基本尺寸和公差HG/T 2021-1991 耐高温滑油O型橡胶密封圈材料GB/T 3452.2-2007 液压气动用O形橡胶密封圈第2部分:外观质量检验规范HG/T 3089-2001 燃油用O形橡胶密封圈材料HG/T 2181-2009 耐酸碱橡胶密封件材料HG/T 2579-2008 普通液压系统用0形橡胶密封圈材料GB/T 3452.1-2005 液压气动用O形橡胶密封圈第1部分尺寸系列及公差GB/T3452.2-2007 液压气动用O形橡胶密封圈第2部分:外观质量检验规范GB/T 12002-1989 塑料门窗用密封条HG/T 3099-2004建筑橡胶密封垫预成型实心硫化的结构密封垫用材料规范TB /T 1964-1987 客车门窗用密封条JB/T 7757.2-2006机械密封用O形橡胶圈JC/T 946-2005混凝土和钢筋混凝土排水管用橡胶密封圈JC/T 483-2006 聚硫建筑密封胶HG/T 3326-2007采煤综合机械化设备橡胶密封件用胶料JC/T 748-1987(1996)预应力与自应力钢筋混凝土管用橡胶密封圈GJB 250A-1996耐液压油和燃油丁腈橡胶胶料规范GB/T 15325-1994往复运动橡胶密封圈外观质量GB/T 10708.1-2000往复运动橡胶密封圈结构尺寸系列第一部分单向密封橡胶密封圈GB/T 10708.2-2000往复运动橡胶密封圈结构尺寸系列第二部分双向密封橡胶密封圈GB/T 10708.3-2000往复运动橡胶密封圈结构尺寸第三部分橡胶防尘密封圈GB5135.11-2006自动喷水灭火系统第11部分:沟槽式管接件JC/T976-2005道桥嵌缝用密封胶GB/T 21873-2008橡胶密封件给、排水管及污水管道用接口密封圈材料规范HG2865-1997汽车液压制动橡胶皮碗HG2950-1999汽车制动气室橡胶隔膜GJB 5258-2003航空橡胶零件及型材用胶料规范八、胶带类:GB/T524-2007平型传动带GB/T1171-2006一般传动用普通V带GB/T7984-2001运输带具有橡胶或塑料覆盖层的普通用途织物芯输送带GB/T9770-2001普通用途钢丝绳芯输送带HG/T2297-1992耐热输送带GB/13552-2008汽车多楔带HG/T3647-1999耐寒输送带GB/T13487-2002一般传动用同步带HG/2014-2005钢丝绳牵引阻燃输送带HG/T2442-2001洗衣机V带HG/2539-1993钢丝绳芯难燃输送带HG/T2577-2006橡胶或塑料提升带GB/T10822-2003一般用途织物芯阻燃输送带GB/T20786-2006橡胶履带GB 13552-2008九、汽车多楔带:GB/T 10716-2000 同步带拉伸性能试验方法GB 10717-1989 同步带齿剪切强度试验方法GB/T 7762-2003 硫化橡胶或热塑性橡胶耐臭氧龟裂静态拉伸试验GB/T 1682-1994 硫化橡胶低温脆性的测定单试样法GB/T 3512-2001硫化橡胶或热塑性橡胶热空气加速老化和耐热试验GB/T 11545-2008 带传动汽车工业用V带疲劳试验GB/T 3686-1998 三角带全截面拉伸性能试验方法GB 12732-2008 汽车V带GB/T 7762-2003 硫化橡胶或热塑性橡胶耐臭氧龟裂静态拉伸试验GB 16897-1997 制动软管FMVSS 106 制动软管GB 16897-1997 制动软管FMVSS 106 制动软管GB 16897-1997 制动软管FMVSS 106 制动软管。
实验二 橡胶混炼和压制实验指导书

《橡胶混炼和压制实验》实验指导书材料与能源学院一、实验目的1、熟悉橡胶开炼机、密炼机、平板压制机的结构及工作原理。
2、学习规范的炼胶操作。
3、制备试样,测试硫化胶的物理机械性能。
二、实验原理橡胶的混炼是将生胶和配合剂在开炼机或密炼机上混合均匀并达到一定分散度,制备符合性能要求的混炼胶。
影响开炼机混炼效果的因素主要有胶料的包辊性、装胶容量、辊距、辊温、加料顺序、混炼时间等。
不同生胶及配方体系的加料顺序不同,如天然橡胶加料顺序原则上是:生胶→硬脂酸→氧化锌、促进剂、防老剂→填料→软化剂→硫黄→薄通→下片。
混炼操作方法可采用薄通法或三角包操作法。
(1)薄通法①将辊距调到1.4mm,使橡胶包辊,时间1分钟;②加硬脂酸,两边各作1次3/4拉刀捣胶,时间1分钟;③加氧化锌和硫磺,两边各作1次3/4拉刀捣胶,时间2分钟;④均匀将填料加在辊筒上,当加入大约1/2时,放辊距到1.9 mm,并两边各作1次3/4拉刀,当填料全部加完时,两边各作1次3/4拉刀捣胶,时间10分钟;⑤加促进剂,每边各作3次3/4拉刀捣胶,时间3分钟;⑥取下胶料,调辊距到0.8 mm,并将整辊胶竖着薄通6次;时间3分钟;⑦调大辊距(2.5mm左右),使胶料包辊,出片。
(2)三角包操作法采用较小辊距(1-1.5mm)或较大辊距(2-2.5mm),操作时先将包在前辊上的胶料横向割断,随着辊筒的旋转将左右两边胶料不断地向中间折叠成一个三角包,如此反复进行到规定的次数,使辊筒之间的胶料不断地由两边折向中间,再由中间分散到两边进行混合。
然后放大辊距(2.5mm左右),包辊、出片。
硫化是橡胶加工中最重要的工艺过程之一。
硫化胶性能随硫化时间的长短有很大变化,正硫化时间的选取,决定了硫化胶性能的好坏。
采用橡胶无转子硫化仪可测定未硫化胶料的硫化特性。
实验时,硫化仪的下模腔作一定角度的摆动,在温度和压力作用下,胶料逐渐硫化,其模量逐渐增加,模腔摆动所需要的转矩也成比例增加,由转矩值的大小可反映胶料的硫化程度。
轮胎硫化胶囊用丁基橡胶的硫化特性及耐热氧老化性能的研究
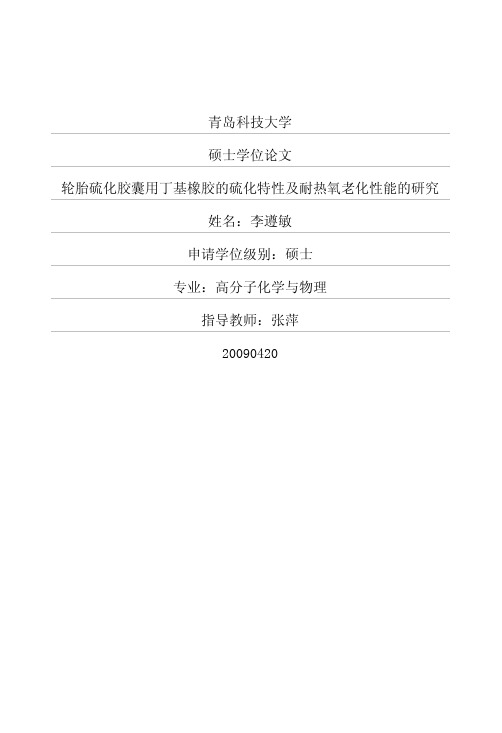
were studied by RPA,tensile strength,tear strength and aging property testing.The eredients doses in the formulation on the vulcanizing and aging properties
KEY WORD S:XIIR Vulcanizing kinetics Orth。g。nal desi弘Scorcmng time
IV
青岛科技人学研究生学位论文
声明
独创性声明
本人声明所呈交的论文是我个人在导师指导下进行的研究工作及取得的研
究成果。尽我所知,除了文中特另J)Jn以标注和致谢中所罗列的内容以外,论文
effects on physical and mechanical properties
of BR.Sulfur has the best combination property as a anti-scorching agent,then are
MgO/DM and DM.CTP almost has no effect on the vulcanization system of resins.
testing of CIIR/BR blend was carried out at 200 oC for 1 2h.The properties of CIIR/BR
vulcanized rubber Can maintain the properties of BR,SO CIIR can substitute CR.
以最优配方为基础,测定了185℃、190℃和195℃三个温度下的硫化曲线,对
轮胎硫化胶囊用丁基橡胶的硫化特性和耐热氧老化性能的研究
橡胶材料检测分类

橡胶材料检测分类
橡胶材料的检测主要涉及物理性质、化学成分、机械性能、耐磨性、耐老化性等方面的测试。
以下是橡胶材料检测的一些常见分类:
1.物理性质测试:
•密度测试:测试橡胶的密度,即单位体积内的质量。
•硬度测试:通过Shore硬度或其他硬度测试方法来测量橡胶的硬度。
•拉伸强度和弹性模量测试:测试橡胶在拉伸时的强度和弹性。
•导电性测试:一些应用需要橡胶具有导电性,通过测试电导率来检测其导电性能。
2.化学成分分析:
•元素分析:测试橡胶中元素的含量,包括碳、氢、氧、硫等。
•有机物分析:通过化学方法分析橡胶中的有机化合物。
•添加剂分析:检测橡胶中的添加剂,如防老剂、硫化剂等。
3.机械性能测试:
•疲劳性能测试:测试橡胶在交变应力下的疲劳性能。
•冲击强度测试:测试橡胶在冲击负载下的性能。
•压缩性能测试:测试橡胶在压缩下的性能。
4.耐磨性和耐老化性测试:
•耐磨性测试:通过磨损测试来评估橡胶的耐磨性。
•耐老化性测试:通过模拟环境老化或加速老化试验来评估橡胶的耐老化性能。
5.温度和湿度测试:
•热性能测试:测试橡胶在高温下的性能,包括热变形温度、膨胀系数等。
•低温性能测试:测试橡胶在低温下的性能,包括冷弯曲、冷屈服等。
•湿热性能测试:评估橡胶在湿热环境下的性能,检测橡胶是否容易发霉、变质等。
这些测试方法和分类会根据橡胶用途的不同而有所变化。
在实际应用中,根据橡胶制品的具体要求,选择适当的测试方法来评估其性能和质量。
干湿法混炼能耗和胶料性能对比研究
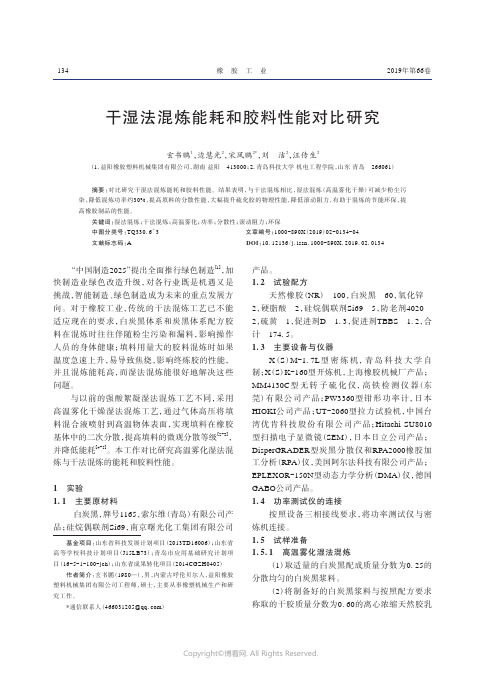
134 橡 胶 工 业2019年第66卷干湿法混炼能耗和胶料性能对比研究玄书鹏1,边慧光2,宋凤鹏2*,刘 洁2,汪传生2(1.益阳橡胶塑料机械集团有限公司,湖南益阳 413000;2.青岛科技大学机电工程学院,山东青岛 266061)摘要:对比研究干湿法混炼能耗和胶料性能。
结果表明,与干法混炼相比,湿法混炼(高温雾化干燥)可减少粉尘污染,降低混炼功率约30%,提高填料的分散性能,大幅提升硫化胶的物理性能,降低滚动阻力,有助于混炼的节能环保,提高橡胶制品的性能。
关键词:湿法混炼;干法混炼;高温雾化;功率;分散性;滚动阻力;环保中图分类号:TQ330.6+3 文章编号:1000-890X(2019)02-0134-04文献标志码:A DOI:10.12136/j.issn.1000-890X.2019.02.0134“中国制造2025”提出全面推行绿色制造[1],加快制造业绿色改造升级,对各行业既是机遇又是挑战,智能制造、绿色制造成为未来的重点发展方向。
对于橡胶工业,传统的干法混炼工艺已不能适应现在的要求,白炭黑体系和炭黑体系配方胶料在混炼时往往伴随粉尘污染和漏料,影响操作人员的身体健康;填料用量大的胶料混炼时如果温度急速上升,易导致焦烧,影响终炼胶的性能,并且混炼能耗高,而湿法混炼能很好地解决这些问题。
与以前的强酸絮凝湿法混炼工艺不同,采用高温雾化干燥湿法混炼工艺,通过气体高压将填料混合液喷射到高温物体表面,实现填料在橡胶基体中的二次分散,提高填料的微观分散等级[2-3],并降低能耗[4-5]。
本工作对比研究高温雾化湿法混炼与干法混炼的能耗和胶料性能。
1 实验1.1 主要原材料白炭黑,牌号1165,索尔维(青岛)有限公司产品;硅烷偶联剂Si69,南京曙光化工集团有限公司产品。
1.2 试验配方天然橡胶(NR) 100,白炭黑 60,氧化锌 2,硬脂酸 2,硅烷偶联剂Si69 5,防老剂4020 2,硫黄 1,促进剂D 1.3,促进剂TBBS 1.2,合计 174.5。
载重子午线轮胎硫化胶囊质量判断标准

载重子午线轮胎硫化胶囊质量判断标准1 目的为了更好的控制成品的质量,减少由于硫化胶囊问题导致的涡气、疏线等缺陷,特制订本标准以适用于本公司使用的载重子午线轮胎硫化胶囊的质量判断。
2 范围本标准适用于本公司使用的载重子午线轮胎硫化胶囊。
3 载重胎硫化胶囊检测3.1 载重胎硫化胶囊抽检频次:在外委托加工和外购且已经正式认可的载重子午线轮胎硫化胶囊,按同生产厂的进货批,进行随机抽检胶囊。
3.2 载重胎硫化胶囊外观检验:通过目视的方法检验硫化胶囊外观质量情况。
①硫化好的胶囊要求没有杂质、气泡和欠硫,没有缺胶、裂口、穿孔等;②上下模口胶边厚度均匀、打磨平整、不能凹陷和凸起;③硫化好的胶囊排气线形式必须符合设计和加工要求。
3.3 载重胎硫化胶囊取样及断面尺寸测量:①胶囊断面测量位置示意图:轴向:D BBd B周向:前右左后②测量步骤一:取单个胶囊分别测出胶囊外直径DB、胶囊夹缘内径dB、胶囊总高度HB、胶囊断面周长LB、胶囊上各段L3、L4、L5的长度及胶囊分模线的定位︱L1-L2︱。
③测量步骤二:把胶囊按90°取4个轴向断面胶条,然后根据胶囊尺寸大小,在每一个轴向断面胶条上都先通过L5的中点定出胶囊中心线CL并量出中心线的厚度Ga;接着找出胶囊分模线并在此分模线上随机取一点A,同时在拐角处定出B、C两点,分别测出A、B、C三点的厚度;接着在A→B每隔50mm取一点并量出该点厚度、在B→C每隔50mm取一点并量出该点厚度;最后量出颈部厚度To、夹缘高度a、夹缘宽度b。
(注意:胶囊的中心线与分模线可能重合,也可能不重合)④完成步骤一与步骤二的测量后,分别将胶囊外直径DB、胶囊夹缘内径dB、胶囊总高度HB、胶囊断面周长LB、胶囊上各段L3、L4、L5的长度、胶囊分模线的定位︱L1-L2︱、中心线的厚度Ga、A、B、C三点的厚度及A→B、B→C这两段各点的厚度、颈部厚度To、夹缘高度a、夹缘宽度b等数据做好相应记录。
硫化橡胶的力学性能
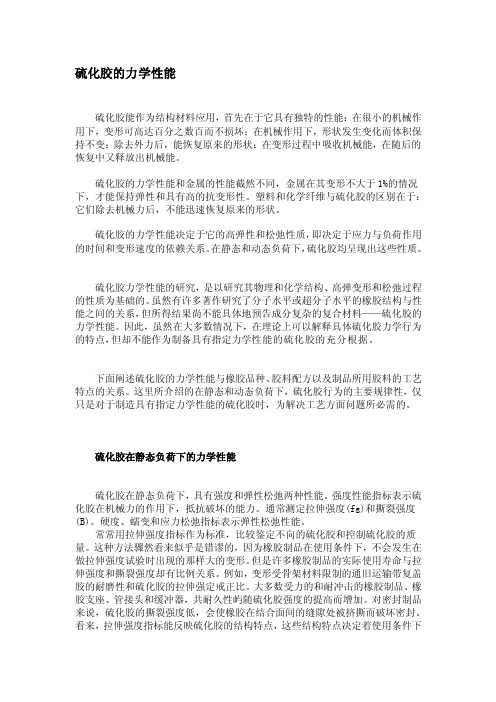
硫化胶的力学性能硫化胶能作为结构材料应用,首先在于它具有独特的性能:在很小的机械作用下,变形可高达百分之数百而不损坏;在机械作用下,形状发生变化而体积保持不变:除去外力后,能恢复原来的形状:在变形过程中吸收机械能,在随后的恢复中又释放出机械能。
硫化胶的力学性能和金属的性能截然不同,金属在其变形不大于1%的情况下,才能保持弹性和具有高的抗变形性。
塑料和化学纤维与硫化胶的区别在于:它们除去机械力后,不能迅速恢复原来的形状。
硫化胶的力学性能决定于它的高弹性和松弛性质,即决定于应力与负荷作用的时间和变形速度的依赖关系。
在静态和动态负荷下,硫化胶均呈现出这些性质。
硫化胶力学性能的研究,是以研究其物理和化学结构、高弹变形和松弛过程的性质为基础的。
虽然有许多著作研究了分子水平或超分子水平的橡胶结构与性能之间的关系,但所得结果尚不能具体地预告成分复杂的复合材料——硫化胶的力学性能。
因此,虽然在大多数情况下,在理论上可以解释具体硫化胶力学行为的特点,但却不能作为制备具有指定力学性能的硫化胶的充分根据。
下面阐述硫化胶的力学性能与橡胶品种、胶料配方以及制品所用胶料的工艺特点的关系。
这里所介绍的在静态和动态负荷下,硫化胶行为的主要规律性,仅只是对于制造具有指定力学性能的硫化胶时,为解决工艺方面问题所必需的。
硫化胶在静态负荷下的力学性能硫化胶在静态负荷下,具有强度和弹性松弛两种性能。
强度性能指标表示硫化胶在机械力的作用下,抵抗破坏的能力。
通常测定拉伸强度(fg)和撕裂强度(B)。
硬度、蠕变和应力松弛指标表示弹性松弛性能。
常常用拉伸强度指标作为标准,比较鉴定不向的硫化胶和控制硫化胶的质量。
这种方法骤然看来似乎是错谬的,因为橡胶制品在使用条件下,不会发生在做拉伸强度试验时出现的那样大的变形。
但是许多橡胶制品的实际使用寿命与拉伸强度和撕裂强度却有比例关系。
例如,变形受骨架材料限制的通旧运输带复盖胶的耐磨性和硫化胶的拉伸强定戒正比。
EPDM硫化体系

性,喷霜就会减轻或不喷霜,如配方A促进剂BZ使用多达 1 5 份仍不喷霜,从结
构上看,TMTD比TRA更易造成EPDM硫化胶喷霜,配方 7 快速喷霜能说
明这一点;喷霜还会由促进剂间相互作用引起,如配方 6,各种促进剂用量都不算
大,但硫化胶却喷霜。总而言之,喷霜首先由配合剂结构决定,与胶料不相容的配
合剂易喷霜;其次,配合剂间的相互作用既可以减少也可能加剧喷霜;再者,胶料
炼胶抗焦烧而且硫化速度快。使用了DM,CZ的配方 8,9,10,11,12 有较长的
t10,配方 10,12 相比,不需要很多CZ即可达到延长t10 的目的,一般情况下 0
5 份DM或CZ就足够了,配方 10,11 可以证明;若超速或超超速的促进剂用量
比较大时,应适当增加DM或CZ的用量,如配方 3 的t10 就较小;DM与CZ
很容易造成喷霜。配方 12 使用了 5 7 份的促进剂,仅硫化特性比较好,而物理机
械性能并不十分突出。ZBPD为新型的进口EPDM专用促进剂,与市场上常
用的EG-3(数种超速促进剂复合物)一样有硫化速度快、交联密度大、不易喷
霜等特点,但某些物理机械性能不佳。ZBPD可能是一种相对分子量很大的促
进剂,它需要较高用量才有较好的效果。对比配方 9,10,有效硫含量相同时,用 0 .1
作用机理又有所不同,配方设计时应加以区分。仅从物理机械性能来看,配方
2,3,10,11 硫化胶的拉伸强度大,撕裂强度高,拉断伸长率高,拉断永久变形低,
综合性能好。
2. 3 各硫化体系对EPDM硫化胶喷霜的影响/VwhX W
配方 5,7 硫化结束后立即喷霜,配方C,D在室温、阴凉处搁置两天后
喷霜,配方D喷霜很轻微,配方 6,9 经加速喷霜实验后才喷霜。配方 9,10 的主要
橡胶制品硫化的三大参数:时间、温度、压力
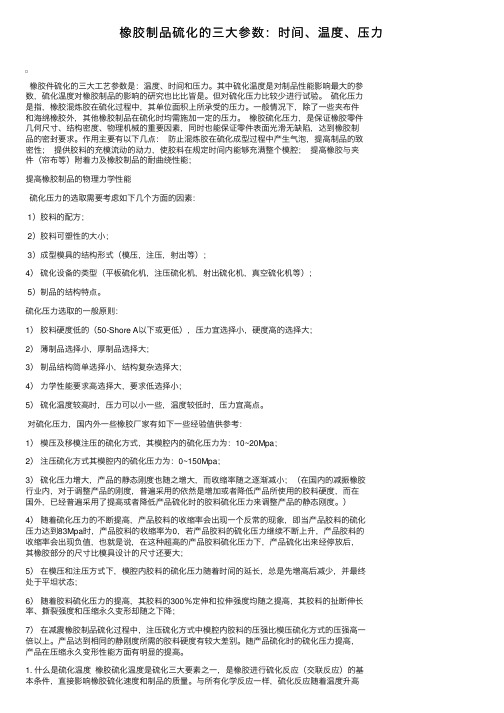
橡胶制品硫化的三⼤参数:时间、温度、压⼒橡胶件硫化的三⼤⼯艺参数是:温度、时间和压⼒。
其中硫化温度是对制品性能影响最⼤的参数,硫化温度对橡胶制品的影响的研究也⽐⽐皆是。
但对硫化压⼒⽐较少进⾏试验。
硫化压⼒是指,橡胶混炼胶在硫化过程中,其单位⾯积上所承受的压⼒。
⼀般情况下,除了⼀些夹布件和海绵橡胶外,其他橡胶制品在硫化时均需施加⼀定的压⼒。
橡胶硫化压⼒,是保证橡胶零件⼏何尺⼨、结构密度、物理机械的重要因素,同时也能保证零件表⾯光滑⽆缺陷,达到橡胶制品的密封要求。
作⽤主要有以下⼏点:防⽌混炼胶在硫化成型过程中产⽣⽓泡,提⾼制品的致密性;提供胶料的充模流动的动⼒,使胶料在规定时间内能够充满整个模腔;提⾼橡胶与夹件(帘布等)附着⼒及橡胶制品的耐曲绕性能;提⾼橡胶制品的物理⼒学性能硫化压⼒的选取需要考虑如下⼏个⽅⾯的因素:1)胶料的配⽅;2)胶料可塑性的⼤⼩;3)成型模具的结构形式(模压,注压,射出等);4)硫化设备的类型(平板硫化机,注压硫化机,射出硫化机,真空硫化机等);5)制品的结构特点。
硫化压⼒选取的⼀般原则:1)胶料硬度低的(50-Shore A以下或更低),压⼒宜选择⼩,硬度⾼的选择⼤;2)薄制品选择⼩,厚制品选择⼤;3)制品结构简单选择⼩,结构复杂选择⼤;4)⼒学性能要求⾼选择⼤,要求低选择⼩;5)硫化温度较⾼时,压⼒可以⼩⼀些,温度较低时,压⼒宜⾼点。
对硫化压⼒,国内外⼀些橡胶⼚家有如下⼀些经验值供参考:1)模压及移模注压的硫化⽅式,其模腔内的硫化压⼒为:10~20Mpa;2)注压硫化⽅式其模腔内的硫化压⼒为:0~150Mpa;3)硫化压⼒增⼤,产品的静态刚度也随之增⼤,⽽收缩率随之逐渐减⼩;(在国内的减振橡胶⾏业内,对于调整产品的刚度,普遍采⽤的依然是增加或者降低产品所使⽤的胶料硬度,⽽在国外,已经普遍采⽤了提⾼或者降低产品硫化时的胶料硫化压⼒来调整产品的静态刚度。
)4)随着硫化压⼒的不断提⾼,产品胶料的收缩率会出现⼀个反常的现象,即当产品胶料的硫化压⼒达到83Mpa时,产品胶料的收缩率为0,若产品胶料的硫化压⼒继续不断上升,产品胶料的收缩率会出现负值,也就是说,在这种超⾼的产品胶料硫化压⼒下,产品硫化出来经停放后,其橡胶部分的尺⼨⽐模具设计的尺⼨还要⼤;5)在模压和注压⽅式下,模腔内胶料的硫化压⼒随着时间的延长,总是先增⾼后减少,并最终处于平坦状态;6)随着胶料硫化压⼒的提⾼,其胶料的300%定伸和拉伸强度均随之提⾼,其胶料的扯断伸长率、撕裂强度和压缩永久变形却随之下降;7)在减震橡胶制品硫化过程中,注压硫化⽅式中模腔内胶料的压强⽐模压硫化⽅式的压强⾼⼀倍以上。
硫化用量对SIBR性能的影响

98在1984年Nordsiek [1]提出集成橡胶概念,即通过分子设计把几种橡胶的特点集于一身后,1985年德国Hüls公司首先开发成功苯乙烯-异戊二烯-丁二烯共聚橡胶(SIBR)并实现工业化,商品名为Vestogral;1990年美国Goodyear公司亦开始研究SIBR,翌年投入生产,商品名为Cyber [2]。
二者都主要用于全天候、长寿命高速轮胎。
集成橡胶SIBR作为一种新型的主要用于轮胎胎面的合成橡胶,是迄今为止性能最为全面的聚二烯烃类橡胶[3]。
其显著特点是分子链由多种结构的链段构成,不同结构的链段提供给橡胶不同的性能。
这样,集成橡胶SIBR 集成了各种橡胶的优点而弥补了各种橡胶的不足,同时满足了轮胎胎面对全天候、长寿命和经济性的要求,集成橡胶的这些优点使它至今仍是科研人员研究的热点[4-6]。
中国石化北京化工研究院燕山分院结合自己的技术优势和特点,采用一步加料法合成SIBR。
在模试和中试装置上进行了大量的基础研究,合成出了物理机械性能和动态力学性能均较突出的集成橡胶并申请了多项专利,还成功开发出了工业化牌号SIBR2505和SIBR2535。
集成橡胶具有优异的动态力学性能和较好的物理机械性能是其他胶种无法比拟的,完全满足胎面用胶要求具有优异的抗湿滑性能和低滚动阻力性能的需求,从而将促进高速公路网的蓬勃发展。
SIBR的成功开发也将进一步解决我国碳五资源的综合利用问题。
本工作主要研究了在硫磺硫化体系下,不同硫磺用量对SIBR的加工性能、硫化特性及硫化胶的物理机械性能、动态力学性能,以及老化性能的影响规律。
1 实验部分1.1 配方生胶SIBR 100份[S/I/B=20/40/40(质量百分比)];炭黑N330 65份;氧化锌 4份;硬脂酸 2份;防老剂 4.5份;芳烃油 10份;其他 1.7份;促进剂NS 1.4份;硫磺1.4~2.0份。
1.2 混炼工艺一段工艺:1.57L Farril密炼机,温度80℃ 、转速 80r/min。
橡胶工艺原理-复习思考题-+答案

橡胶工艺原理-复习思考题-+答案(总12页)--本页仅作为文档封面,使用时请直接删除即可----内页可以根据需求调整合适字体及大小--《橡胶工艺原理》复习思考题名词解释碳链橡胶、硬质橡胶、杂链橡胶、混炼胶、硫化胶、冷冻结晶、拉伸结晶、极性橡胶杂链橡胶:碳-杂链橡胶: 主链由碳原子和其它原子组成全杂链橡胶:主链中完全排除了碳原子的存在,又称为“无机橡胶”,硅橡胶的主链由硅、氧原子交替构成。
混炼胶:所谓混炼胶是指将配合剂混合于块状、粒状和粉末状生胶中的未交联状态,且具有流动性的胶料硫化胶 : 配合胶料在一定条件下(如加硫化剂、一定温度和压力、辐射线照射等)经硫化所得网状结构橡胶谓硫化胶,硫化胶是具有弹性而不再具有可塑性的橡胶,这种橡胶具有一系列宝贵使用性能。
硬质橡胶:玻璃化温度在室温以上、简直不能拉伸的橡胶称为硬质橡胶一般来说,塑料、橡胶、纤维的分子结构各有什么特点影响橡胶材料性能的主要因素有哪些?橡胶性能主要取决于它的结构,此外还受到添加剂的种类和用量、外界条件的影响。
(1) 化学组成:单体,具有何种官能团(2) 分子量及分子量分布(3) 大分子聚集状况:空间结构和结晶(4) 添加剂的种类和用量(5) 外部条件:力学条件、温度条件、介质简述橡胶分子的组成和分子链结构对橡胶的物理机械性能和加工性能的影响。
答:各种生胶的MWD曲线的特征不同,如NR一般宽峰所对应的分子量值为30~40万,有较多的低分子部分。
低分子部分可以起内润滑的作用,提供较好的流动性、可塑性及加工性,具体表现为混炼速率快、收缩率小、挤出膨胀率小。
分子量高部分则有利于机械强度、耐磨、弹性等性能。
简述橡胶的分类方法。
答:按照来源用途分为天然胶和合成胶,合成胶又分为通用橡胶和特种橡胶;按照化学结构分为碳链橡胶、杂链橡胶和元素有机橡胶;按照交联方式分为传统热硫化橡胶和热塑性弹性体。
简述橡胶的分子量和分子量分布对其物理机械性能和加工性能的影响。
- 1、下载文档前请自行甄别文档内容的完整性,平台不提供额外的编辑、内容补充、找答案等附加服务。
- 2、"仅部分预览"的文档,不可在线预览部分如存在完整性等问题,可反馈申请退款(可完整预览的文档不适用该条件!)。
- 3、如文档侵犯您的权益,请联系客服反馈,我们会尽快为您处理(人工客服工作时间:9:00-18:30)。
PPT文档演模板
硫化胶综合物理机械性能的测试
n 电子拉力机自动记录负荷—伸长率曲线
PPT文档演模板
硫化胶综合物理机械性能的测试
五、试验数据处理
• 拉伸强度(tensile strength): • 定伸应力(modulus):
PPT文档演模板
硫化胶综合物理机械性能的测试
• 二.实验设备
PPT文档演模板
拉力试验机,目 前多采用电子拉力 试验机 可进行拉伸、压 缩、弯曲、剪切、 剥离和撕裂等力学 性能试验。 附加控温装置可 进行高低温条件下 的力学性能试验。
硫化胶综合物理机械性能的测试
• 三.试样制备
n 硫化胶试片在室温停放6小时后,选用标准裁刀裁切出 哑铃形试样;
无割口直角形
PPT文档演模板
硫化胶综合物理机械性能的测试
三、试样的制备
国家标准GB529和GB530对试样的裁取和圆弧型试样割 口方法均有规定。
1、试样的裁取
圆弧型和直角型试样均用裁刀裁取。裁刀刃口应保持锋利, 不应出现缺口或卷刃等现象。裁取试样时,裁刀撕裂角等 分线的方向应与胶料压延、压出方向一致,即试样的长度 方向应与压延、压出方向垂直。
撕裂强度(tear strength):
试样撕裂时,单位厚度所承受 的负荷,kN/m
——抗撕裂性、抗裂口增长
式中 Fsz—直角型试样撕裂强度,kN/m(kgf/cm);
F—撕裂试样的最大作用力,N(kgf);
d—试样厚度,mm。
每个样品至少需要五个试样。试样结果以测量结果的 算术平均值表示。
硫化胶综合物理机械性 能的测试
PPT文档演模板
2020/11/30
硫化胶综合物理机械性能的测试
橡胶的性能
n 橡胶的性能可以分为两类:未硫化胶的性能即加工性 能和硫化胶的性能即使用性能。
n 加工性能:门尼粘度、门尼焦烧、硫化特性;
n 使用性能:综合物理机械性能 粘弹性能 老化性能(疲劳、热氧、臭氧、天候) 耐磨性 阻燃性 耐低温性能 …………
2.抬起摆锤至水平位置,并用机架上的挂钩挂住,将指针调至 零位。
3.松开挂钩,摆锤自由落下冲击试样,对试样进行不少于3次 但不多于7次的连续冲击,作为机械调节。(本试验中统 一规定连续冲击四次,不记回弹值)。
4.在进行机械调节后,进行第五次冲击,并读取回弹值。每个 试样测定三点,各点之间距离不少于10mm,取三点数值 的中间值表示一个试样的回弹性,两个试样中值的算术平 均值作为该样品的测试结果。
n 用1公斤外力把硬度计的压针,以弹簧的压力压入试样表 面的深浅来表示其硬度。橡胶受压将产生反抗其压入的反 力,直到弹簧的压力与反力相平衡,橡胶越硬,反抗压针 压入的力量越大,使压针压入使样表面深度越浅,而弹簧 受压越大,金属轴上移越多,故指示的硬度值越大,反之
则相反。
PPT文档演模板
硫化胶综合物理机械性能的测试
3、测试步骤
(1)硫化后的试片应在标准室温下停放(不少于6小时, 不超过15天)。
(2)采取试样,注意压延方向。
(3)将试样垂直夹于夹持器中,调好拉伸速度 (500mm/min),开动试验机,即可对试样施加一个逐 渐增加的牵引力,直至试样被撕断后停机。
PPT文档演模板
硫化胶综合物理机械性能的测试
五、试验结果处理
PPT文档演模板
硫化胶综合物理机械性能的测试
六、结果的影响因素
1.试样形状:试样形状对试验结果有显著影响。直角型试样的 撕裂强度较小,而圆弧型试样的撕裂强度较高。
2.试验温度:橡胶的撕裂性能对试验温度比较敏感。一般来说, 撕裂强度随试验温度的升高而降低。
3.撕裂速度:高速撕裂时,撕裂表现出刚体的脆性破坏,而慢 速撕裂时,则表现出弹性破坏。在试验方法规定的速度下, 撕裂破坏属于后者。拉伸速度增大,撕裂强度降低。
PPT文档演模板
硫化胶综合物理机械性能的测试
撕裂强度
•一、实验目的
1、了解撕裂试样种类,掌握撕裂试样的制 备
2、熟悉测试撕裂强度的设备及其工作原理 3、掌握实验结果的分析 4、掌握影响撕裂强度的因素
PPT文档演模板
硫化胶综合物理机械性能的测试
二、试样种类形状
PPT文档演模板
硫化胶综合物理机械性能的测试
4.压针长度对试验结果的影响:在标准中规定邵尔A型硬度
计的压针露出加压面的高度为
。
5.压针形状和弹簧的性能对结果的影响:硬度计用久后,弹 簧容易变形,或压针的针头易磨损,影响测试结果的准 确性。因此硬度计应定期进行压针形状尺寸的检查和弹 簧应力的校正。
PPT文档演模板
硫化胶综合物理机械性能的测试
冲击弹性
PPT文档演模板
硫化胶综合物理机械性能的测试
•二、实验仪器
邵尔硬度是目前国际上应 用比较广泛的一种硬度。 这种硬度一般分为A、C、 D等几种型号。
邵尔A型为测量软质橡胶, C型测量半硬质橡胶,D型 是测量硬质橡胶硬度。
PPT文档演模板
硫化胶综合物理机械性能的测试
三、实验原理
硬度 (hardness): 抵抗外力压入的 能力,邵A
试样拉断时,不可恢复部分与原始 长度之比,%
——塑性变形
H—扯断永久变形,%; L2—试样扯断后停放3分钟后对起
来的标距,mm; L0—试样初始标距,mm。
PPT文档演模板
硫化胶综合物理机械性能的测试
•注意问题
拉伸性能试验中所需的试样数量应不少于3个,但 是对于一些鉴定、评比、仲裁等试验中的试样数量 应不少于5个,取全部数据中的中位数。试验数据 按数值递增的顺序排列,试验数据如为奇数,取其 中间数值为中位数,若试验数据为偶数,取其中间 的两个数值的算术平均值为中位数。
2、试样割口方法
圆弧形试样试验前应于圆弧凹边的中心处割口。割口深度 为0.500.05mm。可采用特制的割口器进行割口。
PPT文档演模板
硫化胶综合物理机械性能的测试
四、实验方法
1、试样条件:试验应在标准试验室温度232℃下进行。试 验前在标准环境下停放应不少于30分钟。
2、厚度测量:2.00.3mm。
PPT文档演模板
硫化胶综合物理机械性能的测试
六、试验的影响因素
1.温度的影响:当温高时,硬度值降低。
2.试样厚度的影响:试样低于要求的厚度,硬度计压杆则会 受到承托试样用玻璃片的影响,使硬度值增大。
3.读数时间的影响:压针与试样受压后立即读数与指针稳定 后再读数,所得结果相差很大,前者高,后者偏低,二 者之差可达5~7度。
n 如果从成品上直接切取试样,要求试样中应无 纤维或增强骨架材料。如果厚度达不到要求时, 可以用几层叠起来测量,但最多不得超过三层。 各层间严格要求平行、光滑。
PPT文档演模板
硫化胶综合物理机械性能的测试
五、试验步骤
1.调整试验机呈水平状态,将试样平稳地夹在夹持器上,使摆 锤同试样表面呈刚接触(相切)状态。
五、试验步骤
•按GB531标准进行 n 试验前检查试样,如表面杂质需用纱布沾酒精擦净。观
察硬度计指针是否指于零点,并检查压针压于玻璃面上 是否指100。
n 将试样置于硬度计玻璃面上,在试样缓慢地受到负荷后 1秒内读数。
n 试样上的每一点只准测量一次硬度,点与点间距离不少 于10mm。
n 每个试样的测量点不少于3个,取其中值为试验结果。
PPT文档演模板
硫化胶综合物理机械性能的测试
3rew
演讲完毕,谢谢听讲!
再见,see you again
PPT文档演模板
2020/11/30
硫化胶综合物理机械性能的测试
PPT文档演模板
硫化胶综合物理机械性能的测试
•六、试验影响因素
1.试验温度的影响:一般来说,随室温升高,拉伸强度、定伸应力降低, 而扯断伸长率则提高。GB2941标准规定试验温度为232℃。
2.试样宽度的影响:不同规格的试样所得试验结果没有可比性。同一种 试样的工作部分越宽,其拉伸强度和扯断伸长率都有所降低。
•一、实验目的
1、掌握冲击弹性的测试原理 2、掌握冲击弹性的试样要求及制备 3、掌握冲击弹性实验结果的处理
PPT文档演模板
硫化胶综合物理机械性能的测试
二、仪器结构
n 冲击弹性试验机
n 弹性值可直接读 出
PPT文档演模板
硫化胶综合物理机械性能的测试
三、试 样
n 任意形状的胶板,厚度为120.5mm,表面应清 洁、平整、无气泡,上下表面平行。
4.试样厚度:试样厚度对撕裂强度有一定影响,但影响不大。 5.分子的取向:横向的撕裂强度大于纵向。
PPT文档演模板
硫化胶综合物理机械性能的测试
硬度
•一、实验目的
1、了解硬度计的种类 2、熟悉邵尔型硬度计的工作原理 3、掌握测硬度试样的制备方法及测试步骤 4、掌握硬度数据的处理 5、掌握影响硬度的因素
3.试样厚度的影响“标准规定厚度为2.00.3mm。随着试样厚度的增加, 其拉伸强度和扯断伸长率都降低。
4.拉伸速度的影响:标准规定拉伸速度为500mm/min。拉伸速度越快, 拉伸强度越高。
5.试样停放时间的影响:GB2941标准规定,停放时间不能小于16小时, 最多不得超过15天。
6.压延方向与试样ቤተ መጻሕፍቲ ባይዱ持状态:GB528标准规定,片状试样在拉伸时,其 受力方向应与压延、压出方向一致,否则其试验结果会显著降低。
硫化胶综合物理机械性能的测试
断裂伸长率 (elongation at break):
• 试样拉断时,伸长部分与原始长度之比,%
•
——最大变形量
PPT文档演模板