钢材锻造
钢材锻造工艺

钢材锻造是一种常见的金属加工工艺,通过对钢材进行加热和机械力的作用,改变其形状和性能。
下面是一般钢材锻造的工艺流程:
钢材选材:选择适合锻造的钢材,通常选择具有良好锻造性能和适当强度的材料。
加热:将选好的钢材加热至适当温度,使其达到良好的可塑性。
加热温度根据钢材的成分和要求来确定。
锻造准备:将加热好的钢坯放置在锻造设备上,并调整设备的工作参数,如锻造力、锻击次数等。
锻造操作:在加热好的钢坯上施加压力,通过锤击、挤压或压力机等方式,使钢材发生塑性变形,改变其形状。
锤击力和次数根据锻件形状和要求来确定。
退火处理:锻造后的钢件通常会存在一定的残余应力和组织不均匀性,通过热处理,将其加热至适当温度再缓慢冷却,以减少应力和改善组织性能。
后续处理:根据产品要求,可能需要进行后续加工工艺,如切割、修整、热处理、表面处理等。
以上是钢材锻造的一般工艺流程,具体的工艺操作和参数会根据锻件的形状、尺寸和要求而有所不同。
钢材锻造是一项复杂的技术工艺,需要经验丰富的操作人员和先进的设备来保证产品的质量和性能。
钢加工产品分为轧制、锻造钢坯和钢材两大类。

钢加工产品分为轧制、锻造钢坯和钢材两大类。
一、轧制、锻造钢坯轧制、锻造钢坯是用于生产钢材的半成品一般不能直接供社会使用。
轧制钢坯是指对炼钢系统生产的钢锭或连铸坯通过轧钢系统的轧制设备加工成的钢坯锻造钢坯是指对炼钢系统生产的钢锭通过锻造设备加工成的钢坯。
轧制、锻造钢坯产品分类结构如图所示二、钢材钢材是具备了一定质量标准尺寸、形状、化学性能和物理性能并可以直接供社会使用的产品。
一钢材产品的分类钢材用途广泛品种繁多。
为了适应统计、生产、营销、库存等多种管理工作的需要对钢材按各种属性和标志进行归类、分组例如按化学成分、按加工工艺、按品种规格、按用途等进行分类有的采用并列分组有的采用层次分组。
钢材产品的分类结构如图所示二主要钢材类别、品种的名词解释1、型钢型钢是指产品断面形状如字母H、I、U、L、Z、T等较复杂形状的钢材。
生产方法主要有热轧、冷轧、挤压、锻压、冷拔等。
型材产品断面形状复杂、品种规格繁多。
按断面高度分为大型型钢、中小型型钢按断面形状分为H型钢、I型钢工字钢、U型钢槽钢、L型钢角钢、球扁钢等。
型材广泛应用于国民经济各部门如工字钢主要用于建筑构件、桥梁制造、船舶制造等槽钢主要用于建筑结构、车辆制造等窗框钢主要用于工业和民用建筑等。
2、板带板带是指其厚度尺寸远远小于其宽度、长度尺寸的钢材呈单张平板或卷状一般用厚×宽×长表示其规格。
呈单张的称为钢板呈卷状的称为钢带。
钢板按厚度分为特厚板、厚板、中板、薄板按生产方法分为热轧板、冷轧板按表面特征?治 菩堪濉⒍莆 濉⑼坎惆宓劝从猛痉治 帕喊濉⒐ 濉⒃齑 濉⒆凹装濉⑵ 蛋濉⒌绻じ职宓劝锤值幕 С煞址治 呛辖鸶职濉⒌秃辖鸶职濉⒑辖鸶职搴筒恍飧职濉8执 纯矶确治 砀执 ⒄ 执 8职濉⒖砀执 ⒄ 执 那 职床 费槭杖肟馐钡男翁 娓窠 腥范ā0宕 陌匆陨细髦址掷嘧酆戏治 睾癜濉⒑癜濉⒅邪濉⑷仍 “濉⒗湓 “濉⒅泻窨砀执 ⑷仍 】砀执 ⒗湓 】砀执 ⑷仍 执 ⒗湓 执 ⒍撇惆宕 ⑼坎惆宕 ⒌绻じ职宕 ?3个品种。
a105锻钢温度范围

a105锻钢温度范围
(最新版)
目录
1.锻钢的概述
2.锻钢的温度范围
3.锻钢温度范围的重要性
4.结论
正文
一、锻钢的概述
锻钢是一种通过锻造工艺生产的钢材,具有较高的强度、韧性和耐磨性。
它广泛应用于各种重型机械、汽车、船舶、铁路等领域的重要部件制造。
在锻钢生产过程中,温度的控制是至关重要的,因为温度对锻钢的性能和质量有着直接的影响。
二、锻钢的温度范围
锻钢的温度范围通常分为三个阶段:预热、锻造和退火。
1.预热:在锻造之前,需要对钢材进行预热处理,以使其具有较好的塑性和可锻性。
预热的温度一般在 700-900 摄氏度之间,具体温度取决于钢材的种类和厚度。
2.锻造:预热后的钢材进入锻造阶段,此时温度会进一步升高,一般在 900-1200 摄氏度之间。
在这个温度范围内,钢材具有较好的可锻性,能够满足各种锻造工艺的要求。
3.退火:锻造完成后,为了消除内部应力和改善钢材的性能,需要进行退火处理。
退火一般在 500-700 摄氏度进行,这个温度范围内可以有效地改善钢材的组织结构和性能。
三、锻钢温度范围的重要性
在锻钢生产过程中,温度范围的控制对于确保锻钢的质量和性能至关重要。
如果温度过低,钢材的塑性和可锻性会受到影响,导致锻造过程中出现裂纹、折叠等缺陷;如果温度过高,钢材的晶粒结构会变粗,影响其性能和耐久性。
因此,合理控制锻钢的温度范围,对于提高锻钢的质量和性能具有重要意义。
四、结论
总之,锻钢的温度范围在锻造过程中起着关键作用。
热轧圆钢国标和锻造圆钢国标的区别

热轧圆钢国标和锻造圆钢国标的区别1. 概述大家好,今天咱们来聊聊热轧圆钢和锻造圆钢这两位“钢铁兄弟”的故事。
首先,咱们得明白,圆钢这个大家伙可不是随便就能造的,它有自己的国标。
这些国标就像是圆钢的身份证,告诉我们它的性格、品质和用途。
那么,热轧和锻造到底有什么不同呢?别急,咱们慢慢来。
1.1 热轧圆钢的特点先说说热轧圆钢。
想象一下,热轧就像在高温下烹饪美食,先把钢材加热到足够的温度,然后用大机器轧制。
这个过程就像是把面团揉捏成形,最后得出一根光滑的圆钢。
热轧圆钢的优点是生产效率高,价格相对便宜,适合用于建筑、机械等领域。
就像大街小巷的路灯,常见又可靠。
热轧圆钢的表面一般比较光滑,但也不乏一些小瑕疵。
这些瑕疵虽然不影响使用,但就像一块美食上的小沙粒,虽小却得注意。
热轧的规格也很多,从6mm到100mm不等,满足不同需求的朋友们,真是“众口难调”,可是大部分人还是喜欢这款性价比高的选择。
1.2 锻造圆钢的特点再说说锻造圆钢,听这个名字就觉得有点牛气,没错,它就是那种经过高温锻打的“钢铁英雄”。
锻造圆钢的制作过程可比热轧复杂多了,简单来说,就是把钢材在高温下锻打成型,利用锤子的力量把钢材的分子结构调整得更紧密,强度更高。
就像是一个健身达人,经过不断锤炼,变得肌肉发达,浑身都是力量。
锻造圆钢的优点在于它的强度和韧性,像个坚韧不拔的战士,面对各种挑战都能挺得住。
而且,锻造圆钢的表面质量更好,外观整齐漂亮,适合用于航空航天、高端机械等领域。
可不是什么都能用得上它,有点儿像那个总是被追捧的“明星”,可不是谁都能请得起的。
2. 主要区别那么,两者到底有什么区别呢?咱们来对比一下。
2.1 生产工艺首先,生产工艺就是一大关键。
热轧圆钢是通过轧制的方式加工,而锻造圆钢则是通过锻打的方式。
这个就好比是用机器做面包和用手工做面包,后者更讲究工艺,结果自然不同。
2.2 性能对比性能方面,锻造圆钢更胜一筹。
因为它的分子结构更紧密,所以强度和韧性都好很多,抗疲劳能力也很强。
常见锻造缺陷
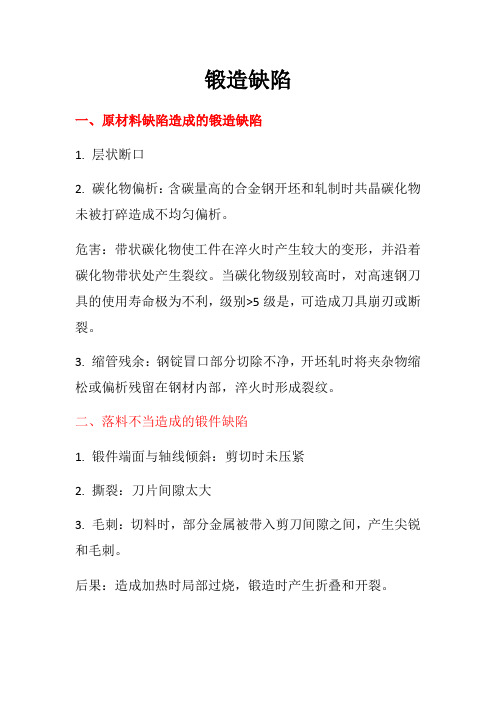
锻造缺陷一、原材料缺陷造成的锻造缺陷1. 层状断口2. 碳化物偏析:含碳量高的合金钢开坯和轧制时共晶碳化物未被打碎造成不均匀偏析。
危害:带状碳化物使工件在淬火时产生较大的变形,并沿着碳化物带状处产生裂纹。
当碳化物级别较高时,对高速钢刀具的使用寿命极为不利,级别>5级是,可造成刀具崩刃或断裂。
3. 缩管残余:钢锭冒口部分切除不净,开坯轧时将夹杂物缩松或偏析残留在钢材内部,淬火时形成裂纹。
二、落料不当造成的锻件缺陷1. 锻件端面与轴线倾斜:剪切时未压紧2. 撕裂:刀片间隙太大3. 毛刺:切料时,部分金属被带入剪刀间隙之间,产生尖锐和毛刺。
后果:造成加热时局部过烧,锻造时产生折叠和开裂。
4. 端部裂纹:剪切大断面坯料时,圆形端面变成椭圆形,材料中产生很大的内应力,引起应力裂纹。
另外,气割落料前,原材料没有预热,产生加工应力导致裂纹5. 凸芯开裂:车床下料时,棒料端面中心留有凸芯,锻造时凸芯冷却快,由于应力集中造成开裂。
三、锻造工艺不当造成的缺陷1. 过热:加热停留时间过长或加热温度过高引起材料晶粒粗大2. 过烧:过烧时,晶粒特别粗大,断口呈石状。
对碳钢,金相组织出现晶界氧化和熔化;工模具钢晶界因为熔化而出现鱼骨状莱氏体;铝合金出现晶界熔化三角区或复熔球。
3. 锻造裂纹1)加热裂纹:尺寸大的坯料快速加热造成内外温差大,热应力大造成开裂。
特征:由中心向四周辐射状扩展,多产生于高合金材料2)心部开裂:常在坯料的头部,开裂深度与加热和锻造有关,有事贯穿整个坯料。
原因:加热时保温不足,坯料未热透,外部温度高,塑性好,变形大,内部温度低变形小,内外产生不均匀变形3)材质缺陷开裂:锻造时在缩孔夹渣碳化物偏析等材料缺陷处形成锻造裂纹4. 脱碳和增碳1)脱碳:钢材表面在高温下,碳被氧化发生脱碳,使表层组织含碳量下降,硬度下降,强度下降,脱碳层的深度与钢的成分、炉内气氛、温度有关。
通常高碳钢易氧化脱碳,氧化性气氛中易脱碳。
第17章锻造成形过程中的缺陷及产生原因
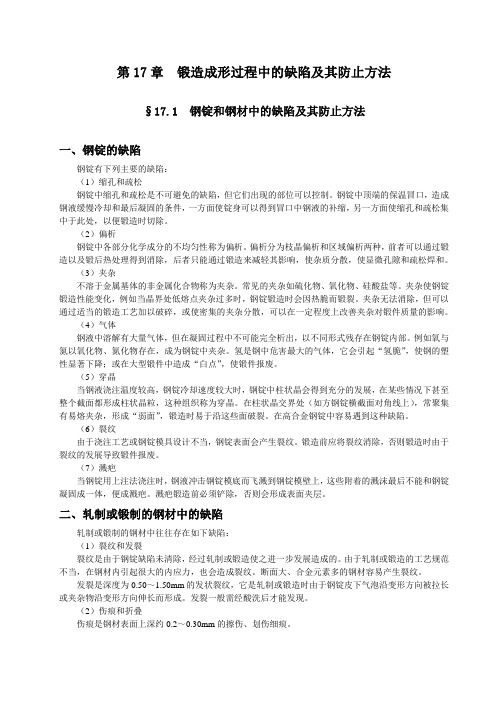
第17章锻造成形过程中的缺陷及其防止方法§17.1 钢锭和钢材中的缺陷及其防止方法一、钢锭的缺陷钢锭有下列主要的缺陷:(1)缩孔和疏松钢锭中缩孔和疏松是不可避免的缺陷,但它们出现的部位可以控制。
钢锭中顶端的保温冒口,造成钢液缓慢冷却和最后凝固的条件,一方面使锭身可以得到冒口中钢液的补缩,另一方面使缩孔和疏松集中于此处,以便锻造时切除。
(2)偏析钢锭中各部分化学成分的不均匀性称为偏析。
偏析分为枝晶偏析和区域偏析两种,前者可以通过锻造以及锻后热处理得到消除,后者只能通过锻造来减轻其影响,使杂质分散,使显微孔隙和疏松焊和。
(3)夹杂不溶于金属基体的非金属化合物称为夹杂。
常见的夹杂如硫化物、氧化物、硅酸盐等。
夹杂使钢锭锻造性能变化,例如当晶界处低熔点夹杂过多时,钢锭锻造时会因热脆而锻裂。
夹杂无法消除,但可以通过适当的锻造工艺加以破碎,或使密集的夹杂分散,可以在一定程度上改善夹杂对锻件质量的影响。
(4)气体钢液中溶解有大量气体,但在凝固过程中不可能完全析出,以不同形式残存在钢锭内部。
例如氧与氮以氧化物、氮化物存在,成为钢锭中夹杂。
氢是钢中危害最大的气体,它会引起“氢脆”,使钢的塑性显著下降;或在大型锻件中造成“白点”,使锻件报废。
(5)穿晶当钢液浇注温度较高,钢锭冷却速度较大时,钢锭中柱状晶会得到充分的发展,在某些情况下甚至整个截面都形成柱状晶粒,这种组织称为穿晶。
在柱状晶交界处(如方钢锭横截面对角线上),常聚集有易熔夹杂,形成“弱面”,锻造时易于沿这些面破裂。
在高合金钢锭中容易遇到这种缺陷。
(6)裂纹由于浇注工艺或钢锭模具设计不当,钢锭表面会产生裂纹。
锻造前应将裂纹消除,否则锻造时由于裂纹的发展导致锻件报废。
(7)溅疤当钢锭用上注法浇注时,钢液冲击钢锭模底而飞溅到钢锭模壁上,这些附着的溅沫最后不能和钢锭凝固成一体,便成溅疤。
溅疤锻造前必须铲除,否则会形成表面夹层。
二、轧制或锻制的钢材中的缺陷轧制或锻制的钢材中往往存在如下缺陷:(1)裂纹和发裂裂纹是由于钢锭缺陷未清除,经过轧制或锻造使之进一步发展造成的。
d2钢的锻件标准

d2钢的锻件标准D2钢锻件标准一、D2钢简介D2钢是一种高碳高铬工具钢,具有优异的耐磨性和硬度。
它的化学成分主要由碳、铬和少量合金元素组成。
这种钢材的主要特点是高硬度、高耐磨性、高韧性以及良好的切削性能。
它在模具制造、工具制造、汽车制造等领域得到了广泛应用。
二、锻件标准概述锻件标准是指在锻造过程中,对原材料、加热温度、锻造工艺、冷却速度等各个环节进行明确规定,以确保最终锻件的质量和性能符合要求。
对于D2钢锻件,这些标准包括了对原材料的选择、加热设备的温度控制、锻造过程中的模具设计和使用、冷却工艺的设计等。
通过遵循这些标准,可以确保D2钢锻件的质量和性能达到最佳水平。
三、质量要求与检验方法1. 质量要求对于D2钢锻件,其质量要求主要包括以下几个方面:(1)化学成分:D2钢的化学成分应符合相关国家标准和企业标准的要求。
(2)表面质量:锻件的表面应光滑,无裂纹、气孔、夹杂物等缺陷。
(3)尺寸精度:锻件的尺寸应符合图纸要求,误差应在允许范围内。
(4)力学性能:D2钢锻件的力学性能应符合相关国家标准和企业标准的要求。
2. 检验方法为了确保D2钢锻件的质量,常用的检验方法包括:(1)化学分析:通过对原材料和锻件进行化学分析,确保其化学成分符合要求。
(2)外观检查:对锻件的表面质量进行肉眼观察或使用放大镜进行检查。
(3)尺寸测量:使用测量工具对锻件的尺寸进行测量,并比较其与设计图纸的误差。
(4)力学性能测试:对锻件进行硬度测试、拉伸试验、冲击试验等,以评估其力学性能。
四、主要应用领域及产品示例1. 主要应用领域D2钢锻件主要应用于以下几个方面:(1)模具制造:D2钢锻件可用于制造各种模具,如冲压模具、注塑模具等。
(2)工具制造:D2钢锻件可用于制造各种工具,如钻头、铣刀、丝锥等。
(3)汽车制造:D2钢锻件可用于制造汽车零部件,如曲轴、连杆、齿轮等。
2. 产品示例以下是D2钢锻件的一些产品示例:(1)注塑模具:使用D2钢锻件制造的注塑模具具有高耐磨性和高韧性,能够满足高效率的生产需求。
3-中国锻造行业、锻造钢材的现状及发展方向

X 0.19 0.28 0.79 0.50 0.47 0.18 39 31 24
σ
0.0066 0.0212 0.0193 0.0086 0.0158 0.0058 1.6839 2.4841 2.0418
X max 0.21 0.35 0.89 0.52 0.53 0.19 41 34 28
X min 0.18 0.23 0.76 0.48 0.44 0.16 35 26 21165、未来锻造用特钢发展趋势
1、高尺寸精度和表面质量适应温锻、冷锻的要求; 2、高度的成分一直性满足智能化锻造需求; 3、高纯净度对大变形、冷变形的塑性要求; 4、高组织均匀性满足热处理变形和精加工的要求; 5、高硫、高磷钢材,夹杂物均匀分布满足车削性能的要求;
17
谢谢!
18
中国有钢铁企业1200家左右,其中特钢企业约32家,包括华北地 区的石钢、太钢,东北地区的东北特钢,华东地区的宝钢、兴澄等。
9
3、中国特殊钢企业现状、锻造用钢材 的质量问题与解决对策
3.2中国特殊钢生产原料
中国特殊钢生产企业主要有转炉和电炉两个流程。生 产特殊钢的原料结构与生产的品种密切相关,小批量、多 品种的高合金钢等适宜采用电炉生产,如工模具等主要以 废钢为主要原料;合金含量较低而批量较大的适宜转炉生 产,如弹簧钢、轴承钢、合金结构钢等主要以铁水为主要 原料。
6
1、中国锻造行业的现状
• 精密锻造以金属体积塑性成型的方法获得表面光洁、尺寸 精确的制品,如冷挤压、温挤压、热挤压、热精密模锻、 冷精密模锻、闭式锻造、高速热镦锻等。精密锻造技术在 工业发达国家已得到了广泛应用,但中国生产体系尚不完 备,达到国际先进水平的企业屈指可数。
• 坯料加热和锻件热处理用加热炉有电加热炉和燃料(煤气、 天然气、油)加热炉,总量超过10000台。其中既有比较 先进的感应加热设备,也有比较落后的燃油加热设备。
a105锻钢温度范围

a105锻钢温度范围锻钢是一种常见的金属加工方法,通过对钢材进行高温加热和塑性变形,可以改善其力学性能和形状。
在进行锻造之前,了解合适的锻钢温度范围是非常重要的,下面将详细介绍。
锻钢温度的选择主要依据于钢材的化学成分、组织结构和所需的锻造工艺。
温度的选择不仅要满足金属的变形能力,还要保持钢材的物理性能在合理范围内。
一般来说,钢材的温度范围为920℃至1300℃之间。
在锻钢温度的选择上,有以下几个因素需要考虑:1.钢材的化学成分:不同的钢材含有不同的元素,例如碳钢、合金钢等,其含碳量、合金元素的种类和含量都会对锻造温度产生影响。
高碳钢通常需要较高的温度进行锻造,以便降低其硬度和强度,增加韧性。
2.钢材的组织结构:钢材的组织结构分为奥氏体、珠光体和铁素体等不同的晶粒结构。
奥氏体是高温下相对较为稳定的组织,具有较强的塑性,因此需要在较高温度下进行锻造。
珠光体则需要较低的温度进行锻造,以维持其稳定的组织结构。
3.锻造工艺要求:根据不同的锻造工艺要求,选择不同的温度范围。
有时需要将钢材加热到较高温度,以便于快速、有效地形成所需形状。
而有时则需要在较低温度下进行锻造,以保持钢材的细小晶粒结构和较高的强度。
综上所述,锻钢温度的选择主要取决于钢材的化学成分、组织结构和锻造工艺要求。
在实践中,还需要根据具体情况进行调整和优化。
总的来说,理想的锻钢温度范围是920℃至1300℃,在此范围内往往能够满足大多数钢材的锻造需求。
但需要注意的是,温度过高或过低都会对钢材的性能产生不良影响。
温度过高可能导致过度软化或过度晶化,从而降低钢材的强度和韧性;温度过低则会导致塑性变形困难,可能会引起裂纹和变形等问题。
因此,在选择锻钢温度时,需要进行全面的分析和测试,以确保获得理想的机械性能和形状。
总的来说,锻钢温度的选择是一个较为复杂的过程,需要综合考虑钢材的化学成分、组织结构和所需的锻造工艺要求。
通过合适的温度范围,可以有效地改善钢材的性能和形状,满足不同应用环境的需求。
20号钢锻造温度与热延伸率_概述及解释说明

20号钢锻造温度与热延伸率概述及解释说明1. 引言1.1 概述本文的研究重点是关于钢锻造温度与热延伸率之间的关系。
钢锻造在现代工业中具有广泛应用,其温度控制对于保证产品质量和性能至关重要。
同时,热延伸率也是一个关键参数,直接影响材料的变形行为和加工性能。
通过了解钢锻造温度和热延伸率之间的联系,我们可以更好地理解这两个因素对钢材加工过程和性能的影响,并提供相应的科学依据和优化方案。
这对于改进现有工艺、降低生产成本及提高材料利用率具有重要意义。
1.2 文章结构本文包括引言、正文、结论与展望以及结束语四个部分。
引言部分主要介绍了文章的背景、目的和组织结构;正文部分将就钢锻造温度的定义、热延伸率概念与意义以及影响钢锻造温度的因素进行详细探讨;接着,我们将深入分析钢锻造温度与热延伸率之间的关系,在实验结果分析、理论解释与模型推导以及工业应用案例探讨三个方面展开讨论;最后,我们将总结结论,并对尚存在的研究不足和未来的研究方向进行展望;文章以结束语作为收尾。
1.3 目的本文旨在系统探究钢锻造温度与热延伸率之间的关系,并进一步分析其影响机理和工业应用。
通过概述这一主题并解释说明其重要性,希望能够提供给读者一个全面的了解框架和知识体系。
同时,我们也希望通过本文的研究内容,为相关领域的科学家、工程师和决策者提供有价值的参考,促进相关技术和工艺水平的进步。
2. 正文:2.1 钢锻造温度的定义:钢锻造温度是指在进行钢铁材料锻造过程中所需的加热温度。
这个温度是通过对具体材料和工艺要求的分析研究得出的,一般会考虑到材料性能、形变抗力以及设备的热衰减等因素。
钢锻造温度直接影响着成品的质量、力学性能以及加工效率。
2.2 热延伸率的概念与意义:热延伸率是一个描述钢材经过高温作用后的尺寸变化情况的参数。
它表示了材料在受热时其线膨胀或收缩程度。
热延伸率反映了材料对于温度变化的敏感程度,对于预测和控制材料在高温下形变过程中产生的尺寸变化具有重要意义。
铸造碳素钢和锻造碳素钢

铸造碳素钢和锻造碳素钢铸造碳素钢和锻造碳素钢是常见的制造碳素钢材的方法,它们在材料性能、工艺过程和应用领域上有着明显的差异。
本文将对这两种方法进行全面比较,以帮助读者更好地理解它们的特点和适用场景。
首先,我们先来了解一下铸造碳素钢。
铸造碳素钢是通过将熔化的钢水倒入模具中,待冷却凝固后形成的。
它具有以下特点:首先,铸造碳素钢的成本相对较低,因为工艺简单、设备要求较低,适用于大批量生产。
其次,铸造碳素钢能够以复杂形状生产,可以满足各种产品的需求。
但与此同时,铸造碳素钢的密度相对较低,力学性能及抗拉强度相对较差,且易产生一些内部缺陷。
因此,在一些对材料性能要求较高的领域,如航空航天、汽车制造等,铸造碳素钢的应用相对有限。
接下来,我们来了解一下锻造碳素钢。
锻造碳素钢是通过将加热后的钢坯放入压力机中进行锻造而得。
它具有以下特点:首先,锻造能够提高碳素钢的密度和力学性能,使其具有较高的强度和硬度。
其次,锻造碳素钢内部结构更加致密,减少了可能存在的内部缺陷,提高了材料的可靠性和耐久性。
但锻造的成本相对较高,需要更复杂的设备和工艺流程。
同时,锻造碳素钢的形状受到一定的限制,难以生产复杂形状的产品。
综上所述,铸造碳素钢和锻造碳素钢各有优劣,适用于不同的领域和产品。
在需求大批量生产、对成本要求较低、形状要求较复杂的场景下,可以选择铸造碳素钢。
而在对材料力学性能和耐久性要求较高、形状相对简单的场景下,锻造碳素钢则是更好的选择。
当然,根据实际需求和制造要求,也可以采用两种方法的组合,以满足不同方面的需求。
最后,无论是铸造碳素钢还是锻造碳素钢,都需要在制造过程中严格控制质量,确保产品符合设计要求。
在选择材料和工艺时,我们需要综合考虑产品的用途、性能要求、生产效率和成本等因素,以制定合理的制造方案。
只有在科学合理的指导下,才能生产出质量过硬、性能优越的碳素钢产品,为各行各业的发展提供有力支持。
锻造和冷拔

钢材的锻造与冷拉、冷拔天津鹏程煤矿设备有限公司锻造:在生产中,采用合理的工艺和工艺参数,可以通过下列几方面来改善原材料的组织和性能:1)打碎柱状晶,改善宏观偏析,把铸态组织变为锻态组织,并在合适的温度和应力条件下,焊合内部孔隙,提高材料的致密度;2)铸锭经过锻造形成纤维组织,进一步通过轧制、挤压、模锻,使锻件得到合理的纤维方向分布;3)控制晶粒的大小和均匀度;4)改善第二相(例如:莱氏体钢中的合金碳化物)的分布;5)使组织得到形变强化或形变——相变强化等。
由于上述组织的改善,使锻件的塑性、冲击韧度、疲劳强度及持久性能等也随之得到了提高,然后通过零件的最后热处理就能得到零件所要求的硬度、强度和塑性等良好的综合性能。
锻造工艺能很好的减少材料浪费,从而降低成本。
宏观上讲锻造对材料基本无影响就像合面团一样合完还是面团。
微观上讲锻造加热可能会使碳元素进入材料,在受冷却温度速度的影响会使材料硬度增加。
事实也正是如此锻造的材料比原材料要稍硬。
但不影响材料整体性能。
冷拉:钢筋冷拉是在常温条件下,以超过原来钢筋屈服点强度的拉应力,强行拉伸钢筋,使钢筋产生一塑性变形达到提高钢筋屈服点强度和节约钢材的目的。
此处常温为平均室外温度大于5℃。
冷拔:钢筋同时经受张拉和挤压而发生塑性变形,拔出的钢筋截面积减小,产生冷作强化,抗拉强度可提高40~90%。
冷拉和冷拔是金属冷加工的两种不同的方法,两者并非一个概念。
冷拉指在金属材料的两端施加拉力,使材料产生拉伸变形的方法;冷拔是指在材料的一端施加拔力,使材料通过一个模具孔而拔出的方法,模具的孔径要较材料的直径小些。
冷拔加工使材料除了有拉伸变形外还有挤压变形,冷拔加工一般要在专门的冷拔机上进行。
经冷拔加工的材料要比经冷拉加工的材料性能更好些;冷拔钢筋是将钢筋用强力拔过比它本身直径还小的硬质合金拔丝模,这是钢筋同时受到纵向拉力和横向压力的作用,截面变小,长度变长,钢丝的强度大大提高,但塑性降低很多。
JIS G 0701-中文版

钢材锻造作业时锻造成形比的表示方法1、该标准规定了钢材锻造作业时锻造成形比的表示方法。
2、锻造成形比2.1 通常将3个方向的变形中最大变形方向的变形比视为锻造成形比。
2.2:锻造成形比表示方法的原理是:用规定的符号把锻造作业的种类按照工程顺序进行记载。
3、锻造作业的种类和锻造成形比的表示方法3.1 实体锻造在要锻造实体、减少断面面积、增加长度的时候采用实体锻造,这时锻造成形比按照如下所示进行表示。
锻造成形比A/a或者l/L 作业种类符号S 表示例:2S3.2 压缩锻造在要锻造实体、增加断面面积、减少长度的时候采用压缩锻造,这时锻造成形比按照如下所示进行表示。
锻造成形比 l/L/L’ = L’/L作业种类符号U 表示例:1/2U但是要同时进行实体锻造的时候,这时锻造成形比按照如下所示进行表示。
锻造成形比 l/L/L’,A’/a或者 l/L/L’, l/L’ 表示例:1/2U3S3.3 伸展锻造伸展锻造是将实体角材沿方向1压缩,在压缩方向上直角方向2的变形度上产生显著的差异。
这时锻造成形比按照如下所示进行表示。
但是压缩在T方向进行的时候要求l/L>w/W.锻造成形比l/T/t, l/L作业种类符号 F 表示例:1/2(1.7)F但是要同时进行方向2的伸展锻炼的时候,这时锻造成形比按照如下所示进行表示,比如将首次的伸展定为l/L>w/W,那么接下来伸展在W方向的压缩后的锻造成形比将如下所示:(1) l/L’>t/T’ 的时候(2) l/L’>t/T’ 的时候表示例:(1)和(2)这里的(1)是和1.7、1.8方向一致的,(2)是和1.6、1.9的方向是不一样的,为了区别以上所述,特别用大括号区分。
之后在第2次在L方向进行压缩的时候,以以上所述为标准进行。
3.4 中空锻造在中空的情况下减少断面面积,增加长度,这时锻造成形比按照如下所示进行表示。
锻造成形比A/a或者l/L 作业种类符号M 表示例:3M但是从钢锭直接初加工进行实体锻造的时候,这时锻造成形比按照如下所示进行表示。
中碳结构钢件的锻造成形与锻后调质一次完成的热加工新技术

中碳结构钢件的锻造成形与锻后调质一次完
成的热加工新技术
中碳结构钢件的锻造成形与锻后调质一次完成的热加工新技术是针对传统钢材热加工工艺缺陷提出的一种新型技术。
该技术通过锻造和调质一次完成,可大大提高工作效率和产品品质。
首先,该技术采用中碳结构钢件作为原料,在高温下进行锻造成形。
这样可以在一定程度上改善材料的组织结构,提高钢材的力学性能和耐磨性。
其次,锻造完成后,中碳结构钢件将通过调质工艺,进一步提高钢材的性能。
该技术采用高温固溶和低温沉淀等工艺,使钢材表面形成均匀细小的碳化物,从而提高钢材的强度和硬度,并且改善钢材的耐腐蚀性。
总而言之,中碳结构钢件的锻造成形与锻后调质一次完成的热加工新技术是当前热加工行业的一种创新技术。
该技术不仅提高了生产效率,而且极大地提高了产品的质量和性能。
未来,该技术将不断优化和完善,助力钢材行业更快、更好、更强的发展。
锻造工艺流程

锻造工艺流程
锻造工艺是金属成型的重要加工手段,在机械制造中发挥着重要的作用,它对形状、尺寸、性能等有着显著的影响。
本文将介绍锻造工艺的一般流程。
首先,需要将钢材或其他金属加热,使其处于高温和软态状态,这是锻造的前提条件。
其次,在锻件塑性变形的过程中,金属受力或压力,以达到我们需要的形态,有炉内锻造和炉外锻造两种方式可以实现锻件的变形。
第三,金属锻造的最后一步便是冷却,它是必不可少的,可以通过浸水或放在空气中处理,以达到一定的析出效果和硬化效果,同时也能控制变形性能。
此外,锻件加工还需要经过抛光、光和表面涂装等处理,以达到更好的表面外观和更多的防腐蚀性能。
最后,在这里还需要提及锻件的检测,通常采用检测仪器,例如X射线检测仪、光谱仪和氮气容量分析仪等进行锻件检测,保证所有工件的性能符合标准要求。
综上所述,锻造工艺的流程是:钢材加热,按需要的形状进行塑性变形,冷却,抛光、光及表面涂装,最后通过检测仪器检测工件。
锻件工艺是形状复杂、尺寸精确、表面有质感的重要加工工艺,在许多重要机械零件的生产中发挥重要作用。
- 1 -。
锻造实验报告

锻造实验报告锻造实验报告引言:锻造是一种重要的金属加工方法,通过对金属材料施加压力和热力,使其形成所需形状和性能的工艺过程。
本实验旨在通过锻造工艺,研究金属材料的塑性变形行为和性能变化规律,为工程实践提供参考。
实验目的:1. 了解锻造工艺对金属材料的塑性变形行为的影响;2. 掌握锻造工艺对金属材料性能的改善作用;3. 分析锻造过程中可能出现的缺陷和解决方法。
实验装置和材料:1. 锻造机:用于施加压力和热力的设备;2. 锻造模具:用于给金属材料施加形状变化的模具;3. 锻造材料:选择常见的低碳钢作为实验材料。
实验步骤:1. 准备工作:清洁锻造机和模具,确保无杂质和污染;2. 材料准备:将低碳钢材料切割成适当大小的块状;3. 加热处理:将钢材块放入加热炉中,加热至适宜的温度;4. 锻造操作:将加热后的钢材块放入锻造模具中,施加适当的压力进行锻造;5. 冷却处理:将锻造后的钢材块进行冷却处理,使其达到所需的性能。
实验结果与分析:通过对锻造后的低碳钢材料进行金相观察和力学性能测试,得到以下结果:1. 金相观察:锻造后的钢材晶粒细化,晶界清晰,无明显的晶间缺陷;2. 强度测试:锻造后的钢材强度明显提高,抗拉强度和屈服强度均有所增加;3. 韧性测试:锻造后的钢材韧性略有下降,但仍处于可接受范围内;4. 硬度测试:锻造后的钢材硬度有所增加,表明其耐磨性能得到改善。
结论:通过本次实验,我们得出以下结论:1. 锻造工艺能够显著改善金属材料的力学性能,提高其强度和硬度;2. 锻造工艺对金属材料的韧性有一定影响,需要在实际应用中进行综合考虑;3. 锻造过程中需要注意控制温度和施加压力,以避免可能出现的缺陷。
进一步研究:为了更深入地了解锻造工艺对金属材料的影响,可以开展以下研究:1. 研究不同温度和压力条件下的锻造效果,寻找最佳工艺参数;2. 探究其他金属材料在锻造过程中的性能变化规律;3. 结合数值模拟和实验验证,研究锻造过程中的应力分布和变形机制。
- 1、下载文档前请自行甄别文档内容的完整性,平台不提供额外的编辑、内容补充、找答案等附加服务。
- 2、"仅部分预览"的文档,不可在线预览部分如存在完整性等问题,可反馈申请退款(可完整预览的文档不适用该条件!)。
- 3、如文档侵犯您的权益,请联系客服反馈,我们会尽快为您处理(人工客服工作时间:9:00-18:30)。
钢材锻造工艺
锻造是利用锻压机械对金属坯料施加压力,使其产生塑性变形,以获得具有一定机械性能、一定形状和尺寸的锻件的加工方法。
锻造和冲压同属塑性加工性质,统称锻压。
锻造是机械制造中常用的成形方法。
通过锻造能消除金属的铸态疏松、焊合孔洞,锻件的机械性能一般优于同样材料的铸件。
机械中负载高、工作条件严峻的重要零件,除形状较简单的可用轧制的板材、型材或焊接件外,多采用锻件。
锻造按坯料在加工时的温度可分为冷锻和热锻。
冷锻一般是在室温下加工,热锻是在高于坯料金属的再结晶温度上加工。
有时还将处于加热状态,但温度不超过再结晶温度时进行的锻造称为温锻。
不过这种划分在生产中并不完全统一。
钢的再结晶温度约为460℃,但普遍采用800℃作为划分线,高于800℃的是热锻;在300~800℃之间称为温锻或半热锻。
锻造按成形方法则可分为自由锻、模锻、冷镦、径向锻造、挤压、成形轧制、辊锻、辗扩等。
坯料在压力下产生的变形基本不受外部限制的称自由锻,也称开式锻造;其他锻造方法的坯料变形都受到模具的限制,称为闭模式锻造。
成形轧制、辊锻、辗扩等的成形工具与坯料之间有相对的旋转运动,对坯料进行逐点、渐近的加压和成形,故又称为旋转锻造。
锻造用料主要是各种成分的碳素钢和合金钢,其次是铝、镁、铜、钛等及其合金。
材料的原始状态有棒料、铸锭、金属粉末和液态金属。
一般的中小型锻件都用圆形或方形棒料作为坯料。
棒料的晶粒组织和机械性能均匀、良好,形状和尺寸准确,表面质量好,便于组织批量生产。
只要合理控制加热温度和变形条件,不需要大的锻造变形就能锻出性能优良的锻件。
铸锭仅用于大型锻件。
铸锭是铸态组织,有较大的柱状晶和疏松的中心。
因此必须通过大的塑性变形,将柱状晶破碎为细晶粒,将疏松压实,才能获得优良的金属组织和机械性能。
经压制和烧结成的粉末冶金预制坯,在热态下经无飞边模锻可制成粉末锻件。
锻件粉末接近于一般模锻件的密度,具有良好的机械性能,并且精度高,可减少后续的切削加工。
粉末锻件内部组织均匀,没有偏析,可用于制造小型齿轮等工件。
但粉末的价格远高于一般棒材的价格,在生产中的应用受到一定限制。
对浇注在模膛的液态金属施加静压力,使其在压力作用下凝固、结晶、流动、塑性变形和成形,就可获得所需形状和性能的模锻件。
液态金属模锻是介于压铸和模锻间的成形方法,特别适用于一般模锻难于成形的复杂薄壁件。
不同的锻造方法有不同的流程,其中以热模锻的工艺流程最长,一般顺序为:锻坯下料;锻坯加热;辊锻备坯;模锻成形;切边;中间检验,检验锻件的尺寸和表面缺陷;锻件热处理,用以消除锻造应力,改善金属切削性能;清理,主要是去除表面氧化皮;矫正;检查,一般锻件要经过外观和硬度检查,重要锻件还要经过化学成分分析、机械性能、残余应力等检验和无损探伤。
锻压是锻造和冲压的合称,是利用锻压机械的锤头、砧块、冲头或通过模具对坯料施加压力,使之产生塑性变形,从而获得所需形状和尺寸的制件的成形加工方法。
在锻造加工中,坯料整体发生明显的塑性变形,有较大量的塑性流动;在冲压加工中,坯料主要通过改变各部位面积的空间位置而成形,其内部不出现较大距离的塑性流动。
锻压主要用于加工金属制件,也可用于加工某些非金属,如工程塑料、橡胶、陶瓷坯、砖坯以及复合材料的成形等。
锻压和冶金工业中的轧制、拔制等都属于塑性加工,或称压力加工,但锻压主要用于生产金属制件,而轧制、拔制等主要用于生产板材、带材、管材、型材和线材等通用性金属材料。
人类在新石器时代末期,已开始以锤击天然红铜来制造装饰品和小用品。
中国约在公元前2000多年已应用冷锻工艺制造工具,如甘肃武威皇娘娘台齐家文化遗址出土的红铜器物,就有明显的锤击痕迹。
商代中期用陨铁制造武器,采用了加热锻造工艺。
春秋后期出现的块炼熟铁,就是经过反复加热锻造以挤出氧化物夹杂并成形的。
最初,人们靠抡锤进行锻造,后来出现通过人拉绳索和滑车来提起重锤再自由落下的方法锻打坯料。
14世纪以后出现了畜力和水力落锤锻造。
1842年,英国的内史密斯制成第一台蒸汽锤,使锻造进入应用动力的时代。
以后陆续出现锻造水压机、电机驱动的夹板锤、空气锻锤和机械压力机。
夹板锤最早应用于美国内战(1861~1865)期间,用以模锻武器的零件,随后在欧洲出现了蒸汽模锻锤,模锻工艺逐渐推广。
到19世纪末已形成近代锻压机械的基本门类。
20世纪初期,随着汽车开始大量生产,热模锻迅速发展,成为锻造的主要工艺。
20世纪中期,热模锻压力机、平锻机和无砧锻锤逐渐取代了普通锻锤,提高了生产率,减小了振动和噪声。
随着锻坯少无氧化加热技术、高精度和高寿
命模具、热挤压,成形轧制等新锻造工艺和锻造操作机、机械手以及自动锻造生产线的发展,锻造生产的效率和经济效果不断提高。
冷锻的出现先于热锻。
早期的红铜、金、银薄片和硬币都是冷锻的。
冷锻在机械制造中的应用到20世纪方得到推广,冷镦、冷挤压、径向锻造、摆动辗压等相继发展,逐渐形成能生产不需切削加工的精密制件的高效锻造工艺。
早期的冲压只利用铲、剪、冲头、手锤、砧座等简单工具,通过手工剪切、冲孔、铲凿、敲击使金属板材(主要是铜或铜合金板等)成形,从而制造锣、铙、钹等乐器和罐类器具。
随着中、厚板材产量的增长和冲压液压机和机械压力机的发展,冲压加工也在19世纪中期开始机械化。
1905年美国开始生产成卷的热连轧窄带钢,1926年开始生产宽带钢,以后又出现冷连轧带钢。
同时,板、带材产量增加,质量提高,成本降低。
结合船舶、铁路车辆、锅炉、容器、汽车、制罐等生产的发展,冲压已成为应用最广泛的成形工艺之一。
锻压主要按成形方式和变形温度进行分类。
按成形方式锻压可分为锻造和冲压两大类;按变形温度锻压可分为热锻压、冷锻压、温锻压和等温锻压等。
热锻压是在金属再结晶温度以上进行的锻压。
提高温度能改善金属的塑性,有利于提高工件的内在质量,使之不易开裂。
高温度还能减小金属的变形抗力,降低所需锻压机械的吨位。
但热锻压工序多,工件精度差,表面不光洁,锻件容易产生氧化、脱碳和烧损。
冷锻压是在低于金属再结晶温度下进行的锻压,通常所说的冷锻压多专指在常温下的锻压,而将在高于常温、但又不超过再结晶温度下的锻压称为温锻压。
温锻压的精度较高,表面较光洁而变形抗力不大。
在常温下冷锻压成形的工件,其形状和尺寸精度高,表面光洁,加工工序少,便于自动化生产。
许多冷锻、冷冲压件可以直接用作零件或制品,而不再需要切削加工。
但冷锻时,因金属的塑性低,变形时易产生开裂,变形抗力大,需要大吨位的锻压机械。
等温锻压是在整个成形过程中坯料温度保持恒定值。
等温锻压是为了充分利用某些金属在等一温度下所具有的高塑性,或是为了获得特定的组织和性能。
等温锻压需要将模具和坯料一起保持恒温,所需费用较高,仅用于特殊的锻压工艺,如超塑成形。
锻压可以改变金属组织,提高金属性能。
铸锭经过热锻压后,原来的铸态疏松、孔隙、微裂等被压实或焊合;原来的枝状结晶被打碎,使晶粒变细;同时改变原来的碳化物偏析和不均匀分布,使组织均匀,从而获得内部密实、均匀、细
微、综合性能好、使用可靠的锻件。
锻件经热锻变形后,金属是纤维组织;经冷锻变形后,金属晶体呈有序性。
锻压是使金属进行塑性流动而制成所需形状的工件。
金属受外力产生塑性流动后体积不变,而且金属总是向阻力最小的部分流动。
生产中,常根据这些规律控制工件形状,实现镦粗拔长、扩孔、弯曲、拉深等变形。
锻压出的工件尺寸精确、有利于组织批量生产。
模锻、挤压、冲压等应用模具成形的尺寸精确、稳定。
可采用高效锻压机械和自动锻压生产线,组织专业化大批量或大量生产。
锻压的生产过程包括成形前的锻坯下料、锻坯加热和预处理;成形后工件的热处理、清理、校正和检验。
常用的锻压机械有锻锤、液压机和机械压力机。
锻锤具有较大的冲击速度,利于金属塑性流动,但会产生震动;液压机用静力锻造,有利于锻透金属和改善组织,工作平稳,但生产率低;机械压力机行程固定,易于实现机械化和自动化。
未来锻压工艺将向提高锻压件的内在质量、发展精密锻造和精密冲压技术、研制生产率和自动化程度更高的锻压设备和锻压生产线、发展柔性锻压成形系统、发展新型锻压材料和锻压加工方法等方面发展。
提高锻压件的内在质量,主要是提高它们的机械性能(强度、塑性、韧性、
疲劳强度)和可靠度。
这需要更好地应用金属塑性变形理论;应用内在质量更好
的材料;正确进行锻前加热和锻造热处理;更严格和更广泛地对锻压件进行无损探伤。
少、无切削加工是机械工业提高材料利用率、提高劳动生产率和降低能源消耗的最重要的措施和方向。
锻坯少、无氧化加热,以及高硬、耐磨、长寿模具材料和表面处理方法的发展,将有利于精密锻造、精密冲压的扩大应用。