轧机操作岗位职责、操作工艺规程
精轧机轧钢岗位操作规程

精轧机轧钢岗位操作规程一、岗位背景精轧机轧钢岗位是钢铁厂生产线上的重要工作岗位之一。
精轧机是指用于对轧制后的钢材进行进一步处理,使其达到特定尺寸、形状和质量要求的设备。
岗位操作规程将对精轧机轧钢岗位的操作流程、安全操作规范等进行规定,以确保安全生产和产品质量。
二、操作流程1. 开机准备a. 确认轧钢任务,并查看轧钢规程和轧钢计划。
b. 检查设备和工具是否正常,若有异常及时报修。
c. 清扫工作区域,确保工作环境整洁。
2. 上机操作准备a. 穿戴好工作服、劳保用品,并戴好安全帽。
b. 熟悉机器的控制面板和操作按钮的位置和功能。
c. 检查润滑油和冷却液是否充足,若不足需及时添加。
3. 开机操作a. 按照启动顺序依次打开电源和气源。
b. 按照设备说明书的操作步骤,正确设置轧辊间隙和轧辊速度。
c. 打开润滑系统,确保轧辊和工作台面充分润滑。
d. 按照工艺要求,调整机器的参数和状态,确保满足生产需求。
4. 操作过程a. 保持警惕,关注机器运行状态,及时发现异常情况,并采取相应措施。
b. 定期检查轧辊和工作台面,确保其表面无损伤和磨损。
c. 积极参与设备维护保养工作,及时清理机器内部的杂质和灰尘。
d. 遵守操作规程,严禁随意调整设备参数和操作方式。
5. 关机操作a. 停止给料,等待机器自行停止运行。
b. 关闭润滑系统,清理润滑点,防止润滑油污染环境。
c. 断开电源和气源,确保设备处于安全状态。
d. 对机器进行基本清洁和维护保养,保持机器干净整洁。
三、安全操作规范1. 安全防护a. 操作人员必须穿戴好工作服、安全帽、安全鞋等劳保用品。
b. 操作人员禁止将头部或身体靠近机器活动部位。
c. 操作人员必须保持机器周围的通道畅通,不得随意堆放杂物。
d. 操作人员发现异常情况或安全隐患时,应立即停机并报告。
2. 机器操作a. 操作人员必须熟悉机器的操作流程和控制面板的功能。
b. 操作人员严禁在机器运行中随意调整设备参数和操作方式。
轧机轧钢工安全技术操作规程范本(2篇)
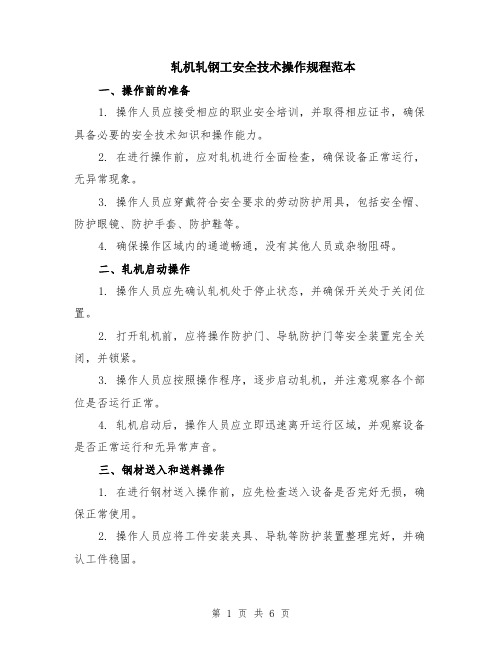
轧机轧钢工安全技术操作规程范本一、操作前的准备1. 操作人员应接受相应的职业安全培训,并取得相应证书,确保具备必要的安全技术知识和操作能力。
2. 在进行操作前,应对轧机进行全面检查,确保设备正常运行,无异常现象。
3. 操作人员应穿戴符合安全要求的劳动防护用具,包括安全帽、防护眼镜、防护手套、防护鞋等。
4. 确保操作区域内的通道畅通,没有其他人员或杂物阻碍。
二、轧机启动操作1. 操作人员应先确认轧机处于停止状态,并确保开关处于关闭位置。
2. 打开轧机前,应将操作防护门、导轨防护门等安全装置完全关闭,并锁紧。
3. 操作人员应按照操作程序,逐步启动轧机,并注意观察各个部位是否运行正常。
4. 轧机启动后,操作人员应立即迅速离开运行区域,并观察设备是否正常运行和无异常声音。
三、钢材送入和送料操作1. 在进行钢材送入操作前,应先检查送入设备是否完好无损,确保正常使用。
2. 操作人员应将工件安装夹具、导轨等防护装置整理完好,并确认工件稳固。
3. 钢材送入时,操作人员应注意观察钢材的大小、形状和位置,确保送入平稳无卡阻。
4. 进行钢材送料操作时,应保持手部和身体与运动部件的距离,避免伸入危险区域。
四、轧制操作1. 轧机操作人员应根据工艺要求选择合适的辊轧和压下程度。
2. 操作人员应随时观察轧机运行情况,确保钢材的轧制过程稳定、均匀。
3. 在轧制过程中,操作人员应随时监控轧制压力、轧制温度等参数,确保在正常范围内。
4. 减轻轧机负荷时,操作人员应逐步减小辊轧和压下程度,确保安全运行。
五、轧机停机操作1. 在轧机停机前,操作人员应提前关闭轧机辊轧和压下功能。
2. 轧机停机后,应迅速关断电源,关闭进料装置,并锁紧操作防护门和导轨防护门。
3. 停机后,操作人员应对设备进行全面检查,清理工作区域,排除设备故障和隐患。
4. 操作人员应记录轧机停机相关信息,包括停机时间、问题描述、解决方案等,以备后续分析和改进。
六、紧急情况应急处理1. 遇到火灾等紧急情况时,操作人员应立即关闭电源和气源,并使用灭火器材进行灭火。
轧机主控台岗位职责、操作工艺规程

轧机主控台岗位职责、操作工艺规程一、岗位名称:轧机操作台工。
二、岗位职责:(1)、热悉和了解轧钢生产工艺流程,全面掌握轧制工艺及控冷工艺的参数。
(2)、负责控制从1#机架到吐丝机的全工艺过程。
(3)、负责监视全生产线的机械,电气能源介质供应系统的设备运行状况。
三、操作规程(A)主控台操作规程1、操作工进入岗位前劳保必须穿戴齐全。
2、准时参加班前会,了解上个班的工艺运行状况,必须听清楚班长工作安排。
3、接班时必须交接当前设备、工艺运行状态,数据必须交接清楚,若有异常及时通知相关负责人进行处理。
4、交接班检查严禁启动机械设备,若需试车,必须得到现场指挥人员的指令并确认线内无人检查时方可启动设备。
5、主轧机启动前,润滑系统、液压系统、冷却系统必须处于运行状态,且指示灯亮。
6、主轧机启动前,必须确认面板上未挂检修牌,且经现场调度同意。
7、主轧机启动前,操作台工必须发出启动信号,方可启动设备。
8、过钢前必须确认各设备运行正常(注意观察空载电流);过钢前必须接到现场指挥人员指令,先送上要钢信号灯,并在钢坯出炉前向全线发出警报。
9、在操作过程中,要适时调整修改工艺技术参数,处理好各架次的堆拉关系,主张微张力轧制,以确保产品质量,时刻观察1—18架轧机,精轧机电流变化,夹送辊、吐丝机转数有电流变化值,6个活套的调节量,如有异常及时通知当班班长和机组负责人!10、严格按信号灯指示,过钢生产,发出堆钢、跑钢事故及时卡断并关闭信号灯(参照特殊操作注意事项)。
11、接到正常停车检查指令时必须先确认轧件已出吐丝机,才可以停车,以免造成压车事故。
12、停车后,各辊道、轧机、飞剪等设备开关手柄按钮应打到O 位,关闭电源,以防设备自动运转造成事故。
(B)主控台操作注意事项一、更换轧制规格1、根据轧制规格选用相对应的轧制程序表。
2、看看表里的工作辊径和现在要换的工作辊径、延伸系数是否一致。
(必须确认现场原始辊径)。
3、输入目前使用精轧辊环工作辊径。
精轧机轧钢岗位操作规程(3篇)

精轧机轧钢岗位操作规程一、安全操作规程1. 操作人员必须经过专业培训,熟悉精轧机的结构、工作原理和操作方法,严禁无证上岗。
2. 操作人员进入作业区域前,必须穿戴好劳动防护用品,包括安全帽、防护眼镜、耳塞、防护手套等。
3. 在操作过程中,禁止携带易燃、易爆、有毒、有害物品进入作业区域。
4. 在操作过程中,禁止操作人员穿戴松散的衣物或饰品,以防被卷入机器。
5. 操作过程中,禁止随意触摸或调整机器的动作部件,必须先停机并切断电源后才能进行相关调整。
6. 发现精轧机运行异常或有异常噪音时,必须立即停机并向上级报告,等待维修人员处理后方可重新开机。
7. 在操作过程中,禁止随意更改设备设置、参数和程序,必须按照操作规程进行操作。
8. 进行设备保养和维修时,必须先切断电源,并进行标识,防止他人误操作。
二、操作规程1. 开机准备(1)检查精轧机的冷却系统、润滑系统和电气系统是否正常运行。
(2)确认熔钢方坯的温度和尺寸是否符合要求。
(3)确认精轧机工作台面清洁,无杂物和毛刺。
2. 开机操作(1)按照程序启动精轧机,等待主机正常运转。
(2)检查轧辊的润滑情况,如有不良应及时处理。
(3)调整轧辊间距,确保符合钢材尺寸要求。
(4)将钢材方坯放置在指定位置,用夹具固定好方坯。
3. 轧钢操作(1)在轧钢操作前,必须确保操作人员有足够的专业技能。
(2)按照规定的工艺参数和轧制要求设置精轧机。
(3)在操作过程中,必须密切观察钢材的轧制情况,及时调整轧辊间距和设备参数,确保轧制质量。
(4)操作人员必须掌握不同类型钢材的轧制规范和要求,严格按照要求进行操作。
4. 关机操作(1)按照规定的程序将精轧机停机。
(2)关闭精轧机的冷却系统、润滑系统和电气系统。
(3)整理并清洁工作区域,清除工作台面上的钢渣和废料。
三、应急处置1. 在发生紧急情况时,操作人员应立即切断电源,并按照应急预案进行处置。
2. 在发生设备故障或异常时,操作人员应立即停止操作,向上级报告并等待维修人员处理。
轧机安全操作规程
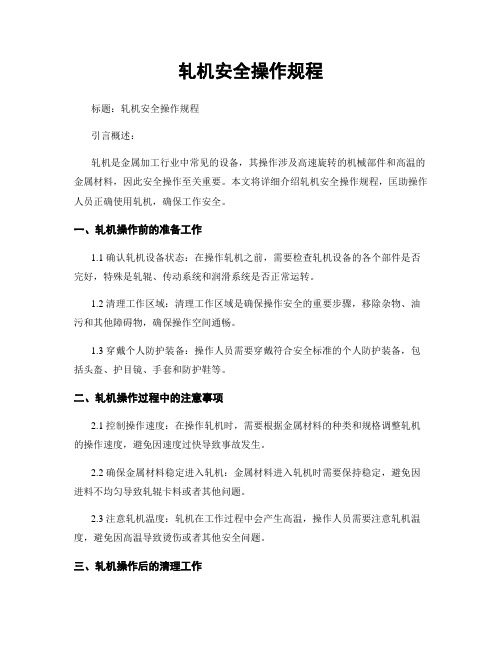
轧机安全操作规程标题:轧机安全操作规程引言概述:轧机是金属加工行业中常见的设备,其操作涉及高速旋转的机械部件和高温的金属材料,因此安全操作至关重要。
本文将详细介绍轧机安全操作规程,匡助操作人员正确使用轧机,确保工作安全。
一、轧机操作前的准备工作1.1 确认轧机设备状态:在操作轧机之前,需要检查轧机设备的各个部件是否完好,特殊是轧辊、传动系统和润滑系统是否正常运转。
1.2 清理工作区域:清理工作区域是确保操作安全的重要步骤,移除杂物、油污和其他障碍物,确保操作空间通畅。
1.3 穿戴个人防护装备:操作人员需要穿戴符合安全标准的个人防护装备,包括头盔、护目镜、手套和防护鞋等。
二、轧机操作过程中的注意事项2.1 控制操作速度:在操作轧机时,需要根据金属材料的种类和规格调整轧机的操作速度,避免因速度过快导致事故发生。
2.2 确保金属材料稳定进入轧机:金属材料进入轧机时需要保持稳定,避免因进料不均匀导致轧辊卡料或者其他问题。
2.3 注意轧机温度:轧机在工作过程中会产生高温,操作人员需要注意轧机温度,避免因高温导致烫伤或者其他安全问题。
三、轧机操作后的清理工作3.1 关闭轧机电源:在轧机操作结束后,需要及时关闭轧机电源,避免因电源未关闭而引起安全事故。
3.2 清理轧机设备:清理轧机设备是确保设备长期稳定运行的关键步骤,及时清理油污和杂物,保持设备清洁。
3.3 检查设备状态:在清理轧机设备的过程中,需要检查设备各部件是否正常,如有异常情况及时处理或者报告。
四、轧机操作中的紧急情况处理4.1 紧急停机:如果在轧机操作过程中发生紧急情况,操作人员需要即将按下紧急停机按钮,住手轧机运转。
4.2 报警处理:轧机设备通常配备有报警系统,一旦发生异常情况,报警系统会及时提醒操作人员,操作人员需要及时处理。
4.3 疏散安全:在发生紧急情况时,操作人员需要迅速疏散到安全区域,避免因事故扩大造成人员伤亡。
五、轧机定期维护保养5.1 定期润滑轧机设备:轧机设备需要定期润滑,保持设备各部件的正常运转,延长设备使用寿命。
轧机工安全操作规程(4篇范文)

轧机工安全操作规程(4篇范文)(经典版)编制人:__________________审核人:__________________审批人:__________________编制单位:__________________编制时间:____年____月____日序言下载提示:该文档是本店铺精心编制而成的,希望大家下载后,能够帮助大家解决实际问题。
文档下载后可定制修改,请根据实际需要进行调整和使用,谢谢!并且,本店铺为大家提供各种类型的经典范文,如工作报告、合同协议、心得体会、演讲致辞、规章制度、岗位职责、操作规程、计划书、祝福语、其他范文等等,想了解不同范文格式和写法,敬请关注!Download tips: This document is carefully compiled by this editor. I hope that after you download it, it can help you solve practical problems. The document can be customized and modified after downloading, please adjust and use it according to actual needs, thank you!Moreover, our store provides various types of classic sample texts, such as work reports, contract agreements, insights, speeches, rules and regulations, job responsibilities, operating procedures, plans, blessings, and other sample texts. If you want to learn about different sample formats and writing methods, please pay attention!轧机工安全操作规程(4篇范文)【第1篇】轧机工安全操作规程1、上班前必须戴好防护用品,上班时严禁穿汗衫、短裤、拖鞋。
轧制安全操作规程(3篇)
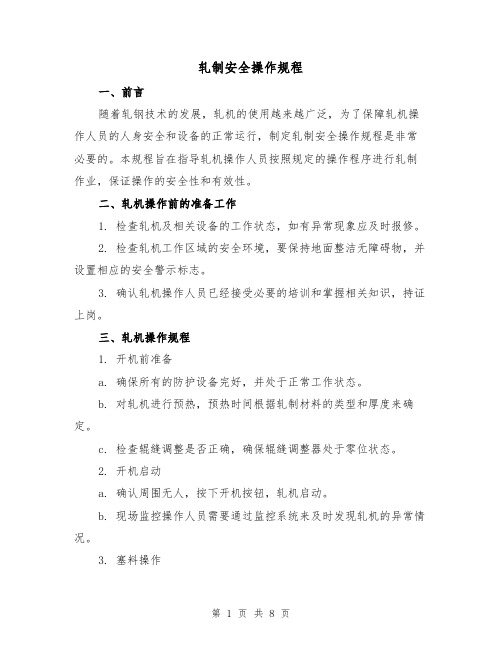
轧制安全操作规程一、前言随着轧钢技术的发展,轧机的使用越来越广泛,为了保障轧机操作人员的人身安全和设备的正常运行,制定轧制安全操作规程是非常必要的。
本规程旨在指导轧机操作人员按照规定的操作程序进行轧制作业,保证操作的安全性和有效性。
二、轧机操作前的准备工作1. 检查轧机及相关设备的工作状态,如有异常现象应及时报修。
2. 检查轧机工作区域的安全环境,要保持地面整洁无障碍物,并设置相应的安全警示标志。
3. 确认轧机操作人员已经接受必要的培训和掌握相关知识,持证上岗。
三、轧机操作规程1. 开机前准备a. 确保所有的防护设备完好,并处于正常工作状态。
b. 对轧机进行预热,预热时间根据轧制材料的类型和厚度来确定。
c. 检查辊缝调整是否正确,确保辊缝调整器处于零位状态。
2. 开机启动a. 确认周围无人,按下开机按钮,轧机启动。
b. 现场监控操作人员需要通过监控系统来及时发现轧机的异常情况。
3. 塞料操作a. 操作人员应严格按照塞料操作程序进行操作,避免将手指或其他物体伸入轧机辊缝内。
b. 打开压料器并逐渐将材料送入辊缝,注意保持均匀的压力,避免堆料导致异常情况。
c. 定期检查辊缝是否堵塞,如有堵塞应及时清理。
4. 运行过程中的注意事项a. 操作人员要随时监控轧机的工作情况,特别是轧辊的温度和辊缝的调整情况。
b. 如有异常声响或振动感应,应立即停机检查,并排除故障,确保设备安全运行。
c. 定期给轧辊进行润滑保养,确保辊缝工作的正常状态。
5. 关机操作a. 停机前应将轧机运行速度调到最低档。
b. 关闭压料器和辊缝调整器,并关闭电源。
c. 检查轧机及周边设备是否处于安全状态,清理工作区域,恢复现场环境。
四、事故应急处理1. 如发生轧机故障或异常情况,应立即停机,并按照应急预案进行处理。
2. 在事故处理过程中要保持冷静,及时通知相关人员,并采取适当的应急措施。
3. 紧急情况下,必要时可通过急停按钮进行紧急停机。
五、轧机操作人员的职责和义务1. 遵守轧机操作规程,严格按照操作程序进行操作。
轧机安全操作规程
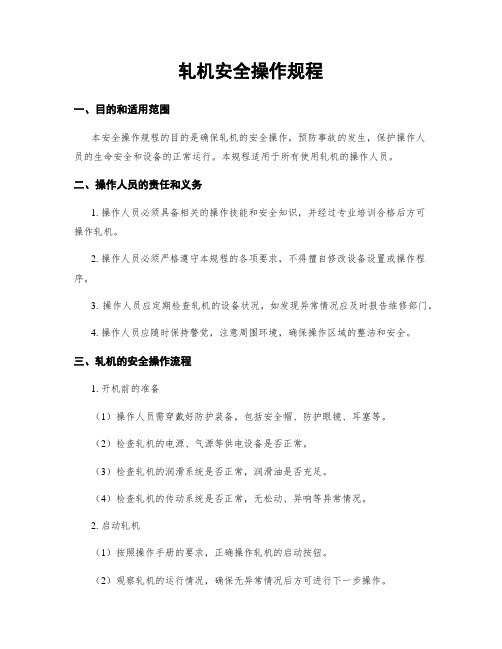
轧机安全操作规程一、目的和适用范围本安全操作规程的目的是确保轧机的安全操作,预防事故的发生,保护操作人员的生命安全和设备的正常运行。
本规程适用于所有使用轧机的操作人员。
二、操作人员的责任和义务1. 操作人员必须具备相关的操作技能和安全知识,并经过专业培训合格后方可操作轧机。
2. 操作人员必须严格遵守本规程的各项要求,不得擅自修改设备设置或操作程序。
3. 操作人员应定期检查轧机的设备状况,如发现异常情况应及时报告维修部门。
4. 操作人员应随时保持警觉,注意周围环境,确保操作区域的整洁和安全。
三、轧机的安全操作流程1. 开机前的准备(1)操作人员需穿戴好防护装备,包括安全帽、防护眼镜、耳塞等。
(2)检查轧机的电源、气源等供电设备是否正常。
(3)检查轧机的润滑系统是否正常,润滑油是否充足。
(4)检查轧机的传动系统是否正常,无松动、异响等异常情况。
2. 启动轧机(1)按照操作手册的要求,正确操作轧机的启动按钮。
(2)观察轧机的运行情况,确保无异常情况后方可进行下一步操作。
3. 加工操作(1)根据工艺要求,选择合适的轧辊和轧机参数。
(2)将待加工的材料放置在轧机上,并确保固定牢固。
(3)根据工艺要求,调整轧机的传动速度和轧辊的间隙。
(4)操作人员应时刻关注轧机的运行情况,确保加工过程中的稳定性。
4. 加工结束(1)加工结束后,操作人员应及时停止轧机的运行。
(2)清理加工区域,将废料和杂物清理干净。
(3)关闭轧机的电源和气源,确保设备处于安全状态。
四、轧机的安全注意事项1. 操作人员在操作轧机时,应保持专注,不得分心或进行无关操作。
2. 操作人员应时刻关注轧机的运行情况,如发现异常情况应立即停机并报告维修部门。
3. 操作人员不得将手部或其他物体靠近轧辊,以免发生夹伤事故。
4. 操作人员不得随意调整轧机的参数或设备设置,必须经过相关部门的批准和指导。
5. 操作人员应定期参加安全培训和演练,提高自身的安全意识和应急处理能力。
轧机工安全操作规程(3篇)

轧机工安全操作规程一、操作前准备1.1 确保轧机设备处于正常工作状态,无故障、无异响等异常情况。
1.2 检查轧机工作区域是否整洁,无杂物、障碍物或其他危险物品。
1.3 确保操作人员佩戴必要的个人防护装备,包括安全帽、防护眼镜、耳塞、防护手套等。
1.4 检查轧机相关的安全设施是否完好,如安全门、急停按钮、防护罩等。
1.5 首次操作前,务必接受专业培训并理解轧机的工作原理、操作步骤和安全规程。
二、操作过程2.1 操作人员应站稳操作台前,保持平衡,注意站姿,避免发生滑倒、摔伤等意外。
2.2 操作人员应将双手干燥,避免使用湿手操作轧机开关和按钮。
2.3 操作人员应始终保持专注,集中注意力,不得分心或与他人交谈。
2.4 操作人员在操作过程中,应严格按照工艺流程和操作指导进行操作,不得随意改变工艺参数或操作步骤。
2.5 操作人员在操作过程中,应时刻关注设备的工作状态,如有异常情况应立即停机检修,并报告相关人员。
2.6 操作人员应保持手部清洁,不得有油污或其他外物,以免影响操作手感或引发事故。
2.7 操作人员在调节轧机参数时,应用力适中,不得用力过猛或过小心。
2.8 操作人员严禁在轧机运行时将手或其他物体靠近辊子或其他运动部件,以免造成伤害。
三、紧急情况处理3.1 在发生紧急情况时,操作人员应立即按下急停按钮,并向周围人员发出警示。
3.2 操作人员应迅速离开工作区域,并告知有关人员。
3.3 在发生事故或紧急情况后,操作人员应立即向相关负责人报告,并积极参与事故处理和事故调查工作。
四、设备维护和保养4.1 在轧机工作结束后,操作人员应及时清理工作区域,排除杂物和危险物品。
4.2 操作人员应定期检查轧机设备的润滑情况,并按规定添加润滑油。
4.3 操作人员应定期检查轧机设备的电气线路,确保无漏电、短路等安全隐患。
4.4 操作人员应定期对轧机设备进行维护保养,包括清洁、紧固螺栓、更换磨损部件等。
4.5 操作人员要定期参加安全培训和技术交流,提高自身安全意识和操作技能。
轧机工岗位职责(4篇)

轧机工岗位职责(4篇)轧机工岗位职责(精选4篇)轧机工岗位职责篇11、做到本工序产品不损坏,设备不人为损坏,确保设备人身安全。
2、正确穿戴劳保用品,严格按照各种设备操作规程进行操作,确保无事故发生。
认真做好班组消防工作,妥善保管好消防器材。
3、严格遵守安全操作规程安全操作。
4、做到场地打扫干净,砂箱摆放整齐,定期清扫设备及地坑里的`砂土。
5、清产工要做到重视安全的同时,提高设备性能的了解,提高工作质量。
6、听从领导安排,按时完成当天的生产任务7、认真执行公司的各项规章制度,不早退不迟到不旷工,工作时间不闲谈不串岗。
轧机工岗位职责篇21、按照管生产必须管安全,谁主管谁负责的原则,对企业的安全生产负主要责任。
2、组织制订、修订和审批安全生产规章制度、安全技术规程及安全技术措施计划,并组织实施。
3、坚持贯彻五同时原则,监督检查生产职能部门安全职责履行和各项安全生产规章制度的执行情况,及时纠正生产中的失职和违章行为。
4、组织生产职能部门对厂生产事故进行调查处理,并及时向上级安全生产部门报告。
5、组织安全生产大检查,落实重大生产事故隐患的.整改,负责审批特级动火。
6、负责安全培训、教育和考核工作。
7、定期召开安全生产工作会议,分析企业安全生产动态,及时解决安全生中存在的问题。
8、按照上述安全职责,每年制订年度安全工作计划,逐条落实在当年具体工作安排中。
轧机工岗位职责篇31、进行新产品铸造工艺设计2、解决铸造生产过程中的技术问题3、负责对现场生产人员进行技术指导4、检查、督促生产人员按有关标准、工艺、规范进行生产操作5、负责铸造模具设计、设备的.选型、原料选型及性能验证等6、负责铸造一线作业员的培训坏防护装臵。
6、开展无事故,无违章,无隐患活动。
严禁违章作业,杜绝事故发生。
7、芯盒,砂箱、卡子摆放整齐,不在班前和工作时间饮酒。
不在不允许吸烟的场所吸烟。
杜绝骂人吵架光背赤脚等不文明行为。
坚持每天一小扫,每周一大扫。
精轧机轧钢岗位操作规程(三篇)
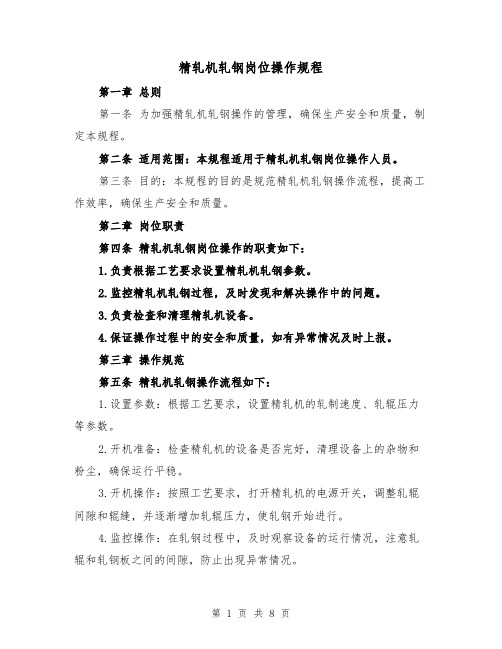
精轧机轧钢岗位操作规程第一章总则第一条为加强精轧机轧钢操作的管理,确保生产安全和质量,制定本规程。
第二条适用范围:本规程适用于精轧机轧钢岗位操作人员。
第三条目的:本规程的目的是规范精轧机轧钢操作流程,提高工作效率,确保生产安全和质量。
第二章岗位职责第四条精轧机轧钢岗位操作的职责如下:1.负责根据工艺要求设置精轧机轧钢参数。
2.监控精轧机轧钢过程,及时发现和解决操作中的问题。
3.负责检查和清理精轧机设备。
4.保证操作过程中的安全和质量,如有异常情况及时上报。
第三章操作规范第五条精轧机轧钢操作流程如下:1.设置参数:根据工艺要求,设置精轧机的轧制速度、轧辊压力等参数。
2.开机准备:检查精轧机的设备是否完好,清理设备上的杂物和粉尘,确保运行平稳。
3.开机操作:按照工艺要求,打开精轧机的电源开关,调整轧辊间隙和辊缝,并逐渐增加轧辊压力,使轧钢开始进行。
4.监控操作:在轧钢过程中,及时观察设备的运行情况,注意轧辊和轧钢板之间的间隙,防止出现异常情况。
5.记录数据:定期记录精轧机的操作数据,包括轧制速度、轧辊压力等参数,以便进行后续工艺分析。
6.收尾工作:结束轧钢操作后,及时关闭精轧机电源,并进行设备的清理和维护工作。
第四章安全操作第六条在精轧机轧钢操作过程中,必须严格遵守以下安全操作规程:1.佩戴个人防护装备:轧钢岗位操作人员必须佩戴安全帽、防护眼镜、耳塞等个人防护装备。
2.设备检修:开机前必须对精轧机设备进行检修,检查各部位是否完好,并清理设备上的杂物和粉尘。
3.操作人员要熟悉精轧机设备的结构和工作原理,掌握各种操作方法和常见故障处理方法,以便及时解决操作中的问题。
4.操作人员要认真观察精轧机的运行情况,如有异常情况及时上报,并采取相应的措施进行处理。
5.禁止用手触摸轧辊和轧钢板,禁止将手或其他物品伸入轧辊间隙。
6.严禁在轧钢过程中进行打闹、吸烟等危险行为。
第五章质量控制第七条在精轧机轧钢操作过程中,必须严格按照质量要求进行操作,确保产品质量。
轧机安全操作规程

轧机安全操作规程一、引言轧机是一种用于金属加工的重要设备,为了保障工作人员的安全以及设备的正常运行,制定轧机安全操作规程是非常必要的。
本文将详细介绍轧机的安全操作规程,包括轧机的基本知识、操作前的准备工作、操作过程中的注意事项以及紧急情况下的应急措施。
二、轧机的基本知识1. 轧机是用于将金属材料进行轧制加工的设备,主要由辊子、电机、减速器、润滑系统等组成。
2. 轧机的工作原理是通过辊子的旋转将金属材料压制成所需的形状和尺寸。
3. 轧机通常分为冷轧机和热轧机两种类型,根据不同的工艺需求选择合适的轧机进行操作。
三、操作前的准备工作1. 工作人员必须穿戴好个人防护装备,包括安全帽、防护眼镜、耳塞、防护手套等。
2. 确保轧机及周围区域的清洁,清除杂物和障碍物,保持工作环境整洁有序。
3. 检查轧机的电气系统、润滑系统和传动系统是否正常运行,如发现异常情况应及时报修。
4. 确保轧机的辊子和工作台面干净,无油污和杂质,以免影响轧制质量和安全操作。
四、操作过程中的注意事项1. 操作人员必须熟悉轧机的操作流程和控制面板的功能,严禁未经培训人员进行操作。
2. 在操作过程中,严禁将手、脚或其他身体部位靠近轧机辊子,以免发生夹伤或其他伤害。
3. 操作人员必须保持专注,不得在操作过程中分心或进行与工作无关的活动。
4. 在调整轧机辊子间隙时,应使用专用工具,严禁用手直接接触辊子,以免造成伤害。
5. 在轧制过程中,应及时观察轧机的工作状态,如发现异常情况应立即停机检修。
6. 操作人员离开工作岗位时,应将轧机停机并切断电源,确保设备处于安全状态。
五、紧急情况下的应急措施1. 在发生火灾或其他紧急情况时,操作人员应立即按下紧急停机按钮,并迅速撤离现场。
2. 如果发生人员伤害或事故,应立即向相关部门报告,并进行急救处理。
3. 在紧急情况下,不得擅自进行设备维修,必须由专业人员进行检修和修复。
六、结语轧机的安全操作规程对于保障工作人员的生命安全和设备的正常运行至关重要。
轧机岗位安全操作规程
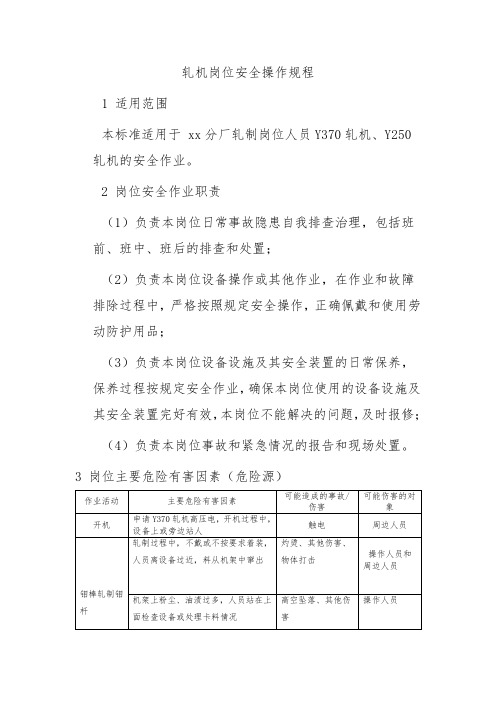
轧机岗位安全操作规程1 适用范围本标准适用于 xx分厂轧制岗位人员Y370轧机、Y250轧机的安全作业。
2 岗位安全作业职责(1)负责本岗位日常事故隐患自我排查治理,包括班前、班中、班后的排查和处置;(2)负责本岗位设备操作或其他作业,在作业和故障排除过程中,严格按照规定安全操作,正确佩戴和使用劳动防护用品;(3)负责本岗位设备设施及其安全装置的日常保养,保养过程按规定安全作业,确保本岗位使用的设备设施及其安全装置完好有效,本岗位不能解决的问题,及时报修;(4)负责本岗位事故和紧急情况的报告和现场处置。
3 岗位主要危险有害因素(危险源)4 劳动防护用品穿戴要求4.1 作业人员应穿戴工作服、劳保鞋,长发应盘在工作帽内,袖口及衣服角应系扣。
4.2 现场作业人员应佩带安全帽、防护眼镜、防尘口罩。
4.4 现场作业时应佩戴耳塞。
5 中频加热炉操作安全要求5.1作业前准备安全操作5.1.1 作业前对工作环境进行检查,中频炉周边是否有多余物品,现场是否带有防坠落的栏杆、防护板并完好有效;5.1.2 作业前,对使用的设备和工具进行检查,确保设备工具及其安全装置完好、有效:(1)检查循环水压力是否正常(压力应为0.15Mpa左右),压缩空气压力是否正常(压力应为0.5Npa左右),检查轧机的机械、电器部分和轧机各部件安装是否正确、紧固。
启动润滑油泵,检查压力是否正常(2)检查机架安全销有无脱落,断裂。
若有,吊下机架,更换新安全销。
并定期检查机架磨损和使用状况。
若需使用起吊设备,必须由专人操作,严禁下方有人站立,使用起吊设备必须检查吊绳,严禁超载。
(3)Y370轧机高压电要求专人到动力分厂配电室要电,填写好设备运行记录。
记录内容包括:通知送电人员,送电时间。
(4) 确认正常后,按照送电程序启动轧机。
进行空载试运行,确认空载运行正常后,进入轧制前的准备。
5.1.3 作业前,应先开启现场通风和除尘装置,按要求填写安全环保设施运行纪录。
轧机操作工岗位职责

轧机操作工岗位职责轧机操作工岗位职责一、岗位职责1、负责轧钢生产线的调度控制。
2、负责主控室轧制工艺参数和控冷工艺参数的设定和调整。
3、负责质量记录和生产记录。
二、操作程序1、严格执行操作牌制,无操作牌不得启动任何电器设备。
2、主操作室属要害部位,无关人员禁止入内,不得将岗位交给他人代为操作。
3、进入岗位后,要集中精力协调好各工序的工作,时刻注意现场情况,重大险情有权立即停车。
4、设备检修或停止作业时,操作室必须有人值班。
所有开关不得随意拨动。
5、生产过程中,操作工要随时注意台下调整工及维修巡检人员的位置,防止发生意外事故。
6、在接到各工序都正常时的通知后,才可发出“要求出钢”信号。
7、操作工应根据不同区域发出的故障信号采取不同的措施。
8、发生堆钢要立即启动飞剪进行碎断,并通知加热炉停止出钢,同时卡断剪卡断,出炉辊道停运。
三、操作要点1、接班后要认真检查喷嘴、导管是否通畅,检查水压及流量是否正常,检查各个阀门开闭是否灵活迅速,检查反风压是否符合要求。
2、各项参数设定钢种不同,控冷风冷的工艺不同,必须根据钢种进行以下各种控制参数的设定:3、水箱的使用数量4、水冷反、正喷嘴的流量和压力大小5、吐丝温度6、各架轧机转速7、集卷温度8、试车检查:各项参数设定后,还必须开车检查实际参数是否达到工艺要求,发现差异通过手动进行调整,当各项参数都满足工艺要求时,向主控台报告,开轧生产。
9、正常生产过程中,要经常检查设备运行情况,监视各参数的变化,随时进行调整,严格控制水量、风量和吐丝温度。
10、要经常检查导槽、吐丝管等部件的磨损情况,并及时更换。
11、注意控制吐丝圈的大小形状,及时调整防止乱线。
精轧机轧钢岗位操作规程

精轧机轧钢岗位操作规程一、工作内容1、该操作规程适用于精轧机轧钢岗位的操作人员。
2、岗位职责:操作精轧机进行锻轧加工,保证产品的质量和产量。
二、工作环境1、工作地点:精轧机轧钢车间。
2、环境条件:(1)室内环境,温度较高,易出汗;(2)声音较大,需佩戴防噪耳塞;(3)操作区域有高温、高压保护装置,请勿随意操作;(4)操作前需检查机台设备和室内环境情况。
三、操作准备1、岗位操作人员应了解产品的生产要求和工艺参数,根据工艺作业指导书和操作规程准备好操作前的准备工作和资料。
2、操作人员应佩戴好防护用品,如手套、安全鞋、防护眼镜等。
3、检查机台设备的电气、油液、气源等各项要求,发现问题及时上报维修人员进行检修。
四、操作步骤1、根据规定的工艺参数,对机台设备进行开机准备,确认设备调整到生产状态。
2、按照要求进行规范化操作。
3、对机台设备操作时,应根据正常的加工要求,严格操作,保证产品的生产质量和产量。
4、对出现的异常问题及时上报或联系相关人员进行处理。
5、根据作业指导书的要求进行设备的保养和维修工作,定期检查并上报相关部门进行维修。
五、操作安全注意事项1、操作人员必须具备一定的专业知识和操作技能,不得私自擅长调整和操作。
2、必须严格遵守生产作业安全规定,检查设备状态和设备周围环境,确保操作安全。
3、禁止将手或脚伸入机台设备中进行操作或维修。
4、严禁私自打开有关机电设备的电源、油门、工具等。
5、设备出现问题时,必须立即停止操作并通知上级主管或技术人员及时处理。
六、操作记录1、操作人员应及时完善操作记录,并上报检查员进行审核。
2、操作记录应包括每次设备操作的时间、产量及生产情况等重要信息。
3、对于发生的事故、问题及时记录和上报,以确保操作安全和设备良好的使用状态。
轧机安全操作规程

轧机安全操作规程一、引言轧机是一种用于金属加工的重要设备,广泛应用于钢铁、有色金属等行业。
为了确保轧机操作过程中的安全,保护操作人员的生命财产安全,制定本安全操作规程。
二、操作人员要求1. 操作人员必须经过相关培训,了解轧机的结构、工作原理以及安全操作规程。
2. 操作人员必须具备良好的身体健康状况,不得患有严重的心脏病、高血压等疾病。
3. 操作人员必须年满18周岁,并持有合法的操作证书。
4. 操作人员必须佩戴符合标准的个人防护装备,包括安全帽、防护眼镜、防护手套等。
三、轧机安全操作规程1. 在开始操作轧机之前,操作人员必须检查轧机的各个部件是否完好,如有异常应及时报告维修人员。
2. 操作人员必须确保轧机周围没有杂物,保持操作区域的整洁和通风良好。
3. 在操作轧机之前,操作人员必须确认轧机的电源已经切断,并进行锁定和标识。
4. 操作人员必须按照轧机的工作规程进行操作,不得擅自调整轧机的参数和工作状态。
5. 在操作轧机时,操作人员必须集中注意力,不得分心或者与他人交谈。
6. 操作人员必须按照规定的工作程序进行操作,如需停机或者调整轧机,必须按照规定的程序进行。
7. 在操作轧机时,操作人员必须保持双手干燥,不得穿戴松散的衣物或者佩戴饰物。
8. 操作人员必须定期检查轧机的润滑系统,确保润滑油的充足和正常运行。
9. 在轧机操作过程中,如发现异常声音、异味或者其他异常情况,操作人员必须即将停机,并报告维修人员。
10. 操作人员在操作轧机时,不得将手指、手臂或者其他身体部位伸入轧机的工作区域。
11. 操作人员必须定期进行体检,确保身体健康状况符合操作要求。
四、紧急情况处理1. 在发生紧急情况时,操作人员必须即将按下紧急停机按钮,并向上级报告。
2. 在发生火灾或者其他严重事故时,操作人员必须即将采取逃生措施,并向消防部门报警。
五、事故处理和报告1. 在发生事故时,操作人员必须即将停机,并采取必要的救援措施,确保受伤人员的安全。
精轧机轧钢岗位操作规程范本

精轧机轧钢岗位操作规程范本第一章总则第一条目的和依据为保障精轧机轧钢工作的安全、高效进行,特制定本操作规程。
本规程的制定依据包括国家相关法律法规、行业标准以及企业安全生产管理要求等。
第二条适用范围本规程适用于精轧机轧钢岗位的作业人员,以及相关管理人员。
第三条术语和定义1. 精轧机:指用于钢材精密轧制的设备。
2. 轧钢工:指在精轧机轧钢岗位从事生产作业的操作人员。
第二章操作安全规范第一条工作前准备1. 轧钢工在上岗前应穿戴好劳动防护用品,包括安全帽、劳动服、防护眼镜、防护手套等。
2. 确保设备处于正常工作状态,并检查液压、电气、机械等系统是否正常。
3. 确保作业区域的环境整洁,清除杂物和易燃物,保持通道畅通。
第二条操作流程1. 熟悉精轧机的结构和工作原理,并掌握操作方法;2. 根据生产任务书,调整精轧机的参数和工作模式;3. 按照工艺要求,将待轧钢材放入精轧机,并调整轧辊的位置和间隙;4. 启动精轧机,调整好轧辊的转速和压力,确保钢材能够顺利通过精轧机;5. 观察轧钢过程中的各项指标,并及时进行调整,确保产品质量符合要求;6. 钢材轧制完毕后,及时停机并将轧辊调整到初始位置;7. 完成轧钢作业后,清理工作现场,做好设备的维护保养工作。
第三条操作注意事项1. 操作人员在操作精轧机时,应专心致志,认真操作,不得分神、闲聊或干扰他人;2. 操作人员应随时观察精轧机的运行情况,如发现异常或故障,应及时报告维修人员进行处理;3. 在清理工作现场时,要注意钢材的锋利边缘和高温部位,避免伤害;4. 在设备维修保养时,应按照相关规定进行,切勿违规操作。
第三章环境保护与节能减排第一条环保要求1. 精轧机使用的润滑油、液压油等应当符合国家环保标准,不得使用过期或废弃的油品。
2. 精轧机的尾气排放应当符合国家相关标准,不得超过规定的排放限值。
第二条节能减排1. 精轧机在不需要使用时,应及时关闭或切换到节能模式;2. 降低精轧机的负荷率,避免不必要的能耗;3. 定期清洗和维护精轧机,确保设备的运行效率和节能效果;4. 合理利用废气和废热资源,降低能源消耗。
精轧机轧钢岗位操作规程范文
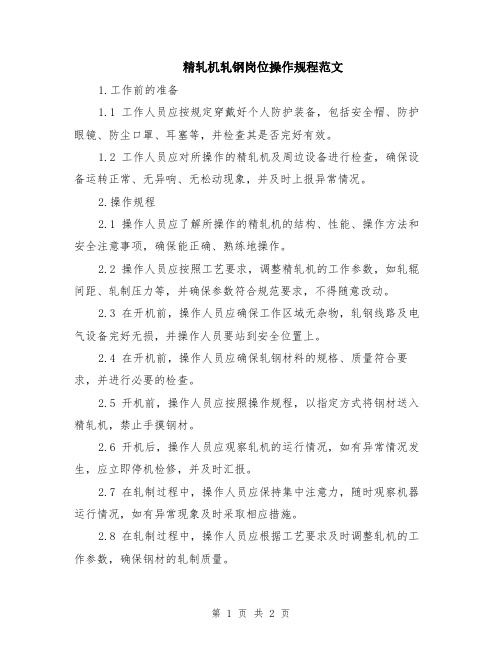
精轧机轧钢岗位操作规程范文1.工作前的准备1.1 工作人员应按规定穿戴好个人防护装备,包括安全帽、防护眼镜、防尘口罩、耳塞等,并检查其是否完好有效。
1.2 工作人员应对所操作的精轧机及周边设备进行检查,确保设备运转正常、无异响、无松动现象,并及时上报异常情况。
2.操作规程2.1 操作人员应了解所操作的精轧机的结构、性能、操作方法和安全注意事项,确保能正确、熟练地操作。
2.2 操作人员应按照工艺要求,调整精轧机的工作参数,如轧辊间距、轧制压力等,并确保参数符合规范要求,不得随意改动。
2.3 在开机前,操作人员应确保工作区域无杂物,轧钢线路及电气设备完好无损,并操作人员要站到安全位置上。
2.4 在开机前,操作人员应确保轧钢材料的规格、质量符合要求,并进行必要的检查。
2.5 开机前,操作人员应按照操作规程,以指定方式将钢材送入精轧机,禁止手摸钢材。
2.6 开机后,操作人员应观察轧机的运行情况,如有异常情况发生,应立即停机检修,并及时汇报。
2.7 在轧制过程中,操作人员应保持集中注意力,随时观察机器运行情况,如有异常现象及时采取相应措施。
2.8 在轧制过程中,操作人员应根据工艺要求及时调整轧机的工作参数,确保钢材的轧制质量。
2.9 在轧制过程中,操作人员应注意钢材的出口附近,防止堆积过多的钢材,避免发生滑倒等意外事故。
2.10 轧制完成后,操作人员应及时停机,清理工作区域,确保安全整洁。
3.安全注意事项3.1 车间内应保持通风良好,防止有害气体积聚。
3.2 禁止在设备运行过程中进行检修、维护或更换零部件等工作。
3.3 车间内应保持整齐、干净,没有杂物堆放,设备周围应有明显的安全标识。
3.4 操作人员应按照规定的操作方法进行操作,禁止随意更改工艺参数。
3.5 操作人员不得私自更改、关闭、绕过设备的安全保护装置和控制系统。
3.6 在操作过程中,操作人员应随时保持警惕,注意观察设备运行状况,如有异常情况应及时报告。
轧机岗位安全操作规程

轧机岗位安全操作规程一、交接班安全注意事项1、交班组在交班前15分钟内仔细点检所属设备状况,将设备异常情况详细记录.通知整备人员并交待接班组。
2、接班组在接班后10分钟内仔细点检所属设备状况,将设备异常情况通知机械电气整备人员。
3、交接时要将设备隐患点详细传达到班组每个成员,避免发生不知情的误操作。
而导致安全事故.4、如果在轧制过程中交接班,交班组必须详细告之接班组钢卷前面的生产情况尤其是异常情况;而接班组也必须了解钢卷前面的生产情况,做到心中有数生产。
5、每天的交接班活动必须进行而且以安全为主,向班员宣传安全生产的意义。
6、交班组要详细向接班组交待前生产形势,上级作业安排,接班组要严格执行。
二、生产准备安全事项1、原料吊运首先检查捆带状况,一根或捆带破损未扣牢的严禁吊运,一定要重新捆好方可吊,其次吊卷人员不得站在钢卷下或正侧面,防止意外伤人,再次正确执行行车指挥信号,确认“C"形钩是否完全插入钢卷内径中,防止“C"形钩伤人。
2、使用相关工具器材前必须检查其完好状况,严重开裂或报废的工具器材严禁使用,也要小心防止滑落砸坏设备。
3、叉运垫纸注意叉车伤人,吊运垫纸注意吊带十分系好,以防垫纸滑落伤人,叉车严谨坐闲杂人员.4、搬运工作辊时两人注意协调,防止辊子伤手、脚,同时一定要注意爱惜工作辊,不要在搬运中碰伤辊子.5、准备好生产所需的各类劳保用品,并按标准佩戴使用.三、机组启动及停止时的安全作业事项启动前:1、确认冷却水阀门是否开,压缩空气阀门是否开,电气整备电是否输上,轧制油、液压油是否可以正常供给,阀门应打开,液位不足应补充。
确认各危险部位有无闲杂人员,命其离开后才能开机。
2、确认电气、机械设备有无异常,如有必须通知有关人员修理好方可开机生产。
确认轧制油、液压油泄露点,有,要通知整备修理。
3、确认机架下滤网有无堵塞,防止轧制油外溢。
4、检查辊系状态,如支撑装置、悬挂装置,锁紧装置,W/S轴承的状态,损坏要马上修理或更换,否则不能开机生产。
- 1、下载文档前请自行甄别文档内容的完整性,平台不提供额外的编辑、内容补充、找答案等附加服务。
- 2、"仅部分预览"的文档,不可在线预览部分如存在完整性等问题,可反馈申请退款(可完整预览的文档不适用该条件!)。
- 3、如文档侵犯您的权益,请联系客服反馈,我们会尽快为您处理(人工客服工作时间:9:00-18:30)。
轧机操作岗位职责、操作工艺规程
目录
一、岗位名称: (3)
二、岗位职责: (3)
三、岗位工艺流程: (3)
1.框图 (3)
2.工艺概述: (3)
四、岗位区域设备及性能 (4)
1、飞剪机械设备 (6)
2、夹送辊设备技术性能 (8)
五、工艺要求 (9)
表1尺寸精度控制 (9)
表2各种规格的终轧速度 (10)
六、正常操作 (10)
1.设备的操作 (10)
2.正常的操作程序 (11)
3.更换轧制规格的操作步骤 (12)
4.控冷操作 (12)
5.轧线速度及联控制 (13)
6.微张力控制 (14)
7.活套控制 (14)
8. 控制系统过程跟踪 (15)
9.飞剪周期控制 (16)
10.存储轧制程序 (17)
七、特殊操作 (18)
一、岗位名称:
轧机操作台工。
二、岗位职责:
①.熟悉和了解轧钢生产工艺流程,全面掌握轧制工艺及控冷工艺的参数。
②.控制从1#机架到吐丝机的全工艺过程。
③.监视全生产线的机械、电气能源介质供应系统的设备运行状况。
三、岗位工艺流程:
1.框图
1#曲柄回转飞剪中轧机组;2#飞剪预精轧水箱;转辙器;碎断剪;卡断剪;精轧机组;水箱夹送辊;吐丝机。
2.工艺概述:
钢坯加热到规定温度出炉轧制,先由悬臂式出炉辊道把钢坯送到炉外辊道上,进入粗轧机组进行轧制,然后1#飞剪进行切头处理。
再进入中轧机组继续轧制,中间设有1#2#活套避免张力轧制, 中轧轧制完毕后2#剪进行切头、尾。
经3#侧活套进入预精轧轧出精轧需要的料型。
经水箱控温后,通过转辙器3#剪切头、尾,再经7#侧活套进入精轧机后经水箱控温生产出合格的成品.成品由水箱冷却在800℃左右,进入夹送辊吐丝机,卷曲成直径1250mm的盘圆进入风冷线进行斯太尔摩风冷线风冷冷却。
四、岗位区域设备及性能
1、飞剪机械设备
2、夹送辊设备技术性能
五、工艺要求
表1尺寸精度控制
表2各种规格的终轧速度
六、正常操作
1.设备的操作
(1)轧线设备的操作是通过三套人机接口的屏幕及键盘完成,其中两套系统功能相同,且互为备用,正常工作时每套系统完成各自的工作,其中一套故障时另一套同样能够完成工作,另一台控制高速区设备。
(2)辅助操作台面:辅助操作台面是整个人机接口系统的不可缺
少组成部分,生产过程中需要快速反应成频进行的操作,一般通过操作台面上的主操作元件来完成。
2.正常的操作程序
轧机的启动准备,运转和停车。
(1)主轧机启动前的准备工作:
①所有的选择开关均处于"允许运行"或"接通"位置。
②可控电源已经通电,处于准备完毕,而且电源准备好,指示灯亮。
③带联锁的辅助传动系统已运转,且处在允许的条件下,包括轧机齿轮润滑,电机通风、液压系统,冷却水系统等。
④所有选择的轧机传动电机的触点应处在闭合位置,且指示灯亮。
⑤操作人员发出轧机启动信号。
(2)启动和运转:
①按下相应的轧机的"START"按钮。
②电机从一个可控制的加速度到设定值。
(3)轧机的停车
①正常的停车--按下相应轧机的"STOP"按钮。
②紧急事故停车--按下"EMERGENCY"按钮。
③故障自动停车--联锁检测系统工作状态超出极限条件,引起轧机停车。
3.更换轧制规格的操作步骤
①根据轧制程序手册明确选用的轧机。
②预设定电机速度(尽可能保持共用孔型的机架参数值不变)。
③输入目前使用的轧辊工作辊径,修改吐丝机、夹送辊、穿水箱的工艺参数。
④接通辅助传动设备。
⑤启动电机。
⑥进行全线信号模拟轧制操作。
⑦开始轧制。
⑧监视和分析轧制过程。
注意:各架轧制电流值不能超过电机额定电流值。
当联锁保护系统出现故障时应采取手动操作。
取样操作取样地点为1#飞剪,2#飞剪和精轧前3#飞剪。
4.控冷操作
(1)在更换控冷程序时需先通知1CS停止出钢,待程序切换完毕后,才能恢复正常轧制。
(2)严格按控冷工艺要求,控制进精轧轧件温度和吐丝温度。
(3)由延迟型向标准型冷却转变时,要等辊道上所有盘卷全都查完之后再打开所有保温罩盖;并启动各段风机吹风,使辊道冷却后方能轧制。
(4)运输机在进行级联式调速时,必须在钢坯间隙间进行调节。
(5)当接到风冷线及双芯棒明确切钢信息后,立即启动飞剪进行碎断轧件。
5.轧线速度及联控制
采用及联调速是为了使控制系统或操作人员能够调整轧线某一对相邻机架的速度关系,而不影响轧线其它机架间距的速度关系。
控制台上配置粗、中、预精轧、精轧机组四个“机旁选择开关”四个“级联调节操作按钮”。
操作员首先通过“级联调节方式”键选择级联控制方式,然后通过“机架选择按钮”选择需改变速度的机架,再通过“调速按钮”对所选择的机架进行向上游级联速度调节。
操作员通过“级联调节方式”键选择级联非正常方式,然后通过“机架选择按钮”选择需改变速度的机架,再通过“调速按钮”对所选择的机架速度单调。
为保证精轧出口速度的稳定,级联方向为逆向级联。
根据级联延伸系数设定及自动级联调节综合产生和各机架成速度给定,再根据对应机架的工作辊径及齿轮减速比等因素折算为电机转速,然后线性变换为速度给定信号,通过实对通讯网络由PLC送给主传动进行速度调节。
6.微张力控制
微张力控制是指第1架至10架轧机间实现轧件微张力控制。
控制原则:
(1)保证轧制的顺利进行,避免严重堆拉钢现象。
(2)控制的张力值要使轧件处于稳定状态的效应大于各种外界因素变化引起的不稳定效应。
(3)使轧件头、中、尾尺寸偏差尽可能小。
(4)张力控制主要靠级联调节来实现。
控制过程:
(1)在轧件进入下一轧机前,测量并记录本机架的负荷。
(2)在轧件进入下一轧机后,未进入第三架轧机前,修正本机架的速度及其上游所有轧机的速度。
使本机架的负荷恢复到记忆或设定值。
在正常生产过程中,操作员用手动通过级联调节控制微张力。
7.活套控制
(1)活套控制是在10架BGV2,BGV2和精轧轧机间实现轧件无张力控制,共设有8个活套。
在正常生产过程中,操作人员选择“活套自动”,系统设有活套调节器,其作用是根据检测的活套高度偏差产生速度修正信号,调整机架速度以维持活套高度(活套量)在给定值上不变。
即修正活套前面各机架的速度,修正值的大小可以通过指示仪表观察,若每次咬入修正量过大或修正次数频繁,操作人员可以通过改变轧制设定或级联调速消除机架间的不等秒流量。
(2)活套高度的基准值通过计算机人机接口系统设定,活套形成靠逆调上游机架的速度来实现。
调整速度比例按1%~3%进行递增、递减。
(3)轧制前必须试车检查起套辊起套情况、起套力等,设置好起套高度。
活套起套高度设定表如下:
8. 控制系统过程跟踪
控制系统对轧件进行头尾跟踪,以产生所需的控制信号及实现协调的顺序控制。
在轧制过程中,故障检测系统通过比较轧件头部到达各架轧机中
心线的时间来完成。
如果检测的时间与设定的时间公差范围内不能重合,认为事故发生。
如果事故发生在粗轧机组,停止加热炉出钢,停止该架轧机及上游所有轧机。
如果事故发生在中轧机组,停止加热炉出钢,停止该架轧机及上游所在轧机,启动1#飞剪碎断。
如果事故发生在精轧机组,停止加热炉出钢,停止该架轧机及上游轧机,启动1#、2#飞剪碎断。
9.飞剪周期控制
1#、2#飞剪均为启停式结构,通过PLC上的智能模块实现飞剪的加速,剪切和制动的精确定位控制,剪节精度≤0.008×轧件速度
(mm/s),开机前必须对飞剪进行试刀和对刀。
(1)选择“操作台”模式和“自动”工作模式,“传动准备好”指示灯应闪光,按下“剪复位”按钮,剪刃复位。
(2)选择“手动”或“自动程序”速度模式,检查剪切超前系数设定。
(3)设定切头切尾长度、切头切尾时的超前率与滞后率,并选择切头、切尾、自动碎断启动在接通位置。
(4)按下“输入切头长度”按钮,如果该值被接受则按钮中的灯将闪光,如时计数器未准备好或最后输入的值不匹配则灯不亮。
(5)如果没有报警,则飞剪可以剪切工作。
(6)切头长度、剪切速度见下表:
10.存储轧制程序
贮存程序包括以下参数:
①产品规格、原料;
②程序存档的最后时间;
③成品轧机和成品速度;
④轧机配置情况,包括空过机架;
⑤每个机架的延伸系数;
⑥每个机架的冲击补偿系数;
⑦每个机架的辊缝;
⑧飞剪的超前系数。
对一个具体的轧制程序操作员可以检索、调用、修改、校对,满意后将该轧制程序传送给传动及控制系统。
控制系统对输入值进行极限检查,即对每个输入值进行判断,看其是否在极限范围内。
七、特殊操作
1.出现故障立即启动快速停车,紧急停车。
2.主传动合闸与分闸。
3.飞剪手动试验剪切。
4.手动切废。
5.速度设定的手动修正。