橡胶衬套试验
橡胶类材料试验项目及试验规范

•标准:GB 3512-83、DIN 53508和ISO 188
•试验规范:
(GB标准)1、温度:50、70、100、120、150、200、300℃
2、时间:24、48、72、96、144h或更长时间
3、温度稳定后,把试样呈自由状态悬挂在老化试验,每两个试样之间的距离不小于5mm,试样与箱壁之间的距离不小于70mm
橡胶类材料试验项目及试验规范
••我们现有标准中多部分用的是国标(GB标准),所以这次主要以GB为主。根据塑料的经验,发展方向是以ISO标准为主,可能橡胶也是以ISO标准为主,但是这并没有什么关系,就橡胶而言,不像塑料那样特别地强调试样或者实验方法的问题。
•就标准而言,DIN标准(德国标准)用得不是很多,而且一般情况下和GB、ISO标准通用。所以,这次以GB标准为主,DIN标准为辅,参考ISO标准。
(DIN标准)3、试样要求直径为30mm的圆片
4、在试样的三个不同位置测量厚度,测量部位之间的距离≥5mm,且离开试样的距离应≥13mm
•实验仪器:硬度计
•拉伸强度/断裂伸长率
•标准:GB/T 528-92、DIN 53504和ISO/DIS 37-1990
•试样规格及试验规范:
(GB标准)1、有四种样块尺寸,以总长分:115、75、35、50(mm),1、2、4型厚度2.0±0.2mm,3型厚度1.0±0.1mm
3、到达规定时间,从恒温箱中取出夹具或容器,在室温下冷却2h,然后打开容器、夹具,取出试样,在自由状态中停放1h
4、时间可选:24、48、72、96、120、144、168h;温度可选:70、85、100、125、150、175、200、225、250℃
(DIN标准)1、两种样块:A型:直径为13±0.5mm,高为6.3±0.3mm;B型:直径为29±0.5mm,高为12.5±0.3mm,如果没有特殊要求,一般使用A型,对应于定位器的高度分别为4.72±0.01mm,9.38±0.01mm
板簧橡胶复合衬套性能分析与实验研究

5
板簧分公司
三、改进方案——基本思路
鉴于该进口车型复合衬套与原设计图纸性能要求的巨大差距,经与整车厂 及衬套专业厂三方沟通,采取以下改进措施:
1、委托国内一流的为乘用车配套的橡胶衬套专业厂家进行CAE分析并提出橡胶 结构优化方案;
2、优选国产天然橡胶材料M170,通过调整橡胶基体配方改性来提升橡胶各向 刚度指标;
2、橡胶材料的型号及同一型号的配方调整对 衬套四个方向刚度和台架寿命影响较大;
3、橡胶硬度在HS60~70,衬套刚度特性及疲 劳寿命等综合性能较好。
15
板簧分公司
五、总结与建议
1、通过对不同型号的橡胶复合衬套反复试验表明:符合产品设计结构尺寸的复合 衬套,其刚度及疲劳寿命不一定合格; 2、通过对天然橡胶配方改性,适当增加橡胶内套与金属外套的过盈量,可获得橡 胶复合衬套较理想的刚度性能和疲劳寿命。建议橡胶硬度HS=60±3; 3、橡胶复合衬套各向刚度参数设计,不能单靠理论计算。建议通过CAE分析与实 测数据、台架试验相结合,科学确定衬套四个方向刚度参数,同时明确检测试验 方法和夹具,减小实验误差; 4、建议板簧厂家配备必要的衬套性能检测设备,重视橡胶复合衬套各方向刚度检 测及台架试验工作,加强对供方质保能力的审核管理。
多数衬套供应商和板簧生产厂缺乏刚度性能及台架寿命试验设备。四个方向刚度和台 架都能检测试验的厂家几乎没有,连社会权威检测机构检测设施也不齐全;
在对复合橡胶衬套进行四个方向刚度及台架寿命试验中,常有四个方向刚度部分不合 格、疲劳寿命不合格。反之,台架疲劳寿命达标,而四个方向刚度与设计性能曲线差 异较大;
16
板簧分公司
感谢大家聆听!
2014-8-19
3 9000 1.125 0.96-1.29 1.350
车用橡胶衬套的非线性有限元分析
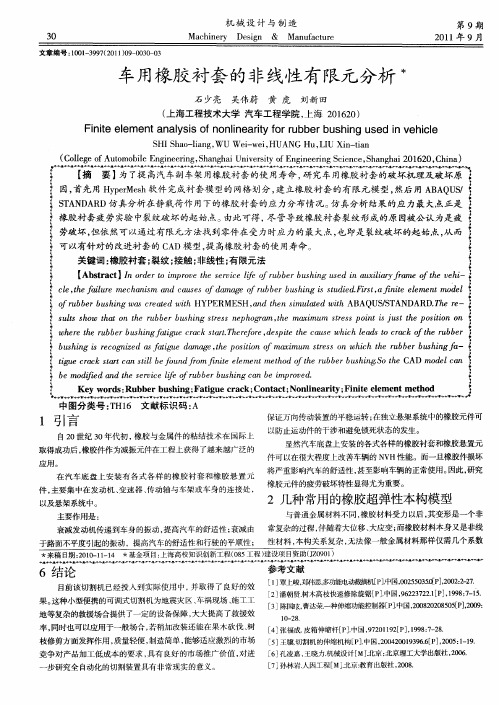
w eeh ubr uhnft e rc trTeeoedsi eC2ew ihl d rc h u br hr te be s i ai aks t hr r,ept t 0s hc asocako erbe r b g g c n a. f eh z e t ft
b hn eo n e f i edmaetep st no ai m s eso hc h u brb hn 一 s gs u i i rcg i d z t u a g a g , oio m xmu t s n w ihterb e u ig h i f r s t u rc t t a tl e o n fo fn eee n m to terb e uhn.oteC d l a i eca ks nsi f u d rm- i lm t eh do h u b r s ig ADm e n g r a c lb i t e f b S h o c b d e dte e i i em i da r c le对 rb e uhn a eipo e. o f i n h sv e f u b r sigcnb rvd b m
Ke y wor : ds Rub rbus ng; tg r c Con a t No lne iy; n t l m e e ho be hi Fa i ue c a k; t c ; n i art Fi ie ee ntm t d
中图分类 号 : H1 文 献标识 码 : T 6 A
t= ( , C1,o z 2Co o K o + ) =
1
设 () 1式中所有 =U )则得到减缩的多项式模型 : 0 ≠0 ,
uZ c(一 ) ∑ = 3+ ,。 。
/ =
( 川 ‘
汽车橡胶衬套试验台操作规程及注意事项

汽车橡胶衬套试验台操作规程及注意事项一、系统开机、关机:(— )开机:使用该设备前,首先控制柜上电,打开计算机后,进入该设备操作软件。
如果使用液压通道,打开“液压上电”钥匙开关,进入液压调试界面,然后启动泵站,调整压力,一般使用 10MPa,最后打开冷却水塔;如果使用旋转通道,打开伺服“上电”钥匙开关。
(二)关机:如果泵站已经启动,首先关闭液压缸进油阀门,然后将系统压力调到最小,然后关闭泵站,同时关闭冷却水塔。
最后退出系统,关闭计算机。
二、试件安装1、直线通道(1)根据试件型号,选择正确的夹具,然后将试件装入夹具中。
(2)在液压调试界面选择位控,将液压缸调到中位附近(远离缸底或缸头)。
(3)将试件及夹具与液压缸头法兰盘相连,穿入内六角螺栓并紧死。
(4)将丝杠锁紧。
(5)试件安装完毕后,在液压调试界面检查此时是否有预压(预拉)力,如果有调整液压缸位置将此力消除。
然后确认零位记录该点位移值(按钮为灰时不用确认零位),作为试件起始位置(6)开始试验。
2、旋转通道(1)根据试件型号,选择正确的夹具,然后将试件装入夹具中。
(2)根据试件旋转角度,调整摆杆相应偏向距(静态试验调整角度为试件加载角度的1.2 倍以上;疲劳试验调整为试件要求角度)。
(3)在伺服调试界面通过连续旋转检查正负旋转角度是否接近,偏差较大时通过自动回(4)零按钮自动调整角度零点,然后通过点动将角度调整为零。
(5)将试件及夹具与法兰盘相连,锁紧试件。
(6)试件安装完毕后,在伺服调试界面检查此时是否有预扭力,如果有通过扭矩扣零将此扭矩扣除。
然后确认零位记录该点角度值(按钮为灰时不用确认零位),作为试件起始角度。
(7)开始试验。
三、试验操作1、直线静态(1)根据试验要求输入相关试验设置,一般加载速度不超过 0.17mm/s,无特殊要求时预压模式选择单向预压,判载条件选择位移时设定位移报警上下限;否则设置载荷报警上下限。
试验结束后,在刚度曲线上选择两点(选定时双击鼠标左键),选择时以最接近曲线为准,以减小试验误差。
橡胶衬套静态特性计算测试相关性分析(final)

统计了衬套三向刚度的测试值与计算值。
衬套 A 的 X、Z 向测试值比计算值低 5%左右,Y 向持平,计算拟合效果良好。
衬套 B 三向刚度的测试 值均比计算值高约 13%,主要原因是该衬套采用模压较高的注橡模制作产品,产品硬
度高造成了刚度上升,但三向刚度比的吻合程度非常好。
衬套 C 的 Y、Z 向测试值比计算值高 8%,但三向刚度比仍控制在 6%之内。
Z
X
2.2 橡胶衬套样件与静态性能测试
图 2 参考坐标系的定义
为获得具统计意义的数据,对零件静态性能测试方法做了统一要求。测试设备为 MTS 833 三轴向试验台, 可利用同一套工装测试衬套三向静刚度曲线,如图 3 所示。
图 3 MTS 833 三轴向试验台 为保持测试数据的可靠性与一致性,在橡胶衬套样件制作与测试过程中进行如下定义:
由于橡胶是一种近似不可压缩材料,在隐式解法中橡胶单元类型通常选用 C3D8RH 和 C3D8H,而 C3D8H 有 更佳变 形能力,适合于计算大变形或接触分析。 这里网格类型采用 C3D8RH(一阶六面体减缩杂交单元)。
衬套线性静刚度是由主簧结构和橡胶类型决定的,因此在建模过程中仅对衬套主簧进行网格划分。考虑到衬 套内外 管均为金属结构,如铝合金、20#钢等,刚度远高于橡胶主簧,因此在 建模过程中 均刚性处理 。内 管与橡胶 主簧硫化结合处,用刚性单元将衬套弹性中心与之关联,作为激励加载端。外管与橡胶主簧硫化结合处,建立 6 自由度的约束。四种衬套结构的有限元网格模型如
样本 1 247.3
68.87
105.4 2.3463 0.6534
样本 2 244.1
69.34
102.8 2.3745 0.6745
样本 3 245.6
扭力梁悬架有限元模态分析中的橡胶衬套动刚度赋值方法
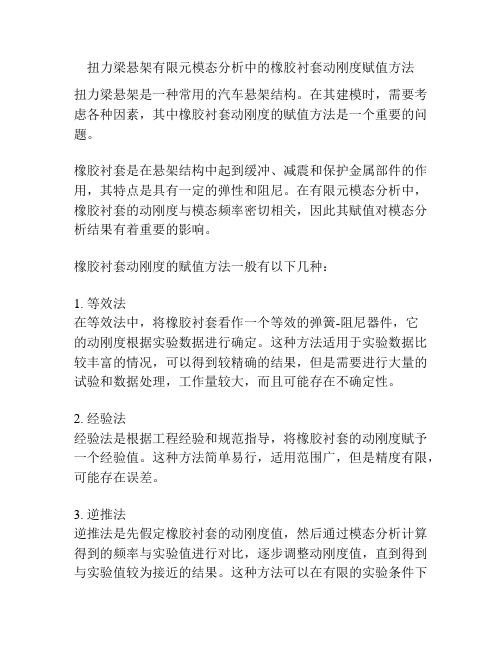
扭力梁悬架有限元模态分析中的橡胶衬套动刚度赋值方法扭力梁悬架是一种常用的汽车悬架结构。
在其建模时,需要考虑各种因素,其中橡胶衬套动刚度的赋值方法是一个重要的问题。
橡胶衬套是在悬架结构中起到缓冲、减震和保护金属部件的作用,其特点是具有一定的弹性和阻尼。
在有限元模态分析中,橡胶衬套的动刚度与模态频率密切相关,因此其赋值对模态分析结果有着重要的影响。
橡胶衬套动刚度的赋值方法一般有以下几种:1. 等效法在等效法中,将橡胶衬套看作一个等效的弹簧-阻尼器件,它的动刚度根据实验数据进行确定。
这种方法适用于实验数据比较丰富的情况,可以得到较精确的结果,但是需要进行大量的试验和数据处理,工作量较大,而且可能存在不确定性。
2. 经验法经验法是根据工程经验和规范指导,将橡胶衬套的动刚度赋予一个经验值。
这种方法简单易行,适用范围广,但是精度有限,可能存在误差。
3. 逆推法逆推法是先假定橡胶衬套的动刚度值,然后通过模态分析计算得到的频率与实验值进行对比,逐步调整动刚度值,直到得到与实验值较为接近的结果。
这种方法可以在有限的实验条件下得到较精确的结果,但是需要计算复杂,运算量大。
综合以上几种方法,可以得到一个相对合理的橡胶衬套动刚度赋值结果。
但需要特别注意的是,由于橡胶材料的本身特性和环境影响,其动刚度随时间和温度的变化非常复杂,因此在实际应用中需要进行实时监测和修正。
在进行扭力梁悬架有限元模态分析时,橡胶衬套动刚度赋值的合理性和准确性是关键。
因此,需要针对不同的具体情况,合理选择方法,进行模拟计算和实验验证,从而得到最优的结果。
在选择橡胶衬套动刚度赋值方法时,需要考虑多方面的因素,如橡胶材料的特性、汽车悬架的结构和工作条件、实验条件等。
以下是一些对橡胶衬套动刚度赋值方法的实践经验和建议。
首先,对于不同的橡胶材料,其动刚度的变化规律也不同。
一般来说,硬度越高的橡胶衬套动刚度越大,而阻尼值则与材料本身有关。
因此在进行动刚度赋值时需要考虑材料的硬度、阻尼和温度等因素。
板簧橡胶复合衬套性能分析与实验研究概述.

载荷
径向
N mm
N mm
0 0.88129
7455.31 1.18478
1085.04 0.92133
7887.38 1.18578
2222.86 0.9814
结构优化方案;
2、优选国产天然橡胶材料M170,通过调整橡胶基体配方改性来提升橡胶各向 刚度指标;
3、完备衬套扭转、偏摆两个方向刚度检测设备和专用夹具,统一试验标准和
方法 ; 4、通过四个方向性能试验和台架试验数据结果分析,确定最佳工艺方案指导 生产和交付。
板簧分公司
6
三、改进方案——CAE模拟分析
3023.07 1.2605 15700
7
板簧分公司
三、改进方案——CAE模拟分析
类型 项目 扭矩 扭转 转角 扭矩 转角 扭矩 转角 扭矩 偏摆 转角 扭矩 转角 扭矩 单位 N.m deg N.m deg N.m deg N.m deg N.m deg N.m 0.00 0.00 3.01 1.62 9.74 2.33 22.30 0.38 0.70 3.25 1.66 11.01 2.40 22.52 0.64 0.87 3.66 1.73 13.15 2.51 22.60 0.76 0.94 4.35 1.84 14.02 2.56 22.73 0.96 1.04 5.62 2.00 15.41 2.62 22.78 1.34 1.19 6.20 2.05 17.67 2.71 22.78 2.08 1.41 7.19 2.14 18.59 2.75 22.79 2.42 1.49 8.98 2.28 20.02 2.80 22.79 0.00 0 0.32 2 1.27 4 CAE分析数据 3.90 7 10.54 12 26.59 18 31.95 20
随机振动条件下的橡胶衬套疲劳寿命预测

随机振动条件下的橡胶衬套疲劳寿命预测随机振动下橡胶衬套的疲劳寿命预测是一项重要的工作,常常用于预测橡胶衬套在工作过程中所承受的振动力,以及其使用寿命。
在预测过程中需要考虑多种因素,包括材料本身的特性,使用条件以及应力情况等。
首先,橡胶衬套是由弹性材料制成,能够很好地吸收振动力,使得机械设备在运行时不会受到影响。
然而,在长时间的使用中,橡胶衬套会因为高强度的振动力而出现疲劳损伤,导致整个机械设备的失效。
因此,疲劳寿命预测对于预防这种损坏非常重要。
其次,在预测过程中需要考虑使用条件。
不同的机械设备在运行时所承受的振动力是不同的,因此需要考虑使用条件对于橡胶衬套的影响。
例如,若机械设备在高温环境下运行,橡胶衬套的使用寿命将会受到极大的影响。
因此,在进行预测时需要考虑使用条件对于疲劳寿命的影响。
最后,预测过程中需要考虑材料的特性以及应力情况等因素。
橡胶衬套的材料并不是完美的,会受到应力的影响而出现疲劳损伤。
因此,预测过程中需要考虑材料的韧性、硬度、抗拉强度等特性,以及在使用过程中出现的拉伸、压缩等应力情况。
在预测过程中,常常采用疲劳试验,通过将橡胶衬套置于振动台上进行震动测试,以模拟实际使用过程中所承受的振动力。
通过试验得到的数据,可以进行数据分析,以便预测橡胶衬套的疲劳寿命。
除了疲劳试验外,还可以采用有限元分析方法进行预测。
通过将橡胶衬套的几何设计与施加的振动力传递进行模拟,得出衬套内部应力分布情况,以预测橡胶衬套的疲劳寿命。
总的来说,随机振动下橡胶衬套的疲劳寿命预测是一项复杂的工作,需要综合考虑多种因素。
通过疲劳试验或有限元分析等方式,可以得出预测结果,并为后续的维护和保养提供有力的基础。
为确保橡胶衬套的工作寿命,需要将预测得出的疲劳寿命与实际使用寿命进行比较。
比较过程中,需要考虑不同因素的影响,例如使用条件、应力情况、环境温度等。
将预测结果与实际情况进行对比,可以发现有些橡胶衬套的使用寿命可能比预测结果更短,而有些则可能比预测结果更长。
减振器橡胶衬套的疲劳试验方法

减振器橡胶衬套的疲劳试验方法孙晓帮;孔令洋;王祥;石晶【摘要】减振器橡胶衬套的疲劳寿命不仅影响其使用寿命,而且影响到悬架的行驶安全性.根据减振器橡胶衬套的实际使用工况,对独立减振器和减振器支柱总成橡胶衬套进行受力分析,确定了橡胶衬套疲劳试验条件中的预压力、激振力幅值、振动频率和激振次数.根据橡胶衬套静刚度的损失率、激振位移的增大率、表观的变化、龟裂值和材料的温升,确立了橡胶衬套疲劳失效的判断准则,为橡胶衬套疲劳试验提供依据.【期刊名称】《汽车工程师》【年(卷),期】2015(000)005【总页数】3页(P52-54)【关键词】减振器橡胶衬套;受力分析;疲劳试验条件;疲劳失效【作者】孙晓帮;孔令洋;王祥;石晶【作者单位】辽宁工业大学汽车与交通工程学院;辽宁工业大学汽车与交通工程学院;辽宁工业大学汽车与交通工程学院;辽宁工业大学汽车与交通工程学院【正文语种】中文减振器橡胶衬套(以下简称橡胶衬套)因具有良好的吸收高频振动和隔振效果,被广泛应用在汽车悬架系统中[1]。
汽车行驶时,橡胶衬套受路面的激励作用处于交变载荷下,因此很容易发生疲劳失效。
通过试验方法研究橡胶衬套的疲劳寿命不仅能提高其使用寿命,而且能提高悬架的行驶安全性。
目前国内外没有完整的汽车悬架橡胶衬套试验标准,各厂家试验规范也不统一。
文章通过橡胶衬套受力分析,建立橡胶衬套的疲劳试验规范,并确立橡胶衬套疲劳失效的判断准则。
1 橡胶衬套的受力分析1.1 独立减振器橡胶衬套受力分析独立减振器是指减振器与弹簧独立安装。
装有橡胶衬套的独立减振器一般有双吊环式和下吊环式2种。
双吊环式减振器结构简图,如图1所示。
在实车使用工况下,减振器上吊环(内含橡胶衬套)与车架或车身相连,下吊环(内含橡胶衬套)与车桥相连。
橡胶衬套外圆柱表面与减振器上下吊环之间为过盈配合;橡胶衬套芯部是与橡胶粘接的刚性套筒,销轴穿过套筒内部将减振器一端与车架或悬架系统托臂梁柔性连接在一起。
汽车橡胶衬套随机疲劳分析
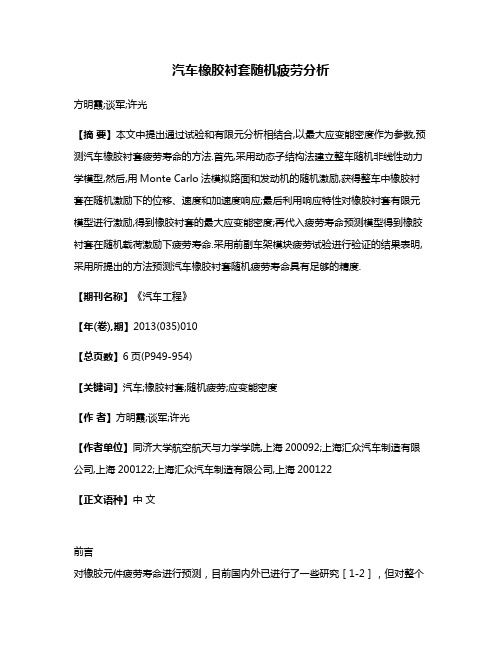
汽车橡胶衬套随机疲劳分析方明霞;谈军;许光【摘要】本文中提出通过试验和有限元分析相结合,以最大应变能密度作为参数,预测汽车橡胶衬套疲劳寿命的方法.首先,采用动态子结构法建立整车随机非线性动力学模型,然后,用Monte Carlo法模拟路面和发动机的随机激励,获得整车中橡胶衬套在随机激励下的位移、速度和加速度响应;最后利用响应特性对橡胶衬套有限元模型进行激励,得到橡胶衬套的最大应变能密度;再代入疲劳寿命预测模型得到橡胶衬套在随机载荷激励下疲劳寿命.采用前副车架模块疲劳试验进行验证的结果表明,采用所提出的方法预测汽车橡胶衬套随机疲劳寿命具有足够的精度.【期刊名称】《汽车工程》【年(卷),期】2013(035)010【总页数】6页(P949-954)【关键词】汽车;橡胶衬套;随机疲劳;应变能密度【作者】方明霞;谈军;许光【作者单位】同济大学航空航天与力学学院,上海200092;上海汇众汽车制造有限公司,上海200122;上海汇众汽车制造有限公司,上海200122【正文语种】中文前言对橡胶元件疲劳寿命进行预测,目前国内外已进行了一些研究[1-2],但对整个系统中橡胶元件疲劳寿命进行研究目前主要依赖于试验。
国外对橡胶减振元件的疲劳试验已采用随机载荷谱或道路谱加载[3-4]。
文献[5]中对机车车辆用橡胶件的寿命进行了研究,以高速转向架转向装置的导向套为例,采用将道路谱信号编辑处理后变换成试验台的控制信号,对车辆用橡胶件进行寿命测试。
文献[6]中对车辆的减振部件空气弹簧的使用寿命进行了研究,通过对气囊橡胶试片的人工加速老化试验,可靠地评价了其使用寿命。
目前国内对橡胶减振元件的疲劳问题研究仍处于起步阶段,文献[7]中对大型履带式拖拉机链轮橡胶减振器疲劳试验程序载荷谱进行了分析;文献[8]中对橡胶减振器疲劳寿命与模具设计的关系进行了研究。
负荷测试和道路模拟试验等虽然在疲劳寿命准确估算中具有一定优势,但却不能在橡胶材料设计阶段进行分析。