铸铁件磷化的处理工艺(汉高)
铁的磷化处理工艺流程

铁的磷化处理工艺流程一、引言铁的磷化处理是一种常见的表面处理方法,通过在铁材料表面形成一层磷化物膜,可以提高铁材料的耐腐蚀性能和机械性能。
本文将介绍铁的磷化处理的工艺流程。
二、前处理1. 清洗:首先,将待处理的铁材料进行清洗,去除表面的油污、灰尘等杂质。
可以使用溶剂或碱性清洗剂进行清洗,确保表面干净。
2. 酸洗:清洗后,将铁材料进行酸洗处理。
酸洗可以去除铁材料表面的氧化层和锈蚀物,提供一个干净的表面供磷化处理。
三、磷化处理1. 磷化液配制:根据具体的磷化要求,配制磷化液。
磷化液的主要成分包括磷酸盐、酸类、缓蚀剂等。
不同的磷化液配方可以得到不同性能的磷化膜。
2. 磷化处理:将清洗后的铁材料浸入磷化液中,进行磷化处理。
磷化液中的磷酸盐会与铁材料表面的铁离子反应,形成磷化膜。
磷化时间和温度可以根据具体要求进行控制。
3. 中和处理:磷化处理后,将铁材料从磷化液中取出,进行中和处理。
中和处理可以使用碱性溶液,将磷化液中的酸性物质中和掉,以防止对环境造成污染。
四、后处理1. 清洗:磷化处理后,将铁材料进行清洗,去除残留的磷化液和中和剂。
清洗可以使用水或溶剂进行。
2. 干燥:清洗后,将铁材料进行干燥处理。
可以使用热风或其他干燥设备,确保铁材料表面干燥。
3. 表面处理:根据具体要求,可以对磷化后的铁材料进行表面处理。
例如,可以进行涂层、喷漆等工艺,以增加铁材料的美观性和耐久性。
五、质量检验经过磷化处理的铁材料需要进行质量检验,以确保磷化膜的质量符合要求。
常用的检验方法包括厚度测量、耐蚀性测试等。
六、结论铁的磷化处理工艺流程包括前处理、磷化处理、后处理和质量检验等步骤。
通过这些步骤,可以在铁材料表面形成一层磷化膜,提高铁材料的性能和耐久性。
在实际应用中,可以根据具体要求进行工艺参数的调整,以获得理想的磷化效果。
金属表面除油工艺过程-磷化
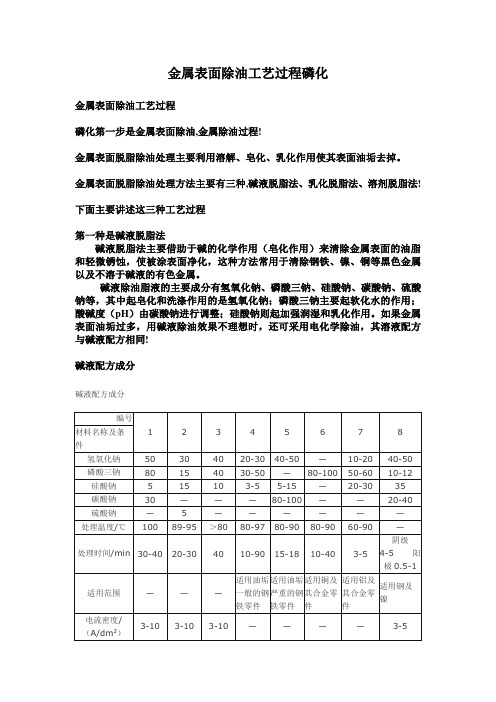
金属表面除油工艺过程磷化金属表面除油工艺过程磷化第一步是金属表面除油,金属除油过程!金属表面脱脂除油处理主要利用溶解、皂化、乳化作用使其表面油垢去掉。
金属表面脱脂除油处理方法主要有三种,碱液脱脂法、乳化脱脂法、溶剂脱脂法!下面主要讲述这三种工艺过程第一种是碱液脱脂法碱液脱脂法主要借助于碱的化学作用(皂化作用)来清除金属表面的油脂和轻微锈蚀,使被涂表面净化,这种方法常用于清除钢铁、镍、铜等黑色金属以及不溶于碱液的有色金属。
碱液除油脂液的主要成分有氢氧化钠、磷酸三钠、硅酸钠、碳酸钠、硫酸钠等,其中起皂化和洗涤作用的是氢氧化钠;磷酸三钠主要起软化水的作用;酸碱度(pH)由碳酸钠进行调整;硅酸钠则起加强润湿和乳化作用。
如果金属表面油垢过多,用碱液除油效果不理想时,还可采用电化学除油,其溶液配方与碱液配方相同!碱液配方成分碱液配方成分碱液脱脂过程的主要方法(1)浸渍法(煮沸法)这种方法是把被清洗物件置于加热的碱清洗液中煮沸而除油脱脂的方法。
为了加速其除油脱脂乳化作用,在浸煮的同时,应该给予充分搅拌或振动等机械作用,以便提高净化质量。
(2)喷射法它适用大量生产和流水线生产,主要是把碱清洗液喷射到置于传送带上的被清洗零件面上,达到除油脂的目的。
(3)电解法这是把浸入碱清洗液中的零件通电电解产生的气体,经物理作用而清除零件表面上的油垢。
(4)旋转法这种方法是把被清洗零件置于碱清洗液的容器中,然后旋转以清除零件表面油垢,一般适用于小件和多油污的零件。
(二)乳化脱脂法这种方法是利用能促使两种互不相溶的液体(如油和水),形成稳定的乳浊液的物质(乳化剂),即在有机溶剂中加入一种或数种表面活性剂,也可添加弱碱性洗净剂组成的混合液,将这种乳浊液浸渍或喷射到被清洗的零件表面上时,浸透油脂层后使油脂微粒化,表面活性剂使油脂微粒乳化分散在水中,从而达到除掉油脂的目的。
乳化洗净液是由有机溶剂和表面活性剂组成的,这种洗净液对湿度反应不大,在室温条件下就可以进行,其特点是无毒,除油效果比碱液高(因为有些水溶性污物在水中就被溶解了),故获得广泛应用。
铸铁产品磷化操作规程

4、喷砂后用清洁的料架运输工件,以免工件沾油。
五、检验要求
1、工件磷化表面形成保护膜,大体均匀致密;
2、工件整体呈灰黑色,无裸露金属面;
3、无锈迹、褐斑等缺陷。编制Fra bibliotek校对审核
批准
标记
处数
更改文件号
签名
日期
3、将清洗的产品放入磷化液(加热后)中,全部浸没,15—20分钟后拿出。
4、再将拿出的产品放入热水中浸泡片刻(10秒钟左右)后取出控干。
5、涂油:将磷化后的产品按“磷化后处理作业指导书”要求浸防锈油
四、注意:
1、磷化液温度保持在60°C—70°C;
2、泵类产品必须立放于酸液及磷化液中,不允许平放,以免内腔及中的残液无法控出。
3、酸洗槽内按1:4(体积比)的比例配好盐酸溶液。
4、清水池加注适量的常温水。
5、热水槽加注适量清水,并加热至75°C以上(越热越好)。
6、准备防锈油,以便磷化后涂油。
三、操作:
1、将产品立着放入磷化筐内,要求摆放整齐,放入酸洗槽内浸泡15~20分钟,并在出料时上下移动料筐5次。
2、将酸洗后的产品放入常温水中上下移动6~10次,清洗掉污渍、盐酸残液后吊出控干。该清水池中的每天至少更换一次。
产品型号
济南汇九泵业有限公司
版次
共1页
各种泵类铸铁产品
01/00
第1页
铸铁产品磷化操作规程
一、主题概述
1、磷化目的:在工件表面形成致密的保护膜,达到防锈、防腐蚀的目的。
2、磷化所需设备和材料:加热装置、磷化液(中温锌钙系)、清水。
二、准备:
1、领取检验合格的泵类铸铁产品(前、后盖、泵体、泵盖等)。
磷化前的预处理和两种常用磷化工艺
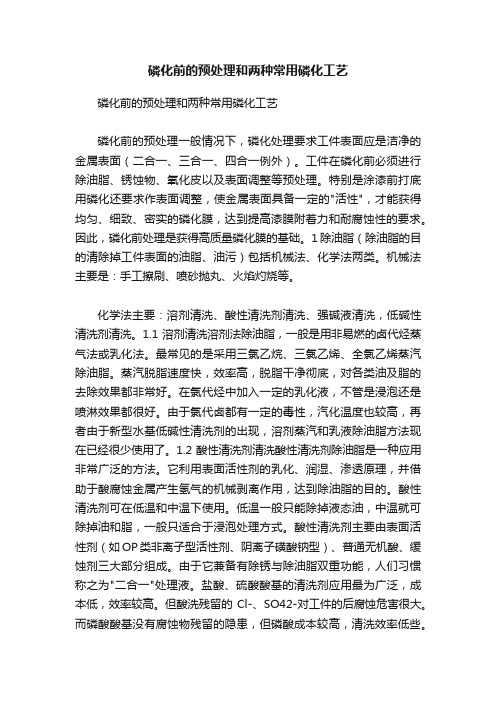
磷化前的预处理和两种常用磷化工艺磷化前的预处理和两种常用磷化工艺磷化前的预处理一般情况下,磷化处理要求工件表面应是洁净的金属表面(二合一、三合一、四合一例外)。
工件在磷化前必须进行除油脂、锈蚀物、氧化皮以及表面调整等预处理。
特别是涂漆前打底用磷化还要求作表面调整,使金属表面具备一定的"活性",才能获得均匀、细致、密实的磷化膜,达到提高漆膜附着力和耐腐蚀性的要求。
因此,磷化前处理是获得高质量磷化膜的基础。
1除油脂(除油脂的目的清除掉工件表面的油脂、油污)包括机械法、化学法两类。
机械法主要是:手工擦刷、喷砂抛丸、火焰灼烧等。
化学法主要:溶剂清洗、酸性清洗剂清洗、强碱液清洗,低碱性清洗剂清洗。
1.1溶剂清洗溶剂法除油脂,一般是用非易燃的卤代烃蒸气法或乳化法。
最常见的是采用三氯乙烷、三氯乙烯、全氯乙烯蒸汽除油脂。
蒸汽脱脂速度快,效率高,脱脂干净彻底,对各类油及脂的去除效果都非常好。
在氯代烃中加入一定的乳化液,不管是浸泡还是喷淋效果都很好。
由于氯代卤都有一定的毒性,汽化温度也较高,再者由于新型水基低碱性清洗剂的出现,溶剂蒸汽和乳液除油脂方法现在已经很少使用了。
1.2酸性清洗剂清洗酸性清洗剂除油脂是一种应用非常广泛的方法。
它利用表面活性剂的乳化、润湿、渗透原理,并借助于酸腐蚀金属产生氢气的机械剥离作用,达到除油脂的目的。
酸性清洗剂可在低温和中温下使用。
低温一般只能除掉液态油,中温就可除掉油和脂,一般只适合于浸泡处理方式。
酸性清洗剂主要由表面活性剂(如OP类非离子型活性剂、阴离子磺酸钠型)、普通无机酸、缓蚀剂三大部分组成。
由于它兼备有除锈与除油脂双重功能,人们习惯称之为"二合一"处理液。
盐酸、硫酸酸基的清洗剂应用最为广泛,成本低,效率较高。
但酸洗残留的Cl-、SO42-对工件的后腐蚀危害很大。
而磷酸酸基没有腐蚀物残留的隐患,但磷酸成本较高,清洗效率低些。
对于锌件,铝件一般不采用酸性清洗剂清洗,特别锌件在酸中的腐蚀极快。
磷化处理工艺流程 磷化常见问题及处理方法

磷化处理工艺流程磷化常见问题及处理方法磷化处理磷化处理是一种化学反应,在表面形成一层膜(磷化膜)的一种表面处理工艺。
磷化处理工艺主要用在金属表面,目的也是为金属表面提供一层保护膜,让金属与空气隔绝,防止其被腐蚀;还会用于一些产品涂漆之前的打底,有了这层磷化膜能够提高漆层的附着力和防腐蚀能力,提高装饰性让金属表面看起来更漂亮,并且还能够在部分金属冷加工过程中起到润滑的作用。
经过磷化处理后能让工件在很长时间内不会氧化生锈,所以磷化处理的应用非常广泛,也是常用的一种金属表面处理工艺,在汽车,船舶,机械制造等行业中应用越来越多。
但磷化处理也有着溶液沉渣多,表面粗糙,磷化温度较高,时间长以及成本较高的缺点。
磷化的发展历史其实磷化处理工艺发展至今已经有很长时间了,它应该是现代金属表面处理中,发明时间较早的一种,其发展也经过了不同的时期。
在1869年的英国,有人就发现了磷化膜可以用在金属表面,能有效的保护金属长时间不被腐蚀,并且当时还将其申请了专利,这也为磷化处理的技术和发展奠定了基础。
从20世纪初开始,磷化处理开始用在工业产品中,这也促进了磷化工艺的发展和进步,从此磷化处理得到了快速的发展和进入实际应用时期。
到了现代,为了适应各种需求,磷化处理工艺也在不断的改进,主要是向着低温,低渣,环保无毒的方向发展。
磷化的分类及应用通常情况下,一种表面处理后都是呈现出一种颜色,但是磷化处理可以根据实际需求,通过使用不同的磷化剂就会呈现不同的颜色,这也就是我们经常会看到磷化处理有灰色,彩色或者是黑色。
铁系磷化磷化后表面会呈现出彩虹色以及蓝色,所以又被称为彩磷,磷化液主要以铝酸盐为原料,会在钢铁材料表面形成彩虹色的磷化膜,也主要是用于涂装底层,以达到工件的防腐蚀能力和提高表面涂层的结合力。
锌系磷化颜色呈灰色,所以被称为灰膜磷化,主要使用的磷化液由磷酸,氟化钠以及乳化剂等组成,会在工件表面形成灰色的磷化膜,它主要也是为涂装底层,与后道的喷塑,喷漆或者电泳等工序进行结合。
磷化处理工艺流程

磷化处理工艺流程
《磷化处理工艺流程》
磷化处理是一种常见的金属表面防腐处理方法,适用于各种金属材料,尤其是钢铁制品。
通过磷化处理,可以形成一层均匀、致密的磷化膜,保护金属表面免受腐蚀和氧化,从而延长金属制品的使用寿命。
下面将介绍磷化处理的工艺流程。
首先,进行表面预处理。
包括去油、脱垢和除锈等步骤,以确保金属表面光洁、干净。
这一步骤对后续的磷化处理非常重要,因为表面的油污、污垢和锈斑会影响磷化膜的形成和质量。
接着,进行磷化处理。
将经过表面预处理的金属制品浸入磷化液中,通过化学反应形成磷化膜。
磷化液通常由磷酸盐、氯化物和激发剂等物质组成,根据不同的金属材料和要求,磷化液的配方也有所不同。
然后,进行水洗和中和处理。
将磷化处理后的金属制品进行水洗,去除残留的磷化液和杂质。
随后进行中和处理,以中和磷化液中的残余酸碱物质,防止对环境造成污染。
最后,进行干燥和涂油处理。
将经过磷化处理的金属制品进行干燥,去除水分。
然后进行涂油处理,将表面覆盖一层防腐蚀的油漆或蜡质,增强抗腐蚀性能。
总的来说,磷化处理工艺流程包括表面预处理、磷化处理、水洗和中和处理、干燥和涂油处理等步骤,通过这些步骤可以形
成均匀、致密的磷化膜,保护金属制品的表面免受腐蚀。
磷化处理不仅提高了金属制品的使用寿命,也对环境友好,是一种常用的金属表面处理方法。
板件表面预处理之磷化处理

板件表面预处理之磷化处理磷化处理钢铁在含有锌、铁、锰的磷酸盐溶液中,由于金属和溶液的界面上发生化学反应,生成难溶于水的磷酸盐,使钢铁表面形成一层附着良好的保护膜,这种方法称为钢铁磷化。
实现磷化的较常用的方法有浸渍法、喷淋法和涂刷法。
1)浸渍法按工艺流程,将工件顺序地浸入磷化液槽中进行处理。
大件可用吊挂方式,小件用篮框盛装,或用滚筒方式磷化。
设备简单,操作方便,处理温度可以较高。
2)喷淋法按工艺流程,将工件传递到处理工位,在规定时间内,经受磷化液喷淋处理。
设备较复杂,但与浸渍法比较,磷化液浓度可以较低,磷化时间较短。
3)涂刷法用刷子把磷化液涂刷到工件上进行处理,方法最简单,但劳动强度较大。
钢铁工件漆前磷化处理一般工艺
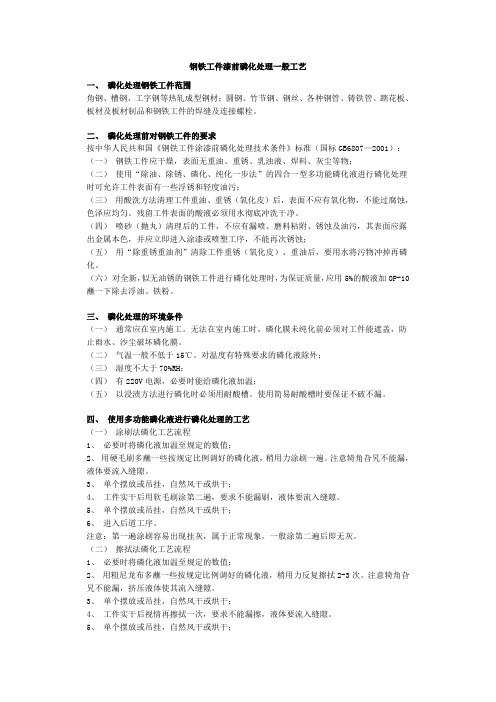
钢铁工件漆前磷化处理一般工艺一、磷化处理钢铁工件范围角钢、槽钢、工字钢等热轧成型钢材;圆钢、竹节钢、钢丝、各种钢管、铸铁管、踏花板、板材及板材制品和钢铁工件的焊缝及连接螺栓。
二、磷化处理前对钢铁工件的要求按中华人民共和国《钢铁工件涂漆前磷化处理技术条件》标准(国标GB6807—2001):(一)钢铁工件应干燥,表面无重油、重锈、乳浊液、焊料、灰尘等物;(二)使用“除油、除锈、磷化、纯化一步法”的四合一型多功能磷化液进行磷化处理时可允许工件表面有一些浮锈和轻度油污;(三)用酸洗方法清理工件重油、重锈(氧化皮)后,表面不应有氧化物,不能过腐蚀,色泽应均匀。
残留工件表面的酸液必须用水彻底冲洗干净。
(四)喷砂(抛丸)清理后的工件,不应有漏喷、磨料粘附、锈蚀及油污,其表面应露出金属本色,并应立即进入涂漆或喷塑工序,不能再次锈蚀;(五)用“除重锈重油剂”清除工件重锈(氧化皮)、重油后,要用水将污物冲掉再磷化。
(六)对全新,似无油锈的钢铁工件进行磷化处理时,为保证质量,应用5%的酸液加OP-10蘸一下除去浮油、铁粉。
三、磷化处理的环境条件(一)通常应在室内施工。
无法在室内施工时,磷化膜未纯化前必须对工件能遮盖,防止雨水、沙尘破坏磷化膜。
(二)气温一般不低于15℃。
对温度有特殊要求的磷化液除外;(三)湿度不大于70%RH;(四)有220V电源,必要时能给磷化液加温;(五)以浸渍方法进行磷化时必须用耐酸槽。
使用简易耐酸槽时要保证不破不漏。
四、使用多功能磷化液进行磷化处理的工艺(一)涂刷法磷化工艺流程1、必要时将磷化液加温至规定的数值;2、用硬毛刷多蘸一些按规定比例调好的磷化液,稍用力涂刷一遍。
注意犄角旮旯不能漏,液体要流入缝隙。
3、单个摆放或吊挂,自然风干或烘干;4、工件实干后用软毛刷涂第二遍,要求不能漏刷,液体要流入缝隙。
5、单个摆放或吊挂,自然风干或烘干;6、进入后道工序。
注意:第一遍涂刷容易出现挂灰,属于正常现象。
钢铁磷化工艺
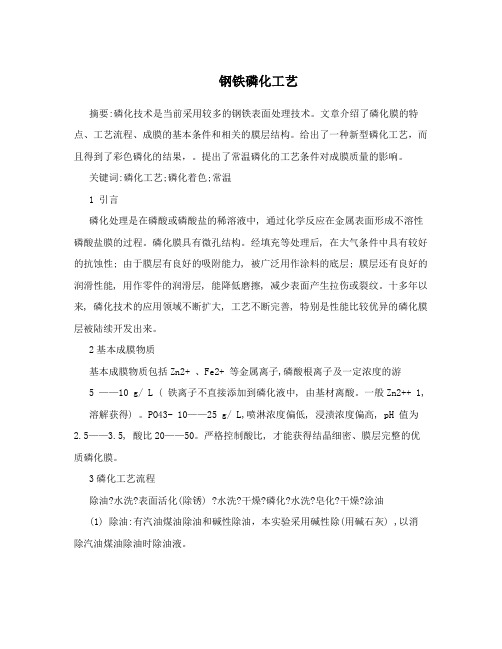
钢铁磷化工艺摘要:磷化技术是当前采用较多的钢铁表面处理技术。
文章介绍了磷化膜的特点、工艺流程、成膜的基本条件和相关的膜层结构。
给出了一种新型磷化工艺,而且得到了彩色磷化的结果,。
提出了常温磷化的工艺条件对成膜质量的影响。
关键词:磷化工艺;磷化着色;常温1 引言磷化处理是在磷酸或磷酸盐的稀溶液中, 通过化学反应在金属表面形成不溶性磷酸盐膜的过程。
磷化膜具有微孔结构。
经填充等处理后, 在大气条件中具有较好的抗蚀性; 由于膜层有良好的吸附能力, 被广泛用作涂料的底层; 膜层还有良好的润滑性能, 用作零件的润滑层, 能降低磨擦, 减少表面产生拉伤或裂纹。
十多年以来, 磷化技术的应用领域不断扩大, 工艺不断完善, 特别是性能比较优异的磷化膜层被陆续开发出来。
2基本成膜物质基本成膜物质包括Zn2+ 、Fe2+ 等金属离子,磷酸根离子及一定浓度的游5 ——10 g/ L ( 铁离子不直接添加到磷化液中, 由基材离酸。
一般Zn2++ 1,溶解获得) 。
PO43- 10——25 g/ L,喷淋浓度偏低, 浸渍浓度偏高, pH 值为2.5——3.5, 酸比20——50。
严格控制酸比, 才能获得结晶细密、膜层完整的优质磷化膜。
3磷化工艺流程除油?水洗?表面活化(除锈) ?水洗?干燥?磷化?水洗?皂化?干燥?涂油(1) 除油:有汽油煤油除油和碱性除油,本实验采用碱性除(用碱石灰) ,以消除汽油煤油除油时除油液。
进入工件沙眼中难以清洗干净(易在磷化膜中产生白色或黄色斑点) 的缺点,但碱性除油可使工件表面钝化。
(2) 表面除锈及活化:用1?4 的HCL 除锈并活化,消除碱性除油对工件表面的钝化,以利于成膜。
(3) 磷化:采用浸入式,有利于工件表面成膜均匀致密。
(4) 皂化:磷化后工件表面呈酸性,经皂化(肥皂液) 后,可消除酸性影响,加固磷化膜牢度。
(5) 涂油:用70 # 机油,常温浸渍5min 左右,磷化膜颜色会进一步加深,由原来黑灰色变为黑亮色,外观效果好,对膜层质量起到保护作用。
铸铁件黑色磷化工艺流程
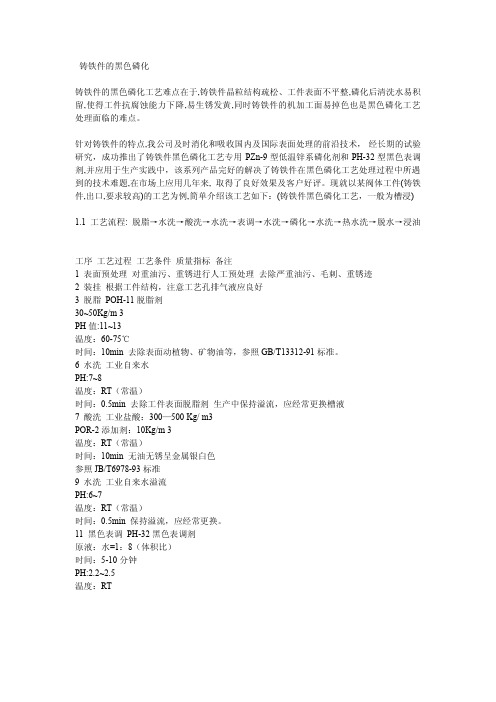
铸铁件的黑色磷化铸铁件的黑色磷化工艺难点在于,铸铁件晶粒结构疏松、工件表面不平整,磷化后清洗水易积留,使得工件抗腐蚀能力下降,易生锈发黄,同时铸铁件的机加工面易掉色也是黑色磷化工艺处理面临的难点。
针对铸铁件的特点,我公司及时消化和吸收国内及国际表面处理的前沿技术,经长期的试验研究,成功推出了铸铁件黑色磷化工艺专用PZn-9型低温锌系磷化剂和PH-32型黑色表调剂,并应用于生产实践中,该系列产品完好的解决了铸铁件在黑色磷化工艺处理过程中所遇到的技术难题,在市场上应用几年来,取得了良好效果及客户好评。
现就以某阀体工件(铸铁件,出口,要求较高)的工艺为例,简单介绍该工艺如下:(铸铁件黑色磷化工艺,一般为槽浸)1.1工艺流程:脱脂→水洗→酸洗→水洗→表调→水洗→磷化→水洗→热水洗→脱水→浸油工序工艺过程工艺条件质量指标备注1表面预处理对重油污、重锈进行人工预处理去除严重油污、毛刺、重锈迹2装挂根据工件结构,注意工艺孔排气液应良好3脱脂POH-11脱脂剂30~50Kg/m3PH值:11~13温度:60-75℃时间:10min去除表面动植物、矿物油等,参照GB/T13312-91标准。
6水洗工业自来水PH:7~8温度:RT(常温)时间:0.5min去除工件表面脱脂剂生产中保持溢流,应经常更换槽液7酸洗工业盐酸:300—500Kg/m3POR-2添加剂:10Kg/m3温度:RT(常温)时间:10min无油无锈呈金属银白色参照JB/T6978-93标准9水洗工业自来水溢流PH:6~7温度:RT(常温)时间:0.5min保持溢流,应经常更换。
11黑色表调PH-32黑色表调剂原液:水=1:8(体积比)时间:5-10分钟PH:2.2~2.5温度:RT12水洗工业自来水溢流PH:6~7温度:RT(常温)时间:0.5min13磷化PZn-9磷化剂:100Kg/M3总酸度(TA):25-30Pt游离酸(FA):2.0-3.0温度:40-45℃时间:15minPH:2.2-2.5参照GB11376-89标准经常清理残渣控制好工艺参数14水洗工业自来水溢流PH:6~7温度:RT(常温)时间:0.5~1min清洗工件表面带出磷化液保持溢流,应经常更换15热水洗工业自来水PH:6~7温度:60-70℃时间:0.5~1min脱水清洗,热封闭经常更换16脱水PDO-2脱水防锈油温度:RT(常温)时间:20-30Min油水分离17浸油PSO-2超薄层防锈油温度:RT(常温)时间:20-30Min此工艺的关键应控制脱脂、表调和磷化工序技术参数1.2脱脂,是涂装前处理工艺的第一步,它要求把附着在铸铁工件表面的防锈油、润滑油、灰尘及与金属工件接触、机加工时留下的油污等污垢彻底去除。
标准件磷化处理工艺流程

标准件磷化处理工艺流程:
除油→水洗→除锈→水洗→表调→磷化→水洗→水洗→烘干(或直接电泳)→喷涂→后处理。
①前处理的除油、除锈要彻底。
②表调剂的配制为2-4g/l,ph值9-10,溶液呈乳白混浊态。
可按每天添加10%表调剂进行调整,也可按具体情况操作,如表调液或透明状则视为失效。
工件表调后,可直接进入到磷化槽中磷化处理。
③磷化膜均匀、致密,灰色膜或灰色带浅金黄彩色膜。
处理的时间可随温度的升高而缩短,以达到工件磷化要求为准。
④阴极电泳时,磷化后经水洗,再用去离子水清洗后,直接进入电泳槽;
⑤当工件需进行喷粉或喷漆时,磷化、清洗后,需烘干后,再进行后续工序。
钢铁的磷化处理注意事项
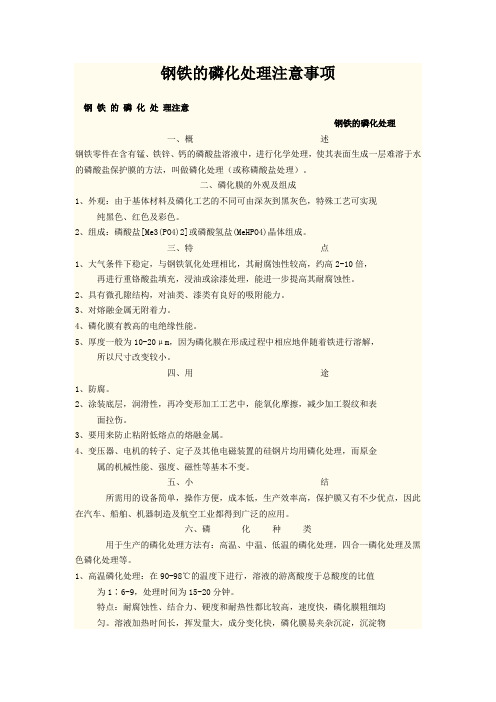
钢铁的磷化处理注意事项钢铁的磷化处理注意钢铁的磷化处理一、概述钢铁零件在含有锰、铁锌、钙的磷酸盐溶液中,进行化学处理,使其表面生成一层难溶于水的磷酸盐保护膜的方法,叫做磷化处理(或称磷酸盐处理)。
二、磷化膜的外观及组成1、外观:由于基体材料及磷化工艺的不同可由深灰到黑灰色,特殊工艺可实现纯黑色、红色及彩色。
2、组成:磷酸盐[Me3(PO4)2]或磷酸氢盐(MeHPO4)晶体组成。
三、特点1、大气条件下稳定,与钢铁氧化处理相比,其耐腐蚀性较高,约高2-10倍,再进行重铬酸盐填充,浸油或涂漆处理,能进一步提高其耐腐蚀性。
2、具有微孔隙结构,对油类、漆类有良好的吸附能力。
3、对熔融金属无附着力。
4、磷化膜有教高的电绝缘性能。
5、厚度一般为10-20μm,因为磷化膜在形成过程中相应地伴随着铁进行溶解,所以尺寸改变较小。
四、用途1、防腐。
2、涂装底层,润滑性,再冷变形加工工艺中,能氧化摩擦,减少加工裂纹和表面拉伤。
3、要用来防止粘附低熔点的熔融金属。
4、变压器、电机的转子、定子及其他电磁装置的硅钢片均用磷化处理,而原金属的机械性能、强度、磁性等基本不变。
五、小结所需用的设备简单,操作方便,成本低,生产效率高,保护膜又有不少优点,因此在汽车、船舶、机器制造及航空工业都得到广泛的应用。
六、磷化种类用于生产的磷化处理方法有:高温、中温、低温的磷化处理,四合一磷化处理及黑色磷化处理等。
1、高温磷化处理:在90-98℃的温度下进行,溶液的游离酸度于总酸度的比值为1∶6-9,处理时间为15-20分钟。
特点:耐腐蚀性、结合力、硬度和耐热性都比较高,速度快,磷化膜粗细均匀。
溶液加热时间长,挥发量大,成分变化快,磷化膜易夹杂沉淀,沉淀物难清理。
2、中温磷化处理:在60-70℃的温度下进行。
溶液游离酸度与总酸度比值为1∶(10-15),处理时间为7-15分钟。
特点:溶液稳定,磷化速度快,生产效率高,溶液成分复杂,难配制。
3、常温磷化处理:在室温下进行,溶液的游离酸度与总酸度的比值为1∶(20-30),处理时间为10-15分钟。
CH_铸铁件磷化工艺的研究

氧溶液中,p H值对价态无影响,皆为正三价;如果溶液中含氧,溶液中三价Ce被氧化成四价。
金属表面微阴极区附近溶液碱性增强,导致在这些部位稀土及镁的氧化物/氢氧化物沉积形成稀土转化膜。
由于金属浸入稀土盐溶液初期反应非常剧烈,转化膜形成速率快,因此,电极电位迅速升高。
当电极表面被一层稀土转化膜完全覆盖后,膜的生长速率受到抑制而明显减缓。
3 结论(1)当稀土盐的质量浓度不断增加,三价铈的质量浓度增大,与氢氧根离子结合机会也随之增大,沉积时产生的氢氧化铈会迅速覆盖在合金表面。
因此,膜的耐蚀性随着三价铈的质量浓度增加而逐渐增强。
本实验确定硝酸铈的质量浓度为21.7g/L。
(2)对于在单稀土铈盐溶液中成膜,加热条件下获得了耐蚀性更好的膜。
实验确定温度为40℃。
(3)膜层厚度并不随着成膜时间的延长而增厚,而存在一个合适的时间段。
超过这段时间,膜厚不再增加;相反,长时间浸泡则会对已形成的膜层有影响。
在不同的稀土盐溶液中成膜,单稀土硝酸铈溶液中最佳成膜时间为6min。
参考文献:[1] 许 越,陈 湘,吕祖舜,等.AZ91镁合金稀土转化膜的制备及耐蚀性能研究[J].中国稀土学报,2005,23(1):40243.[2] Amy L Rudd,Carmel B Breslin,Florian Mansfeld.Thecorrosion protection afforded by rare eart h conversion coatings applied to magnesium[J].Corrosion Science,2000,42(2): 2752288.[3] Scholes F H,Soste C,Hughes A E,et al.The role ofhydrogen peroxide in t he deposition of cerium2based conversion coatings[J].Applied Surface Science,2006,253(4):17702 1780.[4] Katya Brunelli,Maunuele Dabala,Irene Calliari.Effect of HClpre2treat ment on corrosion resistance of cerium2based conversion coatings on magnesium and magnesium alloys[J].Corrosion Science,2005,47(4):98921000.[5] Montemor M F,Simoes A M,Carmezim M J.Characterizationof rare2eart h conversion films formed on t he AZ31magnesium alloy and it s relation wit h corrosion protection[J].Apllied Surface Science,2007,253(16):692226931.收稿日期:2007209216CH2铸铁件磷化工艺的研究Study of Phosphating Process for CH2C ast Iron Parts李敏娇1, 张述林2, 王晓波2, 罗 2(1.四川理工学院化学系,四川自贡643000;2.四川理工学院材料与化学工程系,四川自贡643000)L I Min2jiao1, ZHANG Shu2lin2, WANG Xiao2bo2, L U O Yi2(1.Depart ment of Chemist ry,Sichuan U niversity of Science&Engineering,Zigong643000,China;2.Dept.of Material&Chemical Engineering,Sichuan U niversity ofScience&Engineering,Zigong643000,China)摘要: 研究了一种高耐蚀性常温磷化工艺,优选了磷化液配方,讨论了磷化液各组分对磷化膜的影响。
钢铁件防锈磷化处理工艺

钢铁件防锈磷化处理工艺王文忠【摘要】@@ 0前言rn防锈磷化是以防锈为目的的磷化处理工艺,其属于厚膜磷化,膜厚约为10~20μm,膜重为10~30 g/m2;钢铁件发蓝(氧化)膜厚仅为0.5~1.5μm,因此防锈磷化膜的防锈性能远超过钢铁件氧化膜的.钢铁件经防锈磷化处理,其尺寸不会发生改变,这是由于在磷化膜形成过程中会有部分金属溶解在磷化液中.【期刊名称】《电镀与环保》【年(卷),期】2011(031)003【总页数】1页(P50-50)【作者】王文忠【作者单位】洛阳立微电子有限公司,河南洛阳471003【正文语种】中文【中图分类】TG174防锈磷化是以防锈为目的的磷化处理工艺,其属于厚膜磷化,膜厚约为10~20μm,膜重为10~30 g/m2;钢铁件发蓝(氧化)膜厚仅为 0.5~1.5 μm,因此防锈磷化膜的防锈性能远超过钢铁件氧化膜的。
钢铁件经防锈磷化处理,其尺寸不会发生改变,这是由于在磷化膜形成过程中会有部分金属溶解在磷化液中。
2.1.1 纯锰系高温防锈磷化这类磷化所形成的磷化膜防锈效果最为理想,应用最为广泛,溶液中往往加入少量镍盐及硝酸盐为促进剂。
其工艺规范为:2.1.2 锌系高温厚膜磷化2.1.3 锌-锰系高温厚膜磷化高温磷化温度高,能耗高,溶液蒸发量大,稳定性差。
中温磷化能耗低,磷化速率快,且磷化膜的防锈性能与高温磷化的接近,其酸比控制在10~15,因此中温厚膜磷化应用日趋增多。
其工艺规范为:除此之外,许多中温中厚锌系及锌-锰系磷化应用也很广泛,也有较好的防锈效果,多用在工序间防锈。
对于厚膜磷化,要达到较长期防锈的效果,还必须对其进行后处理。
重铬酸钾50~80 g/L,碳酸钠2~4 g/L,70~90°C,10~15 min。
肥皂 30~50 g/L,80~95 °C,10~15 min。
常温下可浸入脱水防锈油中,时间一般为1~3 min;也可在机油中加入一定量的脱水防锈油,在90~110°C下浸5~7 min。
高磷铸铁热处理工艺
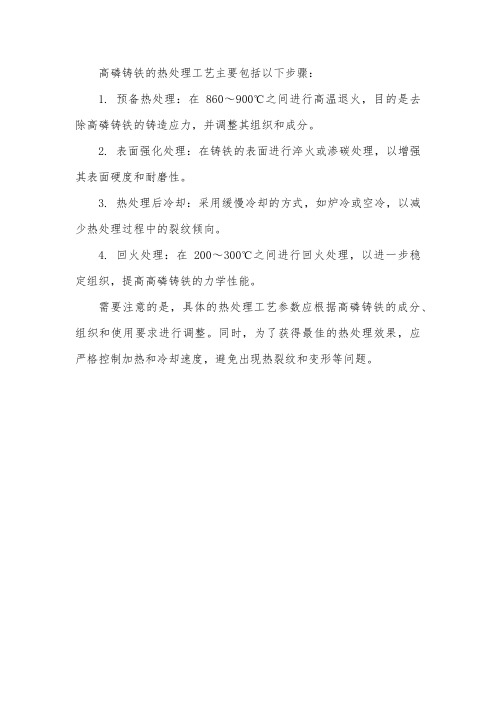
高磷铸铁的热处理工艺主要包括以下步骤:
1. 预备热处理:在860~900℃之间进行高温退火,目的是去除高磷铸铁的铸造应力,并调整其组织和成分。
2. 表面强化处理:在铸铁的表面进行淬火或渗碳处理,以增强其表面硬度和耐磨性。
3. 热处理后冷却:采用缓慢冷却的方式,如炉冷或空冷,以减少热处理过程中的裂纹倾向。
4. 回火处理:在200~300℃之间进行回火处理,以进一步稳定组织,提高高磷铸铁的力学性能。
需要注意的是,具体的热处理工艺参数应根据高磷铸铁的成分、组织和使用要求进行调整。
同时,为了获得最佳的热处理效果,应严格控制加热和冷却速度,避免出现热裂纹和变形等问题。
汉高酸洗磷化工艺控制控制

汉高酸洗磷化工艺现场控制一、脱脂工艺脱脂配槽过程:1)测定槽的容积,2)在槽中注入四分之三水,加热至操作温度,3)加入1022R脱脂主剂和1023S脱脂助剂4)将清水加至操作液位,升温至操作温度,5)测试相关的脱脂数据,来调整到工作范围药剂使用参数:1)药剂使用浓度:脱脂主剂BONDERITE C-AK RT-1022R:3%脱脂助剂BONDERITE C-AD RT-1023S:0.3%2)处理时间和温度:处理时间:3-5分钟处理温度:25-40度参数检测方法:游离碱控制范围:15-20ml1)准确移取10ml槽液加入到250ml的锥形瓶中。
2)滴加2-3滴酚酞指示剂。
3)用0.1N盐酸标准溶液滴定至粉红色消失(30s没有反复)为终点,消耗的盐酸毫升数即为游离碱度。
日常补加方法:每1000L槽液增加游离碱1个点,需加:BONDERITE C-AK RT-1022R2kgBONDERITE C-AD RT-1023S0.2kg二、防锈工艺防锈配槽过程:1)测定槽的容积,2)在槽中注入四分之三水,3)加入BONDERITE C-NE7400防锈剂,4)将清水加至操作液位,开启气循环,5)测试相关的表调数据,来调整到工作范围。
药剂使用浓度:表调剂BONDERITE C-NE7400:0.3%-0.5%参数检测方法:PH值:8-10日常补加方法:每1000L槽液增加pH1个点,需加:BONDERITE C-NE7400:1kg定期更换水洗槽,来保证水洗质量。
建议更换频率为一周一次。
三、表调工艺表调配槽过程:1)测定槽的容积,2)在槽中注入四分之三水,3)加入BONDERITE M-AC Z-5表调剂,4)将清水加至操作液位,开启气循环,5)测试相关的表调数据,来调整到工作范围。
药剂使用浓度:表调剂BONDERITE M-AC Z-5:0.2%-0.3%参数检测方法:表调槽PH值:8-10日常补加方法:每1000L槽液增加pH1个点,需加:BONDERITE M-AC Z-5:1kg定期更换表调槽,来保证表调质量。
- 1、下载文档前请自行甄别文档内容的完整性,平台不提供额外的编辑、内容补充、找答案等附加服务。
- 2、"仅部分预览"的文档,不可在线预览部分如存在完整性等问题,可反馈申请退款(可完整预览的文档不适用该条件!)。
- 3、如文档侵犯您的权益,请联系客服反馈,我们会尽快为您处理(人工客服工作时间:9:00-18:30)。
铸铁件磷化的处理工艺(喷淋)推荐
2007-07-18 09:50
一、前处理工艺情况
1、处理工件:铸铁件
2、清洗方式:喷淋式
3、工艺流程:
铸铁工件进入磷化之前可以不生锈,在铸铁件的加工过程中可以采用工序间的防锈,使用P3 - prevox 6748。
6748的防锈能力为3-4天不生锈。
预脱脂--脱脂--水洗--水洗--磷化--水洗--钝化--烘干
Parco Cleaner1523 (Duridine 7760)P3 - prevox 6748
4、使用汉高化学品:脱脂Parco Cleaner1523 R Parco Cleaner1523S
磷化Duridine 7760
钝化P3 - prevox 6748
二、前处理工艺参数推荐(详见下页表格)前处理工艺客户:工序工位产品名称浓度处理时间温度备注 1 预脱脂Parco Cleaner 1523 建浴量1% 游离碱度20-30PT 0.5--2mins 40-60℃2 脱脂Parco Cleaner 1523 建浴量1% 游离碱度15-20PT 0.5--2mins 40-60℃3 水洗工业用水PH≥9 1-2mins 常温溢流 4 水洗工业用水PH≥7 常温溢流 5 磷化Duridine 7760 建浴量1-3% 全酸度 3.1-9.3 PH 4.5-5.5 45-60℃ 6 水洗自来水PH≥6 1-2mins 常温溢流7 钝化P3 - prevox 6748 建浴量0.5-2% PH=10 0.5--3mins 15-80oC 8 烘干30--50mins 200℃
三.各工位控制Ⅰ. 脱脂1、添加PC-1523在添加时须计算好添加量。
2、本工段要求必须加热,并且搅拌均匀。
3、日常维护:当脱脂槽表面漂有较多油污,加水溢流之。
当脱脂槽含油过多而影响除油效果时,就应排放槽液,重新开槽。
保持各参数在控制范围之内。
4、测试与控制游离碱用移液管将10毫升样品移入150毫升的锥形烧杯中,加5滴3号指示剂(酚酞)。
用20号滴定溶液(0.1N硫酸)滴定直至最后一滴除去粉红色为止。
用掉的20号滴定溶液的毫升数即为以点数计的游离碱的值。
游离碱范围3 ~ 7 ml 在给出的最佳值的 0.5点的范围内。
每1000升槽液增加一个点数,应加入:Parco Cleaner 1523A 2 kg Parco Cleaner 1523S 0.2 kg Parco Cleaner 1523 R的碱性比Parco Cleaner 1523 A要强。
通常,用Parco Cleaner 1523 R进行补加槽液浓度,补加量相当于Parco Cleaner 1523 A。
Ⅱ. 水洗1、控制范围:控制第一道水洗PH〈9.0 控制第二道水洗
四.磷化1. 配制1000l的槽液槽内加水后, 加温到45℃以上, 然后边循环边慢慢加入:Duridine 7760 10 ~ 30 公斤= 7.7~ 23.1 升2. 操作数据浓度:10 ~ 30 g/l = 7.7 ~ 23.1 l/m3 总酸度:3.1 ~ 9.3 pH值: 4.5 ~ 5.5 温度:45 ~ 60 ℃处理时间: 2 ~ 3 分钟喷淋压力:1 ~ 2 bar 3. 如果槽液pH值低于4.5, 可以用缓冲溶液(如Grano starter 65)调整到规定值。
Duridine 7760槽液的浓度可用滴定总酸点数来测定,同时测定pH 槽液补充: 每1000l槽液中每少一个点数应加入: Duridine 7760 3.2公斤= 2.5升“总酸度”滴定: A. 用移液管将10ml 槽液移入锥性烧瓶中并用50ml蒸馏水稀释。
B. 添加4-5滴酚酞指示剂。
C. 在对烧瓶轻微摇动的同时,从滴定管中慢慢地滴加0.1N氢氯化钠标准溶液,当试液保持呈玫瑰色时表明滴定到达终点。
D. 所消耗的0.1N氢氯化钠溶液的毫升数即为"总酸度"。
规定范围: 3.1 ~ 9.3(点数) Ⅴ. 水洗视污染度而定,要不断溢流。
控制PH >6.00 Ⅵ.钝化1、材料:防锈剂P3-6748。
2、开槽:开
回复4 现场管理论坛2007-07-18 09:54
五、注意事项1、检查前处理剂库存,实验室用品;2、检查动力、加热系统、是否正常;
温度表、压力表显是否正确;3、检查各槽液位、溢流情况;4、检查水源(自来水,去离子水)是否符合要求;5、保持各工序工艺参数在工艺范围内,槽液测定频率视产量而定,一般为四小时左右检测一次。
6、定期清理管路、及加热系统是必要的,以确保表面处理质量及加热质量。
槽底的垢也应定期清理。
7、搬运及使用化学品时,要穿戴好必要的保护用品;8、产品说明书,有关人员应熟读;。