微细电加工应用技术研究
微细电火花加工模糊抬刀控制系统的设计及实验研究

De i n a p r me t lS u y o z y J mpi g Co r lS se f r M i r — sg nd Ex e i n a t d fFu z u n nto y t m o c o EDM
Ab ta t sr c :Th s a e rsn s t o ffzyjmpn o to y tm ae nmie rg a i p p rp ee t meh do u z a u igc n r 1 se b s do x dpo rm— s
m i g o ATL n fM AB n a d VC + + .Th u z o t o y t m s d s n d b s d o t t t so h i e f z y c n r l s e i e i e a e n sa i i f t e d s s g sc —
《 电加工与模具》21 年第 1 02 期
关 的方 波信 号 ( 称放 电时 间 波 形 ) 就可 明显 区分 简 ,
出这两 种状 态 。 因此 , 用 放 电时 间 检测 法 检 测 微 采
时 如 以某 一 电压 为基 准 , 其 转 化 为与 放 电 时 间有 将
一
细电火 花加 工 间 隙大 小 的 灵敏 度很 高 , 于 微 细 电 适
—
编写 , 刀控 制 模 块 流 程 见 图 5 抬 。该 模 块 首 先 进 行 放 电状态 的辨 别 与 统计 , 设 计 的 放 电状 态 统 计 模 本 块是 基于 上述 放 电时 间检 测 法 、 脉 冲个 数 为 单 位 以 进行 放 电状态 统 计 的 。采用 累加 计 数 的方 法 , 软 在 件 中设 定 3个 变 量 c u t 、o n 、o n。l 分 别 o n. cu t c u t l S d a, 记 录短 路状 态数 、 花放 电状 态数 及总 放 电状态 数 , 火
微细电火花加工技术

微细电火花加工技术微细电火花加工技术是一种高精度加工方法,它通过利用电火花放电的瞬间高温和高压能量,将工件表面的金属材料溶解、熔化、蒸发和喷射等效应,实现对工件进行微细加工的一种技术。
微细电火花加工技术具有加工精度高、表面质量好、加工效率高等优点,在模具制造、航空航天、医疗器械等领域有着广泛的应用。
微细电火花加工技术的原理是利用电火花放电过程中产生的高温等效应来加工工件。
在微细电火花加工过程中,工件和电极通过一个电解液隔开,当施加足够的电压时,电极上会产生高频率的电火花放电。
电火花放电瞬间产生的高温和高压能量会使电解液中的金属离子快速聚集在工件表面,形成微小的气泡,同时气泡瞬间爆破产生的压力将工件表面的金属材料冲击下来。
通过不断重复这个过程,就可以实现对工件表面的微细加工。
微细电火花加工技术的加工精度非常高,可以达到亚微米级别。
这是因为在电火花放电过程中,由于高温和高压能量的局部聚集作用,使得工件表面的金属材料局部熔化和蒸发,从而实现微细加工。
此外,微细电火花加工技术还可以实现对工件表面的复杂形状、小孔和细槽等微细结构的加工,具有很高的灵活性。
微细电火花加工技术的应用非常广泛。
在模具制造领域,微细电火花加工技术可以用于制造高精度的模具零件,如模具芯、模具腔等。
在航空航天领域,微细电火花加工技术可以用于制造航空发动机的涡轮叶片、航天器的结构零件等。
在医疗器械领域,微细电火花加工技术可以用于制造高精度的医疗器械零件,如人工关节、牙科种植体等。
微细电火花加工技术虽然有很多优点,但也存在一些限制。
首先,由于加工过程中电火花放电会产生高温,工件表面容易产生热应力,从而导致表面质量下降。
其次,微细电火花加工技术只适用于导电材料的加工,对于非导电材料的加工效果不佳。
此外,微细电火花加工技术的加工效率相对较低,加工速度较慢。
微细电火花加工技术是一种高精度加工方法,具有广泛的应用前景。
随着科技的不断进步和发展,微细电火花加工技术将会进一步提高加工精度和效率,为各个领域的微细加工需求提供更好的解决方案。
微细加工工艺技术

微细加工工艺技术微细加工工艺技术是一种应用于微电子、光学、纳米学等领域的高精度加工技术,该技术能够实现对微细结构的精密加工。
在微细加工工艺技术中,常常采用的加工方法有激光刻蚀、化学蚀刻、光刻以及微电子束等。
激光刻蚀是一种应用激光照射,通过激光束的高能量将材料表面局部蚀刻的加工方法。
与传统的机械刻蚀相比,激光刻蚀具有高精度、高效率的优点。
在激光刻蚀中,光束的聚焦度和光斑直径是影响加工精度的重要参数。
化学蚀刻是一种利用特定的化学反应,在材料表面选择性地产生化学蚀刻产物,并将其去除的加工方法。
化学蚀刻通常需要制备特定的蚀刻溶液,通过控制溶液的浓度和温度,来影响化学反应的速率和选择性。
化学蚀刻可以实现微细结构的高精度加工,并被广泛应用于光学元件和微流控芯片等领域。
光刻是一种基于光化学反应的加工方法,通过光阻的选择性暴露和去除,来形成所需的图案结构。
在光刻过程中,首先在材料表面涂敷一层光刻胶,然后利用光刻机的紫外光照射和显影等步骤,实现图案的转移。
光刻具有高精度、高分辨率和高重复性的优点,是微细加工中不可或缺的工艺之一。
微电子束也是一种实现微细结构加工的重要方法。
微电子束利用高能电子束在材料表面定向照射,经过准直、聚焦和偏转等步骤,将电子束的能量转化为对材料的加工作用。
通过控制电子束的参数,如能量、聚焦度和扫描速度等,可以实现对微细结构的精密加工。
微电子束在高精度加工领域具有很大的应用潜力,尤其在微电子器件、光电器件以及半导体器件等方面,具有广阔的发展前景。
总的来说,微细加工工艺技术是一种实现高精度加工的重要方法,包括激光刻蚀、化学蚀刻、光刻和微电子束等。
这些加工方法在微电子、光学、纳米学等领域发挥着重要作用,推动了相关技术的进步和应用的发展。
未来随着科学技术的不断进步,微细加工工艺技术将继续发展壮大,为人类社会带来更多的科技成果和应用产品。
电解加工在微细制造技术中的应用研究

L h —y n , I u S a d n nvri f eh ooyZb 5 0 9 C i ) I i o g J H a(h n o gU i syo c nlg, i 2 5 4 , h a Z e t T o n
【 摘要】 电解加工是利用阳极金属 电化学溶解原理来去除材料的制造技术 , 这种微去除方式使得
to h mia ds o u in prn i e o pr c s s a ig. T i cr —dis l t n mo k s r c e c l is l t i cpl t o es h p n o h mi o— s o u i d m e ECM h v h s o e a a e te
pu lcr o r ea pl d n EM M . eee to s u c p i i e K e r :El c r he ia a hi n y wo ds e t oc m c lm c ni g;M i r a hi n c om c ni g;Eee t o l c r de;Pu s l c r l eee t o
、
0 6 {
01
《 02{
、
\
0 1—— —— — — .. , —— —— — — —— 0 —— , — ——— —一 .
( )A S S 3 N Y 数值模拟结果 与实验测得结果符合较好 ,证 明 了数值模拟的合理性 。有助于进一步研究脉冲磁场作用 下合金 凝 固组织细化机理。
-
k来 稿 日期 :0 5—0 20 8—1 9
主要集 中在铁芯 、圆柱形样品的中间部分 ( 铁芯宽度范围内) ,
~ 、
l
\
j
而在 样 品的 两 端 磁 感 应强 度 较 弱 。
微细电火花加工设备技术研究
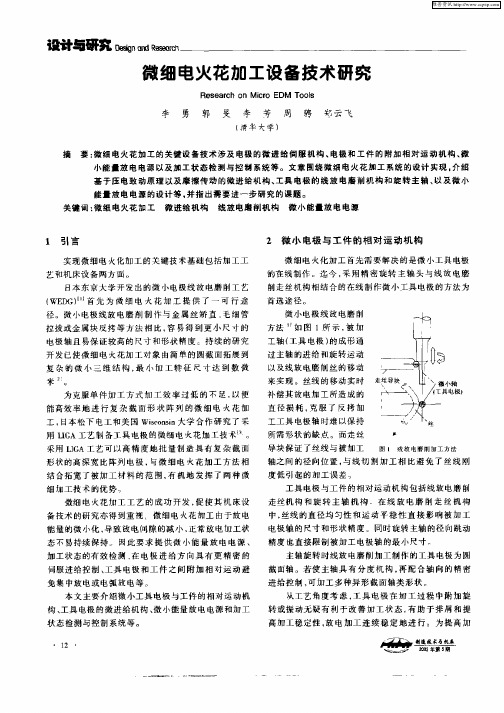
设计与研究
位移 分辨 率 的同时 实现 大位移 行程 的优 点 。其基 本结 构 和运动 原理 见 图 3所示 , 主要 构件 包括 主轴 、 向压 轴键设 备技 术涉及 电极 的 微进 给 伺服 机构 、 微 电极和 工 件 的 附加 相 对运 动机 构 、 微 小能 ■放 电电源 以及 加工状 态检 测与控 制 系统 等。 文章 围绕 微细 电火花 加 工系统 的设计 实现 . 介绍
基 于压 电致动原 理 以及摩 擦传 动 的微进 给机 构 、 具 电极 的 线放 电磨 削机 构 和旋 转 主 轴 、 工 以及 微 小
转 或振动无 疑有 利 于改 善 加 工 状 态 , 助于 排 屑 和提 有
高加 工稳定 性 , 电 加工 连续 稳 定 地 进 行。 为 提高 加 放
维普资讯
Di。 e d sn g
工 效 率 , 必要 进一 步开 发电极 丝连 续进 给补偿 机 构。 有 图 2为微 细 电极旋 转进 丝机构 原 理 示意 图 。由 进 给 活塞 、 常闭式 夹 丝机 构 、 开式 夹丝 机构 和导 向头 常 等构 成 , 机构 与穿 于 其 中 的 电极 丝 被 置 于 旋 转套 筒 该
电极 轴 的尺 寸和形 状精 度 。同时 旋转 主轴 的径 向跳动 精度 也直接 限制 被加工 电极 轴 的最小尺 寸 。 主轴旋 转时 线放 电磨 削加工 制作 的工具 电极 为圆
截面轴 。若 使主轴 具 有 分 度 机构 , 配台 轴 向的 精 密 再 进 给控 制 , 可加工 多种 异 形截面 轴类形 状 。 从工艺 角度考 虑 , 具 电极 在 加 工 过程 中附加 旋 工
能量 放 电电源 的设计 等 , 并指 出需要 进 一步研 究 的课题 。 关键词 : 微细 电火花加 工 微进 绐机构 线 放 电磨削机 构 微小 能■ 放 电电源
微细电火花加工的实验研究

o 2 0Fm, 法满 足需求 。基 于微细 电 火花精 密 加 .3 i 无 l
工 系 统 I D 一0 针 对 所 需 加 工 的 微 小 孔 , 先 加  ̄ M 5, E 首 工 出 了微 细 工 具 电 极 , 后 在 零 件 上 加 工 出 了 6个 然 均 匀 的微 小 孔 , 径 为 0 1 5mm( 3 。 小 孔 的 边 直 .5 图 ) 缘 均 很 规 整 , 径 一 致 性 也 很 高 , 全 满 足 了 需 求 方 直 完
微 细 电 火 花 加 工 技 术 作 为 一 种 实 现 金 属 零 件 微
小 特 征 精 密 加 工 的 重 要 _ 艺 手 段 , 引 了 国 内 外 众 T 吸 多 学 者 进 行 卓 有 成 效 的研 究 。 微 细 电 火 花 加 工 系统
与实验研究 是其 中重要 的研究 内容 。哈尔滨 工业 大
《 电加工与模具》2 I 年第 2 01 期
工 艺・ 备 装
微 细 电火 花 加 工 的 实 验 研 究
张 勇 斌 ,吉 方 ,刘 广 民 ,张 连 新 ,吴 祉 群
(中 国工程 物理研 究 院机械制 造工艺 研究所 , 四川绵 阳 6 1 0 2 9 0)
摘 要 : 于 新 研 发 的 一 套 微 细 电 火花 精 密加 工 系统 E M一0 在 金 属 材 料 上 进 行 了 一 些 典 型 的 基 D 5, 微 小特 征 精 密 加 工 实验 及 电 火花 放 电 沉 积 实验 。 该 系统 已作 为加 工 特 征 尺 寸 介 于数 十 微 米 到 数 毫
的要 求 。
件, 要求 在 围绕 其 中心 、 直 径 为 1 3 且 . 5mm 的 圆周
上 均 匀 加 工 出 6个 直 径 0 1 'n的 微 小 孔 。 用 微 . 5 DI l
电化学加工技术在微细零件制造中的应用研究

电化学加工技术在微细零件制造中的应用研究随着科技的不断进步和发展,微细零件制造成为高精度制造领域的重要技术之一。
其中,电化学加工技术作为一种高效、精密的加工方法,被广泛应用于微细零件制造中,取得了显著的成果。
本文将就电化学加工技术在微细零件制造中的应用做一探讨。
电化学加工技术是利用电解液中的金属离子在工件表面发生可控的电化学反应,实现工件材料的去除或增加。
这种技术与传统的机械加工方式相比,具有更高的加工精度和表面质量,能够制造出更加复杂的微细零件。
例如,在航空航天、医疗器械、电子设备等领域,微细零件的制造需要极高的精度和表面质量,而电化学加工技术能够满足这些要求。
首先,电化学加工技术在微细零件的制造中起到了重要的作用。
以微型齿轮为例,齿廓的精度和表面质量直接影响到齿轮的传动效率和使用寿命。
传统的机械加工方式在加工微细齿轮时存在齿轮齿廓形状控制困难、齿面加工质量差等问题。
而电化学加工技术通过控制电解条件和工艺参数,可以实现对齿轮齿廓形状和表面质量的精确控制。
此外,电化学加工技术还可用于制造微细孔等微细结构,具有很高的加工精度和表面质量。
其次,电化学加工技术在微细零件制造中还具有一定的应用潜力。
虽然电化学加工技术已经在一些领域得到了成功应用,但在一些新兴领域,如微电子器件、光学元件制造等方面,仍然存在一些挑战。
例如,微电子器件的制造要求零件尺寸更小、表面更加光滑,而传统的电化学加工技术在实现这些要求上还存在一些限制。
因此,针对这些新兴领域的需求,需要进一步改进和创新电化学加工技术。
此外,电化学加工技术在微细零件制造中还需要与其他制造技术相结合。
微细零件的制造过程往往需要多个加工步骤的协同作用。
例如,在微型电池的制造中,需要先通过电化学加工技术制造出电极片,然后将其与其他组件进行组装。
因此,电化学加工技术与其他加工技术的协同应用能够实现更加高效和精密的微细零件制造。
综上所述,电化学加工技术在微细零件制造中的应用研究具有重要意义。
微细电火花加工的实验研究

微细电火花加工的实验研究张勇斌;吉方;刘广民;张连新;吴祉群【摘要】Some t ypical experiments of micro-electrical discharge machining are described based on a set of new developed micro-eiectrical discharge machining equipment typed μEDM-50 in the paper.The resuhs about micro-character precise machining and discharging deposition are given. The size of the rnachining character varies mainly from a few decades of micrometers to a few millimeters.%基于新研发的一套微细电火花精密加工系统EDM-50,在金属材料上进行了一些典型的微小特征精密加工实验及电火花放电沉积实验.该系统已作为加工特征尺寸介于数十微米到数毫米范围的重要工艺手段.【期刊名称】《电加工与模具》【年(卷),期】2011(000)002【总页数】3页(P54-56)【关键词】微细电火花加工;工具电极;放电沉积【作者】张勇斌;吉方;刘广民;张连新;吴祉群【作者单位】中国工程物理研究院机械制造工艺研究所,四川绵阳,621900;中国工程物理研究院机械制造工艺研究所,四川绵阳,621900;中国工程物理研究院机械制造工艺研究所,四川绵阳,621900;中国工程物理研究院机械制造工艺研究所,四川绵阳,621900;中国工程物理研究院机械制造工艺研究所,四川绵阳,621900【正文语种】中文【中图分类】TG661微细电火花加工技术作为一种实现金属零件微小特征精密加工的重要工艺手段,吸引了国内外众多学者进行卓有成效的研究。
微细电化学加工技术

微细电化学加工技术现状与进展摘要:微细电电化学加工是微细加工领域的一个重要研究方向,电化学加工是利用电化学阳极溶解的原理将零件加工成型,具有工具无损耗、加工表面质量好、与零件材料硬度无关、加工后工件无应力和变形等优点,近年来随着电解加工理论的进一步成熟,微细电解加工以其独特的优势有望成为微细加工领域的又一主流技术[1]。
微细电化学在未来的微纳加工中必将大有作为。
本文介绍了国内外微细电化学加工技术、微细电化学加工电源及检测技术的研究现状[2]。
结合国内外微细电化学加工技术的最新进展,系统地综述了微细电化学加工在多个方面的研究情况和工艺特点[3]。
关键词:电化学;电化学加工;微细电化学加工;脉冲电源。
电化学电化学是一项古老的技术,是从研究电能与化学能的相互转换开始形成的。
到20 世纪50 年代中期,苏联、美国和我国才相继开始了电解加工工艺的试验研究,电解加工也逐渐得到了发展。
随着科学技术的不断发展和深入,电化学的研究领域不断拓宽和扩展,在电化学基础上开拓的电化学加工技术,支撑了电铸、电镀、电解冶炼和电解合成、电解加工、材料腐蚀的控制等重要的产业部门,已迅速地发展成为具有重大工业意义的一项技术。
电化学加工电化学加工技术主要是利用金属材料发生氧化还原的电化学过程来实现去除材料和增加材料的目的。
电化学加工技术自问世以来,以其新颖的加工原理而得到了极为广泛的应用,已成为当前机械加工领域中不可缺少的加工方法。
电化学加工技术是一种特种加工技术,目前在微细加工中已占有重要的位置。
由于加工过程是以离子单位方式进行的,所以在微细加工中占有重要的位置。
随着现代电力电子技术的发展,针对电化学加工对精度和表面质量的要求,逐渐采用脉冲电源替代直流电源,而且脉冲电源的频率也在不断提高。
另外,计算机控制技术的发展,使采用简单形状电极加工复杂结构的工件成为可能,使电化学加工技术有了广阔的应用前景[4]。
电化学加工是一种基于在溶液中通电,使离子从一个电极移向另一个电极,从而将材料去除或沉积的方法,因此。
压电自适应微细电火花加工电极损耗率实验研究

了该 装 置 的加 工原理 。该装 置有 别 于 常规 的微 型 电火花 加 工装 置 , 实现 放 电 间 隙与放 电状 态的 可 自适 应调 节 , 促进 排屑 , 能有 效控 制提 弧及 短路 现 象的 出现 , 并能 实现短路 自消除 , 而大幅度 提 高 从
加 工效 率。通 过 大量 实Fra bibliotek , 析 了各 参数 对 电板相 对损 耗 率 的影响 。 实验 结果表 明 : 分 电极 相对 损耗
( W R)icesswi h ces f p nv l g n a ai ne E n rae t tei raeo e ot ea dcp c a c ,whl rs tn eRl n h s h n o a t i ei a c a dR2 a e s
s btee f c u l fe ton EW R . Ke r y wo ds:mir c o EDM ; eft ni e u a o ; e e s iz ee tiiy; lcr d a a i s l—u ng r g lt r r v re pe o lc rct ee to e we rr to
(S a d n iest , a 5 0 , ia) h n o g Unv riy Jn n 2 0 6 Chn i 1
Ab ta t s r c :A c o dig t h h r c e itc ir c r n o t e c a a t rs isofm c o ED M , a n w e oee t i d p i e ee tia e piz lc rc a a tv lc rc l
d s ha g c i i g h sb e e eo e ic r e ma h n n a e n d v l p d,a d iswo ki g me h n s a d c a a t rs ish v e n a n t r n c a im n h r c e itc a e b e n— ay e n t spa e .Th sma hi i g me h d,dif r n r m t r l z d i hi p r i c n n t o fe e tfo o he s,c n r a ie hes l—un n e u— a e lz d t e ft i g r g lt rbe we n dic a g n la a e a d dic a gi o ii s,f clt t e v n h h p n ,r — a o t e s h r i g ce r nc n s h r ng c ndton a iia e r mo i g t e c i pigs e la e a cn nd s ri g a d c n ei n t h h ri y is l,t u hema h n n fiinc a e e s r i g a ho tn n a lmi a e t e s o tng b tef h s t c i i g e fce y c n b i r v d d a tc l mp o e r sia l M a y e e i n s a e e n o e a t fe t f pa a e e s o lc r d y. n xp rme t h v b e d n nd he e f cs o r m t r n e e to e we r r to h ve b e nay e i hi a e . Ex e i n a e u t n c t t t ee t o e we r r to a a i a e n a l z d n t s p p r p rme t l r s ls i dia e ha lc r d a a i
微细电火花加工技术的研究进展

行度 偏差在 亚微 米 级的 3维 立体结构 而倍受 世人 瞩 目 。然而要 实现 L GA 工艺 就 必须 使用 昂贵 I 的同 步 辐 射 源 , 时 , 原理 上讲 , I 同 从 L GA 技 术 很
难 用 于 斜 面 、 由 曲 面 的微 细 3维 加 工 n 。 自
单 位 尽可能 小 。 而在 电火 花加工过 程 中 . 其加工 单 位( 即每次放 电 的蚀 除 量 ) 只取决 于单个 放 电脉冲 的能 量 随着 现代 电力 电 子技术 的发展 , 电火 花加 工 的加工 精 度与 表 面 质量 得 到 了极 大 的提 高 , 加
王振 龙 赵 万生 狄 士春 迟 关心
摘 要 : 究 和 综 述 了微 细 电 火 花 加 工技 术 的研 究现 状 和 发 展 趋 势 比 较 研 分 析 了 常 用 微 细 加 工 与 微 细 电 火 花 加 工 方 法 的特 点 及 应 用 . 述 了线 电 极 电 论 火 花 磨 削 枝 木 的 原 理 及 在 微 细 加 工 中 的 作 用 。 合 电 火 花 加 工过 程 中 无 宏 观 结 作 用 力 的 特 点 , 述 了微 细 电 火 花 加 工 装 置 微 小 型 化 的 可 行 性 和 几 种 主 要 形 论
维普资讯
中 国机 械 工 程 第 l 卷 第 l 3 0期 2 0 年 5月 F半月 02
文 章 编 号 : 0 4 1 2x( 0 2 1 —0 9 ~ 0 1 0 — 3 2 0 ) 0 8 4 5
微 细 电火 花加 工 技术 的研 究进 展
而 微 细 加 工 是 实 现 产 品 零 部 件 微 型 化 的 最 基
本技术 , 已成为 涉及机 械 、 它 电子 、 化学 、 料 等多 材 种学科 的现 代高技 术 。目前 . 在微 细加 工 领域 中 , 同步 辐 射 深 度 x 射线 刻蚀 、 将 电铸 成 型 及 塑
微细电解加工技术发展现状

微细电解加工技术发展现状
微细电解加工技术是一种利用电化学原理进行微细加工的先进制造技术,它在微加工领域具有重要的应用价值。
目前,微细电解加工技术的发展现状可以从以下几个方面来进行分析:
1. 技术原理,微细电解加工技术是利用电解液中的离子在工件表面的电化学溶解作用,通过控制电流密度和电解液流动状态,实现对工件进行微细加工的一种制造技术。
目前,该技术已经得到了较为深入的研究和理论积累,技术原理日趋成熟。
2. 加工精度,随着微细电解加工技术的不断发展,加工精度得到了显著提高。
目前,微细电解加工技术可以实现亚微米甚至纳米级的加工精度,能够满足一些高精度微制造领域的需求。
3. 加工效率,微细电解加工技术在加工效率方面也取得了一定的进展,通过优化加工参数和工艺流程,加工效率得到了提升。
然而,与传统加工方法相比,仍然存在一定的改进空间。
4. 应用领域,微细电解加工技术已经在微机械加工、微电子器件制造、生物医学器械加工等领域得到了广泛应用。
随着对微加工
精度和表面质量要求的不断提高,微细电解加工技术的应用领域还将进一步扩大。
5. 发展趋势,未来,微细电解加工技术有望在材料选择、加工参数优化、设备结构改进等方面取得新突破,进一步提高加工精度和效率,拓展应用领域,推动微细加工技术的发展。
总的来说,微细电解加工技术在技术原理、加工精度、加工效率、应用领域和发展趋势等方面都取得了一定的进展,但仍然需要在材料选择、工艺优化等方面继续努力,以满足不断提高的微细加工需求。
微细加工技术的发展与应用

微细加工技术的发展与应用随着科技的不断发展,微细加工技术成为现代工业中不可或缺的一部分。
微细加工技术是指对微小物体进行加工的技术,通常用于制造那些需要高精度或者微小尺寸的零件、设备和器件。
微细加工技术的应用范围非常广泛,包括微型机器人、光学器件、医疗器械、生物传感器等领域。
本文将探讨微细加工技术的发展历程、应用和未来发展趋势。
一、微细加工技术的发展历程微细加工技术源远流长。
在过去的几百年间,人们使用了各种手工工具和机械设备进行微细加工。
例如,19世纪英国人约瑟夫·温斯洛在1822年发明了摆线拖动齿轮切削机,实现了金属齿轮的精细加工。
这一技术被广泛应用于英国的纺织工业,并为工业革命的发展做出了贡献。
20世纪初,随着电气工程和电子学的发展,半导体器件的出现推动了微细加工技术的发展。
1947年,贝尔实验室的威廉·肖克利发明了第一个晶体管,奠定了现代电子工业的基础。
从此以后,微细加工技术得到了巨大的发展,出现了各种各样的微细加工工具和设备。
例如,扫描电子显微镜可以对微小物体进行高分辨率成像和表征,电子束光刻机可以用来制造半导体芯片、具有纳米尺度精度的纳米定位台可以用来进行精细的纳米加工等等。
二、微细加工技术的应用微细加工技术已经广泛应用于多个领域。
以下是一些例子:1. 光学器件光学器件包括激光器、光开关、波导器、光电探测器等。
微细加工技术可以提供高精度和可重复加工,适用于制造这些器件的需求。
例如,电子束光刻机已经被广泛应用于制造半导体激光器和光子晶体器件。
2. 医学器械微细加工技术可以用于制造医学器械,例如微型手术器械和医用传感器。
这些器械需要高精度和微小尺寸,以减少对患者的创伤和疼痛。
微细加工技术可以提供这些要求。
3. 生物传感器生物传感器利用生物体内的化学反应或者生物特性来检测生物分子和细胞。
微细加工技术可以用于制造这些传感器。
例如,电子束光刻机可以用来制造生物芯片,这些芯片可以用于生命科学研究和医学诊断。
微细加工技术研究现状
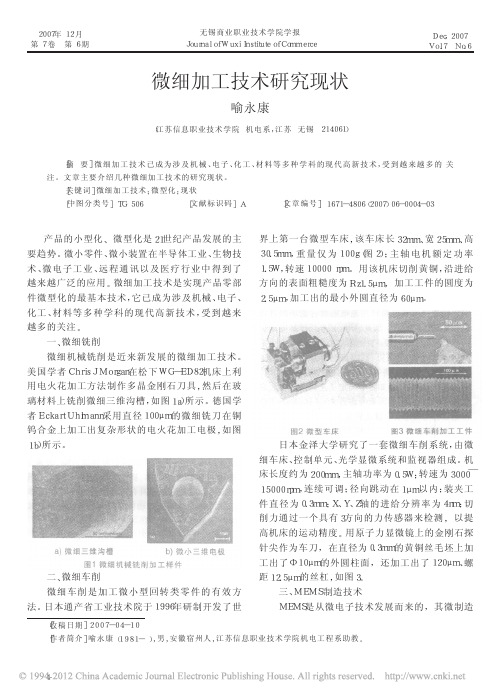
[收稿日期]2007-04-10[作者简介]喻永康(1981-),男,安徽宿州人,江苏信息职业技术学院机电工程系助教。
微细加工技术研究现状喻永康(江苏信息职业技术学院机电系,江苏无锡214061)[摘要]微细加工技术已成为涉及机械、电子、化工、材料等多种学科的现代高新技术,受到越来越多的关注。
文章主要介绍几种微细加工技术的研究现状。
[关键词]微细加工技术;微型化;现状[中图分类号]TG506[文献标识码]A[文章编号]1671-4806(2007)06-0004-03产品的小型化、微型化是21世纪产品发展的主要趋势。
微小零件、微小装置在半导体工业、生物技术、微电子工业、远程通讯以及医疗行业中得到了越来越广泛的应用。
微细加工技术是实现产品零部件微型化的最基本技术,它已成为涉及机械、电子、化工、材料等多种学科的现代高新技术,受到越来越多的关注。
一、微细铣削微细机械铣削是近来新发展的微细加工技术。
美国学者ChrisJMorgan在松下WG-ED82机床上利用电火花加工方法制作多晶金刚石刀具,然后在玻璃材料上铣削微细三维沟槽,如图1a)所示。
德国学者EckartUhlmann采用直径100μm的微细铣刀在铜钨合金上加工出复杂形状的电火花加工电极,如图1b)所示。
a)微细三维沟槽b)微小三维电极图1微细机械铣削加工样件二、微细车削微细车削是加工微小型回转类零件的有效方法。
日本通产省工业技术院于1996年研制开发了世界上第一台微型车床,该车床长32mm、宽25mm、高30.5mm,重量仅为100g(图2);主轴电机额定功率1.5W,转速10000rpm。
用该机床切削黄铜,沿进给方向的表面粗糙度为Rz1.5μm,加工工件的圆度为2.5μm,加工出的最小外圆直径为60μm。
图2微型车床图3微细车削加工工件日本金泽大学研究了一套微细车削系统,由微细车床、控制单元、光学显微系统和监视器组成。
机床长度约为200mm,主轴功率为0.5W;转速为3000 ̄15000rpm,连续可调;径向跳动在1μm以内;装夹工件直径为0.3mm;X、Y、Z轴的进给分辨率为4nm;切削力通过一个具有3方向的力传感器来检测,以提高机床的运动精度。
三维微结构微细电火花和电解组合加工实验研究
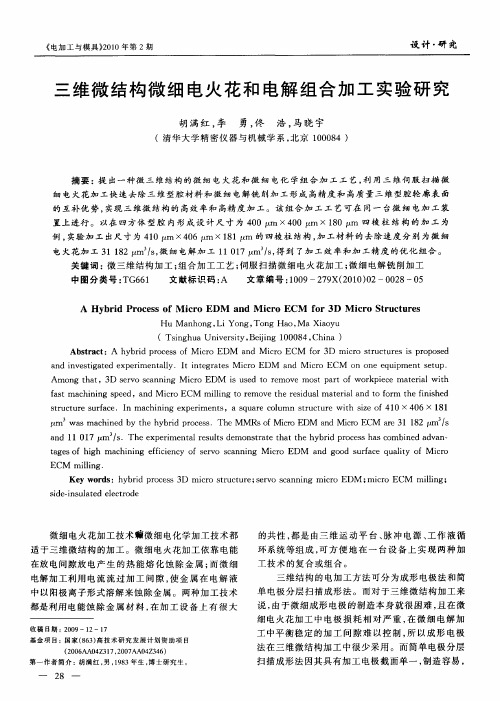
设 计 ・ 究 研
三 维 微 结 构 微 细 电火 花 和 电解 组 合 加 工 实 验 研 究
胡满红 , 李 勇 , 佟 浩 , 晓 宇 马
(清华 大学 精密仪 器与机 械学 系 , 北京 1 0 8 0 0 4)
摘 要 : 出一 种 微 三 维 结 构 的微 细 电 火 花 和 微 细 电 化 学 组 合 加 工 工 艺 , 用 三 维 伺 服 扫 描 微 提 利
ECM li mi ng. l
K e r s:h b i r c s D ir t u t r ; e v c nn n ir y wo d y rd p o e s3 m c o s r c u e s r o s a i g m c o EDM ; ir m co ECM il g; m li n Sd —n 1 a e lcr d ie i s1 t d ee to e 1
(Tsn h aUnv ri , ej g 1 0 8 Chn ) ig u ies y B in 0 0 4, ia t i
Ab ta t sr c :A b i r c s fM ir hy rd p o e so c o EDM n ir a d M c o ECM o f r3D c o s r c u e s p o o e mir t u t r s i r p s d
A b i o e sO ir Hy rd Pr c s f M c o EDM n ir a d M c o ECM 0 D ir tu t r s fr3 M c o Sr cu e
H U M a ho g, n To a M a Xio n n LiYo g, ng H o, a yu
微细加工技术的应用和趋势

改造 客观世 界 的一种 高 新技 术 。微机械 多 的小型 泵 的1 0 0 0 倍 ,而 且机 电一体 化 蚀 ,最 后把 光刻胶 去掉 就得 到 了想要 的
由于 具有 能够在 狭 小空 间 内进 行 作业 , 的微 机械 不存 在信 号延 迟 问题 ,可进 行 图形 。光刻技 术在 微 电子 中 占有 很大 的 比重 ,比如微 电子应用 3 . 1搬迁原子 1 9 9 0 年 ,美 国圣何塞I B M N尔马登研
而 受 到人们 的高 度重 视 ,被 列为 2 1 世 纪 和智 能结 构后 ,更 易于 实现 微机 械 的多 关键 技术 之首。 功能化和智能化 。
1 . 微机械 的特征
1 . 5 适 于大批 量生 产 、制 造成 本低 究所科 学家用S T M 将镍表面 吸附的氙原子
5 个氙 原子排成 I B M - = 微 机 械 在 美 国 常 称 为 微 型 机 电系 廉。微机械采用与 半导体制造工艺类似的 逐一移动 ,最终 以3 统 ;在 日本 称作 微机 器 ;而在 欧 洲则称 方法生产 ,可以象超大规模集成 电路芯片 个字母 。每个字母 高5 n m ,原子间的最短 作微 系统。
而 又 不扰乱 工作 环境 和对 象 的特 点 ,在 高速工作 。
航 空航 天 ,精密 仪器 ,生物 医学 等领域
1 . 4 多功能和 智 能化 。微 机械 最终 宽 来评 价 的,而线 宽 的获得跟 光刻 技术
有 着广 阔 的应用 潜 力 ,且是 实现 纳米技 要达 到集传 感 器 、执行 器和 电子控 制 电 有 很 大 的关 系 。 术 (N a n 0 t e c h n o l o g y ) 的重 要 环 节 , 因 路为 一体 的 目标 ,特别 是应 用智 能材 料
激光微细加工技术的研究与应用

激光微细加工技术的研究与应用激光微细加工技术是一种应用非常广泛的前沿技术,能够在微纳尺度下对材料进行加工。
它具有高精度、高效率、高质量的特点,在现代工业中具有非常关键的应用价值。
本文将从激光微细加工技术的原理、发展历程以及应用领域等方面进行深入探究。
一、技术原理激光微细加工技术主要是通过激光在被加工物表面的作用下,使其产生化学反应、物理变化或消失等效应,实现对材料的加工。
其基本原理是通过激光束的聚焦,使光束与材料相互作用,产生较高的局部温度和压力,使物质发生蒸发、沉积、熔化、氧化等变化,从而实现对材料的加工。
二、技术发展历程激光微细加工技术的发展经历了几十年的漫长历程。
20世纪60年代,美国和苏联的科学家们开始在激光微细加工领域进行探索研究。
20世纪70年代,德国、日本、韩国等国家也开始了相关技术的研究。
80年代初,随着计算机技术和控制技术的快速发展,激光微细加工技术得到了迅速的发展。
90年代以来,随着激光技术和材料科学的不断进步,激光微细加工技术在制造业、材料科学、光学等领域得到了广泛应用。
三、技术应用领域激光微细加工技术具有非常广泛的应用领域,在现代工业、科技领域中得到了广泛的应用。
以下将从军事、航空航天、电子信息、生物医学等方面进行介绍。
1. 军事领域:激光微细加工技术在军事装备中得到了广泛应用,如激光导弹制导系统、光电防护系统、军事雷达成像系统等。
2. 航空航天领域:激光微细加工技术在航空航天领域中也得到了广泛应用,如航天器结构、焊接、修补、表面处理等方面。
3. 电子信息领域:激光微细加工技术在电子信息领域得到了广泛应用,如半导体制造、芯片刻蚀、电路打孔、塑胶雕刻等。
4. 生物医学领域:激光微细加工技术在生物医学领域中也得到了广泛应用,如激光治疗、眼科手术、组织切割、药物释放等方面。
四、技术瓶颈虽然激光微细加工技术得到了广泛的应用和发展,但是其仍然存在一些技术瓶颈,如:1. 能量损耗问题:光束在传输过程中会受到各种因素的影响,从而导致损耗。
微细及小孔电火花加工的关键技术研究的开题报告

微细及小孔电火花加工的关键技术研究的开题报告1. 研究背景微细及小孔电火花加工(Micro-Electrical Discharge Machining,简称Micro-EDM)是一种高精度、高效率、非接触的微细加工技术,可用于加工半导体材料、陶瓷材料、硬质合金材料以及其他难加工材料。
然而,Micro-EDM加工仍存在许多技术瓶颈,特别是在加工大深度、小直径(Diameter<20μm)的细微孔道时,加工效率和精度均面临巨大挑战。
为了解决这些技术难题,需要深入研究Micro-EDM过程的关键技术,提高Micro-EDM加工的效率和精度。
2. 研究目的本研究旨在探究Micro-EDM加工中的关键技术,针对大深度、小直径孔道加工难题,研究并优化Micro-EDM加工参数,提高加工效率和精度,从而为微细及小孔电火花加工技术的发展提供技术支撑。
3. 研究内容(1)Micro-EDM关键技术研究本文将从放电控制方法、电极、工作液以及辅助气体等方面对Micro-EDM关键技术进行研究,探讨各项技术对加工效率和精度的影响。
(2)大深度、小直径孔道加工技术研究本文将研究各项Micro-EDM加工参数对大深度、小直径孔道加工的影响,分析加工过程中的孔道直径误差、加工深度误差等问题,并提出相应的加工优化方案,提高Micro-EDM加工效率和精度。
4. 研究方法(1)理论分析法本文将从Micro-EDM加工过程的放电机理、放电脉冲参数、工作液理论等角度进行理论分析,明确放电控制方法以及其他关键技术。
(2)实验室实验法本文将在微细加工实验中采用一系列微细加工实验,探讨Micro-EDM加工的关键技术和影响因素,进行加工参数优化,提高加工效率和精度。
5. 研究意义研究Micro-EDM加工技术的关键技术,探讨大深度、小直径孔道加工技术优化方案,对提高Micro-EDM加工效率和精度,推动微细及小孔电火花加工技术的发展具有重要意义。
微细电火花加工的技术分析
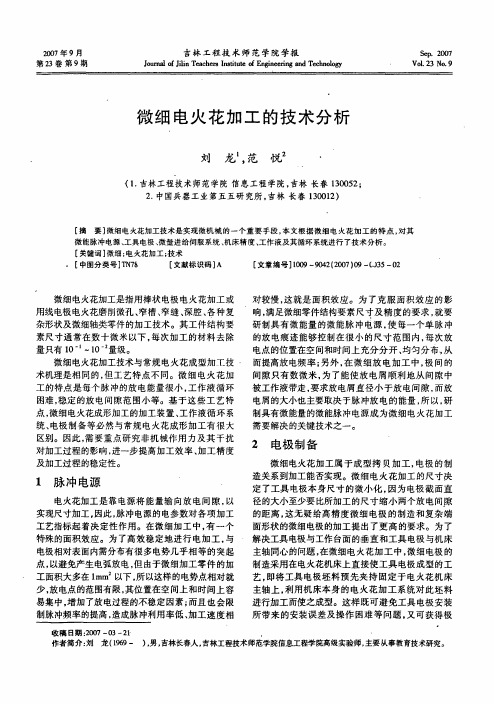
( 1. 吉林工程技术师范学院 信息工程学院, 长春 130 52 吉林 0 ;
2. 中国兵器工业第五五研究所, 吉林 长春 1 0 12 3 )
〔 要1微细电火花加工技术是实现微机械的一个重要手段, 摘 本文根据微细电火花加工的特点, 对其 微能脉冲电源、 工具电极、 微量进给伺服系统、 机床精度、 工作液及其循环系统进行了技术分析。 【 关键词〕 微细;电火花加工;技术 【 中图分类号」 7 N T 8 【 文献标识码」 A 【 文章编号」洲 以 2《( 7 )0 一 J3 一 11 为一 抖 20 0 C 5 0 ) 2
少, 放电点的范围有限, 其位置在空间上和时间上容 易集中, 增加了 放电过程的不稳定因素; 而且也会限 制脉冲频率的提高, 造成脉冲利用率低、 加工速度相
解决工具电 极与工作台面的垂直和工具电极与机床 主轴同心的问题, 在微细电火花加工中, 微细电极的 制造采用在电火花机床上直接使工具电极成型的工 艺, 即将工具电极坯料预先夹持固定于电火花机床 主轴上, 利用机床本身的电火花加工系统对此坯料 进行加工而使之成型。这样既可避免工具电极安装 所带来的安装误差及操作困难等问题, 又可获得极
区别。因此, 需要重点研究非机械作用力及其 干扰 对加工过程的影响, 进一步提高加工效率、 加工精度 及加工过程的稳定性。
2
电极制备
1 脉冲电源
电火花加工是靠电源将能量输向放电间隙, 以 实现尺寸加工, 因此, 脉冲电源的电参数对各项加工 工艺指标起着决定性作用。在微细加工中, 有一个 特殊的面积效应。为了高效稳定地进行电加工, 与 电极相对表面内 需分布有很多电势几乎相等的突起 点, 以避免产生电弧放电, 但由于微细加工零件的加
X 3 收稿 日期 2( 刀 一0 一2 1 作者简介 刘 龙( 1 一 ) , 吉林长春人, %9 男, 吉林工程技术师范学院信息工程学院高级实验师, 主要从事教育技术研究,
微细电解加工技术研究现状与展望

1 微 细 电解 加 工 理 论 基础
在 微 细 电解 加 工 过 程 中 , 、 极 间 电 位 差 在 间 阴 阳
隙电解 液 中形 成 的 电 场会 对 工 件 造 成 杂 散腐 蚀 , 这 在 很大 程度上影 响 了 电解 加工 的精 度 , 约束 电场 、 改
生产 率 高 、 面 质 量 好 、 具 阴 极 无 损 耗 等 显 著 优 表 工
M ) ic d gte fn a n a te r so C M , l to h mia co mahn g tc n lg n - M ,n l i h u d me tl h oi fE M ee rc e clmi c ii eh oo y a d e un e c r n
第 4期
21 0 1年 4月
组 合 机 床 与 自 动 化 加 工 技 术
M o ul r M a hi o d a c ne To l& A u o a i a f c urn c ni ue t m tc M nu a t i g Te h q
NO. 4
Apr .20 1 1
o h a e we n t o ah d nd w o k e e a o ,nd ke e h o o d d v lpme ti h u u e ft e g p b t e o lc t o e a r pic n dea y t c n l g a e eo y n n n t e f t r .
文 章编 号 :0 101—2 6 2 1 ) 4—01 8—0 2 5( 0 1 0 0 5
微 细 电解 加工 技 术研 究 现状 与展 望
王贺宾 , 郭钟 宁 , 罗红 平
( 东工 业大 学 机 电工程学 院 , 州 500 ) 广 广 10 6 摘 要 : 近 年 来 微 细 电解 加 工领 域 的研 究 现 状 和 发展 趋 势进 行 了概 述 , 对 包括 微 细 电解 加 工 的基 础 理 论 、 微 细 电解 加 工技 术 和 加 工 装 置 、 响 因素 与极 间 间 隙检 测 控 制 , 影 以及 关键 技 术 和今 后 的 发展 方 向 。 关 键 词 : 细 电 解 ; 础 理 论 ; 细 装 备 ; 状 ; 展 趋 势 微 基 微 现 发 中 图 分 类 号 : H1 ;G 5 T 6 T 6 文 献 标 识 码 : A
- 1、下载文档前请自行甄别文档内容的完整性,平台不提供额外的编辑、内容补充、找答案等附加服务。
- 2、"仅部分预览"的文档,不可在线预览部分如存在完整性等问题,可反馈申请退款(可完整预览的文档不适用该条件!)。
- 3、如文档侵犯您的权益,请联系客服反馈,我们会尽快为您处理(人工客服工作时间:9:00-18:30)。
图 2 微细电极丝导向器
通过配置微细电极丝进给补偿机构模块 ,结合 高频脉冲放电电源 、加工状态检测及电极伺服进给 控制等系列关键技术的开发应用 ,构建出了精密微 细孔电火花加工系统 。
微细孔电火花加工机床采用机电模块化设计 , 具有 X Y 数控工作台适用于单件微细孔和阵列微 细孔的加工 ,最小孔径尺寸 0. 1 mm ,深径比 10∶1 。 加 工尺寸精度可达 ±2μm ,表面粗糙度 R a 0. 2~ 0. 4μm 。
着眼于微细电加工技术的特点 ,立足于工业应 用背景 ,近年来我们相继进行了微细孔电火花加工 、
三维微细结构电火花伺服扫描加工及微细电化学加 工技术的理论研究和技术开发 ;形成了一些技术思 路和阶段性的技术成果 ,在此做一简要介绍 。
1 微细孔电火花加工
在微细孔电火花加工的工业应用中 ,从加工效 率考虑 ,相对于线电极放电磨削 ( WED G) 在线制作 微细电极 ,采用拉拔出的具有一定长度的微细电极 丝直接作为工具电极依然具有优势 。它在一次装夹 后能连续加工一批工件 ,大大减少电极更换次数 ,节 省辅助时间 。
设计·研究 《电加工与模具》2009 年增刊
Hale Waihona Puke 技术水平 。 理论上 ,微细电加工具有加工方法灵活 、加工装
备成本较低 、适用加工材料范围广 、对加工环境要求 不甚苛刻 、具有向微纳制造发展的潜力以及可迅速 投入应用等优点 。但在实际上 ,考虑到工业应用中 对高精度和高效率加工的同步要求 ,微细电加工尚 需在进一步研究开发中弥补或克服自身原理上的先 天缺陷 ,形成具有实用价值的微细加工手段 。
国家高 技 术 研 究 发 展 计 划 资 助 项 目 ( 2007AA04Z346 , 2006AA04 Z317) 作者简介 : 李勇 , 男 , 1962 年生 , 教授 。
— 32 —
得到微小尺寸的电极轴且易保证较高的尺寸和形状 精度 ,使微细电火花加工的最小加工特征尺寸达到 微米量级 。持续的研究开发也已使微细电火花加工 对象由简单的圆截面微小轴 、孔拓展到复杂的微小 三维结构 。1997 年日本东京大学研究出选择工具 电极端部放电 ,利用简单形状电极进行扫描加工的 方法 ,使三维微小结构的电火花加工成为可能[2] 。
通常的微细电火花扫描加工过程如图 4 所示 。 在图 4a 中 ,电极纵向进给接近工件表面 ,设定加工 层厚 ,电极纵向定位 。之后电极以速度 v x 横向移 动进行扫描加工 。由于存在电极损耗 ,电极与工件 之间间隙增大 ,加工作用逐渐减弱 ,直至超出放电加 工间隙 ,放电加工停止 。在这种无电极损耗补偿的 情况下 ,微细电火花扫描加工无法正常进行 。而基 于工艺实验经验数据 ,在电极损耗速率已知的情况 下 ,在横向扫描加工的同时 ,使电极以一定速度 vz 纵向进给 ,如图 4b 所示 ,可达到电极损耗补偿的效 果 ,保持持续的放电加工状态 ,但缺乏自动加工的柔 性 。图 4c 所示为我们研究开发的基于放电间隙伺 服控制进行电极损耗实时补偿的三维微小结构的微 细电火花扫描加工方法 。在横向扫描加工的同时 , 实时检测电极端面放电的开路 、短路和正常加工状 态 ,通过电极的纵向伺服进给 ,使加工放电间隙始终 保持在正常放电范围 。从而在该扫描加工层 ,均匀 地蚀除掉每一处的被加工材料 。 在微细电火花伺服扫描加工中 ,设定不同的横 向扫描速度 ,在多次实验中发现伺服扫描加工过程
但由于电极截面细微 ,电极损耗问题相对突出 , 因此多工件连续加工的进给和电极损耗自动补偿机 构成为关键 。
基于蠕动运动机理 ,所设计的电极丝损耗补偿 进给机构原理如图 1 所示[4] 。机构受 Z 向伺服进 给驱动 ,主要由常开式 、常闭式夹丝机构和电极丝导 向器构成 (图 1a) 。在正常加工进给过程中 ,常开式 夹丝机构处于松开状态 ,常闭式夹丝机构夹紧电极 丝 ,在 Z 向伺服进给驱动下 ,沿轴向进给电极丝进 行加工 (图 1b) 。当一个工位的进给加工完成后 , Z 向伺服进给驱动常闭式夹丝机构反向快速回退 ,由 于电极丝长度方向的加工损耗 ,为保持每一次加工 状态一致 ,将电极丝前端调至初始位置 ,此时由常开 式夹丝机构夹紧电极丝 ,常闭式夹丝机构松开 (图 1c) 。 Z 向伺服驱动继续反向回退至初始位置 ,再使 常闭式夹丝机构夹紧电极丝 ,常开式夹丝机构处于 松开状态 (图 1d) ,即回到图 1a 所示的状态 。循环 往复上述过程 ,可实现电极丝的的多工件连续加工 进给和电极损耗自动补偿 。 当然 ,该机构通过多次循环进给 ,也可应用于超
关键词 : 微细电火花加工 ;微细电化学加工 ;电极损耗 ;伺服进给 ;伺服扫描 中图分类号 : T G66
Micro Electro Machining Technologies f or Industrial Application
Li Yong ( Tsinghua University , Beijing 100084 , China ) Abstract : Micro elect ro machining technologies including micro2EDM and micro2ECM are devel2 oped to drill micro holes and shape 3D micro st ruct ures for indust rial purposes. An automatic feed mechanism is designed for micro EDM equipment to compensate elect rode wear and guide micro elec2 t rode. A servo scanning EDM met hod is proposed for shaping 3D micro st ruct ures , in which elect rode wear is compensated on real time by servo cont rol of discharge gap . Then a micro ECM process is also t ried to drill array micro holes. Micro holes wit h minimum diameter of 100μm can be drilled efficient2 ly in t he EDM process. 3D micro st ruct ures wit hin area of 1 mm2 square can be shaped conveniently by use of t he servo scanning EDM process. The micro ECM process proposed will be f urt her st udied and used into t he machining of array micro holes and 3D micro st ruct ures. Key words : micro EDM ; micro ECM ; elect rode erosion ; servo feed ; servo scanning
图 3 微细孔加工样件
为实现连续的放电加工 ,达到具有应用价值的 加工效率 ,我们提出了基于放电间隙伺服控制进行 电极损耗实时补偿的微细电火花扫描加工方法[5] 。 通过高速实时采集放电间隙的状态量作为反馈信 号 ,与正常加工的设定状态量进行比较产生控制信 息 ,利用比较控制信息对放电间隙进行闭环控制 ,使 放电间隙始终保持在正常放电加工状态 。
在微 细 电 化 学 加 工 研 究 方 面 , 2000 年 德 国 Fritz2Haber 研究所提出了新颖的利用超短脉冲的微 细电化学加工方法[3] ,使微细电化学加工以材料去 除的加工方式 ,达到加工出微米尺寸的微细结构的
© 1994-2009 China Academic Journal Electronic Publishing House. All rights reserved.
(a)
( b)
(c)
( d)
图 1 电极丝损耗补偿进给机构原理示意图
— 33 —
© 1994-2009 China Academic Journal Electronic Publishing House. All rights reserved.
《电加工与模具》2009 年增刊 设计·研究
《电加工与模具》2009 年增刊 设计·研究
微细电加工应用技术研究
李 勇
( 清华大学制造工程研究所 ,北京 100084 )
摘要 : 微细电加工要达到工业应用的目的 ,需兼顾加工效率和加工精度两方面的要求 。以微 细孔 、微细三维结构的加工为目标 ,进行了微细孔电火花加工 、三维微细结构电火花伺服扫描加工 及微细电化学加工技术的研究开发 。设计出微细电极的损耗补偿进给和导向机构 ,开发出三维微 细结构的电火花伺服扫描加工工艺 ,研究了采用阵列微细电极的微细电化学加工方法 。微细孔电 火花加工可连续加工直径小至 100μm 的孔 。伺服扫描电火花加工可便捷地在小于 1 mm2 区域内 加工出三维微细结构 。提出的微细电化学加工技术路线拟将微细电解加工应用于阵列微细孔和三 维微细结构的加工 。
对于微细电火花加工 ,从原理上可认为是近电 场作用 ,微小放电间隙有助于实现加工精度的控制 , 但在加工过程中电极的损耗往往使预期的形状加工 精度难以实现 。线电极放电磨削 ( WED G) 工艺解决 了微细电极在线制作的问题 ,但在实际加工应用中 , 电极的损耗导致微细电极的反复修整 ,加工效率过 低 。另外 ,在三维微小结构的微细电火花扫描加工 过程中 ,相对电极的微细截面 ,工件需蚀除的材料面 积和体积较大 ,电极损耗更为严重 。电极损耗使在 加工过程中电极与工件的间隙随横向扫描时刻在增 大 ,超出放电加工间隙后 ,加工过程将难以为继 。