塑料件结构设计基本原则
塑料件结构设计要点
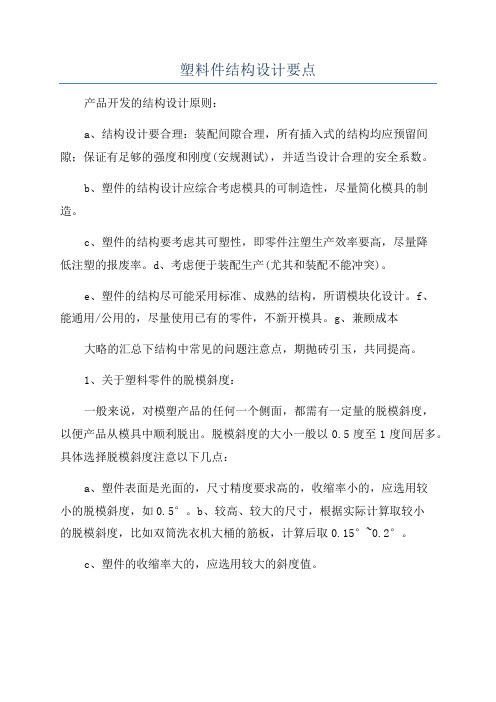
塑料件结构设计要点产品开发的结构设计原则:a、结构设计要合理:装配间隙合理,所有插入式的结构均应预留间隙;保证有足够的强度和刚度(安规测试),并适当设计合理的安全系数。
b、塑件的结构设计应综合考虑模具的可制造性,尽量简化模具的制造。
c、塑件的结构要考虑其可塑性,即零件注塑生产效率要高,尽量降低注塑的报废率。
d、考虑便于装配生产(尤其和装配不能冲突)。
e、塑件的结构尽可能采用标准、成熟的结构,所谓模块化设计。
f、能通用/公用的,尽量使用已有的零件,不新开模具。
g、兼顾成本大略的汇总下结构中常见的问题注意点,期抛砖引玉,共同提高。
1、关于塑料零件的脱模斜度:一般来说,对模塑产品的任何一个侧面,都需有一定量的脱模斜度,以便产品从模具中顺利脱出。
脱模斜度的大小一般以0.5度至1度间居多。
具体选择脱模斜度注意以下几点:a、塑件表面是光面的,尺寸精度要求高的,收缩率小的,应选用较小的脱模斜度,如0.5°。
b、较高、较大的尺寸,根据实际计算取较小的脱模斜度,比如双筒洗衣机大桶的筋板,计算后取0.15°~0.2°。
c、塑件的收缩率大的,应选用较大的斜度值。
d、塑件壁厚较厚时,会使成型收缩增大,脱模斜度应采用较大的数值。
e、透明件脱模斜度应加大,以免引起划伤。
一般情况下,PS料脱模斜度应不少于2.5°~3°,ABS及PC料脱模斜度应不小于1.5°~2°。
f、带皮纹、喷砂等外观处理的塑件侧壁应根据具体情况取2°~5°的脱模斜度,视具体的皮纹深度而定。
皮纹深度越深,脱模斜度应越大。
g、结构设计成对插时,插穿面斜度一般为1°~3°(见后面的图示意)。
2、关于塑件的壁厚确定以及壁厚处理:合理的确定塑件的壁厚是很重要的。
塑件的壁厚首先决定于塑件的使用要求:包括零件的强度、质量成本、电气性能、尺寸稳定性以及装配等各项要求,一般壁厚都有经验值,参考类似即可确定(如熨斗一般壁厚2mm,吸尘器大体为2.5mm),其中注意点如下:a、塑件壁厚应尽量均匀,避免太薄、太厚及壁厚突变,若塑件要求必须有壁厚变化,应采用渐变或圆弧过渡,否则会因引起收缩不均匀使塑件变形、影响塑件强度、影响注塑时流动性等成型工艺问题。
塑料件设计规则
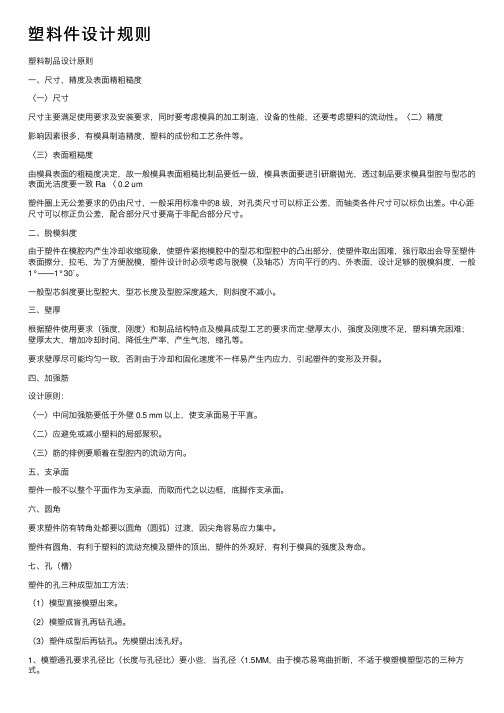
塑料件设计规则塑料制品设计原则⼀、尺⼨,精度及表⾯精粗糙度〈⼀〉尺⼨尺⼨主要满⾜使⽤要求及安装要求,同时要考虑模具的加⼯制造,设备的性能,还要考虑塑料的流动性。
〈⼆〉精度影响因素很多,有模具制造精度,塑料的成份和⼯艺条件等。
〈三〉表⾯粗糙度由模具表⾯的粗糙度决定,故⼀般模具表⾯粗糙⽐制品要低⼀级,模具表⾯要进引研磨抛光,透过制品要求模具型腔与型芯的表⾯光洁度要⼀致 Ra 〈 0.2 um塑件圈上⽆公差要求的仍由尺⼨,⼀般采⽤标准中的8 级,对孔类尺⼨可以标正公差,⽽轴类各件尺⼨可以标负出差。
中⼼距尺⼨可以棕正负公差,配合部分尺⼨要⾼于⾮配合部分尺⼨。
⼆、脱模斜度由于塑件在模腔内产⽣冷却收缩现象,使塑件紧抱模腔中的型芯和型腔中的凸出部分,使塑件取出困难,强⾏取出会导⾄塑件表⾯擦分,拉⽑,为了⽅便脱模,塑件设计时必须考虑与脱模(及轴芯)⽅向平⾏的内、外表⾯,设计⾜够的脱模斜度,⼀般1°——1°30`。
⼀般型芯斜度要⽐型腔⼤,型芯长度及型腔深度越⼤,则斜度不减⼩。
三、壁厚根据塑件使⽤要求(强度,刚度)和制品结构特点及模具成型⼯艺的要求⽽定:壁厚太⼩,强度及刚度不⾜,塑料填充困难;壁厚太⼤,增加冷却时间,降低⽣产率,产⽣⽓泡,缩孔等。
要求壁厚尽可能均匀⼀致,否则由于冷却和固化速度不⼀样易产⽣内应⼒,引起塑件的变形及开裂。
四、加强筋设计原则:〈⼀〉中间加强筋要低于外壁 0.5 mm 以上,使⽀承⾯易于平直。
〈⼆〉应避免或减⼩塑料的局部聚积。
〈三〉筋的排例要顺着在型腔内的流动⽅向。
五、⽀承⾯塑件⼀般不以整个平⾯作为⽀承⾯,⽽取⽽代之以边框,底脚作⽀承⾯。
六、圆⾓要求塑件防有转⾓处都要以圆⾓(圆弧)过渡,因尖⾓容易应⼒集中。
塑件有圆⾓,有利于塑料的流动充模及塑件的顶出,塑件的外观好,有利于模具的强度及寿命。
七、孔(槽)塑件的孔三种成型加⼯⽅法:(1)模型直接模塑出来。
(2)模塑成盲孔再钻孔通。
汽车注塑件(塑料件)设计时需要遵循的14个基本原则

(2)拔模角和高度 通常,筋的拔模角在1-1.5度,最小不能小于0.5度,否则会导致零件脱模困
难。越高的筋顶部往往很薄,导致注塑过程中难以充满也就失去了筋的意义。筋 的顶端厚度一般不低于1毫米,高度一般为零件壁厚的2.5-3倍。当然也会有例外, 需要具体分析。
0.5 deg min 筋厚
Байду номын сангаас
1 min 壁厚
D min D min
塑料件中的柱销也是我们常用到的结构,主要用于提供连接和定位。 • 设计要点:
(1)像筋的设计一样要考虑拔模角度、出模方向、根部厚度与基本壁厚的比 例等。
(2)另外,我们还有一个相互矛盾的问题需要考虑。一方面,我们希望销柱 的厚度(B)尽量薄些,以防止表面出现缩痕。另一方面,我们希望其厚度能厚 一些,以增加结构强度。最终,我们要根据产品结构和材料等综合分析确定。
塑料件翻边结构十分重要,它能够明显提高制件的结构刚度控制变形,是很 有用的结构,我们设计时必须尽量考虑增加翻边结构。 • 设计要点:
(1)翻边的厚度应该与基本壁厚一致。 (2)考虑到零件花纹,我们对翻边的拔模角度有特殊的要求,一般在3-6度之 间。但是不同的花纹会有不同的要求,设计时应根据花纹要求及制造和质量要求 选择适当的拔模角。
P/L P/L
8 有许多种类型的花纹可以用于零件表面的装饰。我们设计时需要针对不同的
花纹选择合适的设计结构。 • 设计要点:
(1)拔模角—总的规则是每增加0.025毫米的花纹深度,需要增加至少1度的拔 模角。关于花纹和拔模角需要设计者和花纹供应商共同检查和确认,并得到 OEM的认可。
(2)翻边—对于翻边结构,花纹和拔模角的关系是最突出的。翻边结构就需 要一定的脱摸角度,以便零件从模具内移出。越长的翻边需要越大的脱模角度, 越深的花纹,也需要越大的脱模角度。如果不注意这点就会产生零件脱模困难, 甚至擦伤零件花纹表面。
塑胶产品结构设计基本规则

塑胶产品结构设计基本规则设计基本规则壁厚的大小取决于产品需要承受的外力、是否作为其它零件的支撑、承接柱位的数量、伸出部份的多少以及选用的塑胶材料而定。
一般的热塑性塑料壁厚设计应以4mm为限。
从经济角度来看,过厚的产品不但增加物料成本,延长生产周期”冷却时间〔,增加生产成本。
从产品设计角度来看,过厚的产品增加引致产生空穴”气孔〔的可能性,大大削弱产品的刚性及强度。
最理想的壁厚分布无疑是切面在任何一个地方都是均一的厚度,但为满足功能上的需求以致壁厚有所改变总是无可避免的。
在此情形,由厚胶料的地方过渡到薄胶料的地方应尽可能顺滑。
太突然的壁厚过渡转变会导致因冷却速度不同和产生乱流而造成尺寸不稳定和表面问题。
对一般热塑性塑料来说,当收缩率”Shrinkage Factor〔低于0.01mm/mm时,产品可容许厚度的改变达;但当收缩率高于0.01mm/mm时,产品壁厚的改变则不应超过。
对一般热固性塑料来说,太薄的产品厚度往往引致操作时产品过热,形成废件。
此外,纤维填充的热固性塑料于过薄的位置往往形成不够填充物的情况发生。
不过,一些容易流动的热固性塑料如环氧树脂”Epoxies〔等,如厚薄均匀,最低的厚度可达0.25mm。
此外,采用固化成型的生产方法时,流道、浇口和部件的设计应使塑料由厚胶料的地方流向薄胶料的地方。
这样使模腔内有适当的压力以减少在厚胶料的地方出现缩水及避免模腔不能完全充填的现象。
若塑料的流动方向是从薄胶料的地方流向厚胶料的地方,则应采用结构性发泡的生产方法来减低模腔压力。
平面准则在大部份热融过程操作,包括挤压和固化成型,均一的壁厚是非常的重要的。
厚胶的地方比旁边薄胶的地方冷却得比较慢,并且在相接的地方表面在浇口凝固后出现收缩痕。
更甚者引致产生缩水印、热内应力、挠曲部份歪曲、颜色不同或不同透明度。
若厚胶的地方渐变成薄胶的是无可避免的话,应尽量设计成渐次的改变,并且在不超过壁厚3:1的比例下。
下图可供叁考。
塑料制品的结构设计规范
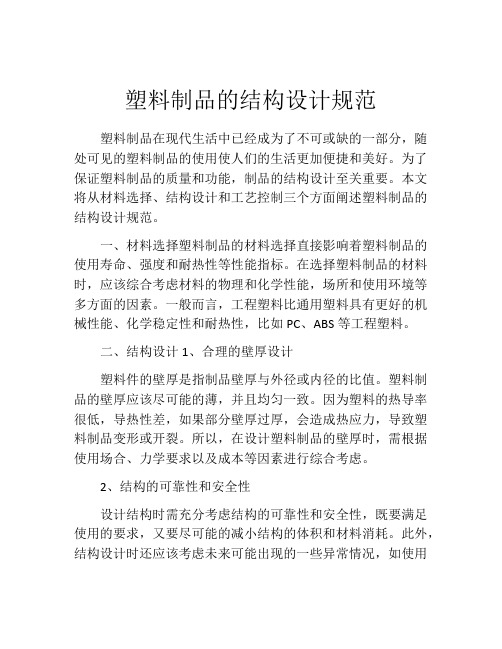
塑料制品的结构设计规范塑料制品在现代生活中已经成为了不可或缺的一部分,随处可见的塑料制品的使用使人们的生活更加便捷和美好。
为了保证塑料制品的质量和功能,制品的结构设计至关重要。
本文将从材料选择、结构设计和工艺控制三个方面阐述塑料制品的结构设计规范。
一、材料选择塑料制品的材料选择直接影响着塑料制品的使用寿命、强度和耐热性等性能指标。
在选择塑料制品的材料时,应该综合考虑材料的物理和化学性能,场所和使用环境等多方面的因素。
一般而言,工程塑料比通用塑料具有更好的机械性能、化学稳定性和耐热性,比如PC、ABS等工程塑料。
二、结构设计1、合理的壁厚设计塑料件的壁厚是指制品壁厚与外径或内径的比值。
塑料制品的壁厚应该尽可能的薄,并且均匀一致。
因为塑料的热导率很低,导热性差,如果部分壁厚过厚,会造成热应力,导致塑料制品变形或开裂。
所以,在设计塑料制品的壁厚时,需根据使用场合、力学要求以及成本等因素进行综合考虑。
2、结构的可靠性和安全性设计结构时需充分考虑结构的可靠性和安全性,既要满足使用的要求,又要尽可能的减小结构的体积和材料消耗。
此外,结构设计时还应该考虑未来可能出现的一些异常情况,如使用环境的变化、超负荷的物理作用和力学应力等因素都应该在结构设计中进行考虑。
三、工艺控制优秀的结构设计标准是塑料制品质量保证的前提,但良好的生产工艺过程也是确保质量的关键。
生产过程中应该选择先进的生产工艺技术,如模具设计、注塑机选型和注射参数的调控等。
此外,应该做好产品的标准化、精细化生产和检验工作,以确保产品品质达到标准。
综上所述,塑料制品的结构设计对产品质量至关重要,必须遵循一定的规范和标准进行设计和制造。
同时,在生产过程中也需要遵循简单、精细、标准化、自动化和人性化原则。
一旦遇到质量问题,企业应该采取积极有效的措施,及时处理,以免造成不必要的损失和影响公司声誉。
塑料件设计准则
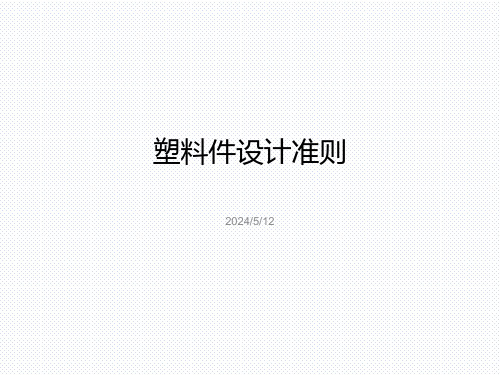
2024/5/12
目录
一. 壁厚均匀原则 二. 加强筋设计原则 三. 倒角原则 四. 拔模原则 五. 形状和结构的简化 六. 避免应力集中 七. 加强刚度的设计 八. 抗变形设计
一.壁厚均匀原则
• 在确定壁厚尺寸时,壁厚均一是一个重要原则。该原则主要是从工艺角度以 及由工艺导致的质量方面的问题而提出来的。均匀的壁厚可使制件在成型过 程中,熔体流动性均衡,冷却均衡。壁薄部位在冷却收缩上的差异,会产生 一定的收缩应力,内应力会导致制件在短期之内或经过一个较长时期之后发 生翘曲变形。
壳体/盒状体 一般≥1.5°;
皮纹面
细皮纹≥3.5° 粗皮纹≥5°
注:皮纹区域在设计数模前必须定义,由客户定义或我们定义客户确认,皮纹状态为客户输入,且必须输入
如出现客户未定义,皮纹面按5°执行,并与客户报警。
四 . 拔模原则
拔模角设计参考 塑胶产品在设计上通常会为了能够轻易的使产品由模具脱离出来而需要在边缘的内侧和外侧各设有一个倾斜角”出模角〔。 若然产品附有垂直外壁并且与开模方向相同的话,则模具在塑料成型後需要很大的开模力才能打开,而且,在模具开启後, 产品脱离模具的过程亦相信十分困难。要是该产品在产品设计的过程上已预留出模角及所有接触产品的模具零件在加工过程 当中经过高度抛光的话,脱模就变成轻而易举的事情。因此,出模角的考虑在产品设计的过程是不可或缺的 因注塑件冷却收缩後多附在凸模上,为了使产品壁厚平均及防止产品在开模後附在较热的凹模上,出模角对应於凹模及凸模 是应该相等的。不过,在特殊情况下若然要求产品於开模後附在凹模的话,可将相接凹模部份的出模角尽量减少,或刻意在 凹模加上适量的倒扣位。 出模角的大小是没有一定的准则,多数是凭经验和依照产品的深度来决定。此外,成型的方式,壁厚和塑料的选择也在考虑 之列。一般来说,高度抛光的外壁可使用1/8度或1/4度的出模角。深入或附有织纹的产品要求出模角作相应的增加,习惯上 每0.025mm深的织纹,便需要额外1度的出模角。
塑料件结构设计要点
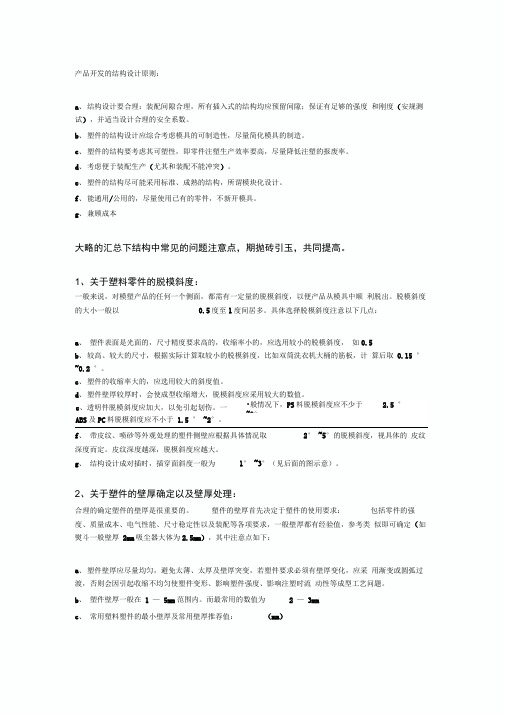
产品开发的结构设计原则:a、结构设计要合理:装配间隙合理,所有插入式的结构均应预留间隙;保证有足够的强度和刚度(安规测试),并适当设计合理的安全系数。
b、塑件的结构设计应综合考虑模具的可制造性,尽量简化模具的制造。
c、塑件的结构要考虑其可塑性,即零件注塑生产效率要高,尽量降低注塑的报废率。
d、考虑便于装配生产(尤其和装配不能冲突)。
e、塑件的结构尽可能采用标准、成熟的结构,所谓模块化设计。
f、能通用/公用的,尽量使用已有的零件,不新开模具。
g、兼顾成本大略的汇总下结构中常见的问题注意点,期抛砖引玉,共同提高。
1、关于塑料零件的脱模斜度:一般来说,对模塑产品的任何一个侧面,都需有一定量的脱模斜度,以便产品从模具中顺利脱出。
脱模斜度的大小一般以0.5度至1度间居多。
具体选择脱模斜度注意以下几点:a、塑件表面是光面的,尺寸精度要求高的,收缩率小的,应选用较小的脱模斜度,如0.5b、较高、较大的尺寸,根据实际计算取较小的脱模斜度,比如双筒洗衣机大桶的筋板,计算后取0.15 ° ~0.2 °。
c、塑件的收缩率大的,应选用较大的斜度值。
d、塑件壁厚较厚时,会使成型收缩增大,脱模斜度应采用较大的数值。
e、透明件脱模斜度应加大,以免引起划伤。
一•般情况下,PS料脱模斜度应不少于 2.5 °~3°,ABS及PC料脱模斜度应不小于1.5 ° ~2°。
f、带皮纹、喷砂等外观处理的塑件侧壁应根据具体情况取2° ~5°的脱模斜度,视具体的皮纹深度而定。
皮纹深度越深,脱模斜度应越大。
g、结构设计成对插时,插穿面斜度一般为1° ~3°(见后面的图示意)。
2、关于塑件的壁厚确定以及壁厚处理:合理的确定塑件的壁厚是很重要的。
塑件的壁厚首先决定于塑件的使用要求:包括零件的强度、质量成本、电气性能、尺寸稳定性以及装配等各项要求,一般壁厚都有经验值,参考类似即可确定(如熨斗一般壁厚2mm吸尘器大体为2.5mm),其中注意点如下:a、塑件壁厚应尽量均匀,避免太薄、太厚及壁厚突变,若塑件要求必须有壁厚变化,应采用渐变或圆弧过渡,否则会因引起收缩不均匀使塑件变形、影响塑件强度、影响注塑时流动性等成型工艺问题。
汽车塑料件结构设计的一般原则及精度

3 6
0.08 0.16 0.12 0.22 0.14 0.34 0.18 0.38 0.24 0.44 0.32 0.52 0.48 0.68
±0.12 ±0.22 ±0.16 ±0.26 ±0.24 ±0.34
6 10
0.09 0.18 0.14 0.24 0.16 0.36 0.20 0.40 0.28 0.48 0.38 0.58 0.58 0.78
下表 列出了常用的注射塑料的成型收缩率。 用无机填料填充、用玻璃纤维增强的塑料有较低的成型收 缩率。
41
6、注塑件的精度
42
②模具
6、注塑件的精度
对于小尺寸的塑料件,模具的制造误差占塑料公差的1/3。 与模具上运动的零件有关的塑件尺寸,其精度较低。 模具上浇注系统和冷却系统设计不当,会使成型塑件的 收缩不均匀。 脱模系统的作用力不当,会使被顶出塑件变形。
30
5、抗变形设计 防止变形的措施
前述的避免应力集中以及刚性设计的一些措施,也都有 助于防止或者降低制件的变形。此外,设计时考虑防止产品 变形,在形状上进行规避。
31
5、抗变形设计
矩形的薄壁容器的侧壁容易发生内凹变 形,为此可将侧壁设计得稍微外凸一些
32
5、抗变形设计
深度较浅的盒类制品,为避免翘曲变形, 可将其底边设计成倒角形状
后果:塑料是对缺口和尖角之类比较敏感的材料,在应 力作用下,这些部位会逐渐产生微细裂纹,随后逐步扩展到 大的裂纹,而裂纹的不断延伸终将导致制件的损坏。
17
3、避免应力集中原则
避免应力集中应作为一条基本的准则
避免应力集中最直接最有效的方法就是在拐角、棱边、 凹槽灯等轮廓过渡与厚薄交接处采用圆弧过渡。
5、抗变形设计
产品结构设计——塑胶件结构设计基本原则

——塑胶件结构设计基本原则塑胶件结构设计基本原则1.避免翘曲准则2.细长筋受拉准则3.避免内切准则4.避免尖锐棱角准则1.避免翘曲准则翘曲现象经常出现于塑料构件中,所以塑料件的结构设计应特别注意避免翘曲。
翘曲的主要原因是由于模塑成型过程中,构件冷却不均匀,产生内应力,引起翘曲变形。
造成冷却不均匀的原因主要有三种:(1)材料分布不均匀;(2)散热边界条件不均匀;(3)结构不对称。
1.避免翘曲准则壁厚不均匀的构件易出现却不均匀现象,从而导致构件翘曲变形。
在因构件本身功能要求的限制无法做到的情况下,应在两不同壁厚之间留有缓慢的过渡段。
不合理结构合理结构1.避免翘曲准则壁厚过大的塑件内部易产生空洞等缺陷,所以常设置加强筋提高构件的刚度。
过薄或过厚的加强筋也会导致构件的翘曲变形。
加强筋的壁厚要与底板壁厚相当,不要超过底板的壁厚。
不合理结构合理结构s 0.6s3s1.避免翘曲准则壁厚均匀的塑件也会产生翘曲变形,下图左侧的大平板从几何形状上来说完全均匀,但冷却不均匀;外部冷却快,内部冷却慢;板越大,不均匀越严重。
解决这个问题的方法是将平板改成拱板,下图右图所示,这样提高了板的抗弯刚度,从而有利于减少或消除构件的翘曲变形。
不合理结构合理结构1.避免翘曲准则另一种因冷却不均匀而产生翘曲变形的结构是带拐角的塑件。
拐角内外散热速度不一样,内慢外快。
解决的措施是加大内拐角的散热面积,改直角为倒角或设置一槽。
不合理结构合理结构2.细长筋受拉准则加强筋是塑胶件中的常见结构,一般比较细长。
塑料的弹性模量很低,所以易出现失稳问题,特别是细长结构。
应使细长筋尽量处于受拉状态。
不合理结构合理结构3.避免内切准则有内切结构无法直接脱模,必须用模芯或侧向抽芯机构,增大了模具制造的复杂性,从而增加了模具成本。
塑料件的结构设计应考虑到脱模的可能与方便,应避免有内切的结构。
下图左侧结构内外都有内切问题,即不可能用单一模具制作,从而增大模具的制造成本,其改进结构如右图所示。
塑胶产品结构设计准则

在塑胶件上开孔使其和其它部件相接合或增加产品功能上的组合是常用的手法,洞 孔的大小及位置应尽量不会对产品的强度构成影响或增加生产的复杂性, 常见孔的 类型如下:
孔离边位或内壁边之要点 :
confidential
16
四、塑胶产品结构设计准则-洞孔 (Hole)
盲孔设计要点: 盲孔是靠模具上的镶针形成,而镶针的设计只能单边支撑在模具上,因此很容易 被溶融的塑料使其弯曲变形,造成盲孔出现椭圆的形状,所以镶针的长度不能过长。 盲孔深度最大是直径的3倍,考虑模具镶针强度要求直径最小0.8mm。 外观件上的各种凹槽,如雕刻文字等,要求棱线分明,导致过渡太急,易产生气
confidential
12
三、塑胶产品结构设计准则-支柱 ( Boss )
对于外观件,当有螺丝柱子,需要进行缩水验证,依照上页图示意,塑胶壁厚 1.5 ,螺丝柱子外径3.4,验证结果 NG:(1.8-1.5)/1.5*100%=20% >8%。 外观面有可能会有缩水痕迹。
改善方案如下图:
当缩水验证NG时,可在增加火山口及加深螺丝孔深度来改善。 外观部品综合考虑缩水与螺丝柱子强度,塑胶壁厚要求大于1.3。 适当的辅以三角或十字加强筋方式,可大幅度提高强度和改善料流填充。
confidential
4
一、塑胶产品结构设计准则-壁厚
B. 转角位的设计准则亦适用於悬梁式扣位。因这种扣紧方式是需要将悬梁臂弯 曲嵌入,转角位置的设计图说明如果转角弧位R太小时会引致其应力集中系数 (Stress Concentration Factor)过大,因此,产品弯曲时容易折断,弧位R太大 的话则容易出现收缩纹和空洞。因此,圆弧位和壁厚是有一定的比例。一般 介乎0.2至0.6T之间,理想数值是在0.5T左右。
塑胶模具结构设计要点
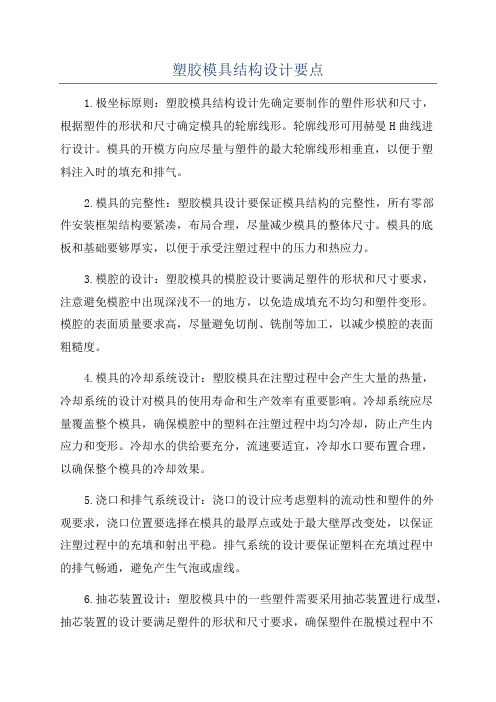
塑胶模具结构设计要点1.极坐标原则:塑胶模具结构设计先确定要制作的塑件形状和尺寸,根据塑件的形状和尺寸确定模具的轮廓线形。
轮廓线形可用赫曼H曲线进行设计。
模具的开模方向应尽量与塑件的最大轮廓线形相垂直,以便于塑料注入时的填充和排气。
2.模具的完整性:塑胶模具设计要保证模具结构的完整性,所有零部件安装框架结构要紧凑,布局合理,尽量减少模具的整体尺寸。
模具的底板和基础要够厚实,以便于承受注塑过程中的压力和热应力。
3.模腔的设计:塑胶模具的模腔设计要满足塑件的形状和尺寸要求,注意避免模腔中出现深浅不一的地方,以免造成填充不均匀和塑件变形。
模腔的表面质量要求高,尽量避免切削、铣削等加工,以减少模腔的表面粗糙度。
4.模具的冷却系统设计:塑胶模具在注塑过程中会产生大量的热量,冷却系统的设计对模具的使用寿命和生产效率有重要影响。
冷却系统应尽量覆盖整个模具,确保模腔中的塑料在注塑过程中均匀冷却,防止产生内应力和变形。
冷却水的供给要充分,流速要适宜,冷却水口要布置合理,以确保整个模具的冷却效果。
5.浇口和排气系统设计:浇口的设计应考虑塑料的流动性和塑件的外观要求,浇口位置要选择在模具的最厚点或处于最大壁厚改变处,以保证注塑过程中的充填和射出平稳。
排气系统的设计要保证塑料在充填过程中的排气畅通,避免产生气泡或虚线。
6.抽芯装置设计:塑胶模具中的一些塑件需要采用抽芯装置进行成型,抽芯装置的设计要满足塑件的形状和尺寸要求,确保塑件在脱模过程中不变形或损坏。
抽芯装置的操作要方便,可靠,要考虑到抽芯力和脱模力的大小,以确保抽芯的顺畅和模具的寿命。
7.快速更换系统设计:塑胶模具在生产过程中需要频繁更换不同的模腔,快速更换系统的设计能够极大地提高模具的使用效率和生产效率。
快速更换系统要求模腔结构尽量简单,易于拆卸和装配,以及固定方式的可靠性。
8.模具的加工工艺:塑胶模具的制作工艺要选择合适的材料和加工工艺,以确保模具的成型精度和表面质量。
塑料产品结构设计应注意事项(doc 17页)

塑料产品结构设计应注意事项(doc 17页)塑料产品结构设计注意事项1、塑料产品开发的结构设计原则⑴、结构设计要合理:装配间隙合理,所有插入式的结构均应预留间隙;保证有足够的强度和刚度(安规测试),并适当设计合理的安全系数。
⑵、塑件的结构设计应综合考虑模具的可制造性,尽量简化模具的制造。
⑶、塑件的结构要考虑其可塑性,即零件注塑生产效率要高,尽量降低注塑的报废率。
⑷、考虑便于装配生产(尤其和装配不能冲突)。
⑸、塑件的结构尽可能采用标准、成熟的结构,所谓模块化设计。
⑹、能通用/公用的,尽量使用已有的零件,不新开模具。
⑺、兼顾成本。
2、材料的选取⑴、ABS:高流动性,便宜,适用于对强度要求不太高的部件(不直接受冲击,不承受可靠性测试中结构耐久性的部件),如内部支撑架(键板支架、LCD支架)等。
还有就是普遍用在电镀的部件上(如按钮、侧键、导航键、电镀装饰件等)。
目前常用奇美PA-757、PA-777D 等。
⑵、PC+ABS:流动性好,强度不错,价格适中。
适用于作高刚性、高冲击韧性的制件,如框架、壳体等。
常用材料代号:拜尔T85、T65。
⑶、PC:高强度,价格贵,流动性不好。
适用于对强度要求较高的外壳、按键、传动机架、镜片等。
常用材料代号如:帝人L1250Y、PC2405、PC2605。
⑵、较高、较大的尺寸,根据实际计算取较小的脱模斜度。
⑶、塑件的收缩率大的,应选用较大的斜度值。
⑷、塑件壁厚较厚时,会使成型收缩增大,脱模斜度应采用较大的数值。
⑸、透明件脱模斜度应加大,以免引起划伤。
一般情况下,PS料脱模斜度应不少于2.5°~3°,ABS及PC料脱模斜度应不小于1.5°~2°。
⑹、带皮纹、喷砂等外观处理的塑件侧壁应根据具体情况取2°~5°的脱模斜度,视具体的皮纹深度而定。
皮纹深度越深,脱模斜度应越大。
⑺、结构设计成对插时,插穿面斜度一般为1°~3°。
塑料件结构设计准则(2)
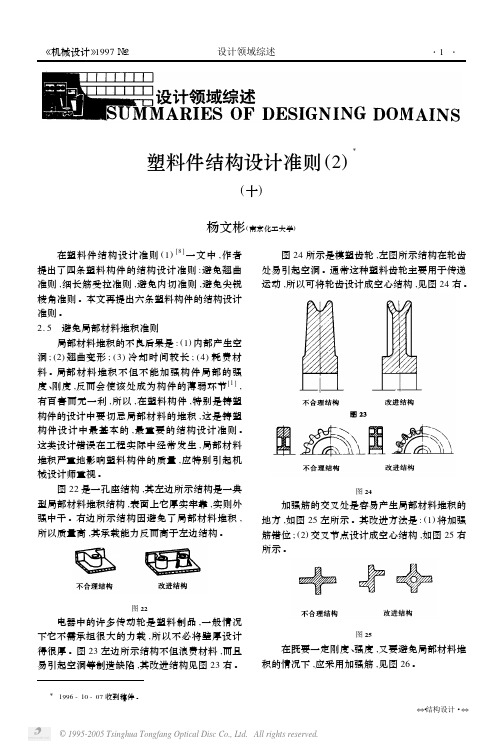
参考文献
图 43
2. 10 螺栓带衬板准则 螺栓连接是另一种常见的塑料件装配方式 。 塑料的强度比金属的强度低得多 ,通常不足以咬 紧螺丝 ,所以尖头螺丝不可直接嵌入塑料中 ,见图 44 所示 。此外 ,平头螺栓连接或铆接式连接也应 带面积较大的衬板 ,以资加大受力面积 ,从而减少 单位面积上的紧固压力 ,参见图 45 、46 和 47 。图
局部材料堆积不但不能加强构件局部的强度刚度反而会使该处成为构件的薄弱环节1有百害而无一利所以在塑料构件特别是铸塑构件的设计中要切忌局部材料的堆积这是铸塑构件设计中最基本的最重要的结构设计准则
《机械设计》1997 №2 设计领域综述
·1 ·
塑料件结构设计准则 (2) Ξ
(十)
杨文彬 ( 南京化工大学)
图 35
带有加强筋的塑料齿轮是一常见塑料制 品 。在啮合精度要求高的情况下 ,图 36 左所示结 构就不合理 ,因为非轴对称分布的加强筋会使齿 轮圆度精度下降 ,使齿轮圆实际上变成一个多边 形 ,其改进结构如图 36 右所示 。
图 36
两半模之间总是有一定的误差 ,所以 ,公 差要求高的部位应尽量放置于同一半模之中 ,见 图 37 右所示 。
31 和图 32 是壁厚太大导致表面倒塌的结构例子 及其改进措施 。
图 26
塑料平板常因刚度不足而设加强筋 ,这种结构平 板上易出现倒塌 ,倒塌正好发生在加强筋对面。 解决这一问题的方法 : (1) 开槽 ,避免局部材料堆 积 ,见图 27 ; (2) 加凸台 ,见图 28 和 29 。
图 32
表面倒塌也会发生在螺栓连接处 ,其原因是 塑料的弹性模量小 ,构件受力后已变形 。其防治 措施 :
(1) 加大壁厚 ; (2) 缩短螺栓 ,参见图生空洞 ,从而进一步引发 表面倒塌 ,其改进原则就是尽量将构件的壁厚设 计得小而匀 ,参见“最小壁厚准则”[1 ] 。图 30 、图
塑料产品结构设计准则

塑料产品结构设计准则
一、塑料产品结构设计方针
1、结构设计应得到实际使用要求,尽量简化结构,使其结构合理、操作简便、制造容易。
2、结构设计应根据使用要求,考虑产品的性能、外形和使用环境,满足产品质量要求。
3、产品的造型要美观大方,满足消费者的审美要求,使之自然统一
4、结构设计应满足模具设计要求,使用质量好、价格便宜的模具来加工熔模塑料件。
5、产品的结构设计要综合考虑材料、模具和模具制造等技术参数,在以上参数内寻求最佳的结构形式。
6、塑料产品的结构设计要考虑体积小、重量轻和低成本的要求,同时要求使用寿命长、性能稳定,力学结构强度要求高。
二、塑料产品结构设计要点
1、考虑材料的特性
塑料产品的结构设计要根据材料的物理特性,特别是在外力、温度负荷作用下,塑料件自身的变形、破坏和损伤等特性,来确定合理的结构形式、尺寸尺度和受力部位等要求。
2、考虑制造工艺
塑料产品的结构设计要根据熔模塑料件的制造工艺,满足模具结构的设计要求,充分发挥塑料的加工性能,力求产品尺寸精度高、表面光滑度强,实现质量稳定、成本低的目的。
塑料件壁厚的设计原则
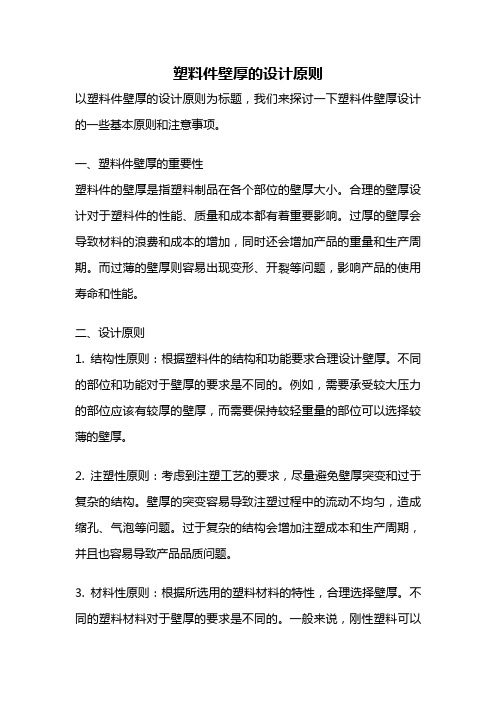
塑料件壁厚的设计原则以塑料件壁厚的设计原则为标题,我们来探讨一下塑料件壁厚设计的一些基本原则和注意事项。
一、塑料件壁厚的重要性塑料件的壁厚是指塑料制品在各个部位的壁厚大小。
合理的壁厚设计对于塑料件的性能、质量和成本都有着重要影响。
过厚的壁厚会导致材料的浪费和成本的增加,同时还会增加产品的重量和生产周期。
而过薄的壁厚则容易出现变形、开裂等问题,影响产品的使用寿命和性能。
二、设计原则1. 结构性原则:根据塑料件的结构和功能要求合理设计壁厚。
不同的部位和功能对于壁厚的要求是不同的。
例如,需要承受较大压力的部位应该有较厚的壁厚,而需要保持较轻重量的部位可以选择较薄的壁厚。
2. 注塑性原则:考虑到注塑工艺的要求,尽量避免壁厚突变和过于复杂的结构。
壁厚的突变容易导致注塑过程中的流动不均匀,造成缩孔、气泡等问题。
过于复杂的结构会增加注塑成本和生产周期,并且也容易导致产品品质问题。
3. 材料性原则:根据所选用的塑料材料的特性,合理选择壁厚。
不同的塑料材料对于壁厚的要求是不同的。
一般来说,刚性塑料可以选择较薄的壁厚,而柔性塑料需要选择较厚的壁厚以保证产品的强度和耐用性。
4. 结构强度原则:根据塑料件所需的强度和刚度要求,设计合理的壁厚。
一般来说,壁厚越大,产品的强度和刚度也越高。
但是过大的壁厚会导致产品重量增加和成本上升,因此需要在强度和成本之间进行权衡。
5. 工艺性原则:考虑到塑料件的成型工艺,尽量选择符合工艺要求的壁厚。
不同的成型工艺对于壁厚的要求是不同的。
一般来说,注塑成型工艺对于壁厚的要求相对较宽松,挤出和吹塑等工艺对于壁厚的要求相对较严格。
6. 经济性原则:在满足产品性能和质量要求的前提下,尽量选择较薄的壁厚以降低成本。
通过合理设计壁厚可以减少材料的使用量,降低成本。
三、注意事项1. 避免壁厚过于薄或过于厚,需要根据具体的产品要求和材料特性进行合理选择。
2. 尽量避免壁厚的突变和过于复杂的结构,以减少生产工艺问题和提高产品质量。
塑料制品的设计原则
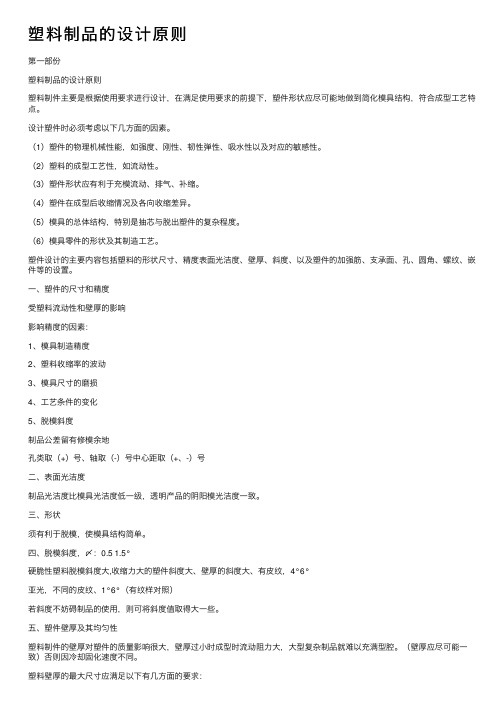
塑料制品的设计原则第⼀部份塑料制品的设计原则塑料制件主要是根据使⽤要求进⾏设计,在满⾜使⽤要求的前提下,塑件形状应尽可能地做到简化模具结构,符合成型⼯艺特点。
设计塑件时必须考虑以下⼏⽅⾯的因素。
(1)塑件的物理机械性能,如强度、刚性、韧性弹性、吸⽔性以及对应的敏感性。
(2)塑料的成型⼯艺性,如流动性。
(3)塑件形状应有利于充模流动、排⽓、补缩。
(4)塑件在成型后收缩情况及各向收缩差异。
(5)模具的总体结构,特别是抽芯与脱出塑件的复杂程度。
(6)模具零件的形状及其制造⼯艺。
塑件设计的主要内容包括塑料的形状尺⼨、精度表⾯光洁度、壁厚、斜度、以及塑件的加强筋、⽀承⾯、孔、圆⾓、螺纹、嵌件等的设置。
⼀、塑件的尺⼨和精度受塑料流动性和壁厚的影响影响精度的因素:1、模具制造精度2、塑料收缩率的波动3、模具尺⼨的磨损4、⼯艺条件的变化5、脱模斜度制品公差留有修模余地孔类取(+)号、轴取(-)号中⼼距取(+、-)号⼆、表⾯光洁度制品光洁度⽐模具光洁度低⼀级,透明产品的阴阳模光洁度⼀致。
三、形状须有利于脱模,使模具结构简单。
四、脱模斜度,〆:0.5 1.5°硬脆性塑料脱模斜度⼤,收缩⼒⼤的塑件斜度⼤、壁厚的斜度⼤、有⽪纹,4°6°亚光,不同的⽪纹、1°6°(有纹样对照)若斜度不妨碍制品的使⽤,则可将斜度值取得⼤⼀些。
五、塑件壁厚及其均匀性塑料制件的壁厚对塑件的质量影响很⼤,壁厚过⼩时成型时流动阻⼒⼤,⼤型复杂制品就难以充满型腔。
(壁厚应尽可能⼀致)否则因冷却固化速度不同。
塑料壁厚的最⼤尺⼨应满⾜以下有⼏⽅⾯的要求:1、⾜够的强度和刚度。
2、脱模时能经受脱模机构的冲击与震动。
3、装配时能承受紧固⼒。
热塑性塑料:制品壁厚增加⼀倍,冷却时间将增加四倍,使⽣产效率⼤⼤降低。
另外也影响产品质量,如易产⽣充⽓泡,缩孔,翘曲等缺陷。
热塑性塑料易于成型薄壁制件,能达⾄0.25mm,但⼀般不宜⼩于0.6-0.9mm,常取2-4毫⽶。
第三章_塑料制件设计原则2019

(4) 模塑通孔要求孔径比(长度与孔径的比值)要小些,
防止型芯受熔体冲击发生弯曲变形或折断。 (5) 当通孔孔径﹤1.5mm,由于型芯易弯曲折断,不适于
模塑成型。 (6)盲孔的深度: h ﹤(3~5)d d﹤1.5mm时, h ﹤3d
图3-27 异形孔设计实例
8 螺纹设计
塑件中的螺纹可用模塑方法成型出来,或切 削方法获得。
强制脱出的浅侧凹,尺寸应满足: (A-B)x100 %≦5%
C
图3-11 内部浅凸台塑件
强制脱出的浅侧凹,尺寸应满足: (A-B)x100 %≦5%
B
图3-12 内部浅侧凹塑件
强制脱出的浅侧凹,尺寸应满足: (A-B)x100 %≦5%
B
2 脱模斜度
塑件在模具型腔中的冷却收缩会使其紧紧包裹在型芯或 其他凸起部分,如图3-13所示。
对塑件的精度要求,要具体分析,根据装 配情况来确定尺寸公差。一般配合部分尺 寸精度高于非配合部分尺寸精度。小尺寸 易达到高精度。
尺寸和精度
1.塑件尺寸
塑件尺寸:指塑件的总体尺寸。
影响因素: (1)塑料的流动性(大而薄的塑件充模困难) (2)设备的工作能力(注射量、锁模力、工作台面)
注意事项: (1) 对流动性差的塑料和薄壁制件,尺寸不能设计 过大,否则容易造成充填不足或形成冷接缝。 (2) 塑件尺寸设计要进行流动距离比校核,还需对 注射机的相关参数进行校核(如注射量、锁模力、工 作台面尺寸)。
图3-3 侧孔变侧凹
(a) 侧孔件成型凹模
(b) 侧凹件成型凹模
图3-4 成型凹模
图3-5 模具开模示意图
图3-6 侧孔形状的变化 图3-7 变化后的模具
塑件的内外侧凸凹形状较浅并允许带有园角,可以采用强 制脱模方式脱出塑件,塑件在脱模温度下应具有足够的弹性 (PE、PP、POM)。
- 1、下载文档前请自行甄别文档内容的完整性,平台不提供额外的编辑、内容补充、找答案等附加服务。
- 2、"仅部分预览"的文档,不可在线预览部分如存在完整性等问题,可反馈申请退款(可完整预览的文档不适用该条件!)。
- 3、如文档侵犯您的权益,请联系客服反馈,我们会尽快为您处理(人工客服工作时间:9:00-18:30)。
可怜得机械狗之塑料件结构设计基本原则(一)
一,产品结构设计前言
正式进入话题之前,咱先抱怨两句,机械工程得待遇可真不咋地,奉劝想要进入机械行业得童鞋们三思后行。
待遇低,工作环境差就算了,可美女咋也凤毛麟角呢!都说机械好就业, 工作稳主,可那初始工资頁•就是没得说,就说自己刚毕业时,每月2000块,去厂房里做装配工, 铁块在手里滚来滚去,整天脏兮兮得,还累得跟狗一样。
可相比较其她呢,那些学计算机得,学财务,学管理得,那待遇真就是没法比,想我当时就就是因为瞧这个专业名字好听,就跳坑里了。
虽然这个说,可梦想仍在,咱还就是要向着那里疋着,一点一点地疋。
进入正题,在玩具,消费类电子产品,大小家电,汽车等相关行业中,都离不开产品得结构设计,各■种有形得产品,配件等都必须先确泄其外形,所以就是产品结构设计就是产品研发阶段得核心之一。
就拿消费类电子产品来说,结构,硬件,软件就是产品研发得三个主要工作团体, 而硬件与结构又就是结合最紧密得。
一般公司要研发一款产品,首先就是市场部签发开发指令,经过部门评审后,研发部开始进行结构外观建模,然后再进行建模评审,评审通过后,才开始内部得结构设计,然后才就是做手板,开模,试模,试产,量产等。
而其中得内部结构设讣就就是产品结构设计师最主要得工作内容。
在我国,工业外观设il•跟结构设il•就是分开得,就就是说决左产品初步外观得并不就是机构工程师,而就是工业设计师,她们会依照市场调差与基本得性能需要去绘制产品得外观,这个当然需要一运绘画艺术与审美能力。
可怜大多说人都怀疑作为理工科得结构工程师欠缺这些细胞,可事实好像也就是这样。
最近接手国外得一个充电器产品,就是她们已经做好了3D 图,要我们来开模生产,可就是拿到手后根本开不了膜,不符合开模要求,当然做个样品可以用3D打印做出来,可想要大批量得还就是要靠传统模具。
这体现了结构工程师得作用了,尽可能保证产品用料,外观,性能,工艺,装配得最佳化,就就是在各个环节省钱省时省力,想想就够累得啊!
二,塑料件料厚
我们接触得很多产品就是塑料件,其大部分塑料件都就是通过塑胶模具注塑成型,而料厚就是塑料件最基本得设计要求。
1,塑料件料厚可依摇产品外形尺寸来选择,一般范围0、6~6、0mm,常用范用1、5mm~3、
0mm。
小型产品(小于80mm)—般料厚选1、0~1、4mm.中型产品(80mm~200mm Z间)一般料厚
选1、4~2、0mm,大型产品(大于200mm)选2、0mm~6、0mm.依据材质不同略微有所调整。
当然我
们不一>^按着这个规楚来,要根据实际情况来设计,最好就是问一下做模具得厂商,她们对自己得工
艺最了解,对于可不可行,她们最有发言权。
2.塑料件料厚尽量均匀,不均匀可能引起变形、局部凹陷等不良,当然,不可能毎个产品全就
是统一料厚,在料厚变换得地方,我们需要均匀过度,以方便塑料溶体得流动,避免^^^力集中。
三,塑料件得脱模斜度
脱模斜度得设立就就是为了顺利脱模,与于产品得外观、材料、外形尺寸等有关,具体可以概括为:产品得外观要求高、精度高、表而光亮、尺寸大得,脱模斜度要小。
产品外形粗糙、外形复杂、塑料溶体流动性差、料厚大、收缩率大、透明得塑料件,脫模斜度要大。
实际工作中,重要配合面拔模斜度要给出,其她如筋位等不重要得而无需给出,模具设计师自己会加上。
1,产品外观以大端为基准,斜度采用减胶拔模方向向小端取得。
(如下图)
4■特殊情况,可一侧减胶一侧加胶。
四,塑料件得圆角设计
圆角得设il 就是为了提高产品强度,避免应力集中与便于脱模。
1•无特殊要求时,过度圆角由产品料厚决企,内侧圆角取0、5卜1、5说为产品料厚)。
劭///722L
2■内孔以小端直径为基准,斜度采用减胶拔模方式向扩大方向取得。
(如下图)
村直径-
3•筋位以大端为基准,斜度采用减胶拔模方向向小端取得。
(如下图)
2, 为保持产品料厚均匀,外拐角圆角半径等于内圆角半径加上料厚。
3, 产品得分型而上不能有鬪角,会增加模具费用,外观也会不良。
4产品外观而不能有尖角利边,要做圆角处理。
以上最小圆角半径不要小于0、3mm 。
五,塑料件加强筋设计
设计加强筋能增加塑料件得强度与刚度,可防止产品变形,也有助于塑料溶体得流动。
1•加强筋设计要求:
大端厚度A 取值0. 4X0、61—般取0、5to 加强筋高度B-般不大于31。
两加强筋距离C -般不小于4t 。
加强筋离表面距离D —般不小于1mm.
2.螺终柱加强筋:
当螺丝柱过高或者受力时,需要要给螺丝•柱加加强筋。
六,塑料件上文字.图案设计及塑料件支撑面设计
1•塑料产品上得文字或者图案有凹凸两种,但最好采用凸出表而得方式,这样会使模具容 易加
工。
如果文字图案不允许突出表而(为保持表而平成)时,可先在产品表而凹去一块,再在加强筋平而宽度A 不小于0. 5mm 。
加强筋底部宽度B 就是螺丝柱高度得0、2~0、5倍。
加强筋表而离柱顶距离C 不小于1、0mm 。
凹下得这块凸出文字•
两字符间距B不小于0、4mm。
字符离边缘得距离C、D不小于0、6mim
2,塑料件得底面来支撑产品重呈,如果使用平而就不利于底部得平整,特别对一些大尺寸产品很不利。
所以要设il•一些凸边或者凸台,再或者贴上脚垫来支撑。
支撑而尺寸高度一般取0、
3mm~2、0mm。
七,塑料件孔得设计
孔分为圆孔与非圆孔,要注意孔得位置,减少模具加工难度。
1 •孔设计一般要求:
D
孔之间得距离A不小于D(Dv3、0mm),或者A取0. 7D(D>3、0mm)。
孔距边得距离B不小于D。
2•孔径与孔深得关系(非螺丝柱孔):
>1
盲孔深度A 不大于5D 。
通孔深度B 不大于10D 。
3•螺丝头孔得选用:
螺丝头孔优先选用(a),如果特殊需要,比如表而要就平整得产品,选用了平头螺丝,螺丝孔选用 (b),锥形而低于端面不小于0、
5mm.
JCa)
I
4 i。