材料成形工艺学-钢管轧制
钢管生产工艺流程
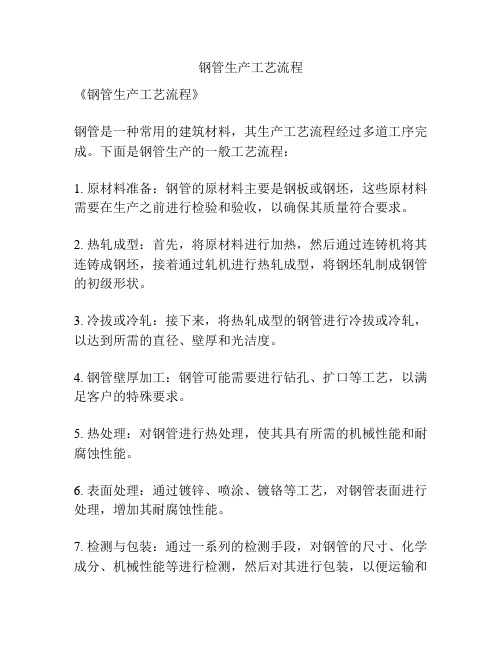
钢管生产工艺流程
《钢管生产工艺流程》
钢管是一种常用的建筑材料,其生产工艺流程经过多道工序完成。
下面是钢管生产的一般工艺流程:
1. 原材料准备:钢管的原材料主要是钢板或钢坯,这些原材料需要在生产之前进行检验和验收,以确保其质量符合要求。
2. 热轧成型:首先,将原材料进行加热,然后通过连铸机将其连铸成钢坯,接着通过轧机进行热轧成型,将钢坯轧制成钢管的初级形状。
3. 冷拔或冷轧:接下来,将热轧成型的钢管进行冷拔或冷轧,以达到所需的直径、壁厚和光洁度。
4. 钢管壁厚加工:钢管可能需要进行钻孔、扩口等工艺,以满足客户的特殊要求。
5. 热处理:对钢管进行热处理,使其具有所需的机械性能和耐腐蚀性能。
6. 表面处理:通过镀锌、喷涂、镀铬等工艺,对钢管表面进行处理,增加其耐腐蚀性能。
7. 检测与包装:通过一系列的检测手段,对钢管的尺寸、化学成分、机械性能等进行检测,然后对其进行包装,以便运输和
使用。
通过以上工艺流程,钢管的生产就完成了。
这些工艺流程的质量控制和技术创新,对于生产高品质的钢管具有重要意义。
钢管的生产工艺流程

钢管的生产工艺流程钢管是一种广泛应用于各个领域的金属制品,使用领域包括建筑、石油、天然气、化工、电力、交通等。
钢管的生产工艺流程经历了多个步骤,下面将详细介绍钢管的生产工艺流程。
第一步:材料准备首先,需要准备合适的原材料,一般选择优质的钢坯作为原料。
钢坯可以通过多种方式生产,例如连铸、轧制等。
在准备原材料的过程中,还需要对钢坯进行化学成分分析,确保其符合生产要求。
第二步:加热坯料将准备好的钢坯送入前处理工序中,通过加热的方式将钢坯加热到一定温度。
加热的目的是为了改善钢坯的塑性,便于进行下一步的成型工艺。
第三步:轧制成型经过加热处理的钢坯送入轧机中进行轧制。
根据不同的产品要求,可以采用不同类型的轧机,例如热轧机、冷轧机等。
轧制的目的是将钢坯塑型成所需的形状和尺寸,形成初步的钢管。
第四步:穿孔经过轧制成型的钢管需要进行进一步的加工,首先是穿孔。
穿孔可以使用多种方式进行,例如经过连续穿孔机的连续穿孔、压力等。
穿孔的目的是将钢管中心的孔洞形成所需的尺寸和形状。
第五步:轧制管材穿孔完成后,钢管需要再次送入轧机进行管材的轧制。
这一步骤主要是将管材的外径、厚度进行精确控制,以满足不同应用场合的需求。
轧制管材的方式通常是采用冷轧或者热轧工艺。
第六步:酸洗和冷却经过轧制的钢管会有一层氧化皮,需要进行酸洗处理以去除。
酸洗的目的是清除钢管表面的氧化皮和杂质,使钢管表面光滑,便于后续的加工。
完成酸洗后,钢管需要进行冷却处理,以使其达到所需的机械性能。
第七步:继续轧制经过酸洗和冷却处理后,钢管再次进入轧机,继续轧制。
这一步骤通常被称为成形轧制,目的是进一步改善钢管的形状和尺寸,使其更加精确。
第八步:终轧和校直继续轧制后,钢管进入终轧机,通过多次轧制使钢管的外径和内径达到精确控制的尺寸。
完成终轧后,钢管需要进行校直处理,以消除轧制过程中产生的偏差,使钢管的形状更加直线。
第九步:涂层和测试经过校直后的钢管需要进行涂层处理,以提高钢管的耐腐蚀性能。
钢管生产过程(3篇)

第1篇一、引言钢管作为一种重要的金属材料,广泛应用于建筑、交通、能源、机械制造等领域。
钢管的生产过程涉及到多个环节,包括原料准备、炼钢、轧钢、矫直、切割等。
本文将详细介绍钢管的生产过程。
二、原料准备1. 原料来源钢管的主要原料是铁矿石、焦炭和石灰石。
铁矿石是炼铁的主要原料,焦炭用于高炉炼铁,石灰石用于去除铁水中的杂质。
2. 原料处理(1)铁矿石:铁矿石经过破碎、磨粉、筛选等工序,得到一定粒度的铁矿石。
(2)焦炭:焦炭经过破碎、筛分等工序,得到一定粒度的焦炭。
(3)石灰石:石灰石经过破碎、磨粉、筛分等工序,得到一定粒度的石灰石。
三、炼钢1. 高炉炼铁高炉炼铁是将铁矿石、焦炭和石灰石等原料在高温下进行还原反应,得到生铁。
高炉炼铁的主要设备包括高炉、鼓风机、除尘器等。
2. 炼钢炼钢是将生铁和废钢在转炉、电炉或平炉中熔化,去除杂质,得到钢水。
炼钢的主要设备包括转炉、电炉、平炉等。
四、轧钢1. 轧制工艺轧钢是将钢水通过轧机轧制成一定规格的钢材。
轧制工艺包括粗轧、中轧、精轧等。
(1)粗轧:粗轧是将钢坯轧制成一定厚度的钢带。
(2)中轧:中轧是将钢带轧制成一定规格的钢管。
(3)精轧:精轧是将钢管轧制成最终规格。
2. 轧钢设备轧钢设备主要包括轧机、加热炉、冷却装置等。
(1)轧机:轧机是轧钢的核心设备,分为板带轧机和钢管轧机。
(2)加热炉:加热炉用于加热钢坯,使其达到轧制温度。
(3)冷却装置:冷却装置用于冷却轧制后的钢材,使其达到规定温度。
五、矫直矫直是将轧制后的钢管进行矫直处理,消除其弯曲、波浪等缺陷。
矫直设备主要包括矫直机、冷却装置等。
六、切割切割是将矫直后的钢管按照客户需求进行切割。
切割设备主要包括切割机、输送带等。
七、表面处理钢管生产完成后,需要对钢管表面进行处理,以提高其表面质量。
表面处理主要包括清洗、酸洗、磷化、涂层等。
八、包装钢管生产完成后,需要进行包装,以便运输和储存。
包装方式包括卷筒包装、散装包装等。
(金属轧制工艺学)1轧制工艺基础
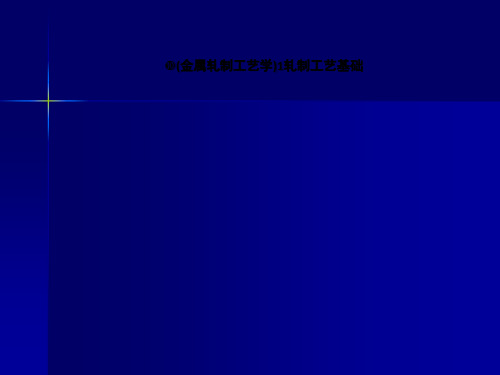
2020/7/22
24
型钢生产系统
型钢生产系统的规模往往并不很大。就 其本身规模而言又可分为大型、中型和 小型三种生产系统。
➢一般年产100万t以上的可称为大型的系统; ➢年产30万t~100万t的为中型的系统; ➢年产30万t以下的可称为小型的系统。
2020/7/22
25
混合生产系统
在一个钢铁企业中可同时生产板带钢、 型钢或钢管时,称为混合系统。
现代化的轧钢生产系统向着大型化、连续化、 自动化的方向发展,生产规模日益增大。
近年来大型化的趋向已日见消退,而投资省、 收效快、生产灵活且经济效益好的中、小型钢 厂在很多国家中却有了较快的发展。
2020/7/22
27
碳素钢的生产工艺流程
碳素钢生产工艺流程一般可分4个基本类型:
➢(1)采用连铸坯的工艺过程
➢按用途来分:
常用型钢(方钢、圆钢、扁钢、角钢、槽钢、 工字钢等)和专用型钢(钢轨、钢桩、球扁钢、 窗框钢等)。
➢按其断面形状:
简单断面型钢和复杂或异型断面型钢。
2020/7/22
9
轧材种类
型线材
➢按生产方法:
轧制型钢、弯曲型钢、焊接型钢。
➢用纵轧、横旋轧或楔横轧等特殊轧制方法 生产的各种周期断面或特殊断面钢材,又 分为:
28
碳素钢的生产工艺流程
➢ (3)采用铸锭的中型生产系统的工艺过程
其特点是:一般有Ø650~Ø900二辊或三辊开坯机,通常 采用冷锭作业及二次(或一次)加热轧制方式,这种工艺 流程不仅用来生产碳素钢材,也常用以生产合金钢材。
➢ (4)采用铸锭的小型生产系统的工艺过程
其特点是:通常在中、小型轧机上用冷的小钢锭经一次 加热轧制成材。所有采用铸锭的生产工艺都是落后的, 已经或将要遭到淘汰。
《压制钢管成型加工》课件

02 成型方法
根据不同的工艺要求,可以采用不同的成型方法 ,如弯曲成型、拉伸成型和压缩成型等。
03 成型设备
成型设备主要包括压机、模具和辅助设备等。
表面处理技术
表面处理的目的
提高钢管的耐腐蚀性、耐 磨性和美观度等。
表面处理工艺流程
02
压制钢管成型加工技术
压制工艺
01 工艺原理
通过施加外力,使金属板料在模具内产生塑性变 形,从而获得所需形状和尺寸的钢管。
02 工艺流程
包括板料剪切、压制前准备、压制成型、脱模和 后处理等步骤。
03 工艺参数
压制过程中需要控制的主要参数包括模具温度、 压力、时间以及润滑等。
成型技术
01 成型原理
新材料应用
探索和研发新型材料,提高钢管的性能和品质,满足更高要求的应 用场景。
工艺优化与改进
持续优化生产工艺,提高产品质量和稳定性,降低不良品率。
环保与节能要求
绿色生产技术
推广环保生产技术,降低生产过程中的能耗和排放,实现绿色可 持续发展。
资源循环利用
提高废旧钢管的回收利用率,减少资源浪费,降低对环境的影响。
THANKS
感谢观看
案例一:某大型工程项目的管道压制加工
总结词
大型工程项目、复杂管道系统
详细描述
该案例介绍了某大型工程项目中,如何采用压制钢管成型技术,加工出满足工程需求的复杂管道系统。涉及的工 艺流程、材料选择、设备配置以及质量检测等方面的详细说明。
案例二:高精度薄壁钢管的压制成型
总结词
高精度、薄壁钢管
详细描述
该案例探讨了如何通过精密的压制工艺,生产出高精度薄壁钢管的过程。重点 介绍了材料选择、模具设计、压制参数设定以及后处理等方面的关键要素。
《钢管轧制》课件
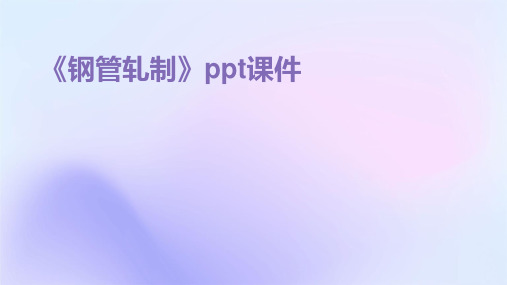
冷却设备的种类较多,根据冷却方式的不同可以分为多种类型,如水 冷、风冷、油冷等。
03
冷却设备的技术参数包括冷却速度、冷却均匀性等,这些参数的选择 直接影响钢管的性能和质量。
04
为了确保冷却设备的正常运行和钢管的质量,需要定期对冷却设备进 行维护和保养,检查冷却介质的质量和流量。
其他辅助设备
其他辅助设备包括矫直机、剪切机、检验设备等,这些 设备在钢管轧制过程中起到重要的辅助作用。
加热炉的性能参数包括加热速 度、温度均匀性、燃料消耗等 ,这些参数直接影响钢管的轧 制质量和生产效率。
为了确保加热炉的稳定运行和 钢管的质量,需要定期对加热 炉进行维护和保养,检查炉衬 、燃烧器等关键部件。
轧机
轧机的种类也较多,根据用途和结构可以分为 多种类型,如二辊轧机、三辊轧机、多辊轧机
等。
为了确保轧机的正常运行和钢管的轧制质量,需要定 期对轧机进行维护和保养,检查轧辊、轴承等关键部
冷却
冷却方式
选择适当的冷却方式,如自然冷却、 水冷等,以控制钢管的冷却速度和组 织转变。
冷却工艺参数
冷却效果检测
对冷却后的钢管进行质量检测,确保 冷却效果符合要求。
根据钢管的材质和规格设定合理的冷 却工艺参数,如冷却时间、水温等。
矫直与切头尾
矫直目的
通过矫直工序消除钢管在轧制过 程中产生的弯曲和扭曲。
矫直设备
选用适合钢管矫直的设备,如矫 直机。
切头尾
切除钢管的两端不规则部分,保 证产品长度和外观质量。
03
钢管轧制设备
加热炉
加热炉是钢管轧制过程中的重 要设备之一,其主要功能是将
钢坯加热至轧制所需温度。
加热炉的种类繁多,根据燃料 和加热方式的不同可以分为多 种类型,如燃气加热炉、电加
无缝钢管的轧制

硬度检测
检测无缝钢管的硬度,以评估其材料的硬度和工艺处理效果。
06
无缝钢管的未来发展与 挑战
新技术应用
01
自动化和智能化技术
02
新材料应用
随着工业4.0和智能制造的发展,无缝 钢管轧制过程将更加自动化和智能化 ,提高生产效率和产品质量。
随着新材料技术的不断发展,新型材 料如高强度、高耐腐蚀性、高导电性 等材料将逐渐应用于无缝钢管的生产 中,满足更广泛的应用需求。
03
高效轧制技术
研究和发展更高效的轧制技术,如高 速轧制、低温轧制等,以降低能耗和 减少生产成本。
环保要求
严格的环境法规
随着全球环保意识的提高,各国政府将制定更为严格的环保法规, 要求无缝钢管行业降低污染排放和提高资源利用率。
绿色生产技术
无缝钢管企业需要积极推广和应用绿色生产技术,如废气处理、废 水循环利用等,以实现清洁生产和可持续发展。
根据无缝钢管的用途和要求选 择合适的表面处理方法
外观检测
01
02
03
表面质量
检查无缝钢管表面是否光 滑、无划痕、无裂纹、无 气泡等缺陷。
颜色均匀性
检查无缝钢管的颜色是否 均匀一致,无明显色差。
弯曲度
检查无缝钢管的直线度和 弯曲度,确保满足工艺要 求。
轧辊调整
轧辊间距
01
根据不同规格和工艺要求,调整轧辊间距,确保钢管的壁厚和
直径符合标准。
轧辊硬度
02
选择合适的轧辊硬度,以适应不同材质和规格的钢锭,提高轧
制效率和产品质量。
轧辊平衡
03
确保轧辊在高速旋转时保持平衡,减少振动和噪音,延长轧辊
使用寿命。
03
无缝钢管的轧制过程
钢管制造工艺流程

钢管制造工艺流程一、原料准备阶段钢管制造的第一步是原料准备阶段。
钢管的主要原料是钢板或钢坯。
在这个阶段,首先需要对原材料进行质量检测,确保原材料符合生产要求。
然后,对原材料进行切割、修整和去除表面缺陷等处理,以确保原材料的质量和尺寸符合要求。
二、加热和穿孔阶段在原料准备完成后,进入加热和穿孔阶段。
这个阶段的目的是将原料加热到一定温度,使其变得易于加工。
加热通常使用高频感应加热或火焰加热。
加热后,原料被送入穿孔机进行穿孔。
穿孔是将原料中心部分打通的过程,以形成管状。
三、管坯轧制阶段穿孔完成后,进入管坯轧制阶段。
管坯轧制是将穿孔后的管坯通过轧机进行加工,使其形成所需的外径和壁厚。
在这个阶段,管坯经过多次轧制和拉拔,逐渐减小直径并调整壁厚,以达到所需的尺寸和精度。
四、管坯拉拔阶段管坯轧制完成后,进入管坯拉拔阶段。
在这个阶段,管坯通过拉拔机拉伸,使其形成更长的管材。
拉拔过程中,利用轧制机构的作用,将管坯逐渐拉伸并减小直径,以获得所需的尺寸和表面光洁度。
五、管材成型阶段管坯拉拔完成后,进入管材成型阶段。
在这个阶段,通过不同的成型机构,将拉拔后的管材进行成型,如焊接成型、冷拔成型等。
成型过程中,管材的表面经过清洗和除锈处理,以确保管材的表面质量。
六、管材热处理和调质阶段管材成型完成后,进入管材热处理和调质阶段。
在这个阶段,通过加热和冷却等控制工艺,对管材进行热处理和调质处理,以改善其力学性能和耐腐蚀性能。
七、管材表面处理阶段管材热处理和调质完成后,进入管材表面处理阶段。
在这个阶段,对管材表面进行抛光、喷砂、喷涂等处理,以提高管材的表面质量和外观。
八、管材检测和质量控制阶段管材表面处理完成后,进入管材检测和质量控制阶段。
在这个阶段,对管材进行各项检测,如化学成分分析、力学性能测试、无损检测等,以确保管材的质量符合要求。
同时,对管材进行尺寸检测和外观检查,以确保管材的尺寸和外观符合标准要求。
九、管材包装和运输阶段管材检测和质量控制完成后,进入管材包装和运输阶段。
《钢管轧制》ppt课件
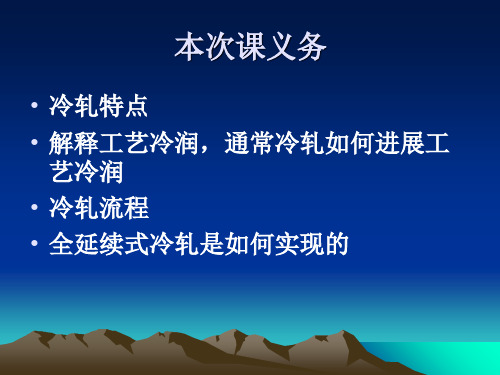
电阻焊
焊缝结合方式
二、炉焊
• 对接炉焊法:管坯〔短钢带〕切角翻转——加热——去炉 渣与氧化皮——漏斗模弯卷焊接——定径——矫直
• 消费直径小于60mm的焊管。 • 延续炉焊法:带钢——开卷——边部加热——吹边——成
型——焊接——轧制——剪切成定尺 • 适用于消费大批量小直径焊管。
送进角:使 轧件既旋转 又前进
碾轧角:决议孔型 尺寸,调理变形过 程和钢管尺寸
轧制过程:芯棒插入穿孔后的毛管中——抽出芯 棒——回炉加热——减径或定径〔回转定径机〕
轧制特点:内外表平滑;外径与壁厚尺寸精度高而均匀,适宜消 费高精度¢40~200,壁厚4~50mm的碳素钢合金钢高合金钢
四、顶管机组
• 工艺流程:热轧方坯——加热——水压机冲成杯 型毛管——退出冲头推出毛管——加热——顶管 机顶管——均整——抽掉芯棒——锯切毛管底 部——定径——精整
送
阶 段
进 及 翻
转
咬
阶 段
入 及 轧
制
定
阶 段
径 及 终
轧
3、工艺流程:主要消费石油工业用 大直径厚壁管
• 小锥度钢锭或多边形钢锭 • 轧制或锻坯〔¢140以下〕
清理——加热—
穿孔——周期轧管机轧管——切头尾——回炉加热——定径——精整
• 二、延续式轧管机组 • 轧制设备 7~9架二辊成90度布置的不可逆连轧管机 ,
第二节 自动轧管机组的工艺及设备
剪断机 定心车床
环形加热炉
热定心机 穿孔机 自动轧管机
1剪断—— 2冷定心—————— 3加热——4热定心——5穿孔——6轧管—— 7均整——8定径——9废品管——————10冷却——11矫直——精整—入库
轧制工艺学

1管钢:大部分为圆,按成型方式分。
板带钢:板、带按宽度分。
规格按厚度分。
2管钢分类:1热加工管(无缝钢管):热轧穿孔、挤压、P.P.M(压力穿孔)、冲压法;2焊管(有缝钢管):包括直缝钢管与螺旋焊管3冷加工管:冷轧、冷拔和冷旋压3钢管生产的基本方法:热轧无缝管:实心管坯.穿孔.延伸.定(减)径.冷却.精整焊管:板带坯料.成型(管状),焊接成管.精整连轧管机组:坯料加热.热定心.穿孔.空减连轧.切头.尾.再加热.高压水除鳞.张力减径冷却.切头尾.矫直.无损探伤.表面检查入库4坯料的截断方式一般有四种:1剪断:适用中小断面的管坯,生产效率高,费用低,但管坯易被压扁2火焰切割:适合大断面、合金钢等管坯,操作方便,费用低,但金属损耗大(烧损、氧化),断面质量差3折断:适合Dp>φ140mm或σb>60Kg/mm2管坯。
⑷锯断:适合小断面管坯,合金钢及高合金钢等;是切断质量最好的方法。
5管坯加热:加热目的:提高塑性,降低变形抗力,为穿孔和轧管准备良好的加工组织,改善金属的性能。
坯料加热遵循三个原则:1温度准确,确保可穿性最好的温度2加热均匀,纵向、横向都均匀,内外温差不大于30~50℃,最好小于15℃3烧损少,并且不产生有害的化学成分变化(C↑或C↓) 6环形加热优缺点:优点1适合加热圆形管坯,适应多种不同直径和长度的复杂坯料;2管坯加热时间短、受热均匀、加热质量好;3炉底转动,坯料与炉底无相对滑动,氧化铁皮不易脱落,且炉子装出料炉门在一侧,密封好,冷空气吸入少、氧化铁皮少4管坯放置位置灵活(可放料也可空出),便于更换管坯规格,操作灵活5机械化和自动化程度高。
缺点1炉子占用车间面积大2管坯在炉底上呈辐射状间隔布料,炉底面积的利用较差3炉子结构复杂,维修困难,造价高。
7管坯定心:1管坯定心:是指在管坯前端面钻孔或冲孔2定心目的:使顶头鼻部正确地对准管坯轴线,防止穿孔时穿扁;减小毛管壁厚不均;改善二次咬入条件3定心方式:a:热定心:效率高,应用广;b:冷定心:效率较低,仅用于穿孔性能较差的钢材,如高合金钢、高碳钢及重要用途的钢材。
《材料成形工艺学》大作业

《材料成形工艺学》大作业题目:解析无缝钢管二辊斜轧穿孔过程中轧件运动特点以及孔腔形成机理作业内容无缝钢管轧制过程中二辊斜轧穿孔,斜轧轧制方式、轧辊形式为桶形辊,轧辊在水平面左右布置,固定不动导板在上下布置,中间为随动顶头、轧辊轴线与轧制线在过轧制线主垂直平面上倾斜成送进角为β,轧辊旋转速度为u,如图1所示。
图2为各类斜轧运动方式示意图。
图1:二辊斜轧穿孔过程示意图图2:斜轧运动方式示意图 利用平面解析方法或其他方法解析斜轧穿孔过程中轧件运动方式(旋转和前进方向)、穿孔过程中孔腔形成机理和影响因素。
(a ) (c ) (b )(d )一、孔腔形成机理1、切应力理论分析:将二辊斜轧穿孔简化为平锤锻压方坯模型。
图1:在“锻造十字”区金属的流动方向(a)锤头在A区压缩;(b)锤头在B区压缩当平锤头锻压方坯时(图1(a)),由于锤头接触表面上外摩擦的作用,使坯料A区处于三向压应力状态,成为难变形区,在压缩时该区沿垂直方向移动,且带动与它相邻的a区金属沿箭头方向移动。
B区处于变形体的外侧受摩擦影响很小,又没有其他部分的阻碍,因此在压缩时B区金属向横向移动,带动它邻接的b区沿与a区相反方向移动。
于是在坯料对角线方向产生了金属的激烈错动。
当翻转90 压缩时(图1(b)),a、b区金属产生沿相反方向的错动,于是在激烈地反复错动下,便沿坯料对角线方向产生疲劳开裂,最终形成孔腔。
2、正应力理论分析:将二辊斜轧穿孔简化为平锤锻压圆坯模型。
如图2所示,用平锤头锻压圆坯时,假如没有外端(指接触变形区abcd以外的两个弓形区aAb、cCd),则可不受限制地产生双鼓变形(图2(a)中虚线所示)。
实际上由于外端的作用,而使心部受到大的水平拉应力的作用,当此应力超过材料的断裂应力时,就会在心部产生与拉应力方向垂直的裂口,(如图3(a)所示1-1裂口)。
当翻转90°锻压时,便会产生如图3(b)所示的2-2裂口。
如果继续旋转锻造便会形成如图3(c)所示的孔腔。
冷轧钢管生产工艺
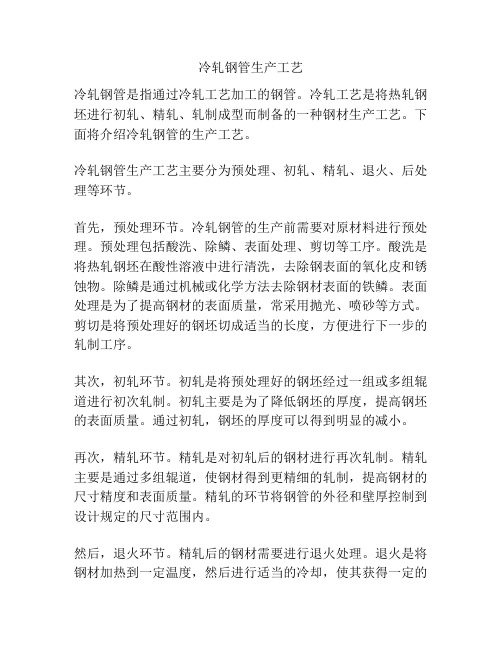
冷轧钢管生产工艺冷轧钢管是指通过冷轧工艺加工的钢管。
冷轧工艺是将热轧钢坯进行初轧、精轧、轧制成型而制备的一种钢材生产工艺。
下面将介绍冷轧钢管的生产工艺。
冷轧钢管生产工艺主要分为预处理、初轧、精轧、退火、后处理等环节。
首先,预处理环节。
冷轧钢管的生产前需要对原材料进行预处理。
预处理包括酸洗、除鳞、表面处理、剪切等工序。
酸洗是将热轧钢坯在酸性溶液中进行清洗,去除钢表面的氧化皮和锈蚀物。
除鳞是通过机械或化学方法去除钢材表面的铁鳞。
表面处理是为了提高钢材的表面质量,常采用抛光、喷砂等方式。
剪切是将预处理好的钢坯切成适当的长度,方便进行下一步的轧制工序。
其次,初轧环节。
初轧是将预处理好的钢坯经过一组或多组辊道进行初次轧制。
初轧主要是为了降低钢坯的厚度,提高钢坯的表面质量。
通过初轧,钢坯的厚度可以得到明显的减小。
再次,精轧环节。
精轧是对初轧后的钢材进行再次轧制。
精轧主要是通过多组辊道,使钢材得到更精细的轧制,提高钢材的尺寸精度和表面质量。
精轧的环节将钢管的外径和壁厚控制到设计规定的尺寸范围内。
然后,退火环节。
精轧后的钢材需要进行退火处理。
退火是将钢材加热到一定温度,然后进行适当的冷却,使其获得一定的力学性能和组织结构。
退火可以改善钢材的塑性和韧性,提高其加工性能。
退火后的钢材还需要进行后处理,如酸洗、抛光等工序,以提高表面质量。
最后,进行质检和包装。
经过上述工序后的冷轧钢管需进行质量检查,包括外观检查、尺寸检查、机械性能检验等。
合格的钢管进行包装,包括喷油、套塑料膜等,以保证产品质量。
以上就是冷轧钢管生产工艺的主要环节。
冷轧工艺通过多道轧制和退火处理,可以大幅提高钢管的尺寸精度和表面质量,使其更适用于需要高精度、高质量的领域。
钢管轧制工艺

钢管轧制工艺
1. 你知道钢管轧制工艺有多神奇吗?就像魔法一样把钢坯变成坚固又光滑的钢管!比如生产石油管道的过程,那可是厉害得很呐!
2. 钢管轧制工艺啊,那可不是一般的复杂,简直就是一场钢铁的华丽蜕变!像造汽车的钢梁,没有这工艺怎么行呢!
3. 嘿,钢管轧制工艺真的超重要!你想想看,那些高楼大厦的钢架结构,不都是靠它来实现的嘛!
4. 钢管轧制工艺,这可是个技术活呀!就好比雕琢一件艺术品,要多精细有多精细,像做那种高精度的仪器用管!
5. 哇塞,钢管轧制工艺简直太牛了!能让钢有了全新的模样,就像丑小鸭变成白天鹅,比如那些漂亮的不锈钢管!
6. 你说钢管轧制工艺难不难?那肯定难呀,但成果也是超棒的!像家里的水管,都是这么来的呢!
7. 钢管轧制工艺,这可是钢铁行业的核心呀!没有它,好多东西都没法造出来,好比没有了灵魂,像那些大型的输送管道!
8. 哎呀,钢管轧制工艺可太有意思了!能把硬邦邦的钢变得这么有用,像铁路上的钢轨就是这么诞生的呀!
9. 钢管轧制工艺,真的是让人惊叹不已!它就像一个神奇的魔术师,把钢变成各种形状的钢管,比如那些弯弯的盘管!
10. 你可别小瞧钢管轧制工艺哟!它的作用大着呢,就像建筑的基石,像造大桥用的钢管就是这么来的呀!
原创不易,请尊重原创,谢谢!。
材料成形工艺学 钢管绪论

石油管:石油、天然气的钻采用管 ; 热交换管:普通高压锅炉管; 其他部门用管:容器用管、仪器仪表用管、医疗器械。
20
电力塔
独管微波管
21
钢结构底座
钢结构柱
22
化工厂火炬塔
铁塔构件
23
大型建筑
大型建筑
24
大型建筑
桥梁建设
6
主要内容
管材生产绪论 热轧无缝管材的主要加工形式和基本工艺过程 斜轧原理及工具设计 管材纵轧原理和工具设计 管材冷加工 焊管生产工艺
7
参考书目
王廷溥等.塑性加工学-轧制理论与工艺,第3版.北京:冶金工 业出版社,2013 李连诗.钢管塑性变形原理.北京:冶金工业出版社,1985 康永林.轧制工程学,冶金工业出版社,北京,2003 高秀华.钢管生产知识问答.北京:冶金工业出版社,2007 轧钢技术3000问(下)管材分册,中国科学技术出版社 王先进 徐树成.钢管连轧理论 北京:冶金工业出版社,2005 王廷溥.现代轧钢学,北京:冶金工业出版社,2014 严泽生.现代热连轧无缝钢管生产,北京:冶金工业出版社, 2009 《钢管》、《焊管》、《轧钢》、《钢铁》期刊。
连续辊式成型机
直
连续排辊式成型机
焊
辊式弯板机
埋弧焊接
电
缝
UO 压力成型机弧来自螺旋成型机焊TIG
惰性气体保
护电弧焊
MIG
连续辊式成型机 压力成型机 辊式弯板机
产品规格范围
外径/mm
壁厚/mm
21.7~114.3 12.7~508.0
1.9~8.6 0.8~14.0
400~1200 300~4000 400~1625
钢管成形理论及工艺

第三章 钢管成形理论及工艺1.管材穿孔为什么一般采用斜轧?试述斜轧穿孔过程中穿孔机调整参数对“孔腔”形成的影响。
穿孔的变形过程主要取决于工具的形状及位置,因此调整穿孔机工具的相对位置对实现顺利穿孔,提高穿孔质量是至关重要的。
二辊斜轧穿孔机调整的主要参数有:1)轧制中心线:即穿孔机顶杆的中心线。
它也是管坯到毛管的中心线的运动轨迹。
2) 轧机中心线:即穿孔机本身的中心线。
一般说来为了使穿孔过程比较稳定,安装设备时使轧制线比轧机中心线低3∼6mm。
3) 前-后台中心线:常以管坯受料槽与轧制线的相对高度衡量,原则上以受料槽中的管坯中心线略低于轧制线为宜。
调整三条线的目的就是使三条线处于一个合适的位置或三线对中,使轧辊、导板(导盘)、顶头在轧制中处于正确的空间关系,以获得合理的变形区。
4) 辊间距 B:指两轧辊辗轧带之间的间距。
间距的大小必须保证管坯有足够的顶前压下量;同时应保证轧辊相对于轧制线对称。
5)导板距 L:指两导板过渡带之间的距离。
调整导板距主要依据椭圆度的大小ξ=L /B,一般ξ≈1.01~1.15。
同时还要调整导板在轧制线方向上的位置,原则上要保证管坯接触轧辊经约两个螺距后再接触导板;同时要保证毛管最后离开轧辊。
6) 顶前压下率:它指坯料在碰到顶头之前其径向的压下程度。
顶前压下量过大则坯料穿孔前容易出现孔腔,影响穿孔质量;过小则坯料中心不能形成有利于穿孔的“疏松”状态,造成顶头阻力过大而“轧卡”。
7) 顶头位置 C:因为实测顶头位置较困难,常用顶杆位置Y表示。
C指顶头鼻部伸出辗轧带的距离,其大小直接影响穿孔能否进行及穿后毛管的质量。
C过大则不利于咬入,顶头阻力大,易轧卡;C过小则坯料中心容易出现“孔腔”,影响毛管的质量。
8) 轧辊倾角α和轧辊转速:轧辊倾角是斜轧穿孔中最积极的工艺参数。
适当增加α弊少利多,α增加可提高穿孔效率和改善毛管质量,不利是穿孔负荷增加。
轧辊转速会影响穿孔速度。
穿孔机调整的目的就是保证能在穿孔时轧机顺利地咬入管坯和抛出毛管,并获得一定尺寸精度和内外表面质量,为此需要对三条线、四个主要参数(顶前压下率除外)进行调整,原则上应使管坯能按时顺利通过变形区内各点各段,完成变形的全过程。
轧管工艺流程

轧管工艺流程轧管工艺是一种将钢坯加工成管道的工艺,其具有工艺简单、生产效率高、成本低等优点,是现代钢铁生产中广泛采用的一种技术。
下面我们将针对轧管工艺流程进行整体介绍并详细描述每个环节,希望能够对读者有所帮助。
一、轧管工艺流程1.原材料准备:将钢坯进行切割、热处理等预处理工艺,使其达到生产要求。
2.热轧:将预处理后的钢坯通过热轧机组进行加热和轧制,以形成钢卷。
3.钢卷开卷:将钢卷通过开卷机进行开卷,并利用飞剪机对钢卷进行切割。
4.焊接:将切割后的钢板进行输送,并通过高频焊接技术进行焊接。
5.冷卷:将焊接后的钢管通过冷卷机进行加工,形成成品钢管。
6.成品加工:对成品钢管进行校直、切断等加工工艺,使之符合生产要求。
7.检验:对成品钢管进行外观质量和物理性能等方面的检验。
8.包装和运输:对符合生产要求的成品钢管进行包装和运输。
以上为轧管工艺的整体流程,下面对每个环节进行详细描述。
二、详细步骤分析1.原材料准备轧管的原材料多采用热轧钢板,也有一部分采用冷轧钢板及其他原材料。
对于热轧钢板来说,由于长时间的热轧加工过程,其内部结构已经较为均匀,因此需要对其进行裁切。
裁切工艺的要求是尽可能减少切头和切尾缺陷,同时能够满足不同材料规格及尺寸的需求。
裁切后的钢板还需进行热处理,以消除内部应力,提高钢板性能,这样才能满足后续工艺的需要。
2.热轧钢坯经预处理后,进入热轧机组进行轧制,形成钢卷。
热轧一般使用粗轧和精轧两种轧制工艺。
粗轧采用完成度较低的轧辊进行轧制,使钢坯变形量大,锻造性能得到改变。
粗轧后的钢坯进入精轧机组进行精轧,精轧主要分为单机和多机轧制两种方式。
单机精轧是指通过精轧机组一次性完成轧制的工艺,多机轧制则是通过多台机组的不同轧制次序,逐步完成产品的轧制加工。
3.钢卷开卷轧制完成后的钢卷进入开卷机组,通过卷扬、卷弯等方式将钢卷完成开卷,以进行下一步的加工处理。
为了提高加工效率,减少废料产生,开卷后的钢卷需通过飞剪机进行切割,使之得到符合要求的钢板。