检查表(批量生产)
2016版VDA6.3过程审核检查表
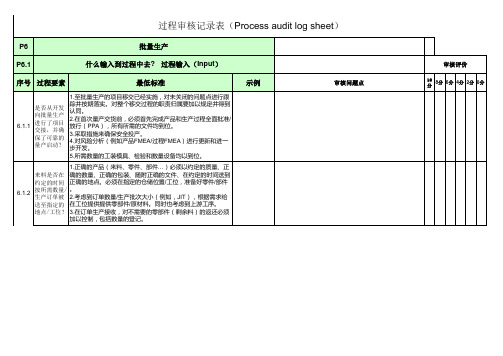
是否对原材 污染。仓储区/加工区/容器必须达到零部件/产品所需的必要的
料进行适当 整洁/清洁要求。要定义清洁周期,并且加以监控。
的仓储,所 3.加工工位/装配线上的零部件/物料的供应必须便与安全操作
6.1.3
使用的运输 。 工具/包装设 4.必须通过合适的方法,监控为特殊材料/零部件规定的仓储时
备是否适合 间以及使用有效期(最长、最短仓储时间,规定的中间临时仓
量要求? 性有影响的测量装置的校准。
4.对于影响到测量结果合试验的附属装置,要采取同样的方式
加以监控。
加工工位和
6.4.4
检验工位是 否满足具体
要求?
1.加工工位及周边布置的条件环境适合于生产操作和产品的要 求,从而可以预防或避免污染、损伤、混料。 2.这也适用于临时的和永久的返工返修、拣选、检验工位。 3.除此以外,还根据具体的工作任务,在人机工程学的基础上 对加工工位设计进行了调整。
P6.2
工作内容/过程流程(所有生产过程是否受控?)
控制计划里 的要求是否 6.2.1* 完整,并且 得到有效实 施?
1.基于控制计划的生产和检验文件完备。其中必须对检验文件 、检验设备、检验方法、检验频度/周期、重新评定等加以规 定。 2.这些文件必须随时可获取。 3.对于影响到产品特性/质量的过程参数必须加以完整地描述。 过程参数和检验特性必须带有公差。 4.在过程控制图上规定控制限,控制限可探测、可追溯。 5.针对过程要求和检验特性,要对发现的不符合项以及启动的 措施加以记录。 6.对过程异常所要采取的措施(反应计划),相关责任人必须 清楚,实施措施并加以记录。 7.如产品对生产工艺有特殊要求,那么相关的机器/工装/辅助 设备的参数数据要在控制计划和/或生产检验文件中加以规定 。 8.详细规定返工条件,并且在过程中加以保障(零部件标识, 重新检验)
生产企业安全检查表

5.结构件不稀有松脱、裂及,扭曲、腐蚀、凹陷或凸出等严里变形.
目视
6.高于1.5m的走台或平台必须有防护栏;台面板周国的甥脚挡板高度不小于150三,
目视/测a
21
特种设招
1.使用单位应使用符合安全技术规范要求的特种设备.
目视
2.特种设符使用场所,应符合相关设计标掂要求,采取相应的管理措施,以S⅛保其安全运行.
目视
10
作业区域地面
状况
1.地面平整,无障碍物和绊胆物,如有绊脚物应设曲目标志或防护措施:坑、燎,池应设置可贫的孟板或护栏,夜间有照明.
目视
2.地面无快水、枳油或垃圾杂物.
目视
3.因作业环境或工艺原因,易产生机油、积水的,应有防滑措睡.
目视
11
设备设您布局
1.设备设施弓堵、柱间以及设备设施之间应留自足修的苑离.或安全隔离.
目视/记录
30
仓库
1.仓库耐火等段设计与储存物品的火灾危冷程度相适应。
目视
2.仓库车行道'人行道宽度应符合标准.路而平坦.无绊脚物.
目视
3.物品应分类储存,定置区域标战清晰,故址和区域不超限。
目视
4.物视
5.电气设得安袋,使用符合安全规范。
目视
6.消防设施、器材配备合理,完整好用.
1.现场使用点的危险化学乩存:放盘不得超过耳班的使
目视
2.使用前、后必须对盛装容腓进行检查,标签清暗.且定点存放.
目视/记泉
3.化学废料及容器应统•回收,按规定进行妥善处理.
目视
15
危险化学品仓
库
I.危险化学品应按其危险特性进行分类、分区、分库贮存,库房符合安全标准的要求,各种危险化学M有中文安全技术说明的.
生产前确认检查表
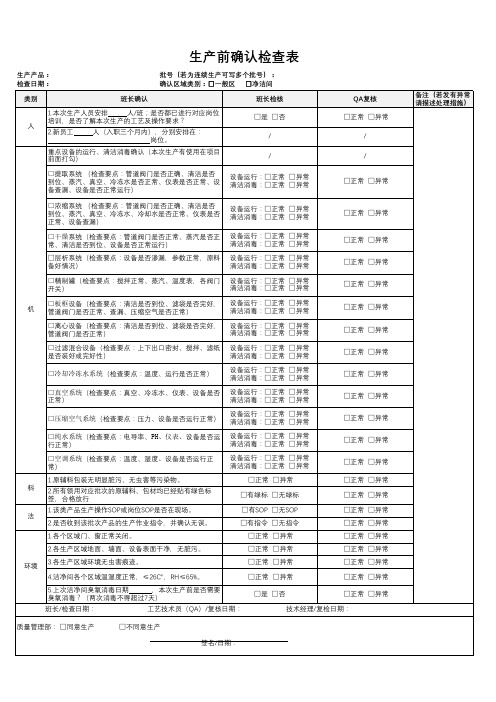
行正常)
清洁消毒:□正常 □异常
□ห้องสมุดไป่ตู้常 □异常
料 法
环境
□空调系统(检查要点:温度、湿度、设备是否运行正 常) 1.原辅料包装无明显脏污、无虫害等污染物。 2.所有领用对应批次的原辅料、包材均已经贴有绿色标 签,合格放行 1.该类产品生产操作SOP或岗位SOP是否在现场。 2.是否收到该批次产品的生产作业指令,并确认无误。 1.各个区域门、窗正常关闭。 2.各生产区域地面、墙面、设备表面干净,无脏污。 3.各生产区域环境无虫害痕迹。
设备运行:□正常 □异常 清洁消毒:□正常 □异常
□正常 □异常
□干燥系统(检查要点:管道阀门是否正常、蒸汽是否正 设备运行:□正常 □异常
常、清洁是否到位、设备是否正常运行)
清洁消毒:□正常 □异常
□正常 □异常
□层析系统(检查要点:设备是否渗漏,参数正常,原料 设备运行:□正常 □异常
备好情况)
设备运行:□正常 □异常 清洁消毒:□正常 □异常
□正常 □异常
□真空系统(检查要点:真空、冷冻水、仪表、设备是否 设备运行:□正常 □异常
正常)
清洁消毒:□正常 □异常
□正常 □异常
□压缩空气系统(检查要点:压力、设备是否运行正常)
设备运行:□正常 □异常 清洁消毒:□正常 □异常
□正常 □异常
□纯水系统(检查要点:电导率、PH、仪表、设备是否运 设备运行:□正常 □异常
清洁消毒:□正常 □异常
□正常 □异常
□精制罐(检查要点:搅拌正常、蒸汽、温度表,各阀门 设备运行:□正常 □异常
开关)
清洁消毒:□正常 □异常
□正常 □异常
□板框设备(检查要点:清洁是否到位、滤袋是否完好, 设备运行:□正常 □异常
VDA6.3检查表-2010版

- 物流要求(JIT、JIS、合同)
- 时间表,技术交货条件
- 互联网上信息平台访问入口(顾客/供方) - 在智能归口的框架范围内,和顾客一起定义针对下级供方/服 务提供商的责权关系(例如资格,原型件技术放行程序、审批
标准化生产系统方法: - 标杆,实践比较
、检验……) - 检验规范 - 产品/过程特性 - 订货文件,内容包括数量/时间安排
- 顾客要求
标准化生产系统的方法:
- 时间安排,时间框架
- 标杆,实践比较
- 针对下级供方权责关系的定义
- 顾客质量传感器
- 规范,标准,法律,环保
- 从过去产品上积累的经验
- 顾客规范
- 生产计划安排
- 产品责任要求
- 产能
- VDA第4卷,经济的过程设计和控制
- 原材料到位情况
- VDA第4卷,课制造性分析
P2.4 项目组织是否在项目进程中提供了可靠的变更管理? 项目中的变更管理需要满足特定的顾客要求。 将开展针对变更的可行性检验,并做好相关记录。 针对变更,应及时加以说明,并做好相关记录。 应在一道定义的过程的基础上,对所有变更开展记录。 对于不是由顾客触发的变更,应同顾客协商沟通。 对于影响到产品质量的变更,必须和顾客一起对风险开展评价。 在变更管理中,应确保供方(关键群体)能够主动参与。 对变更停止的时间点有明确的定义,因而必须遵守。 如果不能遵守,则在顾客和供方之间必须以书面形式加以记录。 SOP之间的变更时间段不会影响到产品质量。 变更的实现应考虑到SOP之间剩余的时间,综合加以评价。
为变更的负责人定义了一套规定。
- 时间表 - 变更管理过程描述 - 责权的确定 - 变更表单 - 变更历史 - 变更评价 - 变更认可
IATF16949--过程审核检查表-(含审核记录)-
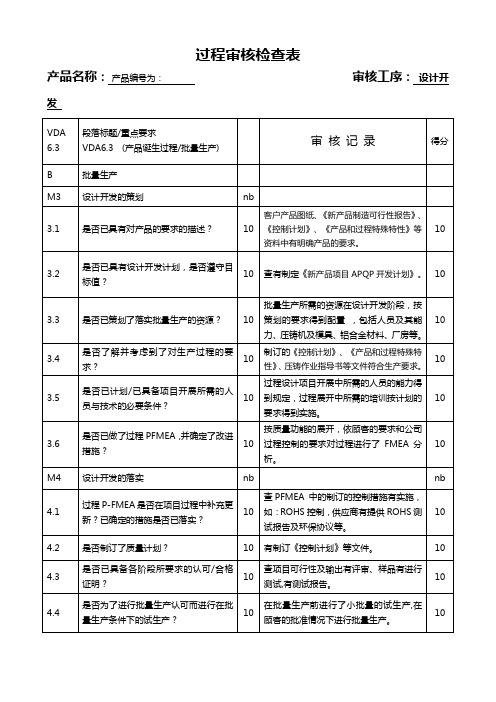
生产数量按下达的生产计划进行,能满足顾客要求,对车间的产品流向策划了流程图,确保产品有序运往下道工序。
10
6.3.2
产品/零件是否按要求贮存?运输器具/包装方法是否按产品/零件的特性而定?
10
产品现场无堆积,摆放整齐。用纸箱包装。
10
6.3.3
废品、返修件和调整件以及车间内的剩余料是否坚持分别贮存与并标识?
10
查岗位说明书中有明确员工、品管人员的职责和权限。询问品管负责人何平生,清楚自己的职责。
10
6.1.2
是否对员工委以负责生产设备/生产环境的职责和权限?
10
询问压铸员工邹、贾,明确生产设备的操作和现场5S工作要求。
10
6.1.3
员工是否适合于完成所交付的任务并保持其素质?
10
查压铸机作业员工邹、贾,明确生产及产品品质要求。
10
有制定了成品合格率、生产计划及时完成率、过程CPK等目标,目标达标。
10
过程审核检查表
产品名称:产品编号为:审核工序:包装入库
VDA
6.3
段落标题/重点要求
VDA6.3 (产品诞生过程/批量生产)
审 核 记 录
得分
M6
生产
6.1
人员/素质
nb
6.1.1
是否对员工委以监控产品质量/过程质量的职责和权限?
10
查员工职务说明书中有明确员工的职责和权限。
10
6.1.2
是否对员工委以负责生产设备/生产环境的职责和权限?
10
询问包装工吴学文清楚相关要求。
10
6.1.3
员工是否适合于完成所交付的任务并保持其素质?
10
询问包装工吴,明确生产要求。
生产质量检查表
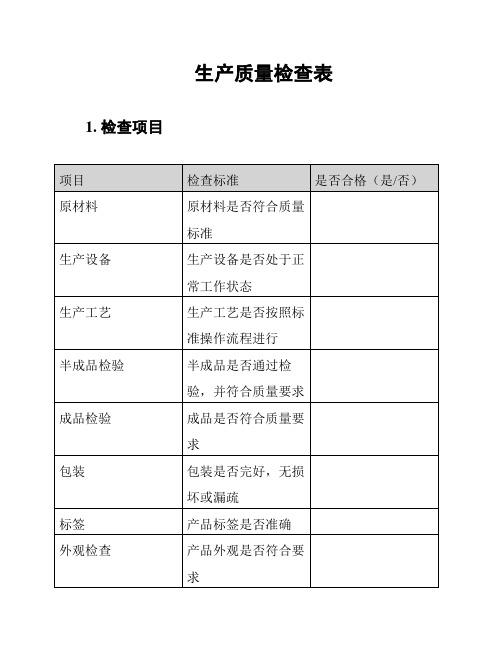
生产质量检查表1. 检查项目
2. 检查过程
1. 检查人员应提前熟悉质量检查表中的检查项目和标准。
2. 按照生产质量检查表逐一进行检查,记录检查结果。
3. 若某项不合格,则立即停止生产,并采取相应措施进行整改。
4. 经整改后,重新进行检查,直至符合质量要求为止。
5. 检查人员应将检查结果记录在检测记录栏中。
3. 检查人员责任
检查人员应严格按照检查标准进行检查,并及时记录检查结果。
对于不合格的项目,检查人员应立即通知相关部门进行整改,并确
保整改措施的有效性。
---
以上是生产质量检查表的内容,请按照表格填写检查结果,并根据需要进行相应的整改。
04 过程审核(批量生产)检查表-填写好
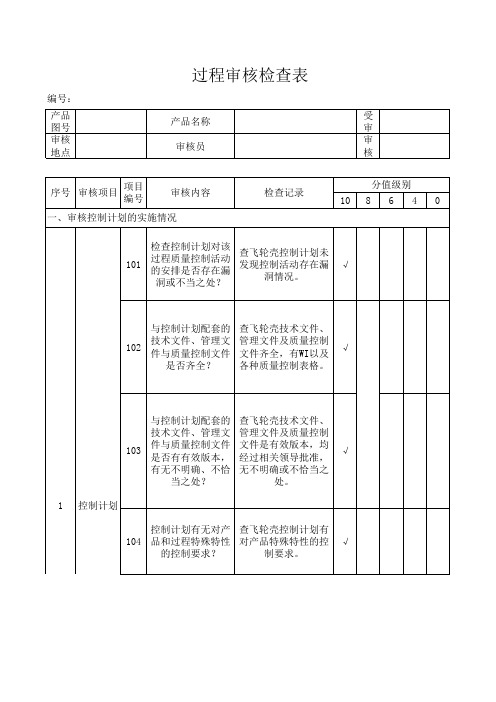
506
能否防止文件误 用?
查飞轮壳及47974572 后取力现场工艺文 件,文件混放严重, 并未单独分开放置, 文件在使用过程中可 能会误用。
√
查飞轮壳及47974572 后取力现场作业指导 507 操作方法安全否? 书,指导书要求的操 作方法是合理安全的 。
√
查产品流程图,产品 前、后工序的衔接 508 在各工序生产过程中 是否良好? 的流转衔接良好 小计 8 小结分值 68
√
6 小结分值 二、审核过程因素受控情况
小计
0
201
是否持证上岗?
查HR管理室员工技能 培训统计表,有人员 上岗证发放记录。
√
202
技能掌握否?
查各车间员工技能考 试试卷,均达到部门 要求成绩。
√
查HR管理室无入职前 培训记录,但现场有 上岗前是否接受过 进行岗前培训,由各 203 上岗培训? 班、组长具体负责培 训事宜,且有培训考 试记录。 查HR管理室培训记 录,对公司各班、组 有无过程质量控制 长以上人员进行了质 204 知识? 量体系培训,但并未 对全厂所有员工进行 培训。
√
查HR管理室无人员 生产过程中人员的 顶岗管理规定,现场 212 临时顶岗如何处 临时顶岗由各班、组 置? 长顶岗。 小计 12 小结分值 108 7
√
4
1
0
0
制造现场设备的选 设备选用及使用符合 301 择、使用是否恰 消失模铸造设备要求 当? 。
√
设备设计产能为年产 设备是否满足生产 302 5000T,现年产能不足 √ 能力? 1200T,产能富足。
√
5
查制造部清理区现场 飞轮壳及47974572后 现场使用的工艺文 取力作业指导书,文 504 件是否齐全、统一 作业方法 件齐全,但表面污物 、清晰? 较多,字迹不能清晰 分辨。
批量生产检查表Manufacture Readiness Review

Production layout established Material flow route reasonable Tooling in place 模具到位 3~4 Equipment, fixture, jig in place 设备,工装到位 3~5 Inspection fixture/instrument in place Process 检验设备,检具到位 Audit 3~6 Sample in place 过程准备 样品准备到位 3~7 Production capability 生产能力确认 3~8 Raw material readiness 3~9 First batch production plan 3~10 Operator/inspector qualification 人员资格培训认可
Supplier: Item
CCCS: Major Description Flow Chart 流程图 CPC 明确关键产品特性 CPP established 过程关键参数建立 CPP verified 过程关键参数的验证 In-coming SIP 进料检验指导书 In-coming report 进料检验报告 In-coming inspection plan 进料检验规范 material certification 材质保证书 Out-going SIP 出货检验指导书 Out-going report 出货检验报告 Out-going inspection plan 出货检验规范 Function test established 建立测试装置 Function test report 测试报告 Control plan 控制计划 Prototype 样品 Pilot run 试生产(如果有) Project build issue report 生产问题报告 Customer approval notice 首件批准通知 Drawing, Specification 最新的图纸及规范 ECN 设计变更 BOM 材料清单 Approved vendor list 认可之供应商 SOP 制程作业指导书 SIP 制程检验指导书 Process inspection plan 制程检验计划 Packaging procedure 包装指导书 All docu. revision controlled 文件版本控制 Products revision contol 成品版本控制
生产检查表(每月)
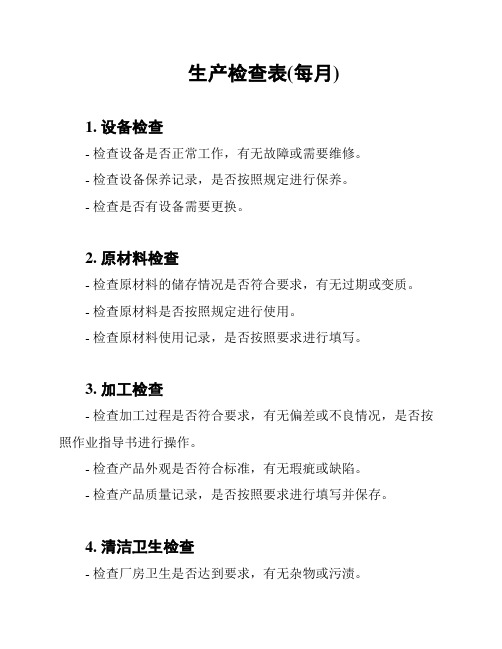
生产检查表(每月)
1. 设备检查
- 检查设备是否正常工作,有无故障或需要维修。
- 检查设备保养记录,是否按照规定进行保养。
- 检查是否有设备需要更换。
2. 原材料检查
- 检查原材料的储存情况是否符合要求,有无过期或变质。
- 检查原材料是否按照规定进行使用。
- 检查原材料使用记录,是否按照要求进行填写。
3. 加工检查
- 检查加工过程是否符合要求,有无偏差或不良情况,是否按照作业指导书进行操作。
- 检查产品外观是否符合标准,有无瑕疵或缺陷。
- 检查产品质量记录,是否按照要求进行填写并保存。
4. 清洁卫生检查
- 检查厂房卫生是否达到要求,有无杂物或污渍。
- 检查员工操作区域是否清洁卫生,有无生产废弃物或垃圾。
- 检查员工是否按照要求穿着工作服,是否洗手并戴好手套。
5. 安全生产检查
- 检查生产区域内安全设施是否符合要求,如灭火器、安全出口等。
- 检查员工是否按照要求佩戴防护用品。
- 检查员工是否严格遵守安全操作规程。
以上是每月的生产检查表,检查后及时解决问题,并将检查记录进行保存。
养殖场批次生产检查表

6
胶鞋 有无备用拖鞋、进单元是否换鞋
7
卫生 网床、下料器、饮水碗、风机、网底
8
消毒 有无消毒记录
9
空圈时间
转猪日期 ;
、刷圈日期
、消毒日期
10
药品 是否有库存药品,是否已跟猪群流转至育肥
11
物品
是否干净卫生,是否经过消毒(桶、粪刷、拖 把)
12 供电系统 是否正常
13 通风系统 调试、是否能正常使用(皮带、扇叶、粉尘)
XXXXXXX养殖场批次生产检查表
日期:
序号
明细
检查标准
检查结果 处理措施
1
更衣室
工装、胶鞋是否按要求摆放和清洗,有无值班 表
2更衣室消毒设 施来自消毒桶、消毒盆、消毒壶、消毒液、
3 单元门口 有无隔离设施、有无石灰对泥土地面进行覆盖
4 单元检查 是否有检查标签,是否签字确认(工段长)
5 单元消毒 有无消毒桶、有无消毒剂
14 饮水系统 有无滴漏、能否正常使用、饮水碗是否干燥
15
饲喂系统
能否正常使用、保持干燥、料管是否有陈旧饲 料
16 转猪车辆 是否清洗干净、是否干燥、是否消毒
17 行车路线 行车路线是否清晰(与司机沟通)
18 行走路线 员工行走路线是否清晰(工段长安排)
19
批次管理
批次是否清晰、是否有交叉(人员、物品、饲 料)
VDA6.3过程检查表

—进行/报请维修与保养
—零件准备/贮存
—进行/报请对检测、试验设备的检定和校准。
4.1.3员工是否适合于完成所交付的任务并保持其素质?
—过程上岗指导/培训/资格的证明
小明回答
—产品以及发生缺陷的知识
—对安全生产/环境意识的指导
—资格证明(例如:焊接证书,视力测定,厂内机动车驾驶证)。
4.1.4是否有包括上岗规定的人员配置计划?
—图纸/订货要求/规范
—质量保证协议
—检验方法、检验流程、检验频次的商定
3.3是否评价供货实物质量?与要求有偏差时是否采取措施?
—质量会谈的纪要
是否发生过来料质量问题(现场IQC)检验记录,处理结果。重新测量的依据夏敏回答
—改进计划的商定与跟踪
—改进后零件的检验记录和测量记录
—对重点缺陷/有问题供方的分析评定。
要素1:过程开发的策划
1.1是否已具有对产品的要求?
---顾客要求
---法规,标准,规定
---物流方案
---技术供货条件(TI)
---质量协议/目标协议
---重要特性
---材料
1.2是否已具有过程开发计划,是否遵守目标值?
---顾客要求
---成本
---进度表:策划认可/采购认可,样件(样车)/试生产,批量生产起始
3.4是否与供方就产品与过程的持续改进商定质量目标,并付诸落实?
—工作小组(由各相关部门组成)
供应商管理方面,是否有供应商的目标、指标要求。夏敏回答
—确定质量、价格及服务的定量目标
—在提高过程受控状态的同时降低检验成本
—减少废品(内部/外部)
---提高顾客满意程度。
3.5对已批量供货的产品是否具有所要求的批量生产认可,可落实所要求改进措施?
VDA6.3量产产品过程审核检查表

1、不同状态产品应分区域存放 2、不合格品或返工品标注标识 3、隔离区域产品要有不能擅自进入的措施跟进
P 6.2.6
是否采取了措施,防止在材料/零部件流转的过 程中,发生混合/搞错的情况?
1、合理/优化的材料和零部件流转,防止不同物料发生混合 2、必须确保能够识别错误装配件,并能够及时地加以剔除 3、针对剩余料、隔离件、返工件以及经过产品审核后再用的零部件 等,重新投入生产的程序,必须进行明确的规范 4、对于内部搁置的剩余料,必须清点数量,相应加以标识并储存好
运行证据
1、作业文件、检验文件易于得到 2、检测工具配置到位 3、过程参数一览表 4、过程质量控制卡界限设定 5、设备、工装模具编号 6、设备能力证明
P 6.2.2
对生产工艺流程是否进行了放行,并且对设置数 据进行了采集?
P 6.2.3
使用的生产设备是否可以满足客户对具体产品提 出的要求?
*P 6.2.4
1、过程指标设定 2、对过程实现数据收集与评价 3、当未达成目标时的原因分析和改进记录
1、编制了质量控制卡;对过程数据以及过程参数进行了监控 2、一旦过程出现问题,及时采取了措施并加以记录 3、对于过程的偏差,如对产品有影响,就必须得到客户批准 4、缺陷类型及其发生频次,应记录并分析评价,同时采取针对性的措 施 5、对缺陷成本加以记录,并按失效原因进行评价
1、产品标识/物资流转卡 2、防止不良品混合的管理文件
P 6.3 哪些岗位为过程提供了支持?(人力资源)
最低要求/与评价的相关性
出发点
P 6.3.1
在监控产品/过程质量方面,是否将相关的责权 和权限委托给了员工?
职责
关注点
1、对于员工各自工作范围内的职责、任务以及权限必须加以描述 2、必须定期以合适的方式,推动和提供员工的质量意识 3、应定期向员工通报客户处的质量状况 4、员工应被包括到持续改进过程当中
过程审核检查表(根据大众FORMEL-Q要求)

要求/说明 过程参数和检验特性必须标明公差。生产文件和检验文件必须位于生产岗 位和检验岗位。对偏差和由此采取的措施要进行记录保存。 考虑要点,例如: -过程参数(如压力、温度、时间、速度) -机器/工装模具/辅助器具的数据 2.2.4 -检验规范(重要的特性、检验器具、方法、检验频次) -过程控制图中的控制限 -机器能力和过程能力的证明 -设备操作指导 -作业指导书 -检验指导书 -反映最新缺陷状况的信息
过 程 审 核 提 问 表
B
批量生产 问题清单 检查记录
2
生产
生产设备/工装模具 投入使用的生产设备必须能够满足产品的质量要求,必须达到并保持过程能力。检测设备也必须满足这些要求。 2.2 每次开工时要遵守一些特别的规定,要根据所生产的产品布置生产工位和检验工位,要在生产开始之前对产品和 过程进行认可。必须知道此生产工序之前的质量信息和过程信息,所有制订的改进措施必须得到落实。
生产设备/工装模具是否能确保产品特定的质量要求? 生产设备/工装模具是否能确保产品特定的质量要求?
要求/说明 对于选定的重要产品特性/过程特性,要测算其过程能力并不断进行验证 。对于短期过程能力MFU或临时过程能力PFU,Cmk/PpK值必须至少达到1.67。 长期过程能力CPK必须至少为1.33,并对其进行持续改进。 2.2.1 考虑要点,例如: -针对重要产品特性/过程参数的机器能力/过程能力的证明 -重要过程参数的强制性控制/调整 -超出控制界限时的报警(如灯光、喇叭、自动断闸) -上/下料装置 -工装模具/设备/机器的保养和维修状态(包括有计划
在批量生产中使用的测量和检验设备能否有效监控质量要求?
要求/说明 考虑要点,例如: 2.2.2 -可靠性试验、功能试验和耐腐蚀试验 -测量精度/检测设备能力 -数据采集和可评价性 -检测设备的校准证明
批量生产能力检查表

《批量生产能力检查表》
编号:是否
1.最新更改状态的规范、图纸、配方、标准已具备
2.有适用的质量计划(控制计划)
3.有足够的经过培训的合格专职检验人员
4.有足够的经过培训的合格操作人员
5.满足批量生产条件的设备已具备( Cmk/1.67 )
6.专用的工装/模具巳具备
7.满足材料分析/试验的设备条件巳具备
8.满足随线生产用的计量器具巳具备
9.满足检验和试验用的计量器具巳具备
10.满足产品性能试验的条件巳具备
11.已具备了对产品特殊特性的控制手段
12.计量器具的检定条件巳具备
13.认可的供应商巳具备
14.认可的材料和供方产品巳具备
15.最新状态的控制计划巳具备
16.规范化的产品工艺流程巳具备
17.对产品过程特性的控制手段已具备
18.操作指导书已具备
19.检验指导书巳具备
20.生产过程能力CPK/1.33
21.设备维护保养指导书都巳具备
22.具备保障生产作业的工作环境
2 —1
《批量生产能力检查表》
编号:是否
23.对定置管理作了规定
24.已具备合适/足够的工位器具
25.巳建立了物流跟踪系统和可追溯性手段
26.已具备合适的(经确认的)产品包装
27.装箱单/合格证已具备
28.生产过程满足“安全生产法规”的要求
29.生产过程满足“环境保护法规”的要求
30.各工序生产效率已进行了测评
31.已作了整体的生产能力计划
32.首批样品的供货已获得了认可
33.对前阶段的质量缺陷是否已具有纠正预防措施
2 —2。
生产准备检查表
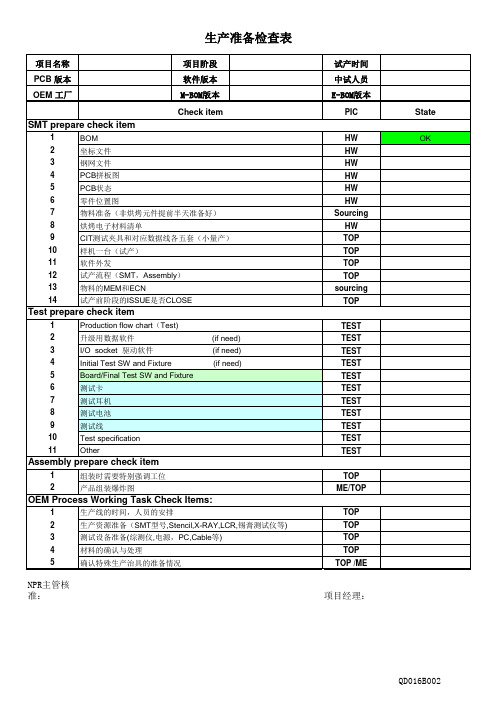
Test prepare check item
Assembly prepare check item
OEM Process Working Task Check Items:
NPR主管核准:
项目经理:
QD016B002
生产准备检查表
编号:QD025003
项目名称 PCB 版本 OEM 工厂 项目阶段 软件版本 M-BOM版本 Check item 试产时间 中试人员 E-BOM 版本
PIC HW HW HW HW HW HW Sourcing HW TOP TOP TOP TOP sourcing TOP TEST (if need) (if need) (if need) TEST TEST TEST TEST TEST TEST TEST TEST TEST TEST TOP ME/TOP TOP TOP TOP TOP TOP /ME
State
OK
SMT prepare check item
1 2 3 4 5 6 7 8 9 10 11 12 13 14 1 2 3 4 5 6 7 8 9 10 11 1 2 1 2 3 4 5 BOM 坐标文件 钢网文件 PCB拼板图 PCB状态 零件位置图 物料准备(非烘烤元件提前半天准备好) 烘烤电子材料清单 CIT测试夹具和对应数据线各五套(小量产) 样机一台(试产) 软件外发 试产流程(SMT,Assembly) 物料的MEM和ECN 试产前阶段的ISSUE是否CLOSE Production flow chart(Test) 升级用数据软件 I/O socket 驱动软件 Initial Test SW and Fixture Board/Final Test SW and Fixture 测试卡 测试耳机 测试电池 测试线 Test specification Other 组装时需要特别强调工位 产品组装爆炸图 生产线的时间,人员的安排 生产资源准备(SMT型号,Stencil,X-RAY,LCR,锡膏测试仪等) 测试设备准备(综测仪,电源,PC,Cable等) 材料的确认与处理 确认特殊生产治具的准备情况
试生产检查表
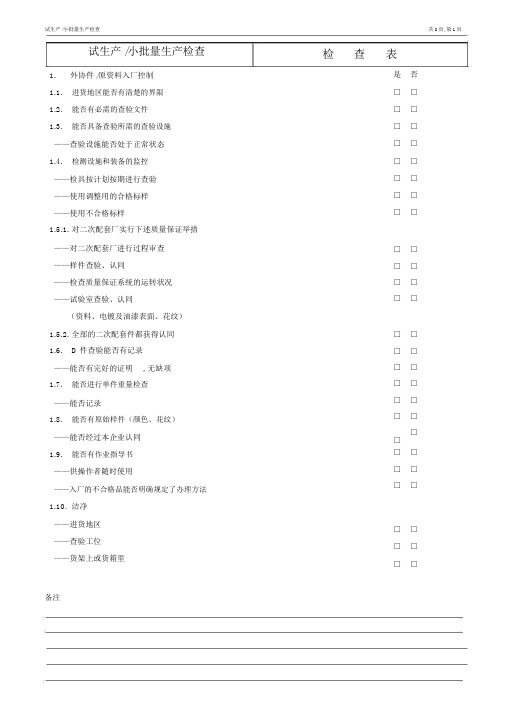
试生产 /小批量生产检查试生产 /小批量生产检查1.外协件 /原资料入厂控制1.1.进货地区能否有清楚的界限1.2.能否有必需的查验文件1.3.能否具备查验所需的查验设施——查验设施能否处于正常状态1.4.检测设施和装备的监控——检具按计划按期进行查验——使用调整用的合格标样——使用不合格标样1.5.1. 对二次配套厂实行下述质量保证举措——对二次配套厂进行过程审查——样件查验、认同——检查质量保证系统的运转状况——试验室查验、认同(资料、电镀及油漆表面、花纹)1.5.2. 全部的二次配套件都获得认同1.6. D 件查验能否有记录——能否有完好的证明, 无缺项1.7.能否进行单件重量检查——能否记录1.8.能否有原始样件(颜色、花纹)——能否经过本企业认同1.9.能否有作业指导书——供操作者随时使用——入厂的不合格品能否明确规定了办理方法1.10. 洁净——进货地区——查验工位——货架上或货箱里共8页,第1页检查表是否□□□□□□□□□□□□□□□□□□□□□□□□□□□□□□□□□□□□□□□□□□□□□□□□□□备注试生产 /小批量生产检查2.库房2.1.能否按照先进先出原则2.2.储藏预批量件,送入生产线前由质保部同意或由产品部同意2.3.隔绝库——用于外协件——用于自制件2.4.能否由以下部门参加隔绝库房的管理——质管部——生产车间——货物发运部门2.5.部件表记——使用标签——拥有可追忆性2.6.洁净——库区内——工作岗位——工位用具——工位用具能否有盖备注检查表是否□□□□□□□□□□□□□□□□□□□□□□□□□□□□□□试生产 /小批量生产检查3.生产线3.1.能否为专用生产线3.2.多产品使用同一设施加工3.3.能否确立了工艺文件3.4.能否确立了查验计划3.5.能否考证了重要部件的机器能力3.6.用于生产批量件的模具能否——制造完成——投入使用3.7.装置线流程——全自动——半自动——手动—— SPC 控制——逼迫控制(防差错装置)3.8.能否使用了适合的查验设施3.9.能否设置了SPC 质量控制点并作出表记3.10. D 件工位能否作了表记3.11. 工位上能否有作业指导书——关于废品能否有明确的办理规定——废品件能否有表记3.12. 能否有废品箱——有显然的表记——废品箱能否能够上锁3.13. 能否明确规定了返修件的物流路线3.14. 能否出缺点采集卡——能否洁净、有序地使用采集卡——剖析评论的频率——能否制定举措——能否有记录归档——能否对举措的有效性进行考证3.15. 过程工艺参数控制卡——适合——按规定实行3.16.对装置线和生产设施实行监控:—— SPC 控制——调整用标准样件——不合格样件——巡检——计算机数字控制及故障诊疗3.17.工位用具能否适合——数目能否知足生产需求——最后产品能否需另行包装检查表是否□□□□□□□□□□□□□□□□□□□□□□□□□□□□□□□□□□□□□□□□□□□□□□□□□□□□□□□□□□□□□□□□□□□□□□□□□□□□□□□□□□□□试生产 /小批量生产检查3.18.在投入使用压铸及注塑设施时,能否有明确的操作规程3.19.何部门对马上投入批量生产的设施进行查收——生产车间——品管部3.20.调整、监测设施参数或工艺参数的方式——自动——手动—— SPC 控制——巡检3.21.能否采纳了在线检测设施——检测部件的百分比: % ——终检能否考证了在线检测的质量特征防备3.22.能否洁净——锻造线——工位——工位用具内检查表是否□□□□□□□□□□□□□□□□□□□□□□□□□□□□□□□□□□□□试生产 /小批量生产检查共8页,第5页试生产 /小批量生产检查检查表3.23.工序及机器能力考证部件名称额定技术要求额定值公差Cmk Cpk试生产 /小批量生产检查共8页,第6页试生产 /小批量生产检查检查表4.终检4.1.能否有效地管理合格部件的表记——能否能够有效地追忆过程查验的结果4.2.查验项目4.3.查验方式—— 100% 查验——依据质量控制的要求进行抽检——目视查验——其余查验:4.4.合格率% 4.5.能否对查验结果作记录——能否作统计剖析——频率——能否制定了举措——成效能否监控4.6.废品件能否表记4.7.能否对不合格件进行剖析——能否记录缺点——能否制定相应的改良举措——能否进行了有效的考证4.8.针对废品件有无明确的办理方法——各相应的检查点能否拟订了作业指导书4.9.重要的单件及总成件能否有生产日期是否□□□□□□□□□□□□□□□□□□□□□□□□□□□□□□□□□□□□备注试生产 /小批量生产检查试生产 /小批量生产检查5.增补的质保手段5.1.能否进行功能及寿命试验——试验结果能否知足技术要求——试验直至部件无效否——频率:5.2.能否约定了批量生产的查验项目有哪些:5.3.对花纹能否监控——能否记录——频率:——检测仪器:5.4.能否确立对润滑脂用量及质量进行监控——能否记录——频率:——依据TL/进行查验能否记录查验结果——能否作统计剖析5.6.依据的查验结果能否制定了相应的举措——能否对举措的成效进行考证备注共8页,第8页检查表是否□□□□□□□□□□□□□□□□□□□□□□□□5.5.试生产 /小批量生产检查共8页,第7页试生产 /小批量生产检查检查表6.发货6.1.能否实行发货审查(或发货前的开箱查验)——频率:6.2.能否对样件实行目视检查,防止发货件与拟发货件混装或错装。
过程审核检查表--示例

2.3.5工装模具、设备和检测设备是否合适地存放?
考虑要点:防损伤的存放;有序清洁;定置存放区;有管理的发放;环境影响;标识;明确的认可状态和更改状态;
此工序配置的所有工装、设备及量具要求操作者保持其清洁状态,确保其使用,并执行
考虑要点:足够的、合适的运输器具;定置库位;最小的/无中间库存;看板(KANBAN);JIT;先进先出(FIFO);仓库管理;更改状态;向下道工序只供给合格件;产量记录分析;信息流;
在生产过程中,规定由下工序的作业人员向本工序进行适时领用,一次性领用量不超过XX箱,保证各工序间的物流均衡流动。
2.3.2产品/零件是否按要求存放,运输器具/包装设备是否与产品/零件的特点相适应?
过程审核检查表
审核日期:年月日~年月日审核员:
检查项目
检查要点
客观论据记录
评分
10
8
6
4
0
3顾客关怀/顾客满意度(服务)
3.1是否满足顾客对质量管理体系、产品和过程的要求?
考虑要点:质量管理体系按照ISO/TS16949:2002标准;质量协议;针对零缺陷要求的目标协议;交付审核;耐久试验(调查失效模式);功能检验;
公司建立了相应的程序文件及应急计划程序,对于突出事件能及时做出反映,特殊是当顾客出现抱怨时的及时处理。
8
3.4与质量要求有偏差时,是否进行了缺陷分析并实施了改进措施?
考虑要点:分析的可能性(实验室、检验和试验设施、人员);;实验室符合ISO/IEC17025的要求;针对缺陷特性进行排列图-分析(内部/外部)各有关部门的介入(内部/外部);运用解决问题的方法(如8D-报告);
- 1、下载文档前请自行甄别文档内容的完整性,平台不提供额外的编辑、内容补充、找答案等附加服务。
- 2、"仅部分预览"的文档,不可在线预览部分如存在完整性等问题,可反馈申请退款(可完整预览的文档不适用该条件!)。
- 3、如文档侵犯您的权益,请联系客服反馈,我们会尽快为您处理(人工客服工作时间:9:00-18:30)。
关于检验方法.检验流程、检验频 次是否与分供方商定
有无对分供方供货质量能力的审核 计划及审核记录
1・3
是否评价供货实物质量,在出现与 要求有偏差时是否采取措施?
有无分供方的自检报告和本厂进料 检验的检验记录
有无定期对分供方的质量能力和实
物质量进行统计评定的记录
2.1・2
是否对员工委以生产设备/生产环 境的职责和权限?
保持生产环境整齐清洁的职责是否 落实
设备日保养和报请维修的职责是否 落实
设备零件准备和储存的职责是否落 实
检测设备点检和报请检修校准的职 责,计量器具校验和标定的职责是 否落实
2・1.3
员工是否适合于完成所交付的任 务,并保持其素质?
是否进行了必要的培训,包括应知 应会,产品,产品缺陷,安全生产
检测设备、试验设备是否都处在正 常工作状态,设备是否够用
有无重要检测设备测量精度/检具 能力的调査记录
有无对试验数据的采集和分析记录
有无检具标定的证明
有无标样管理制度
2.2・3
生产岗位、检验岗位是否符合要 求?
各工作岗位(包括返工岗位)是否都 符合整齐清洁,能方便地进行零部 件鉴定.样件存放、文件阅读.填 写记录、更换工具
2・1・1
是否对员工委以监控产品质量/过 程质量的职责和权限?
有无8D小组等明确员工参与改进 项目的措施
过程自检的职责是否落实
过程认可、设备点检、首件检验、 末件检验的职责是否落实
制作并分析控制图的职责是否落 实,控制对象是否明确
有无关于终止生产权的规定,是否 明确规定了检验员对不合格产品、 可疑产品、紧急转序状态的隔离职 责
有无在原材料出现瓶颈时的紧急战 略,是否采用一种材料有二家合格 分供方
库存状况是否能满足合同中顾客提 出的所有要求,保证生产计划进度, 实现准时化生产
策划库存量时是否考虑7先进先出
对原材料库存是否规定了最高/最 低库存量
1・8
原材料/内部剩余料是否有合适的 进料和储存方法?
仓库环境条件是否适宜,有无漏雨、 返潮、发霉
有无周期形式试验报告及由此制订 的改进措施
主要特性的CPK是否符合>1.67
1. 6
是否对由顾客提供的产品执行了与
顾客商定的方法?
有无就顾客提供的产品与顾客签订 的质量协议
有无在出现缺陷、丢失、损坏等情 况时与顾客的信息交流记录
有无反映顾客提供产品质量现状、 质量历史的质量记录
1・7
原材料库存(量)状况是否适合于 生产要求?
生产设备/工装模具是否能满足产 品特定的质量要求?
有无针对产品重要特性或过程参数 进行的机器能力调查记录和过程能 力调査记录
有无对重要参数实施强制控制/调
整的规定
设备的上下料装置是否能保证满足 产品质量要求
有无设备/工装模具的维修保养计 划
设备有无偏离规定值时的报警、自 动断电装置
2. 2.2
在批量生产中使用的检测、试验设 备是否能有效地监控质量要求?
若评定结果不佳,分供方有无质量
改进计划以及对计划落实情况的验
证记录
在出现与要求有偏差时,有无与分 供方质量会谈的纪要
有无不合格品的退货程序及记录
有无改进后零件(含新开模和模具 改进)的首件认可.首批认可记录
有无对重点缺陷/有问题的分供方 的统计分析评定记录
1. 4
1.4:是否与分供方就产品与过程的 持续改进商定质量目标并付之落 实?
2. 1.5
是否有效地使用了提高员工工作积 极性的方法?
是否开展了质量管理的宣传活动, 促进员工的投入意识
有无员工提出的书面改进建议
有无员工在参加培训、开展质量小 组方面的志愿行动
病假率是否低
对质量改进的贡献是否进行鼓励
检查表
基于VDA6.3编制
VDA6.3
生产(生产设备/工装)
检查方法
审核记录
2・2・1
是否对每个合格分供方建立了完整 的档案(内容包括:定点撤点申请 表、质量能力审核报告;首件认可. 首批认可报告;实物质量统计分析; 分供方的改进计划;质量信息反馈 单;服务质量记录)
1・2
是否确保分供方所供产品的质量达 到供货协议的要求?
有无采购文件,技术协议
工艺辅助材料有无明确的技术特性 规定
有无与分供方签订的质量保证协议
有无易受气候条件影响的原材料/ 内部剩余料清单
有无混批混料现象
是否执行了先进先出
下雨天厂内运输是否会淋湿原材料
标识是否完整齐全(包括批次号、 检验状态、加工状态),有无可追溯 性
账卡物是否相符
对不合格品,可疑物品有无隔离措 施
材料包装是否符合要求
库房中的存放器具、运输器具是否 适宜和干净,有无适合码放的托架、 箱子
有无负责这项工作的由ห้องสมุดไป่ตู้相关部门
组成的工作小组名单
有无与分供方商定的质量目标协议
协议中有无针对质量、价格、服务 所规定的具体定量目标,包括质量 能力>85、一次合格率等
1・5
对已批量供货的产品是否具有所要 求的批量生产认可并落实了所要求 的改进措施?
对分供方的所有产品,在批量 使用前必须对新产品.更改的产品 及其生产过程进行认可。有无认可 报告
材料的有效期是否保证,如果过期
如何处理
有无消防措施
1.9
员工是否具有相应的岗位培训?
是否接受过产品规范、顾客要求、 包装知识、产品加工、统计方法、 因果图、8D方法等内容的培训
有无采购员、外协评审员、包装检 验员、库房管理员的培训记录
检査表
基于VDA6.3编制
VDA6.3
生产(人员/素质)
检査方法
审核记录
检査表(批量生产)
检査表
基于VDA6.3编制
VDA6.3
分供方/原材料
检査方法
审核记录
1・1
是否仅允许已认可的且有质量能力 的分供方供货?
有无合格分供方名单
名单上新增加的合格分供方有无评 审记录
有无上年度对合格分供方从质量、 成本、服务三方面进行的统计评定 记录
实际供货单位是否仅限于合格分供
方名单的范围
操作工有无上岗证
从事某些特殊作业、过程、试验或
检验的人员有无资格证书
从事SPC的员工是否接受过培训, 他们要注意哪些偏差做哪些工作是 否明确
2. 1.4
是否有人员配置计划及有关岗位顶 替的规定?
有无人员配置计划和顶岗计划
配置计划中是否考虑了缺勤因素
顶岗人员是否有资格证明
有无所有检验人员每年一次的视力 测定记录
各工作岗位(包括返工岗位)的照明
是否都符合要求,如何检验照明度 够否
各工作岗位(包括返工岗位)是否会 对环境带来污染
各工作岗位(包抵返工岗位)以日产 量所需部件数为尺度,有无足够的 周转货架、容器,有无防止混批混 料的措施