铣刀铣削速度
铣削工时参照表

铣削宽度Ac 12
L2(mm) 2.5 2.5 2.5 2.5 2.5 2.5 2.5
铣削基本时间计算公式表
超出量L2(mm)
每分进给量Vf(mm)
2.5
80.0
铣削宽度Ac(mm)
工件直径D(mm)
12
走刀次数i(mm) 1
铣削平面(纵横): 铣切齿轮:
T基1: 4.25
切入量L1(mm) 17.8
工件齿数Z 5
T基=(L0+L1+L2)/Vf*i T基=(Ac+L1+L2)/Vf*Z
T基2 4.25
L—加工长度(mm) 加工工步
S—对边长度(mm) 常量部分Tf1(min)
60-130 50-105 35-50 35-45 55-120 35-80 30-60 45-80
230 0.2 65 0.22 135 0.27 35 0.33 24 0.51 24 0.86 2、变量部分Tf2(min)
270 0.25 75 0.18 160 0.32 45 0.39 27 0.61 27 1.04 3、变量部分Tf2(min)
40 0.08 15 0.56 25 0.11
2
加工长度L(mm) Tf2(min)
加工长度L(mm) Tf2(min)
加工长度L(mm) Tf2(min)
加工长度L(mm) Tf2(min)
加工长度L(mm) Tf2(min)
加工长度L(mm) Tf2(min)
20 0.07 10 0.66 10 0.09
6 0.11
8 0.17
铣刀铣削速度的确定
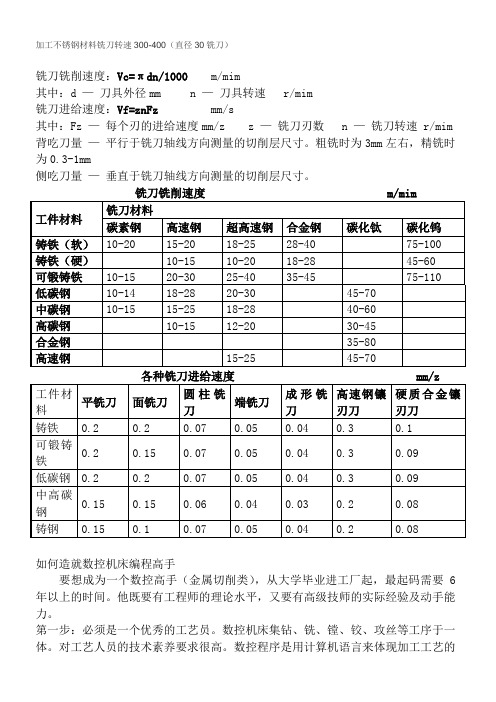
加工不锈钢材料铣刀转速300-400(直径30铣刀)铣刀铣削速度:Vc=πdn/1000 m/mim其中:d —刀具外径mm n —刀具转速 r/mim铣刀进给速度:Vf=znFz mm/s其中:Fz —每个刃的进给速度mm/z z —铣刀刃数 n —铣刀转速 r/mim 背吃刀量—平行于铣刀轴线方向测量的切削层尺寸。
粗铣时为3mm左右,精铣时为0.3-1mm侧吃刀量—垂直于铣刀轴线方向测量的切削层尺寸。
如何造就数控机床编程高手要想成为一个数控高手(金属切削类),从大学毕业进工厂起,最起码需要6年以上的时间。
他既要有工程师的理论水平,又要有高级技师的实际经验及动手能力。
第一步:必须是一个优秀的工艺员。
数控机床集钻、铣、镗、铰、攻丝等工序于一体。
对工艺人员的技术素养要求很高。
数控程序是用计算机语言来体现加工工艺的过程。
工艺是编程的基础。
不懂工艺,绝不能称会编程。
通过长时间的学习与积累,你应达到下列技术水准和要求:1、熟悉钻、铣、镗、磨、刨床的结构、工艺特点,2、熟悉加工材料的性能。
3、扎实的刀具理论基础知识,掌握刀具的常规切削用量等。
4、熟悉本企业的工艺规范、准则及各种工艺加工能达到的一般要求,常规零件的工艺路线。
合理的材料消耗及工时定额等。
5、收集一定量的刀具、机床、机械标准的资料。
特别要熟悉数控机床用的刀具系统。
6、熟悉冷却液的选用及维护。
7、对相关工种要有常识性的了解。
比如:铸造、电加工、热处理等。
8、有较好的夹具基础。
9、了解被加工零件的装配要求、使用要求。
10、有较好的测量技术基础。
第二步:精通数控编程和计算机软件的应用。
这一点,我觉得比较容易,编程指令也就几十个,各种系统大同小异。
一般花1-2个月就能非常熟悉。
自动编程软件稍复杂些,需学造型。
但对于cad基础好的人来说,不是难事。
另外,如果是手工编程,解析几何基础也要好!读书人对这些知识的学习是最适应的。
在实践中,一个好程序的标准是:1、易懂,有条理,操作者人人都能看懂。
锯片铣刀切削速度计算【干货经验】
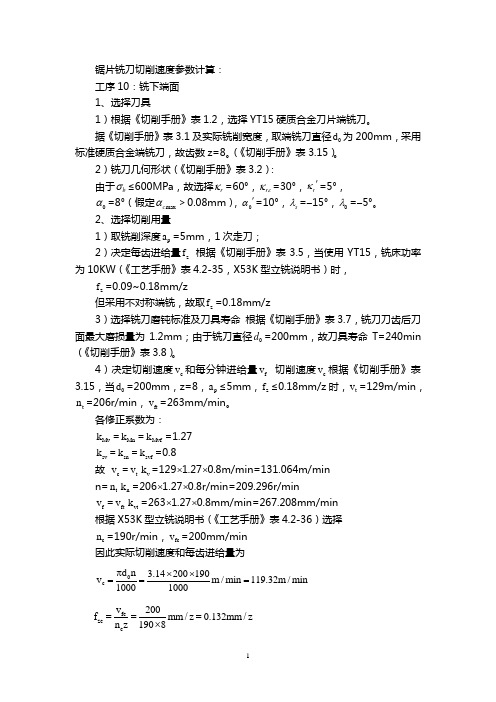
锯片铣刀切削速度参数计算: 工序10:铣下端面 1、选择刀具1)根据《切削手册》表1.2,选择YT15硬质合金刀片端铣刀。
据《切削手册》表3.1及实际铣削宽度,取端铣刀直径0d 为200mm ,采用标准硬质合金端铣刀,故齿数z=8。
(《切削手册》表3.15)。
2)铣刀几何形状(《切削手册》表3.2):由于b σ≤600MPa ,故选择r κ=60°,r εκ=30°,r κ'=5°,0α=8°(假定max c α>0.08mm ),0α'=10°,s λ=-15°,0λ=-5°。
2、选择切削用量1)取铣削深度p a =5mm ,1次走刀;2)决定每齿进给量z f 根据《切削手册》表3.5,当使用YT15,铣床功率为10KW (《工艺手册》表4.2-35,X53K 型立铣说明书)时,z f =0.09~0.18mm/z但采用不对称端铣,故取z f =0.18mm/z3)选择铣刀磨钝标准及刀具寿命 根据《切削手册》表3.7,铣刀刀齿后刀面最大磨损量为1.2mm ;由于铣刀直径0d =200mm ,故刀具寿命T=240min (《切削手册》表3.8)。
4)决定切削速度c v 和每分钟进给量f v 切削速度c v 根据《切削手册》表3.15,当0d =200mm ,z=8,p a ≤5mm ,z f ≤0.18mm/z 时,t v =129m/min ,t n =206r/min ,ft v =263mm/min 。
各修正系数为:Mv k =Mn k =Mvf k =1.27 sv k =sn k =svf k =0.8故 c v =t v v k =129⨯1.27⨯0.8m/min=131.064m/min n=t n n k =206⨯1.27⨯0.8r/min=209.296r/minf v =ft v vt k =263⨯1.27⨯0.8mm/min=267.208mm/min 根据X53K 型立铣说明书(《工艺手册》表4.2-36)选择c n =190r/min ,fc v =200mm/min 因此实际切削速度和每齿进给量为0c d n 3.14200190v m /min 119.32m /min 10001000π⨯⨯=== fc zc c v 200f mm /z 0.132mm /z n z 1908===⨯5)校验机床功率 根据《切削手册》表3.23,当b σ<560MPa ,e a ≤138mm ,p a ≤5.9mm ,0d =200mm ,z=8,f v =200mm/min ,近视为cc P =7.8KW根据X53K 型立铣说明书(《工艺手册》表4.2-35),机床主轴允许的功率为cM P =10⨯0.85KW=8.5KW故cc P <cM P ,因此所选择的切削用量可以采用,即p a =5mm ,f v =200mm/min ,n=190r/min ,c v =119.32m/min ,z f =0.132mm/z 。
铣削加工参数

铣削加工参数
1铣削要素
铣削速度v:铣刀旋转运动的线速度,单位为m/min。
铣削深度ap:平行于铣刀轴线测量的切削层尺寸,单位为mm。
铣削宽度ae:垂直于铣刀轴线测量的切削层尺寸,单位为mm。
每齿进给量af:铣刀每转过一个刀齿,工件与铣刀的相对位移量,单位为mm/z。
Ra:以轮廓算术平均偏差评定的表面粗糙度参数,单位为μm。
dd:刀具直径,单位为mm。
切削速度与转速关系:
m/min
r/min
v:切削速度,铣刀旋转运动的线速度,单位为m/min。
n:刀具的转速,单位为r/min。
d:刀具观察点直径,单位为mm。
2铣削参数。
铣削用量进给量给速度

铣削用量进给量给速度————————————————————————————————作者:————————————————————————————————日期:铣削用量如何确定? 1. 铣削速度υ指铣刀旋转的圆周线速度,单位为m/min 。
2.计算公式:1000dnπυ=3. 式中 d ——铣刀直径,mm;n ——主轴(铣刀)转速,r/min;从上公式可得到主轴(铣刀)转速 dn πυ1000=表一铣削速度υ推荐表工件材料 硬度/HB 铣削速度υ/m/min高速钢铣刀 硬质合金铣刀 低、中炭钢<22021~40 60~150 225~290 15~36 54~115 300~425 9~15 36~75 高炭钢<220 18~36 60~130 225~325 14~21 53~105 325~375 8~21 36~48 375~425 6~10 35~45 合金钢 <220 15~35 55~120 225~325 10~24 37~80 325~425 5~9 30~60 工具钢 200~250 12~23 45~83 灰铸铁110~140 24~36 110~115 150~225 15~21 60~110 230~290 9~18 45~90 300~320 5~10 21~30 可锻铸铁110~160 42~50 100~200 160~200 24~36 83~120 200~240 15~24 72~110 240~280 9~11 40~60 铸 钢低炭100~150 18~27 68~105 中炭 100~160 18~27 68~105 160~200 15~21 60~90 200~240 12~21 53~75 钢炭 180~2409~18 53~80 铝合金 180~300 360~600 铜合金 45~100 120~190 镁合金180~270150~600进给量在铣削过程中,工件相对于铣刀的移动速度称为进给量。
铣刀进给速度计算公式

铣刀进给速度计算公式铣刀进给速度是指铣削过程中刀具在工件表面移动的速度。
在机械加工中,铣刀进给速度的计算对于保证加工质量、提高生产效率至关重要。
本文将介绍铣刀进给速度的计算公式及其相关内容。
一、铣刀进给速度的定义铣刀进给速度即刀具在单位时间内在工件表面移动的距离,通常用mm/min表示。
铣刀进给速度的大小直接影响到加工效率和加工质量,因此在进行铣削加工时需要合理选择进给速度。
二、铣刀进给速度的计算公式铣刀进给速度的计算公式为:Vf = fn × n × z其中,Vf表示铣刀进给速度,fn表示进给量,n表示主轴转速,z 表示刀具齿数。
进给量fn是指每个齿面在单位时间内切削的金属量。
它的计算公式为:fn = fz × z × n其中,fz表示每齿进给量。
主轴转速n是指铣床主轴每分钟转动的圈数,单位为r/min。
刀具齿数z是指刀具上的刃数,通常为2、4、6、8等。
根据以上公式,我们可以计算出铣刀进给速度的具体数值。
三、铣刀进给速度的影响因素铣刀进给速度的大小受到多个因素的影响,下面列举几个主要因素:1. 切削材料的硬度:不同硬度的材料对铣刀的进给速度有不同的要求。
通常来说,硬度较高的材料要求较低的进给速度,以保证刀具的寿命和切削效果。
2. 切削深度:切削深度越大,铣刀进给速度应相应增加,以保证切削效率和加工表面质量。
3. 刀具材料和涂层:不同材料和涂层的刀具具有不同的切削性能,因此对进给速度的要求也不同。
4. 切削方式:不同的切削方式对进给速度的要求不同。
例如,高速切削要求较高的进给速度,而硬切削则要求较低的进给速度。
四、铣刀进给速度的优化选择在实际加工中,为了保证加工效率和加工质量,需要合理选择铣刀进给速度。
一般来说,进给速度过高容易导致刀具磨损加剧,加工表面质量下降;进给速度过低则会导致加工效率低下。
因此,在选择铣刀进给速度时,需要综合考虑材料硬度、切削深度、刀具材料和涂层等因素,并参考相关的经验数据进行调整。
铣削加工参数

铣削加工参数1铣削要素铣削速度v:铣刀旋转运动的线速度,单位为m/min。
铣削深度ap:平行于铣刀轴线测量的切削层尺寸,单位为mm。
铣削宽度ae:垂直于铣刀轴线测量的切削层尺寸,单位为mm。
每齿进给量af:铣刀每转过一个刀齿,工件与铣刀的相对位移量,单位为mm/z。
Ra:以轮廓算术平均偏差评定的表面粗糙度参数,单位为μm。
dd:刀具直径,单位为mm。
切削速度与转速关系:m/XXXr/minv:切削速度,铣刀旋转运动的线速度,单位为m/min。
n:刀具的转速,单位为r/min。
d:刀具观察点直径,单位为mm。
2铣削参数XXX热轧状态(硬度:187HB)面铣刀铣削硬质合金飞刀(YT15等)类别Raae(mm)ap(mm)af(mm/z)v(m/min)2~30.12801004~50.粗铣6.32~30.12802004~50.0.20.1000.40.精铣3.20.20.2000.40.钢热轧状态(硬度:187HB)柱铣刀侧齿铣削类别Raddap高速钢铣刀(W18Cr4V等)硬质合金铣刀(YT15等)ae(mm)af(mm/z)v(m/min)ae(mm)af(mm/z)v (m/min)10..10520..粗铣6.310..1120201020..0.10..10.1050.20..20.精铣3.20.10..10.20100.20..20.钢热轧状态(硬度:187HB)柱铣刀底齿铣削高速钢铣刀(W18Cr4V等)硬质合金铣刀(YT15等)类别Raddaeap(mm)af(mm/z)v(m/min)ap(mm)af(mm/z)v (m/min)10..101020..粗铣6.310..1120202020..0.10..10.10100.20..20.精铣3.20.10..10.20200.20..20.钢调质状况(硬度:28~32HRC)面铣刀铣削硬质合金飞刀(YT15等)类别Raae(mm)ap(mm)af(mm/z)v(m/min)1~20.12501002~30.粗铣6.31~20.12502002~30.0.20.1000.40.精铣3.20.20.2000.40.钢调质状态(硬度:28~32HRC)柱铣刀侧齿铣削高速钢铣刀(W18Cr4V等)硬质合金铣刀(YT15等)类别Raddapae(mm)af(mm/z)v(m/min)ae(mm)af(mm/z)v (m/min)10..058010520..0360粗铣6.310..180201020..0860精铣3..10..10.02800.20.120100.20.010.030.021520150.20.10.20.010.030.0260806045钢调质状况(硬度:28~32HRC)柱铣刀底齿铣削高速钢铣刀(W18Cr4V等)硬质合金铣刀(YT15等)类别Raddaeap(mm)af(mm/z)v(m/min)ap(mm)af(mm/z)v (m/min)10..0580101020..0360粗铣6.310..180202020..08600.10..10.028010100.20..20.0160精铣3.20.10..10.038020200.20..20.Cr钢热轧状况(硬度:212HB)面铣刀铣削硬质合金飞刀(YT15等)类别Raae(mm)ap(mm)af(mm/z)v(m/min)1~20.12501002~30.粗铣6.31~20.12502002~30.0.20.1000.40.精铣3.20.20.2000.40.Cr钢热轧状态(硬度:212HB)柱铣刀侧齿铣削高速钢铣刀(W18Cr4V等)硬质合金铣刀(YT15等)种别Raddapae(mm)af(mm/z)v(m/min)ae(mm)af(mm/z)v (m/min)10..10520..粗铣6.310..1110201020..0.10..10.1050.20..20.精铣3.20.10..10.20100.20..20.Cr钢热轧状况(硬度:212HB)柱铣刀底齿铣削种别Raddae高速钢铣刀(W18Cr4V等)硬质合金铣刀(YT15等)ap(mm)af(mm/z)v(m/min)ap(mm)af(mm/z)v (m/min)10..101020..粗铣6.310..1110202020..0.10..10.10100.20..20.精铣3.20.10..10.20200.20..20.Cr钢调质状况(硬度:28~32HRC)面铣刀铣削硬质合金飞刀(YT15等)种别Raae(mm)ap(mm)af(mm/z)v(m/min)1~20.12201002~30.粗铣6.31~20.12202002~30.0.20.1000.40.精铣3.20.20.2000.40.Cr钢调质状态(硬度:28~32HRC)柱铣刀侧齿铣削高速钢铣刀(W18Cr4V等)硬质合金铣刀(YT15等)种别Raddapae(mm)af(mm/z)v(m/min)ae(mm)af(mm/z)v (m/min)10..057010520..0360粗铣6.310..170201020..08600.10..10.02701050.20..20.0160精铣3.20.10..10.037020100.20..20.Cr钢调质状态(硬度:28~32HRC)柱铣刀底齿铣削高速钢铣刀(W18Cr4V等)硬质合金铣刀(YT15等)类别Raddaeap(mm)af(mm/z)v(m/min)ap(mm)af(mm/z)v (m/min)10..0570101020..0360粗铣6.310..170202020..0860精铣3..10..10.02700.20.120200.20.010.030.021520150.20.10.20.010.030.02607060H62硬化状态(硬度:164HB)面铣刀铣削硬质合金飞刀(YG8等)类别Raae(mm)ap(mm)af(mm/z)v(m/min)2~30.23501004~50.1300粗铣6.32~30.23502004~50.13000.20.1000.40.精铣1.60.20.2000.40.H62软化状况(硬度:164HB)柱铣刀侧齿铣削高速钢铣刀(W18Cr4V等)硬质合金铣刀(YG8等)类别Raddapae(mm)af(mm/z)v(m/min)ae(mm)af(mm/z)v (m/min)20..10530..粗铣6.320..1180201030..0.10..10.1050.20..20.精铣3.20.10..10.20100.20..20.H62硬化状态(硬度:164HB)柱铣刀底齿铣削高速钢铣刀(W18Cr4V等)硬质合金铣刀(YG8等)类别Raddaeap(mm)af(mm/z)v(m/min)ap(mm)af(mm/z)v (m/min)20..101030..粗铣6.320..1180202030..0.10..10.10100.20..20.精铣3.20.10..10.20200.20..20.A12-T4固溶处置惩罚并时效状况(硬度:105HB)面铣刀铣削类别Ra硬质合金飞刀(YG8等)ae(mm)100粗铣6.3200100精铣1.6200ap(mm)2~34~52~34~50.20.40.20.4af(mm/z)0.30.150.30.150.060.040.060.04v(m/min)5004005004005004005004002A12-T4固溶处置惩罚并时效状况(硬度:105HB)柱铣刀侧齿铣削高速钢铣刀(W18Cr4V等)硬质合金铣刀(YG8等)类别Raddapae(mm)af(mm/z)v(m/min)ae(mm)af(mm/z)v (m/min)20..10530..粗铣6.320..1250201030..0.10..10.1050.20..20.精铣3.20.10..10.20100.20..20.A12-T4固溶处置惩罚并时效状况(硬度:105HB)柱铣刀底齿铣削高速钢铣刀(W18Cr4V等)硬质合金铣刀(YG8等)种别Raddaeap(mm)af(mm/z)v(m/min)ap(mm)af(mm/z)v (m/min)20..101030..粗铣6.320..1250202030..0.10..10.10100.20..20.精铣3.20.10..10.20200.20..20.TC4固溶处置惩罚并时效状况(硬度:320~380HB)面铣刀铣削硬质合金飞刀(YG8等)类别Raae(mm)ap(mm)af(mm/z)v(m/min)20.083610040.0425粗铣6.320.083620040.0425精铣1..20.03452000.40.20.40.020.030.02304530TC4固溶处理并时效状态(硬度:320~380HB)柱铣刀侧齿铣削高速钢铣刀(W18Cr4V等)硬质合金铣刀(YG8等)种别Raddapae(mm)af(mm/z)v(m/min)ae(mm)af(mm/z)v (m/min)1.50..50.084010530..0430粗铣6.31.50.1121.50.140201030..08300.20..20.05401050.40..40.0330精铣3.20.20..20.054020100.40..40.0330TC4固溶处置惩罚并时效状况(硬度:320~380HB)柱铣刀底齿铣削高速钢铣刀(W18Cr4V等)硬质合金铣刀(YG8等)类别Raddaeap(mm)af(mm/z)v(m/min)ap(mm)af(mm/z)v (m/min)1.50..50.0840101030..0430粗铣6.31.50.1121.50.140202030..08300.20..20.054010100.40..40.0330精铣3.2 0.20..20.05402020。
常用的铣刀速度表
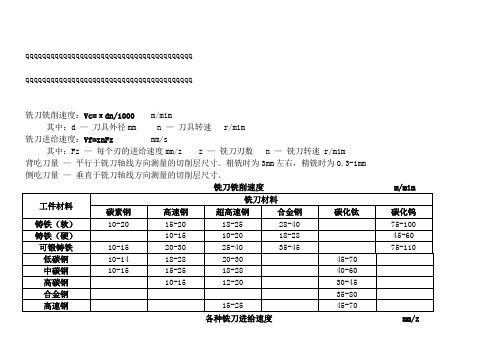
qqqqqqqqqqqqqqqqqqqqqqqqqqqqqqqqqqqqqqqq
铣刀铣削速度:Vc=πdn/1000m/mim
其中:d—刀具外径mm n—刀具转速r/mim
铣刀进给速度:Vf=znFzmm/s
其中:Fz—每个刃的进给速度mm/zz —铣刀刃数 n—铣刀转速 r/mim
18-28
45-60
可锻铸铁
10-15
20-30
25-40
35-45
75-110
低碳钢
10-14
18-28
20-30
45-70
中碳钢
10-15
15-25
18-28
40-60
高碳钢
10-15
12-20
30-45
合金钢
35-80
高速钢
15-25
45-70
各种铣刀进给速度mm/z
工件材料
平铣刀
面铣刀
圆柱铣刀
端铣刀
成形铣刀
高速钢镶刃刀
硬质合金镶刃刀
铸铁
0.2
0.2
0.07
0.05
0.04
0.3
0.1
可锻铸铁
0.2
0.15
0.07
0.05
0.04
0.3
0.09
低碳钢
0.2
0.2
7
0.05
0.04
0.3
0.09
中高碳钢
0.15
0.15
0.06
0.04
0.03
0.2
0.08
铸钢
0.15
0.1
0.07
数控铣削加工切削速度、进给量、背吃刀量选取参考表

合 金 钢 ( 中 碳 ) ~
合 金 钢 ( 高 碳 ) ~
高 强 度 钢 ~
225 350 200 275 150 250
高 速 钢 ~
工 具 钢 ~
12 12 12 18 18 18 18 25~ 50 25~ 50 25~ 50 25~ 50 10 10 10 10 12 12 12 12 18 18 18 18 25~ 50 25~ 50 25~ 50 25~ 50 10 10 10 10 12 12 12 12 18 18 18 18 25~ 50 25~ 50 25~ 50 25~ 50 10 10 10 10 12 12 12 12 18 18 18 18 25~ 50 25~ 50 25~ 50 25~ 50 10 10 10 10 12 12 12 12 18 18 18 18 25~ 50 25~ 50 25~ 50 25~ 50 10 10 10 10 12 12 12 12 18 18
低 碳 钢
HB:125 225
~
中 碳 钢 ~
175 275 175 275
高 碳 钢 ~
合 金 钢 ~( 低 碳 )
125 225
0.5 1.5 d0/4 d0/2 0.5
1.5 d0/4 d0/2 0.5 1.5 d0/4 d0/2 0.5 1.5 d0/4 d0/2 0.5 1.5 d0/4 d0/2 0.5 1.5 d0/4 d0/2 0.5 1.5 d0/4 d0/2 0.5 1.5 d0/4 d0/2 0.5 1.5 d0/4 d0/2 0.5 1.5 d0/4 d0/2 0.5 1.5 d0/4 d0/2 0.5 1.5 d0/4 d0/2 0.5 1.5 d0/4 d0/2 0.5 1.5 d0/4 d0/2 0.5 1.5 d0/4 d0/2 0.5 1.5 d0/4 d0/2 0.5 1.5 d0/4 d0/2 0.5 1.5 d0/4 d0/2 0.5 1.5 d0/4 d0/2 0.5 1.5 d0/4 d0/2 0.5 1.5 d0/4 d0/2 0.5 1.5 d0/4 d0/2 0.5 1.5
常用的铣刀速度表
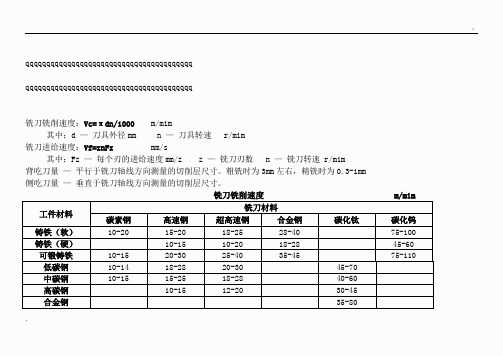
qqqqqqqqqqqqqqqqqqqqqqqqqqqqqqqqqqqqqqqqqqqqqqqqqqqqqqqqqqqqqqqqqqqqqqqqqqqqqqqq铣刀铣削速度:Vc=πdn/1000 m/mim其中:d —刀具外径mm n —刀具转速 r/mim铣刀进给速度:Vf=znFz mm/s其中:Fz —每个刃的进给速度mm/z z —铣刀刃数 n —铣刀转速 r/mim背吃刀量—平行于铣刀轴线方向测量的切削层尺寸。
粗铣时为3mm左右,精铣时为0.3-1mm侧吃刀量—垂直于铣刀轴线方向测量的切削层尺寸。
铣刀铣削速度 m/mim工件材料铣刀材料碳素钢高速钢超高速钢合金钢碳化钛碳化钨铸铁(软)10-20 15-20 18-25 28-40 75-100 铸铁(硬)10-15 10-20 18-28 45-60 可锻铸铁10-15 20-30 25-40 35-45 75-110 低碳钢10-14 18-28 20-30 45-70中碳钢10-15 15-25 18-28 40-60高碳钢10-15 12-20 30-45合金钢35-80’.高速钢15-25 45-70各种铣刀进给速度 mm/z 工件材料平铣刀面铣刀圆柱铣刀端铣刀成形铣刀高速钢镶刃刀硬质合金镶刃刀铸铁0.2 0.2 0.07 0.05 0.04 0.3 0.1可锻铸铁0.2 0.15 0.07 0.05 0.04 0.3 0.09低碳钢0.2 0.2 0.07 0.05 0.04 0.3 0.09中高碳钢0.15 0.15 0.06 0.04 0.03 0.2 0.08 铸钢0.15 0.1 0.07 0.05 0.04 0.2 0.08’.。
铣刀铣削速度的确定

加工不锈钢材料铣刀转速300-400(直径30铣刀)定基准刀为标准刀,自动设置刀偏置法:对刀步骤如下:(1)用▲、键移动蓝色亮条对准2号基准刀的刀偏号#0002位置处,按F5键设置2号刀为标准刀具,则所在行变成红色亮条。
(2)用基准刀试切工件右端面,记录试切点A的Z机床坐标;试切工件外圆,记录A 点的X机床坐标,退刀后停车,测量已切削轴段外径ΦD。
(3)基准刀按记录值通过“点动+步进”方式重回A点,在刀偏表的试切直径和试切长度栏内分别输入ΦD和零。
(4)退刀,选择非基准刀的刀号手动换刀,让各非基准刀的刀尖分别在主轴转动下通过“点动+步进”方式目测对准A点,然后分别在相应刀偏号的试切直径栏和试切长度栏内输入ΦD和零,则各非基准刀的刀偏置会在X、Z偏置栏处自动显示。
(5)基准刀重回A点后,MDI运行“G91 G00/或G01 X[100-ΦD] Z50”,使其处于程序起点位置。
2.将基准刀在对刀基准点处坐标置零,自动显示刀偏置法:对刀步骤如下:(1)与前述步骤(2)相同。
(2)基准刀按记录值通过“点动+步进”方式重回试切点A。
(3)在图4界面按F1键“X轴置零”,按F2键“Z轴置零”,则CRT显示的“相对实际坐标”为(0,0)。
(4)手动换非基准刀,使其刀尖目测对齐A点,这时CRT上显示的“相对实际坐标”的数值,就是该刀相对于基准刀的刀偏置,用▲、键移动蓝色亮条到非基准刀的刀偏号,分别将其记录并输入到相应位置。
(5)与前述步骤(5)相同。
3. 多刀试切外圆轴段,人工计算获得刀偏置法:系统在手动状态下对好1、2、4号刀,并切出一个台阶轴,分别记录各刀切削终点的机床坐标,并测量各段的直径和长度。
换3号切断刀,切一退刀槽,以切断刀的右尖点对刀,记录B点坐标,测量ΦD3和L3。
获得了上述数据后,根据各刀对应的F、E、D、B点与程序原点O的坐标增量关系,可知基准刀的程序起点的机床坐标为(X2-ΦD2+100,Z2-L2+50);而且可以推出各非基准刀对应程序原点的机床坐标并通过人工计算获得刀偏置,将记录值和计算值填入相应空格处。
数控铣削加工切削速度 进给量 背吃刀量选取参考表

0.075 0.05 0.038 0.075-0.102 0.102-0.13 0.075-0.102 0.05-0.075
0.102-0.13
0.13-0.15
0.102-0.13
0.075-0.102
0.025 0.05 0.038 0.025 0.05 0.075 0.05 0.038 0.075 0.102 0.075 0.05
d0/2
0.5
1.5
d0/4
d0/2
0.5
1.5
合 金 钢
d0/4 d0/2
(
0.5
高 碳
1.5
)
d0/4
d0/2
~
0.5
175 275
1.5
d0/4
d0/2
0.5
1.5
d0/4
d0/2
0.5
1.5
d0/4
高 强 度
d0/2 0.5
钢
1.5
d0/4
~
d0/2
225 350
0.5
1.5
d0/4
d0/2
0.102
0.13
0.102
0.075
0.013-0.018 0.018-0.025
0.013 0.013 0.025 0.025-0.05 0.013-0.025 0.013 0.038-0.05 0.038-0.075 0.025-0.05 0.013-0.025
0.05-0.075
0.063-0.102
18
30-34
23-26
20-21
18
18-26 14-20 12--17 11--15 18-26 14-20 12--17 11--15 18-26 14-20 12--17 11--15
铣削的切削用量
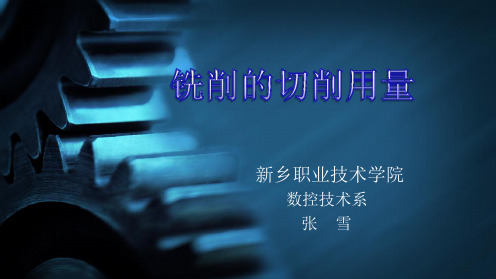
新乡职业技术学院数控技术系张 雪1.了解切削用量的选择。
2.掌握切削用量的计算方法。
铣削要素的分类:铣削速度Vc进给量f铣削深度ap铣削宽度ae。
1.铣削速度Vc铣削时,铣刀切削刃上选定点相对于工件的主运动的瞬时速度称为铣削速度。
即指铣刀旋转的圆周线速度,单位为m/min。
计算公式为:例1:在X6132型铣床上,用直径为80mm的圆柱形铣刀,以25m/min 的铣削速度进行铣削。
铣床主轴转速应调整到多少?解:已知d=80mm,Vc=25m/min= =99.5r/min答:根据铣床铭牌,实际应调整到95r/min。
2、进给量f在铣削过程中,工件相对于铣刀的移动速度称为进给量。
有三种表示方法:(1)每齿进给量fz 铣刀每转过一个刀齿,工件沿进给方向移动的距离,单位为mm/z。
(2)每转进给量f 铣刀每转过一转,工件沿进给方向移动的距离,单位为mm/r。
(3)每分钟进给量Vf 铣刀每旋转1min,工件沿进给方向移动的距离,单位为mm/min。
三种进给量的关系为: Vf =fn= fz zn例2:用一把直径为25mm、齿数为3的立铣刀,在X5032型铣床上铣削,采用每齿进给量fz为0.04mm/z,铣削速度Vc为24m/min。
试调整铣床的转速和进给速度。
解:已知d=25mm,z=3,fz=0.04mm/z,Vc=24m/min= =305.7r/min根据铣床铭牌,实际选择转速为300r/min.V f = f z zn=0.043300=36mm/min根据铣床铭牌,实际选择37.5mm/min.答:调整铣床的转速为300r/min,进给速度为37.5mm/min3、铣削宽度ae即铣刀在一次进给中所切掉的工件表层的宽度,单位为mm。
一般立铣刀和端铣刀的铣削宽度约为铣刀的直径的50%~60%左右。
4、背吃刀量ap即铣刀在一次进给中所切掉的工件表层的厚度,即工件已加工表面和待加工表面间的垂直距离,单位为mm。
- 1、下载文档前请自行甄别文档内容的完整性,平台不提供额外的编辑、内容补充、找答案等附加服务。
- 2、"仅部分预览"的文档,不可在线预览部分如存在完整性等问题,可反馈申请退款(可完整预览的文档不适用该条件!)。
- 3、如文档侵犯您的权益,请联系客服反馈,我们会尽快为您处理(人工客服工作时间:9:00-18:30)。
铣刀铣削速度:Vc=πdn/1000 m/mim其中:d —刀具外径mm n —刀具转速 r/mim铣刀进给速度:Vf=znFz mm/s其中:Fz —每个刃的进给速度mm/z z —铣刀刃数 n —铣刀转速 r/mim 背吃刀量—平行于铣刀轴线方向测量的切削层尺寸。
粗铣时为3mm左右,精铣时为0.3-1mm侧吃刀量—垂直于铣刀轴线方向测量的切削层尺寸。
如何造就数控机床编程高手要想成为一个数控高手(金属切削类),从大学毕业进工厂起,最起码需要6年以上的时间。
他既要有工程师的理论水平,又要有高级技师的实际经验及动手能力。
第一步:必须是一个优秀的工艺员。
数控机床集钻、铣、镗、铰、攻丝等工序于一体。
对工艺人员的技术素养要求很高。
数控程序是用计算机语言来体现加工工艺的过程。
工艺是编程的基础。
不懂工艺,绝不能称会编程。
通过长时间的学习与积累,你应达到下列技术水准和要求:1、熟悉钻、铣、镗、磨、刨床的结构、工艺特点,2、熟悉加工材料的性能。
3、扎实的刀具理论基础知识,掌握刀具的常规切削用量等。
4、熟悉本企业的工艺规范、准则及各种工艺加工能达到的一般要求,常规零件的工艺路线。
合理的材料消耗及工时定额等。
5、收集一定量的刀具、机床、机械标准的资料。
特别要熟悉数控机床用的刀具系统。
6、熟悉冷却液的选用及维护。
7、对相关工种要有常识性的了解。
比如:铸造、电加工、热处理等。
8、有较好的夹具基础。
9、了解被加工零件的装配要求、使用要求。
10、有较好的测量技术基础。
第二步:精通数控编程和计算机软件的应用。
这一点,我觉得比较容易,编程指令也就几十个,各种系统大同小异。
一般花1-2个月就能非常熟悉。
自动编程软件稍复杂些,需学造型。
但对于cad基础好的人来说,不是难事。
另外,如果是手工编程,解析几何基础也要好!读书人对这些知识的学习是最适应的。
在实践中,一个好程序的标准是:1、易懂,有条理,操作者人人都能看懂。
2、一个程序段中指令越少越好,以简单、实用、可靠为目的。
从编程角度对指令的理解,我以为指令也就G00和G01,其他都为辅助指令,是方便编程才设置的。
3、方便调整。
零件加工精度需做微调时最好不用改程序。
比如,刀具磨损了,要调整,只要改刀具偏置表中的长度、半径即可。
4、方便操作。
程序编制要根据机床的操作特点来编,有利于观察、检查、测量、安全等。
例如,同一种零件,同样的加工内容,在立式加工中心和卧式加工中心分别加工,程序肯定不一样。
在机械加工中,最简单的方法就是最好的方法。
只要有实践经验的同行,想必都会同意这句话吧!第三步:能熟练操作数控机床。
这需要1-2年的学习,操作是讲究手感的,初学者、特别是大学生们,心里明白要怎么干,可手就是不听使唤。
在这过程中要学:系统的操作方式、夹具的安装、零件基准的找正、对刀、设置零点偏置、设置刀具长度补偿、半径补偿,刀具与刀柄的装、卸,刀具的刃磨、零件的测量(能熟练使用游标卡尺、千分卡、百分表、千分表、内径杠杆表)等。
最能体现操作水平的是:卧式加工中心和大型龙门(动粱、顶梁)加工中心。
操作的练习需要悟性!有时真有一种“悠然心会,妙处难与君说”的意境!在数控车间你就静下心来好好练吧!一般来说,从首件零件的加工到加工精度合格这一过程都是要求数控编程工艺员亲自完成。
你不能熟练操作机床,这一关是过不了的。
第四步:必须有良好的工装夹具基础和测量技术水平。
我这里把工装夹具及测量技术单列一条是因为:它对零件加工质量起到与机床精度一样重要的作用,是体现工艺人员水平的标志之一。
整个工艺系统:机床精度是机床生产厂保证的,刀具及切削参数是刀具商提供的,一般问题都不大,只有工装夹具是工艺人员针对具体零件专门设计的,大凡上数控机床的零件都是有一定难度的,因而往往会出现难于预料的问题,我从事数控机床用户零件切削调试10来年,不要整改的夹具还真没碰上过。
调试时,首件零件加工不合格,一半以上原因是由于夹具的定位、夹压点、夹紧力不合理引起的。
夹具方面的原因分析难度在于只能定性,很难定量。
如对夹具设计、零件装夹没有经验的话,那困难就大了。
在这方面的学习,建议向做精密坐标镗床的高级技师们请教。
精准的测量水平时从事机加工的基本功之一,要能熟练使用游标卡尺、千分卡、百分表、千分表、内径杠杆表、卡钳等。
有时零件加工,三坐标测量仪是指望不上的。
必须靠手工测量。
试想,零件都量不准确,哪个领导和工人师傅会信任你?练好测量技术可要花很长时间哟!第五步熟悉数控机床。
精通数控机床的维护保养。
所谓熟悉数控机床,应做到:1、熟悉数控电气元件及控制原理。
能说出电箱里各个元件的名称及作用,能看懂电气原理图。
能根据电气报警号,查出报警内容。
2、了解滚珠丝杆的结构、传动原理。
清楚哪些因素对机床精度的影响比较大。
3、了解机床丝杆两端轴承的结构及对机床精度的影响。
4、了解机床的润滑系统(轴承、主轴、各运动副、齿轮箱等),清楚各润滑点的分布。
机床润滑油的牌号及每周或每月油的正常消耗量。
5、了解机床的致冷系统:切削(水、气)冷却、主轴冷却、电箱冷却等6、了解机床的主传动结构,每台机床转速与扭矩之间具体数据特性。
7、了解机床导轨副特点:是线轨还是滑轨,刚性(承载能力)如何?8、能排除常见操作故障(如:超极限、刀库刀号出错等)9、精通机床的各项精度(静态、动态)指标及检测方法。
10、熟悉刀库机构及换刀原理。
以上几条没有3年以上的时间锻炼,恐怕是很难达到要求的。
而且很多企业还不具备学习的条件。
建议多向设备维修部门的师傅请教。
机床的维护保养细节我就不多讲了,各企业都有各自的经验和标准。
第六培养良好的习惯,适应数控加工的特点。
(这一条是我个人所见,是否合理,大家可以讨论。
)适合数控加工的高手应该是谦逊、严谨,冷静,思维缜密,做事有条理而又有主见的人。
1、一些大型零件的加工,不但加工内容多,还有空间三维坐标的转换。
加工轨迹的计算非常复杂和难以确定,如果考虑问题不细致、全面,计算不精确,调试时程序修改越改越乱,出错的概率就大。
“三思而后行”用在这里是最恰当不过的了。
2、零件调试过程是多人合作的过程,其中包括操作工、检验员、夹具设计、夹具装配人员等。
出现问题时,要多征询他们的意见,多做试验,切忌武断下定论。
对出错的员工不要过多责备,要有“慈悲”的心态。
3、数控机床的工作是靠指令来控制的,调试时,在“启动”按钮按下去之前,你必须十分是清楚机床运行的轨迹。
要严谨、细致,千万不能让机床先动了再说。
一旦程序有误或补偿参数不正确,或选错了坐标系。
轻则报废零件,重则出安全事故。
脾气暴糙、做事无头绪,而且屡教不改者是不适应数控机床操作的。
我告诉大家一个事实:原来我们公司十多位用户调试切削工艺员,都是见多识广、经验老到之辈,可没有哪一个、哪一年不撞断过刀具的。
4、调试加工时出现问题,要冷静,千万不能慌张,再出现误操作。
心理素质要好。
5、零件调试多次不合格时,做分析要有条理,给出责任要有依据。
某些相关部门出于各种原因,会给出各种解释,这时你要有主见,记住:做错一件事不要紧,却不能选错做事的方法。
以上是我心目中理想的数控编程高手,其实说到底,应该有高级工艺师、高级技师水平的编程员。
数控车床精确对刀方法本文就是一篇非常实用的文章,文中首先介绍了数控车床常用的“试切对刀法”的原理及对刀思路;接着,介绍了华中世纪星车削数控系统的四种手动试切对刀方法;为改进其对刀精度,根据“自动试切→测量→误差补偿”的思路,设计出了用程序控制的自动试切法,并总结介绍了四种精确对刀方法。
文后还给出了几种对刀的示例程序,可能会对大家有所帮助。
对刀是数控加工中的主要操作和重要技能。
对刀的准确性决定了零件的加工精度,同时,对刀效率还直接影响数控加工效率。
华中世纪星车削系统是武汉华中数控股份公司近年推出的优秀国产数控车削系统,是2004年首届全国数控技能大赛的指定数控车削系统之一。
但遗憾的是,华中公司以往多通过其技术人员口头向用户说明对刀操作,在他们编写的《操作说明书》中却没有提到对刀操作,给用户学习、使用带来不便。
笔者通过实践探索,结合教学、技能考证培训与加工实践的经验,将该系统的几种快速准确的试切对刀方法予以小结,供大家参考,希望借此对国产数控系统的推广,推动我国数控技能人才的培训尽一点微薄之力。
一、数控车试切对刀法的原理及对刀思路深入理解数控车床的对刀原理对于操作者保持清晰的对刀思路、熟练掌握对刀操作以及提出新的对刀方法都具有指导意义。
对刀的实质是确定随编程而变化的工件坐标系的程序原点在唯一的机床坐标系中的位置。
对刀的主要工作是获得基准刀程序起点的机床坐标和确定非基准刀相对于基准刀的刀偏置。
本文作以下约定来说明试切法对刀的原理与思路:使用华中世纪星教学型车削系统HNC-21T(应用软件版本号为 5.30);以工件右端面中心为程序原点,用G92指令设定工件坐标系;直径编程,程序起点H的工件坐标为(100,50);刀架上装四把刀:1号刀为90°外圆粗车刀、2号基准刀为90°外圆精车刀、3号刀为切断刀、 4号刀为60°三角螺纹刀(全文所举实例均与此相同)。
基准刀按照“手动试切工件的外圆与端面,分别记录显示器(CRT)显示试切点A 的X、Z机床坐标→推出程序原点O的机床坐标→推出程序起点H 的机床坐标”的思路对刀。
根据A点与O点的机床坐标的关系:XO= XA-Φd,ZO =ZA,可以推出程序原点O的机床坐标。
再根据H相对于O点的工件坐标为(100,50),最后推出H点的机床坐标:XH=100-Φd,ZH= ZA+50。
这样建立的工件坐标系是以基准刀的刀尖位置建立的工件坐标系。
由于各刀装夹在刀架的X、Z方向的伸长和位置不同,当非基准刀转位到加工位置时,刀尖位置B 相对于A点就有偏置,原来建立的工件坐标系就不再适用了。
此外,每把刀具在使用过程中还会出现不同程度的磨损,因此各刀的刀偏置和磨损值需要进行补偿。
获得各刀刀偏置的基本原理是:各刀均对准工件上某一基准点(如图1的A点或O 点),由于CRT显示的机床坐标不同,因此将非基准刀在该点处的机床坐标通过人工计算或系统软件计算减去基准刀在同样点的机床坐标,就得到了各非基准刀的刀偏置。
受多种因素的影响,手动试切对刀法的对刀精度十分有限,将这一阶段的对刀称为粗略对刀。
为得到更加准确的结果,加工前在零件加工余量范围内设计简单的自动试切程序,通过“自动试切→测量→误差补偿”的思路,反复修调基准刀的程序起点位置和非基准刀的刀偏置,使程序加工指令值与实际测量值的误差达到精度要求,将这一阶段的对刀称为精确对刀。
由于保证基准刀程序起点处于精确位置是得到准确的非基准刀刀偏置的前提,因此一般修正了前者后再修正后者。
综合这两个阶段的对刀,试切法对刀的基本操作流程如下:用基准刀手动试切得到对刀基准点的机床坐标→人工计算或自动获得各非基准刀的刀偏置→基准刀处于大概的程序起点位置→基准刀反复调用试切程序,测量尺寸后,以步进或MDI方式移动刀架进行误差补偿,修正其程序起点的位置→非基准刀反复调用试切程序,在原刀偏置的基础上修正刀偏置→基准刀处于准确的程序起点不动。