水性(2K)丙烯酸聚氨酯:汽车漆系列产品及施工方法-北京钰林化工有限公司
开启汽车涂料水性化时代
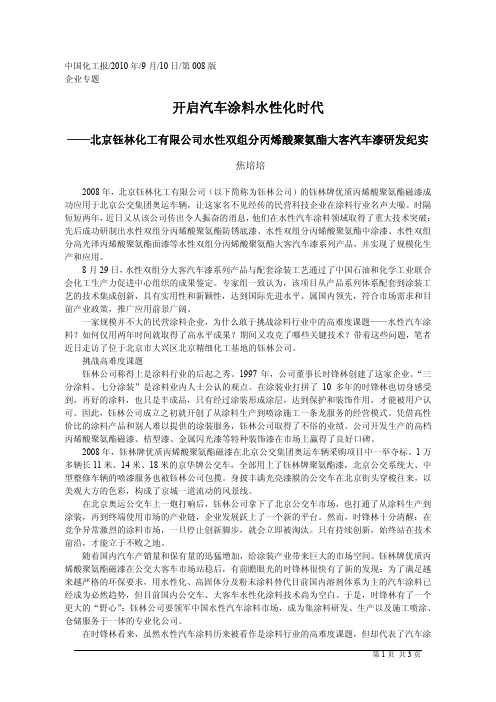
中国化工报/2010年/9月/10日/第008版企业专题开启汽车涂料水性化时代——北京钰林化工有限公司水性双组分丙烯酸聚氨酯大客汽车漆研发纪实焦培培2008年,北京钰林化工有限公司(以下简称为钰林公司)的钰林牌优质丙烯酸聚氨酯磁漆成功应用于北京公交集团奥运车辆,让这家名不见经传的民营科技企业在涂料行业名声大噪。
时隔短短两年,近日又从该公司传出令人振奋的消息,他们在水性汽车涂料领域取得了重大技术突破:先后成功研制出水性双组分丙烯酸聚氨酯防锈底漆、水性双组分丙烯酸聚氨酯中涂漆、水性双组分高光泽丙烯酸聚氨酯面漆等水性双组分丙烯酸聚氨酯大客汽车漆系列产品,并实现了规模化生产和应用。
8月29日,水性双组分大客汽车漆系列产品与配套涂装工艺通过了中国石油和化学工业联合会化工生产力促进中心组织的成果鉴定。
专家组一致认为,该项目从产品系列体系配套到涂装工艺的技术集成创新,具有实用性和新颖性,达到国际先进水平,属国内领先,符合市场需求和目前产业政策,推广应用前景广阔。
一家规模并不大的民营涂料企业,为什么敢于挑战涂料行业中的高难度课题——水性汽车涂料?如何仅用两年时间就取得了高水平成果?期间又攻克了哪些关键技术?带着这些问题,笔者近日走访了位于北京市大兴区北京精细化工基地的钰林公司。
挑战高难度课题钰林公司称得上是涂料行业的后起之秀。
1997年,公司董事长时锋林创建了这家企业。
“三分涂料、七分涂装”是涂料业内人士公认的观点。
在涂装业打拼了10多年的时锋林也切身感受到,再好的涂料,也只是半成品,只有经过涂装形成涂层,达到保护和装饰作用,才能被用户认可。
因此,钰林公司成立之初就开创了从涂料生产到喷涂施工一条龙服务的经营模式。
凭借高性价比的涂料产品和别人难以提供的涂装服务,钰林公司取得了不俗的业绩。
公司开发生产的高档丙烯酸聚氨酯磁漆、桔型漆、金属闪光漆等特种装饰漆在市场上赢得了良好口碑。
2008年,钰林牌优质丙烯酸聚氨酯磁漆在北京公交集团奥运车辆采购项目中一举夺标。
丙烯酸聚氨酯面漆施工方案

丙烯酸聚氨酯面漆施工方案1. 引言丙烯酸聚氨酯面漆是一种优质的涂料,在建筑和工业领域中广泛应用。
它具有耐候性、耐磨性和化学抗性等优点,常用于室内外墙面和地面的保护和装饰。
本文将介绍丙烯酸聚氨酯面漆的施工方案,包括准备工作、施工步骤和质量控制等内容。
2. 准备工作在进行丙烯酸聚氨酯面漆的施工前,需要进行一系列的准备工作,确保施工顺利进行和最终效果的质量。
•清洁表面:要确保涂料施工表面的清洁,去除油脂、灰尘和其他污染物。
•补修和磨光:对有裂缝和凹陷的表面进行修补和磨光处理,以保证漆膜的平整度。
•防护措施:如有需要,需要对建筑物周围的设备和其他表面进行防护,以免受到施工过程中的损坏。
•温度和湿度控制:根据丙烯酸聚氨酯面漆的要求,控制施工环境的温度和湿度,以确保涂料施工效果和干燥时间。
3. 施工步骤以下是丙烯酸聚氨酯面漆的施工步骤,可根据具体情况进行调整和优化。
3.1 涂料调配根据丙烯酸聚氨酯面漆的配方和要求,将漆料和稀释剂按照一定比例进行混合调配。
确保搅拌均匀,并严格控制好稀释剂的使用量。
3.2 涂料施工涂料施工是丙烯酸聚氨酯面漆施工的核心步骤,需要注意以下几点:•施工工具:根据具体要求,选择合适的刷子、滚筒或喷枪等施工工具。
确保工具清洁、无毛刺等瑕疵。
•运动方向:根据施工面的形状和大小,采用合适的运动方向进行涂刷,以避免出现重叠和涂层不均匀等问题。
•施工厚度:根据涂料的要求,控制好施工厚度,避免过度或不足。
•涂刷次数:根据需要,涂刷多层涂料,确保涂膜的质量和效果。
3.3 干燥和固化涂料施工完成后,需要进行干燥和固化,以确保涂膜的性能和耐久性。
•温度控制:根据丙烯酸聚氨酯面漆的要求,控制施工环境的温度,加快涂膜的干燥速度。
•通风保护:为了确保涂膜的质量,要保证空气流通和排气,避免施工环境中有害气体的滞留。
•固化时间:根据涂料的要求,在涂刷完成后,保持施工环境的稳定,等待涂膜的固化和硬化。
4. 质量控制丙烯酸聚氨酯面漆施工过程中的质量控制对于最终效果的质量至关重要。
丙烯酸防水涂料施工方案

一、工艺流程清理基层→涂刷基层处理剂→细部附加层施工→涂刷第一遍涂→涂刷第二遍涂膜→涂刷第三遍涂膜→涂刷第四遍涂料→涂刷第五遍涂料直至达到2.0mm厚为止→防水层蓄水试验→质量验收。
二、操作要点清理基层:将基层清扫干净;基层应做到找坡正确,排水顺畅,表面平整、坚实,无起灰、起砂、起壳及开裂现象。
涂刷基层处理剂前,基层表面应达到干燥状态。
涂刷基层处理剂:基层处理剂为低粘度丙稀酸,可以起到隔离基层潮汽处理灰尘,提高涂料与基层粘接强度的作用。
涂刷时,将丙稀酸涂料对于适量的水(配合比涂料:水=4:1),用搅拌器搅拌均匀,即可涂刷于基层上。
先在阴阳角、管道根部均匀涂刷一遍,然后进行大面积涂刷。
材料用量为0.20~0.25kg/m2涂刷后应干燥4h以上,才能进行下道工序的施工。
附加层施工:在管道、地漏、阴阳角和出入口等易发生的薄弱部位,应先用丙稀酸防水涂料均匀涂刮一次,起厚度0.5mm,做附加层处理。
按设计要求,细部构造也可做带胎体增强材料的附加层处理。
第一遍涂膜施工:将丙稀酸防水涂料用胶皮刮板涂刮在基层表面,涂刷厚度要均匀一致,用量为0.8~1.0kg/m2。
立面涂刷高度根据设计要求1800mm。
第二遍涂膜施工:在第一遍涂膜固化干燥后,再按上述方法涂刮第二涂料,对平面的涂刮方向应与第一遍涂刷方向相垂直每涂刮量仍与第一遍相同。
第三遍涂膜施工:在第二遍涂膜施工固化(即实干,用手触摸不粘手)干燥后,再按上述方法涂刮第三遍涂料。
对平面的涂刮方向应与第二遍涂刷方向相垂直每涂刮量仍与第二遍相同。
第四遍涂膜施工:在第三遍涂膜施工固化干燥后,再按上述方法涂刮第四遍涂料。
对平面的涂刮方向应与第三遍涂刷方向相垂直每涂刮量仍与第三遍相同。
第五遍涂膜施工:在第四遍涂膜固化后,再按上述方法涂刮第五遍涂料,用量0.4~0.5kg/m2。
五遍丙稀酸涂料涂刷后,用料量总计4.3kg/m2,用工量平均为0.15工日/m2,防水厚度不小于2.0mm。
水性丙烯酸地坪漆施工方案
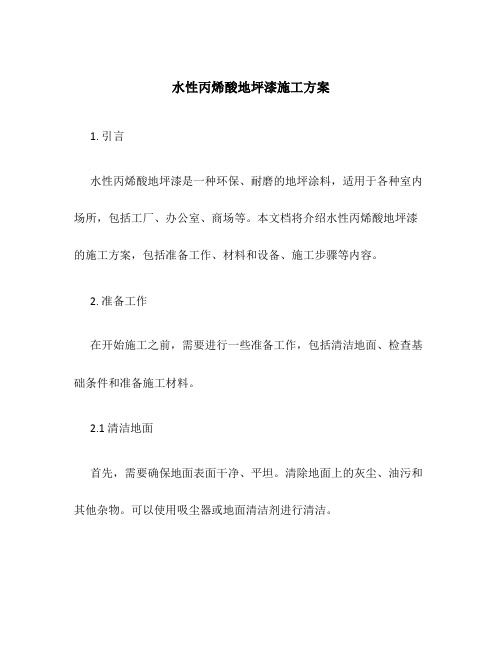
水性丙烯酸地坪漆施工方案1. 引言水性丙烯酸地坪漆是一种环保、耐磨的地坪涂料,适用于各种室内场所,包括工厂、办公室、商场等。
本文档将介绍水性丙烯酸地坪漆的施工方案,包括准备工作、材料和设备、施工步骤等内容。
2. 准备工作在开始施工之前,需要进行一些准备工作,包括清洁地面、检查基础条件和准备施工材料。
2.1 清洁地面首先,需要确保地面表面干净、平坦。
清除地面上的灰尘、油污和其他杂物。
可以使用吸尘器或地面清洁剂进行清洁。
2.2 检查基础条件检查地面的基础条件,确保没有明显的裂缝或起伏。
如果存在问题,需要提前修复。
可以使用修补剂填平裂缝,或使用砂浆修复不平的地面。
2.3 准备施工材料准备水性丙烯酸地坪漆、底漆和涂刷工具。
确保材料的质量良好,避免施工过程中出现质量问题。
3. 材料和设备3.1 材料•水性丙烯酸地坪漆:根据需求选择合适的产品,确保其环保、耐磨性能良好。
•底漆:使用合适的底漆可以提高地坪漆的附着力和耐久性。
•涂刷工具:根据施工面积选择合适的涂刷工具,如滚筒刷、刷子等。
3.2 设备•搅拌器:用于搅拌地坪漆,使其达到均匀的状态。
•平衡仪:用于确保施工面积的平整和水平度。
•电动扫把:用于清理地面上的灰尘和杂物。
4. 施工步骤4.1 施工准备首先,将水性丙烯酸地坪漆放在搅拌器中进行搅拌,直至达到均匀的状态。
确保地面干燥和清洁,没有明显的污垢。
4.2 涂刷底漆在开始涂刷地坪漆之前,先涂刷一层底漆。
底漆可以提高地坪漆的附着力和耐久性。
使用刷子或滚筒刷将底漆均匀地涂刷在地面上,确保底漆均匀分布。
4.3 涂刷地坪漆等待底漆干燥后,开始涂刷水性丙烯酸地坪漆。
使用刷子或滚筒刷将地坪漆均匀地涂刷在地面上,确保涂层平整、厚度均匀。
根据需要涂刷多层地坪漆,每层之间需要等待上一层完全干燥后再进行下一层的涂刷。
4.4 平整地面在涂刷地坪漆后,使用平衡仪检查施工面积的平整度和水平度。
如果有不平整的地方,可以使用砂纸打磨平整。
聚氨酯水性漆施工方案

聚氨酯水性漆施工方案聚氨酯水性漆是一种环保型涂料,具有较好的耐磨、耐污、耐候性,同时还具有较好的附着力和良好的装饰效果。
下面是一份聚氨酯水性漆施工方案,共计700字左右。
一、前期准备工作1. 准备好所需的聚氨酯水性漆及相关涂装工具,确保质量可靠。
2. 对待涂装表面进行清洗,除掉油污、尘土等杂物,确保涂装表面光洁。
3. 处理涂装表面的毛刺、粗糙面,确保涂装效果均匀。
二、涂装过程1. 进行底漆施工:使用底漆对涂装表面进行打底处理,提高漆膜附着力。
2. 细部修补:根据涂装表面的具体情况,对局部细节进行修补,确保涂装表面的光滑度。
3. 进行薄涂施工:先对涂装表面进行一次薄涂,涂装时应注意均匀刷涂,确保涂装表面无气泡、不起皮。
4. 进行中涂施工:对第一次薄涂的涂装表面进行第二次涂装,增加涂膜厚度,提高涂层的耐磨性和耐候性。
5. 进行面漆施工:对中涂的涂装表面进行第三次涂装,增加涂层的光泽度和装饰效果。
6. 进行涂装面的养护:待面漆涂装完成后,对涂装表面进行充分的干燥和硬化,避免在硬化过程中受到外界的损伤。
三、安全措施1. 严格按照涂料包装上的说明进行操作,避免误食、误吸入,确保人身安全。
2. 在施工现场设置必要的警示标志,提醒他人注意施工区域,避免发生意外事故。
3. 使用好质量可靠的个人防护用具,包括手套、口罩、安全镜等,保护自身安全。
4. 做好环保措施,避免涂料渗漏到周围环境中,造成二次污染。
四、施工质量检验及验收标准1. 涂装表面应平整、光滑、无刷痕、灰尘等杂质,视觉效果好。
2. 涂层应平整、饱满,无起皮、脱落等现象。
3. 涂层附着力好,无剥离现象。
4. 涂层的颜色和光泽度符合要求。
以上就是聚氨酯水性漆的施工方案,希望对您有所帮助!在涂装过程中,一定要严格按照规范要求执行,做好安全措施,确保施工质量和人身安全。
丙烯酸聚氨酯中涂漆标准

丙烯酸聚氨酯中涂漆标准丙烯酸聚氨酯是一种常用于涂料领域的聚合物,具有良好的附着力、耐候性和耐化学性能。
涂漆是将丙烯酸聚氨酯涂覆在物体表面的过程,以提供保护、美化或功能改善的效果。
在进行丙烯酸聚氨酯涂漆时,需要遵循一定的标准和要求,以确保涂层质量和性能的稳定性。
下面我们将详细介绍丙烯酸聚氨酯涂漆的标准。
1.基材要求:丙烯酸聚氨酯涂漆适用于多种基材,如金属、塑料、木材等。
在进行涂漆之前,需要对基材进行处理,确保其表面干净、无油脂、无灰尘、无锈蚀等杂质。
2.涂料选择:丙烯酸聚氨酯涂料应选择符合国家标准的产品,具有良好的附着力、耐候性和耐化学性能。
涂料应具有较低的挥发性有机化合物(VOC)含量,以减少对环境的污染。
3.涂层厚度:丙烯酸聚氨酯涂漆的涂层厚度应根据具体应用要求来确定,一般情况下,涂层厚度应符合国家标准的规定。
4.涂装方法:丙烯酸聚氨酯涂漆可采用喷涂、滚涂或刷涂等方法进行涂装。
涂装过程中应确保均匀涂布,避免出现漏涂、浪涂、鳞片等缺陷。
5.干燥时间:丙烯酸聚氨酯涂漆在涂装后需要经过一定的干燥时间才能达到最佳性能。
干燥时间应根据涂料的配方、环境湿度和温度等要素来确定。
在干燥过程中,应避免暴露在高温、高湿度环境下,以免影响涂层的质量。
6.涂漆环境要求:丙烯酸聚氨酯涂漆应在相对湿度低于80%、温度适宜的环境中进行。
在涂装过程中,应确保环境无风尘和其他杂质的干扰,以保证涂层的质量。
7.涂漆工艺记录:在进行丙烯酸聚氨酯涂漆过程中,应建立涂漆工艺记录,记录涂料配方、涂装方法、干燥时间等重要参数,以便进行后续的质量控制和追溯。
8.涂漆质量检测:涂漆质量检测是保证丙烯酸聚氨酯涂漆质量的重要环节。
常见的涂漆质量检测方法包括涂层附着力测试、耐候性测试、耐化学性能测试等。
这些测试可以通过实验室设备和标准测试方法进行。
通过以上几个方面的标准和要求,可以确保丙烯酸聚氨酯涂漆的质量和性能达到预期目标。
在具体的涂漆过程中,还需要根据实际情况进行调整和优化,以满足不同应用领域的需求。
水性(2K)丙烯酸聚氨酯:汽车漆系列产品及施工方法-北京钰林化工有限公司
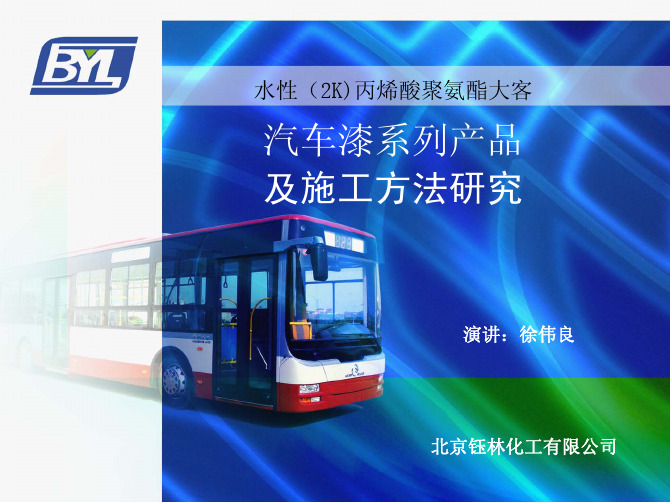
70℃烘干2h
轻微起皱
2
起泡
底漆脱落
70℃烘干1h
平整
0
平整
附着力优良
结论:
1、水性丙烯酸改性醇酸底漆, 水性环氧底漆固化速度太慢。 ● 2、水性丙烯酸聚氨酯底漆满足 客车涂装工艺要求
●
2.2 防锈颜料的选择
• ● 尽量采用惰性颜料 • ● 少用重金属化合K)丙烯酸聚氨酯防锈漆性能检测结果
检验项目
溶剂型汽车底漆 国家标准
168h通过一级 一级 不咬起、不渗红
水性丙烯酸 聚氨酯防锈漆 企业标准
380h通过一级 一级 不咬起、不渗红
国家涂料质量 监督检测中心 检验结果
432h通过一级 一级 不咬起、不渗红 76 未检出 14
耐盐雾性切割 线一侧2mm外 耐湿热性 96h 耐硝基性 VOC含量 g/L 苯、甲苯、二甲苯、乙苯 含量mg/kg 游离甲醛含量mg/kg
国家涂料质量 监督检测中心 检验结果
13 无变化
杯突实验 mm 杯突实验 mm
耐温变性
级
1 0.8 1500h 变色贰级, 失光率贰级。 135 未检出 10 1 未检出 未检出 未检出
鲜映性 Gd值
人工加速老化,无明显龟裂,可 轻微变色,失光率≤30%
VOC含量 g/L 苯、甲苯、二甲苯、乙苯 含量mg/kg 游离甲醛含量mg/kg 可溶性铅 mg/kg 可溶性镉 mg/kg 可溶性铬 mg/kg 可溶性汞 mg/kg 游离异氰酸酯含量% 0.7
2.1 树脂体系的选择 国内外钢结构防腐涂料,通常采用水性丙烯酸改性醇酸、水性环 氧底漆二大系列,针对国内客车涂装工艺要求,将可供选择的树 脂体系平行对比,试验结果如表一所示: 表一
丙烯酸聚氨酯漆施工工艺及涂装技巧
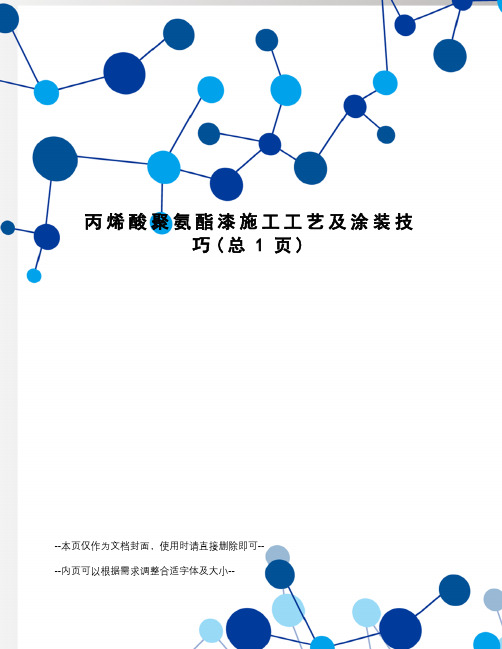
丙烯酸聚氨酯漆施工工艺及涂装技巧(总1页)--本页仅作为文档封面,使用时请直接删除即可----内页可以根据需求调整合适字体及大小--丙烯酸聚氨酯施工工艺及涂装技巧【丙烯酸聚氨酯漆主要组成】丙烯酸聚氨酯漆不仅有一定的保护作用,也有一定的装饰作用。
丙烯酸聚氨酯漆要耐久、耐晒、保色、保光泽。
面漆与腐蚀介质(空气、水分、紫外线、化学药品等)接触,所以对它的防护性能要求较高。
漆膜要有一定的机械强度,有一定的硬度,可以抛光、打磨、上蜡以获得高装饰性的漆膜。
漆膜的色彩应鲜艳丰满。
应用领域包括码头、港口、采油平台、矿井下的金属构筑物、油轮的油水舱、埋地管道等。
【丙烯酸聚氨酯漆主要特性】1、低污染性:先进的涂料复合技术,涂膜难以污染2、高耐候性:大大提高了耐候性、抗水性,使用寿命达10年以上3、优异的附着力:独特分子结构,附着力优异,适用于多种基面4、优良的作业性:与普通型油性漆相比,异味少,可以改善作业环境,并可用多种涂装工具施工5、干燥时间短,低温施工性好,有效缩短工期【丙烯酸聚氨酯漆施工工艺】1.开桶搅拌:打开桶后,将涂料搅拌至桶底无沉积物,并按涂料:固化剂=4:1(重量比)的比例混合搅匀,经15~20分钟熟化后即可施工,若涂料确实太稠,可适当添加XHDAC503型聚氨酯专用稀释剂,其用量为5~15%,严禁用水、醇、香蕉水和汽油等稀释,且在涂料使用后立即盖严密封,以防受潮变质。
2.表面处理要求:钢铁结构,基材处理要求达到国家标准级以上,或采用手工除锈达到St3级以上;也可采用化学除锈,要求达到无油、无锈、无杂物、干燥清洁。
3.理论消耗量:如果不考虑实际施工时的涂装环境、涂装方法、涂装技术、表面状况及结构、形状、表面积大小等的影响,一般消耗量为㎡。
4.最佳施工温度为0~35℃,相对湿度为≤85℃,在有雨、雾、雪和较严重灰尘条件下,不得施工。
5.第一道涂装后,最好待24小时以上再涂装第二道,常温条件施工须固化七天以后施工场地才能投入使用。
2K 水性丙烯酸聚氨酯涂料的成膜物质体系
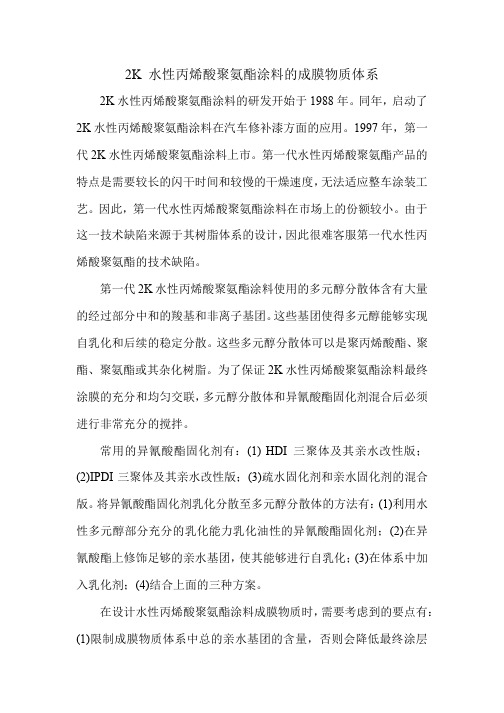
2K 水性丙烯酸聚氨酯涂料的成膜物质体系2K水性丙烯酸聚氨酯涂料的研发开始于1988年。
同年,启动了2K水性丙烯酸聚氨酯涂料在汽车修补漆方面的应用。
1997年,第一代2K水性丙烯酸聚氨酯涂料上市。
第一代水性丙烯酸聚氨酯产品的特点是需要较长的闪干时间和较慢的干燥速度,无法适应整车涂装工艺。
因此,第一代水性丙烯酸聚氨酯涂料在市场上的份额较小。
由于这一技术缺陷来源于其树脂体系的设计,因此很难客服第一代水性丙烯酸聚氨酯的技术缺陷。
第一代2K水性丙烯酸聚氨酯涂料使用的多元醇分散体含有大量的经过部分中和的羧基和非离子基团。
这些基团使得多元醇能够实现自乳化和后续的稳定分散。
这些多元醇分散体可以是聚丙烯酸酯、聚酯、聚氨酯或其杂化树脂。
为了保证2K水性丙烯酸聚氨酯涂料最终涂膜的充分和均匀交联,多元醇分散体和异氰酸酯固化剂混合后必须进行非常充分的搅拌。
常用的异氰酸酯固化剂有:(1) HDI三聚体及其亲水改性版;(2)IPDI三聚体及其亲水改性版;(3)疏水固化剂和亲水固化剂的混合版。
将异氰酸酯固化剂乳化分散至多元醇分散体的方法有:(1)利用水性多元醇部分充分的乳化能力乳化油性的异氰酸酯固化剂;(2)在异氰酸酯上修饰足够的亲水基团,使其能够进行自乳化;(3)在体系中加入乳化剂;(4)结合上面的三种方案。
在设计水性丙烯酸聚氨酯涂料成膜物质时,需要考虑到的要点有:(1)限制成膜物质体系中总的亲水基团的含量,否则会降低最终涂层的耐水性;(2) 成膜物质体系中的多元醇和固化剂必须能够被比较容易的混合均匀,市场比较青睐能够只通手动搅拌就能混合均与的成膜物质体系。
水性丙烯酸聚氨酯涂料的混合受到包含水性多元醇分散体的主漆粘度和固化剂粘度之间差异的影响。
水性丙烯酸聚氨酯涂料经常遇到的问题是涂膜的起泡。
起泡的机制有:(1) 在空气喷涂的过程中,大量的气泡被限制在涂膜内,而水性涂料中的乳化剂成分会起到稳泡的作用,进而阻碍的涂膜中气泡的释放;(2) 在水性丙烯酸聚氨酯涂料中,固化剂中的异氰酸酯基能够与水反应生产二氧化碳,进一步加剧了涂膜中气泡的产生,多元醇分散体中的胺中和剂能够催化异氰酸酯与水的反应,进一步加剧了这一过程;(3) 在水性丙烯酸聚氨酯涂料中,多元醇分散体上含有大量的羧基,在干燥的过程中,羧基与固化剂上的异氰酸酯基团反应生成二氧化碳,进而产生气泡。
丙烯酸聚氨酯漆施工方案及流程
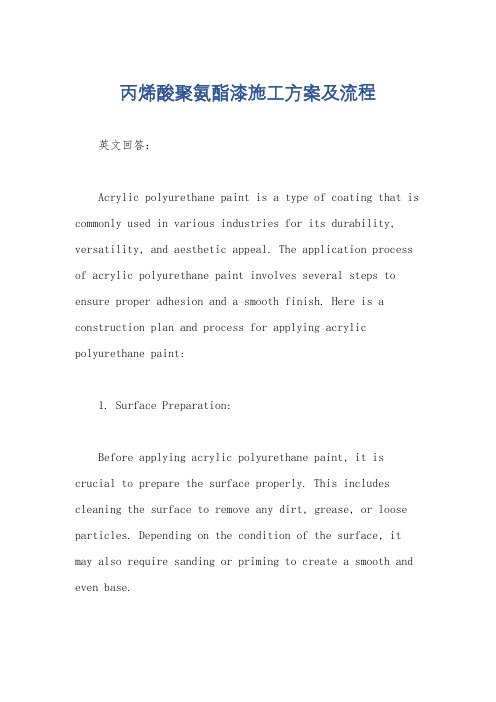
丙烯酸聚氨酯漆施工方案及流程英文回答:Acrylic polyurethane paint is a type of coating that is commonly used in various industries for its durability, versatility, and aesthetic appeal. The application process of acrylic polyurethane paint involves several steps to ensure proper adhesion and a smooth finish. Here is a construction plan and process for applying acrylic polyurethane paint:1. Surface Preparation:Before applying acrylic polyurethane paint, it is crucial to prepare the surface properly. This includes cleaning the surface to remove any dirt, grease, or loose particles. Depending on the condition of the surface, it may also require sanding or priming to create a smooth and even base.2. Mixing the Paint:Acrylic polyurethane paint usually comes in two partsthe base and the activator. These two components need to be mixed in the correct ratio as instructed by the manufacturer. It is essential to follow the instructions carefully to ensure the paint's effectiveness and longevity.3. Application:Once the paint is mixed, it is ready for application. There are several methods to apply acrylic polyurethane paint, including brushing, rolling, or spraying. The choice of application method depends on the size and nature of the surface. For larger areas, spraying may be more efficient, while smaller areas can be brushed or rolled.4. Multiple Coats:To achieve a durable and long-lasting finish, multiple coats of acrylic polyurethane paint are usually required. Each coat should be applied after the previous one hasdried completely. It is essential to follow the manufacturer's instructions regarding drying time between coats.5. Curing and Drying:After the final coat is applied, the paint needs to cure and dry properly. This process typically takes several days, depending on the environmental conditions and the type of acrylic polyurethane paint used. It is crucial to avoid any contact or damage to the painted surface during this curing period.6. Finishing Touches:Once the paint has cured and dried, any necessarytouch-ups or finishing touches can be done. This may include sanding any imperfections, applying a clear coatfor added protection, or adding decorative elements if desired.中文回答:丙烯酸聚氨酯漆是一种常用于各个行业的涂料,因其耐用性、多功能性和美观性而受到青睐。
北京聚氨酯防水涂料使用方法

北京聚氨酯防水涂料使用方法嘿!说起北京聚氨酯防水涂料,这可是在建筑防水领域中相当重要的材料呢!那咱们就来好好聊聊它的使用方法。
首先呀,在使用北京聚氨酯防水涂料之前,准备工作那是必不可少的!要把施工的表面清理干净,哎呀呀,不能有灰尘、油污、杂物等等,不然会影响涂料的附着力和防水效果哟!还得检查基层是否平整,如果有裂缝、坑洼的地方,得先进行修补处理。
接下来,就是涂料的调配啦!按照产品说明书上的比例,将主剂和固化剂混合均匀。
这一步可不能马虎,要是比例不对,涂料的性能可就大打折扣了呢!在调配的过程中,要充分搅拌,确保没有沉淀和结块。
然后呢,就可以开始涂刷啦!用刷子或者滚筒,从一个方向均匀地涂刷。
第一遍要薄涂,不要涂得太厚,不然容易出现开裂。
等第一遍干了之后,再进行第二遍涂刷,方向要与第一遍垂直,这样可以增加涂层的密实度和防水效果。
在涂刷的时候,要注意一些细节。
比如墙角、阴阳角、管根等部位,要多刷几遍,加强防水处理。
还有呀,涂刷的厚度要达到设计要求,一般来说,不少于1.5 毫米。
哇!施工环境也很重要哦!施工温度最好在5℃到35℃之间,湿度不能太大,不然涂料干得慢,影响施工进度和质量。
还有还有,在涂刷过程中,如果发现气泡或者有漏涂的地方,要及时处理。
等涂料完全干燥后,要进行闭水试验,看看防水效果到底怎么样。
哎呀呀,使用北京聚氨酯防水涂料可真是个细致活儿,每一个步骤都不能马虎。
只有严格按照正确的使用方法来操作,才能确保防水工程的质量,让我们的建筑远离渗漏的烦恼呢!另外呀,在施工过程中,一定要做好个人防护,戴上手套、口罩等,避免涂料接触到皮肤和呼吸道。
总之呢,掌握好北京聚氨酯防水涂料的使用方法,就能为我们的建筑穿上一层坚固的“防水铠甲”,让我们的生活更加舒适和安心!怎么样,是不是对这种涂料的使用方法有了更清晰的了解啦?。
DSM与北京钰林化工共同研发水性大巴漆
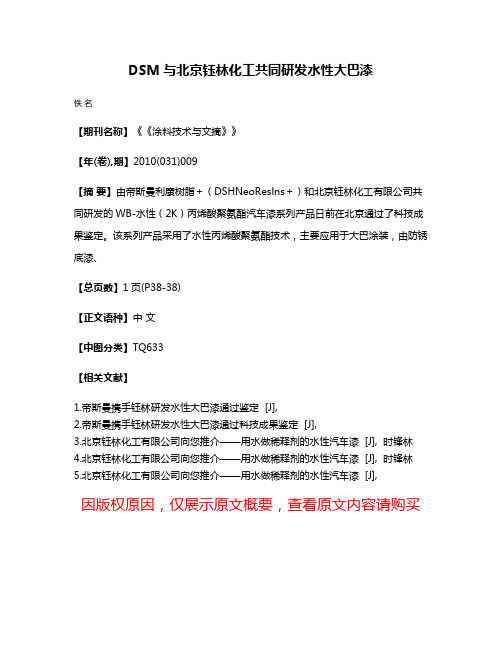
DSM与北京钰林化工共同研发水性大巴漆
佚名
【期刊名称】《《涂料技术与文摘》》
【年(卷),期】2010(031)009
【摘要】由帝斯曼利康树脂+(DSHNeoReslns+)和北京钰林化工有限公司共同研发的WB-水性(2K)丙烯酸聚氨酯汽车漆系列产品日前在北京通过了科技成果鉴定。
该系列产品采用了水性丙烯酸聚氨酯技术,主要应用于大巴涂装,由防锈底漆、
【总页数】1页(P38-38)
【正文语种】中文
【中图分类】TQ633
【相关文献】
1.帝斯曼携手钰林研发水性大巴漆通过鉴定 [J],
2.帝斯曼携手钰林研发水性大巴漆通过科技成果鉴定 [J],
3.北京钰林化工有限公司向您推介——用水做稀释剂的水性汽车漆 [J], 时锋林
4.北京钰林化工有限公司向您推介——用水做稀释剂的水性汽车漆 [J], 时锋林
5.北京钰林化工有限公司向您推介——用水做稀释剂的水性汽车漆 [J],
因版权原因,仅展示原文概要,查看原文内容请购买。
- 1、下载文档前请自行甄别文档内容的完整性,平台不提供额外的编辑、内容补充、找答案等附加服务。
- 2、"仅部分预览"的文档,不可在线预览部分如存在完整性等问题,可反馈申请退款(可完整预览的文档不适用该条件!)。
- 3、如文档侵犯您的权益,请联系客服反馈,我们会尽快为您处理(人工客服工作时间:9:00-18:30)。
国家涂料质量 监督检测中心 检验结果
无杂质,易搅起的均匀 液体 60 5 0 3H 易打磨、不粘砂纸 无变化 无变化 很轻微变色
原漆状态 细度 um 杯突试验 mm 附着力1mm格 级 铅笔硬度 打磨性 20次 耐油性 48h 耐汽油性 6h 耐酸性 7h 0.05mol/L H2SO4 耐碱性 7h 0.1mol/L NaOH
水性(2K)丙烯酸聚氨酯大客
汽车漆系列产品 及施工方法研究
演讲:Байду номын сангаас伟良
北京钰林化工有限公司
1、目的与意义
大型客车、汽车修补涂装、塑料件涂装因不能承受高温烘 烤,一般均采用低温烘干体系,即在60-80℃烘干或常温自干, 通常为丙烯酸聚氨酯双组份涂料。例如国内公交车、豪华大巴均 采用溶剂型环氧防锈漆 ,溶剂型丙烯酸聚氨酯或聚酯聚氨酯中涂 漆,溶剂型丙烯酸聚氨酯面漆配套涂装,水性化技术尚为空白。 国外虽有少量采用水性化技术涂装公交、大巴的实例,但是 因为很难达到高光泽、高鲜映性的涂装效果,目前一般采用水性 半光或哑光实色漆+溶剂型高固体份清漆罩光配套工艺,本质上 仍属于半水性水平。 本公司研制水性(2K)防锈底漆、水性(2K)中涂漆、水 性(2K)高光泽汽车面漆系列产品完全满足公交车、豪华大巴涂 装工艺要求,从底到面配套,毋需溶剂型清漆罩光,VOC含量大 幅度下降,可满足欧美最严格的环保法规要求,对节能减排、低 碳环保具有非常重要的现实意义。
5、施工技术
水性漆的施工方法与溶剂型漆差异很大。由于水的基本特性就是: 表面张力大、热容量大、蒸发热高、挥发率低,因此施工过程中容 易出现如下各种弊病: ①立面喷涂易流挂, ②对底材湿润性差,桔皮严重,流平性不佳, ③湿膜干燥过程中容易产生缩孔、针孔, ④喷涂施工时环境温度、湿度对涂装质量影响非常显著, ⑤不易渗入到被涂表面的小细缝中。当涂料配方确定以后,选择优 质喷枪及辅助施工设备,采用正确的施工方法是保障涂装质量的决 定性因素。
无变化
表二 水性(2K)丙烯酸聚氨酯防锈漆性能检测结果
检验项目
溶剂型汽车底漆 国家标准
168h通过一级 一级 不咬起、不渗红
水性丙烯酸 聚氨酯防锈漆 企业标准
380h通过一级 一级 不咬起、不渗红
国家涂料质量 监督检测中心 检验结果
432h通过一级 一级 不咬起、不渗红 76 未检出 14
耐盐雾性切割 线一侧2mm外 耐湿热性 96h 耐硝基性 VOC含量 g/L 苯、甲苯、二甲苯、乙苯 含量mg/kg 游离甲醛含量mg/kg
检验项目 溶剂型汽车底漆 国家标准
无杂质,易搅起的均匀 液体 ≤60 ≥5 0 ≥H 易打磨、不粘砂纸 外观无明显变化 不起泡、不起皱 允许轻微变色 不起泡、不起皱 允许轻微变色 不起泡、不起皱 允许轻微变色
水性丙烯酸 聚氨酯防锈漆 企业标准
无杂质,易搅起的均匀 液体 ≤60 ≥5 0 ≥2H 易打磨、不粘砂纸 外观无明显变化 不起泡、不起皱 允许轻微变色 不起泡、不起皱 允许轻微变色 不起泡、不起皱 允许轻微变色
5.5 创新点
5.5.1 从底到面配套,全部水性化。 达到国际先进、国内领先水平 5.5.2 施工工艺幅度宽广: 5—40℃,湿度:10—80%均可施工 5.5.3 制定出一套比较完整的施工工艺指南
6、水性汽车漆系列产品涂装工艺
水性汽车漆系列产品可于70-80℃低温烘干,也 可于常温自干,故可以用作OEM原厂漆,也可用于 旧车翻新及汽车修补。喷涂方法与溶剂型汽车漆有 很大差异,其施工流程如图一、图二所示
2.3助剂的选择
2.3.1 底材湿润剂的选择 ● 含氟表面活性剂 ● 聚醚改性有机硅 ● 烷氧基表面活性剂 2.3.2 防闪锈剂的选择 不含:VOC 重金属 亚硝酸盐
2.4水性2K丙烯酸聚氨酯防锈漆性能 水性2K丙烯酸聚氨酯防锈漆性能检测结果见表二所示: 表二 水性(2K)丙烯酸聚氨酯防锈漆性能检测结果
0.07
4.4 创新点
4.4.1 将水性羟基丙烯酸树脂与水性羟基聚氨酯树脂併合 使用,在保证流平性、鲜映性基础上,改善施工工艺幅度。 4.4.2 将HDI水性固化剂与IPDI水性固化剂併合使用,调节 表干速度,降低产生气泡、失光、针孔等漆病的可能性。 4.4.3 降低NCO/OH配比,尽量减少水与-NCO的副反应。 4.4.4 选择适当催化剂,引导交联反应向预期方向进行。
表四 水性(2K)高光泽丙烯酸聚氨酯面漆性能检测结果
检验项目 溶剂型汽车面 漆国家标准
≥3 不起泡、不起皱、 不脱落,允许轻微 变色 ≤2 0.6-0.8 800h
水性(2K) 高光泽丙烯酸 聚氨酯磁漆企业标准
≥5 不起泡、不起皱、不脱落, 允许轻微变色 ≤2 0.7-0.9 1000h无明显龟裂,允许轻微 变色,失光率≤30%
无杂质硬块,易搅起 的均匀液体
原漆状态
无杂质硬块,易 搅起的均匀液体
细度
um
≤10 8 10 ≤1 ≥0.4
<10 8 10 1 0.4 2 90
贮存稳定性(沉淀性) 级 贮存稳定性(结皮性) 级 划格试验(间距2mm)级 双摆硬度 弯曲试验 mm 光泽60°单位值
2 白色85,其它 色90
2 ≥90
外观 平整 划格附着力 2 刮原子灰 起泡 90°弯曲 底漆脱落
70℃烘干2h
轻微起皱
2
起泡
底漆脱落
70℃烘干1h
平整
0
平整
附着力优良
结论:
1、水性丙烯酸改性醇酸底漆, 水性环氧底漆固化速度太慢。 ● 2、水性丙烯酸聚氨酯底漆满足 客车涂装工艺要求
●
2.2 防锈颜料的选择
• ● 尽量采用惰性颜料 • ● 少用重金属化合物 • ● 防锈颜料用量不宜过高
4.2.1选择适当的树脂品种 可供使用的树脂品种: 聚丙烯酸酯、聚氨酯水分散体 聚酯、聚醚 4.2.2固化剂的选择 ● HDI亲水固化剂 ● IPDI亲水固化剂 4.2.3提高树脂与固化剂的相容性 若相容性好,二种树脂迅速混匀,-NCO与-OH反应程 度提高,易于获得均匀一致的涂膜。
4.2.4降低NCO/OH比例 应将NCO/OH控制于1.1—1.3:1 4.2.5选择适当催化剂 选用金属化合物作催化剂,促进NCO与OH反应 。 4.2.6提高雾化程度 添加可促进超细雾化的助剂
水性(2K)丙烯酸聚 氨酯中涂漆企业标准
无杂质,易搅起的均匀液体 ≤45 ≥5 ≤2 易打磨、不粘砂纸 外观无明显变化 不起泡、不起皱 允许轻微变化 不起泡、不起皱 允许轻微变化 不起泡、不起皱 允许轻微变化
国家涂料质量监督 检测中心检测结果
无杂质,易搅起的均匀液体 45 5 2 易打磨、不粘砂纸 无变化 无变化 无变化 无变化
3.3 水性(2K)丙烯酸聚氨酯中涂漆性能 由于溶剂型汽车中涂漆无国家标准和行业标准,故水性(2K)丙烯 酸聚氨酯中涂漆按溶剂型汽车底漆国家标准检测项目制订企业标准 ,实际检测结果如表三所示: 表三 水性(2K)丙烯酸聚氨酯中涂漆性能检测结果
检验项目
原漆状态 细度 um 杯突试验 mm 附着力 1mm格·级 打磨性 20次 耐油性 48h 耐汽油性 6h 耐酸性 耐碱性 7h 0.05mol/L H2SO4 7h 0.1mol/L NaOH
2、水性2K丙烯酸聚氨酯防锈底漆
大型客车由于车身体积大,模具化程度低,目前普遍采用如下涂装 工艺: 车身前处理→环氧底漆→70℃烘干→打磨→刮原子灰→70℃烘干 →打磨→中涂漆→70℃烘干→打磨→面漆→70℃烘干→分线 →70℃烘干→验收 无烘烤条件时,则在喷涂底漆后,自干放置过夜,再刮原子灰。此 外为了提高整车防锈性能,车身常采用镀锌板、合金板。因此研制 水性防锈底漆必须解决四个问题:①与镀锌板附着力优良。②刮涂 原子灰不起泡。③耐盐雾性优良。④抗闪锈能力强。
国家涂料质量 监督检测中心 检验结果
13 无变化
杯突实验 mm 杯突实验 mm
耐温变性
级
1 0.8 1500h 变色贰级, 失光率贰级。 135 未检出 10 1 未检出 未检出 未检出
鲜映性 Gd值
人工加速老化,无明显龟裂,可 轻微变色,失光率≤30%
VOC含量 g/L 苯、甲苯、二甲苯、乙苯 含量mg/kg 游离甲醛含量mg/kg 可溶性铅 mg/kg 可溶性镉 mg/kg 可溶性铬 mg/kg 可溶性汞 mg/kg 游离异氰酸酯含量% 0.7
4、水性2K高光泽丙烯酸聚氨酯面漆
4.1颜料的分散与稳定 选用高分子量、解絮凝湿润分散剂、降低体系 粘度、改进流平性、提高光泽、减小雾影。
4.2 提高成膜质量的稳定性。 在水性丙烯酸聚氨酯涂料系统中,固化剂 与水的副反应是不可避免的,在最终形成 的涂层结构中聚氨酯和聚脲结构共存,二 者比例的大小将直接影响干膜性能,因此 只有综合使用各种方法尽量控制固化剂与 水的副反应,才能保障成膜质量稳定。
2.1 树脂体系的选择 国内外钢结构防腐涂料,通常采用水性丙烯酸改性醇酸、水性环 氧底漆二大系列,针对国内客车涂装工艺要求,将可供选择的树 脂体系平行对比,试验结果如表一所示: 表一
类别 水性丙烯酸 改性醇酸底漆 水性(2K) 环氧底漆 水性(2K) 丙烯酸聚氨酯 底漆 干燥条件 70℃烘干2h
三种树脂体系工艺性能对比
整车精修、交验 合格后转交装配 车间
分色500目砂纸精磨,粗 糙度10-20u→喷涂清洁 促进剂→划分,喷涂彩色 线条(喷枪口径1.7-1.8 ㎜,气压6-8㎏/厘米2, 喷枪距离15-20㎜,环境 温度15-35℃,湿度1080%,膜厚30-50u)— 70℃ 1h烘干
5.1 喷枪的选择
● 德国萨塔(SATA)
● 高压喷枪:进气压力 雾化压力 4.0巴 2.5巴
5.2 油水分离器的选择
德国萨塔三节油水分离器: 第一节:旋风分离器 第二节:纤维棉过滤器 第三节:活性炭过滤器
5.3 空压机的选择 空压机或储气罐出口 压力应为6-8kg为宜