LCD偏光片生产的基本方法
偏光片生产工艺资料
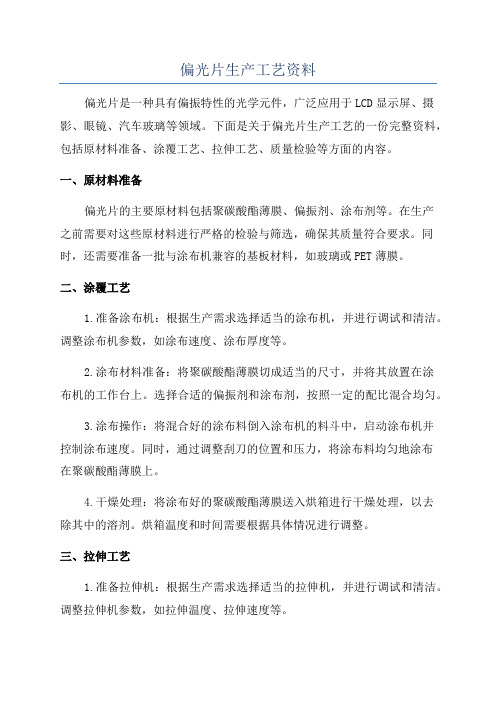
偏光片生产工艺资料偏光片是一种具有偏振特性的光学元件,广泛应用于LCD显示屏、摄影、眼镜、汽车玻璃等领域。
下面是关于偏光片生产工艺的一份完整资料,包括原材料准备、涂覆工艺、拉伸工艺、质量检验等方面的内容。
一、原材料准备偏光片的主要原材料包括聚碳酸酯薄膜、偏振剂、涂布剂等。
在生产之前需要对这些原材料进行严格的检验与筛选,确保其质量符合要求。
同时,还需要准备一批与涂布机兼容的基板材料,如玻璃或PET薄膜。
二、涂覆工艺1.准备涂布机:根据生产需求选择适当的涂布机,并进行调试和清洁。
调整涂布机参数,如涂布速度、涂布厚度等。
2.涂布材料准备:将聚碳酸酯薄膜切成适当的尺寸,并将其放置在涂布机的工作台上。
选择合适的偏振剂和涂布剂,按照一定的配比混合均匀。
3.涂布操作:将混合好的涂布料倒入涂布机的料斗中,启动涂布机并控制涂布速度。
同时,通过调整刮刀的位置和压力,将涂布料均匀地涂布在聚碳酸酯薄膜上。
4.干燥处理:将涂布好的聚碳酸酯薄膜送入烘箱进行干燥处理,以去除其中的溶剂。
烘箱温度和时间需要根据具体情况进行调整。
三、拉伸工艺1.准备拉伸机:根据生产需求选择适当的拉伸机,并进行调试和清洁。
调整拉伸机参数,如拉伸温度、拉伸速度等。
2.拉伸操作:将涂布干燥的聚碳酸酯薄膜送入拉伸机的进料区域,并通过加热和拉伸的方式将其延伸至所需的尺寸和厚度。
拉伸温度和速度需要根据具体情况进行调整。
3.冷却处理:将拉伸好的薄膜送入冷却装置进行快速冷却,以固化其结构。
冷却温度和时间需要根据具体情况进行调整。
四、质量检验为了确保偏光片的质量符合要求,需要进行一系列的质量检验。
常见的检验项目包括偏振性能、厚度均匀性、表面平整度和可见光透过率等。
根据检验结果,可以对生产过程进行调整和改进,以提高产品质量和性能。
lcd基本知识简介及制造流程介绍

视角分类 •3点 •6点 •9点
法法线方向 =0° =180° 12 点方向
θ
Y
观测位置
=270° 9 点钟方向
•12点
•其他
X
=0° 6 点钟方向
=90° 3 点钟方向
4.4 响应速度
LCD经常显示不断变化的图象。人眼的反应时间大约为
100毫秒。故显示图象的变化以外加信号电压变化的响应 不应低于这个速度,描述液晶显示器动态特性的响应时间, 通常用三个常数等表示延迟时间,上升时间(Tr)和下降 时间(Tf)
39
5.2 LCD制作工艺流程简介
从LCD工艺流程图可知,LCD全部制作过程 大体分为40多道工序,其中实际TN制程有20 多道工序,STN有30多道工序,有些工序是特 殊制程,只当客户有特殊要求才实施.这些工 序又可分为ITO图形蚀刻(图形段)﹑定向排 列(PI 及摩擦) ﹑空盒制作﹑切割与灌液 晶和成品检测与包装五个阶段
蚀刻
TOP涂 布
坚膜 UV烘 烤 摩擦定 向
显影
曝光
清洗
TOP固化
印密封 框
印导电 点
清洗
PI固化
涂取 向剂
对位贴合
压烤 固化
38
后制程
切割 裂片 X方向) 灌注液晶 封口 固化
电测
光台检测
再定 向
清洗
打粒(Y 方向)
印油 墨
固化油 墨
贴偏光 片
消泡
外观检 察
入库
包装
FQC/QA
上针脚/ 热压纸
喷码
24
偏光片基本原理图:
25
偏光片的基本结构
保護膜
TAC膜 PVA膜 TAC膜 压敏膠 離型膜 一般透过型偏光片
偏光片生产工艺资料
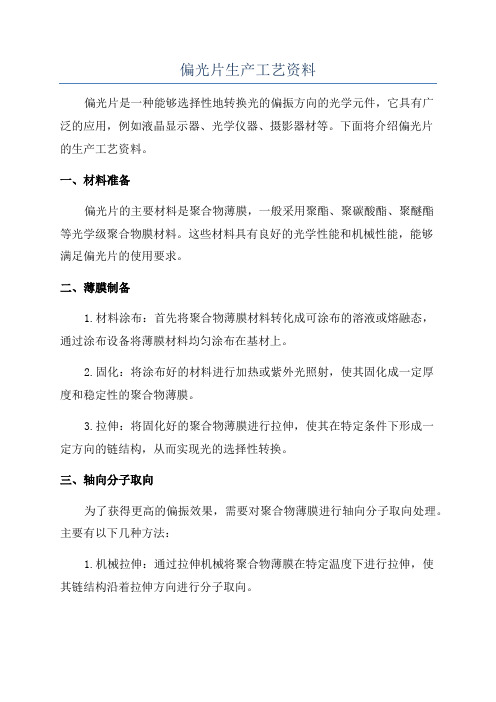
偏光片生产工艺资料偏光片是一种能够选择性地转换光的偏振方向的光学元件,它具有广泛的应用,例如液晶显示器、光学仪器、摄影器材等。
下面将介绍偏光片的生产工艺资料。
一、材料准备偏光片的主要材料是聚合物薄膜,一般采用聚酯、聚碳酸酯、聚醚酯等光学级聚合物膜材料。
这些材料具有良好的光学性能和机械性能,能够满足偏光片的使用要求。
二、薄膜制备1.材料涂布:首先将聚合物薄膜材料转化成可涂布的溶液或熔融态,通过涂布设备将薄膜材料均匀涂布在基材上。
2.固化:将涂布好的材料进行加热或紫外光照射,使其固化成一定厚度和稳定性的聚合物薄膜。
3.拉伸:将固化好的聚合物薄膜进行拉伸,使其在特定条件下形成一定方向的链结构,从而实现光的选择性转换。
三、轴向分子取向为了获得更高的偏振效果,需要对聚合物薄膜进行轴向分子取向处理。
主要有以下几种方法:1.机械拉伸:通过拉伸机械将聚合物薄膜在特定温度下进行拉伸,使其链结构沿着拉伸方向进行分子取向。
2.涂布时的拉伸:在材料涂布过程中,通过合适的方式将薄膜进行拉伸,使其取向在涂布方向上。
3.离子束辐照:使用高能离子束辐照材料,使其分子产生取向运动,从而实现分子取向。
四、涂层制备为了增强偏光片的性能和使用寿命,通常需要在聚合物薄膜上进行涂层。
常用的涂层有防反射涂层、硬质涂层等。
涂层制备主要包括以下几个步骤:1.前处理:对聚合物薄膜进行清洗和表面处理,以提高涂层的附着力。
2.涂层:将涂层材料溶解成溶液或融化成熔融液,通过涂布或蒸镀等方法将涂层材料均匀地涂在聚合物薄膜上,形成所需的涂层。
3.固化:对涂层进行加热或紫外光照射,使其固化成一定的厚度和稳定性。
四、切割和加工将固化好的聚合物薄膜进行切割和加工,制成符合要求的偏光片产品。
切割和加工方式可以采用机械切割、激光切割、压花等方法。
同时,也可以进行软化处理、钝化处理等,以提高产品的品质和稳定性。
五、性能检测对生产好的偏光片进行性能检测,包括透光率、偏振效果、耐热性、表面硬度等指标的测试,确保产品符合设计要求和行业标准。
偏光片生产线的生产工艺,掌握了多少

偏光⽚⽣产线的⽣产⼯艺,掌握了多少偏光⽚,⼜称偏振光⽚,是液晶显⽰模块的重要组成部分,可以控制特定光束的偏振⽅向。
当⾃然光通过偏光⽚时,其振动⽅向垂直于偏光⽚轴的光将被吸收,只剩下振动⽅向平⾏于偏光⽚轴的偏光⽚。
偏光⽚有着⼴泛的应⽤,主要⽤于液晶显⽰模块,液晶显⽰模块成像必须依赖偏光⽚,少任何⼀张偏光⽚⽚,液晶显⽰模块不能显⽰图像。
偏光⽚还可⽤于太阳镜、防眩光护⽬镜、照相器材滤镜、汽车前照灯防眩光处理和调光等偏光显微镜和特殊医疗眼镜。
偏光⽚⽣产线的⽣产⼯艺,碘系⽣产技术和湿法拉伸⼯艺,TAC膜的预处理和PVA膜的延伸与复合是核⼼环节。
TAC膜的预处理⼯艺是对TAC膜的碱溶液进⾏处理。
清洗完洗涤槽中残留的碱溶液后,将TAC膜⼲燥并卷起。
该⼯艺的主要⽬的是降低TAC膜的接触⾓,促进与PVA膜的粘附。
学过⾼中物理的童靴们肯定都知道偏正⽚,拿⼀⽚偏振⽚观察⾃然光,亮度降低⼀半,再拿另⼀⽚偏振⽚,两⽚叠在⼀起观察,旋转其中⼀⽚偏光⽚,观察到的亮度将在0~50%范围内变化。
同样的原理也被应⽤在液晶显⽰领域。
在液晶显⽰器中,玻璃基板两侧有两⽚正交的偏光⽚,在不加电压时,由第⼀⽚偏光⽚起偏后的偏正光向前传输经过液晶层,由于液晶的旋光效应,振动⽅向发⽣改变,顺利通过过第⼆⽚偏光⽚,如图(a);⽽加载电压后,液晶不再有旋光作⽤,偏振光⽆法穿过第⼆⽚偏光⽚,如图(b)。
(a)(b)因此,偏光⽚可以说是液晶显⽰器中⾮常重要的部件,其成本约占整个液晶显⽰器的11%。
但是如此重要的显⽰材料,我国⾃主⽣产能⼒却很差。
根据IHS 2016年数据,我国偏光⽚产能占全球产能不⾜10%。
为什么偏光⽚⽣产这么难?国产化率这么低,⼩编接下来做简要分析。
01偏光⽚结构复杂,涉及专业技术多偏光⽚不是单⼀材料成分膜状结构,⽽是由多层不同性能的膜组成的复合膜结构,其每⼀层膜的成分、性状及作⽤如下表。
有时为了提升膜的其他功能,如增量功能,还要再增加其它膜层。
偏光片工艺流程共35页

偏光片工艺流程共35页
第一步:原材料准备
在偏光片的制作过程中,需要准备一些原材料,主要包括聚合物材料、导向层材料和偏光层材料。
这些材料需要进行筛选和检测,确保其质量符
合要求。
第二步:基片制备
在基片制备过程中,需要将聚合物材料经过熔融后浇铸到平滑的玻璃
片上,然后通过加热和冷却过程使其凝固固化,形成平整的基片。
第三步:导向层制备
导向层是偏光片中的一个重要组成部分,用于确定偏光片的光线传播
方向。
导向层的制备过程中,需要将导向层材料溶解在溶剂中,然后通过
涂覆、加热和固化等过程使其形成薄膜。
第四步:偏光层制备
偏光层是偏光片的核心部分,主要通过染色剂和聚合物材料的混合来
实现。
在偏光层制备过程中,需要将染色剂和聚合物材料溶解在溶剂中,
然后通过涂覆、烘干和固化等过程使其形成厚度均匀的偏光层。
第五步:偏光片装配
在偏光片装配过程中,需要将导向层和偏光层依次贴合到基片上,然
后通过热压等工艺将其固定在一起。
同时,还需要对偏光片进行清洗、干
燥和筛选等处理,以确保其质量符合要求。
第六步:产品检测
在偏光片工艺流程的最后阶段,需要对制作完成的偏光片进行各项检测,以验证其技术指标是否满足要求。
主要包括外观检测、透光性检测、光学性能检测和耐久性检测等。
以上是关于偏光片工艺流程的一个大致概述,其中涉及的具体工艺步骤可能还有其他细节和特殊要求,具体实施情况可能因厂家和产品而有所不同。
这仅仅是一个简要介绍,实际的工艺流程可能更加复杂和详细。
偏光片工艺流程共35页

偏光片工艺流程共35页一、引言通过偏光片的制造过程,我们可以获得偏光效果,使得光线只沿着一个特定方向通过材料。
本文将详细介绍偏光片的工艺流程,以确保最佳的质量和效果。
二、材料准备1.选择适用的材料,例如聚合物材料或玻璃材料。
2.准备材料,确保其干净、无尘,以免影响制造过程和最终产品的质量。
三、制备偏光层1.准备涂层溶液,根据需求调整涂层成分,以获得所需的偏光效果。
2.在材料表面上涂布涂层溶液,使用刮板或喷涂等方法,确保均匀覆盖整个表面。
3.将涂层材料经过干燥或固化过程,以使其形成稳定的偏光层。
4.检查涂层质量,确保没有缺陷或污染。
四、制备偏光结构1.使用湿法或干法将偏光层与基材结合。
2.将偏光层轻轻地贴附到基材上,确保无气泡和偏光层与基材之间的紧密结合。
3.将偏光结构经过压制或加热,以增强其结合力,并确保稳定的偏光效果。
五、切割与整形1.根据需要,使用切割工具将偏光片切割成所需的形状和尺寸。
2.经过整形和打磨等工艺,使偏光片表面光滑,以提高其外观和质量。
六、检测与质量控制1.对偏光片进行检测和测试,以确保其符合规定的标准和质量要求。
2.检查偏光片的表面、偏光效果和结构等方面,确保没有缺陷或损坏。
七、包装与出货1.将偏光片进行适当的包装,以保护其免受运输和储存过程中的损坏。
2.准备出货文件和记录,以便追踪和记录偏光片的相应信息。
八、结论本文详细介绍了偏光片的工艺流程,包括材料准备、制备偏光层、制备偏光结构、切割与整形、检测与质量控制以及包装与出货等环节。
遵循这些工艺流程,可以确保偏光片的最佳性能和质量。
lcd生产工艺流程

lcd生产工艺流程LCD(Liquid Crystal Display)是液晶显示器的简称,是一种利用液晶材料来显示图像的平面显示技术。
下面是LCD生产的工艺流程:1. 玻璃基板制备:首先需要准备两片大型的玻璃基板,一片作为液晶显示面板的正面(TFT面板),另一片作为背面(色彩滤光片面板)。
2. 制作TFT面板:在TFT面板上,首先需要通过薄膜沉积工艺,在玻璃基板上涂覆一层透明导电层(通常是氧化铟锡层),用于传输电流。
然后在导电层上,使用光刻和薄膜沉积等工艺,依次制作薄膜晶体管(TFT)和电路结构。
3. 制作色彩滤光片面板:在色彩滤光片面板上,首先需要将一层有机色彩滤光片涂覆在玻璃基板上。
然后通过光刻等工艺,制作出三原色(红、绿、蓝)的像素点阵。
4. 液晶填充:将两个制作好的玻璃基板中间加上一层液晶材料,并进行密封。
液晶材料是由两层平行的玻璃基板包裹,基板上都有导电层和透明导电物体。
在液晶层内部,每个像素点都有一个类似液态的晶体,有正常、液态、正常三种状态,通过施加不同的电压来控制液晶的状态。
5. 封装:将液晶显示结构加热至封装温度,然后通过化学反应或机械焊接等工艺,将两个玻璃基板粘合在一起,并在侧面密封,防止液晶材料泄漏。
6. 模组制作:将封装好的液晶显示结构整合成一个完整的液晶模组,加入背光源、控制电路和接口等元件。
7. 调试和测试:对液晶模组进行调试和测试,确保其正常工作和质量符合要求。
8. 封装和组装:将调试好的液晶模组封装在塑料外壳中,并进行最后的组装工作,包括安装支架、接口线等。
9. 最后测试和质量控制:对成品进行最后的测试和质量控制,确保产品的性能和质量符合标准要求。
10. 出厂:最后,通过包装和运输等工序,将产品出厂,并投放市场。
以上是LCD生产的主要工艺流程,涵盖了从原材料制备到成品生产的过程。
该流程需要严格的质量控制和技术要求,以确保生产出高质量的LCD产品。
偏光片生产经验范文

偏光片生产经验范文标题:偏光片生产经验分享导言:偏光片是一种广泛应用于光学领域的材料,具有独特的光学性能和应用价值。
作为一名从业多年的光学工程师,我在偏光片生产方面积累了丰富的经验和心得体会。
本文将从材料选择、生产工艺和质量控制等方面分享我的经验,以期对从事相应行业的同行有所帮助。
一、材料选择:偏光片常用的材料有偏光膜、偏光复合板和偏光玻璃等。
在选择材料时应根据具体的应用需求和成本因素综合考虑。
比如,对于需要高透过率和低折射率的场合,可以选择偏光玻璃作为基材;而对于需要更高的透过率和柔韧性的场合,可以选择偏光膜。
二、生产工艺:1.材料预处理:在生产过程中,材料的预处理非常重要。
例如,对于偏光膜,需要进行表面处理以提高其附着力和光学性能。
2.偏光膜涂覆:将偏光膜涂覆在基材上是偏光片生产的关键步骤。
在涂覆过程中,应确保涂层均匀,不出现气泡或污染。
3.光学修整:生产出的偏光片通常会存在一些光学缺陷,如刮痕、气泡和光学偏差等。
通过光学修整工艺,可以去除这些缺陷,提高产品的质量和性能。
4.切割和送料:在生产过程中,将大规格的偏光片切割成所需的尺寸。
切割过程需要精确控制角度和尺寸,以确保产品的几何形状。
5.检测质量控制:生产出的偏光片需要经过严格的质量控制程序,包括外观检查、光学性能测试和耐久性测试等。
只有合格的产品才能够进入市场。
三、质量控制:在偏光片生产中,质量控制是至关重要的。
以下是我在质量控制方面的一些建议:1.建立严格的质量控制流程,并进行相应的培训和指导,确保操作人员熟练掌握。
2.定期检查生产设备和工艺流程,及时发现和修复问题,以防止出现质量问题。
3.建立完善的质量管理体系,包括设立质量目标、实施过程控制和持续改进等。
4.进行充分的产品测试和检验,包括外观、光学性能和耐久性等方面的测试。
5.与供应商建立良好的合作关系,确保原材料的质量和供货稳定性。
结语:偏光片是光学领域中不可或缺的材料,其生产需要严格的工艺和质量控制。
lcd工艺流程

lcd工艺流程
《LCD工艺流程》
LCD(Liquid Crystal Display,液晶显示)是一种常见的平板显示器,其制造过程涉及复杂的工艺流程。
下面将介绍LCD 的工艺流程:
1. 衬底制备:首先,选择合适的玻璃或聚酯基板作为LCD的衬底。
然后,在基板上涂覆一层透明的导电层,用于驱动液晶显示的像素。
接着,再涂覆一层辅助层,用于提高玻璃与液晶的附着力。
2. 制造电极:通过光刻技术,在导电层上制造出细小的电极阵列,形成LCD的基本显示单元。
3. 液晶注入:在两块玻璃基板之间注入液晶材料,并保持一定的压力和温度条件。
这个过程需要高度的洁净度和精确的操作控制,以确保液晶充填均匀和无杂质。
4. 封装:将两块涂有电极的基板用密封胶边封装在一起,形成完整的液晶显示器模组。
在这一步骤中,还要加入偏光膜和色彩滤光片,以提高显示效果。
5. 光学调试:对LCD进行逐一的光学调试,检查显示效果和色彩表现,确保每个像素的显示质量。
6. 后期加工:进行最终的边框打磨、组装、测试等后续加工工
艺,生产完成LCD显示器。
以上便是LCD工艺流程的简要介绍,涉及到的工艺技术和设备都需要高度的精密度和稳定性。
随着科技的不断发展,LCD 制造工艺也在不断完善和创新,向着更高的清晰度、更薄的厚度和更广的色域发展。
lcd生产工艺流程

lcd生产工艺流程
《LCD生产工艺流程》
LCD(Liquid Crystal Display,液晶显示屏)是一种广泛应用
于电子产品中的显示技术,其生产工艺流程经过多道精细加工步骤。
首先,LCD的生产从玻璃基板的制备开始。
玻璃基板通常经
过锻压、打磨、清洗等步骤,以确保表面光滑度和干净度,为后续工艺做好准备。
接下来是对基板进行透明导电膜的涂布。
这一步骤需要精密的设备和专门的化学材料,以确保导电膜的均匀和透明度。
然后是液晶层的制备。
这一步骤涉及到在基板上涂覆液晶材料,然后通过加热和其他方法使其在基板上形成均匀的分布。
紧接着是色滤片的制备。
色滤片是用于给液晶显示器赋予色彩的重要组成部分,其制备需要特殊的化学材料和精密的图形加工工艺。
最后是封装和测试。
在这一步骤中,将制备好的基板组装成LCD模组,并进行各种测试以确保其性能和质量。
整个生产工艺流程中,涉及到许多关键的技术和工艺,需要高度的精密度和自动化程度。
通过不断的技术创新和工艺改进,
LCD的生产工艺流程在不断地提高效率和产品质量,满足不断增长的市场需求。
LCD制造工艺流程

LCD制造工艺流程LCD(Liquid Crystal Display)是液晶显示器的英文缩写,是一种广泛应用于各种电子产品的显示技术。
LCD制造工艺流程可以简单分为六大步骤:基板制备、导电及栅极制备、液晶材料填充、封装、模组制备和组装测试。
一、基板制备1.玻璃基板准备:使用特种玻璃片制作成圆形或矩形的底座。
这些玻璃片将成为液晶分子的基质。
2.清洗:用酸、碱和去离子水等溶液对玻璃基板进行清洗,以去除表面的污垢和杂质。
3.涂覆:将光学薄膜涂覆在玻璃表面,以提高光学透明度和反射率。
二、导电及栅极制备1.导电层制作:在玻璃基板上溅射或喷涂一层透明导电层(通常为氧化铟锡或氧化铟锡锌)。
2.刻蚀:使用光刻技术在导电层上制作触摸和驱动电极。
3.栅极层制作:在玻璃基板上溅射或喷涂一层低温氧化硅(SiOx)或其他绝缘材料,用于隔离栅极和导电层。
4.刻蚀:使用光刻技术在绝缘层上制作栅极电极。
三、液晶材料填充1.在两片玻璃基板上的栅极电极上均匀涂覆一层聚合物,以形成液晶分子定向的基准面。
2.制作液晶间距:使用小玻璃珠或者薄膜作为间距标准,将两片基板固定在一起,形成液晶显示器的夹层结构。
3.注液:通过特殊装置将液晶材料注入夹层结构中,填充液晶间距,然后封口。
四、封装1.导电胶片制作:制备导电胶片,此胶片具有接触电极和连接电源的功能。
2.连接导电胶片:将导电胶片粘贴在液晶显示器的边缘区域上,与栅极电极和驱动电极连接。
3.封装结构制作:使用封装材料将液晶显示器的背光模块、面板和底座固定在一起,并确保显示器的稳定工作。
五、模组制备1.背光模块制作:制作光源模块,常用的包括冷阴影式背光模块和LED背光模块。
2.声音模块制作:如果需要,可以制作声音模块,用于播放声音或发出警报。
3.灰度控制器制作:制作液晶显示器的灰度控制器,用于调节显示屏的亮度和对比度。
六、组装测试1.组件安装:将模组组件安装到设备的框架中。
2.电气连接:将电气连接器连接到液晶显示器的导电胶片和驱动电路上。
偏光片制造工序

偏光片制造工序
偏光片制造工序是将原始光学材料(如玻璃或塑料)加工成光学元件的过程。
偏光片是一种用于折射光波的特殊光学元件,它可以改变光线的传播方向,并能够对折、分解或把光强度分配到不同的频带中。
偏光片制作工艺大致分为以下几个步骤:
1. 材料准备:在制作偏光片之前,必须准备好原材料,包括玻璃、塑料等,并根据设计要求进行尺寸和形状的调整。
2. 加工:根据设计要求,使用抛光机、切割机等设备对材料进行加工,加工出所需的反射镜、折射镜、折射面和其他光学元件。
3. 处理:使用化学腐蚀剂处理材料表面,使其具有特殊的光学性能。
4. 表面处理:将材料进行表面处理,使其具有特殊的光学性能。
5. 涂层:使用特殊的涂层技术,在光学元件表面涂上特殊的镀层,使其具有抗氧化、耐高温等特性。
6. 测试:使用特殊的测试仪器进行光学特性测试,确保其达到设计要求。
7. 包装:将加工好的偏光片封装,以便防止污染和损坏。
偏光片制造工艺是一个复杂的过程,从材料的选择、加工到最终成品的测试,都需要掌握复杂的光学原理和技术,以及对材料加工时的精细控制。
在制造偏光片时,应该特别注意材料的选择、加工过程、表面处理以及抗氧化涂层的施工,以确保偏光片具有良好的性能和可靠性。
LCD生产工艺流程
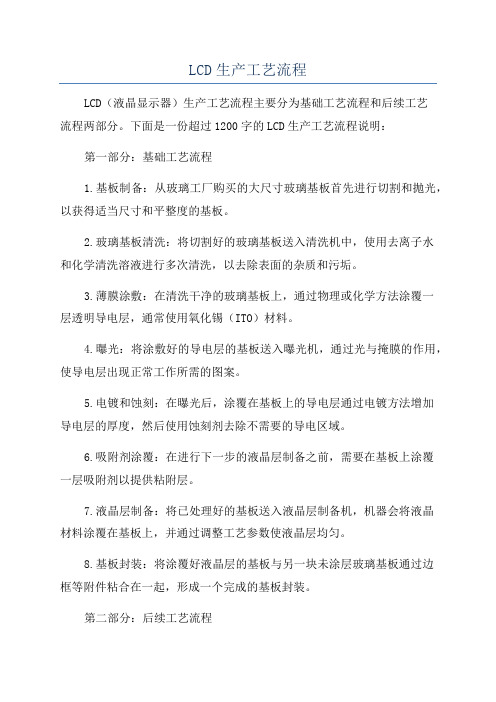
LCD生产工艺流程LCD(液晶显示器)生产工艺流程主要分为基础工艺流程和后续工艺流程两部分。
下面是一份超过1200字的LCD生产工艺流程说明:第一部分:基础工艺流程1.基板制备:从玻璃工厂购买的大尺寸玻璃基板首先进行切割和抛光,以获得适当尺寸和平整度的基板。
2.玻璃基板清洗:将切割好的玻璃基板送入清洗机中,使用去离子水和化学清洗溶液进行多次清洗,以去除表面的杂质和污垢。
3.薄膜涂敷:在清洗干净的玻璃基板上,通过物理或化学方法涂覆一层透明导电层,通常使用氧化锡(ITO)材料。
4.曝光:将涂敷好的导电层的基板送入曝光机,通过光与掩膜的作用,使导电层出现正常工作所需的图案。
5.电镀和蚀刻:在曝光后,涂覆在基板上的导电层通过电镀方法增加导电层的厚度,然后使用蚀刻剂去除不需要的导电区域。
6.吸附剂涂覆:在进行下一步的液晶层制备之前,需要在基板上涂覆一层吸附剂以提供粘附层。
7.液晶层制备:将已处理好的基板送入液晶层制备机,机器会将液晶材料涂覆在基板上,并通过调整工艺参数使液晶层均匀。
8.基板封装:将涂覆好液晶层的基板与另一块未涂层玻璃基板通过边框等附件粘合在一起,形成一个完成的基板封装。
第二部分:后续工艺流程9.偏光膜粘合:在玻璃基板的一侧粘贴一层偏光膜,以改善图像质量和视觉效果。
10.显示模组组装:将完成的基板封装与背光源模组进行组装,包括灯泡、反射层和调整器,以实现液晶显示器的亮度调整和背光效果。
11.模组封装:将组装好的显示模组与控制电路板、电源等组件进行连接,然后通过机械方式进行封装,以保护内部组件。
12.功能测试:将封装好的液晶显示器进行功能测试,包括显示质量、电源功耗、背光亮度等各项功能的测试。
13.清洗和检查:在功能测试后,对液晶显示器进行清洗以去除表面的污垢,并进行目视检查和光学测试,以检查是否有任何缺陷。
14.包装和入库:通过机械方式将已检查和清洗好的液晶显示器进行包装,并将其存放在仓库中,准备进行下一步的分销和销售。
偏光片制造技术4

第4章偏光片的工艺基础4.1 工艺分类偏光片的生产工艺按拉伸工艺来分,有干法拉伸和湿法拉伸两种;按染色工艺来分,有染料染色和碘系染色两种。
4.1.1 干法生产工艺流程偏光片的干法生产技术是指PV A膜是在具有一定温度和湿度条件的蒸汽环境下进行拉伸取向,再进行染色、固色、复合、干燥的偏光片制备工艺。
其基本工艺流程为:退卷——热辊拉伸——水洗——染色——水洗——固色——水洗——PV A素子干燥——复合TAC——烘干——复合保护膜——收卷。
如图4-1-1所示,定制的PV A膜经由退卷展送到多个热辊中,由热辊加热,在惰性气体环境中将PV A膜延伸到一定倍率;拉伸后膜经由纯水浸泡清洗然后进入染色槽进行染色;染色的膜经水洗把表面浮碘洗掉再进入固色槽进行固色以稳定色调;再经过一次水洗,挤水后进行PV A素子干燥、复合TAC、烘干,再覆上保护膜,收卷后就完成偏光片基板的生产。
图4-1-1 干法生产工艺流程图干法拉伸盛行于70年代,我国深纺乐凯光电子在上世纪90年代末,也曾采用这种延伸工艺生产TN型偏光片。
早期使用这种工艺方法,是因为其PV A利用率比较高,每平方米PV A膜可生产偏光片约3.3-3.6平方米;使用幅宽较宽的PV A 进行生产时不会经常断膜。
但这种工艺的局限性在于PV A膜在延伸过程中的均匀性受到限制,拉伸的倍率低,拉伸后染色深度低,染色效率不高,因此所形成的偏光片原膜的复合张力、色调的均匀性和耐久性不易稳定,膜表面粗糙,用这种方法生产的产品只能满足在TN产品上的应用;而且产能较低,也不易于操作机控制,因此这种生产工艺中已经慢慢淡出了偏光片生产行业。
4.1.2 湿法生产工艺流程湿法拉伸工艺是指PVA膜先进行染色,而后在一定配比的液体中进行拉伸、固色、复合、干燥的偏光片制备工艺。
其基本工艺流程为:退卷——水洗——彭润——染色——水洗——拉伸——补色——PV A素子干燥——复合TAC——烘干——复合保护膜——收卷。
LCD生产工艺制程
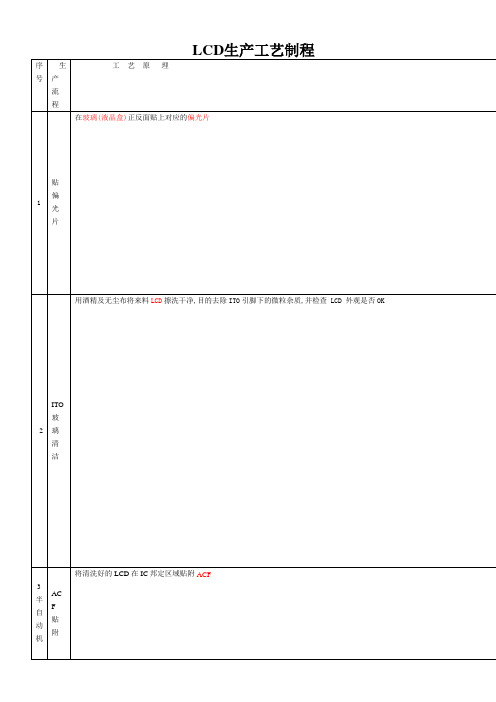
注意事项:
1、COG工序作业人员双手需戴手套,十指再戴手指套,手腕配戴防静电环(必须接地),其它工序作业人员需戴手指套和手腕配戴
防静电环。
2、机器操作前必须由设备工程人员调试确认OK 后方可作业。
3、作业人员不得擅自更改机器参数,按作业指导书规范作业。
4、吸塑防静电盘必须时刻保持清洁。
5、接触 LCD 及 IC 等物料必须使用防静电工具,以免静电击伤产品。
也不可使用尖锐锋利的器具以免刮伤产品。
6、LCM组装需在独立且洁净度较高的净房车间进行,组装时应轻拿轻放为原则,避免让酒精、丙酮等化学药水碰触及渗进模组。
7、机器操作开始作业时应试产几个产品经相关人员确认后再进行批量生产。
8、作业人员应时刻保持端正的工作态度,做好自检工作。
PQC 及生产管理人员应不定时对各工序进行抽检以利于一些潜在问题能及时发现。
9、邦定 IC 及热压 FPC 之前必须清洁 LCD ITO 及 FPC 金手指,擦拭溶剂需用酒精,擦拭 LCD 表面采用无水乙醇(酒精浓度99.7%
以上)。
编写/日期: 审批/日期:。
lcd工艺流程

lcd工艺流程LCD工艺流程。
LCD(Liquid Crystal Display)是一种广泛应用于电子产品中的显示技术,其制造过程是一个复杂而精密的工艺流程。
本文将对LCD工艺流程进行详细介绍,以帮助读者更好地了解LCD的制造过程。
首先,LCD的制造过程可以分为几个主要步骤,基板制备、涂布、曝光、蚀刻、清洗、组装和封装等。
在基板制备阶段,需要使用玻璃基板作为LCD的基础材料,经过切割、打磨和清洗等工艺步骤,以确保基板表面的平整度和清洁度。
接下来是涂布阶段,涂布是将液态材料均匀地涂布在基板表面,形成一层薄膜。
这一步骤需要高精度的设备和技术支持,以确保涂布薄膜的均匀性和厚度的一致性。
曝光和蚀刻是LCD制造过程中非常关键的步骤,曝光是利用光刻技术将图案投影在涂布薄膜上,形成所需的图案结构。
而蚀刻则是利用化学腐蚀或物理蚀刻的方式,将未曝光部分的薄膜材料去除,从而形成所需的图案结构。
这两个步骤需要高精度的设备和严格的工艺控制,以确保图案的精确度和清晰度。
清洗是LCD制造过程中不可或缺的环节,清洗是为了去除曝光和蚀刻过程中产生的残留物和杂质,以保证LCD的质量和性能。
清洗过程需要使用高纯度的溶剂和严格的清洗工艺,以确保基板表面的洁净度和光洁度。
最后是LCD的组装和封装,组装是将各个部件组装在一起,形成完整的LCD显示屏。
而封装则是将LCD显示屏封装在外壳中,以保护其不受外界环境的影响。
组装和封装需要严格的工艺控制和质量检测,以确保LCD显示屏的稳定性和可靠性。
总的来说,LCD的制造过程是一个高精度、高技术含量的工艺流程,需要严格的工艺控制和质量管理。
只有通过精密的设备和严格的工艺控制,才能制造出高质量、高性能的LCD显示屏。
希望本文能够帮助读者更好地了解LCD的制造过程,对LCD技术有更深入的认识。
LCD偏光板的结构和原理介绍

以PVA膜的延伸工艺划分
干法
LCD偏光板生 产的基本方法 以PVA膜染色方法划分
湿法 染料系
碘染色
偏光板的表面处理技术以及度量标准 (Surface Treatment Technology of Polarizer&standard of measure) 一、表面处理偏光板的结构( Structure of Polarizer ) 如右图一所示:经过表面处理——防眩(Antiglare)和防反射(Anti-reflection)的偏振片薄膜 由三部分组成: 偏光板薄膜(Polarizing Film) 防眩涂层(Anti-glare Layer) 防反射层(Anti-reflection Layer) 图一 偏光板剖面图(Cross Section of Polarizer) 防眩处理(anti-glare(AG) treatment): 主要是将含有3 m粒子的树脂(resin)涂敷于保护膜的表面。 防反射处理(anti-reflection(AC) treatment): 将具有低折射率(Low Refraction index)的物质涂敷于AG膜的表面。
2.耐久性技术指标包括:耐高温、耐湿热、耐低温和耐冷热冲击四项技术指标,其 中最重要的是耐湿热性能指标的高低。
说明
耐高温是指偏光片在宜定烘烤温度下的耐温工作条件,由于构成偏光膜的 基本材料PVA膜和碘及碘化物都是极易水解的材料,同时也由于偏光片所 使用的压敏胶在高温高湿条件下也容易劣化,因此,在偏光片的耐久性技 术指标中最重要的就是耐高温和耐湿热指标,如果耐高温和耐湿热指标通 过,其它耐久性型指标通常都不会发生间题
LCD偏光片的基本性能ቤተ መጻሕፍቲ ባይዱ标
光学性能、耐久性性、粘接特性、外观性能和其他特殊性能几个方面的基本技术指标要求。 1.光学性能包括:偏光度、透过率和色调三项主要性能指标,其它还包括防紫外线性能以 及半透过型偏光片半透膜的透过率、全反射率和漫反射率指标。 说明 在一般LCD产品的使用中。要求偏光度和透过率性能指标越高越好。偏光 度和透过率越高,LCD显示器件的显示效率就越高,相对能耗就小对常规 碘染色的偏光片产品而言,偏光度和透过率是一对矛盾,偏光度越高, 透过率就会越低,而且还要受到色调的约束,因此一般普通型的偏光片产 品的偏光度都在90%一99%之间,透过率在41%一44%之间。
- 1、下载文档前请自行甄别文档内容的完整性,平台不提供额外的编辑、内容补充、找答案等附加服务。
- 2、"仅部分预览"的文档,不可在线预览部分如存在完整性等问题,可反馈申请退款(可完整预览的文档不适用该条件!)。
- 3、如文档侵犯您的权益,请联系客服反馈,我们会尽快为您处理(人工客服工作时间:9:00-18:30)。
L C D偏光片生产的基本方法-标准化文件发布号:(9556-EUATWK-MWUB-WUNN-INNUL-DDQTY-KII
LCD偏光片生产的基本方法
发布时间:2006-5-30 10:37:15 编辑:xjr 来源:
目前偏光片生产技术以PVA膜的延伸工艺划分,有干法和湿发两大类;以PVA 膜染色方法划分,有染料系和碘染色两大类。
偏光片的干法生产技术是指PVA膜是在具有一定温度和湿度条件的蒸汽环境下进行延伸的工艺方法,早期使用这种工艺方法的目的,是可以提高工艺的生产效率,使用幅宽较大的PVA膜进行生产而不至于经常断膜。
但这种工艺的局限性在于PVA膜在延伸过程中的均匀性受到限制,因此所形成的偏光片原膜的复合张力、色调的均匀性和耐久性不易稳定,因而在实际生产工艺中应用较少。
偏光片的湿法生产技术是指PVA膜是在一定配比的液体中进行染色、拉伸的工艺方法。
这种工艺方法早期的局限性在于PVA膜在液体中延伸的稳定控制难度较大,因此使用这种工艺加工时PVA膜容易断膜,且PVA膜的幅宽受到限制。
但随着工业控制技术的改进,这些湿法加工工艺的局限性已经得到极大的改进,从20世纪90年代末起,日本偏光片企业已经普遍采用幅宽1330㎜的TAC膜用湿法工艺进行偏光片的生产。
特别是由于大尺寸TFT-LCD产品的大规模普及,为提高偏光片产品的利用率,以1330㎜为基本宽度的偏光片生产已经成为液晶用偏光片生产的基本方法。
偏光片生产工艺中的染色方法有碘染色法和染料染色法两种工艺。
碘染色法是指在偏光片染色、拉伸过程中,使用碘和碘化钾作为二向性介质使PVA膜产生极性化偏光特性。
这种染色方法的优点是比较容易获得%以上的高偏光度和42%以上高透过率的偏光特性。
所以在早期的偏光材料产品或需要高偏光、高透过特性的偏光材料产品中大多都采用碘染色工艺进行加工。
但这种工艺的不足之处就是由于碘的分子结构在高温高湿的条件下易于破坏,因此使用碘染色工艺生产的偏光片耐久性较差,一般只能满足干温:80℃×500HR,湿热:60℃×90%RH×500HR以下的工作条件使用。
但随着LCD产品使用范围的扩大,对偏光产品的湿热工作条件的要求越来越苛刻,已经出现要求在100℃和90%RH条件下工作的偏光片产品需求,对这种工作条件要求,碘染色工艺就无能为力了。
为满足这种技术要求,首先由日本化药公司发明了偏光片生产所需的染料,并由日本化药的子公司日本波拉公司生产了染料系的高耐久性偏光片产品。
利用二向性染料进行偏光片染色工艺所生产的偏光片产品,目前最高可以满足干温:105℃×500HR,湿热:90℃×95%RH×500HR以下的工作条件的使用要求。
但这种工艺方法所生产的偏光片产品一般偏光度和透过率较低,其偏光度一般不超过90%、透过率不超过40%,且价格昂贵。
本文来自中华液晶网地址。