等离子刻蚀机技术参数
等离子体刻蚀机使用说明书(最新版)

中国电子科技集团公司第四十八研究所
e) 电源: 三相交流 380(1±10%)V,频率 50(1±1%)Hz; f) 所用工艺气体压力: 0.1MPa~0.2MPa;压缩空气压力:0.3MPa~0.5Mpa; g) 有良好的接地点,接地电阻小于 4Ω。 2. 工作原理及结构特征 2.1 总体结构 本设备由反应室、真空系统、送气系统、高频电源、匹配器等部分组成,见附录 1——等离子体刻蚀机平面安装图。 2.2 设备系统及工作原理
300 片/批
3.4 射频电源
13.56MHZ ,100~1000W 连续可调
3.5 气路系统
手动、1 路浮子流量计,2 路质量流量计
3.6 抽气系统
2X-15 机械泵,工作压力自动控制
3.7 载片架旋转
3.8 刻蚀速率
Si3N4
50nm/min
掺杂硅 200nm/min
3.9 批间时间
25min
3.10 电源
6
中国电子科技集团公司第四十八研究所
4.3.3 设备断电,将隔断放气阀与泵进气法兰的快卸卡箍拆下,用 KF40 盲板堵住泵进 气法兰口,并装上快卸卡箍。给设备上电,“泵关”有指示后,点动“泵开”按钮,观 察机械泵旋转方向是否与标记一致,若反向则任意交换机械泵进线中的两相。确认机 械泵旋转方向与标记一致后,拆下盲板,重新装好隔断放气阀。 4.3.4 将旋转开关旋至手动,开机械泵和预抽阀,2min~3min 后压力表应显示有压 力值;当压力的测量值小于 600Pa 时,关预抽,开主抽,三分钟后压力值显示应小于 15Pa,如达不到该值,应检查各管路接头。若压升率<10Pa/min(关闭主抽后,反应室 内压力上升的速率),则更换机械泵内的机械泵油(泵油型号为 1 号真空泵油)或机械 泵。 4.3.5 各开关复位,将旋转开关旋到自动,从控制界面进入手动界面(操作程序见 《等离子体刻蚀机 PLC 自动控制操作说明书》),测试各阀门工作状态,确认无异常后, 准备进行手动工艺的调试。 4.3.6 将射频电源功率粗调旋钮逆时针旋到底,按下射频电源的“预热”(“电源预 热”)按钮,预热 30 分钟。 4.3.7 按下“泵开”按钮,启动机械泵。将O2、CF4的流量及反应室压力设定到工艺 值(设定过程详见《等离子体刻蚀机PLC自动控制操作说明书》),并按工艺步骤进行 操作。当进行到送气步骤时,电机转速为 10rpm。 4.3.8 当压力稳定后,按下射频电源的“高压开”按钮,将功率旋钮顺时针转动(注 意:只能轻微的、缓慢的转动),当板压达到约 500V 时,调节调谐 1 和调谐 2,,使反 应室内会产生辉光,并且使反射功率最小(小于入射功率的 5%); 4.3.9 缓慢旋转功率粗调旋钮,并不断调整匹配盒上的调谐 1 和调谐 2 旋钮,保证反 射功率一直最小(小于入射功率的 5%),直到功率增至需要的数值。 4.3.10 等功率稳定 10 分钟后,将功率粗调旋钮逆时针旋到底,等到压力稳定在设 定值后,再将功率粗调旋钮顺时针旋转到刚才的位置,观察各参数应与刚才的一致。 4.3.11 关射频电源高压后,用N2清洗反应室 1min(N2流量约 400sccm),按“充气” 开关,蜂鸣器报警后,再次按下“充气”开关,停止充气,退出手动操作界面。 4.3.12 完成上述步骤后,将旋转开关旋至自动,设定各工艺参数,开盖,将待刻蚀 的硅片放入反应室,关上盖,按下运行按钮,刻蚀工艺将自动完成。完成后关运行按 钮,开盖取片。
等离子刻蚀机技术参数
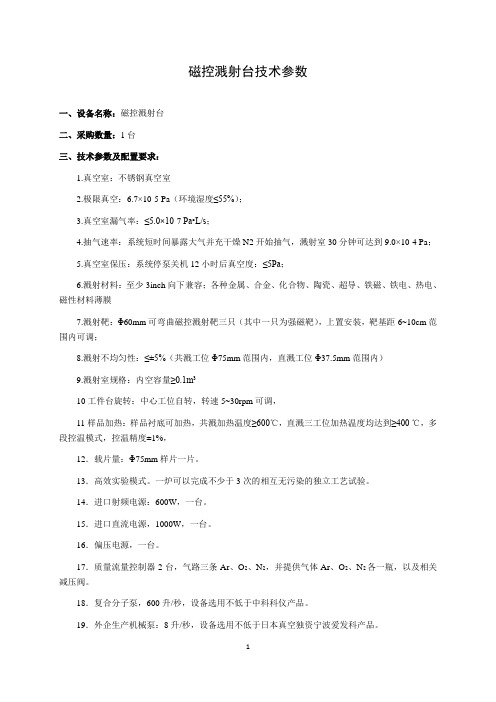
磁控溅射台技术参数一、设备名称:磁控溅射台二、采购数量:1台三、技术参数及配置要求:1.真空室:不锈钢真空室2.极限真空:6.7×10-5 Pa(环境湿度≤55%);3.真空室漏气率:≤5.0×10-7 Pa•L/s;4.抽气速率:系统短时间暴露大气并充干燥N2开始抽气,溅射室30分钟可达到9.0×10-4 Pa;5.真空室保压:系统停泵关机12小时后真空度:≤5Pa;6.溅射材料:至少3inch向下兼容;各种金属、合金、化合物、陶瓷、超导、铁磁、铁电、热电、磁性材料薄膜7.溅射靶:Φ60mm可弯曲磁控溅射靶三只(其中一只为强磁靶),上置安装,靶基距6~10cm范围内可调;8.溅射不均匀性:≤±5%(共溅工位Φ75mm范围内,直溅工位Φ37.5mm范围内)9.溅射室规格:内空容量≥0.1m310工件台旋转:中心工位自转,转速5~30rpm可调,11样品加热:样品衬底可加热,共溅加热温度≥600℃,直溅三工位加热温度均达到≥400℃,多段控温模式,控温精度±1%,12.载片量:Φ75mm 样片一片。
13.高效实验模式。
一炉可以完成不少于3次的相互无污染的独立工艺试验。
14.进口射频电源:600W,一台。
15.进口直流电源,1000W,一台。
16.偏压电源,一台。
17.质量流量控制器2台,气路三条Ar、O2、N2,并提供气体Ar、O2、N2各一瓶,以及相关减压阀。
18.复合分子泵,600升/秒,设备选用不低于中科科仪产品。
19.外企生产机械泵:8升/秒,设备选用不低于日本真空独资宁波爱发科产品。
20.超高真空插板阀。
21.自动压力控制系统,配套进口规管。
22.全自动控制系统,包括进口控制模块、工控机、控制软件。
23.配套循环冷却水机、静音空气压缩机。
24. 配套靶材7种:Al、Cu、Cr、Ti、Si、SiO2、Au(其中靶材Au为Φ60mm*3mm,纯度不低于99.99%,其他6种为Φ60mm*5mm,高纯)。
等离子体刻蚀中工艺参数对刻蚀速率影响的研究
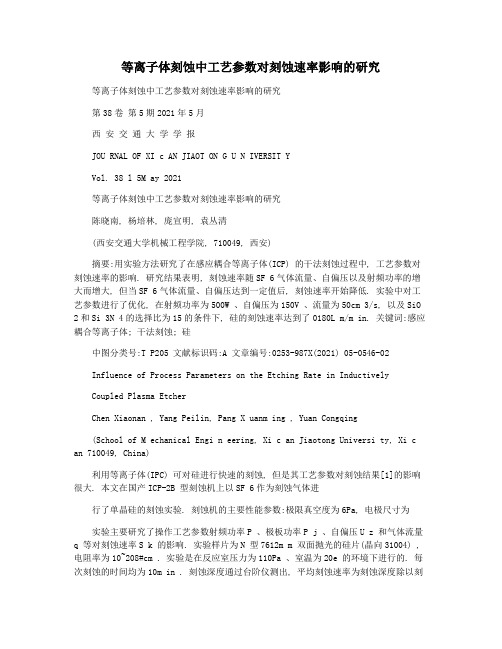
等离子体刻蚀中工艺参数对刻蚀速率影响的研究等离子体刻蚀中工艺参数对刻蚀速率影响的研究第38卷第5期2021年5月西安交通大学学报JOU RNAL OF XI c AN JIAOT ON G U N IVERSIT YVol. 38 l 5M ay 2021等离子体刻蚀中工艺参数对刻蚀速率影响的研究陈晓南, 杨培林, 庞宣明, 袁丛清(西安交通大学机械工程学院, 710049, 西安)摘要:用实验方法研究了在感应耦合等离子体(ICP) 的干法刻蚀过程中, 工艺参数对刻蚀速率的影响. 研究结果表明, 刻蚀速率随SF 6气体流量、自偏压以及射频功率的增大而增大, 但当SF 6气体流量、自偏压达到一定值后, 刻蚀速率开始降低. 实验中对工艺参数进行了优化, 在射频功率为500W 、自偏压为150V 、流量为50cm 3/s, 以及SiO 2和Si 3N 4的选择比为15的条件下, 硅的刻蚀速率达到了0180L m/m in. 关键词:感应耦合等离子体; 干法刻蚀; 硅中图分类号:T P205 文献标识码:A 文章编号:0253-987X(2021) 05-0546-02Influence of Process Parameters on the Etching Rate in InductivelyCoupled Plasma EtcherChen Xiaonan , Yang Peilin, Pang X uanm ing , Yuan Congqing(School of M echanical Engi n eering, Xi c an Jiaotong Universi ty, Xi c an 710049, China)利用等离子体(IPC) 可对硅进行快速的刻蚀, 但是其工艺参数对刻蚀结果[1]的影响很大. 本文在国产ICP-2B 型刻蚀机上以SF 6作为刻蚀气体进行了单晶硅的刻蚀实验. 刻蚀机的主要性能参数:极限真空度为6Pa, 电极尺寸为实验主要研究了操作工艺参数射频功率P 、极板功率P j 、自偏压U z 和气体流量q 等对刻蚀速率S k 的影响. 实验样片为N 型7612m m 双面抛光的硅片(晶向31004) , 电阻率为10~208#cm . 实验是在反应室压力为110Pa 、室温为20e 的环境下进行的. 每次刻蚀的时间均为10m in . 刻蚀深度通过台阶仪测出, 平均刻蚀速率为刻蚀深度除以刻蚀时间. 操作的方式为:¹当P 为500W , SF 6的q 分别为15、30、50和80cm /s , 以及U z 分别为40、80、150和250V 时, 得到S k 与SF 6的q 和U z 的关系曲线; º在反应室压力、温度固定不变的情况下, 设SF 6的q 为50cm /s , U z 为150cm /s , P 分别为300、500和700W 时, 得到Sk 与P 的关系曲线.2 实验结果分析2. 1 U z 与P j 的关系U z 是刻蚀工艺参数综合作用的结果. 在一般情况下, 反应室气压、P 和P j 都会影响U z , 从而对刻蚀过程产生影响. 在P =500W , SF 6的q 分别为15、30、50和80cm3/s 时, U z 与P j 的关系如图1所示. 由图1可见, U z 与P j 成正比关系, 而q 对U z 的影响不大, 可以忽略. 由于U z 的产生原因是由等离子体中离子与电子的巨大速度差异所致, 而在P 和反应室压力不变的情况下, 等离子体中离子和电子的数量基本是不变的, 所以改变q 不会对U z 产生影响.2. 2 U z 对S k 的影响由于U z 与P j 具有线性关系, 因此P j 对S k 的影响与U z 对S k 的影响是相同的, 两者可任选其一, 这里选择后者作为讨论对象. 在上述工艺参数下, S k 与U z 的关系如图2所示. 由图2可见, 在不同的q收稿日期:2021-07-15. 作者简介:陈晓南(1955~) , 男, 副教授. 基金项目:陕西省自然科学研究基金资助项目(2002E 07).第5期陈晓南, 等:等离子体刻蚀中工艺参数对刻蚀速率影响的研究547下, S k 开始是随着U z 的增大而增大, 但U z 达到一定值后, S k 不再增加反而有所下降, 其原因是U z 增大时, 离子获得了较大的加速度, 由于轰击能量的增加, 因此对硅片曲解离子轰击的S k 也就提高了. 显然, 总体S k 较高, U z 过大, 即P j 过大, 会导致等离子体中离子壳层的厚度增大, 进而影响离子入射到硅片方向上的一致性. 这种由离子入射角产生的分散性使S k 降低, 尽管离子的轰击能量还在增加, 但总体的S k却发生了下降. 2. 3 q 对S k 的影响在P 为500W 、U z 分别为40、80、150和250V 时, S k 与SF 6的q 的关系如图3所示. 由图3可以看出, 在不同的U z 下, S k 开始随着SF 6的q 的增加而增大, 当达到最大值后, 却开始随着q 的增加而降低, 这是因为当q 刚开始增大时, 反应活性原子F 的自由基更新快, 且反应生成物SiF 4重新沉积的机会减少, 因此S k 会提高. 但是, 当q 过大时, 反应室中F 的自由基驻留时间短, 许多还没来得及参与反应就被真空泵抽走了, 因而导致了S k 的降低. 2. 4 P 对S k 的影响当U z 设定为150V 、SF 6的q 为50cm 3/s 时, S k 与P 的关系曲线如图4所示. 由图4可见, S k 随着P 的增大而增大, 这是因为P 越大, 产生的等离子体密度就越大, 那么会有更多的离子和F 的自由基用于刻蚀, 使S k 自然增大. 但是, 当P 增大时,图4 S k 与P 的关系图3 S k 与q 的关系曲线导致离子壳层的厚度增加, 使离子入射方向的一致性降低, 因此对S k 产生影响, 使S k 增大的趋势缓慢下来.2. 5 优化工艺参数由于检测手段的限制, 所以仅进行了简单的优化. 如果确定S k 为优化目标时, 其优化工艺参数为P =500V , U z =150V , q =50cm /s . 将SiO 2、Si 3N 4的选择比定为15, 则硅的S k 可达到0180L m/min.(1) 由以上讨论可知, 当反应室的压力、温度一定时, U z 、SF 6的q 和P 对S k 均有较大的影响. (2) 由于对硅的刻蚀是以SiO 2、Si 3N 4作掩蔽层, 因此在确定优化工艺参数时, 需要同时考虑对SiO 2、Si 3N 4的选择比. 又因为SiO 2、Si 3N 4的刻蚀主要是以离子轰击为主的刻蚀, 而硅主要是F 的化学图1 U z 与P j刻蚀, 因此在刻蚀工艺参数中, U z 不宜过大. 参考文献:[1] Chen K S, A y n Arturo A , Zhang X in, et al. Effect ofprocess par ameters o n the surface morphology and me -chanical perfo rmance of silicon structur es after deep reac -tive io n etching (DR IE)[J ].Jour nal of M icro -Elec -tromechanical Systems, 2002, 11(3) :264~274.。
ICP刻蚀工艺要点讲解

ICP刻蚀工艺要点讲解ICP(Inductively Coupled Plasma)刻蚀是一种常见的刻蚀技术,广泛应用于微电子器件制造中。
以下是对ICP刻蚀工艺要点的详细讲解,供参考。
1.ICP刻蚀原理:ICP刻蚀是利用高频激励电源产生电磁场,在反应室中形成等离子体,将基片表面产生化学反应的活性物质以离子的形式输送到基片表面,从而实现对基片表面进行刻蚀的过程。
ICP刻蚀的等离子体源通常采用偏压感应耦合状的圆锥状电极结构,通过加载高频电场,在反应室中形成高密度等离子体。
2.ICP刻蚀设备:ICP刻蚀设备由等离子体源、反应室和抽气系统等组成。
等离子体源通常采用二次加热结构,通过绕组在等离子体源周围产生交变磁场,从而使等离子体得以加热。
反应室主要是一个真空室,用于容纳等离子体和基片。
抽气系统则用于维持反应室的真空度。
3.ICP刻蚀气体选择:ICP刻蚀的气体选择是关键的一步。
常见的气体有氧气(O2)、氟化物(SF6、CF4等)和氯化物(Cl2等)。
不同气体具有不同的化学反应性质,可以实现对不同材料的刻蚀。
例如,氧气常用于氧化层的刻蚀,氟化物常用于硅基材料的刻蚀,而氯化物则常用于金属层的刻蚀。
4.ICP刻蚀参数调节:ICP刻蚀参数的调节对刻蚀结果具有重要影响。
主要参数包括功率、气体流量、工作压力和刻蚀时间等。
功率的大小决定了等离子体的密度,气体流量决定了刻蚀速率,工作压力则决定了气体的密度。
刻蚀时间取决于所需的刻蚀深度。
5.ICP刻蚀模板设计:6.ICP刻蚀优点:ICP刻蚀具有许多优点。
首先,ICP刻蚀具有较高的刻蚀速率,可用于制备较深的结构。
其次,ICP刻蚀能够实现较高的刻蚀选择比,能够实现高精度的刻蚀。
再次,ICP刻蚀对基片的损伤较小,能够保持较好的表面质量。
此外,ICP刻蚀工艺在刻蚀金属、绝缘体和半导体等材料时均具有良好的适应性。
7.ICP刻蚀应用:总结:ICP刻蚀是一种常见的微纳米加工技术,具有高刻蚀速率、高刻蚀选择比、低基片损伤等优点。
等离子体刻蚀中工艺参数对刻蚀速率影响的研究

等离子体刻蚀中工艺参数对刻蚀速率影响的研究在等离子体刻蚀(plasma etching)过程中,工艺参数的选取对刻蚀速率具有显著的影响。
本文将探讨等离子体刻蚀中几个常用的工艺参数,并分析其对刻蚀速率的影响。
首先,气体种类是刻蚀速率的重要因素之一、不同的气体种类具有不同的刻蚀特性,例如,氧气(O2)对有机材料具有很强的化学反应性,可以实现高速刻蚀,而氟化氢(HF)对硅材料具有较强的刻蚀特性。
因此,在等离子体刻蚀过程中选择适当的气体种类对于达到预期的刻蚀速率非常重要。
其次,气体流量是影响刻蚀速率的另一个重要参数。
增加气体流量会增加刻蚀速率,因为更多的气体分子参与反应过程。
然而,当气体流量超过一定范围时,过多的气体流量会导致过多的稀释效应,从而减缓刻蚀速率。
因此,合理选择气体流量可以提高刻蚀速率。
第三,加热温度对刻蚀速率也有显著影响。
增加加热温度可以提高刻蚀速率,因为提高温度可以增强化学反应速率,增加反应活性。
然而,当温度过高时,可能会导致样品的表面融化,甚至损坏样品。
因此,操作过程中需要控制好加热温度,以保证刻蚀速率的同时不损坏样品。
此外,等离子体功率也是影响刻蚀速率的重要因素。
增加等离子体功率可以增加刻蚀速率,因为提高功率可以增强等离子体中的电子能量,增加反应活性。
然而,当功率过高时,可能会导致样品表面的局部过热和损坏。
因此,在确定合适的功率时,需要综合考虑刻蚀速率和样品的热稳定性。
此外,还有一些其他的工艺参数,如气体压力、RF功率等也会对刻蚀速率产生影响。
因此,在具体的等离子体刻蚀过程中,需要根据实际需求和材料的特性来优化工艺参数,并进行合理的调整。
总之,等离子体刻蚀中的工艺参数对刻蚀速率具有显著的影响。
适当选择气体种类、气体流量、加热温度和等离子体功率等参数可以实现理想的刻蚀速率。
合理调整工艺参数可以提高刻蚀效率,实现高质量的刻蚀结果。
因此,对工艺参数与刻蚀速率之间的关系进行深入研究和分析,对于优化等离子体刻蚀过程具有重要意义。
o2等离子刻蚀 功率
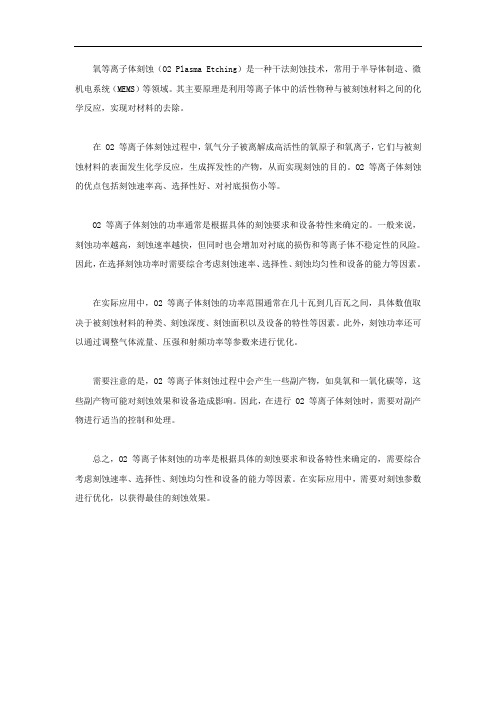
氧等离子体刻蚀(O2 Plasma Etching)是一种干法刻蚀技术,常用于半导体制造、微机电系统(MEMS)等领域。
其主要原理是利用等离子体中的活性物种与被刻蚀材料之间的化学反应,实现对材料的去除。
在 O2 等离子体刻蚀过程中,氧气分子被离解成高活性的氧原子和氧离子,它们与被刻蚀材料的表面发生化学反应,生成挥发性的产物,从而实现刻蚀的目的。
O2 等离子体刻蚀的优点包括刻蚀速率高、选择性好、对衬底损伤小等。
O2 等离子体刻蚀的功率通常是根据具体的刻蚀要求和设备特性来确定的。
一般来说,刻蚀功率越高,刻蚀速率越快,但同时也会增加对衬底的损伤和等离子体不稳定性的风险。
因此,在选择刻蚀功率时需要综合考虑刻蚀速率、选择性、刻蚀均匀性和设备的能力等因素。
在实际应用中,O2 等离子体刻蚀的功率范围通常在几十瓦到几百瓦之间,具体数值取决于被刻蚀材料的种类、刻蚀深度、刻蚀面积以及设备的特性等因素。
此外,刻蚀功率还可以通过调整气体流量、压强和射频功率等参数来进行优化。
需要注意的是,O2 等离子体刻蚀过程中会产生一些副产物,如臭氧和一氧化碳等,这些副产物可能对刻蚀效果和设备造成影响。
因此,在进行 O2 等离子体刻蚀时,需要对副产物进行适当的控制和处理。
总之,O2 等离子体刻蚀的功率是根据具体的刻蚀要求和设备特性来确定的,需要综合考虑刻蚀速率、选择性、刻蚀均匀性和设备的能力等因素。
在实际应用中,需要对刻蚀参数进行优化,以获得最佳的刻蚀效果。
等离子体刻蚀技术的操作指南与优化要点
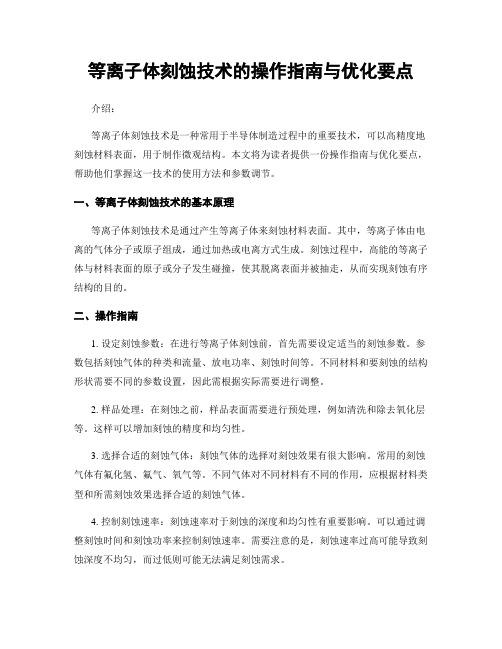
等离子体刻蚀技术的操作指南与优化要点介绍:等离子体刻蚀技术是一种常用于半导体制造过程中的重要技术,可以高精度地刻蚀材料表面,用于制作微观结构。
本文将为读者提供一份操作指南与优化要点,帮助他们掌握这一技术的使用方法和参数调节。
一、等离子体刻蚀技术的基本原理等离子体刻蚀技术是通过产生等离子体来刻蚀材料表面。
其中,等离子体由电离的气体分子或原子组成,通过加热或电离方式生成。
刻蚀过程中,高能的等离子体与材料表面的原子或分子发生碰撞,使其脱离表面并被抽走,从而实现刻蚀有序结构的目的。
二、操作指南1. 设定刻蚀参数:在进行等离子体刻蚀前,首先需要设定适当的刻蚀参数。
参数包括刻蚀气体的种类和流量、放电功率、刻蚀时间等。
不同材料和要刻蚀的结构形状需要不同的参数设置,因此需根据实际需要进行调整。
2. 样品处理:在刻蚀之前,样品表面需要进行预处理,例如清洗和除去氧化层等。
这样可以增加刻蚀的精度和均匀性。
3. 选择合适的刻蚀气体:刻蚀气体的选择对刻蚀效果有很大影响。
常用的刻蚀气体有氟化氢、氟气、氧气等。
不同气体对不同材料有不同的作用,应根据材料类型和所需刻蚀效果选择合适的刻蚀气体。
4. 控制刻蚀速率:刻蚀速率对于刻蚀的深度和均匀性有重要影响。
可以通过调整刻蚀时间和刻蚀功率来控制刻蚀速率。
需要注意的是,刻蚀速率过高可能导致刻蚀深度不均匀,而过低则可能无法满足刻蚀需求。
5. 监控刻蚀过程:在刻蚀过程中,应定期监控刻蚀深度和均匀性。
可以使用显微镜、扫描电镜等工具进行观察和测量,以调整刻蚀参数和纠正不均匀的情况。
6. 发现问题时的处理方法:在刻蚀过程中可能会出现一些问题,如表面残留物、刻蚀不均匀等。
处理方法可以是更换刻蚀气体、调整刻蚀参数或对样品进行再处理。
三、优化要点1. 材料选择:材料的选择直接影响刻蚀效果和刻蚀速率。
应根据具体需求选择合适的材料,例如对于硅基材料,可以选择氟化氢作为刻蚀气体。
2. 气体流量控制:气体流量对刻蚀效果和材料去除速率有直接影响。
等离子体蚀刻技术

等离子体蚀刻技术等离子体蚀刻技术是一种常用的微纳加工技术,广泛应用于半导体、光电子、微电子等领域。
本文将从等离子体蚀刻技术的基本原理、设备和工艺参数的选择以及应用领域等方面进行介绍。
一、等离子体蚀刻技术的基本原理等离子体蚀刻技术是利用高能粒子或分子束对材料表面进行刻蚀的一种方法。
其基本原理是通过在低压气体环境中产生等离子体,利用等离子体中的离子轰击材料表面,使其发生化学反应或物理过程,从而实现对材料表面的刻蚀。
等离子体蚀刻技术具有高精度、高选择性和高均匀性等优点,能够实现微纳米级的加工。
二、等离子体蚀刻设备等离子体蚀刻设备主要由气体供给系统、真空系统、射频功率源、电极系统以及控制系统等组成。
其中,气体供给系统用于提供刻蚀气体,真空系统用于提供蚀刻环境,射频功率源用于产生等离子体,电极系统用于加速和聚焦离子束,控制系统用于控制蚀刻过程的参数。
三、等离子体蚀刻工艺参数的选择等离子体蚀刻工艺参数的选择对于实现理想的加工效果至关重要。
其中,气体种类和流量、工作压力、射频功率和电极系统的设计等是需要考虑的关键因素。
不同材料的刻蚀速率和选择性不同,需要根据具体材料的特性和加工要求进行合理选择。
四、等离子体蚀刻的应用领域等离子体蚀刻技术在半导体、光电子、微电子等领域具有广泛的应用。
在半导体行业中,等离子体蚀刻技术常用于制备集成电路和光刻掩膜等工艺步骤。
在光电子领域,等离子体蚀刻技术可以用于制备光波导器件和微结构等。
在微电子领域,等离子体蚀刻技术可以用于制备微机械系统(MEMS)和纳米加工等。
等离子体蚀刻技术是一种重要的微纳加工技术,具有广泛的应用前景。
通过合理选择蚀刻工艺参数和设备设计,可以实现高精度、高选择性和高均匀性的加工效果。
随着科技的不断进步,相信等离子体蚀刻技术将在微纳加工领域发挥更加重要的作用。
等离子体刻蚀
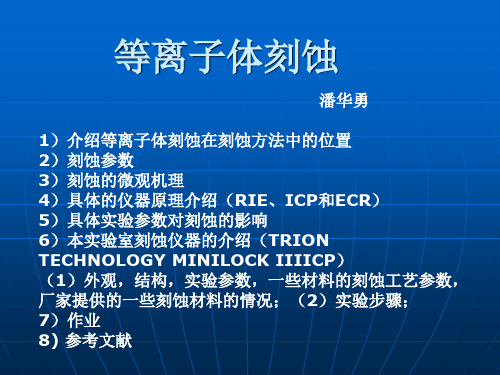
6 电极材料 电极包括阴极和阳极。要求阴极材料是化学惰性的,否则 被刻蚀,消耗反应物质,影响样品的刻蚀速率。 阳极与侧壁在离子的溅射下不会形成挥发性产物,而是将 溅射产物再沉积到其他表面, 包括样品材料表面, 影响 样品的进一步刻蚀。 即使材料本身是化学惰性的,样品材料在刻蚀过程中也会 因物理溅射,尤其是掩膜材料的溅射,将溅射物沉积到阳 极或反应室腔体内部。把这种环境带给下一次实验,“记 忆效应”。 为了尽量减少这种“交叉污染”,应尽量避免同一刻蚀系 统刻蚀多种不同材料,或者要求在每一次新的刻蚀前对反 应室腔体进行等离子体 “清洁”,即在未放样品前用氧 气或氩气对腔室体预刻蚀一段时间。
根据产生等离子体的方式又分为 ICP感性耦合等 离子体(inductively coupled plasma), CCP 容性耦合等离子体 (capacitively coupled plasma), ECR微波电子回旋共振等离子体 (microwave electron cyclotron resonance)。
物理加化学的过程 离子的溅射和解吸附的物理特性加上化学 反应特性,刻蚀速度大于单一的任何的单 一过程。
4)具体的仪器原理介绍(RIE、 ICP和ECR)
等离子放电刻蚀技术分类
根据使用离子的物理和化学的作用,可分为 反应离子刻蚀(reactive ion etch)(物理和化 学作用)、离子溅射刻蚀(物理作用)。
等离子体刻蚀
潘华勇 1)介绍等离子体刻蚀在刻蚀方法中的位置 2)刻蚀参数 3)刻蚀的微观机理 4)具体的仪器原理介绍(RIE、ICP和ECR) 5)具体实验参数对刻蚀的影响 6)本实验室刻蚀仪器的介绍(TRION TECHNOLOGY MINILOCK IIIICP) (1)外观,结构,实验参数,一些材料的刻蚀工艺参数, 厂家提供的一些刻蚀材料的情况;(2)实验步骤; 7)作业 8) 参考文献
ibe 刻蚀速率 刻蚀深度 工艺参数-概述说明以及解释

ibe 刻蚀速率刻蚀深度工艺参数-概述说明以及解释1.引言1.1 概述概述部分概述了本文的主要内容和目的。
本文主要介绍IBE(离子束刻蚀)技术中刻蚀速率和刻蚀深度的影响因素以及工艺参数对其的影响。
IBE是一种常用的表面加工技术,其通过使用离子束对材料进行刻蚀,可以用于微纳加工、半导体制造等领域。
刻蚀速率是IBE过程中一个重要的性能指标,它表示单位时间内刻蚀所能达到的深度,影响着刻蚀效率和加工质量。
本文将详细探讨刻蚀速率受离子束能量、角度、离子束流密度等因素的影响,并介绍相关实验方法和测量技术。
刻蚀深度的测量是判断刻蚀效果的重要手段,本文将介绍几种常用的刻蚀深度测量方法,如显微镜观察法、表面轮廓测量法等,并分析它们的优缺点以及适用范围。
此外,工艺参数作为IBE加工过程中的调控因素,对刻蚀速率和刻蚀深度有着重要的影响。
文章将研究不同工艺参数(如离子束能量、离子束流密度、刻蚀时间等)对刻蚀效果的影响,并提出相应的优化建议,以提高IBE技术的加工效率和加工质量。
通过本文的研究和分析,我们可以更全面地了解IBE技术中刻蚀速率和刻蚀深度的关系以及工艺参数的影响,为实际应用和工艺优化提供参考。
文章结构部分的内容可以参考以下写法:1.2 文章结构本文主要分为引言、正文和结论三个部分。
引言部分主要概述了IBE刻蚀速率、刻蚀深度以及相关的工艺参数的研究背景和意义。
正文部分包括了四个小节。
首先是IBE的介绍,介绍了IBE的基本原理和应用领域。
接着是刻蚀速率的影响因素,主要阐述了影响刻蚀速率的各种因素,如气体成分、压力、功率等。
然后是刻蚀深度的测量方法,详细介绍了几种常用的刻蚀深度测量方法以及其原理和应用。
最后是工艺参数对刻蚀速率和刻蚀深度的影响,主要探讨了不同工艺参数对IBE刻蚀速率和刻蚀深度的影响规律。
结论部分对刻蚀速率和刻蚀深度的关系进行了总结,并提出了对工艺参数的优化建议,以提高IBE的刻蚀效率和精度。
通过以上的文章结构,全面系统地介绍了IBE刻蚀速率、刻蚀深度和工艺参数的相关知识,为读者提供了一个较为清晰的学习框架。
等离子体刻蚀中工艺参数对刻蚀速率影响的研究

等离子体刻蚀中工艺参数对刻蚀速率影响的研究等离子体刻蚀是一种常用的微纳加工技术,广泛应用于半导体制造、显示器制造、光学器件制造等领域。
工艺参数对刻蚀速率的影响是等离子体刻蚀研究中的重要课题之一、本文将从放电功率、刻蚀气体流量和工作压强三个方面对工艺参数对刻蚀速率的影响进行探讨。
首先,放电功率是等离子体刻蚀的关键参数之一、放电功率的大小直接决定了等离子体的电子密度和电流密度,进而影响刻蚀速率。
一般来说,放电功率越大,等离子体的电子密度和电流密度越高,刻蚀速率越快。
然而,当放电功率过高时,等离子体的温度也会上升,导致局部过热和气体分解,从而影响刻蚀速率。
因此,放电功率的选择需要综合考虑等离子体的激发和湮灭过程,以及物料表面的稳定性。
其次,刻蚀气体流量是影响等离子体刻蚀速率的重要参数之一、刻蚀气体流量的增加会增加等离子体中活性粒子的浓度,从而提高刻蚀速率。
但是,当刻蚀气体流量过大时,等离子体中的活性粒子会稀释过多,导致刻蚀速率饱和或下降。
因此,刻蚀气体流量的选择要充分考虑等离子体中活性粒子的生成和扩散过程,以及刻蚀气体与物料之间的反应性。
最后,工作压强是等离子体刻蚀速率的重要参数之一、工作压强的增加会增加等离子体中粒子的碰撞频率,从而提高刻蚀速率。
但是,当工作压强过大时,等离子体中的粒子碰撞过于剧烈,容易造成物料表面的损伤和不均匀刻蚀。
因此,工作压强的选择需要在充分考虑刻蚀速率和表面质量之间的平衡。
综上所述,工艺参数对等离子体刻蚀速率有着重要的影响。
在实际应用中,需要根据具体的刻蚀对象和要求,综合考虑放电功率、刻蚀气体流量和工作压强等工艺参数,以实现理想的刻蚀效果。
未来的研究可以通过理论模拟和实验验证相结合的方法,深入探究不同工艺参数对刻蚀速率的影响机制,进一步优化等离子体刻蚀工艺,提高刻蚀效率和表面质量。
等离子体刻蚀机使用说明书

等离子体刻蚀机使用说明书【使用说明书】等离子体刻蚀机(最新版)第一部分:简介1.1产品概述本产品是一种使用等离子体技术进行刻蚀的专用设备,广泛应用于半导体、光电子、微纳加工等领域。
本产品结构紧凑、操作简单、稳定可靠,适用于各种规格的衬底材料。
1.2主要特点(1)采用高频等离子体生成系统,能够产生高浓度的等离子体,提高刻蚀效率;(2)设备中配备了多种腐蚀和刻蚀气体,满足不同材料的刻蚀需求;(3)具备自动控制系统,实现精确的刻蚀参数设定和控制;(4)设备外壳采用防腐蚀材料制作,确保设备长期稳定的工作;(5)设备具备自动清洗功能,方便用户进行日常维护。
第二部分:安装与调试2.1安装(1)将设备放置在通风良好的地方;(2)将设备连接至电源,并确保电源接地可靠;(3)连接进气管道,确保刻蚀气体供应正常;(4)确保设备周围环境无振动和灰尘。
2.2调试(1)打开设备电源,确保设备正常启动;(2)检查刻蚀气体供应是否正常并按需设定气体流量;(3)按照刻蚀材料的要求设定刻蚀参数,如功率、时间等;(4)开始刻蚀,观察刻蚀结果并根据需求调整参数;(5)在设备切换或维护前,先关闭电源,并等待设备冷却后再进行操作。
第三部分:操作说明3.1设备界面设备界面包括显示屏、按键、控制面板等。
显示屏显示当前设备状态和刻蚀参数设定,按键用于选择和调整参数,控制面板用于启动和停止设备等。
3.2参数设定(1)使用方向键选择需要设定的参数;(2)使用增减键调整参数值;(3)按下确认键保存设定值。
3.3刻蚀操作(1)将待刻蚀样品放置在夹持台上,并调整位置;(2)打开气源,确保刻蚀气体正常供应;(3)设定刻蚀参数,确保设定值符合实际需求;(4)开始刻蚀,观察刻蚀过程中的参数波动;(5)刻蚀完成后关闭设备,等待设备冷却后取出样品。
第四部分:维护与保养4.1日常维护(1)定期清洁设备外壳,以防止腐蚀和灰尘积累;(2)检查气源管道和阀门是否正常,定期更换损坏或老化的部件;(3)检查设备接地是否可靠,防止静电积累;(4)定期检查刻蚀参数和设备状态,确保设备正常工作。
IPC刻蚀机介绍
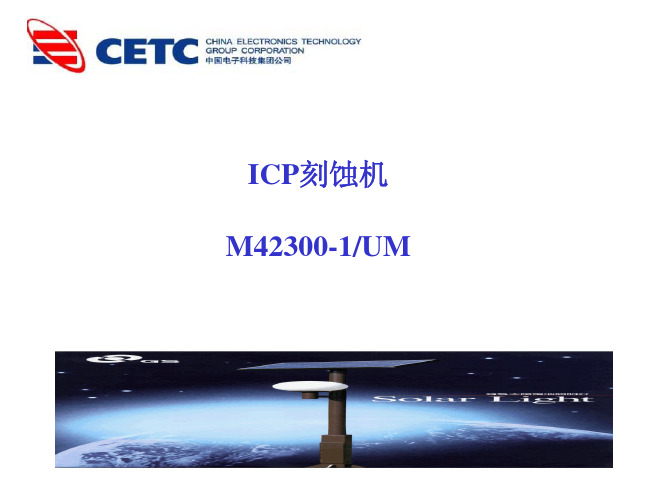
原理框图 elements diagram
片夹及工装
采用自定位片夹, 硅片直接插入片夹中的 两个限位条之间,在限 位条的作用下,硅片自 动对准,保证各硅片对 齐,然后用上端螺杆通 过滑块将硅片压紧。
产地 1 1 1 1 1 1 4 2 2 1 1 1
数量
1
1 1 1 1 1 2 1
五、刻蚀机对比
指标 刻蚀介质 刻蚀部位 射频电源 匹配网络 气路系统 抽气系统 载片架 装片量 批间时间 刻蚀均匀性 电源 抗干扰性 一条25MW线需配备量 维护周期 传统刻蚀机 掺杂硅、氮化硅 5”,6”方片周边 国产13.56MHZ ,100~1000W 连续可调 手动调节 手动、1 路浮子流量计,2 路质量流量计 2X-15 机械泵,工作压力自动控制 旋转,转速10rpm 300片/批 25min ±5% 3N, 380V,50HZ,5KVA 差 3台 1周 ICP刻蚀机 掺杂硅、氮化硅 5”,6”方片周边 进口13.56MHZ ,100~1000W 连续可调 自动调节 手动、2 路浮子流量计, 2 路质量流量计 进口90m3/h干式泵,工作压力自动控制 旋转,转速0-10rpm可调 800片/批 25min ±5% 3N, 380V,50HZ,5KVA 好 1台 24周 备注
整机布置图
整机布局图
四、主要配置
序号 1 2 3 4 5 6 7 8 9 10 11 12 13 14 15 16 17 18 19 20
名称 主机架、反应室等加工件 耦合石英窗 RF电源 射频匹配器 PLC显示器 PLC模块 气路电磁阀1/4” 质量流量计 浮子流量计 电气动挡板阀 电磁阀DN10 压控仪 蝶阀 电子执行器 薄膜规 真空泵机组 电机 调速器 同步轮 同步带 48所 进口 进口 进口 进口 进口 进口 进口 国产 合资 合资 国产 国产 国产 进口 进口 国产 国产 国产 国产
等离子体刻蚀中工艺参数对刻蚀速率影响的研究
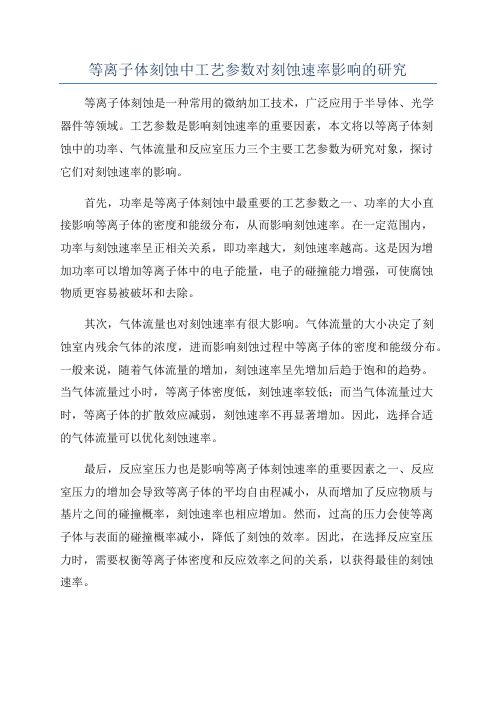
等离子体刻蚀中工艺参数对刻蚀速率影响的研究等离子体刻蚀是一种常用的微纳加工技术,广泛应用于半导体、光学器件等领域。
工艺参数是影响刻蚀速率的重要因素,本文将以等离子体刻蚀中的功率、气体流量和反应室压力三个主要工艺参数为研究对象,探讨它们对刻蚀速率的影响。
首先,功率是等离子体刻蚀中最重要的工艺参数之一、功率的大小直接影响等离子体的密度和能级分布,从而影响刻蚀速率。
在一定范围内,功率与刻蚀速率呈正相关关系,即功率越大,刻蚀速率越高。
这是因为增加功率可以增加等离子体中的电子能量,电子的碰撞能力增强,可使腐蚀物质更容易被破坏和去除。
其次,气体流量也对刻蚀速率有很大影响。
气体流量的大小决定了刻蚀室内残余气体的浓度,进而影响刻蚀过程中等离子体的密度和能级分布。
一般来说,随着气体流量的增加,刻蚀速率呈先增加后趋于饱和的趋势。
当气体流量过小时,等离子体密度低,刻蚀速率较低;而当气体流量过大时,等离子体的扩散效应减弱,刻蚀速率不再显著增加。
因此,选择合适的气体流量可以优化刻蚀速率。
最后,反应室压力也是影响等离子体刻蚀速率的重要因素之一、反应室压力的增加会导致等离子体的平均自由程减小,从而增加了反应物质与基片之间的碰撞概率,刻蚀速率也相应增加。
然而,过高的压力会使等离子体与表面的碰撞概率减小,降低了刻蚀的效率。
因此,在选择反应室压力时,需要权衡等离子体密度和反应效率之间的关系,以获得最佳的刻蚀速率。
综上所述,功率、气体流量和反应室压力是等离子体刻蚀中常见的关键工艺参数,它们对刻蚀速率都有着显著的影响。
研究发现,在一定范围内,增加功率和气体流量可以提高刻蚀速率,而增加反应室压力可以增加碰撞概率,从而提高刻蚀效率。
但是,需要注意的是,不同的刻蚀目标材料、刻蚀模式和刻蚀设备都可能对这些影响因素有所不同,因此在具体应用中需要进行实验验证和参数优化。
- 1、下载文档前请自行甄别文档内容的完整性,平台不提供额外的编辑、内容补充、找答案等附加服务。
- 2、"仅部分预览"的文档,不可在线预览部分如存在完整性等问题,可反馈申请退款(可完整预览的文档不适用该条件!)。
- 3、如文档侵犯您的权益,请联系客服反馈,我们会尽快为您处理(人工客服工作时间:9:00-18:30)。
磁控溅射台技术参数
一、设备名称:磁控溅射台
二、采购数量:1台
三、技术参数及配置要求:
1.真空室:不锈钢真空室
2.极限真空:6.7×10-5 Pa(环境湿度≤55%);
3.真空室漏气率:≤5.0×10-7 Pa•L/s;
4.抽气速率:系统短时间暴露大气并充干燥N2开始抽气,溅射室30分钟可达到9.0×10-4 Pa;
5.真空室保压:系统停泵关机12小时后真空度:≤5Pa;
6.溅射材料:至少3inch向下兼容;各种金属、合金、化合物、陶瓷、超导、铁磁、铁电、热电、磁性材料薄膜
7.溅射靶:Φ60mm可弯曲磁控溅射靶三只(其中一只为强磁靶),上置安装,靶基距6~10cm范围内可调;
8.溅射不均匀性:≤±5%(共溅工位Φ75mm范围内,直溅工位Φ37.5mm范围内)
9.溅射室规格:内空容量≥0.1m3
10工件台旋转:中心工位自转,转速5~30rpm可调,
11样品加热:样品衬底可加热,共溅加热温度≥600℃,直溅三工位加热温度均达到≥400℃,多段控温模式,控温精度±1%,
12.载片量:Φ75mm 样片一片。
13.高效实验模式。
一炉可以完成不少于3次的相互无污染的独立工艺试验。
14.进口射频电源:600W,一台。
15.进口直流电源,1000W,一台。
16.偏压电源,一台。
17.质量流量控制器2台,气路三条Ar、O2、N2,并提供气体Ar、O2、N2各一瓶,以及相关减压阀。
18.复合分子泵,600升/秒,设备选用不低于中科科仪产品。
19.外企生产机械泵:8升/秒,设备选用不低于日本真空独资宁波爱发科产品。
20.超高真空插板阀。
21.自动压力控制系统,配套进口规管。
22.全自动控制系统,包括进口控制模块、工控机、控制软件。
23.配套循环冷却水机、静音空气压缩机。
24. 配套靶材7种:Al、Cu、Cr、Ti、Si、SiO2、Au(其中靶材Au为Φ60mm*3mm,纯度不低于99.99%,其他6种为Φ60mm*5mm,高纯)。
四、安装、售后及培训:
1、交货期:合同正式生效后30天内到货。
2、质保期:自验收之日起,仪器设备至少免费保修三年。
3、包含该设备运输,上楼搬运,所需气路实验室内部铺设。
仪器安装、验收:专业工程师提供免费的安装调试,并按照出厂指标验收。
4、培训:免费提供该仪器设备培训;提供本设备全套操作教学视频。