等离子刻蚀的基本原理
ICP刻蚀工艺要点讲解

ICP刻蚀工艺要点讲解ICP(Inductively Coupled Plasma)刻蚀是一种常见的刻蚀技术,广泛应用于微电子器件制造中。
以下是对ICP刻蚀工艺要点的详细讲解,供参考。
1.ICP刻蚀原理:ICP刻蚀是利用高频激励电源产生电磁场,在反应室中形成等离子体,将基片表面产生化学反应的活性物质以离子的形式输送到基片表面,从而实现对基片表面进行刻蚀的过程。
ICP刻蚀的等离子体源通常采用偏压感应耦合状的圆锥状电极结构,通过加载高频电场,在反应室中形成高密度等离子体。
2.ICP刻蚀设备:ICP刻蚀设备由等离子体源、反应室和抽气系统等组成。
等离子体源通常采用二次加热结构,通过绕组在等离子体源周围产生交变磁场,从而使等离子体得以加热。
反应室主要是一个真空室,用于容纳等离子体和基片。
抽气系统则用于维持反应室的真空度。
3.ICP刻蚀气体选择:ICP刻蚀的气体选择是关键的一步。
常见的气体有氧气(O2)、氟化物(SF6、CF4等)和氯化物(Cl2等)。
不同气体具有不同的化学反应性质,可以实现对不同材料的刻蚀。
例如,氧气常用于氧化层的刻蚀,氟化物常用于硅基材料的刻蚀,而氯化物则常用于金属层的刻蚀。
4.ICP刻蚀参数调节:ICP刻蚀参数的调节对刻蚀结果具有重要影响。
主要参数包括功率、气体流量、工作压力和刻蚀时间等。
功率的大小决定了等离子体的密度,气体流量决定了刻蚀速率,工作压力则决定了气体的密度。
刻蚀时间取决于所需的刻蚀深度。
5.ICP刻蚀模板设计:6.ICP刻蚀优点:ICP刻蚀具有许多优点。
首先,ICP刻蚀具有较高的刻蚀速率,可用于制备较深的结构。
其次,ICP刻蚀能够实现较高的刻蚀选择比,能够实现高精度的刻蚀。
再次,ICP刻蚀对基片的损伤较小,能够保持较好的表面质量。
此外,ICP刻蚀工艺在刻蚀金属、绝缘体和半导体等材料时均具有良好的适应性。
7.ICP刻蚀应用:总结:ICP刻蚀是一种常见的微纳米加工技术,具有高刻蚀速率、高刻蚀选择比、低基片损伤等优点。
o2等离子刻蚀 功率
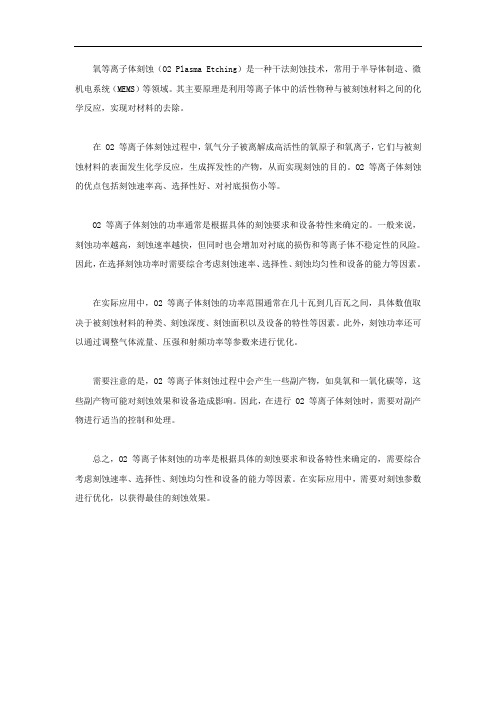
氧等离子体刻蚀(O2 Plasma Etching)是一种干法刻蚀技术,常用于半导体制造、微机电系统(MEMS)等领域。
其主要原理是利用等离子体中的活性物种与被刻蚀材料之间的化学反应,实现对材料的去除。
在 O2 等离子体刻蚀过程中,氧气分子被离解成高活性的氧原子和氧离子,它们与被刻蚀材料的表面发生化学反应,生成挥发性的产物,从而实现刻蚀的目的。
O2 等离子体刻蚀的优点包括刻蚀速率高、选择性好、对衬底损伤小等。
O2 等离子体刻蚀的功率通常是根据具体的刻蚀要求和设备特性来确定的。
一般来说,刻蚀功率越高,刻蚀速率越快,但同时也会增加对衬底的损伤和等离子体不稳定性的风险。
因此,在选择刻蚀功率时需要综合考虑刻蚀速率、选择性、刻蚀均匀性和设备的能力等因素。
在实际应用中,O2 等离子体刻蚀的功率范围通常在几十瓦到几百瓦之间,具体数值取决于被刻蚀材料的种类、刻蚀深度、刻蚀面积以及设备的特性等因素。
此外,刻蚀功率还可以通过调整气体流量、压强和射频功率等参数来进行优化。
需要注意的是,O2 等离子体刻蚀过程中会产生一些副产物,如臭氧和一氧化碳等,这些副产物可能对刻蚀效果和设备造成影响。
因此,在进行 O2 等离子体刻蚀时,需要对副产物进行适当的控制和处理。
总之,O2 等离子体刻蚀的功率是根据具体的刻蚀要求和设备特性来确定的,需要综合考虑刻蚀速率、选择性、刻蚀均匀性和设备的能力等因素。
在实际应用中,需要对刻蚀参数进行优化,以获得最佳的刻蚀效果。
电感耦合等离子体刻蚀和离子束刻蚀的区别
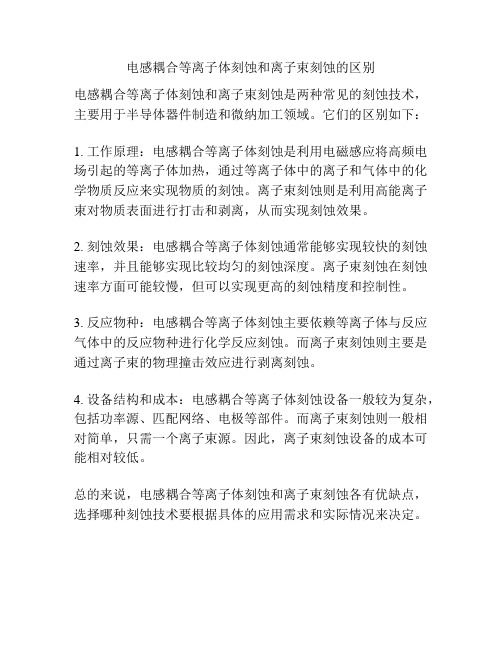
电感耦合等离子体刻蚀和离子束刻蚀的区别
电感耦合等离子体刻蚀和离子束刻蚀是两种常见的刻蚀技术,主要用于半导体器件制造和微纳加工领域。
它们的区别如下:
1. 工作原理:电感耦合等离子体刻蚀是利用电磁感应将高频电场引起的等离子体加热,通过等离子体中的离子和气体中的化学物质反应来实现物质的刻蚀。
离子束刻蚀则是利用高能离子束对物质表面进行打击和剥离,从而实现刻蚀效果。
2. 刻蚀效果:电感耦合等离子体刻蚀通常能够实现较快的刻蚀速率,并且能够实现比较均匀的刻蚀深度。
离子束刻蚀在刻蚀速率方面可能较慢,但可以实现更高的刻蚀精度和控制性。
3. 反应物种:电感耦合等离子体刻蚀主要依赖等离子体与反应气体中的反应物种进行化学反应刻蚀。
而离子束刻蚀则主要是通过离子束的物理撞击效应进行剥离刻蚀。
4. 设备结构和成本:电感耦合等离子体刻蚀设备一般较为复杂,包括功率源、匹配网络、电极等部件。
而离子束刻蚀则一般相对简单,只需一个离子束源。
因此,离子束刻蚀设备的成本可能相对较低。
总的来说,电感耦合等离子体刻蚀和离子束刻蚀各有优缺点,选择哪种刻蚀技术要根据具体的应用需求和实际情况来决定。
0 等离子刻蚀工艺原理介绍

Feed Gases
BCl3/Cl2 HBr/Cl2
Comments
Cl etches Si, B improves passivation HBr provides passiviation and selectivity to PR, Cl2 providdes main etchants O2 improves selectivity to SiO2 Higher etch rate, good oxide selectivity, isotropic High etch rate, but isotropic Good profile control for deep trench
--- Process Time
工艺控制和结果
工艺可控变量 Plasma 参数 结果
Temperature Gas Flows
Gas density Residence time
Etch Rate Uniformity Selectivity
Pressure
Power Time (Magnetic Field) BSC He (Gap)
Bias 功率的作用: 离子能量
功率 --> 控制离子浓度/能量。提高 Bias 功率,提高腐蚀速率。
Bias 低离子能量
--> 低的碰撞速度。
离子能量影响方向性
--> 高离子能量意 味着离子更少偏离原来运动方向。
问答
Q&A
HBr/Cl2/O2 SF6 NF3 HBr/NF3/O2
Metal Etch平衡图
物理
离子轰击
BCl3+
化学腐蚀
Cl*
化学淀积
刻蚀常见异常培训

等离子刻蚀的作用:
去除太阳能电池的周边结,扩散工艺中在硅片的上表面和周边都扩散上了N型结,如果不 去除周边的N型结会导致电池片正负极被周边的N型结联接起来,使电池正负极接通,起不到 电池的作用了。
等离子刻蚀机介绍(外观)
捷佳创刻蚀机
七星刻蚀机
等离子刻蚀机介绍(反应室)
捷佳创刻蚀机:
反应室里面是石英缸,外面是线圈, 线圈在高频电的激发下起辉放电,激发石 英缸内的特气进行反应,生成活性离子基。
送工艺气体,当压力稳定在设定值时开高频辉光放电,关高频,关工艺气体,送氮气,充 气开盖,取片,放片,开始新的工艺“(或抽空停机)。
工艺流程框图: 装片 运行开 预抽 尾气 主抽 送气(CF4 O2)稀释
取片
运行关
充气
清洗
高频辉光
等离子刻蚀效果检测:
热探针和N型半导体接触时,传导电子将流 向温度较低的区域,使得热探针处电子缺 少,因而其电势相对于同一材料上的室温 触点而言将是正的;
刻蚀白圈处理方法:
I. 出现刻蚀白圈立即空刻观察刻蚀机仓体是否异常或督查生产操作是否有误,若发现该机台异常
立即通知生产人员空刻2次,无异常情况则复机生产;
II. 对已产生的刻蚀白圈片由生产通知质量部判别是否下传,并对当班出现的刻蚀白圈进行仔细 统计;
刻蚀机的保养和安全保护事项:
1. 使用环境 温度5℃-40℃,湿度<70%,净化等级优于万级。
同样道理,P型半导体热探针触点相对于室温触点而言将是负的; 此电势差可以用简单的微伏表测量; 热探针的结构可以是将小的热线圈绕在一个探针的周围,也可以用小型的电烙铁;
检查手法见《PN型检测SOP》。
刻蚀异常处理流程:
等离子刻蚀原理

等离子刻蚀原理
等离子刻蚀是一种常用的微纳加工技术,用于在半导体制造中去除杂质、形成纳米结构以及精确地刻蚀表面。
其原理基于等离子体(即带正电荷的高能离子和自由电子)与被刻蚀材料表面发生相互作用。
在等离子刻蚀过程中,首先需要产生等离子体。
这通常是通过将高纯度的气体(如氯气、氟气、苦味气等)引入到封闭的真空室中,并在高能电场和电弧场下对气体进行激发。
这种激发将气体分解成离子和电子,并形成带电的等离子体。
然后,这些带电的等离子体会被加速,并通过电场和磁场的调控,使其定向地撞击到待刻蚀材料表面。
撞击过程中,离子会传递给待刻蚀材料表面一部分能量,并激发该材料表面原子或分子的束缚电子。
这些激发的表面原子或分子可能会离开其原子或分子固定位置,形成反应产物,然后通过扩散和抛射的方式迁移到其他位置。
与此同时,撞击后的原子或分子释放出来的电子也会在等离子体中传递,并参与到一系列的电子和离子反应中。
这些反应将控制刻蚀速度、形状、深度和表面粗糙度等参数。
此外,通过调节激发条件、等离子体密度、控制气体的种类和流量等因素,可以对刻蚀过程进行精确控制,实现不同的刻蚀效果和图形。
总的来说,等离子刻蚀原理是利用带电的等离子体与待刻蚀材料表面相互作用,通过离子和电子的传递和相互反应,实现对
材料表面的精确刻蚀。
这种技术在半导体制造、光学器件制造和微纳加工领域具有广泛的应用。
等离子体刻蚀反应离子刻蚀
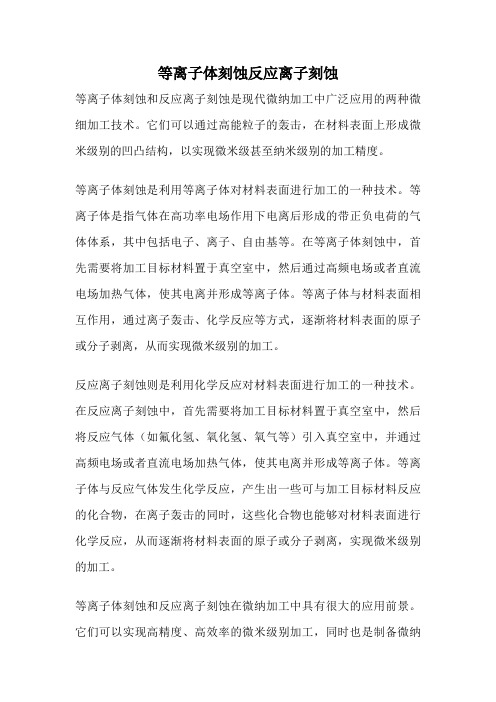
等离子体刻蚀反应离子刻蚀
等离子体刻蚀和反应离子刻蚀是现代微纳加工中广泛应用的两种微细加工技术。
它们可以通过高能粒子的轰击,在材料表面上形成微米级别的凹凸结构,以实现微米级甚至纳米级别的加工精度。
等离子体刻蚀是利用等离子体对材料表面进行加工的一种技术。
等离子体是指气体在高功率电场作用下电离后形成的带正负电荷的气体体系,其中包括电子、离子、自由基等。
在等离子体刻蚀中,首先需要将加工目标材料置于真空室中,然后通过高频电场或者直流电场加热气体,使其电离并形成等离子体。
等离子体与材料表面相互作用,通过离子轰击、化学反应等方式,逐渐将材料表面的原子或分子剥离,从而实现微米级别的加工。
反应离子刻蚀则是利用化学反应对材料表面进行加工的一种技术。
在反应离子刻蚀中,首先需要将加工目标材料置于真空室中,然后将反应气体(如氟化氢、氧化氢、氧气等)引入真空室中,并通过高频电场或者直流电场加热气体,使其电离并形成等离子体。
等离子体与反应气体发生化学反应,产生出一些可与加工目标材料反应的化合物,在离子轰击的同时,这些化合物也能够对材料表面进行化学反应,从而逐渐将材料表面的原子或分子剥离,实现微米级别的加工。
等离子体刻蚀和反应离子刻蚀在微纳加工中具有很大的应用前景。
它们可以实现高精度、高效率的微米级别加工,同时也是制备微纳
器件的重要工艺之一。
比如,在集成电路、光学器件、生物芯片等领域,等离子体刻蚀和反应离子刻蚀被广泛应用,为微纳加工提供了可靠的技术支持。
等离子体刻蚀和反应离子刻蚀是现代微纳加工中不可或缺的两种技术。
它们通过高能粒子的轰击和化学反应,实现了微米级别的加工精度,为微纳器件制备提供了有效的技术支持。
等离子体蚀刻技术

等离子体蚀刻技术等离子体蚀刻技术是一种常用的微纳加工技术,广泛应用于半导体、光电子、微电子等领域。
本文将从等离子体蚀刻技术的基本原理、设备和工艺参数的选择以及应用领域等方面进行介绍。
一、等离子体蚀刻技术的基本原理等离子体蚀刻技术是利用高能粒子或分子束对材料表面进行刻蚀的一种方法。
其基本原理是通过在低压气体环境中产生等离子体,利用等离子体中的离子轰击材料表面,使其发生化学反应或物理过程,从而实现对材料表面的刻蚀。
等离子体蚀刻技术具有高精度、高选择性和高均匀性等优点,能够实现微纳米级的加工。
二、等离子体蚀刻设备等离子体蚀刻设备主要由气体供给系统、真空系统、射频功率源、电极系统以及控制系统等组成。
其中,气体供给系统用于提供刻蚀气体,真空系统用于提供蚀刻环境,射频功率源用于产生等离子体,电极系统用于加速和聚焦离子束,控制系统用于控制蚀刻过程的参数。
三、等离子体蚀刻工艺参数的选择等离子体蚀刻工艺参数的选择对于实现理想的加工效果至关重要。
其中,气体种类和流量、工作压力、射频功率和电极系统的设计等是需要考虑的关键因素。
不同材料的刻蚀速率和选择性不同,需要根据具体材料的特性和加工要求进行合理选择。
四、等离子体蚀刻的应用领域等离子体蚀刻技术在半导体、光电子、微电子等领域具有广泛的应用。
在半导体行业中,等离子体蚀刻技术常用于制备集成电路和光刻掩膜等工艺步骤。
在光电子领域,等离子体蚀刻技术可以用于制备光波导器件和微结构等。
在微电子领域,等离子体蚀刻技术可以用于制备微机械系统(MEMS)和纳米加工等。
等离子体蚀刻技术是一种重要的微纳加工技术,具有广泛的应用前景。
通过合理选择蚀刻工艺参数和设备设计,可以实现高精度、高选择性和高均匀性的加工效果。
随着科技的不断进步,相信等离子体蚀刻技术将在微纳加工领域发挥更加重要的作用。
等离子体刻蚀机原理

等离子体刻蚀机原理什么是等离子体?▪随着温度的升高,一般物质依次表现为固体、液体和气体。
它们统称为物质的三态。
▪当气体的温度进一步升高时,其中许多,甚至全部分子或原子将由于激烈的相互碰撞而离解为电子和正离子。
这时物质将进入一种新的状态,即主要由电子和正离子(或是带正电的核)组成的状态。
这种状态的物质叫等离子体。
它可以称为物质的第四态。
等离子体的应用等离子体的应用等离子体的产生等离子体刻蚀原理▪等离子体刻蚀是采用高频辉光放电反应,使反应气体激活成活性粒子,如原子或游离基,这些活性粒子扩散到需刻蚀的部位,在那里与被刻蚀材料进行反应,形成挥发性反应物而被去除。
▪这种腐蚀方法也叫做干法腐蚀。
等离子体刻蚀反应▪首先,母体分子CF4在高能量的电子的碰撞作用下分解成多种中性基团或离子。
CF4→CF3,CF2,CF,C,F▪其次,这些活性粒子由于扩散或者在电场作用下到达SiO2表面,并在表面上发生化学反应。
▪生产过程中,在CF4中掺入O2,这样有利于提高Si和SiO2的刻蚀速率。
等离子体刻蚀工艺▪装片在待刻蚀硅片的两边,分别放置一片与硅片同样大小的玻璃夹板,叠放整齐,用夹具夹紧,确保待刻蚀的硅片中间没有大的缝隙。
将夹具平稳放入反应室的支架上,关好反应室的盖子。
检验方法▪冷热探针法检验原理▪热探针和N型半导体接触时,传导电子将流向温度较低的区域,使得热探针处电子缺少,因而其电势相对于同一材料上的室温触点而言将是正的。
▪同样道理,P型半导体热探针触点相对于室温触点而言将是负的。
▪此电势差可以用简单的微伏表测量。
▪热探针的结构可以是将小的热线圈绕在一个探针的周围,也可以用小型的电烙铁。
检验操作及判断•确认万用表工作正常,量程置于200mV。
•冷探针连接电压表的正电极,热探针与电压表的负极相连。
•用冷、热探针接触硅片一个边沿不相连的两个点,电压表显示这两点间的电压为负值,说明导电类型为p,刻蚀合格。
相同的方法检测另外三个边沿的导电类型是否为p型。
等离子刻蚀工艺原理介绍

-------+- -+- +- -+ -+- +-
+
•射频功率通过隔直电容加到圆片背面,这样隔离直流
而能通过射频,使圆片和基座充电为负偏压状态(平均).
整理课件
5
圆片偏压的产生-1
• 非对称的腔体中,圆片面积<<腔体面积, 所以较高 的鞘层/暗区(Sheath/Dark Space)电压出现在Plasma到 圆片之间。
等离子刻蚀工艺原理介绍
Etch/CSMC 2011.10.14
整理课件
1
概述
等离子刻蚀工艺原理介绍包含以下几个方面:
• 等离子体基本概念 • 等离子刻蚀基本原理 • 等离子Plasma
• Plasma就是等离子体(台湾一般称为电浆), 由气体电 离后产生的正负带电离子以及分子, 原子和原子团组 成. 只有强电场作用下雪崩电离发生时, Plasma才会产 生.
time
heavy ions decay voltage slowly
plasma potential
整理课件
time wafer voltage
v2 v1
7
Plasma刻蚀中的功率耦合 • 电容耦合: RF功率通过RF电场直接传导到Plasma,涉 及到的电极也直接暴露在Plasma中(但是一般有Wafer 在基座/电极上).
STEP 2. 活性粒子扩散到反应膜层附近
STEP 3. 活性粒子被表面吸附
STEP 4. 反应发生
STEP 5. 反应生成物能解吸附
STEP 6. 反应生成物扩散整到理气课件体当中被泵抽走
icp刻蚀工艺技术

icp刻蚀工艺技术ICP(Inductively Coupled Plasma)刻蚀工艺是一种利用感应耦合等离子体进行化学气相刻蚀的技术。
该技术能够实现高精度、高均匀度的刻蚀,已广泛应用于半导体、光电子、纳米材料等领域。
下面将介绍ICP刻蚀工艺的基本原理及其应用。
ICP刻蚀工艺是利用高频电场感应在低压气体中产生的高温等离子体对材料进行刻蚀。
工艺流程一般包括预处理、腐蚀、刻蚀等几个步骤。
首先,在预处理阶段,将待刻蚀的样品进行清洗,去除表面的污染物和氧化层,以保证刻蚀的质量和精度。
然后,在腐蚀阶段,将样品放置在腐蚀室中,通过辅助电源提供电场,使得样品表面均匀地被腐蚀,形成蚀刻层。
最后,在刻蚀阶段,通过改变气体组分、功率密度等参数,控制蚀刻速率和刻蚀深度,实现对样品的精确刻蚀。
ICP刻蚀工艺具有许多优点。
首先,由于高能量等离子体的使用,ICP刻蚀能够实现更深和更均匀的蚀刻深度,刻蚀速率高。
其次,在刻蚀过程中,等离子体对样品的表面进行蚀刻,从而形成良好的刻蚀质量和表面平整度。
此外,ICP刻蚀操作简单,可以进行批量生产,提高生产效率。
ICP刻蚀工艺在各个领域都有广泛的应用。
首先,在集成电路制造中,ICP刻蚀工艺可以用于制备光刻掩膜、图案转移、开窗等工艺步骤,实现半导体器件的精细加工。
其次,在光电子器件制造中,ICP刻蚀工艺可以用于制备光栅、波导等光学元件,提高器件的性能和稳定性。
此外,ICP刻蚀工艺还被广泛应用于纳米材料的制备和研究中,可以实现对纳米结构的精细刻蚀。
然而,ICP刻蚀工艺也存在一些问题。
首先,等离子体的高温和高能量可能会导致材料的损伤和变形,降低器件性能。
其次,刻蚀过程中产生的副产物和气体可能会对设备和环境造成污染和损害。
综上所述,ICP刻蚀工艺是一种高精度、高均匀度的刻蚀技术,广泛应用于半导体、光电子、纳米材料等领域。
随着对器件制备和研究要求的不断提高,ICP刻蚀工艺将会得到更广泛的应用和发展。
等离子体刻蚀发展史

等离子体刻蚀发展史等离子体刻蚀是一种重要的微纳加工技术,广泛应用于集成电路、显示器、MEMS器件等领域。
它的基本原理是将反应气体电离成等离子体,在强电场的作用下将表面物质去除。
下面我们来看一下等离子体刻蚀的发展历程。
20世纪60年代末期,等离子体刻蚀开始应用于半导体微电子领域。
最初的等离子体刻蚀是在高真空条件下使用电容放电的方法,称为电容放电等离子体刻蚀(CDE)。
这种方法虽然简单易行,但是存在一些问题,如功率因素低、能耗大、放电条纹等,使得其应用受到限制。
70年代初期,出现了射频(RF)感应等离子体刻蚀,可以大大改善电容放电等离子体刻蚀的问题。
射频感应等离子体刻蚀是通过射频电场激发气体分子而形成等离子体的刻蚀方法。
这种方法具有刻蚀速率高、平稳性好、占用面积小等优点,成为当时半导体微电子领域主要的刻蚀方法。
80年代初期,随着对微电子集成度和性能的要求越来越高,传统的射频感应等离子体刻蚀已经不能满足需求。
此时出现了电子回旋共振(ECR)等离子体刻蚀,ECR能够在相对低的压力下形成高浓度等离子体,刻蚀效率高、刻蚀精度高,是高精度微纳加工的重要工具之一。
90年代初期,出现了另一种新的等离子体刻蚀方法——电子束等离子体刻蚀(EBP),可以实现更高的刻蚀精度和面积选择性。
EBP通过在氩气等离子体中激发出高能电子束,使表面的物质离子化并从表面脱离,实现表面刻蚀。
这种方法被广泛应用于集成电路的制造过程中。
20世纪90年代中期,出现了另外一种新的等离子体刻蚀技术——电磁共振等离子体刻蚀(ICP)。
ICP利用外部磁场使等离子体在容器中旋转,增加反应物的输运速率,提高反应速率、刻蚀效率和精度,并可用于多种材料的刻蚀,被广泛应用于半导体、MEMS和纳米加工。
总而言之,随着等离子体刻蚀技术的不断发展,其应用领域也日益拓宽。
未来,等离子体刻蚀技术还将继续向着高效、高精度、多功能、低成本的方向发展,为微纳加工领域的进一步发展提供强有力的支撑。
等离子体刻蚀工艺的物理基础

等离子体刻蚀工艺的物理基础随着科技的不断发展,等离子体刻蚀工艺已经成为微电子、纳米科技、光电子等领域中不可或缺的关键技术。
本文将深入探讨等离子体刻蚀工艺的物理基础,包括基本概念、应用领域、技术细节以及未来发展趋势等方面。
等离子体刻蚀工艺是一种利用等离子体中的高速粒子对材料进行物理轰击,从而去除表面污染或刻蚀特定图形的工艺方法。
刻蚀过程中,目标材料表面的原子在等离子体粒子的撞击下获得足够的能量,从表面脱离或被溅射,最终形成刻蚀图案或去除污染物。
等离子体刻蚀工艺的基本原理是能量传递。
当高速的等离子体粒子撞击目标材料表面时,会将其能量传递给表面原子。
当这些原子的能量超过其结合能时,便会从表面脱附或被溅射。
这一过程可在气体辉光放电或电感耦合等条件下进行。
在等离子体刻蚀工艺中,有几个基本概念需要理解。
首先是刻蚀速率,它表示单位时间内材料表面的去除速率;其次是选择比,指不同材料在同样的刻蚀条件下,刻蚀速率的比值;还有刻蚀均匀性和刻蚀终止层厚度,它们分别表示刻蚀过程中材料表面受影响的均匀程度和刻蚀深度。
等离子体刻蚀工艺广泛应用于微电子、纳米科技、光电子等领域。
在微电子领域,等离子体刻蚀工艺被用于制造集成电路和半导体器件,如动态随机存储器(DRAM)和互补金属氧化物半导体(CMOS)等。
在纳米科技领域,等离子体刻蚀工艺被用于制造纳米材料、纳米器件以及纳米结构的加工。
在光电子领域,等离子体刻蚀工艺被用于制造光电子器件,如激光器、光电检测器等。
随着科技的发展,市场对等离子体刻蚀工艺的需求也在不断增加。
为了满足市场需求,业界不断研发新的等离子体刻蚀技术,以提高刻蚀速率、选择比、刻蚀均匀性和终止层厚度等指标。
在等离子体刻蚀工艺的发展历程中,出现了多种技术,如反应离子束刻蚀(RIBE)、磁控溅射刻蚀(MSPE)、电子回旋共振刻蚀(ECR)等。
这些技术在不同的应用领域有着各自的优势和局限。
高质量的等离子体刻蚀工艺需要精确控制技术参数,如等离子体的密度、温度、电场强度等。
等离子刻蚀
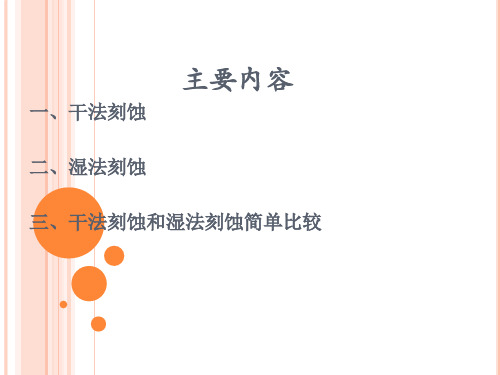
刻蚀槽溶液流向图
刻蚀反应为氧化,放热反应. 刻蚀反应为氧化,放热反应.
液面与硅片吸附反应后流入外槽 流回储液槽,溶液温度较高 刻蚀槽内槽温度较低 内槽槽壁可调节高度, 刻蚀槽液不断循环降温, 且循环流量(一定范围 内)越大,液面越高
冷却器 泵液至冷却器
泵液至刻蚀槽内槽
泵
储液槽
刻蚀槽液面
硅片
硅片间液面
在低HNO3及高 及高HF浓度区,生成 浓度区, 的能力弱而去除SiO2的能力 在低 及高 浓度区 生成SiO2的能力弱而去除 的能力弱而去除 的能力 反应过程受HNO3氧化反应控制,所以腐蚀曲线平行于等 氧化反应控制, 强,反应过程受 氧化反应控制 所以腐蚀曲线平行于等HNO3 浓度线 。 在低HF高HNO3浓度区,生成 高 浓度区, 的能力强而去除SiO2的能力弱, 的能力弱, 在低 浓度区 生成SiO2的能力强而去除 的能力强而去除 的能力弱 反应过程受HF反应控制,所以腐蚀线平行于 反应控制, 浓度线。 反应过程受 反应控制 所以腐蚀线平行于HF浓度线。 浓度线
图:硅在70%(重量)HNO3+49% (重量)HF混合液中的腐蚀速率与 成分的关系
根据这一特性,我们可以把常用的酸性腐 根据这一特性,我们可以把常用的酸性腐 蚀液(通常由不同比率的硝酸( 蚀液(通常由不同比率的硝酸(HNO3),氢氟酸 氢氟酸 (HF)及缓冲液等组成)的腐蚀机理分为两步: )及缓冲液等组成)的腐蚀机理分为两步: 1.利用硝酸(HNO3)氧化硅片表面 利用硝酸( 利用硝酸
HF/HNO3体系腐蚀机理特点 体系腐蚀机理特点
大致的腐蚀机制是先氧化再去除,酸对硅的腐蚀速 度与晶粒取向无关,因此酸腐蚀又称为各向同性腐蚀 。
在HF-HNO3溶液中的刻蚀速率是各向同性,(100)面的 刻蚀速率和(111)面的腐蚀速率非常接近。 而碱性腐蚀液为典型的各向异性腐蚀,(111)面的腐蚀速 率远远大于(100)的腐蚀速率。 刻蚀只腐蚀边缘,而不影响太阳电池的工艺结构,而碱性 腐蚀液各向异性大,已经做好的绒面引起更大的差异,不利于 后道的工序。
rie刻蚀原理

rie刻蚀原理
刻蚀是一种用于制造微米和纳米器件的重要技术,在半导体和电子工业中得到广泛应用。
其中,rie刻蚀技术是一种常用的深度刻蚀技术,其原理主要是利用等离子体在离子轰击下与物质表面发生反应,使表面物质被剥离或氧化,从而实现刻蚀目的。
riec刻蚀过程中需
要控制多个参数,如气体组成、功率、压力、温度等,以实现所需的刻蚀效果。
此外,riec刻蚀还可以实现高选择性、高均匀性和高精
度的刻蚀结果,因此在半导体和电子工业中应用广泛。
- 1 -。
- 1、下载文档前请自行甄别文档内容的完整性,平台不提供额外的编辑、内容补充、找答案等附加服务。
- 2、"仅部分预览"的文档,不可在线预览部分如存在完整性等问题,可反馈申请退款(可完整预览的文档不适用该条件!)。
- 3、如文档侵犯您的权益,请联系客服反馈,我们会尽快为您处理(人工客服工作时间:9:00-18:30)。
大类:圆筒型和平行板型。其中圆 筒型设备在等离子腐蚀工艺中最先采用,至今仍在腐
蚀硅、多晶硅、氮化硅和去பைடு நூலகம்工艺中 广泛应用。
4)等离子腐蚀
①多晶硅的腐蚀一般采用CF4作为基本工作气体,它腐 蚀硅的活性基是F*,即有:进一步发现,对于圆筒隧 道型反应器,在CF4中加入2~6%的02能使等离子体中 的F*比例增大,提高腐蚀速率。
基塑绫金速室坦 等时,则维持等离子体状态。 等离子腐蚀就是利用放电过程中所形成的这些化学活性基与被腐蚀的膜
层发生选择性 的化学腐蚀反应,反应生成能够被气流带走的挥发性气体。其反应机理举
例如下: 其中“{”表示活性基,是具有很强的化学反应活性的物质。当它们与硅、
二氧化硅或氮化硅作用时,则反应生成可挥发的SiF等气体。 (2)等离子腐蚀特性 ①腐蚀材料的影响材料不同,腐蚀速度也不同。;
等离子腐蚀原理
在气体中,一般总存在微量的杂散电子。这些电子在高电场的加速下获
得能量,当它 跟气体中的原子或分子发生非弹性碰撞时,便产生二次发射电子。它们进
一步再与其它原 子或分子碰撞电离,就会产生气体辉光放电。在放电过程中,非弹性碰撞
可以产生分子激 励和活性基,它们的化学性质很活泼,但寿命很短,很快就被缔合。当激
对于图6一12(b)所示的石英圆管型反应器,其氧气比 例增加到50%左右。根据质量分析结果推断,在这种 情况下,由于cof*具有较长的寿命,并大都能随气流 到达硅片表面进行如下反应:
研生成的F*与Si作用,即达到腐蚀的目的。由于COF* 寿命较长,它随腐蚀区与等离子产生区距离的变化不 大,所以能快速而均匀地腐蚀硅片,
(3)等离子腐蚀设备
腐蚀设备主要包括三部分;一个或几个由金属、玻璃 或石英做的圆筒形反应器,一台射频发生器和一个控 制组件。对它的要求是:
① 等离子体分布均匀,浓度高,稳定性好。 ②芯片不受辐射损伤和沾污。 ③芯片温度低,且稳定。 ④反应管内气体流动均匀,设备简单,操作方便,一