制造过程设计开发检查表检查表
制造过程审核检查表

4
1、文件与工装、刀具、模具、检具其中任意 一项未符合最终版本各扣1分。
3
1、包装方案未按照和客户达成一致的包装方 案扣3分。
1、包装上未有客户标识扣1分。
4
2、包装上未有产品名称标识扣1分。 3、包装上未有产品零件号扣1分。
4、包装上未有产品数量标识扣1分。
3
1、无安全库存资料扣2分。 2、安全库存资料不完善扣1分。
1、物料未按要求区域划分待检区、合格区、
不合格区或划分不合理扣1分。
5
2、划分标识不明确扣1分。 3、每批次产品无编码标识扣1分。
4、每批次产品无厂家标识扣1分。
5、每批产品无炉批号扣1分。
第 1 页,共 4 页
文件编号: OK
检具精度能否满足要求,检具 3 得到了有效的验证,检测,
并有有效期标签
4
库存管理程序,来料的安全库 存
三: 生产工位 按照控制计划审核生产过
1 程,设备参数与文件一致
2 产出产品的追溯方案
3 RPN的改进
偶发事件的应急方案,人 4 员,设备,备用工装,检
具,刀具,模具 关键特性是否都在控制方式 5 之内
明确的产品状态及分析报
6
告,红盒子,黄盒子,绿盒 子及调机品,首末件,存储
2
1分。 2、控制计划版本与版本记录不相符不正确扣
1分
1、无工装夹具扣2分。
8
2、工装夹具与清单不相符扣2分。 3、过程责任者不明确扣2分。
4、过程责任者未经培训考核就上岗扣2分
1、未采用SPC统计过程控制扣2分。
5
2、未采用防错过程控制扣2分.
3、未采用全检的控制方式扣1分
5
1、来料未按要求进行检验扣3分。 2、未有检验报告扣2分。
C2-设计与开发过程检查表

√
3.3制订包装规范
是否根据顾客提供的产品包装标准编制公司的产品包装标准,并将其填 写于《包装作业指导书》
√
APQP小组 查《包装作业指导书》
√
3.4产品/过程质量评审
APQP小组是否对公司的质量体系进行评审,并将结果记录于《产品/过 程质量体系检查表》
√
APQP小组 查《产品/过程质量体系检查表》
√
4.7包装评价
APQP小组是否对公司或客户规定的包装方式进行包装评价,并记录于《 产品包装评价表》
√
4.8制订生产控制计划
研发是否制定生产《控制计划》,品管部是否制订生产《控制计划检查 表》
√
4.9质量策划认定
APQP小组是否做正式的质量策划认定,并将结果记录于《产品质量策划 总结和认定报告》中,并呈报管理者代表核准
√
APQP小组 查APQP资料《新产品开发申请单》
√
研发是否根据客户要求或者客户提供图面、样品等制订开模图面
√
APQP小组 查客户提供图面
√
APQP小组是否制订样品《控制计划》
√
APQP小组 查APQP资料《控制计划》
√
模具课是否根据研发提供的图纸等资料编制模具计划/进度表。模具制 造完成后进行试模是否填写《试模报告》
√
APQP小组 查PFEMEA、控制计划、过程流程图
√
研发是否绘制《车间平面布置图》
√
APQP小组 查《车间平面布置图》
√
3.6制订车间平面布置图
品管部是否制订《车间平面布置图检查表》,APQP小组是否对平面布置 图进行评审
√
APQP小组 查《车间平面布置图检查表》
√
3.过程设
设计和开发输出要求点检表(TS16949要求)

设计和开发输出要求点检表(ISO/TS16949:2009要求)
定义/说明/要求/目的:
维修性是指:产品在规定的条件和规定的时间内,按规定的程序和方法进行维修时,保持或恢复到规定状态的能力。
放行是指:对进入一个过程的下一阶段的许可。
降级是指:为使不合格产品符合不同于原有的要求而对其等级的变更。
主要设计特性是指:指某一零件、系统或总成有公差规定并可测量的特性,且这些特性在超出公差的情况下,会对该零件或系统的功能、质量成本或可靠性产生不利的或降级的影响。
设计和开发的输出应以能够针对设计和开发的输入进行验证的方式提出,并应在放行之前得到批准。
制造或加工过程可以包括:生产材料、生产或维修零件、装配、热处理、焊接、喷漆、电镀或其他表面处理。
检查表:。
制造过程检查表

制造过程检查表制造过程审核检查表被审核的制造过程:审核员/日期:审核项目涉及的标准条款审核内容审核中的观察和证据记录判**果备注P-FEMEA及控制计划7.3.2.37.3.3.27.5.1.11.是否有识别产品和过程的特殊特性?这些特殊特性的制定,形成文件和控制方面是否符合顾客的要求?2.是否建立产品的过程流程图?流程图与实际的作业过程是否一致?3.P-FMEA中是否包含了过程流程图中的全部作业步骤?4.P-FMEA所确定采取的措施是否被列入到控制计划或作业指导书中?5.是否有试生产和生产的控制计划?控制计划是否包含了对所有特殊特性的控制方法?6.控制计划是否包含了顾客要求信息?7.当任何影响产品、制造过程、测量、供货来源或FMEA的更改发生时,是否更新了控制计划?8.是否为所有负责过程操作的人员提供了文件化的作业指导书?9.这些作业指导书是否在操作这得工作岗位并易于得到?人员素质/能力6.2.1?6.2.2.26.2.2.36.2.2.41.对于新上岗和调整岗位的人员是否进行了岗位培训,并具备了从事岗位工作所需的能力?2.所有操作人员是否具备了相应的资格和能力?特殊岗位人员是否进行了资格鉴定?3.员工是否了解所从事工作的相关性和重要性?是否知道不符合质量要求会给顾客带来怎养的后果?4.员工是否了解本部门的质量目标,以及如何为实现质量目标做出贡献?5.员工是否明确工作职责,是否知道如何清楚的与上下工序沟通各种情况?6.当发生质量异常时,员工是否知道如何反馈给现场管理者?7.是否有效地使用了提高员工工作积极性的方法?生产设备/工装管理7.5.1.47.5.1.51.是否有建立机器/设备的预防性与预见性维护计划?并按计划执行日常保养和定期保养活动,是否有维护记录?2.设备出现异常时现场如何处理?3.是否建立关键生产设备的零配件清单?并在需要时可以得到?4.生产设备/工装模具是否能满足产品特定的质量要求?5.在批量生产中使用的检测、试验设备是否能有效的监控质量要求?6.设备、工装、量具的储存和防护是否有规定的要求、并按其执行?7.是否建立易损工装的更换?8.工装的使用、存放、标识和维护是否有规定要求,并按其执行?9.是否有工装的设计图纸或文件?设计图纸/文件与实际工装是否相符合?7.5.1????????7.5.1.38.2.3.18.2.41.生产前应作哪些生产准备?这些准备是否能充分满足生产的要求?2.生产的安排和布置是否符合工艺流程或流程图的规定?3.是否有执行首件确认并有相应记录?4.有关过程参数的设定是否符合作业指导书或控制计划的规定?关键参数的设定是否有做记录?5.生产中的各作业步骤是否按控制计划的要求执行相应的控制?6.控制计划中要求用控制图控制的特殊特性是否有收集数据并绘制相应的控制图?7.当控制图显示过程不稳定时,是否进行了分析和采取了什么措施来改进?8.是否有做生产能力分析?当生产能力不满足≥1.33或顾客的要求时,是如何处置的?9.是否有按控制计划安排执行生产检验并有记录?10.当生产异常时是否启动控制计划中的反映计划?11.生产中的物料、半成品、成品、合格品、不合格品等是否按规定的要求标识清楚?12.当生产中的工作环境条件有规定要求时,是否按规定要求实施控制?不合格品控制8.3????8.3.2????????8.3.41.当生产中发生不合格时是如何处理的?如何将不合格及时通知给负有纠正措施的管理者?是否有处理结果的记录?2.是否有返工作业指导书?这些作业指导书是否易于被适当的人员得到并使用?3.当产品或制造过程与当前批准的不同,在继续生产之前,是否获得顾客的让步或偏离许可?4.返工半成品、成品是否经过重新检验合格**转入下工序或出货?包装与搬运7.5.51.产品包装是否按照包装规范的要求进行包装?2.产品的包装是否符合顾客的要求,并能确保对产品的防护?3.产品的搬运和转移是否能确保不混批、不混料并保证可追溯性?4.是否有规定搬运的工具和方法?这些方法是否确保物料/产品不被跌落或损坏?纠正与预防措施8.5.2?8.5.2.28.5.2.3?8.5.31.当外部发生异常或顾客投诉,是否将相关信息通知到生产部门?生产部门是否针对异常原因进行了分析,采取了什么措施?是否验证措施的有效性?2.纠正措施是否应用了防错方法?3.是否将纠正措施和实施的控制应用与其他类似的过程和产品?4.当内部和外部发生异常时,是否有评审P-FMEA和控制计划?是否有作适当的更新?5.当数据分析或控制图显示有潜在异常的趋势时,是否有采取预防措施以防不合格的发生?数据分析和目标业绩8.41.是否有根据生产的目标和衡量指标定期统计和分析?2.当数据显示目标或指标未达成时,采取了哪些改进措施?持续改进8.5.1.21.当制造过程有能力且稳定或当产品特性可预测且满足顾客要求时,是否有考虑持续改进的措施?2.当数据显示目标或指标未达成时,是否有作进一步的提升?备注:要求程度的打分依据分数对符合要求程度的评定10完全符合8绝大部分符合,只有微小的偏差6部分符合,有较大的偏差4小部分符合,有严重的偏差0完全不符合。
C2过程设计和开发过程-检查表(1)

程序方法: 确认点:文件和记录、监视和测量工具、方法等; 确认结果:
绩效评价: 确认点:监视和测量标准、要求,绩效目标; 确认结果:
注:上述抽样(事实)方案中,黑色粗体字部分为优先/重点审核问题。
LY-R-9.2-003 A1
标准条款 过程名称
QMS:8.3\8.5.6 ESD:2\6.1
C2过程设计和开发过程
过程拥有者 过程责任人
内部审核检查表
审核时间
审核人员
优先/重点 8.3.3.3产品和过程的特殊特性
资源环境: 确认点:基础设施、办公设备,使
用工具、用品等; 确认结果:
输入: 1.法律法规标准及其他要求; 2.客户特殊要求; 3.加工合同/质保协议; 4.加工合同/质保协议评审; 5.以往同类产品过程设计开发知识; 6.客户图纸、加工测试规范; 7.加工测试程序、时间、良率; 8.加工/测试/储存/运输环境; 9.设施/设备、工装/配件; 10.ERP/MES生产管理系统; 11.数据传输/对接; 12.售后服务。
确认结果:
输出: 1.新产品调查表; 2.新产品特殊特性评估确认表; 3.制造可行性报告; 4.项目立项表/产品保证计划; 5.APQP开发计划/目标; 6.工艺流程图/流程卡; 7.PFMEA/检查评审表; 8.工程批/量产控制计划; 9.新产品制程评估表; 10.程序/机台/板卡等验证记录; 11.工程批测试验证确认记录; 12.PSW零部件提交保证书; 13.各过程/工序作业标准书等。
抽样(事实)方案
1.查看产品清单,确认汽车用芯片种类; 2.选取三例产品过程开发进行抽查审核: 例1:以QS车规产品(FT)*2 例2:以HD非车规产品(CP)*2 例3:以TF非车规产品(FT)*2 3.抽查确认上述三例已完成的过程设计开发 各阶段资料记录,包括输入、输出。 4.抽查确认上述三例进行中的过程设计开发 产品资料,包括输入、输出。 5.抽查确认QS、HD、TF三家客户特殊要求、 产品和过程特殊要求落实情况。 6.抽查确认三家客户的测试程序接收、验证 资料记录。 7.现在审查确认车规和非车规产品产品在制 造过程开发中的资源环境(包括ESD静电放 电)、风险、人力/能力、绩效评价等。
IATF16949-2016内审检查表-过程设计和开发

1of4
IATF16949:2016内部质量体系审核检查表
4of4
S9
8.5.3
S118.5.1.6S138.5.1.6S14
9.1.2;9.1.3;10.1
S158.5.1.1顾客的技术资料和提供的工装如何管理?是否清楚表明权属关系?当顾客财产不适用/损坏/丢失,是否记录并通知顾客?在顾客所有的工具上是否做永久性标记?
顾客的财产已清楚表明权属关系
合格如何制定工装制造计划和监控工装的到来?新的工装如何验收和入库?工装的修改如何控制?是否定义易损件更换计划并实施?
有新的工装验收单
合格是否考虑新进的监视和测量装置精度要求?定义了校准/检定期限并按计划委托校准/检定?对CP 中的测量装置是否进行了MSA 分析?
测量装置定义 了校准检定甚好并按计划委托校准/检定,并进行了MSA 分析合格通过哪些指标衡量顾客满意度?了解这些指标的变化趋势的原因吗?是否分析了与竞争对手的差距?确定了改进方向和措施?
通过顾客满意度评分和准时交付率
合格如何定义对产品特性的监测要求,是否考虑顾客的要求/法规要求/过程的稳定情况?对特殊特性的测量如何考虑?是否考虑了全尺寸检验和功能试验的
要求?
是
合格。
IATF16949设计和开发内部审核检查表
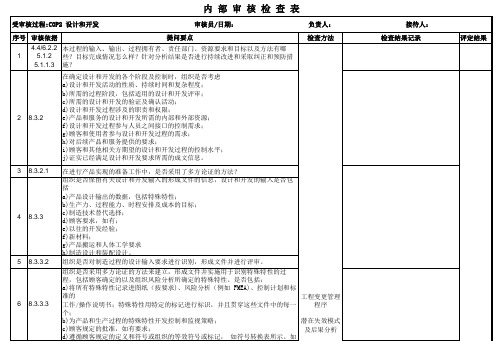
内 部 审 核 检 查 表生产件批准程78.3.4 88.3.4.198.3.4.4 108.3.5118.3.5.1 128.3.5.2 138.3.6组织是否建立,实施和保持一个符合顾客规定要求的产品和制造过程的批准过程生产件批准程序过程设计开发程序设计和开发的输出是否形成文件。
产品设计输出是否符合标准要求?a) 设计风险分析(FMEA);b) 可靠性研究结果;c) 产品特殊特性;d) 产品设计防错结果,例如:DFSS、DFMA 和 FTA;e) 产品定义,包括三维模型、 技术数据包、产品制造信息,以及几何尺寸与公差 (GD&T);f) 二维图纸、产品制造信息以及几何尺寸与公差(GD&T);g) 产品设计评审结果;h) 服务诊断指南及修理和可服务性说明;i) 服务件要求;j) 运输的包装和标签要求。
制造过程的设计输出是否包括a)规范和图纸; b)产品和制造过程的特殊特性;c)对影响特性的过程输入变量的识别;d)用于生产和控制的工装和设备,包括设备和过程的能力研究;e)制造过程流程图/制造过程平面布置图,包括产品、过程和工装的联系;f)产能分析; g)制造过程 FMEA;h)维护计划和说明; i)控制计划(见附录 A);j)标准作业和工作指导书; k)过程批准的接收准则;l)质量、可靠性、可维护性和可测量性的数据;m)适用时,防错识别和验证的结果;n)产品/制造过程不符合的快速探测、反馈和纠正的方法。
组织是否识别,评审和控制在产品和服务设计和开发期间以及后续所作的更改,以避免不利影响,审计和开发的变更,变更评审的结果,变更的授权,为防止不利影响所采取的措施是否形成文件组织对设计和开发的过程控制是否实施评审,验证,确认,针对评审,验证和确认的问题是否采取必要的措施,这些活动是否形成文件的信息组织是否将产品和过程的设计和开发期间特定阶段的测量应被确定、分析,以汇总结果的形式来报告,作为对管理评审的输入。
制造过程审核检查表
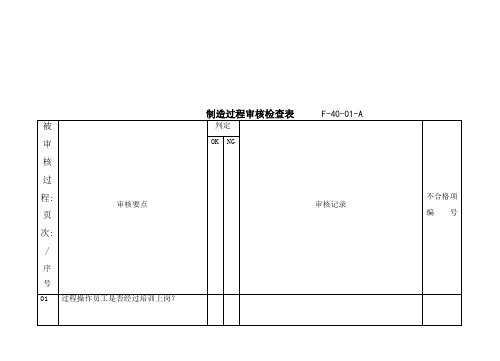
是否根据作业指导书(控制计划、作业指导、操作规程等)对工序进行控制并保留记录?
07
是否根据控制计划中规定的控制方法(控制图、工序能力分析、防错等)对特殊特性进行控制并保留记录?
序号
审核要点
判定
审核记录
不合格项
编 号
OK
NG
08
使用控制图时, 是否掌握失控的判定准则?
09
控制图失控时是否及时采取措施使过程恢复到稳定状态? 是否记录这些措施?
10
产品标识是否符合规定?需要时, 是否能保持可追溯性?
11
检验和试验状态是否清楚地予以区分?
12
不合格的材料和产品是否按规定予以标识和隔离?
13
是否收集、汇总不否和实际一致?
15
是否按规定实施和记录设备的日常保养?
16
工装的状态是否标识? 是否和实际一致?
23
对过程和产品是否进行持续改进?
24
是否制定过程和产品的目标值并监控其完成情况?
页次: /
17
工装的日常管理是否符合规定要求?
18
检验、测量和试验设备是否按规定位置存放?
19
检验、测量和试验设备是否经过检定或校准? 是否在有效期内?
20
生产和检验工位的工作环境条件是否符合要求?
21
库房管理是否符合规定要求(标识、先进先出、帐卡物一致等)?
22
在过程和产品出现缺陷时, 是否分析原因实施纠正措施并验证其有效性?
制造过程审核检查表F-40-01-A
被审核过程: 页次: /
序号
审核要点
判定
审核记录
不合格项
编 号
OK
NG
01
制造过程检查表(过程设计)

5
是否已计划/已具备项目开展所需的人员与技术的必要条件?
6
是否已做过PFMEA,并确定了改进措施?
二、过程开发的落实
7
过程PFMEA是否在项目过程中补充更新?已确定的措施是否已落实?
8
是否制定了质量计划?
9
是否已具有各阶段所要求的认可/合格证明?
10
是否为了获得批量生产认可而进行在批量生产条件下的试生产?
0
4
6
8
10
一、供方/原材料
1
是否允许已认可的且有质量能力的供方供货?
2
是否确保供方产品的质量达到供货协议要求?
3
是否评价供货实物质量?与要求有偏差时是否采取措施?
4
是否与供方就产品与过程的持续改进商定质量目标,并付诸落实?
5
对已批量供货的产品是否具有所要求的批量生产认可,并落实了所要求的改进措施?
11
生产文件和检验文件是否具备且齐全?
12
是否已具备所要求的批量生产能力?
合计
总平均得分值:各相关问题实际得分的总和
Ee(%)= --------------------------- × 100% =
各相关问题满分的总和
审核员:审核日期:
制造过程检查表
受审核单位:受检查过程名称:
序号
检查内容
检查结果
6
是否对顾客提供的产品执行了与顾客商定的方法?
7
原材料库存状况是否适合于生产要求?
8
原材料/内部剩余料是否有合适的进料和贮存方法?
9
员工是否已具有相应的岗位培训?
合计
总平均得分值:各相关问题实际得分的总和
Ee(%)= --------------------------- × 100% =
COP2设计和开发过程内审检查表

质量记录齐全,保存得当
符合
支持文件
根据要求建立相应的作业指导文件
符合Leabharlann 符合涉及的流 程依据文件编制日期看, 潍坊丰东气淬炉项目设 计和开发过程符合流程
符合
过程绩效 指标
设计开发按时完成率:100%
潍坊丰东气淬炉设计开发计划完成于 4 月 18 日, 完成日期为 4 月 18 日,按期完成,设计开发 按时完成率 100%
符合
质量记录
质量记录签字齐全、清晰完整、易于 检索
依据条款 8.2 建立了《设计和开发管理程序》
过程输入
潍坊丰东高压气淬真空炉项目设计开发一览 表中有 9 项, 其中有借鉴日照金马高压高流率 气淬真空炉和烟台海德机电高压气淬真空炉 制造经验。
符合
过程输出
潍坊丰东气淬炉总成图号:QC-WFFD-OOA。 高压气淬真空炉(10BAR)GVF-500 技术说明 书。 潜在失效模式分析(DFMEA、PFMEA) 、 设计和开发评审报告(2016 年 4 月 6 日,经 评审合格) 、设计开发验证报告(2016 年 4 月 17 日,经验证符合要求)设计可开发确认报 告(2016 年 4 月 18 日,确认合理) 、设计和 开发输出一览表(2016 年 4 月 15 日批准) , GVF-500 10bar 气淬真空炉平面和布置节点 图, 由张子健设计、 申敏京审核、 宋绪臻批准。 设计和开发过程无更改
内审检查、记录表
编号: 过程名称 过程类型
项目 体系文件
NO: 杨琳 高玮
设计和开发 COP2
要求
审核区域 过程所有者
技术部 技术部长
审 核 员 审核日期
检查情况
2017.2.17
符合情况 符合
制造过程审核检查表

2.4 项目管理机构是否可以在项目进行进程中提供可靠的变更管理?
2.5* 组织内部以及客户那里相关负责的人员是否已经被纳入变更管理?
2.6
是否为项目编制了一份质量管理计划表,该计划表是否得到落实,其落实情形是否被 定期监控?
2.7* 是否建立了事态升级程序,该程序是否得到有效的落实?
P3 产品和进程开发的计划
制造进程审核检查表
编号
问题
P2 2.1 2.2*
项目管理
是否建立了项目组织机构(项目管理),并且为项目管理以及团队成员肯定了各自的 任务以及权限?
是否为落实项目计划了必要的资源,相关的资源是否已经到位,并且说明了变更情 形?
2.3 是否已经编制了一份项目计划表,并且与客户进行了协商沟通?
得分 一样情形
7.6 针对各具体的任务,相关的人员是否具有资质,是否定义了责权关系?
核准: 表单编 号:G-
审核:
检查记录,包括客观证据
是否转入应急 措施
制表: 储存期限:产品生命周期后一年
第 4 页,共 4 页
产品 进程
3.1 针对具体产品和进程的要求是否已经到位?
3.2* 在为产品和进程肯定的要求的基础上,是否从跨部门的可行性展开了评判?
3.3 是否为产品和进程开发编制了相关的计划?
3.4 针对产品和进程开发,是否推敲到了所需的资源?
3.5 P4 4.1 4.2 4.3 4.4 4.5* 4.6 4.7 4.8
6.3.2* 员工是否有合适完成托付的任务,其资质是否始终保持?
6.3.3 是否编制了员工上岗计划
一样情形
第 3 页,共 4 页
检查记录,包括客观证据
是否转入应急 措施
制造进பைடு நூலகம்审核检查表
面向制造和装配的设计(DFMA)检查表
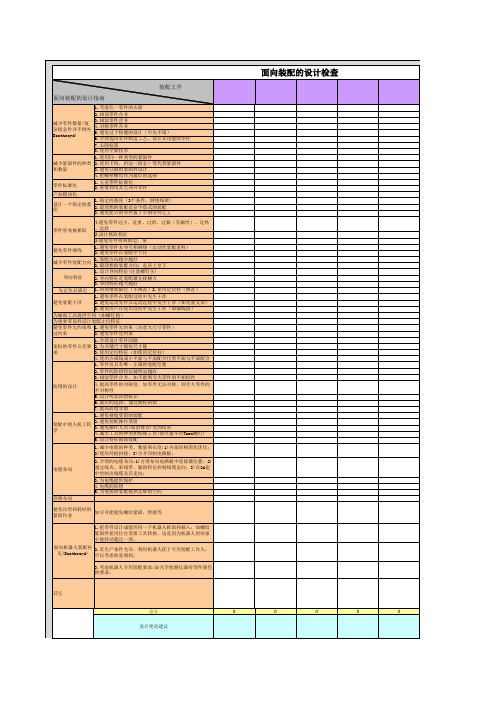
、过软
2.设计抓取特征 3.避免零件锋利的边、角
避免零件缠绕
1.避免零件本身互相缠绕(自动化装配进料) 2.避免零件在装配中卡住
减少零件装配方向
1.装配方向越少越好 2.最理想的装配方向:是从上至下
1.设计导向特征(注意螺钉头)
导向特征 2.导向特征是装配最先接触点
3.导向特征越大越好
先定位后固定 1.四周增加限位(不推荐)2.使用定位柱(推荐)
装配工序
面向装配的设计指南
1.考虑任一零件的去除
2.相邻零件合并
减少零件数量(复 杂钣金件亦不例外 Boothroyd)
3.相似零件合并 4.对称零件合并 5.避免过于稳健的设计(可先不填)标签 8.使用全新技术
1.使用同一种类型的紧固件
减少紧固件的种类 2.使用卡钩、折边(钣金)等代替紧固件
3.为电缆提供保护 4.电缆的防错 5.为电缆的装配提供足够的空间
管路布局
避免昂贵和耗时的 紧固作业
如尽可能避免螺纹紧固,焊接等
1.把零件设计成能用同一个机器人抓取和插入:如螺纹 紧固件使用往往需要工具转换,这是因为机器人肘结很 少能转动超过一周。
面向机器人装配补 2.若生产条件允许,利用机器人优于专用装配工作头, 充(Boothroyd) 可以考虑放宽规则。
和数量
3.避免分散的紧固件设计
4.把螺栓螺母作为最后的选择
零件标准化
1.五金零件标准化 2.重复利用其它项目零件
产品模块化
设计一个稳定的基 座
1.稳定的基座(3个条件,例绕线架) 2.最理想的装配是金字塔式的装配 3.避免把大的零件置于小的零件之上
1.避免零件过小、过重、过滑、过黏(有磁性)、过热
制造过程审核检查表

26
员工是否严格按作业指导书作业?
27
现场的照明是否充足,是否适合作业\检查等操作?
28
现场产品标示看板等是否清楚标示产品相关生产信息,记录是否与产品相符
29
每天工作计划安排清晰,各生产岗位数量与安排一致;
30
生产计划安排是否与当班生产设备等吻合?
31
对特性有关的测量系统是否有进行MSA分析?
32
测量工具是否
不符合项目编号
20160304 ZTQR01092 AO
制造过程审核检查表
审核员:
日期:
审核过程:
陪同人员:
1、评分标准:10分---完全符合要求,不存在偏差; 8分---绝大部分符合要求,有少量偏差; 6分---部分符合要求,有较大偏差;
4分----少部分符合要求,偏差严重; 0分---完全不符合要求;
制程的物料、半成品、成品、合格品、不合格品等是否按规定要求标识清楚?
22
当制程的工作环境条件有规定要求时,是否按规定要求来实施控制?
23
是否有执行首件确认并做相应的记录?是否有按控制计划的安排执行制程检验并作记录?
24
发生变更后是否有进行验证和批准?
制造过程控制
25
作业指导书是否受控?是否为最新版?是否与现场作业相符?
序号 审核项目
审核内容
得分
审核情况描述
1
所有操作人员是否具备了相应的资格和能力?
2
员工对本岗位的作业指导书的要求是否清楚?
3
特殊岗位人员是否进行了资格鉴定?
4
员工是否明确工作职责,是否知道如何清楚的与上下级沟通各种情况?
5
人员素质 当发生质量异常时,员工是否知道如何反馈?
APQP检查表(含设计、过程、控制计划等)

试验频率?
22
样本容量?
23
反应计划?
24
文件化?
目测辅具
25
是否容易理解?
26
是否适用?
27
可接近性?
28
是否被批准?
制订/日期:批准/日期:
产品/过程质量检查表
顾客或厂内零件号:
问题
是
否
所要求的意见/措施
负责人
完成日期
目测辅具(续)
29
注明日期并是现行的?
30
对于统计控制图表,是否有实施、保持和制定及反应计划的程序?
24
所有的产品试验是否都将在厂内进行?
25
如不是,是否由批准的分承包方进行?
26
规定的抽样容量和/或抽样频率是否可行?
27
如要求,对试验设备是否已获得顾客批准?
制订/日期:批准/日期:
设计输出检查表
顾客或厂内零件号:
问题
是
否
所要求的意见/措施
负责人
完成日期
D:材料规范
28
是否明确材料特殊特性?
29
在已被明确的环境中,规定的材料、热处理和表面处理是否和耐久性要求相一致?
问题
是
否
所要求的意见/措施
负责人
完成日期
14
问题的解决?
15
防错?
16
被识别的其他项目?
17
对每一个控制计划来说非常关键的操作是否都提供过程指导书?
18
每一个操作上是否都具备标准的操作人员指导书?
19
操作人员/小组领导人员是否参与了标准的操作人员指导书的制定工作?
检验指导书是否包括以下内容:
20
最新版APQP 设计信息检查表
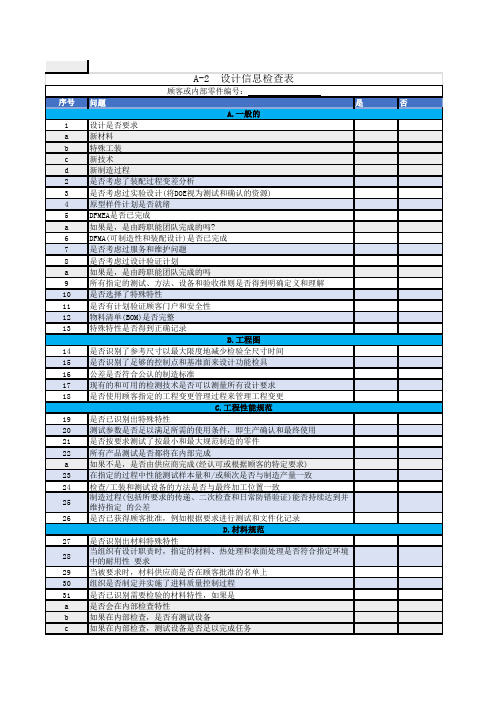
1设计是否要求a新材料b特殊工装c新技术d新制造过程2是否考虑了装配过程变差分析3是否考虑过实验设计(将DOE视为测试和确认的资源)4原型样件计划是否就绪5DFMEA是否已完成a如果是,是由跨职能团队完成的吗?6DFMA(可制造性和装配设计)是否已完成7是否考虑过服务和维护问题8是否考虑过设计验证计划a如果是,是由跨职能团队完成的吗9所有指定的测试、方法、设备和验收准则是否得到明确定义和理解10是否选择了特殊特性11是否有计划验证顾客门户和安全性12物料清单(BOM)是否完整13特殊特性是否得到正确记录14是否识别了参考尺寸以最大限度地减少检验全尺寸时间15是否识别了足够的控制点和基准面来设计功能检具16公差是否符合公认的制造标准17现有的和可用的检测技术是否可以测量所有设计要求18是否使用顾客指定的工程变更管理过程来管理工程变更19是否已识别出特殊特性20测试参数是否足以满足所需的使用条件,即生产确认和最终使用21是否按要求测试了按最小和最大规范制造的零件22所有产品测试是否都将在内部完成a如果不是,是否由供应商完成(经认可或根据顾客的特定要求)23在指定的过程中性能测试样本量和/或频次是否与制造产量一致24检查/工装和测试设备的方法是否与最终加工位置一致25制造过程(包括所要求的传递、二次检查和日常防错验证)能否持续达到并维持指定 的公差26是否已获得顾客批准,例如根据要求进行测试和文件化记录27是否识别出材料特殊特性28当组织有设计职责时,指定的材料、热处理和表面处理是否符合指定环境中的耐用性 要求29当被要求时,材料供应商是否在顾客批准的名单上30组织是否制定并实施了进料质量控制过程31是否已识别需要检验的材料特性,如果是a是否会在内部检查特性b如果在内部检查,是否有测试设备c 如果在内部检查,测试设备是否足以完成任务D.材料规范A-2 设计信息检查表顾客或内部零件编号:A.一般的B.工程图C.工程性能规范d如果在内部进行检查,是否有称职的人员来保证准确的测试32对于材料的传递特性,所需的控制是否已与您的顾客达成一致33会使用外部实验室吗a组织是否已经有确保实验室能力(如认证)的过程注:无论组织与实验室的关系如何,都需要保证能力34是否考虑了以下材料要求a处理,包括环境方面b如何储存,包括环境方面c是否按照顾客要求(例如IMDS)报告了材料/物质成分d聚合物零件是否已根据顾客要求进行识别/标记e运输、集装箱和部件的标签要求。
过程审核检查表(制造过程)

合计
审核结果
说明
审核要素总分数=1070
过程符合率=(实际得分总和/满分总和)×100%=
分值级别的意义:分值10—完全符合要求,不存在偏差; 分值8—绝大多数符合要求,只有少量偏差,不存在风险; 分值6—部分符合要求,有较大偏差;分值4—少部分符合 要求,有严重的偏差;分值0—完全不符合要求
4格 品 如 何 处 理 ? 废 品 、 余 料 、
4返 0修 5件
如 何 管 理 ? 废 品 、 余 料 、 返 修 件 有 4无 0隔 6离 区 标 识 、 返 修 工 位 等 ?
怎 样 防 止 物 料 搬 运 、 贮 4存 0时 7磕 碰 划 伤 、 损 坏 或 变 质 ? 对 过 程 用 的 辅 助 4材 0料 8有 无 管 理 措 施 ? 物 4料 0的 9流 动
是 否 通 畅 ? 产 品 标 识 与 检 验 和 试 验 状 态 4的 1标 0识 及 移 动 是 否 符 合 有 关 规 定 ? 能 否 对 物 料 4做 1到 1适 当 的 追 溯
?
有
无
4浪
1费
2问
题
?
是
否
4便
1于
3取
拿
?
是
否
4配
1置
4得
当
?
小1
计4
是
否
有
切
实
可 50 行 1的
作
工
业
艺
5方
是 否 有 效 版 本 ? 能 否 防 5止 0文 7件 误 用 ? 操 作 方 5法 0安 8全 否 ? 是 否 有 5防 0错 9的 方 法 ? 是 否 是 高 5效 1率 0的 方 法 ? 5前
1、 1后
IATF16949内审检查表-制造过程(按过程方法编制)

来料是否具备必要的标识/记录/放行,并且得以适当地体现?
1.5
是否对在量产过程中的产品或过程变更开展了跟踪和记录?
2
所有生产过程是否受控?(过程管理)
2.1
控制计划的要求是否完整并得到有效落实?
2.2
是否进行了生产启动的重复性放行?
2.3
是否对生产中的特殊特性进行了管理?
2..4
是否对未放行和/或缺陷零件进行了管理?
2.5
是否能确保材料/零部件在流转过程中不发生混合/弄错?
3
哪些岗位为过程提供支持?(人力资源)
3.1
员工是否能从事安排的工作?
3.2
员工是否了解监视产品和过程质量的职责与权限?
3.3
是否有必要的人力资源?
4
使用哪些手段执行过程?(物质资源)
4.1
是否能够利用生产设备满足顾客对产品的具体要求?
4.2
5.4
是否对过程和产品定期开展审核?
6
过程应产生什么?过程结果(输出)
6.1
是否根据需要确定产量/生产批量,并且有目的地运往下道工序?
6.2
是否根据要求对产品/零部件进行适当仓储,所使用的运输设备/包装设备是否与产品/零部件的特殊特性相适应?
6.3
是否保持了必要的记录和放行?
6.4
最终产品交付时是否满足顾客的要求?
部 门
产类别
制造过程
审核日期
序号
审核内容
审核结果
判 定
符合
不符合
观察
1
过程输入是什么?(过程输入)
1.1
是否在开发和批量生产之间进行了项目交接,以确保生产顺利启动?
1.2
来料是否在约定的时间按所需数量/生产批次大小被送至正确的存放位置/工位?
TS16949制造过程审核检查表

2.3
作业员是否具有代理人?
3:设备
3.1
设备是否均需具有操作指导书置放于作业现场?
7.5.1
3.2
各工序设备是否具有设备的日常保养记录?
3.3
设备作业参数是否与控制计划/QC工程表、参数对照表一致?
4:工装
4.1
摆放于作业现场的工装是否标示明确?
7.5.1.5
ISO/TS16949制造过程审核检查表
部门
过程名称
序号
制程管制过程检查提问表
要素
检查结果记录或判定
生产
制程管制过程
请按以下1-9点核对每1个制造过程,以确认其有效性
1:信息输入
1.1
生产指令是什么?
7.5.1
MI
2:作业人员
2.1
工序作业员是否有明确上岗资格要求?
6.2.2/
5.5.1
基本有
2.“工装更换计划”,并定期更换,具有更换记录?是否对工装进行了定期保养?
5:现场检具
5.1
现场检具是否有明确的校正合格标示,并能追溯到校正记录?
7.6
6:作业方法
6.1
各工作工序具有易于获得的作业指导书?
7.5.1
6.2
现场作业指导书是否与控制计划要求基本一致,作业人员作业是否与其要求一致?
10.3
关键过程CPK能力不足时,是否有证据采取了纠正预防措施,包括:工序全检、措施实施记录?
8.2.3
8.2.3
8.5.2/3
部门
过程名称
序号
制程管制过程检查提问表
要素
检查结果记录或判定
生产
制程管制过程
设计和开发策划内审检查表模板

编号
检查内容
1
设计和开发的目的
确保后续的产品和服务的提供
2
设计和开发过程要求
应建立、实施和保持适当的设计和开发过程
3
产品和制造过程的设计和开发,应着重于错误预防,而不是探测
4
应对设计和开发过程形成文件
5
应对产品的设计和开发进行控制。说明:控制的目的是确保设计和开发依据策划的方式进行,并在必要的时候进行策划更新
18
使用多方论证方法的方面
19
设计和开发的策划输出应及时更新。说明:这些更新是依据设计和开发的进展、客户的需求和期望的变化、产品要求及标准的更变、资源需求的要求等而进行的
20
设计和开发策划应确定的内容
设计和开发阶段。说明:可以根据产品的特点、过程复杂程度、组织的水平、历史经验、和顾客的要求等因素来划分设计和开发阶段
13
顾客和使用者参与设计和开发过程的需求
14
对后续产品和服务提供的要求
15
顾客和其他相关方期望的设计和开发过程的控制水平
16
证实已经满足设计和开发要求所需的成文信息
17
设计和开发策划要求
应确保设计和开发策划涵盖组织内部所有受影响的利益相关者及其(适当的)供应链。说明:采购、供应商和维护功能也许会作为利益相关方被包括
21
设计和开发的评审活动。说明:明确活动的方式、时机、参与人员等
22设Leabharlann 和开发的验证活动23设计和开发的确认活动。说明:设计和开发的评审、验证和确认具有各自明确的目的,根据产品和组织的具体情况,可以单独或一起进行并记录
24
设计和开发的职责
25
设计和开发确认要求点检表(TS16949要求)
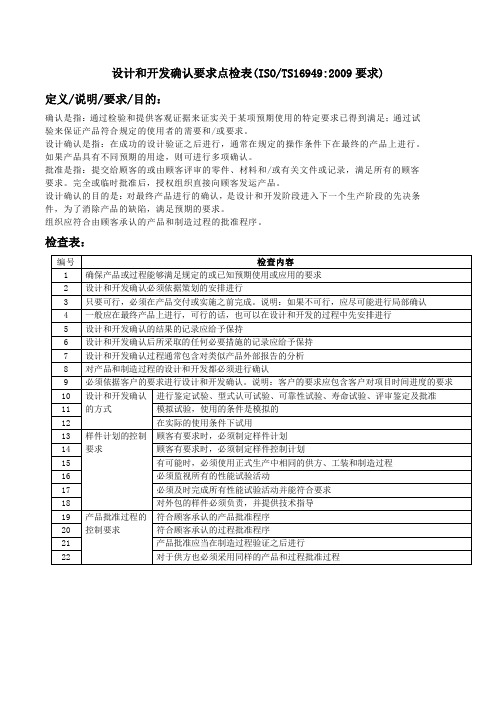
设计和开发确认要求点检表(ISO/TS16949:2009要求)
定义/说明/要求/目的:
确认是指:通过检验和提供客观证据来证实关于某项预期使用的特定要求已得到满足;通过试验来保证产品符合规定的使用者的需要和/或要求。
设计确认是指:在成功的设计验证之后进行,通常在规定的操作条件下在最终的产品上进行。
如果产品具有不同预期的用途,则可进行多项确认。
批准是指:提交给顾客的或由顾客评审的零件、材料和/或有关文件或记录,满足所有的顾客要求。
完全或临时批准后,授权组织直接向顾客发运产品。
设计确认的目的是:对最终产品进行的确认,是设计和开发阶段进入下一个生产阶段的先决条件,为了消除产品的缺陷,满足预期的要求。
组织应符合由顾客承认的产品和制造过程的批准程序。
检查表:。
- 1、下载文档前请自行甄别文档内容的完整性,平台不提供额外的编辑、内容补充、找答案等附加服务。
- 2、"仅部分预览"的文档,不可在线预览部分如存在完整性等问题,可反馈申请退款(可完整预览的文档不适用该条件!)。
- 3、如文档侵犯您的权益,请联系客服反馈,我们会尽快为您处理(人工客服工作时间:9:00-18:30)。
PFMEA 资料
多方认证小组/ 06.8
工 艺 平 面 布 按产品工艺过程实际绘制反映产品流程及合
2.8
工艺平面布置图
置图
适检验点的布置图
技质部/ 06.8
样件控制计
2.8
编制样件控制计划
划
样件控制计划
技质部/ 06.8
2.10 样件制造
按样件控制计划制造样品
样品测试记录
生产部/技质部 06.8
试生产控制
2.14 导书、检验规
验规范
检验规范
范
技质部/ 06.9
2.15 包装规范
编制总成包装箱标准
包装瓦楞纸箱
技质部/ 06.9
完成 完成 完成 完成 完成 完成 完成 完成 完成 完成 完成
XXX/8.16 XXX/8.23 XXX/8.25-26 XXX/8.25 XXX/8.26 XXX/9.25 XXX/9.10 XXX/9.10 XXX/9.18-20 XXX/8.24-26 XXX/8.12
评估 APQP 有效性
顾客满意度调查表
销售部/ 06.10
加强交付监控,及时与顾客沟通,了解顾客的
4.3 交付、服务
交付记录/服务记录
期望,搞好售后服务
销售部/ 06.10-06.11
完成 完成 完成 完成
XXX/10.11 XXX/10.15 XXX/10.16 XXX/10.25
2.11
试生产控制计划编制
计划
试生产控制计划
技质部/ 06.9
测量系统分
2.12
编制测量系统分析(MSA) 计划及实施
析
MSA 计划
技质部/ 06.9
过程初始能
2.13
编制初始过程能力业研究计划
力研究策划
初始过程能力业研究计 划
技质部/ 06.9
过程作业指
编制提供现场操作人员可理解的作业文件、检 加工工序卡片、
包装要求
产品/过程质
评审质量体系文件对卡钳总成产品/过程的符
2.3 量保证体系
评审会议记录
合性
评审
2.4 顾客图纸
顾客图纸评审并 CAD 厂化及顾客再确认
CAD 图纸 顾客确认传真
销售部/技质部 06.8
多方认证小组/ 06.8
技质部/销售部 06.8
检
是否完成
完成 完成
完成
完成 完成 完成 完成
查
评估
试生产评审纪要 MSA 报告 SPC 资料
多方认证小组/ 06.9
多方认证小组/ 06.9
多方认证小组/ 06.9
生产过程 3.5
确认
全尺寸、全性能检测,验证产品/过程是否符 全尺寸、全性能检测结
合工程规范
果、验证确认结论
技质部/ 06.10
3.6 包装评价
包装评价和试验
产品试验报告单
技质部/06.10
用正式生产的工装、设备按生产控制计划进行
生产控制计
3.7
作业,通过生产实践,对控制计划进行修订、 生产控制计划
划
评价
多方认证小组/ 06.10
用正式生产的工装、设备按生产控制计划进行 3.8 生 产 控 制 计
作业,通过生产实践,对控制计划进行修订、 生产控制计划
划评价 评价
多方认证小组/ 06.10
检查人/日期
XXX/8.1 XXX/8.2
XXX/8.15
XXX/8.15 XXX/8.3 XXX/8.18 XXX/8.16
过程设计开
2.5
编制产品设计和开发总进度计划
发总计划Biblioteka 产品设计和开发 总进度计划
多方认证小组/ 06.8.1
过程流程设
2.6
编制产品过程流程图
想
过程流程图
技质部/ 06.8
2.7 过程 FMEA 小组进行产品过程 FMEA 分析
KY/QR7.3-06
XXXXXXX 有限公司
产品名称
XXXX
产品型号
UFP
项目组长
XXX
序阶 号段
立 项 和 1组 织 准 备
过 2
程 设 计 开 发
输入/输出
项目/内容
相应的 支件/资料
责任部门/ 完成日期
1.1 顾客的信息 与顾客沟通,达成试制销轴的意向
电话记录本
销售部/ 06.8.1
总经理/各部门
06.8.15
行性承诺》,确定关键过程
小组可行性承诺
设计开发输 编制设计开发任务书,评审输入适宜性和充分 新产品设计开发任务书 多方认证小组/
2.1
入及其评审 性、是否完整清楚不自相矛盾
评审会议记录
06.8.1
顾客包装要 索取顾客对包装的要求,收集包装规范,作为 工程规范、
2.2
求
编制包装规范的依据
质量策划总 3.9 结认定和管 对 APQP 过程总结认定
理者支持
多方认证小组/
产品质量策划总结认定 06.10
完成 完成 完成 完成 完成 完成 完成 完成 完成
XXX/8.18 XXX/9.8 XXX/9.15 XXX/9.18-30 XXX/10.2 XXX/10.8 XXX/10.9 XXX/10.9 XXX/10.10
2.16 管理者支持
总经理参入过程设计开发资源配置(设备、工 工装、模具、量辅具计 装、量辅具)承诺支持,编制工装、模具计划 划
总经理/ 全过程时段 06.8-06.10
产 3
品
和
过
程
确
认
3.1 试生产
按正式生产的工装、设备进行作业
测量系统 3.3
分析
进行 MSA 并报告结论
过程初始能 3.4 力 研 究 分 析 初始过程性能分析报告评价
成立多方 成立以副总为组长的 APQP 小组,并明确小组 APQP 小组成员及职责
1.2
负责人
论证小组 成员职责分工
分配表
06.8.2
小组分析顾客图样,明确理解顾客期望,根据 产品要求记录单、
多 方 论 证 小 小组经验进行可行性初期策划,确定初始材料 产品和过程特殊特性清 多方认证小组/
1.3
组确定项目 清单及特殊特性, 小组成员同时签署《小组可 单、
编制 PPAP 资料 4.0 生产件批准
PPAP 提交
PPAP 资料 PPAP 提交
技质部/销售部 06.10
反 馈 评 定 4和 纠 正 措 施
4.1 减少变差
分析过程,减少变差,制定不合格品优先减少 不合格品优先减少计划、 多方认证小组/
计划并跟踪验证,进行持续改进
质量跟踪表
06.10
对顾客走访,调查,收集顾客满意度信息, 4.2 顾客满意度