SMT用焊锡膏知识介绍和使用过程中常见问题之原因分析报告
焊锡膏使用常见问题分析
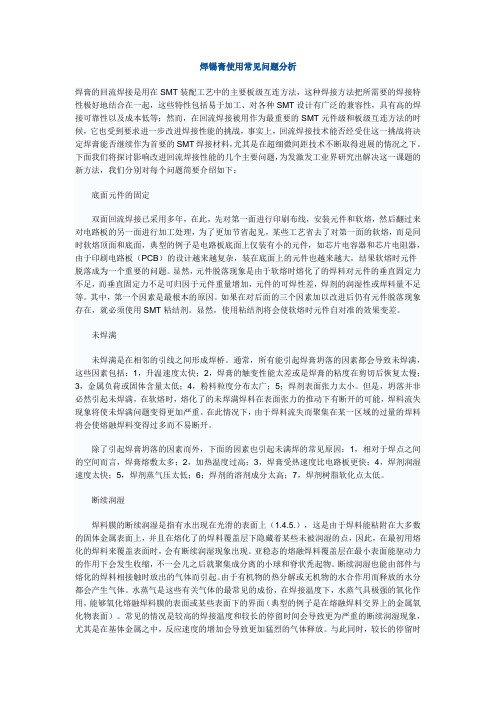
焊锡膏使用常见问题分析焊膏的回流焊接是用在SMT装配工艺中的主要板级互连方法,这种焊接方法把所需要的焊接特性极好地结合在一起,这些特性包括易于加工、对各种SMT设计有广泛的兼容性,具有高的焊接可靠性以及成本低等;然而,在回流焊接被用作为最重要的SMT元件级和板级互连方法的时候,它也受到要求进一步改进焊接性能的挑战,事实上,回流焊接技术能否经受住这一挑战将决定焊膏能否继续作为首要的SMT焊接材料,尤其是在超细微间距技术不断取得进展的情况之下。
下面我们将探讨影响改进回流焊接性能的几个主要问题,为发激发工业界研究出解决这一课题的新方法,我们分别对每个问题简要介绍如下:底面元件的固定双面回流焊接已采用多年,在此,先对第一面进行印刷布线,安装元件和软熔,然后翻过来对电路板的另一面进行加工处理,为了更加节省起见,某些工艺省去了对第一面的软熔,而是同时软熔顶面和底面,典型的例子是电路板底面上仅装有小的元件,如芯片电容器和芯片电阻器,由于印刷电路板(PCB)的设计越来越复杂,装在底面上的元件也越来越大,结果软熔时元件脱落成为一个重要的问题。
显然,元件脱落现象是由于软熔时熔化了的焊料对元件的垂直固定力不足,而垂直固定力不足可归因于元件重量增加,元件的可焊性差,焊剂的润湿性或焊料量不足等。
其中,第一个因素是最根本的原因。
如果在对后面的三个因素加以改进后仍有元件脱落现象存在,就必须使用SMT粘结剂。
显然,使用粘结剂将会使软熔时元件自对准的效果变差。
未焊满未焊满是在相邻的引线之间形成焊桥。
通常,所有能引起焊膏坍落的因素都会导致未焊满,这些因素包括:1,升温速度太快;2,焊膏的触变性能太差或是焊膏的粘度在剪切后恢复太慢;3,金属负荷或固体含量太低;4,粉料粒度分布太广;5;焊剂表面张力太小。
但是,坍落并非必然引起未焊满,在软熔时,熔化了的未焊满焊料在表面张力的推动下有断开的可能,焊料流失现象将使未焊满问题变得更加严重。
在此情况下,由于焊料流失而聚集在某一区域的过量的焊料将会使熔融焊料变得过多而不易断开。
SMT产品常见不良及其原因分析_产品不良的分类

SMT产品常见不良及其原因分析_产品不良的分类SMT 产品常见不良及其原因分析_产品不良的分类SMT 常见不良及其原因分析一. 主要不良分析主要不良分析.锡珠(Solder Balls):1. 丝印孔与焊盘不对位,印刷不精确,使锡膏弄脏PCB 。
2. 锡膏在氧化环境中暴露过多、吸空气中水份太多。
3. 加热不精确,太慢并不均匀.4. 加热速率太快并预热区间太长。
5. 锡膏干得太快。
6. 助焊剂活性不够。
7. 太多颗粒小的锡粉。
8. 回流过程中助焊剂挥发性不适当。
锡球的工艺认可标准是:当焊盘或印制导线的之间距离为0.13mm 时,锡珠直径不能超过0.13mm ,或者在600mm平方范围内不能出现超过五个锡珠。
锡桥(Bridge solder):1. 锡膏太稀, 包括锡膏内金属或固体含量低、摇溶性低、锡膏容易榨开.2. 锡膏颗粒太大、助焊剂表面张力太小.3. 焊盘上太多锡膏.4. 回流温度峰值太高等.开路(Open):1. 锡膏量不够.2. 组件引脚的共面性不够.3. 锡湿不够(不够熔化、流动性不好) ,锡膏太稀引起锡流失.4. 引脚吸锡(象灯芯草一样) 或附近有联机孔. 引脚吸锡可以通过放慢加热速度和底面加热多、上面加热少来防止.5. 焊锡对引脚不熔湿, 干燥时间过长引起助焊剂失效、回流温度过高/时间过长引起氧化.6. 焊盘氧化, 焊锡没熔焊盘.墓碑(Tombstoning/Part shift):墓碑通常是不相等的熔湿力的结果,使得回流后组件在一端上站起来, 一般加热越慢,板越平稳,越少发生。
降低装配通过183° C 的温升速率将有助于校正这个缺陷。
空洞:是锡点的X 光或截面检查通常所发现的缺陷。
空洞是锡点内的微小“气泡”, 可能是被夹住的空气或助焊剂。
空洞一般由三个曲线错误所引起:不够峰值温度;回流时间不够;升温阶段温度过高。
造成没挥发的助焊剂被夹住在锡点内。
这种情况下,为了避免空洞的产生,应在空洞发生的点测量温度曲线,适当调整直到问题解决。
焊锡膏及其使用
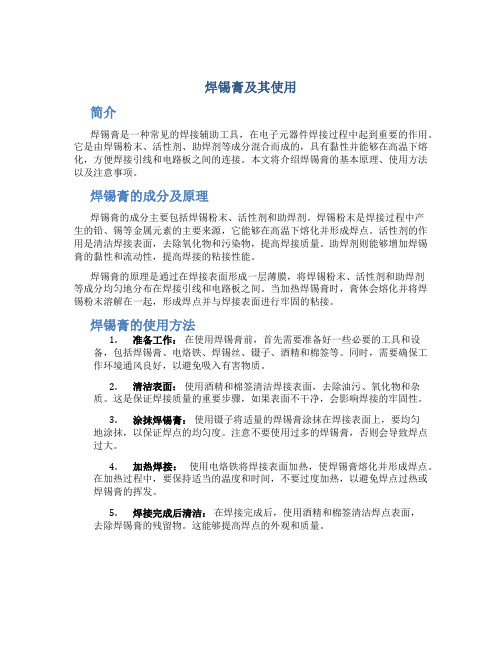
焊锡膏及其使用简介焊锡膏是一种常见的焊接辅助工具,在电子元器件焊接过程中起到重要的作用。
它是由焊锡粉末、活性剂、助焊剂等成分混合而成的,具有黏性并能够在高温下熔化,方便焊接引线和电路板之间的连接。
本文将介绍焊锡膏的基本原理、使用方法以及注意事项。
焊锡膏的成分及原理焊锡膏的成分主要包括焊锡粉末、活性剂和助焊剂。
焊锡粉末是焊接过程中产生的铅、锡等金属元素的主要来源,它能够在高温下熔化并形成焊点。
活性剂的作用是清洁焊接表面,去除氧化物和污染物,提高焊接质量。
助焊剂则能够增加焊锡膏的黏性和流动性,提高焊接的粘接性能。
焊锡膏的原理是通过在焊接表面形成一层薄膜,将焊锡粉末、活性剂和助焊剂等成分均匀地分布在焊接引线和电路板之间。
当加热焊锡膏时,膏体会熔化并将焊锡粉末溶解在一起,形成焊点并与焊接表面进行牢固的粘接。
焊锡膏的使用方法1.准备工作:在使用焊锡膏前,首先需要准备好一些必要的工具和设备,包括焊锡膏、电烙铁、焊锡丝、镊子、酒精和棉签等。
同时,需要确保工作环境通风良好,以避免吸入有害物质。
2.清洁表面:使用酒精和棉签清洁焊接表面,去除油污、氧化物和杂质。
这是保证焊接质量的重要步骤,如果表面不干净,会影响焊接的牢固性。
3.涂抹焊锡膏:使用镊子将适量的焊锡膏涂抹在焊接表面上,要均匀地涂抹,以保证焊点的均匀度。
注意不要使用过多的焊锡膏,否则会导致焊点过大。
4.加热焊接:使用电烙铁将焊接表面加热,使焊锡膏熔化并形成焊点。
在加热过程中,要保持适当的温度和时间,不要过度加热,以避免焊点过热或焊锡膏的挥发。
5.焊接完成后清洁:在焊接完成后,使用酒精和棉签清洁焊点表面,去除焊锡膏的残留物。
这能够提高焊点的外观和质量。
焊锡膏的注意事项1.遵循安全操作:在使用焊锡膏时,要注意安全操作,避免直接接触皮肤和眼睛。
使用时应佩戴手套和护目镜,避免焊接过程中的飞溅和烟尘对身体的危害。
2.注意通风:焊锡膏使用过程中会产生一定的烟尘和挥发物,建议在通风良好的环境下进行操作,以避免吸入有害物质。
SMT常见不良现象原因分析报告

缺锡 摇动 手印锡膏
零件沾锡性差
库存条件不佳
使用 过久
含助 量焊
过 大
粒 子
周 期
过 使
剂 径用
膏
黏 性亲 度 低金 高属
通风设备不好
心情不佳 手拨零件
力度 不饱 不够 满
零件掉落地上
零件尺寸不符 无尘布起毛
手印台钢板偏移
锡膏搅拌 不均
炉温曲线的测量 钢板开口方式
手印台不洁
停电
其他
PCB 上有 染物
轨道残留锡膏 机器置件不稳
机器
Nozzle Size Error
part data
置件速 度过快
真空 不畅
置件偏移
吃锡
不良
環境
人
材料
溼度影響錫膏特性
拿零件未戴手套 未做好來料檢驗
工作態度 錫 膏被抹掉
熟練程度
工作壓力
鋼板
零 件 拆 真 空 包 裝 后氧 化
手放散 料
鋼 板 未抆 拭 干 淨
錫 膏 添 加 不及 時
錫尖
無塵布使用 次數過多
人為點 錫/點漆 零件 管制
軌道 內有 異物
參數 設定 不當
水平
排風 不通
角度
鋼板 張力
鋼板 材質
開口 規格
鋼板 厚度
鋼板
錫膏 選
回焊爐
擇不 當
錫膏的管制
機 器的保養 未依 SOP
溫度 設定 預熱
抽
鋼 板底 貼 紙多
開口 不良
表面 粗糙
鋼板不 平
損壞
不當
不足
風
置件
T able
两边 不一致
有小孔 表面 内距 不洁 损伤
SMT知识介绍和常见问题分析.pptx
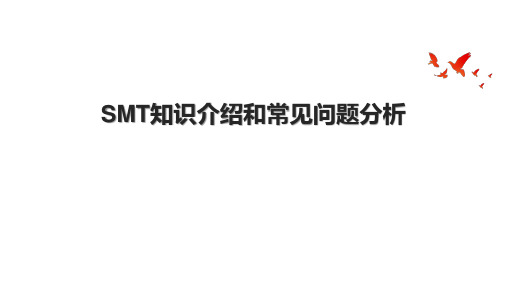
焊料粉又称锡粉生要由锡铅合金组成,一股比例为63/37;另有特殊要求时,也有在锡铅合金中添加肯定破的银 、锡等金属的锡粉”概括来讲锡粉的相关特性与其品质要求方如下几点:
A、锡粉的颗粒形态对锡膏的工作性能有很大的影响:
A-U重要的一点是要求锡粉颗粒大小分布匀称,这里要谈到锡粉颗粒度分布比例的问题;在国内的焊料粉或焊 锡膏生产厂商,大家常常用分布比例来衡量锡粉的匀称度:以25~45μm的锡粉为例,通常要求35Um左右的颗粒分 度比例为60%左右,35μm以卜与以上部份各占20%左右;
SMT知识介绍和常见问题分析
SMT焊锡膏学问介绍之二:锡青的分类方式与选择标准
锡存的分类方式与选择标准
一般状况下,首先选择焊锡密大类,再依据合金组成、颗粒度、粘度等指标来选择。
(一)、分类方式:
A、一般松香清洗型[分RA(R。SINACTIVATED)与RMA(R。SINMI1.D1.YACTIVATED)):此种类型锡膏在焊接 过程中表现出较好“上锡速度”并能保证良好的“焊接效果”;在焊接工作完成后,PCB表面松香残留相对较多,可用适 当清洗剂清洗,清洗后板面光滑无残留,保证r清洗后的板面具有良好的绝缘阻抗,并能通过各种电气性能的技术检 测;B、免清洗型焊锡膏[NC(N。C1.EAN)]:此种锡膏焊接完成后,PCB板面较为光滑、残留少,可通过各种电气 性能技术检测,不须要再次清洗,在保证焊接品质的同时缩短了生产流程,加快了生产进度;
・两端白色挡锡块可以依据PCB的长度调整至合理的印刷宽度,锡膏可以依据PCB宽度来确定锡音的投放,大 大削减锡育作无效滚动。
・挡锡块的底部与钢网紧密贴合,使锡华不易从挡锡块两边溢出,这样可以保证锡育在疗效的丝印区域滚动运 用,削减由于助焊剂挥发,锡粉辄化,锡膏粘度变小等引起的印刷品质不良
SMT用焊锡膏知识介绍及其使用过程中常见问题之原因分析
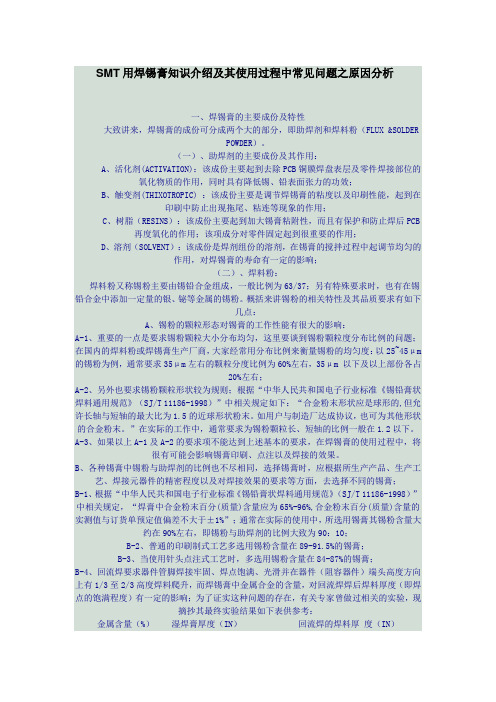
SMT用焊锡膏知识介绍及其使用过程中常见问题之原因分析一、焊锡膏的主要成份及特性大致讲来,焊锡膏的成份可分成两个大的部分,即助焊剂和焊料粉(FLUX &SOLDERPOWDER)。
(一)、助焊剂的主要成份及其作用:A、活化剂(ACTIVATION):该成份主要起到去除PCB铜膜焊盘表层及零件焊接部位的氧化物质的作用,同时具有降低锡、铅表面张力的功效;B、触变剂(THIXOTROPIC) :该成份主要是调节焊锡膏的粘度以及印刷性能,起到在印刷中防止出现拖尾、粘连等现象的作用;C、树脂(RESINS):该成份主要起到加大锡膏粘附性,而且有保护和防止焊后PCB再度氧化的作用;该项成分对零件固定起到很重要的作用;D、溶剂(SOLVENT):该成份是焊剂组份的溶剂,在锡膏的搅拌过程中起调节均匀的作用,对焊锡膏的寿命有一定的影响;(二)、焊料粉:焊料粉又称锡粉主要由锡铅合金组成,一般比例为63/37;另有特殊要求时,也有在锡铅合金中添加一定量的银、铋等金属的锡粉。
概括来讲锡粉的相关特性及其品质要求有如下几点:A、锡粉的颗粒形态对锡膏的工作性能有很大的影响:A-1、重要的一点是要求锡粉颗粒大小分布均匀,这里要谈到锡粉颗粒度分布比例的问题;在国内的焊料粉或焊锡膏生产厂商,大家经常用分布比例来衡量锡粉的均匀度:以25~45μm 的锡粉为例,通常要求35μm左右的颗粒分度比例为60%左右,35μm 以下及以上部份各占20%左右;A-2、另外也要求锡粉颗粒形状较为规则;根据“中华人民共和国电子行业标准《锡铅膏状焊料通用规范》(SJ/T 11186-1998)”中相关规定如下:“合金粉末形状应是球形的,但允许长轴与短轴的最大比为1.5的近球形状粉末。
如用户与制造厂达成协议,也可为其他形状的合金粉末。
”在实际的工作中,通常要求为锡粉颗粒长、短轴的比例一般在1.2以下。
A-3、如果以上A-1及A-2的要求项不能达到上述基本的要求,在焊锡膏的使用过程中,将很有可能会影响锡膏印刷、点注以及焊接的效果。
SMT用焊锡膏使用过程中常见问题之原因分析报告
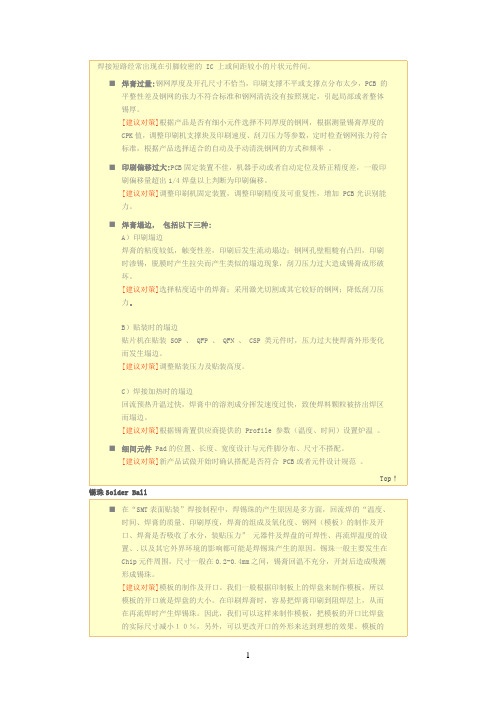
焊接短路经常出现在引脚较密的 IC 上或间距较小的片状元件间。
■焊膏过量:钢网厚度及开孔尺寸不恰当,印刷支撑不平或支撑点分布太少,PCB 的平整性差及钢网的张力不符合标准和钢网清洗没有按照规定,引起局部或者整体锡厚。
[建议对策]根据产品是否有细小元件选择不同厚度的钢网,根据测量锡膏厚度的CPK值,调整印刷机支撑块及印刷速度、刮刀压力等参数,定时检查钢网张力符合标准,根据产品选择适合的自动及手动清洗钢网的方式和频率。
■印刷偏移过大:PCB固定装置不佳,机器手动或者自动定位及矫正精度差,一般印刷偏移量超出1/4焊盘以上判断为印刷偏移。
[建议对策]调整印刷机固定装置,调整印刷精度及可重复性,增加 PCB光识别能力。
■焊膏塌边,包括以下三种:A)印刷塌边焊膏的粘度较低,触变性差,印刷后发生流动塌边;钢网孔壁粗糙有凸凹,印刷时渗锡,脱膜时产生拉尖而产生类似的塌边现象,刮刀压力过大造成锡膏成形破坏。
[建议对策]选择粘度适中的焊膏;采用激光切割或其它较好的钢网;降低刮刀压力。
B)贴装时的塌边贴片机在贴装 SOP 、 QFP 、 QFN 、 CSP 类元件时,压力过大使焊膏外形变化而发生塌边。
[建议对策]调整贴装压力及贴装高度。
C)焊接加热时的塌边回流预热升温过快,焊膏中的溶剂成分挥发速度过快,致使焊料颗粒被挤出焊区而塌边。
[建议对策]根据锡膏置供应商提供的 Profile 参数(温度、时间)设置炉温。
■细间元件 Pad的位置、长度、宽度设计与元件脚分布、尺寸不搭配。
[建议对策]新产品试做开始时确认搭配是否符合 PCB或者元件设计规范。
Top↑锡珠Solder Ball■在“SMT表面贴装”焊接制程中,焊锡珠的产生原因是多方面,回流焊的“温度、时间、焊膏的质量、印刷厚度,焊膏的组成及氧化度、钢网(模板)的制作及开口、焊膏是否吸收了水分,装贴压力” 元器件及焊盘的可焊性、再流焊温度的设置、.以及其它外界环境的影响都可能是焊锡珠产生的原因。
SMT常见不良原因分析

SMT常见不良原因分析一.锡球:1.印刷前,锡膏未充分回温解冻并搅拌均匀。
2.印刷后太久未回流,溶剂挥发,膏体变成干粉后掉到油墨上。
3.印刷太厚,元件下压后多余锡膏溢流。
4.REFLOW时升温过快(SLOPE>3),引起爆沸。
5.贴片压力太大,下压使锡膏塌陷到油墨上。
6.环境影响:湿度过大,正常温度25+/-5,湿度40-60%,下雨时可达95%,需要抽湿。
7.焊盘开口外形不好,未做防锡珠处理。
8.锡膏活性不好,干的太快,或有太多颗粒小的锡粉。
9.锡膏在氧化环境中暴露过久,吸收空气中的水分。
10.预热不充分,加热太慢不均匀。
11.印刷偏移,使部分锡膏沾到PCB上。
12.刮刀速度过快,引起塌边不良,回流后导致产生锡球。
P.S:锡球直径要求小于0.13MM,或600平方毫米小于5个.二、立碑:1.印刷不均匀或偏移太多,一侧锡厚,拉力大,另一侧锡薄拉力小,致使元件一端被拉向一侧形成空焊,一端被拉起就形成立碑。
2.贴片偏移,引起两侧受力不均。
3.一端电极氧化,或电极尺寸差异太大,上锡性差,引起两端受力不均。
4.两端焊盘宽窄不同,导致亲和力不同。
5.锡膏印刷后放置过久,FLUX挥发过多而活性下降。
6.REFLOW预热不足或不均,元件少的地方温度高,元件多的地方温度低,温度高的地方先熔融,焊锡形成的拉力大于锡膏对元件的粘接力,受力不均匀引起立碑。
三、短路1.STENCIL太厚、变形严重,或STENCIL开孔有偏差,与PCB焊盘位置不符。
2.钢板未及时清洗。
3.刮刀压力设置不当或刮刀变形。
4.印刷压力过大,使印刷图形模糊。
5.回流183度时间过长,(标准为40-90S),或峰值温度过高。
6.来料不良,如IC引脚共面性不佳。
7.锡膏太稀,包括锡膏内金属或固体含量低,摇溶性低,锡膏容易榨开。
8.锡膏颗粒太大,助焊剂表面张力太小。
四、偏移:一).在REFLOW之前已经偏移:1.贴片精度不精确。
2.锡膏粘接性不够。
SMT常见不良及原因分析

SMT常见不良及原因分析1、立碑产生原因:通常由于回流焊时元件两端的湿润力不平衡,引发元件两端的力矩也不平衡,导致“立碑”。
成因分析因素A:焊盘设计与布局不合理①元件的两边焊盘之一与地线相连接或有一侧焊盘面积过大,焊盘两端热容量不均匀;②PCB表面各处的温差过大以致元件焊盘两边吸热不均匀;③大型器件QFP、BGA、散热器周围的小型片式元件焊盘两端会出现温度不均匀。
解决方法:工程师调整焊盘设计和布局因素B:焊锡膏与焊锡膏印刷存在问题①焊锡膏的活性不高或元件的可焊性差,焊锡膏熔化后,表面张力不一样,将引起焊盘湿润力不平衡。
②两焊盘的焊锡膏印刷量不均匀,一侧锡厚,拉力大,另一侧锡薄拉力小,致使元件一端被拉向一侧形成空焊,一端被拉起就形成立碑。
解决办法:需工厂选用活性较高的焊锡膏,改善焊锡膏印刷参数,特别是钢网的窗口尺寸因素C:贴片移位Z轴方向受力不均匀该情况会导致元件浸入到焊锡膏中的深度不均匀,熔化时会因时间差而导致两边的湿润力不平衡,如果元件贴片移位会直接导致立碑。
解决办法:调节贴片机工艺参数因素D:炉温曲线不正确如果回流焊炉炉体过短和温区太少就会造成对PCB加热的工作曲线不正确,以致板面上湿差过大,从而造成湿润力不平衡。
解决办法:需要工厂根据每种不同产品调节好适当的温度曲线2、“锡珠”现象产生原因:它不仅影响外观而且会引起桥接(下文会讲)。
锡珠可分两类:一类出现在片式元器件一侧,常为一个独立的大球状(如下图1);另一类出现在IC 引脚四周,呈分散的小珠状。
因素A:温度曲线不正确回流焊曲线可以分为预热、保温、回流和冷却4个区段。
预热、保温的目的是为了使PCB表面温度在60~90s内升到150℃,并保温约90s,这不仅可以降低PCB 及元件的热冲击,更主要是确保焊锡膏的溶剂能部分挥发,避免回流焊时因溶剂太多引起飞溅,造成焊锡膏冲出焊盘而形成锡珠。
解决办法:工厂需注意升温速率,并采取适中的预热,使溶剂充分挥发因素B:焊锡膏的质量①焊锡膏中金属含量通常在(90±0.5)℅,金属含量过低会导致助焊剂成分过多,因此过多的助焊剂会因预热阶段不易挥发而引起飞珠;②焊锡膏中水蒸气和氧含量增加也会引起飞珠。
SMT不良分析报告

空焊现象的产生可能是由于焊盘与焊料之间的润湿性差、焊点尺寸过小、焊接 温度过低等原因所致。空焊可能导致电气连接不良、机械连接不稳定等问题, 影响电子产品的性能和可靠性。
短路现象
总结词
短路是指SMT加工过程中,两个原本 不应该连接的焊点意外地形成了连接 的现象。
详细描述
短路现象的产生可能是由于焊料飞溅 、元器件贴装位置偏差、焊盘重叠等 原因所致。短路可能导致电路功能异 常、安全风险等问题,影响电子产品 的性能和可靠性。
提高焊接温度和时间
适当提高焊接温度和时间,确 保焊点充分熔融、浸润,减少 空焊现象的产生。
控制焊膏量
根据焊接需求,合理调整焊膏 量,确保焊点表面光滑、饱满 。
加强工艺控制
定期对设备和工艺进行检查和 校准,确保工艺稳定、可靠。
短路现象的预防措施
短路现象
在SMT工艺中,由于焊点之间存在杂质 或气泡等原因,可能导致焊接后出现短
锡珠
在焊接过程中,锡 膏熔化后形成的小 珠状突起。
冷焊
焊接点表面不光滑 ,呈现凹凸不平的 状态。
元件移位
元件在焊接过程中 位置发生偏移。
CHAPTER 02
SMT不良现象分析
锡珠现象
总结词
锡珠是指在SMT加工过程中,焊料在经过回流焊后形成的球状物,通常出现在焊 点周围。
详细描述
锡珠现象的产生通常是由于焊料在熔融状态下受到重力、表面张力以及温度梯度 的影响,导致焊料在冷却过程中无法完全回流,从而形成球状物。锡珠可能导致 电气连接不良、机械卡滞等问题,影响电子产品的性能和可靠性。
选用低残留焊膏
选择低残留、低松香含量的焊 膏,减少锡珠形成。
锡珠现象
在SMT工艺中,由于焊膏过多 或温度过高,导致焊膏在回流 过程中形成锡珠状残留物。
SMT不良分析报告

SMT不良分析报告一、概述本报告旨在分析SMT(Surface Mount Technology,表面贴装技术)生产过程中的不良现象,并提供相应的解决方案。
SMT是一种将电子元件贴装到PCB板表面的技术,具有高效、高精度、高可靠性等优点。
然而,在实际生产过程中,由于各种原因会导致SMT不良现象的发生。
二、SMT不良现象分类1、元件贴装不良:元件贴装位置偏离、倾斜、立碑等现象。
2、焊接不良:焊接点缺陷、虚焊、冷焊等现象。
3、元件质量问题:元件本身存在缺陷,如破损、功能不良等。
4、PCB板质量问题:PCB板存在缺陷,如划伤、变形、污染等。
5、操作不当:操作人员技能不足、操作不规范等导致的不良。
三、SMT不良原因分析1、元件贴装不良原因:a)贴装设备精度不高;b)操作人员技能不足;c)定位基准不准确;d)元件本身质量问题。
2、焊接不良原因:a)温度和时间控制不当;b)焊点表面污染;c)元件和PCB板质量问题;d)焊接设备故障或参数设置不当。
3、元件质量问题原因:a)供应商质量控制不严格;b)运输和存储过程中损坏;c)生产过程中质量控制不严格。
4、PCB板质量问题原因:a)供应商质量控制不严格;b) PCB板制作过程中出现缺陷;c) PCB板运输和存储过程中损坏。
5、操作不当原因:a)操作人员技能培训不足;b)操作流程不完善;c)质量控制意识不强。
四、SMT不良解决方案1、提高设备精度:对贴装设备和焊接设备进行定期维护和校准,确保设备精度在规定范围内。
2、加强操作人员技能培训:定期组织技能培训,提高操作人员的技能水平。
3、完善操作流程:制定严格的SMT操作流程,确保操作人员严格按照规定进行操作。
4、加强来料质量控制:对供应商进行严格筛选,并对来料进行严格的质量控制。
同时,加强存储和运输过程中的保护措施,防止元件和PCB板损坏。
5、加强生产过程中的质量控制:建立完善的质量控制体系,对每个生产环节进行严格的质量监控。
SMT焊点常见问题及解决方法有哪些

SMT焊点常见问题及解决方法有哪些SMT焊点常见问题及解决方法有哪些,我们一起了解一下:1.1、拉丝/拖尾1.1.1、拉丝/拖尾是点胶中常见的缺陷,产生的原因常见有胶嘴内径太小、点胶压力太高、胶嘴离PCB的间距太大、贴片胶过期或品质不好、贴片胶粘度太好、从冰箱中取出后未能恢复到室温、点胶量太大等.1.1.2、解决办法:改换内径较大的胶嘴;降低点胶压力;调节“止动”高度;换胶,选择合适粘度的胶种;贴片胶从冰箱中取出后应恢复到室温(约4h)再投入生产;调整点胶量.1.2、胶嘴堵塞1.2.1、故障现象是胶嘴出胶量偏少或没有胶点出来.产生原因一般是针孔内未完全清洗干净;贴片胶中混入杂质,有堵孔现象;不相溶的胶水相混合.1.2.2解决方法:换清洁的针头;换质量好的贴片胶;贴片胶牌号不应搞错.1.3、空打1.3.1、现象是只有点胶动作,却无出胶量.产生原因是贴片胶混入气泡;胶嘴堵塞.1.3.2、解决方法:注射筒中的胶应进行脱气泡处理(特别是自己装的胶);更换胶嘴.1.4、元器件移位1.4.1、现象是贴片胶固化后元器件移位,严重时元器件引脚不在焊盘上.产生原因是贴片胶出胶量不均匀,例如片式元件两点胶水中一个多一个少;贴片时元件移位或贴片胶初粘力低;点胶后PCB放置时间太长胶水半固化.1.4.2、解决方法:检查胶嘴是否有堵塞,排除出胶不均匀现象;调整贴片机工作状态;换胶水;点胶后PCB放置时间不应太长(短于4h)1.5、波峰焊后会掉片1.5.1、现象是固化后元器件粘结强度不够,低于规定值,有时用手触摸会出现掉片.产生原因是因为固化工艺参数不到位,特别是温度不够,元件尺寸过大,吸热量大;光固化灯老化;胶水量不够;元件/PCB有污染.1.5.2、解决办法:调整固化曲线,特别是提高固化温度,通常热固化胶的峰值固化温度为150℃左右,达不到峰值温度易引起掉片.对光固胶来说,应观察光固化灯是否老化,灯管是否有发黑现象;胶水的数量和元件/PCB是否有污染都是应该考虑的问题.1.6、固化后元件引脚上浮/移位1.6.1、这种故障的现象是固化后元件引脚浮起来或移位,波峰焊后锡料会进入焊盘下,严重时会出现短路、开路.产生原因主要是贴片胶不均匀、贴片胶量过多或贴片时元件偏移.1.6.2、解决办法:调整点胶工艺参数;控制点胶量;调整贴片工艺参数.二、焊锡膏印刷与贴片质量分析焊锡膏印刷质量分析由焊锡膏印刷不良导致的品质问题常见有以下几种:①、焊锡膏不足(局部缺少甚至整体缺少)将导致焊接后元器件焊点锡量不足、元器件开路、元器件偏位、元器件竖立.②、焊锡膏粘连将导致焊接后电路短接、元器件偏位.③、焊锡膏印刷整体偏位将导致整板元器件焊接不良,如少锡、开路、偏位、竖件等.④、焊锡膏拉尖易引起焊接后短路.深圳市盛鸿德电子有限公司(深圳市易连科技开发有限公司)是一家专注于SMT贴片加工、OEM及ODM专业服务、PCB及物料代采购、中高端蓝牙方案(“易连”模块)定制开发及电子产品定制生产的公司;特别是研发样板及中小批量OEM在物料代采购、SMT贴片加工、后焊、测试组装等全流程在性价比、质量保证、快速交付等方面有极大优势,受到了广大客户的欢迎和一致肯定.公司PCBA工厂高起点规划,占地面积近2000平,位于西乡固戍,在交通便利的107国道旁,现有人员120名,采用二十余年资深团队进行专业规范的SMT工厂管理,其中中高级人才30名,研发人员6名,获得ISO9000及部分产品的UL认证。
SMT常见不良及原因分析

SMT常见不良及原因分析1、立碑产生原因:通常由于回流焊时元件两端的湿润力不平衡,引发元件两端的力矩也不平衡,导致“立碑”。
成因分析因素A:焊盘设计与布局不合理①元件的两边焊盘之一与地线相连接或有一侧焊盘面积过大,焊盘两端热容量不均匀;②PCB表面各处的温差过大以致元件焊盘两边吸热不均匀;③大型器件QFP、BGA、散热器周围的小型片式元件焊盘两端会出现温度不均匀。
解决方法:工程师调整焊盘设计和布局因素B:焊锡膏与焊锡膏印刷存在问题①焊锡膏的活性不高或元件的可焊性差,焊锡膏熔化后,表面张力不一样,将引起焊盘湿润力不平衡。
②两焊盘的焊锡膏印刷量不均匀,一侧锡厚,拉力大,另一侧锡薄拉力小,致使元件一端被拉向一侧形成空焊,一端被拉起就形成立碑。
解决办法:需工厂选用活性较高的焊锡膏,改善焊锡膏印刷参数,特别是钢网的窗口尺寸因素C:贴片移位Z轴方向受力不均匀该情况会导致元件浸入到焊锡膏中的深度不均匀,熔化时会因时间差而导致两边的湿润力不平衡,如果元件贴片移位会直接导致立碑。
解决办法:调节贴片机工艺参数因素D:炉温曲线不正确如果回流焊炉炉体过短和温区太少就会造成对PCB加热的工作曲线不正确,以致板面上湿差过大,从而造成湿润力不平衡。
解决办法:需要工厂根据每种不同产品调节好适当的温度曲线2、“锡珠”现象产生原因:它不仅影响外观而且会引起桥接(下文会讲)。
锡珠可分两类:一类出现在片式元器件一侧,常为一个独立的大球状(如下图1);另一类出现在IC 引脚四周,呈分散的小珠状。
因素A:温度曲线不正确回流焊曲线可以分为预热、保温、回流和冷却4个区段。
预热、保温的目的是为了使PCB表面温度在60~90s内升到150℃,并保温约90s,这不仅可以降低PCB 及元件的热冲击,更主要是确保焊锡膏的溶剂能部分挥发,避免回流焊时因溶剂太多引起飞溅,造成焊锡膏冲出焊盘而形成锡珠。
解决办法:工厂需注意升温速率,并采取适中的预热,使溶剂充分挥发因素B:焊锡膏的质量①焊锡膏中金属含量通常在(90±0.5)℅,金属含量过低会导致助焊剂成分过多,因此过多的助焊剂会因预热阶段不易挥发而引起飞珠;②焊锡膏中水蒸气和氧含量增加也会引起飞珠。
SMT制程常见异常分析
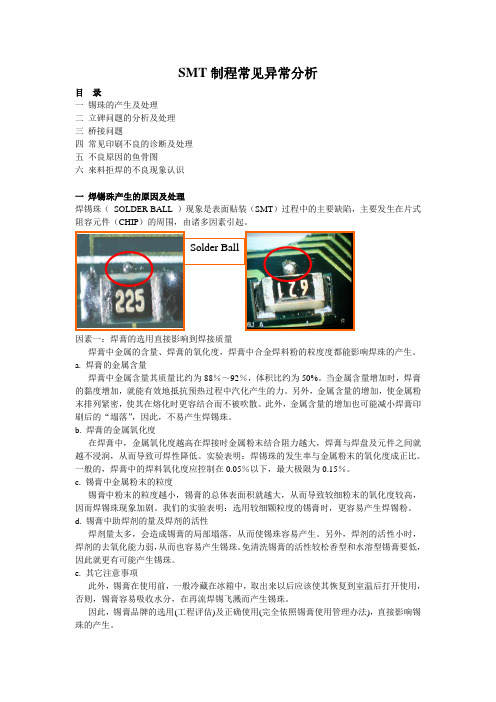
SMT制程常见异常分析目录一锡珠的产生及处理二立碑问题的分析及处理三桥接问题四常见印刷不良的诊断及处理五不良原因的鱼骨图六來料拒焊的不良现象认识一焊锡珠产生的原因及处理焊锡珠(SOLDER BALL )现象是表面贴装(SMT)过程中的主要缺陷,主要发生在片式阻容元件(CHIP)的周围,由诸多因素引起。
S o l d e r B a l l因素一:焊膏的选用直接影响到焊接质量焊膏中金属的含量、焊膏的氧化度,焊膏中合金焊料粉的粒度度都能影响焊珠的产生。
a. 焊膏的金属含量焊膏中金属含量其质量比约为88%~92%,体积比约为50%。
当金属含量增加时,焊膏的黏度增加,就能有效地抵抗预热过程中汽化产生的力。
另外,金属含量的增加,使金属粉末排列紧密,使其在熔化时更容结合而不被吹散。
此外,金属含量的增加也可能减小焊膏印刷后的“塌落”,因此,不易产生焊锡珠。
b. 焊膏的金属氧化度在焊膏中,金属氧化度越高在焊接时金属粉末结合阻力越大,焊膏与焊盘及元件之间就越不浸润,从而导致可焊性降低。
实验表明:焊锡珠的发生率与金属粉末的氧化度成正比。
一般的,焊膏中的焊料氧化度应控制在0.05%以下,最大极限为0.15%。
c. 锡膏中金属粉末的粒度锡膏中粉末的粒度越小,锡膏的总体表面积就越大,从而导致较细粉末的氧化度较高,因而焊锡珠现象加剧。
我们的实验表明:选用较细颗粒度的锡膏时,更容易产生焊锡粉。
d. 锡膏中助焊剂的量及焊剂的活性焊剂量太多,会造成锡膏的局部塌落,从而使锡珠容易产生。
另外,焊剂的活性小时,焊剂的去氧化能力弱,从而也容易产生锡珠。
免清洗锡膏的活性较松香型和水溶型锡膏要低,因此就更有可能产生锡珠。
e. 其它注意事项此外,锡膏在使用前,一般冷藏在冰箱中,取出来以后应该使其恢复到室温后打开使用,否则,锡膏容易吸收水分,在再流焊锡飞溅而产生锡珠。
因此,锡膏品牌的选用(工程评估)及正确使用(完全依照锡膏使用管理办法),直接影响锡珠的产生。
焊锡膏常见问题分析及解决办法
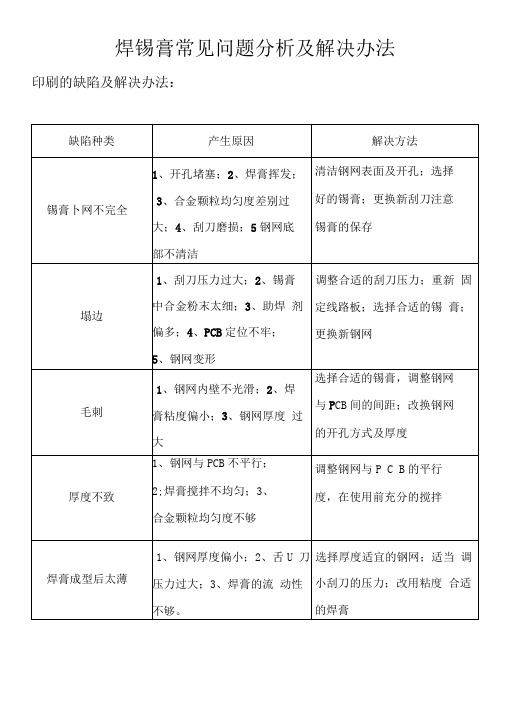
调整合适的刮刀压力;重新 固定线路板;选择合适的锡 膏;更换新钢网
毛刺
1、钢网内壁不光滑;2、焊 膏粘度偏小;3、钢网厚度 过大
选择合适的锡膏,调整钢网
与PCB间的间距;改换与PCB不平行;
2;焊膏搅拌不均匀;3、
合金颗粒均匀度不够
调整钢网与P C B的平行
焊锡膏常见问题分析及解决办法
印刷的缺陷及解决办法:
缺陷种类
产生原因
解决方法
锡膏卜网不完全
1、开孔堵塞;2、焊膏挥发;
3、合金颗粒均匀度差别过 大;4、刮刀磨损;5钢网底 部不清洁
清洁钢网表面及开孔;选择
好的锡膏;更换新刮刀注意
锡膏的保存
塌边
1、刮刀压力过大;2、锡膏 中合金粉末太细;3、助焊 剂偏多;4、PCB定位不牢;
度,在使用前充分的搅拌
焊膏成型后太薄
1、钢网厚度偏小;2、舌U刀压力过大;3、焊膏的流 动性不够。
选择厚度适宜的钢网;适当 调小刮刀的压力;改用粘度 合适的焊膏
SMT用焊锡膏使用过程中常见问题之原因分析报告
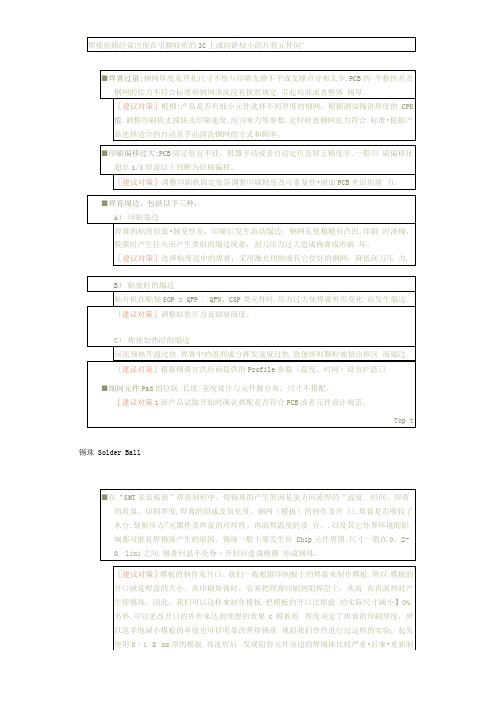
印刷时出现拖尾.粘连.图像模糊等问题印刷在匸艺控制过程中显得尤其重要.这里针对印刷问题做如下I纲述。
■锡膏的」:艺选型不对,锡膏触变性差.或者是焊锡彥保存不、”1或者已过使用期限
粘性被破坏等。
[建议对策]根据自身之工艺条件选择适合黏度等级和锡粉颗粒型号的锡膏•按规 定保存和使用锡膏
■锡膏中的金属成份偏低.助焊剂成份比例偏高所致。
[建议对策]模板的制作及开口。我们一般根据印制板上的焊盘來制作模板.所以 模板的开口就是焊盘的大小。在印刷焊膏时,容易把焊膏印刷到阻焊层上,从而 在再流焊时产生焊锡珠。因此,我们可以这样來制作模板.把模板的开口比焊盘 的实际尺寸减小】0%.另外.可以更改开口的外形來达到理想的效果c模板的 厚度决定了焊膏的印刷厚度,所以适半地减小模板的卑度也可以明显改善焊锡珠 现叙我们曾经进行过这样的实验:起先使用0・18mm厚的模板.再流烬后 发现阻容元件旁边的焊锡珠比较严重•后來•重新制作了一张模板•厚度改为0・15mm,再流焊基木上消除了焊锡珠。
〔建议对策]锡粉与助焊剂重虽比及体枳比应在规定范用内调配C
■刮刀材质、长度选用不、S刮刀损坏,刮刀水平不好,印刷机固定装宜松动或者 不平。
[建议对策]检査涮整刮刀•选用合适的刮刀,调整印刷机固定装宜。
■卬刷机参数设宜不佳,印刷机参数包括印刷速度、刮刀压力、脫膜距离及速度.
清洗频率及清洗方法。
〔建议对策]根据产品特性调整印刷参数C
〔建议对策]根据锡膏宜供应商提供的Profile参数(温度、时间)设宜炉温□
■细间元件Pad的位臥 长度.宽度设汁与元件脚分布、尺寸不搭配。
[建议对策1新产品试做开始时确认搭配是否符合PCB或者元件设计规范。
Top t
锡珠Solder Ball
SMT焊接上锡不良分析

SMT焊接上锡不良分析SMT(Surface Mount Technology,表面贴装技术)焊接是一种常见的电子组装技术,它通过将电子元器件直接焊接在PCB(PrintedCircuit Board,印制电路板)的表面,从而实现更高的装配密度和更好的电气性能。
然而,由于焊接过程中的各种因素,有时会出现上锡不良的情况,影响产品的质量。
本文将针对SMT焊接上锡不良进行分析,分析其可能的原因,并提出相应的解决方案。
首先,上锡不良可能是由于焊接温度不当引起的。
焊接过程中,焊料需要达到足够的熔点才能进行焊接。
如果焊接温度过低,焊料无法完全熔化,导致焊点与PCB之间无法充分接触,从而造成上锡不良。
另一方面,如果焊接温度过高,焊料可能会过度熔化,融化PCB上的电路线路,导致短路或焊点与线路之间的断开。
因此,合理控制焊接温度是解决SMT焊接上锡不良的关键。
其次,上锡不良可能是由于焊接时间不足引起的。
焊接过程中,焊料需要适当的时间才能完全熔化,并形成牢固的连接。
如果焊接时间过短,焊料无法完全融化,焊点与PCB之间的接触不牢固,容易出现冷焊现象,导致上锡不良。
因此,合理控制焊接时间,确保焊料充分熔化是解决上锡不良的重要措施之一第三,上锡不良可能是由于焊接质量不良引起的。
焊接质量主要包括焊料的品质以及焊接工艺的控制。
焊料的成分和纯度会直接影响焊接质量,低质量的焊料容易引起上锡不良。
此外,焊接工艺的控制也十分重要。
例如,焊接时需要控制好焊料的质量,确保其不受空气中的氧气和水蒸气的影响;焊接过程中需要避免PCB或元器件受到机械冲击,以免造成焊接不牢;还需要定期检测焊接设备的状态,保证其正常运行。
最后,上锡不良可能是由于焊接材料不匹配引起的。
焊接材料包括焊料、PCB和元器件等。
如果焊料与PCB或元器件的材料不匹配,会导致焊接困难,从而出现上锡不良。
因此,在进行SMT焊接前,需要仔细选用合适的焊料、PCB和元器件,确保它们的材料相互匹配。
SMT制程不良原因及改善对策

调整印刷机平台的水平度平行度;
6
基板表面异物造成周边元件锡膏印刷 过厚;
基板使用前进行除尘作业;
7
一次面基板背面残留锡膏过炉形成锡 珠,二次面锡膏印刷时垫起钢网形成 多锡;
避免一次面基板粘附锡膏,避免洗 板作业;
8 修理员回锡过多;
指导修理员按标准作业。
11
立起
产生原因
1 铜铂两边大小不一产生拉力不均; 2 预热升温速率太快; 3 机器贴装偏移; 4 锡膏印刷厚度不均; 5 回流焊内温度分布不均; 6 锡膏印刷偏移; 7 机器轨道夹板不紧导致贴装偏移; 8 机器头部晃动贴装偏移; 9 焊盘两端的散热程度不一致融化速度差异; 10 炉温设置不当; 11 铜铂间距过大; 12 MARK点误照造成元件打偏; 13 料架不良,元件吸着不稳打偏; 14 原材料不良; 15 钢网开孔不良;
发形成干锡膏,混入印刷产生钢网堵孔。
改善对策
10
多锡
产生原因
改善对策
1 钢网开孔过大或厚度过厚;
按标准制作钢网;
2 锡膏印刷厚度过厚;
调整印刷参数(压力、脱模等) ;
3 钢网底部粘锡;
清洗钢网;
4 IC元件底部接地焊盘锡膏溢出形成多 接地焊盘开孔适当减小,贴装高度适
锡;
当调高;
5
印刷平台不平行或高于基板导致印刷 多锡;
19 原材料设计不良;
反馈IQC联络供应商;
20 料架中心偏移;
校正料架中心;
21 机器吹气过大将锡膏吹跑;
将贴片吹气调整为0.2mm/cm² ;
22 元件氧化;
更换OK之材料;
23 PCB贴装后长时间没过炉,导致活性剂挥发; 及时将PCB-A过炉,生产过程中避免堆积;
smt虚焊整改报告

竭诚为您提供优质文档/双击可除smt虚焊整改报告篇一:smT常见不良原因分析smT常见不良原因分析一.锡球:1.印刷前,锡膏未充分回温解冻并搅拌均匀。
2.印刷后太久未回流,溶剂挥发,膏体变成干粉后掉到油墨上。
3.印刷太厚,元件下压后多余锡膏溢流。
4.ReFLow时升温过快(sLope>3),引起爆沸。
5.贴片压力太大,下压使锡膏塌陷到油墨上。
6.环境影响:湿度过大,正常温度25+/-5,湿度40-60%,下雨时可达95%,需要抽湿。
7.焊盘开口外形不好,未做防锡珠处理。
8.锡膏活性不好,干的太快,或有太多颗粒小的锡粉。
9.锡膏在氧化环境中暴露过久,吸收空气中的水分。
10.预热不充分,加热太慢不均匀。
11.印刷偏移,使部分锡膏沾到pcb上。
12.刮刀速度过快,引起塌边不良,回流后导致产生锡球。
p.s:锡球直径要求小于0.13mm,或600平方毫米小于5个.二、立碑:1.印刷不均匀或偏移太多,一侧锡厚,拉力大,另一侧锡薄拉力小,致使元件一端被拉向一侧形成空焊,一端被拉起就形成立碑。
2.贴片偏移,引起两侧受力不均。
3.一端电极氧化,或电极尺寸差异太大,上锡性差,引起两端受力不均。
4.两端焊盘宽窄不同,导致亲和力不同。
5.锡膏印刷后放置过久,FLux挥发过多而活性下降。
6.ReFLow预热不足或不均,元件少的地方温度高,元件多的地方温度低,温度高的地方先熔融,焊锡形成的拉力大于锡膏对元件的粘接力,受力不均匀引起立碑。
三、短路1.sTencIL太厚、变形严重,或sTencIL开孔有偏差,与pcb焊盘位置不符。
2.钢板未及时清洗。
3.刮刀压力设置不当或刮刀变形。
4.印刷压力过大,使印刷图形模糊。
5.回流183度时间过长,(标准为40-90s),或峰值温度过高。
6.来料不良,如Ic引脚共面性不佳。
7.锡膏太稀,包括锡膏内金属或固体含量低,摇溶性低,锡膏容易榨开。
8.锡膏颗粒太大,助焊剂表面张力太小。
四、偏移:一).在ReFLow之前已经偏移:1.贴片精度不精确。
SMT 产品常见不良及其原因分析

SMT 产品常见不良及其原因分析一、主要不良分析主要不良分析、锡珠(Solder Balls):1、丝印孔与焊盘不对位,印刷不精确,使锡膏弄脏PCB。
2、锡膏在氧化环境中暴露过多、吸空气中水份太多。
3、加热不精确,太慢并不均匀、4、加热速率太快并预热区间太长。
ﻫ5、锡膏干得太快。
ﻫ6、助焊剂活性不够。
7、太多颗粒小得锡粉。
ﻫ8、回流过程中助焊剂挥发性不适当。
ﻫ锡球得工艺认可标准就是:当焊盘或印制导线得之间距离为0、13mm 时,锡珠直径ﻫ不能超过0、13m m,或者在600mm平方范围内不能出现超过五个锡珠。
ﻫ锡桥(Bridge solder):1、锡膏太稀,包括锡膏内金属或固体含量低、摇溶性低、锡膏容易榨开、ﻫ2、锡膏颗粒太大、助焊剂表面张力太小、ﻫ3、焊盘上太多锡膏、ﻫ4、回流温度峰值太高等、ﻫ开路(Open):1、锡膏量不够、2、组件引脚得共面性不够、3、锡湿不够(不够熔化、流动性不好),锡膏太稀引起锡流失、4、引脚吸锡(象灯芯草一样)或附近有联机孔、引脚吸锡可以通过放慢加热速度与底面加热多、上面加热少来防止、ﻫ5、焊锡对引脚不熔湿, 干燥时间过长引起助焊剂失效、回流温度过高/时间过长引起氧化、6、焊盘氧化,焊锡没熔焊盘、墓碑(Tombstoning/Part shift):墓碑通常就是不相等得熔湿力得结果,使得回流后组件在一端上站起来,一般加热越ﻫ慢,板越平稳,越少发生。
降低装配通过183°C得温升速率将有助于校正这个缺陷。
空洞:ﻫ就是锡点得 X 光或截面检查通常所发现得缺陷。
空洞就是锡点内得微小“气泡”,可能就是被夹住得空气或助焊剂。
空洞一般由三个曲线错误所引起:不够峰值温度;回流时间不够;升温阶段温度过高。
造成没挥发得助焊剂被夹住在锡点内。
这种情况下,为了避ﻫ免空洞得产生,应在空洞发生得点测量温度曲线,适当调整直到问题解决。
二、印刷问题印刷问题ﻫ印刷偏位: ﻫ1、机器换线生产前首片印刷偏移2、PCBmark 不好3、PCB 夾持不好ﻫ4、機器Vision系統出故障及機器 XY Table有問題ﻫﻫ錫膏橋1、鋼板刮傷或張力不足ﻫ2、2、鋼板擦拭不好3、3、鋼板背面膠帶就是否脫落ﻫ4、4、鋼板背面粘有錫膏ﻫ5、5、 PCB 零件面有凸出物6、6、印刷機XY Table傾斜﹐導制與鋼板有間隙7、7、印刷機刮刀水平度校正不良,造成印刷錫膏多錫現象ﻫ錫膏塞孔ﻫ1、錫膏太幹ﻫ2、2、Slow Snapoff Speed 設定太快3、3、 Slow Snapoff distance設定太小ﻫ錫膏下塌ﻫ1、錫膏粘度太低或吸入濕氣ﻫ2、刮刀速度太快ﻫ少印漏印錫膏1、鋼板上錫膏量少2、錫膏粘刮刀ﻫ錫膏拉尖1、 Slow Snap-off速度設置太快ﻫ2、2、 PCB与 STENCIL間隙太大ﻫ3、3、刮刀印刷速度設定太高ﻫ4、4、刮刀壓力設定太低ﻫ5、5、板子支承不夠ﻫ錫膏過薄1、鋼板上錫膏量少2、刮刀印刷速度設定太高ﻫ3、錫膏粘刮刀ﻫﻫ錫膏過厚1、 PCB 零件面有凸出物﹒2、PCB 与 STENCIL間隙太大ﻫ3、刮刀Down stop設定太小ﻫ4、刮刀壓力設定太低三、元件贴装不元件贴装不良问题良问题ﻫ元件偏位1、 Program中定義坐標差异ﻫ2、元件置放速度太快ﻫ3、元件尺寸數据設置錯誤4、元件高度設置錯誤元件出現翻件/側件ﻫ1、料架安放不良ﻫ2、料帶安裝不良3、料架送帶不良ﻫ元件漏件ﻫ1、元件高度設置錯誤2、元件置放速度太快ﻫ3、 Nozzle有螢光紙臟或歪斜現象ﻫ元件拋料ﻫ1、 Camera鏡片臟2、 Nozzle 有螢光紙臟或歪斜現象ﻫ3、元件尺寸數据設置錯誤ﻫ絞帶現象ﻫ1、料帶安裝不良2、料架送帶不良ﻫ四、Reflow四、Reflow不良问题不良问题溫度偏高ﻫ1、爐溫設置太高2、鏈條速度設置太慢ﻫ3、測溫點異常4、熱風頻率設置過大、5、測溫方法不正確、溫度偏低1、爐溫設置太低ﻫ2、鏈條速度設置太快3、測溫點異常4、熱風頻率設置過小、5、測溫方法不正確、熔錫時間太短1、溫度設置不佳ﻫ2、鏈條速度設置太快ﻫ3、測溫點異常4、冷卻速度過快、5、測溫方法不正確、ﻫ熔錫時間太長ﻫ1、溫度設置不佳2、鏈條速度設置太慢ﻫ3、測溫點異常ﻫ4、冷卻速度太慢5、測溫方法不正確、6、測溫方法不正確、ﻫ7、鏈條速度設置太快、ﻫ8、測溫方法不正確、ﻫ升溫斜率太快ﻫ1、溫度設置不佳2、測溫點異常ﻫ3、鏈條速度設置太慢4、測溫方法不正確、ﻫ升溫斜率太慢1、溫度設置不佳ﻫ2、測溫點異常ﻫ3、鏈條速度設置太快、ﻫ4、測溫方法不正確、ﻫﻫ預熱時間太長1、溫度設置不佳ﻫ2、測溫點異常3、鏈條速度設置太快、4、測溫方法不正確、ﻫ預熱時間太短1、溫度設置不佳2、測溫點異常3、鏈條速度設置太快、4、測溫方法不正確、。
- 1、下载文档前请自行甄别文档内容的完整性,平台不提供额外的编辑、内容补充、找答案等附加服务。
- 2、"仅部分预览"的文档,不可在线预览部分如存在完整性等问题,可反馈申请退款(可完整预览的文档不适用该条件!)。
- 3、如文档侵犯您的权益,请联系客服反馈,我们会尽快为您处理(人工客服工作时间:9:00-18:30)。
SMT用焊锡膏知识介绍及其使用过程中常见问题之原因分析作者: jackerxia发表日期: 2006-06-07 15:58 复制描述:图一图片:SMT用焊锡膏知识介绍及其使用过程中常见问题之原因分析夏杰一、焊锡膏的主要成份及特性大致讲来,焊锡膏的成份可分成两个大的部分,即助焊剂和焊料粉(FLUX &SOLDER POWDER)。
(一)、助焊剂的主要成份及其作用:A、活化剂(ACTIVATION):该成份主要起到去除PCB铜膜焊盘表层及零件焊接部位的氧化物质的作用,同时具有降低锡、铅表面力的功效;B、触变剂(THIXOTROPIC) :该成份主要是调节焊锡膏的粘度以及印刷性能,起到在印刷中防止出现拖尾、粘连等现象的作用;C、树脂(RESINS):该成份主要起到加大锡膏粘附性,而且有保护和防止焊后PCB再度氧化的作用;该项成分对零件固定起到很重要的作用;D、溶剂(SOLVENT):该成份是焊剂组份的溶剂,在锡膏的搅拌过程中起调节均匀的作用,对焊锡膏的寿命有一定的影响;(二)、焊料粉:焊料粉又称锡粉主要由锡铅合金组成,一般比例为63/37;另有特殊要求时,也有在锡铅合金中添加一定量的银、铋等金属的锡粉。
概括来讲锡粉的相关特性及其品质要求有如下几点:A、锡粉的颗粒形态对锡膏的工作性能有很大的影响:A-1、重要的一点是要求锡粉颗粒大小分布均匀,这里要谈到锡粉颗粒度分布比例的问题;在国的焊料粉或焊锡膏生产厂商,大家经常用分布比例来衡量锡粉的均匀度:以25~45μm 的锡粉为例,通常要求35μm左右的颗粒分度比例为60%左右,35μm 以下及以上部份各占20%左右;A-2、另外也要求锡粉颗粒形状较为规则;根据“中华人民国电子行业标准《锡铅膏状焊料通用规》(SJ/T 11186-1998)”中相关规定如下:“合金粉末形状应是球形的,但允许长轴与短轴的最大比为1.5的近球形状粉末。
如用户与制造厂达成协议,也可为其他形状的合金粉末。
”在实际的工作中,通常要求为锡粉颗粒长、短轴的比例一般在1.2以下。
A-3、如果以上A-1及A-2的要求项不能达到上述基本的要求,在焊锡膏的使用过程中,将很有可能会影响锡膏印刷、点注以及焊接的效果。
B、各种锡膏中锡粉与助焊剂的比例也不尽相同,选择锡膏时,应根据所生产产品、生产工艺、焊接元器件的精密程度以及对焊接效果的要求等方面,去选择不同的锡膏;B-1、根据“中华人民国电子行业标准《锡铅膏状焊料通用规》(SJ/T 11186-1998)”中相关规定,“焊膏中合金粉末百分(质量)含量应为65%-96%,合金粉末百分(质量)含量的实测值与订货单预定值偏差不大于±1%”;通常在实际的使用中,所选用锡膏其锡粉含量大约在90%左右,即锡粉与助焊剂的比例大致为90:10;B-2、普通的印刷制式工艺多选用锡粉含量在89-91.5%的锡膏;B-3、当使用针头点注式工艺时,多选用锡粉含量在84-87%的锡膏;B-4、回流焊要求器件管脚焊接牢固、焊点饱满、光滑并在器件(阻容器件)端头高度方向上有1/3至2/3高度焊料爬升,而焊锡膏中金属合金的含量,对回流焊焊后焊料厚度(即焊点的饱满程度)有一定的影响;为了证实这种问题的存在,有关专家曾做过相关的实验,现摘抄其最终实验结果如下表供参考:金属含量(%)湿焊膏厚度(IN)回流焊的焊料厚度(IN)90 0.009 0.004585 0.009 0.003580 0.009 0.002575 0.009 0.0020从上表看出,随着金属含量减少,回流焊后焊料的厚度减少,为了满足对焊点的焊锡量的要求,通常选用85%~92%含量的焊膏。
C、锡粉的“低氧化度”也是非常重要的一个品质要求,这也是锡粉在生产或保管过程中应该注意的一个问题;如果不注意这个问题,用氧化度较高的锡粉做出的焊锡膏,将在焊接过程中严重影响焊接的品质。
二、锡膏的分类方式及选择标准一般情况下,首先选择焊锡膏大类,再根据合金组成、颗粒度、粘度等指标来选择。
(一)、分类方式:A、普通松香清洗型[分RA(ROSIN ACTIVATED )及RMA(ROSIN MILDLY ACTIVATED)]:此种类型锡膏在焊接过程中表现出较好“上锡速度”并能保证良好的“焊接效果”;在焊接工作完成后,PCB表面松香残留相对较多,可用适当清洗剂清洗,清洗后板面光洁无残留,保证了清洗后的板面具有良好的绝缘阻抗,并能通过各种电气性能的技术检测;B、免清洗型焊锡膏[NC(NO CLEAN)]:此种锡膏焊接完成后,PCB板面较为光洁、残留少,可通过各种电气性能技术检测,不需要再次清洗,在保证焊接品质的同时缩短了生产流程,加快了生产进度;C、水溶性锡膏[WMA(WATER SOLUBLE PASTES)]:早期生产的锡膏因技术上的原因,PCB 板面残留普遍过多,电气性能不够理想,严重影响了产品品质;当时多用CFC清洗剂来清洗,因CFC对环保不利,许多国家已禁用;为了适应市场的需求,应运产生了水溶性焊锡膏,此种锡膏焊接工作完成后它的残留物可用水清洗干净,既降低了客户的生产成本,又符合环保的要求。
(二)、选择标准:1、合金组份:一般情况下,选择Sn63/Pb37焊料合金组份即可满足焊接要求;对于有银(Ag)或钯(Pd)镀层器件的焊接,一般选择合金组份为Sn62/Pb36/Ag2的焊锡膏;对于有不耐热冲击器件的pcb焊接选择含Bi的焊粉。
2、锡膏的粘度(VISCOSITY):在SMT的工作流程中,因为从印刷(或点注)完锡膏并贴上元件,到送入回流焊加热制程,中间有一个移动、放置或搬运PCB的过程;在这个过程中为了保证已印刷好(或点好)的焊膏不变形、已贴在PCB焊膏上的元件不移位,所以要求锡膏在PCB进入回流焊加热之前,应有良好的粘性及保持时间。
A、对于锡膏的粘性程度指标(即粘度)常用“Pa·S”为单位来表示;其中200-600Pa·S的锡膏比较适合用于针式点注制式或自动化程度较高的生产工艺设备;印刷工艺要求锡膏的粘度相对较高,所以用于印刷工艺的锡膏其粘度一般在600-1200 Pa·S左右,适用于手工或机械印刷;B、高粘度的锡膏具有焊点成桩型效果好等特点,较适于细间距印刷;而低粘度的锡膏在印刷时具有较快下落、工具免洗刷、省时等特点;C、锡膏粘度的另一特点是:其粘度会随着对锡膏的搅拌而改变,在搅拌时其粘度会有所降低;当停止搅拌时略微静置后,其粘度会回复原状;这一点对于如何选择不同粘度的锡膏有着极为重要的作用。
另外,锡膏的粘度和温度有很大的关系,在通常状况下,其粘度将会随着温度的升高而逐渐降低。
3、目数(MESH):在国焊锡膏生产厂商多用锡粉的“颗粒度”来对不同锡膏进行分类,而很多国外厂商或进口焊锡膏多用“目数(MESH)”的概念来进行不同锡膏的分类。
目数(MESH)基本概念是指筛网每一平方英寸面积上的网孔数;在实际锡粉生产过程中,大多用几层不同网眼的筛网来收集锡粉,因每层筛网的网眼大小不同,所以透过每层网眼的锡粉其颗粒度也不尽相同,最后收集到的锡粉颗粒,其颗粒度也是一个区域值;A、从以上概念来看,锡膏目数指标越大,该锡膏中锡粉的颗粒直径就越小;而当目数越小时,就表示锡膏中锡粉的颗粒越大;参考下表对照:目数(MESH) 200 250 325 500 625颗粒度(μm) 75 63 45 25 20B、如果锡膏的使用厂商按锡膏的目数指标选择锡膏时,应根据PCB上距离最小的焊点之间的间距来确定:如果有较大间距时,可选择目数较小的锡膏,反之即当各焊点间的间距较小时,就应当选择目数较大的锡膏;一般选择颗粒度直径约为模板开口的1/5以。
三,使用锡膏应注意的问题(一)、焊锡膏的保存要求:焊膏的保存应该以密封形态存放在恒温、恒湿的冷柜,保存温度为0℃~10℃,如温度过高,焊膏中的合金粉未和焊剂起化学反应后,使粘度、活性降低影响其性能;如温度过低,焊剂中的树脂会产生结晶现象,使焊膏形态变坏。
在保管过程中,更重要的一点是应注意保持“恒温”这样一个问题,如果在较短的时间,使锡膏不断地从各种环境下反复出现不同的温度变化,同样会使焊锡膏中焊剂性能产生变化,从而影响焊锡膏的焊接品质。
(二)、使用前的要求:焊膏从冷柜(或冰箱)中取出时,应在其密封状态下,待其回到室温后再,约为2-3小时;如果刚从冷柜中取出就,存在的温差会使焊膏结露、凝成水份,这样会导致在回流焊时产生焊锡珠;但也不可用加热的方法使焊锡膏回到室温,急速的升温会使焊膏中焊剂的性能变坏,从而影响焊接效果。
这也是锡膏使用厂商在使用过程中应该注意的一个问题。
(三)、使用时的注意事项:1、刮刀压力:保证印出焊点边缘清晰、表面平整、厚度适宜;2、刮刀速度:保证焊膏相对于刮刀子为滚动而非滑动,一般情况下,10-20mm/s为宜;3、印刷方式:以接触式印刷为宜;另外,在使用时要对焊膏充分搅拌,再按印刷设定量加到印刷网板上,采用点注工艺的,还须调整好点注量。
在长时间的印刷情况下,因焊膏中溶剂的挥发,会影响到印刷时锡膏的脱模性能,因此对存放焊锡膏的容器不可重复使用(只可一次性使用),印刷后网板上所剩的焊锡膏,应用其它清洁容器装存保管,下次再用时,应先检查所剩锡膏中有无结块或凝固状况,如果过分干燥,应添加供应商提供的锡膏稀释剂调稀后再用。
操作人员作业时,要注意避免焊膏与皮肤直接接触。
另外,印刷完成的基板,应当天完成焊接。
(四)、工作环境要求:焊锡膏工作场所最佳状况为:温度20~25℃,相对湿度50~70%,洁净、无尘、防静电。
四、回流曲线的调节理想状态回流焊工艺曲线图(见图一)回流焊的目的:使表贴电子元器件(SMD)与PCB正确而可靠地焊接在一起;工艺原理:当焊料、元件与PCB的温度达到焊料熔点温度以上时,焊料熔化,填充元件与PCB间的间隙,然后随着冷却、焊料凝固,形成焊接接头;工艺流程:1、第一升温区(预热区)升温的目的:是将焊锡膏、PCB及元器件的温度从室温提升到预定的预热温度;预热温度是一低于焊料熔点的温度。
升温段的一个重要参数是“升温速率”,一般情况下其值应在1-2.00C/S;由于PCB及元器件吸热速率不同,各元器件升温速率也会有所不同,从而导致PCB板面上的温度分布出现梯度。
因为此段所有点的温度均在焊料熔点以下,所以“温度梯度”的存在并无大碍。
第一升温区结束时,温度约为1000C-1100C;时间约为30-90秒,以60秒左右为宜。
2、保温区(又称干燥渗透区)“保温”的目的是让焊锡膏中的助焊剂有充足的时间来清理焊点、去除焊点的氧化膜,同时使PCB及元器件有充足的时间达到温度均衡,消除“温度梯度”;此阶段时间应设定在60-120秒;保温段结束时,温度为140-1500C。