硅烷陶化液成分分析,陶化液配方原理及生产技术工艺
硅烷化处理

金属表面处理环保新技术——硅烷化处理硅烷化处理是以有机硅烷水溶液为主要成分对金属或非金属材料进行表面处理的过程。
在涂装行业,涂装前的表面处理以磷化为主,硅烷化处理与传统磷化相比具有节能、环保和降低成本的优点。
本文简述了硅烷化处理的特点、基本原理、施工工艺等。
Si-OH的低聚硅氧烷;(3)低聚物中的Si-OH与基材表面上的OH形成氢键;(4)加热固化过程中伴随脱水反应而与基材形成共价键连接,但在界面上硅烷的硅羟基与基材表面只有一个键合,剩下两个Si-OH 或者与其他硅烷中的Si-OH缩合,或者游离状态。
为缩短处理剂现场使用所需熟化时间,硅烷处理剂在使用之前第一步是进行一定浓度的预水解。
①水解反应:在水解过程中,避免不了在硅烷间会发生缩合反应,生成低聚硅氧烷。
低聚硅氧烷过少,硅烷处理剂现场的熟化时间延长,影响生产效率;低聚硅氧烷过多,则使处理剂浑浊甚至沉淀,降低处理剂稳定性及影响处理质量。
随着涂装行业中环保压力的逐渐增大,环保型涂装前处理产品以代替传统磷化如今显的尤为重要。
硅烷前处理技术做为磷化替代技术之一,目前已引起了世界涂装行业的广泛关注。
与传统磷化相比,硅烷处理技术具有环保性(无有毒重金属离子)、低能耗(常温使用)、低使用成本(每公斤处理量为普通磷化的5-8倍),无渣等优点。
美国已于上世纪90年代就开始对金属硅烷前处理技术进行理论研究,欧洲于上世纪90年代中期也开始着手对于硅烷进行试探性研究。
我国在本世纪初迫于环保方面的巨大压力,各大研究机构及生产企业也着手对硅烷进行研究。
1.1工位工序方面比较备用。
在改换槽位功能的同时提高链速进行生产,以加快前处理生产节拍,提高生产率。
1.2处理条件方面比较传统磷化处理因沉渣、含磷及磷化后废水等环保问题,一直是各涂装生产企业为之困扰的问题。
随着国家对环保及节能减排的重视程度不断提高,在未来时间里,涂装行业的环保及能耗问题会越来突出。
硅烷技术的推出,对于整个涂装行业的前处理环保及节能降耗问题,进行了革命性的改善。
硅烷化处理

金属表面处理环保新技术——硅烷化处理硅烷化处理是以有机硅烷水溶液为主要成分对金属或非金属材料进行表面处理的过程。
在涂装行业,涂装前的表面处理以磷化为主,硅烷化处理与传统磷化相比具有节能、环保和降低成本的优点。
本文简述了硅烷化处理的特点、基本原理、施工工艺等。
[关键词] 硅烷;表面处理;磷化硅烷化处理是以有机硅烷为主要原料对金属或非金属材料进行表面处理的过程。
硅烷化处理与传统磷化相比具有以下多个优点:无有害重金属离子,不含磷,无需加温。
硅烷处理过程不产生沉渣,处理时间短,控制简便。
处理步骤少,可省去表调工序,槽液可重复使用。
有效提高油漆对基材的附着力。
可共线处理铁板、镀锌板、铝板等多种基材0 基本原理硅烷含有两种不同化学官能团,一端能与无机材料(如玻璃纤维、硅酸盐、金属及其氧化物)表面的羟基反应生成共价键;另一端能与树脂生成共价键,从而使两种性质差别很大的材料结合起来,起到提高复合材料性能的作用。
硅烷化处理可描述为四步反应模型,(1)与硅相连的3个Si-OR基水解成Si-OH;(2)Si-OH之间脱水缩合成含Si-OH的低聚硅氧烷;(3)低聚物中的Si-OH与基材表面上的OH 形成氢键;(4)加热固化过程中伴随脱水反应而与基材形成共价键连接,但在界面上硅烷的硅羟基与基材表面只有一个键合,剩下两个Si-OH或者与其他硅烷中的Si-OH缩合,或者游离状态。
为缩短处理剂现场使用所需熟化时间,硅烷处理剂在使用之前第一步是进行一定浓度的预水解。
①水解反应:在水解过程中,避免不了在硅烷间会发生缩合反应,生成低聚硅氧烷。
低聚硅氧烷过少,硅烷处理剂现场的熟化时间延长,影响生产效率;低聚硅氧烷过多,则使处理剂浑浊甚至沉淀,降低处理剂稳定性及影响处理质量。
②缩合反应:成膜反应是影响硅烷化质量的关键步骤,成膜反应进行的好坏直接影响涂膜耐蚀性及对漆膜的附着力。
因此,对于处理剂的PH值等参数控制显的尤为重要。
并且对于硅烷化前的工件表面状态提出了更高的要求:1、除油完全;2、进入硅烷槽的工件不能带有金属碎屑或其他杂质;3、硅烷化前处理最好采用去离子水。
纳米陶化与硅烷
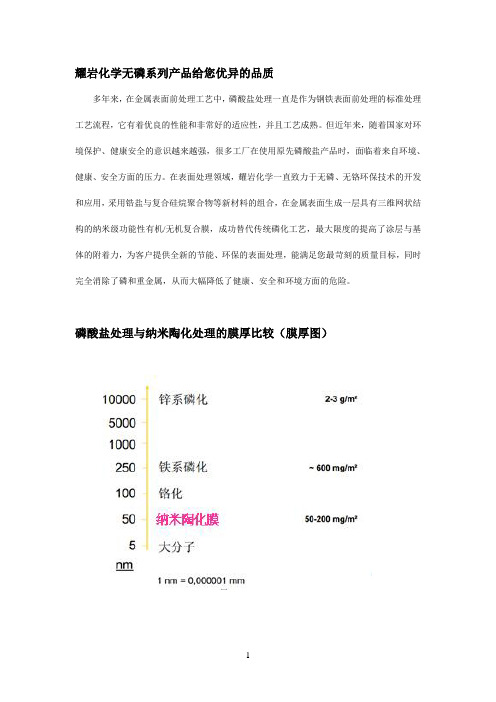
耀岩化学无磷系列产品给您优异的品质
多年来,在金属表面前处理工艺中,磷酸盐处理一直是作为钢铁表面前处理的标准处理工艺流程,它有着优良的性能和非常好的适应性,并且工艺成熟。
但近年来,随着国家对环境保护、健康安全的意识越来越强,很多工厂在使用原先磷酸盐产品时,面临着来自环境、健康、安全方面的压力。
在表面处理领域,耀岩化学一直致力于无磷、无铬环保技术的开发和应用,采用锆盐与复合硅烷聚合物等新材料的组合,在金属表面生成一层具有三维网状结构的纳米级功能性有机/无机复合膜,成功替代传统磷化工艺,最大限度的提高了涂层与基体的附着力,为客户提供全新的节能、环保的表面处理,能满足您最苛刻的质量目标,同时完全消除了磷和重金属,从而大幅降低了健康、安全和环境方面的危险。
磷酸盐处理与纳米陶化处理的膜厚比较(膜厚图)
纳米陶化/硅烷处理具有更简单的处理工艺流程
喷淋处理工艺
脱脂水洗纯水洗无磷转化纯水洗浸泡处理工艺
脱脂水洗纯水洗无磷转化纯水洗
纳米陶化/硅烷处理的优势
①无磷①常温处理
②无COD/BOD—无有机物②简单的工艺控制
③无重金属③适合多金属处理
④无危险物质④减少废水、废渣量产出
传统的锌系磷化与纳米陶化/硅烷处理的比较
锌系磷化硅烷处理
工位数量8 5-6
能耗槽液加热高低
能耗—泵高低
过滤装置等等有无
磷化渣排放有无
传统磷化前的表调槽有无
人工或化学清洗槽体,管道和喷嘴等经常偶尔
水/纯水消耗高低
含重金属的废水处理(例如,镍)需要不需要
反应时间 1.5-3分钟20-120秒。
金属环保硅烷陶化剂801

金属环保硅烷陶化剂801
本产品属于环保型硅烷、陶化二合一金属表面剂,不含镍、铬等重金属、磷酸根,不含强酸,不需要使用促进剂,不需要表调,在常温下即可使用,不易产生沉渣;可用来处理钢铁、镀锌板等金属材料,无需加热使用,节能、反应产物易处理,不含COD,氨氮,可生物降解。
污水处理只需酸碱中和,絮凝就可以,对环境友好,符合欧盟RoHS指令要求。
可用于浸渍,喷淋。
产品外观针对材料的不同:可无色,可金黄色,可浅蓝色,可蓝色。
本产品的陶化膜坚韧,耐磨,耐腐蚀,耐高温,不易返锈。
与涂层有着优良结合性。
涂层后中性盐雾试验最高可达500小时。
可完全替代磷化。
本产品无色透明液体。
产品包括:
硅烷陶化剂801;
本产品的使用方法:
喷淋开槽:2.5% 浸渍开槽:3.0%
PH值:4-5 PH值:4-5
陶化点数:15-25 陶化点数:15-30
温度:常温温度:常温
检测方法:
1.PH值:陶化液的工作指数PH值:4-5,用精密PH试纸或酸度计直接测试读取。
2.陶化点。
①取2mL陶化工作液于250mL锥形瓶中;
②加入10mLP1缓冲液,摇匀;
③接着加入20mLP2缓冲剂,摇匀;
④再加入2~3滴HP指示剂;
⑤在电炉加热至80~90℃(或沸腾状态)
⑥趁热迅速用1m mol/L的EDTA标准溶液滴定,溶液由酒红色变为浅黄色为滴定终点;
⑦EDTA标准溶液消耗的毫升数即为陶化点。
硅烷处理和纳米陶瓷处理.doc

——硅烷处理和纳米陶瓷处理全国金属与非金属覆盖层标准化技术委员会委员徐贺北京科华富达工程技术有限公司总经理最近几年,金属表面涂装前处理工艺和材料发生了比较大的变化,甚至有人称为“革命性的变化”,这主要是指部分厂家采用了硅烷处理或纳米陶瓷处理取代了磷化处理。
这两年,来自东北和北京等地的散热器行业的企业家不止一次向我咨询,了解散热器行业的涂装前处理有无更新更环保的处理工艺和材料,我当时只简单地回应说:“新东西在别的行业有,但还没有大量采用,目前来看暂不适合咱们散热器行业”,以后也没有在杂志上或行业会议上专门就此进行过介绍。
9月10-12日我到西安参加了2010中国涂料涂装国际峰会暨专家集结年会,并在会上做了《环保型涂装前处理材料在散热器行业的应用前景》的演讲,10月10-12日,我又到佛山参加了全国金属与非金属覆盖层标准化技术委员会(SAC/TC57)2010年涂装标准工作会议,在此我把通过参加这两次会议及平时了解到的关于涂装前处理的最新技术与各位在此一起分享,希望能为我们散热器行业同仁了解最新科技潮流提供一个窗口。
1.背景长期以来,磷化处理是金属表面涂装前处理中应用最为广泛的工艺,经过磷化处理的工件,其涂层的附着力和耐蚀性大大提高。
但是,传统的磷化处理不可避免地存在着能耗高、重金属离子含量高、三废排放多、钝化剂中含有致癌物等缺陷,所以人们一直在为寻找磷化的替代工艺和产品而绞尽脑汁,适应环保和节能要求的工艺和材料的问世呼之欲出。
最典型的工艺就是取代磷化处理的硅烷处理和纳米陶瓷处理,各厂家对硅烷处理的叫法比较统一,但对纳米陶瓷处理则有多种叫法,比如汉高叫纳米陶瓷处理,PPG公司叫锆系前处理,科富则叫无磷纳米陶化处理,其原理基本都是一样的。
2.硅烷处理技术2.1 硅烷技术原理硅烷处理剂的主要成分是有机硅烷,其基本分子式为:R′-Si-(OR)3,其中OR是可水解的基因(如烷氧基/酰氧基),R′是有机官能团(如氨基/环氧基等)。
硅烷处理和纳米陶瓷处理

硅烷处理和纳米陶瓷处理——硅烷处理和纳米陶瓷处理全国金属与非金属覆盖层标准化技术委员会委员徐贺北京科华富达工程技术有限公司总经理最近几年,金属表面涂装前处理工艺和材料发生了比较大的变化,甚至有人称为“革命性的变化”,这主要是指部分厂家采用了硅烷处理或纳米陶瓷处理取代了磷化处理。
这两年,来自东北和北京等地的散热器行业的企业家不止一次向我咨询,了解散热器行业的涂装前处理有无更新更环保的处理工艺和材料,我当时只简单地回应说:“新东西在别的行业有,但还没有大量采用,目前来看暂不适合咱们散热器行业”,以后也没有在杂志上或行业会议上专门就此进行过介绍。
9月10-12日我到西安参加了2010中国涂料涂装国际峰会暨专家集结年会,并在会上做了《环保型涂装前处理材料在散热器行业的应用前景》的演讲,10月10-12日,我又到佛山参加了全国金属与非金属覆盖层标准化技术委员会(SAC/TC57)2010年涂装标准工作会议,在此我把通过参加这两次会议及平时了解到的关于涂装前处理的最新技术与各位在此一起分享,希望能为我们散热器行业同仁了解最新科技潮流提供一个窗口。
1.背景长期以来,磷化处理是金属表面涂装前处理中应用最为广泛的工艺,经过磷化处理的工件,其涂层的附着力和耐蚀性大大提高。
但是,传统的磷化处理不可避免地存在着能耗高、重金属离子含量高、三废排放多、钝化剂中含有致癌物等缺陷,所以人们一直在为寻找磷化的替代工艺和产品而绞尽脑汁,适应环保和节能要求的工艺和材料的问世呼之欲出。
最典型的工艺就是取代磷化处理的硅烷处理和纳米陶瓷处理,各厂家对硅烷处理的叫法比较统一,但对纳米陶瓷处理则有多种叫法,比如汉高叫纳米陶瓷处理,PPG公司叫锆系前处理,科富则叫无磷纳米陶化处理,其原理基本都是一样的。
2.硅烷处理技术2.1 硅烷技术原理硅烷处理剂的主要成分是有机硅烷,其基本分子式为:R′-Si-(OR)3,其中OR 是可水解的基因(如烷氧基/酰氧基),R′是有机官能团(如氨基/环氧基等)。
陶化液配方分析开发及专利技术转让

陶化液配方分析开发及专利技术转让本文为读者推荐一款陶化液产品——禾川化学专利技术之一研究背景随着环保要求的日趋重要,传统的磷化工艺含磷、镍及沉渣问题,已无法满足环保要求;工件表面陶化处理是涂装前处理的环保节能新技术;硅烷化和陶化等无磷成膜技术的应用,使得金属表面化学转化膜技术发生了重大变革,新型陶化膜正逐步取代传统的磷化膜;陶化液是一种常温、快速、无磷、无锌、无铬、无氟、无钼、无锆、无渣的新型超浓缩环保产品;室温:浸渍、喷淋、游浸、涂刷、滚涂1至2秒就能够在金属表面迅速形成一种纳米级高分子渗透膜;成功地解决了目前常温条件下磷化速度慢、沉淀多、挂灰重、防腐弱、附着力差,且对环境污染严重等系列科技难题。
陶化液因具备优异的防腐性能、附着性能被大力推广应用于铝材、铜材、钢材、镁合金等不同金属的表面处理。
陶化液优点1. 无任何重金属,低碳环保、经济高效;2. 不含磷、硝酸盐、亚硝酸盐及氟化物;3. 无需表调处理,钝化处理及封面处理,不用倒槽,药剂耗费量和添加量极少;4. 陶化液可在脱脂清洗或酸洗后进行处理,耐酸碱、机械性和热稳定性良好;5. 可共线处理铁、铝锌、及不锈钢等金属制品;6. 超浓缩,超时速,多功能;7. 单液使用、工艺简单,不需用纯水配槽;8. 渗透膜质量优异;9. 陶化后工件不会有粉尘现象缺陷;10. 陶化液附着力为0级;磷化附着力普通是1~2级;11. 综合使用成本低,可大大节约场地、人工、能源、设备等费用。
技术参数工艺流程水洗活化水洗陶化游浸式(喷淋式)陶化烘干新型环保工艺:喷砂抛丸陶化烘干新型环保工艺陶化液为专利项目,可做配方技术转让,禾川化学提供各种钝化陶化产品的定制服务!禾川简介苏州禾川化学技术服务有限公司(简称“禾川化学”);成立于2012年,先后为全球500企业在内近3500家企业、科研所,提供了整套配方技术服务方案。
经历近五年积淀,在精细化学品领域(工业清洗、表面处理、水处理、纺织印染、加工制造、日化洗涤、胶黏剂、功能性助剂)形成自身专长;在精细化学品领域已形成具有一定影响力的配方服务机构。
硅烷的纯化技术与检测分析方法_窦仕川
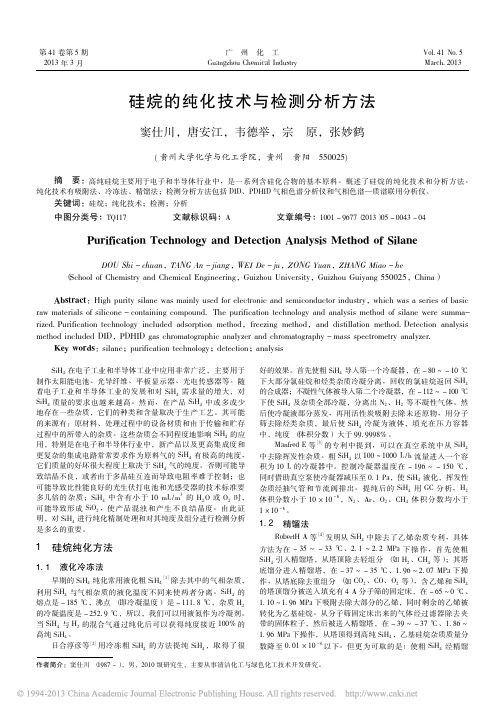
关键词: 硅烷; 纯化技术; 检测; 分析
中图分类号: TQ117
文献标识码: A
文章编号: 1001 - 9677( 2013) 05 - 0043 - 04
Purification Technology and Detection Analysis Method of Silane
DOU Shi - chuan,TANG An - jiang,WEI De - ju,ZONG Yuan,ZHANG Miao - he ( School of Chemistry and Chemical Engineering,Guizhou University,Guizhou Guiyang 550025,China)
1. 2 精馏法
RobertH A 等[4]发明从 SiH4 中除去了乙烯杂质专利,具体
方法为在 - 35 ~ - 33 ℃ 、2. 1 ~ 2. 2 MPa 下 操 作,首 先 使 粗 SiH4 引入精馏塔,从塔顶除去轻组分 ( 如 H2 、CH4 等) ; 其塔 底馏分进入精馏塔,在 - 37 ~ - 35 ℃ 、1. 96 ~ 2. 07 MPa 下操 作,从塔底除去重组分 ( 如 CO2 、CO、O2 等) ,含乙烯和 SiH4 的塔顶馏分被送入填充有 4 A 分子筛的固定床,在 - 65 ~ 0 ℃ 、 1. 10 ~ 1. 96 MPa 下吸附去除大部分的乙烯,同时剩余的乙烯被 转化为乙基硅烷。从分子筛固定床出来的气体经过滤器除去夹 带的固体粒子,然后被送入精馏塔,在 - 39 ~ - 37 ℃ 、1. 86 ~ 1. 96 MPa 下操作,从塔顶得到高纯 SiH4 ,乙基硅烷杂质质量分 数降至 0. 01 × 10 - 6 以下。但更为可取的是: 使粗 SiH4 经精馏
一种金属表面前处理用硅烷陶化剂及其制备方法和使用方法[发明专利]
![一种金属表面前处理用硅烷陶化剂及其制备方法和使用方法[发明专利]](https://img.taocdn.com/s3/m/5cb8bac27d1cfad6195f312b3169a4517723e5d5.png)
(19)中华人民共和国国家知识产权局(12)发明专利申请(10)申请公布号 (43)申请公布日 (21)申请号 201910679838.0(22)申请日 2019.07.26(71)申请人 佛山市顺德区新琪洗涤用品有限公司地址 528000 广东省佛山市顺德区容桂华口社区华新路17号首层之三(72)发明人 曹新平 沈凯 (74)专利代理机构 深圳市科吉华烽知识产权事务所(普通合伙) 44248代理人 谢肖雄(51)Int.Cl.C23C 22/34(2006.01)C23C 22/73(2006.01)C23C 22/78(2006.01)C23C 22/82(2006.01)(54)发明名称一种金属表面前处理用硅烷陶化剂及其制备方法和使用方法(57)摘要本发明公开了一种金属表面前处理用硅烷陶化剂,该金属表面前处理用硅烷陶化剂由以下重量百分比的原料构成:1-2%的硅烷偶联剂、5-10%的含锆化合物、0.2-1%的络合剂、0.1-1%的纳米化合物、1-5%的含氟酸、2-8%的氧化剂、1-5%的pH调整剂以及余量的水;该硅烷陶化剂其具备完全水性体系、无挥发性有毒化学品且可以有效提高有机涂层对各种底材的结合力的特点。
权利要求书2页 说明书5页CN 112111732 A 2020.12.22C N 112111732A1.一种金属表面前处理用硅烷陶化剂,其特征在于,所述金属表面前处理用硅烷陶化剂由以下重量百分比的原料构成:1-2%的硅烷偶联剂、5-10%的含锆化合物、0.2-1%的络合剂、0.1-1%的纳米化合物、1-5%的含氟酸、2-8%的氧化剂、1-5%的pH调整剂以及余量的水。
2.根据权利要求1所述的一种金属表面前处理用硅烷陶化剂,其特征在于:所述硅烷偶联剂为KH-570、KH-560、SJ-42、KH-792和KH-602中的一种或多种。
3.根据权利要求1所述的一种金属表面前处理用硅烷陶化剂,其特征在于:所述锆化物为醋酸锆、氧氯化锆、硝酸锆、碱式碳酸锆和硝酸氧锆中的一种或多种。
环保金属表面陶化剂配料及制备方法详解

环保金属表面陶化剂配料及制备方法详解随着环保意识的普及和环境法规的日益严格,环保金属表面陶化剂逐渐成为研究热点。
环保金属表面陶化剂是一种能够在金属表面形成紧密氧化物层,保护金属表面不受腐蚀的化学制剂。
本文将详细介绍环保金属表面陶化剂的配料及制备方法。
一、配料1.主体材料:主体材料是环保金属表面陶化剂的主要成分,其质量占整个配方的60-80%。
主体材料通常选择磷酸盐或硝酸盐等化合物。
2.助剂:助剂是环保金属表面陶化剂的辅助成分,其质量占整个配方的20-40%。
助剂的种类较多,一般包括氨水、硝酸、磷酸、过氧化氢等。
3.缓蚀剂:缓蚀剂是环保金属表面陶化剂的重要组成部分,其主要作用是减缓金属表面的腐蚀速度,保护金属表面不受腐蚀。
常用的缓蚀剂有硝酸钾、磷酸二铵等。
4.稳定剂:稳定剂的作用是稳定环保金属表面陶化剂的化学性质,提高其存储稳定性。
常用的稳定剂有硼酸、硼酸钠等。
二、制备方法1.按照配方将主体材料、助剂、缓蚀剂、稳定剂等按比例称量。
2.将主体材料和助剂充分混合,加入适量的水溶液中搅拌均匀。
3.将缓蚀剂加入搅拌均匀的溶液中,继续搅拌至完全溶解。
4.加入稳定剂,继续搅拌至溶液稳定。
5.将制备好的环保金属表面陶化剂过滤,去除杂质。
6.环保金属表面陶化剂制备完成,可以用于金属表面的陶化处理。
三、注意事项1.在制备过程中应注意安全,避免化学品接触皮肤和吸入有害气体。
2.配料时应按照比例称量,严格控制配方中各成分的质量比例,确保制备出的环保金属表面陶化剂质量稳定。
3.在制备过程中应注意环保要求,尽可能选用绿色、环保的原材料和助剂。
4.制备好的环保金属表面陶化剂应密封保存,避免受潮、污染和氧化。
5.环保金属表面陶化剂的使用应根据具体情况进行控制,严格遵守安全操作规程,避免对环境和人类健康造成危害。
环保金属表面陶化剂的配料及制备方法是一个非常重要的环节,只有严格按照比例称量、控制质量、注意环保要求,并严格遵守安全操作规程,才能制备出高质量、环保的金属表面陶化剂。
电泳硅烷陶化点

电泳硅烷陶化点
电泳硅烷陶化点是一种新型的化合物,它对于改善各种材料的性
能具有显著的效果。
电泳硅烷陶化点通过化学反应将硅烷陶化剂陶化
到基材表面,可有效提高基材的附着力和耐久性,同时也能改善其耐
腐蚀性、耐高温性和表面润湿性等特性。
首先,电泳硅烷陶化点具有优异的附着力。
与传统的涂层技术相比,电泳硅烷陶化点可以直接将硅烷陶化剂化学反应陶化到基材表面,从而形成一层紧密的、无缝的化学键结构,这种紧密的结构可以大幅
度提高涂层的附着力,使涂层更加耐用。
其次,电泳硅烷陶化点具有良好的耐腐蚀性能。
硅烷陶化剂能够
在基材表面形成致密的硅氧化物层,无论是在水中还是在酸性、碱性
介质中,都具有优异的稳定性。
因此,在涂层表面形成的硅氧化物层
也能够有效防止氧化、腐蚀和酸碱侵蚀等现象的发生,从而保护基材
的完整性和稳定性。
此外,电泳硅烷陶化点也具有一定的耐高温性能。
硅氧化物层在
高温下也可以保持完整和稳定,对于高温环境下的使用更加耐受。
同
时,硅氧化物层也可以通过改变硅烷陶化剂的种类和加工条件来优化其硬度和耐磨性,从而满足不同材料在高温环境下的使用要求。
最后,值得一提的是,电泳硅烷陶化点还能够改善涂层表面的润湿性。
它可以改变基材表面的微观形貌和表面能量,从而使其具有更好的亲水性和润湿性,提高涂层和基材之间的结合力和摩擦力,从而使涂层也具有更好的透气性和防水性。
总的来说,电泳硅烷陶化点是一种应用广泛的新型涂层技术,它可以提高材料的机械性能、化学稳定性和环境适应性,为各种工业领域的应用提供了更优质、更可靠的选择。
- 1、下载文档前请自行甄别文档内容的完整性,平台不提供额外的编辑、内容补充、找答案等附加服务。
- 2、"仅部分预览"的文档,不可在线预览部分如存在完整性等问题,可反馈申请退款(可完整预览的文档不适用该条件!)。
- 3、如文档侵犯您的权益,请联系客服反馈,我们会尽快为您处理(人工客服工作时间:9:00-18:30)。
硅烷陶化液成分分析,陶化原理及配方技术开发
导读:本文详细介绍了硅烷陶化液的研究背景,理论基础,参考配方等,本文中的配方数据经过修改,如需要具体信息请联系我们的技术咨询。
进口陶化液广泛应用于金属表面处理,禾川化学引进国外配方破译技术,专业从事硅烷陶化液成分分析、配方还原、研发外包服务,为陶化液相关企业提供一整套配方技术解决方案。
一.背景
钢铁在进行涂装前通常需要进行前处理,包括除油、除锈等工艺,化学前处理方法通常还要在钢铁的表面形成一层化学转化膜,该转化膜既有一定的防腐能力,可以避免零件在喷涂前短暂的时间内返锈,也可以增加零件表面的粗糙度,增强涂料与基底的结合力。
目前大部分采用的是磷化工艺,随着节能减排的不断推进,新型无磷转化膜(陶化膜)正在悄然取代传统的磷化膜。
陶化液应该就是所谓的锆系、锆钛系、硅烷系、锆硅烷系、等无磷金属表面处理剂,可部分替代磷化液,主要原料为氟锆酸盐,硅烷偶联剂等。
这种新型氧化锆转化膜技术在实验室里已取得了成功,全面生产试验正在进行中。
该新型转化膜是由无定形态ZrO2组成的,而不是Zn3(PO4)2多晶体。
它主要是用氧化锆组成的纳米陶瓷涂层取代传统的结晶型磷化保护层,与金属表面和随后的油漆涂层之间有良好的附着力,耐腐蚀性能优良。
相信氧化锆转化膜技术的应用一定会给钢铁行业前处理工艺带来巨大的变革。
硅烷化和陶化等无磷成膜技术的应用,使钢铁表面化学转化膜技术发生了重大变革。
尽管这些转化膜工艺尚未成熟,与磷化处理相比,在实际生产应用中还存在一些难度,但我们相信,随着技术的不断发展,在不久的将来,这些处理技术一定会逐步取代传统的磷化工艺,或者出现更为先进的处理工艺。
2007年以来,氧化锆转化膜技术在通用、沃尔沃、大众等三家汽车公司分别进行了附着力和耐腐蚀性能的检测,结果基本达到了各家公司的测试指标。
新型氧化锆转化膜技术在汽车前处理上的应用,还需做以下方面的工作。
当前汽车前处理行业充满挑战和竞争,随着环保法规的日益严格、能源和原材料成本的日益增加,以及劳动力成本的上涨,促使原材料供应商不断进行技术创新。
氧化锆转化膜技术的发明,给汽车前处理行业带来了全新的发展前景。
禾川化学技术团队具有丰富的分析研发经验,经过多年的技术积累,可以运用尖端的科学仪器、完善的标准图谱库、强大原材料库,彻底解决众多化工企业生产研发过程中遇到的难题,利用其八大服务优势,最终实现企业产品性能改进及新产品研发。
样品分析检测流程:样品确认—物理表征前处理—大型仪器分析—工程师解谱—分析结果验证—后续技术服务。
有任何配方技术难题,可即刻联系禾川化学技术团队,我们将为企业提供一站式配方技术解决方案!
二、陶化液
2.1陶化液的组成
1) 硅烷处理剂
水溶液中通常以水解的形式存在:硅烷水解后通过其SiOH基团与金属表面的MeOH基(M表示金属)的缩水反应而快速吸附于金属表面;一方面硅烷在金属界面上形成Si-O-Me共价键。
Si(OR)3+H2O →Si(OH)+3ROH (1)
Si(OH)+MOH →SiOM+ H2O (2)
一般来说,共价键问的作用力可达70010,硅烷与金属之间的结合是非常牢固的;另一方面,剩余的硅烷分子通过SiOH基团之间的缩聚反应在金属表面形成具有Si-O-Si三维网状结构的硅烷膜。
该硅烷膜在烘干过程中和后道的电泳漆或喷粉通过交联反应结合在一起,形成牢固的化学键。
这样,基材、硅烷和油漆之间可以通过化学键形成稳固的膜层结构。
优点:①不含重金属和磷酸盐,废水处理简单,可以降低废水处理的成本,减轻环境污染。
②不需表调,也不需要亚硝酸盐促进剂等,药剂用量少,可加快处理速度,提高生产效率,也减少了这类化学物质的对环境污染。
③可在常温下进行,不需加温,减少能源消耗。
④一种处理液可同时处理铁、铝等材料,不需更换槽液,降低生产成本。
2.2陶化机理
它是以锆盐为基础在金属表面生成一层纳米级陶瓷膜。
陶化剂不含重金属、磷酸盐和任何有机挥发组分,成膜反应过程中几乎不产生沉渣,可处理铁、锌、铝、镁等多种金属。
陶化原理:
1)酸的侵蚀使金属表面H+浓度降低:Fe-2e—Fe2+,2H++2e—2[H]
2)纳米硅促进反应加速:
[Si]:ZrO2+4[H]—[Zr]+2H2O
式中[Si]为纳米硅,[Zr]为还原产物,纳米硅为反应活化体,加快了反应速度,进一步导致金属表面H+浓度急剧下降,生成的[Zr] 成为成膜晶核。
3)锆酸根的两级离解:
H2ZrF6+H+—ZrF62-+2H+
由于表面的H+浓度急剧下降,导致锆酸根各级离解平衡向右移动,最终为ZrF6-。
4)锆酸盐沉淀结晶成膜:当表面离解出的ZrF6-,与溶解中的金属离子Fe2+达到溶度积常数Ksp时,就会形成锆酸盐沉淀。
Fe2++ ZrF62-+H2O —FeZrF6+2H20
锆酸盐沉淀与水分子一起形成成膜物质,以[Zr]为膜晶核不断堆积,晶核继续长大成为晶粒,无数个经理堆积形成转化膜。
硅烷化处理和陶化处理都可称之为无磷成膜处理,目前市场上还有其它方式的无磷成膜处理方法,这些新技术与硅烷化或陶化处理有很多相似之处,一般都含有微量甚至不含重金属和磷酸盐,不需要表调,可处理多种板材等,处理时间短,可以提高生产效率,在节能减排方面具有相当大的优势,无磷成膜技术必将成为未来钢铁表面化学转化膜的主要处理方式。
三、新型陶化液相关案例
3.1MD-350纳米陶化剂
美硕公司研发生产的MD-350纳米陶化剂具有技术成熟、稳定、使用寿命长等特点。
MD-350纳米陶化剂是一种无磷酸盐的环保型前处理剂,是针对目前对环境保护要求越来越严格的前处理环境下,研发的新一代环保型处理液。
不含磷和重金属,符合欧盟RoHS环保指令要求,适合于钢铁、锌和铝表面处理,在处理的工件上形成从无色、金黄色、蓝色到蓝紫色陶化皮膜,能增强涂装的结合力和耐腐蚀性能,并和各种型号的涂料匹配。
室温(不需要加热)处理,适用于喷淋或浸泡处理方式。
处理的工件上形成从无色、金黄色、蓝色到蓝紫色陶化皮膜,能增强涂装的结合力和耐腐蚀性能,并和各种型号的涂料匹配。
室温(不需要加热)处理,适用于喷淋或浸泡处理方式。
适用范围:MD-350纳米陶化剂适用于钢铁、锌和铝表面处理,在处理的工件上形成从无色、金黄色、蓝色到蓝紫色纳米陶瓷转化膜,增强涂装的附着力和耐腐蚀性能。
PH值为3.8~5.5。
3.2与钼酸盐复配的锆系钝化液
钼酸盐是主成膜物质,钼酸盐在酸性介质中具有氧化性,金属锌暴露在钼酸盐的酸性介质中将其还原为钼酸根,形成由锌的氧化物和钼的化合物构成的钼酸盐转化膜,本研究选用了钼酸铵作为主要成膜物质,钼酸盐的浓度宜控制在6 g/L~5 g/L范围。
氟化锆作为辅助成膜剂和钼酸盐钝化膜的促进剂加入的。
本研究采用锆的氧化物和氟化物反应制得氟化锆,其浓度控制在10 g/L~20 g/L为宜。
3.3氟锆系陶化剂
有发明专利公开了一种陶化剂,其由下述质量组成份数的原材料制成:钛锆复合物:20~30份,氟化物:5~10份,络合剂:5~10份,水:40~60份。
通过本工艺制作出来的陶化剂稳定性好,无沉渣,不含磷酸盐,可以在钢铁、锌和铝的表面上形成一层陶化层,其与各型号的涂料结合力强,适合常温的喷淋和浸泡处理,无须加热设备,达到节约能源、易于生产的目的。
配制过程:先在60%的水中加入氟锆酸钾(氟锆酸钠),搅拌至溶解;继续加入氟化物,搅拌至溶解;接着加入酒石酸钠,搅拌至溶解后,加入其余的40%水,搅拌20min即可。
本工艺的pH值的最佳范围为4.5~5.5之间,温度控制在25℃~45℃为宜,钝化处理时问控制在60 s~120 s为宜.钝化膜与铬酸盐钝化膜耐蚀性相当。
此钝化液不含六价铬,对环境的污染小,适用于锌镀层的彩色钝化处理。
四.陶化液参考配方(仅供参考)
组分投料量(g/L)
氟锆酸20~50
硅10~15
氟钛酸32~35
氟化锆15~20
KH550 2~5
氟钛酸钙6~6.5
酒石酸5~10
硝酸钠5~10
月桂醇聚氧乙烯醚3~5
水余量
通过对化工产品的配方分析还原,有利于企业了解现有技术的发展水平,实现知己知彼;有利于在现有产品上进行自主创新,获得知识产权;有利于在生产过程中发现问题、解决问题。
通过对化工产品的配方改进,配方研发,可以加快企业产品更新换代的速度,提升市场竞争力,因此,对于化工产品的分析、研发已变得刻不容缓!。