3鼓风炉熔炼
重有色冶金习题

铜冶金主要步骤:造锍熔炼、铜硫吹炼、火法精炼、电解精炼。
1.何谓造锍熔炼?造锍熔炼的目的是什么?定义:在1150-1250℃的高温下,是硫化铜精矿和溶剂在熔炼炉进行熔炼,炉料中的铜、硫与硫化亚铁形成液态的铜硫。
目的:将铜精矿中铜及其他有价金属(Ni、Co、Pb、Zn和贵金属)富集于冰铜中从而达到与脉石、部分硫铁的分离。
2.造锍熔炼时铜在渣中的损失有哪几种形式?并说明原因及降低渣含铜的可采取的措施。
损失形式:机械夹带、溶解两种形式。
原因:机械夹带损失是由于细颗粒冰铜未能沉降到锍层而夹带于炉渣中而引起的损失;溶解损失是由于铜的硫化物(Cu2S)及氧化物(Cu2O)溶于FeO炉渣中造成的损失,又分别为物理损失、化学损失。
措施:为降低渣含铜,实践中采取的主要措施是控制冰铜品位不要太高,渣中要有足够的二氧化硅以及良好的沉清条件和足够的沉清时间。
3.造锍熔炼过程中Fe3O4有何危害?生产实践中采用哪些有效措施抑制Fe3O4的形成?危害:1、Fe3O4的熔点高在渣中以Fe-O复杂离子状态存在。
当其量较多时,会使炉渣熔点升高,粘度增大,比重增大,恶化了渣与锍的沉清分离。
2、当熔体温度下降时,Fe3O4会析出沉于炉底及某些部位形成炉结,还会在冰铜与炉渣界面上形成一层粘渣隔膜层,危害正常操作。
有效措施:1.尽量提高熔炼温度;2.适当增加炉渣中SiO2含量;3.降低冰铜品位,控制适当的冰铜品位, 以保持足够的FeS量;4.创造Fe3O4与FeS和SiO2的良好接触条件。
3Fe3O4+FeS=10FeO+SO24.在吹炼过程中Fe3O4有何危害?怎样抑制其形成?危害:使炉渣熔点升高、粘度密度增大,转炉渣中Fe3O4含量较高时,会导致渣含铜显著增高,喷溅严重,风口操作困难。
在转炉渣回炉处理的情况下,还会给熔炼过程带来诸多问题。
抑制其形成:适当提高吹炼温度,勤放渣。
5.冰铜吹炼的目的?冰铜吹炼分哪两个阶段?并写出各阶段的主要方程式。
3鼓风炉熔炼

炉料和焦炭由加料斗加入。 炉料和焦炭由加料斗加入。 炉子两侧的块料和焦炭多, 炉子两侧的块料和焦炭多,炉中心为夹有块料和 焦炭的中心精矿料柱, 焦炭的中心精矿料柱,从而形成炉料分布不均匀的状 态。 由于炉内炉料分布的不均匀,导致炉气沿炉子水 由于炉内炉料分布的不均匀, 平断面分布也不均匀。炉子两侧料柱中块料多, 平断面分布也不均匀。炉子两侧料柱中块料多,对炉 气阻力小,而炉子中心的混捏铜精矿多, 气阻力小,而炉子中心的混捏铜精矿多,再加上料斗 的密封料柱的压力,故对烟气的阻力较大。因而炉气 的密封料柱的压力,故对烟气的阻力较大。因而炉气 由炉子两侧流过的多,而流经炉子中心的则极少。 由炉子两侧流过的多,而流经炉子中心的则极少。
6
预备区下部温度较高,中心料柱的铜精矿又受到上 预备区下部温度较高, 部较柱的压力作用,且与侧料柱交界的界面上温度很高, 部较柱的压力作用,且与侧料柱交界的界面上温度很高, 从而发生固结和烧结,产出具有一定强度的精矿块。 从而发生固结和烧结,产出具有一定强度的精矿块。 固结和烧结 在预备区石灰石受热发生分解: 在预备区石灰石受热发生分解: CaCO3→CaO + CO2
1
鼓风炉是一种具有垂直作业空间的冶金设备。 鼓风炉是一种具有垂直作业空间的冶金设备。炉料 和燃料从炉子上部加料口分批加入, 和燃料从炉子上部加料口分批加入,空气或富氧空气从 炉子下部两侧的风口鼓入, 炉子下部两侧的风口鼓入,产出的高温烟气通过炉料与 燃料的空隙而上升,并经炉子上部的烟气出口排出炉外。 燃料的空隙而上升,并经炉子上部的烟气出口排出炉外。
7
(2)焦点区 ) 焦点区是进行激烈化学反应和熔化过程的区段, 焦点区是进行激烈化学反应和熔化过程的区段,一 般位于风口上方一米左右的地方,最高温度达 般位于风口上方一米左右的地方,最高温度达1250 ~ 1350 ℃。 在焦点区内,被氧化的主要是FeS,产出的 在焦点区内,被氧化的主要是 ,产出的FeO与 与 炉料中的SiO2造渣。此外,转炉渣中的 3O4也直接与 造渣。此外,转炉渣中的Fe 炉料中的 SiO2和FeS作用造渣。 作用造渣。 作用造渣 焦炭几乎全部在焦点区被鼓入的空气燃烧: 焦炭几乎全部在焦点区被鼓入的空气燃烧: C + O2 = CO2
鼓风炉富氧熔炼炼铜

铜密闭鼓风炉熔炼技术经济指标

邵武厂
铜陵二冶
富冶
(新厂)
试生产期
生产期
精矿成分
Cu
S
富氧浓度,O2
16~22
25~28
24
17.7~22.4
26.5~32.5
27~30
21~24
28~30
27
10~15
25~30
22~24
块料率
焦率
铜硫品位
脱硫率
42.4
6.80
30~33
46.0
35~40
6.5~7.0
34.3~41.5
53.5~57.2
理论脱硫率可根据精矿到化学组成用以下经验公式粗略计算(假定精矿中的硫化物主要为Cu2S、mFeS.nFeS2):
式中:
DS1-一次脱硫率(FeS2分解);
DS2-二次脱硫率(FeS氧化);
DST-总脱硫率(炉渣和烟尘中的硫除外),%;
(Fe)-精矿含铁,%;
(S)-精矿含硫,%;
(Cu)-精矿含铜,%;
55~60
7~8.5
① 铜陵二冶A为富氧空气工业试验数据;B为1986~1993年生产平均值;
② 富氧空气工业试验数据;
③ 富氧空气生产资料。
四、铜回收率
密闭鼓风炉由于流程简单,中间环节少,铜锍品位较低,炉渣含四氧化三铁较少,渣含铜较低,故铜回收率较高。但如果精矿混捏不好,烟尘率加大,可降低铜回收率。一般直收率可达94%~96.5%。铜总回收率可达98%~98.5%。
4.1~4.7
6.5~8.5
9.5
1.46
14.18
20.73
35.34
4.4~4.5
7~8
8.77
铜密闭鼓风炉熔炼技术操作条件
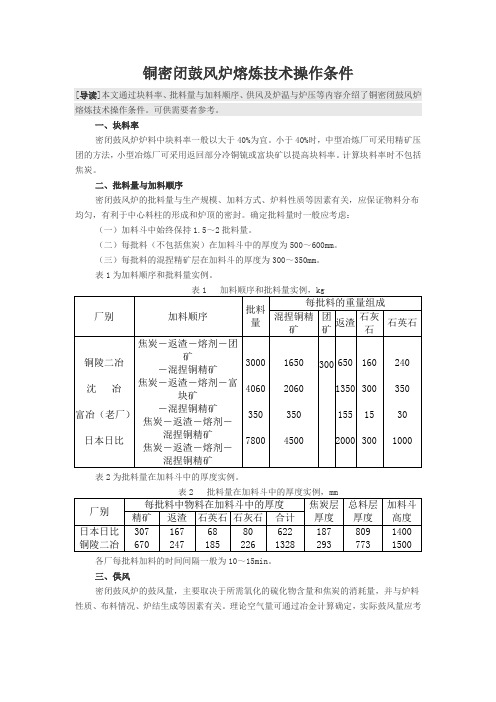
密闭鼓风炉的批料量与生产规模、加料方式、炉料性质等因素有关,应保证物料分布均匀,有利于中心料柱的形成和炉顶的密封。确定批料量时一般应考虑:
(一)加料斗中始终保持1.5~2批料量。
(二)每批料(不包括焦炭)在加料斗中的厚度为500~600mm。
(三)每批料的混捏精矿层在加料斗的厚度为300~350mm。
铜密闭鼓风炉熔炼技术操作条件
[导读]本文通过块料率、批料量与加料顺序、供风及炉温与炉压等内容介绍了铜密闭鼓风炉熔炼技术操作条件。可供需要者参考。
一、块料率
密闭鼓风炉炉料中块料率一般以大于40%为宜。小于40%时,中型冶炼厂可采用精矿压团的方法,小型冶炼厂可采用返回部分冷铜锍或富块矿以提高块料率。计算块料率时不包括焦炭。
340
420
470
烟气单体硫含量,g/m³0.78
0.35
密闭鼓风炉炉顶负压过高,漏入空气量增加,降低了烟气中二氧化硫浓度。但负压过低又会造成炉顶操作条件恶化,一般控制在50~100Pa为宜。表11为炉顶负压与烟气二氧化硫浓度的测定值。
表11 炉顶负压与烟气二氧化硫浓度的测定值
㎡
t/(㎡·d)
m³/min
%
m³/(㎡·d)
m³/t
10.5
38~45
390~400
21
30~38
~1400
10
40~45
330~400
21
33~40
~1240
2
40~45
75~80
21
38~40
~1320
1.5
45~50
50~55
21
33~37
~1060
2、风压 密闭鼓风炉的鼓风压力主要取决于炉内阻力,在一定范围内增加风压对熔炼过程有利。但风压过高会增加烟尘率和料层穿孔而跑空风。目前各厂的鼓风压力一般控制在8~10kPa。表4为鼓风压力实例。
鼓风炉熔炼富铅渣工艺流程三维动画演示系统

609 ) 50 3
( 明理工 大学 ,云南 昆 明 昆
摘
要 :针对鼓风炉熔炼 富铅渣技 术进行 多媒体演示和动画模拟 ,一方 面为基础理论提供感观 资料 以促进其
研 究 ,另一方 面,采用有别于传统的工艺讲解方式形象地再现整个流程 ,能够帮助使用人们尽 快了解新工艺 。在 此演示 系统 中,通过三维动画形式对此新工 艺的炉 内部状况进行模拟 ,创造出一种虚拟现实 的铅冶炼环境 。直观 的表现 了熔炼过程 中各种组分在炉 内的运动及走 向,为解决熔炼过程中无法观察冶金炉 内部状况 的问题提 出解决
1 三维动 画内容 的设计
1 1 概论 [ . 1 ]
富铅 渣 的鼓 风炉 熔 炼 是一 个 比较 复杂 的过 程 。 炉料 在炉 内形 成垂 直 的料 柱 ,它 支承 在熔炼 产 物 的
因为风况为了解决这个问题在炉体两侧边缘分别加入口在侧壁的下面风力较强鼓入的风常有沿着侧4了四个导向板加大其反弹力和摩擦力参数壁上升的倾向如果大块的炉料集中在两侧而较将到达导向板的离子反弹回炉内同时这样的处理小块分布在中央炉内的阻力会比较大使得鼓入使得料块在炉内的运动方向稍具不确定性有如强的风不能到达炉子中央区域而集中于两侧导致炉劲的气流推动炉料使之平衡于下还原区
KE W ORD Y S:ai t n c m ue ; l tun c ; e d i l n i ; o p t ba frae l —r hs ma o r s a e a g
日 U
吾
的工艺讲解方式形象地再现整个流程 ,帮助使用人 群尽快 了解新工 艺 ,节省 其学 习 时间 和精力 。在 此 演示系统中,利用 3 A DM X技术进行主要工艺过程 的动画制作 ,为熔炼过程 中无法观察冶金炉内状况
鼓风炉还原熔炼的基本原理

4.4.2 熔炼过程发生的主要过程
碳质燃料燃烧;
金属氧化物还原; 脉石及氧化锌成分造渣等过程; 可能还发生硫化物形成锍、砷化物形成黄渣过程; 上述熔体产物的沉淀分离过程
4.4.3 铅鼓风炉还原熔炼的理论基础
氧化铅还原热力学 (根据炉内上下区域温度)
327℃ :PbO(s)+CO=Pb(s)+CO2+63625J 327~883℃:PbO(s)+CO=Pb(l)+CO2+58183J >883℃: PbO(l)+CO=Pb(l)+CO2+67895J 均为放热反应,反应的平衡常数方程为 lgKp=3250/T+0.417×10-3T+0.3
如表4-4。
块度:50~120mm,小于50mm和大于120mm的不大于25%;空隙度:不小于 50%~60%;强度:烧结块的转鼓率为28%~40%,或从1.5m高处三次自然落
至水泥地面或钢板上,经筛分后,小于10mm的重量低于15%~20%。铅鼓风炉
用焦炭性质实例
4-2
4-3
鼓风炉中一般不加返渣(占用炉子生产能力,增加焦炭的消耗)。铁、硅、钙熔剂 和萤石应严格拒绝入炉,只作炉况不好,渣型变化时临时措施之用。
铁;
As, Sb, Bi部分以低价氧化物 挥发,部分被还原进入粗铅。
图4-1
4.4 鼓风炉炼铅
4.4.1 铅烧结块鼓风炉还原熔炼的目的 和少量的PbS、金属Pb及PbSO4形态存在,此外还含有伴存的Cu、Zn、Bi等 有价金属和贵金属Ag、Au以及一些脉石氧化物。 最大限度地将烧结块中的铅还原出来获得金属铅,同时将Au、Ag、 Bi等贵 金属富集其中; 将铜还原进入粗铅;若烧结块中含Cu、S 都高时,则使铜呈Cu2S形态进入 铅锍(俗称铅冰铜)中,以便下一步回收; 如果炉料中含有Ni、Co时,使其还原进入黄渣(俗称砷冰铜); 将烧结块中一些易挥发的有价金属化合物(CdO)富集于烟尘中,便于进一 步综合回收; 使脉石成分(SiO2、FeO、CaO、MgO、Al2O3)造渣,锌也以ZnO形态入渣, 便于回收。
鼓风炉熔炼再生铜(5)

书山有路勤为径,学海无涯苦作舟鼓风炉熔炼再生铜(5)鼓风炉熔炼的配料计算鼓风炉熔炼时需根据原料性质计算出所加熔剂量,常用的方法有两种。
一、有效熔剂法原料为含铜炉渣。
(1)已知条件a、含铜炉渣的化学成分为SiO2 21.50%、CaO 2.20%、FeO 14.40%、其他61.90%。
b、石英石成分为SiO2 92.4%、CaO 1.2%、FeO 0.3%。
c、石灰石成分为SiO2 1.3%、CaO 54%、FeO 0.5%。
d、选择的渣型为SiO2 30%、CaO 28%、FeO 14%。
(2)配料计算以100kg 含铜炉渣为计算基础a、计算石英石和石灰石的有效溶剂率100kg 石英石中含有1.2kg CaO,炉渣中CaO 与SiO2 之比是28:30 1.2kg CaO 造渣需1.2×30/28=1.2kg SiO2 100kg 石英石中游离的SiO2=92.4-1.29=91.11kg,即石英石的有效熔剂率为91.11%。
同样,100kg 石灰石中有1.3kg SiO2,因此石灰石中有1.3×28/30=1.2kg CaO 与SiO2 造渣,故石灰石的有效熔剂率为(54-1.2)÷100=52.8% b、计算炉渣量和各组成的量通过渣型和铜炉渣中含FeO 量计算出渣量为14.4/14×100=103kg 渣型各组成的量如下SiO2=103×0.30=30.9kgCaO=103×0.28=28.84kgFeO=103×0.14=14.40kg c、计算补加的石英石和石灰石量除去原料中SiO2、CaO 的含量,炉渣中还缺的量为SiO2=30.9-21.5=9.4kgCaO=28.8-2.2=26.64kg 需补加的石英石熔剂为9.4/91.11%=10.3kg 补加的石灰石熔剂为26.64/52.8%=10.3kg 故造渣率为103/ (100+10.3+50.5)×100%=64% 当熔剂质量稳定且加入量不大时,可近似取石英石的有效熔剂率为92%,石灰石的有效熔剂率为53%。
氧气底吹熔炼——鼓风炉还原炼铅新技术及应用
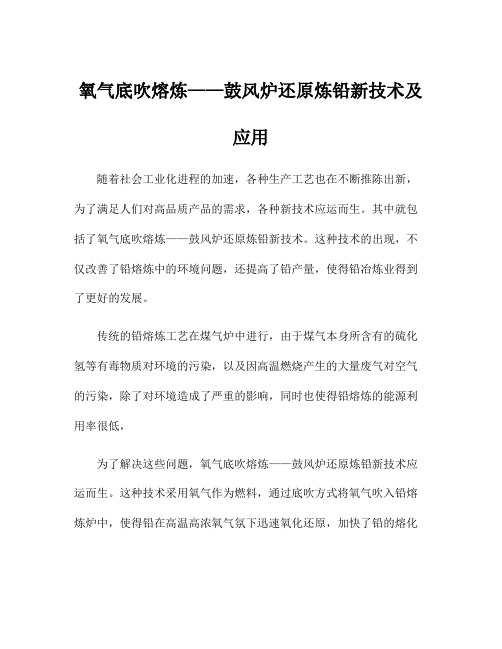
氧气底吹熔炼——鼓风炉还原炼铅新技术及
应用
随着社会工业化进程的加速,各种生产工艺也在不断推陈出新,为了满足人们对高品质产品的需求,各种新技术应运而生。
其中就包括了氧气底吹熔炼——鼓风炉还原炼铅新技术。
这种技术的出现,不仅改善了铅熔炼中的环境问题,还提高了铅产量,使得铅冶炼业得到了更好的发展。
传统的铅熔炼工艺在煤气炉中进行,由于煤气本身所含有的硫化氢等有毒物质对环境的污染,以及因高温燃烧产生的大量废气对空气的污染,除了对环境造成了严重的影响,同时也使得铅熔炼的能源利用率很低,
为了解决这些问题,氧气底吹熔炼——鼓风炉还原炼铅新技术应运而生。
这种技术采用氧气作为燃料,通过底吹方式将氧气吹入铅熔炼炉中,使得铅在高温高浓氧气氛下迅速氧化还原,加快了铅的熔化
和反应速率,同时废气、废渣产生率也得到了大幅度降低,不仅对环
境影响减小,而且对于铅产出质量的提高也有明显作用。
在现如今的铅冶炼业,氧气底吹熔炼——鼓风炉还原炼铅新技术
得到了广泛应用。
采用这种技术可以使得铅炉的能耗比传统炉子降低
约25%~35%不等,同样的情况下也能产生更多的铅产出,同时在生产过程中无污染的废气排放,使得工作环境更加安全,这给企业的生产过
程增加了很多收益和竞争力。
综上所述,氧气底吹熔炼——鼓风炉还原炼铅新技术的广泛应用,不仅对于环保和节能的发展产生了积极的推动作用,而且在提高生产
成本的同时也促进了铅冶炼业的发展。
因此,这种技术的应用前景非
常广阔,也值得我们在实际生产中予以重视。
铜矿冶炼工艺流程

铜矿冶炼工艺流程1.矿石准备铜矿的冶炼第一步是准备好入选的矿石。
矿石应符合一定的品位要求,即铜含量达到一定标准。
将矿石破碎至一定粒度,然后进行磨粉,以便于后续的化学反应。
磨好的矿石粉末需妥善储存,等待下一步处理。
2.焙烧与吹炼焙烧的目的是将矿石中的铜氧化物转化为可以被熔炼的硫酸铜。
焙烧过程中需严格控制焙烧温度和时间,以防止生成其他不希望的产品。
吹炼则是一个还原过程,将高价铜转化为低价铜,同时去除杂质。
这一步中的关键是控制吹炼终点,以获得最佳的铜品位和回收率。
3.鼓风炉熔炼鼓风炉熔炼是将焙烧和吹炼后的铜锍熔化,并还原为粗铜的过程。
在此过程中,需要控制鼓风量、熔炼温度和时间,以获得高质量的粗铜。
同时,炉温的控制也非常重要,以确保锍熔化完全,且不致于炉体损坏。
4.转炉吹炼转炉吹炼是将粗铜中的杂质进一步氧化,并吹入空中进行回收。
这一步的关键是控制吹炼温度和时间,以确保杂质充分氧化,同时不致于使铜品位下降。
5.火法精炼火法精炼是在高温下除去粗铜中的杂质,以获得高纯度的精铜。
这一步的关键是控制熔炼温度、时间和炉内气氛,以使杂质充分氧化并挥发出去。
6.电解精炼电解精炼是通过电解的方式将火法精炼后的铜进一步提纯。
在电解过程中,杂质会留在阳极或阴极上,从而去除杂质。
此步骤的关键是控制电解液的温度、电流密度和通电时间等参数,以确保提纯效果最佳。
7.铜烟处理铜烟是在冶炼过程中产生的有害气体,必须进行处理以防止环境污染。
一般采用的铜烟处理方法有吸收法、吸附法和燃烧法等。
无论采用哪种方法,应控制处理温度、时间和气氛,以确保充分除去铜烟中的有害物质。
鼓风炉炼铜工艺操作规程

鼓风炉炼铜工艺操作规程鼓风炉炼铜是一种常用的冶金工艺,下面是一份鼓风炉炼铜工艺操作规程,包括操作步骤、安全要求和工艺参数等。
一、操作步骤1. 准备工作:(1) 确保鼓风炉的设备完好,检查炉体、炉门、炉衬等部位是否有损坏。
(2) 准备足够的原料和草木灰作为还原剂。
(3) 检查鼓风机的运行情况,确保正常工作。
(4) 将铜料和还原剂按炉子容量的比例放入鼓风炉中。
2. 点火:(1) 打开鼓风机,确保有足够的氧气供给。
(2) 在鼓风炉的底部放入易燃物质,点火点燃。
(3) 等待火焰彻底燃烧后,逐渐加大鼓风机的风力,使火焰达到合适的温度。
3. 加热和处理:(1) 在火焰稳定后,逐渐加入铜料。
(2) 观察铜料的熔化情况,根据需要调整鼓风机的风力和炉温。
(3) 当铜料熔化后,根据需要加入其他合金元素。
(4) 在炉温达到所需温度时,进行合金的调整和均匀搅拌。
(5) 根据需要,逐渐加入除杂剂,并进行除渣操作。
4. 浇铸:(1) 确保合金熔池中没有杂质和渣滓后,进行浇铸操作。
(2) 将熔融的合金从鼓风炉中倒入预先准备好的铸模中。
5. 冷却和取出:(1) 等待铸件冷却,并确保冷却完全后再取出铸件。
(2) 对铸件进行必要的后处理,例如去除表面氧化皮等。
二、安全要求1. 在操作鼓风炉时,必须佩戴防护眼镜、防火服等个人防护用品。
2. 确保炉体周围的通风良好,以防止有毒气体积聚。
3. 操作时要保持清醒,避免酒精等物质的影响。
4. 加热时要小心熔融物溅出造成烫伤,使用合适的工具进行操作。
5. 遵循电力安全操作规程,确保电气设备的接地和绝缘良好。
三、工艺参数1. 炉温:根据需要决定,一般在1000-1200摄氏度之间。
2. 风力:根据铜料的熔化情况和操作要求适当调整,通常在30-80立方米/小时之间。
3. 加铜速度:根据铜料的熔化情况和炉子容量确定,一般控制在10-20千克/小时之间。
4. 加合金元素和除杂剂的比例和时间根据具体合金的需求而定,需谨慎操作。
熔池熔炼 (1)

上,其值取决于炉渣的熔点。
2
图2-16 密闭鼓风炉的构造
1-水套梁;2-顶水套;3-加料斗;4-端水套;5-风口;6-侧水套;
7-山型;8-烟道;9-咽喉口;10-风管
3
表2-5 铜精矿密闭鼓风炉熔炼的技术经济指标
4
为什么密闭鼓风炉的床能率和冰铜品位低? 炉料刚离开加料斗的下口时,块料自然向两侧滚动,而混 捏精矿和少量块料在炉子中央形成料柱。这就形成了炉子两侧 以块料和焦炭为主并夹有少量精矿,而炉子中央则以混捏精矿
18
白银炉炉体结构
19
白银法主要生产指标
项目 床能率/(t· m-2· d-1) 冰铜中ω(Cu)/% 精矿中ω(Cu)/% 精矿中ω(S)/% 渣中ω(Cu)/% 铜直收率/% 白银炼铜法 8.48 30.11 17.29 33.42 0.351(未返转炉渣) 96.42 项目 粉煤率/% 排风机进口烟气 中ψ(SO2)/% 脱硫率/% 烟尘率/% 总能耗(KJ· t精矿-1 ) 白银炼铜法 9.49 5.12
1995 - 2001 Technology transfer of the original innovation to a new application: Metals Recycling
27
13
表2-6 诺兰达法生产指标
项目
混合干精矿/(t· h-1) 高硫干精矿/(t· h-1) 石英石/(t· h-1) 石油焦/(t· h-1) 返料/(t· h-1) 风口鼓空气量/(万m3· h-1) 风口鼓氧量/(m3· h-1) 风口ψ(O2)/% 加料口鼓空气量/(m3· h-1) 烧嘴烧油量/(Kg· h-1) 烧嘴鼓空气量/(m3· h-1) 冰铜中ω(Cu)/% 渣中ω(Cu)/% 渣铁硅比 计算出炉烟量/(m3· h-1) 计算出炉烟气中ψ(SO2)/% 烟尘率/%
铅烧结矿的鼓风炉还原熔炼

熔炼压力对炉内气体组成和反应速率有一定影响。在高压下 ,气体在炉内的停留时间增加,有利于铅烧结矿的还原反应 进行。
操作参数对熔炼过程的影响
01
送风量
送风量的大小直接影响到炉内的氧气供应和燃烧强度,从而影响铅烧结
矿的还原效率和产品质量。
02
配料速度
配料速度决定了炉内物料反应的速度和时间,对最终产品的质量和产量
铅烧结矿的鼓风炉还原熔 炼
• 引言 • 铅烧结矿的特性 • 鼓风炉还原熔炼过程 • 鼓风炉还原熔炼的影响因素 • 鼓风炉还原熔炼的优化和改进 • 结论
01
引言
目的和背景
目的
铅烧结矿的鼓风炉还原熔炼是一种将铅烧结矿中的铅、锌等有价金属还原熔炼 成粗金属的方法。
背景
随着全球矿产资源的不断开采,低品位、复杂难处理矿石的利用问题日益突出。 铅烧结矿作为一种常见的低品位矿石,其高效、环保的冶炼技术成为研究热点。
熔炼过程中的排放主要包含烟气、炉渣和废水等,其中 烟气是主要的污染源。
能源消耗与生产规模、工艺参数、原料性质等因素有关, 降低能耗是提高生产效率的重要方向。
通过采用先进的工艺技术和设备,可以有效降低污染物 排放,提高环保水平。
04
鼓风炉还原熔炼的影响因素
原料的品质和配比
原料品质
铅烧结矿的品质对鼓风炉还原熔炼的 效率和产品质量有重要影响。高品质 的铅烧结矿通常含有较低的杂质,能 够提高熔炼过程的效率并降低能耗。
鼓风炉还原熔炼在处理复杂铅烧结矿 方面具有较大的优势,能够处理多种 含铅矿物,并实现多组分的综合回收。
鼓风炉还原熔炼具有较高的熔炼效率、 较低的能耗和较好的环保性能,能够 满足当前对环境保护和资源综合利用 的要求。
3铅烧结矿的鼓风炉熔炼(3)炉渣
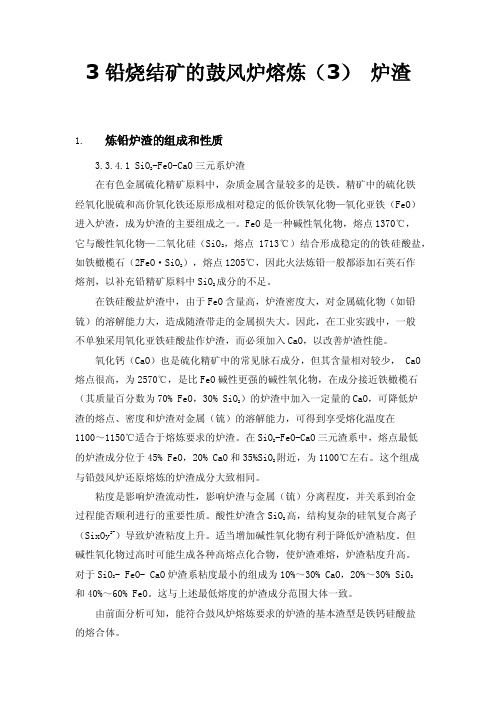
3铅烧结矿的鼓风炉熔炼(3)炉渣1.炼铅炉渣的组成和性质3.3.4.1 SiO2-FeO-CaO三元系炉渣在有色金属硫化精矿原料中,杂质金属含量较多的是铁。
精矿中的硫化铁经氧化脱硫和高价氧化铁还原形成相对稳定的低价铁氧化物—氧化亚铁(FeO)进入炉渣,成为炉渣的主要组成之一。
FeO是一种碱性氧化物,熔点1370℃,它与酸性氧化物—二氧化硅(SiO2,熔点1713℃)结合形成稳定的的铁硅酸盐,如铁橄榄石(2FeO·SiO2),熔点1205℃,因此火法炼铅一般都添加石英石作熔剂,以补充铅精矿原料中SiO2成分的不足。
在铁硅酸盐炉渣中,由于FeO含量高,炉渣密度大,对金属硫化物(如铅锍)的溶解能力大,造成随渣带走的金属损失大。
因此,在工业实践中,一般不单独采用氧化亚铁硅酸盐作炉渣,而必须加入CaO,以改善炉渣性能。
氧化钙(CaO)也是硫化精矿中的常见脉石成分,但其含量相对较少, CaO 熔点很高,为2570℃,是比FeO碱性更强的碱性氧化物,在成分接近铁橄榄石(其质量百分数为70% FeO,30% SiO2)的炉渣中加入一定量的CaO,可降低炉渣的熔点、密度和炉渣对金属(锍)的溶解能力,可得到享受熔化温度在1100~1150℃适合于熔炼要求的炉渣。
在SiO2-FeO-CaO三元渣系中,熔点最低的炉渣成分位于45% FeO,20% CaO和35%SiO2附近,为1100℃左右。
这个组成与铅鼓风炉还原熔炼的炉渣成分大致相同。
粘度是影响炉渣流动性,影响炉渣与金属(锍)分离程度,并关系到冶金过程能否顺利进行的重要性质。
酸性炉渣含SiO2高,结构复杂的硅氧复合离子(SixOy2-)导致炉渣粘度上升。
适当增加碱性氧化物有利于降低炉渣粘度。
但碱性氧化物过高时可能生成各种高熔点化合物,使炉渣难熔,炉渣粘度升高。
对于SiO2- FeO- CaO炉渣系粘度最小的组成为10%~30% CaO,20%~30% SiO2和40%~60% FeO。
鼓风炉技术操作规程解析

鼓风炉熔炼操作分开炉、正常操作和停炉三个部分。
1开炉1.1烘烤炉缸新炉缸及虹吸井砌筑好后,先用木炭小火烘烤,使水分逐渐蒸发,应严格按照升温曲线,尽可能做到温度缓慢上升。
切记不可升温太急,以防砖缝开裂,使生产中大量铅液渗入而损坏炉缸。
甚至翻底而被迫停炉。
在木炭烘烤期间,应勤除灰,保证热的传递,烘热炉底。
用木炭烘烤时间一般为5~7天。
视具体情况而定。
烘烤后,清除干净炉缸余灰,改用木柴,逐渐提高温度。
木柴烤期间一般4~7天。
烘炉缸理论升温曲线如图1所示。
可参照控制。
烘烤的各个阶段,均应仔细检查炉缸各部受热和耐火砖的膨胀情况,及时做好记录。
发现情况有异。
迅速研究,采取措施处理。
当炉缸温度升到700°C以上时,即转入正常开炉操作。
温度(℃)1000 紧接开炉900800 保温700 7℃/h600 保温500400 5℃/h300 保温200 3℃/h1000 1 2 3 4 5 6 7 8 9 10 11 12 13 14 15 16 17时间(天)图1 鼓风炉炉缸升温曲线1.2开炉操作开炉作业包括5 个步骤,按加入顺序依次为:木柴——底焦——渣料——过渡料——正式料。
底铅在加底焦过程中分批加入。
(1)加木柴。
首先,用2:1的耐火泥和焦粉拌合料,堵好炉底排铅口(即安全口)虹吸口。
木柴主要作引火之用,分3批加入。
点火前先把木柴规整铺满炉缸,不得乱扔形成架空。
在木柴上适当浇上废机油,然后点火。
待木柴全部点着,火苗上来后,从炉顶或炉身工作门投入第二批木柴,投到风口处,待第二批木柴火满上来后,再加第三批木柴,投到风口上方1~1.5米处。
投木柴时,必须按照炉口纵向平行投入,保持厚薄一致。
将柴面找平,防架空现象。
(2)加底焦待第三批木柴上火后,即开始加底焦。
底焦分5批加入,每批加焦碳600 kg,同时结合焦碳灰分量及成分,计算加入定量铁矿石和石灰石。
下批底焦要在上批底焦上火后再加。
从第三批底焦开始配加底铅。
火法炼铜的主体部分-熔炼

书山有路勤为径,学海无涯苦作舟
火法炼铜的主体部分-熔炼
熔炼是火法炼铜的主体部分,其方法较多。
反射炉熔炼是传统的主要炼铜方法之一,曾经发展较快,现在仍占全世界铜熔炼总生产能力的50%左右。
但是反射炉熔炼具有热效率低和烟气含二氧化硫浓度低,污染环境,难以处理回收两大缺点,所以除有的工厂已用其它新工艺取代了熔炼反射炉外,全世界对现存的熔炼反射炉都在着手进行技术改造。
但它在炼铜工业具有悠久的历史中起过重大作用,积累了较丰富的经验和技术资料可供借鉴。
鼓风炉熔炼为最早的传统炼铜方法。
现在国外采用鼓风炉炼铜的工厂已很少,仅在某些老厂使用。
我国原有的鼓风炉均为敞开式,现已全部改为料封式密闭鼓风炉。
因其取消了烧结过程使流程简化,并可将烟气与吹炼炉烟气混合制酸,故在中小型厂设计中仍可采用。
电炉熔炼适于处理高熔点原料,对原料的适应性强。
在电力资源较丰富的地区,现在采用电炉的工厂略有增加。
由于环境保护的要求,国外有些工厂以电炉取代反射炉,引电炉烟气制酸。
闪速熔炼是一种强化冶金过程,其生产率较高,铜锍品位高,燃料消耗较低,烟气中含二氧化硫浓度较高,适于回收制酸,进来发展较快。
其发展的趋势是:设备大型化和操作自动化;采用高温富氧空气以强化熔炼过程;采用双接触法制酸,可使排放尾气中二氧化硫含量达300×10-6 以下,硫的回收率可达95%;近来有在闪速炉内直接产出粗铜的。
其缺点是:通常要求炉料粒度在1mm 以下,含水0.3%以下,备料系统比较复杂,烟尘率约10%,炉渣含铜较高,需另行处理。
白银炼铜法是我国白银有色金属公司开发的一种熔炼技术,与诺兰达法、瓦。