材料成型加工与工艺学 习题解答6
(完整word版)材料成型工艺基础习题及答案
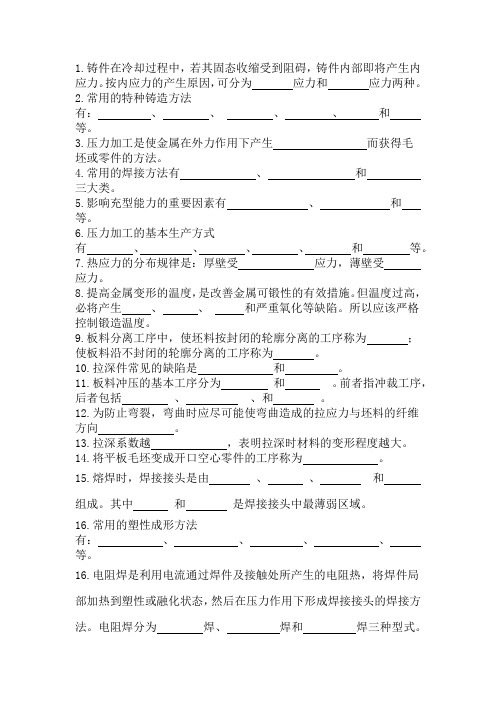
1.铸件在冷却过程中,若其固态收缩受到阻碍,铸件内部即将产生内应力。
按内应力的产生原因,可分为应力和应力两种。
2.常用的特种铸造方法有:、、、、和等。
3.压力加工是使金属在外力作用下产生而获得毛坯或零件的方法。
4.常用的焊接方法有、和三大类。
5.影响充型能力的重要因素有、和等。
6.压力加工的基本生产方式有、、、、和等。
7.热应力的分布规律是:厚壁受应力,薄壁受应力。
8.提高金属变形的温度,是改善金属可锻性的有效措施。
但温度过高,必将产生、、和严重氧化等缺陷。
所以应该严格控制锻造温度。
9.板料分离工序中,使坯料按封闭的轮廓分离的工序称为;使板料沿不封闭的轮廓分离的工序称为。
10.拉深件常见的缺陷是和。
11.板料冲压的基本工序分为和。
前者指冲裁工序,后者包括、、和。
12.为防止弯裂,弯曲时应尽可能使弯曲造成的拉应力与坯料的纤维方向。
13.拉深系数越,表明拉深时材料的变形程度越大。
14.将平板毛坯变成开口空心零件的工序称为。
15.熔焊时,焊接接头是由、、和组成。
其中和是焊接接头中最薄弱区域。
16.常用的塑性成形方法有:、、、、等。
16.电阻焊是利用电流通过焊件及接触处所产生的电阻热,将焊件局部加热到塑性或融化状态,然后在压力作用下形成焊接接头的焊接方法。
电阻焊分为焊、焊和焊三种型式。
其中适合于无气密性要求的焊件;适合于焊接有气密性要求的焊件;只适合于搭接接头;只适合于对接接头。
1.灰口铸铁的流动性好于铸钢。
()2.为了实现顺序凝固,可在铸件上某些厚大部位增设冷铁,对铸件进行补缩。
()3. 热应力使铸件的厚壁受拉伸,薄壁受压缩。
()4.缩孔是液态合金在冷凝过程中,其收缩所缩减的容积得不到补足,在铸件内部形成的孔洞。
()5.熔模铸造时,由于铸型没有分型面,故可生产出形状复杂的铸件。
()6.为便于造型时起出模型,铸件上应设计有结构斜度即拔模斜度。
()7.合金的液态收缩是铸件产生裂纹、变形的主要原因。
()8.在板料多次拉深时,拉深系数的取值应一次比一次小,即m1>m2>m3…>mn。
《材料成型工艺基础》部分习题答案
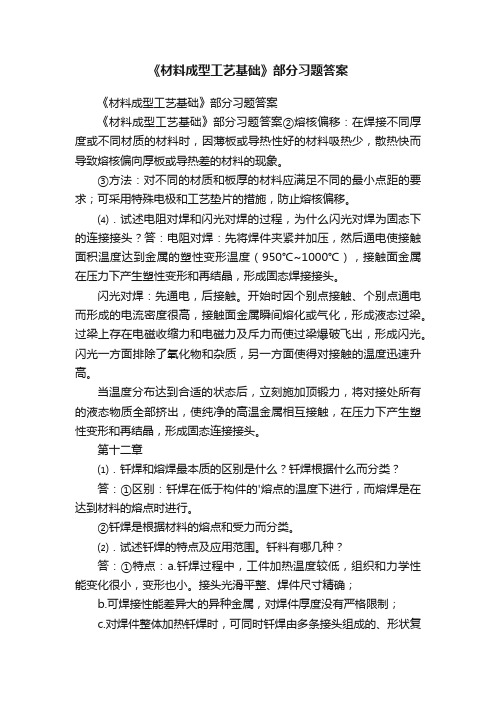
《材料成型工艺基础》部分习题答案《材料成型工艺基础》部分习题答案《材料成型工艺基础》部分习题答案②熔核偏移:在焊接不同厚度或不同材质的材料时,因薄板或导热性好的材料吸热少,散热快而导致熔核偏向厚板或导热差的材料的现象。
③方法:对不同的材质和板厚的材料应满足不同的最小点距的要求;可采用特殊电极和工艺垫片的措施,防止熔核偏移。
⑷.试述电阻对焊和闪光对焊的过程,为什么闪光对焊为固态下的连接接头?答:电阻对焊:先将焊件夹紧并加压,然后通电使接触面积温度达到金属的塑性变形温度(950℃~1000℃),接触面金属在压力下产生塑性变形和再结晶,形成固态焊接接头。
闪光对焊:先通电,后接触。
开始时因个别点接触、个别点通电而形成的电流密度很高,接触面金属瞬间熔化或气化,形成液态过梁。
过梁上存在电磁收缩力和电磁力及斥力而使过梁爆破飞出,形成闪光。
闪光一方面排除了氧化物和杂质,另一方面使得对接触的温度迅速升高。
当温度分布达到合适的状态后,立刻施加顶锻力,将对接处所有的液态物质全部挤出,使纯净的高温金属相互接触,在压力下产生塑性变形和再结晶,形成固态连接接头。
第十二章⑴.钎焊和熔焊最本质的区别是什么?钎焊根据什么而分类?答:①区别:钎焊在低于构件的'熔点的温度下进行,而熔焊是在达到材料的熔点时进行。
②钎焊是根据材料的熔点和受力而分类。
⑵.试述钎焊的特点及应用范围。
钎料有哪几种?答:①特点:a.钎焊过程中,工件加热温度较低,组织和力学性能变化很小,变形也小。
接头光滑平整、焊件尺寸精确;b.可焊接性能差异大的异种金属,对焊件厚度没有严格限制;c.对焊件整体加热钎焊时,可同时钎焊由多条接头组成的、形状复杂的构件,生产率很高;d.钎焊设备简单,生产投资费用少。
②范围:焊接精密仪表,电器零部件,异种金属构件,某些复杂薄板结构。
③类型:硬钎焊、软钎焊。
第十三章⑴.什么叫焊接性?怎样评价和判断材料的焊接性?答:焊接性:被焊金属在一定的焊接方法、焊接材料、工艺参数及结构形式条件下,获得优质焊接接头的难易程度,即金属材料在一定的焊接工艺条件下,表现出“好焊”和“不好焊”的差别。
2019年自考《材料加工和成型工艺》试题及答案

2019年自考《材料加工和成型工艺》试题及答案选择题1.为了防止铸件过程中浇不足以及冷隔等缺陷产生,可以采用的工程措施有( )。
A.减弱铸型的冷却能力;B.增加铸型的直浇口高度;C.提高合金的浇注温度;D.A、B和C;E.A和C。
2.顺序凝固和同时凝固均有各自的优缺点。
为保证铸件质量,通常顺序凝固适合于( ),而同时凝固适合于( )。
A.吸气倾向大的铸造合金;B.产生变形和裂纹倾向大的铸造合金;C.流动性差的铸造合金;D.产生缩孔倾向大的铸造合金。
3.铸造应力过大将导致铸件产生变形或裂纹。
消除铸件中残余应力的方法是( );消除铸件中机械应力的方法是( )。
A.采用同时凝固原则;B.提高型、芯砂的退让性;C.及时落砂;D.时效处理。
4.合金的铸造性能主要是指合金的( )和( )。
A.充型能力;B.流动性;C.收缩;D.缩孔倾向;E.应力大小;F.裂纹倾向。
6.如图2-2所示应力框铸件。
浇注并冷却到室温后,各杆的应力状态为( )。
若用钢锯沿A-A线将φ30杆锯断,此时断口间隙将( )。
断口间隙变化的原因是各杆的应力( ),导致φ30杆( ),φ10杆( )。
图2-2A.增大;B.减小;C.消失;D.伸长;E.缩短;F.不变;G.φ30杆受压,φ10杆受拉; H.φ30杆受拉,φ10杆受压。
7.常温下落砂之前,在下图所示的套筒铸件中( )。
常温下落砂以后,在该铸件中( )。
A.不存在铸造应力;B.只存在拉应力;C.存在残余热应力;D.只存在压应力;E.存在机械应力;F.C和E。
8.铸铁生产中,为了获得珠光体灰口铸铁,可以采用的方法有( )。
A.孕育处理;B.适当降低碳、硅含量;C.适当提高冷却速度;D.A、B和C;E.A和C。
9.HTl00、KTH300-06、QT400-18的力学性能各不相同,主要原因是它们的( )不同。
A.基体组织;B.碳的存在形式;C.石墨形态;D.铸造性能。
10.灰口铸铁(HT)、球墨铸铁(QT)、铸钢(ZG)三者铸造性能的优劣顺序( );塑性的高低顺序为( )。
材料成形工艺基础习题答案
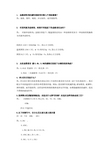
1.金属材料的机械性能通常用哪几个指标衡量?答:强度、塑性、硬度、冲击韧性、疲劳极限等。
2.何谓同素异晶转变,纯铁不同温度下的晶格变化如何?答:同素异晶转变:金属在固态下,随温度的改变由一种晶格转变为另一种晶格的现象称为同素异晶转变。
纯铁在1538。
C结晶为σ-Fe ,体心立方结构;温度降到1394。
C时,σ-Fe转变为γ-Fe,面心立方结构;降到912。
C时,γ-Fe转变为α-Fe,为体心立方结构3.从状态图看含碳0.4%、0.9%的碳钢在室温下由哪些组织构成?答:0.4%由铁素体(F)+珠光体(P)0.9%由二次渗碳体(Fe3CⅡ)+珠光体(P)4. 淬火的目的是什么?答:淬火的主要目的是使奥氏体化后的工年获得尽量多的马氏体(或下贝氏体组织),然后配以不同的温度回火获得各种需要的性能。
例如:提高钢件的机械性能,诸如硬度、耐磨性、弹性极限、疲劳强度等,改善某些特殊钢的物理或者化学性能,如增强磁钢的铁磁性,提高不锈钢的耐蚀性等。
5.某弹簧由优质碳素钢制造,应选用什么牌号的钢?应选用怎样的热处理工艺?答:含碳量在0.6%-0.9%之间,65、70、85、65Mn.65Mn淬火+中温回火6.从下列钢号中,估计出其主要元素大致含量20 45 T10 16Mn 40Cr答:0.2%C 、0.45%C、1.0%C,Mn≤0.4%,Si≤0.35、0.16%C,Mn1.2%-1.6% 、0.4%C,0.8-1.1%Cr7.简述铸造成型的实质及优缺点。
答:铸造成型的实质是:利用金属的流动性,逐步冷却凝固成型的工艺过程。
优点:1.工艺灵活生大,2.成本较低,3.可以铸出外形复杂的毛坯缺点:1.组织性能差,2机械性能较低,3.难以精确控制,铸件质量不够稳定4.劳动条件太差,劳动强度太大。
8.合金流动性取决于哪些因素?合金流动性不好对铸件品质有何影响?答:合金流动性取决于 1.合金的化学成分 2.浇注温度 3.浇注压力 4.铸型的导热能力5.铸型的阻力合金流动性不好:产生浇不到、冷隔等缺陷,也是引起铸件气孔、夹渣和缩孔缺陷的间接原因。
材料成型工艺基础习题解答

第一章金属材料与热处理1、常用的力学性能有哪些?各性能的常用指标是什么?答:刚度:弹性模量E强度:屈服强度和抗拉强度塑性:断后伸长率和断面收缩率硬度:冲击韧性:疲劳强度:2、4、金属结晶过程中采用哪些措施可以使其晶粒细化?为什么?答:过冷细化:采用提高金属的冷却速度,增大过冷度细化晶粒。
变质处理:在生产中有意向液态金属中加入多种难溶质点(变质剂),促使其非自发形核,以提高形核率,抑制晶核长大速度,从而细化晶粒。
7、9、什么是热处理?钢热处理的目的是什么?答:热处理:将金属材料或合金在固态范围内采用适当的方法进行加热、保温和冷却,以改变其组织,从而获得所需要性能的一种工艺。
热处理的目的:强化金属材料,充分发挥钢材的潜力,提高或改善工件的使用性能和加工工艺性,并且可以提高加工质量、延长工件和刀具使用寿命,节约材料,降低成本。
第二章铸造成型技术2、合金的铸造性能是指哪些性能,铸造性能不良,可能会引起哪些铸造缺陷?答:合金的铸造性能指:合金的充型能力、合金的收缩、合金的吸气性;充型能力差的合金产生浇不到、冷隔、形状不完整等缺陷,使力学性能降低,甚至报废。
合金的收缩合金的吸气性是合金在熔炼和浇注时吸入气体的能力,气体在冷凝的过程中不能逸出,冷凝则在铸件内形成气孔缺陷,气孔的存在破坏了金属的连续性,减少了承载的有效面积,并在气孔附近引起应力集中,降低了铸件的力学性能。
6、什么是铸件的冷裂纹和热裂纹?防止裂纹的主要措施有哪些?答:热裂是在凝固末期,金属处于固相线附近的高温下形成的。
在金属凝固末期,固体的骨架已经形成,但树枝状晶体间仍残留少量液体,如果金属此时收缩,就可能将液膜拉裂,形成裂纹。
冷裂是在较低温度下形成的,此时金属处于弹性状态,当铸造应力超过合金的强度极限时产生冷裂纹。
防止措施:热裂——合理调整合金成分,合理设计铸件结构,采用同时凝固原则并改善型砂的退让性。
冷裂——对钢材材料合理控制含磷量,并在浇注后不要过早落砂。
2021自考《材料加工和成型工艺》习题集及答案

2021自考《材料加工和成型工艺》习题集及答案一、选择题1.为了防止铸件过程中浇不足以及冷隔等缺陷产生,可以采用的工程措施有( )。
A.减弱铸型的冷却能力;B.增加铸型的直浇口高度;C.提高合金的浇注温度;D.A、B和C;E.A和C。
2.顺序凝固和同时凝固均有各自的优缺点。
为保证铸件质量,通常顺序凝固适合于( ),而同时凝固适合于( )。
A.吸气倾向大的铸造合金;B.产生变形和裂纹倾向大的铸造合金;C.流动性差的铸造合金;D.产生缩孔倾向大的铸造合金。
3.铸造应力过大将导致铸件产生变形或裂纹。
消除铸件中残余应力的方法是( );消除铸件中机械应力的方法是( )。
A.采用同时凝固原则;B.提高型、芯砂的退让性;C.及时落砂;D.时效处理。
4.合金的铸造性能主要是指合金的( )和( )。
A.充型能力;B.流动性;C.收缩;D.缩孔倾向;E.应力大小;F.裂纹倾向。
6.如图2-2所示应力框铸件。
浇注并冷却到室温后,各杆的应力状态为( )。
若用钢锯沿A-A线将φ30杆锯断,此时断口间隙将( )。
断口间隙变化的原因是各杆的应力( ),导致φ30杆( ),φ10杆( )。
图2-2A.增大;B.减小;C.消失;D.伸长;E.缩短;F.不变;G.φ30杆受压,φ10杆受拉; H.φ30杆受拉,φ10杆受压。
7.常温下落砂之前,在下图所示的套筒铸件中( )。
常温下落砂以后,在该铸件中( )。
A.不存在铸造应力;B.只存在拉应力;C.存在残余热应力;D.只存在压应力;E.存在机械应力;F.C和E。
8.铸铁生产中,为了获得珠光体灰口铸铁,可以采用的方法有( )。
A.孕育处理;B.适当降低碳、硅含量;C.适当提高冷却速度;D.A、B和C;E.A和C。
9.HTl00、KTH300-06、QT400-18的力学性能各不相同,主要原因是它们的( )不同。
A.基体组织;B.碳的存在形式;C.石墨形态;D.铸造性能。
10.灰口铸铁(HT)、球墨铸铁(QT)、铸钢(ZG)三者铸造性能的优劣顺序( );塑性的高低顺序为( )。
工程材料与成型工艺基础习题及答案
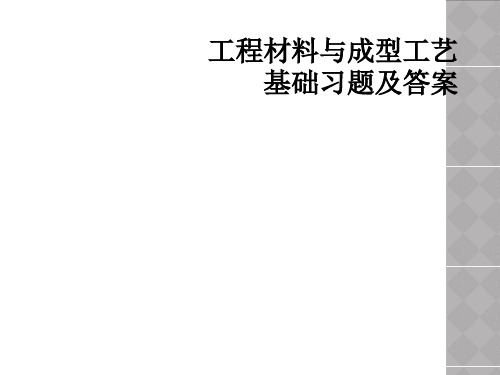
素异晶转变温度和晶格类型 。
(1)固态下随着温度的变化, 金属的晶体结构从一种晶格类 型转变为另一种晶格类型的过
温度℃
1538 ℃ Fe
体心 1394 ℃
Fe
面心
程。
912 ℃
体心
Fe
时间
8.图1-1所示为部分的铁碳合金状态图,请在右边的T-t图中 画出含碳量为0.45%的铁碳合金的结晶过程并标注出各温度 段的组织。
(1)常用力学性能指标有:
强度、塑性、刚度、硬度、冲击韧性、疲劳强度。
(2) 零件在使用过程中突然发生断裂,是由于强度、塑 性、冲击韧性、疲劳强度等力学性能指标不足所造成 的。
2.画出低碳钢的应力-应变曲线,并简述拉伸变形的几 个阶段。
oe段:弹性变形
b
esbk段:塑性变形
s
s点:屈服点
e
k
b点:最大应力点
温度 ℃
1538 ℃
A
T
L
912
℃G
E
1147 ℃
S 727
P
℃
Q
0.45
C
C%
L L+A
A
A+F F+P t
11. 填表回答:
钢号
普 Q235
15 45 60Si2Mn T8A 9SiCr W18Cr4V
质量 优 高优
类别
含碳量
成分
低 中 高 碳素 合金
用途 结构 工具
适用零 件举例
冲压件 冲压件
其余
上 下
11.确定如图2-7 所示铸件的铸造工艺方案。要求如下: (1)画出几种可能的分型方案 ; (2)在单件、小批生产条件下,分析并确定最佳工艺方案; (3)按所选最佳方案绘制铸造工艺图(包括浇注位置、分型 面、机械加工余量、起模斜度、铸造圆角、型芯及芯头等)
(完整版)高分子材料成型加工课后习题答案

1、什么是“非分散混合”,什么是“分散混合”,两者各主要通过何种物料运动和混合操作来实现?答:①非分散混合在混合中仅增加离子在混合物中空间分布均匀性而不减小粒子初始尺寸的过程称为非分散混合或简单混合。
这种混合的运动基本形式是通过对流来实现的,可以通过包括塞形流动和不需要物料连续变形的简单体积排列和置换来达到。
②分散混合是指在混合过程中发生粒子尺寸减小到极限值,同时增加相界面和提高混合物组分均匀性的混合过程。
分散混合主要是靠剪切应力和拉伸应力作用实现的。
分散混合的目的是把少数组分的固体颗粒和液相滴分散开来,成为最终粒子或允许的更小颗粒或滴,并均匀地分散到多组分中,这就涉及少组分在变形粘性流体中的破裂为题,这是靠强迫混合物通过窄间隙而形成的高剪切区来完成的。
2、在热固性塑料模压成型中,提高压力应相应地降低还是升高模压压力才对模压成型工艺有利?为什么?答:在一定温度范围内,模温升高,物料流动性提高,模压压力可降低,但模温提高也会使塑料的交联反应速率加速,从而导致熔融物料的粘度迅速增高,反而需要更高的模压压力。
3、热固性塑料模压成型中物料的预热温度对模压压力有何影响?为什么?答:对塑料进行预热可以提高流动性,降低模压压力,但如果预热温度过高或预热时间过长会使塑料在预热过程中有部分固化,会抵消预热增大流动性效果,模压是需更高的压力来保证物料充满型腔。
1、什么是聚合物的结晶取向?它们有何不同?研究结晶和取向对高分子材料加工有何实际影响?答:结晶是聚合物分子在三维空间呈周期性重复排列的过程,而取向是取向单元在外力作用下择优排列的过程,取向单元可以是:基团、链段、分子链、晶粒、晶片或变形的球晶等。
结晶是材料自身的性质,只发生在分子、原子、离子这些基础的单元上,取向的产生是外力作用的结果,取向单元也更多样。
结晶可以影响材料的拉伸强度、弹性模量、冲击强度、耐热性、耐候性、吸水性、透明性、透气性、成型收缩性等物性。
取向后的聚合物,在取向方向和垂直于取向方向上性能差异特别显著。
材料加工成型 课后习题答案
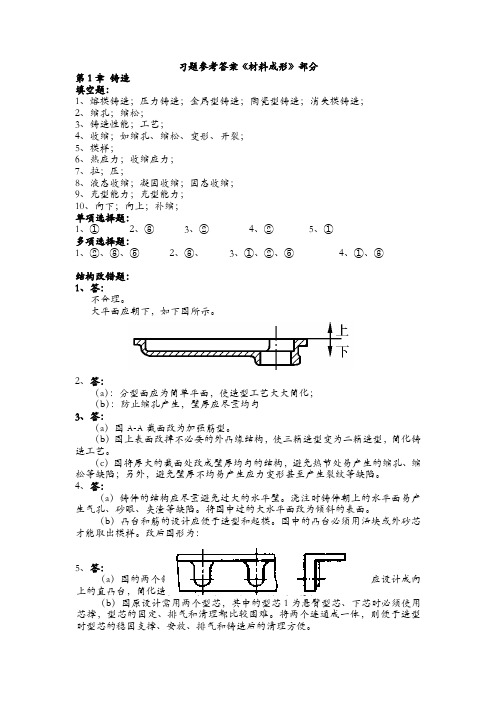
习题参考答案《材料成形》部分第1章铸造填空题:1、熔模铸造;压力铸造;金属型铸造;陶瓷型铸造;消失模铸造;2、缩孔;缩松;3、铸造性能;工艺;4、收缩;如缩孔、缩松、变形、开裂;5、模样;6、热应力;收缩应力;7、拉;压;8、液态收缩;凝固收缩;固态收缩;9、充型能力;充型能力;10、向下;向上;补缩;单项选择题:1、①2、③3、②4、②5、①多项选择题:1、②、③、⑤2、③、3、①、②、⑤4、①、③结构改错题:1、答:不合理。
大平面应朝下,如下图所示。
2、答:(a):分型面应为简单平面,使造型工艺大大简化;(b):防止缩孔产生,壁厚应尽量均匀3、答:(a)图A-A截面改为加强筋型。
(b)图上表面改掉不必要的外凸缘结构,使三箱造型变为二箱造型,简化铸造工艺。
(c)图将厚大的截面处改成壁厚均匀的结构,避免热节处易产生的缩孔、缩松等缺陷;另外,避免壁厚不均易产生应力变形甚至产生裂纹等缺陷。
4、答:(a)铸件的结构应尽量避免过大的水平壁。
浇注时铸件朝上的水平面易产生气孔、砂眼、夹渣等缺陷。
将图中过的大水平面改为倾斜的表面。
(b)凸台和筋的设计应便于造型和起模。
图中的凸台必须用活块或外砂芯才能取出模样。
改后图形为:5、答:(a)图的两个斜凸台在造型时影响起模,需采用活快。
因此,应设计成向上的直凸台,简化造型工艺,减低成本、提高生产效率。
(b)图原设计需用两个型芯,其中的型芯1为悬臂型芯、下芯时必须使用芯撑,型芯的固定、排气和清理都比较困难。
将两个连通成一体,则便于造型时型芯的稳固支撑、安放、排气和铸造后的清理方便。
简答题: 1、答: 起始阶段两杆处于塑性阶段,冷却到t 1-t 2阶段后,细杆进入弹性状态而粗干仍处于塑性,导致在横杆的作用下将对粗干产生压应力,细杆受到拉应力。
这时粗杆将产生压塑变形,使粗细两杆收缩趋于一致,应力将消失。
继续冷却T2-T3,此时两杆均进入弹性状态,粗杆温度高,产生较大收缩,而细杆温度低,收缩以几乎停止。
《材料成型工艺基础》部分习题答案
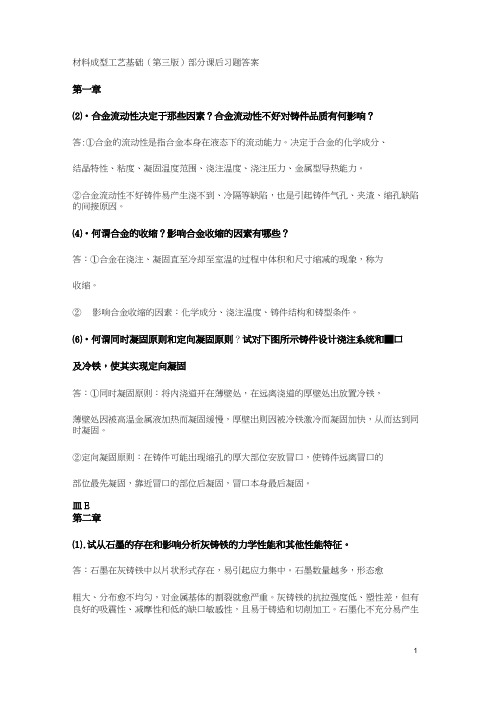
材料成型工艺基础(第三版)部分课后习题答案第一章⑵•合金流动性决定于那些因素?合金流动性不好对铸件品质有何影响?答:①合金的流动性是指合金本身在液态下的流动能力。
决定于合金的化学成分、结晶特性、粘度、凝固温度范围、浇注温度、浇注压力、金属型导热能力。
②合金流动性不好铸件易产生浇不到、冷隔等缺陷,也是引起铸件气孔、夹渣、缩孔缺陷的间接原因。
⑷•何谓合金的收缩?影响合金收缩的因素有哪些?答:①合金在浇注、凝固直至冷却至室温的过程中体积和尺寸缩减的现象,称为收缩。
②影响合金收缩的因素:化学成分、浇注温度、铸件结构和铸型条件。
⑹•何谓同时凝固原则和定向凝固原则?试对下图所示铸件设计浇注系统和■口及冷铁,使其实现定向凝固答:①同时凝固原则:将内浇道开在薄壁处,在远离浇道的厚壁处出放置冷铁,薄壁处因被高温金属液加热而凝固缓慢,厚壁出则因被冷铁激冷而凝固加快,从而达到同时凝固。
②定向凝固原则:在铸件可能出现缩孔的厚大部位安放冒口,使铸件远离冒口的部位最先凝固,靠近冒口的部位后凝固,冒口本身最后凝固。
皿E第二章⑴.试从石墨的存在和影响分析灰铸铁的力学性能和其他性能特征。
答:石墨在灰铸铁中以片状形式存在,易引起应力集中。
石墨数量越多,形态愈粗大、分布愈不均匀,对金属基体的割裂就愈严重。
灰铸铁的抗拉强度低、塑性差,但有良好的吸震性、减摩性和低的缺口敏感性,且易于铸造和切削加工。
石墨化不充分易产生白口,铸铁硬、脆,难以切削加工;石墨化过分,则形成粗大的石墨,铸铁的力学性能降低。
⑵•影响铸铁中石墨化过程的主要因素是什么?相同化学成分的铸铁件的力学性能是否相同?答:①主要因素:化学成分和冷却速度。
②铸铁件的化学成分相同时铸铁的壁厚不同,其组织和性能也不同。
在厚壁处冷却速度较慢,铸件易获得铁素体基体和粗大的石墨片,力学性能较差;而在薄壁处,冷却速度较快,铸件易获得硬而脆的白口组织或麻口组织。
⑸•什么是孕育铸铁?它与普通灰铸铁有何区别?如何获得孕育铸铁?答:①经孕育处理后的灰铸铁称为孕育铸铁。
《高分子材料成型加工》课后部分习题参考答案
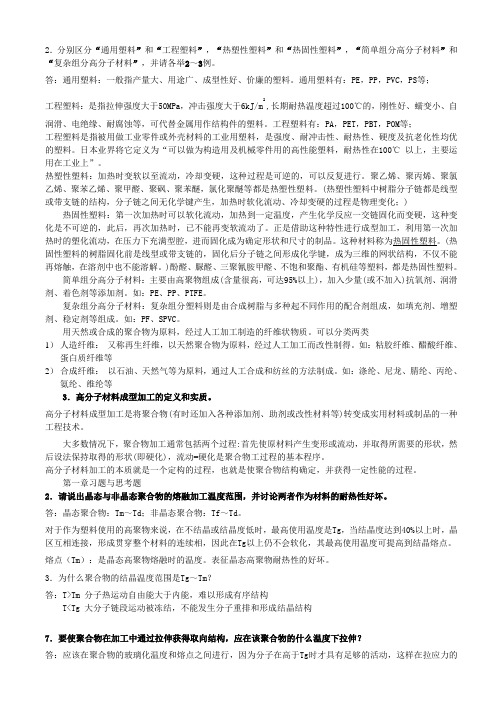
2.分别区分“通用塑料”和“工程塑料”,“热塑性塑料”和“热固性塑料”,“简单组分高分子材料”和“复杂组分高分子材料”,并请各举2~3例。
答:通用塑料:一般指产量大、用途广、成型性好、价廉的塑料。
通用塑料有:PE,PP,PVC,PS等;工程塑料:是指拉伸强度大于50MPa,冲击强度大于6kJ/m2 ,长期耐热温度超过100℃的,刚性好、蠕变小、自润滑、电绝缘、耐腐蚀等,可代替金属用作结构件的塑料。
工程塑料有:PA,PET,PBT,POM等;工程塑料是指被用做工业零件或外壳材料的工业用塑料,是强度、耐冲击性、耐热性、硬度及抗老化性均优的塑料。
日本业界将它定义为“可以做为构造用及机械零件用的高性能塑料,耐热性在100℃以上,主要运用在工业上”。
热塑性塑料:加热时变软以至流动,冷却变硬,这种过程是可逆的,可以反复进行。
聚乙烯、聚丙烯、聚氯乙烯、聚苯乙烯、聚甲醛、聚砜、聚苯醚,氯化聚醚等都是热塑性塑料。
(热塑性塑料中树脂分子链都是线型或带支链的结构,分子链之间无化学键产生,加热时软化流动、冷却变硬的过程是物理变化;) 热固性塑料:第一次加热时可以软化流动,加热到一定温度,产生化学反应一交链固化而变硬,这种变化是不可逆的,此后,再次加热时,已不能再变软流动了。
正是借助这种特性进行成型加工,利用第一次加热时的塑化流动,在压力下充满型腔,进而固化成为确定形状和尺寸的制品。
这种材料称为热固性塑料。
(热固性塑料的树脂固化前是线型或带支链的,固化后分子链之间形成化学键,成为三维的网状结构,不仅不能再熔触,在溶剂中也不能溶解。
)酚醛、脲醛、三聚氰胺甲醛、不饱和聚酯、有机硅等塑料,都是热固性塑料。
简单组分高分子材料:主要由高聚物组成(含量很高,可达95%以上),加入少量(或不加入)抗氧剂、润滑剂、着色剂等添加剂。
如:PE、PP、PTFE。
复杂组分高分子材料:复杂组分塑料则是由合成树脂与多种起不同作用的配合剂组成,如填充剂、增塑剂、稳定剂等组成。
材料成型工艺基础习题解答

第一章金属材料与热处理1、常用的力学性能有哪些?各性能的常用指标是什么?答:刚度:弹性模量E强度:屈服强度和抗拉强度塑性:断后伸长率和断面收缩率硬度:冲击韧性:疲劳强度:2、4、金属结晶过程中采用哪些措施可以使其晶粒细化?为什么?答:过冷细化:采用提高金属的冷却速度,增大过冷度细化晶粒。
变质处理:在生产中有意向液态金属中加入多种难溶质点(变质剂),促使其非自发形核,以提高形核率,抑制晶核长大速度,从而细化晶粒。
7、9、什么是热处理?钢热处理的目的是什么?答:热处理:将金属材料或合金在固态范围内采用适当的方法进行加热、保温和冷却,以改变其组织,从而获得所需要性能的一种工艺。
热处理的目的:强化金属材料,充分发挥钢材的潜力,提高或改善工件的使用性能和加工工艺性,并且可以提高加工质量、延长工件和刀具使用寿命,节约材料,降低成本。
第二章铸造成型技术2、合金的铸造性能是指哪些性能,铸造性能不良,可能会引起哪些铸造缺陷?答:合金的铸造性能指:合金的充型能力、合金的收缩、合金的吸气性;充型能力差的合金产生浇不到、冷隔、形状不完整等缺陷,使力学性能降低,甚至报废。
合金的收缩合金的吸气性是合金在熔炼和浇注时吸入气体的能力,气体在冷凝的过程中不能逸出,冷凝则在铸件内形成气孔缺陷,气孔的存在破坏了金属的连续性,减少了承载的有效面积,并在气孔附近引起应力集中,降低了铸件的力学性能。
6、什么是铸件的冷裂纹和热裂纹?防止裂纹的主要措施有哪些?答:热裂是在凝固末期,金属处于固相线附近的高温下形成的。
在金属凝固末期,固体的骨架已经形成,但树枝状晶体间仍残留少量液体,如果金属此时收缩,就可能将液膜拉裂,形成裂纹。
冷裂是在较低温度下形成的,此时金属处于弹性状态,当铸造应力超过合金的强度极限时产生冷裂纹。
防止措施:热裂——合理调整合金成分,合理设计铸件结构,采用同时凝固原则并改善型砂的退让性。
冷裂——对钢材材料合理控制含磷量,并在浇注后不要过早落砂。
材料成型基础课后习题答案

材料成型基础课后习题答案材料成型基础课后习题答案材料成型是一门重要的工程学科,涉及到材料的加工、成型和变形等方面。
在学习这门课程时,我们经常会遇到一些习题,通过解答这些习题,可以加深对材料成型基础知识的理解和掌握。
下面是一些常见的材料成型基础课后习题及其答案,供大家参考。
1. 什么是材料成型?答:材料成型是指将原始材料通过一系列的工艺操作,使其发生形状、尺寸和性能的变化,最终得到所需的成品的过程。
2. 材料成型的分类有哪些?答:材料成型可以分为塑性成型和非塑性成型两大类。
塑性成型是指通过材料的塑性变形来实现成型的过程,如锻造、压力成型等;非塑性成型是指通过材料的断裂、破碎等非塑性变形来实现成型的过程,如切削加工、焊接等。
3. 什么是锻造?答:锻造是一种常用的塑性成型方法,通过对金属材料进行加热后的塑性变形,使其在模具的作用下得到所需的形状和尺寸。
锻造可以分为冷锻和热锻两种方式。
4. 锻造的优点有哪些?答:锻造具有以下几个优点:- 可以改善金属材料的内部组织结构,提高其力学性能;- 可以提高材料的密度和均匀性;- 可以减少材料的加工量,提高生产效率;- 可以节约材料和能源。
5. 什么是压力成型?答:压力成型是一种常用的塑性成型方法,通过对材料施加压力,使其发生塑性变形,最终得到所需的形状和尺寸。
压力成型包括挤压、拉伸、冲压等多种方法。
6. 压力成型的应用领域有哪些?答:压力成型广泛应用于汽车制造、航空航天、电子产品等领域。
例如,汽车制造中的车身板件、发动机零件等都是通过压力成型得到的。
7. 什么是切削加工?答:切削加工是一种常用的非塑性成型方法,通过对材料进行切削、剪切等操作,使其发生变形,最终得到所需的形状和尺寸。
切削加工包括车削、铣削、钻削等多种方法。
8. 切削加工的优点有哪些?答:切削加工具有以下几个优点:- 可以实现高精度的加工,得到精确的形状和尺寸;- 可以加工各种材料,包括金属、塑料、陶瓷等;- 可以加工复杂的形状和结构。
- 1、下载文档前请自行甄别文档内容的完整性,平台不提供额外的编辑、内容补充、找答案等附加服务。
- 2、"仅部分预览"的文档,不可在线预览部分如存在完整性等问题,可反馈申请退款(可完整预览的文档不适用该条件!)。
- 3、如文档侵犯您的权益,请联系客服反馈,我们会尽快为您处理(人工客服工作时间:9:00-18:30)。
1. 物料的混合有哪三种基本的运动形式? 聚合物成型时熔融物料的混合以哪一种运动形
式为主? 为什么?
i. 分子扩散
ii. 涡流扩散
iii. 体积扩散
体积扩散为主, 因为他主要是指流体质点、液滴或固体粒子由系统的一个空间位置向另一空间位置的运动, 或两种或多种组分在相互占有的空间内发生运动,以期达到各组分的均布.对流混合通过两种机理发生, 一种体积对流,另一种层流对流混合, 前者通过塞流对物料进行体积重新排列, 而不需要物料连续变形, 这种重复的重新排列可以是无规的, 也可以是有序的. 在固体掺混机中混合式无规的, 而在静态混合机的混合则是有序的. 而层流对流混合是通过层流而使物料变形, 它发生在熔体之间的混合, 在固体粒子之间的混合不会发生层流混合. 层流混合中, 物料要受到剪切、伸长(拉伸)和挤压(捏合).
分子扩散主要在与低分子的混合.在浓度梯度驱使下,各组分自发地由浓度较大的区域迁移到浓度较小的区域从而达到各处组分均化的一种扩散形式。
分子扩散在气体和低粘度液体中占支配地位。
在固体与固体间,分子扩散作用是很小的。
在聚合物加工中,熔体与熔体间分子扩散极慢,无实际意义。
但若参与混合的组分之一是低分子物质,则分子扩散可能是一个重要因素。
涡流扩散主要会造成聚合物的黏度提高导致混合时施予聚合物的剪切力要上升, 容易导致聚合物降解.由系统内产生的紊流而实现的一种扩散形式。
在聚合物加工中粘度高,而且要实现紊流,熔体的速度必须很高,势必使熔体发生破裂,也会造成聚合物的降解,故很少发生涡旋扩散。
2. 什么是”非分散混合”,什么是”分散混合”,两者各主要通过何种物料运动和混合操
作来实现?
Page 154
非分散均匀的定义在混合中仅增加粒子在混合物中空间分布均匀性而不减小尺寸的过程称为非分散均匀或简单混合。
主要通过对流方式来实现的, 可以通过塞流和不需要物料连续变形便发生简单的体积重排和置换来达到混合。
分散混合的定义: 将呈现出屈服点的物料混合在一起时,要将它们分散开来,使结块和液滴破裂。
这种混合为分散混合。
分散混合的目的是把少组分的固体颗粒和液相滴分散开来,成为最终粒子或允许的更小颗粒或滴,并均匀地分布到多组分中。
涉及少组分在变形粘性流体中的破裂问题。
这是靠强迫混
合物通过窄间隙而形成的高剪切区来完成的。
对固体结块来说,当剪切对其形成的粘性拖曳在结块内产生的应力超过某个临界值时,结块就破裂。
图:分散混合时,发生的主要机械现象和流变现象示意图
I -使聚合物和添加剂粉碎
n -使粒状和粉粒状固体添加剂渗入聚合物中
川-分散
IV -分布均化
1-聚合物
2, 3-任何粒状和粉状固体添加剂
3. 为什么评定固体物料的混合状态时不仅要比较取样中各组分的比率与总体比率的差异
大小而且还要考察混合料的分散程度?
Page 156T58
混合状态的判定,有直接描述和间接描述两种方法。
直接描述法:该法是直接对混合物取样,对其混合状态进行检验,观察混合物形态结构、各组分微粒的大小及分布情形。
常用的检测分析方法可以是视觉观察法、聚团计算
法、光学显微镜法和电子显微镜法以及光电法。
1. 均匀程度指混得匀不匀,浓度变化大小如何,即分散相浓度分布是否
均匀。
2. 分散程度是指被分散物质的破碎程度如何。
破碎程度大,粒径
小,其分散度就高;反之,粒径大,破碎度小,则分散得不好。
间接描述法:是指不检查混合物各组分的混合状态,而是检测与混合物的混合状态密切相关的制品或试样的物理性能、力学性能和化学性能等,间接地判断多组分体系的混合状态。
4. 温度对生胶塑炼有何影响?为什么橡胶在115C时塑炼效果最差?
Page 167
随着温度升高,生胶黏度下降,塑炼时受到的作用力较小,因而塑炼效果降
低•
在高温塑炼时(110度以上),虽然受到机械作用力下降,但由于热和氧的自动催化氧化破坏作用随着温度升高而集剧增大,大大加快了橡胶大分子的氧化降解速度,塑炼效果也迅速增大.
6•何谓橡胶的混炼?用开炼机和密炼机分别进行混炼时应控制的工艺条件有哪些?有何影响?
将塑炼后的生胶和配合剂混合均匀的过程。
Page171~173
在橡胶工业中,最常用的塑炼方法有机械塑炼法和化学塑炼法。
机械塑炼法
所用的主要设备是开放式炼胶机、密闭式炼胶机和螺杆塑炼机。
化学塑炼法是在机械塑炼过程中加入化学药品来提高塑炼效果的方法。
开炼机塑炼时温度一般在
80C以下,属于低温机械混炼方法。
密炼机和螺杆混炼机的排胶温度在120C以上,甚至高达160-180C,属于高温机械混炼。
几种胶的塑炼特性:
天然橡胶用开炼机塑炼时,辊筒温度为30-40 C,时间约为15-20mi n;采用密炼机塑炼当温度达到120C以上时,时间约为3-5min。
丁苯橡胶的门尼粘度多在35-60之间,因此,丁苯橡胶也可不用塑炼,但是经过塑炼后可以提高配合机的分散性
顺丁橡胶具有冷流性,缺乏塑炼效果。
顺丁胶的门尼粘度较低,可不用塑炼。
氯丁橡胶得塑性大,塑炼前可薄通3-5次,薄通温度在30-40°C
乙丙橡胶的分子主链是饱和结构,塑炼难以引起分子的裂解,因此要选择门尼粘度低的品种而不用塑炼。
丁腈橡胶可塑度小,韧性大,塑炼时生热大。
开炼时要采用低温40C以下、小辊距、低容量以及分段塑炼,这样可以收到较好的效果。
7•何谓胶料混炼过程中产生的结合橡胶?
生胶在塑炼时橡胶的大分子断链生成自由基,这种情况在混炼时同样会发生。
在混炼过程中,橡胶分子断链生成大分子自由基可以与炭黑粒子表面的活性部位结合,也可以与炭黑聚集体在混炼时被搓开所产生的具有较高活性的新生面结合,或者已与炭黑结合的橡胶又通过缠结或交联结合更多的橡胶,形成一种不溶于橡胶溶剂的的产物(结合橡胶)。
11.塑料的塑化与橡胶的塑炼两者的目的和原理有何异同?
塑料的塑化:是使物料在温度和剪切力的作用下熔融,获得剪切混合的作用, 驱出其中的水分和挥发物,使各组分的分散更趋均匀,得到具有一定可塑性的均匀物料,是分散混合过程。
橡胶的塑炼:强迫生胶反复通过两个转速不同的滚筒之间的间隙,使之在强剪切力作用下长分子链被切断,相对分子量减小,降低生胶的弹性,从而流动性增加(即可塑性增加)的工艺过程,使橡胶与配合剂在混炼过程中易于混合分散均匀,此外使得制得的胶料质量也均匀一致。