转炉双渣法炼钢少渣冶炼51页PPT
合集下载
转炉双渣法炼钢少渣冶炼推荐PPT资料
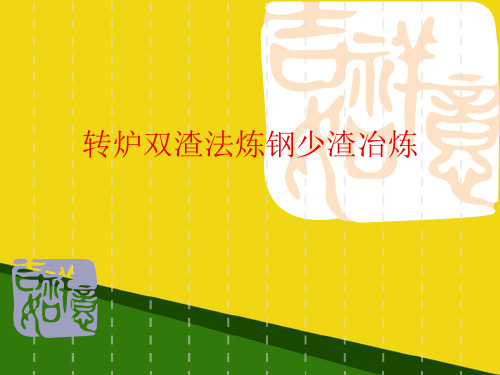
1、转炉双渣法少渣冶炼现状
▪ 北科大何肖飞等对少渣炼钢的前期渣进行 了研究,发现当前期渣碱度在1.2~1.8范围 内时,其半球点温度基本上在1380度以下, 渣中游离CaO含量在0.7%左右。
▪ 迁钢210t转炉的前期渣倒渣量可达8t,首秦 100t转炉的前期渣倒渣量可达可达5t。
1、转炉双渣法少渣冶炼现状
1、转炉双渣法少渣冶炼现状
▪ 国内已经发表的工业试验和生产的报告有20余篇, 基本反映了该炼钢方法的技术操作特点。从已发 表的报道来看,值得注意的有以下2点。
▪ (1)转炉容量:80t~300t,表明少渣冶炼生产
的规模大 ▪ (2)讨论内容:操作技术;经济效益;前期渣
特点,形成了完整的工艺方法
1、转炉双渣法少渣冶炼现状
采用少渣冶炼工艺,由于所留炉渣中已含1.
炼过程喷溅,改善脱磷效果,曾采用过出钢后留 1、转炉双渣法少渣冶炼现状
1)氧枪枪位较常规工艺吹炼前期枪位降低100~200mm,供氧强度控制在3. 渣量减少必然带来钢铁料消耗减少,日照钢铁的消耗从1080kg/t钢降到了1053kg/t钢,减幅达27kg/t钢。
▪ 已经发表文章的单位(不完全统计)及生产转炉 的容量:
▪ 首钢京唐300t转炉 ;鞍钢260吨转炉 ;首钢迁安 210t转炉;沙钢180t转炉;酒钢120t转炉;日照 120t转炉;马钢120t转炉 ;莱钢120t转炉;首钢首 秦100t转炉;湘钢80t转炉;首钢长治80t转炉
▪ 由此可见,少渣冶炼在全国工业生产中已经推广 开来,各种规模的转炉都适应。
1、转炉双渣法少渣冶炼现状
▪ 主要相关经济技术指标: ▪ 有些转炉已经达到了 MUCR工艺操作的水平,如
首钢迁钢公司210t转炉和首秦公司100t转炉取得了 炼钢石灰消耗减少47%以上,轻烧白云石消耗减 少55%以上,渣量降低30%以上的效果。 ▪ 渣量减少必然带来钢铁料消耗减少,日照钢铁的 消耗从1080kg/t钢降到了1053kg/t钢,减幅达27kg/t 钢。
某炼钢分厂转炉双渣工艺培训

05
转炉双渣工艺经济效益分 析
成本分析
原材料成本
转炉双渣工艺需要使用更多的原材料 ,如铁矿石、废钢等,增加了生产成 本。
能耗成本
人工成本
转炉双渣工艺需要更多的操作人员和 技术支持,增加了人工成本。
转炉双渣工艺需要消耗更多的能源, 如电力、燃气等,增加了能源成本。
效益分析
提高产量
转炉双渣工艺能够提高钢的产量 和质量,从而提高企业的生产效
泛应用,降低能耗和污染物排放。
新型炉衬材料
03
采用新型耐火材料和复合炉衬技术,提高炉龄和减少维护成本
。
市场发展前景
全球市场需求持续增长
随着全球经济的发展和钢铁行业的复苏,转炉双渣工艺市场将保 持稳定增长。
市场竞争格局变化
新兴市场和技术创新将改变转炉双渣工艺市场竞争格局,为优势企 业提供更多机会。
绿色环保标准推动市场发展
03
转炉双渣工艺安全注意事 项
安全防护措施
01
02
03
穿戴防护服
所有操作人员必须穿戴符 合要求的防护服,包括但 不限于安全帽、防护眼镜 、口罩等。
定期检查设备
对所有设备进行定期检查 ,确保设备处于良好状态 ,无安全隐患。
设置安全警示标识
在危险区域和设备上设置 明显的安全警示标识,提 醒操作人员注意安全。
长期效益
虽然转炉双渣工艺的投资回报周期较长,但长期来看,该工艺能够 为企业带来稳定的收益和竞争优势。
06
转炉双渣工艺未来发展展 望
技术发展趋势
自动化与智能化
01
随着工业4.0和智能制造的推进,转炉双渣工艺将实现自动化和
智能化,提高生产效率和产品质量。
钢铁冶炼过程PPT课件

—氮气在钢铁厂的应用主要是用作保护气,如轧钢、镀锌、镀铬、热处理(尤为薄钢片)连续铸 造等都要用氮气作保护气,而且氮气纯度要求99.99%以上。
—氩气在炼钢过程的作用:如向熔融的钢水中吹入氩气,使成份均匀,钢液净化,并可除掉溶解 在钢水中的氢、氧、氮等杂质,提高钢坯质量。吹氩还可以取消还原期,缩短冶炼时间,提高产 量,节约电能等。氩气吹炼和保护是提高钢材质量的重要途径。
自学互学共同学习一起成才生铁和钢铁的合金生铁含碳的质量分数2430032杂质硅锰较多硫磷较多硅锰适量硫磷较多机械加工可铸不可锻可铸可锻可压延机械性能硬而韧有弹性生铁和钢的比较球墨生铁合金生铁碳素钢低碳钢中碳钢高碳钢炼钢生铁白口铁铸造生铁灰口铁合金钢炼铁
Objectives:
1。重温炼铁和炼钢的基础知识 2。了解炼铁和炼钢的流程和设备 3。通过学习加深对我们用户的了解 4。自学,互学,共同学习,一起成才
原料 设备
铁矿石、石灰石、焦碳、空气 炼铁高炉
生铁(废钢)、纯氧、氧化钙 转炉、平炉、电炉
13
第13页/共29页
ห้องสมุดไป่ตู้
炼钢
转炉结构图
14
第14页/共29页
转炉炼钢:
15
第15页/共29页
电炉炼钢:
16
第16页/共29页
平炉炼钢示意图:
17
第17页/共29页
18
第18页/共29页
19
第19页/共29页
硫、磷杂质与生石灰作用形成炉渣被除去。
④脱氧: Si+2FeO=SiO2+2Fe (脱氧剂:硅铁,锰铁) 调节合金元素
12
第12页/共29页
炼铁和炼钢
炼铁和炼钢的比较
炼铁
炼钢
—氩气在炼钢过程的作用:如向熔融的钢水中吹入氩气,使成份均匀,钢液净化,并可除掉溶解 在钢水中的氢、氧、氮等杂质,提高钢坯质量。吹氩还可以取消还原期,缩短冶炼时间,提高产 量,节约电能等。氩气吹炼和保护是提高钢材质量的重要途径。
自学互学共同学习一起成才生铁和钢铁的合金生铁含碳的质量分数2430032杂质硅锰较多硫磷较多硅锰适量硫磷较多机械加工可铸不可锻可铸可锻可压延机械性能硬而韧有弹性生铁和钢的比较球墨生铁合金生铁碳素钢低碳钢中碳钢高碳钢炼钢生铁白口铁铸造生铁灰口铁合金钢炼铁
Objectives:
1。重温炼铁和炼钢的基础知识 2。了解炼铁和炼钢的流程和设备 3。通过学习加深对我们用户的了解 4。自学,互学,共同学习,一起成才
原料 设备
铁矿石、石灰石、焦碳、空气 炼铁高炉
生铁(废钢)、纯氧、氧化钙 转炉、平炉、电炉
13
第13页/共29页
ห้องสมุดไป่ตู้
炼钢
转炉结构图
14
第14页/共29页
转炉炼钢:
15
第15页/共29页
电炉炼钢:
16
第16页/共29页
平炉炼钢示意图:
17
第17页/共29页
18
第18页/共29页
19
第19页/共29页
硫、磷杂质与生石灰作用形成炉渣被除去。
④脱氧: Si+2FeO=SiO2+2Fe (脱氧剂:硅铁,锰铁) 调节合金元素
12
第12页/共29页
炼铁和炼钢
炼铁和炼钢的比较
炼铁
炼钢
转炉炼钢造渣制度教材(PPT 51张)

5
转炉炼钢造渣制度
吹炼中期: 由于炉温升高石灰进一步熔化,同时因为Vc加快而导 致渣中∑(FeO)逐渐降低,使石灰熔化速度有所减缓。
随着C-O反应进行,炉渣泡沫化程度迅速提高。
由于C-O反应大量消耗渣中∑(FeO),以及有时得不到 超过渣系液相线的正常过热温度,使化渣条件恶化, 引起炉渣异相化,并出现“返干”。
15
转炉炼钢造渣制度
作用: 第一,它能显著降低炉渣粘度,从而加速石灰熔化过 程中传质; 第二,它能改善炉渣对石灰的润湿和炉渣向石灰孔隙 中的渗透; 最根本的原因是:它的离子半径不大 ( 而且与 CaO同属立方晶系,这些都有利于向CaO晶格 中迁移并生成低熔点物质; 因此,大大减少石灰块表面的2CaO SiO2生成,降低其 熔点,使2CaO SiO2变疏松。
20℃
新流程
多功能RH
[P]≤0.01% [S]≤0.005% T=1350℃ 0.04% [P]=0.11% [C]>3.5% [S]≤0.005% T=1300℃
0.065% 0.004% [P]≤0.005% T=1650℃ 0.001% [P]≤0.003%
34
2.转炉炼钢的脱硫 1)硫在钢中的存在形式及其对钢性能的影响 从Fe-S二元系相图可知,硫能溶解于液态铁中形成无 限溶液。 钢铁中的含量约为:0.001-0.1%。 硫在液态纯铁中,究竟以何种状态存在? 到目前为止还不能完全确定。 多数观点认为它以[FeS]的形式存在,少数[MnS]。 硫在铁中的溶解热较高,扩散系数较小。
24
离子理论的脱磷反应式为: [P] + (O2-) + [O]= (PO43-) lgK=40067/T-15.06 其中: K=a(4 CaO.P5O2)/[%P]2a5(Feo) a4(CaO) 脱磷率: LP = (% P2O5)/ [%P]2 = K a5(Feo) a4(CaO)
(优)转炉炼钢主要过程及特点PPT资料

点的氧气压力 (0.8~1.2MPa); 枪位:喷头至静止金属熔池液 面的距离(化渣枪位、基本 吹炼枪位、拉碳枪位)
供气制度(底部供气)
底吹类型 非氧化性气体:Ar、N2 氧化性气体:O2、CO2、
为6~8%,采用溅渣护炉则8~10%.
❖ 4.造渣方法:单渣法、双渣法、双渣 留渣法.渣料分批加入,开吹时加入 1/2~1/3,其余分批加入.
❖ 顶部供气
供气制度
❖ 底部供气
供气制度(顶部供气)
供氧操作控制以下参数: 氧气流量:单位时间向熔池吹
入氧气体积; 供氧强度:单位时间向熔池吨
钢提供氧气的体积; 氧气工作压力:设定压力测定
持每炉的金属装入量不变; 块、重油)。
主要有造渣料〔石灰、白云石),熔剂〔萤石、氧化铁皮),冷却剂〔铁矿石、石灰石、废钢),增碳剂和燃料〔焦炭、石墨籽、煤
块转、炉❖重 一油炉)钢2。的.定基本深冶炼装过程入:随容积的扩大 供氧强度:而单位增时间加向熔装池吨入钢提量供氧,气保的体持积; 熔池的 深度不变; 2:炉渣氧化性:用∑(%FeO)表示,高利于成渣,脱P,但降低金属非金属料和气 体。金属料包括铁水、废钢、铁合金,非金属料包 括造渣料、熔剂、冷却剂,气体包括氧气、氮气、 氩气、二氧化碳等。非金属料是在转炉炼钢过程 中 为了去除磷、硫等杂质,控制好过程温度而加入的 材料。主要有造渣料〔石灰、白云石),熔剂〔萤 石、氧化铁皮),冷却剂〔铁矿石、石灰石、废 钢),增碳剂和燃料〔焦炭、石墨籽、煤块、重 油)。
转炉一炉钢的基本冶炼过程
(1〕上炉出钢、倒渣,检查炉衬和倾动设备等并进行必要的修补和修理; (2〕倾炉,加废钢、兑铁水,摇正炉体〔至垂直位置); (3〕降枪开吹,同时加入第一批渣料〔起初炉内噪声较大,从炉口冒出赤
供气制度(底部供气)
底吹类型 非氧化性气体:Ar、N2 氧化性气体:O2、CO2、
为6~8%,采用溅渣护炉则8~10%.
❖ 4.造渣方法:单渣法、双渣法、双渣 留渣法.渣料分批加入,开吹时加入 1/2~1/3,其余分批加入.
❖ 顶部供气
供气制度
❖ 底部供气
供气制度(顶部供气)
供氧操作控制以下参数: 氧气流量:单位时间向熔池吹
入氧气体积; 供氧强度:单位时间向熔池吨
钢提供氧气的体积; 氧气工作压力:设定压力测定
持每炉的金属装入量不变; 块、重油)。
主要有造渣料〔石灰、白云石),熔剂〔萤石、氧化铁皮),冷却剂〔铁矿石、石灰石、废钢),增碳剂和燃料〔焦炭、石墨籽、煤
块转、炉❖重 一油炉)钢2。的.定基本深冶炼装过程入:随容积的扩大 供氧强度:而单位增时间加向熔装池吨入钢提量供氧,气保的体持积; 熔池的 深度不变; 2:炉渣氧化性:用∑(%FeO)表示,高利于成渣,脱P,但降低金属非金属料和气 体。金属料包括铁水、废钢、铁合金,非金属料包 括造渣料、熔剂、冷却剂,气体包括氧气、氮气、 氩气、二氧化碳等。非金属料是在转炉炼钢过程 中 为了去除磷、硫等杂质,控制好过程温度而加入的 材料。主要有造渣料〔石灰、白云石),熔剂〔萤 石、氧化铁皮),冷却剂〔铁矿石、石灰石、废 钢),增碳剂和燃料〔焦炭、石墨籽、煤块、重 油)。
转炉一炉钢的基本冶炼过程
(1〕上炉出钢、倒渣,检查炉衬和倾动设备等并进行必要的修补和修理; (2〕倾炉,加废钢、兑铁水,摇正炉体〔至垂直位置); (3〕降枪开吹,同时加入第一批渣料〔起初炉内噪声较大,从炉口冒出赤
转炉双渣法炼钢少渣冶炼

1、转炉双渣法少渣冶炼现状
对于转炉吹炼前期渣的操作控制也进行了研究,
北京科技大学的王新华等在首钢迁安210t转炉上 试验,脱磷阶段采用低碱度(R=1.3~1.5)和低
MgO质量分数(≤7.5%)的渣系,能够形成流动
性良好和适度泡沫化的炉渣,解决了脱磷阶段结
束难以快速足量倒渣和渣中金属铁含量高这两大
3、少渣冶炼的关键技术
图7和图8分别为氧枪枪位和炉渣FeO含量
对脱磷阶段结束[P]含量的影响,可以看到, 采用较低枪位和高强度供氧,由于熔池搅 拌显著加强,尽管炉渣FeO含量降低至 9.5%附近,脱磷效率非但没有降低,反而 有较大幅度的提高。
3、少渣冶炼的关键技术
采用上述高效脱磷工艺,在铁水磷含量为
溅,引发重大安全事故。迁钢公司曾采用加入多
量石灰、白云石或废钢直接冷却对液态炉渣进行 固化的方法,但发现存在以下问题: ①如石灰、白云石加入量多,造成脱磷阶段炉渣 碱度和MgO含量过高,导致倒渣困难;
3、少渣冶炼的关键技术
②如采用废钢对液态渣进行冷却固化,由于废钢
尺寸不均衡,常发生炉内废钢“搭棚”情况,炉 底液态渣不能被充分固化,存在安全隐患。通过
稳定运行。
3、少渣冶炼的关键技术
为了使炉渣具有良好的流动性,还须对MgO含量
进行严格控制。后面的图为210t转炉脱磷阶段结
束时倒渣量与渣中MgO含量的关系,当将MgO含
量控制在7.5%以下时,倒渣量可在8t以上,能够
满足少渣冶炼工艺稳定运行的要求,为此规定对 脱磷阶段炉渣MgO含量按低于7.5%控制。这一 MgO含量控制目标低于常规工艺初期渣的MgO含 量控制目标值,采用后并未发现对炉龄有不利影
③传统工艺出钢后会有钢水留在炉内,一部分会
电炉炼钢操作方法及冶炼工艺-PPT文档资料-PPT文档资料
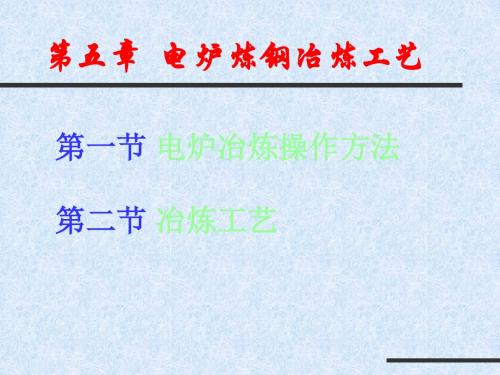
熔末升温 期
电弧、 大电流
水冷+ 泡沫渣
典型的供电曲线
2)及时吹氧与元素氧化
熔化期吹氧助熔,初期以切割为主,当炉料
基本熔化形成熔池时,则以向钢液中吹氧为主。 吹氧是利用元素氧化热加速炉料熔化。当固体 料发红(~900℃)开始吹氧最为合适,吹氧过 早浪费氧气,过迟延长熔化时间。 一般情况下,熔化期钢中的Si、Al、Ti、V等几 乎全部氧化,Mn、P氧化40%~50%,这与渣
脱磷反应与脱磷条件:
脱磷反应:
2[P]+5(FeO)+4(CaO)=(4CaO· P2O5)+5 [Fe], △H<0 分析:反应是在渣-钢界面上进行,是放热反应。
1)炉料熔化过程及供电
装料完毕即可通电熔化。炉料熔化过程图, 基本可分为四个阶段(期),即点弧、穿井、主 熔化及熔末升温。
•点(起)弧期
从送电起弧至电极端部下降到深度为d电极为 点弧期。 此期电流不稳定,电弧在炉顶附近燃烧辐射, 二次电压越高,电弧越长,对炉顶辐射越厉害, 并且热量损失也越多。 为保护炉顶,在炉上部布一些轻薄料,以便让 电极快速进入料中,减少电弧对炉顶的辐射。 供电上采用较低电压、较低电流。
一、补炉 1)影响炉衬寿命的“三要素”
炉衬的种类、性质和质量; 高温电弧辐射和熔渣的化学浸蚀; 吹氧操作与渣、钢等机械冲刷以及装料的冲击。
2)补炉部位
炉衬各部位的工作条件不同,损坏情况也不一 样。炉衬损坏的主要部位如下: 炉壁渣线 受到高温电弧的辐射,渣、钢的化学 侵蚀与机械冲刷,以及吹氧操作等损坏严重; 渣线热点区 尤其2#热点区还受到电弧功率大、 偏弧等影响侵蚀严重,该点的损坏程度常常成为换 炉的依据; 出钢口附近 因受渣钢的冲刷也极易减薄; 炉门两侧 常受急冷急热的作用、流渣的冲刷及 操作与工具的碰撞等损坏也比较严重。
8-转炉“留渣-双渣”少渣炼钢工艺实践
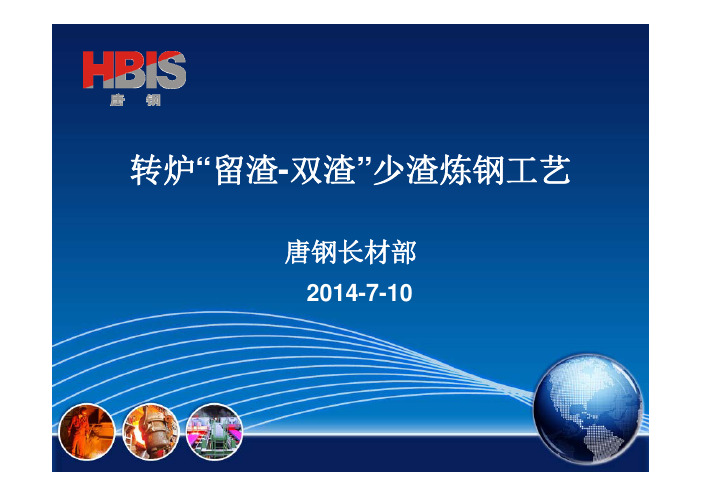
“留渣-双渣”工艺示意图
3.转炉脱磷影响因素
3.脱磷的基本原理
2[P]+5(FeO)+4(CaO)=4CaO·P2O5+5[Fe]
a 4CaO P2 O 5 a a
2 p 5 F eO
Kp
a
4 C aO
% 4CaO P2 O 5 4CaO P O 4 5 4 % P 2 f P2 % F e O 5 F e O % CaO C aO
演变:首钢公司从2011年开始,在首钢首秦和迁钢分别连续试验单
转炉“留渣-双渣”操作,取得较好的效果,目前首钢集团首钢长治, 首钢水钢均推广应用“留渣-双渣”少渣炼钢操作工艺,工艺相对成熟 。
1. 大幅度减少炼钢石灰、白云石等渣料消耗和炼钢渣量; 2. 可以利用出钢后炉渣的物理热,预热废钢; 3. 炼钢终渣含Tfe:15~25%,渣量减少可以降低钢铁料消耗; 4. 双渣倒渣的炉渣主要为脱磷阶段低碱度渣,自由CaO含量低, 可以简化炉渣处理; 5. 常规转炉出钢后留在炉内钢水随炉渣倒出,采用“留渣-少渣”工 艺终点少倒渣、出钢后不倒渣,可以提高钢水收得率。
FeO%
H11Mn2SiA
3A14306-1 3A14306-2 3B14615-1 3B14615-2 3C14935-1 3C14935-2 3A14301-1 3A14301-2 3B14603-1 3B14603-2 3B14612-1 3B14612-1
1 冶炼周期影响
类别 加料 脱磷期 双渣 脱碳期 终点 加废钢 兑铁时间 前期吹炼时间 氮气刹渣 倒渣时间 中后期吹炼 拉碳、补吹时间 等待终点成分 出钢时间 溅渣时间 总冶炼周期 留渣-双渣 1.7 2.4 4.5 2.1 3 8.8 2 1 2.5 2 30 单渣法 1.7 2.2 4.5 / / 8.7 2 1 2.5 2.5 25.1
炼钢工艺流程及典型案例介绍PPT课件

氧装置都带两只氧枪,一只工作,一只
备用。
枪身由三层同心圆钢管组成,枪尾 与
进水管、出水管和进氧管相连。
喷头 :是将压力能转换成动能的能量
器,
氧枪:氧气转炉炼钢中的主要工艺设备之一
14
第14页/共63页
2.4氧气转炉的辅助设备
•
炉料喷补设备:喷补方法分为湿法
和干法两种。喷补机的驱动电机经减
速器带动搅拌器旋转,将料斗内的补
2.7氧气转炉的主要原料
• 转炉对铁水进行冶炼操作
•
转炉炼钢主要是以液态生铁为原料的炼钢方法。其主要特
点是:靠转炉内液态生铁的物理热和生铁内各组分(如碳、锰、
硅、磷等)与送入炉内的氧进行化学反应所产生的热量,使金
属达到出钢要求的成分和温度。
转炉冶炼的炉料主要为铁水、造渣料(如石灰、石英、 萤石等)、铁合金(如硅铁、锰铁等)、脱氧剂(如硅化铁等) 以及增碳剂(如碳粉等),为调整温度,可加入废钢及少量的 冷生铁块和矿石等。
15
第15页/共63页
2.4氧气转炉的辅助设备
•铁(钢)包车的作用是承载钢包、接受钢水并运送钢包过跨 铁水包 鱼 雷 铁 包 车
炉渣盆
16
第16页/共63页
2.5氧气转炉的气体
• 一、氧气 • 氧气是氧气转炉炼钢的主要氧化剂,要求含氧量达到99.5%
以上,并脱除水分与皂液。 • 工业用氧是通过制氧机把空气中的氧气分离、提纯来实现的。
3
第3页/共63页
第一章 炼钢的主要任务:
脱碳
措施
炼钢过程使用氧化剂,如吹入氧 气,加入铁矿石等
主 要
脱磷、脱硫
措施 使用造渣剂造好渣
任 务
脱氧合金化
转炉生产工艺介绍PPT课件

块度要求:<300×800×1800mm,单重<1.0吨
薄板、钢丝、盘丝、 机械打包 绳及民用薄废钢
尺寸:<800×500×400mm,比重>2.5吨/米3
3
生产工艺流程介绍—装入制度
300吨转炉对高炉铁水的要求
1、高炉铁水受入目标成份及入炉硫要求:单位:%
C
Si
4.00~4.50 0.25~0.80
出钢后倒渣或溅渣护炉
1、出钢结束后,若不需溅渣护炉炉座,摇炉工根据炉况,决定是 否倒净或挂渣护炉。 2、对于需溅渣护炉炉座,需注意以下要点: (1)钢水未出完,又无其它措施处理,禁止溅渣; (2)炉渣中MgO含量控制在8~10%; (3)溅渣炉座如有底吹,底吹流量要控制在800~1000Nm3/h; (4)溅渣时间控制在2~4分钟内,最长不超过5分钟。
6
生产工艺流程介绍—供氧制度
2、氧枪间隙 (1)若氧枪间隙设置不当,会造成如下图所示情况:
因各炉子的条件而不同,
ห้องสมุดไป่ตู้
废钢未熔 (特别是冶炼钢种能力操作稳定性)
软吹 渣过氧化
喷溅
能 力
O2流速 L/LO up(max0.8)
适当地范围
的
硬吹
炉底熔损 喷孔破损 喷溅激烈
提
高
炉龄
确保对钢水的搅拌
(2)L、L0基本计算式 <O2流股穿透深度(L)>﹡考虑超音速的实验式 L=LHOexp(-0.78h/Lho) Lho=63.0(FO2/nd/k)2/3
9
生产工艺流程介绍—温度制度
一、 目标停吹温度的制定。 1、目标停吹温度计算方式
目标停吹温度=目标钢包温度+钢包温度修正值+温度下降量 2、目标钢包温度、目标停吹温度决定方法
转炉炼钢主要工艺介绍(PPT 68页)

炼钢用原材料一般分为主原料、辅料 和各种铁合金。
6
1.金属料
• 1)铁水:占钢铁料的(75~100%) 主要要求 成分:[Si]、[Mn]、[P]、[S] 温度: T
7
铁水成分及温度影响
• Si影响 • 转炉炼钢重要发热元素,[Si]↑0.1%,废钢比↑1.0%。 • 铁水合适的[Si]0.3-0.5%。 • [Si] >0.6%,渣量增加并引起喷溅;渣中(SiO2)↑。 • 石灰加入量=(2.14×R× [Si] )×1000 /(石灰CaO
• 热来源于:
• 转炉炼钢不需要外来热源;
铁水物理热及元素氧化化学热。 铁水及废钢的合理配比须根据炉子的热平衡计算确定。 • 硅的作用 优点:因发热量大,增大废钢加入量,一般铁水中Si增 加0.1%,废钢比增大1%。 缺点:增大渣量,侵蚀炉衬一般控制在0.3-0.5%。
29
转炉兑铁水操作现场图示
一范围 0.75-1.1Mpa。 • 枪位,由冲击深度决定,1/3-1/2。 • 供氧强度(Nm3/t.min) 决定冶炼时间,但太大,喷溅可
能性增大,一般3.0-4.0。
34
氧枪
氧枪是转炉供氧的 主要设备,它是由 喷头、枪身和尾部 结构组成。 喷头是用导热性良 好的紫铜经锻造和 切割加工而成,也 有用压力浇铸而成 的。喷头的形状有 拉瓦尔型、直筒型 和螺旋型等。目前 应用最多的是多孔 的拉瓦尔型喷头。
30
2.2造渣制度
• 造渣制度就是确定合适的造渣方法、渣料加入量和时 间,以及如何快速成渣。
• 炼钢就是炼渣。通过造渣,快速脱P、脱S,减少喷溅, 保护炉衬,降低终点氧含量。
• 石灰的熔解: 加开石始灰后吹,氧由时2渣Fe中O·主Si要O2是→CSaiOO·2F,eOM·nSOi,O2F→eO2,C是aO酸·S性iO渣2 ,, 2CaO·SiO2难熔渣,石灰溶解有些停滞,出现返干。
6
1.金属料
• 1)铁水:占钢铁料的(75~100%) 主要要求 成分:[Si]、[Mn]、[P]、[S] 温度: T
7
铁水成分及温度影响
• Si影响 • 转炉炼钢重要发热元素,[Si]↑0.1%,废钢比↑1.0%。 • 铁水合适的[Si]0.3-0.5%。 • [Si] >0.6%,渣量增加并引起喷溅;渣中(SiO2)↑。 • 石灰加入量=(2.14×R× [Si] )×1000 /(石灰CaO
• 热来源于:
• 转炉炼钢不需要外来热源;
铁水物理热及元素氧化化学热。 铁水及废钢的合理配比须根据炉子的热平衡计算确定。 • 硅的作用 优点:因发热量大,增大废钢加入量,一般铁水中Si增 加0.1%,废钢比增大1%。 缺点:增大渣量,侵蚀炉衬一般控制在0.3-0.5%。
29
转炉兑铁水操作现场图示
一范围 0.75-1.1Mpa。 • 枪位,由冲击深度决定,1/3-1/2。 • 供氧强度(Nm3/t.min) 决定冶炼时间,但太大,喷溅可
能性增大,一般3.0-4.0。
34
氧枪
氧枪是转炉供氧的 主要设备,它是由 喷头、枪身和尾部 结构组成。 喷头是用导热性良 好的紫铜经锻造和 切割加工而成,也 有用压力浇铸而成 的。喷头的形状有 拉瓦尔型、直筒型 和螺旋型等。目前 应用最多的是多孔 的拉瓦尔型喷头。
30
2.2造渣制度
• 造渣制度就是确定合适的造渣方法、渣料加入量和时 间,以及如何快速成渣。
• 炼钢就是炼渣。通过造渣,快速脱P、脱S,减少喷溅, 保护炉衬,降低终点氧含量。
• 石灰的熔解: 加开石始灰后吹,氧由时2渣Fe中O·主Si要O2是→CSaiOO·2F,eOM·nSOi,O2F→eO2,C是aO酸·S性iO渣2 ,, 2CaO·SiO2难熔渣,石灰溶解有些停滞,出现返干。