石油、化工企业火灾爆炸事故案例及其引发原因
石油石化行业安全事故案例分析

投运第 6 套脱水脱烃装置。上午 10∶50 分左右, 该装置的系统压力( 介质为氮 气 ) 为 0.18 兆 帕 , 值 班 人 员 按 投 运 方 案 开始进气建压, 并用肥皂水对各密封 点 进 行 检 漏 , 11: 30 分 , 低 温 分 离 器 升 压 至 6.24 兆 帕 , 打 开 第 6 套 装 置 干 气 外 输 阀 , 此 时 J- T 阀 前 端 压 力 9.4 兆 帕 , 低 温 分 离 器 压 力 为 6.2 兆 帕 , 系 统 压 力 正 常 。12: 42 分 , 停 运 第 4 套 脱 水 脱烃装置, 第 6 套脱水脱烃装置低温 分 离 器 温 度 逐 渐 降 至 - 21℃( 低 温 分 离 器 设 计 最 低 工 作 温 度 为 - 41℃) , 13: 00 再次对各密封点进行肥皂水检漏, 没 有 发 现 漏 点 , 装 置 运 行 正 常 。15: 10 分 左右, 处理厂中心控制室值班人员听 到强烈的爆炸声, 随后看到装置区第 6 套装置附近的火光, 操作主岗立即启 动全厂紧急停车程序, 实施火灾爆炸 应急预案。正在生产的 4 口气井全部 自动关井, 切断进站气源。同时, 立即 启动消防喷淋系统, 对凝析油储罐进 行喷淋降温。由于自动控制电缆在爆 炸时严重损坏, 出站外输切断阀已不 能实现自动关断, 当时出站外输切断 阀处于着火的下风口, 抢险人员曾几 次试图靠近出站外输切断阀实行手动 关闭, 但终因火势太大, 热辐射温度过 高, 人员无法靠近。只能开车至输气干 线 1 号 阀 室 ( 距 该 处 理 厂 大 约 14 公 里 左 右 ) 进 行 人 工 切 断 输 气 干 线 气 源 , 16 时左右关闭了输气干线 1 号阀室切断 阀 , 16: 30 分 左 右 装 置 区 火 势 逐 步 减 弱 , 17 时 左 右 抢 险 人 员 身 穿 防 火 服 进 入出站外输切断阀处手动关断切断 阀, 并打开现场的消防干粉罐, 对管廊 架上着火的导热油管线等着火处进行 扑 救 , 17: 50 分 左 右 装 置 区 火 焰 完 全 被 扑灭。
安全管理中的安全事故案例分析
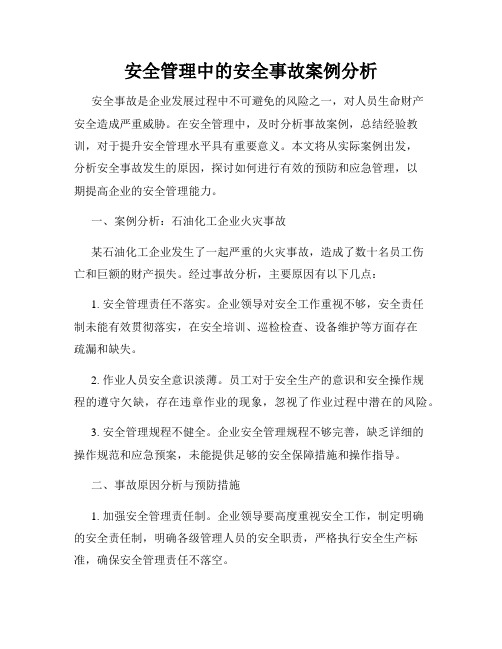
安全管理中的安全事故案例分析安全事故是企业发展过程中不可避免的风险之一,对人员生命财产安全造成严重威胁。
在安全管理中,及时分析事故案例,总结经验教训,对于提升安全管理水平具有重要意义。
本文将从实际案例出发,分析安全事故发生的原因,探讨如何进行有效的预防和应急管理,以期提高企业的安全管理能力。
一、案例分析:石油化工企业火灾事故某石油化工企业发生了一起严重的火灾事故,造成了数十名员工伤亡和巨额的财产损失。
经过事故分析,主要原因有以下几点:1. 安全管理责任不落实。
企业领导对安全工作重视不够,安全责任制未能有效贯彻落实,在安全培训、巡检检查、设备维护等方面存在疏漏和缺失。
2. 作业人员安全意识淡薄。
员工对于安全生产的意识和安全操作规程的遵守欠缺,存在违章作业的现象,忽视了作业过程中潜在的风险。
3. 安全管理规程不健全。
企业安全管理规程不够完善,缺乏详细的操作规范和应急预案,未能提供足够的安全保障措施和操作指导。
二、事故原因分析与预防措施1. 加强安全管理责任制。
企业领导要高度重视安全工作,制定明确的安全责任制,明确各级管理人员的安全职责,严格执行安全生产标准,确保安全管理责任不落空。
2. 提高作业人员的安全意识。
通过加强安全教育培训,让员工深刻认识到安全生产的重要性,加强对操作规程的培训和执行力度,强化员工对安全作业的自我监督和约束。
3. 健全安全管理规程和应急预案。
完善企业的安全生产规程和操作规范,全面编制应急预案,确保在事故发生时能够及时有效地进行应急处置,降低事故损失。
三、应急管理在事故发生后,企业需要采取一系列应急措施,确保人员及时疏散、火灾得到控制,并在事后进行事故调查和总结,从中吸取经验教训。
以下是一些建议的应急管理措施:1. 及时启动紧急预案。
企业应制定明确的紧急预案,并组成应急小组,当事故发生时,迅速启动预案,进行事故处置和人员疏散,确保人员生命安全。
2. 停止火源供给。
对于火灾事故,首先需要切断火源的供给,避免火势继续扩大,降低事故影响。
十大爆炸火灾事故案例分析

十大爆炸火灾事故案例分析火灾是一种常见的灾害事件,它可以给人们的生命和财产带来巨大的损失。
而爆炸火灾更是其中的一种极端情况,它具有瞬间破坏力大、扩散速度快、危害程度深等特点,往往是造成重大伤亡和财产损失的主要原因。
下面将对十大爆炸火灾事故案例进行分析,以期为防范类似事故提供借鉴和指导。
1. 天津港爆炸事故2015年8月12日晚,中国天津港发生了一起重大的爆炸事故,事故共造成165人死亡,789人受伤。
经调查发现,爆炸原因主要是由于储存在港口的危险化学品及其不当管理引发。
这次事故极大地震惊了全国,也引起了政府和企业对危化品管理的高度重视。
2. 比利时皮可尼宣告火灾2004年5月,比利时皮可尼市一家化工公司发生了严重的爆炸火灾,爆炸处附近的一栋楼房被彻底摧毁,至少15人死亡,数百人受伤,临近地区的数千人被疏散。
调查发现,该公司未按法定程序处理危险废物,也没有采取适当的安全措施。
3. 阿姆斯特丹Schiphol机场火灾1992年10月4日,荷兰阿姆斯特丹Schiphol机场发生了一起严重爆炸火灾,事故导致43人丧生,这起事故的爆炸原因是一家航空公司的货机所携带的危险品爆炸,引发大面积火灾。
事后,荷兰政府对危险货物的运输和处理进行了全面检讨。
4. 法国第戎化肥厂爆炸火灾2001年9月21日,法国第戎市一家化肥厂发生了爆炸火灾,至少30人死亡,200多人受伤,事故附近的大量建筑物被摧毁。
事故原因主要是工厂内储存的危险化学品发生泄漏导致火灾,事后法国政府对危险化学品储存和管理进行了整改。
5. 英国格兰费尔炼油厂爆炸火灾2005年12月11日,英国格兰费尔炼油厂发生严重的爆炸火灾,至少22人死亡,多人受伤。
事故调查显示,是厂内的原油处理装置发生了泄漏并引发火灾,且该装置未采用足够的安全措施。
6. 斯里兰卡Kurunegala燃气公司爆炸火灾2008年3月,斯里兰卡Kurunegala燃气公司发生了一起重大的爆炸火灾,事故造成至少23人丧生,150多人受伤。
石化企业火灾事故案例分析

石化企业火灾事故案例分析一、事故背景该石化企业是一家规模较大的化工企业,主要生产石化产品,并且拥有自己的石化厂。
该企业位于华北地区一个工业园区,距离城市约30公里,占地面积较大,拥有数千名员工。
该企业的石化厂主要用于生产石油制品,并且在生产过程中需要使用大量的化学品和高温炼制设备。
由于生产过程中使用大量的易燃易爆化学品,并且存在高温高压设备,该企业的火灾风险较高。
二、事故过程2018年7月10日,该石化企业发生了一起严重火灾事故。
据事故调查报告显示,事故发生的当天上午11点左右,一名操作工在工作中意外发生了意外操作错误,导致一台高温炼制设备发生泄漏,并迅速引发了火灾。
由于该高温炼制设备所处的位置较为隐蔽,且位置较为狭窄,其周围的通风条件不佳,导致火灾蔓延速度非常快。
当事故发生时,现场的工作人员迅速进行了应急处置,立即启动了应急报警系统,并且对火灾进行了初期扑救。
但是由于火灾发生位置较为隐蔽,加之炼制设备内部存在大量的易燃化学品,火势迅速蔓延,扑救难度较大。
同时,事故发生地点周围存在大量存储的易燃化学品,火灾蔓延迅速。
在火势蔓延的过程中,现场的应急处置人员受到了较大的干扰,且现场的通风条件较差,烟雾较浓,导致了很多的应急处置人员难以接近火灾现场,火灾扑救难度大增。
在火灾发生后的短时间内,消防部门迅速接到了报警,立即出动了多辆消防车和上百名消防官兵前往救援。
但是由于火势蔓延迅速且火灾现场周围存在较多的易燃化学品,消防官兵在扑救火灾的过程中遇到了很大的困难。
最终,经过几个小时的扑救,火灾得到了控制,但现场造成了重大的人员伤亡和财产损失。
三、事故原因根据初步调查结果和事故原因调查报告显示,该石化企业火灾事故的发生主要原因包括以下几个方面:1.操作错误:事故发生当日,一名操作工在工作中使用高温炼制设备时发生了操作错误,导致了设备的泄漏,并且忽略了设备周围的通风条件不佳,导致火灾的迅速蔓延。
2.安全管理不到位:该企业在化工生产中使用大量的易燃易爆化学品,但是对于这些化学品的存储、使用和管理存在较大的安全隐患,企业未能充分做好化学品的存储分区管理和防火阻燃工作。
国有企业较大安全生产事故案例

国有企业较大安全生产事故案例近年来,国有企业在安全生产方面发生了一系列较大的事故,给人民群众的生命财产安全带来了严重威胁。
下面列举了十个典型的国有企业较大安全生产事故案例。
1. 中国石油大庆油田火灾事故2013年11月,中国石油大庆油田发生火灾事故,导致9人死亡,4人重伤。
事故原因是油罐漏油,引发火灾,导致火势迅速蔓延。
2. 中国铁路武汉火灾事故2010年6月,中国铁路武汉火灾事故造成44人死亡,94人受伤。
事故原因是火车站的电缆发生短路,引发火灾。
3. 中国石化大庆炼化厂爆炸事故2013年11月,中国石化大庆炼化厂发生爆炸事故,造成55人死亡,136人受伤。
事故原因是在装卸过程中发生泄漏,引发爆炸。
4. 中国航天科技集团火箭发射事故1996年1月,中国航天科技集团火箭发射事故造成6人死亡。
事故原因是火箭发射时发生异常,导致火箭坠毁。
5. 中国煤矿安全事故中国煤矿安全事故频发,造成大量人员伤亡。
其中,2010年山西矿难造成了104人死亡,2005年辽宁矿难造成了214人死亡。
6. 中国电力公司电网事故中国电力公司电网事故时有发生,造成人员伤亡和电力中断。
2011年湖南电力公司电网事故造成了9人死亡,2014年广东电力公司电网事故造成了12人死亡。
7. 中国航空工业集团飞机事故中国航空工业集团飞机事故时有发生,造成机上人员伤亡和飞机损毁。
2018年中国航空工业集团一架飞机在试飞中坠毁,机上3人死亡。
8. 中国化工集团化学品泄漏事故中国化工集团化学品泄漏事故时有发生,造成环境污染和人员伤亡。
2015年天津港爆炸事故造成173人死亡,798人受伤。
9. 中国冶金集团冶炼事故中国冶金集团冶炼事故频发,造成环境污染和人员伤亡。
2018年山东冶金集团一处冶炼厂发生爆炸事故,造成4人死亡。
10. 中国船舶工业集团船舶事故中国船舶工业集团船舶事故时有发生,造成人员伤亡和船舶损毁。
2016年江苏船舶工业集团一艘船舶在试航中发生事故,3人死亡。
石油、化工、交通等行业安全生产典型事故案例分析

1 根据预定的方案进行停车。根据检修计划的规定及各工序要求,实现各部门之间及时
的信息交换,根据检修方案在适当的时间进行停车,停止相关设备的运行。
检 修
2 进行泄压时要注意力度。泄压的过程应当缓慢进行,没有进行完全的泄压之前,禁止
对任何化工设备进行移动或者拆装。
之
3 设备内的材料和垃圾要进行彻底的清洁。对排放口的仔细观察,防止易燃、易
工业安全生产
典型事故案例分析
前车之鉴征
1 发生火灾、爆炸、中 毒事故机率大且后果 严重 ;
2 触发事故的因素多 ; 3 设备材质和加工缺陷
以及腐蚀等原因触发 事故; 4 事故的集中与多发 。
编辑ppt
案例一: 河北廊坊一座加油站爆炸
事故因静电火花引发
2011年12日16时45分许,河北省 廊坊市和平路一中石化加油站发 生起火爆炸事故。廊坊市官方称 ,事故未造成人员伤亡,起火原 因为油罐车卸油后,静电火花引 发起火爆炸。
3 高危险性: 危化品生产的危险性决定了检修 工作的危险性。易燃、易爆、有 毒有害物质残存。检修过程的动 火、进塔入罐等作业使得客观具 备了发生火灾、爆炸、中毒窒息 、化学灼伤、触电等事故的条件 。加之频次高、作业复杂、参加 检修人员变化大,因此,危险化编辑ppt 学品检修具有高危险性。
化工设备检修过程中所需要的安全措施
的
故障。对高温设备进行降温时,应当首先切断热源,然后进行通风,以适当的自然降温达到降温的目的 ,切不可以直接浇灌冷水进行降温,尤其是外部气温较高时,应当缓慢的降温,防止温度的剧烈变化引
安
起设备的损坏,防止发生火灾或者爆炸事故,同时防止有毒有害的物质对环境的污染。
全
5 阀门的开启速度要适当。正确的阀门开启方法应当是在打开阀门扣之后,停止片刻,使
石油化工行业火灾事故发生的原因

石油化工行业火灾事故发生的原因一、设备故障1、设备老化石油化工行业的设备往往需要长时间运行,设备老化是导致火灾事故的一个重要原因。
随着设备使用时间的延长,设备的结构和功能容易发生问题,从而引发火灾事故。
为了避免因设备老化导致的火灾事故,企业需要定期进行设备维护和检修,并及时更换老化设备。
2、设备设计缺陷在石油化工行业,设备的安全性和稳定性非常重要。
如果设备设计存在缺陷,容易导致设备故障,从而引发火灾事故。
企业需要注重设备的设计和制造质量,确保设备符合相关标准和规定,减少因设备设计缺陷导致的火灾事故。
3、设备维护不及时在石油化工行业,设备的定期维护和检修非常重要,可以有效预防设备故障和火灾事故的发生。
如果企业对设备的维护不及时,容易导致设备故障,从而引发火灾事故。
因此,企业需要加强设备维护管理,保证设备的正常运行和安全性。
二、操作失误1、操作不当在石油化工行业,操作不当是导致火灾事故的一个重要因素。
员工在操作设备和工艺过程中,如果操作不当,容易引发设备故障和火灾事故。
为了避免因操作不当导致的火灾事故,企业需要加强员工的操作培训和管理,确保员工具备良好的操作技能和安全意识。
2、化学品混合在石油化工行业,化学品是常见的危险品,如果化学品混合不当,容易引发火灾事故。
因此,企业需要加强化学品管理,确保化学品的存储和使用符合相关标准和规定,避免因化学品混合导致的火灾事故。
3、违反操作规程企业在制定操作规程时,需要重视操作规程的制定和执行,确保员工严格遵守操作规程,避免因违反操作规程导致的火灾事故。
同时,企业需要对员工进行操作规程的培训和教育,提高员工对操作规程的遵守度。
三、安全管理不善1、安全管理制度不健全在石油化工行业,安全管理制度是防范火灾事故的重要手段。
如果企业的安全管理制度不健全,容易导致火灾事故的发生。
企业需要建立健全的安全管理制度,明确安全责任和管理程序,加强监督和检查,确保安全管理制度的有效执行。
石油化工火灾、爆炸事故案例分析
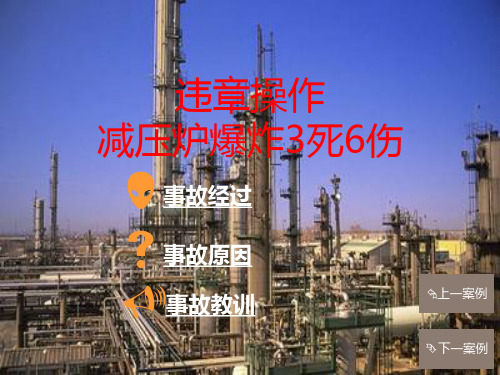
(其中1人经抢救无效,于10月26日
死亡),轻伤5人。直接经济损失3.5 万元,间接经济损失7万元。
可燃气体积聚 明火引起爆炸 ——事故经过
10月8日13时30分,按计划检修后的催化装置投料开车。 15时,前部操作基本正常,但因解析塔底再沸器泄漏,稳 定系统迟迟不能正常,不合格汽油开始出装置,送汽油罐 区214号储罐(该罐是容积为2000m3的钢制内浮顶罐)。 15时30分许,催化车间稳定岗位负责人为了降低稳定塔 304的液面,将塔内油品同时送往214号储罐,因稳定系统 的热源没有建立起来,汽油携带轻组分进入罐区。
油气线侧法兰口处出现青烟,接着爆燃起火。检修人员在躲闪时,
2人从6m高的平台上坠落,1人死亡,1人腰部受伤,其余5人被火 燎伤。
催化两器检修 引起爆炸伤人 ——事故原因
⑴此次停工仅检查两器,对分馏塔稳定系统不进行 动火检修,在翻盲-201前按操作规程对分馏塔 只进行了粗吹扫,残存的可燃气体进入大油气 线。 ⑵在翻盲-201过程中,由于2个螺栓卸不下来,被 迫用钢锯锯断螺栓,大大延长了装盲板的时间, 空气进入油气线内时间过长,大油气线内结焦 多,造成自然闪爆。
2. 应加强对设备的维修管理,定期对止逆阀进行检 查和维护,确保其灵敏好用。 3. 对设计上没有安装安全阀的低压脱氧水罐,应采 取有效的补救防护措施。
加热炉点火 发生闪爆 1人死亡 事故经过 事故原因 事故教训
下一案例
加热炉点火 发生闪爆 1人死亡 ——事故经过
2003年9约11日,乌鲁木齐石化分公司化肥厂二合成车间合成
含油污水溢出地面 浸泡高温管线着火 ——事故经过
化工厂火灾事故案例及分析总结
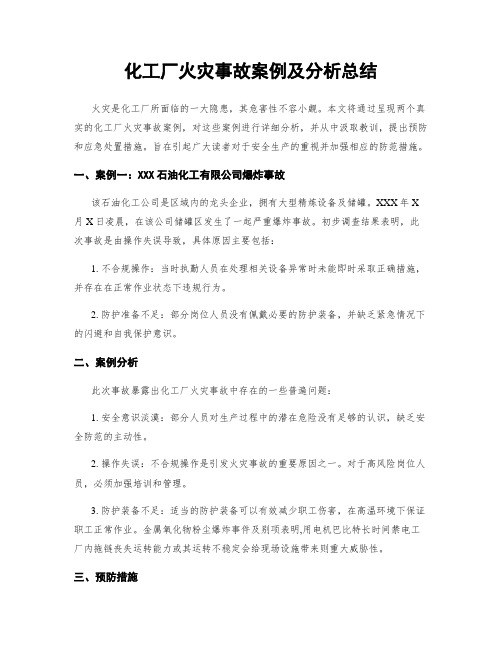
化工厂火灾事故案例及分析总结火灾是化工厂所面临的一大隐患,其危害性不容小觑。
本文将通过呈现两个真实的化工厂火灾事故案例,对这些案例进行详细分析,并从中汲取教训,提出预防和应急处置措施。
旨在引起广大读者对于安全生产的重视并加强相应的防范措施。
一、案例一:XXX石油化工有限公司爆炸事故该石油化工公司是区域内的龙头企业,拥有大型精炼设备及储罐。
XXX年X 月X日凌晨,在该公司储罐区发生了一起严重爆炸事故。
初步调查结果表明,此次事故是由操作失误导致,具体原因主要包括:1. 不合规操作:当时执勤人员在处理相关设备异常时未能即时采取正确措施,并存在在正常作业状态下违规行为。
2. 防护准备不足:部分岗位人员没有佩戴必要的防护装备,并缺乏紧急情况下的闪避和自我保护意识。
二、案例分析此次事故暴露出化工厂火灾事故中存在的一些普遍问题:1. 安全意识淡漠:部分人员对生产过程中的潜在危险没有足够的认识,缺乏安全防范的主动性。
2. 操作失误:不合规操作是引发火灾事故的重要原因之一。
对于高风险岗位人员,必须加强培训和管理。
3. 防护装备不足:适当的防护装备可以有效减少职工伤害,在高温环境下保证职工正常作业。
金属氧化物粉尘爆炸事件及别项表明,用电机巴比特长时间禁电工厂内拖链丧失运转能力或其运转不稳定会给现场设施带来则重大威胁性。
三、预防措施通过上述案例的分析,提出以下预防措施以确保化工厂火灾事故得到有效预防:1. 安全培训与技能考核:对所有从业人员进行系统且定期的安全培训,并建立相应的技能考核制度,保证人员具备必要的安全技能。
2. 制定操作规范:明确各类设备的操作规程和标准,严格执行,禁止任何不合规或擅自更改操作步骤。
3. 责任分工与制度落实:明确岗位责任与义务,在每个岗位上配备专职负责人,并建立相应的考核评价机制。
4. 增强防护意识:加强员工对火灾风险的认知,定期组织相关演练活动,并普及逃生和自救知识。
5. 配备合适的防护装备:确保所有员工都配备适当的个人防护装备,在作业过程中正确佩戴和使用。
炼油化工厂火灾事故案例分析

炼油化工厂火灾事故案例分析引言炼油化工厂是从原油中提取石油化工产品的工厂,它们在生产过程中常常面临着各种安全隐患。
由于化工产品的特殊性,一旦发生火灾事故,往往影响面广,后果严重。
本文结合实际案例,对炼油化工厂火灾事故进行细致分析,探讨其原因和处理方法,以期为工业生产提供一定的参考价值。
一、案例描述在某炼油化工厂,一次火灾事故给厂家和当地社会带来了极大的损失。
事故发生在夜间,当时工厂正在生产硫酸。
据当时值班工作人员描述,他们当时发现某个生产装置突然起火,随即立即启动了应急预案,联系了消防队赶到现场扑救,并通知了相关部门和厂家领导。
在消防队到达前,工作人员已经紧急疏散了全部员工,并利用厂内消防设施对火灾进行了初步扑救,但火势迅速扩大,整个生产区域被烟雾和火焰覆盖。
事故发生后,该炼油化工厂发生了严重的财产损失,一座生产装置被烧毁,大量原材料被烧毁,导致生产中断数周,厂家形象受损,相关部门对其进行了处罚。
二、事故分析1.事故原因火灾事故的发生通常涉及多个方面的原因,常见的有人为因素、设施设备故障、管理不当等。
我们对此次事故的原因分析如下:(1)人为因素在炼油化工厂生产中,人为因素是常见的事故原因之一。
据事故调查,火灾事件发生时正在生产硫酸,硫酸生产过程中有一定的安全隐患,一旦操作不当极易引发火灾。
在该事故中,可能是操作人员在生产过程中存在操作失误,或者在清理生产设备时未按程序规定操作,导致硫酸泄漏并引发火灾。
(2)设备故障事故中的设备故障也是造成火灾的一个主要原因。
可能是在生产设备运行时发生了设备故障,导致设备失控,硫酸泄漏并引发火灾。
设备故障通常是由于设备老化、维护不当、损坏等原因造成的,因此在生产过程中,对设备的维护和检查至关重要。
(3)管理不当管理方面的不当也可能是造成事故的原因之一。
可能是由于生产过程中监管不到位,未能及时发现问题并采取措施加以修复,或者是对员工的安全教育培训不足,导致员工在操作设备时存在风险,进而引发了火灾。
石油石化行业安全事故案例分析

仪) 不可靠, 有时不能使用, 而反应器在 运行中的绝大部分温度数据都是靠这 些仪器记录的。
( 6) 操作人员培训不够。培训教材 过时, 单元更新培训计划没有制定。操 作 人 员 缺 乏 异 常 操 作 情 形 的 知 识 、以 及 处理紧急程序能力的培训。
3.事故教训 ( 1) 管理层不能只 考 虑 成 本 和 生 产 。管 理 层 必 须 让 操 作 人 员 了 解 运 行 目 标 和 存 在 的 危 险 。生 产 装 置 的 管 理 必 须 设置安全操作极限, 必须为操作人员提 供一个在必要时能有效执行的紧急停 车程序。 ( 2) 在设计工艺控制仪表时应考虑 到 便 于 操 作 。加 氢 处 理 反 应 器 的 温 度 控 制应将控制室内所有可以利用的必要 数据汇总在一起, 应使用某种备用温度 指示系统, 以便在仪表发生故障时仍可 继 续 安 全 运 行 装 置 。各 报 警 系 统 的 设 计 应允许将关键的紧急报警从其他操作 报警中分出来。 ( 3) 应对操作人员 实 行 适 当 的 监 督 。监 督 人 员 必 须 保 证 所 有 规 定 的 程 序 得到遵循。 ( 4) 对操作人员加强培训。管理层 必须确保操作人员在工艺单元操作和 化学知识方面接受定期培训, 在使用紧 急停车系统以及何时需要启用该系统 方面接受培训。
2.原因分析 ( 1) 直接原因是从铁路罐车经油泵 往储罐(B 罐) 卸轻柴油时, 由于操作工 开错阀门, 使轻柴油进入了满载的石脑 油 A 罐, 导致石脑油从罐顶大量溢出 ( 约 637 立方米) , 溢 出 的 石 脑 油 及 其 油 气在扩散过程中遇到明火, 产生第一次 爆炸和燃烧, 继而引起罐区内乙烯罐等 其他罐的爆炸和燃烧。 ( 2) 安全设施上存在问题。该大型 危化品储存区的重要储罐没有必要的 液位报警连锁系统; 可燃气体检测报警 器 数 量 不 够 、位 置 不 合 理 ; 关 键 阀 门 无 信号回讯功能; 消防泵配备不合理( 在 电源不可靠情况下, 柴油消防泵应 100%备用) 。 ( 3) 企 业 安 全 教 育 不 够 , 从 业 人 员 的安全意识淡薄, 敬业精神与责任心不 强, 导致出现不应有的操作失误。 3.事故教训 ( 1) 应 加 强 应 急 管 理 , 提 高 应 急 处 理能力。由于事发时间为周末, 事故发 生后, 企业一片混乱, 丧失了事故初期 必要的自救功能, 致使事故扩大。 ( 2) 危化品储存区应完善安全防护 技 术 措 施 。一 是 在 设 计 上 应 有 防 止 误 操 作的安全技术措施; 二是在出现操作失 误的情况下, 应有及时发现与信息反馈 的安全警示技术设施。 ( 3) 应 完 善 安 全 管 理 体 系 , 落 实 各 项 安 全 生 产 管 理 制 度 。从 开 始 卸 轻 柴 油 到发生大爆炸, 历时 1 小 时 40 分 , 在 这 期间, 只要能切断“多米 诺 骨 牌 ”事 故 链 中的任何一个环节, 都能有效地制止这 次事故的发生。遗憾的是, 由于该企业 在安全管理体系上的不健全, 对企业内 各个关键环节不能实施有效的安全监 控与检查, 最终酿成了此次悲剧的发 生。■
石油化工油罐火灾爆炸事故案例分析

事故背景:油罐 区内一油罐发生 火灾,火势迅速 蔓延至周边油罐, 引发爆炸。
事故涉及人员和物质
事故涉及人员: 操作工、维修工、 管理人员等
事故涉及物质: 石油、天然气、 油品等易燃易爆 物质
事故发生时间: 2022年7月1日
事故发生地点: 某石油化工企业 油罐区
事故发生经过和后果
事故发生时间、地点和原 因
处理方式:对责任 人员进行相应的处 罚,包括罚款、拘 留等;对责任单位 进行整顿、吊销执 照等处理
预防措施:要求责 任人员和单位采取 相应的预防措施, 防止类似事故再次 发生
追责过程中应注意的问题和改进措施
证据收集:确保收集到充分、可 靠的证据,以证明事故责任。
改进措施:针对事故原因,采取 切实可行的改进措施,预防类似 事故再次发生。
05
事故责任认定和追责
事故责任认定依据和过程
依据法律法规进行责任认定
确定责任主体和责任人
添加标题
添加标题
调查事故原因和过程
添加标题
添加标题
依法追究相关责任人的法律责任
责任人员和单位的确定及处理
责任人员的确定: 根据事故调查结果, 确定相关责任人员
责任单位的确定: 根据事故调查结果, 确定相关责任单位
预防措施:根据事 故原因分析,提出 针对性的预防措施, 如加强设备维护、 规范操作流程等。
处理经验:总结类 似事故的处理经验, 如及时切断火源、 使用专用灭火器材 等。
教训反思:对类似 事故进行深刻反思, 提出加强安全意识、 完善安全管理制度 等建议。
对石油化工行业的安全管理和监管的建议和展望
强化安全意识,提高员工安全素质
事故教训总结: 从每个案例中总 结出教训,如加 强安全管理、提 高员工安全意识、 完善应急预案等。
石油化工企业火灾爆炸事故的原因及预防措施

石油化工企业火灾爆炸事故的原因及预防措施一、火灾爆炸事故的常见原因1、可燃气体泄漏由于可燃气体外泄容易与空气形成爆炸性混合气体,因此,可燃气体的泄漏就容易造成火灾爆炸事故。
可燃性气体泄漏有以下几种情况:(1)设备的动静密封处泄漏;(2)设备管道腐蚀泄漏;(3)水封因断水,未加水跑气泄漏;(4)设备管道阀门缺陷或断裂造成泄漏。
这类事故大致是由于生产设备管理混乱,密封材料材质或检修不合要求,操作维护不当,在检修中未泄压却加外力,操作中巡回检查开停车不按操作规程进行等因素引起的,因此,必须按原化工部规定的检修操作规程、无泄漏工厂的标准以及设备动力管理条例等有关规定加以管理。
对已出现的泄漏,及时发现,及时消除,暂不能消除的要有预防措施,避免扩大或发生灾害事故。
2、系统负压,空气与可燃气体混合造成可燃性混合气体情况(1)系统停车,停车后随温度下降造成负压,由敞口吸入空气;(2)系统停水,停水后水封水因泄漏失去作用而导致空气吸入;(3)操作失误,联系不当,报警联锁装置不全或失灵,造成气体抽送不平衡而至负压,由敞口或泄漏处吸人空气。
(4)气体人口管线被杂物、结晶体或水堵塞,造成抽负,由敞口或泄漏处吸入空气;(5)用空气作试压、试漏,系统可燃物未清除干净、未加盲板,造成可燃气体与空气混合。
这类事故大部分发生在气体输送岗位或与气体压缩有关的岗位,当发生在加压过程中时更加危险,因为在爆炸性混合气体中,一方面氧含量在增加,另一方面在加压后,爆炸极限范围扩大,更容易发生事故。
3、系统生产时氧含量超标氧含量超标,可能在许多部位出现,但究其原因集中在造气岗位,通常由操作失误、设备缺陷、人员违章、断油断汽或安全报警装置失灵所造成,氧含量超标可能超出造气岗位范围而在脱硫、变换、压缩等部位发生,应当引起特别重视。
4、系统串气系统串气有2种情况:一种情况是高压串低压,形成超压爆炸;另一种是空气与可燃性气体互串形成化学性爆炸。
前一种情况大部分是由于操作失误及低压无安全附件或附件失灵造成。
全国范围石化企业火灾爆炸事故案例汇总讲解

全国范围石化企业火灾爆炸事故案例汇总讲解案例一:上海某石油化工公司炼油厂液化气爆炸一、事故概况及经过1988年10月22日凌晨,上海某石油化工公司炼油厂小凉山球罐区发生液化气爆燃事故,死亡25人,烧伤17人,直接经济损失9.8万余元。
10月21日23时40分,该厂在三区14号球罐开阀放水,违反操作规程,没切换开关,阀门全部打开,致使液化气随水外溢达9.7吨,通过污水池扩散到罐区西墙外,与工棚明火相遇,在连续沉闷的爆炸声中,南北350米、东西250米的地带燃起熊熊大火。
毗邻球罐区的10多间简易工棚代为灰烬,围墙内建筑受到破坏,变压器、电缆、电讯仪表等严重损坏,变电室房顶开裂,一扇铁门飞出60多米远。
二、事故原因分析这是一起违章操作,纪律松驰,管理混乱,领导上的官僚主义引起的重大责任事故。
班长在接到门岗保安人员发现异常气味的报告后麻痹大意,保安队书记、保卫科、值班室等接到门岗电话后不及时处理,贻误了时机。
当班的7个工人中,3个拨葱做饭,后又有2人关门睡觉。
球罐区民工安炉灶,各级领导熟视无睹,无人制止。
案例二:某石化公司炼油厂储油罐爆炸起火一、事故概况及经过1993年10月21日18时15分,南京某石化公司炼油厂油品分厂罐区发生爆炸,引起310号油罐燃烧,造成2人死亡,直接经济损失约39万元。
1993年10月21日13时许,某石化公司炼油厂油品分厂半成品车间工人黄某某在当班期间,发现310号油罐油面高度已达14.21米,接近警戒高度14.30米,黄马上向该厂总调度进行了报告,并向总调度请示310号油罐汽油调合量。
根据总调度的指示,黄某某进入罐区将油切换至304号油罐。
13时30分许,黄在给31O号油罐作汽油调合流程准备时,本应打开310号罐D400出口阀门,却误开了311号油罐D400出口阀门。
15时许,黄开启11A号泵欲对310号油罐进行自循环调合,由于错开了311号B400出口阀门,实际上此时310号油罐不是在自循环,而是将311号罐中的汽油抽入310号油罐。
化工企业火灾事故案例分析总结
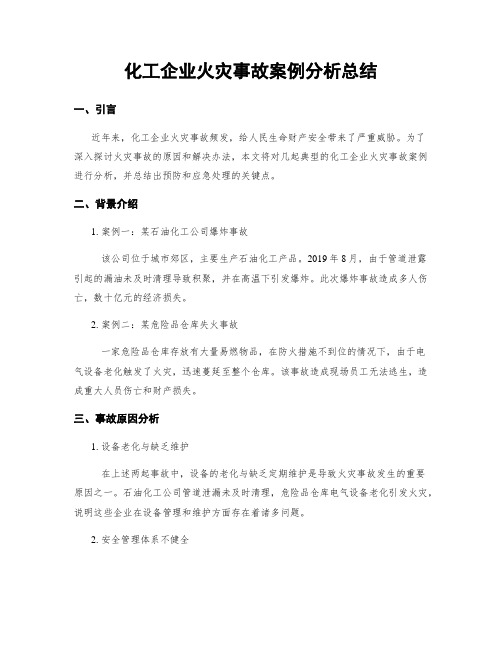
化工企业火灾事故案例分析总结一、引言近年来,化工企业火灾事故频发,给人民生命财产安全带来了严重威胁。
为了深入探讨火灾事故的原因和解决办法,本文将对几起典型的化工企业火灾事故案例进行分析,并总结出预防和应急处理的关键点。
二、背景介绍1. 案例一:某石油化工公司爆炸事故该公司位于城市郊区,主要生产石油化工产品。
2019年8月,由于管道泄露引起的漏油未及时清理导致积聚,并在高温下引发爆炸。
此次爆炸事故造成多人伤亡,数十亿元的经济损失。
2. 案例二:某危险品仓库失火事故一家危险品仓库存放有大量易燃物品,在防火措施不到位的情况下,由于电气设备老化触发了火灾,迅速蔓延至整个仓库。
该事故造成现场员工无法逃生,造成重大人员伤亡和财产损失。
三、事故原因分析1. 设备老化与缺乏维护在上述两起事故中,设备的老化与缺乏定期维护是导致火灾事故发生的重要原因之一。
石油化工公司管道泄漏未及时清理,危险品仓库电气设备老化引发火灾,说明这些企业在设备管理和维护方面存在着诸多问题。
2. 安全管理体系不健全火灾事故也暴露了这些企业安全管理体系不完善、操作规程不规范等问题。
例如,在某石油化工公司爆炸事故中,未能通过合理的保养措施及时发现并消除隐患;在危险品仓库失火事故中,缺乏有效的应急预案和应对措施。
3. 人为操作错误另一个共同点是人为操作错误。
石油化工公司在处理管道泄漏时未采取正确的措施加以修复;危险品仓库工作人员使用老旧设备进行操作,并没有严格遵守相关安全程序。
四、经验教训总结1. 加强设备维护和管理为了避免因设备老化和缺乏维护导致的事故,化工企业应加强对设备的定期检查、维护和更新。
利用先进的技术手段进行设备运行状态监测,并建立健全的设备寿命周期管理制度。
2. 完善安全管理体系建立并执行科学有效的安全管理规章制度,明确各岗位之间的职责和权限。
定期开展培训和演练,提高员工的安全意识与操作技能。
加强隐患排查,及时消除存在问题。
3. 提高人员素质与专业水平需要在招聘、培训等方面加大力度,确保从业人员具备足够的技能、知识和经验。
石油化工油罐火灾爆炸事故案例分析

石油化工油罐火灾爆炸事故案例分析案例概述:该事故发生在一家石油化工企业的油罐区域。
当时,由于各种原因导致了油罐区域内的石油产品发生泄漏,油气呈现累积状态。
随后,火源引发了油罐区域的火灾,从而导致严重的爆炸。
事故发生后,许多工人被困在事故现场,造成了重大的人员伤亡。
事故原因分析:1.过程控制失误:在事故中,油罐区域内的石油产品泄漏,这主要是由于过程控制失误导致的。
可能是由于操作员疏忽大意或不当操作,导致了泄漏的发生。
2.安全管理不完善:石油化工企业内油罐区域的安全管理存在问题,缺乏完善的安全标准和操作规程。
例如,缺乏泄漏应急响应程序和适当的漏油控制措施等。
3.隐患未及时发现和消除:在此事故中,存在一些潜在的安全隐患,但这些隐患未及时发现和消除。
比如,油罐的检修不充分,存在泄漏隐患。
及时发现并修复这些隐患,有可能避免事故的发生。
经验教训总结:1.强化安全培训和意识教育:加强对员工的安全培训,提高员工的安全意识和工作素质,提醒他们时刻注意安全问题,并熟悉应急处理措施。
2.加强安全管理:建立并完善安全管理体系,明确各个岗位的责任和义务,制定详细的安全操作规程和应急预案。
确保安全设施的完善、安全器材的运行正常,并定期进行维护和检修。
3.加强隐患排查:建立健全的隐患排查和处理制度,定期开展隐患排查工作,及时发现和消除潜在的安全隐患。
4.强化事故应急响应能力:建立健全的应急响应机制,定期进行应急演练,提高应急处理能力和反应速度。
5.重视现场安全管理:对于易发生泄漏和火灾爆炸的危险品装置和设备,要加强现场管理,切实做好安全防护措施。
通过对石油化工油罐火灾爆炸事故案例的分析,我们可以看出事故的发生往往是由于多种因素综合作用的结果。
要提高企业的安全生产水平,必须全面考虑工艺设计、设备设施、人员素质等方面的问题,并加强安全管理和培训等工作。
只有这样,才能及时发现和消除安全隐患,预防和减少事故的发生,保障员工的安全和企业的可持续发展。
石油化工火灾事故案例分析
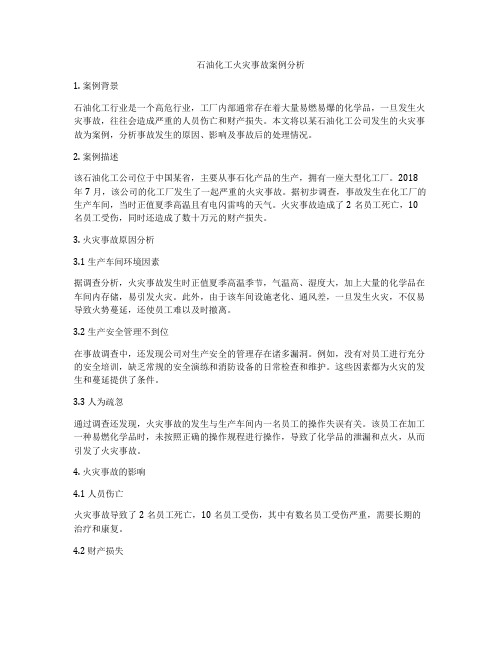
石油化工火灾事故案例分析1. 案例背景石油化工行业是一个高危行业,工厂内部通常存在着大量易燃易爆的化学品,一旦发生火灾事故,往往会造成严重的人员伤亡和财产损失。
本文将以某石油化工公司发生的火灾事故为案例,分析事故发生的原因、影响及事故后的处理情况。
2. 案例描述该石油化工公司位于中国某省,主要从事石化产品的生产,拥有一座大型化工厂。
2018年7月,该公司的化工厂发生了一起严重的火灾事故。
据初步调查,事故发生在化工厂的生产车间,当时正值夏季高温且有电闪雷鸣的天气。
火灾事故造成了2名员工死亡,10名员工受伤,同时还造成了数十万元的财产损失。
3. 火灾事故原因分析3.1 生产车间环境因素据调查分析,火灾事故发生时正值夏季高温季节,气温高、湿度大,加上大量的化学品在车间内存储,易引发火灾。
此外,由于该车间设施老化、通风差,一旦发生火灾,不仅易导致火势蔓延,还使员工难以及时撤离。
3.2 生产安全管理不到位在事故调查中,还发现公司对生产安全的管理存在诸多漏洞。
例如,没有对员工进行充分的安全培训,缺乏常规的安全演练和消防设备的日常检查和维护。
这些因素都为火灾的发生和蔓延提供了条件。
3.3 人为疏忽通过调查还发现,火灾事故的发生与生产车间内一名员工的操作失误有关。
该员工在加工一种易燃化学品时,未按照正确的操作规程进行操作,导致了化学品的泄漏和点火,从而引发了火灾事故。
4. 火灾事故的影响4.1 人员伤亡火灾事故导致了2名员工死亡,10名员工受伤,其中有数名员工受伤严重,需要长期的治疗和康复。
4.2 财产损失火灾事故造成了数十万元的财产损失,其中包括生产设施的损坏和生产中断所带来的经济损失。
4.3 对社会的影响由于火灾的发生还造成了工厂周边居民的恐慌和对环境的担忧,对社会稳定产生了影响。
5. 火灾事故后的处理情况5.1 紧急救援和治疗火灾事故发生后,公司立即展开紧急救援工作,将受伤员工及时送往医院接受治疗,并出资进行了相关的医疗费用报销。
石油化工火灾爆炸事故案例分析

典型石油化工火 灾爆炸事故案例
案例一:某石化公司火灾事故
事故时间:XXXX年XX月XX日 事故地点:某石化公司厂区内 事故经过:厂区内一储罐发生泄漏,引发火灾爆炸事故 事故原因:储罐长期未进行维护,导致罐体腐蚀穿孔,发生泄漏
事故原因调查和善后处理
事故原因调查: 确定事故发生的 原因,为预防类 似事故再次发生
提供依据。
善后处理:包括 赔偿、处罚、整 改等措施,以最 大程度地减少事 故对人员、环境 和社会的影响。
石油化工火灾爆 炸事故的教训和 启示
重视安全管理和预防措施
事故案例分析:了解事故发生的原 因、过程和后果
预防措施的有效性:加强隐患排查、 监测预警和应急处置能力
应急资源的调配:根据事故现 场情况,合理调配人力、物力、
财力等资源
应急处置的注意事项:在处置 过程中,应注意安全、科学、
高效等原则
现场救援和处置
启动应急预案,组 织专业人员迅速到 达事故现场
疏散周边人员,划 定警戒区域,防止 事态扩大
对事故现场进行安 全评估,采取相应 的防护措施
根据事故情况,采 取相应的灭火措施 ,控制火势
案例二:某油库爆炸事故
事故概述:某油库发生爆炸事故,造成重大人员伤亡和财产损失 事故原因:油库安全管理不善,设备故障导致油品泄漏并引发爆炸 事故后果:造成多人伤亡,周边环境受到严重污染 事故教训:加强油库安全管理,定期进行设备维护和检查
案例三:某石油化工企业火灾事故
事故概述:某石油化工企业在生产过程中发生火灾事故,造成多人伤亡和重大财产损失。 事故原因:设备故障、操作失误、安全管理不到位等原因导致泄漏引发火灾。 事故后果:多人伤亡,企业停产整顿,政府展开调查。 事故教训:加强设备维护保养,规范操作流程,完善安全管理制度等。
石油化工企业火灾爆炸事故案例及其引发原因

石油、化工企业火灾爆炸事故案例及其引发原因 1•这里只列举部分发生在国内外石油、化工企业的已发事故限定在生产作业期间及生产作业准备阶段发生的事故以及个别未遂事故,并对事故发生的直接原因进行粗略划分;这里只列举部分发生在国内外石油、化工企业的已发事故限定在生产作业期间及生产作业准备阶段发生的事故以及个别未遂事故,并对事故发生的直接原因进行粗略划分;1、工程设计失误1、设计单位对设计任务认识不深某沿海企业在海边建设油罐,设计单位因无经验在设计中未对罐底外壁采取防腐措施;由于地处海边,化学腐蚀现象严重,若不对罐底外壁采取防腐措施,则油罐建成后罐底将很快被腐蚀穿透,不仅油罐将报废,若油品大量漏失,还会引发严重的次生事故如火灾、爆炸、环境污染等等;建设单位在最后一次审查时发现了这个问题,并予以纠正;某厂在建设一套采用了新技术的装置时,由于企业技术人员没有搞清新技术到底新在什么地方,向设计单位提供了过时的物料数据对于老技术来说,这些数据仍然可用,设计单位也没有进行认真审查;装置建成投产后,核心设备每天都处在超温工况下工作;不到一年就将该核心设备烧坏,只好再花5000多万元进行改造;辽阳石聚乙烯新线工艺是按老线工艺照搬过来的,而多处设计错误是导致2002年2月23日发生爆炸的直接原因;A、设计单位擅自将悬浮液接收罐的安全阀开启压力从MPa,改为MPa;视镜是在MPa时破裂后引发爆炸事故的;如果设计不改变新线安全阀的起跳压力视镜很可能不会破碎,爆炸事故也就不会发生;B、原化学工业部压力容器视镜设计要求规定:视镜最大直径为150mm,最大公称压力为MPa;而设计部门违反规定擅自选择直径为200mm,公称压力为MPa非标视镜,这种视镜目前国内尚无法生产;C、厂房是封闭的,这也不符合国家的规范要求;d、将沸腾床引风机的入口设置在聚合釜的上方,设计上也是错误的;2、工艺过程设计不合理1982年、1993年,分属两个企业的两套催化裂化装置的中间罐先后于发生了爆炸,1993年1月1日的那次爆炸还引发大火;两次事故相隔近10年,且分别是两个设计单位作的设计;但这两个设计单位都没有处理好中间罐的工艺设计,都存在若阀门关不严,不同性质物料发生串通的可能性;结果,由于阀门关不严,造成不同性质物料的相互混合,致使中间罐压力急剧升高而发生爆炸; 某合成氨装置,设计时在原料天然气管线与压缩空气管线之间设计了一个连通阀,导致天然气窜入空气管线中,发生爆炸;3、总图布置设计不合理有一个企业把乙烯装置的紧急放空口设在空分装置的上风位置,结果在乙烯装置紧急放空时,空分装置将从乙烯装置放出的烃分子吸入;经压缩后烃和纯氧在空分装置内相遇,发生剧烈氧化而爆炸;造成3人死亡、31人受伤,其中1人是被飞出200米外的一块钢板砸死;2、由于操作人员的违规操作或各种原因造成的误操作在化工生产中,由于人员的违章作业、违章指挥、违反劳动纪律而发生的各类事故所占比率很高;据有关统计,在已经发生的各类事故中,由于人员“三违”引发的占到75%左右;其中,仅因操作工开错阀门或没有及时关闭阀门而引发的事故就有多起,并都造成了很大影响;而这些由“三违”引发的事故,多数表现为设备的破坏;以设备破坏为表面现象的事故,大约也占到了70%以上;2006年12月5日抚顺市液化气公司因为操作工没有及时关闭放水阀门,致使49吨液化气泄漏,周围地区就象笼罩在大雾中一样;抚顺市紧急采取措施疏散人员,并将该地区隔离才没有引发更大的事故;1997年6月27日,北京东方化工厂罐区,在收油时操作工开错阀门,致使石脑油大量外溢,遇明火引发爆炸及两次后续爆炸;此次事故共有9人死亡、39人受伤,直接损失亿元人民币,造成该厂几乎全部主要装置停产10个月; 198 8年高桥石化的液化气罐区,因为操作工没有及时关闭切水阀门,致使液化气大量泄漏;泄漏出的液化气沿管沟流到工厂外的民工居住地,遇明火引发爆炸,造成多名人员伤亡;约十年前,荆门石化原油罐区连续两年跑损原油事故,其中一次是也是由于因为操作工没有及时关闭放水阀门,致使原油大量泄漏,并污染了下游水库; 某企业一套装置在开车过程中,操作工点炉子,违反操作规程,在没有进行炉膛气体成分的分析之前,就去点火,结果引起炉膛爆炸; 某企业一套装置,泵出口因物料结焦而堵塞,为赶生产任务,没有将装置内的油全部退出,也没有切断检修部位与系统的连接,就开始检修,结果把焦捅掉后热油冒出把检修工烫死了; 东北某厂酸性水系统进行防冻排液操作,操作工打开切水阀门后忘记关阀门,导致硫化氢气体沿地沟流进操作工休息间,4人死亡; 某化肥厂包装机发生故障停车,操作工正在处理;班长未和操作工打招呼就进入机器内查看,操作工处理完后立即开机,结果将班长挤死在包装机内; 1973年10月23日18时13分,江苏某化肥厂造气车间造气工段由于操作工操作失误,,加之安全阀、压力表失灵,造成煤气发生炉夹套内满水、超压破裂,夹套内的水进入煤气发生炉内,造成炉体爆炸,当场炸死3人; 1989年2月17日14时38分,江西省鹰潭市某橡胶厂,胶鞋二车间一台规格为Φ1.7米×4米的硫化罐在使用过程中,由于当班负责人违章指挥、操作工误操作发生爆炸;3名临时工死亡,伤8人; 1977年6月2日14时35分,某炼油厂研究所中型工厂用汽油清洗地面,遇明火发生汽油爆炸事故,死亡14人,轻重伤4 0人; 1999年7月30日上午7时40分,江苏省靖江市磷肥厂四氧胺车间工人用锤子锤打设备,敲击产生的火星引爆了混合气体发生爆炸,500平方米的车间被炸塌,重伤3人,其中1人因抢救无效而死亡; 1991年10月8日6时50分,某化工厂中试室操作人员违反了加料操作工艺,同时没有按规定调好安全阀的起跳压力,也没有按规定定好爆破片压力;一台生产高分子聚醚的100升高压反应釜由于超温超压突然发生爆炸,三名操作人员当场被炸死;1993年10月21日下午3点,金陵石化炼油厂油品分厂操作工在进行1000 0ms汽油罐出循环调合时,误开阀门,造成汽油罐浮顶被顶破;汽油大量外冒,油蒸气遇明火爆炸燃烧,燃烧面积达;江苏、上海、安徽三省市12个城市共动用了187辆消防车,军警民6000余人联合作战,经过17小时的扑救,大火于次日上午11时15分被扑灭,2人死亡; 1996年7月,某有机化工厂乌洛托品车间进行粗甲醇直接加工甲醛的技术改造;7月30日15时30分左右,在进行焊接作业时,因没有与甲醇计量槽完全隔绝,电火花掉落在进料管敞口处,引燃了甲醇计量槽内的爆炸物;两名焊工当场因爆炸、灼烧致死,在场另有5人受伤、6人死亡;在救火过程,因泡沫灭火器底部锈蚀严重而发生爆炸,有1人致死; 2001年9月6日下午2时02分,茂名石化公司北山岭油库工人对阀室的管线进行检修时,不小心引燃了地上的残油,导致油库的油泵房突然起火,造成茂名市自1976年以来所发生的最大的同类型火灾;该油库内共有12个大油罐,原油总储油量60万吨;共出动29台消防车、近200名消防官兵;于下午4时30分左右,基本控制了火势;5时50分左右,大火被彻底扑灭;火灾发生后,周围约二万居民需紧急疏散、学校全部停课; 1997年5月4日9时许,长寿化工总厂工程公司安装队在污水处理车间进行乙醛污水配管的扫尾工作;当时该厂氯丁橡胶生产线正在开车,安装队未采取任何防范措施盲目动焊,11时30分引发火灾;扑救过程中,一号调节池发生爆炸,参加灭火的7名厂专职消防人员和5名污水车间职工牺牲,6人受轻伤; 江苏省盐城市射阳县盐城氟源化工有限公司是2002年盐城氟都化工有限公司与德国CCI公司成立的中外合资企业,2006年7月28日,由于企业违章指挥,违规操作,现场管理混乱,边施工、边试生产;操作工人操作错误导致氯化反应塔发生爆炸;死亡22人,受伤29人,其中3人重伤;据估算,氯化反应塔物料的爆炸当量相当于406千克梯恩梯T NT,爆炸半径约为30米; 2006年7月27日7时57分,中外合资上海远大过氧化物有限公司四万吨/年双氧水生产装置在试生产过程中因操作不当发生爆炸并引起燃烧事故造成4人受伤;7时59分消防部门接警后迅速出动,赶赴现场控制火情,火灾于9时50分被扑灭; 2006年8月7日下午3时许,天津宜坤精细化工科技开发有限公司硝化车间反应釜发生爆炸事故并引起火灾,一小时后火被及时扑灭;事故造成9人死亡,3人受伤;据报道,是由于操作不当引起事故的发生; 2002年12月14日,张家口市宣化钢铁公司焦化厂值班人员在将液态萘冷却为固态萘的过程中,发生误操作,造成液态萘温度升高自燃,引起火灾;当时火势非常凶猛,火苗窜至几十米高,在约600平方米的厂区内迅速蔓延开来,厂房的房顶已被大火吞噬,墙体倾斜;而且该厂堆放的十几吨固体萘、煤气管及沥青反应堆也已燃烧; 1988年4月21日15时35分,吉林省辽源市石油化工厂环氧化物工段皂化岗位1名女工操作中严重违反操作规程,大量氮气进人三塔釜残罐,造成此罐超压罐为非压力容器发生开裂,罐内环氧丙烷、环氧乙烷喷出时摩擦起火造成爆炸,并引起大火,事故的直接责任者当场死亡, 2004年9月,德克萨斯城炼油厂几名工人在没有进行减压处理的情况下试图打开一个热水管道的阀门,结果过热蒸汽大量涌出,导致2名工人死亡,1人严重烫伤; 2003年9月12日,锦州石化公司300万吨/年常减压装置检修后进行开车,17:10分在减压炉点火时,因违反规定,管理混乱而发生闪爆事故;事故造成3人死亡、1人重伤、5人轻伤的严重后果; 2004年12月3 0日14时20分左右,吉化化肥厂合成气车间气化工段由于当班操作工严重违章,没有认真监盘,填写“假记录”,操作失控,导致过氧及炉温持续升高,在终洗塔后部形成氧气积聚,与合成气中的高浓度氢气及一氧化碳混合,形成爆炸混合物,发生爆炸; 3、设备损坏动设备或静设备或因其质量不符合工艺生产要求造成设备损坏,或在长期使用过程中由于磨损或腐蚀造成设备损坏,都可引起继发的火灾爆炸等事故设备质量有问题,可能是制造时产生的,也可能是设计有问题;因此,我们国家对承压静设备的设计制造有严格的规定,只有具有相应资质的设计单位和制造单位才能进行设计或制造;所有承压设备,如耐压容器、锅炉等必须经过国家监管部门检测合格发放使用证以后才能投用; 在一些企业中,对设备的质量问题十分重视;对于所有新建设的动设备,在安装以前都要进行解体;即拆开来进行彻底检查,并更换密封垫片;多年实际工作证明,在进行设备的解体时经常发现设备内有异物、有砂眼、用材不当、安装错误、缺少部件等等不可忽视的问题进口设备照样出问题,需要逐一解决,以消除安全隐患; 在石油、化工行业中,由于设备出问题而引发的事故,在事故总数中所占比例也很大; 某企业常减压装置,因一接头损坏,造成瓦斯泄露,引发大火;这既是因设备损坏引起的事故,也是操作工未及时进行巡回检查而引起的事故,但也有一些偶然性;某企业的一台高压泵,在泵体有一个暗砂眼,在解体检查时没有发现;运转一段时间后,高温油料从砂眼哧出,引起大火; 某厂原油罐的蒸汽加热盘管破裂,造成原油罐突沸外溢而着火,直到把原油烧光为止; 1979年12月18日,吉林市煤气公司1台400立方米液化气球罐开裂,76秒钟内扩散至40万平方米;在200米处遇火源发生爆炸,造成3 6人死亡、58人受伤的惨剧;这个事故是由于液化气球罐的罐体焊接质量不良引起的,为此,进行了一次全国范围的液化气球罐大检查,不少液化气球罐停用; 1998年3月516时30分,西安市煤气公司液化气一个400立方米球罐根部的球阀损害液化气外泄;18时40分发生闪爆;后又在一个小时内发生两次闪爆,导致在现场进行抢险的四十多人伤亡,其中消防官兵牺牲7人、液化气站职工牺牲5人;爆炸并引燃百米之外的棉花垛;1989年,美国休斯顿一石化公司乙烯管线破裂,发生乙烯泄漏;共泄漏吨,遇明火后发生了相当于级地震的爆炸;死亡33人、伤130人,损失亿美元;2006年12月9日早上6时21分,灯塔市辽阳华兴化学品有限公司导热油锅炉车间存有1. 5吨导热油的3号炉发生泄漏,泄漏出来的290多度的导热油遇到空气后猛烈燃烧;经过数十名消防队员奋力将火扑灭,避免了一场爆炸事故;某企业规定,每三年对设备进行一次大规模检修;2007年3月9日,在距规定的检修时间还差6天时,常减压蒸馏装置的原油和轻油换热器阀门因密封垫老化于8时25分发生泄漏,高温高压油品喷出,引发火灾,着火面积约200平方米;最近,有两个企业的新建装置在开车过程中均因管道密封破损,热油泄漏,引起火灾;这两个企业的建设项目均是由工程公司总承包建设的,工程公司毕竟不是业主,责任心及经济利益都可能影响工程质量;2007年5月29日晚7时57分,延川县永坪炼油厂Ⅱ套催化装置换热器法兰发生泄漏,造成着火事故,一人死亡,一人受伤;2007年6月11日晚8时38分许,位于宜昌市开发区的宜化股份公司尿素事业部合成氨生产线发生爆炸;爆炸原因初步确定为该公司合成氨1号、2号系统合成工段热交换器顶部发生煤气泄漏,泄漏的高压气体与周围空气和阀门等产生摩擦导致空间爆炸,引发燃烧;茂名石化和沧州炼油厂两个企业,都发生过延迟焦化装置因高温重油管线用错材质,造成腐蚀泄漏,引发大火的事故;2002年2月23日,农历正月十二, 辽阳石化聚乙烯新线开车;7时20分,新线发生了剧烈爆炸;结果造成8人死亡,1人重伤,18人轻伤;整个“”事故调查前后历经半年的时间,而事故善后工作一直持续到2006年;经过深入的事故调查取证分析,认定这起事故发生的直接原因是一块不合格的玻璃视镜在开车过程中破裂,导致大量的乙烯气体瞬间喷出,又被引风机吸入沸腾床干燥器内,与聚乙烯粉末、热空气形成的爆炸混合物达到爆炸极限,被静电火花引爆,发生了爆炸; 2006年6月28日,兰州石化公司炼油厂第二套催化裂化装置中的40万吨气体分馏装置因507换热器盖头介质为液态烃发生泄漏引起火灾爆炸事故,并且引燃旁边的1个25立方米的液化气贮罐;造成1名消防队员壮烈牺牲、10名队员受伤; 4、自动控制系统失误引发的事故此处拟举一个钢铁行业的例子;2006年10月30日20时,重庆钢铁公司在煤气管网上进行焊接施工;由于电焊机的接地线直接搭接在管网上,而煤气管网上的压力测试仪表的抗干扰能力不强;电焊机的强电磁干扰了煤气压力测试仪表,误报出系统压力超高的信号;致使自动控制仪表按系统压力超高进行了自动动作,将煤气紧急快开阀门打开,造成煤气泄漏大约1万1千立方米的重大事故5、由于管理不善、违章指挥而造成的事故此类事故易发生在建设过程和装置检修过程中,在投产后也发生过; 如某厂一装置发生波动,操作工正在处理;按规定管生产的副厂长只应是一个指挥者,不能自己动手,但这个副厂长觉得自己干过这个岗位的操作,十分熟悉情况;来到现场后看了看,未跟当班操作工打招呼,就自行启动了核心设备,导致该设备报废; 某厂在道路施工时,施工机械挖坏地下电缆,造成大面积停电;事故发生的原因是,电力管理部门和施工部门衔接不够而引起的; 吉林石化松花江污染事件,原本是操作人员违规操作而引起的一起爆炸事故,但因没有设立必要的水体防护设施,也没有制定相应的应急处理预案,导致松花江被污染的严重事件; 1974年8月21日,北京石油化工总厂所属的向阳化工厂,苯酚丙酮车间氧化岗位321贮罐发生爆炸事故,造成死亡职工13人,伤22人;在这次爆炸事故前,321贮罐曾经发生过几次事故,被迫停过产;但是均没有引起该厂领导的高度重视,没有采取相应的防范措施,以致酿成了这次重大爆炸事故; 2006年8月7日,天津一化工厂发生爆炸,车间被夷为平地;据新华社报道,爆炸至少造成7人死亡,3人受伤,2人下落不明;据称,此次爆炸可能是由于生产车间内的酒精和香精管理不善造成的; 2006年7月30日上午,安徽滁州来安县县城西面的金邦医药化工有限公司甲醇钠生产车间因原料金属钠保管不善发生火灾,几百个平方的厂房燃起熊熊大火,浓烟遮蔽了附近方圆几公里的天空;由于甲醇钠易燃,且遇水分解成甲醇和剧毒的氢氧化钠,来安县城被迫疏散了七八千群众;最后在从南京、合肥、蚌埠、马鞍山等地驰援的消防官兵的奋力扑救下,历经7小时才将火势扑灭; 2001年9月21日法国南方城市图鲁兹AZF化工厂发生爆炸,据外电报道是由工厂库存的200吨到300吨硝酸铵管理不善造成的;据24日的最新统计,死亡人员上升到29人,受伤人员总数2442人,其中留住医院治疗782人;爆炸毁坏住房约2万套,毁坏小学、幼儿园69所,其中3所学校完全被毁,1万名儿童近期将无处上学;毁坏中学18所,毁坏大学2所,同时受损的还有体育场馆3座,剧院1座,音乐厅2座,医院1所,商店数千家,其中3家大型商场完全被毁;此外,位于图鲁兹南部工业区的所有企业都受到程度不同的破坏,占全市公交车辆总数四分之一约100辆公交车受损;这起法国历史上“罕见”的大爆炸,给当地居民带来了极大恐慌和心理压力; 6、静电某厂在给一汽车装汽油时,因产生静电引发爆炸; 某厂一台轻汽油罐,内壁防腐涂料导电不良,与内浮盘的橡胶密封圈因摩擦产生静电,引起内浮盘上的油气起火爆炸;7、雷击1989年8月12日黄岛油库因库内钢筋混凝土罐遭受雷击,发生特大火灾爆炸事故;大火燃烧了104个小时才完全扑灭,烧掉原油36000吨,烧毁油罐5座, 65人受伤,14名消防干警和5名油库职工牺牲;来不及撤退的8辆消防车、l 辆指挥车全都葬身火海;共疏散了1800多户、l万余人,烧毁民房4000多平方米,毁坏路面2万平方米;这场大火燃烧的高温、水域的污染、爆炸的震动,使万尾名贵的黑鱼、近3000只水貂死亡,5200亩虾池、1160亩贻贝、万亩滩涂上成亿尾鱼苗死亡; 在燃烧、爆炸中,外溢流人胶州湾水面的原油估计有600多吨,黄岛四周的102公里的海岸线受到严重污染;黑乎乎的原油还扩散到青岛市区沿岸;由于钢筋混凝土罐,既容易积聚静电,又易遭受雷击;而且当发生火灾时,对钢筋混凝土罐难以进行冷却,也无法判断罐内液面高低;此次事故发生后,全国范围内开始将混凝土罐、砖罐全部更换为钢罐,以免此类事故的发生;武汉市黄陂县石油总公司横店石油储库1998年7月13日下午4时10分遭直击雷击,造成库区4号储罐起火爆炸,烧毁0号柴油125t及1000m3柴油罐一座;美国当地时间,2007年4月27日中午,俄克拉荷马州温尼伍德炼油厂因雷击中一个轻油罐引发大火爆炸,大火蔓延到柴油罐;因柴油没有烧光,一直到29日晨大火仍未扑灭;在多雷地区,因雷击而停车停工的事故每年都有发生;8、其它因素南方某企业的电力电缆,被老鼠咬坏,引起电缆爆炸,造成大面积停电;2004年2月18日,一辆载满硫磺、汽油和化肥的火车在伊朗东北部发生出轨和爆炸事件,295人死亡、350人受伤;剧烈的爆炸将铁路沿线的五座村庄几乎夷为平地;在距离爆炸地点10公里处,几乎所有房屋的玻璃窗都被震碎,而在距离爆炸地点70公里的地方也能感觉到明显的震动;据报道,是由于附近发生了一次级地震颠覆了列车,引发易燃货物的燃烧爆炸; 9、不明原因有一些事故发生后一直未能找到其原因;如60年代末,大庆石化厂我国第一套自行设计自行建设的高压加氢装置发生爆炸,死亡数十人;当时是先发生了一个小事故,从厂长、总工程师、技术科干部到车间干部数十人全都到现场处理事故,结果发生了第二次爆炸,使现场人员全部死亡;由于参与第一次爆炸原因调查的人员全部死亡,再加之正处在文化大革命时期,一切源于阶级斗争致力于抓内外阶级敌人,致使后来对事故发生的直接原因没有明确的结论; 1973年,石油化工科学研究院发生爆炸死亡一人,后来发现是一个高压氮气瓶发生了爆炸;很多单位都参与了调查,但未能找出引发事故的直接原因; 10、人为破坏2004年4月24日22时许,中国石油化工股份有限公司山西运城石油分公司半坡油库甲区6号大型储油罐发生特大火灾,造成直接经济损失325万元;根据公安部调查结果,是油库职工在值班期间相互勾结,从油库的计量孔往外倒油引发静电起火导致火灾;。
石油化工企业火灾爆炸原因及防范对策

(2)爆裂管线介质为高温蜡油,硫含量3.4%左右(最大值达到4.4%),属于典型高温硫腐蚀环境。
此管线已运行9年,未按照《中国石化加工高含硫原油企业设备及管道测厚管理规定》(中国石化炼〔2011〕618号)进行在线定点测厚,未能及时发现管线腐蚀减薄。
1.3 荆门石化2·8火灾事故2019年2月8日0时50分,荆门石化炼油二部二区S Zorb 装置反应器收集器(D-105)出口法兰垫片失效,催化剂和油气(温度:380~400℃,压力:2.6MPa)泄漏着火。
2时10分,明火被扑灭,未造成人员伤亡。
事故暴露出的主要问题有:(1)事故后检查发现,S Zorb 反应器收集器松动氢气喷嘴与设备轴线不同心,偏移达7mm, 超过设计允许偏差(±1.5mm);下游法兰垫片密封石墨被偏移的气流冲刷,造成失效泄漏;对夹式法兰在泄漏着火后,螺栓膨胀,加大了泄漏;(2)泄漏部位采用平面对夹式法兰,该结构在此工作条件下,密封可靠性差;(3) S Zorb 反应器收集器平台区域高温密封点多,操作频繁(每30min 放料一次),为易泄漏区,容易发生火灾,但该区域没有设计火灾及可燃气体报警器。
视频监控存在盲点,不能及时发现泄漏异常。
1.4 齐鲁石化6·9闪爆事故2020年6月9日,齐鲁石化改制单位一齐商建设公司在烯烃厂石脑油罐区一台1万立方米石脑油储销项部进行外壁防腐刷漆作业时,储罐突然发生闪爆,西侧罐顶与罐体连接处被撕裂掀开,火焰冒出。
2人被烧伤,抢救无效死亡。
事故暴露出的主要问题有:(1)特殊作业管控流于形式①临时用电作业许可证(NO:0008805)中明确“在防爆场所使用的临时电源,电气元件和线路达到防爆等级要求”并要有专业电工进行确认,但电工未进行确认,现场也未落实防爆要求;②动火作业可燃气体分析流于形式,只在地面上进行了环0 引言随着我国经济的快速发展,石油化工企业在国民生产和社会发展中占有越来重要的地位。
- 1、下载文档前请自行甄别文档内容的完整性,平台不提供额外的编辑、内容补充、找答案等附加服务。
- 2、"仅部分预览"的文档,不可在线预览部分如存在完整性等问题,可反馈申请退款(可完整预览的文档不适用该条件!)。
- 3、如文档侵犯您的权益,请联系客服反馈,我们会尽快为您处理(人工客服工作时间:9:00-18:30)。
编号:SM-ZD-26608石油、化工企业火灾爆炸事故案例及其引发原因Organize enterprise safety management planning, guidance, inspection and decision-making, ensure the safety status, and unify the overall plan objectives编制:____________________审核:____________________时间:____________________本文档下载后可任意修改石油、化工企业火灾爆炸事故案例及其引发原因简介:该安全管理资料适用于安全管理工作中组织实施企业安全管理规划、指导、检查和决策等事项,保证生产中的人、物、环境因素处于最佳安全状态,从而使整体计划目标统一,行动协调,过程有条不紊。
文档可直接下载或修改,使用时请详细阅读内容。
·这里只列举部分发生在国内外石油、化工企业的已发事故(限定在生产作业期间及生产作业准备阶段发生的事故)以及个别未遂事故,并对事故发生的直接原因进行粗略划分。
这里只列举部分发生在国内外石油、化工企业的已发事故(限定在生产作业期间及生产作业准备阶段发生的事故)以及个别未遂事故,并对事故发生的直接原因进行粗略划分。
1、工程设计失误1)、设计单位对设计任务认识不深某沿海企业在海边建设油罐,设计单位因无经验在设计中未对罐底外壁采取防腐措施。
由于地处海边,化学腐蚀现象严重,若不对罐底外壁采取防腐措施,则油罐建成后罐底将很快被腐蚀穿透,不仅油罐将报废,若油品大量漏失,还会引发严重的次生事故(如火灾、爆炸、环境污染等等)。
建设单位在最后一次审查时发现了这个问题,并予以纠正。
某厂在建设一套采用了新技术的装置时,由于企业技术人员没有搞清新技术到底新在什么地方,向设计单位提供了过时的物料数据(对于老技术来说,这些数据仍然可用),设计单位也没有进行认真审查。
装置建成投产后,核心设备每天都处在超温工况下工作。
不到一年就将该核心设备烧坏,只好再花5000多万元进行改造。
辽阳石聚乙烯新线工艺是按老线工艺照搬过来的,而多处设计错误是导致20xx年2月23日发生爆炸的直接原因。
A、设计单位擅自将悬浮液接收罐的安全阀开启压力从0.3 MPa,改为0.58 MPa。
视镜是在0.5 MPa时破裂后引发爆炸事故的。
如果设计不改变新线安全阀的起跳压力视镜很可能不会破碎,爆炸事故也就不会发生。
B、原化学工业部《压力容器视镜》设计要求规定:视镜最大直径为150mm,最大公称压力为0.8 MPa。
而设计部门违反规定擅自选择直径为200mm,公称压力为2.5 MPa非标视镜,这种视镜目前国内尚无法生产。
C、厂房是封闭的,这也不符合国家的规范要求;d、将沸腾床引风机的入口设置在聚合釜的上方,设计上也是错误的。
2)、工艺过程设计不合理1982年、1993年,分属两个企业的两套催化裂化装置的中间罐先后于发生了爆炸,1993年1月1日的那次爆炸还引发大火。
两次事故相隔近10年,且分别是两个设计单位作的设计。
但这两个设计单位都没有处理好中间罐的工艺设计,都存在若阀门关不严,不同性质物料发生串通的可能性。
结果,由于阀门关不严,造成不同性质物料的相互混合,致使中间罐压力急剧升高而发生爆炸。
某合成氨装置,设计时在原料天然气管线与压缩空气管线之间设计了一个连通阀,导致天然气窜入空气管线中,发生爆炸。
3)、总图布置设计不合理有一个企业把乙烯装置的紧急放空口设在空分装置的上风位置,结果在乙烯装置紧急放空时,空分装置将从乙烯装置放出的烃分子吸入。
经压缩后烃和纯氧在空分装置内相遇,发生剧烈氧化而爆炸。
造成3人死亡、31人受伤,其中1人是被飞出200米外的一块钢板砸死。
2、由于操作人员的违规操作或各种原因造成的误操作在化工生产中,由于人员的违章作业、违章指挥、违反劳动纪律而发生的各类事故所占比率很高。
据有关统计,在已经发生的各类事故中,由于人员“三违”引发的占到75%左右。
其中,仅因操作工开错阀门或没有及时关闭阀门而引发的事故就有多起,并都造成了很大影响。
而这些由“三违”引发的事故,多数表现为设备的破坏。
以设备破坏为表面现象的事故,大约也占到了70%以上。
20xx年12月5日抚顺市液化气公司因为操作工没有及时关闭放水阀门,致使49吨液化气泄漏,周围地区就象笼罩在大雾中一样。
抚顺市紧急采取措施疏散人员,并将该地区隔离才没有引发更大的事故。
1997年6月27日,北京东方化工厂罐区,在收油时操作工开错阀门,致使石脑油大量外溢,遇明火引发爆炸及两次后续爆炸。
此次事故共有9人死亡、39人受伤,直接损失1.17亿元人民币,造成该厂几乎全部主要装置停产10个月。
1988年高桥石化的液化气罐区,因为操作工没有及时关闭切水阀门,致使液化气大量泄漏。
泄漏出的液化气沿管沟流到工厂外的民工居住地,遇明火引发爆炸,造成多名人员伤亡。
约十年前,荆门石化原油罐区连续两年跑损原油事故,其中一次是也是由于因为操作工没有及时关闭放水阀门,致使原油大量泄漏,并污染了下游水库。
某企业一套装置在开车过程中,操作工点炉子,违反操作规程,在没有进行炉膛气体成分的分析之前,就去点火,结果引起炉膛爆炸。
某企业一套装置,泵出口因物料结焦而堵塞,为赶生产任务,没有将装置内的油全部退出,也没有切断检修部位与系统的连接,就开始检修,结果把焦捅掉后热油冒出把检修工烫死了。
东北某厂酸性水系统进行防冻排液操作,操作工打开切水阀门后忘记关阀门,导致硫化氢气体沿地沟流进操作工休息间,4人死亡。
某化肥厂包装机发生故障停车,操作工正在处理。
班长未和操作工打招呼就进入机器内查看,操作工处理完后立即开机,结果将班长挤死在包装机内。
1973年10月23日18时13分,江苏某化肥厂造气车间造气工段由于操作工操作失误,,加之安全阀、压力表失灵,造成煤气发生炉夹套内满水、超压破裂,夹套内的水进入煤气发生炉内,造成炉体爆炸,当场炸死3人。
1989年2月17日14时38分,江西省鹰潭市某橡胶厂,胶鞋二车间一台规格为Φ1.7米×4米的硫化罐在使用过程中,由于当班负责人违章指挥、操作工误操作发生爆炸。
3名临时工死亡,伤8人。
1977年6月2日14时35分,某炼油厂研究所中型工厂用汽油清洗地面,遇明火发生汽油爆炸事故,死亡14人,轻重伤40人。
1999年7月30日上午7时40分,江苏省靖江市磷肥厂四氧胺车间工人用锤子锤打设备,敲击产生的火星引爆了混合气体发生爆炸,500平方米的车间被炸塌,重伤3人,其中1人因抢救无效而死亡。
1991年10月8日6时50分,某化工厂中试室操作人员违反了加料操作工艺,同时没有按规定调好安全阀的起跳压力,也没有按规定定好爆破片压力。
一台生产高分子聚醚的100升高压反应釜由于超温超压突然发生爆炸,三名操作人员当场被炸死。
1993年10月21日下午3点,金陵石化炼油厂油品分厂操作工在进行10000ms汽油罐出循环调合时,误开阀门,造成汽油罐浮顶被顶破。
汽油大量外冒,油蒸气遇明火爆炸燃烧,燃烧面积达23437.5m。
江苏、上海、安徽三省市12个城市共动用了187辆消防车,军警民6000余人联合作战,经过17小时的扑救,大火于次日上午11时15分被扑灭,2人死亡。
1996年7月,某有机化工厂乌洛托品车间进行粗甲醇直接加工甲醛的技术改造。
7月30日15时30分左右,在进行焊接作业时,因没有与甲醇计量槽完全隔绝,电火花掉落在进料管敞口处,引燃了甲醇计量槽内的爆炸物。
两名焊工当场因爆炸、灼烧致死,在场另有5人受伤、6人死亡。
在救火过程,因泡沫灭火器底部锈蚀严重而发生爆炸,有1人致死。
20xx年9月6日下午2时02分,茂名石化公司北山岭油库工人对阀室的管线进行检修时,不小心引燃了地上的残油,导致油库的油泵房突然起火,造成茂名市自1976年以来所发生的最大的同类型火灾。
该油库内共有12个大油罐,原油总储油量60万吨。
共出动29台消防车、近200名消防官兵。
于下午4时30分左右,基本控制了火势;5时50分左右,大火被彻底扑灭。
火灾发生后,周围约二万居民需紧急疏散、学校全部停课。
1997年5月4日9时许,长寿化工总厂工程公司安装队在污水处理车间进行乙醛污水配管的扫尾工作。
当时该厂氯丁橡胶生产线正在开车,安装队未采取任何防范措施盲目动焊,11时30分引发火灾。
扑救过程中,一号调节池发生爆炸,参加灭火的7名厂专职消防人员和5名污水车间职工牺牲,6人受轻伤。
江苏省盐城市射阳县盐城氟源化工有限公司是20xx年盐城氟都化工有限公司与德国CCI公司成立的中外合资企业,20xx年7月28日,由于企业违章指挥,违规操作,现场管理混乱,边施工、边试生产。
操作工人操作错误导致氯化反应塔发生爆炸。
死亡22人,受伤29人,其中3人重伤。
据估算,氯化反应塔物料的爆炸当量相当于406千克梯恩梯(TNT),爆炸半径约为30米。
20xx年7月27日7时57分,中外合资上海远大过氧化物有限公司四万吨/年双氧水生产装置在试生产过程中因操作不当发生爆炸并引起燃烧事故造成4人受伤。
7时59分消防部门接警后迅速出动,赶赴现场控制火情,火灾于9时50分被扑灭。
20xx年8月7日下午3时许,天津宜坤精细化工科技开发有限公司硝化车间反应釜发生爆炸事故并引起火灾,一小时后火被及时扑灭。
事故造成9人死亡,3人受伤。
据报道,是由于操作不当引起事故的发生。
20xx年12月14日,张家口市宣化钢铁公司焦化厂值班人员在将液态萘冷却为固态萘的过程中,发生误操作,造成液态萘温度升高自燃,引起火灾。
当时火势非常凶猛,火苗窜至几十米高,在约600平方米的厂区内迅速蔓延开来,厂房的房顶已被大火吞噬,墙体倾斜。
而且该厂堆放的十几吨固体萘、煤气管及沥青反应堆也已燃烧。
1988年4月21日15时35分,吉林省辽源市石油化工厂环氧化物工段皂化岗位1名女工操作中严重违反操作规程,大量氮气进人三塔釜残罐,造成此罐超压(罐为非压力容器)发生开裂,罐内环氧丙烷、环氧乙烷喷出时摩擦起火造成爆炸,并引起大火,事故的直接责任者当场死亡,20xx年9月,德克萨斯城炼油厂几名工人在没有进行减压处理的情况下试图打开一个热水管道的阀门,结果过热蒸汽大量涌出,导致2名工人死亡,1人严重烫伤。
20xx年9月12日,锦州石化公司300万吨/年常减压装置检修后进行开车,17:10分在减压炉点火时,因违反规定,管理混乱而发生闪爆事故。
事故造成3人死亡、1人重伤、5人轻伤的严重后果。
20xx年12月30日14时20分左右,吉化化肥厂合成气车间气化工段由于当班操作工严重违章,没有认真监盘,填写“假记录”,操作失控,导致过氧及炉温持续升高,在终洗塔后部形成氧气积聚,与合成气中的高浓度氢气及一氧化碳混合,形成爆炸混合物,发生爆炸。