最大扭矩及满功率切削试验检查表
金属切削机床铣削加工安全检查表范本(三篇)

金属切削机床铣削加工安全检查表范本1. 检查机床外观及电源线:- 检查机床外部是否有明显损坏或松动的部件;- 检查电源线是否完好,并确认接地是否良好。
2. 检查操作面板:- 检查操作面板上的按钮、开关是否正常;- 确认操作面板上的指示灯能正常显示。
3. 检查刀具和刀具夹持装置:- 检查刀具是否完整、锋利;- 检查刀具夹持装置是否紧固可靠;- 若使用自动刀具夹持装置,确认其正常运行。
4. 检查切削液系统:- 确认切削液系统的管路是否完好;- 检查切削液箱内切削液的余量,并添加足够的切削液;- 若使用切削液回收系统,检查其工作是否正常。
5. 检查切削区域安全防护:- 确认切削区域周围是否有足够的防护栏杆;- 检查防护门、防护罩是否完好,并确认其能正常开启和关闭;- 检查加工过程中的切屑排放装置是否畅通。
6. 检查机床运行状态:- 启动机床,观察其运行是否平稳,无异常噪音和振动;- 检查机床各轴的运动是否灵活、准确。
7. 检查冷却系统:- 检查冷却水管路是否完好;- 检查冷却液箱内冷却液的余量,并添加足够的冷却液;- 检查冷却系统的温度和压力是否在正常范围内。
8. 检查机床润滑系统:- 确认润滑油箱内润滑油的余量,并添加足够的润滑油;- 检查润滑系统管路是否完好;- 检查润滑系统的工作是否正常,无异常的润滑点。
9. 检查电气系统:- 检查电气线路是否完好,无短路或接触不良;- 检查电气设备的接地是否良好;- 若使用变频器进行控制,检查其工作是否正常。
10. 检查运输锁定装置:- 检查运输锁定装置是否已全部解除。
11. 检查紧固件:- 检查机床上的紧固件是否全部紧固可靠。
12. 检查安全标识:- 检查机床上的安全标识是否清晰可见;- 确认操作人员是否了解并遵守相应的安全规范。
以上为金属切削机床铣削加工安全检查表范本,详细检查内容,请根据具体机床的型号和使用情况进行相应的调整和补充。
请在使用任何机床之前,先进行安全检查,确保操作人员的安全。
金属切削机床/车削加工安全检查表(最新版)

( 安全管理 )单位:_________________________姓名:_________________________日期:_________________________精品文档 / Word文档 / 文字可改金属切削机床/车削加工安全检查表(最新版)Safety management is an important part of production management. Safety and production are inthe implementation process金属切削机床/车削加工安全检查表(最新版)车削加工安全检查表说明1)车床就是利用车刀对工件进行车削加工的设备。
2)车削加工的不安全因素主要来自两个方面:一是工件及其夹紧装置的旋转;二是车床在切屑钢件时产生的切屑富有韧性,边缘比较锋利、温度较高,高速切削会形成较长的带状切屑。
3)车床事故的发生就是由于上述物的不安全因素和操作者的不安全行为同时发生所致。
4)普通车床安全检验表适用C620型、C630型、CA6140型等普通车床,其他普通车床,包括鞍马车床等亦可参照执行。
5)立式车床安全检查表适用于C512A、C516A型单柱式车床及与之类似的立式车床和C523型、C534J1型等双柱式车床及与之类似的立式车床。
6)铲齿车床安全检查表适用于C8955型铲齿车床及类似的铲齿车床。
(1)普通车床安全检查表1.设备检查1.1机床上应设局部照明,机床上的照明灯应采用安全电压供电,照明变压器应有接地(零)保护。
1.2摩擦离合器应能控制主轴的转动并起过载保护作用。
1.3脱落蜗杆机构应起走刀过载保护作用。
1.4在设置行程档块时,脱落蜗杆机构应能在行程档块的作用下起行程控制作用。
1.5溜板箱内如设置非脱落蜗杆式过载行程控制机构,如齿形离合器安全机构、摩擦离合器安全机构等,亦应起过载保护及行程控制作用。
1.6溜板箱内设置的互锁机构应能防止丝杆、光杆同时传动。
机械设计结果检查表(更新)

机械设计结果检查表(更新)机械设计结果检查表一、规划1.是否真的有制作意义,目标是否切实可行2.技术规格(性能、大小、重量等)是否满足要求3.制作费用、制作期限是否合适二、功能1.是否可实现目标所设定的功能2.必要的功能是否都考虑到了3.是否考虑了机械要求的动力源、信息源、信号线和控机器等装配问题三、机构、结构1.机构与结构是否满足功能要求2.是否采用了最合适的机构3.是否采用了最简单的机构和结构4.力的作用线是否形成封闭回路5.平衡性是否良好,结构是否美观6.力线作用回路上,结构尺寸是否与作用力大小成比例7.轴的回转方向以及手柄、衬套的动作及方向是否正确,是否明确做了图示8.空气、油液的流动方向是否正确,是否做了图示标注9.是否考虑了振动的问题(是否避开了共振店,对振动系统相应的部分是否已加以固定)10.对高速回转部分的考虑是否周到全面(因噪声、离心应力、油的搅拌等产生的损耗和发热)11.对于平面度的不良部位的安装,是否讨论采用3点式安装法12.对负荷问题是否不仅从驱动侧方面做了考虑,而且也对零件的重力及惯性力方面的影响做了研究、考虑13.对装配、配管是否采用了合适的固定四、与外部环境的关系1.能否抵抗外部条件的影响2.是否对高温、低温、沙尘、腐蚀性、振动等做了考虑3.是否考虑了伴随温度的变化而产生长度变化和间隙减少4.对大气条件下的滑动部、调整螺旋部等的生锈问题是否有所考虑5.是否有因积水而产生冻结破裂的危险性6.对周围的影响是否允许(振动、噪音、发热)7.是否安置在能够利用的空间之内8.移动及动作时,与周围是否有干涉现象9.所利用的设备(水、空气、电力)是否可及时满足要求10.对安全、防灾等是否做了周密的考虑五、形状1.形状是否满足功能要求2.是否采用了最简单的形状3.其形状是否具有加工的可能性4.其形状是否便于组装及拆卸5.零件的形状、孔形状、凹部形状是否合乎规范6.是否为适应操作的最佳形状六、强度1.是否保证了静力学强度和疲劳强度2.弯曲变形是否没有问题3.带有电动机等强制振动要素的机械,其机械的固有振动频率是否高于强制振动频率4.力线作用回路上,结构尺寸是否与作用力大小成比例七、尺寸1.尺寸有否遗漏2.是否有重复的尺寸3.其尺寸是否可行(要考虑到加工性)4.对倒角C及圆弧过渡R是否做了指定5.是否检查了C、R处的配合零件的相应尺寸6.是否尽可能采用整数尺寸7.配合的指定是否合适8.(与相关零件的)关联尺寸对否合适9.是否已采用制图法对关联零部件的相互关系进行了检查(间隙、关涉、机罩的开闭、检查,加润滑油、调整等)10.是否正确计入了用于固定、搬运时的尺寸11.是否计入了可动部分的行程(动作范围)12.锐角、棱边、形状复杂、厚度变化大的零件,由于淬火等易产生局部应力集中及裂痕,为了防止出现这种现象是否对过渡圆弧的大小做了考虑13.尺寸的计入方法是否合适(考虑累计误差)14.累计尺寸是否无误15.是否标出了整体尺寸16.是否正确表示了占用空间的大小17.是否考虑了公差(尺寸的允许误差)18.是否有不必要过严公差要求(并包含配合公差)19.对表面粗糙度是否做了指定20.表面粗糙度是否合适,是否有要求过严现象21.是否考虑了形位公差(平行度、垂直度、圆柱度等)22.公差是否合乎制作误差及组装误差要求23.是否考虑了加工基准面八、重量1.重量是否满足基本性能要求2.零件的重量是否限制在适合搬运的20kg以下3.20kg以上的零件是否配置了吊装结构九、材料1.机械性质(拉伸强度、刚性、硬度、比重)是否合适2.温度变化时,是否也能充分满足强度要求3.是否不至于因温度变化而产生热膨胀4.加工性能(切削性、焊接性、延伸性)是否没问题5.对有导电性、导热性要求的场合,是否给予了考虑6.有否足够的耐腐蚀性,不够时,是否指定了表面处理7.对钢铁材料是否考虑了热处理问题8.是否考虑了尽可能从库存品种选择材料9.没有库存品的场合,所选择的材料是否能采购到10.是否无意中指定了特殊材料(高价、无库存、加工性差)十、加工方法(一)钣金、焊接1.是否可以弯曲2.能否焊接3.焊接指定有否遗漏4.焊缝处是否对联结螺母等有干涉现象5.是否考虑了焊接变形6.是否考虑了钣金公差7.是否考虑了防止应力集中问题8.是否没超出钢板的规格范围9.是否考虑了钢板厚度的统一性,以及使用扁钢及型钢(二)切削加工1.机械加工是否可能2.是否考虑了用什么样的机械加工问题(用现有设备加工是否可能)(是否有未经验过的机械加工之处)3.是否考虑了刀具的形状及尺寸4.是否考虑了在凹处设置圆弧R的问题5.是否在凸处要设置倒角C6.精加工符号是否合适,记入有否遗漏7.精加工要求是否过于严格8.尺寸公差能否降低9.形位公差能否降低10.对滑动面、油密封及垫圈等部位是否采用了合适的表面粗糙度11.是否考虑了加工顺序12.加工是否可从同一方向进行13.尺寸的指示方法从加工方法、加工顺序的角度看是否合适14.有否夹紧余量15.是否考虑了加工基准面的问题(三)热处理1.材质是否合适2.对淬火的深度、硬度等是否做了指示3.是否指定了淬火范围(四)表面处理1.是否有必要进行电镀或涂漆2.对电镀,涂漆部位的指定是否合适3.是否注意到了生锈的问题4.采取了那些防锈措施十一、装配、拆卸1.是否能组装2.是否留有工具作业空间3.是否考虑工具作业范围4.拆卸是否可能(对静配合部分是否能拆卸)5.拆卸时,必须要更换的部件是否做了考虑6.油密封、防尘密封、O型圈等在组装与拆卸时,是否不至于损伤7.是否能从部件单元进行组装拆卸(对部件更换时的作业顺序、拆卸余量、拆卸空间是否做了考虑)8.是否考虑了组装调整的问题9.是否妥善处理了由于加工、组装等造成的累计误差问题10.是否可按零件号码的顺序进行组装11.是否能减少维修保养时的工具种类12.对维修作业上必要的仪器能否连接得上13.是否已用图示法对维修作业时的人体动作姿势进行了确认检查14.维修性是否良好十二、检查1.对指定的精度能否进行检查确认2.是否研究了使用什么样的检查器具的问题十三、搬运、安装1.是否考虑了放置场所2.是否考虑了怎样搬运3.是否考虑了门的宽度、通道、吊车、天棚的高度以及可用手拿起的重量等问题4.是否考虑了拆卸输送的场合下,对所有零件的搬运问题5.是否检查了产品和零件的包装及放置形式的问题6.重心的位置是否合适7.是否考虑了现场安装8.地面是否足以承受载荷十四、机械要素1.使用的机械要素是否满足设计性能要求2.是否考虑了机械要素的通用性问题(特别是弹簧、齿轮等)3.对购入零件的库存品有无及交货问题是否做了确认4.没有库存品的场合,实际上是否能够买到十五、电气要素1.电机的动力是否充分2.是否留有配线空间3.是否采取了对噪声、干扰等的处理措施4.接地是否良好十六、操作性1.是否考虑了人的体格和作业空间、移动空间的问题2.是否考虑了最大操作力、最合适操作力的问题3.手柄等的操作方向与人的习惯是否和谐一致4.是否考虑了视觉角度等问题5.对明亮度、温度、音响等方面的舒适性是否做了考虑十七、安全性1.是否考虑了棱角割手以及碰伤、掉落、爆炸、开裂、火灾、人体卷入等问题2.是否考虑了避免操作员与高温部接触的危险性,以及具备了紧急脱离性能、升降性和安全闸等措施3.是否存在由于燃料配管及油压配管的松动、损伤而产生的泄露,或者由于电线短路而发生火灾的危险性4.有否安装作业时的照明装置5.带轮、传动带等可动部件是否设置了防护罩6.为了防止组装差错、调整差错、操作失误等问题是否设定了相应的防止措施7.是否设置了误操作、不良情况发生时,机械可自动停止于安全部位的自我保险装置8.绝缘零部件是否绝缘可靠9.非绝缘零部件(需要导电)是否导电良好十八、制图法(一)投影法1.投影法:第一视角法2.视图安排的位置是否容易看清楚3.视图的表示是否正确(尽可能按可视部位方向描绘)4.视图的粗细线是否正确,粗细线是否可以区别5.对实线、虚线、点划线是否区别画出6.向视图的指示是否妥当7.剖视图的位置和方向是否妥当8.剖视图的表示方法是否妥当(尽可能采用全剖视)9.是否使用了国标规定的文字、数字10.尺寸的比例是否采用了标准规定的比例11.不易看清楚的部位是否画了详细的放大图(二)标题栏1.是否标记出第一视角2.比例是否无误3.是否有设计者、制图者的签字,联系地址明确记载了吗4.是否写入了实验名及装置名5.零件的名称是否贴切并已记入6.是否已记入零件号,图号7.是否已记入材质、热处理及其他特殊事项及重量8.是否指定了一般加工误差。
金属切削机床刨削加工安全检查表范本(2篇)

金属切削机床刨削加工安全检查表范本1. 设备检查:- 检查机床是否稳固放置在平坦的地面上。
- 检查所有电源线、电缆和气管是否完好无损。
- 检查操作控制台是否正常工作,所有按钮、开关和指示灯是否有效。
- 检查切削工具是否安装正确,以及切削工具的固定螺丝是否紧固。
- 检查机床床面是否清洁,并且无任何障碍物。
- 检查切削润滑系统是否正常工作,润滑油是否充足。
- 检查切削液系统是否正常工作,切削液的喷射是否均匀。
- 检查废料排放系统是否通畅,及时清理废料。
- 检查机床的防护装置是否完好,包括刀具防护罩、防护门、防护栏等。
- 检查紧急停止按钮是否正常工作,且易于操作。
2. 操作员检查:- 检查操作员是否装备个人防护设备,包括安全眼镜、耳塞、帽子等。
- 检查操作员是否清楚了解机床的操作规程和安全注意事项。
- 检查操作员是否疲劳,是否适宜进行切削加工操作。
- 检查操作员是否熟悉切削加工的基本知识和技能。
- 检查操作员是否定期接受安全培训,并了解最新的安全操作规范。
- 检查操作员是否保持良好的操作习惯,不慌不忙、稳重可靠。
3. 安全环境检查:- 检查工作区域是否干燥、通风良好。
- 检查工作区域是否清洁整齐,无杂物、油污等障碍物。
- 检查工作区域是否有明显的警示标志,如禁止入内、高危险区等。
- 检查工作区域是否有充足的照明设备,确保工作区域明亮清晰。
- 检查工作区域是否设有紧急停止装置,方便操作员进行应急停机。
- 检查工作区域是否有灭火器等消防设施,以备紧急情况使用。
4. 操作安全检查:- 检查操作员是否正确佩戴个人防护设备。
- 检查操作员是否正确调整切削工具和工作件之间的间隙。
- 检查操作员是否注意切削工具和工作件的相对位置,避免碰撞和冲击。
- 检查操作员是否保持适度的切削速度,避免过快或过慢导致危险。
- 检查操作员是否定期检查切削工具的磨损情况,并及时更换。
- 检查操作员是否定期清理切削液和废料,保持工作区域的清洁。
金属切削机床/刨削加工安全检查表实用版

YF-ED-J7839可按资料类型定义编号金属切削机床/刨削加工安全检查表实用版In Order To Ensure The Effective And Safe Operation Of The Department Work Or Production, Relevant Personnel Shall Follow The Procedures In Handling Business Or Operating Equipment.(示范文稿)二零XX年XX月XX日金属切削机床/刨削加工安全检查表实用版提示:该操作规程文档适合使用于工作中为保证本部门的工作或生产能够有效、安全、稳定地运转而制定的,相关人员在办理业务或操作设备时必须遵循的程序或步骤。
下载后可以对文件进行定制修改,请根据实际需要调整使用。
刨削加工安全检查表说明1)牛头刨床使用较广,它主要用来加工中小型零件,刨削长度不超过1m。
切削加工时,滑枕带动刨刀的直线往复运动是主运动,工作台带动工件的间歇运动是进给运动。
每个往复运动中,刀具都要重新切入工件,刀具受冲击较大,易使刀具崩刃或工件滑出,而造成伤害事故。
滑枕则可能使操作者的手挤在刀具与工件之间或将工人身体挤伤,切削时飞溅出的切屑亦可能伤人。
2)龙门刨床主要是用来加工大型零件,工作台带动工件沿床身导轨作往复直线运动为主运动,刀架带动工具做间歇的垂直或横向直线运动为进给运动。
龙门刨床比牛头刨床形体大刚性好、结构复杂、加工精度高。
不安全因素则是运动着的工作台撞击操作者、行程开关失灵而造成“飞床”事故。
3)插床则用于单件小批生产中加工内表面和内曲面,其主运动是滑枕带动刀具做垂直方向的往复直线运动,进给运动是工作台带动工件的纵、横向间歇直线运动和转动。
主要危险是操作者的手被挤在刀具与工件之间,或是刀具与工作之间。
4)牛头刨床安全检查表适用于B665牛头刨床及与之类似的牛头刨床。
5)龙门刨床安全检查表适用于B2016、B2012型龙门刨床及类似的龙门刨床。
机械连接扭力矩检查表全集文档
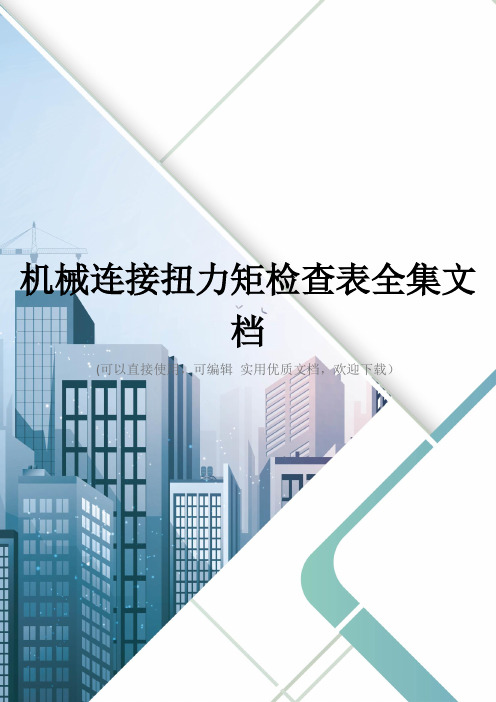
机械连接扭力矩检查表全集文
档
(可以直接使用,可编辑实用优质文档,欢迎下载)
直螺纹接头安装扭力矩检查表工程名称:检查时间:
监理:
附件:
直螺纹接头安装时最小拧紧扭矩值
常规机械设备和机具进场检查表
检查日期:
检查日期:机具故障维修记录
施工机具检查维修记录表
单位/项目部:xxxxxxxx施工项目部
附表4 施工机械(具)和设备清单
说明:1、类别分为五类“特种设备(TZ)”、“自制设备(ZZ)”、“试验设备(SY)”、“个人防护用品(PPE)”、“常规设备和机具(CG)”;
2、“特种设备”、“试验设备”、“个人防护用品(PPE)”需要填写“检验报告编号”、“检验日期”、“检验有效期”栏目。
附表5 机械(具)和设备特种作业人员清单
单位/项目部:编制人:更新日期:。
金属切削机床/磨削加工安全检查表实用版

YF-ED-J6581可按资料类型定义编号金属切削机床/磨削加工安全检查表实用版In Order To Ensure The Effective And Safe Operation Of The Department Work Or Production, Relevant Personnel Shall Follow The Procedures In Handling Business Or Operating Equipment.(示范文稿)二零XX年XX月XX日金属切削机床/磨削加工安全检查表实用版提示:该操作规程文档适合使用于工作中为保证本部门的工作或生产能够有效、安全、稳定地运转而制定的,相关人员在办理业务或操作设备时必须遵循的程序或步骤。
下载后可以对文件进行定制修改,请根据实际需要调整使用。
磨削加工安全检查表说明1)磨削加工是用得最广泛的切削加工方法之一。
2)磨削速度很高,每秒30~50m,高速旋转砂轮的破裂可使人致伤;切削温度较高,可达1500℃,可烫伤人体;切削过程历时很短,只有万分之一秒。
砂轮型号选择不当、砂轮平衡不好、安装不当、磨削量选择不当、缺乏及明修整和操作不当,均可发生砂轮破裂,碎块崩出造成严重伤亡事故。
在砂轮运转时调整、坚固或测量工作时,可能触及高速旋转的砂轮而造成伤害。
工件夹固不牢或电磁盘失灵等原因造成工件飞出伤人事故。
3)安装砂轮必须满足下列安全要求:①根据砂轮使用说明书,选用与机床主轴转数相符的砂轮。
②所选用的砂轮要有出厂合格证或检查试验标志。
③对砂轮进行全面检查,发现砂轮质量、硬度、强度、粒度和外观有裂纹等缺陷时不能使用。
④安装砂轮的法兰不能小于砂轮直径的三分之一或大于二分之一。
⑤法兰盘与砂轮之间要垫好衬垫。
⑥砂轮在安装前要搞好静平衡。
⑦砂轮孔径与主轴间的配合要适当。
⑧紧螺帽时要用专用扳手,不要用力过猛以防滑倒,螺帽紧固要适当。
⑨砂轮装完后,要安装好防护罩,砂轮侧面要与防护罩内壁之间保持20~30mm以上的间隙。
高强度螺栓终拧扭矩检测作业指导书(含全部附表)
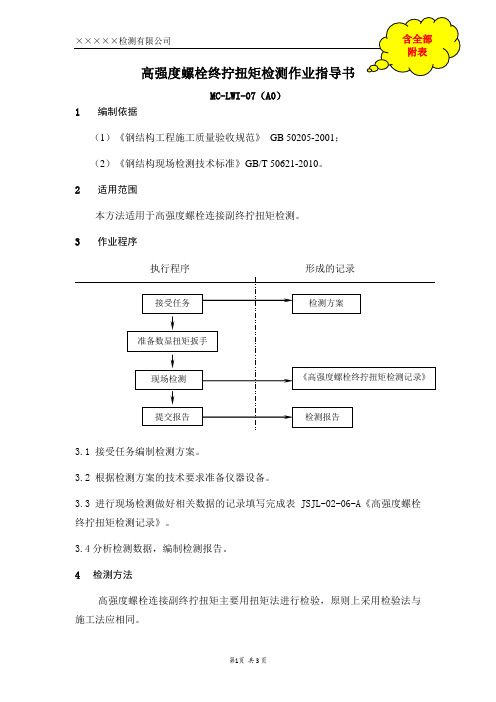
MC-LWI-07(A0)1编制依据(1)《钢结构工程施工质量验收规范》GB 50205-2001;(2)《钢结构现场检测技术标准》GB/T 50621-2010。
2适用范围本方法适用于高强度螺栓连接副终拧扭矩检测。
3作业程序执行程序形成的记录3.1接受任务编制检测方案。
3.2 根据检测方案的技术要求准备仪器设备。
3.3 进行现场检测做好相关数据的记录填写完成表JSJL-02-06-A《高强度螺栓终拧扭矩检测记录》。
3.4分析检测数据,编制检测报告。
4检测方法高强度螺栓连接副终拧扭矩主要用扭矩法进行检验,原则上采用检验法与施工法应相同。
4.1 试验准备:检验所用的扭矩扳手其扭矩精度误差应在3%以内。
4.2 扭矩法检验4.2.1 在螺尾端头和螺母相对位置划线,将螺母退回60°左右。
4.2.2 用扭矩扳手测定拧回至原来位置时扭矩值,并做好记录。
4.2.3 比较测定扭矩值与施工扭矩值的偏差,其偏差在10%以内为合格。
4.3 扭剪型高强度螺栓施工扭矩检验,观察尾部梅花头被拧掉者视同终拧扭矩达到合格标准,未被拧掉者应按上述扭矩法检验。
5 结果计算高强度螺栓连接副终拧扭矩值按下式计算:Tc=K·Pc·d式中,Tc—终拧扭矩值(N·m);Pc—施工预拉力标准值(kN),见附表1;d—螺栓公称直径(mm);T0—初拧扭矩值可按0.5Tc取值。
K—扭矩系数,按GB50205附录B·0·4的规定试验确定(或由委托提供高强度螺栓扭矩系数复验报告)。
.其中高强度螺栓连接副施工扭矩范围如表5-1所示.表5-1 高强度螺栓连接副施工扭矩范围6 测量记录检测记录应按规定格式填写,具体要求执行《记录管理程序》(MC-LQP-21)。
7 记录表格1) JSJL-02-06 高强度螺栓终拧扭矩检测记录×××××检测有限公司高强度螺栓终拧扭矩检测记录JSJL-02-06 项目名称:项目编号:检测设备:检测环境:检测依据:检测人:记录人:校核人:检测日期:年月日。
通用螺栓及螺母最大扭矩预紧力推荐表
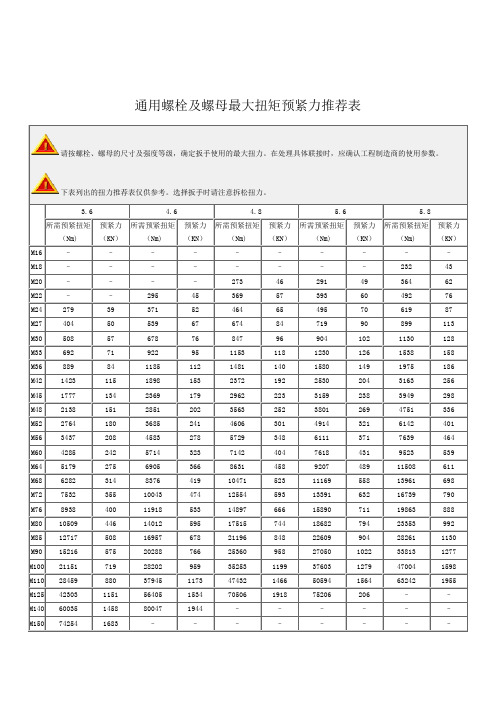
通用螺栓及螺母最大扭矩预紧力推荐表请按螺栓、螺母的尺寸及强度等级,确定扳手使用的最大扭力。
在处理具体联接时,应确认工程制造商的使用参数。
下表列出的扭力推荐表仅供参考。
选择扳手时请注意拆松扭力。
3.64.6 4.85.6 5.8所需预紧扭矩(Nm) 预紧力(KN)所需预紧扭矩(Nm)预紧力(KN)所需预紧扭矩(Nm)预紧力(KN)所需预紧扭矩(Nm)预紧力(KN)所需预紧扭矩(Nm)预紧力(KN)M16 ––––––––––M18 ––––––––232 43 M20 ––––273 46 291 49 364 62 M22 ––295 45 369 57 393 60 492 76 M24 279 39 371 52 464 65 495 70 619 87 M27 404 50 539 67 674 84 719 90 899 113 M30 508 57 678 76 847 96 904 102 1130 128 M33 692 71 922 95 1153 118 1230 126 1538 158 M36 889 84 1185 112 1481 140 1580 149 1975 186 M42 1423 115 1898 153 2372 192 2530 204 3163 256 M45 1777 134 2369 179 2962 223 3159 238 3949 298 M48 2138 151 2851 202 3563 252 3801 269 4751 336 M52 2764 180 3685 241 4606 301 4914 321 6142 401 M56 3437 208 4583 278 5729 348 6111 371 7639 464 M60 4285 242 5714 323 7142 404 7618 431 9523 539 M64 5179 275 6905 366 8631 458 9207 489 11508 611 M68 6282 314 8376 419 10471 523 11169 558 13961 698 M72 7532 355 10043 474 12554 593 13391 632 16739 790 M76 8938 400 11918 533 14897 666 15890 711 19863 888 M80 10509 446 14012 595 17515 744 18682 794 23353 992 M85 12717 508 16957 678 21196 848 22609 904 28261 1130 M90 15216 575 20288 766 25360 958 27050 1022 33813 1277 M100 21151 719 28202 959 35253 1199 37603 1279 47004 1598 M110 28459 880 37945 1173 47432 1466 50594 1564 63242 1955 M125 42303 1151 56405 1534 70506 1918 75206 206 ––M140 60035 1458 80047 1944 ––––––M150 74254 1683 ––––––––表中扭矩为达到屈服强度的80%时所测定)。
金属切削机床磨削加工安全检查表

金属切削机床磨削加工安全检查表第一篇:金属切削机床磨削加工安全检查表金属切削机床(磨削加工)安全检查表转载自智安网:磨削加工安全检查表说明1)磨削加工是用得最广泛的切削加工方法之一。
2)磨削速度很高,每秒30~50m,高速旋转砂轮的破裂可使人致伤;切削温度较高,可达1500℃,可烫伤人体;切削过程历时很短,只有万分之一秒。
砂轮型号选择不当、砂轮平衡不好、安装不当、磨削量选择不当、缺乏及明修整和操作不当,均可发生砂轮破裂,碎块崩出造成严重伤亡事故。
在砂轮运转时调整、坚固或测量工作时,可能触及高速旋转的砂轮而造成伤害。
工件夹固不牢或电磁盘失灵等原因造成工件飞出伤人事故。
3)安装砂轮必须满足下列安全要求:① 根据砂轮使用说明书,选用与机床主轴转数相符的砂轮。
② 所选用的砂轮要有出厂合格证或检查试验标志。
③ 对砂轮进行全面检查,发现砂轮质量、硬度、强度、粒度和外观有裂纹等缺陷时不能使用。
④ 安装砂轮的法兰不能小于砂轮直径的三分之一或大于二分之一。
⑤ 法兰盘与砂轮之间要垫好衬垫。
⑥ 砂轮在安装前要搞好静平衡。
⑦ 砂轮孔径与主轴间的配合要适当。
⑧ 紧螺帽时要用专用扳手,不要用力过猛以防滑倒,螺帽紧固要适当。
⑨ 砂轮装完后,要安装好防护罩,砂轮侧面要与防护罩内壁之间保持20~30mm以上的间隙。
⑩ 砂轮装好后要经过5~10min的试运转,起动时不要过急,要点动检查。
4)无心磨床安全检查表适用于M10型及与之类似的无心磨床。
5)平面磨床安全检查表适用于M71型卧轴矩台平面磨床及与之类似的平面磨床。
6)螺纹磨床安全检查表适用于M7520型螺纹磨床及与之类似的精密磨床。
7)光学曲线磨床安全检查表适用于M9050型及与之类似的光学曲线磨床。
(1)无心磨床安全检查表1.设备检查1.1砂轮架应齐全、完好、固定可靠、调整方便、工作时应运行平稳、无异常噪声。
1.2砂轮主轴的螺纹旋向必须与砂轮工作时的旋转方向相反。
1.3主轴轴向止推装置必须安装牢固,能有效地控制主轴的轴向串动。
金属切削机床镗削加工安全检查表(3篇)

金属切削机床镗削加工安全检查表1. 安全设备检查1.1 检查切削机床的各项安全装置是否完好,并能正常运转。
1.2 检查切削机床的各种防护罩是否完好,能够有效防止金属屑、碎片等飞溅出来。
1.3 检查切削机床的紧急停机按钮是否灵敏可用,能在发生意外情况时及时切断电源。
1.4 检查切削机床的井盖、散热器等部件是否牢固,无松动现象。
2. 电气系统检查2.1 检查切削机床的电气线路是否损坏、松动,是否有漏电等情况。
2.2 检查切削机床的电气设备是否有过热现象,是否需要更换、修理。
2.3 检查切削机床的漏电保护设备是否正常运作。
3. 润滑系统检查3.1 检查切削机床的润滑系统是否正常运转,油品是否充足,润滑部位是否有异常磨损。
3.2 检查切削机床的润滑设备是否有漏油现象,是否需要更换、修理。
4. 切削工具检查4.1 检查切削机床的刀具是否磨损严重,是否需要更换。
4.2 检查切削机床的刀具是否正确安装,是否有松动现象。
4.3 检查切削机床的刀具是否干净,无油污和剩屑,以免影响切削工作。
5. 工作区域检查5.1 检查切削机床周围的工作区域是否整洁有序,避免堆放杂物和易燃物品。
5.2 检查切削机床周围的地面是否平整,是否有滑倒、绊倒的隐患。
5.3 检查切削机床周围的照明设备是否正常运作,确保工作区域有足够的光线。
6. 操作员检查6.1 检查切削机床操作员是否穿戴符合要求的工作服、工作帽等个人防护用品。
6.2 检查切削机床操作员是否接受过相应的培训,是否了解切削机床的操作规程和安全注意事项。
6.3 检查切削机床操作员是否熟悉各项操作控制手柄和按钮,并且能正确操作。
7. 镗削加工操作检查7.1 检查切削机床的工件夹紧装置是否可靠,避免在加工过程中工件脱离或变形。
7.2 检查切削机床的进给机构是否正常,切削速度是否适中,避免过高的速度引起危险。
7.3 检查切削机床的加工液循环系统是否正常运转,确保切削过程中工件和刀具得到足够的冷却和润滑。
扭矩检查记录表
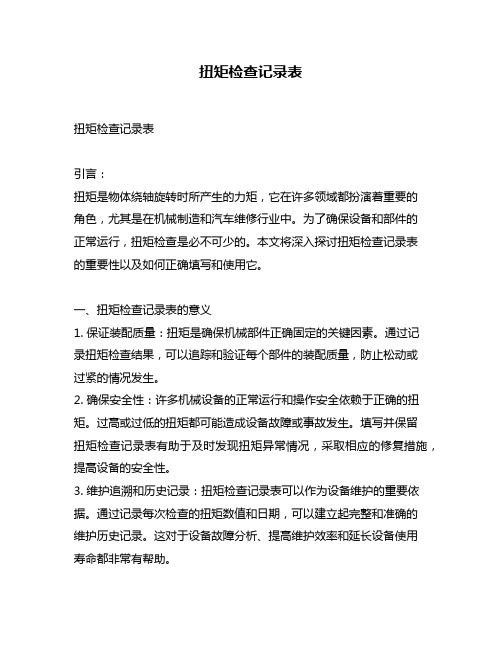
扭矩检查记录表扭矩检查记录表引言:扭矩是物体绕轴旋转时所产生的力矩,它在许多领域都扮演着重要的角色,尤其是在机械制造和汽车维修行业中。
为了确保设备和部件的正常运行,扭矩检查是必不可少的。
本文将深入探讨扭矩检查记录表的重要性以及如何正确填写和使用它。
一、扭矩检查记录表的意义1. 保证装配质量:扭矩是确保机械部件正确固定的关键因素。
通过记录扭矩检查结果,可以追踪和验证每个部件的装配质量,防止松动或过紧的情况发生。
2. 确保安全性:许多机械设备的正常运行和操作安全依赖于正确的扭矩。
过高或过低的扭矩都可能造成设备故障或事故发生。
填写并保留扭矩检查记录表有助于及时发现扭矩异常情况,采取相应的修复措施,提高设备的安全性。
3. 维护追溯和历史记录:扭矩检查记录表可以作为设备维护的重要依据。
通过记录每次检查的扭矩数值和日期,可以建立起完整和准确的维护历史记录。
这对于设备故障分析、提高维护效率和延长设备使用寿命都非常有帮助。
二、如何正确填写扭矩检查记录表填写扭矩检查记录表需要严谨和准确,以下是一些需要注意的要点:1. 标明项目和参数:记录表应包含需要进行扭矩检查的项目和相应的参数。
可以列出不同的螺栓规格和相应的扭矩要求。
对于大型设备,可以将其分成不同的模块和部件,并为每个部件列出必要的检查参数。
2. 记录检查结果:在填写记录表时,必须准确记录每次的检查结果。
可以使用数字或颜色来表示不同的状态,如正常、过紧或过松。
还可以在记录表中添加备注栏,用于记录其他需要特别说明的事项。
3. 注明检查日期和操作者:每次进行扭矩检查时,都应该在相应的记录栏中注明日期和操作者的尊称或编号。
这有助于追溯问题,并确保检查的一致性和准确性。
4. 签字确认:每次完成扭矩检查后,操作者和相关人员应在记录表上签字确认。
这是对工作的一种负责任态度,也可以作为审查和审核的依据。
三、总结与回顾扭矩检查记录表是设备维护和质量控制的重要工具。
通过正确填写和使用记录表,可以保证装配质量、提高安全性,并建立起完整的维护历史记录。
金属切削机床铣削加工安全检查表范本(2篇)
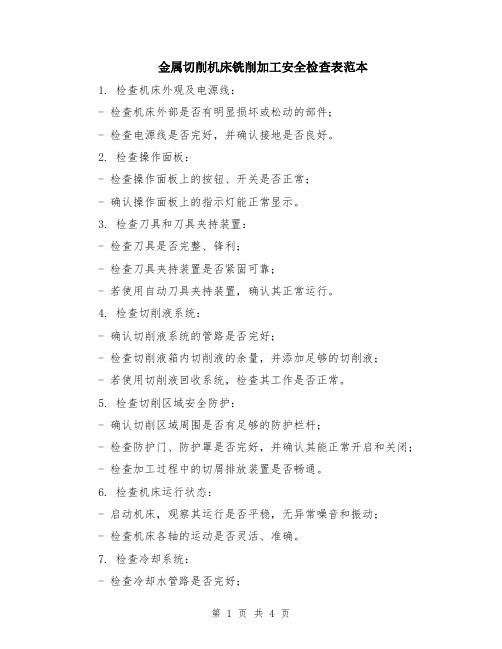
金属切削机床铣削加工安全检查表范本1. 检查机床外观及电源线:- 检查机床外部是否有明显损坏或松动的部件;- 检查电源线是否完好,并确认接地是否良好。
2. 检查操作面板:- 检查操作面板上的按钮、开关是否正常;- 确认操作面板上的指示灯能正常显示。
3. 检查刀具和刀具夹持装置:- 检查刀具是否完整、锋利;- 检查刀具夹持装置是否紧固可靠;- 若使用自动刀具夹持装置,确认其正常运行。
4. 检查切削液系统:- 确认切削液系统的管路是否完好;- 检查切削液箱内切削液的余量,并添加足够的切削液;- 若使用切削液回收系统,检查其工作是否正常。
5. 检查切削区域安全防护:- 确认切削区域周围是否有足够的防护栏杆;- 检查防护门、防护罩是否完好,并确认其能正常开启和关闭;- 检查加工过程中的切屑排放装置是否畅通。
6. 检查机床运行状态:- 启动机床,观察其运行是否平稳,无异常噪音和振动;- 检查机床各轴的运动是否灵活、准确。
7. 检查冷却系统:- 检查冷却水管路是否完好;- 检查冷却液箱内冷却液的余量,并添加足够的冷却液;- 检查冷却系统的温度和压力是否在正常范围内。
8. 检查机床润滑系统:- 确认润滑油箱内润滑油的余量,并添加足够的润滑油;- 检查润滑系统管路是否完好;- 检查润滑系统的工作是否正常,无异常的润滑点。
9. 检查电气系统:- 检查电气线路是否完好,无短路或接触不良;- 检查电气设备的接地是否良好;- 若使用变频器进行控制,检查其工作是否正常。
10. 检查运输锁定装置:- 检查运输锁定装置是否已全部解除。
11. 检查紧固件:- 检查机床上的紧固件是否全部紧固可靠。
12. 检查安全标识:- 检查机床上的安全标识是否清晰可见;- 确认操作人员是否了解并遵守相应的安全规范。
以上为金属切削机床铣削加工安全检查表范本,详细检查内容,请根据具体机床的型号和使用情况进行相应的调整和补充。
请在使用任何机床之前,先进行安全检查,确保操作人员的安全。
高强度螺栓终拧扭矩检查记录(通用表格)

(通用表格)
工程名称
苏盐合作园区港区片标准厂房一期4#厂房
分项工程名称
高强度螺栓安装
C~Q轴/1~7轴
隐蔽项目
高强度螺栓终拧扭矩检查
总包单位
苏盐合作园区港区片标准厂房一期4#厂房
分包单位
施工图号
检查部位
标准规定
施工单位自查记录
监理(建设)单位验收记录
高强度螺栓终拧扭矩
扭剪型高强度螺栓的扭矩法施工的终拧扭矩应符合现行国家标准《钢结构工程施工及验收规范》的规定。观察尾部梅花头拧掉情况,尾部梅花头被拧掉者视同其终拧矩达到合格质量标准,尾部梅花头未被拧掉者应按转角法检验如下:在螺母端头和螺母相对位置划线,将螺母退回60°左右,用扭矩扳手测定拧回至原来位置时的扭矩值,该扭矩值与施工扭矩的偏差在10%以内为合格 Nhomakorabea符合规范规定
施工单位
自查结论
经检查符合施工质量验收规范规定
质检员:
施工单位项目负责人:年月日
监理(建设)
单位验收结论
监理工程师(建设单位项目负责人):年月日
金属切削机床铣削加工安全检查表(4篇)

金属切削机床铣削加工安全检查表以下是一个金属切削机床铣削加工安全检查表的示例:1. 检查机床是否稳定,底座是否牢固。
2. 检查电源线是否完好,是否有裸露的电线。
3. 检查机床的动力系统,如电机、皮带传动等是否正常工作。
4. 检查切割工具,如铣刀、刀片、夹具等是否坚固,是否有损坏。
5. 检查切割区域是否清洁,无杂物堆积。
6. 检查润滑系统是否正常工作,如油量是否充足,润滑点是否清洁。
7. 检查机床的安全保护装置是否完好,如防护罩、限位开关等。
8. 检查操作台是否标有相关警示标识,如禁止开启、停止等。
9. 检查操作人员是否穿戴个人防护装备,如安全帽、防护眼镜等。
10. 检查周围环境是否安全,如没有其他人员靠近、无易燃物质等。
11. 检查操作人员是否熟悉机床的操作规程,是否具备相关操作技能。
12. 检查机床的紧急停机装置是否正常,是否能够及时切断电源。
以上是金属切削机床铣削加工安全检查表的一些常见项目,根据具体的机床类型和工作环境,还可以根据实际情况添加或调整检查项目。
在操作机床时,一定要保证安全,遵守相关操作规程和安全注意事项。
金属切削机床铣削加工安全检查表(二)1. 机床是否良好运行,无明显异常声响或震动?2. 机床是否固定牢固,无松动或倾斜?3. 切削液是否加足,且没有泄漏?4. 切削液是否经过配制和使用说明,并定期更换?5. 机床是否接地良好?6. 切削工具是否磨损或损坏?如有需要及时更换。
7. 进给系统是否正常工作,无卡滞或异常?8. 机床是否设有足够的安全保护装置,如防护罩、安全开关等?9. 操作人员是否熟悉并遵守安全操作规程?10. 应急停机按钮是否正常工作?11. 机床周围是否存在杂物或障碍物,有无影响安全的因素?12. 机床是否定期维护,保持良好的工作状态?请注意,这只是一个通用的安全检查表,具体的情况还需要根据实际的机床类型和操作要求进行调整和补充。
同时,确保操作人员接受过相关培训,并且具备相关的安全意识和操作技能。
- 1、下载文档前请自行甄别文档内容的完整性,平台不提供额外的编辑、内容补充、找答案等附加服务。
- 2、"仅部分预览"的文档,不可在线预览部分如存在完整性等问题,可反馈申请退款(可完整预览的文档不适用该条件!)。
- 3、如文档侵犯您的权益,请联系客服反馈,我们会尽快为您处理(人工客服工作时间:9:00-18:30)。
最大扭矩及满功率切削试验检查表
一.满功率切削
1.记录
刀具直径(mm)切削深度(mm)主轴转速(rpm)
刀数切削宽度/直径(mm)进给速度(mm/min)
主轴负荷最大功率(KW)输出功率(KW)
实测功率(KW)
2.测试方法
1)在机床主轴恒功率调速范围内,选择一适当的主轴转速,采用铣削方式进行试验,改变进给速度或切削深度,使机床达到主轴动机大的额度功率或设计室的最大功率
2)试验时,机床各部门工作应正常,可靠,无得显示颤振现象。
3)以功率计测试主轴电机输入功率,乘以功率因子0.85转化得实测功率
二.最大扭矩切削
1.记录
刀具直径(mm)切削深度(mm)主轴转速(rpm)
刀数切削宽度/直径(mm)进给速度(mm/min)
主轴负荷空载功率(KW)实测功率(KW)
最大扭矩(N.m)实测扭矩(N.m)
2.测试方法
1)在机床主轴恒扭矩调速范围内,选择一适当的主轴转速,采用铣削或铣前方式进行试验,改变进给速度或切削深度,使机床主电机系统达到设计规定的了大扭矩
2)试验时,机床电机系统多元部件和变速机构工作应正常,可靠,运转应平稳,准确。
3)实测扭矩计算公式:T=9550(P-PO)/n.
T:扭矩N.m
PO=机床加载工件,主轴空转时功率KW;P=实际切削时主轴电机输入功率KW;n=实切时主轴转速rpm
三.切削条件:
1、工作材质:HT200
2、面锐刀具需用BT-40
3、切削参数参见技术文件
检验装配
表单编号修订日期版次审核技术拟定。