从高炉热平衡分析看炼铁工艺节能方向(标准版)
正确把握炼铁系统节能方向
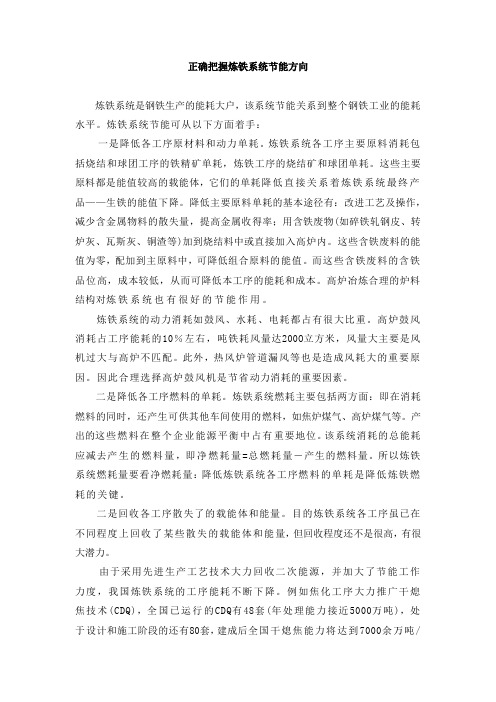
正确把握炼铁系统节能方向炼铁系统是钢铁生产的能耗大户,该系统节能关系到整个钢铁工业的能耗水平。
炼铁系统节能可从以下方面着手:一是降低各工序原材料和动力单耗。
炼铁系统各工序主要原料消耗包括烧结和球团工序的铁精矿单耗,炼铁工序的烧结矿和球团单耗。
这些主要原料都是能值较高的载能体,它们的单耗降低直接关系着炼铁系统最终产品——生铁的能值下降。
降低主要原料单耗的基本途径有:改进工艺及操作,减少含金属物料的散失量,提高金属收得率;用含铁废物(如碎铁轧钢皮、转炉灰、瓦斯灰、铜渣等)加到烧结料中或直接加入高炉内。
这些含铁废料的能值为零,配加到主原料中,可降低组合原料的能值。
而这些含铁废料的含铁品位高,成本较低,从而可降低本工序的能耗和成本。
高炉冶炼合理的炉料结构对炼铁系统也有很好的节能作用。
炼铁系统的动力消耗如鼓风、水耗、电耗都占有很大比重。
高炉鼓风消耗占工序能耗的10%左右,吨铁耗风量达200O立方米,风量大主要是风机过大与高炉不匹配。
此外,热风炉管道漏风等也是造成风耗大的重要原因。
因此合理选择高炉鼓风机是节省动力消耗的重要因素。
二是降低各工序燃料的单耗。
炼铁系统燃耗主要包括两方面:即在消耗燃料的同时,还产生可供其他车间使用的燃料,如焦炉煤气、高炉煤气等。
产出的这些燃料在整个企业能源平衡中占有重要地位。
该系统消耗的总能耗应减去产生的燃料量,即净燃耗量=总燃耗量-产生的燃料量。
所以炼铁系统燃耗量要看净燃耗量:降低炼铁系统各工序燃料的单耗是降低炼铁燃耗的关键。
二是回收各工序散失了的载能体和能量。
目的炼铁系统各工序虽已在不同程度上回收了某些散失的载能体和能量,但回收程度还不是很高,有很大潜力。
由于采用先进生产工艺技术大力回收二次能源,并加大了节能工作力度,我国炼铁系统的工序能耗不断下降。
例如焦化工序大力推广干熄焦技术(CDQ),全国已运行的CDQ有48套(年处理能力接近5000万吨),处于设计和施工阶段的还有80套,建成后全国干熄焦能力将达到7000余万吨/年。
从高炉热平衡来看炼铁节能工艺方向
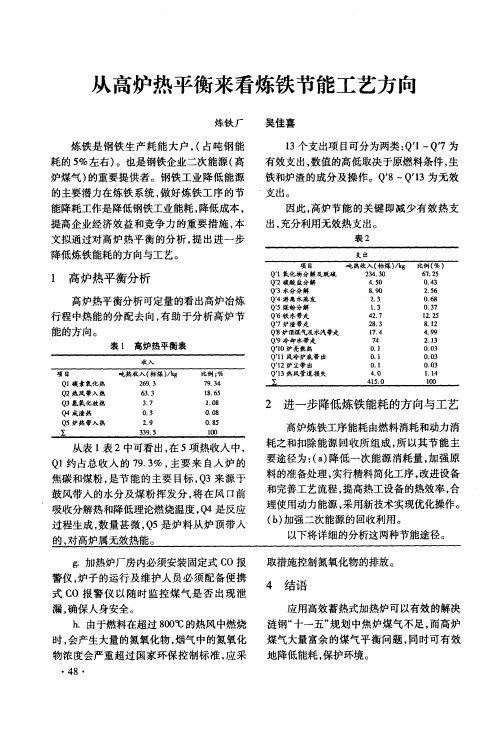
" £ j ∞叮∞ HⅪ 耗之和扣除能源回收所组成, 以其节能主 所
躬
要途径为 :a 降低 一次能源消耗量 , () 加强原 料的准备处理 , 实行精料简化工序 , 改进设备 和完善工艺流程 , 提高热工设备的热效率 , 合 理使用动力能源 , 采用新技术实现优化操作。
( ) 强二次 能源 的 回收 利用 。 b加 以下将详 细的 分析这两 种节 能途 径 。
∑
40 . 4 50 1.
2 进一步降低炼铁能耗 的方向与工艺
n 乞
高炉炼铁工序能耗 由燃料消耗和动力消 n & n n ● n L
从表 1 2中可看 出, 5 表 在 项热收人 中,
Q 约 占总 收 入 的 7。 % , 要 来 自人 炉 的 1 93 主 焦碳 和煤 粉 , 节 能 的主 要 目标 , 3来源 于 是 Q
鼓风带人的水分及煤粉挥发分 , 将在风 口前 吸收 分解 热和降 低理论燃 烧温 度 ,} ( 4是反 应 过程生成 , 数量甚微 , 5是炉料从炉顶带人 Q
的, 对高 炉属无效 热能 。
g .加热炉厂房内必须安装固定式 C O报 警仪, 炉子的运行及维护人员必须配备便携 式C O报警仪 以随时监 控煤气是否 出现泄 漏, 确保人身安全。 h .由于燃料在超过 80 0 ℃的热风中燃烧 时, 会产生大量的氮氧化物 , 烟气中的氦氧化 物浓度会严重超过国家环保控制标准 , 应采
机合理 运 行 , 减少 漏风 率 、 少 临 时休 风 率 , 减 减少蒸 汽的漏 气 。
£高炉冷却水落差发电。 利用高炉冷却水落差 , 自集水槽底引出,
经导 管流人 位 于炉 台下 的水 轮机 发 电
3 结语
通过对高炉热平衡 的分析 , 论了实现 讨 高炉 节能 的方 向与工艺 , 主要 是 : 减少 一次 能
高炉热平衡分析炼铁工艺的节能方向

高炉热平衡分析炼铁工艺的节能方向摘要以某高炉炼铁过程中的热平衡为研究对象,将高炉内部热平衡分析作为节能控制的分析途径,提出了优化炉内煤气流速与分布、增加高炉内部炉料的表面积、提高热传导性能、使用富氧喷煤技术以及充分回收炉渣焓等节能措施,形成了基于高炉热平衡的节能改造方向。
关键词高炉;热平衡;节能高炉热平衡是保证高炉热效率,提高高炉热能利用能力以及增加高炉热工特性的重要途径。
针对高炉炼铁工艺节能改造的过程中,通过高炉热平衡来分析炼铁工艺中存在的节能缺陷,最终提出针对性的节能措施,是炼铁工艺节能的一个重要方法。
1 某高炉节能改造前概况根据盖斯定律,在忽略高炉内部的具体反应过程,而只考虑物料进入炉内的状态,并将之作为反应的起点,之后将产出状态作为反应终点,对高炉内部的热平衡状态进行分析计算。
在整个反应过程中,热收入项目主要包括风口前碳素燃烧热量的释放、炼铁工艺的直接还原发热(C氧化成CO)、炼铁过程中的间接还原放热(CO 氧化成CO2,H2 氧化成H2O)、热风携带的热量、少量的成渣热以及炉料带入的热量等。
而炉内的热释放主要包括脱硫,氧化物的分解,溶剂的分解,炉渣焓、铁水焓、炉顶煤气焓以及冷却水带走的其他热损失。
通过采用对应的热平衡检验方式,得到表1中所示的高炉热平衡计算结果。
从表1 的具体数据分析可知,高炉的热收入项目中,碳素氧化热占到高炉热收入总量的77.8%,主要来自高炉的焦炭以及煤粉燃烧发热,因此可以将之作为高炉节能的主要方向。
2 节能改造措施2.1 优化炉内煤气流速与分布煤气内部传递给炉内的热量与煤气内部的流速以及气体内部的分布情况存在着直接关系。
当煤气量越大时,炉内的煤气流速将增加,热交换量将增加,这时炉料的吸热能力也增强,但是炉内顶部温度的数值变化也增加,煤气带走的热量损失也增大。
所以,煤气含量以及流速之间存在着一个最优值。
通过使用高压以及超高压的操作方式,增加炉内边缘的矿焦比,将能够有效的提高高炉的热交换效率,同时降低煤气带走的热量,减少由此带来的热量损失。
高炉炼铁工艺的节能减排优化探讨

高炉炼铁工艺的节能减排优化探讨摘要:我国钢铁产量非常高,促进国民经济进行了更好发展。
但因为在进行钢铁产品制作时,引发了环境污染和能源消耗过度问题,对社会建设存在不良影响。
因此钢铁企业需要在传统生产技术基础上,对其创新和优化,并积极引进节能减排生产技术,才能在提高产量同时降低经济成本,并且满足绿色化生产目标。
钢铁企业要做好高炉炼铁工艺优化,并且根据节能减排建设需求,选择合适生产设备,才能促进整个行业进行绿色化发展。
本文就高炉炼铁工艺的节能减排优化进行相关分析和探讨。
关键词:高炉炼铁工艺;节能;减排;优化探讨在进行钢铁产品制作和生产时,高炉炼铁工艺应用价值比较高,可以满足日常生产需求。
在现代科技不断发展期间,高炉炼铁工艺在应用时变得更加完善,大多数企业已经根据自身生产需求,构建了相对应高炉炼铁技术应用体系,一些企业也对高炉喷煤制造系统进行了改进和优化,提高了节能减排生产水平。
钢铁企业在对现有高炉炼铁工艺更新时,要根据自身发展目标,结合日常生产需求做好生产链完善,还需要引进更加专业技术人员,为技术优化提供承充足人才支撑,提高高炉炼铁水平[1]。
一、高炉炼铁应用现状在现代工业不断发展期间,对钢铁产品生产量提出了更高需求。
但因为钢铁产品生产期间排放的二氧化碳含量增加会危害自然环境,不符合环保要求。
我国在制定可持续发展战略之后,已经根据战略要求对钢铁行业生产提出了严格要求。
钢铁企业在日常生产时,需要做好高炉设备改造,并更新高炉炼铁工艺,才能提高钢铁领域生产产值,降低整体能耗。
钢铁企业还需要选择可替代资源,提高自身生产水平。
在现代科技不断发展期间,高炉炼铁工艺应用形式变得更加完善,可以在一定程度上降低生产期间负面影响。
在对高炉炼铁工艺节能改造之后,可以提高这项技术应用价值。
目前在进行高炉炼铁节能减排改造时,主要是从提高煤气利用率,并对生产期间产生的废弃物循环利处理,满足各个环节上绿色化生产要求。
钢铁企业还要对高炉炼铁生产期间产生的污染性气体有效处理,并且做好生产期间温度控制,在满足日常生产需求的同时,对生产资源高效利用。
高炉炼铁工艺节能减排技术分析

高炉炼铁工艺节能减排技术分析摘要:现今钢铁工业面临着巨大的减排压力。
有研究显示,高炉炼铁产量在全球产量中占94%。
而高炉炼铁过程中的二氧化碳排放与能耗占整个钢铁生产制造流程中的80%及以上,根据本国国情,制定相应的改善措施,开发出了一些新型的高炉炼铁节能减排技术。
文章简单阐述分析了高炉炼铁工艺的节能减排技术。
关键词:高炉;炼铁工艺;节能减排技术一、节能减排技术在高炉炼铁中的应用价值从上世纪九十年代中后期开始,我国的基础建设进入了高速发展期,对钢铁产品的需求量也呈现出快速增长态势,这就给我国的钢铁行业带来黄金发展机遇,现有的钢铁企业经营生产规模不断扩大,新兴的钢铁产业也如同雨后春笋般应运而生。
因此,高炉冶炼过程中二氧化碳的排放量也不断增加,“温室效应”的环境污染问题也日渐突显,给人们赖以生存的生活空间造成了严重的负面影响。
面对这种严峻形势,国家针对钢铁行业相继出台了节能减排的相关法律、法规及政策条文,进一步加大了环境保护的管理力度,诸多钢铁企业为了响应国家号召,不断创新高炉炼铁的节能减排新技术,旨在通过高产值、低能耗、少排放使企业在激烈的市场竞争当中占据一席之地。
据调查统计表明,在钢铁产品的生产过程中,高炉炼铁系统的能量消耗占据总能耗的60%以上,如果从生产成本方面考虑,占据生产总成本的50%以上。
由此可见,节能减排技术在高炉炼铁中的实际应用势在必行,它不仅能够降低对环境的污染和破坏程度,减少二氧化碳、二氧化硫等有害气体的排放量,同时,能够节约大量的投入成本,为企业创造更大的利润空间。
二、高炉炼铁工艺节能减排新技术1.新型旋风除尘器在处理高炉粗煤气与半净煤气时,倘若选用重力除尘+干法净化除尘或重力除尘+湿法除尘时,这些设备的实际应用过程中,往往需要大量的运行成本,并且有着较高的维护费用,难于调节,耐磨块掉落堵塞卸灰系统。
根据相关调查研究表明,部分钢铁企业在进行高炉改造时,选用湿法除尘方式,引进了肖夫塔设备,在实际的应用过程中尝尽了苦头,之所以出现这一现象,主要在于重力除尘效率低,比肖夫旋流塔磨损严重。
炼钢高炉系统化能耗分析与优化
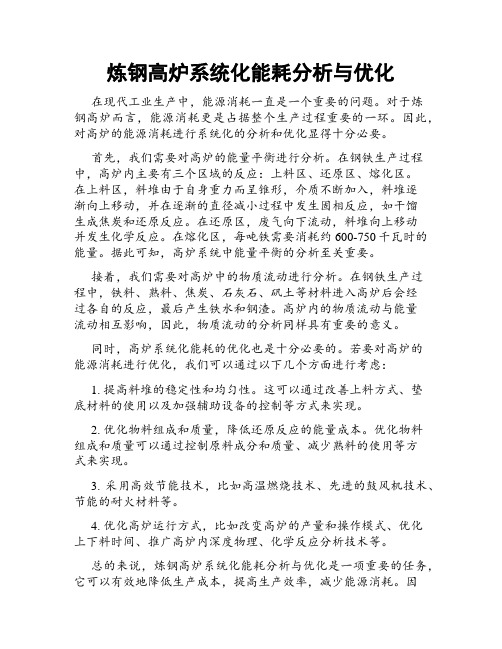
炼钢高炉系统化能耗分析与优化在现代工业生产中,能源消耗一直是一个重要的问题。
对于炼钢高炉而言,能源消耗更是占据整个生产过程重要的一环。
因此,对高炉的能源消耗进行系统化的分析和优化显得十分必要。
首先,我们需要对高炉的能量平衡进行分析。
在钢铁生产过程中,高炉内主要有三个区域的反应:上料区、还原区、熔化区。
在上料区,料堆由于自身重力而呈锥形,介质不断加入,料堆逐渐向上移动,并在逐渐的直径减小过程中发生固相反应,如干馏生成焦炭和还原反应。
在还原区,废气向下流动,料堆向上移动并发生化学反应。
在熔化区,每吨铁需要消耗约600-750千瓦时的能量。
据此可知,高炉系统中能量平衡的分析至关重要。
接着,我们需要对高炉中的物质流动进行分析。
在钢铁生产过程中,铁料、熟料、焦炭、石灰石、矾土等材料进入高炉后会经过各自的反应,最后产生铁水和钢渣。
高炉内的物质流动与能量流动相互影响,因此,物质流动的分析同样具有重要的意义。
同时,高炉系统化能耗的优化也是十分必要的。
若要对高炉的能源消耗进行优化,我们可以通过以下几个方面进行考虑:1. 提高料堆的稳定性和均匀性。
这可以通过改善上料方式、垫底材料的使用以及加强辅助设备的控制等方式来实现。
2. 优化物料组成和质量,降低还原反应的能量成本。
优化物料组成和质量可以通过控制原料成分和质量、减少熟料的使用等方式来实现。
3. 采用高效节能技术,比如高温燃烧技术、先进的鼓风机技术、节能的耐火材料等。
4. 优化高炉运行方式,比如改变高炉的产量和操作模式、优化上下料时间、推广高炉内深度物理、化学反应分析技术等。
总的来说,炼钢高炉系统化能耗分析与优化是一项重要的任务,它可以有效地降低生产成本,提高生产效率,减少能源消耗。
因此,我们需要对高炉的能量平衡和物质流动进行全面的分析,找出各种能源和物料的损失,并寻找优化措施。
只有通过不断地优化和改进,才能够将高炉系统的能源消耗最小化,从而使其更加环保、节能、经济和可持续。
高炉炼铁工艺节能减排技术分析
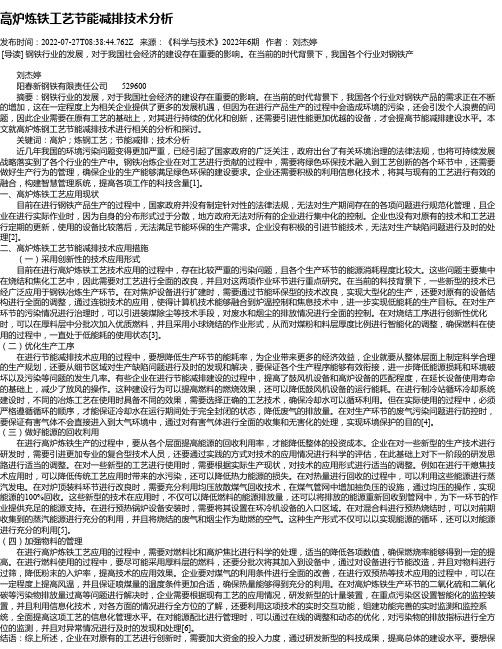
高炉炼铁工艺节能减排技术分析发布时间:2022-07-27T08:38:44.762Z 来源:《科学与技术》2022年6期作者:刘杰婷[导读] 钢铁行业的发展,对于我国社会经济的建设存在重要的影响。
在当前的时代背景下,我国各个行业对钢铁产刘杰婷阳春新钢铁有限责任公司 529600摘要:钢铁行业的发展,对于我国社会经济的建设存在重要的影响。
在当前的时代背景下,我国各个行业对钢铁产品的需求正在不断的增加,这在一定程度上为相关企业提供了更多的发展机遇,但因为在进行产品生产的过程中会造成环境的污染,还会引发个人浪费的问题,因此企业需要在原有工艺的基础上,对其进行持续的优化和创新,还需要引进性能更加优越的设备,才会提高节能减排建设水平。
本文就高炉炼钢工艺节能减排技术进行相关的分析和探讨。
关键词:高炉;炼钢工艺;节能减排;技术分析近几年我国的环境污染问题变得更加严重,已经引起了国家政府的广泛关注,政府出台了有关环境治理的法律法规,也将可持续发展战略落实到了各个行业的生产中。
钢铁冶炼企业在对工艺进行贡献的过程中,需要将绿色环保技术融入到工艺创新的各个环节中,还需要做好生产行为的管理,确保企业的生产能够满足绿色环保的建设要求。
企业还需要积极的利用信息化技术,将其与现有的工艺进行有效的融合,构建智慧管理系统,提高各项工作的科技含量[1]。
一、高炉炼铁工艺应用现状目前在进行钢铁产品生产的过程中,国家政府并没有制定针对性的法律法规,无法对生产期间存在的各项问题进行规范化管理,且企业在进行实际作业时,因为自身的分布形式过于分散,地方政府无法对所有的企业进行集中化的控制。
企业也没有对原有的技术和工艺进行定期的更新,使用的设备比较落后,无法满足节能环保的生产需求。
企业没有积极的引进节能技术,无法对生产缺陷问题进行及时的处理[2]。
二、高炉炼铁工艺节能减排技术应用措施(一)采用创新性的技术应用形式目前在进行高炉炼铁工艺技术应用的过程中,存在比较严重的污染问题,且各个生产环节的能源消耗程度比较大。
关于高炉炼铁工艺节能减排技术分析

关于高炉炼铁工艺节能减排技术分析摘要:本文将通过对几项高炉炼铁工艺节能减排技术进行介绍,即全氧高炉、利用炉渣显热、风温的提升、燃料比的降低、二次能量回收比的提升、高炉精料技术、回收炉顶均压放散煤气以及高炉热风炉自动寻优燃烧等技术,以期为有关技术人员提供有效参考。
关键词:高炉炼铁工艺;节能;减排引言:高炉炼铁工艺在日常生产钢铁的过程中占据着重要地位,经过从古至今的长期发展,已经获得多次改良。
相对其他工艺,高炉炼铁工艺流程相对简捷,产量较大,生产率较高且具备较低能耗,几乎已被世界各国使用。
我国要求高炉炼铁趋向低碳、循环发展,因此有关人员应及时引入相应节能减排技术。
1全氧高炉技术在以往的高炉炼铁工艺中,高风温富氧冶铁技术所鼓入空气中氮气的含量极大,常常导致煤气量中的氮气含量占据极大部分,最高时甚至会占据约49%,不仅会形成NOx,更会使大量热能无法被有效利用,最终使煤气整体的品质被降低[1]。
此技术中会应用公式1:公式1通过公式可知,只有约50%的C元素被转换成CO,且浪费了大约37%的能量。
如今,先进的全氧高炉技术能够有效使喷煤量提升,同时将煤气风口安置于炉身,还可以使入炉焦比降低。
经过实践,全氧高炉技术的节能率超过了25%,并且减少CO2的排放量也高达25%,最终将焦比降至低于200kg。
由此可见,全氧高炉技术拥有十分良好的应用前景。
2利用炉渣显热通常情况下,每一吨的炉渣显热与60kg的标准煤热值相当,几乎占据高炉工艺14%的能耗,即有效利用炉渣显热可以充分提升整体能源的利用率,同时也能使高炉渣出炉的温度范围高达1400-1550℃。
如今一些发达国家已经在利用炉渣显热的工艺中开发出“化学热回收法”以及“物理热回收法”,而“物理热回收法”又可以按照不同的炉渣前处理技术细化成转杯法、滚筒法、连铸式余热锅炉法以及风淬法等,但是仍然需要进一步的实验才能确定其应用前景。
其中,水淬法是如今我国利用大部分高炉渣制成水渣的常用方法,常常被应用在水泥原料。
从高炉热平衡分析看炼铁工艺节能方向
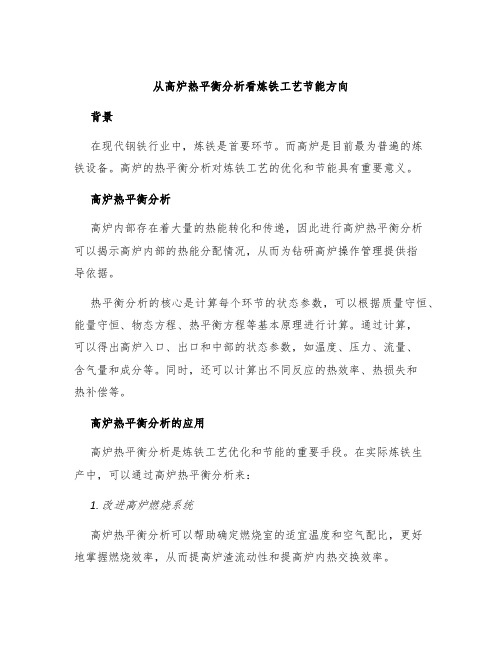
从高炉热平衡分析看炼铁工艺节能方向背景在现代钢铁行业中,炼铁是首要环节。
而高炉是目前最为普遍的炼铁设备。
高炉的热平衡分析对炼铁工艺的优化和节能具有重要意义。
高炉热平衡分析高炉内部存在着大量的热能转化和传递,因此进行高炉热平衡分析可以揭示高炉内部的热能分配情况,从而为钻研高炉操作管理提供指导依据。
热平衡分析的核心是计算每个环节的状态参数,可以根据质量守恒、能量守恒、物态方程、热平衡方程等基本原理进行计算。
通过计算,可以得出高炉入口、出口和中部的状态参数,如温度、压力、流量、含气量和成分等。
同时,还可以计算出不同反应的热效率、热损失和热补偿等。
高炉热平衡分析的应用高炉热平衡分析是炼铁工艺优化和节能的重要手段。
在实际炼铁生产中,可以通过高炉热平衡分析来:1. 改进高炉燃烧系统高炉热平衡分析可以帮助确定燃烧室的适宜温度和空气配比,更好地掌握燃烧效率,从而提高炉渣流动性和提高炉内热交换效率。
2. 减少热损失高炉热平衡分析可以揭示热传递的路径和热损失的大小,并为减少热损失提供思路和依据。
例如,通过合理的冷却水温度和流量控制来减少锅炉&吹风机丢失的热量。
3. 优化原料配比高炉热平衡分析可以帮助确定不同原料的热值、结合水量和其他参数,从而优化炉内原料的配比和分层情况,提高冶炼效率。
4. 提高热效率高炉热平衡分析可以分析炉内气体和固体物料的热量分配情况,从而提高热效率。
比如炉煤气的回收和利用,以及余热回收系统的建设和利用。
通过提高炼铁热效率,可以减少排放并降低对环境的影响。
炼铁工艺节能的发展方向炼铁工艺节能应当注重整个工艺流程的优化和协调。
在高炉热平衡分析的基础上,可以通过以下几个方向来推动炼铁工艺节能发展:1. 推广先进冶炼技术先进冶炼技术具有很大的节能潜力和环保效益。
例如氧气增压燃烧技术、双流解炉技术、高效物料预热技术和高炉赤铁合成制备技术等。
2. 加强热能回收利用热能回收利用是重要的节能手段,可以通过余热回收、炉煤气回收等方式利用分散热能,从而降低能源消耗。
基于高炉热平衡角度分析炼铁工艺节能发展

基于高炉热平衡角度分析炼铁工艺节能发展随着我国钢铁工业的发展,炼铁工艺的研究和优化已经成为产业升级的重要方向之一。
而在这个工艺中,高炉扮演着至关重要的角色。
通过研究高炉的热平衡,可以更好地理解炼铁工艺的本质,并且为其节能发展提供技术支持。
本文将基于高炉热平衡的角度,分析炼铁工艺的节能发展现状和未来发展方向。
1、高炉的工作原理及热平衡分析高炉作为炼铁过程中最重要的设备之一,其工作原理非常复杂。
简单来说,高炉的原理是利用铁矿石的还原反应,将矿石中的铁和其他金属元素分离出来。
同时,高炉还会产生一定的热量,这些热量可以用来支持后续的冶炼工艺。
因此,高炉的工作热平衡非常重要。
高炉的热平衡可以分为两个方面:热学平衡和物质平衡。
热学平衡是指高炉内部各个区域之间的热量平衡,包括高炉的上、中、下部以及风道等部分。
物质平衡则是指高炉内部不同物质之间的平衡。
2、炼铁工艺节能发展现状分析我国的钢铁工业是非常庞大的一个行业,也是国家的支柱产业之一。
但是,在这个行业中,能源的消耗量非常大,而且工艺上的不断升级也对钢铁生产造成了不小的冲击。
因此,钢铁行业的节能发展已经成为一个非常重要的问题。
在炼铁工艺中,高炉是最消耗能源的一个设备。
而高炉的热平衡分析对节能发展也有着很大的作用。
通过对高炉内部的热平衡状态进行分析,可以找到相应的节能方案,如下面几种:(1)合理选择高炉的工作参数。
在炼铁工艺中,高炉的工作参数非常重要。
通过选择合理的高炉进料参数、煤气流参数等,可以达到节能的效果。
(2)适当地增加矿石热量。
在高炉工作中,矿石的热量是非常重要的。
通过适当地增加矿石的热量,可以减少其他燃料的使用量,从而达到节能减排的效果。
(3)提高高炉的热效率。
高炉的热效率是节能的重要方面。
通过提高高炉的利用率和热效率,可以减少不必要的能源浪费。
3、炼铁工艺节能发展未来趋势随着新型材料技术和高性能钢的不断涌现,炼铁工艺的节能发展也将面临新的挑战。
钢铁企业需要寻找新的技术路线,从而提高钢铁产业的竞争力。
高炉炼铁能耗与节能分析

高炉炼铁能耗与节能分析发布时间:2008-8-21 来源: 中国钢铁企业网本网专家顾问:王维兴李忠核心提示:据统计,2005年我国生产原煤21.9亿吨(居世界第一),消费21.4亿吨原煤;生产原油1.81亿吨(居世界第六),消费原油3.0亿吨;生产天然气500亿m3(居世界第十四),消费500亿m3;全年发电24747亿千瓦时(居世界第二)。
1.我国钢铁工业能耗现状据统计,2005年我国生产原煤21.9亿吨(居世界第一),消费21.4亿吨原煤;生产原油1.81亿吨(居世界第六),消费原油3.0亿吨;生产天然气500亿m3(居世界第十四),消费500亿m3;全年发电24747亿千瓦时(居世界第二)。
2005年我国能源消费结构是:煤炭为68.7%,油气为24%,水电+核电为7.3%。
2004年我国钢铁工业能源消耗占全国能源总消费量的15.18%,其能源消费结构是:煤炭69.9%,石油类3.2%,天然气0.5%,电力26.4%。
2.钢铁工业节能情况按不变价格计算,2005年我国万元GDP能耗比1980年下降64%。
改革开放以来,累积节约和少用超过10亿吨标准煤,以能源消费翻一番支持了GDP值翻两番。
1980~2005年,我国大中型钢铁企业吨钢可比能耗从1285Kgce/t降到714Kgce/t,节约571Kgce/t,降低了44.43%。
这说明,我国钢铁工业的节能步伐是与我国经济发展中的节能力度是同步进行,也说明了钢铁工业节能工作取得巨大成绩。
据统计2006年前三季度,全国产钢3.08亿吨,比上年度同期增长18.49%,但全国重点大中型钢铁企业总能耗为14535万吨标煤,比上年度降低6.8%。
这说明,我国钢铁工业节能工作还在深化发展。
2000年,工业发达国家吨钢可比能耗平均值在642Kgce/t。
2005年,我国重点大中型钢铁企业吨钢可比能耗值为714Kgce/t。
经对比分析可看出,我国钢铁工业的能耗水平与工业发达国家相比,尚高出11.2%。
炼铁生产中的能耗优化与节能减排措施

炼铁生产中的能耗优化与节能减排措施能源是现代社会发展的基石,然而在能源有限的情况下,如何优化炼铁生产中的能耗,实现节能减排已经成为了一个迫切的问题。
本文将探讨炼铁生产中的能耗优化与节能减排措施,并提出具体的解决方案。
一、炼铁生产中的能耗现状炼铁生产是消耗能源的重要行业之一,其能耗情况直接关系到国家能源安全和环境保护。
然而,目前我国炼铁企业的能耗水平普遍较高,存在一系列问题。
首先,传统的高炉炼铁工艺存在能源利用率低的问题。
其次,炼铁生产中的废气、废水和废渣等排放物对环境造成了严重的污染。
因此,亟需采取有效的节能减排措施,优化能源利用,降低能耗水平。
二、能耗优化措施1. 提高高炉燃烧效率高炉是炼铁生产的核心设备,提高高炉燃烧效率是降低能耗的关键一步。
可以通过优化燃烧参数、改善高炉炉况、提高燃烧设备的热效率等方式来提高高炉的燃烧效率。
2. 采用先进的炼铁技术传统的高炉炼铁工艺存在能源损失较大的问题,可以考虑采用先进的炼铁技术来降低能耗。
比如,采用高炉煤气发电技术、煤气制氢技术等可以实现能源的全面利用。
3. 引进节能设备与技术在炼铁生产过程中,引进先进的节能设备与技术是降低能耗的重要手段。
比如,可以引进高效节能的燃烧设备、烟气余热回收技术、废气处理设备等来提高能源利用效率。
三、节能减排措施1. 废气治理高炉炼铁过程中产生大量的废气,其中含有大量的烟尘和有害气体。
应建立完善的废气治理系统,采用高效的除尘设备和废气脱硫、脱硝技术,减少废气的排放,降低对环境的影响。
2. 废水处理炼铁生产中的废水含有较高的悬浮固体和重金属等有害物质,对水环境造成较大污染。
应采用生物法、化学法等多种处理技术对废水进行处理,确保排放水质符合相关标准。
3. 废渣综合利用炼铁过程中产生的废渣具有一定的资源价值,应加强废渣的综合利用。
比如,可以将废渣进行回收再利用,用于生产水泥、建材等,减少对自然资源的占用。
四、结语炼铁生产中的能耗优化与节能减排是实现可持续发展的关键之一。
从高炉热平衡分析看炼铁工艺节能方向
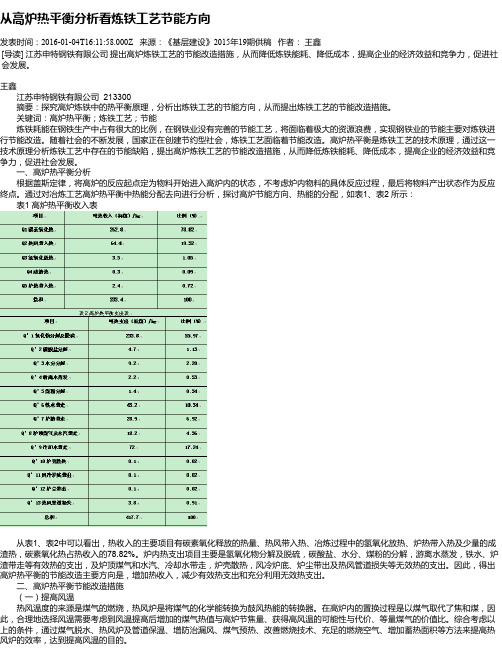
从高炉热平衡分析看炼铁工艺节能方向发表时间:2016-01-04T16:11:58.000Z 来源:《基层建设》2015年19期供稿作者:王鑫[导读] 江苏申特钢铁有限公司提出高炉炼铁工艺的节能改造措施,从而降低炼铁能耗、降低成本,提高企业的经济效益和竞争力,促进社会发展。
王鑫江苏申特钢铁有限公司 213300摘要:探究高炉炼铁中的热平衡原理,分析出炼铁工艺的节能方向,从而提出炼铁工艺的节能改造措施。
关键词:高炉热平衡;炼铁工艺;节能炼铁耗能在钢铁生产中占有很大的比例,在钢铁业没有完善的节能工艺,将面临着极大的资源浪费,实现钢铁业的节能主要对炼铁进行节能改造。
随着社会的不断发展,国家正在创建节约型社会,炼铁工艺面临着节能改造。
高炉热平衡是炼铁工艺的技术原理,通过这一技术原理分析炼铁工艺中存在的节能缺陷,提出高炉炼铁工艺的节能改造措施,从而降低炼铁能耗、降低成本,提高企业的经济效益和竞争力,促进社会发展。
一、高炉热平衡分析根据盖斯定律,将高炉的反应起点定为物料开始进入高炉内的状态,不考虑炉内物料的具体反应过程,最后将物料产出状态作为反应终点。
通过对冶炼工艺高炉热平衡中热能分配去向进行分析,探讨高炉节能方向、热能的分配,如表1、表2 所示:表1 高炉热平衡收入表从表1、表2中可以看出,热收入的主要项目有碳素氧化释放的热量、热风带入热、冶炼过程中的氢氧化放热、炉热带入热及少量的成渣热,碳素氧化热占热收入的78.82%。
炉内热支出项目主要是氢氧化物分解及脱硫,碳酸盐、水分、煤粉的分解,游离水蒸发,铁水、炉渣带走等有效热的支出,及炉顶煤气和水汽、冷却水带走,炉壳散热,风冷炉底、炉尘带出及热风管道损失等无效热的支出。
因此,得出高炉热平衡的节能改造主要方向是,增加热收入,减少有效热支出和充分利用无效热支出。
二、高炉热平衡节能改造措施(一)提高风温热风温度的来源是煤气的燃烧,热风炉是将煤气的化学能转换为鼓风热能的转换器。
基于高炉热平衡角度分析炼铁工艺节能发展
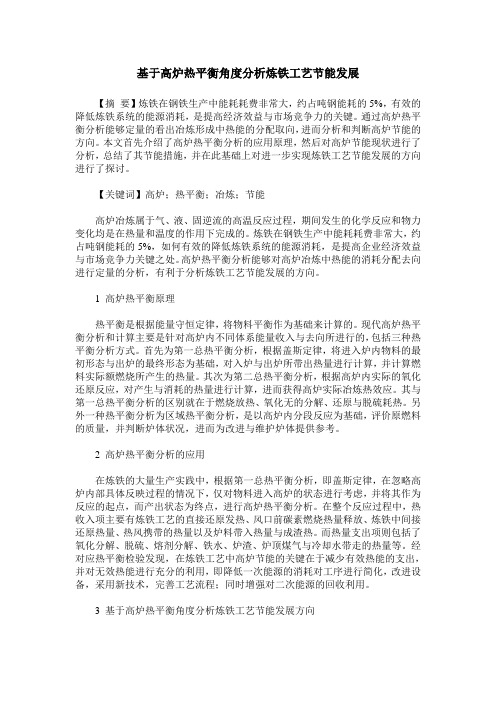
基于高炉热平衡角度分析炼铁工艺节能发展【摘要】炼铁在钢铁生产中能耗耗费非常大,约占吨钢能耗的5%,有效的降低炼铁系统的能源消耗,是提高经济效益与市场竞争力的关键。
通过高炉热平衡分析能够定量的看出冶炼形成中热能的分配取向,进而分析和判断高炉节能的方向。
本文首先介绍了高炉热平衡分析的应用原理,然后对高炉节能现状进行了分析,总结了其节能措施,并在此基础上对进一步实现炼铁工艺节能发展的方向进行了探讨。
【关键词】高炉;热平衡;冶炼;节能高炉冶炼属于气、液、固逆流的高温反应过程,期间发生的化学反应和物力变化均是在热量和温度的作用下完成的。
炼铁在钢铁生产中能耗耗费非常大,约占吨钢能耗的5%,如何有效的降低炼铁系统的能源消耗,是提高企业经济效益与市场竞争力关键之处。
高炉热平衡分析能够对高炉冶炼中热能的消耗分配去向进行定量的分析,有利于分析炼铁工艺节能发展的方向。
1 高炉热平衡原理热平衡是根据能量守恒定律,将物料平衡作为基础来计算的。
现代高炉热平衡分析和计算主要是针对高炉内不同体系能量收入与去向所进行的,包括三种热平衡分析方式。
首先为第一总热平衡分析,根据盖斯定律,将进入炉内物料的最初形态与出炉的最终形态为基础,对入炉与出炉所带出热量进行计算,并计算燃料实际额燃烧所产生的热量。
其次为第二总热平衡分析,根据高炉内实际的氧化还原反应,对产生与消耗的热量进行计算,进而获得高炉实际冶炼热效应。
其与第一总热平衡分析的区别就在于燃烧放热、氧化无的分解、还原与脱硫耗热。
另外一种热平衡分析为区域热平衡分析,是以高炉内分段反应为基础,评价原燃料的质量,并判断炉体状况,进而为改进与维护炉体提供参考。
2 高炉热平衡分析的应用在炼铁的大量生产实践中,根据第一总热平衡分析,即盖斯定律,在忽略高炉内部具体反映过程的情况下,仅对物料进入高炉的状态进行考虑,并将其作为反应的起点,而产出状态为终点,进行高炉热平衡分析。
在整个反应过程中,热收入项主要有炼铁工艺的直接还原发热、风口前碳素燃烧热量释放、炼铁中间接还原热量、热风携带的热量以及炉料带入热量与成渣热。
从高炉热平衡分析看炼铁工艺节能方向
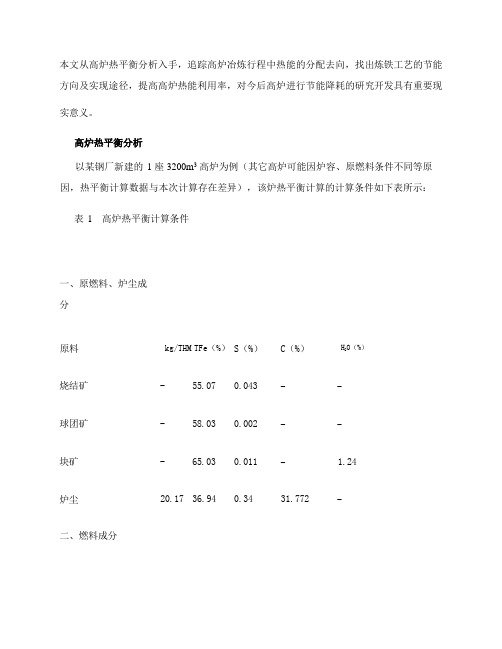
2.2.减少铁水焓损失的途径 2.2.1.所谓铁水罐“一罐到底”就是高炉承接铁水的铁水罐和转炉铁水罐为统一罐车,此 过程温降少,温度起伏低,生产节奏快时,铁水罐到达高炉时包衬和包底温度还较高,使 得高炉铁水流入铁水罐内温降相对较少,有利于减少铁水热损失。 2.2.2.近年研究出在安全衬后用致密、高强度隔热板的鱼雷罐车,具体安装方法为在整 个罐车中安装隔热层为第一层衬,再安装安全衬,最后一层为耐磨衬。已隔热的鱼雷罐车 较无隔热的罐车中铁水温度平均可提高 20℃。
全炉热平衡计算结果如下表:
表 2 全炉热平衡表
数
项
目
量
GJ/t
%
热收入:
Q1 风口前碳素燃烧
2.94
Q2 直接还原 C 氧化成 CO 1.00
Q3 间接还原 CO 氧化成 CO2 4.40
Q4 间接还原 H2 氧化成 H2O 0.36
Q5 热风带入
2.05
Q 总热收入:
10.75
热支出:
Q1 ’氧化物分解
2.2.3.3.高炉渣干式粒化处理: 目前国内外对此处理方式的研究已进入中试阶段,分为
普通式和流化床式两类。
本文通过对高炉的热平衡分析,找出高炉的主要节能方向为降低燃料消耗、减少铁水 焓损失、充分回收炉渣和煤气焓、减少高炉热损失,探讨了上述几个节能方向的实现途径 及节能效果,对今后开展高炉节能降耗方面的研究具有重要的现实意义。
表 1 高炉热平衡计算条件
一、原燃料、炉尘成分
高炉炼铁工艺节能减排技术分析_1
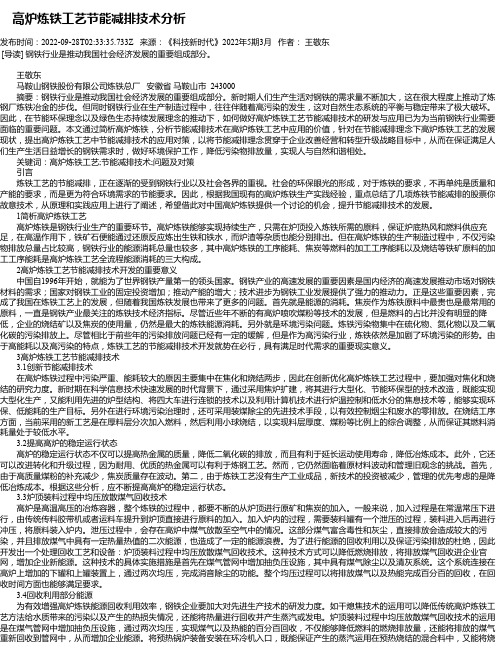
高炉炼铁工艺节能减排技术分析发布时间:2022-09-28T02:33:35.733Z 来源:《科技新时代》2022年5期3月作者:王敬东[导读] 钢铁行业是推动我国社会经济发展的重要组成部分。
王敬东马鞍山钢铁股份有限公司炼铁总厂安徽省马鞍山市 243000摘要:钢铁行业是推动我国社会经济发展的重要组成部分。
新时期人们生产生活对钢铁的需求量不断加大,这在很大程度上推动了炼钢厂炼铁冶金的步伐。
但同时钢铁行业在生产制造过程中,往往伴随着高污染的发生,这对自然生态系统的平衡与稳定带来了极大破坏。
因此,在节能环保理念以及绿色生态持续发展理念的推动下,如何做好高炉炼铁工艺节能减排技术的研发与应用已为为当前钢铁行业需要面临的重要问题。
本文通过简析高炉炼铁,分析节能减排技术在高炉炼铁工艺中应用的价值,针对在节能减排理念下高炉炼铁工艺的发展现状,提出高炉炼铁工艺中节能减排技术的应用对策,以将节能减排理念贯穿于企业改善经营和转型升级战略目标中,从而在保证满足人们生产生活日益增长的钢铁需求时,做好环境保护工作,降低污染物排放量,实现人与自然和谐相处。
关键词:高炉炼铁工艺;节能减排技术;问题及对策引言炼铁工艺的节能减排,正在逐渐的受到钢铁行业以及社会各界的重视。
社会的环保眼光的形成,对于炼铁的要求,不再单纯是质量和产能的要求,而是更为符合环境需求的节能要求。
因此,根据我国现有的高炉炼铁生产实践经验,重点总结了几项炼铁节能减排的股票你故意技术,从原理和实践应用上进行了阐述,希望借此对中国高炉炼铁提供一个讨论的机会,提升节能减排技术的发展。
1简析高炉炼铁工艺高炉炼铁是钢铁行业生产的重要环节。
高炉炼铁能够实现持续生产,只需在炉顶投入炼铁所需的原料,保证炉底热风和燃料供应充足,在高温作用下,铁矿石便能通过还原反应炼出生铁和铁水,而炉渣等杂质也能分别排出。
但在高炉炼铁的生产制造过程中,不仅污染物排放总量占比较高,钢铁行业的能源消耗总量也较多,其中高炉炼铁的工序能耗、焦炭等燃料的加工工序能耗以及烧结等铁矿原料的加工工序能耗是高炉炼铁工艺全流程能源消耗的三大构成。
关于高炉炼铁工艺节能减排技术分析

关于高炉炼铁工艺节能减排技术分析发布时间:2022-07-11T05:55:00.871Z 来源:《科技新时代》2022年7期作者:邓志成[导读] 高炉炼铁时,需要大量的一氧化碳,其起到还原剂的作用,应用煤气干法布袋除尘技术,会形成较多的一氧化碳,满足高炉炼铁需求,并且该技术具有突出的节能降耗优势,研究表明,1吨铁煤气所产生的热量值约等于175kg标准煤所产生的热量值。
柳州钢铁股份有限公司炼铁厂广西柳州 545002摘要:高炉炼铁,具有能耗大、污染重等特征,节能减排背景下,要加快钢铁行业转型升级发展,应用技能减排技术,优化高炉炼铁工艺,减少能源消耗,减轻环境污染,助推钢铁行业清洁化生产与发展。
基于此,本文着重对高炉炼铁工艺节能减排技术应用要点展开了深入研究。
关键词:高炉炼铁工艺;节能减排技术;应用研究我国是钢铁大国,钢铁行业快速发展的背景下,能源消耗及环境污染问题引发了社会各界的高度关注。
现如今,钢铁行业面临着严峻的节能减排压力,如何实现绿色化生产与发展成为研究思考的关键问题。
一、煤气干法布袋除尘技术高炉炼铁时,需要大量的一氧化碳,其起到还原剂的作用,应用煤气干法布袋除尘技术,会形成较多的一氧化碳,满足高炉炼铁需求,并且该技术具有突出的节能降耗优势,研究表明,1吨铁煤气所产生的热量值约等于175kg标准煤所产生的热量值。
但是,因一氧化碳为有害气体,所以在利用应做好净化处理工作。
首先,要实施粗除尘处理,将煤气当中的大颗粒粉尘去除后进行精除尘,将煤气当中的含尘量控制在5mg/m3。
高炉煤气经深度净化处理后,能够用作余压发电,亦可继续供给热风炉使用。
以某钢铁厂高炉为例,该高炉在尚未实施节能减排前,焦炭节省量为0,发电功率为5500kw·h,补充新水量为50-60t/d,煤气出口热效率为0。
而在应用煤气干法布袋除尘技术后,焦炭节省量达26.4t/d,成本节约近3000万元,发电功率为11000kw·h,成本节约近1800万元,补充新水量为0,成本节约近400万元,煤气出口热效率提高5.5%,成本节约近400万元,不难看出,高炉炼铁中应用煤气干法布袋除尘技术起到了突出的节能降耗效果。
炼铁生产过程中的耗能分析与节能措施

炼铁生产过程中的耗能分析与节能措施铁是不可缺少的资源之一,而炼铁生产则是一项高能耗、高排放的产业。
在我国经济建设中占据着重要的地位。
但是在制造过程中的能耗问题是制约工业发展和环境保护的重要问题之一。
因此,对炼铁生产过程中的能耗问题进行分析和研究,以实现节能降耗,具有重要的实用价值。
1. 炼铁生产过程中的能耗问题在炼铁生产过程中,最主要的能耗来自于高炉和焦炉。
高炉负责将铁矿石还原成生铁,而焦炉则是供给高炉热力能源的主要设备。
具体来看,高炉会在还原铁矿石的同时,释放出大量的热能,这些热能可以通过高炉炉顶的烟气传递给蒸汽锅炉,进而制造蒸汽驱动汽轮机发电,实现对高炉废热的利用。
但是在实际生产过程中,由于高炉运行条件复杂,热传递效果不佳,导致高炉废热的利用率较低,从而造成了不少的能源浪费。
另外,由于焦炉所需的热能来自于煤炭的燃烧,其过程中会产生大量的各种有毒有害气体,主要包括一氧化碳和二氧化碳等。
虽然目前通过改进焦炉工艺等手段,可以在一定程度上降低焦炉排放的有害气体,但仍然存在着很大的安全隐患。
除了以上两大能源,矿泉水的制备和物料输送等环节也都需要消耗大量的能源,从而增加了炼铁生产的总能耗。
2. 炼铁生产中的节能措施(1) 提高热能利用效率作为炼铁生产过程中最主要的能耗来源,高炉和焦炉的能源利用效率直接影响整个生产的能耗指标。
因此提高高炉和焦炉的热能利用效率,是炼铁生产节能的主要手段之一。
其中,提高高炉烟气能量利用率是节能降耗的关键点之一。
目前实现高炉废热的利用较为常见的方法,是通过蒸汽锅炉和汽轮机等设备实现对高炉废热的二次利用。
这种方法需要充分考虑高炉炉顶烟气的温度、烟气输送以及蒸汽锅炉等设备带来的热损失等因素。
因此,在此过程中需要合理设计设备和参数,实现烟气高温、高速、高湿的冷凝。
(2) 提高炉缸效率在炼铁生产中焦炉所产生的有害气体问题一直是亟待解决的难题。
为了减少焦炉对环境的影响,我们可以从多方面入手,如通过改进炉壁材料、调整设计参数等方式优化焦炉结构,逐步提高焦炉效率,减少有害气体的排放。
高炉炼铁工艺节能减排技术探析
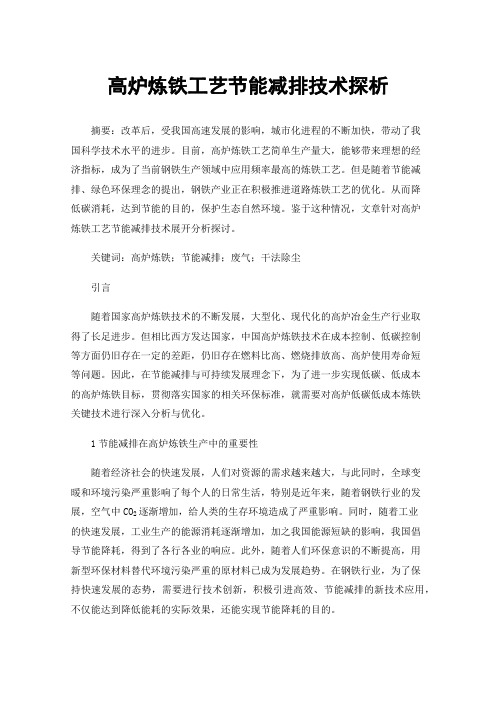
高炉炼铁工艺节能减排技术探析摘要:改革后,受我国高速发展的影响,城市化进程的不断加快,带动了我国科学技术水平的进步。
目前,高炉炼铁工艺简单生产量大,能够带来理想的经济指标,成为了当前钢铁生产领域中应用频率最高的炼铁工艺。
但是随着节能减排、绿色环保理念的提出,钢铁产业正在积极推进道路炼铁工艺的优化。
从而降低碳消耗,达到节能的目的,保护生态自然环境。
鉴于这种情况,文章针对高炉炼铁工艺节能减排技术展开分析探讨。
关键词:高炉炼铁;节能减排;废气;干法除尘引言随着国家高炉炼铁技术的不断发展,大型化、现代化的高炉冶金生产行业取得了长足进步。
但相比西方发达国家,中国高炉炼铁技术在成本控制、低碳控制等方面仍旧存在一定的差距,仍旧存在燃料比高、燃烧排放高、高炉使用寿命短等问题。
因此,在节能减排与可持续发展理念下,为了进一步实现低碳、低成本的高炉炼铁目标,贯彻落实国家的相关环保标准,就需要对高炉低碳低成本炼铁关键技术进行深入分析与优化。
1节能减排在高炉炼铁生产中的重要性随着经济社会的快速发展,人们对资源的需求越来越大,与此同时,全球变暖和环境污染严重影响了每个人的日常生活,特别是近年来,随着钢铁行业的发展,空气中CO2逐渐增加,给人类的生存环境造成了严重影响。
同时,随着工业的快速发展,工业生产的能源消耗逐渐增加,加之我国能源短缺的影响,我国倡导节能降耗,得到了各行各业的响应。
此外,随着人们环保意识的不断提高,用新型环保材料替代环境污染严重的原材料已成为发展趋势。
在钢铁行业,为了保持快速发展的态势,需要进行技术创新,积极引进高效、节能减排的新技术应用,不仅能达到降低能耗的实际效果,还能实现节能降耗的目的。
2高炉炼铁工艺节能减排技术研究2.1炉顶装料过程中均压放散煤气回收技术高炉是高温高压冶炼容器,在整个炼铁过程中,需要持续添加原矿、煤炭等进去。
一般情况下,加入过程是在常温常压下进行,通过传料胶带机运输至炉顶添加可燃物。
- 1、下载文档前请自行甄别文档内容的完整性,平台不提供额外的编辑、内容补充、找答案等附加服务。
- 2、"仅部分预览"的文档,不可在线预览部分如存在完整性等问题,可反馈申请退款(可完整预览的文档不适用该条件!)。
- 3、如文档侵犯您的权益,请联系客服反馈,我们会尽快为您处理(人工客服工作时间:9:00-18:30)。
Safety is the goal, prevention is the means, and achieving or realizing the goal of safety is the basic connotation of safety prevention.
(安全管理)
单位:___________________
姓名:___________________
日期:___________________
从高炉热平衡分析看炼铁工艺节
能方向(标准版)
从高炉热平衡分析看炼铁工艺节能方向(标
准版)
导语:做好准备和保护,以应付攻击或者避免受害,从而使被保护对象处于没有危险、不受侵害、不出现事故的安全状态。
显而易见,安全是目的,防范是手段,通过防范的手段达到或实现安全的目的,就是安全防范的基本内涵。
本文从高炉热平衡分析入手,追踪高炉冶炼行程中热能的分配去向,找出炼铁工艺的节能方向及实现途径,提高高炉热能利用率,对今后高炉进行节能降耗的研究开发具有重要现实意义。
高炉热平衡分析
以某钢厂新建的1座3200m3
高炉为例(其它高炉可能因炉容、原燃料条件不同等原因,热平衡计算数据与本次计算存在差异),该炉热平衡计算的计算条件如下表所示:
表1高炉热平衡计算条件
一、原燃料、炉尘成分
原料
kg/THM
TFe(%)
S(%)C(%)H2
O(%)烧结矿- 55.07 0.043 -
-
球团矿- 58.03 0.002 -
-
块矿-
65.03
0.011
-
1.24
炉尘
20.17
36.94
0.34
31.772
-
二、燃料成分燃料
kg/THM
CF(%)
灰分(%)
挥发分(%)H2
O(%)
焦炭
360
86.83
11.8
0.89
-
煤粉
180
82.94
11.05
3.86
1.80
以盖斯定律为基础,不考虑炉内的反应过程,而以物料入炉状态为起点,产出状态为终点,进行高炉热平衡计算。
热收入项包括风口前碳素燃烧放热,直接还原放热(C氧化成CO),间接还原放热(CO 氧化成CO2
,H2
氧化成H2
O),热风带入的热量,少量成渣热和炉料带入的热量(本次计算忽略此项);热支出项包括氧化物分解,脱硫,溶剂分解,炉渣焓,铁水焓,炉顶煤气焓,冷却水带走和散热损失等。
全炉热平衡计算结果如下表:
表2全炉热平衡表
项目
数量
GJ/t
%
热收入:
Q1
风口前碳素燃烧
2.94
27.35
Q2
直接还原C氧化成CO
1.00
9.30
Q3
间接还原CO氧化成CO2 4.40
40.93
Q4
间接还原H2
氧化成H2
O
0.36
3.35
Q5
热风带入
2.05
19.07
Q总热收入:
10.75
100.00
热支出:
Q1
’氧化物分解7.94
73.86
Q2
’脱硫
0.02
0.19
Q3
’炉渣焓
0.64
5.95
Q4
’铁水焓
1.24
11.53
Q5
煤气焓
0.47
4.37
Q6
’冷却和其它热损失
0.44
4.09
Q’总热支出:
10.75
100.00
热效率
生铁单位热耗
从表2可以看出,在高炉的热收入项中,碳素氧化热(Q1、Q2、Q3)占总热收入(Q)的77.58%,主要来自入炉的焦炭和煤粉,是高炉的节能重点。
从上述热收入结构及数据可得,高炉的主要节能方向为降低燃料消耗,亦即降低焦比、燃料比。
2.实现途径
2.1.降低燃料消耗的途径
2.1.1.提高入炉精料水平的有效工艺
槽下供料筛分、整粒工艺:入炉料的粉末每降低1%,可使高炉利用系数提高0.4%~1.0%,入炉焦比降低0.5%。
烧结矿分级入炉工艺:烧结矿分级入炉后矿仓烧结矿粉化率降低1.8%,燃料比降低4.3kg/tFe,生铁含硅降低0.05%。
焦丁回收工艺:根据生产经验焦丁对焦炭的置换比是大于1.05,在一定的冶炼条件下,改善了炉内的透气性,提高了煤气利用率,起到了增产节焦,降低吨铁成本的效果。
2.1.2.高炉的热风温度可以增加带入高炉的热量,减少热收入项中碳素燃烧放热(碳素氧化热)的比例,降低高炉的燃料消耗。
同时,可使煤粉升温加快,改善燃烧条件,提高煤粉燃烧率。
2.1.
3.采用富氧喷煤技术。
一般来说,富氧喷煤冶炼操作,富氧率提高1%,增加喷煤量在12~13kg/t,喷烟煤时增加喷煤量在
17~23kg/t,可有效降低焦比。
2.1.4.高炉采用干熄焦的焦炭生产(可降低入炉焦炭含水量),其焦比可降低2%,以本文所述高炉为例,全年可节约焦炭约1.8万t,按每吨焦炭1800元计,全年因此项节约焦炭产生的经济效益达3240万元。
2.1.5.目前高炉普遍采用富氧喷吹煤粉的技术,但存在问题较多,
因此,高炉利用喷煤的方法达到焦比的极小值是比较困难的。
喷吹煤气(或焦炉煤气)可减少热收入项中碳素燃烧放热(碳素氧化热)的比例,增加喷吹煤气放热,可降低焦比、燃料比。
2.2.减少铁水焓损失的途径
2.2.1.所谓铁水罐“一罐到底”就是高炉承接铁水的铁水罐和转炉铁水罐为统一罐车,此过程温降少,温度起伏低,生产节奏快时,铁水罐到达高炉时包衬和包底温度还较高,使得高炉铁水流入铁水罐内温降相对较少,有利于减少铁水热损失。
2.2.2.近年研究出在安全衬后用致密、高强度隔热板的鱼雷罐车,具体安装方法为在整个罐车中安装隔热层为第一层衬,再安装安全衬,最后一层为耐磨衬。
已隔热的鱼雷罐车较无隔热的罐车中铁水温度平均可提高20℃。
2.2.
3.充分回收炉渣焓的途径
近年来,各钢铁企业也加强了对炉渣热能回收方面的研究,目前有效的实现途径为:
2.2.
3.1.回收炉渣显热产生蒸汽,蒸汽用来发电或采暖;
2.2.
3.2.利用冲渣水采暖,将渣池内热水经沉淀、过滤、加压后供暖,并回流于渣池循环使用,首钢和鞍钢采用过此方法,可节省大
量的能源及人力、物力。
2.2.
3.3.高炉渣干式粒化处理:目前国内外对此处理方式的研究已进入中试阶段,分为普通式和流化床式两类。
本文通过对高炉的热平衡分析,找出高炉的主要节能方向为降低燃料消耗、减少铁水焓损失、充分回收炉渣和煤气焓、减少高炉热损失,探讨了上述几个节能方向的实现途径及节能效果,对今后开展高炉节能降耗方面的研究具有重要的现实意义。
XX设计有限公司
Your Name Design Co., Ltd.。