基于脱丙烷塔的精馏塔建模及稳态仿真
精馏塔的仿真操作
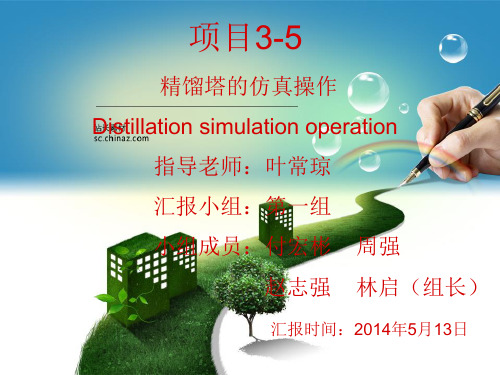
当塔釜液位无法维持时(>35%),逐渐打开fc102 当塔釜产品采出量稳定在7349kg/h,将fc102设置为自动 设定fc102为7349kg/h 将lc101设置为自动 设定lc101为50% 将fc102设置为串级 塔釜产品采出量稳定在7349kg/h 打开fv103前截止阀v41 打开fv103后截止阀v42 当回流罐液位无法维持时,逐渐打开fv103,采出塔顶产品 待产出稳定在6707kg/h,将fc103设置为自动 设定fc103为6707kg/h 将lc103设置为自动 设定lc103为50% 将fc103设置为串级
冷态开车启动
打开PV102A前截止阀V48 打开PV102A后截止阀V49 待塔顶压力PC101升至0.5atm(表压)后,逐渐打开冷凝水调节 待塔釜液位LC101升至20%以上,打开加热蒸汽入口阀V13 打开TV101前截止阀V33 打开TV101后截止阀V34 再稍开TC101调节阀,给再沸器缓慢加热 打开LV102前截止阀V36 打开LV102后截止阀V37 将蒸汽冷凝水储罐FA414的液位控制LC102设为自动 将蒸汽冷凝水储罐FA414的液位LC102设定在50% 逐渐开大TV101至50%,使塔釜温度逐渐上升至100摄氏度
将fc103设置为手动 关闭fc103,停止产品采出 关闭fv103前截止阀v41 关闭fv103后截止阀v42 打开塔釜泄液阀v10 打开回流罐泄压阀v23排不合格产品 将lc102设置为手动 打开lc102,对fa414泄液 当回流罐液位为0时,关闭v23 关闭回流泵Ga412A出口阀v17 停泵GA412A 关闭回流泵GA412A入口阀v19 当塔釜液位为0时,关闭v10 当塔顶压力降至常压,关闭冷凝器 关闭pv102A前截止阀v48 关闭pv102A后截止阀v49
精馏塔仿真指导书
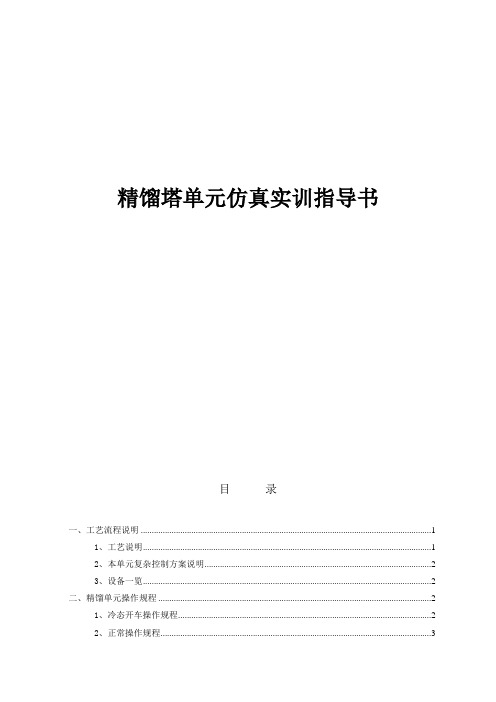
精馏塔单元仿真实训指导书目录一、工艺流程说明 (1)1、工艺说明 (1)2、本单元复杂控制方案说明 (2)3、设备一览 (2)二、精馏单元操作规程 (2)1、冷态开车操作规程 (2)2、正常操作规程 (3)3、停车操作规程 (4)4、仪表一览表 (6)三、事故设置一览 (7)四、仿真界面 (9)附:思考题 (11)一、工艺流程说明1、工艺说明本流程是利用精馏方法,在脱丁烷塔中将丁烷从脱丙烷塔釜混合物中分离出来。
精馏是将液体混合物部分气化,利用其中各组分相对挥发度的不同,通过液相和气相间的质量传递来实现对混合物分离。
本装置中将脱丙烷塔釜混合物部分气化,由于丁烷的沸点较低,即其挥发度较高,故丁烷易于从液相中气化出来,再将气化的蒸汽冷凝,可得到丁烷组成高于原料的混合物,经过多次气化冷凝,即可达到分离混合物中丁烷的目的。
原料为67.8℃脱丙烷塔的釜液(主要有C4、C5、C6、C7等),由脱丁烷塔(DA-405)的第16块板进料(全塔共32块板),进料量由流量控制器FIC101控制。
灵敏板温度由调节器TC101通过调节再沸器加热蒸汽的流量,来控制提馏段灵敏板温度,从而控制丁烷的分离质量。
脱丁烷塔塔釜液(主要为C5以上馏分)一部分作为产品采出,一部分经再沸器(EA-418A、B)部分汽化为蒸汽从塔底上升。
塔釜的液位和塔釜产品采出量由LC101和FC102组成的串级控制器控制。
再沸器采用低压蒸汽加热。
塔釜蒸汽缓冲罐(FA-414)液位由液位控制器LC102调节底部采出量控制。
塔顶的上升蒸汽(C4馏分和少量C5馏分)经塔顶冷凝器(EA-419)全部冷凝成液体,该冷凝液靠位差流入回流罐(FA-408)。
塔顶压力PC102采用分程控制:在正常的压力波动下,通过调节塔顶冷凝器的冷却水量来调节压力,当压力超高时,压力报警系统发出报警信号,PC102调节塔顶至回流罐的排气量来控制塔顶压力调节气相出料。
操作压力 4.25atm (表压),高压控制器PC101将调节回流罐的气相排放量,来控制塔内压力稳定。
脱丙烷精馏塔设计
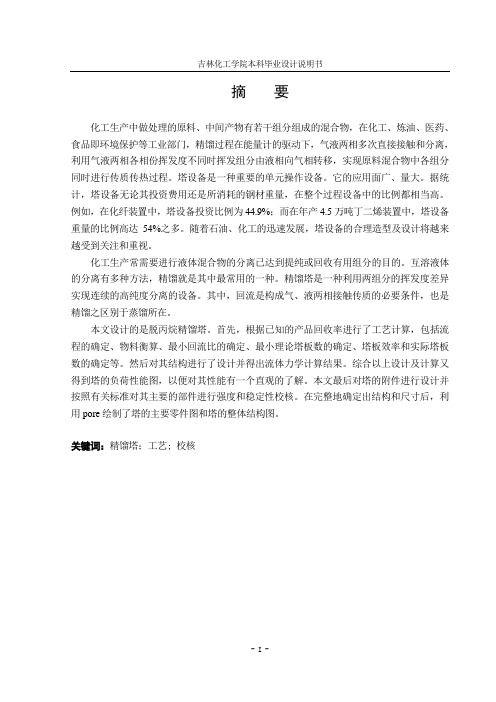
设 , ,查 图得 列下表
表2-3
组分
i
i
n
反
%
1.0
55.0
8.5
15.8
4.8
10.5
1.7
2.7
1
3.6
1.52
1.34
0.675
0.63
0.6
0.52
0.5
1
0.00278
0.3618
0.06343
0.234
0.07762
0.175
三元物系共沸精馏塔建模与仿真

Dy n a mi c S i mu l a t i o n a n d Mo d e l i n g o f t h e Az e o t r o p i c Di s t i l l a t i o n Co l u mn o f Me t h y l a c r y l a t e— — Me t h a n o l— — Wa t e r S y s t e m
ABS TRACT: S t u d y t h e d y n a mi c c h a r a c t e r i s t i c s o f me t h y l a c r y l a t e r e i f n i n g u n i t d i s t i l l a t i o n c o l u mn .I n t h e d i s t i l l a t i o n p r o c e s s ,t h e me t h y l a c r y l a t e a n d w a t e r ,me t h y l a c yl r a t e a n d me t h a n o l f o m r a n a z e o t r o p i c s y s t e m i n t h e r e i f n i n g u n i t d i s t i l l a t i o n c o l u mn .T h e y a r e d i s t i l l e d o u t f r o m t h e t o p o f t h e t o w e r .I n o r d e r t o s t u d y t h e i n t e r n a l c h a r a c t e r i s t i c s o f t h e d i s t i l l a t i o n c o l u mn,MET S H e q u a t i o n s w e r e u s e d t o e s t a b l i s h a me c h a n i s t i c mo d e l o f s t e a d y - s t a t e a n d d y n a mi c ma t h e - ma t i c 1 .T a h e ma t h e ma t i c l a mo d e l wa s s i mp l i ie f d t o c o mp l e t e t h e f a s t c a l c u l a t i o n .F o r t h e t w o a b n o ma r l c o n d i t i o n s , t h e e n t r a i n me n t a n d l e a k a g e t h a t ma y o c c u r i n t h e a c t u l a p l a n t ,e s t bl a i s h e d t h e t r a y e ic f i e n c y e q u a t i o n i n l i n e wi t h t h e a c t u a l s i t u a t i o n .W e c a n s e e t h e p o i n t o f t h e d i s t i l l a t i o n c o l u mn wi t h i n t h e p ra a me t e s r f r o m t h e s i mu l a t i o n r e s u l t s
精馏塔机理模型 matlab

精馏塔机理模型 matlab
精馏塔是化工工业中常见的一种分离设备,它通过蒸馏原理将
混合物分离成不同成分。
在化工工程中,使用Matlab建立精馏塔的
机理模型可以帮助工程师分析和优化精馏塔的操作。
建立精馏塔的
机理模型涉及到多个方面,包括热力学、传质动力学、流体力学等。
首先,建立精馏塔的机理模型需要考虑塔内的物质传递过程。
这包括了液相和气相之间的质量传递和热量传递。
在建立模型时,
需要考虑不同组分在塔内的浓度分布以及塔板上的传质过程。
通过Matlab可以建立相应的传质动力学模型,包括质量平衡方程和能量
平衡方程。
其次,建立精馏塔的机理模型还需要考虑流体力学方面的因素。
这包括了塔内气液两相流的特性,如压降、流速分布等。
在Matlab
中可以建立相应的流体力学模型,通过求解Navier-Stokes方程和
质量守恒方程来描述塔内流体的运动状态。
此外,建立精馏塔的机理模型还需要考虑热力学方面的因素。
这包括了塔内的温度分布、热量平衡等。
在Matlab中可以建立相应
的热力学模型,包括热平衡方程和热传导方程。
综上所述,建立精馏塔的机理模型涉及到多个方面,包括传质
动力学、流体力学和热力学。
通过Matlab可以建立相应的数学模型,并进行数值求解和仿真分析,从而帮助工程师深入理解精馏塔的运
行机理,并进行优化设计。
希望这些信息能够对你有所帮助。
精馏塔的优化及仿真问题

编号:____________审定成绩:____________毕业设计(论文)设计(论文)题目:______________________________单位(系别):______________________学生姓名:______________________专业:______________________班级:______________________学号:______________________指导教师:______________________答辩组负责人:______________________填表时间:20 年月重庆邮电大学移通学院教务处制摘要精馏塔广泛应用于化工行业中的传质传热过程中,精馏塔动态特性复杂,具有多变量、强耦合等特点,所以建立精馏塔的动态数学模型,对精馏塔的动态特性研究以及优化控制研究等具有重要的指导意义。
本文首先研究了建模过程中需要使用的基础物性数据的计算方法,然后针对双组分连续筛板塔建立动态机理模型,包括塔板、进料板、冷凝器、再沸器、塔釜五个模块,各模块相对独立又有明确的输入输出关系。
对各个模块单独使用MESH方程组得到各自以非线性微分方程形式表示的机理数学模型,再通过输入输出顺序获得整塔模型计算方法。
本文将精馏塔数学模型实例化,通过观察不同输入条件和扰动下模型的动态响应和稳态响应,并与实际过程进行比较,表明本模型能较好地模拟精馏过程的动态特性,对精馏塔的控制研究具有较高的实际价值。
根据本文建立的模型,利用离散控制系统设计并实施了多变量预测函数控制系统,以塔顶温度和塔底温度作为间接质量指标控制塔顶和塔底产品浓度,以塔顶回流量和塔底再沸器过热蒸汽流量作为操作变量,构成两输入两输出系统,采用多变量最小二乘法获得预测模型。
通过PCS7结构化控制语言SCL,编写两输入两输出预测函数控制器;通过PCS7连续功能图语言CFC,实现针对精馏塔塔顶温度和塔底温度的多变量预测函数控制系统,并将控制效果与常规单输入单输出PID控制的控制效果进行比较,结果表明,本文提出的控制方案具有更好的鲁棒性和稳定性。
催化精馏过程模拟稳态模型的研究进展

2010年第29卷第4期CHEMICAL INDUSTRY AND ENGINEERING PROGRESS ·101·化工进展催化精馏过程模拟稳态模型的研究进展齐永君,翁惠新(华东理工大学石油加工研究所,上海200237)摘要:对催化精馏过程模拟的平衡级模型、非平衡级模型和非平衡池模型三个常用的稳态模型及其求解方法进行了综述,并简要分析了各模型和求解方法的优缺点,讨论了催化精馏过程模拟的稳态模型及其求解方法未来的发展方向。
关键词:催化精馏;模拟;平衡级模型;非平衡级模型;非平衡池模型中图分类号:TQ 018 文献标识码:A 文章编号:1000–6613(2010)04–0000–00Progress in steady-state models for simulation ofcatalytic distillation processQI Yongjun,WENG Huixin(Petroleum Processing Research Center,East China University of Science and Technology,Shanghai 200237,China)Abstract:Three commonly used steady-state models for catalytic distillation process and their algorithms are reviewed,inc luding the equilibrium stage model,the non-equilibrium stage model and the non-equilibrium cell model. Advantages and disadvantages of each model and algorithm are summarized. Prospects for future development of steady-state models and their algorithms of catalytic distillation are also discussed.Key words:catalytic distillation;simulation;equilibrium stage model;non-equilibrium stage model;non-equilibrium cell model传统的化学反应和精馏分离两个单元操作分别是在反应器和精馏塔两类单独的设备中完成的。
基于脱丙烷塔的精馏塔建模及稳态仿真

化工动态建模报告题目:基于脱丙烷塔的精馏塔建模及稳态仿真姓名: 赵东学号:2011200832班级:信研1102目录一、背景介绍 (3)1、课题背景 (3)2、气分脱丙烷装置介绍 (3)二、模型分析 (5)1、建模方法 (5)2、机理分析 (5)三、模型建立 (7)1、参数整理 (7)2、逐板递推计算公式 (8)四、仿真实验 (10)1、仿真界面 (10)2、仿真验证 (12)2.1、脱丙烷塔的仿真检验 (12)2.2、其它模型工况参数检验 (16)参考文献 (18)附录程序 (19)一、背景介绍1、课题背景精馏塔作为化工流程中最重要的设备之一,一直是人们研究的热点。
而一套好的精馏塔模型,可以给我们的研究和控制带来很多便利。
本课题基于气分脱丙烷过程,研究学习了脱丙烷塔的模型建立,用脱丙烷过程中实际工况数据加以验证。
此外,基于此模型还编制了一个精馏塔稳态仿真的MATLAB界面,适用于其它相似的分离过程,达到方便且快捷仿真的目的。
2、气分脱丙烷装置介绍气体分馏装置是以催化裂化装置所产液化气经脱硫、脱硫醇后作为原料,主要生产精丙烯,再作为聚丙烯装置的原料。
丙烷馏分可作为工业丙烷或与碳四混合后作为民用液化气。
脱除硫化氢和硫醇的催化液化气进入装置,经凝聚脱水器脱除游离水后进入脱丙烷塔进料罐,液化气通过脱丙烷塔进料泵从进料罐抽出,经原料—碳四换热器换热后,再经脱丙烷塔进料加热器加热,以泡点状态进入脱丙烷塔的进料塔板。
脱丙烷塔采用了69层高效浮阀塔。
塔顶蒸出的碳二、碳三馏分经脱丙烷塔顶冷凝器冷凝冷却后进入脱丙烷塔顶回流罐,冷凝液自脱丙烷塔顶回流罐抽出,一部分用脱丙烷塔顶回流泵送入塔顶第69层塔板上作为塔顶回流,另一部分用脱乙烷塔进料泵抽出作为进料。
脱丙烷塔底再沸器热源为中压蒸汽。
塔底碳四采出馏分经于原料换热后,再经碳四馏分冷却器冷却后送至液化气罐区。
如图1.1[1]。
图1.1 气分装置流程图二、模型分析1、建模方法系统建模的方法一般有机理建模、实验建模(系统辨识)以及前两种方法的综合。
精馏塔操作仿真训练

技能训练二精馏塔操作仿真训练●训练目标能利用仿真系统操作精馏塔。
●训练准备熟悉工艺流程及原理。
本单元是一种加压精馏操作,原料液为脱丙烷塔塔釜的混合液,分离后馏出液为高纯度的C4产品,残液主要是C5以上组分。
67.8℃的原料液经流量调节器FICl01控制流量(14056kg/h)后,从精馏塔DA405的第16块塔板(全塔共32块塔板)进料。
塔顶蒸气经全凝器EA419冷凝为液体后进入回流罐FA408;回流罐FA408的液体由泵GA412A/B抽出,一部分作为回流液由调节器FCl04控制流量(9664kgm)送回DA405第32层塔板;另一部分则作为产品,其流量由调节器FCl03控制(6707kg/h)。
回流罐的液位由调节器LCl03与FCl03构成的串级控制回路控制。
DA405操作压力由调节器PCI02分程控制为5.0kg/m2,其分程动作如图3-34所示。
同时调节器PCI01将调节回流罐的气相出料,保证系统的安全和稳定。
图3-34调节阀PVl02分程动作示意图塔釜液体的一部分经再沸器EA408A/B回精馏塔,另一部分由调节器FCl02控制流量(7349kg/h),作为塔底采出产品。
调节器LCl01和FCl02构成串级控制回路,调节精馏塔的液位。
再沸器用低压蒸汽加热,加热蒸汽流量由调节器TCl01控制,其冷凝液送FA414。
FA414的液位由调节器LCl02调节。
其工艺流程如图3-35所示。
图3-58 精馏塔单元带控制点工艺流程图●训练步骤(要领)(一)冷态开车进料前确认装置冷态开工状态为精馏塔单元处于常温、常压、氮气吹扫完毕的氮封状态,所有阀门、机泵处于关停状态、所有调节器置于手动状态。
1.进料及排放不凝气(1)打开PVl01(开度>5%)排放塔内不凝气;(2)打开FVl01(开度>40%),向精馏塔进料;(3)进料后,塔内温度略升、压力升高;当压力升高至0.5atm(表)时(4)控制塔顶压力大于1.0atm(表),不超过4.25atm(表)。
精馏塔工艺仿真实验报告

精馏塔工艺仿真实验报告一、实验目的1. 了解精馏塔的基本工作原理及其应用。
2. 掌握精馏塔工艺仿真实验装置的操作方法。
3. 学习利用工艺仿真软件进行精馏塔操作仿真。
二、实验原理精馏塔是一种重要的化工分离设备,其主要功能是将混合物中的组分分离出来,获得高纯度或高浓度的单一组分。
精馏塔工艺仿真实验是通过模拟精馏塔在实际运行中的操作过程和工作状态,评估和优化精馏塔的操作参数和工艺流程。
在精馏塔中,混合物从塔底进入,经过塔中逐级升温蒸发,产生蒸汽。
蒸汽在较低的温度下与更易挥发的组分混合物相互作用,从而达到分离的目的。
高浓度的组分随着蒸汽上升到塔顶,经过冷凝器冷却变成液态,分离出来并从顶部流出。
该液态物质通常称为“顶产”,而在塔底下部残留的液态混合物则称为“底产”。
三、实验步骤1. 检查精馏塔工艺仿真实验装置是否完好无损,确认实验用品及原材料准备充分。
2. 打开工艺仿真软件,建立相应的工艺流程和模型。
3. 添加需要分离的混合物,并设置该混合物在塔中的初始浓度和物理性质。
4. 设置塔的操作参数,包括初始温度、加热速率、冷却速率、运行时间等。
5. 开始模拟操作,并对模型进行观察和监控。
6. 收集并记录塔顶和底部的产物,并测量其浓度和物理性质。
7. 分析和评估操作结果,根据需要进行调整和优化。
8. 关闭工艺仿真软件和实验装置,做好清洗和消毒工作。
四、实验结果和分析通过精馏塔工艺仿真实验,可以获得不同操作参数和工艺流程下的顶产和底产,从而评估和优化精馏塔的操作效果。
实验结果直接关系到产品质量和产量的稳定性,因此需要进行详细的分析和评估。
在模拟操作过程中,精馏塔中的温度、压力、产物流速等参数变化会影响精馏的分离效率。
通常情况下,较高的温度和压力可以促进蒸发和挥发,加快顶产的产出速度,但也容易造成部分组分不完全挥发和分离,影响底产的纯度和产量。
需要根据实际需要和产品质量要求来确定合适的操作参数和控制策略。
在实验过程中还需要注意操作安全和环保问题,避免产生对人体健康和环境产生危害的化学物质。
精馏过程中非稳态数学模型的建立与求解研究概述
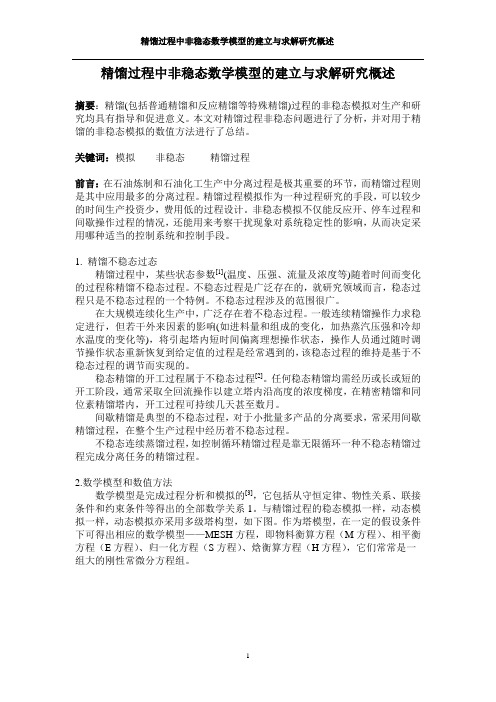
精馏过程中非稳态数学模型的建立与求解研究概述摘要:精馏(包括普通精馏和反应精馏等特殊精馏)过程的非稳态模拟对生产和研究均具有指导和促进意义。
本文对精馏过程非稳态问题进行了分析,并对用于精馏的非稳态模拟的数值方法进行了总结。
关键词:模拟非稳态精馏过程前言:在石油炼制和石油化工生产中分离过程是极其重要的环节,而精馏过程则是其中应用最多的分离过程。
精馏过程模拟作为一种过程研究的手段,可以较少的时间生产投资少,费用低的过程设计。
非稳态模拟不仅能反应开、停车过程和间歇操作过程的情况,还能用来考察干扰现象对系统稳定性的影响,从而决定采用哪种适当的控制系统和控制手段。
1. 精馏不稳态过态精馏过程中,某些状态参数[1](温度、压强、流量及浓度等)随着时间而变化的过程称精馏不稳态过程。
不稳态过程是广泛存在的,就研究领域而言,稳态过程只是不稳态过程的一个特例。
不稳态过程涉及的范围很广。
在大规模连续化生产中,广泛存在着不稳态过程。
一般连续精馏操作力求稳定进行,但若干外来因素的影响(如进料量和组成的变化,加热蒸汽压强和冷却水温度的变化等),将引起塔内短时间偏离理想操作状态,操作人员通过随时调节操作状态重新恢复到给定值的过程是经常遇到的,该稳态过程的维持是基于不稳态过程的调节而实现的。
稳态精馏的开工过程属于不稳态过程[2]。
任何稳态精馏均需经历或长或短的开工阶段,通常采取全回流操作以建立塔内沿高度的浓度梯度,在精密精馏和同位素精馏塔内,开工过程可持续几天甚至数月。
间歇精馏是典型的不稳态过程,对于小批量多产品的分离要求,常采用间歇精馏过程,在整个生产过程中经历着不稳态过程。
不稳态连续蒸馏过程,如控制循环精馏过程是靠无限循环一种不稳态精馏过程完成分离任务的精馏过程。
2.数学模型和数值方法数学模型是完成过程分析和模拟的[3],它包括从守恒定律、物性关系、联接条件和约束条件等得出的全部数学关系1。
与精馏过程的稳态模拟一样,动态模拟一样,动态模拟亦采用多级塔构型,如下图。
使用仿真系统建立塔模型及简要分析

应用过程模拟软件对脱乙烷塔工艺流程分析都炎飞,宋力恒(大庆炼化公司培训中心,黑龙江大庆 163411)摘要:利用应用过程模拟软件PRO/II和Dynsim对脱乙烷塔进行了工艺流程仿真模拟分析。
由于装置的局部改造及外界干扰因素的影响,在建立动态过程模型之前,应先建好PRO/II静态模型,以便获得合理的物料平衡、能量平衡以及相关的重要工艺参数等数据,这些数据对使用Dynsim建立动态过程模型尤为重要。
关键词:过程仿真;脱乙烷塔; PRO/II; DynsimPRO/II和Dynsim均为功能全面的、基于严格计算的、成熟的过程模拟软件,其中,PRO/II 是静态版本,Dynsim则是动态版本。
这2种软件在模型计算方面都运用了基于机理的技术和严格的热力学方法进行计算,能够通过计算获得准确可靠的结果,用于解决从工程分析、控制系统校核到操作员培训等动态模拟问题[1]。
1 塔模型的建立(1)热力学计算塔动态模型搭建出现问题的重要的原因就是热力学和闪蒸的设置不合适,所以在开始Dynsim建模前,应当先确认好热力学的设置。
轻烃精馏通常可以采用PR、SRK以及SRKM等热力学方法计算,在建模过程中,应当先使用PRO/II通过选取各种热力学方法来对模型进行计算,对计算结果与生产工艺参数或设计参数进行对比,以最终确定在使用Dynsim建立动态过程模型时所应用的算法[2]。
(2)稳态模型搭建由于PRO/II在计算时只考虑稳态结果,不考虑流量调整对其产生的动态影响,因此,塔的模型中直接包含了塔底再沸系统和塔顶的回流系统,以某气体分馏装置中脱乙烷塔为例,该塔主要应用于裂解气分离,是用来将乙烷(包括更轻组分)与丙烯及更重组分进行分离的精馏塔,塔顶出乙烷和更轻组分(如乙烯、甲烷),塔底出丙烯和更重组分,在炼油装置中比较常见。
该塔的主要进料包括乙烷、丙烯和丙烷等组分。
由于文中所模拟的装置为已投产装置,因此在搭建过程中对原设计数据只进行了参考,模型搭建所采用的数据是来源于生产操作台帐及产品分析数据,在PRO/II中对塔的模型做了如下工艺规定:塔顶回流量38 t/h;塔顶温度58 ℃。
精馏塔的仿真操作
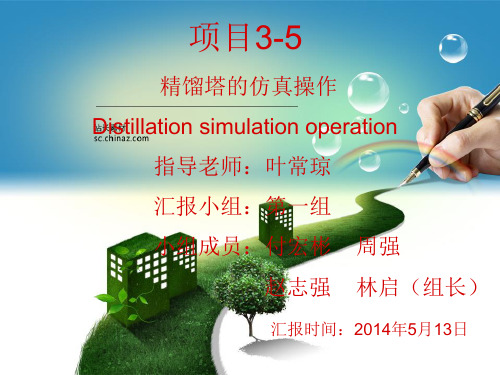
将fc103设置为手动 关闭fc103,停止产品采出 关闭fv103前截止阀v41 关闭fv103后截止阀v42 打开塔釜泄液阀v10 打开回流罐泄压阀v23排不合格产品 将lc102设置为手动 打开lc102,对fa414泄液 当回流罐液位为0时,关闭v23 关闭回流泵Ga412A出口阀v17 停泵GA412A 关闭回流泵GA412A入口阀v19 当塔釜液位为0时,关闭v10 当塔顶压力降至常压,关闭冷凝器 关闭pv102A前截止阀v48 关闭pv102A后截止阀v49
项目3-5
精馏塔的仿真操作 Distillation simulation பைடு நூலகம்peration
指导老师:叶常琼 汇报小组:第一组 小组成员:付宏彬 周强
赵志强 林启(组长)
汇报时间:2014年5月13日
任务要求
➢冷态开车的操作规程编制 ➢冷凝水中断的操作规程编制 ➢停电的操作规程编制
冷态开车的操作规程编制 冷态开车的进料
打开PV102B前截止阀V51 打开PV102B后截止阀V52 打开PV101前截止阀V45 打开PV101后截止阀V46 微开PV101排放塔内不凝气 打开FV101前截止阀V31 打开FV101后截止阀V32 向精馏塔进料:缓慢打开FV101,直到开度大于40% 当压力升高至0.5atm(表压)时,关闭PV101 塔顶压力大于1atm,不超过4.25atm
停电的操作规程编制
将pc101设置为手动 打开回流罐放空阀pv101 将fic101设置为手动 关闭fic101,停止进料 关闭fv101前截止阀v31 关闭fv101后截止阀v32 将tc101设置为手动 关闭tc101,停止加热蒸汽 关闭tv101前截止阀v33 关闭tv101后截止阀v34 将fc102设置为手动 关闭fc102,停止产品产出 关闭fv102前截止阀v39 关闭fv102后截止阀v40
精馏塔

文档编号:TSS_C4.DOC精馏塔单元仿真培训系统操作说明书北京东方仿真软件技术有限公司二〇〇六年十月目录一、工艺流程说明 21、工艺说明 22、本单元复杂控制方案说明 23、设备一览 3二、精馏单元操作规程 31、冷态开车操作规程 32、正常操作规程 43、停车操作规程 54、仪表一览表 6三、事故设置一览7四、仿真界面9附:思考题11一、工艺流程说明1、工艺说明本流程是利用精馏方法,在脱丁烷塔中将丁烷从脱丙烷塔釜混合物中分离出来。
精馏是将液体混合物部分气化,利用其中各组分相对挥发度的不同,通过液相和气相间的质量传递来实现对混合物分离。
本装置中将脱丙烷塔釜混合物部分气化,由于丁烷的沸点较低,即其挥发度较高,故丁烷易于从液相中气化出来,再将气化的蒸汽冷凝,可得到丁烷组成高于原料的混合物,经过多次气化冷凝,即可达到分离混合物中丁烷的目的。
原料为67.8℃脱丙烷塔的釜液(主要有C4、C5、C6、C7等),由脱丁烷塔(DA-405)的第16块板进料(全塔共32块板),进料量由流量控制器FIC101控制。
灵敏板温度由调节器TC101通过调节再沸器加热蒸汽的流量,来控制提馏段灵敏板温度,从而控制丁烷的分离质量。
脱丁烷塔塔釜液(主要为C5以上馏分)一部分作为产品采出,一部分经再沸器(EA-418A、B)部分汽化为蒸汽从塔底上升。
塔釜的液位和塔釜产品采出量由LC101和FC102组成的串级控制器控制。
再沸器采用低压蒸汽加热。
塔釜蒸汽缓冲罐(FA-414)液位由液位控制器LC102调节底部采出量控制。
塔顶的上升蒸汽(C4馏分和少量C5馏分)经塔顶冷凝器(EA-419)全部冷凝成液体,该冷凝液靠位差流入回流罐(FA-408)。
塔顶压力PC102采用分程控制:在正常的压力波动下,通过调节塔顶冷凝器的冷却水量来调节压力,当压力超高时,压力报警系统发出报警信号,PC102调节塔顶至回流罐的排气量来控制塔顶压力调节气相出料。
精馏塔的动态模拟

精馏塔的动态模拟目录一、数学建模二、分析与讨论三、优化四、程序清单(1)分析和讨论(2)分析和讨论(3)最优化部分前言化学工业中,精馏过程是能量消耗最大的单元操作之一,自从发生了世界性的能源问题以来,精馏过程的节能问题已广泛引起了人们的重视。
近年来,已经开发了多种精馏节能的工艺流程,如多效精馏.热泵精馏、热偶精馏等。
多效精馏作为一种精馏节能新工艺近几年来其理论研究不断深入,在工业生产中的应用日益广泛。
工业上普遍存在非稳定状态或动态的精馏过程.实际的生产过程不可避免地受到各种人为或非人为因素的扰动,使一些操作参数和过程变量随时间发生变化,因此对于连续精馏过程的动态特性的研究和模拟具有重要的实际意义.研究精馏塔的动态特性时通常使用数学模拟方法,这首先需要建立1个模型精馏塔,然后对模型塔中的各个塔板作非稳态物料衡算、热量衡算等,得到动态精馏过程的数学模型,在一定的初始条件下经过求解,可得到操作条件发生扰动时各个精馏过程参数随时间变化的历程,即动态响应.若精馏系统内无约束某些参数变化速度和变化范围的控制器,其动态响应称为开环响应,否则为闭环响应.反应精馏技术将反应与分离过程在一个塔内实现, 相对传统的先反应后分离过程具有转化率高、选择性好、操作易、投资省等一系列优点, 但反应精馏过程需同时遵循质量作用定律和精馏分离原理, 其过程影响因素复杂. 自20 世纪70 年代以来, 有关反应精馏的研究重点从工艺转向数学模拟. 现已开发有灵活可靠的过程模拟计算软件. 另一方面, 自20 世纪70 年代末催化精馏技术成功地应用于甲基叔丁基醚(M TBE) 生产以后, 该技术的应用受到了学者们的关注.一、精馏塔数学模型的建立:根据对过程系统中状态变量分布特征的不同描述方法,一般可以把数学模型分为集中参数模型,分布参数模型和多级集中参数模型。
本次大作业利用多级集中参数模型对精馏塔动态特性进行分析和模拟。
对于控制的动态数学模型,我们希望用最简单的形式,最大限度地概括出过程的特性。
一种气分脱丙烷塔模拟优化的方法探讨

一种气分脱丙烷塔模拟优化的方法探讨隋晓东;王海霞【摘要】2016年检修前后,对大庆炼化公司一套气分装置的脱丙烷塔的工况进行分析,发现其塔压及回流量有可优化的空间.然后应用流程模拟技术对其进行建模,并对操作条件进行研究,优化得到最佳的生产工况,确保其在保证产品质量的前提下,尽可能地节约蒸汽消耗.%Before and after the overhaul in 2016,the working conditions of the de-propane tower of a gas divider in Daqing Refining & Chemical Company were analyzed and it was found that there was room for optimization of the tower pressure and the reflux rate.Then it uses the flow simulation technology to model it,studies the operating conditions and optimizes the optimal production conditions to ensure that it can save steam consumption as much as possible under the premise of ensuring product quality.【期刊名称】《化工设计通讯》【年(卷),期】2018(044)002【总页数】2页(P112,156)【关键词】流程模拟;气分装置;脱丙烷塔;节能降耗【作者】隋晓东;王海霞【作者单位】大庆炼化公司生产技术处,黑龙江大庆 163411;大庆炼化公司润滑油厂,黑龙江大庆 163411【正文语种】中文【中图分类】TE961 装置简介大庆炼化公司一套气分装置设计规模35万t/a,装置原料为经过脱硫后的液化石油气,主要产品为纯度≥99.6%的精丙烯。
气体分馏装置脱丙烷塔的流程模拟

气体分馏装置脱丙烷塔的流程模拟刘宗林;苏成利;李平【期刊名称】《化工自动化及仪表》【年(卷),期】2011(038)010【摘要】以某石化公司300kt/a气体分馏装置中脱丙烷塔为研究对象,运用流程模拟软件PRO/Ⅱ进行稳态模拟,使脱丙烷塔在产品质量符合要求的条件下,塔的操作参数最佳,塔的能耗值达到最小.综合考虑各关键影响因素,采用流程模拟软件PRO/Ⅱ的灵敏度分析方法,对该塔进行模拟分析,并对分析的结果进行总结和讨论.%Taking the depropanizer in a 300kt/a gas fractionation unit as study object and having it simulated in steady state with PRO/II software and the simulation result analyzed. The result shows that by optimizing the operating parameters, the energy consumption can be decreased while the products quality is satisfied.【总页数】4页(P1254-1257)【作者】刘宗林;苏成利;李平【作者单位】辽宁石油化工大学信息与控制工程学院,辽宁抚顺 113001;辽宁石油化工大学信息与控制工程学院,辽宁抚顺 113001;辽宁石油化工大学信息与控制工程学院,辽宁抚顺 113001【正文语种】中文【中图分类】TP393【相关文献】1.48万吨/年气体分馏装置脱丙烷塔运行及优化 [J], 叶辉2.应用流程模拟优化气体分馏装置塔底温度 [J], 吴章柱;马建民;于兆臣;张磊;林雪飞3.一种气分脱丙烷塔模拟优化的方法探讨 [J], 隋晓东;王海霞4.前脱丙烷流程乙烯装置脱丙烷塔改造方案 [J], 瞿笑蕾5.气体分馏装置脱丙烷塔浮压控制 [J], 周仲琦因版权原因,仅展示原文概要,查看原文内容请购买。
- 1、下载文档前请自行甄别文档内容的完整性,平台不提供额外的编辑、内容补充、找答案等附加服务。
- 2、"仅部分预览"的文档,不可在线预览部分如存在完整性等问题,可反馈申请退款(可完整预览的文档不适用该条件!)。
- 3、如文档侵犯您的权益,请联系客服反馈,我们会尽快为您处理(人工客服工作时间:9:00-18:30)。
化工动态建模报告题目:基于脱丙烷塔的精馏塔建模及稳态仿真姓名: 赵东学号:2011200832班级:信研1102目录一、背景介绍 (3)1、课题背景 (3)2、气分脱丙烷装置介绍 (3)二、模型分析 (5)1、建模方法 (5)2、机理分析 (5)三、模型建立 (7)1、参数整理 (7)2、逐板递推计算公式 (8)四、仿真实验 (10)1、仿真界面 (10)2、仿真验证 (12)2.1、脱丙烷塔的仿真检验 (12)2.2、其它模型工况参数检验 (16)参考文献 (18)附录程序 (19)一、背景介绍1、课题背景精馏塔作为化工流程中最重要的设备之一,一直是人们研究的热点。
而一套好的精馏塔模型,可以给我们的研究和控制带来很多便利。
本课题基于气分脱丙烷过程,研究学习了脱丙烷塔的模型建立,用脱丙烷过程中实际工况数据加以验证。
此外,基于此模型还编制了一个精馏塔稳态仿真的MATLAB界面,适用于其它相似的分离过程,达到方便且快捷仿真的目的。
2、气分脱丙烷装置介绍气体分馏装置是以催化裂化装置所产液化气经脱硫、脱硫醇后作为原料,主要生产精丙烯,再作为聚丙烯装置的原料。
丙烷馏分可作为工业丙烷或与碳四混合后作为民用液化气。
脱除硫化氢和硫醇的催化液化气进入装置,经凝聚脱水器脱除游离水后进入脱丙烷塔进料罐,液化气通过脱丙烷塔进料泵从进料罐抽出,经原料—碳四换热器换热后,再经脱丙烷塔进料加热器加热,以泡点状态进入脱丙烷塔的进料塔板。
脱丙烷塔采用了69层高效浮阀塔。
塔顶蒸出的碳二、碳三馏分经脱丙烷塔顶冷凝器冷凝冷却后进入脱丙烷塔顶回流罐,冷凝液自脱丙烷塔顶回流罐抽出,一部分用脱丙烷塔顶回流泵送入塔顶第69层塔板上作为塔顶回流,另一部分用脱乙烷塔进料泵抽出作为进料。
脱丙烷塔底再沸器热源为中压蒸汽。
塔底碳四采出馏分经于原料换热后,再经碳四馏分冷却器冷却后送至液化气罐区。
如图1.1[1]。
图1.1 气分装置流程图二、模型分析1、建模方法系统建模的方法一般有机理建模、实验建模(系统辨识)以及前两种方法的综合。
在精馏塔的建模中,机理建模在同类对象中推广能力强,工况变化时仍能给出较好的结果。
相反,辨识法得到的模型的推广能力就差一些,但是不要求对对象的运行机理有多少了解。
在这里我们选用机理建模。
机理建模有简化法[2]和逐板计算法[1,2]。
简化法一般只用于二元精馏、轻烃分离中的快速估算。
逐板计算则是依据理论板的定义,在给定条件下对每一板进行物料平衡、相平衡和热量平衡的计算,一般需要反复迭代。
本课题选用逐板计算方法。
2、机理分析脱丙烷塔的精馏过程可由物料平衡、相平衡、热量平衡和摩尔分率总和四组方程来描述。
为了简化模型,提出如下假设:1)每块塔板上的汽液相充分混合; 2)塔板液相滞留量保持恒定; 3)忽略热量损失及塔板热容;4)液相与气相在离开塔板时处于汽液平衡状态; 5)精馏段和提馏段上升气量及下降液量保持不变。
建立热力学方程如下:1) 物料平衡方程:11j ,,,1,11,1j jj j j i j j i j j i jj i j j i j F V L V L F z V y L x V y L x -+--++++=+++=+ (2.1)2) 组分相平衡:,,,i j i j i j y k x =(2.2),i j k 为平衡常数。
3) 分子分率归一化方程:,,11i ji i jixy==∑∑(2.3)4) 热量平衡: ,,,1,11,1f v l v l j i j j j i j j i j j i j j i j F h V h L h Q V h L h --+++++=+(2.4)其中:i 为物料中组分; j 为塔板位置; F 为进料量; Z 为进料组成;f h 为进料焓值;V 为塔中气相流量; L 为塔中液相流量; y 为气相中物料组成; x 为液相中物料组成;l h 为液相焓值; v h 为气相焓值; j Q 为热交换量。
三、模型建立1、参数整理将脱丙烷塔分为三部分,塔板段、冷凝器和再沸器(也可分为四部分,其中塔板段又分为精馏段和提留段[2,3,4])。
总有69层塔板,为了便于计算,将再沸器和塔顶冷凝器均算作一块塔板(若不想这样处理,只要在逐板计算的第一个和最后一个方程计算时,带入适当参数即可[2]),则该塔有71块塔板,塔板编号按照从下到上的顺序排列,进料在第38块塔板。
如图3.1所示:图3.1 脱丙烷塔原理图若不考虑能量损失,将塔内的乙烷和丙烷看作轻组分,其余为重组分,则得到一个二元精馏塔对象。
这样模型中只有一类状态变量,即每层塔板上轻组分含量(这里不考虑各层塔板的温度和压力)。
图3.2列出了脱丙烷塔的四个组成部分:塔板、进料板、塔顶冷凝器和塔底再沸器。
脱丙烷塔有三个进出流量,分别是进料流量F,塔顶采出量D,塔底采出量B。
内部有塔顶回流量L,塔底再沸器产生蒸汽量V。
图3.2 脱丙烷塔机理分析图其中参数为:L 为塔顶回流量;V 为再沸器产生的蒸汽量;D x 为塔顶采出轻组分含量;B x 为塔底采出轻组分含量;F 为进料流量;zF 为进料中轻组分含量; qF 为进料中液体含量; n 为塔板数量。
由图可以得出D=V-L ,B=F+L-V 。
若是在控制系统中,L 与V 为控制变量,塔顶和塔底轻组分含量为被控变量。
2、逐板递推计算公式由恒相对挥发度假设,气液平衡方程为:()1,2,...,1,()01(1)ii n iax k x i n k x a x ==-=+-(3.1)若假设每层塔板气体滞留量相同,都等于塔底再沸器蒸汽量,有,1,2,...,1,0i n V V i n V ==-=(3.2)假设每层塔板液体滞留量相同,从下往上编号,得到以下逐板递推计算公式: 塔底再沸器:11211()()()dx H L F x L F V x Vk x dt=+-+-- (3.3)提馏段塔板:11()()()()2,...,1iii i i i dx H L F x Vk x L F x Vk x dti nf +-=++-+-=- (3.4)进料塔板: 11()()()nf nfnf nf nf nf dx H Lx Vk x L F x Vk x FzF dt+-=+-+-+(3.5)精馏段:111,...,1iii i i i dx H Lx Vy Lx Vy i nf n dt+-=+--=+- (3.6)塔顶冷凝器:1()()nnn n n dx H Vk x Lx V L x dt-=--- (3.7)因为公式3.5-3.11需要编程实现,故需要对原始递推公式做一定的整理。
具体来说,对于每层塔板的轻组分的浓度的导数idx dt需要离散化,以保证能够编程实现。
上面得到的都是常系数线性微分方程,这里采用一阶欧拉法来求解,具体方法如公式3.12:1i i idx x x dt h+-=(3.8)其中h 是微分步长,h 的大小一般不易取太大,否则会加大累积的截断误差;若取太小,可能会造成仿真最终结果不是稳态值(具体见仿真平台部分),一般可取1。
四、仿真实验1、仿真界面基于逐板计算的递推公式,编制了脱丙烷塔的稳态仿真程序,并为之配备了交互界面,如图4.1所示。
图4.1 精馏塔稳态仿真界面仿真界面分为精馏塔稳态运行参数输入和仿真计算参数输入两大输入模块,其中各个参数输入时,需要注意该参数的单位是否与仿真界面上的单位一致,如果不同,请自行转换,此外,若输入塔板数和进料塔板数不是整数,仿真程序会自动提醒。
点击“OK”按钮,则报错窗口关闭。
如图4.2所示图4.2 自动提醒在输入完仿真程序运行所必须的参数后,可以选择查看某些塔板的轻组分浓度过渡过程曲线,请按照1*n的矩阵形式输入(用空格或者“,”分隔)。
若输入为“[0]”,则程序默认为选择查看塔底和塔顶的浓度曲线。
所有输入数据完成后,点击“RUN”按钮,运行仿真程序,运行完毕后,我们可以在仿真界面的右下角看到稳态时,塔顶和塔底的轻组分浓度比率数值。
在输入计算参数时,若“h”选择过小,“dt”过大,“tt”过小,可能会造成仿真程序运行完后,精馏塔还未达到稳态,如图4.4所示。
系统会自动弹出警告窗口,如图4.3所示,提醒用户选择更好的计算参数输入。
这时候就需要在查看相应塔板浓度曲线的基础上,结合警告窗口的提示信息,修改以上计算参数,确保塔顶和塔底轻组分浓度数值为稳态值。
图4.3 警告示意图注意,由于程序中采用的是欧拉法离散化模型进而求解的,不能无限增大微分步长h(h过大,会增大累积误差,可能使最后的结果误差很大),建议修改时尽量修改dt和tt。
图4.4 未达到稳态时的塔顶和塔底浓度曲线2、仿真验证现在,输入相应的工况参数,查看仿真效果。
2.1、脱丙烷塔的仿真检验首先,输入脱丙烷塔的工况参数,具体参数值见下表。
表4.1 脱丙烷塔稳态工况参数进料流量(F )288.39kmol/h 塔顶轻组分(xd ) 0.99 进料液体含量(qF ) 1塔底轻组分(xb ) 0.034进料轻组分含量(zF ) 50.01%塔顶回流量(L ) 475.42kmol/h 塔底再沸量(V ) 619.49kmol/h 相对挥发度(a ) 1.55 塔板数(n )71进料塔板(nf )38塔板滞液量(1-38)0.48kmol塔板滞液量(39-71)0.46kmol可以由D=V-L 得塔底采出为144.07kmol/h ,B=F+L-V 为144.32kmol/h 。
下面将会用到这些参数。
根据仿真界面的要求,进行相应的单位转换之后,输入工况参数,选择h=0.5,dt=1,tt=4000,运行仿真程序,得到塔底和塔顶的的轻组分浓度数据以及动态曲线,其中 Xd=0.9615850100150200250300Time(s)浓度塔顶和塔底浓度过渡过程曲线Xb=0.038812 曲线见图4.5图4.5 塔顶和塔底浓度动态曲线仿真得到的结果与表4.1中给出的实际工况塔顶及塔底浓度相比有一定误差,但是已经非常接近与真实值。
假若想要仿真效果更进一步,可以从求解微分方程的方法(如龙格-库塔法)以及确定合适的迭代次数入手。
下面检验工况变化对浓度的影响,由于精馏塔内部各个参数都不是独立存在的,所以严格来说,根据目前的工况参数信息是不能够100%准备地模拟出某个参数变化对塔顶和塔底轻组分浓度的影响的;但是这里做近似处理,为了得到单个参数的变动影响,设其它参数都不会有太大的改变,这样我们就能够从仿真的角度,知道参数变动的效果了。
1)假若进料中轻组分浓度增大,如0.6001,查看仿真效果如图4.6。
其中xd=0.99002 Xb=0.17911由化工原理的知识可以得到,增大进料轻组分浓度,可以一定程度上提高塔顶轻组分浓度,但是同时塔底轻组分浓度也相应的增大。